Highlight the line item of interest on the PO Receiving and Inspection screen.
Depress the Work Order Shortage List and Issue button.
Highlight the work order shortage at top of screen.
Drag Available Qty located in the middle of your screen under Incoming Receipt.
Drop it in the quantity issued at the bottom of your screen as displayed below. System will allow users to pick to each of the individual shortages within the same Work Order and/or different Work Orders.
The Approved box will be checked if the AVL that you are receiving is an approved AVL for that shortage. This will give the users the needed information on screen to make the decision to use or not use a non-approved AVL to fulfill a shortage.
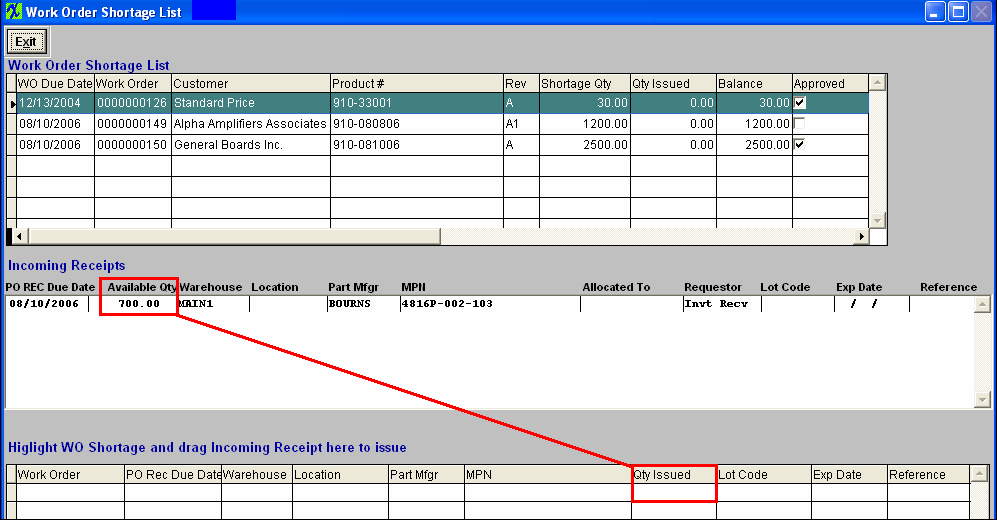
System will not allow user to issue quantities greater than the shortage quantity. See Article #2479 for further detail.
The following messge will be displayed if user issues a quantity greater than the shortage quantity.

NOTE: If a user has the Work Order Checklist feature active and tries to use the PO Receiving shortage and issues feature within the PO Receiving, it will not recognize the shortages until the kit has been flagged as "Kit Complete". It is designed this way because the user will not know if the parts are short until the kit is completed.
You may have parts in the inventory and have not pulled them to the kit yet. If you allow seeing the shortage (which may not be a shortage because parts are not pulled yet) from the PO receiving, the receiver may be trained to automatically issue to the shortages first, but it may not be a shortage because parts have not been pulled from inventory, so how would they know if it is a real shortage or just not pulled from inventory yet.
|