1. FAQ - Bill of Material (BOM) |
1.1. BOM Unit of Measure | If a user tries to enter in a fraction of a number for a part that is setup with a UOM of EACH or EA, they will receive the following warning:
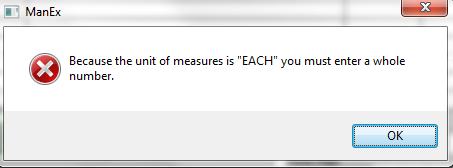
EACH or EA in the system is considered a whole number and you will not be allowed to enter in a fraction of a number for those UOMs. The reason is you can NOT actually have a Fraction of whole number. If you need to have a fraction of a number on the bom, etc. . . we recommend that you use a UOM other than EACH or EA then the system will allow you to enter in the Fraction.
The maximum number of decimals in the BOM quantity is 2, allowing for 1/100th of an item. The reason is so the system operates properly (mainly the MRP and Kitting). If we allowed a fraction of a number to be used the order or kitting quantities may be incorrect for the customers that use the MRP and Kitting modules. If users need a finer resolution, you may want to consider using a different UoM than EACH, and buy in one unit and use a fractional unit for inventory (e.g. Purchase in Gallons, and Stock/Issue in ounces). The system will allow you to create other categories in the UOM to correct this problem. With this fix, both the MRP and Kitting works correctly.
|
1.2. Do Users Tie Parts to Specific Operations to Help Issue Separate Kits to Various Dept? |
Do Users Tie Parts to Specific Operations to Help Issue Separate Kits to Various Dept?
ManEx does have the ability, and many users utilize it, to identify the work station where components will be used. This is identified in the BOM. Kitting may then kit specifically for work stations for which the parts are consumed.
|
1.3. How does the Std Bld affect the Std Cost Roll-up? |
1.4. How do I create a list of BOMs with and without components loaded? | ManEx has created a utility called bomlisting.exe that will create an excel file of all make parts in ManEx and designate which have components and which do not.
stats |
part_no |
revision |
descript |
Has Components: |
000-0000259 |
|
PAGER,OPTION LCR5000H |
Has Components: |
000-0000258 |
A |
PAGER,OPTION LCR5000H |
Has Components: |
910-0000288 |
|
QPLTESTBOM1 |
Has Components: |
910-0000290 |
|
QPLTESTBOM2 |
Has Components: |
000-0000324 |
|
SMART DISPLAY |
Has Components: |
COH-0011-0855 |
A |
COH-0011-0855 |
Has Components: |
000-0000335 |
|
Test BoM |
Has Components: |
910-1001.1 |
A |
Test-1A |
No Components: |
910-1000 |
A |
Test-a |
No Components: |
910-247767-01900 |
9 |
PCB,MAIN W/O ATP |
No Components: |
5FG6HJ791 |
|
Test 1 |
No Components: |
910-TEST2 |
|
TEst2 |
Although this executable is not commonly available, it can be made available upon request. If you would like a copy of this file, please contact cs@manex.com requesting this executable. |
1.5. Possible Reasons why the Std Cost Roll differs from the Cost BOM Rpts |
The values displayed should be in sync with the BOM with Std Cost Report values. The following may be why the Standard Cost Roll is different from the Cost BOM Reports.
a) On the costed BOM Report for a Make/Buy assembly we display the value of the BOM in the costed report, but that total is NOT used in subsequent rollups to higher levels only the standard cost is.
b) In Kit Default Setup , user can exclude scrap and setup scrap in Kitting, MRP, and Cost Rollup, this will overwrite what user check in the BOM. Therefore, if user checks "Setup Scrap" checkbox in BOM, but checks to exclude in cost roll, the costroll will not calculate setup scrap cost, but BOM will always calculate setup scrap cost if the Setup Scrap checkbox in check in BOM.
|
1.6. When using the Excel printing option for a Bill of Material, why is there multiple columns used for the reference designators? | Question: When using the Excel printing option for a Bill of Material, why is there multiple columns used for the reference designators?
Answer: When there is a large number of reference designators loaded on the BOM for a particular item and the BOM is exported from the system to an excel spreadsheet the Reference Designators will be split into separate columns. We could attempt to make some changes to the excel spreadsheet and place all Ref Designators in one column but then you would be unable to read the contents. We are aware of the capability to create a larger length cell using excel 2003, but the engine that produces the excel sheets from Visual FoxPro is an older version and this is where the limitations are coming from.
Resolution: At this point in time the Excel output will have to remain as is.
|
1.7. Why doesn’t MRP use Alternate Parts in its Calculations? |
|
1.8. Why am I unable to Change Customer Name on BOM? | Q. Why am I unable to Change the Customer Name on a BOM?
Possiblity #1
The system will not allow to reassign customer for the assembly, which has subassembly with the customer attached to it. It is true that the subassembly does not have any CONSGN parts, but it is also true that this subassembly is attached to a customer. And unless you detach the customer from that subassembly first, you will not be able to change the customer for the top level.
Possibility #2
Unable to actually change the name of the sub-level BOM. Run the Bill of Material , outdented report and you will see all of the top assemblies which are using this part as a component. Once you find all of those records and updated accordingly you should then also be able to edit the desired bom record customer name to match.
|
1.9. Why is MRP giving me Demands for an Inactive BOM? | Q. Why is MRP giving me Demands for an Inactive BOM?
A. Changing the BOM status to Inactive will NOT remove the MRP demands you MUST Inactivate the part number in ICM to remove the MRP demands.
Resolution. Add a warning when user trys to create a SO and/or WO for a Make part if the BOM status is something other than "ACTIVE". Also, modify the BOM module so that the quote module will automatically change the BOM status to "Quote" when a quote for the BOM is initiated, and change it back to ‘Active’ when quote is approved.
|
1.10. Why isn't the Customer Part Number Displayed on the BOM Main Screen? | Q. Why isn't the Customer Part Number Displayed on the BOM Main Screen if the part source is "BUY"?
A. The customer part number is only shown on the BOM Main Screen when it is a "CONSG" part, unless user has checked the box to "Display Customer # for the "BUY" parts if BOM linked with a customer" located on the find screen, (however this may slow down the results). This is why the customer part number for a "BUY" part is only shown on the Detail screen and not the BOM Main screen for a "BUY" part.
|
1.11. Why are the XLS output truncating or exporting corrupted information? | Issue: When exporting the Bill of Material reports to XLS output some of the items are truncating or corrupting the information that is exported out of the system.
Answer or Possible Solution: Check the description loaded for that item and make sure that it does not start with a quotation mark. During exporting of the files to XLS the excel does not like the quotation mark and may cause truncating or corrupting results. Please make sure that there are no quotation mark as the first character of the description, and that should resolve the issue.
|
1.12. When the "Bill of Material with Ref Desg & AVL" report is exported to XLS format why does it show ALL AVL's? | Q. When the "Bill of Material with Ref Desg & AVL" report is exported to XLS format why does it show ALL AVL's?
A. When the "Bill of Material with Ref Desg & AVL" report is exported to XLS format the system dumps all raw data and it can not be a controlled form. When the "Bill of Material with Ref Desg & AVL" report is printed to screen or paper, the requirements of this particular report is that it needs to see parts even if all Mfgrs on the list are not approved, then in the report form the form manipulates the data dump to show only the approved MPNs and filters out non-approved MPN's.
Resolution: The raw data does however have a column named "Uniqanti" if the "Uniqanti" has a "NULL" value the MPN is approved. ManEx suggests that you create an XL template which would have a macro that will remove MPN information if "Uniqanti" is NOT "NULL". Then you can simply copy our XL output into this template and it will show the correct data.
|
1.13. SYSTEM LOCK ERROR - What to do when if System Lock appears when Attempting to Edit a BOM? |
What to do if system locks up while attempting to edit a Bill of Material, and the following messages appear:
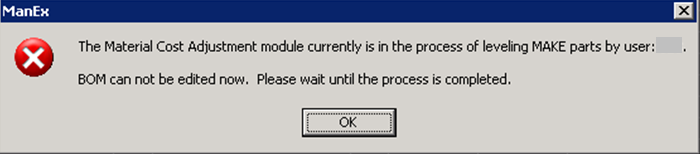
Or if user attempts to launch a new Leveling process within the Standard Cost Adjustment module and the following message appears:
.
A resetcostrolllock.exe has been made available within this article. Running this program from the Manex Directory will remove the Standard Cost Adjustment Lock placed on your tables.
Reason: The lock will occur either by the user saving a record lost connection to the network (or computer crashed) Normally the lock is only on for a small amount of time to allow the first user to finish saving the record and then the next user usually then can proceed. If Users becomes impatient during the leveling process and Clt+Alt+Delete out of the system, this too would place the permanent lock on the records and would then require you to run the resetcostrolllock.exe file.
|
|