There are two methods of returning an over issue:
Method 1:
For the situation where the user has created a line shortage, before the Work Order has been completed (reached the Finished Goods Inventory Work Center in Production), the user has the option of returning the unused components which were over-issued to the Work Order back into Inventory.
Using the Finding a Kitting & Shortage procedure, find the Work Order with the over-issue (remembering to select ALL). You will note that the shortage column contains a negative amount, as shown in the screen below:
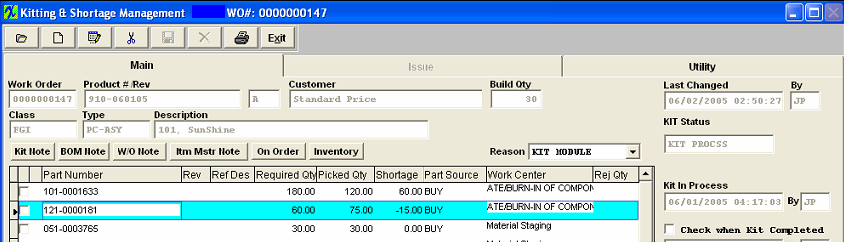
-
Depress the Edit action button. The following selection will appear:
- Select the Issue Parts option.
- Enter password.
|
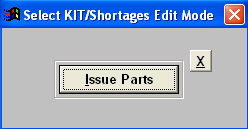 |
- Highlight the Part Number with the negative shortage.
- Move the cursor into the Pick Quantity field.
- Type in the corrected amount of picked quantity that was actually used in the assembly.
- Depress the Enter key. The actual over-issue will display. As shown in screen displayed.
Depress the Save action button. The difference between the original over-issue and the actual overissue will be returned to inventory. The inventory records will update and the appropriate accounting entry removing the part from WIP will also be made. (If the parts in WO-WIP have been allocated to another work order/project user will not be able to return the over-issue qty using this method).
Method 2:
This method covers the situation where the user has a reel of 750 parts and he/she doesn't want to count out 500 for the Work Order. All of the 750 is issued by clicking on the quantity in the lower right hand screen of the Issue tab and changing the amount to 750. (Please refer to procedures above regarding the Issue tab.) Then the system will over-issue 250 parts to the Work Order.
Once the assembly has been completed and reaches the Work Center for Finished Goods Inventory, these un-used over-issued parts can now be issued to the next Work Order, or returned to stock, as follows:
Using the Finding a Kitting & Shortage procedure, find the Work Order with the over-issue (remembering to select ALL).
- Open the Utility tab.
- Depress the Close Kit button, the following screen will appear.
3. If then you want the un-used overissue returned to stock, depress the OK button. Notice that the over issue has disappeared from the Main tab, as shown in the screen below: (If the user does not want the un-used over-issues returned to Raw Materials Inventory, he/she edits the Quantity Transfer Amount at the bottom right hand side of the screen. The user may transfer 0 quantity or any amount up to the amount of the over-issue).
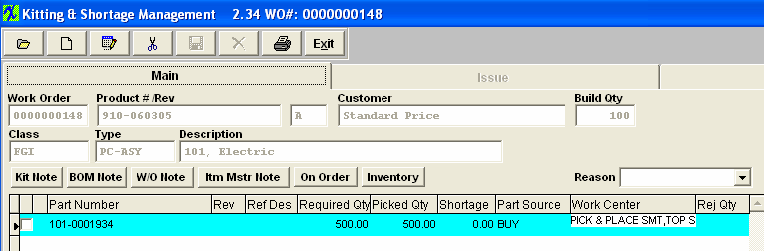
Once the above steps are completed, the "Qty Transfer" parts are returned to their warehouse location, WIP is relieved, the Quantity on Hand in Raw Materials Inventory is increased in the Inventory Item Master and the appropriate accounting entries are generated.
Lot Coded Parts - If parts have been issued from different Lot Codes with over-issued qty, those over-issued parts are moved to "WO-WIP" location, and the system saves what lots they come from, when the Kit is closed, the system locates all the WO-WIP locations and lot information, and returns it back to the original lot, if the lot is deleted (due to the lot qty is 0), is will re-create it.
Allocated Parts - If a part in WO-WIP is allocated to other work orders/projects, and user chooses to return back to stock, the program will unallocate from the work orders WO-WIP, return to the original location and then re-allocate to the original locatiion, if user chooses to issue to work order the program will remove the allocation and cost it to the work order.
|