1.1. Prerequisties for Physical Inventory | Before entering transactions, the following must be setup in Manex.
After activation, "Physical Inventory" access for each user must be setup in the ManEx System Security module. Users with “Supervisor Rights” will automatically have access.
|
1.2. Introduction for Physical Inventory |
The Physical Inventory module is to manage the physical inventory count. The user has the choice of using count tags or a count worksheet. The inventory is physically counted and then input into the system. More than one user may input into the system at a time. Note: The users must exit and re-enter the screen to refresh if an action was done on another work station. Only one user may post. IMPORTANT NOTE: DO NOT MOVE ANY MATERIAL WHILE THE COUNT IS TAKING PLACE. Once the count is input into the system, the system provides for a reconciliation between the Inventory Master and the physical count. If the count is different than the record, the user is prompted whether to accept the difference or to recount and re-enter. If the count equals the Inventory Master, there is no adjustment required and the number counted will drop off of the reconciliation list. Once the reconciliation is completed, the user may print out a reconciliation report. Then, after reviewing, the user may update the quantity on hand in the Inventory Master. Note: This takes a high level password or special rights as assigned in Security. Once this is done, the accounting journal entries will update automatically, if the MANEX accounting module is used. |
1.3. Fields & Definitions for Physical Inventory |
1.3.1. The Setup Tab | 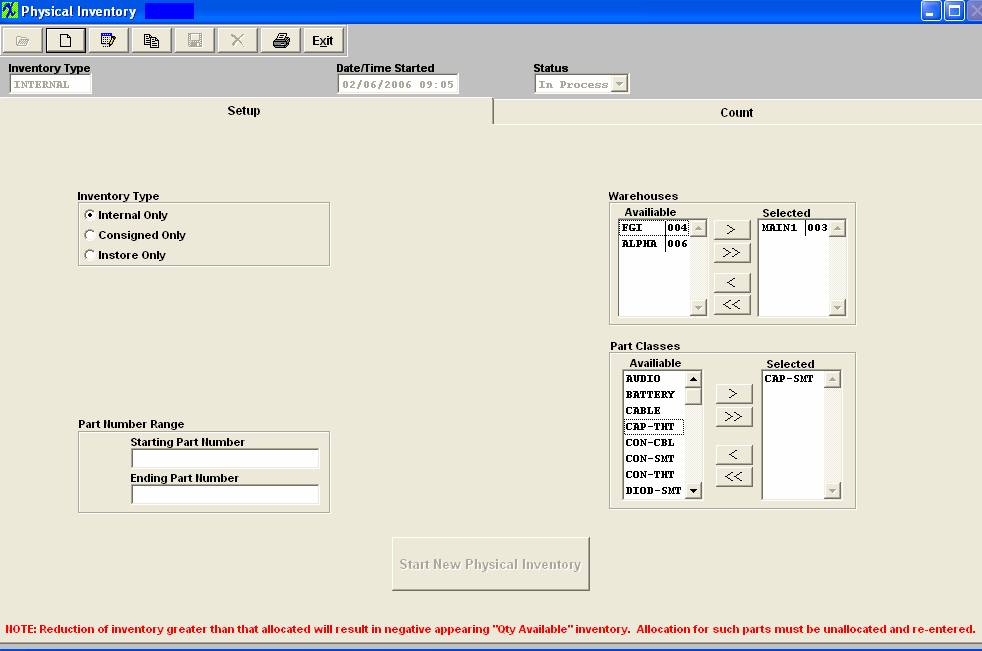
Setup tab field definitions
Inventory Type |
The type of Inventory, either Internal, Consigned or Instores. |
Customer |
If the Inventory Type is Consigned, the Customer name will display in this field. |
|
Supplier |
If the Inventory Type is Instore, the Supplier name will display in this field |
 |
Date/Time Started |
The date and time (24 hour clock) when the Inventory was originally started. |
Status |
The status of the physical inventory, either In Process, Completed or Cancelled. |
Inventory Type |
The radial selected will display either Internal, Consigned or Instores only. |
Part Number Range |
The range or internal part numbers selected for counting. |
Warehouses
Available |
The name of any available warehouses selected for counting. |
Selected |
The name of the warehouses that were actually selected for counting. |
Part Classes
Available |
The part classifications which were available for counting. |
Selected |
The part classifications that were actually selected for counting. |
|
Depressing this button will start a new Physical Inventory. |
|
1.3.2. The Count Tab | Depressing on the Count Tab brings up the following screen:
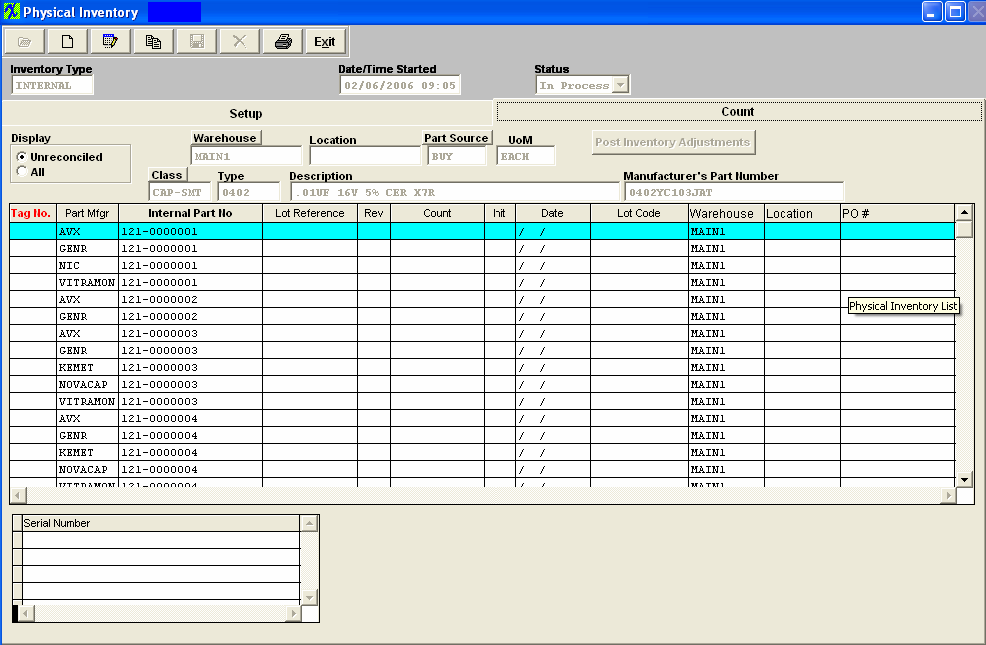
Count Screen Fields
Inventory Type |
The type of Inventory, either Internal, Consigned or Instores.
|
Supplier/Customer |
If the Inventory Type is Instore, the Supplier name will display in this field.If the Inventory Type is Consigned, the Customer name will display in this field.
|
Date/Time Started |
The date and time (24 hour clock) when the Inventory was originally started.
|
Status |
The status of the physical inventory, either In Process, Completed or Cancelled.
|
For the part number highlighted:
Warehouse |
The warehouse location for the part to be counted.
|
Location |
The warehouse location for the part to be counted.
|
Part Source |
The Make/Buy/Consigned/In Store type for the part to be counted.
|
UOM |
The Unit of Measure to be counted. Same as stocking unit. |
Class |
The classification of the part.
|
Type |
The type within the classification to which the part belongs.
|
Description |
The description of the part.
|
Manufacturer’s Part No |
The number used by the manufacturer to identify the part.
|
Tag No. |
If you have already printed Physical Inventory Tags, the Tag Number will appear in the Tag Number column. (Unless you numbered them manually, as described above.)I f you have not printed tags, the Tag Number column will be blank. |
Part Mfgr |
The Manufacturer for the part to be counted. |
Part Number |
The Internal Part Number that has been assigned to the item to be counted.
|
Lot Reference |
If the part type has been designated as requiring lot tracking, then the lot tracking reference number appears.
|
Rev |
The part number revision for the item. An item may exist under multiple revisions.
|
Count |
The physical count quantity of the item observed during Physical Inventorying. |
Init |
The initials of the individual who performed the Physical Inventory.
|
Date |
The date that the inventory was counted.The date will default to the current date, but may be over-written.
|
 |
This button is used to post the Inventory Adjustments.This is used after the inventory has been reconciled and the Physical Inventory Detail Report has been printed and reviewed. This button will update the Inventory Master for the quantity on hand. Note: this action requires a supervisor’s password or specific "Post Inventory Adjustments" authorization in the Security module. |
|
1.4. How To ..... for Physical Inventory |
1.4.1. Setup a Physical Inventory |
Enter Inventory Mgt/Inventory Control Management/Physical Inventory Module |
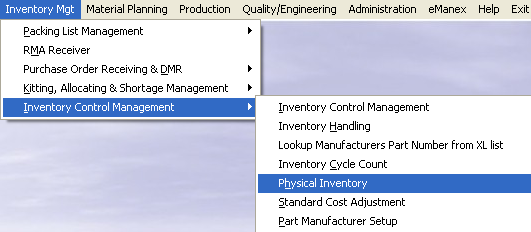 |
The following screen will appear:
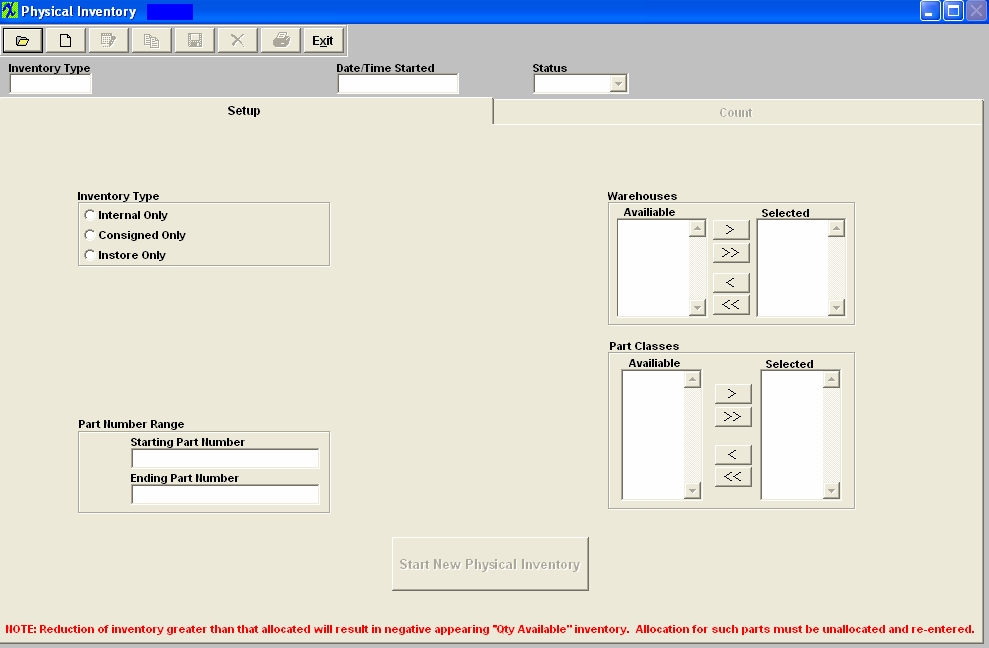
Depress the Add record action button. Type in your password. The following warning will appear:

Depress Ok and the following options screen will appear:
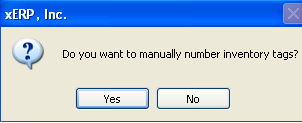
Selecting “Yes” will allow the user to manually number the inventory tags, item by item.
Selecting “No” causes the system to automatically number the tags.
Please refer to the Tags and Work Sheets instructions.
The following screen will appear:
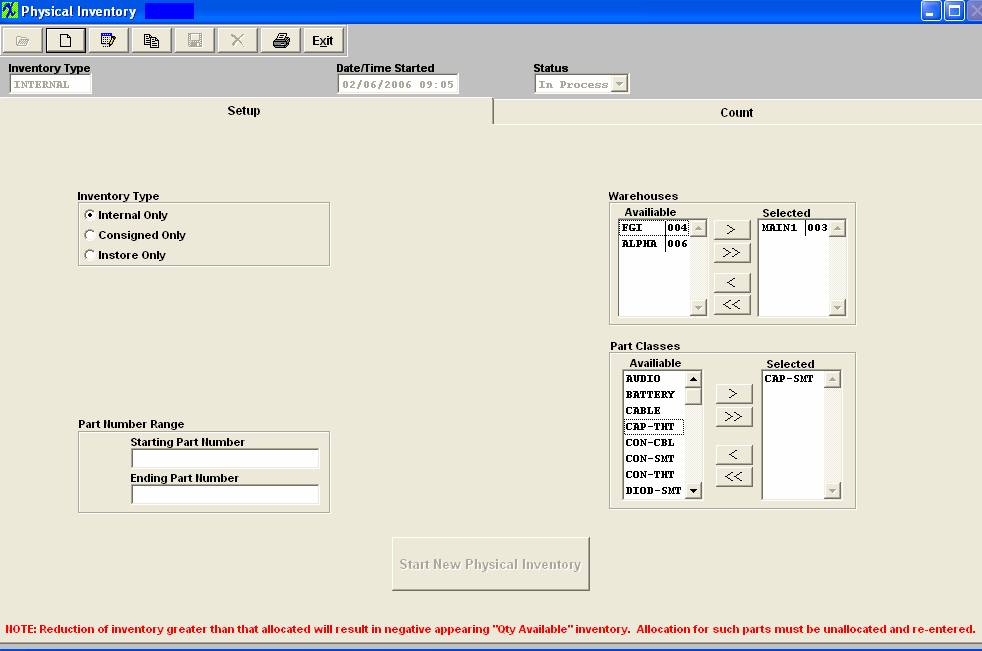
Select the Inventory type by clicking on the appropriate radial. Select from Internal, Consigned or In StoresInventory. Internal inventory represents user-owned inventory. Consigned inventory is owned by the user’s Customer. In Stores inventory is owned by the Supplier.
In-Store purchasing overview: In-Store is the situation where the Supplier has placed raw materials in the user’s warehouse. The raw materials still are owned by the Supplier. When the user is ready to use the Supplier’s raw materials, he/she issues an In-Store Purchase Order. For In-Store POs, the user may select by Supplier or by Part Number. Then the user may find records according to the selection. Once found, the user may create a PO for the In-Store Consumption. In-Store Purchasing also includes receiving.
If you select the Inventory Type to be Consigned, a list of customers will appear:
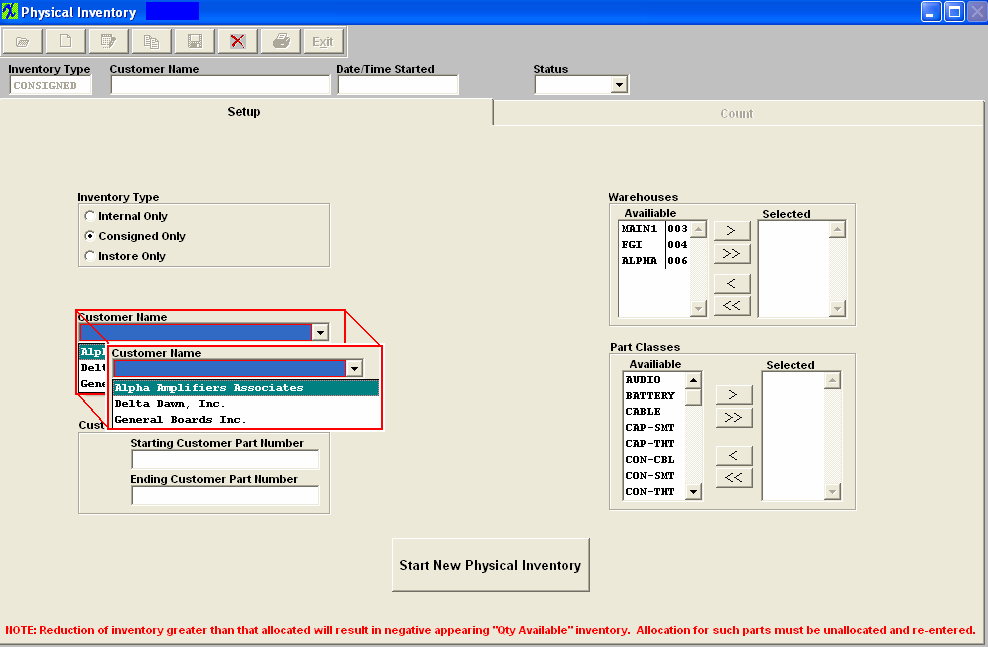
Select the Customer.
If you select In stores Inventory, a list of Suppliers will appear:
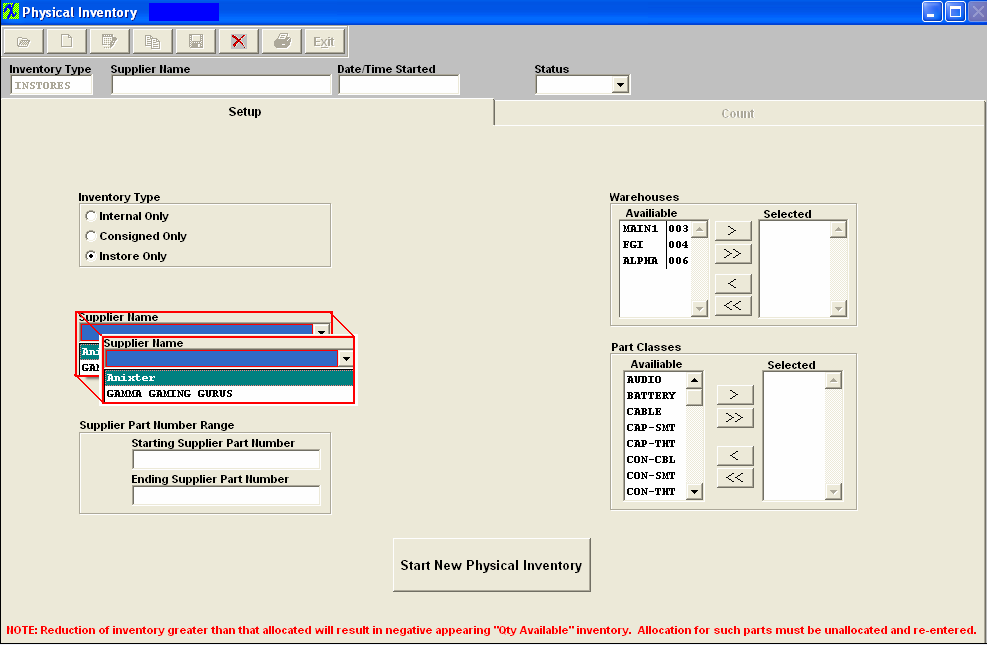
Select the supplier.
Select the warehouses to be counted by highlighting a warehouse and depressing the > button. If you want to count all warehouses, depress the >> button.
To select part number range, enter the starting part number and the ending part number.
To select the part classes, highlight the class desired and depress the > button. For all of the part classes, depress the >> button.
A view of the screen would be as follows:
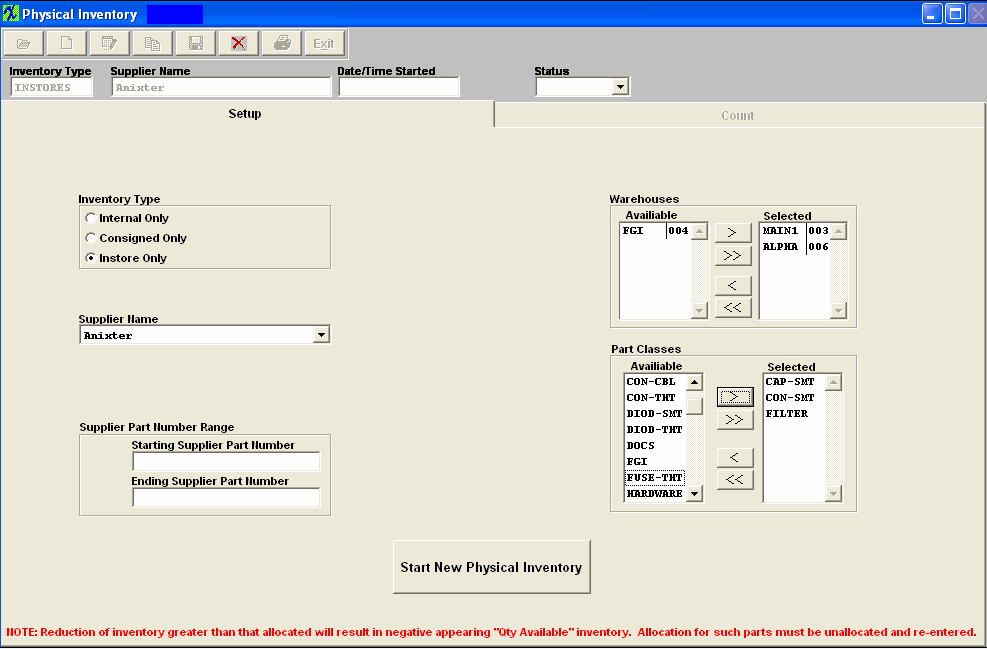
Depress the button to Start New Physical Inventory. A message will appear on the screen:

Depress the OK button. Information is transfered to the Count Tab.
Important Caution: The user must finish the Physical Inventory completely before the system is enhanced. |
1.4.2. Finding a Physical Inventory |
Enter Inventory Mgt/Inventory Control Management/Physical Inventory Module |
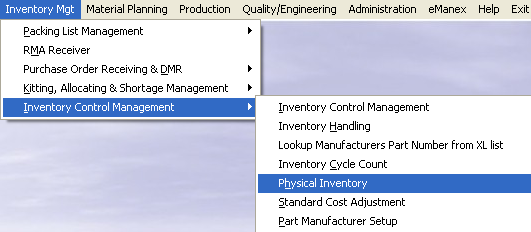 |
The following screen will appear:
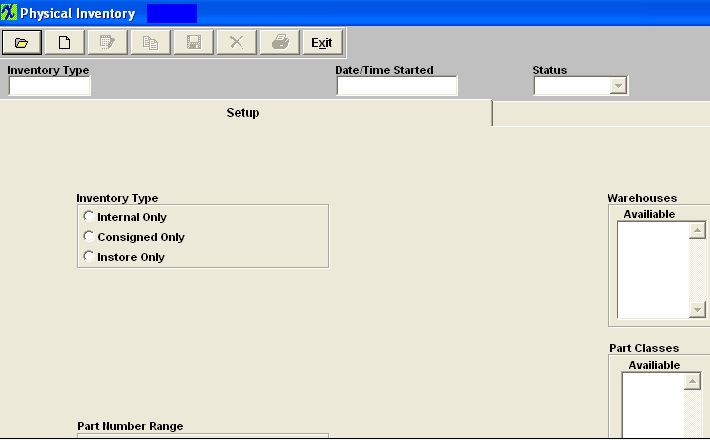
Depress the Find action button. The following screen will appear:
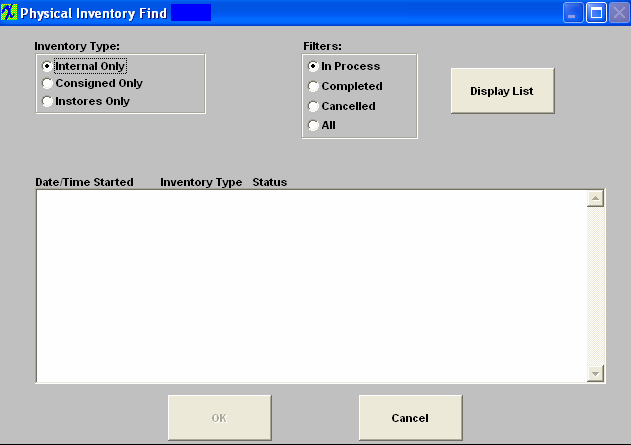
Decide upon the Inventory Type that you want to find. Select from Internal Only, Consigned Only or Instores Only by clicking on the appropriate radial.
Then choose the appropriate filter, either In Process, Completed, Cancelled or All by clicking on the appropriate radial. Depress the Display List button once the selections are made. The information at the bottom of the screen will display Date/Time Started, Inventory Type and Status.
If you select Consigned, you’ll be prompted for the Customer name. If you select Instores, you will be prompted for the Supplier name.
Once you’ve found the Inventory you’re seeking, the information will populate the Count tab screen, as follows:
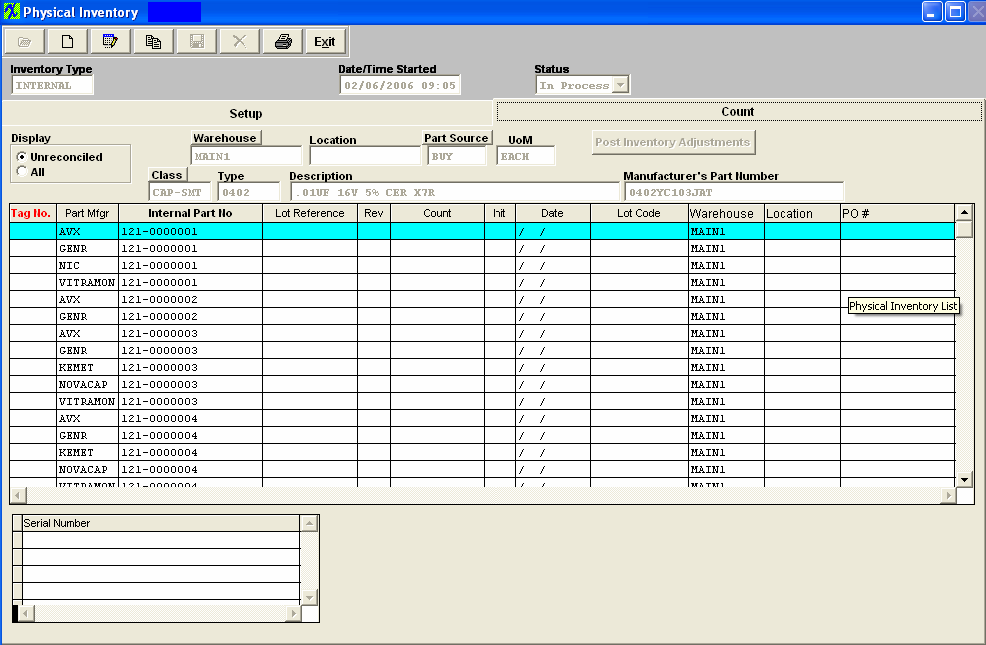
|
1.4.3. Record a Physical Count | Find an In-Process Physical Inventory. The following information will appear in the Count tab screen.
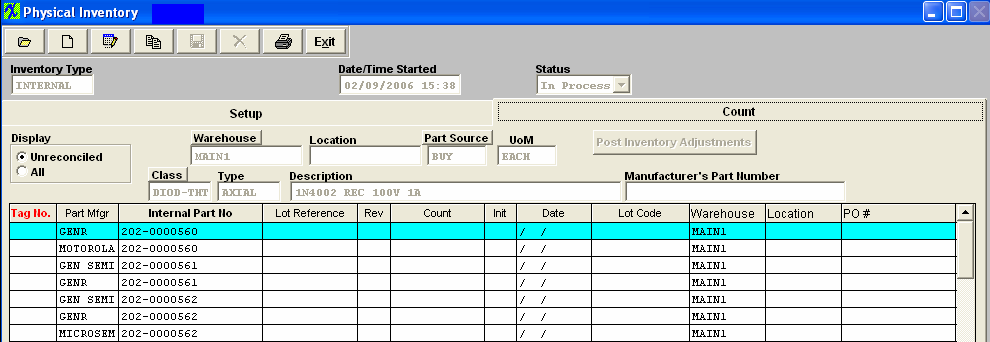
Depress the Edit action button. Type in your password.
To sort by warehouse, depress the Warehouse button. To sort by Class, depress the Class button. To sort by part source, depress the Part Source button. You will also be able to sort by tag number or part number by depressing on the heading.
Enter the final count from the tag or the worksheet. The system will capture the initials from your password. The system will enter the date.
All warehouses and location will be listed for the internal part pulled forward for a count, with the exception of quantities that are in WO-WIP, these quantities are not included in the Physical Inventory. At this time user may move parts from one warehouse/location to another if needed by entering the count that resides in that location/warehouse. User are not allowed to add new items to the PI inventory listing, due to the fact that the count could phycially already be in process. If we allow you to keep adding and deleteing records from the count it might cause issues for what is already in process.
Also, ManEx does not allow user to edit a lot code for inventory items once they have been accepted into the system. ManEx does not allow you to change the Lot Code information anywhere within the system once received. Once in the system we have to maintain that lot code with those records through out the system, to have good Lot Control.
Depress the Save action button.
The screen would appear as follows:
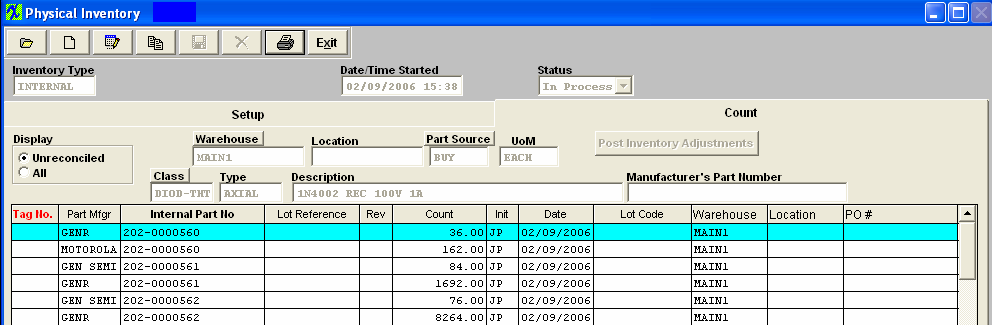
|
1.4.4. Reconcile the Physical Count | When the recording is complete, depress the Reconcile button (as highlighted below). Enter your password. This will reconcile the inventory.

If the inventory count does not match the system on hand quantity, the following screen will appear:
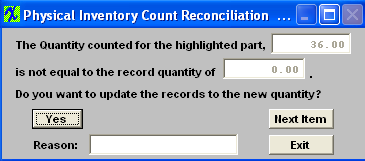
If you want to update the records for the counted quantity, depress the Yes button. Type in the reason in the Reason box.
If you want to skip over the record, depress the Next Item button. Note, however, that you can’t update the quantity on hand until all of the inventory items are reconciled.
Once all of the counts are reconciled, the detail will disappear from the screen.
|
1.4.5. Update the Inventory Master for Inventory on Hand | Once you’ve reconciled the inventory and printed and reviewed the Physical Inventory Detail Report, you may update the Inventory Master for the Inventory on hand.
Depress the Count tab. Depress the Post Inventory Adjustments button. Note: this action requires a supervisor’s password or specific "Post Inventory Adjustments" authorization in the Security module.
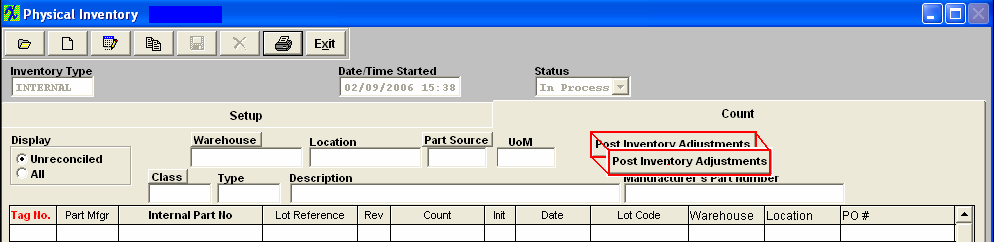
All of the reconciled count numbers will update the quantity on hand in the Inventory Master. The status will change to Posted. The following message will appear:
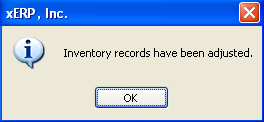
Additionally, the requisite GL Transaction for any variances will forward into the accounting module.
Note that GL Transactions will not be created in the following circumstances: Consigned stock or In Store additions. |
1.5. Reports - Physical Inventory |
To obtain the Inventory reports, select the Print button from the ManEx action buttons at the top of the screen.

The following screen will appear:
Select the appropriate radio for the output format you desire: Screen, Printer, XL File, TXT File, or PDF.
Highlight the desired report and then depress the Option tab if applicable.
NOTE: Users MUST have special rights within the Security module to "Enable Printing On-Hand Quantities on the PI Reports"
|
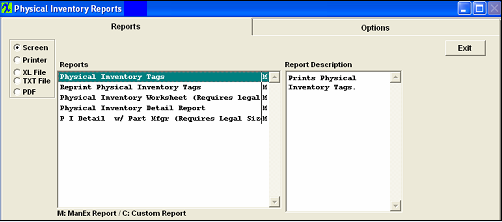 |
TAGS:
If you selected Manual Inventory Tags from this screen:
|
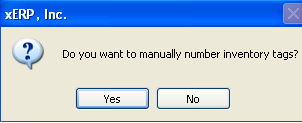 |
Depress the Count tab. The following screen will appear:
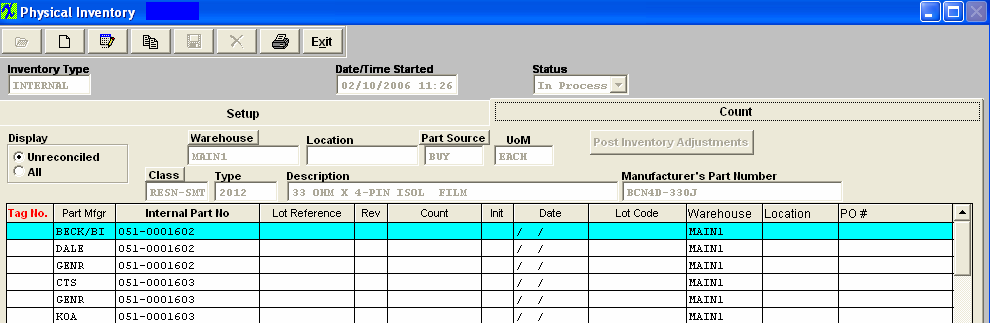
Depress the Edit button. Type in your password. Manually type in the Tag No. for each item. The system will automatically re-order the tags in numerical order.
Physical Inventory Tags
When you have finished, depress the Print button. The following screen will appear:
|
|
Select Physical Inventory Tags. Depress the Options tab. The following screen will appear:
Choose between All Locations and Only Locations with Quantities > 0.Choose the sort options, either Warehouse + Location + Part Number + Rev + Lot Code or Part No + Rev + Lot Code.
Depress the OK button. An Inventory Tag will be printed for each mfgr per item.
The tags will print 3 each on 8 ½ X 11 paper. If the Inventory type is consigned, the Customer’s part number will print.
If you did not select manual inventory tag numbering:
A box will appear on the screen to Enter Starting Tag No:
|
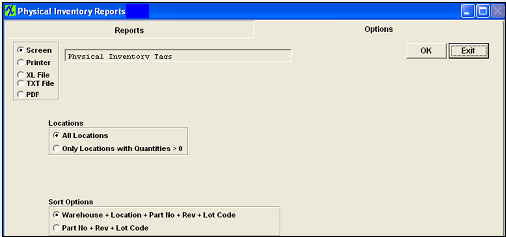 |
The Printed tags will appear as follows:
Below we have attached blank Inventory Tags <<blank IT.doc>> and <<blank IT.pdf>> that may be used if for some reason NO tags were printed for parts that may have inventory but are NOT being displayed in the Physical Inventory listing, etc. NOTE: These are only intended to be used if user happens to find product that was not on the physical Inventory list for some reason.
Reprint Physical Inventory Tags
Select the Reprint Physical Inventory Tags, depress the Options tab and the following screen will appear:
Enter Tag Number Range to Print.
Depress the OK button
The tags will print 3 each on 8 ½ X 11 paper. If the Inventory type is consigned, the Customer’s part number will print.
|
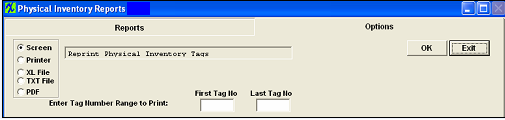 |
Physical Inventory Worksheet
Select the Physical Inventory Worksheet, and depress the Options tab. Note that this report requires Legal size paper. Selecting this report will bring up the following screen:
Click on the appropriate radial selection criteria. Choose one of the following: All Records, Internal (excluding In stores), In Stores or Consigned. If the Inventory type is consigned, the Customer’s part number will print.
Click on the appropriate radial for Locations selection. Choose between All Locations or only Locations with Quantities greater than zero.
Click on the desired radial to select whether to print On Hand quantity. Select between Not printing or printing the on hand quantities.
Click on the appropriate radial for Sort Options.Choose between (Warehouse, Location, Part Number, Revision number and Lot Code), (Part Number, Revision Number and Lot Code) or by (Tag Number).
|
|
The report will appear as follows: 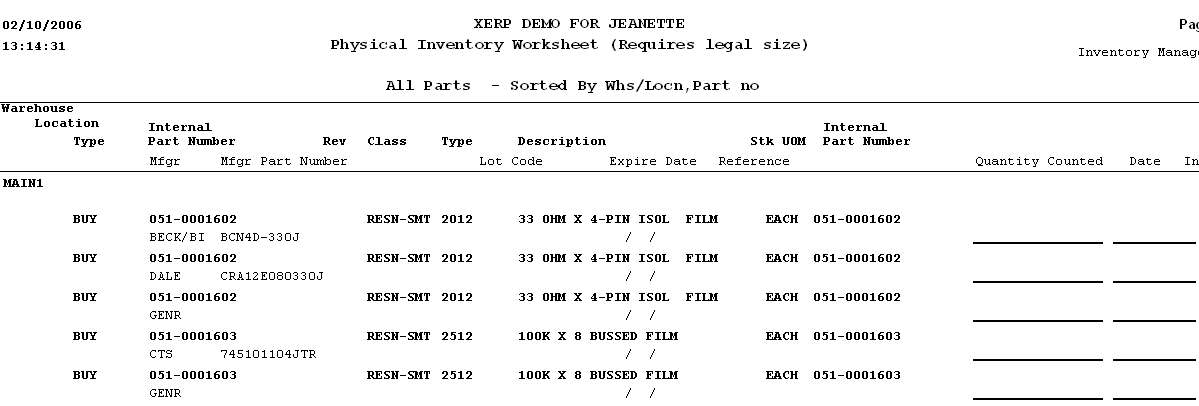
Physical Inventory Detail Report
Select Physical Inventory Detail Report, depress the Option tab, and the following screen will appear:
Click on the appropriate radial selection criteria. Choose one of the following: All Records, Internal (excluding In stores), In Stores or Consigned. If the Inventory type is consigned, the Customer’s part number will print.
Click on the appropriate radial for Locations selection. Choose between All Locations or only Locations with Quantities greater than zero.
Click on the appropriate radial for Sort Options.Choose between (Warehouse, Location, Part Number, Revision number and Lot Code), (Part Number, Revision Number and Lot Code) or by (Tag Number).
Depress the OK button
Note that this report is designed to be printed after the count has taken place and been reconciled.
|
|
The report will appear as follows:
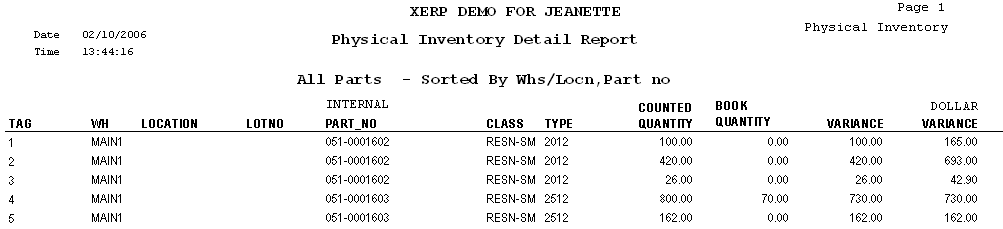
PI Detail w/Part Mfgr Report
Select the PI Detail w/Part Mfgr Report, and depress the Options tab. Note that this report requires Legal size paper. Selecting this report will bring up the following screen:
Click on the appropriate radial selection criteria. Choose one of the following: All Records, Internal (excluding In stores), In Stores or Consigned. If the Inventory type is consigned, the Customer’s part number will print.
Click on the appropriate radial for Locations selection. Choose between All Locations or only Locations with Quantities greater than zero.
Click on the appropriate radial for Sort Options.Choose between (Warehouse, Location, Part Number, Revision number and Lot Code), (Part Number, Revision Number and Lot Code) or by (Tag Number).
Depress the OK button
Note that this report is designed to be printed after the count has taken place and been reconciled.
|
|
The report will appear as follows:
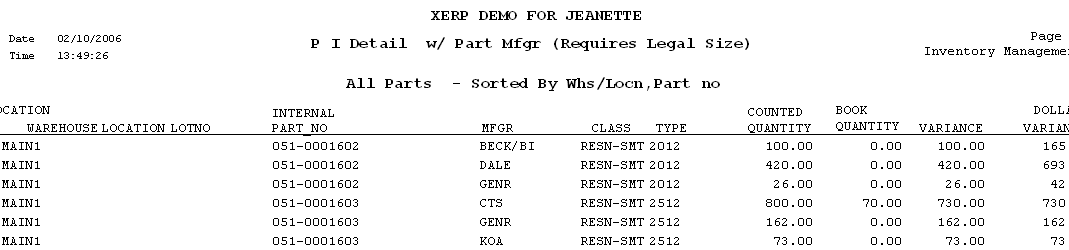
|
|