MRP Actions: displays the results of a find and allows further item sorting and selection
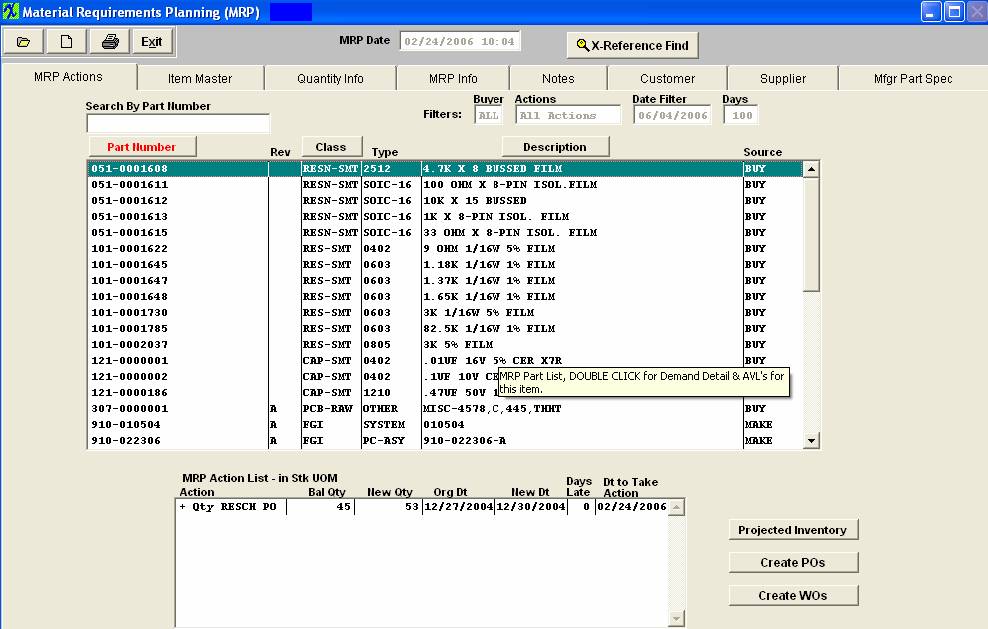
Definition of Material Requirements Planning Action Fields:
MRP Date |
This is the date and time for the last material Requirements Planning run. |
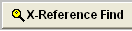 |
See Article #4765 for further detail on how to Use the X-Reference Find |
 |
The "Last MRP Run" button located in RED at the top of the screen will be displayed in a larger font if MRP run failed due to an AVL issue and there will be brief comment explaining what issues the MRP run encountered. This will allow any user that might not have seen the xls spreadsheet to be aware of what had taken place on the last attempt to run MRP. For further detail see Article #729. |
Sorting, Searching and Selecting in the MRP Action Screen
The user may sort by the Part Number, Class or Description by depressing the appropriate button.
To sort the contents of the Summary screen by Part Number, Part Class or Description, click the button. It will turn red and the list will automatically sort in ascending alphanumeric sequence per the selection.
To search for an item by Part Class, click Class and enter the first few characters of the Part Class in the Search by Part Class field. The list will scroll down to the first incidence of each character in the sequence entered.If a character is not found in the position typed, the list will scroll to the bottom.
To Search for an item by Description starting with the 1st character on the left, click Description and begin entering the first characters in the field. The list will scroll down to the first incidence of each character in the sequence entered.If a character is not found in the position typed, the list will scroll to the bottom.
To Search for an item by a word or character string anywhere in the Description, click on Description, click on the Left button next to the Search by Description window (changes to Random).
Enter the search word or characters in the window. Hit return and the first match in the list will be highlighted. Click on the window and hit return to highlight the next match in the summary list. After the last match or if a match is not found, the last item in the summary list will be highlighted.
To visually search the summary list, use the scroll bar or arrows to the right of the list.The Source (Buy, Make or Phantom) and total On Hand quantity is displayed in the last two columns.
For further Details on any item in the Actions main body list, highlight the item by a search or mouse click and select the appropriate Tab to display the desired detail information. To display changes made in other windows or by other users while this window is open, repeat the Material Requirements Find and refresh the screen data.
FILTERS:
Buyer |
The valid buyer code, or ALL buyers. |
Actions |
The Material Requirements Planning action displayed, or ALL Actions.
|
Date Filter |
The horizon date for the Material Requirement Planning actions.Parts with actions beyond this date are excluded from the report.
|
Days |
A short-cut to the horizon date. Entering the number of days (from the current date), changed the Date Filter accordingly.
|
Main Body
Part Number |
The item/part number is a unique identifier for every Item Master record entered into the database.
|
Revision |
The part Number revision for the item.
|
Part Class |
This is a general part, product or item classification.
|
Part Type |
Type is a sub-classification of Part Class.
|
Description |
This is the field of descriptive data about the item. |
Part Source |
This field is hard coded in the system.BUY is for purchased parts and assemblies, MAKE for an item made in-house (assemblies and sub-assemblies) and PHANTOM for a number used to define a collection of items that does not exist as a separate assembly built on a Work Order (ship kits, upgrade packages, spares kits, etc.).
|
Material Requirements Planning Action List in Stock Units Of Measure:
The information listed in this section pertains to the highlighted part number in the main body above. To see the list for another part number, highlight the part number in the main body.
Note: Dates are calculated with the Production Calendar
Action |
Defines the Material Requirements Planning action to be taken for the highlighted part. There are several different actions that will appear depending on the part. For example if the Part is a Make/Phantom part and the action originates from a higher level assembly for the Phantom, MRP will display "PHANTOM" in this section and that will indicate to the user that there are no actions required but is listed so users can investigate where component actions are originating from. If the Make/Phantom is required directly for an order itself, it will now follow the same WO action rules as a regular Make Product would.
|
Balance Quantity |
The projected balance of inventory for the part selected. MRP will display the stock qty UOM.
|
New Quantity |
Displays the new quantity that the action requires. MRP will instruct you to Purchase the Stock qty UOM, not the Purchase UOM. The PO Module will display the UOM conversion (if applicable).
NOTE: When creating a PO for an item with different purchasing and stocking UoMs, be sure to enter the MRP suggestion into the Stocking qty field rather than the purchasing qty field. The system will automatically convert the stocking unit into the purchasing unit for the purchase order qty.
For Example: if the item has inches for Stock UoM and Feet for Purchasing UoM, and the MRP demand is 24 , the buyer would enter the qty of 24 into the stocking qty field and the PO would automatically convert it to 2 feet in the purchasing qty field. So the supplier deals in feet, but ManEx deals in inches. The conversion between the two are established in the Unit of Measure & Conversion module.
|
Original Date |
Displays the original (current) date of the existing action.
|
New Date |
Displays the new date that the action requires. For a buy part the New Date is arrived by subtracting the Kitting and Production Lead times setup for the Make part from the Sales Order Ship Date. For a Make part the New Date is the Sales Order Ship date. See Article #3064 for futher detail on how the Lead Times for a Level BOM are calculated. |
Days Late |
If the action date is earlier than the current date, the number of days late for the action is shown.
|
Date to Take Action |
This is the date by which the action listed must take place. Changing the leadtime of a Buy part will NOT change the due date, only the date to take action. For a Buy part this date is arrived by subtracting the Purchase Lead time from the New Date. For a Make part this date is arrived by subtracting the Kitting and Production Lead times from the New Date which is the Sales Order ship date.
|
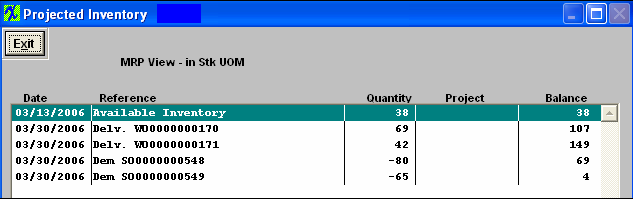
Definition of fields in the Projected Inventory screen:
Date |
The projected date of a Materials Requirements Planning action.
|
Reference |
The Material Requirements Action.
|
Quantity |
The quantity of parts involved in the Material Requirements Planning action. |
Project |
The project number assigned to the PO. |
Balance |
The projected balance of inventory for the part selected.
|
After depressing the Projected inventory button, the reference field was highlighted in the Projected Inventory Material Requirements Planning View in Stock Unit Of Measure and double clicked. The Material Requirements Planning Detail appears.
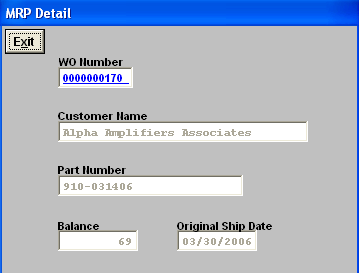
Material Requirements Planning Field Definitions:
Work Order Number |
This is the Work Order Number in the system. |
Customer Name |
The name of the Customer for which the assembly will be made. |
Part Number |
This is the assembly part number where the component part number is highlighted.
|
Balance |
This is the balance for the Work Order Listed.
|
Original Ship Date |
This is the original scheduled ship date of the assembly. |
After highlighting a part number in the main body, the Material Requirements Planning Demands and Approved Vendors List appeared, as displayed above:
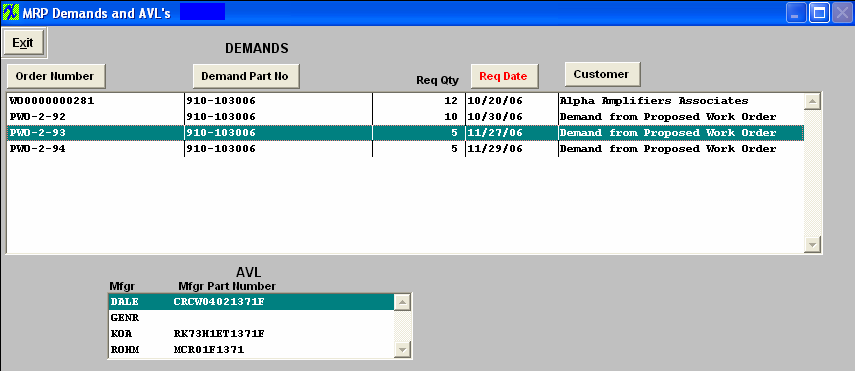
Material Requirements Planning Demands and Approved Vendor List Field Definitions:
Order Number |
This is the Work Order Number the system is proposing.
|
Demand Part No |
This is the Assembly No the demand is for. |
Required Quantity |
For the Work Order proposed, this is the quantity of the component part number which will be required. |
Required Date |
The date when the component part number highlighted is required to be released to the assembly floor. |
Customer |
The name of the Customer for which the assembly will be made, if known. If the customer is not known, an explanation will appear. |
AVL
Mfgr
|
This will list the Mfgr's approved on the BOM
|
Mfgr Part Number
|
This will list the Mfgr PN's approved on the BOM. NOTE: If "GENR" is approved on the BOM MRP will consider any inventory for that part even if the AVL is not approved on the BOM.
|
|