Enter the SQLMANEX.EXE (within the ManEx root directory)
This action will then prompt the user for a password
|
 |
The following screen will be displayed, select Production/Work Order Management/Unreleased Work Order List Module
NOTE: For this module to be available the "Use Work Order Checklist" box must be checked in the Shop Floor Tracking Default Screen in System Setup.
|
 |
The following screen will be displayed:
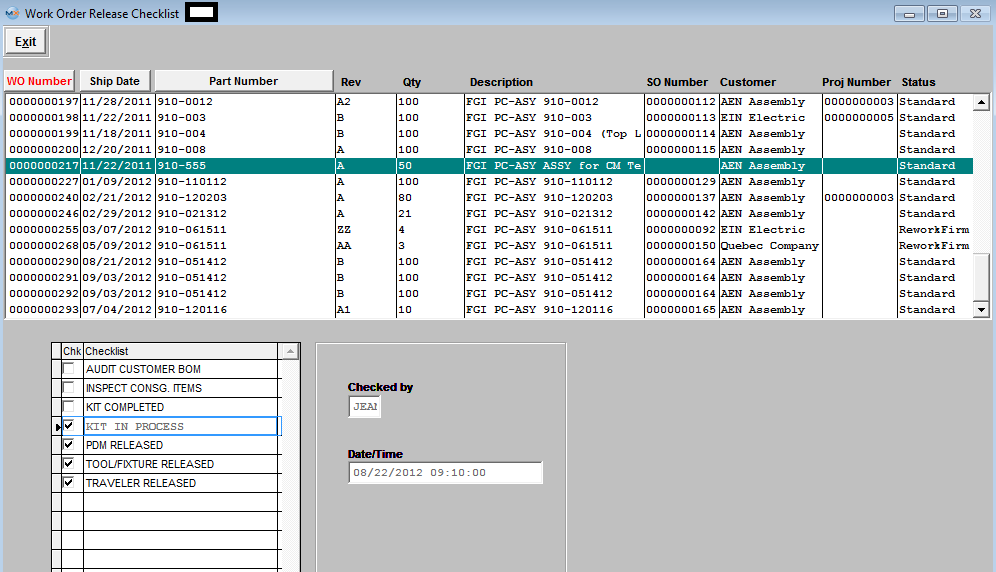
Highlight the line you are interested in viewing. The information at the bottom of the screen will display the check list items associated with the assembly.
KIT IN PROCESS |
This item will be checked, once the "Manual Kit or Auto Kit" button has been selected within the Kitting & Shortage Mgmt module. This checklist item is hard coded into the system. |
KIT COMPLETED |
This item will be checked, when the "Kit Complete" box is checked within the Kitting & Shortage Mgmt module. This checklist item is hard coded into the system |
TOOL/FIXTURE RELEASED |
This item will be checked, when the Tool/Fixture released check box is checked within the PDM module. This checklist item is hard coded into the system |
PDM RELEASED |
This item will be checked, when the PDM released check box is checked within the PDM module. This checklist item is hard coded into the system |
TRAVELER RELEASED |
This item will be checked, when the Traveler Released check box is checked within the Work Order Traveler Setup module. This checklist item is hard coded into the system |
Audit Customer BOM |
This item is defaulted in from the Work Order Check List (within the Work Order Traveler Setup module). This item will need to be approved within the Unreleased Work Order screen. |
Inspect Consg. Items |
This item is defaulted in from the Work Order Check List (within the Work Order Traveler Setup module). This item will need to be approved within the Unreleased Work Order screen |
If the item listed has been performed, there will be a check mark at the left of the item and the user may view the name of the person who performed the checking plus the date and time checked. User will NOT be allowed to process material through SFT until the Work Order Release box within the Work Order module has been checked off ( Note: this box will NOT be checked until ALL checkpoints including the "Kit Complete" have been checked). This is to prevent moving material in SFT until everything has been approved.
NOTE: If a user has the Work Order Checklist feature active and tries to use the PO Receiving shortage and issues feature within the PO Receiving, it will not recognize the shortages until the kit has been flagged as "Kit Complete". It is designed this way because the user will not know if the parts are short until the kit is completed.
You may have parts in the inventory and have not pulled them to the kit yet. If you allow seeing the shortage (which may not be a shortage because parts are not pulled yet) from the PO receiving, the receiver may be trained to automatically issue to the shortages first, but it may not be a shortage because parts have not been pulled from inventory, so how would they know if it is a real shortage or just not pulled from inventory yet.
|