Add (Run) a Material Requirements Planning
MRP runs through a large number of tables and records to compile its calculations, and provides a snapshot of suggested actions at the same time it is ran. If users are changing things during this process it could definitely cause some strange outcome. To prevent this situation we strongly suggest that you use the Nightly MRP trigger. (Refer to Article #416 for more detail on trigger setup).
If you find the need to re-run MRP during the production work day then we suggest that you notify all departments that MRP is going to be ran and ask them to remain out of the system until the MRP run is complete. This will help assure that the most accurate MRP run is possible. Then follow the procedure below:
Enter the SQLMANEX.EXE (within the ManEx root directory)
This action will then prompt the user for a password
|
 |
The following screen will be displayed, select Material Planning/Material Requirements Planning (MRP), Material Requirements Planning (MRP) Module
|
 |
The following Screen will be displayed:
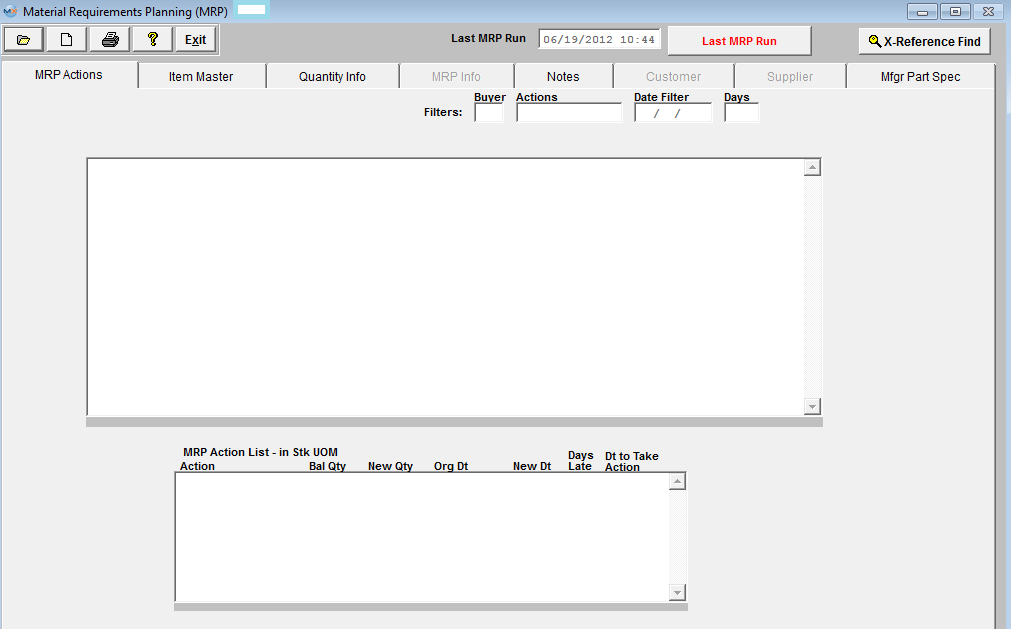
To run a new Material Requirements Planning (MRP) manually, depress the Add action button (Generate MRP), and enter your password.
The run percentage will be displayed on the header as displayed below:

The time it takes MRP to run is dependent on a number of factors. Here is a list of items that affect the processing time:
the number of open Sales orders
the number of open Work orders
the number of open Purchase Orders
the complexity of the BOMs (levels)
the number of AVL's for parts
the number of active parts
Inventory safety stock, minimum orders, order multiples
A company with high annual sales but only a few open orders of all types and only a few simple BOMs will process quickly, a company with low annual sales, but with a large number of small orders, many BOMs and AVL's will take a long time to process.
We are not able to come up with an average time because there are too many conditions that affect the run time.
Once the MRP run is completed and was successful, user will receive the following message:

Depress the OK button. The Material Requirements Planning Date at the top right hand side of the screen will change.

If the MRP run was NOT successful due to AVL issues (missing, or exists but is marked as "Do Not Purchase and/or Kit, etc) the following message wil be displayed on screen indicating that MRP will NOT be able to continue until the BOM and/or part records have been correct. Then in addtion to the message an XLS file will be generated and placed in the ManEx Main Directory. This XLS file will contain the records that the user will need to review and address. If an XLS file is generated multiple times a day the system will add "_N" to the name of the XL file, where "N" is the dequence number. For example if MRP is run today three times without fixing a problem or a new problem is generated, the generated files will have names; badavls_2009.03.31_1.xls, badavls_2009.03.31_2.xls, badavls_2009.03.31_3.xls, unless one or all of the files were removed. The user will have the option of viewing the XL file now or later. NOTE: These XL files will need to be manually removed from the ManEx Main Directory.

If the user selects "No" the user will receive the following message and they may review the XL file placed in the ManEx Main Directory.
If user selects "Yes" an XL file (similar to the one shown below) will be displayed on screen and also placed in the ManEx Main Directory for later review:
The date displayed in the "Last Successful MRP Run" will NOT change. The "Last MRP Run" button located in RED at the top of the screen will be displayed in a larger font if MRP run failed due to an AVL issue and there will be brief comment expaining what issues the MRP run encountered. This will allow any user that might not have seen the xls spreadsheet to be aware of what had taken place on the last attempt to run MRP.
Double click on the "Last MRP Run" button and similar information will be displayed:
NOTE: If MRP runs from Trigger, and MRP run was NOT successful due to AVL issues an XLS file will be generated and placed in the ManEx Main Directory for review and also be attached to the e-mail sent, informing user that the MRP run was NOT COMPLETED (similar to the one shown below). Upon opening the MRP screen the "Last MRP Run" button will be displayed in a larger font and will have information about the file as displayed above.
If MRP runs Successfully from Trigger the e-mail sent will be similar to this:
|