Enter the SQLMANEX.EXE (within the ManEx root directory)
This action will then prompt the user for a password
|
 |
The following screen will be displayed, select Quality/Engineering/ECO,BCN, & Deviation Control Management (EBD) module.
|
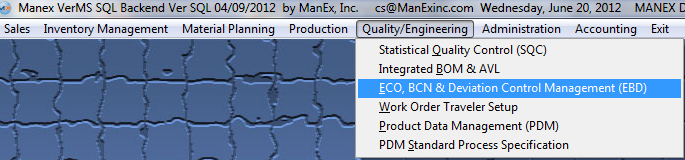 |
The following screen will be displayed:
Depress the Add Record Action button. Enter your password. The following selection screen will be displayed:
Select the desired Filter: by selecting the appropriate radio button - Active, Inactive, or All.
Select the desired Find: by selecting the appropriate radio button - Product Number, Part Class, Customer, or All.
Enter the information into the red box, depress the Enter key and the information will populate the screen.
|
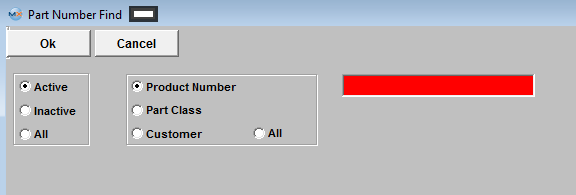 |
If user selects Any of the Filters and Find by All - a screen will appear listing all the Products, in numerical order, along with the Revision, Part Class, Part Type, Part Number, and Part Status.
|
|
Information pertaining to that part number will appear on the screen, as follows:
Select the type of change by depressing the down arrow next to the Type box.
An ECO selection is for a permanent change to the Inventory Master, Bill of Materials and Product Data Management normally a revision added. NOTE: These records will ONLY be updated if the Revision or Part Number has been changed.
A Deviation selection is for a one time change to existing Finished Goods Inventory and/or Work In Process. A selection of Deviation will NOT update no records; such as Inventory Master, Bill of Materials or Product Data Management.(The Update/Create Record tab will be grayed out.) This is a document for reference only.
A BCN selection is to change all part information just like an ECO, but user will NOT be able to create a new product number/rev, or click any "COPY" checkboxes on "Update/Create records" page. Also, the WO and SO lists will NOT be available for selections when creating a BCN .
|
 |
Select the ECO Source by depressing the down arrow next the the ECO Source box.
|
 |
Enter in the ECO Reference, Effective Date. (Note: This date MUST be prior to the WO Due Date to be applied), Expiration Date if applicable (this field is only enabled when creating a Deviation), enter in the purpose of the change and Description of change, and name of the ECO Coordinator.
The screen will appear as follows:
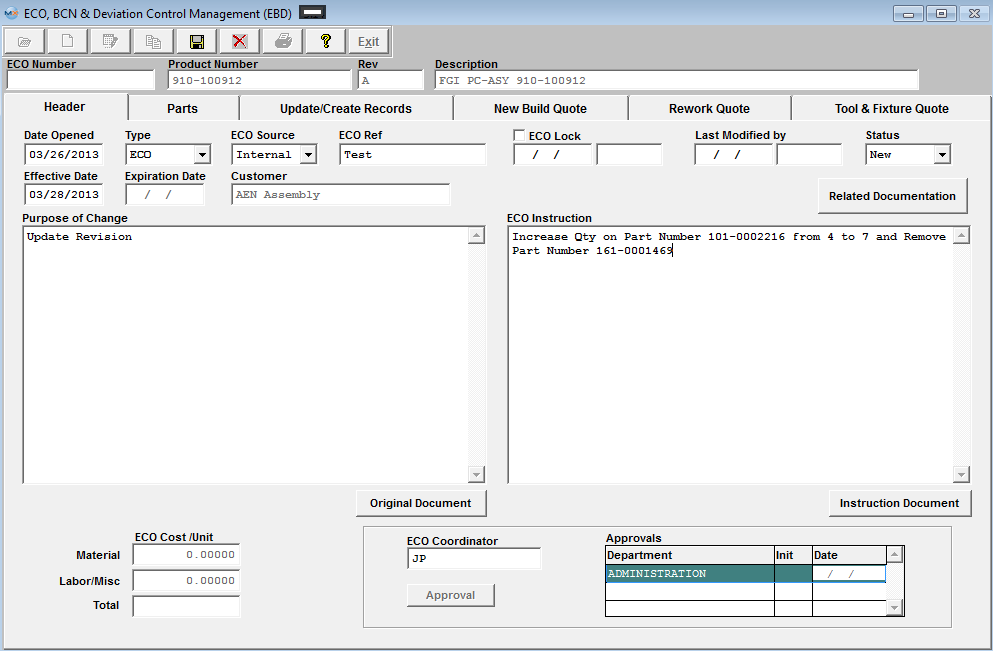
PARTS TAB
Enter the Parts screen
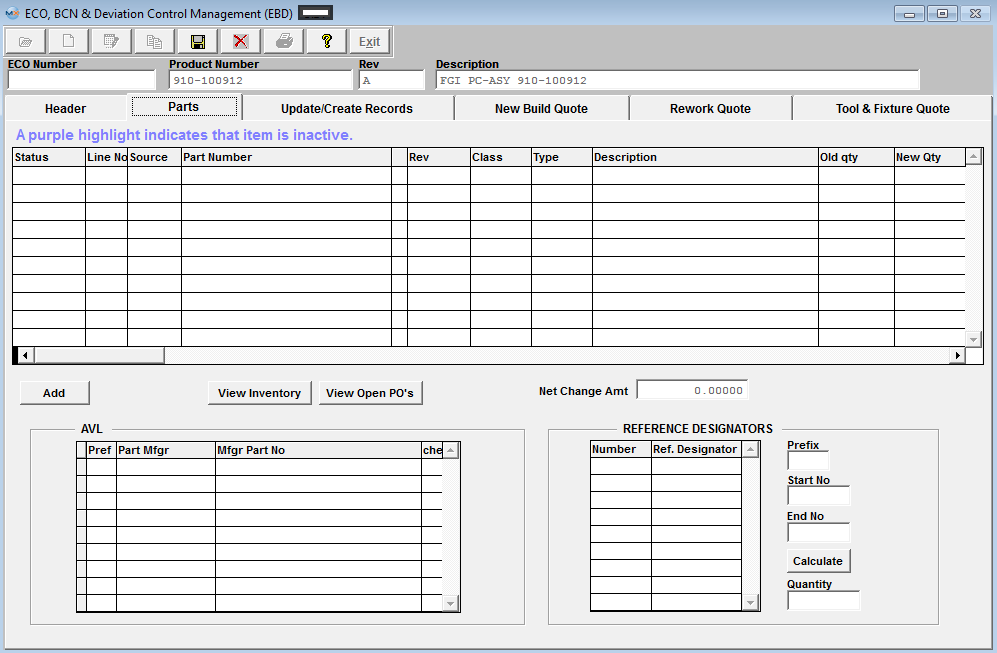
To record an ADD to an ECO record
Depress the Add Button.
The system will then default to the Status field. Depress the down arrow next to the Status field.
The following choices will appear.
Select Add from the Status listing.
|
 |
Enter in the new Line No that it will be listed as on the BOM.
Select Source by depressing on the down arrow next to that field.
The following selection will appear:
|
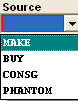 |
Enter in the Part Number, and the Revision number, Type, Class, Description, and AVL information will update automatically. If the part added has a status of "Inactive" within the Inventory Control Management, it will be highlighted in purple as an indicator to the user that this item is inactive at this time. If the user chooses to leave the inactive part on the ECO, that part number record status will automatically be changed to Active upon the "Update Records" button being depressed, so user will not have inactive parts listed on the BOM. The user will receive a warning that an XLS file has been created for reivew.
Enter in the new quantity to be used in the assembly, and Customer Part Number and Rev. if applicable.
Scroll over to the right and select the Work Center by clicking within the Work Center field. The following selection screen will appear.
|
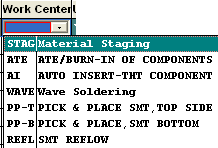 |
Note: The system will give the user the following warning and will not allow user to save the ECO if the same part number and work center are duplicate in ECO. |
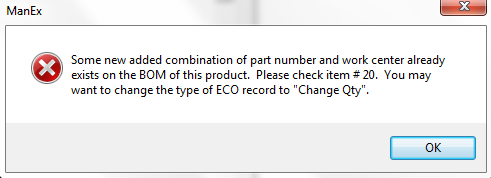
|
The system will default into the U/K field, for the component to be included in the kit. You have the option to change this entry to one of the following Yes, No, or Free Stock.
If the user attempts to enter any other characters into this field they will receive the following warning message.
|
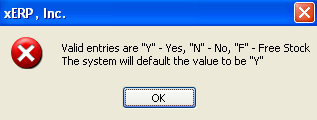 |
Enter in the Reference designator(s). First enter the character in the prefix box, then the Start number. Depress the "Calculate" button and the Reference Designator will update.
|
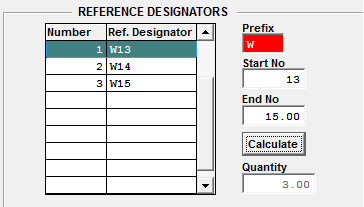 |
You will then be able to view the Inventory Locations for the highlight part number, by depressing the button. The following information will be displayed:
|
|
You will also be able to view any Open PO for the highlighted part number, by depressing the button. The following information will be displayed:
|
 |
The AVL info will default in from the Inventory Control module. You may check or uncheck the approved AVLs. If the program finds duplicate part numbers in a BOM, any Alternate part number associated with the original line item will be carried fwd to the new item using the same part. As far as the AVLs, the program will get all unchecked AVLs from all items and to update all items. For example, BOM item #2 have AVL A,B,C, and D, only C is unchecked. Now in ECO, user adds item #5, it has AVL A unchecked. And if item #2 had a alternate part associated with it, that ALT part will also be carroed fwd to Item #5. We have added a message in the updating routine, if the system does find duplicate Part number, then a message will popup and let the users know then system will take the actions explained above. |
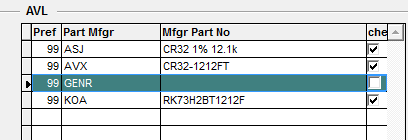 |
If user enters a part number that already exists in the BOM, but for a different WC, the program will use the AVLs from the new added part number(s) and update the AVLs for the existing part number (as stated in the message received upon Update Records).
For Example: If a part already exists on the BOM, and now the user adds the same part again (with different WC), and makes changes to the AVL. When the ECO gets updated, the system will use the new AVL(s) from new added part and update the AVL(s) for existing part.
If I have a part on the BOM already, with 5 part/mfgr/mfgr part no (A,B,C,D,E) and 3 of them (A,C,E) are currently checked on BOM. Now the user creates an ECO and adds the same part in ECO and changes the AVL to have on (A,B) checked. When the ECO record gets updated, both parts will now have only (A,B) checked.
|
cell |
If user adds the same part multiple times to the ECO and doesn't enter the same AVLs for the same part(s) that appears multiple times in the ECO, this message will appear and user must change the AVLs to be the same before they can save the ECO.
|
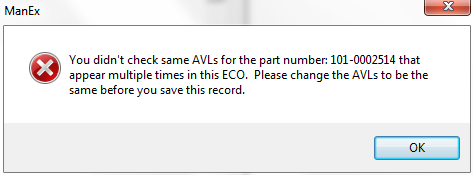 |
To record a DELETE to an ECO
Depress the Add Button.
The system will then default to the Status field. Depress the down arrow next to the Status field.
The following choices will appear.
Select Delete from the Status listing.
|
 |
Enter in the Bill of Material line Item, that you wish to have removed from the BOM.
The screen will then update with the information pertaining to that item.
Leave the New Quantity as zero.
If you do NOT want the part scrapped, scroll to the right and remove the check mark from the Scrap Item field. (Note: This field is for internal reference only, it does NOT affect any other modules).
To record a CHANGE to an ECO
Depress the Add Button.
The system will then default to the Status field. Depress the down arrow next to the Status field.
The following choices will appear.
Select Change Qty from the Status listing.
|
 |
Enter in the Bill of Material line Item, that you wish to have changed on the BOM.
The screen will then update with the information pertaining to that item.
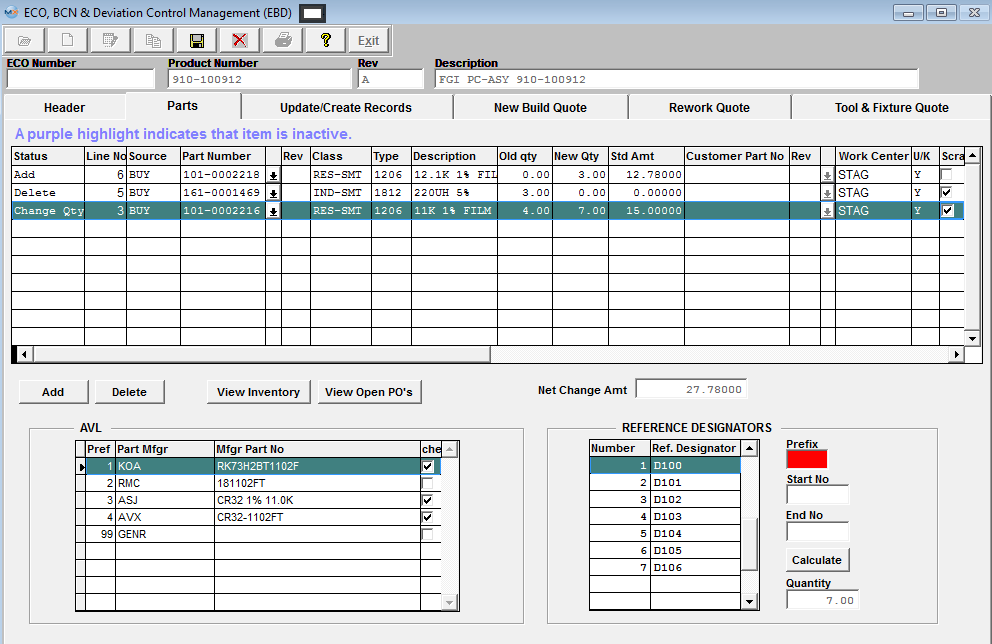
Enter in the new quantity.
Update the Reference Designator information.
In the U/K field, change to if you do not want the change to be used in the kit.
If you do NOT want the item scrapped, remove the check mark from the Scrap Item box (Note: This field is for internal reference only, it does NOT affect any other modules).
To change the Work Center where the component is added, depress the down arrow next to the Work Center field. The following selection screen will be displayed:
Make your selection.
|
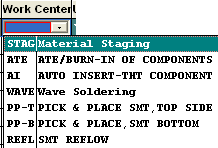 |
UPDATE/CREATE RECORDS TAB
Enter the Update Records screens.(Note: that if the type was selected as Deviation within the Header screen, then the Update Records screen will be grayed out and unavailable for selection)
Inventory Changes Section:
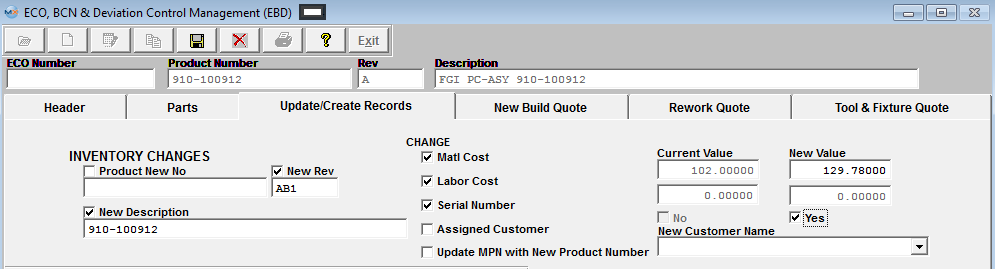
Check the applicable box and then Enter in a new product number, revision number, or new description, if desired.
NOTE: For the purpose of many users wanting to create several ECOs for the same product number without really updating the records (meaning creating a new part in inventory) Manex will allow you to save and approve the ECO even if they have not selected to create a new Part or Rev within the system. Upon depressing the Update Records button the system will check to see if New Product No or New Rev has been marked, if left blank then the system will just update the status of the ECO to Complete without creating a new product number in the system.
NOTE: When product is changed through ECO module the Material Type will be carried fwd to the next/new Product/Rev that is being generated at the part level, but will not carry fwd the material type at the AVL level. The system will default in "UNK" as the Material Type for the AVL Level.
To update the Material Cost, then check mark the box next to Matl Cost. The new Value field will update based on the changes made within Parts screen.
To update the Labor Cost, then check mark the box next to Labor Cost. The New Value field will update based on the changes made within the New Build Quote screen.
To require a serial number, then check mark the box next to Serial # Required. Then go to the box under the New Value column it will remain NO until checked then it will update to YES.
To change or assign a customer, check the Assigned Customer box. Depress the down arrow to see a list of customers. Select the customer of choice.
Note: Customer name can be changed on the BOM for the product, only if either the Product number or revision and the product has NO consigned parts for another customer nor any make/phantom parts that are assigned to another customer, and the product is not a sub-assembly for another product.
NOTE: This field is only editable if there are NO open Sales Orders or Work Orders linked to this product.
|
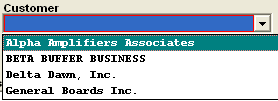 |
If user is attempting to assign a new customer name to a product with customer consigned parts reporting to it, user will receive the message displayed and will NOT be allowed to change customer name. |
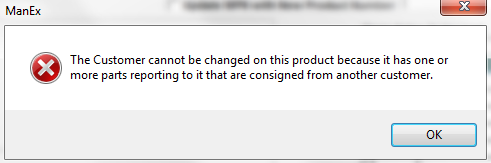 |
If user is attempting to assign a new customer to a product with any Open Sales Orders or Work Orders linked to it they will receive one of the messages displayed and will NOT be able to save the ECO. |
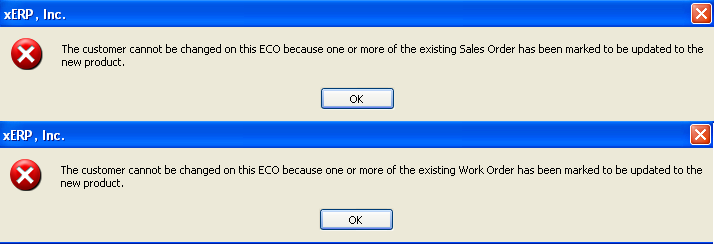 |
In the ECO process of modifying or adding Parts to the ECO, there is a field which contains the Customer Part number, if available. At the present time, this field is empty and non-editable for changing or deleting a part from the BOM. But if the user wishes to add a part, they may do so by entering in either the internal part number or the customer part number in the customer part number field, and the program will locate the corresponding internal part number and enter it. The search is based on the customer part number entered AND the customer associated with the BOM from which the ECO was originated.
Because Manex allows users the ability to use the ECO module to create New Part Numbers via the ECO process, and even assign a new customer to the new part number, we must limit the customer information to that of the original customer, as we cannot determine at what point the reference should change customers, or even if it should. Furthermore, if the user does elect to create a new part number for a new customer, items unchecked on the AVL will transfer to the new bom (if checked on the update sheet). However, there may be a conflict between the AVL of the original customer and the AVL of the new customer, so the user is urged to verify the AVL content of a new bom for a new customer created with this module.
COPY SECTIONS:
Look at the items all ready checked to be copied. If you do not want the items copied, uncheck them.
Note: When creating new Product within Inventory via ECO change the new Product's AVL will be auto assigned with the Material Type of "Unk". It will not keep the MT from the original Product the ECO was originated from.
|
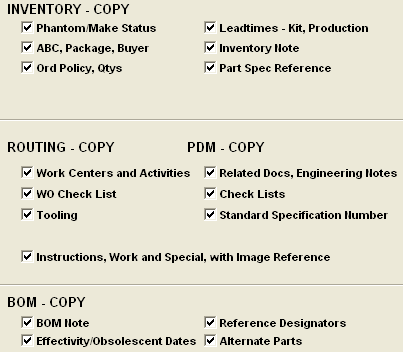 |
OPEN SALES ORDER LIST:
The Open Sales Order List will include all open Sales Orders including the ones that are flagged as "Admin Hold" and//or "Mfgr Hold", and any open RMAs against this product.
In the Open Sales Order List, check mark within the Change box column if you want the Sales Order and/or RMA to be changed.
Note: If there have been NO items shipped against the sales order selected then the system will just replace the existing product with the new product and/or revision within the Sales Order.
If there have been shipments made against the item the old line item will have the Ord Qty updated to equal the total Shipped and the status changed to Closed. A new line item will have been created for the new Product/Rev for the remaining balance that was left on the original item.
If you do NOT want the price changes to affect the sales order prices check the "Retain Sales Order Prices" box. If you would like to retain any extra charges against the line item check the "Retain Remaining Extra Pricing Items" box.
Refresh SO button has been provided so the user can refresh the Sales Order list to check for any new SO created in the system since the ECO was first created.
|
|
The completed screen will appear as follows:
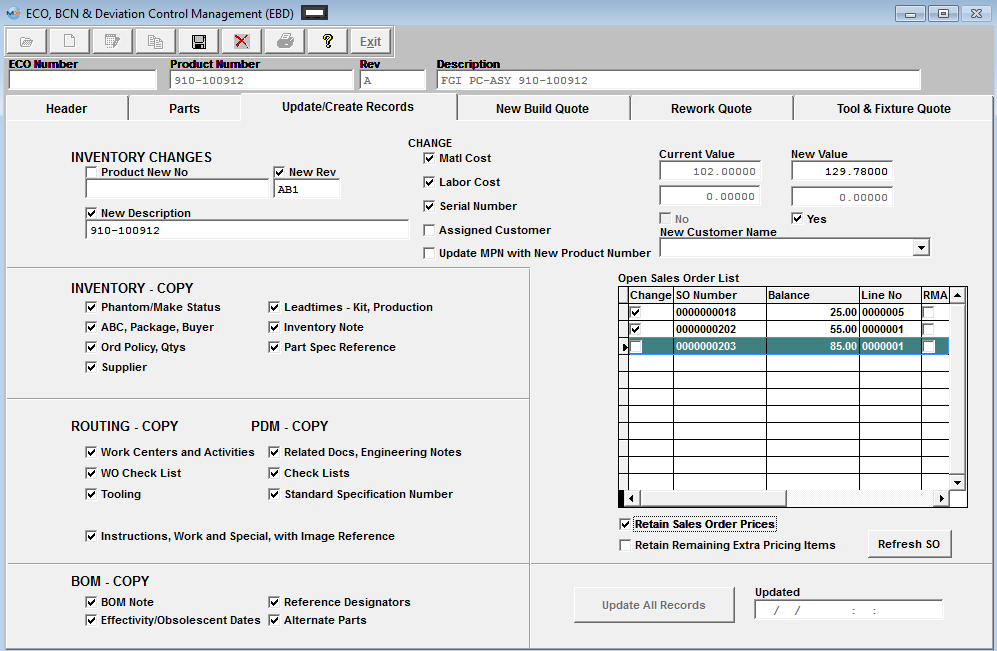
NEW BUILD QUOTE TAB
Enter the New Build Quote screen.
To add a new Labor Cost associated with the new revision, depress Add the button. Type in the Labor Cost Description. Type in the new revision cost per unit. Continue to Add as required.
The completed screen will appears as follows:
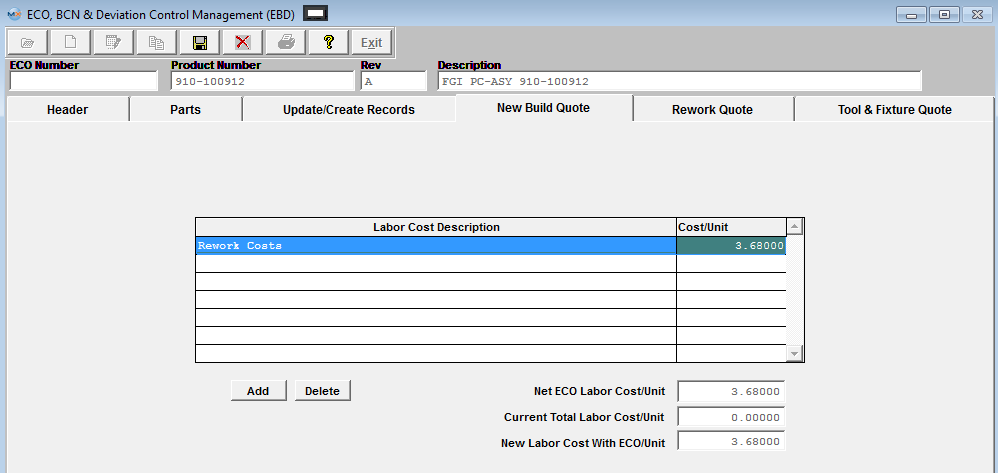
REWORK QUOTE TAB
Enter the Rework Quote screen.
In the Open WO List (As of ECO Open Date), check mark within the Change box column if you want the WO to be changed/reworked. The WO's checked will only be changed/reworked when creating an ECO. They will not be changed/reworked when creating a deviation. (This field is for reference only when creating a deviation).
You will receive the following message, as you check each box:

Depress the OK button to continue.
If Work Order is shaded in WHITE - that means that this Work Order has no qty in FGI so the system will automatically update the Work Order to the New Revision. If a kit is in process for the Work Order selected user MUST depress the "Update Kit" button within the kitting module after the ECO is approved for any part changes to be reflected. NOTE: When the ECO takes place and the WO record is updated SFT losses the transfer history for the old revision and starts over with only xfer history for the new revision from that point on. See Article #3401 for further detail.
If Work Order is shaded in BLUE - this means that this Work Order is partially completed and will be split into two Work Orders: The system will change the original Work Order (original product number and revision) build qty to match the qty completed and close this Work Order. The KIT for that work order will retain only enough material to build the completed quantities. The system will then create a new work order for new product number/revision for the balance quantity. All the extra material issued to the original work order will be de-kitted from original Work Order and issued to the new Work Order.
If Work Order is shaded in PINK - These Work Orders are partially completed and some of the issued components are either serialized or lot code traceability activated. These specific components have to be de-kitted manually prior to proceeding. Or the original Work Order, has to be closed (balance reduced to completed quantities) and extra material de-kitted manually. Then, the new Work Order has to be created for the balance quantities.
If needed, you have the option to refresh the Work Order listing to see if any new Work Orders have been created for this product since this ECO was originally opened, by depressing the "Refresh WO" button.
To add costs solely associated with the rework of open Work Orders and/or Finished Goods Inventory, depress the Add button under the Rework Cost Description window. Type in the Rework Cost Description and the related cost per unit.
The Inventory Locations (As of ECO Open Date), will default in and is for reference only.
The Totals (As of ECO Open Date) will default in displaying the quantity in WIP and the quantity in FGI. The Units to Rework and the Cost to Rework will update automatically.
If any new Work Order's were created they will be displayed in the "New Work Order" field for reference:
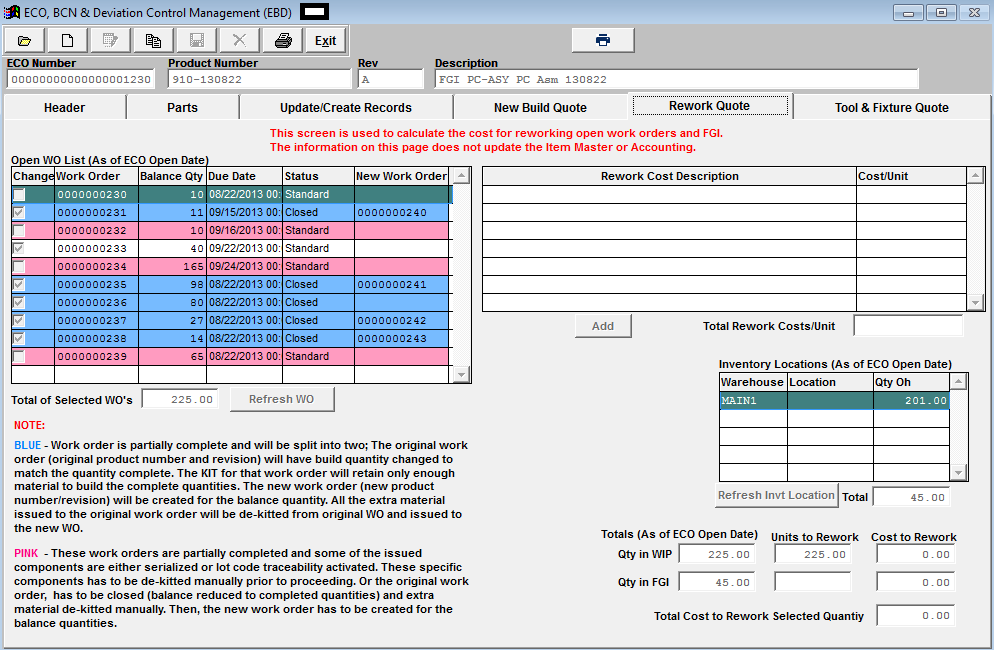
TOOL & FIXTURE QUOTE TAB
To add new Tool/Fixture Information, depress the Add button below the section.
Add the Tool/Fixture information from the pull down.
|
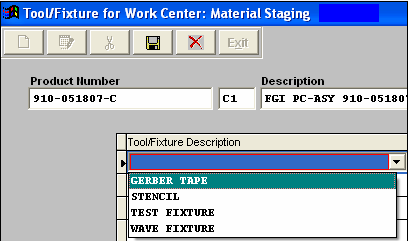 |
Choose the Work Center from the pull down. |
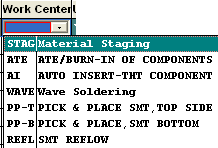 |
Fill in the cost amount, Charge Amount, Effective Date, and Termination Date.
Once the ECO record has been approved and updated within the system, this Tool/Fixture information will be carried forward into the PDM and Routing Setup modules.
The completed screen will appears as follows:
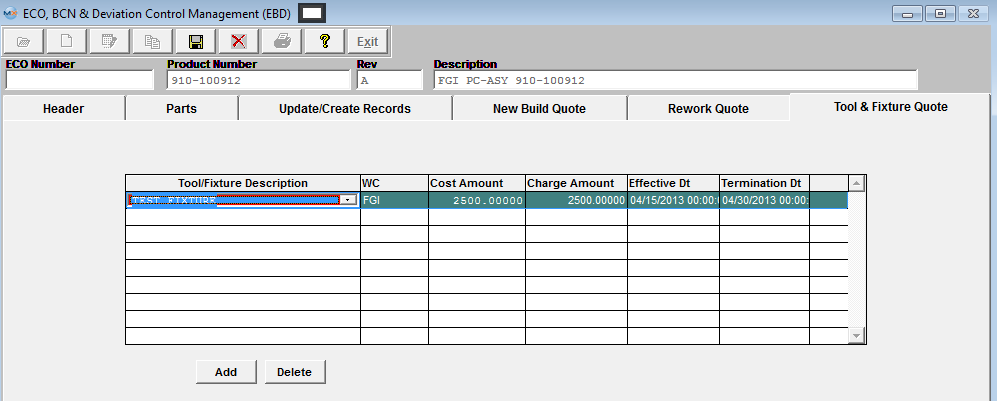
Depress the Header tab. Note that the ECO Cost/Unit columns have updated at the bottom left hand side of the screen:
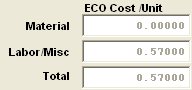
Depress the Save record action button or the Abandon changes action button.
Upon Saving the user may be given a message if one or more of the parts do not have the same number of reference designators as the new quantity within the ECO, or BCN. This is giving the users the option to print out a report to list these item or not.

If Yes is selected the report, ECO Report Incorrect number of reference designators will go directly to the default printer and the next message will be displayed.
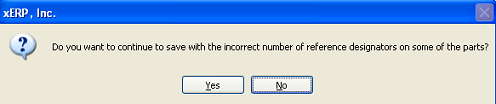
The user now has the option to cancel out of the save or continue.
The user should go back to the reference designators section for the part listed in the report and change the number of designators to equal the quantity required.
The Approval button will be available. Depress the Approval button. You will be prompted for the appropriate department password. Continue this process until all of the departmental approvals have been entered, as displayed:
|
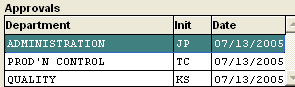 |
Once all of the Approvals have been fulfilled then within the Update Records tab the “Update All Records" button will become available.
Depress the Update All Records button. The records you selected will update. The ECO or BCN will now show with the following Updated time stamp.
Note: For a new revision, P/N, etc., go into the Inventory Master and if desired, update for the Warehouse location in the Quantity Information tab (the system will copy the warehouse information from original Product selected). Also, update for Mfgr Part Spec.
Adding A New Deviation Record
Overview:
The difference between the ECO and the Deviation is: A Deviation is a method to document and approve a temporary change from the normal operation until an ECO is created to replace the Deviation, it is only a record that someone approved a change in some method for a work order(s). That is the reason the Deviation has an Expiration Date field in the main page and it will not update any active modules, part number change, rev change, description change or anything else. Whereas, ECO is a permanent change and change the part number, or rev or description, or standard cost, or anything thing else including updating any or all active files.
The basic procedure of processing a Deviation follow basically the same rules as a Regular ECO except for the Update Records button is disabled.
Enter the ECO module. Depress the Add Record action button Select the desired product number. Then for the Type Select Deviation
|
|
Once Deviation has been selected as the Type, continue on and enter in the remaining Deviation information as explained in the Adding ECO section above. Note: For a Deviation you MUST make sure you complete the expiration date so users know that it is for a limited period of time. If this field is left blank the deviation will NOT be displayed in the SFT module.
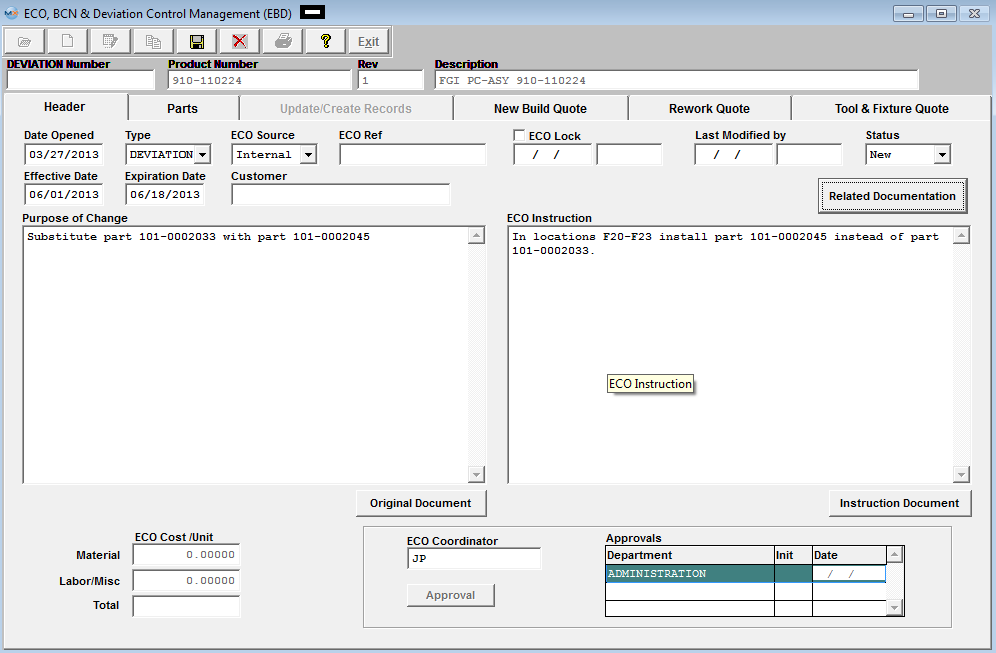
Note: The Update Create Records tab will remain grayed out and unavailable for any Deviation records entered within the system.
Once the Deviation has been completed the normal list of Approvals need to be entered.
The status of the Deviation record will update to Approved.
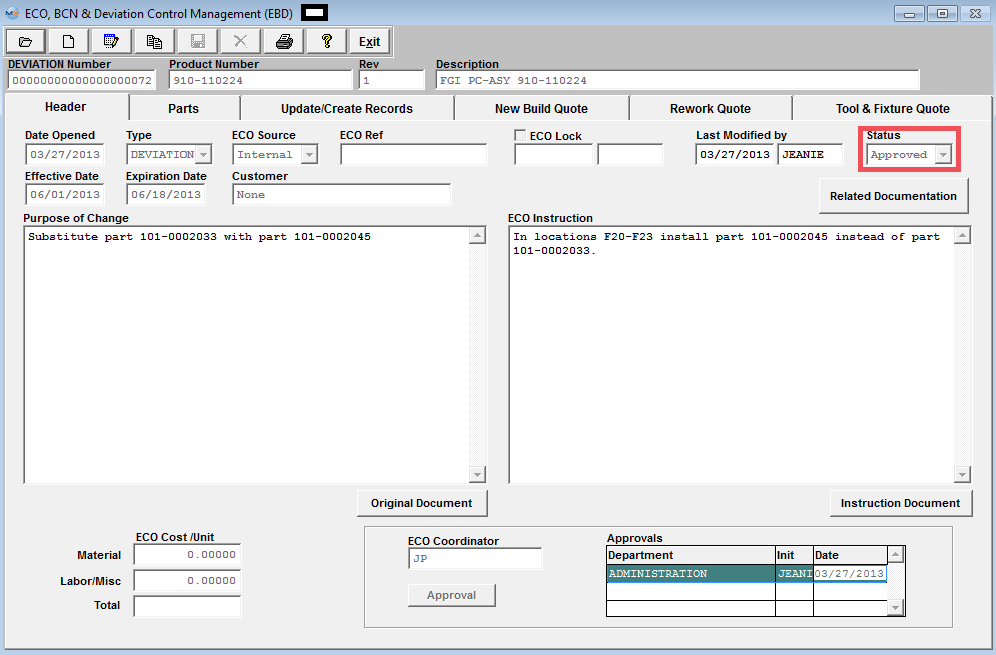
Changing the status of a Deviation from Approved to Completed.
The Status of a Deviation will remain as Approved in the system until the users manually changes the status to Completed. Once the status of a deviation has been changed from Approved to Completed it will no longer appear in the SFT (Shop Floor Tracking) module.
Find the desired Deviation record. |
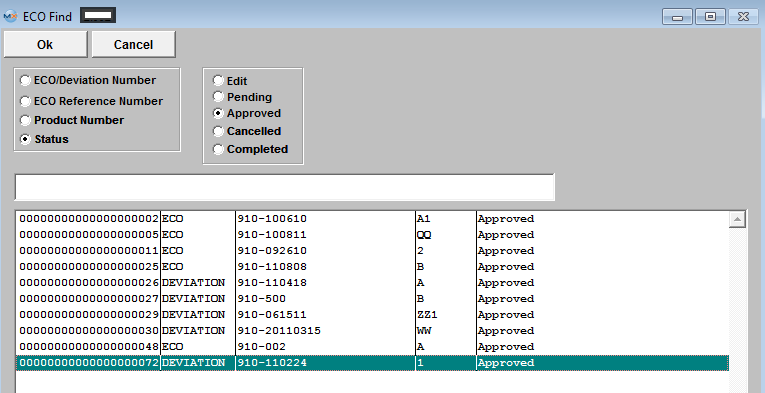 |
Depress the Edit record action button. Click on the down arrow next to the Status field, the following selections will be available for Deviations.
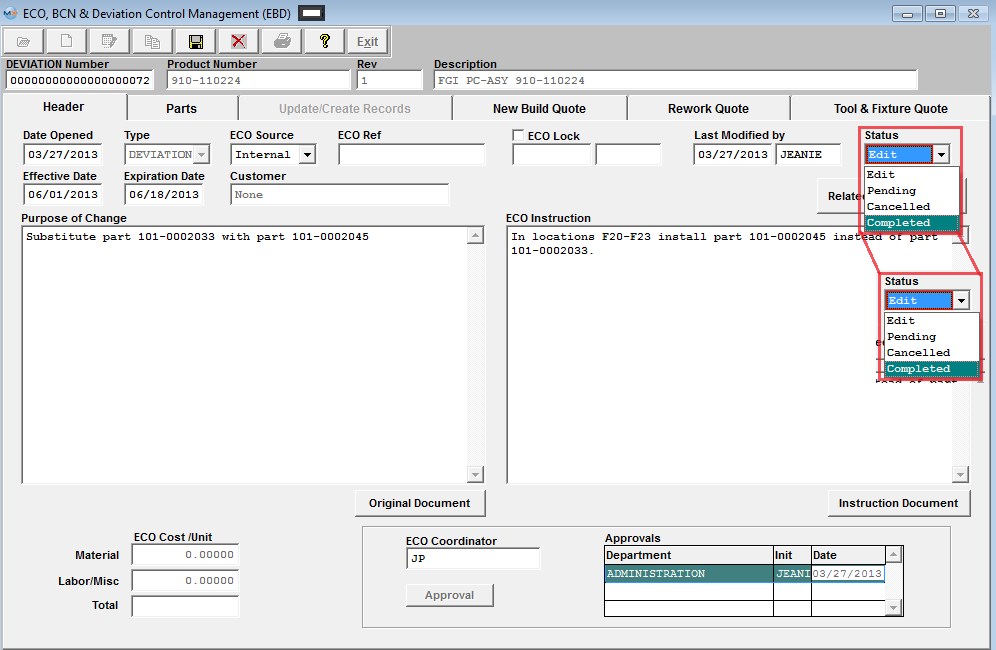
Change the status to Completed. Depress the Save record action button to save the changes the changes, or depress the Abandon changes action button.
The Deviation will now show in the Status listing of Completed Records.
|