To display or print a Report for a BOM, first find the BOM. (See Article #4795).
To obtain the Bill of Material Reports within the Web, select the WEB Print button from the ManEx action buttons at the top of the screen. For further detail on How the Reports work within the Web refer to Article #5477. (Note: The only BOM Report available on the WEB right now is the PO BOM Addendum)
Note: In order to access the Reports within the Web the Company Root URL must be setup within the System Appearance module and user must be linked to web within the System Security Module.
Select
the Report Type: BOM - A List of Reports will be displayed that are
available on the Web for BOM
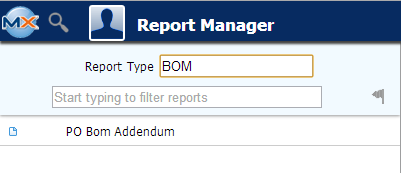
To obtain the Bill of Material Reports within the desktop, select the Print button from the ManEx action buttons at the top of the screen.
The
following reports screen will display a list of reports that are available on
the ManEx Desktop:
Highlight the report desired and click on the Option tab. (The BOM reports will indicate in the Source column if the item is setup as Make/Buy or Make/Phantom, along with Consigned or Buy).
BILL OF MATERIAL by Part Numbers
Select if you want to print the Report to the screen or a Printer.
Check the box if you want to Explode BOM Out to all Levels.
Depress the OK button.
|
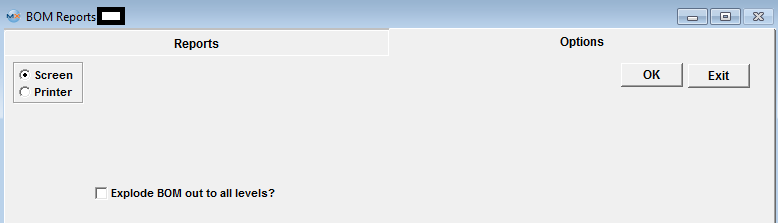 |
The BOM displayed on screen will print as follows. (The two PN's boxed in Red are parts that have been exploded out for Sub-Assembiles)
BILL OF MATERIAL BY ITEM NUMBERS
Select if you want to print the Report to the screen or a Printer.
Check the box if you want to Show BOM item notes list? Show BOM note? and Explode BOM Out to all Levels?
Depress the OK button.
|
|
The BOM displayed on screen will print as follows: (The parts in the Red boxes are parts that have been exploded out)
BILL OF MATERIAL WITH STANDARD COST
Select By Item #, By Part #, or Descending Extended Cost from the Detail Report.
In VFP the system used to take the Std Cost from the Make/Phantom itself even through when a Make/Phantom is added as a sublevel it is always exploded out to the components. So it really should be taking the component values in this case. SQL version of the report will do that.
· in VFP the report did not explode out the components for a true Phantom bom - but in SQL version of the report it will.
· V VFP did not have the Setup Scrap Cost per individual part number, now that will be available in SQL version
· In SQL Version I am still listing the Make/Phantom or Phantoms on the report as reference but they will display as Grey and will not list out the Cost Value
Depress Ok.
|
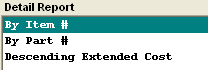 |
Note: This report takes into consideration the Std Bld Qty when calculating the setup scrap. You might find the cost calculated in SFT is different from the calculation shown on this report due to, that if the part UOM is "EACH" and the part has scrap % the code will round it up to next inter number.
a) For the PHANTOM parts in this report the standard cost calculated is based on their components (SUM of component's qty * component standard cost). Once the standard cost is calculated for the PHANTOM part, the report will treat the PHANTOM part as a single entity on the top assembly BOM and proceed as it was a BUY part with the std cost already entered.
b) If one of the component parts is a MAKE (not MAKE_BUY) and HAVE components assigned to it, the report will NOT show std cost of the parts itself, it will only show std cost of its subcomponents.
c) If one of the component parts is a MAKE (not MAKE_BUY) and does NOT HAVE parts assigned to it the report will show std cost of the part itself.
d) If one of the component part is a MAKE and MAKE_BUY the report will show price for the part itself and will show 0.00 costs for the subcomponents.
e) If one of the component part is a MAKE and a Phantom/Make the report will NOT display the std price for this part because the report will show the cost of this parts components.
Note: This report will only display the costs for ACTIVE parts and subassemblies as of the date of the report and will NOT include any parts that may have been identified as inactive either in the item master or in the obsolete date of the part on the BOM.
The values displayed should be in sync with the Cost Roll Up values. The following may be why the Standard Cost Roll is different from the Cost BOM Reports.
a) On the costed BOM Report for a Make/Buy assembly we display the value of the BOM in the costed report, but that total is NOT used in subsequent rollups to higher levels only the standard cost is.
b) In Kit Default Setup , user can "Exclude Scrap and Setup Scrap" in Kitting, MRP, and Cost Rollup, and this will override the "Setup Stcrp" box in the BOM. Therefore, if user checks "Setup Stcrp" checkbox along with a Standard Bld qty in BOM header, but has the checkbox checked in Kit Default Setup to "Exclude Scrap and Setup Scrap" for Cost Roll, the Cost Roll will NOT calculate the Setup Scrap cost, but this report will always calculate the Setup Scrap cost and this will cause unfavorable Configuration Variances. For further detail on how Excluding Scrap and Setup Scrap values will affect the variances see Articles #3067, #3053, and #3320 .
The BOM displayed on screen will print as follows: This report ALWAYS includes ALL the parts (including the items flagged as "N" for Used in kit)
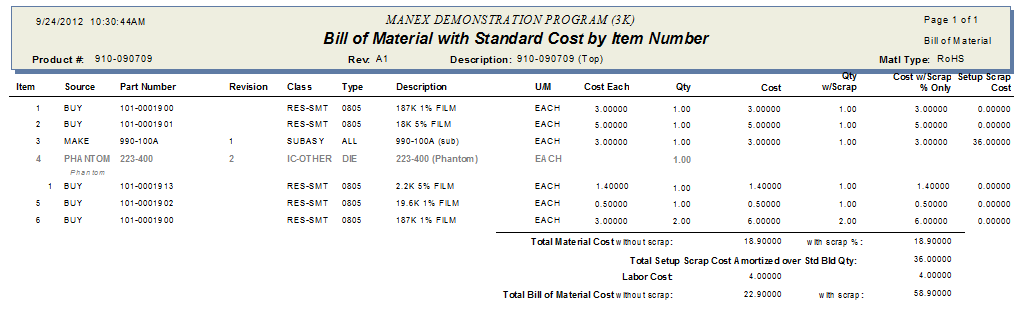
BILL OF MATERIALS WITH REFERENCE DESIGNATORS & AVL
Select; Current, As Of, and All from the Detail Report.
Current = This report will display the Material Type to the Component Level, and the components on the BOM based off of the Computer Date at the time the report is ran.
As Of = This report should function basically the same as the Bill of Material with Ref Designator ~ Current report. Except that this one will require the users to populate an AS OF date. Then the resulting report will display the BOM Items based off of that AS OF date compared to the Eff/OB Dates.
All = This report should function basically the same as the Bill of Material with Ref Designator ~ Current report, Except that is will display ALL components that exist on the Obsoleted or not. This report will also list the Eff date and OB Date. If either or both of these are blank then the report will not display the information. It will only display if they are populated. This way the users can get a good look at ALL the parts that were ever on this BOM and when they become Effective or Obsolete.
Depress Ok.
|
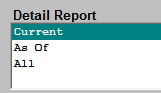 |
Check the boxes if you want to Show BOM item notes list? Show BOM note? and Explode BOM Out to all Levels?
Depress the OK button.
|
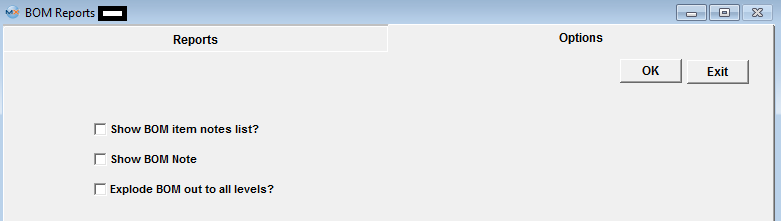 |
The following screen will be displayed. Select "Yes" if you want to export the report to XLS Layout. |
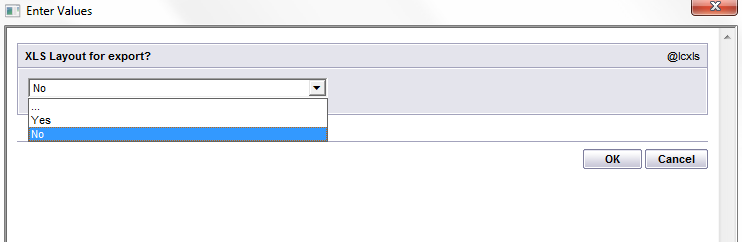 |
If the user selects 'YES' the display will show as follows. Keep in mind not all of the field could be displayed on this page size, but upon export all fields will be displayed.
Select the Export option
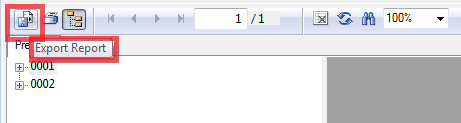
The followng screen will be displayed, Select format 'Excel - Data only'
The following screen will be displayed, within the option section be sure to select to include the Header Info
Select file name and destination
XLS results should look very similar to the VFP XLS dumps we have as displayed below

If user selects "No' to export report to XLS file The BOM displayed on screen will print as follows:
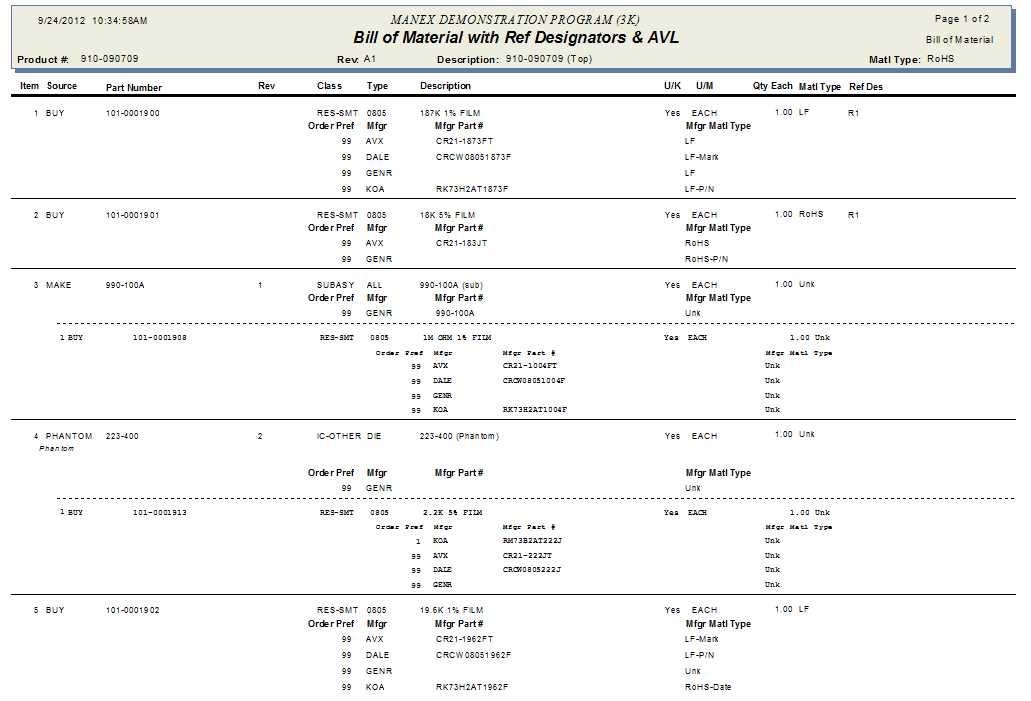
TOP ASSEMBLY PART USAGE
Enter a quantity.
Select to Ingore Scrap, Setup Scrap, Both, or None.
Select to Suppress Not Used in Kit Items or Not or Use System Default.
Depress Ok.
|
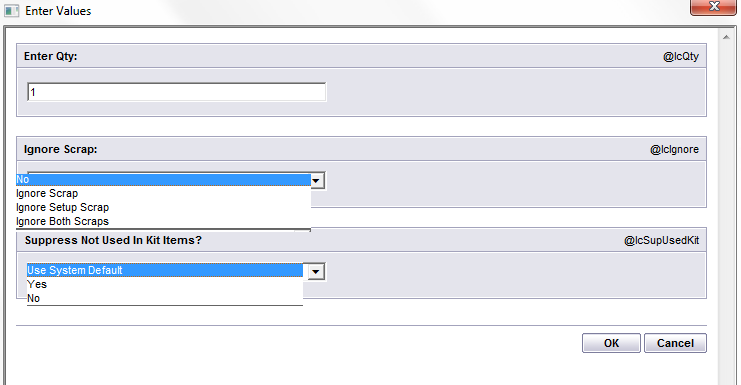 |
The following report is printed:
|