1. Purchase Order Receiving & DMR |
1.1. Purchase Order Dock Receiving |
1.1.1. Prerequisties for PO Dock Receiver | Prerequisites Required for Entering a New RECEIVER
After activation, "Purchase Order & Dock Receiving" access for each user must be setup in the ManEx System Security module. Users with “Supervisor Rights” will automatically have access.
Open Purchase Order |
There must be an open purchase order for the receipt and the PO status MUST be "Approved". If the PO is in "Edit" mode the PO Dock will not find receipt.
|
|
1.1.2. Introduction - PO Dock Receiver | In Purchasing Setup it gives the user the option to use PO Dock Receiving. If this box is checked, the purchases are received at the dock requiring the user to complete a PO Dock Receiving record, listing the supplier’s packing list number and the quantities per that packing list. An inspection report is printed. The purchases are inspected and counted. (If this box is left unchecked the user can skip the PO Dock Receiving step and go directly to the PO Receiving and Inspection record.)
|
1.1.3. Fields & Definitions for PO Dock Receiving | 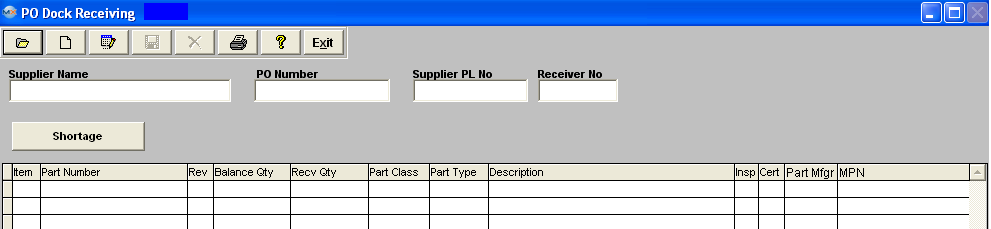
Fields & Definitions
Supplier Name |
The Name of the supplier. |
PO Number |
The Purchase Order Number. |
Supplier PL No |
The Supplier’s Packing List number. |
Receiver No |
The user’s receiver number. |
 |
Clicking on this button will bring up a screen listing any shortages for the part number highlighted. If there are no shortages for this part a message will appear informing user that there are no shortages for this part. |
Item |
The item number per the Purchase Order. |
Part Number |
The number the user has assigned to the part. |
Rev |
The revision number related to the Part Number. |
Balance Qty |
The un-received quantity portion of the item. |
Recv Qty |
The quantity received per PO Dock Receiving. See Article #1240 for more detail on why the system will not allow user to enter in a fraction of a number, and an alternative. Note: Users must have special access in order to receive overages, There is a checkbox to allow overages within Security/User Rights for PO Receiving.
Note: The overage is applied to the entire PO order qty - it does not go down to the schedule level. Example: If you have an order qty of 100 and an allowed overage of 5% the system will allow you to receive in a total overage of 105. But if you have only scheduled a qty of 25 and go to recieve in qty of 30 the system will allow you to do so, because it has not met the order overage yet.
|
Part Class |
The classification to which the part number belongs. |
Part Type |
The type within the class to which the part number belongs. |
Description |
The description of the Part Number. |
Insp |
Displays whether Inspection is required as set up in the Inventory Control Management module. |
Cert |
Displays whether Certificates are required per the Inventory Control Managment module. |
Part Mfgr |
The name of the manufacturer for listed part. |
MPN (Mfgr Part No) |
The manufacturers part number for listed part. |
|
1.1.4. How To ..... for PO Dock Receiver |
1.1.4.1. Find Dock Receiver |
Enter the SQLMANEX.EXE (within the ManEx root directory)
This action will then prompt the user for a password
|
 |
The following screen will be displayed, enter Inventory Management/Purchase Order Receiving & DMR/Purchase Order Dock Receiving Module
.
|
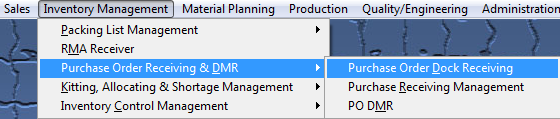
|
IF DOCK RECEIVING is DISABLED in Purchase Setup user will receive the following message:
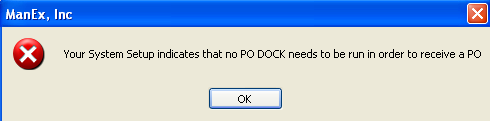
IF DOCK RECEIVING is ENABLED in Purchase Setup the following screen will be displayed:
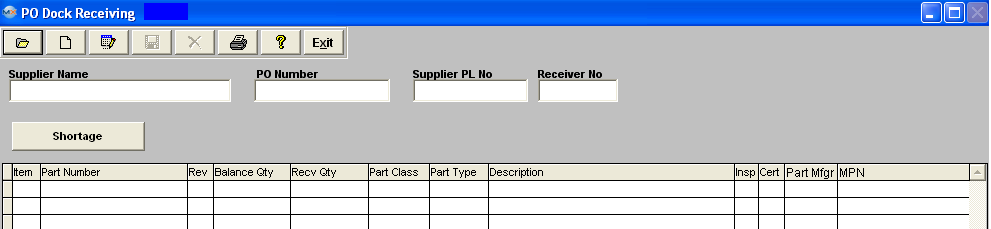
To Find an existing PO Dock Receiver, depress the Find record action button. The following selection screen will be displayed.
Select the desired Filter: by selecting the appropriate radio button - Open Receivers, Closed Receivers, or All.
Select the desired Find: by selecting the appropriate radio button - PO No., Supplier, Receiver No., Inventory Part No., Inventory Mfgr Part No., All, MRO Part No., MRO Mfgr Part No., or MRO Description.
Enter the information into the red box, depress the Enter key and the information will populate the screen. If you do not know the exact number, Customer, etc you may enter in a partial number, letter, etc, then once you depress the enter key the system will pull up the matching record onto the screen or a list of all PO Docks that contain the partial number, letter, etc. entered, to select from.
The user may exit the selection screen without a selection by selecting the Cancel button.
|
|
If user selects ANY of the Filters and Find by All - a screen will appear listing all the PO Dock Receivers filtered by the PO Number in numerical order, along with the Supplier name, Receiver Number, date PO Dock Receiver was created and Status of PO.
The user has the option to view the PO Dock Receiver by either entering the Purchase Order number into the red box, or scrolling down the list, highlighting the desired record and double click on it.
|
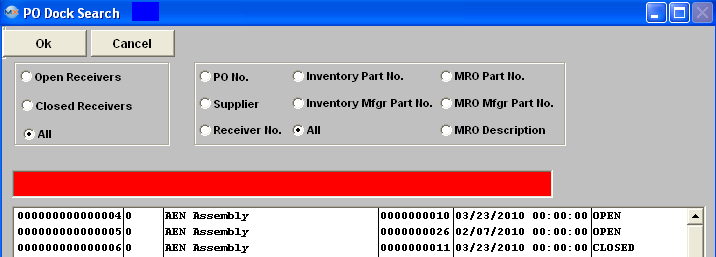 |
Once you have made your choice, the information will be displayed as follows:
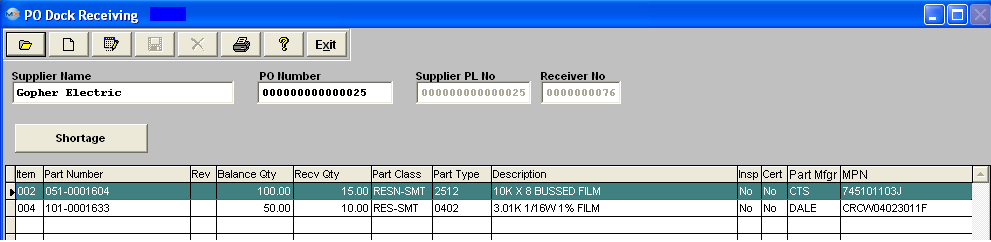
|
1.1.4.2. Add a Dock Receiver |
Enter the SQLMANEX.EXE (within the ManEx root directory)
This action will then prompt the user for a password
|
 |
The following screen will be displayed, enter Inventory Management/Purchase Order Receiving & DMR/Purchase Order Dock Receiving Module
.
|
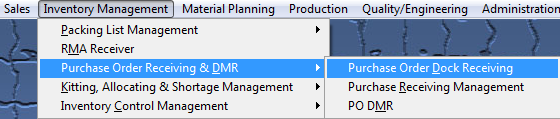
|
IF DOCK RECEIVING is DISABLED in Purchase Setup user will receive the following message:
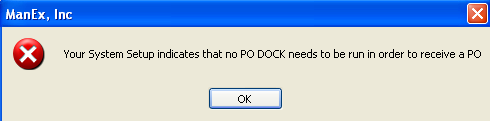
IF DOCK RECEIVING is ENABLED in Purchase Setup the following screen will be displayed:
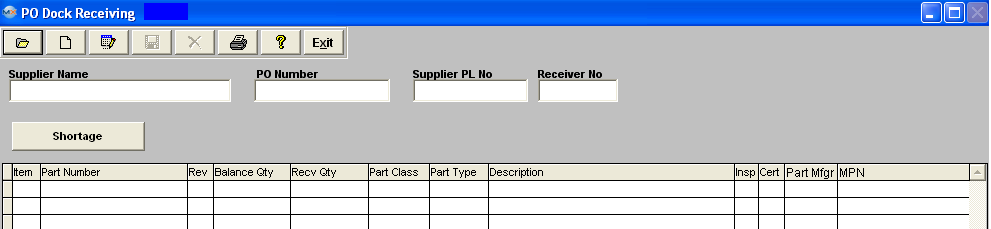
To add a new receiving record, depress the Add action button. User will be prompted for their password. The following selection screen will be displayed.
Select the desired Find: by selecting the appropriate radio button - PO No., Supplier, All, Inventory Part No., Inventory Mfgr Part No., MRO Part No., MRO Mfgr Part No., MRO Description.
Enter the information into the red box, depress the Enter key and the information will populate the screen.
The user may exit the selection screen without a selection by selecting the Cancel button.
|
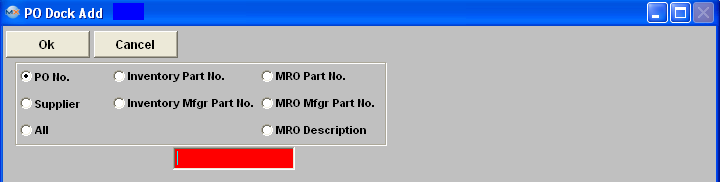 |
If user selects ALL, the following screen will appear:
Enter the PO number into the red box or highlight the PO Number of choice and double click.The PO information will populate the screen.
|
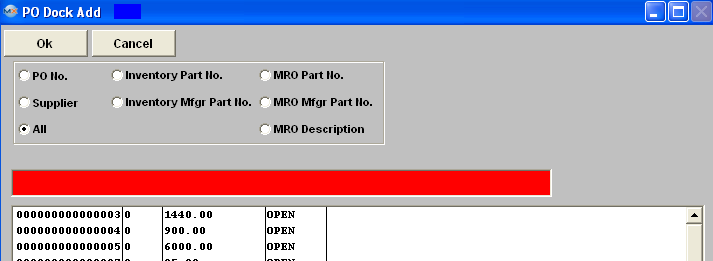 |
The purchase order selected will populate the Dock Receiving screen, as displayed:
Enter the Supplier’s Packing List Number into the red box. Fill in the Received Qty column. (The qty entered in this field will have to either be accepted or rejected when completing the PO Receiver, user will not be allowed to create a PO receiver for only a Partial of this qty).
Depress the Save changes action button.
If the "Shortage" button is RED that reminds the user that there are shortages for this part. Depress the "Shortage" button and a screen will be displayed listing the shortage's for this specific part.
User will receive the following warning if the qty received is larger than the PO balance.
Users must have special access in order to receive overages, there is a checkbox to allow overages within Security/User Rights for PO Receiving. If user does NOT have these rights, they will not be able to continue.
Note: The overage is applied to the entire PO order qty - it does not go down to the schedule level. Example: If you have an order qty of 100 and an allowed overage of 5% the system will allow you to receive in a total overage of 105. But if you have only scheduled a qty of 25 and go to recieve in qty of 30 the system will allow you to do so, because it has not met the order overage yet. Note: A negative qty will appear in the balance column on the PO when an overage has been received.
|
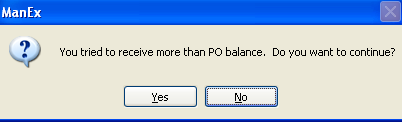 |
User will receive the following warning if one or more of the items on the receipt is before the PO due date and the early tolerance time allowed in the Purchase Setup screen.
Note: This warning will only display the item # of the first item found that the receipt is before the PO due date. It will not display other item #'s' that have early deliveries on the same PO Dock receiver. Depress OK to continue.
Note: Users must have special access in order to receive early shipments. There is a checkbox to allow eary shipments within Security/User Rights for PO Receiving. If user does NOT have these rights, they will NOT be able to continue.
|
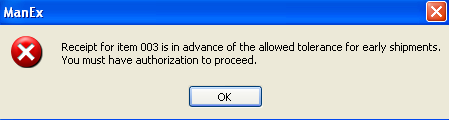 |
Users that have the special access to receive early shipments or users with Supervisor rights will receive this reminder message if the receipt is before the PO due date and the early tolerance time allowed the Purchase Setup screen.
|
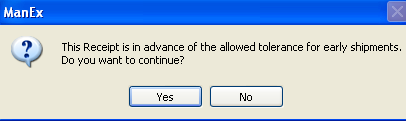 |
The Complete PO Dock Receiving Screen will look like this:
|
1.1.4.3. Editing a Dock Receiver |
Enter the SQLMANEX.EXE (within the ManEx root directory)
This action will then prompt the user for a password
|
 |
The following screen will be displayed, enter Inventory Management/Purchase Order Receiving & DMR/Purchase Order Dock Receiving
|
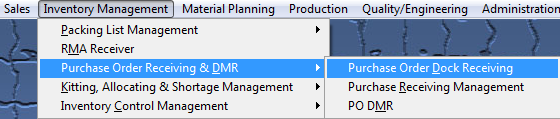 |
The Following screen will be displayed:
The user may edit the Dock Receiving record as long as a related PO Receiving has NOT been done.
- Find Dock Receiver.
- Depress the Edit action button.
- You’ll be prompted for your password.
- User may edit the supplier's Packing List Number or the quantity received. The system does allow you to receive more then the PO quantity/Overage. Note: Users must have special access in order to receive overages, there is a checkbox to allow overages within Security/User Rights for PO Receiving.
- Depress the Save changes action button.
If you try to receive more than the PO quantity, you’ll receive the following warning message: |
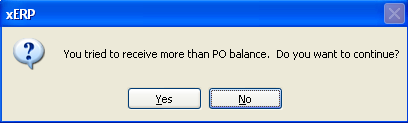 |
If you enter YES and depress the Save action button (and if you have exceeded the overage percentage from the Purchase Setup and\or PO line item) you will receive the following warning message.
Note: The overage is applied to the entire PO order qty - it does not go down to the schedule level. Example: If you have an order qty of 100 and an allowed overage of 5% the system will allow you to receive in a total overage of 105. But if you have only scheduled a qty of 25 and go to recieve in qty of 30 the system will allow you to do so, because it has not met the order overage yet.
|
|
|
1.1.5. Reports - PO Dock Receiving |
To obtain the AP
Aging Reports within the Web, select the WEB Print button from the ManEx action buttons at the top
of the screen. For further detail on How the Reports work within the Web refer
to Article #5477.
Note: In order to access the
Reports within the Web the Company Root URL must be setup within the System Appearance module and user must be linked to web within the System Security Module.

Select the Report Type: PO DOCK - A List of Reports will be displayed that are available on the Web
for PO DOCK
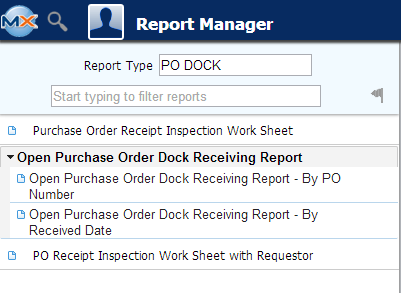
To obtain the PO Dock Receiving reports, select the Print button from the ManEx action buttons at the top of the screen.
The following reports screen
will display a list of reports that are available on the ManEx Desktop:
Highlight the desired report and then depress the OK button.
If you select the Purchase Order Receipt Inspection Work Sheet report, or Purchase Order Receipt Inspection Work Sheet with Requester report highlight that report. Depress the OK button. This screen appears:
Highlight the Purchase Order and depress the > button. If you want all of the Purchase Orders listed, depress the >> button.
Depress the OK button.
|
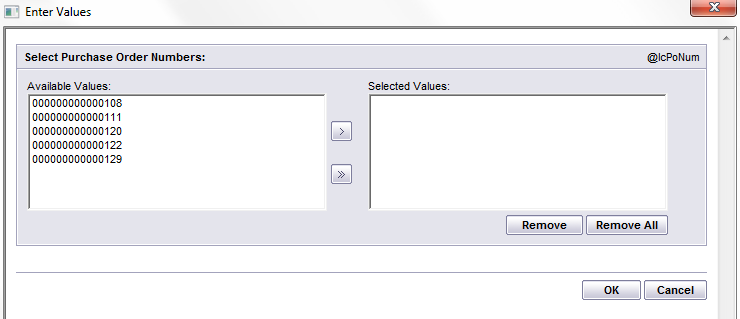
|
The following is printed:
If you select the Open PO Dock Receiving Report, the following additional window will display at the bottom of the screen:
Select detail either by PO Number or by Received Date.
Depress the OK button.
|
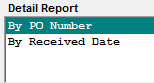 |
The following is printed:
|
1.2. Purchase & Receiving Management |
1.2.1. Prerequisties for Purchase & Receiving Mgmt | After activation, "Purchase Order & Dock Receiving" access for each user must be setup in the ManEx System Security module. Users with “Supervisor Rights” will automatically have access.
Dock Received Purchase Order
|
There must be a dock receiver for the purchase order. (If required in Purchase Setup). |
Return/Shortage Reasons |
Return/Shortage reasons must have been entered in System Setup - Return/Shortage Reasons Setup. |
|
1.2.2. Introduction for Purchase & Receiving Mgmt | Receiving is the next step after creating and submitting a Purchase Order.
In System setup/Purchase Setup it gives the user the option to use PO Dock Receiving. If this box is checked, the purchases are received at the dock requiring the user to complete a PO Dock Receiving record, listing the supplier’s packing list number and the quantities per that packing list. An inspection report is printed. The purchases are inspected and counted. (If this box is left unchecked the user can skip the PO Dock Receiving step and go directly to the Purchase Order Receiving & Inspection record.
The user then is required to complete a PO Receiving & Inspection record. This module has a provision for rejected purchases.
For rejected materials, ManEx provides for a PO DMR (Discrepant Materials Receipt) module. The Discrepant Material Receiver is used to receive material which does not meet the specifications for the purchased part or purchase order. This module allows for review by the Materials Review Board. Then, if not acceptable, the material may be returned to the supplier. The user may reject in the Purchase & Receiving Management module OR may return an item From Inventory. If an item is returned From Inventory, and the PO has been reconciled, a Debit Memo forwards into Accounting along with the appropriate journal entry.
Once the data entry is completed, the purchase receivers are forwarded to the Accounting module for PO Receipt Reconciliation. (The attached Print Screens below <<PO_Recv_Resulting_Trans.docx>> displays the resulting transactions that affect the Un-reconciled Receipt accounts after accepting items into stock through PO Receiving).
Within the PO Receiving module there is a "Shortage List and Issue" button. This will allow users to issue parts from receiving directly to the Kit Shortages. This screen will display all shortages for that part and AVL. There is an Approved Check box for reference to the Work Order Shortage List. This will be checked if the AVL that you are receiving is an approved AVL for that shortage. This will give the users the needed information on screen to make the decision to use or not use a non-approved AVL to fulfill a shortage.
|
1.2.3. Fields & Definitions for Purchase & Receiving Mgmt | 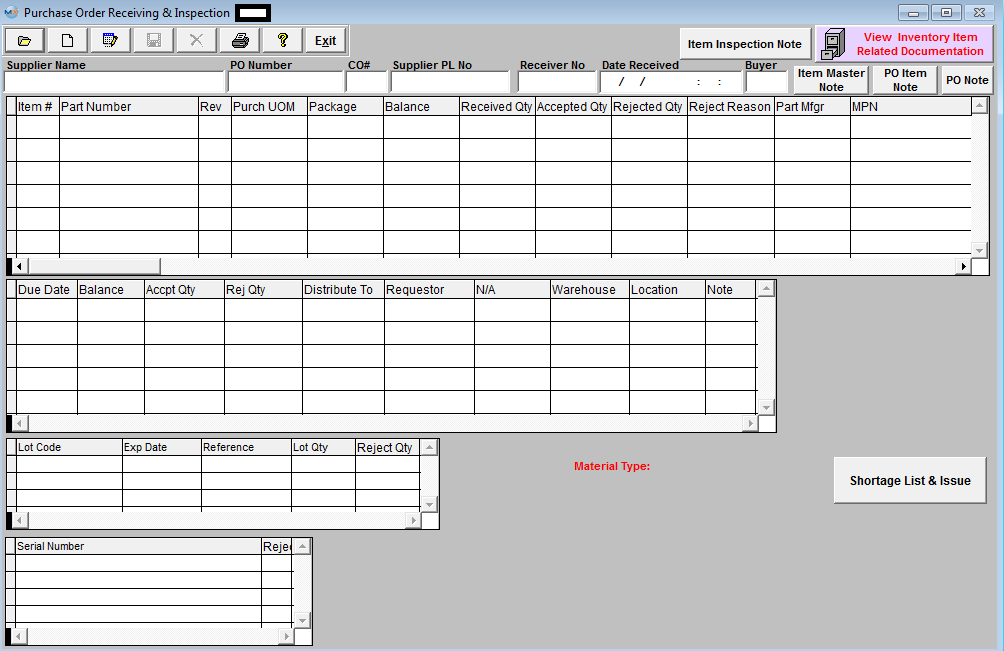
Supplier Name |
The supplier or vendor with whom the order was placed. |
P O Number |
The Purchase Order number of the order. |
CO Number |
The Change Order revision status of the order placed. |
Supplier PL No |
The number of the supplier’s Packing List. |
Receiver No |
The Purchase Order Dock Receiving number. |
Date Received |
The date the Purchase Order Receiving was completed. |
Buyer |
The initials of the buyer for the order. |
Item |
The Purchase Order Item Number. |
Part Number |
The number the user has assigned to the part. |
Rev |
The revision number assigned to the part. |
Purch UOM |
The Purchased unit of measure. (May be different than stocking unit of measure). |
Package |
The package type assigned to part in Inventory Control module. |
Balance |
The un-received quantity. |
Received Qty |
The quantity received in Purchase Order Dock Receiving. See Article #1240 for more detail on why the system will not allow user to enter in a fraction of a number, and an alternative. Note: Users must have special access in order to receive overages, There is a checkbox to allow overages within Security/User Rights for PO Receiving. Note: The overage is applied to the entire PO order qty - it does not go down to the schedule level. Example: If you have an order qty of 100 and an allowed overage of 5% the system will allow you to receive in a total overage of 105. But if you have only scheduled a qty of 25 and go to recieve in qty of 30 the system will allow you to do so, because it has not met the order overage yet. |
Accept Qty |
The quantity accepted within Purchase Order Receiving. |
Reject Qty |
The quantity rejected. |
Reject Reason |
The rejection reason Pull down list, (which is created within the System Setup Return/Shortage Reasons), is to allow the users to be able to select the Reject Reason code rather then writing notes and to be more consistent. |
Part Mfgr |
The manufacturer for the part. |
MPN |
The manufacturer part number. |
Description |
The description pertaining to the part number. |
For the Highlighted Line Item:
Due Date |
The date the item was due to the user’s dock. |
Balance |
The un-received balance of the order. |
Accept Qty |
The quantity accepted in Purchase Order Receiving. |
Reject Qty |
The quantity rejected which will be placed in the Material Review Board warehouse. |
Distribute To |
This is classification of the distribution of the item when received, either to regular Inventory Receiving or to Allocate to a specific Work Order or Project. |
Requestor |
On MRO and Services Purchase Orders, the name of the requestor is indicated. |
N/A |
For future use. |
WO Number |
The number of the Work Order for which the item was purchased. |
Warehouse |
The name of the warehouse where the accepted quantity will be placed. |
Location |
The specific location within the warehouse. |
Note |
Schedule notes pertaining to that specific item and scheduled date. |
Material Type |
The material type listed is at the AVL level |
Inspection Required |
This will be visible ONLY when selected in the Inventory module. Check box when complete. If box is NOT checked user will NOT be able to save record. |
Certificate Required |
This will be visible ONLY when selected in the Inventory and/or PO module. Check box when complete. If box is NOT checked user will NOT be able to save. |
First Article Required |
This will be visible ONLY when selected in the Inventory module. Check box when complete. If box is NOT checked user will NOT be able to save record. |
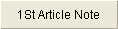 |
Enter any special notes pertaining to the 1st article. |
Lot Code |
Lot Code number assigned to part. |
Exp. Date |
Expiration date of Lot Code. |
Reference |
User assigned number or code for reference |
Lot Qty |
Qty of parts lot includes. |
Reject Qty |
Qty of parts rejected out of lot. |
Serial Number |
Serial numbers assigned to parts. |
Reject |
Check box if that serial number is being rejected. |
Insp Exception Note |
This information is displayed as reference information for processing the Receipts through the system. |
Insp Excep Doc. |
This information is displayed as reference information for processing the Receipts through the system. |
Directive Buttons:
|
The Item Inspection Note screen will be editable in the Add/Edit mode within the PO Receiving module (not editable when in view mode). This button will turn Red when information has been entered. The information added in the PO Receiving module will also be viewable in the Purchase Order module.
|
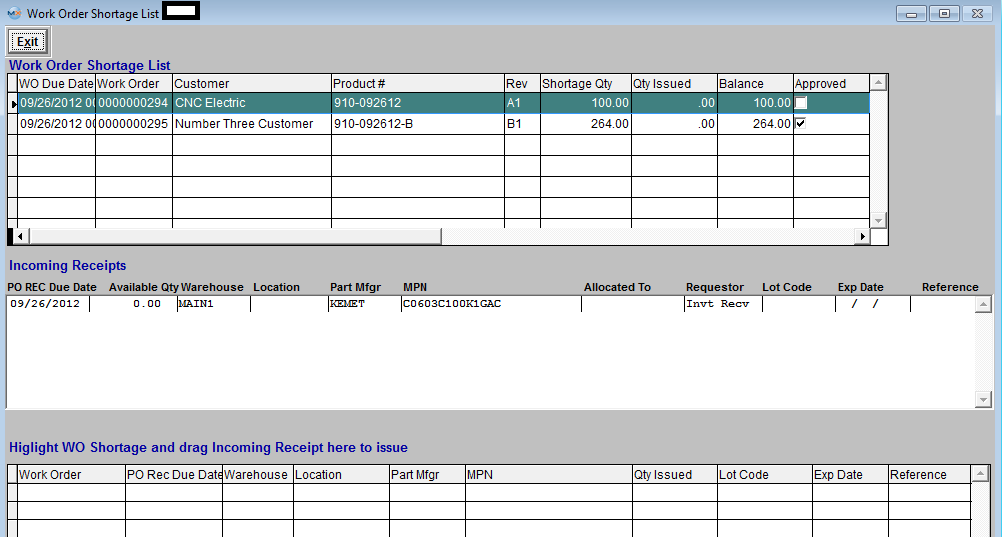
The system shows all the shortages for the part that is received, if:
- the WO is not closed or cancelled
- the WO balance is more than 0
- the kit line "Ignore Kit" flag is not on
- the Kit status is "Released"
It is up to the user to decide which receipt has to be applied to which shortage.
Work Order Shortage List field definitions:
Work Order Due Date |
The date the Work Order was due to be completed and ready to ship. |
Work Order Number |
The number of the Work Order. |
Customer |
The name of the customer listed on the Work Order. |
Product Number |
The Product number listed on the Work Order. |
Revision |
The revision listed on the Work Order. |
Shortage Quantity |
The amount of the Work Order shortage. |
Qty Issued
|
The quantity issued to the Work Order shortage. System does not allow you to issue quantities greater than the shortage quantity. For more detail see Article #2479.
|
Balance
|
The balance of the shortage after issuing parts to WO.
|
Approved
|
This will be checked if the AVL that you are receiving is an approved AVL for that shortage. This will give the users the needed information on screen to make the decision to use or not use a non-approved AVL to fulfill a shortage.
|
Incoming Receipts field definitions:
PO REC Due Date |
The date the Purchase Order Receiving was completed. |
Available Qty |
The quantity accepted within Purchase Order Receiving. |
Warehouse |
The name of the warehouse where the accepted quantity will be placed. |
Location |
The specific location within the warehouse. |
Part Mfgr |
The manufacturer for the part. |
MPN |
The manufacturer part number. |
Allocated To |
If the parts have been allocated to a WO or project when PO was created. |
Requestor |
On MRO and Services Purchase Orders, the name of the requestor is indicated. |
Lot Code |
Lot Code number assigned to part. |
Exp Date |
Expiration date of Lot Code. |
Reference |
User assigned number or code for reference |
Highlight WO Shortage and drag Incoming Receipt here to issue field defintions:
Work Order |
The number of the Work Order. |
PO Rec Due Date |
The date the Purchase Order Receiving was completed. |
Warehouse |
The name of the warehouse where the accepted quantity will be placed. |
Location |
The specific location within the warehouse. |
Part Mfgr |
The manufacturer for the part. |
MPN |
The manufacturer part number. |
Qty Issued |
The quantity issued to Work Order Shortage |
Lot Code |
Lot Code number assigned to part. |
Exp Date |
Expiration date of Lot Code. |
Reference |
User assigned number or code for reference |
|
1.2.4. How To ..... for Purchase & Receiving Mgmt |
1.2.4.1. Find a Purchase Order in Receiving Inspection |
Enter the SQLMANEX.EXE (within the ManEx root directory)
This action will then prompt the user for a password |
 |
The following screen will be displayed, enter Inventory Management/Purchase Order Receiving & DMR/Purchase & Receiving Management module
|
|
The following screen will be displayed:
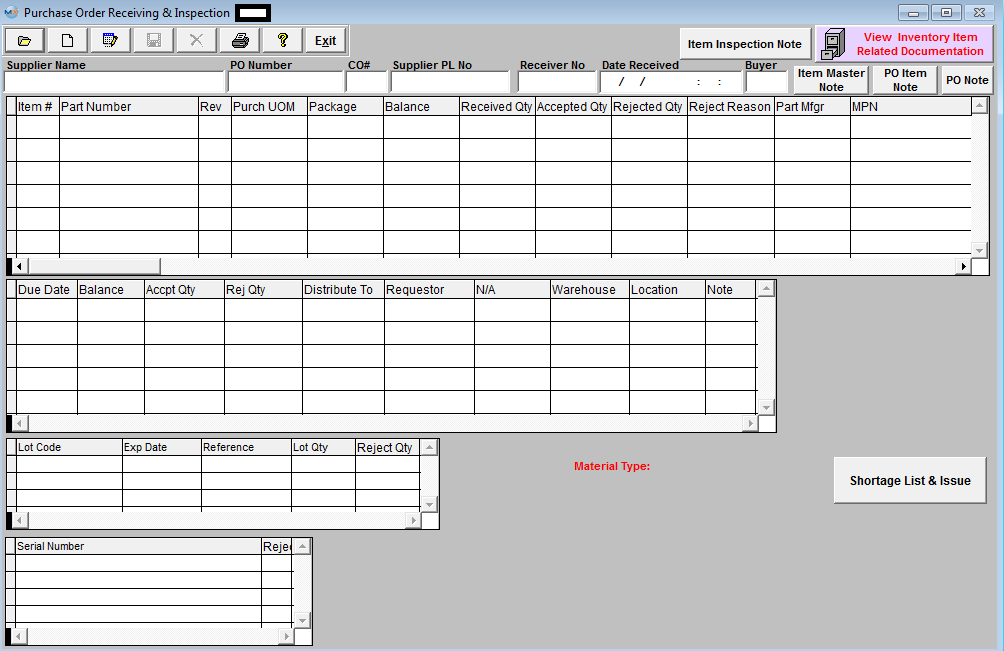
1. To Find an existing PO Dock Receivier, depress the Find action button at the top of the main screen and the following selection screen will be displayed.
Select the desired Filter: by selecting the appropriate radio button - Open Receivers, Closed Receivers, or All.
Select the desired Find: by selecting the appropriate radio button - PO No., Supplier, Receiver No., Inventory Part No., Inventory Mfgr Part No., All, MRO Part No., MRO Mfgr Part No., or MRO Description.
Enter the information into the red box, depress the Enter key and the information will populate the screen. If you do not know the exact number, Customer, etc you may enter in a partial number, letter, etc, then once you depress the enter key the system will pull up the matching record onto the screen or a list of all PO Receiving records that contain the partial number, letter, etc. entered, to select from.
The user may exit the selection screen without a selection by selecting the Cancel button.
|
|
2. If the user selects to find by ALL, the screen displayed will be shown listing all the PO Number's in numerical order, along with the Supplier name, and Receiver Number.
The user has the option to view the PO Receiving Recordr by either entering the Purchase Order number into the red box, or scrolling down the list, highlighting the desired record and double click on it.
|
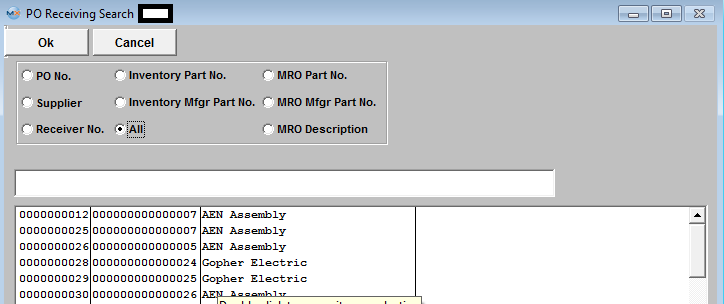 |
3. The found information will populate the screen, as follows:
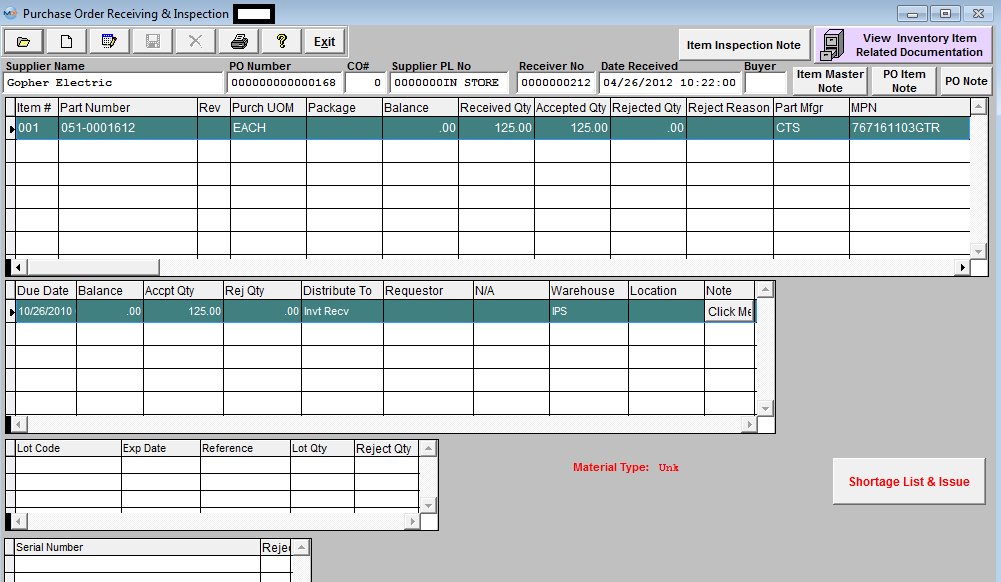
|
1.2.4.2. Add a PO Receiving Inspection Record |
Enter the SQLMANEX.EXE (within the ManEx root directory)
This action will then prompt the user for a password
|
 |
The following screen will be displayed, enter Inventory Management, Purchase Order Receiving & DMR, Purchase Receiving Management
|
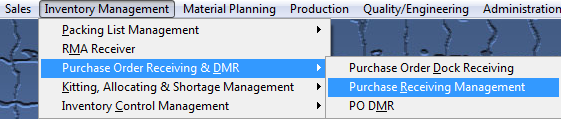 |
The following screen will be displayed:
If system is setup for Dock Receiving a PO Dock receiver MUST be created before the PO will be available.
- Add a record.
- The user will be prompted for the password.
- Find a Purchase Order
- If Supplier Packing List Number is NOT already entered, enter it now.
- Select the part to receive.
- Enter the quantity accepted and/or rejected and reject reasons. (When using the PO Dock, user has to either accept the entire Dock qty or reject the balance. User can NOT accept only a partial PO Dock qty). Note: Users must have special access in order to receive overages, receive early shipments,and/or receive banned MPNs. There is a checkbox to allow user to receive overages, receive early shipments, and/or receive banned MPSs, within Security/User Rights for PO Receiving.
User will receive the following warning if the number of parts received is higher than the qty ordered.
The overage is applied to the entire PO order qty - it does NOT go down to the schedule level. Example: If you have an order qty of 100 and an allowed overage of 5% the system will allow you to receive in a total overage of 105. But if you have only scheduled a qty of 25 and go to receive in qty of 30 the system will allow you to do so, because it has not met the order overage yet. Note: A negative qty will appear in the balance column on the PO when an overage has been received.
Note: User must have special access in order to receive overages. There is a checkbox to allow overages within Security/User Rights for PO Receiving. If user does NOT have these rights, they will NOT be able to continue.
|
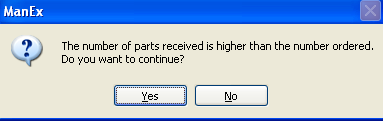 |
User will receive the following warning if the receipt is before the PO due date and the early tolerance time allowed in the Purchase Setup screen.
Note: Users must have special access in order to receive early shipments. There is a checkbox to allow early shipments within Security/User Rights for PO Receiving. If user does NOT have these rights, they will NOT be able to continue.
|
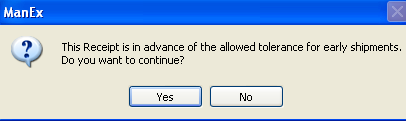 |
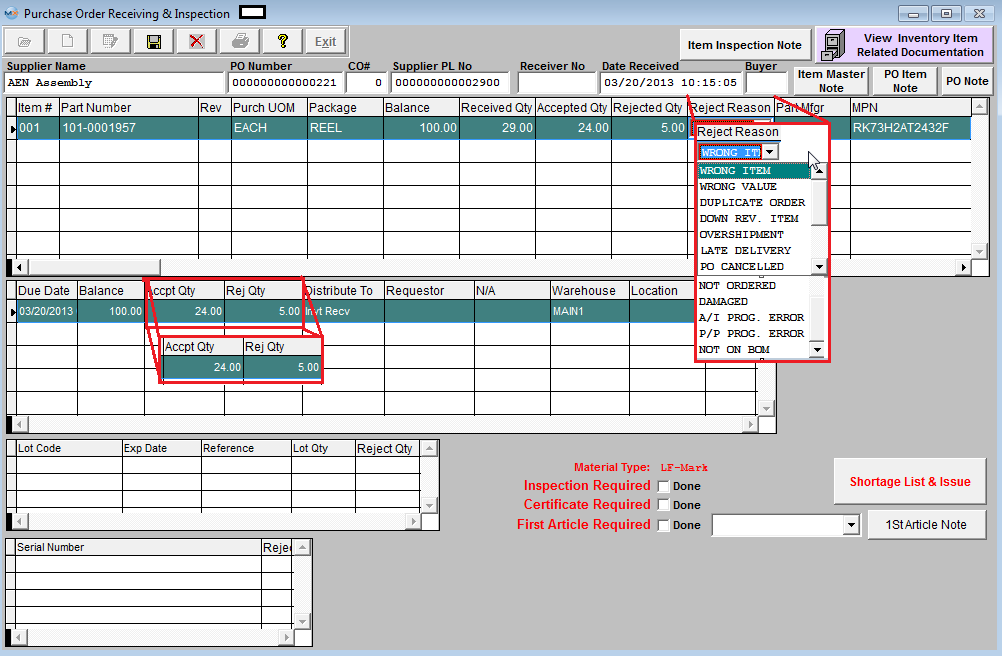
-
If the “Allow auto creating location at receiving” box is checked in Inventory Control, AVL level & Warehouse Setup, this will allow the user to add or edit the location at time of receipt. User may also select an existing warehouse at receiving instead of having to create one before receiving. For further information on the "Allow auto creating location at receiving" see Inventory Control & Warehouse setup. If the Inspection Required, Certificate Required, and/or the First Article Required is setup in the Inventory Control Management module, these boxes will be displayed in Red and the "DONE" boxes MUST be checked to continue the receiving process.
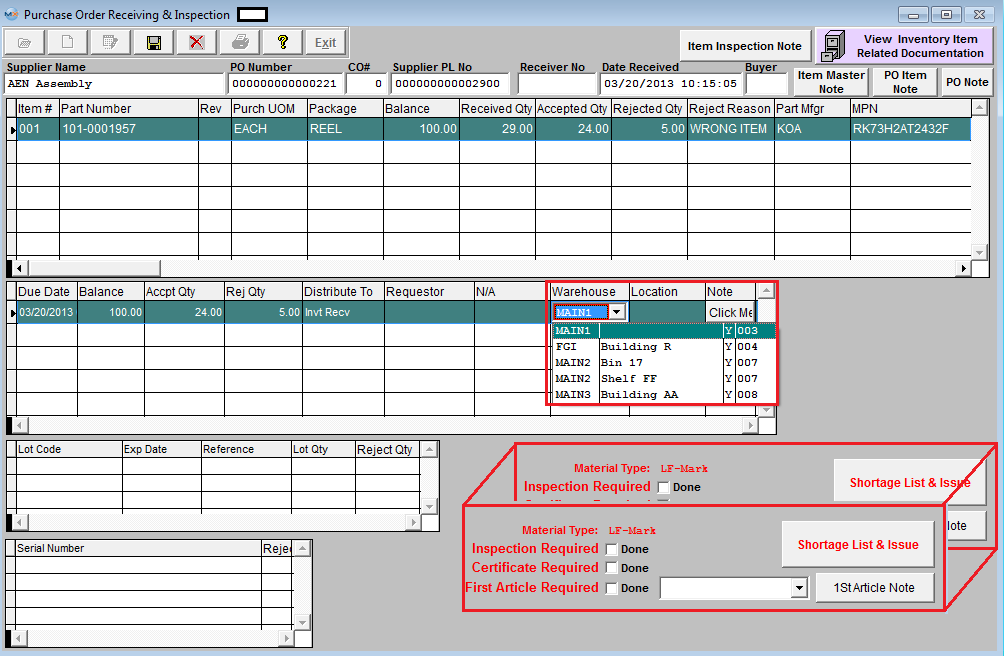
-
In the system setup - Purchase Setup user can choose to allow receiver to change AVL at the receipt. The pull down will display all the Mfgr and Mfgr PN's listed in the AVL screen in the ICM module.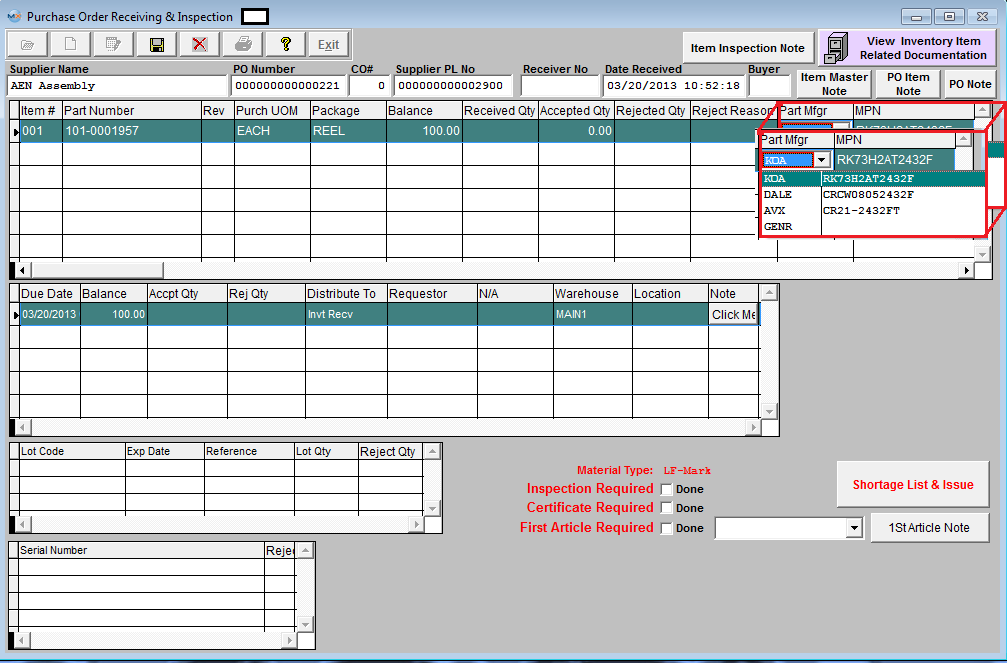
-
Enter Serial Number and/or Lot Information if required.
-
Issue parts directly to Work Order Shortages.
-
Save the record.
NOTE: If there is a Item Master Note, Purchase Order Item Note, or a Purchase Order Note, it will be RED. To view the note, depress the button of interest. When finished viewing Depress the OK button at the bottom of the screen. The user will have the ability to edit the Item Master Notes if they have “Edit” rights to the Inventory Module, which can be setup in the Security Module.
|
1.2.4.2.1. Entering Serial Number and/or Lot Information | Introduction
The users can receive components that require Lot Code Only, Serial Number Only, or both Serial Number and Lot Code, following the instructions listed below. A part that requires a Lot Coded is setup in the Inventory Part Type set-up module. A part that requires Serial numbers is set-up in Inventory Control Module.
- Fill in accepted item quanitity as instructed in the Add a PO Receiving Inspection Record.
- Depress the Add button next to the Lot Code section.
-
Type in the Lot Code. The expiration date, reference date and quantity will automatically update, (if the part class/type setup is set to auto update expiration date and reference for the lot code). In order for a Lot Code to be unique, the system looks at four fields for comparison. They are Lot Code, Reference, and PO Number. So while a batch may have the same Lot Code as another batch, if it arrives in a different PO, the it will be classified as a different lot. The expiration date is optional and is not required when creating a new lot.
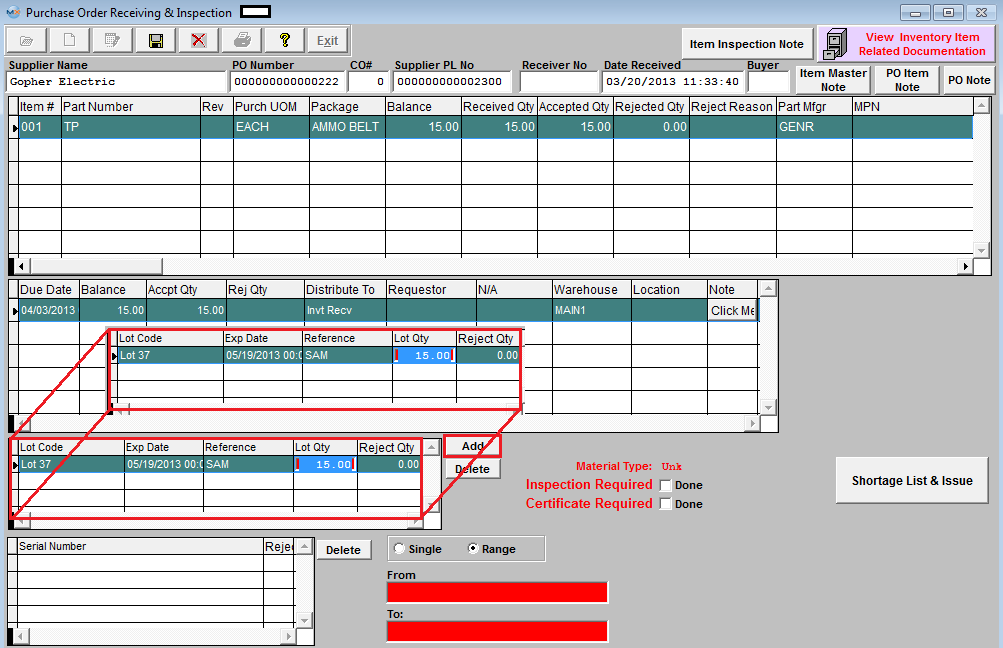
- Serial numbers will have to be assigned only if a part has the serial number box checked in the inventory module.
- Select either single or range.
- Enter the serial number in the red box and depress enter.
- The serial numbers will automatically update. (Serial numbers may or may not have lot codes).
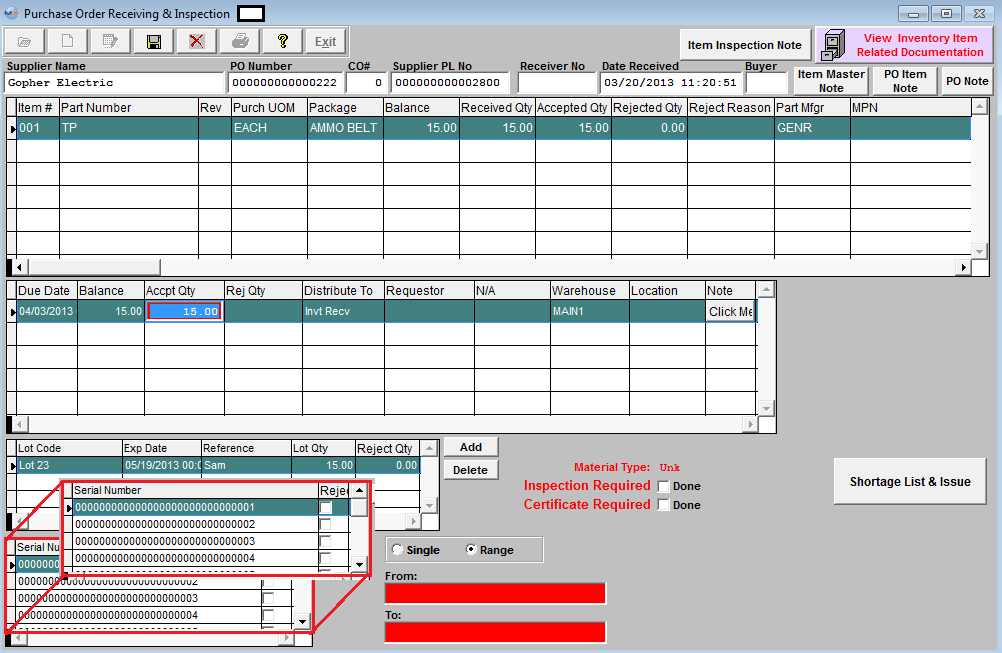
|
1.2.4.2.2. Issue Directly to Work Order Shortages | Highlight the line item of interest on the PO Receiving and Inspection screen.
Depress the Work Order Shortage List and Issue button.
Highlight the work order shortage at top of screen.
Drag Available Qty located in the middle of your screen under Incoming Receipt.
Drop it in the quantity issued at the bottom of your screen as displayed below. System will allow users to pick to each of the individual shortages within the same Work Order and/or different Work Orders.
The Approved box will be checked if the AVL that you are receiving is an approved AVL for that shortage. This will give the users the needed information on screen to make the decision to use or not use a non-approved AVL to fulfill a shortage.
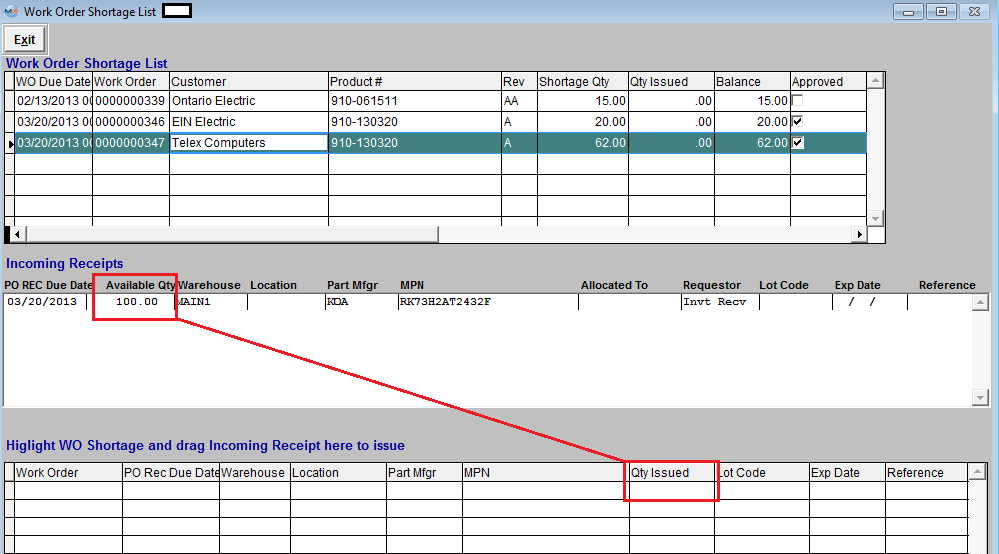
System will not allow user to issue quantities greater than the shortage quantity. See Article #2479 for further detail.
The following messge will be displayed if user issues a quantity greater than the shortage quantity.

NOTE: If a user has the Work Order Checklist feature active and tries to use the PO Receiving shortage and issues feature within the PO Receiving, it will not recognize the shortages until the kit has been flagged as "Kit Complete". It is designed this way because the user will not know if the parts are short until the kit is completed.
You may have parts in the inventory and have not pulled them to the kit yet. If you allow seeing the shortage (which may not be a shortage because parts are not pulled yet) from the PO receiving, the receiver may be trained to automatically issue to the shortages first, but it may not be a shortage because parts have not been pulled from inventory, so how would they know if it is a real shortage or just not pulled from inventory yet.
|
1.2.4.3. Rejecting Quantity in PO Receiving & Inspection |
- Highlight the PO item number located in the middle section of the PO Receiving and Inspection screen.
- Type in the accepted quantity (if any).
- Place the cursor in the next box (rej qty) and type in the rejected quantity.
- Select a reject reason from the pull down in the top section of the screen.
- If lot coded type in the accepted qty and rejected qty in the lot code screen.
- If serial numbers are required check the serial numbers that have been rejected.
- Continue this process until all items are either accepted or rejected.
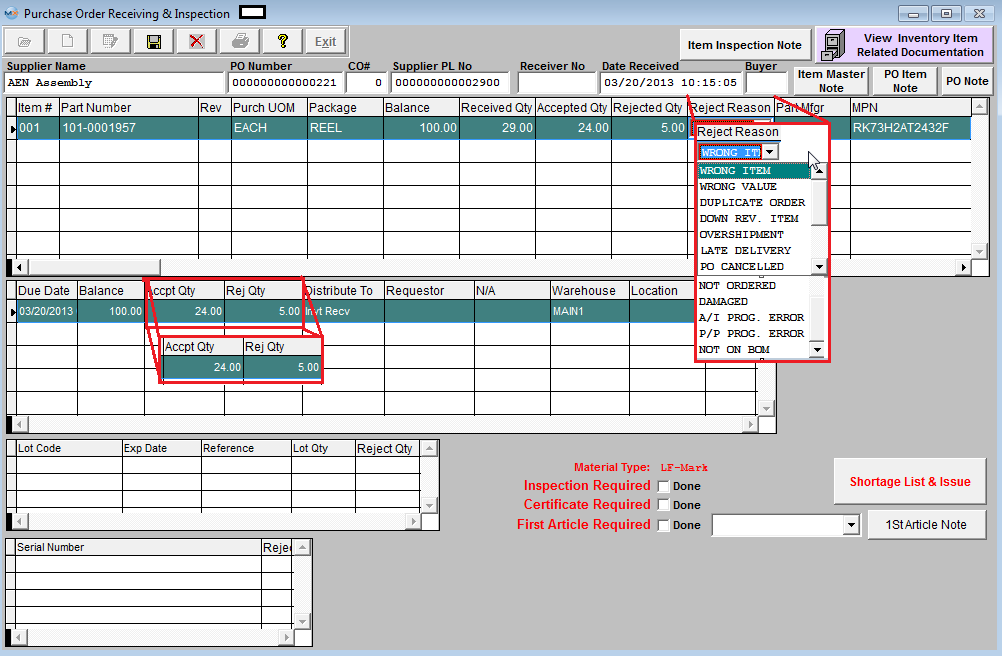
- Depress the Save button.
- If all items on the Purchase Order have been received it will be marked "CLOSED".
|
1.2.4.3.1. Rejecting Items if Accounting has Processed the Invoice |
- If the Purchase Order has been processed through accounting:
- Transfer the discrepant material into the MRB (materials review board) warehouse via Inventory Handling.
- Enter the PO DMR module (discrepant material return).
- Add from Inventory. (This is called an INVENTORY DMR).
- If the user has already pulled the kit associated with the part to be returned to the supplier.
- Enter the Kitting module.
- Find the work order.
- Depress the Utility tab and depress the De Kit button. This process will return the part into the inventory warehouse. (Please refer to the Kitting & Shortage Mgmt module).
|
1.2.4.3.2. Rejecting Items if Accounting hasn't Processed the Invoice | Introduction
After the user has accepted all of the items on a Closed Purchase Order and then subsequently it’s discovered that the material received is discrepant, do the following if Accounting hasn’t already processed the Supplier’s Invoice for payment:
-
Enter the Purchase and Receiving Managment Module.
-
Find the closed PO, using the Find a Purchase Order.
-
-
Type in your password.
-
Highlight the discrepant Part Number Line Item in the top section of the screen.
-
In the middle section of the screen, enter the revised accepted quantity, and the rejected quantity.
-
Go back up to the top section of the screen and select a reject reason.
-
If there is Lot Code Tracking involved, also adjust the Lot accepted quantity and rejected quantity, and check the serial numbers that have been rejected.
-
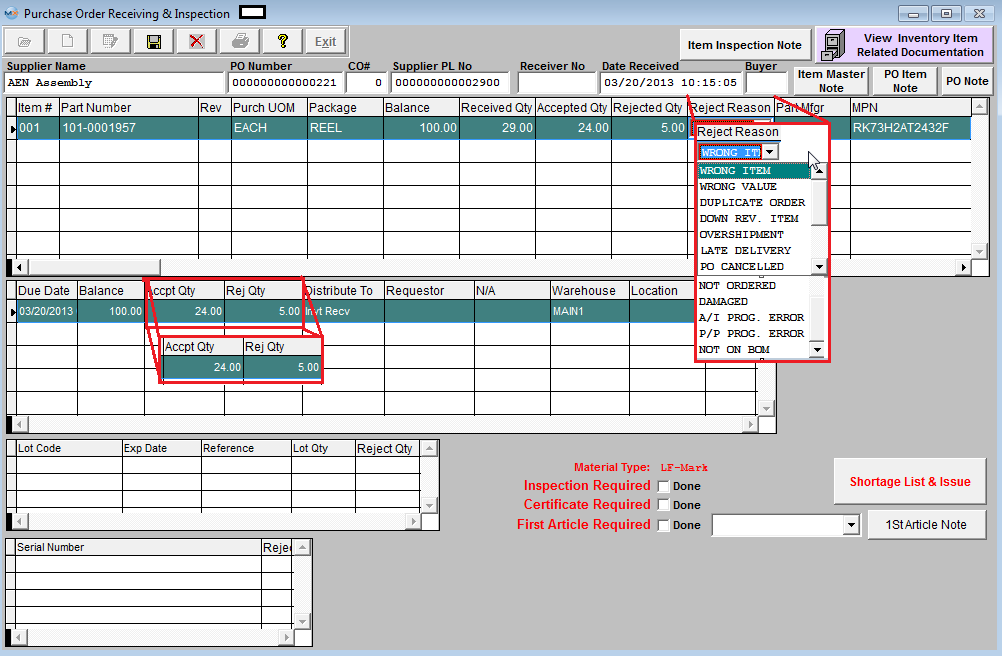
|
1.2.5. Reports - Purchase & Receiving Mgmt |
To obtain the AP
Aging Reports within the Web, select the WEB Print button from the ManEx action buttons at the top
of the screen. For further detail on How the Reports work within the Web refer
to Article #5477.
Note: In order to access the
Reports within the Web the Company Root URL must be setup within the System Appearance module and user must be linked to web within the System Security Module.

Select the Report Type: PO RECEIVING - A List of Reports will be displayed that are available on the Web
for PO RECEIVING
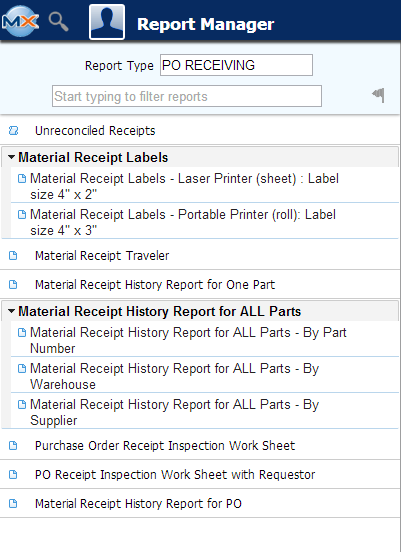
To obtain the PO Receiving reports, select the Print button from the ManEx action buttons at the top of the screen.

The following reports screen
will display a list of reports that are available on the ManEx Desktop:
Highlight the desired report and then depress the OK button.
MATERIAL RECEIPT LABELS - Prints labels for receipt by part no, desc, whse locn, qty
For the PO Receiving Material Receipt Labels, you can choose between the Avery label #5163 (laser Sheet 4x2) or the Zebra Printer
|
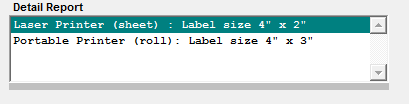 |
Enter in a Purchase Order number.
The information will automatically fill in. All labels will be displayed on screen, if users desire they can then determine which labels they want and using the printing dialog box select the label to print and/or the number of labels.
Note: The Mfgr and Mfgr PN info is being pulled from the PO Module and not the Receiving Module.
|
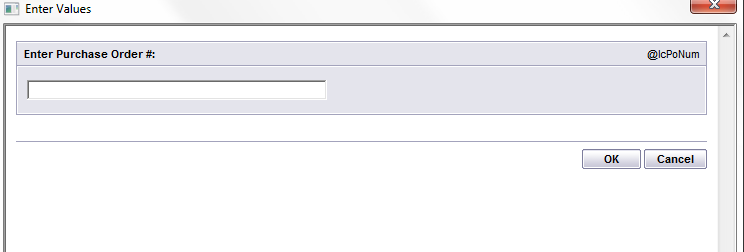 |
The following is printed (This example is Printing to the Laser Printer (Sheet): Label size 4" x 2")
MATERIAL RECEIPT TRAVELER REPORT - This report will display requestor, par no, PO #, accept qty, receiver #
For the Material Receipt Traveler report, highlight that report.
Depress the OK button and the following report will be displayed.
Note: This report will now display ALL receipt records that have been created and not yet printed on this report. Records will only display once, as soon as you run this report the field IS_PRINTED will be flagged within the tables and the records will no longer display on this report again.
|
|
MATERIAL RECEIPT HISTORY FOR ONE PART REPORT - This report will display PO#, Supplier, requestor, date, recd qty, rej qty
For the Material Receipt History for One Part report, highlight that report.
Depress the OK button
Enter the part number and revison (if applicable) within the Single Quotes.
Enter the desired date range.
Select 'Yes' or 'No' to Suppress leading "0" when printing serial numbers.
Depress the OK button.
|
|
The following is printed:
MATERIAL RECEIPT HISTORY REPORT FOR ALL PARTS - This report will display PO#, supplier, requestor, date, recd qty, location, mfg pn
For the Material Receipt History Report for ALL Parts, highlight that report and make the appropriate selection at the bottom of the screen, By Part Number, By Warehouse or By Supplier.
Depress the OK button.
|
|
The following screen will be displayed.
Enter the desired date range.
Select 'Yes' or 'No' to Suppress leading "0" when printing serial numbers.
The Project/Work Order Allocation information will be displayed on the report.
NOTE: The report has to pull the allocation information from the Purchase Order Item Schedule, if the item schedule allocation is modified after receipts have already been made against this item, the report will also change to display what is currently assigned for allocation, not what they were received into the system as.
If a Serial Number has been rejected "Rejected" will be displayed on the report to the right of the serial number. If a Lot Coded part has a reject qty it will display the Lot Code information on the receipt that had the items rejected.
|
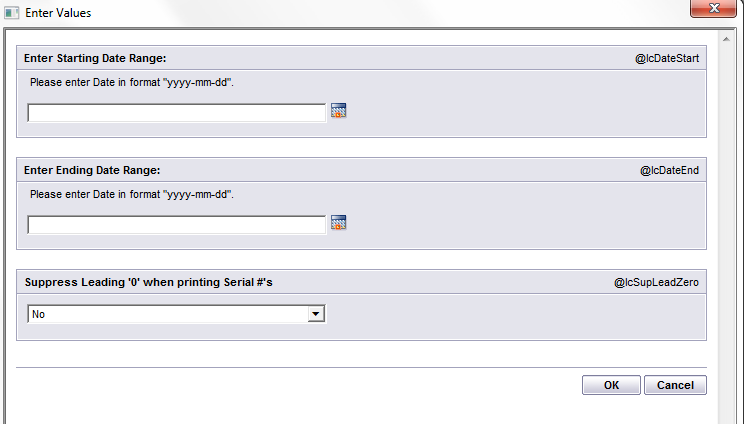 |
The following is printed:
PURCHASE ORDER RECEIPT INSPECTION WORKSHEET - Purchase Order Receipt Inspection Work Sheet for the items had been received in PO DOCK module
PURCHASE ORDER RECEIPT INSPECTION WORKSHEET with REQUESTER - Purchase Order Receipt Inspection Work Sheet for the items had been received in PO DOCK module with Requester Information
For the Purchase Order Receipt Inspection Work Sheet, or Purchase Order Receipt Inspection Work Sheet with Requester, highlight that report.
Depress the OK button.
Select a Purchase Order from the list by highlighting it then depress the > button. If you want all of the Purchase Orders listed, depress the >> button.
Depress the OK button.
|
|
The following is printed:
Material Receipt History Report for PO - This report displays the Item #, type, date, qty rec'd,. price, total $
For the Material Receipt History Report for PO, highlight that report.
Enter a Purchase Order number.
Enter a Date Range.
Enter 'Yes' or 'No' to Suppress leading "0" when printing serial numbers.
The Project/Work Order Allocation information will be displayed on the report. NOTE: The report has to pull the allocation information from the Purchase Order Item Schedule, if the item schedule allocation is modified after receipts have already been made against this item, the report will also change to display what is currently assigned for allocation, not what they were received into the system as.
If a Serial Number has been rejected "Rejected" will be displayed on the report to the right of the serial number. If a Lot Coded part has a reject qty it will display the Lot Code information on the receipt that had the items rejected.
|
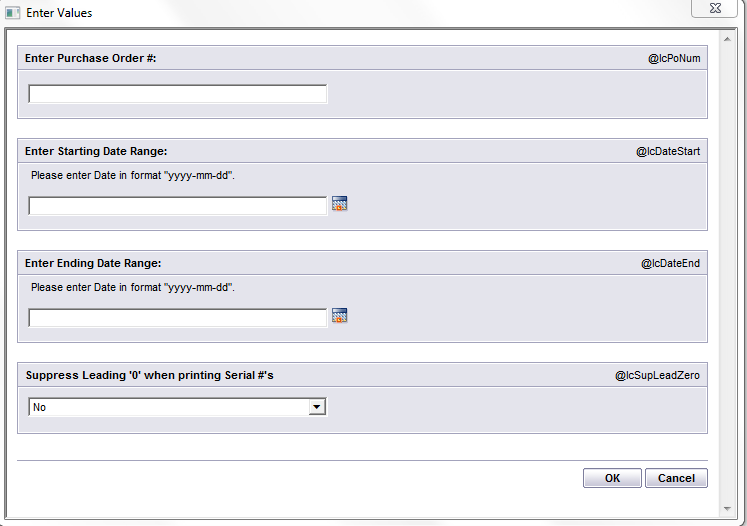 |
The following will print:
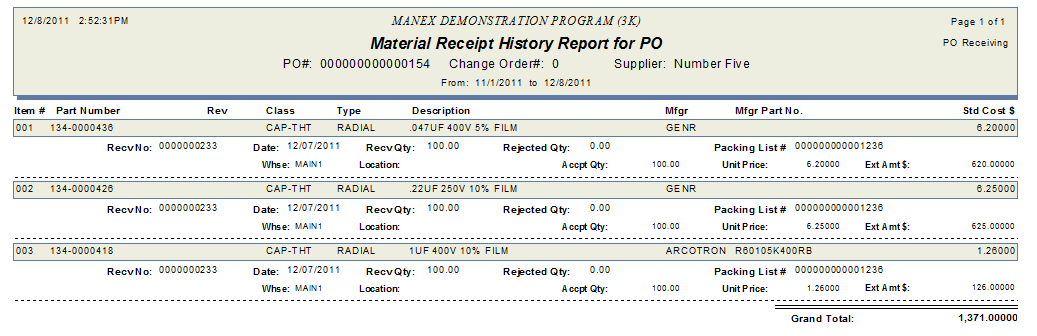
|
1.2.6. FAQs - Purchase & Receiving Mgmt | Facts and Questions for the PO Receiving & DMR Module |
1.3.1. Prerequistes for PO DMR | Prerequisites for PO Inspection/Acceptance Received with Rejected Quantities:
After activation, "Purchase Order Management" access for each user must be setup in the ManEx System Security module. Users with “Supervisor Rights” will automatically have access.
Prerequisites for Rejects from Inventory:
MRB (materials review board) Warehouse |
A MRB (materials review board) Warehouse must be set up in Warehouse Setup.
|
Inventory transferred to MRB (materials review board) whse |
Within Inventory Handling the discrepant quantity must have been transferred to MRB (materials review board) warehouse.
|
|
1.3.2. Introduction for PO DMR | Discrepant Material Return is used to return material which is different than what was ordered, received late, over shipment, damaged, etc.
There are two ways to return discrepant materials.
1. The discrepancy is discovered in PO Inspection/Acceptance Receiving and rejected there.
2. The discrepancy is discovered after the Inventory has been placed into stock. This module allows for review by the Materials Review Board. Then, if not acceptable, the material may be returned to the supplier. Once the DMR (discrepant material return) is created, information regarding the return is forwarded into Accounting where a Debit Memo and the accompanying accounting journal entry is created.
Once the Discrepant Material is added, the user may print out a DMR (discrepant material return) Packing List.
In Defect Code Entry we allow users to move product into FGI, when a part is transferred to FGI, the program will compare the total cost of components with the "material cost" of the assembly, then create the configuration variance. In addition to that, the system will create additional 4 records for "Labor", "Overhead", "Other Costs" and "User Defined" costs.
|
1.3.3. Fields & Definitions for PO DMR |
1.3.3.1. Return Items Tab | 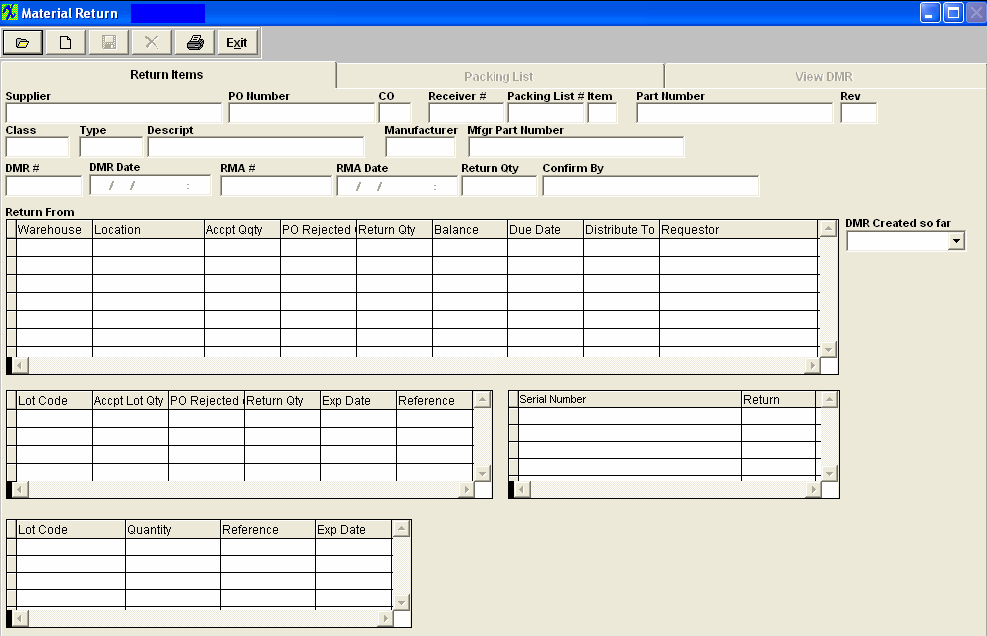
Fields & Definitions
Supplier |
The name of the supplier |
PO Number |
The number of the Purchase Order. |
CO |
The Change Order pertaining to the Purchase Order |
Receiver # |
The number of the Purchase Order Receiver |
Packing List # |
The number the supplier assigned to the Packing list |
Item |
The number of the line item per the Purchase Order. |
Part Number |
The user assigned number for the part being returned |
Rev |
The revision of the part number, if applicable. |
Class |
The classification of the part number returned. |
Type |
The type within the classification. |
Description |
The description of the part number |
Manufacturer |
The name of the part manufacturer |
Mfgr part Number |
The number assigned to the part by the manufacturer |
DMR # |
The number assigned to the DMR. |
DMR Date |
This is the date the DMR was created. |
RMA # |
The number the Supplier provided for the Return Material Authorization. |
RMA Date |
The date of the Supplier’s Return Material Authorization |
Return Quantity |
The number of units returned to the supplier. See Article #1240 for more detail on why the system will not allow user to enter in a fraction of a number, and an alternative. |
DMR Confirm By |
The name of the user who authorized the DMR. |
DMR Created so far |
Previous DMR's Created |
Return Items tab field definitions
Warehouse
|
Part Number Original Warehouse
|
Location
|
Part Number Original Location
|
Accpt Qty
|
Qty after returns processed
|
PO Rejected
|
PO number that qty was rejected against
|
Return Qty
|
The quantity of material returned
|
Balance
|
The quantity balance
|
Due Date
|
The date to expect the replacements
|
Distribute to
|
A special person or department to deliver the parts to
|
Requestor
|
A person or department requesting the DMR
|
Lot Code |
The lot code as assigned in PO Receiving module. |
Accpt Lot Qty |
The total quantity of the lot |
PO Rejected |
PO number that qty was rejected against
|
Returned Qty |
The quantity of material returned
|
Exp Date |
The expiration date assigned to the lot |
Reference |
The reference number assigned to the lot |
Lot Code |
The lot code as assigned in PO Receiving module. |
Quantity |
The balance left after all returns. |
Reference |
The reference number assigned to the lot |
Exp Date |
The expiration date assigned to the lot |
Serial Number |
The serial numbers being returned |
Return |
The quantity of material being returned |
|
1.3.3.2. Packing List Tab | 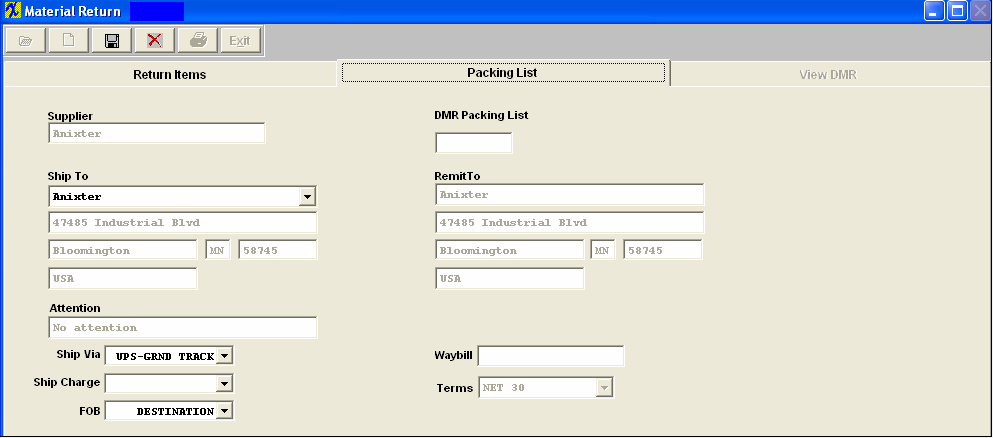
Field & Definitions
Supplier |
The name of the supplier |
DMR Packing List |
The Packing List number the user has assigned to the material return. |
Ship to |
The address where the return will be shipped. |
Remit To |
The address for the receipt of the Debit Memo, if applicable. |
Attention |
The supplier representative to whom the Purchase Order was sent. |
Ship Via |
The name of the carrier for the returned material. |
Ship Charge |
The mode of the charge of the shipping for the return |
FOB |
The point where title of the returned goods passes. |
Terms |
The payment terms offered by the supplier |
Waybill |
The carrier’s waybill number pertaining to the material return. | |
1.3.3.3. View DMR Tab | 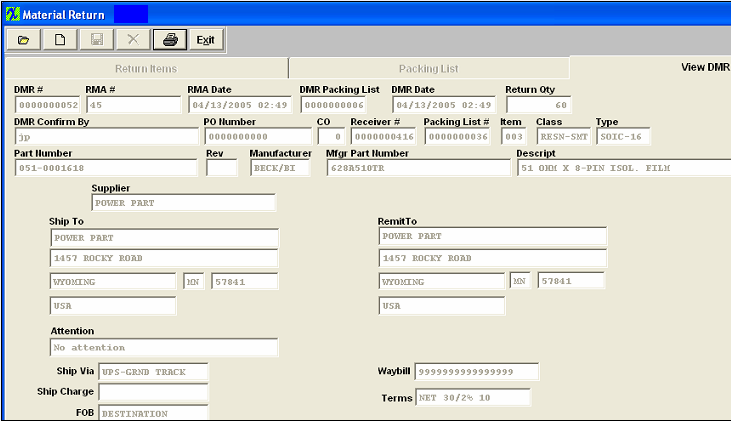
DMR # |
The number assigned to the DMR. |
RMA # |
The number the Supplier provided for the Return Material Authorization. |
RMA Date |
The date of the Supplier’s Return Material Authorization |
DMR Packing List |
This is the alphanumeric packing list identifier |
DMR Date |
This is the date the DMR was created. |
Return Quantity |
The number of units returned to the supplier. |
DMR Confirm By |
The name of the user who authorized the DMR. |
PO Number |
The number of the Purchase Order. |
CO |
The Change Order pertaining to the Purchase Order |
Receiver # |
The number of the Purchase Order Receiver |
Packing List # |
The number the supplier assigned to the Packing list |
Item |
The number of the line item per the Purchase Order. |
Class |
The classification of the part number returned. |
Type |
The type within the classification. |
Part Number |
The user assigned number for the part being returned |
Rev |
The revision of the part number, if applicable. |
Manufacturer |
The name of the part manufacturer |
Mfgr part Number |
The number assigned to the part by the manufacturer |
Description |
The description of the part number |
Supplier |
The name of the supplier |
Ship to |
The address where the return will be shipped. |
Remit To |
The address for the receipt of the Debit Memo, if applicable. |
Attention |
The name of the supplier’s contact. |
Ship Via |
The method of shipment for the return |
Ship Charge |
The mode of the charge of the shipping for the return |
FOB |
The point at which legal title passes. |
Terms |
The payment terms offered by the supplier |
Waybill |
The number of the shipper’s document |
|
1.3.4. How To ..... for PO DMR |
1.3.4.1. Adding a DMR from Inventory | This procedure is used after accounting has Reconciled the Purchase Order. If accounting has NOT yet reconciled the purchase order, see Rejecting Items if Accounting hasn't Processed the Invoice.
Note that the discrepant material must be transfer into the MRB (materials review board) warehouse via Inventory Handling before you can proceed.
Enter the SQLMANEX.EXE (within the ManEx root directory)
This action will then prompt the user for a password
|
 |
The following screen will be displayed, enter Inventory Management / Purchase Order Receiving & DMR (discrepant material return) / PO DMR (discrepant material return).
|
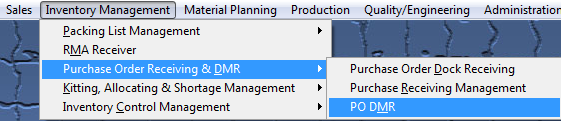 |
The following screen will be displayed:
Depress the Add button and user will be prompt for a password.
The following screen will be displayed:
Select the "From Inventory" radio and the following screen will be displayed.
Enter in the Part Number and depress the OK button. The following screen will appear (If there is more than one Purchase Order involved it will list them all)
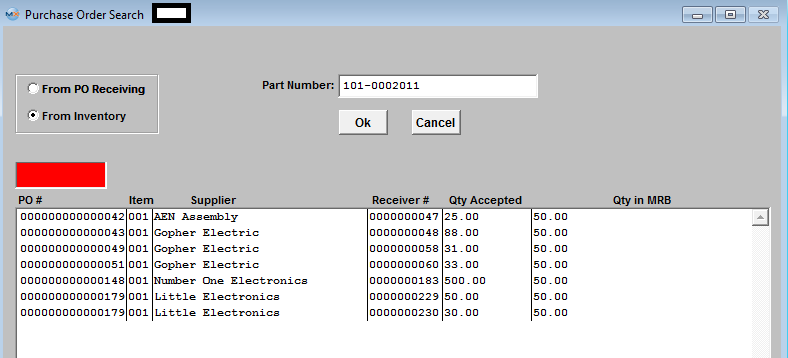
Highlight the Purchase Order of Choice, Depress the OK button. Information regarding that part number for the Purchase Order selected will display:
Enter in the returned qty in the "Return Qty" field, enter in the RMA number in the "RMA # field" and enter in your name, initials, etc in the "Confirm By" field.
Depress the Packing List tab, and enter in a DMR Packing List number (if set to manual) for the return, and a Waybill number if applicable.
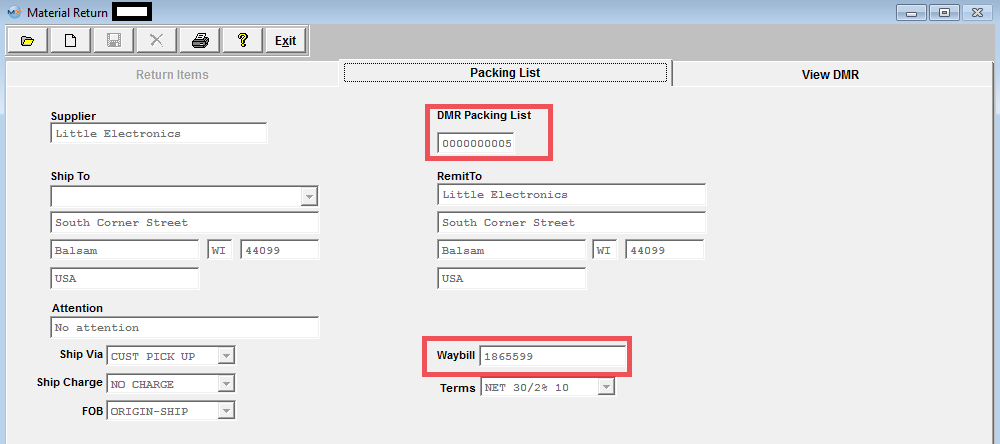
Depress the Save button. The following screen will be displayed:
Once the DMR (discrepant material return) has been added and saved, a Debit Memo will be created, if an AP invoice exists (in order for a AP Invoice to exist you have to have reconciled the PO and transferred it to AP). If Debit memo numbering is manual, the user will be prompted for the number. Additionally, the corresponding entry will be created and the balance in the Accounts Payable Aging will adjust as soon as the Debit Memo is printed. If a PO DMR is created for parts "From Inventory" and the PO has NOT been reconciled and Transferred to AP the qty rejected will be put back on the PO.
The following message will be displayed and the system will NOT be able to create a DMR from Inventory for a part that has been changed from being a Lot-Coded part to a Non-Lot Coded part or visa-versa after PO Receipt has been created.
User should change lot code tracking status with caution. If a part has lot code history and the lot code tracking is de-activated the entire lot code history is wiped out.
1.
If accounting HAS reconciled the PO but HAS NOT transferred the reconciled invoice into AP Aging, the following message will appear:
If the invoice happens to be in a Saved Check batch the following warning will be displayed:
|
1.3.4.2. Add a DMR from a PO Inspection/Acceptance Receiving Rejection |
Enter the SQLMANEX.EXE (within the ManEx root directory)
This action will then prompt the user for a password
|
|
The following screen will be displayed, enter Inventory Management / Purchase Order Receiving & DMR (discrepant material return) / PO DMR (discrepant material return).
|
|
The following screen will be displayed:
Depress the Add button and user will be prompt for a password, enter their password and the following screen will be displayed:
The defaults for this screen are "From PO Receiving" and "Purchase Order #"
If you chose the default (Purchase Order #), you will need to enter in the number of the PO on which the material was rejected. If you chose Supplier, you must then enter in the name of the Supplier.
Enter in the number of the PO which the material was rejected and the PO and related information will populate on screen.
Highlight the PO and depress the OK button.
Note: Ther are additional fields displayed on screen if there are Serial Numbers and Lot Codes involved.
Enter in the DMR number (if set-up for manual numbering) you are assigning to this return. Enter in the RMA number as provided by the supplier. Then enter your name in the Confirm By space.
Highlight the line item containing the rejected quantity. (If returning a part that involves a Lot Code, type in the returned quantity in the Lot Code section and it will automatically update the Return From section. Check the serial numbers being returned).
Depress the Packing List Tab, enter in a Packing List number you wish to assign to the return (if set to manually numbering). (Note that this number is NOT tied to regular shipping Packing Lists. This field is only for reference on the DMR’s. Any alpha-numeric code can be used here. DMR packing list numbers cannot be found in the regular shipping module – Packing List Management. It is suggested that the user manually log these codes or type in some kind of significant code, such as the date followed by the PO#). Enter in the Waybill.
Depress the Save button. The View DMR screen will appear:
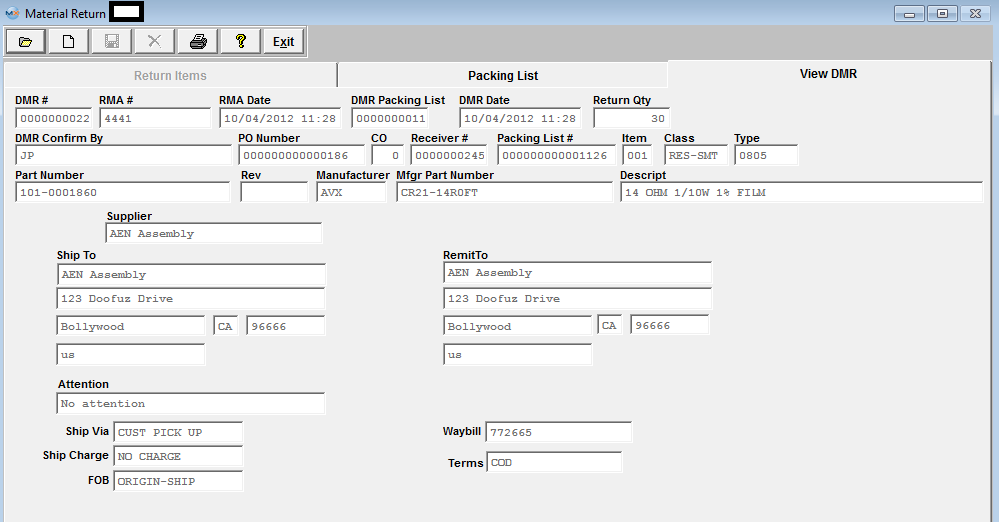
|
1.3.4.3. Find an Existing Discrepant Material Record (DMR) |
Enter the SQLMANEX.EXE (within the ManEx root directory)
This action will then prompt the user for a password
|
 |
The following screen will be displayed, enter Inventory Mgt / Purchase Order Receiving & DMR (discrepant material return) / PO DMR (discrepant material return).
|
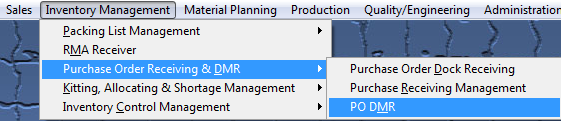 |
The following screen will be displayed:
Depress the Find icon, the following screen will be displayed. User can select to find an existing DMR by entering the DMR Number or entering the Receiver Number in the Rd box and depressing the OK button:
If the system cannot find any information about the DMR # entered the following message will be displayed giving the user the option to select from a list of existing DMR's:
If User Selects "YES" the following screen will be displayed listing all of the existing DMR's
Enter the DMR# in the Red box or double click on the DMR# and the following information will be displayed:
|
1.3.5. Reports - PO DMR |
To obtain the DMR (Discrepant Material Return) Packing List Report within the Web, select the WEB Print button from the ManEx action buttons at the top of the screen. For further detail on How the Reports work within the Web refer to Article #5477.
Note: In order to access the Reports within the Web the Company Root URL must be setup within the System Appearance module and user must be linked to web within the System Security Module
Select the Report Type: PO DMR - A List of Reports will be displayed that are available on the Web
for PO DMR
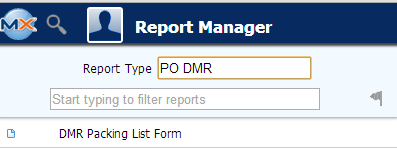
To obtain the DMR Reports within the desktop, select the Print button from the ManEx action buttons at the top of the screen.

The following reports screen
will display a list of reports that are available on the ManEx Desktop: The following screen will be displayed:
Highlight the DMR (discrepant material return) Packing List Form.
Depress the OK button
|
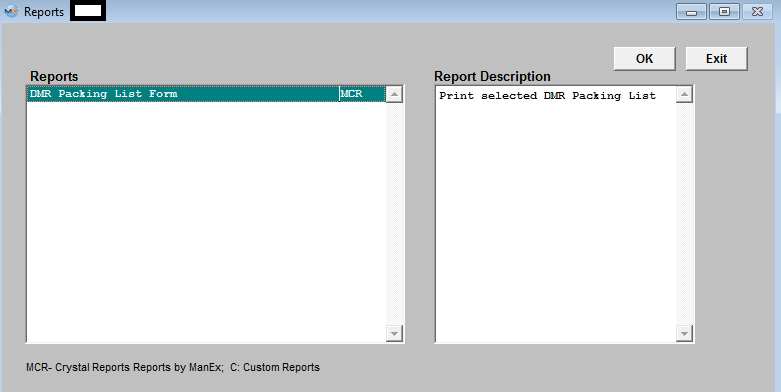 |
The following screen will be displayed:
Enter the DMR Number you wish to view.
|
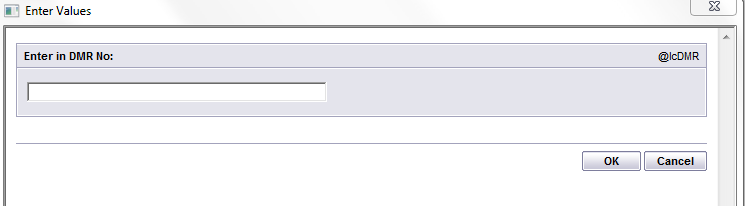 |
The following will print:
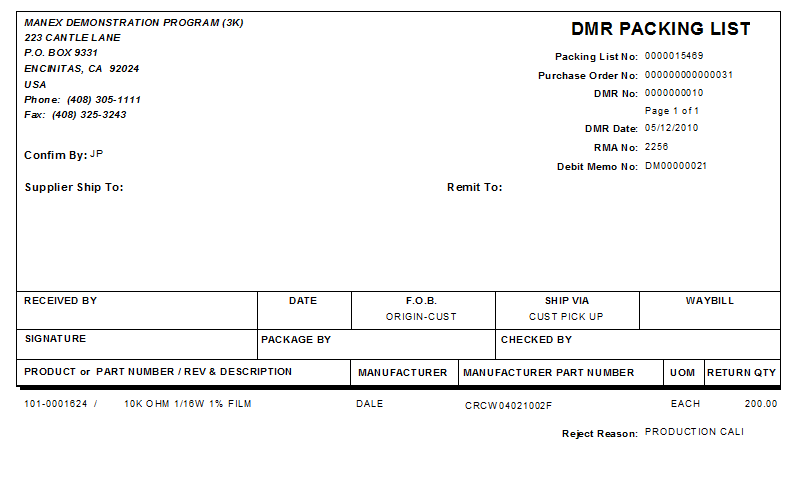
|
|