Enter the SQLMANEX.EXE (within the ManEx root directory)
This action will then prompt the user for a password
|
 |
The following screen will be displayed, select Quality Engineering/Product Data Management (PDM)
|
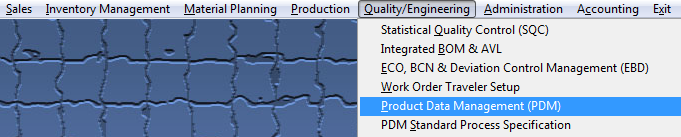 |
The following screen will be displayed:
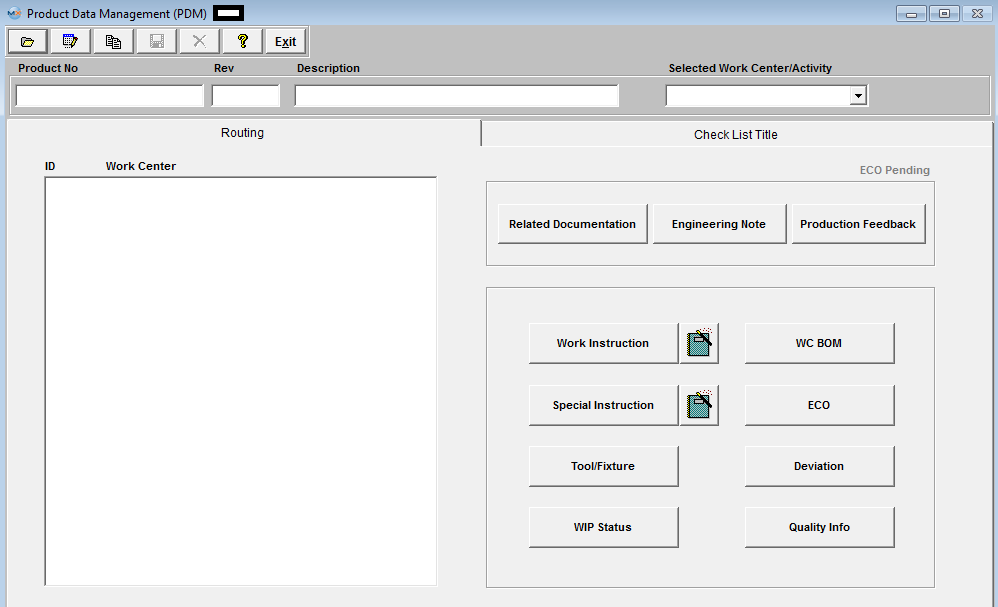
Depress the Find Record action button. The following Selections will appear. User may select to find a record by Product Number, Part Class, or All. If user selects by Product Number they may enter the PN in the Red box or enter in a partial Product Number and a list of Product Numbers will be displayed that contain this number to select from. To Find by Part Class user may enter in a Part Class and a list of Product Numbers within this class will be displayed to select from. |
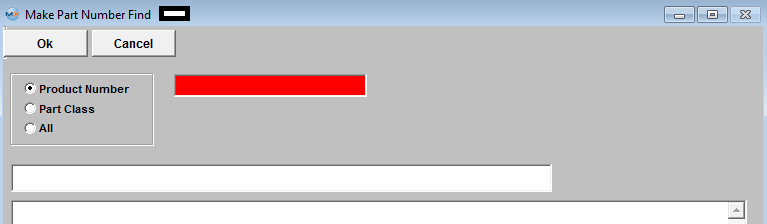 |
If the user selected to find by All. All the Product Numbers within the Inventory records will be displayed to select from:
|
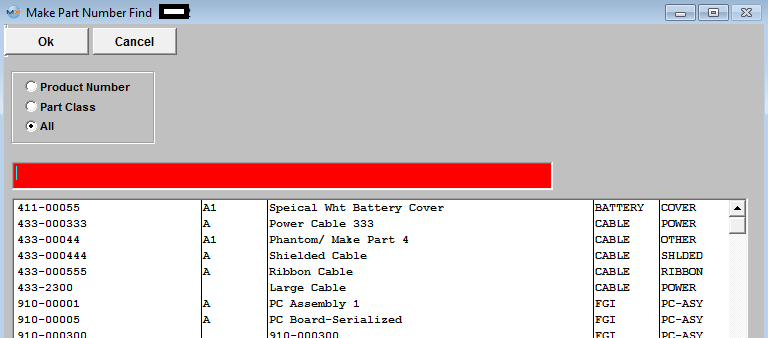 |
When the part number is located, the screen displays Work Order Traveler Setup information about the product.
The plus (+) mark preceding work centers indicate that additional activities are included in the work center, and may be viewed by clicking on the plus sign.
|