The Work Order Release Check List tab is for the user to select check list items for the Work Center listed in the Current Work Center field. The Work Order Release Check List is set up in the Shop Floor Tracking Default set up screen. In this module, the Check List items are selected, as detailed. Then when the user reaches the Work Order Shop Floor Tracking module, the items added in this module will be available.
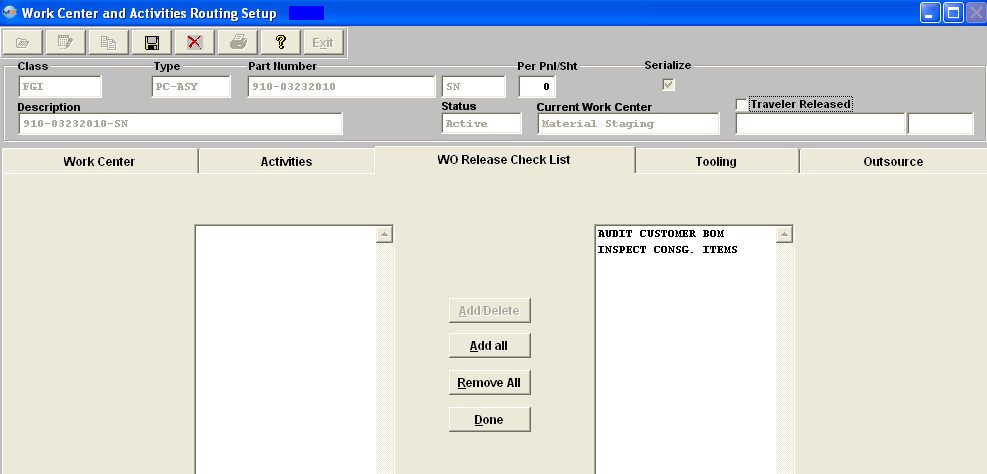
Fields & Definitions
Add/Delete |
This button allows the user to add or delete the check list items to or from the Work Center being displayed above.
|
Add all |
This button allows user to add all check list items (displayed on the right) to the current work center being displayed above. |
Remove All |
This button allows user to remove all check list items (displayed on the left) from the current work center being displayed above. |
Done |
Depress this button when you are done making changes. |
|