1.1. Purchase Order Management |
1.1.1. Purchase Order Management |
1.1.1.1. Prerequisties - PO Mgmt |
After activation, "Purchase Order Management" access for each user must be setup in the ManEx System Security module. Users with “Supervisor Rights” will automatically have access.
Supplier
|
The Supplier must be setup in the Supplier Information module. |
Part number in Item Master |
The part number must exist for a product or part in the ICM module. |
AVL |
The Manufacturer Names must have been set up in Part Manufacturer Setup module. |
Buyer Codes |
The Buyer codes must be established in the Inventory Buyer Setup module. |
Purchasing Approvals |
A list of employees and their approval authorizations must exist in Purchase Setup module. |
Optional Prerequisites for Entering a New PURCHASING
|
1.1.1.2. Introduction for PO Mgmt |
The PURCHASING Module is the place where all procurement is done. This module allows the user to add purchase orders to the system, and to add items to each purchase order. Edit functions are available both at the purchase order level and at the item level.
The process begins by selecting a Regular PO or an In-Store PO, then selecting a supplier for the order. The supplier is selected from a list of suppliers established in the Supplier Information module.
After selecting a supplier, the user may enter orders for various types of material. Inventory material is ordered to be placed in on hand inventory and used in the making of product. The user may also select MRO parts, parts which are not kept in inventory, but are expensed as they are purchased and distributed to the requester when they are received. (MRO parts may be defined in the item master and kept in inventory, if desired.) There is also a selection for Services.
The user may add a new part by selecting the part class and type, then choosing from a part matching that criteria, or go directly to the part number edit box and enter the part number without visiting the class and type box.
The buyer may have entered a specific manufacturer of the item, providing that the manufacturer and the part number have been entered in the inventory item master. If there is only one manufacturer, that manufacturer will be the default manufacturer entered in the purchase order.
If the user is adding an inventory item to the order, the system will add in the details from the item master once the part number is established.
Purchased items may have the delivery schedule established for one or more deliveries. The delivery date entered in the purchase order is meant to be the date the material lands on the user’s dock.
The user may enter either the stocking quantities based on the stocking unit of measure or the purchasing quantities, based on the purchase unit of measure. If the units of measure are different, the user must have defined the relationship between the different units in the Unit of Measure Conversion. Entering one quantity will automatically calculate and enter the other quantity.
The user enters the unit price and whether or not the item is taxable. If it is taxable, the tax percentage will be supplied based on the data entered in the Tax &Shipping Mode tab. The system will display the extended amount of the item on the order based on the quantity and price. Note: If the Tax Information has not been filled in, the Purchase Order will NOT calculate any sales tax. Therefore, it is important that the user set this up properly.
The user may define the quantity that may be received over the amount of the order by entering an overage percentage. This will allow incoming receiving to accept quantities up to the amount of overage specified for the order.
The user may enter specific notes about the item on the purchase order, to be printed on the order. They may also view and edit any item master notes that may exist for the part, and may also view the procurement history for the part.
Once entered, all orders require an approval. The approval authority established in the Purchase Order Authorization tab is used to determine whether or not an individual may approve an order. It is possible to allow two approvals to orders, and to set different approval limits for each of them.
Orders will be identified as temporary orders until approved, after which they will have a permanent number assigned.
Change orders to purchase orders must also be approved in the same manner. Once an order is changed, it cannot be printed or acted upon until it is approved again.
Details about the remittance, delivery point, billing etc. will be completed with Supplier default information, and may be reviewed for the order if necessary.
In-Store purchasing overview: In-Store is the situation where the Supplier has placed raw materials in the user’s warehouse. The Supplier still owns the raw materials. When the user is ready to use the Supplier’s raw materials, he/she issues an In-Store Purchase Order. For In-Store POs, the user may select by Supplier or by Part Number. Then the user may find records according to the selection. Once found, the user may create a PO for the In-Store Consumption. In-Store Purchasing also includes receiving.
|
1.1.1.3. Fields & Definitions - PO Mgmt | 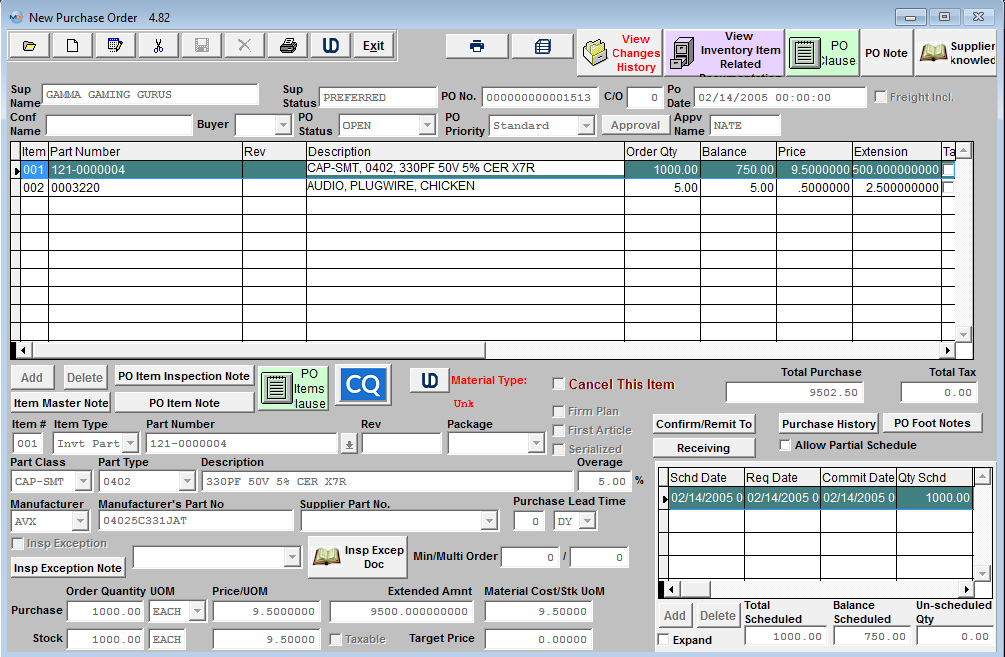
Sup Name |
The supplier or vendor with whom the order was placed. |
Sup Status |
The status of the Supplier, whether Approved, Inactive, etc. |
PO Number |
The Purchase Order number of the order. If PO Numbering is set to Auto (in Number System Setup ) the system automatically places a "T" in the PO number to flag it as a temporary number. Then upon approval the system auto finds and replaces that "T" with a "0". Note: If PO Numbering is set to manual, users enters a PO number manually using a "T", then changes the numbering to Auto, if this PO is edited and approved the "T" will be changed to "0". The system has no way of knowing that the <st1:place w:st="on">PO was manual numbered before the change.
|
CO |
The Change Order revision status of the order. This field can be automatically increased upon approval or controlled by the user and is only changed if the user manually assigns a Change Order number. (This is setup in the System Setup/Material/Purchase Order Setup module). Change Order History is tracked under the View Changes History screen automatically. NOTE: If auto assign the next change order will be referenced in the change history but the PO change order will not increase until PO has been approved. If not auto assigned the change order will be referenced to what ever change order user enters.
|
Po Date |
The date the purchase order was created. |
Freight Included |
If this box is checked, the vendor has agreed to pay the freight. "Freight Included" will be added to the print out of the PO form and will be displayed in PO Reconciliation module for reference. If this box is not checked "Freight Not Included" will be displayed on PO Reconciliation module. |
Conf Name |
The contact at the supplier who confirmed the purchase order. |
Buyer |
The initials of the buyer for the order. |
PO Status |
The status of the purchase order. Indicates if the order is new, being edited, is open, closed or cancelled. |
PO Priority |
The status of the purchase order.Indicate if the order is standard, priority, or hot. |
|
When the purchase order is approved, the "T" in the Purchase Order number will be replaced with a "0" and the initials of the person who approved the order will be displayed. (Note: The PO must be approved before being able to create a PO Dock receiver). |
Final Approval |
When two approvals are required, and both are granted, the initials of the second person approving the purchase order will be displayed in this field. |
Purchase Order Items
Item |
The purchase order item number of an item being purchased. |
Part Number |
The part number of the item being purchased. NOTE: User has the option to drill down to view the inventory record info for a part by double clicking on the part number. |
Rev |
The revision of the part number being purchased. |
Description |
The Description of the part number. |
Order Qty |
The quantity of parts being ordered. See Article #1240 for more detail on why the system will not allow user to enter in a fraction of a number, and an alternative. |
Balance |
The un-received balance of the item. |
Price |
The agreed upon price for the items being ordered. |
Extension |
The extension of the price and quantity. |
Tax |
Indicates whether or not the item is taxable. |
 |
This will allow user to cancel an individual item on a PO. Since the system does not allow you to delete a line item that has had any kind of transaction, we needed a way for users to cancel individual line items without having to cancel the entire order within the system. If any parts have been accepted, it cannot be cancelled. Once a part has any receipts the user cannot delete the line, so if they reject the total received qty they can cancel the line to prevent it from affecting the PO, or PO history for the other line items. If they do not want to reject the entire qty then their only option is to reduce the balance qty to the accepted qty. Cancelled line items will be excluded from the Purchase Order reports within the module.
|
|
The total amount of all items on the purchase order (excluding taxes). |
Total Tax |
The total tax amount of all items on the purchase order. |
Detail Definitions
Item # |
The purchase order item number of an item being viewed. |
Item Type |
The type of inventory being purchased (Inventory, MRO, or Services). These are hard coded into the system and cannot be changed or edited in anyway. Inventory is for a part that exists in the ICM module. MRO stands for Management Required Options. Generally this is used for supplies, purchases. Services items are for those instances where the assembly is outsourced. |
Part Number
|
The internal part number of the item being purchased. |
Rev
|
The revision of the part number. |
Package
|
The packaging method used to package the parts.
|
Material Type |
The material type (per AVL level) will be displayed in Red once user selects the mfgr and mfrg PN. |
Firm Plan |
If this box is checked, the MRP module will NOT try to override the purchasing decision. For example: If the need is for 100 parts per month for the next six months. But the user makes a decision to block order 600 parts and marks the PO as Firm Planned. Without any Firm Plan command, the MRP module would instruct the user to cancel the PO for 600 quantity and re-issue for 6 separate purchases of 100 each. But since the PO is marked as Firm Planned this tells MRP that the purchasing decision was intentional and NOT to override. So MRP will work around this PO
|
|
If this box is checked, this part requires a first article inspection and the users will be required to check off the First Article Done box within PO receiving (This information is usually defaulted from the ICM module, but can be edited within the PO module also).
|
|
If this box is checked, the user will be required to enter serial numbers at time of Purchase Order Receipt and Inspection. (This information is defaulted from the ICM module).
|
Allow Partial Schedule
|
If user wants this box to be checked at all times they must set the default as checked within the System Setup/Materila/Purchase Order Setup module, and user can change it any time while in the PO module. If user wants to be able to save a partial schedule on a one to one basis they will have the default setup as unchecked within the System Setup/Materila/Purchase Order Setup module. If un-checked user will receive the popup warning them that they have not scheduled all the order qty and ask if they want to finish scheduling the order qty, upon saving a PO with only a partial schedule. If the box is checked the system will not ask any questions when saving a po with only partial schedule. (Note: MRP will NOT acknowledge qty's that are not scheduled).
|
Part Class
|
The Part Class of the part number.
|
Part Type
|
The Part Type of the part number.
|
Description
|
The Description of the part type.
|
Overage
|
The percentage of parts allowed to be received over the ordered quantity.
|
Manufacturer
|
The manufacturer for the part.
|
Manufacturer Part Number
|
The commercial part number.
|
Supplier Part No.
|
If the Mfgr AVL has a Supplier and Supplier PN associated within the ICM module, the Supplier PN will be displayed in this field as additional reference.
|
Purchase Lead Time
|
The time between the Supplier receipt of the PO and receipt at the users dock.
|
Insp Exception
|
Checking this box will allow the receiver to receive the parts for this Purchase Order Only without inspection. Upon checking this box the Insp Exception Note Field and the Insp Excep Doc will become available for use and then user must then select an Insp Exception Type from the pull down screen. User MUST have special rights within the Security module or supervisor rights to edit this field.
|
 |
The Insp Exception box MUST be checked for this field to become available. This information will then be displayed within the PO Receiving as reference information to the users that are processing the Receipts through the system. |
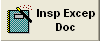
|
The Insp Exception box MUST be checked for this field to become available. This will allow users to attached documents. This information will then be displayed within the PO Receiving as reference information to the users that are processing the Receipts through the system.
|
Min/Multi Order
|
The Min/Multi order quantities are defaulted in from the Inventory Control module (MRP Info tab) to display the minimum quantity that must be ordered for this part and the increments this part must be purchased in. (If this information is edited within the Purchase Order Module, it will be updated to the ICM module upon saving). For Example: if the Min order qty is 500 and the order multi is 100 and the order is for 515, then the order will need to be rounded up to 600.
|
Purchase Order Qty
|
The quantity of parts being ordered based on the purchasing units of measure.
|
UOM
|
The Purchased unit of measure. (May be different than stocking unit of measure).
|
Price/UOM
|
The agreed upon unit price for the items being ordered.
|
Extended Amt
|
The extension of the price and quantity.
|
Standard Cost/Stock UOM
|
This field displays the Standard MATERIAL Cost. (This is defaulted in from the ICM module, if no standard material cost is found in the ICM module the user will be allowed to enter in a standard material cost at the time of purchase). For a BUY part, this is the value against which PPV should be calculated, and the value the user should expect to pay for the part.
|
Stock/Order Qty
|
The quantity of parts ordered based on the stocking unit of measure.
|
Stock UOM
|
The stocking unit of measure.
|
Stock Price/UOM |
The stocking price.
|
Taxable
|
Indicates whether or not the item is taxable.
|
Target Price
|
The target price is a reference for the buyers to use. (This information is defaulted from the ICM module).
|
Directive Buttons
The following buttons are displayed on the Purchase Order Screen.
After a purchase order is created or edited, it must be approved before it can be printed and issued to a supplier. Certain employees may be granted authority to approve purchases up to a certain total dollar value. Those authorized personnel may approve purchase orders under that amount. If only one signature is required, the order will be finalized and released. If it is a new order, and automatic PO numbering is enabled, Manex will assign the next available number to the order. The action is taken by clicking on the Approval button and responding with an authorized password.
If two signatures are required in order to release a purchase order, then a second person with approval authority for the amount of the order must approve the order, by clicking on the Final Approval button and responding with an authorized password.
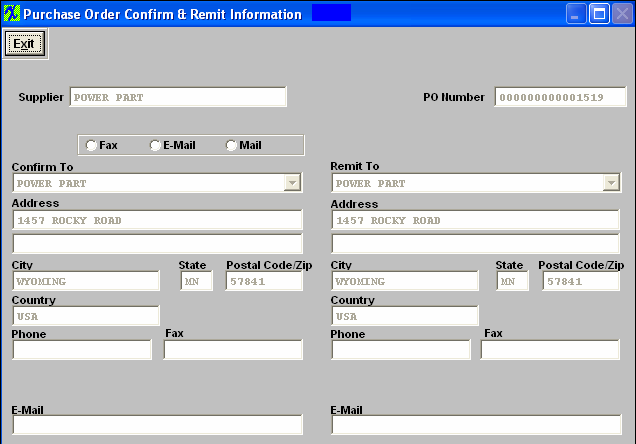
Confirm/Remit Screen Field Definitions
Supplier |
The supplier or vendor with whom the order was placed. |
PO Number |
The Purchase Order number of the order. New purchase orders that have not been approved will display a temporary number until approved. |
Fax, eMail, Mail |
How to communicate with the supplier. |
CONFIRM TO
Confirm To |
The name of the supplier. |
Address, City, State, Postal Code, Country
|
The address of the supplier to which the order is sent. |
Phone, Fax |
How to communicate with the supplier. |
E-Mail |
Email address enter within the Supplier Setup module. |
REMIT TO
Remit To |
The name of the supplier or their agent. |
Address, City, State, Postal Code, Country |
The address of the supplier to which the payment is sent. |
Phone, Fax |
How to communicate with the supplier accounting department. |
E-Mail |
Email address enter within the Supplier Setup module. |
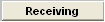 |
When the user has displayed a purchase order with items on the Purchase Order screen, pressing on the Receiving button will display information about where the supplier is to ship the material on the purchase order, and the terms and conditions of the order.
|
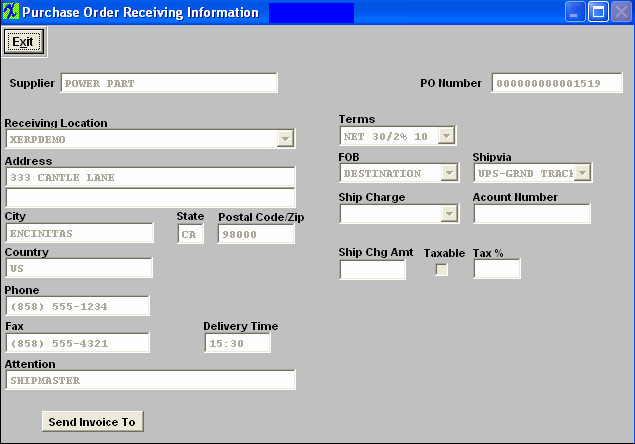
Receiving Screen Field Definitions
|
The supplier or vendor with whom the order was placed. |
|
The Purchase Order number of the order. New purchase orders that have not been approved will display a temporary number until approved. |
|
The company and address to which the order is to be shipped. |
|
The terms of the purchase order. |
|
The FOB point for the order. |
|
The preferred shipping carrier for the order. |
|
How the freight costs are to be paid. |
|
If needed, the freight company account number for the carrier to charge. |
|
The shipping charge cost for the order. This is referenced on Purchase Order Forms Only. These amounts wIll not be carried over to the PO Reconcilliation. |
|
Indicates if the freight charges are taxable. This is referenced on Purchase Order Forms Only. These amounts wIll not be carried over to the PO Reconcilliation. |
|
The tax rate for the shipping charges. This is referenced on Purchase Order Forms Only. These amounts wIll not be carried over to the PO Reconcilliation. |
|
The preferred delivery time for receipts. |
|
The name of the person to whom the shipment is directed. |
DIRECTIVE BUTTONS
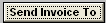 |
When the user has displayed a purchase order with items on the Purchase Order screen, pressing on the Send Invoice To button will display the billing information for the supplier. This button is displayed on the Purchase Order Receiving Information screen |
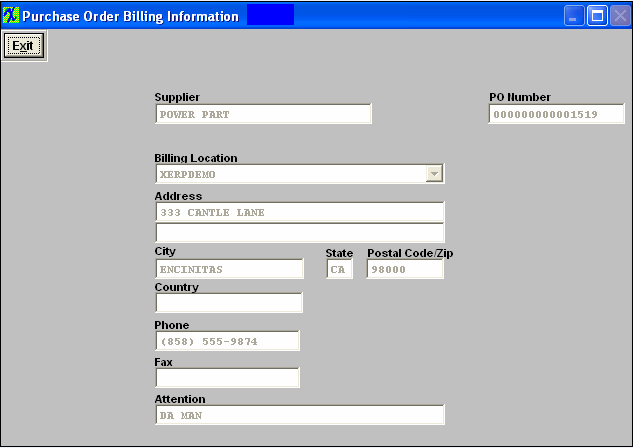
Send Invoice To Screen Field Definitions
|
The supplier or vendor with whom the order was placed. |
|
The Purchase Order number of the order. New purchase orders that have not been approved will display a temporary number until approved. |
|
The users company and address to which the order is to be billed. |
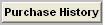 |
Depressing the Purchase History button will display the purchase history for that line item. The user may sort by Clicking on any of the Headers, and Search for specific items by typing in the column. Note: If an order has status “EDITING” it will not be displayed on the history list. Once the order is approved and the status is changed to "Open" or "Closed" the order will then be displayed on the purchase history list. |
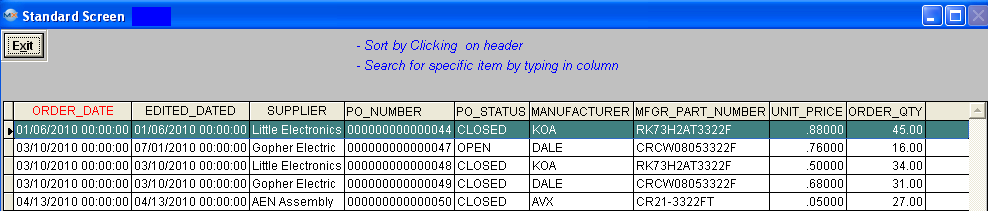
 |
When the user has displayed a purchase order with items on the Purchase Order screen, and has highlighted one of the line items, checking the Expand box will display the schedule information about the item being purchased. |

 |
When the user has finished viewing the schedule information about the item, the user may check the Shrink box and the schedule information will shrink down. |
Schedule Field Definitions
|
The date the material is due to land on the users dock. This is the date MRP uses. |
|
This is the internally required or desired date. It is not used for the supplier or MRP. |
Commit Date |
The commit date is a reference field for the buyer. |
|
The quantity scheduled for the due date. |
|
This will display the balance left to receive from the Qty scheduled. |
|
The User can choose the Warehouse from the pulldown or leave it blank. The Y next to the Warehouse location indicates that, that Warehouse is set-up in the AVL. The N next to the Warehouse location indicates that, that Warehouse is not set-up in the AVL. If the warehouse field is left blank then the warehouse can then be assigned at PO Receiving Management. Once the record has been saved within the PO Receiving this information will then be updated within the Inventory Control Management under the Qty info screen. |
|
The Location field will update automatically from the Inventory Control Management module. The user can edit this field in the scheduling detail. This will not change the location in the Inventory Control Management module under the quantity info screen. |
|
This is classification of the distribution of the item when received, either to regular Inventory Receiving or to Allocate to Special Work Order or Project |
|
This Field is for future use, it is non-applicable at this time. |
|
The General Ledger number where the purchase order will post. These GL numbers are defaulted in from the Purchase Setup under the MRO Receiving Setup. |
|
|
Depressing on the button will bring up a screen where the user can enter in specific notes that pertain to that one schedule, item, and date. Type in the note. Depress the Save button. Exit |
 |
When Creating a new PO or Editing an existing PO this button will be enable. Depressing this button will allow the user to add additional scheduled deliveries. |
 |
When Creating a new PO or Editing a existing PO this button will be enabled. Highlight a scheduled delivery then depressing this button will delete that delivery from this screen. |
|
This field will display the total qty scheduled for the highlighted item. |
|
This field will display the Balance left to receive from the qty scheduled for the highlighted item. |
|
This field will display the qty un-scheduled for the highlighted item. |
|
1.1.1.4. How To ..... for PO Mgmt |
1.1.1.4.1. Find a Purchase Order |
Enter the SQLMANEX.EXE (within the ManEx root directory)
This action will then prompt the user for a password
|
 |
The following screen will be displayed, select Material Planning/Purchase Order Management/Purchase Order Management
|
 |
The following screen will be displayed:
1. Depress the Find Record icon. The following screen will be displayed.
2. On the left hand side of the screen, select the desired Filter: by selecting the appropriate radio button - Open PO, All, Closed/Cancelled PO, For Approval, or ALL.
3. Once you’ve made your “Filter” choice, determine the "Find by" search method by choosing between PO Number, Inventory Part Number, MRO Part Number, Supplier, Inventory Manufacturer Part Number, MRO Manufacturer Part Number, All, Inventory Description, or MRO Description.
If you do not know the exact number, Customer, etc you may enter in a partial number, letter, etc, then once you depress the enter key the system will pull up the matching record onto the screen or a list of all Purchase Orders that contain the partial number, letter, etc. entered, to select from.
|
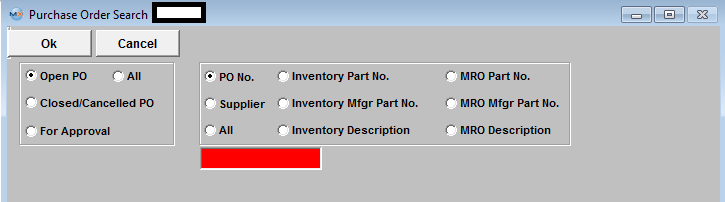 |
4a. For example, a selection on the left for an Open PO, and a selection of ALL on the right will produce the following screen, listing all open purchase orders.
|
|
4b. A selection on the left for All and a selection of All on the right will produce a list of all purchase orders, open, closed, etc. |
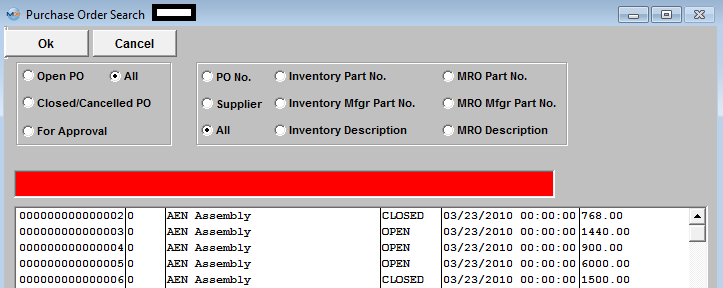 |
If you enter information in the Red Box and the system cannot find any information, users will receive the following message and if they select "YES" a list of Open PO will be displayed.
The rest of the right hand selections are essentially the same as for those illustrated above.
|
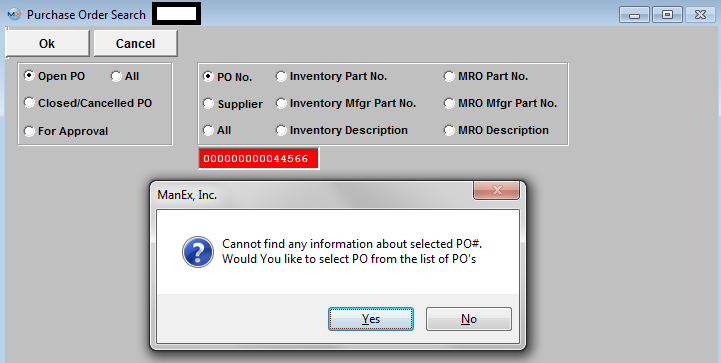 |
5. After finding the Purchase Order, the Purchase Order screen will be displayed, populated with any parts on order.
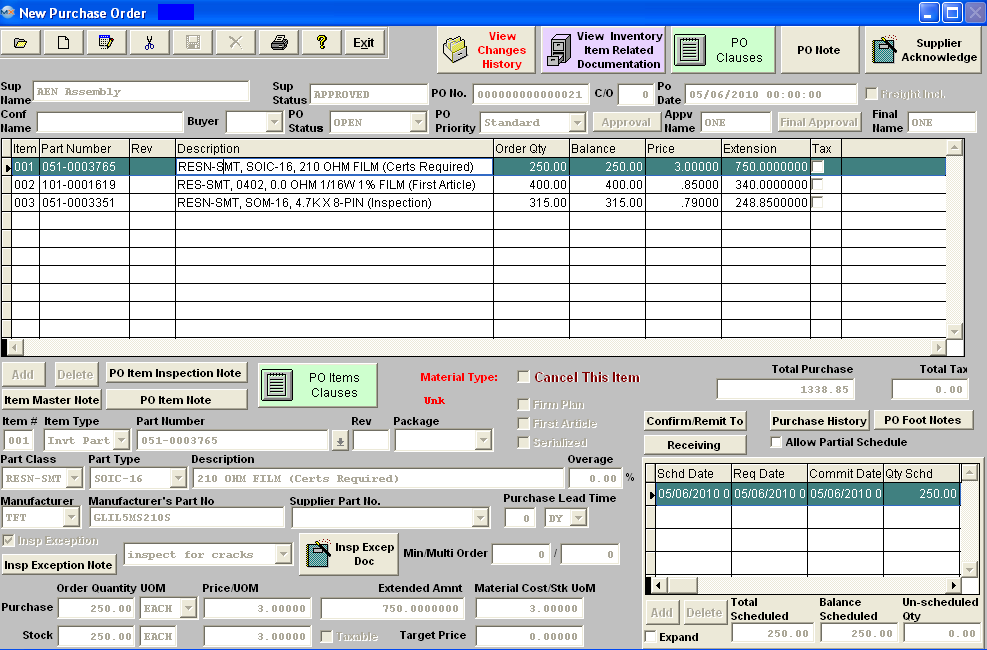
|
1.1.1.4.2. Add A Purchase Order |
Enter the SQLMANEX.EXE (within the ManEx root directory)
This action will then prompt the user for a password
|
|
The following screen will be displayed, select Material Planning/Purchase Order Management/Purchase Order Management
|
 |
The following screen will be displayed:
Depress the Add Record Button (in the Purchase Order Tab screen) displays the following sequences:
The first step is to Select Regular PO or In-Store PO
|
|
After selecting "Regular PO" user will be prompted for their password and the following screen will be displayed:
The user must first select the Supplier from the Pull down, and all the head information will default in:
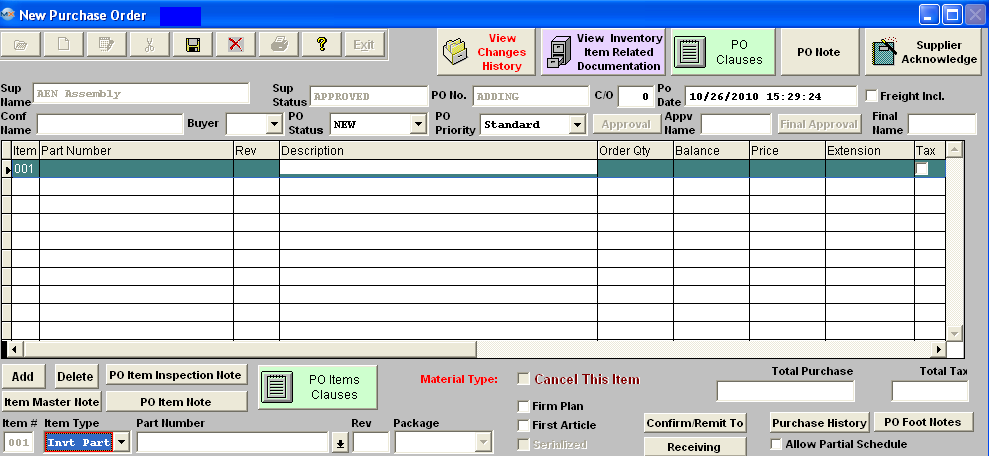
Entering Item Detail Information
The user must first select the Item Type to be entered as a line item. Item types include Inventory Parts (parts to be delivered to on hand inventory), MRO (expensed items) or Services .
|
|
|
1.1.1.4.2.1. Inventory Part | Selecting Inventory Parts as the item type, the user may jump directly to the part number box (click on it) and enter a part number. Or, the user may step through the Part Classes and Part Types to narrow the focus and then select a part from the desired part type. Once a part number from Inventory has been entered, ManEx completes the boxes associated with the item master.
If more than one manufacturer exists for the part, the user may click on the down-arrow next to the manufacturer edit box and select the appropriate manufacturer for the order. The Material type will be displayed in the pulldown next to the Mfg. and Mfgr. PN. |
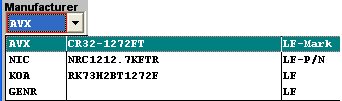 |
If more than one supplier part number exists for the part, the user may click on the down-arrow next to the supplier part no. edit box and select the appropriate supplier part no. for the order.
The system will look for the preferred supplier part number and if found will show it as a display. At this time the user can leave the part number as is or select a different one if available. After a user will save the PO, the supplier part number will be saved and next time you will see the selected suppler part number when viewing the same PO.
No history will be saved because this field is for the information only.
|
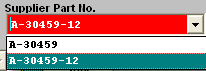 |
Firm Plan |
If this box is checked, the MRP module will not try to override the purchasing decision. For Example: The user makes a decision to block order 600 parts, but the need is only for 100 parts per month for the next six months. Without the Firm Plan command, the MRP module would tell the user to cancel the PO for 600 quantity and re-issue for 6 separate purchases of 100 each. With the Firm Plan command, this tells MRP that the purchasing decision was intentional. (Please refer to the Material Requirements Planning article).
|
First Article |
This box will be checked if set-up in the Inventory Control Management Module. You may uncheck it or check it if user has been instructed that it may be changed for this item only. This information will be carried forward to the PO Receiving screen for reference. |
Serialized |
This box will be checked if set-up in the Inventory Control Management Module and will not be editable within the Purchase Order Management. This indicates to the user that this BUY part has been marked as Serialized and any product coming in or out of the system will require serial number tracking. |
The user may edit or add a percentage amount of extra material that will be allowed to be shipped against the order. By entering a percentage in the OVERAGE field, receiving will be allowed to receive extra parts up to the limit imposed in this field.
The user may also edit or add in purchasing lead time and min/mult order quantities through the Purchase Order Management module. Once the record has been saved this information will then be updated within the Inventory Control Management under the MRP Info screen.
The user may check the box for Inspection Exception and select from the Inspection Exception Pulldown (which is established in the Inspection Exception Setup module). The user will then also be allowed to enter any Inspection Exception Notes and/or Load Insp Excep doc that pertain to that PO line item. This information will then be displayed within the PO Receiving as reference information to the users that are processing the Receipts through the system.
The user is then prompted for the purchase order quantity of parts to be ordered. The user may enter either the Purchase Quantity or the Stocking Quantity, and ManEx will complete the other field based on the purchase/stocking unit of measure and conversion field.
NOTE: When creating a PO for an item with different purchasing and stocking UoMs, be sure to enter the MRP suggestion into the Stocking qty field rather than the purchasing qty field. The system will automatically convert the stocking unit into the purchasing unit for the purchase order qty.
For example if the buyer is creating a PO for an item that is used by inches but sold by the foot, the user would enter qty of 36 into the stocking qty field and the PO would automatically convert it to 3 feet in the purchasing qty field (as shown in the example below). So the supplier deals in feet, but ManEx deals in inches. The conversion between the two are established in the Unit of Measure & Conversion module.
Then the unit price is entered (Price Each). The extended amount is shown, calculated by extending the quantity by price. If the inventory part that you are creating a line item for currently has a standard cost of 0.00 within inventory control the system will prompt the user with the following message, giving the user the option to assign the purchase price to be the standard cost for this item.
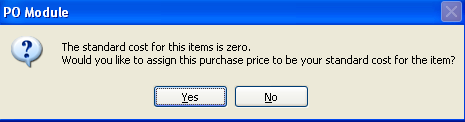
This can not be controlled by the Security level due to the fact that it is better practice to have a $$ assigned to the ICM record before the Purchase Order Receipt is accepted into the system. Otherwise you will have stock that is not valued properly, accounting records that will not be correct, etc. . . . So this is why ManEx allows any Purchase Order user to populate the STD cost field for that record with the purchase $ that you are loading. BUT . . Once a Std Cost is associated with the ICM record - the users within Purchase Order Management should no longer be able to change that value through the PO module.
The user may then indicate that the items are taxable by clicking on the Taxable check box.
The Stock/BOM field will update automatically based upon the conversion table defined in setup. The completed screen should appear as follows:
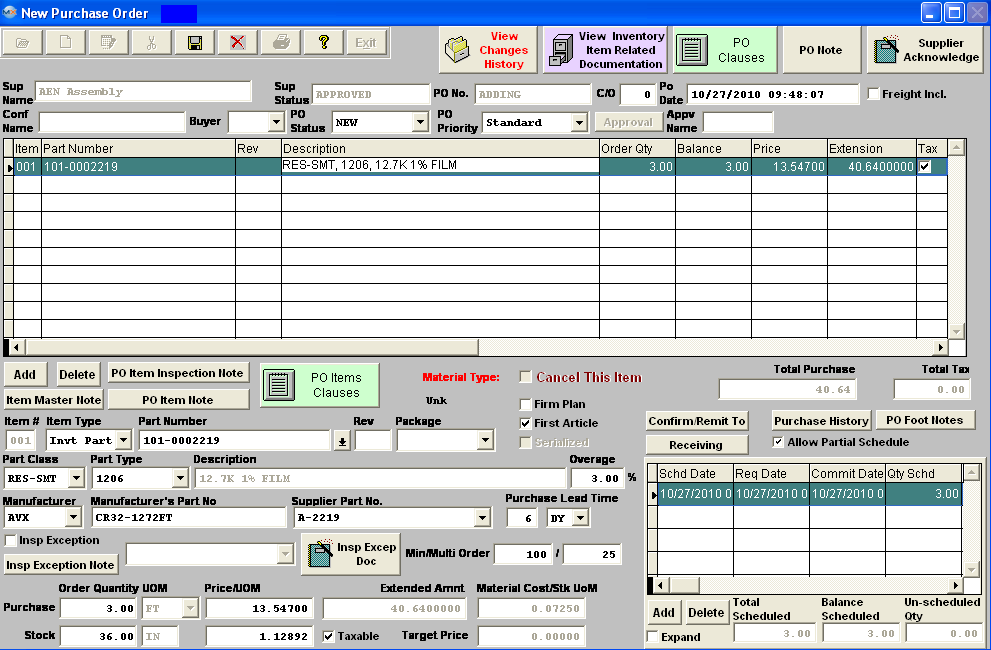
Before saving the order you will need to check the expand box and enter the Schedule detail information.
There are situations when the users will either not enter a schedule or enter a partial schedule at time of creating PO. If the scheduled qty does not match the order qty or the "Allow Partial Schedule" box is unchecked, upon depressing the Save button the following message will be displayed. This gives the user the option to stop the save process and return to the item and schedule or continue on and save without scheduling. Some users may not know an exact date for scheduling at the time of the PO creation and just create the PO to get the part on order. Then upon the supplier response add the scheduled dates to the PO at a later time. This is why we do not enforce the scheduling at the time of the PO creation.
If the "Allow Partial Schedule" box is checked upon saving the PO without a schedule or a partial schedule this message will not be displayed.
Entering Schedule Detail Information
The item will schedule automatically by adding the lead time to todays date and schedule the entire order amount. (Note: MRP will NOT acknowledge qty's that are NOT scheduled).
At this time the user has the option to change the Schd date/Req date/commit date information and also the Qty Schd.
Note: If user is NOT following MRP suggestions when creating POs they need to keep in mind inspection time when entering a schedule for a PO.
If the user wants to modify the automatic scheduled date, they can either manually adjust the Date information by highlighting the field and typing in the new date, or place the cursor in the Due Date field.Type in a ?. A calendar will appear.
Depress the desired delivery date.To advance into the next month, depress the > button.
|
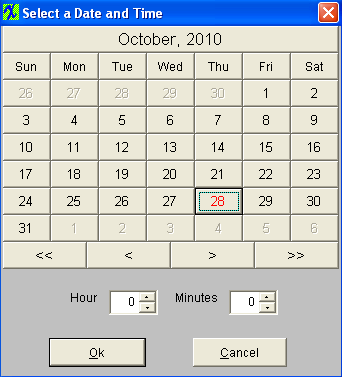 |
Schedule Field Definitions
Schd Date |
The date the material is due to land on the users dock. This is the date MRP uses. |
Req Date |
This is the internally required or desired date. It is not used for the supplier or MRP. |
Commit Date |
The commit date is a reference field for the buyer. |
Qty Schd |
The quantity scheduled for the due date. |
Warehouse |
The User can choose the Warehouse from the pulldown or leave it blank. The "Y" next to the Warehouse indicates that, that Warehouse is set-up in the AVL. The "N" next to the Warehouse indicates that, that Warehouse is NOT set-up in the AVL. If the warehouse field is left blank the user will receive the following message
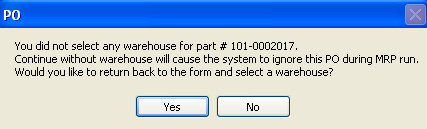
upon saving the record and the user has the option to go back and add the warehouse at this time or leave it blank and assign it at PO Receiving Management. Once the record has been saved within the PO Receiving this information will then be updated within the Inventory Control Management under the Qty info screen.
|
Location |
The Location field will update automatically from the Inventory Control Management module. The user can only edit this field in the scheduling detail if the "Allow Auto Create Location at Receiving" is checked within the ICM module. |
Distribute To |
This is classification of the distribution of the item when received, either to regular Inventory Receiving or to Allocate to Special Work Order or Project |
GL Number |
The General Ledger number where the purchase order will post. |
Schd Notes |
Depressing on the button will bring up a screen where the user can enter in specific notes that pertain to that one schedule, item, and date. Enter in the note. Depress the Save button. Exit. |
Pressing the Save button at the top of the screen saves the order and item(s) entered, and assigns a temporary number to the order. After adding items to the purchase order and saving them, the Purchase Order will display all items added to the order.
The user may use the scroll bars at the right and bottom of the items listed to scroll over additional information.
The user may modify the column widths in the current view by placing the cursor on the right border of the column in the column header, and pressing the left mouse button. Moving the border while holding the mouse button then releasing at the new location resizes the columns.
|
1.1.1.4.2.1.1. Allocate to Special Work Order or Project | Introduction
Inventory Allocation is used to allocate (reserve) quantities of existing items in stock or future Purchase Order deliveries to a Work Order or Project Number. This allocation prevents issuing the quantity reserved to any other use except the Work Order or Project Number specified. Purchase Order Line Item allocations may be removed prior to receipt of the parts by editing the Purchase Order. After receipt of parts allocated by Purchase Order, the allocation may only be removed after the parts are in stock, by using the Inventory Allocation module.
ALLOCATION OF PURCHASE ORDER DELIVERIES
Allocating a PO Line Item is used to make sure that the item will be reserved for a particular Work Order or Project Number when it is received. PO line item allocation is generally used when allocating to a Work Order or Project Number for which the items are not available in stock. Line Shortages of items NOT on the BOM, which are NOT in stock, are an example of typical PO Line Item Allocations. To allocate Purchase Order Line Item Deliveries to a Work Order or Project Number:
- A Work Order or Project Number must be open for the product.
- The Item to be allocated must be entered in the Inventory Control Item Master.
- The quantity allocated must equal the quantity ordered. ie. The total quantity ordered on a line item may be allocated to multiple Work Orders or Project Numbers through the schedule screen.
PROCEDURES
To Allocate a PO Line Item to a Work Order or Project Number:
- Allocate to a new or existing PO.
- Select the desired PO in Article #4557
- Highlight the line item you want to allocate.
- (If it is an existing PO) Depress the Edit action button.
- Expand the Schedule Screen, tab and click on the "Distribute to" field.
- Select WO Alloc or Prj Alloc, enter the Work Order number or Project number to allocate to in the WO # field or Project # field.
- Follow normal PO Mgmt procedures to save and approve.
NOTE:The user may wish to allocate a line item to multiple Work Orders and/or Project Numbers. In the schedule for an item, the user can create as many schedule lines as required. Each schedule line can have a different allocation. If the user had a requirement for 5 Work Orders and/or Project Numbers of 100 parts for each Work Order and/or Project Number, the user would add a line to the PO for 500 parts, then in the schedule, the user can add a line for each Work Order and/or ProjectNumber to which the parts are allocated. The schedule dates can be the same or different. The supplier will see only the total quantity required by the schedule date and is not bothered with the individual allocations.
To Un-allocate a PO Line Item that has not yet been Dock Received:
- Select the desired PO in Article #4557
- Highlight the line item you want to un-allocate.
- Depress the Edit action button.
- Expand the Schedule Screen, tab or click on the "Distribute to" field.
- Select Inv Recv.
- Follow normal PO Mgmt procedures to save and approve.
To Un-allocate a PO Line Item that has already been Dock Received:
-
-
|
1.1.1.4.2.2. MRO Items | MRO stands for Management Required Options. Generally this is used for supplies, etc. purchases.
After selecting the Item Type to be "MRO"
If the MRO item is included in inventory
a. The user may jump directly to the part number box (click on it) and enter a part number. Or, the user may step through the Part Classes and Part Types to narrow
the focus and then select a part from the desired part type.
b. Fill in the quantity and unit price.
If the MRO item is NOT included in inventory
a. The user may enter in a part number manually (or leave blank) and then jump to the description field and enter the description.
The finished screen should look like the screen displayed:
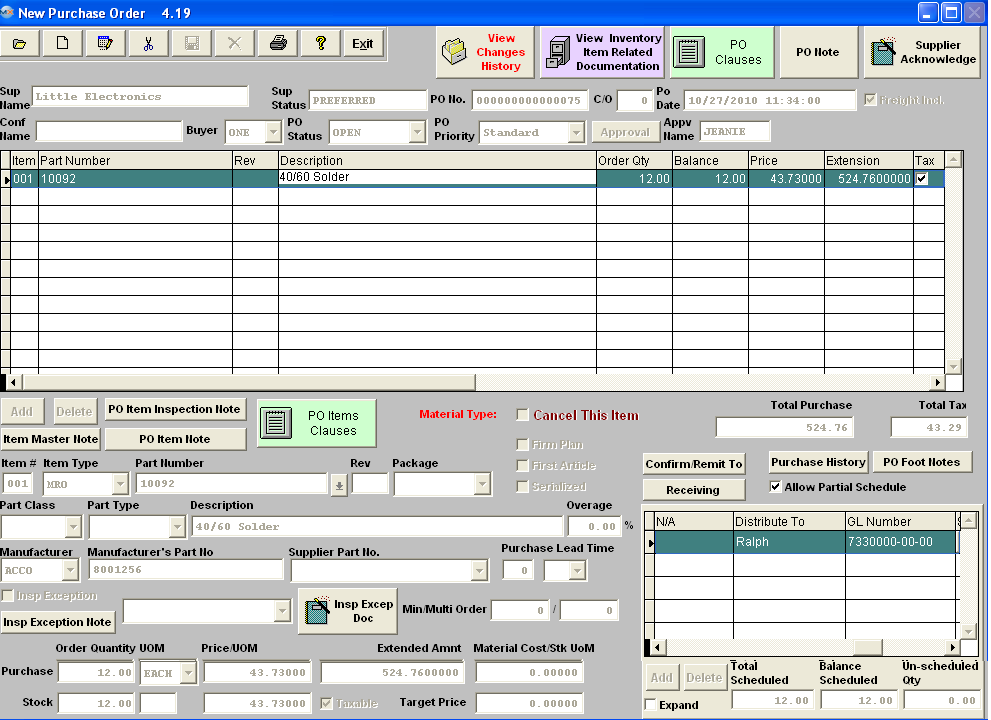
- Check the Expand box in the Schedule screen.
- Enter schedule dates and quantity scheduled.
- Type in the title or name of the person requesting the item in the “Distribute To” field.
- Enter or Select a General Ledger account number in the GL Number field. These GL numbers are defaulted in from the Purchase Setup module.
The completed Schedule screen will appear as follows:
- At the conclusion of entry for the item, the user may depress the Save record action button or the Abandon record action button.
- User must then Approve the Purchase order.
|
1.1.1.4.2.3. Service Items | Service items are for those instances where the assembly is outsourced.
After selecting the Item Type to be "Service"
- The user may enter a Part number manually (or leave blank) and then go to the description field and enter the description.
- Fill in the quantity and unit price.
The finished screen should look like the screen displayed:
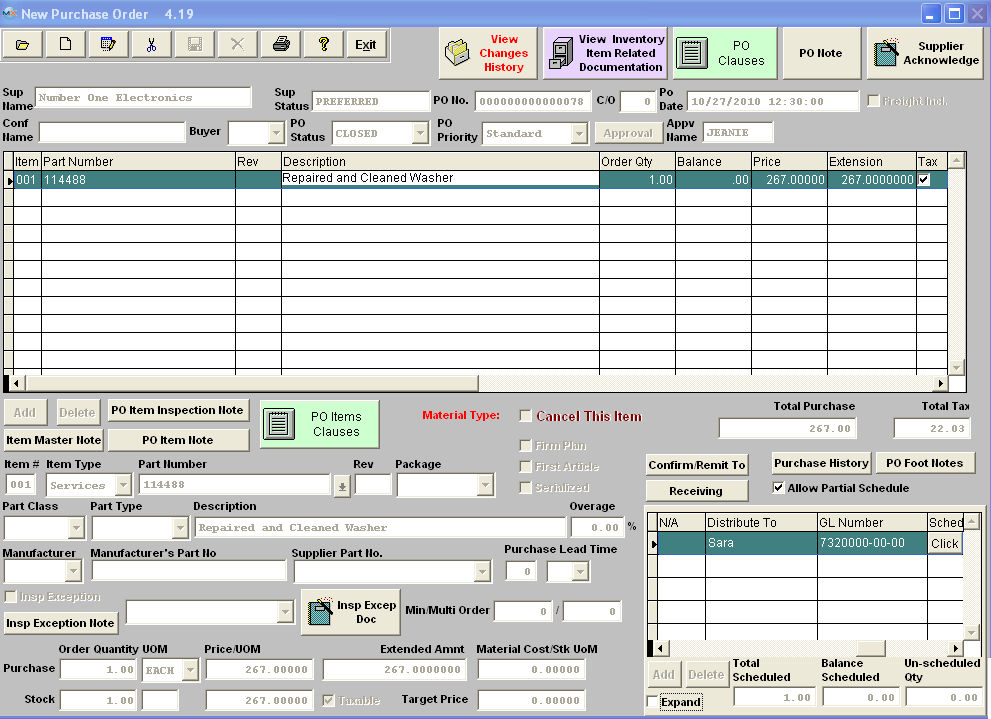
- Check the Expand box in the Schedule screen.
- Enter schedule dates and quantity scheduled.
- Type in the title or name of the person requesting the item in the “Distribute To” field.
- Enter or select a General Ledger account number in the GL Number field. These GL numbers are defaulted in from the Purchase Setup module.
The completed Schedule screen will appear as follows:
- At the conclusion of entry for the item, the user may depress the Save record action button or the Abandon changes action button.
- User must then Approve the Purchase Order. Upon Approval the PO Status will change from Open to Closed.
|
1.1.1.4.3. Edit, Cancel, or Close a Line Item or Purchase Order | Find the Purchase Order that you would like to edit.
Pressing the Edit record action button in the Purchase Order screen will allow the user to modify all the following information:
- The Confirmation Name, Buyer, PO Priority, Supplier Ack., check or uncheck Freight Included box.
- The Status field will only be enabled in the edit mode for users with approval rights. User MUST have approval rights to Modify the PO Status.
- Order quantity and unit price, min/multi qty, purchase lead time, overage amount, Firm Plan or First Article.
- Add or Deletion of a Line Item
- By depressing the Add button allows the user to add additional items to the PO.
- By depressing the Delete button you can delete an existing line Item from the PO, only if there have been no receipts against the line item. If there have been receipts against the line item user will receive the following warning and will not be able to delete the line item.
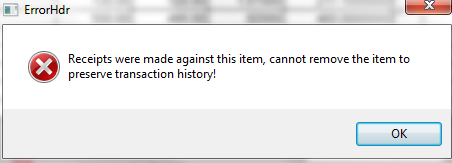
- If there have been no receipts agains the line item, highlight the line item that you wish to delete, then depress the Delete button.
- The user will be asked to validate the deletion before proceeding.
- If you select OK the item will be deleted from the order. Once a line item has been deleted from the Purchase Order user will loose all links and will NOT be able to restore the item.
A user can Cancel a line item rather than deleting the line item from the PO by checking the "Cancel this Item" box.
-
This will allow user to cancel an individual item on a PO. Since the system does not allow you to delete a line item that has had any kind of transaction, we needed a way for users to cancel individual line items without having to cancel the entire order within the system. If any parts have been accepted, it cannot be cancelled. Once a part has any receipts the user cannot delete the line, so if they reject the total received qty they can cancel the line to prevent it from affecting the PO, or PO history for the other line items. If they do not want to reject the entire qty then their only option is to reduce the balance qty to the accepted qty. Cancelled line items will be excluded from the Purchase Order reports within the module. A line item that has been cancelled will be displayed in Red. A cancelled line item will be able to be restored by unchecking the "Cancel this Item" box.
- Information about the terms, FOB, Ship Via, Ship Charge, and Account number, Ship Charge Amount, whether taxable, the tax %
- Schd Date, Requested Date, Commit Date, Quantity Scheduled, Warehouse, Location, Distribute To and Schd Notes.
- Modify or add any information in the Item Master Notes, PO Item Notes, PO Notes, and PO Foot Notes. (Depending on how the user has System Setup/Material/Purchase Setup module marked depends on whether user can edit the notes without going into edit mode on the PO record. If the "Require approvals for Date changes and Notes" is marked as "Yes" then it will force the users to first put the PO in edit mode before they will be allowed to edit any notes and the note changes will be recorded in the "View Changes History" screen. But if it is marked "No" then the notes become editable without the actual record in Edit mode and the note changes will NOT be recorded in the "View Changes History" screen).
Depress the Save record action button after you have finished with editing the record. The user will then need to approve the order. If user has the "Auto Assign new Change Order # Upon Approval" box checked within the System Setup/Material/Purchase Setup module, the reminder will NOT be issued and CO# field becomes NOT editable. When the user approves the change the Change Order number will be automatically increased. If user has the "Auto Assign New Change Order # Upon Approval" box unchecked within the System Setup/Material/Purchase Setup module when user makes changes the CO# will stay the same, the system will prompt the reminder, and user may manually assign a change order number if applicable.

There are situations when an item may not have a schedule or may have a partial schedule. If the "Allow Partial Schedule" box is unchecked within the System Setup/Material/Purchase Setup module, user will receive the following popup warning when editing and saving that line item or any other line item on that same purchase order. If the box is checked the system will not ask any questions when saving a po with only partial schedule. (Note: MRP will NOT acknowledge qty's that are not scheduled).
NOTE: If the "Auto Assign new Change Order # Upon Approval" box is checked, and PO is new and the user goes into the "Edit" mode prior to approval, no changes will be made to the CO# on screen or in the "View Changes History" screen. If PO has been approved and the user goes into the "Edit" mode the next CO# will be referenced in the "View Changes History" screen but will NOT increase on screen until PO has been approved. If the user goes to the "Edit" mode more than once before approving the change the CO# will only increase once in the "View Changes History" screen.
NOTE: If users enter a PO number manually using a "T", then changes the numbering to Auto, and later edits and approves this PO the "T" will be changed to "0". The system has no way of knowing that the PO was manual numbered before the change.
If multiple users are editing the same PO and the PO has not been approved yet, so it still has a temp # and the 1st users approves the PO, while the 2nd user is still making their changes, when the 2nd user goes to exit and save their changes they will receive the following message:
Manex tracks all revisions of a Purchase Order and each receipt against each revision of the order. The system will NOT allow any changes to a Purchase Order which has parts in Dock Receiving that have not yet been processed in the Purchase Order Receiving & Inspection module.
Cancel a Purchase Order
Find the Purchase Order you want to cancel. Press the Edit record action button in the Purchase Order screen this will allow the user to change the PO status from Open to Cancel. Note: User MUST have approval rights to Modify the PO Status.
Closing out a Purchase Order
At times, the user may wish to close out a PO to suppliers who have either shipped short or overages of ordered components. For example, say a user has a Purchase Order for 100 components. 100 units are received with 5 rejections. (See the DMR procedures). This would show the Purchase Order showing a quantity of 5 for a balance. What if the user informs the supplier that they do not want the last 5 pieces.
In the above set of circumstances, the user will be allowed to change the ORIGINAL order quantity by removing the rejected quantity via the DMR procedure. When the Received quantity PLUS the DMR quantity is LESS than the order quantity, the user will be allowed to decrease the order quantity by that many. Original Order 100; Received quantity 100; Rejected quantity 5. Returned to supplier via DMR 5. At this point, the user may reduce the quantity ordered, AND the accompanying amount scheduled to 95. This action will close out the Purchase Order.
The user must depress the Edit button. Change the Purchase Order Quantity, then change the Quantity Scheduled so that the total of the schedule dates exactly equals the new quantity. Depress the Save button. Approve the PO and the PO status will change to close.
|
1.1.1.4.4. Approve a Purchase Order |
Enter the SQLMANEX.EXE (within the ManEx root directory)
This action will then prompt the user for a password
|
 |
The following screen will be displayed, select Material Planning/Purchase Order Management/Purchase Order Management
|
 |
The following screen will be displayed:
Depress the Find record button and follow the Find a PO procedures to find a PO for Approval.
Approve PO
Pressing the Approval button in the Purchase Order module will ask for the user’s password. The user must enter a password that has been authorized (within the Purchase Setup module) to approve the dollar amount of the order.
Entry of an un-authorized password will receive the following message:
|
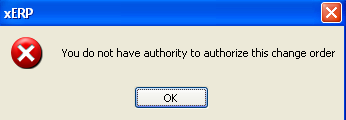 |
Entry of an authorized password and approval will inactivate the 1st approval button and place the initials of the person approving the order next to the approval button , (If in the Purchase Setup , the company has selected to allow one approval of purchase orders). Then upon approval the temporary Purchase Order number will be replaced with a permanent PO number (replacing the "T" with a "0").
If in the Purchase Setup , the company has selected requiring two approvals, then the process must be repeated for the second approval, and the temporary Purchase Order number will be replaced with a permanent PO number (replacing the "T" with a "0") once both approval are granted.
Note: That if the Purchase Order is an Service or In-store order, once the PO has received it’s final approval the temporary Purchase Order number will be replaced with a permanent PO number (replacing the "T" with a "0") and the PO Status marked as closed.
If the user has elected to use manual purchase order number,the screen will prompt the user for an order number to be applied to the purchase order. Note: If users enter a PO number manually using a "T", then changes the numbering to Auto, and later edits and approves this PO the "T" will be changed to "0". The system has no way of knowing that the PO was manual numbered before the change.
|
1.1.1.4.4.1. Load Supplier Acknowledgement |
To attached or Load a Supplier Acknowledge document to a PO
Depress the "Supplier Acknowledge" button and the following screen will appear:
To load images or documents, depress the "Load Document" button, up in the right hand corner of the screen. A browser screen will appear similar to the one below:
Find and highlight the desired Image file, as illustrated.
Once the file name appears, depress the Ok button.
Note: that the user can also load other document types by changing the File of Type to ALL
The file will appear in the screen as displayed:
Depress the Save action button to save the changes or depress the Abandon changes action button to abandon changes. Exit will bring the user back to the Purchase Order Management module and the Supplier Acknowledge button will be displayed in Red as shown below.
|
1.1.1.4.5. Copy "View Change History" Notes | Find the Purchase Order you want to Copy the "View Changes History" notes on.
Depress the "View Changes History" button, When in the “Change PO history” screen, click on the vertical scroll (on your keyboard), you will see the cursor appeared on the top inside the window with the text.
Depress the "CTRL" button + the vertical scroll buttons to highlight the information you wish to copy;
Depress the "CTRL + C" to copy, then paste to a document, e-mail, etc....
|
1.1.1.4.6. Link User Defined Fields to a Purchase Order | The User Defined fields MUST be setup within Web ManEx. For further detail see Article #5454.
The User Defined Fields can
then be linked to Purchase Order or a Purchase Order Item.
To link a UDF to a PO select a record in the ManEx
Desktop, and select the UD action button (as displayed below).
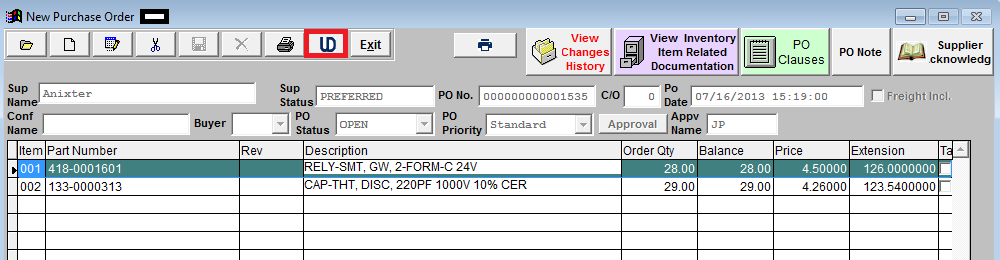
The UDF for that section will
then be displayed, and user can make changes (if applicable), Save & Exit or
Cancel.
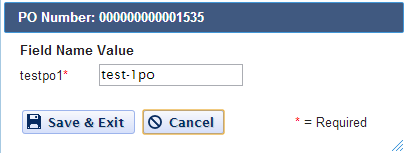
To link a UDF to a Line Item
on the PO select the line item, then select the UD action button that is
located in the PO body (as displayed below)
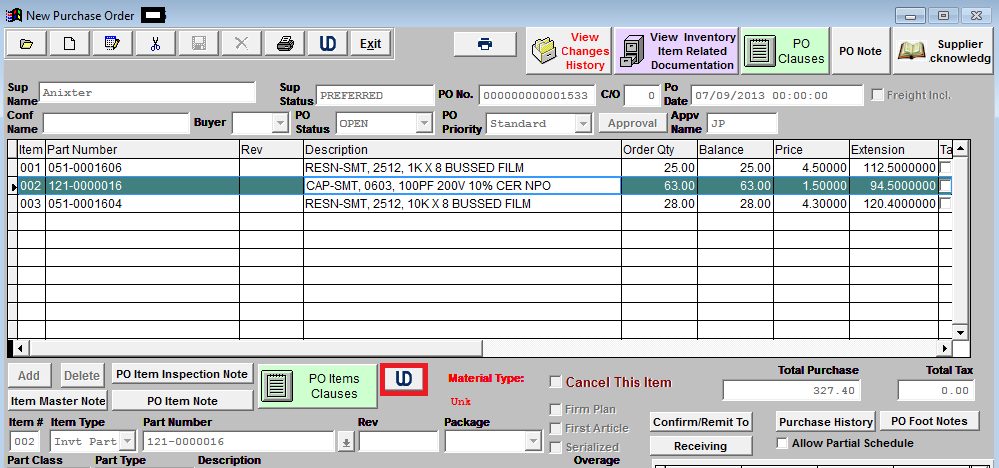
The UDF for that section will then be displayed, and user can make changes (if applicable), Save & Exit or Cancel.
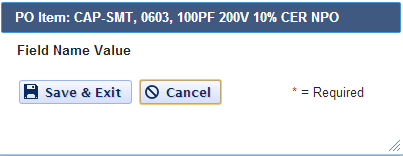
|
1.1.1.5. Reports - PO Mgmt |
To obtain the Purchse Order Reports within the Web, select the WEB Print button from the ManEx action buttons at the top of the screen. For further detail on How the Reports work within the Web refer to Article #5477.
Note: In order to access the Reports within the Web the Company Root URL must be setup within the System Appearance module and user must be linked to web within the System Security Module
Select the Report Type: PO - A List of Reports will be displayed that are available on the Web
for PO
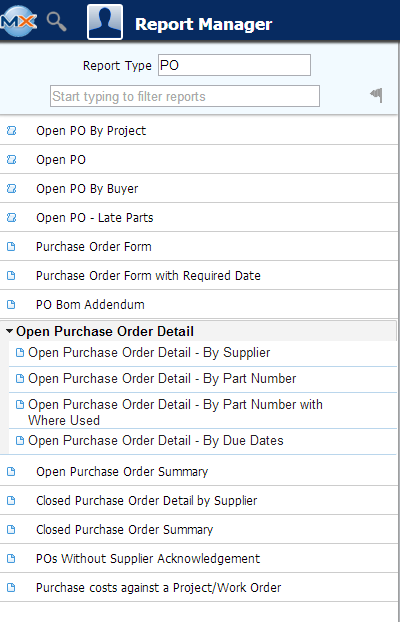
To obtain the Purchase Order Reports within the desktop, select the Print button from the ManEx action buttons at the top of the screen.
The following reports screen
will display a list of reports that are available on the ManEx Desktop:
PURCHASE ORDER FORM report
Select Purchase Order Form and depress the Option tab and the following screen will be displayed:
If you want all line items & scheduled quantities to print, check that box.
Select one of the following options: Unprinted PO, Open PO, Close/Cancel PO, New Orders, Reprint Last Batch, Single PO #, In Store Orders by clicking on the radial.
NOTE: Depending on which one of these options you select will depend on what will be displayed on the report. For Example: If User selects Open/Active the report will have "APPROVED" at the top of the report (as displayed below) and prints out the Purchase Order form AFTER some receiving has occurred against that PO, then ONLY the un-received still open amounts will print on this form. Any line items COMPLETELY RECEIVED or CANCELED will NOT display on the PO form. If User selects Close/Cancel PO the report will have "CLOSED" at the top of the report and will display the original scheduled balance.
Highlight the PO of interest and depress the > button. To select all POs, depress the >> button.
Check the "Show All MPNs for the Parts on the PO" box if you want all MPNs listed on the report.
Check the "Show Item Master Note" box if you would like the Item master notes to be displayed on the report.
Check the "Print BOM Addendum for all "MAKE" parts on the Selected PO" When the users add a Make/Buy part to a Suppliers PO, and checks this option the system will then print a "BOM Indented with AVL" report as an addendum to the PO form. Each BOM will be printed as a separate report and will reference PO and item on the PO. If the AVL on the approve vendor list for any of the items on the BOM happens to be checked as "disallow to buy" this AVL will not be included within the addendum to the PO.
Depress the OK button
When this report is printed is will display the Approval status of the order, it will also display the Supplier Part Number if entered in the ICM module.
-
If purchase order status is "NEW" report will print "NOT APPROVED"
-
If purchase order status is "OPEN" and has been approved, report will display "APPROVED"
-
If purchase order status is "EDITING" meaning order was once approved but now in edit status, the report will display "EDITING PENDING APPROVAL"
|
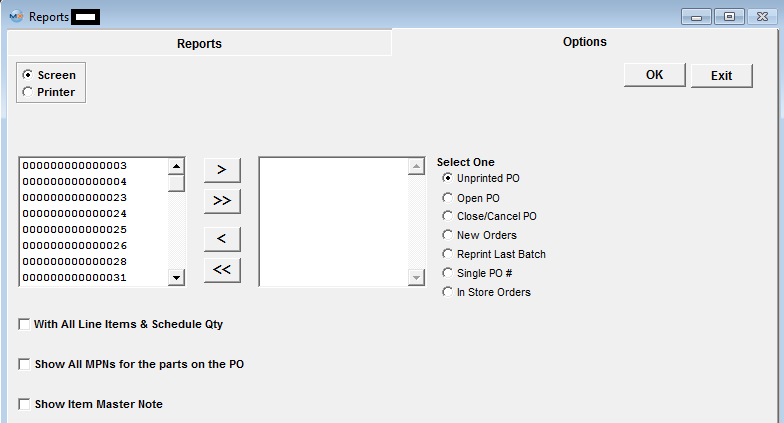 |
The following report will be displayed:
NOTE: If the user prints out the Purchase Order form AFTER some receiving has occurred against that PO, then ONLY the un-received still open amounts will print on this form. Any line items COMPLETELY RECEIVED or CANCELED will NOT display on the PO form.
PURCHASE ORDER FORM with REQUIRED DATE report
This report is exactly the same as the Purchase Order Form report above, except that this report will also show the Required Date information.
User must first enter in a Purchase order Number. Note: If the status is "New" the PO number will still have the "T" in front of it, so the users will be required to enter in the entire PO Number.
Then select "Y" (yes) or "N" (no) to display All Line Items and Schedule Qty's, All MPN's for the parts on the PO, and Show Item Master Notes to print on report. These selections are all defaulted to "N" but can be changed.
Depress the OK button.
This report will display the Supplier Part Number if entered in the ICM module.
|
|
The following report will be displayed:
PO BOM ADDENDUM report
Check the "Print BOM Addendum for all "MAKE" parts on the Selected PO" When the users add a Make/Buy part to a Suppliers PO, and checks this option the system will then print a "BOM Indented with AVL" report as an addendum to the PO form. Each BOM will be printed as a separate report and will reference PO and item on the PO. If the AVL on the approve vendor list for any of the items on the BOM happens to be checked as "disallow to buy" this AVL will not be included within the addendum to the PO.
Enter the desired Purchase Order Number.
Note: If the status is "New" the PO number will still have the "T" in front of it, so the users will be required to enter in the entire PO Number.
Depress OK.
|
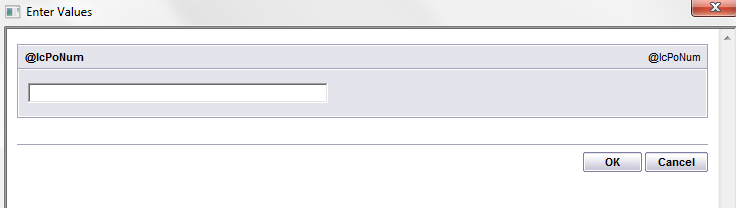 |
The following report will be printed.
OPEN PURCHASE ORDER DETAIL report
At the bottom of the screen, highlight the Detail Report, By Supplier, By Part Number, By Part Number with Where Used or By Due Dates.
Note: If you select ANY of the Detail selects other than “By Supplier” then you can click directly on the OK button and ALL open PO's will be displayed.
The “Open Purchase Order Detail” report shows only items that still have balance. So if you have an open PO with three items and only one of those items have a balance the report will only show the one item with the balance.
|
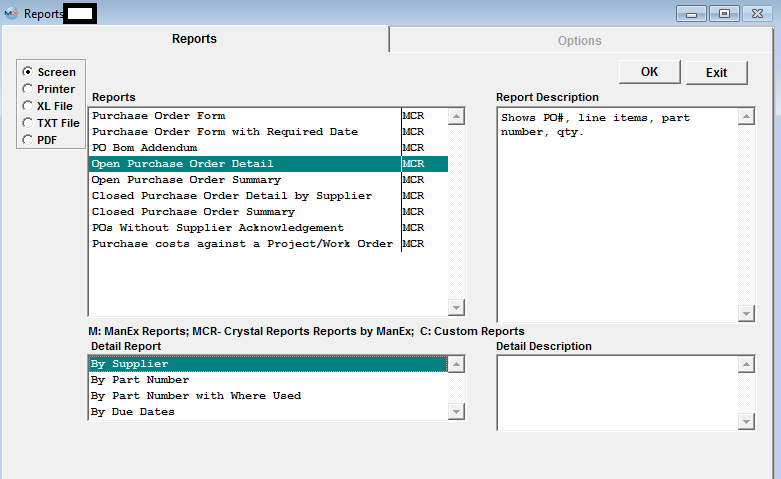 |
If user selects “By Supplier”, the Values screen will be displayed for further options.
Enter the desired Date Range to filter the search more.
Enter a Supplier of interest between the single quotes. If All Suppliers are desired leave '*' Defaulted
Depress the OK button.
|
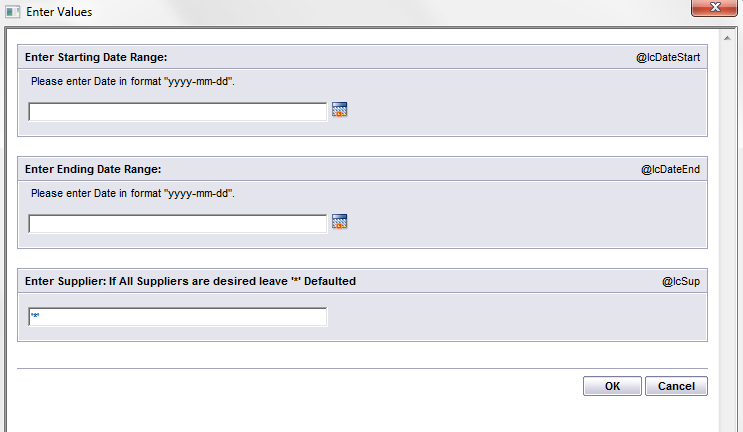 |
The following report will be displayed:
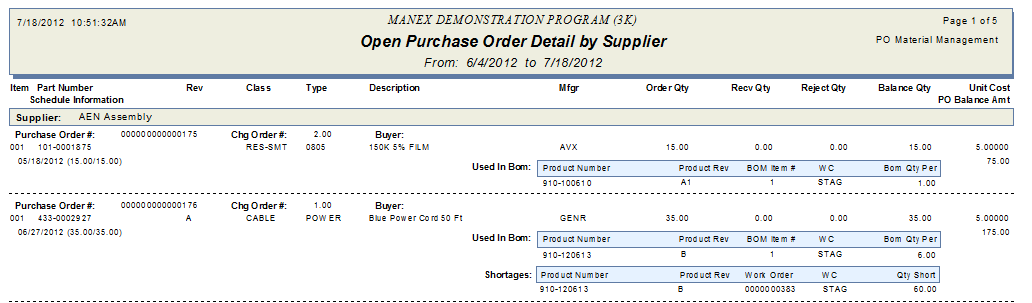
OPEN PURCHASE ORDER SUMMARY report
Enter in the desired Date Range.
Depress the OK button.
The “Summary” report shows all open orders based on the status of the PO. If the open PO has no items with balance left the "Open Purchase Order Detail" report will not show this PO at all, but the "Open Purchase Order Summary "report will.
|
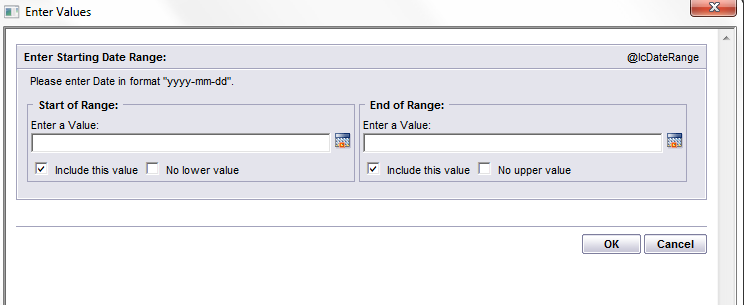 |
The following report will be displayed
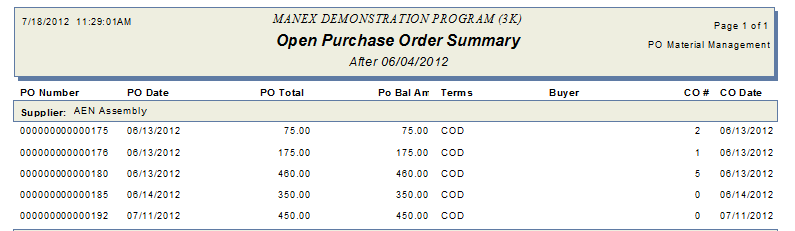
CLOSED PURCHASE ORDER DETAIL BY SUPPLIER report
Enter in the desired Date Range.
Enter a Supplier, If All Suppliers are desired leave '*' Defaulted.
Depress the OK button.
|
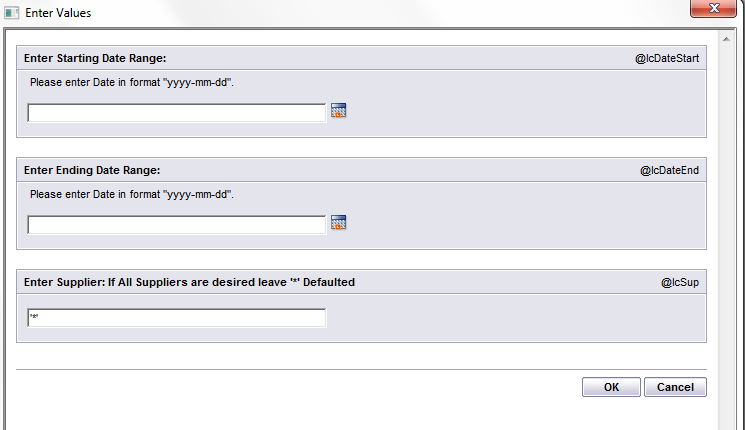 |
The following report will be displayed
CLOSED PURCHASE ORDER SUMMARY report
Enter in the desired Date Range.
Depress the OK button.
|
|
The following report will be displayed
POs WITHOUT SUPPLIER ACKNOWLEDGEMENT report
Select one of the Group By options: Supplier, PO Date, Earliest Schedule Date
Depress the OK button.
|
|
The following report will be displayed
PURCHASE COSTS against a PROJECT/WORK ORDER report
Select Project # or Work Order
Enter a Record # or If All Prj's/Wo's are desired leave '*' Defaulted
Depress the OK button.
|
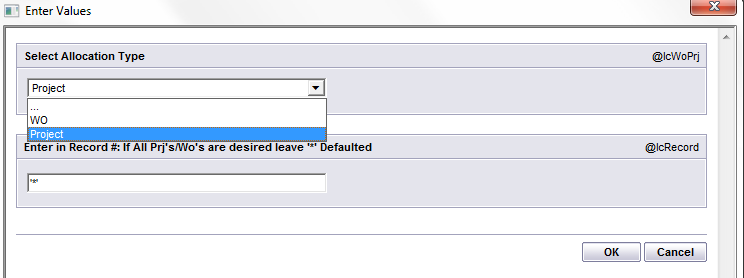 |
The following report will be displayed
|
1.1.1.6. FAQs - PO Mgmt | Facts and Questions for the Purchase Order Module |
1.1.1.7. ManEx Minutes (PO) |
1.1.2. Supplier Line Card Information |
Enter the SQLMANEX.EXE (within the ManEx root directory)
This action will then prompt the user for a password
|
 |
The following screen will be displayed, select Material Planning/Purchase Order Management/Supplier Line Card Information
Note: After activation, "Supplier Information" access for each user must be setup in the ManEx System Security module. Users with “Supervisor Rights” will automatically have access.
|
 |
The following screen will be displayed. The Supplier Status, and Purchase Type are defaulted in from the Supplier Information module.
The user has the option to drill down to the Supplier level to View Supplier Information by double clicking on the Supplier name and the screen below will be displayed.
The user also has the option to drill down to the PO level and view the last Purchase Order by double clicking in the "Last Purchase PO Number" field.
To Add a Class to a Supplier, highlight the desired supplier. Depress the Edit action button.
Then enter the Part Class tab. The following screen will be displayed:
Highlight the desired Part Class. Depress the > button. The selected Class will then populate the selection box to the right.
Depress the Part Manufacturer tab.The following screen will be displayed:
Highlight the desired Part Manufacturer.Depress the > button. The selected Manufacturer will then populate the selection box to the right.
Depress the Save record action button.
Depress the Supplier Lookup tab. The following screen will be displayed:
Enter the Part Class and the Part manufacturer. Depress the Search button. The name of the associated Supplier(s) will appear in the Supplier List section.
|
1.1.3. Upload New Purchase Orders |
1.1.3.1. Prerequisites for New PO Upload |
After activation, "PO Import" access for each user must be setup in the ManEx System Security module. Users with “Supervisor Rights” will automatically have access.
User has to complete the required fields in the PoUploadTemplate.xlt in the xlfiles directory to create <st1:place w:st="on">PO upload XL file.
If user wants the system to automatically approve all the POs uploaded the "Auto Approve PO when importing from XL" box must be checked in the Purchase Setup module. If this is NOT checked in the Purchase Setup module then all the POs will be uploaded as "NEW" and users will be required to approve within the Purchase Order Management module.
|
1.1.3.2. Introduction for New PO Upload | This module gives our users the capability to take electronic files provided by the suppliers from quote and availability of items, copy and paste that information into the ManEx PO Upload template format. Users will have the flexibility to load a large PO into the system all at once, or upload multiple purchase orders for different suppliers at once, etc. During the upload process the system will find any problems with the template, the user will be prompted and exception XL files will be created within the POExceptionXL directory for the users to review and disposition.
|
1.1.3.3. Fields and Definitions for New PO Upload |
1.1.3.3.1. PO Upload Template | 
Ponum |
Required field: If Auto PO numbering is setup: Even though user has the PO's set to auto, you can NOT upload a PO without something in this column. Something has to be entered in this column so the system can distinguish one po line item from another PO line item on a different PO. If there is no data in this column the program will think the rest of the spreadsheet is also blank. PO Upload will group per change in Ponum field (it will then use the Ponum field as a reference to change) when uploaded user will receive a message that the PO number entered in XL spreadsheet will be overwritten by a system generated number ... and give you the option to continue the upload or abort. If manual PO numbering is setup: PO Upload will group per change in Ponum field (it will then use the Ponum field as a reference to change) when uploaded system will use PO numbers entered in XL spreadsheet. |
Supname |
Required field. Existing Supplier Name in ManEx System. If it does not exist the user will be prompted and an exception XL file will be created in the POExceptionXL directory on the server. |
Terms |
Optional: If left blank it will take the default from the supplier setup. User may manually enter in a supplier term that does not match the Supplier Setup information, but must exist within the System Setup. |
Buyer |
Optional: Buyer entered must Exist in System Setup. If it does not exist the user will be prompted and an exception XL file will be created in the POExceptionXL directory on the server. |
Shipping Charge |
Optional: If left blank it will take the default from the Receiving & Billing Information setup. User may manually enter in a Shipping Charge that does not match the Receiving & Billing Info Setup information, but must exist within the System Setup. |
Shipping Tax |
Optional If left blank it will take the default from the Receiving & Billing Information setup. User may manually enter in a Shipping Charge that does not match the Receiving & Billing Info Setup information, but must exist within the System Setup . |
Shipping Charge |
Optional: (Example: "PREPAY & BILL", "NO-CHARGE", etc) |
FOB |
Optional: If left blank it will take the default from the Receiving & Billing Information setup. User may manually enter in a FOB that does not match the Receiving & Billing Info Setup information, but must exist within the System Setup. |
Ship Via |
Optional: If left blank it will take the default from the Receiving & Billing Information setup. User may manually enter in a ship Via that does not match the Receiving & Billing Info Setup information, but must exist within the System Setup. |
Include Freight Cost? |
Optional: Can enter Y or N or leave blank |
PO Line Item Number |
Required field |
MRO or Invt Part |
Required field |
Part Number |
Required field: If entering Inventory Part Number, it must exist in ManEx. If it does not exist the user will be prompted and an exception XL file will be created in the POExceptionXL directory on the server. |
Part Revision |
Required field |
Package |
Optional: This gives the user to enter in a package type that exists in System Setup. If this column is left blank the "Package" field in the PO will be populated with the default in System Setup. If the user enters a package type that does NOT exists in the system setup, the use will receive a prompt and the XL file will be created for them to review. They will also have a choice to continue and fill the missing package information from inventory or cancel and fix the XL file. |
Cost each Purchasing Unit |
Required field |
Tax-pct |
Optional: If left blank it will take the default from the supplier setup. User may manually enter in a Tax-pct that does not match the Supplier Setup information, but must exist within the System Setup. |
Manufacturer |
Required field: Manufacturer must exist in ManEx and match the ICM AVL for the part that is being uploaded. If it does not exist the user will be prompted and an exception XL file will be created in the POExceptionXL directory on the server. |
Manufacturer Part Number |
Required field: Manufacturer Part Number must exist in ManEx and match the ICM AVL for the part that is being uploaded. If it does not exist the user will be prompted and an exception XL file will be created in the POExceptionXL directory on the server. |
Firm PO? |
Optional |
First Article |
Default from Item Master |
Inspection Exception? |
Optional |
Exception |
Optional |
Date Required |
Required field: You can have a order qty of 1000 and have 200 scheduled out of 5 different days. |
Quantity Required (Purchase Unit of Measure) |
Required field: Purchase Unit of Measure must exist in System Setup. If it does not exist the user will be prompted and an exception XL file will be created in the POExceptionXL directory on the server. |
Warehouse |
Required field: (if Invt Part) Warehouse must exist in ManEx and match the ICM AVL for the part that is being uploaded. If it does not exist the user will be prompted and an exception XL file will be created in the POExceptionXL directory on the server. |
Warehouse Location |
Optional: (if warehouse entered)
If Auto Location Creation is not Enabled in system setup:
• And template has a WHSE that does exist on the ICM AVL for that part the upload will complete
• And the template has a Location that does exist on the ICM for that part the upload will complete
If Auto Location Creation is enabled
• And template has a Whse that does not exist on the ICM for that part, the upload will continue AS LONG AS that WHSE exist within your Whse setup.
• And template has a Location that does not exist on the ICM. The upload will complete.
|
Allocated to WO Number |
Optional: The system will do a check to make sure that the WO number exists within the ManEx System. If it does not exist the user will be prompted and an exception XL file will be created in the POExceptionXL directory on the server. |
Allocated to Project Number |
Optional: The system will do a check to make sure that the Prj number exists within the ManEx System. If it does not exist the user will be prompted and an exception XL file will be created in the POExceptionXL directory on the server. |
Requestor if MRO |
Required field: (if MRO item) If this field is not populated the user will be prompted and an exception XL file will be created in the POExceptionXL directory on the server. |
GL Number |
Required field: (if MRO item) The system will do a check on the GL number to make sure that it not only exists in the Accounting setup, but also has to exist on the MRO Purchase GL number section within the Purchase Setup module. If it does not exist the user will be prompted and an exception XL file will be created in the POExceptionXL directory on the server. |
|
1.1.3.4. How To ....... for New PO Upload |
1.1.3.4.1. Add - Upload a New PO |
Enter Material Planning/Purchase Order Management/Upload New Purchase Orders
NOTE: If user wants the system to automatically approve all the POs uploaded the "Auto Approve PO when importing from XL" box must be checked in the Purchase Setup module. If this is not checked in the Purchase Setup module then all the POs will be uploaded as "NEW" and users will be required to approve within the Purchase Order Management module.
|

|
Locate XL File to Upload
|
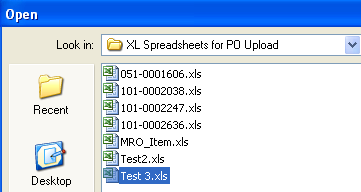 |
If the system finds any problems with template the user will be prompted the following message and PoUploadErrors.xls file and a Validation.xls file will be created in the PoExceptionXL folder within the ManEx directory.
|
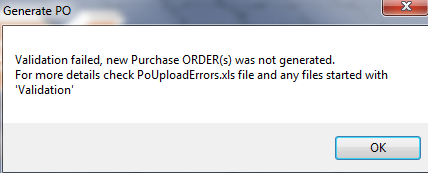
|
If any of the information is missing from the required fields in the first row of the XL file, user will receive the following message.
Depress OK and user will receive the message (shown below) that the "PO Upload was not complete" and system will abort.
Note: Even though user has the PO numbering set to auto, you can NOT upload a PO without something in the Ponum column and all other required fields. Something has to be entered in this column along with all other required fields so the system can distinguish one po line item from another PO line item on a different PO. If there is no data in this column or the other required fields the program will think the rest of the spreadsheet is also blank. PO Upload will group per change in Ponum field (it will then use the Ponum field as a reference to change) when uploaded user will receive a message that the PO number entered in XL spreadsheet will be overwritten by a system generated number ... and give you the option to continue the upload or abort (as shown below). If manual PO numbering is setup and Auto Approve: PO Upload will group per change in Ponum field (it will then use the Ponum field as a reference to change) when uploaded system will use PO numbers entered in XL spreadsheet. If manual PO numbering is setup but Auto Approve is NOT selected then PO upload will assign a temporary PO number until <st1:place w:st="on">PO is approved manually. At that time you will be prompted for the manual <st1:place w:st="on">PO number.
|
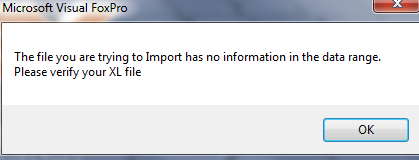
|
The user will be prompted the following message that the PO Upload was not complete and system will abort. |
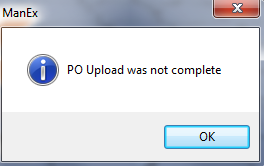 |
If system does NOT find any problems with the template the following message will appear: This message is for user to verify the number of records being loaded from the import sheet. User may depress "YES" to continue the upload or "NO" to abort the upload.
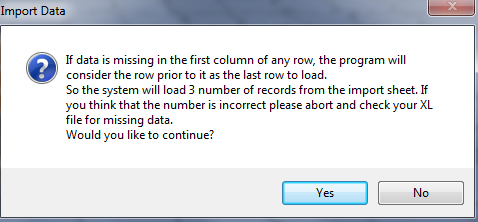
If you depress Yes to Continue the user will be prompted the following message that the PO Upload complete. |
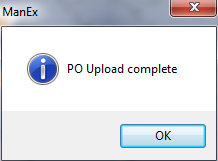
|
If you depress No to Abort Upload the user will be prompted the following message that the PO Upload was not complete. |
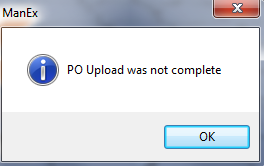
|
|
1.1.4. Upload PO Items Additions |
1.1.4.1. Prerequisites for PO Upload Addtions |
After activation, "PO Import" access for each user must be setup in the ManEx System Security module. Users with “Supervisor Rghts” will automatically have access.
User has to complete the PoItemsAddTemplate.xlt in the xlfiles directory to create <st1:place w:st="on">PO Items Deletions upload XL file.
If user wants the system to automatically approve all the POs after the "Upload PO Items Additions" the "Auto Approve PO when importing from XL" box must be checked in the Purchase Setup module. If this is not checked in the Purchase Setup module then all the POs will be updated with the PO Items Additions and the PO status will be changed to "EDITING" and users will be required to approve the PO within the Purchase Order Management module.
If user wants the system to automatically assign a new change order number upon upload after approval the "Auto Assign New Change Order # Upon Approval" box must be checked in the Purchase Setup module. If this is not checked in the Purchase Setup module then upon upload user will receive a popup window giving them the option of updating the change order # after the upload or not. |
1.1.4.2. Introduction for PO Upload Additions | This module will allow users to upload additional items to an existing PO.
|
1.1.4.3. Fields and Definitions for PO Upload Addtions |
1.1.4.3.1. Upload PO Items Additons | 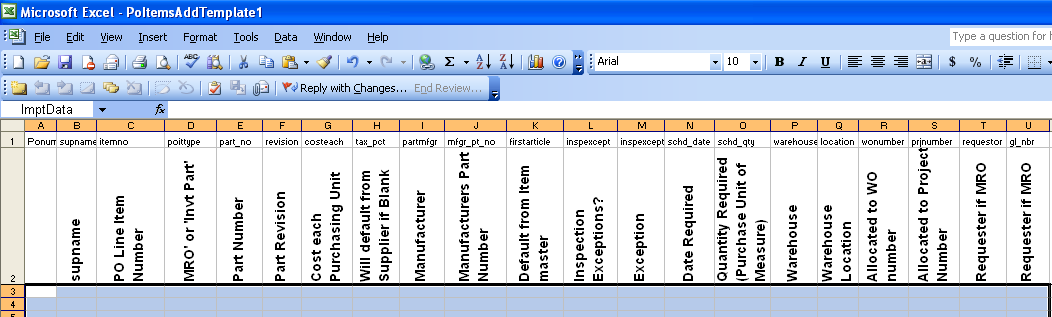
Ponum |
Required field Enter existing PO number, user wants to add items to. |
Supname |
Required field Supplier Name on existing PO in ManEx System. If it does not exist the user will be prompted and an exception XL file will be created in the POExceptionXL directory on the server. |
PO Line Item Number |
Required field Assign a line item number to the item that is being added (cannot be a duplicate) |
MRO or Invt Part |
Required field Must enter "MRO" or "Invt Part" cannot enter just "Invt or Inventory" must be "Invt Part" |
Part Number |
Required field: If enterning Inventory Part Number, it must exist in ManEx. If it does not exist the user will be prompted and an exception XL file will be created in the POExceptionXL directory on the server. |
Part Revision |
Required field If a revision exists |
Cost each Purchasing Unit |
Required field Enter a Cost each |
Tax-pct |
Optional: If left blank it will take the default from the supplier setup. User may manually enter in a Tax-pct that does not match the Supplier Setup information, but must exist within the System Setup. |
Manufacturer |
Required field: Manufacturer must exist in ManEx and match the ICM AVL for the part that is being uploaded. If it does not exist the user will be prompted and an exception XL file will be created in the POExceptionXL directory on the server. |
Manufacturer Part Number |
Required field: Manufacturer Part Number must exist in ManEx and match the ICM AVL for the part that is being uploaded. If it does not exist the user will be prompted and an exception XL file will be created in the POExceptionXL directory on the server. |
First Article |
Default from Item Master |
Inspection Exception? |
Optional |
Exception |
Optional |
Date Required |
Required field: You can have a order qty of 1000 and have 200 scheduled out of 5 different days. |
Quantity Required (Purchase Unit of Measure) |
Required field: Purchase Unit of Measure must exist in System Setup. If it does not exist the user will be prompted and an exception XL file will be created in the POExceptionXL directory on the server. |
Warehouse |
Required field: (if Invt Part) Warehouse must exist in ManEx and match the ICM AVL for the part that is being uploaded. If it does not exist the user will be prompted and an exception XL file will be created in the POExceptionXL directory on the server. |
Warehouse Location |
Optional: (if warehouse entered)
If Auto Location Creation is not Enabled in system setup: • And template has a WHSE that does exist on the ICM AVL for that part the upload will complete • And the template has a Location that does exist on the ICM for that part the upload will complete If Auto Location Creation is enabled • And template has a Whse that does not exist on the ICM for that part, the upload will continue AS LONG AS that WHSE exist within your Whse setup.
• And template has a Location that does not exist on the ICM. The upload will complete.
|
Allocated to WO Number |
Optional: The system will do a check to make sure that the WO number exists within the ManEx System. If it does not exist the user will be prompted and an exception XL file will be created in the POExceptionXL directory on the server. |
Allocated to Project Number |
Optional: The system will do a check to make sure that the Prj number exists within the ManEx System. If it does not exist the user will be prompted and an exception XL file will be created in the POExceptionXL directory on the server. |
Requestor if MRO |
Required field: (if MRO item) If this field is not populated the user will be prompted and an exception XL file will be created in the POExceptionXL directory on the server. |
GL Number |
Required field: (if MRO item) The system will do a check on the GL number to make sure that it not only exists in the Accounting setup, but also has to exist on the MRO Purchase GL number section within the Purchase Setup module. If it does not exist the user will be prompted and an exception XL file will be created in the POExceptionXL directory on the server. |
|
1.1.4.4. How To ............. for PO Upload Additions |
1.1.4.4.1. Add - Upload PO Items Additions |
Enter Material Planning/Purchase Order Management/Upload PO Items Additions
NOTE: If user wants the system to automatically approve all the POs after the uploaded is complete the "Auto Approve PO when importing from XL" box must be checked in the Purchase Setup module. If this is not checked in the Purchase Setup module then users will be required to approve within the Purchase Order Management module.
|

|
Locate XL File to Upload
|
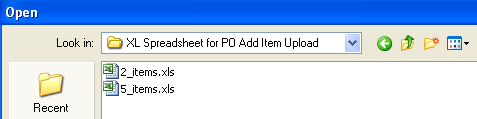 |
If the system finds any problems with template the user will be prompted the following message and exception XL file will be created in the PO Exception XL directory on the server.
Depress OK and user will receive the message (shown below) that the "PO Upload was not complete" and system will abort.
|
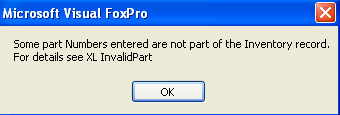 |
If any of the information is missing from the required fields in the first row of the XL file, user will receive the following message.
Depress OK and user will receive the message (shown below) that the "PO Upload was not complete" and system will abort.
|
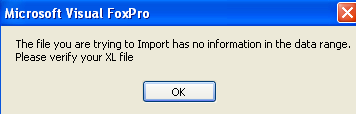 |
If part being uploaded has the "Disallow this part from Purchasing" box checked within the Inventory Control Mgmt module, this message will be displayed and PO upload will not complete. |
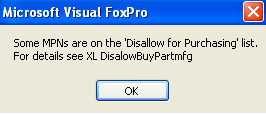 |
The user will be prompted the following message that the PO Upload was not complete and system will abort. |
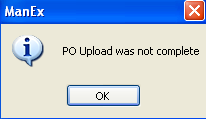 |
If system does not find any problems with the template and system is setup to Auto create PO Numbers the following message will appear: This message is for user to verify the number of recorrds being loaded from the import sheet. User may depress "YES" to continue the upload or "NO" to abort the upload.
If you depress Yes to Continue the user will be prompted the following message that the PO Upload complete. |
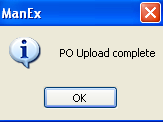 |
If you depress No to Abort Upload the user will be prompted the following message that the PO Upload was not complete. |
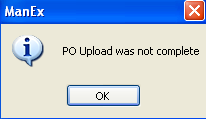 |
|
1.2. Material Requirement Planning (MRP) |
1.2.1. Prerequisties for MRP |
Prerequisites Required for Entering a New MATERIAL REQUIREMENTS PLANNING:
After activation, "Material Requirements Planning" (MRP) access for each user must be setup in the ManEx System Security module. Users with “Supervisor Rights” will automatically have access.
Customer |
The Customer database must be established for Consigned part numbers. |
Part number in Item Master |
The part number must exist for a product or part. |
AVL |
The Manufacturer Names must exist when using the AVL in the Bill Of Materials. |
MRP Policies |
The Material Requirements Planning policies should exist for each product or part in Inventory Control. |
|
1.2.2. Introduction to MRP | The Material Requirements Planning (MRP) Module is the heart of Inventory Control. In ManEx, the Material Requirements Planning actions drive the user towards zero inventory on hand through the scheduling and rescheduling of open orders for products and parts.
When the Material Requirements Planning module runs, it accumulates all of the demands for products and parts, determines the available supply and recommends actions to be taken to meet the demand in the time required. (The attached Print Screens below <<BOM_Setup_MRP_Actions.docx>> displays an example of a BOM setup and how MRP gives the actions). The MRP module will also modify those recommendations by MRP policies established in the MRP Default Setup and in the Inventory Control Mgmt MRP Info for each part. MRP runs through a large number of tables and records to compile its calculations, and provides a snapshot of suggested actions at the same time it is ran. If users are changing things during this process it could definitely cause some strange outcome. To prevent this situation we strongly suggest that you use the Nightly MRP trigger. (Refer to Article #416 for more detail on trigger setup). Note: If you find the need to re-run MRP during the production work day then we suggest that you notify all departments that MRP is going to be ran and ask them to remain out of the system until the MRP run is complete. This will help assure that the most accurate MRP run is possible.
Run Scrap and Setup Scrap
If the Top Level Assembly has a run scrap and user would like MRP to calculate this run scrap in the demands for all parts on the BOM, it must be set up in the MRP Defalut Setup Screen.
If the user has scrap setup in the Inventory Control module and wants MRP to calculate it they must set it up in MRP Defalut Setup Screen. Note: If this field is changed it will update the setting in the Kit Default Setup and visa versa.
If the user wishes for the setup scrap qty’s to be included in the Kitting and MRP calculations, the Setup Stcrp box MUST be checked on the BOM. Checking this box along with a Standard Bld qty will tell the system to use Setup Scrap when calculating the standard cost. Note: The "Exclude Scrap & Setup Scrap" options within the Kitting Setup module will overwrite this option.
All lead times are calculated with the Production Calendar.
Policies may be used to determine whether the part is ordered on a Lot for Lot basis, on a Daily basis, Weekly, Semi-Monthly, Monthly, or quarterly basis. (Refer to Article #3032 for further detail on how the AVL Pref Codes affect MRP based on the Order Policy). The part may have minimum and multiple order quantities that influence the recommendations. Note: If the Order Policy happens to be left blank within the Inventory Control module, MRP will enforce the Order Policy of "Lot to Lot". If the Stock UoM is different than the Purchase UoM MRP will instruct you to Purchase the Stock qty UoM, not the Purchase UoM.
NOTE: When creating a PO for an item with different purchasing and stocking UoMs, be sure to enter the MRP suggestion into the Stocking qty field rather than the purchasing qty field. The system will automatically convert the stocking unit into the purchasing unit for the purchase order qty.
For example if the buyer is creating a PO for an item that is used by inches but sold by the foot, the user would enter qty of 24 into the stocking qty field and the PO would automatically convert it to 2 feet in the purchasing qty field. So the supplier deals in feet, but ManEx deals in inches. The conversion between the two are established in the Unit of Measure & Conversion module.
Article #3597 explains the process MRP goes through to optimize the On-Hand Inventory to Demands.
Buffer times for placing purchase orders and for placing work orders may be defined and included.
The Dock to Stock value (setup in the ABC types ) is taken into consideration for MRP leadtime calculations in the projected requirement of the receipt of purchased parts. (For more detail refer to Article #1469).
If a part has a Production Off-set time setup in the Bill of Materials , this is also taken into consideration for MRP leadtime calculations. (For more detail refer to Article #572).
The Material Requirements Planning module will run the Master Production Schedule generation automatically before running the Material Requirements Planning module.
ManEx Material Requirements Planning module may be run without logging users off the system. The work station used to run Material Requirements Planning should have at least 120MB available on the hard drive, and works best with 96MB memory or more.
A Material Requirements Planning regeneration creates time-phased material requirements at the part (component) level by netting demand from the Master Production Schedule (MPS), open Sales Orders, Internal orders, Shortages and open Work Orders (released but not picked) against supply from inventory, open purchase orders and Finished Goods.
The regeneration must also occur with demand synchronized: Master Production Schedule forecasted demand that has been consumed by Sales Orders should be relieved and Work Orders that are released but not picked should be picked or cancelled.
MRP Actions for Make/Phantom parts - If the actions originates from a higher level assembly for the Make/Phantom, then the MRP will display "Phantom" in the action section. This indicates to the user that there are no actions required and is listed so users can investigate where component actions are originating from. If the Make/Phantom is required directly for an Order itself, it will follow the same WO action rules as a regular Make product.
Planned Purchase Orders from previous demand that have been placed must be entered and/or firmed.
A Firm Planned Purchase Order tells MRP that the purchasing decision was intentional and MRP will NOT try to override.
Discrepant material should either be moved into Material Review Board or Inspection Hold for disposition. If Material Review Board or Held material is not to be looked at as available material for Material Requirements Planning purposes, it should be in a Non-nettable warehouse or inventory location. For example: (If parts are rejected in PO receiving the parts are dispositioned into the MRB warehouse (which is Non-nettable) so MRP is not seeing the qty in MRB but is seeing the open PO). Transactions must be current with the location of materials. WIP (Work In Process) shrinkages must be expressed as Work Order shortages in the system.
MRP is designed to calculate from the Kit Shortage and not from the Lead times once the parts have been pulled to the kit and the kit status is changed to "Kit in Process". Once the parts have been pulled to the kit, the systems is assuming that the shortages are needed by the WO due date, rather than the Prooduction lead time, so MRP then calculates using the due date of the WO as the date the materials must be on hand, MRP no longer takes the production lead time into consideration.
NOTE: The Re-Order Point/Qty fields have NO AFFECT on MRP at all. MRP will NOT consider these fields for any calculations (these fields have no connection with MRP). These fields are intended to control stock on overhead items. Print the "Inventory Material Reorder List" report (located in the Inventory Control module) to show items which have dropped below re-order point minimums.
MATERIAL REQUIREMENTS PLANNING PROCESS
Confirm status of system data for Material Requirements Planning validity
Updated Forecast and Master Schedule
Updated Item Master file data
Lead Times entered and up to date
Shrinkage factors current
Order policies set
Orders firmed as required
Independent Demand items identified
Inventories current
Receivings current
Safety Stocks appropriate
Bills of Material current and complete
Confirm system availability to run Material Requirements Planning
Timing good for snapshot of data
Transactions current
Set the parameters for running the Material Requirements Planning
Netable Inventory Locations flagged
Discrepant material dispositioned
Horizon set
Time fences set for change control
Bucket size and number set
When executed, the Material Requirements Planning Module takes a snap-shot of the demand for parts and assemblies (created by Sales Orders, Work Order Shortages, Forecasts) and compares it with supply (on-hand inventory, open Purchase Orders with scheduled qty, open Work Orders) in order to generate an Action List of planned new orders and changes to existing ones to meet demand. The comparison is done one day at a time using the make and/or buy parameters from the Item Master/Material Requirements Planning Information screen in Inventory Control Management.
The Parameters include:
· Order Policy
· Minimum Order Quantity
· Order Multiples
· Purchase Lead Time
· Kitting Lead Time
· Transit Days
· Pull In Days
· Push Out Days
If the AVL suggested to the PO actions is flagged as "DO NOT PURCHASE" MRP will give Release PO actions if there is a need for the part and the part will be displayed on the Create PO screen with the Mfgr and MPN fields blank. This should flag the user to further investigate and see that it is flagged as "DO NOT PURCHASE" and that they will need to either remove the flag or add additional AVL's to ful-fill the demands. Notice at the top there is a note that explains what the empty "MFGR" field means.
Sales Orders on Hold
When the Sales Order is on HOLD it does NOT drive MRP.
User does have the ability to turn off the function of the Sales order driving the demands for the MRP and just use the Work Order for buying components by checking the MRP on Hold box in the Sales Order module per line item or in the System Setup/Sales Order Default module.
If the MRP on Hold is checked in the SO module, MRP will instruct you to cancel all PO(s) you have open for the components needed for this SO.
If the MRP on Hold is checked in the SO module and you create a WO Manually, the MRP will tell you to cancel the WO since there is no SO demand. This can be solved one of two ways.
Use the MPS module (Forecast) or Open/Create Firm planned WO’s so the MRP will NOT keep instructing you to cancel the order.
This is a perfect solution for customer who wants to build products based on forecast or promised to maintain certain amount of FGI in inventory. The can use the MPS module to accomplish this and use the SO to ship products from FGI inventory.
MRP will consider any SO items for the demands unless marked as MRP on Hold. See Article #1244 for further information.
Check on Work Orders on either Admin or Production hold. Production Hold on a Work order will disallow movement of the parts. See Article #896 for more detail. MRP is checking work orders to be sure that they aren’t cancelled or closed. Everything else will be considered. MRP checks Sales Orders for OPEN status. Everything else is ignored. If the objective is to stop the shipment from the Sales Order, then in the Sales Order, the user may uncheck the “Sales Ack” box and then shipping won’t be able to initiate a Packing List.
Inventory Items Allocated
MRP does NOT distinguish between inventory items allocated to projects nor Purchase orders allocated to projects in the determination of the available supply (current and future). To do so would enormously complicate the MRP process. MRP WILL determine that the supply will meet the demand, whatever it is.
Should we have locked the requirements by project in MRP, then we could have the situation where we have unallocated inventory on hand, but since it's not for a specific product that requires it, MRP action could create an order action to buy more of the parts specifically for that project. This could result in an enormous amount of excess inventory. Since our objective in MRP is to drive to zero inventory, we do NOT want to ignore any available inventory that might satisfy demands. Conversely, when inventory is allocated to a specific project, and the demands created for another project are analyzed, the inventory on hand will be available to meet the other project demands, but also create the order actions to supply parts for the original project, if there are still demand requirements.
In the case of having just enough inventory on hand for a given Project (A), but there are new requirements for Project (B) that precede those for the same parts as project (A), MRP will assume that the inventory on hand will be used for Project (B) first, but get more parts to meet the later date of Project (A). As long as there is inventory available to meet every demand, it will be up to the user to reallocate inventory for the most urgent need.
If for some reason user has inventory that belongs to a specific customer and does not want MRP to consider it for any other customer they can change the inventory location to non-nettable.
|
1.2.3. Fields & Definitions for MRP |
1.2.3.1. MRP Action Tab |
MRP Actions: displays the results of a find and allows further item sorting and selection
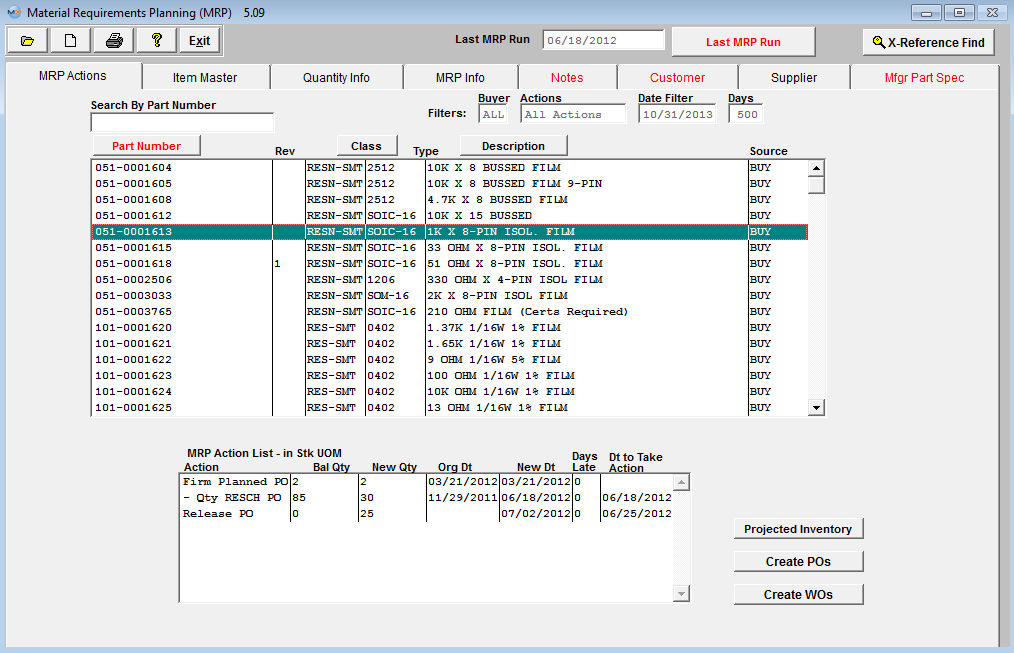
Definition of Material Requirements Planning Action Fields:
Last MRP Run |
This is the date and time for the last material Requirements Planning run. |
 |
The "Last MRP Run" button located in RED at the top of the screen will be displayed in a larger font if MRP run failed due to an AVL issue and there will be brief comment explaining what issues the MRP run encountered. This will allow any user that might not have seen the xls spreadsheet to be aware of what had taken place on the last attempt to run MRP. For further detail see Article #729. |
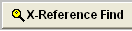 |
See Article #4765 for further detail on how to Use the X-Reference Find |
Sorting, Searching and Selecting in the MRP Action Screen
The user may sort by the Part Number, Class or Description by depressing the appropriate button.
To sort the contents of the Summary screen by Part Number, Part Class or Description, click the button. It will turn red and the list will automatically sort in ascending alphanumeric sequence per the selection.
To search for an item by Part Class, click Class and enter the first few characters of the Part Class in the Search by Part Class field. The list will scroll down to the first incidence of each character in the sequence entered.If a character is not found in the position typed, the list will scroll to the bottom.
To Search for an item by Description starting with the 1st character on the left, click Description and begin entering the first characters in the field. The list will scroll down to the first incidence of each character in the sequence entered.If a character is not found in the position typed, the list will scroll to the bottom.
To Search for an item by a word or character string anywhere in the Description, click on Description, click on the Left button next to the Search by Description window (changes to Random).
Enter the search word or characters in the window. Hit return and the first match in the list will be highlighted. Click on the window and hit return to highlight the next match in the summary list. After the last match or if a match is not found, the last item in the summary list will be highlighted.
To visually search the summary list, use the scroll bar or arrows to the right of the list.The Source (Buy, Make or Phantom) and total On Hand quantity is displayed in the last two columns.
For further Details on any item in the Actions main body list, highlight the item by a search or mouse click and select the appropriate Tab to display the desired detail information. To display changes made in other windows or by other users while this window is open, repeat the Material Requirements Find and refresh the screen data.
FILTERS:
Buyer |
The valid buyer code, or ALL buyers. |
Actions |
The Material Requirements Planning action displayed, or ALL Actions.
|
Date Filter |
The horizon date for the Material Requirement Planning actions.Parts with actions beyond this date are excluded from the report.
|
Days |
A short-cut to the horizon date. Entering the number of days (from the current date), changed the Date Filter accordingly.
|
Main Body
Part Number |
The item/part number is a unique identifier for every Item Master record entered into the database.
|
Revision |
The part Number revision for the item.
|
Part Class |
This is a general part, product or item classification.
|
Part Type |
Type is a sub-classification of Part Class.
|
Description |
This is the field of descriptive data about the item. |
Part Source |
This field is hard coded in the system.BUY is for purchased parts and assemblies, MAKE for an item made in-house (assemblies and sub-assemblies) and PHANTOM for a number used to define a collection of items that does not exist as a separate assembly built on a Work Order (ship kits, upgrade packages, spares kits, etc.).
|
Material Requirements Planning Action List in Stock Units Of Measure:
The information listed in this section pertains to the highlighted part number in the main body above. To see the list for another part number, highlight the part number in the main body.
Note: Dates are calculated with the Production Calendar
Action |
Defines the Material Requirements Planning action to be taken for the highlighted part. There are several different actions that will appear depending on the part. For example if the Part is a Make/Phantom part and the action originates from a higher level assembly for the Phantom, MRP will display "PHANTOM" in this section and that will indicate to the user that there are no actions required but is listed so users can investigate where component actions are originating from. If the Make/Phantom is required directly for an order itself, it will now follow the same WO action rules as a regular Make Product would.
|
Balance Quantity |
The projected balance of inventory for the part selected. MRP will display the stock qty UOM.
|
New Quantity |
Displays the new quantity that the action requires. MRP will instruct you to Purchase the Stock qty UOM, not the Purchase UOM. The PO Module will display the UOM conversion (if applicable).
NOTE: When creating a PO for an item with different purchasing and stocking UoMs, be sure to enter the MRP suggestion into the Stocking qty field rather than the purchasing qty field. The system will automatically convert the stocking unit into the purchasing unit for the purchase order qty.
For Example: if the item has inches for Stock UoM and Feet for Purchasing UoM, and the MRP demand is 24 , the buyer would enter the qty of 24 into the stocking qty field and the PO would automatically convert it to 2 feet in the purchasing qty field. So the supplier deals in feet, but ManEx deals in inches. The conversion between the two are established in the Unit of Measure & Conversion module.
|
Original Date |
Displays the original (current) date of the existing action.
|
New Date |
Displays the new date that the action requires. For a buy part the New Date is arrived by subtracting the Kitting and Production Lead times setup for the Make part from the Sales Order Ship Date. For a Make part the New Date is the Sales Order Ship date. See Article #3064 for futher detail on how the Lead Times for a Level BOM are calculated. |
Days Late |
If the action date is earlier than the current date, the number of days late for the action is shown.
|
Date to Take Action |
This is the date by which the action listed must take place. Changing the leadtime of a Buy part will NOT change the due date, only the date to take action. For a Buy part this date is arrived by subtracting the Purchase Lead time from the New Date. For a Make part this date is arrived by subtracting the Kitting and Production Lead times from the New Date which is the Sales Order ship date.
|
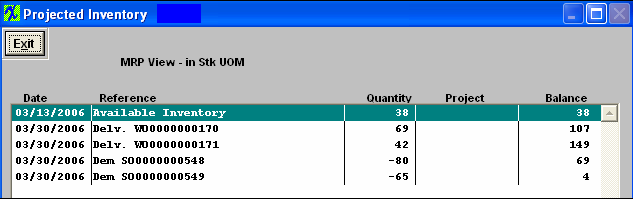
Definition of fields in the Projected Inventory screen:
Date |
The projected date of a Materials Requirements Planning action.
|
Reference |
The Material Requirements Action.
|
Quantity |
The quantity of parts involved in the Material Requirements Planning action. |
Project |
The project number assigned to the PO. |
Balance |
The projected balance of inventory for the part selected.
|
After depressing the Projected inventory button, highlight and double click on a WO, SO, PO, etc. This will bring up another drill down screen as follows which will display the Material Requirements Planning Detail. This screen allows user to Sort, Search, or Drill down to the WO, SO, PO. etc.

Material Requirements Planning Field Definitions:
Work Order Number |
This is the Work Order Number in the system. |
Customer Name |
The name of the Customer for which the assembly will be made. |
Part Number |
This is the assembly part number where the component part number is highlighted.
|
Balance |
This is the balance for the Work Order Listed.
|
Original Ship Date |
This is the original scheduled ship date of the assembly. |
After highlighting and double clicking on a part number in the main body, the Material Requirements Planning Demands and Approved Vendors List will appeared, as displayed below. This screen will allow users to Sort, Search, or Drill Down to the WO, SO, etc. level.
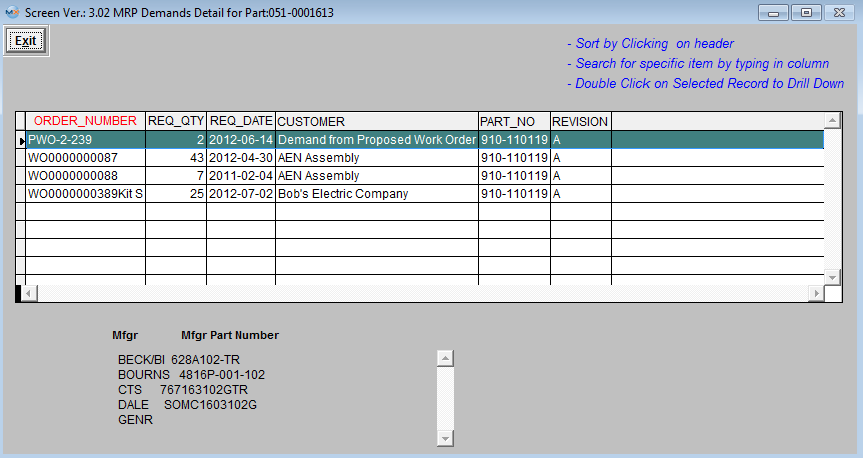
Material Requirements Planning Demands and Approved Vendor List Field Definitions:
Order Number |
This is the Work Order Number the system is proposing.
|
Required Quantity |
For the Work Order proposed, this is the quantity of the component part number which will be required. |
Required Date |
The date when the component part number highlighted is required to be released to the assembly floor. |
Customer |
The name of the Customer for which the assembly will be made, if known. If the customer is not known, an explanation will appear. |
Part No |
This is the Assembly/Part number No the demand is for |
Revision |
This is the Revision for the assembly/Part number the demand is for |
AVL
Mfgr
|
This will list the Mfgr's approved on the BOM
|
Mfgr Part Number
|
This will list the Mfgr PN's approved on the BOM. NOTE: If "GENR" is approved on the BOM MRP will consider any inventory for that part even if the AVL is not approved on the BOM.
|
|
1.2.3.1.1. Create POs |
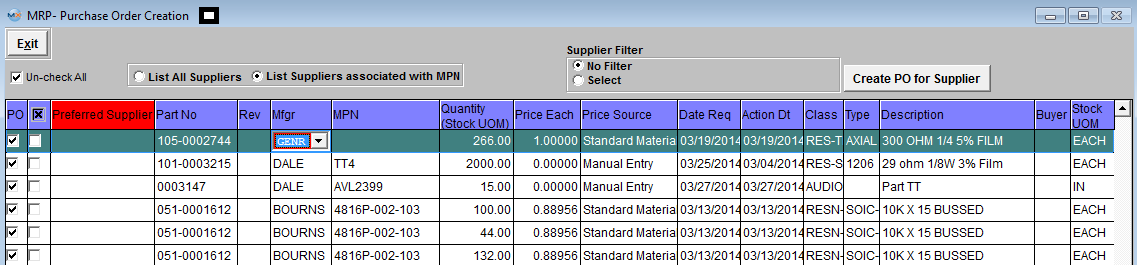
Un-Check All |
Check or Un-check all records in the grid to create POs. |
List All Suppliers
List Suppliers assigned to the MPN in the ICM Module
|
Check the radial to list all suppliers or list only the suppliers assigned to the MPN in the ICM module. Once the radial is selected this will control the information defaulted into the Preferred Supplier column. |
Supplier Filter |
If "No Filter" is selected and multiple records with different suppliers are selected multiple POs will be created (one for each supplier). If "Select" is checked, user can select from the pull down which Supplier records to display. Then when the "Create PO for Supplier" button is clicked, the system will create POs for selected supplier only.
|
 |
Depress this button to Create the POs for the items checked. |
PO |
Checking this box indicates which PO is to be created for the selected item. If you place your mouse pointer over the column it will display the tool tip. |
X |
If there is no Supplier information available in the ICM module the system will allow user to select a supplier from a pick list. Once this supplier is selected this supplier will default into the Prefered Supplier coulmn for the records that have this box checked. |
Preferred Supplier |
The default supplier assigned in the ICM module will appear in this column. If no Preferred Supplied is listed user may select one from the pull down. |
Part No |
Defaults in from the MRP action list with "Release PO" action. |
Rev |
Defaults in from the MRP action list with "Release PO" action. |
Mfgr |
Defaults in from the MRP action list with "Release PO" action. There is a pull down available that will display all the Approved Mfgr and allow user to select a different one if they choose to do so. |
MPN |
Defaults in from the MRP action list with "Release PO" action. |
Quantity |
Defaults in from the MRP action list with "Release PO" action. This field can be changed. |
Cost Each |
Unit price for the item defaults to the value based on the "Price Source" column. This field can be changed. |
Price Source |
Derived from the list of "Price Sources" setup in the Purchase Setup module. There is a pull down giving the user the option to change the Price Source if the choose to do so. |
Date Req |
Defaults in from the MRP action list with "Release PO" action. This field can be changed. |
Action Dt |
Defaults in from the MRP action list with "Release PO" action. |
Class |
Defaults in from the MRP action list with "Release PO" action. |
Type |
Defaults in from the MRP action list with "Release PO" action. |
Description |
Defaults in from the MRP action list with "Release PO" action. |
Buyer |
Defaults in from the MRP action list with "Release PO" action. |
|
1.2.3.1.2. Create WO's |
This portion of the MRP module is not fully completed yet in the current version. It is still a work in progress. While it displays the WO’s for quick reference you will still actually have to go into the WO module to create the WO’s as needed. You can also create WO’s directly in the SO module as well at the time you’re creating the Sales orders.
|
1.2.3.2. Item Master Tab |
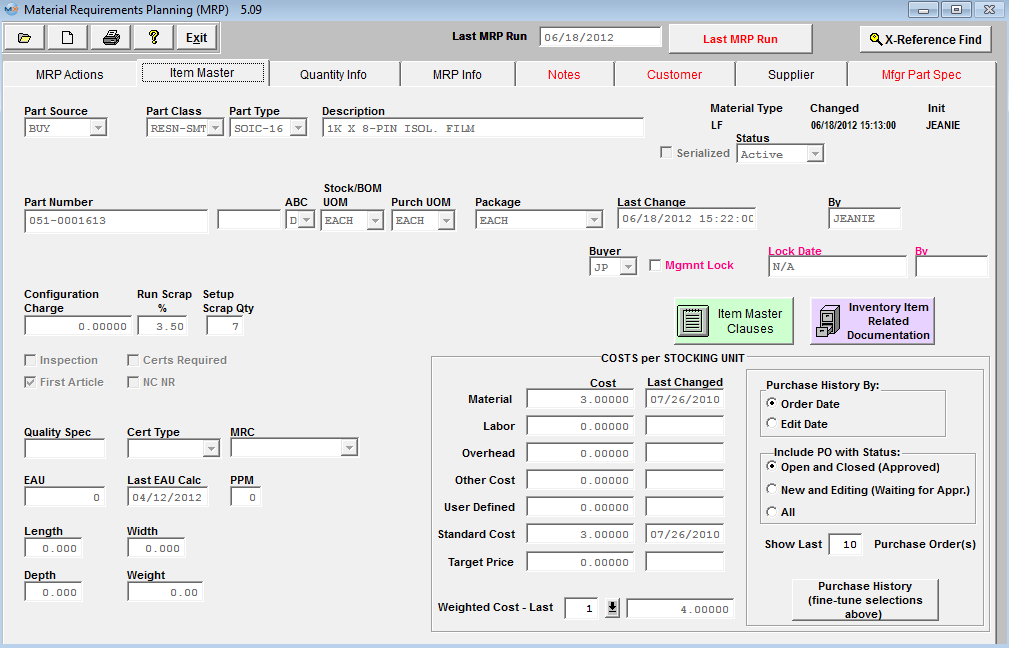
|
1.2.3.3. Quantity Info Tab |
Complete inventory stock, allocation and usage information by Manufacturer is displayed or available at the click of a button. All current inventory information about any selected part can be displayed here.
|
1.2.3.6. Customer Tab |
This screen will display customer part number(s) assigned to the internal part number for the item highlighted in the MRP Action tab, which is being defaulted in from the Inventory Control Management module. See Article #4042 for field definitions. These fields may be edited in Inventory Control Management .
|
1.2.3.8. Manufacturer Part Spec Tab |
|
1.2.4. How To ..... for MRP |
1.2.4.1. Find a Material Requirements Planning (MRP) Record |
Enter the SQLMANEX.EXE (within the ManEx root directory)
This action will then prompt the user for a password
|
 |
The following screen will be displayed, select Material Planning/Material Requirements Planning (MRP)/Material Requirements Planning (MRP) Module
|
 |
The following screen will be displayed:
Tips on Using the Material Requirements Planning Find Screen
Selection of at least one parameter will reduce the time to retrieve the information. The Find by Parent BOM is specific down to the Revision level.
If no information is selected in a Find operation, all part numbers with MRP actions will be displayed.
Pressing the Find action Button displays the following sequences:
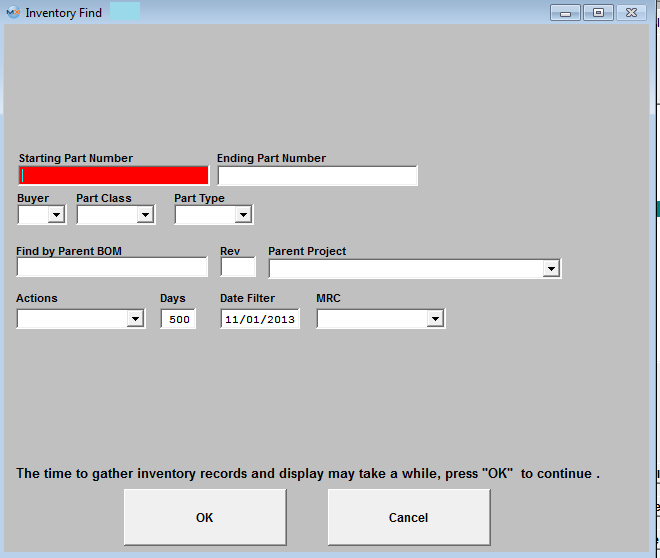
Definition of Material Requirements Planning Find Fields:
Starting Part Number and an Ending Part Number
|
Be sure to enter all prefixes, dashes, spaces and alpha characters to find the exact number you are trying to locate. To find one item, enter the part number in the 1st box, depress the return key and only that record will display. To view a series of items, enter the first and last part number of the series and all items numbered between will display. If you want All part numbers, leave this area blank.
If an incorrect part is entered into the range that does not exist within inventory, or there are no MRP records for the part entered user will receive the following message:
|
Buyer |
Select Buyer from the pull down menu. If you want ALL buyers, leave this area blank. Assigned Buyer will bring up all items assigned to that particular Inventory Buyer within the Inventory Control Management module. The Buyer assignment is setup in Part Class and Type System Setup Defaults or in the Inventory Control Management module/Item Master tab.
|
Part Class |
Select the Class from the pull down menu Part Class and/or Part Type will bring up only those items that match all entries made. If you want all Classes, leave this field blank. |
Part Type |
If you selected a Class, depressing on the down arrow will bring up a list of Types within that Class. Select the Part Type within the Class selected. If you want all of the Types within the Class, leave this field blank.
|
Find by Parent BOM |
The "Find by Parent BOM" is specific down to the Revision level. This filters MRP results per Selected Bill of Material. You MUST enter the exact part number and revision of the Parent BOM to get only the parts with actions per that BOM. Note: Only parts listed on the BOM with MRP action messages will be displayed. Parts with all actions from all sources will be shown on the screen if the part has actions from the entered BOM and other demands. A part may appear on the list even if there are not direct actions from the entered BOM if there are actions from the demands or such actions as Cancel PO/WO. There is no way to filter out the actions just to those actions resulting from demands from entered BOM. |
Rev |
Revision of Parent BOM. If applicable this MUST be entered to located the exact Parent BOM. The "Find by Parent BOM" is specific down to the Revision level. If the exact part number and revison of the Parent BOM is not correct user will receive the following message:
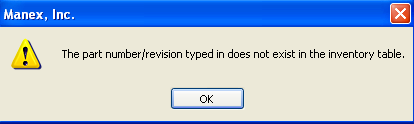
|
Parent Project |
If you select to find by a Project this is going to filter and display only parts that are assigned or associated to a project, but will display , ALL actions for that part , not just those that are associated with the project. If you had 3 actions for a part, each assigned to a different project, all three actions would be displayed when you Find by any of the three projects. |
Actions |
Select the action from the pull down. There are the various Material Requirements Planning actions, which the user may filter on such as: All Actions, All Purchase Order Actions, All Work Order Actions, Pull-Ins, Push-Outs, Release Purchase Orders, Release Work Orders, Cancel Purchase Orders, and Cancel Work Orders.
Note: When you filter by any of the selections, MRP will filter through the actions and display ONLY the parts that have an action that matches the selection. If it finds a match it will display all the the actions against that particular part.
For example: if you select to filter by "Release PO Actions". MRP will display ONLY the parts that have "Release PO Actions". If it finds a match it will still display all the other PO actions against that particular part. If it didn't users may overlook the fact that there are other PO actions for that particular part as well. However, it does filter out all the parts that "DO NOT" have any "Release PO Actions" against it.
|
Days |
Type in the number of days (from the current date), changes the Date Filter accordingly. This is a short-cut to the horizon date.
|
Date Filter |
The horizon date for the Material Requirements Planning actions. Parts with actions beyond this date are excluded from the report.
|
MRC |
Select the Material Risk Code from the Pull Down, which are setuup in System Setup/ Material Risk Code Setup . |
The filtered information will populate the Material Requirements Planning Actions screen, as displayed below:
|
1.2.4.2. Add (Generate) A Material Requirements Planning (MRP) | Add (Run) a Material Requirements Planning
MRP runs through a large number of tables and records to compile its calculations, and provides a snapshot of suggested actions at the same time it is ran. If users are changing things during this process it could definitely cause some strange outcome. To prevent this situation we strongly suggest that you use the Nightly MRP trigger. (Refer to Article #416 for more detail on trigger setup).
If you find the need to re-run MRP during the production work day then we suggest that you notify all departments that MRP is going to be ran and ask them to remain out of the system until the MRP run is complete. This will help assure that the most accurate MRP run is possible. Then follow the procedure below:
Enter the SQLMANEX.EXE (within the ManEx root directory)
This action will then prompt the user for a password
|
 |
The following screen will be displayed, select Material Planning/Material Requirements Planning (MRP), Material Requirements Planning (MRP) Module
|
 |
The following Screen will be displayed:
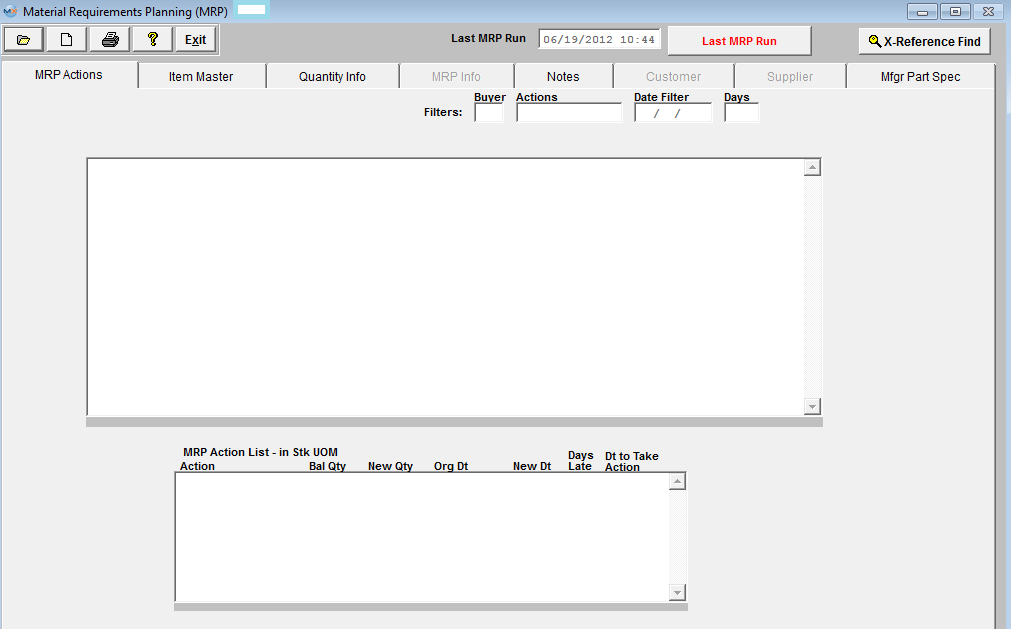
To run a new Material Requirements Planning (MRP) manually, depress the Add action button (Generate MRP), and enter your password.
The run percentage will be displayed on the header as displayed below:

The time it takes MRP to run is dependent on a number of factors. Here is a list of items that affect the processing time:
the number of open Sales orders
the number of open Work orders
the number of open Purchase Orders
the complexity of the BOMs (levels)
the number of AVL's for parts
the number of active parts
Inventory safety stock, minimum orders, order multiples
A company with high annual sales but only a few open orders of all types and only a few simple BOMs will process quickly, a company with low annual sales, but with a large number of small orders, many BOMs and AVL's will take a long time to process.
We are not able to come up with an average time because there are too many conditions that affect the run time.
Once the MRP run is completed and was successful, user will receive the following message:

Depress the OK button. The Material Requirements Planning Date at the top right hand side of the screen will change.

If the MRP run was NOT successful due to AVL issues (missing, or exists but is marked as "Do Not Purchase and/or Kit, etc) the following message wil be displayed on screen indicating that MRP will NOT be able to continue until the BOM and/or part records have been correct. Then in addtion to the message an XLS file will be generated and placed in the ManEx Main Directory. This XLS file will contain the records that the user will need to review and address. If an XLS file is generated multiple times a day the system will add "_N" to the name of the XL file, where "N" is the dequence number. For example if MRP is run today three times without fixing a problem or a new problem is generated, the generated files will have names; badavls_2009.03.31_1.xls, badavls_2009.03.31_2.xls, badavls_2009.03.31_3.xls, unless one or all of the files were removed. The user will have the option of viewing the XL file now or later. NOTE: These XL files will need to be manually removed from the ManEx Main Directory.

If the user selects "No" the user will receive the following message and they may review the XL file placed in the ManEx Main Directory.
If user selects "Yes" an XL file (similar to the one shown below) will be displayed on screen and also placed in the ManEx Main Directory for later review:
The date displayed in the "Last Successful MRP Run" will NOT change. The "Last MRP Run" button located in RED at the top of the screen will be displayed in a larger font if MRP run failed due to an AVL issue and there will be brief comment expaining what issues the MRP run encountered. This will allow any user that might not have seen the xls spreadsheet to be aware of what had taken place on the last attempt to run MRP.
Double click on the "Last MRP Run" button and similar information will be displayed:
NOTE: If MRP runs from Trigger, and MRP run was NOT successful due to AVL issues an XLS file will be generated and placed in the ManEx Main Directory for review and also be attached to the e-mail sent, informing user that the MRP run was NOT COMPLETED (similar to the one shown below). Upon opening the MRP screen the "Last MRP Run" button will be displayed in a larger font and will have information about the file as displayed above.
If MRP runs Successfully from Trigger the e-mail sent will be similar to this:
|
1.2.4.3. Drilling Down In MRP | There are several drill downs within the MRP screen.
Highlight a Buy or Make Part number of interest on the MRP main screen:
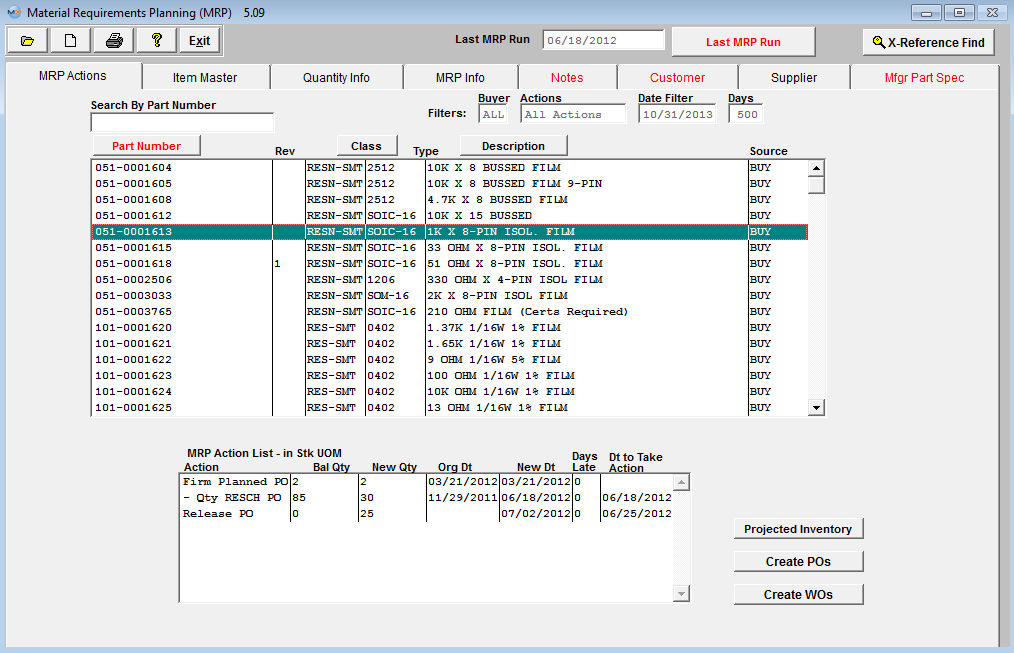
Double click on the highlighted buy part number 051-0001613 and the user can see the assembly of the proposed work order. Highlight the Proposed Work Order Number and the Approved AVL's will be listed per the BOM.
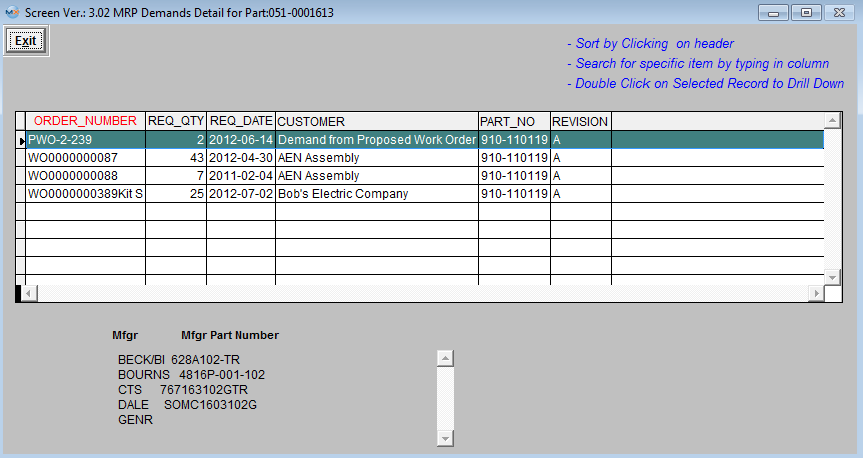
If the User double clicks on the PWO-2-239 (Proposed Work Order) the Sales Order, the assembly, required qty, and Customer will be displayed.:
Highlight and double click on the SO0000000057 and the Original Sales Order will display.
Another Drill down located within the MRP Actions screen - is by highlighting one of the actions located in the MRP Action List-in Stk UOM box:
Double Click on the PO, WO, SO, etc of interest and the following screen will be displayed: All the Drill Down screens may be used to Sort, Search, or keep drilling down to actual PO, SO, WO, etc.
Depress the button. The user will see the same proposed work order number being delivered instead of demand. By this screen, the user can also see what’s driving the requirement for the product and the next level, etc.
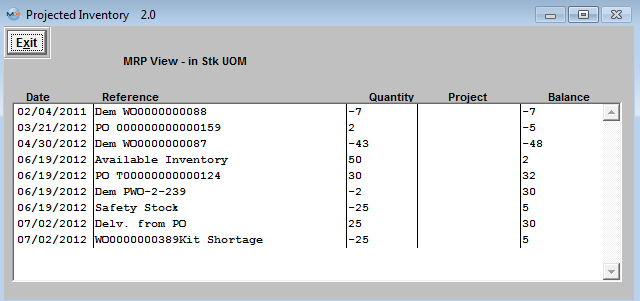
Within this screen you may highlight any of the Reference items and drill down to the original Sales Order, Inventory Level, Purchase Order, etc.
|
1.2.4.4. Create POs from MRP Action List |
Enter the SQLMANEX.EXE (within the ManEx root directory)
This action will then prompt the user for a password
|
 |
The following screen will be displayed, select Material Planning/Material Requirements Planning(MRP)/Material Requirements Planning (MRP)
|
 |
The following screen will be displayed:
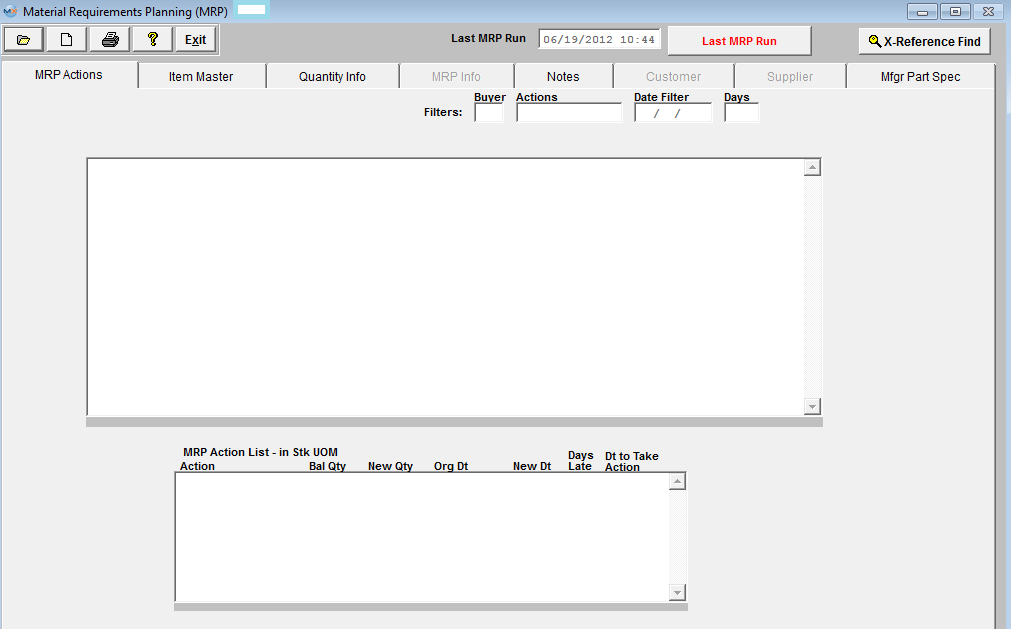
Note: To start creating POs from the MRP action list, make sure you have run MRP creating a fresh MRP action list, and user must have "ADD" rights to the PO module in Security setup.
Find an MRP record.
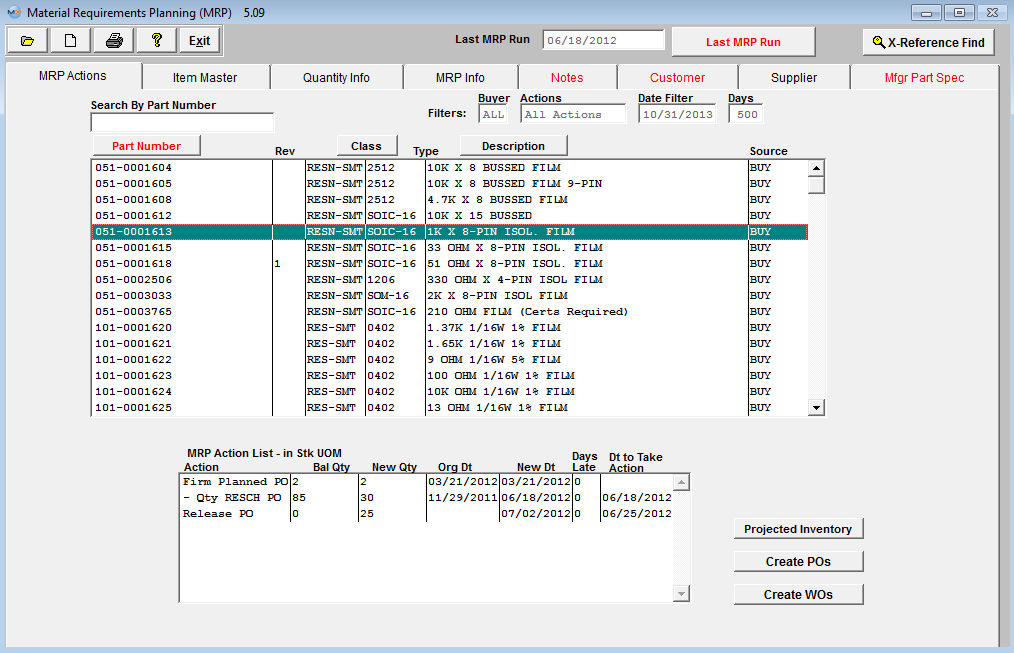
Highlight a part number of interest and depress the Create POs button in the bottom right hand corner, enter user password (user must have "ADD" rights to the PO module), and a list of Release PO suggestions based on the MRP filter that was applied and displayed within the MRP screen will appear. This will allow the buyers to auto created purchase order records based on what MRP is suggesting (mfgr, mfgr pn, etc...)
Note: ManEx does offer a pull down next to the Mfgr to select from listing only the approved AVL's for that BOM. Double clicking on MPN field will open a web browser session and navigate to Calculquote's web site Search.calculquote.com allowing you to use their search engine to find a matching part for quoting purposes. More info on Calculquote and how it integrates with ManexERP can be found here. Calculquote.com
Note: If the AVL suggested to the PO action is flagged as "DO NOT PURCHASE" MRP will give Release PO actions if there is a need for the part and the part will be displayed on the Create PO screen with the Mfgr and MPN fields blank. This should flag the user to further investigate and see that it is flagged as "DO NOT PURCHASE" and that they will need to either remove the flag or add additional AVL's to ful-fill the demands. Notice at the top there is a note that explains what the empty "MFGR" field means.
User may view records by selecting All Suppliers or only Suppliers assigned to the MPN in the ICM module. User may also use the Supplier filter to view records for one supplier at a time.
User may manually select the records to have POs created by placing a check in the box in the PO column. If no supplier is defaulted in the Preferred Supplier column from the ICM module, user may check item in the "x" column, select a supplier from the pull-down and receive the following message:
Depress "Yes" to continue and user will receive the following message:
Depress "Yes" and all the records that have the check box to the left of the "Preferred Supplier" column checked will be updated with the selected supplier.
The Cost Each is defaulted in based on the "Price Source" column (which is setup in the Purchase Setup module). The standard Material Price and the Target Price defaults in from the Inventory Control Mgmt module. The Contract Price is defaulted in from the Supplier Contract Mgmt module. The Quote Price is defaulted in from the Quotation & Estimating module. The quote MUST be approved. If the part is on more than one quote the system will use the price from the most recent quote. The Mfgr and Supplier listed on the Auto PO screen must match the Mfgr and Supplier that was selected on the quote. The Last Purchase Price and Last Purchase Price for a Supplier will only be listed if they are within the last 6 months, if not then zero dollars will be displayed. Manual Entry allows user to manually enter in a cost each.
NOTE: The Auto PO screen will only find existing parts entered in the "Material 1" screen. There is no way to identify parts from "Material 2" screen. There is no connection between part entered in the quote module "Material 2" screen and the part before it becomes an Inventory part in ManEx until after the "Transfer".
All coulmns in the grid are sortable. To sort on the specific column click the header of the column. By default the items are sorted by "Preferred Supplier" column (red color of the header indicates that the data sored by the values in the column). Part No and Rev columns are both sorted by Part No and Rev vaules. If the cursor is in Part No, Mfgr,or MPN columns and the user begins to type the information, the interactive search will be performed and the record pointer will be moved to the appropriate record.
Once user has selected the records, they can depress the "Create PO for Supplier" button and PO's will be created (one for each supplier).
Once the POs have been created an xls report will be generated in the Manex local directory for review. The XL file name is based on the user initials plus the date and time the file is created. For Example if the file created has a name "ONE-20070524-9-37.xls" "ONE" - this is the user's initials; "20070524" - is the date when file was created (YYYYMMDD); "9-37" is the time (Hours-Min) when file was created, so this file was created at 09:37 am.
User has the option of opening the created excel file by depressing Yes or No.
|
1.2.5. Reports - MRP |
To obtain the MRP Reports within the Web, select the WEB Print button from the ManEx action buttons at the top of the screen. For further detail on How the Reports work within the Web refer to Article #5477.
Note: In order to access the Reports within the Web the Company Root URL must be setup within the System Appearance module and user must be linked to web within the System Security Module
Select the Report Type: MRP - A List of Reports will be displayed that are available on the Web
for MRP
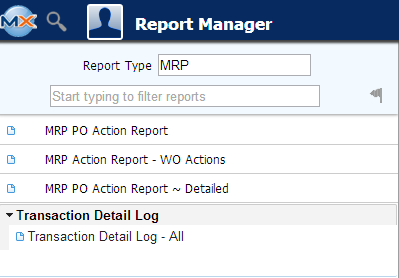
To obtain the MRP Reports within the desktop, select the Print button from the ManEx action buttons at the top of the screen.
The following reports screen
will display a list of reports that are available on the ManEx Desktop:
Highlight the report, depress the option tab (if applicable) and depress the OK button.
MRP Action Report - PO Actions - MRP Report of all recommended PO Actions for all "BUY'" parts that have at least one action within the "Last Action Date" filter on the MRP screen.
The following report is printed:
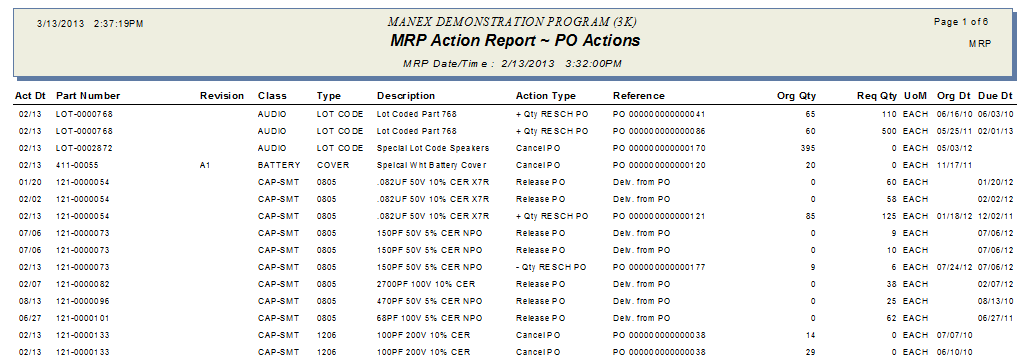
MRP Action Report - WO Actions - MRP Report of all recommended PO Actions for all "BUY'" parts that have at least one action within the "Last Action Date" filter on the MRP screen.
The following report is printed:
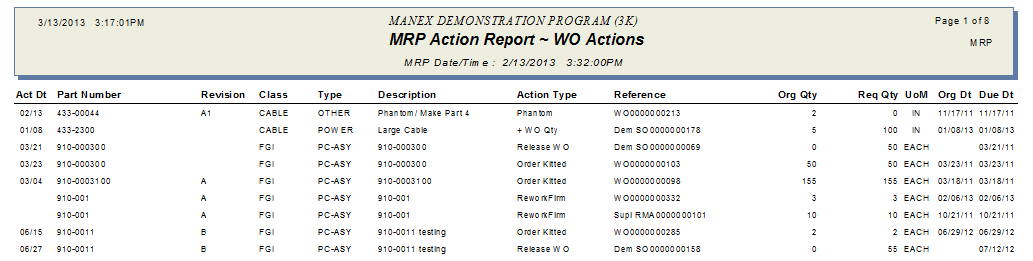
Inventory Part View by Manufacturer - This report displays the inventory information, supply, demands and action messages for a part that are the results of the latest MRP run.
For Inventory Part View By Manufacturer, depress the Options tab:
Select the Part Number Range desired. To clear the range entries, click on the "Clear Range Entries" radio.
Depress the OK button.
This report is divided into three sections: Inventory; Demands/Supply; and Actions
|
|
The following report is printed:
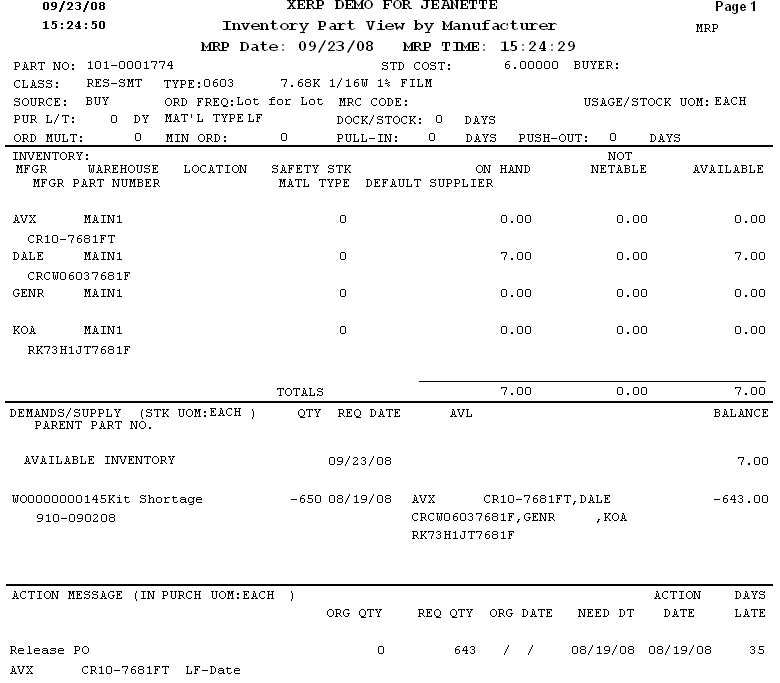
Order Action Report - This report displays the inventory information, purchase history, open PO's and MRP actions for 'BUY' parts that are the results of the latest MRP run.
Depress the Options tab.
Select the Part Number Range desired. To clear the range entries, click on the "Clear Range Entreis" radio.
Depress the OK button.
NOTE: The MFGR and MFGR part number will only be printed in the Order Action Message Section if the order policy for the part is LOT for LOT.
|
|
The following report is printed:
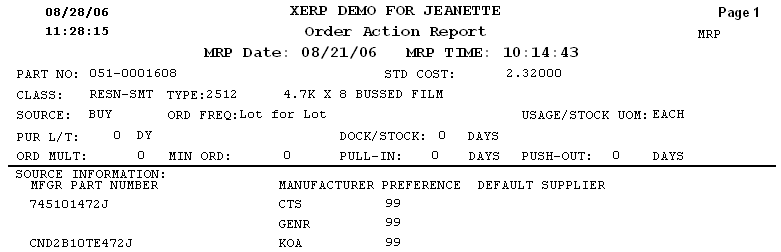
Projected Excess Inventory List - This report list the projected excess inventory that is on hand but not needed after MRP requirements.
Depress the Options tab.
Select the radio for "All Inventory", "Internal Inventory" or "In-Plant Store Inventory".
Depress the OK button.
Note: The Projected Excess Inventory report runs off of the entire MRP run, not just based off of the MRP find filter that might be applied.
|
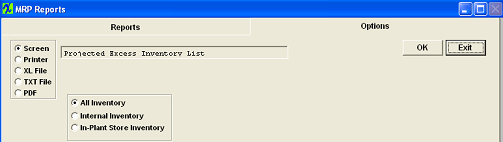 |
The following report will print:

MRP Horizontal Planning Summary - This reports displays the supply and demand for each part on the MRP action list with the quantities in weekly buckets.
Note:This report requires Legal size paper.
The following message will appear:
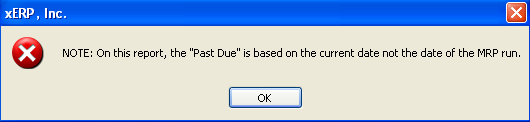
Depress the OK button and the following report will be printed:

Multi Division Purchase Order Action Report - NOTE: The system does NOT require that you have Multi-Divisions setup to utilize this report.
Depress the Options tab.
Select the Part Number Range desired, then enter the Last Action Date.
To clear the range entries, click on the "Clear Range Entries" radio.
Select the Part Class from the pull down. Select the Supplier List from the pull down.
Select the radio to list the Report by: "All Contact Suppliers", "Single Contract Supplier", "Parts with no Contract Supplier", "All Parts Contract & Non-Contract".
Select Buyer from the pull down.
Depress the OK button.
|
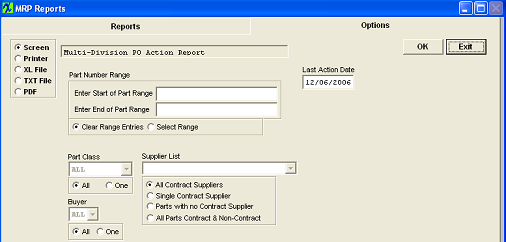 |
The following report will be printed: The report is intended to break down the PO actions from the MRP run by Buyer, then part number.

MRP Action Report - PO Actions by Supplier - MRP Report of all recommended PO Actions for all "BUY'" parts that have at least one action within the "Last Action Date" filter on the MRP screen by Supplier
Depress the Options tab.
Select Apply All "Find" Filters or Apply only Date Filter by clicking on the radio.
Select the Supplier from the pull down.
Select the radio butto to list the report by: "All Default Suppliers", "Single Default Supplier", "Parts with no Default Supplier", "All Parts Contract & Non-Contract".
Select to Show only #1 pref or Show all Preferences by clicking on the radio.
Depress the OK button.
|
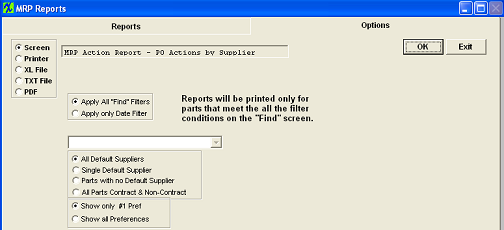 |
The following report will print:
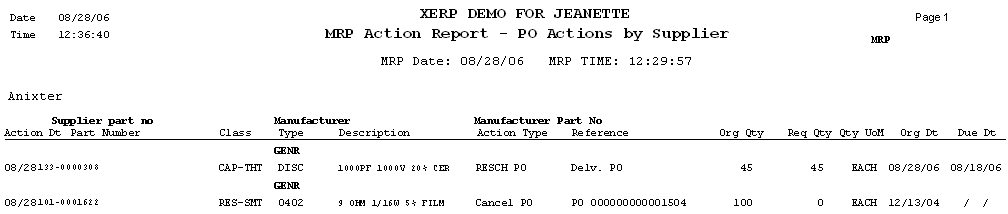
MRP Action Analysis by Part Number
Depress the Options tab.
Depress the down arrow next to the Part Number box.
Use the slider to reach the Part Number of interest.
Highlight it and click. The Actions will be displayed.
Depress the Ok button.
|
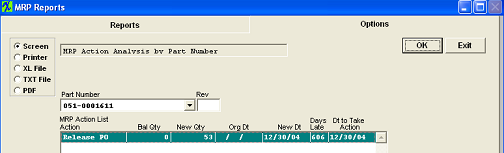 |
The following report is available:

Customer Projected Excess - This report list the projected excess inventory that is on hand but not needed after MRP requirements for a selected customer.
Note: This report requires Legal size paper.
Depress the Options tab.
Select All Inventory, Internal Inventory or In-Plant Store Inventory by clicking on the radio.
Select a Customer fron the pull down.
Select to Sort by System Part Number or Customer Part Number by clicking on the radio.
Depress the Ok button.
Note: The BOM MUST be associated to a Customer for the report to work. If you select a customer, the program will find all the assembly’s and sub assembly’s assigned to that customer find all the parts on those BOMs. Then it will exclude the parts that are used on the BOM of a different customers.
|
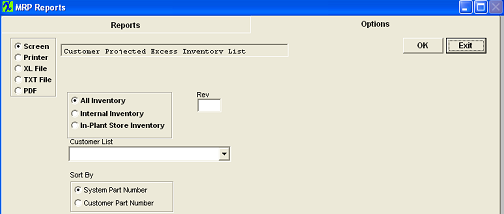 |
The following report will be printed:
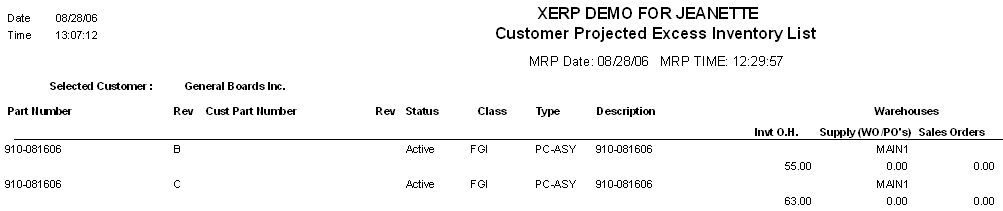
MRP PO Action Report by Buyer - MRP Report of all recommended PO Actions for all "BUY'" parts that have at least one action within the "Last Action Date" filter on the MRP screen.
Note: A default Supplier MUST be linked to the inventory part before it will display on the report.
The following report will print:

|
1.2.6. FAQs - MRP | Facts & Questions for the MRP Module |
1.2.7. MRP Hot List |
After activation, "Material Requirements Planning" (MRP) access for each user must be setup in the ManEx System Security module. Users with “Supervisor Rights” will automatically have access.
Material Requirements Planning Hot List Field Definition:
Days Late |
If the action date is earlier than the current date, the number of days late for the action is shown.
|
Required Date |
The date when the component part number highlighted is(was) required to be released to the assembly floor. |
Action |
The Material Requirements Planning action required. |
Part Number |
The Part Number for the item highlighted. |
Class |
The classification of the highlighted part number.
|
Type |
The Part Type assigned to the item.
|
Quantity |
The quantity of parts involved in the Material Requirements Planning action.
|
Buyer |
The valid buyer of the item highlighted |
|
1.3.1. Supplier Information |
1.3.1.1. Prerequisites - Supplier Information |
After activation, "Supplier Information" access for each user must be setup in the ManEx System Security module. Users with “Supervisor Rights” will automatically have access.
Supplier Numbering
|
The System Setup/Number System must be defined for either automatic or manual supplier numbers. |
Account Status |
The codes for supplier account status must be setup in Supplier Status. |
Supplier Types |
The types of suppliers must be setup in Supplier Type. |
Terms |
The Purchase terms for the Supplier must be set up in Payment Terms. |
Contacts |
If used, The contacts used at the Supplier. |
|
1.3.1.2. Introduction for Supplier Infomration | The Supplier Module is used to enter the details about Suppliers. This information is used to prepare purchase orders and receivers, as well as establish defaults to be used when new purchase orders are created for a supplier. A supplier may have more than one remit-to address, if there are different divisions for the supplier with different accounting departments. One supplier remit-to address will be identified as the default address to be used in the creation of new purchase orders. One supplier confirm-to address will be identified as the default address in new purchase orders. Also, terms and conditions identified in these screens will be used as defaults for purchasing, receiving and accounting. The user has the opportunity to modify the default information at the time a new purchase order is created.
The Receiving and Billing Information is the user’s addresses which will print on the Purchase Order. |
1.3.1.3. Fields & Definitions for Supplier Information |
1.3.1.3.1. Supplier Tab |
Supplier Information tab field definitions
Supplier No |
The number assigned to the Supplier. |
Supplier Name |
The name of the Supplier. |
Prefix |
This is only a reference field and does not affect any other modules within the system at this time. This field has been implemented for future use. |
Account Status |
Allows the user to select the status of the Supplier; Preferred, Approved, Under Evaluation, Inactive or Disqualified. "APPROVED" will default in, but can be changed during the Add or Edit process. The status is displayed on screen when creating a PO. If a supplier has an account status of either "Inactive" or "Disqualified" this supplier will NOT be displayed on the Supplier List when creating a New PO. Other than that the status doesn't have any other influence throughout the system. |
Supplier Type |
The type of Supplier, either Manufacturer, Distributor, Independent Rep. or In-Stores. |
Purchase Type |
The type of purchases the user makes from the Supplier, either Inventory, MRO or both. (MRO stands for Materials, Repairs and other, usually used for almost everything else other than Inventory.) |
Account Number |
The number the Supplier has assigned the user. |
Phone |
The Supplier’s telephone number. |
1099 |
If this box is checked, the system will track all of the checks written to the Supplier during a calendar year and a report will be available in Accounting / Accounts Payable / Issue Checks. |
Terms |
The terms the Supplier affords the user, such as 30 Days Net, 2% 10 days, net 30, COD, etc. |
Fax |
The Supplier’s fax number. |
Credit Limit |
The amount of credit the Supplier affords the user. |
CONTACTS
Name |
The name of the supplier contact. |
Title |
The contact’s title at the supplier. |
Phone |
How to reach the Contact. |
Fax |
How to reach the Contact. |
|
1.3.1.3.2. Remit To Tab |
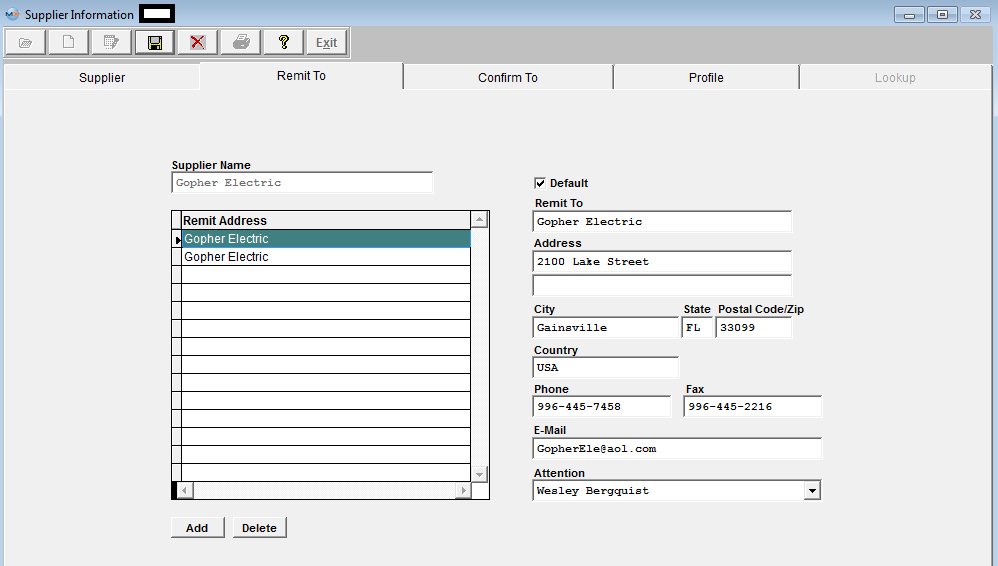
Remit To tab field definitions
Supplier Name |
The name of the Supplier. |
Default |
If this box is checked, it’s the default address where to send the Purchase Order. |
Remitting Address |
The list of available remittance addresses for this supplier. Ther are no limitations to the number of addresses that can be added to this field. |
Remit To |
The name of the check payee.
|
Address |
The mailing address where the remittance will be sent.
|
Phone/Fax/E-Mail |
How to contact the remittance address personnel.
|
Attention |
The contact at the remittance address.
|
Buttons |
Used to Add, Edit or Delete a remittance address. |
|
1.3.1.3.2.1. Supplier e-Bank Information |
Information populated here would be the Supplier's banking information

Link Bank in List |
when this is selected it will allow the user to select from ebanks that already exist for the selected supplier and associate to the highlight Remit To address |
Existing eBanks |
List of existing eBanks for Supplier |
Add New Bank |
allow the user to create a new eBank |
|
|
Originator (Name on Account) |
This would be the your name associated with your Bank Account |
Address |
The bank institution address information |
City |
The bank institution City |
State |
The bank institution state |
Postal Code/Zip |
The bank institution zip code |
Country |
The bank institution country |
Phone |
The bank institution phone number |
Fax |
The bank institution fax number |
Attention |
Person or department at bank institution |
E-Mail |
email address for the bank institution |
Destination Bank Name |
|
Destination Bank Account Number |
This is the bank account number carried forward from the prior screen for the highlighted record |
Bank Branch |
The bank institution branch |
Bank Routing |
The bank institution routing number |
Bank ID/SWIFT |
international bank code that identifies particular banks worldwide. It's also known as a Bank Identifier Code (BIC). CommBank uses SWIFT codes to send money to overseas banks. A SWIFT code consists of 8 or 11 characters |
Country Code |
The bank institutions country code |
Default Payment Type |
Choose from the following options:
|
|
CHECK
WIRE TRANSFER
ACH: for future development
ONLINE BANKING: for future development
CREDIT CARD, BANK DRAFT: for future development |
Next E-Reference # |
The next desired reference number that will be assigned to the next e-record |
Automatic Number |
if checked the system will assign the next reference number automatically |
|
1.3.1.3.3. Confirm To Tab |
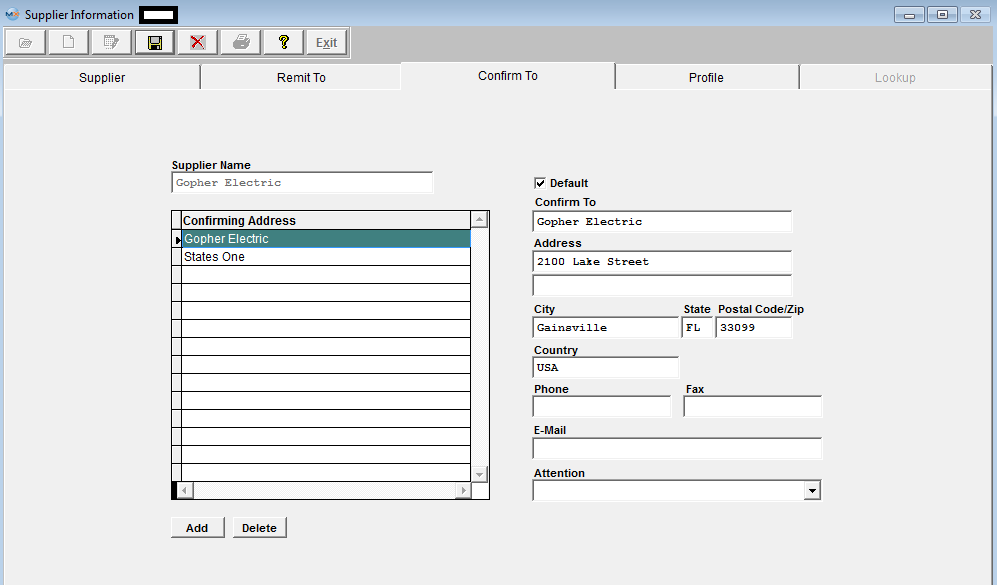
Confirm To tab field definitions
Supplier Name |
The name of the Supplier. |
Default |
If this box is checked, it’s the default address where to send the Purchase Order. |
Confirming Address |
The list of available addresses where to send the Purchase Order for this supplier. |
Confirm To |
The name of the Purchase Order recipient. |
Address |
The mailing address where the Purchase Order will be sent. |
Phone/Fax/E-Mail |
How to contact the confirming address personnel. |
Attention |
The contact at the confirming address. This is probably the name of the Sales Representative. |
Buttons |
Used to Add, Edit or Delete a confirming address. |
|
1.3.1.3.4. Profile Tab |
This tab is available for the user to make notes/comments about the Supplier.
|
1.3.1.4. How To .... for Supplier Information |
1.3.1.4.1. Find Supplier Information |
Enter the SQLMANEX.EXE (within the ManEx root directory)
This action will then prompt the user for a password
|
 |
The following screen will be displayed, select Material Planning/Purchase Setup/Supplier Information
|
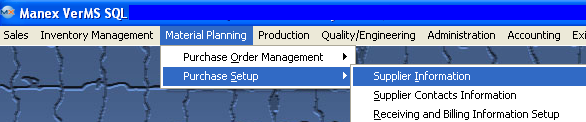 |
The following screen will be displayed:
Depress the Find action button, a list of supplier names will appear along with their id:
Select the Supplier name by either either entering it into the red box, or scrolling down the list and clicking on the selected suppler.
|
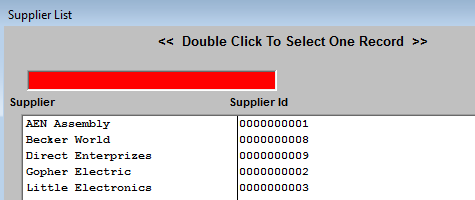
|
|
1.3.1.4.2. Add Supplier Information |
Enter the SQLMANEX.EXE (within the ManEx root directory)
This action will then prompt the user for a password
|
 |
The following screen will be displayed, select Material Planning/Purchase Setup/Supplier Information
|
|
The following screen will be displayed:
To ADD a new Supplier, the user selects the Add action button, enter password, this enables the fields on the screen for data entry.
Enter the following fields:
The Supplier Number assigned to the Supplier. If automatic numbering assignment was selected in Number System Setup, it will be completed when the data is saved. If manual, it must be entered.
The Supplier Name.
A Prefix if desired.
The Account Status, such as preferred, approved, etc. Select from the pulldown:
Note: "APPROVED" will default in upon depressing the Add button, but can be changed.
|
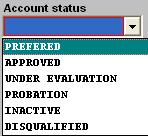 |
The Type of Supplier, such as Distributor, Manufacturer, etc.Select from the pulldown: |
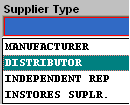 |
The Type of Purchase, such as inventory, MRO, or both.Select from the pulldown: |
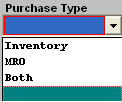 |
Enter the user’s Account Number with the Supplier.
Enter the Phone Number of the Supplier.
Check the box nex to (1099) if the Supplier is to receive a 1099.
The Terms the Supplier has for the user, such as Net 30, 2% 10, COD, etc..... Select from the pull down:
|
 |
Enter the Fax Number of the Supplier.
Enter the Credit Limit established by the Supplier for the user.
When this screen is viewed for an existing Supplier, Contacts entered in the Contacts Module will show for this Supplier. This field is NOT editable from this module.
After completing the Supplier information screen, the user may tab (clicks on the next) to the Remit To screen.
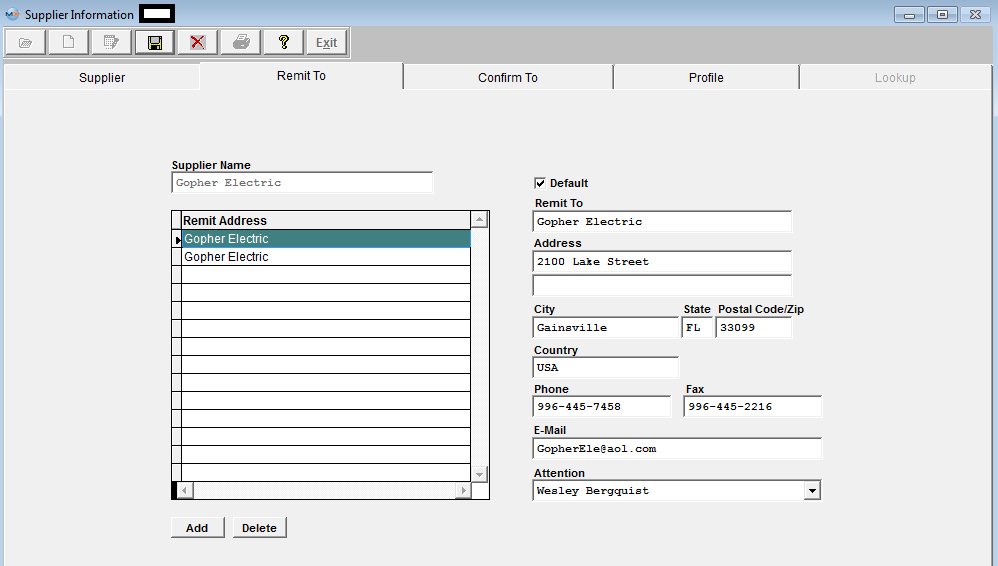
In this screen, the user defines the Supplier information for payment purposes.
The Supplier Remit-To Directive buttons will now be active:
|
This button allows the user to define multiple remit-to locations for the Supplier.
|
 |
This button allows the user to modify existing remit-to information about a Supplier. If more than one remit to address exists for a Supplier, the address highlighted is the one that will be opened for editing. |
 |
This button allows the user to delete an existing remit-to record for a Supplier.
|
 |
This button allows the user to save the modified bill-to information.
|
 |
This button will cancel any modifications made to the screen after the edit button has been pressed.
|
 |
This button is selected for the default Remit-To location. The Remit to address with the default checked is the one that will automatically be placed in New Purchase Orders. However, the user still has the opportunity to change the remit to address in the Purchase Order module by selecting another address. Note: There must be one Default Remit To address.
|
Enter information as follows:
The name of the Supplier, Defaulted from the first screen, but may be over-written.
A list of Remit-To addresses created for the Supplier, from which to choose for editing data.
The name of the organization to which payment is to be sent. (It may be a different division.)
Enter the Supplier Remit-To Address (may use two lines).
Enter the City, State and Zip Code for the Supplier Remit-to Address.
Enter the Supplier Country.
Enter the phone number at the Supplier’s Remit-to Address.
Enter the Fax Number of the Supplier’ Remit-to Address.
Enter the e-mail address of the Supplier Remit-to Address.
The Contact Name at the Remit-to address (if established in the Contacts Module).
After completing the Remit To information screen, the user may tab (clicks on the next) to the Confirm-To screen.
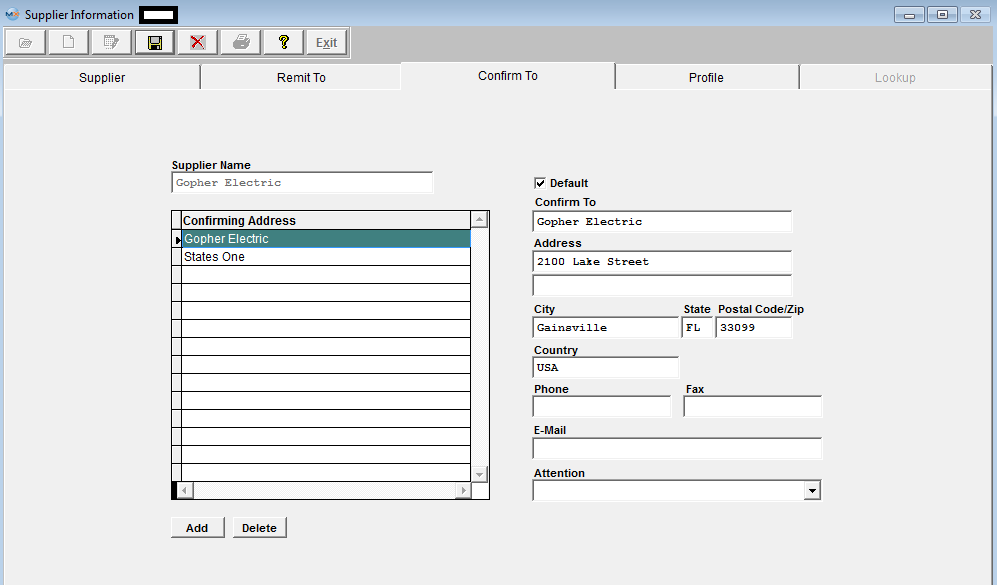
In this screen, the user defines the Supplier information for ordering purposes.
This screen and fields are identical to the Remit-to screen, except that the information will be used for the mailing address of the Supplier.
Pressing the Add action button will automatically fill the information from the Remit-to screen, if it has been completed. All data may be edited and saved, or new data may be added to the database. Note: There must be a default Confirm To address.
After completing the Confirm-To screen, the user may tab (clicks on the next) to the Profile screen.
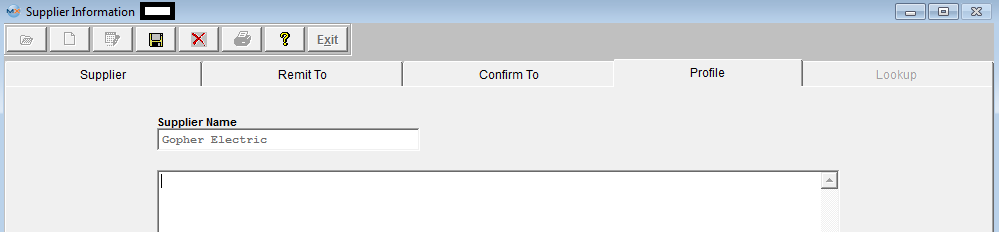
In this screen, the user defines the Supplier Profile notes for internal purposes. This screen is a memo field that may be used to record Supplier company information.
Once all of the data entry is complete. Depress the Save action button. You will be asked if you want to create another Supplier.
|
1.3.1.4.3. Edit Supplier Information |
Find the Supplier Information you need to edit.
Depress the Edit action button. All fields on the Supplier tab will be enabled for modification.
All fields on the Remit To tab will be enabled for modification.
Note: The system will keep the address information (on existing PO's) that was actually selected at the time the PO was created. If you add a new Supplier Remit To address and mark the new address as the Default. The previously created PO's will still carry the original Remit to (ManEx cannot assume that the user wants to change all Remit To's across the board for already created and approved PO's). The user will be required to edit each PO that the change affects and update the Remit to with the new default (any new PO's created will properly take the new default).
The Invoices created through the PO Reconciliation module also carry the original Remit to Address information. Any invoice that already was created and remains on your AP Aging will need to be edited through the Manual AP Entry screen. IF it was already released to the GL at that time, I don’t think that the Edit feature would be available. If you are unable to edit the Remit to information via the Manual AP Entry, then you can control the Remit to information that will print on the AP Check, by creating a Manual check through the Check Maintenance screen.
If you completely delete a Remit To address any previously created PO's will no longer have a Remit to address to refer to, therefore the remit to information on existing PO's will be blank. The AP check module prints the checks per the Remit To information that is associated with each PO, so the address printed on the check will also be blank. So, each PO that still has invoices residing within the AP Aging, will have to be edited and the Remit To information will have to be updated with the new address, if a Remit To address is deleted. We would suggest that the person making changes to the Remit To Address information is careful before deleting one from the system. You have to make sure that any record that has already been associated with that record has been processed through the system, and/or updated with the new address information.
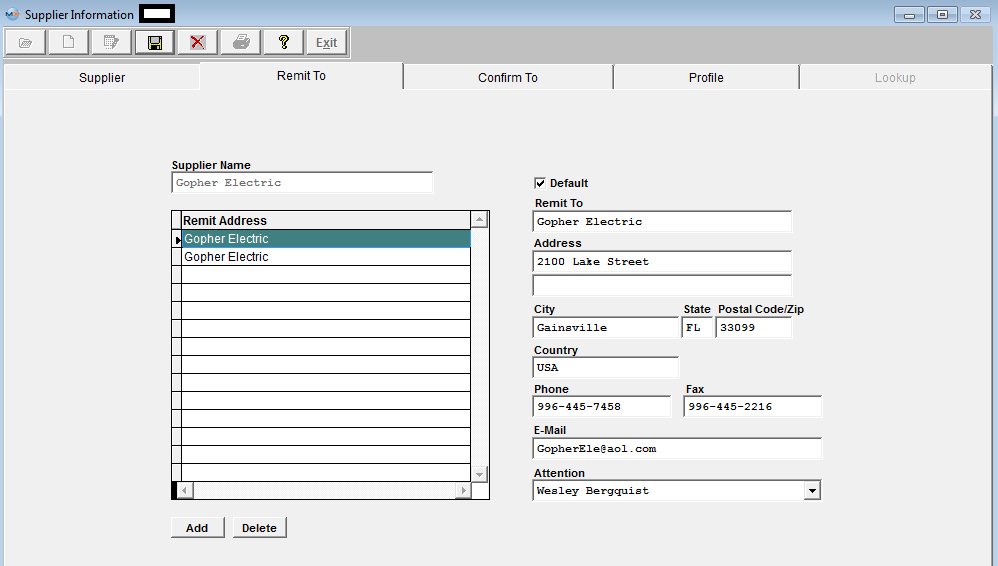
All fields on the Confirm To tab will be enabled for modification.
All fields on the Profile tab will be enabled for modification.
At the conclusion of the modification process, the user must either depress the Save action button or the Abandon changes action buttons.
|
1.3.1.5. Reports - Supplier Information |
To obtain the Supplier Information Reports within the Web, select the WEB Print button from the ManEx action buttons at the top of the screen. For further detail on How the Reports work within the Web refer to Article #5477.
Note: In order to access the Reports within the Web the Company Root URL must be setup within the System Appearance module and user must be linked to web within the System Security Module
Select the Report Type: SUPPLIER OR SUPPLIER CONTACT - A List of Reports will be displayed that are available on the Web
for SUPPLIER OR SUPPLIER CONTACT
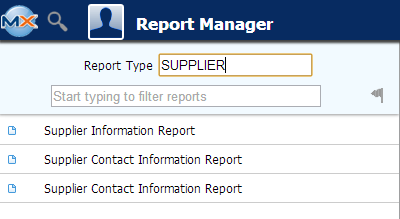 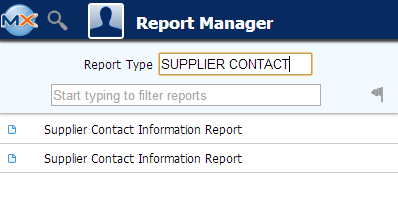
To obtain the Sales Order Reports within the desktop, select the Print button from the ManEx action buttons at the top of the screen.
The following reports screen
will display a list of reports that are available on the ManEx Desktop:
Highlight the report desired and Depress the OK button.
Supplier Information report
Select the Desired Supplier Status by highlighting your selection and depressing the > button .If you want all Suppliers with any status listed, depress the >> button.
Depress the OK button
|
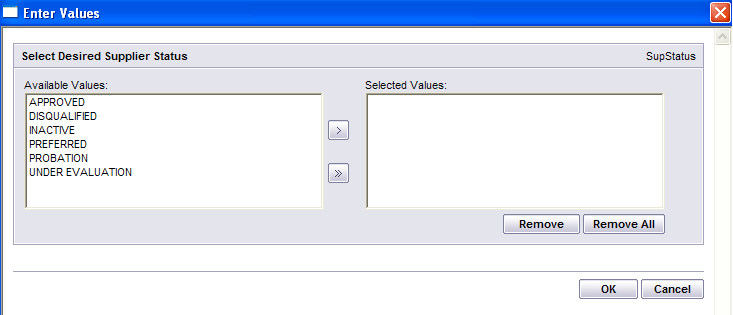 |
The following report will print:
Supplier Contact Information report
Select the Desired Supplier Status by highlighting your selection and depressing the > button .If you want all status's, depress the >> button.
Depress the OK button.
|
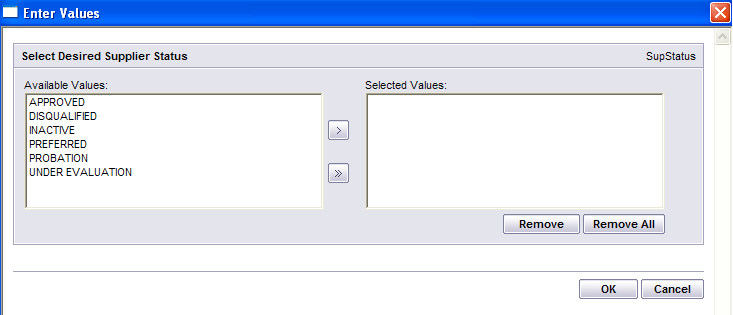 |
The following report will print:
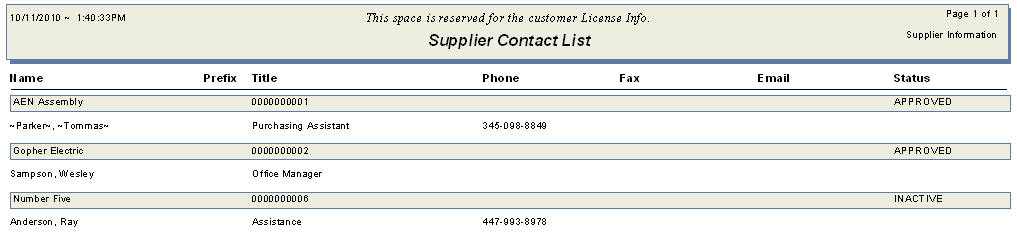
|
1.3.2. Supplier Contacts Information | |
1.3.2.1. Prerequisites for Supplier Contact Information | Prerequisites for Entering a New Contact:
After activation, "Supplier Contact Information" access for each user must be setup in the ManEx System Security module. Users with “Supervisor Rights” will automatically have access.
Supplier Name |
The Contact must refer to a Supplier, which has been set up in the Supplier module.
|
Picture File |
A picture of the contact may optionally be included as a memory jogger, but the picture must already be available to pickup in a picture format.
|
|
1.3.2.2. Introduction for Supplier Contact Information | The Contact Module is used to record the details of supplier contacts. Contacts may be of any nature, but must be associated with a supplier. Manex provides the user with the ability to maintain both professional and personal details about a contact, including provision for personal tastes and affiliations. Contacts must be entered in this module if they are to be included in the supplier remit-to and confirm-to data fields at a later time. A contact who has moved to another supplier may have a new supplier assigned to him/her without having to re-enter their personal data. |
1.3.2.3. Fields & Definitions for Supplier Contact Information |
1.3.2.3.1. Business Tab | Fields & Defintions
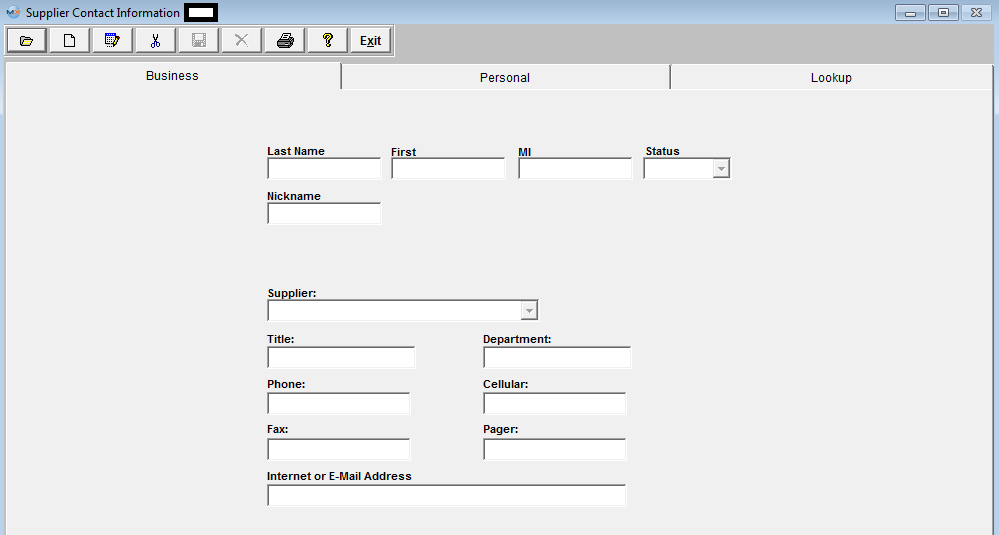
Last Name |
The last name of the contact being added or edited. |
First |
The first name of the contact being added or edited. |
MI |
The middle initial of the contact |
Status |
The status of the Supplier Contact, either Active or inactive. |
Nickname |
The nickname of the contact. |
Company |
The name of the Supplier. |
Title |
The title of the contact at the Supplier. |
Department |
The name of the department in which the contact is at the Supplier. |
Phone |
The phone number and/or extension for the contact at the Supplier (may be different than the supplier main number). |
Cellular |
The Cellular phone number for the contact. |
Fax |
The FAX number for the contact at the Supplier (may be different than the supplier main number). |
Pager |
The Pager number for the contact. |
Internet or E-mail Address |
The E-Mail address of the contact. |
|
1.3.2.3.2. Personal Tab |
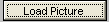 |
This button allows the user to load a photo for a Supplier contact. The photo file should be in the MANEX directory, and should be BMP or TIF format.
|
Birthday |
The Supplier Contact Birth Date.
|
Spouse's Name |
The Supplier Contact’s Spouse Name. |
Spouse's Birthday |
The Contact’s Spouse’s Birthday. |
Anniversary |
The Contact’s Anniversary. |
Home Phone |
The Contact’s Home Phone.
|
Address |
The Contact’s Home Address (two lines available). |
City |
The Contact’s Home City.
|
State, Zip |
The Contact’s Home State and Zip code.
|
Country |
The Contact’s home country.
|
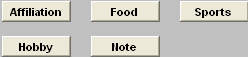 |
This set of buttons allow the user to record specific information that they may wish to retain about the supplier contact. It is divided into several categories to narrow the search for information later. Pressing any of these buttons brings up a memo window that may be added to, edited or canceled at will.
|
|
1.3.2.3.3. Lookup Tab | Fields & Defintions
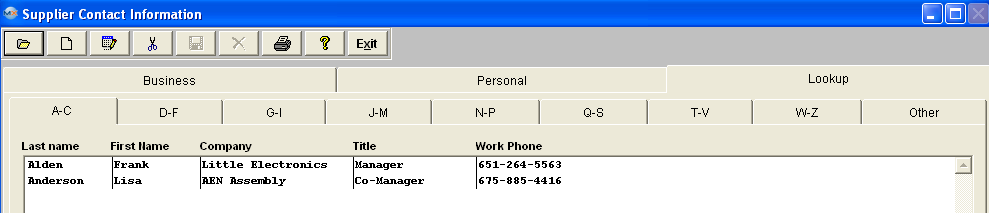
Last Name |
The last name of the contact. |
First Name |
The first name of the contact. |
Company |
The company to which the contact belongs. |
Title |
The title of the contact at the supplier. |
Work Phone |
The phone number and/or extension of the contact at the supplier (may be different than the supplier main number). |
|
1.3.2.4. How To .... for Supplier Contact Information |
1.3.2.4.1. Find a Supplier Contact |
Enter the SQLMANEX.EXE (within the ManEx root directory)
This action will then prompt the user for a password
|
 |
The following screen will be displayed, select Material Planning/Purchase Setup/Supplier Contacts Information
|
 |
The following screen will be displayed:
There are two ways to Find Existing Supplier Contacts:
1. By using the Find button located in the tool bar at the top of the screen. The following screen will appear: Select the desired Filter: by selecting the appropriate radio button - Active, InActive, or All. Select the desired Find: by selecting the appropriate radio button - Last Name, First Name, or Supplier
Enter the information into the red box, depress the Enter key and the information will populate the screen.
2. Depress the Lookup tab. This screen allows the user to locate a supplier contact alphabetically. Double click on the supplier contact name will bring the associated data into all screens without having to use the FIND action button. This screen will list all of the supplier contacts entered beginning with the Last Name, First Name, Company, Title and Contact Phone number (not the company phone number).
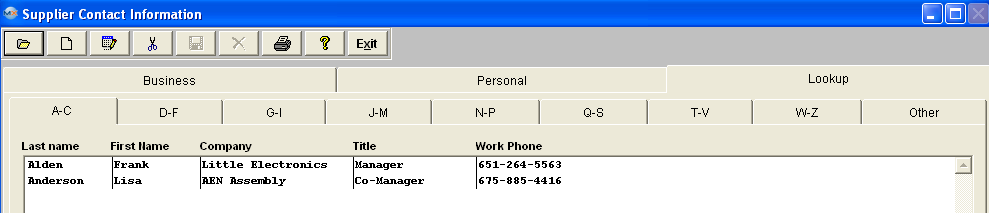
|
1.3.2.4.2. Add a Supplier Contact |
Enter the SQLMANEX.EXE (within the ManEx root directory)
This action will then prompt the user for a password
|
 |
The following screen will be displayed, select Material Planning/Purchase Setup/Supplier Contacts Information
|
 |
The following screen will be displayed:
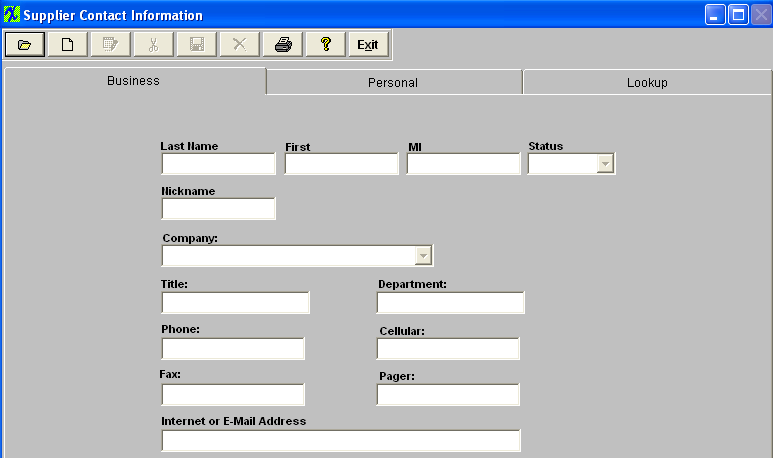
Depress the Add action button. The user will be prompted for an authorized password.
Type in the last name of the contact being added.
Type in the first name of the contact being added.
Type in the middle initial of the contact.
Select the status of the Customer Contact, either Active or Inactive.
Type in the nickname of the contact.
Select the company to which the contact belongs by depressing on the down arrow located on the right hand side of this field and highlighting the selection.
Type in the title of the contact at the supplier.
Type in the phone number and/or extension of the contact at the supplier (may be different than the supplier main number).
Type in the FAX number of the contact at the supplier (may be different than the supplier main number).
Type in the E-Mail address of the contact.
Type in the department at the supplier in which the contact works.
Type in a Cellular phone number for the contact.
Type in a Pager number for the contact.
After completing the Business information, the user may click on the Personal tab. In this screen, the user may enter personal information relating to the contact.
The Supplier Contact Directive buttons will now be active.
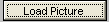 |
This button allows the user to load a photo for a supplier contact. The photo file should be in the MANEX directory, and should be BMP or TIF format. Select the desired image. It will appear in the window.
|
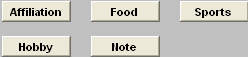 |
This set of buttons allow the user to record specific information that they may wish to retain about the customer contact. It is divided into several categories to narrow the search for information later. Pressing any of these buttons brings up a memo window that may be added to, edited or canceled at will.
|
Type in the Supplier Contact Birth Date.
Type in the Supplier Contact’s Spouse Name.
Type in the Contact’s Spouse’s Birthday.
Type in the Contact’s Anniversary.
Type in the Contact’s Home Phone.
Type in the Contact’s Home Address(two lines available).
Type in the Contact’s Home City.
Type in the Contact’s Home State and Zip code.
Type in the Contact’s home country.
Depress the Save action button to save changes, or depress the Abandon changes action button to abandon changes.
|
1.3.2.4.3. Edit a Supplier Contact |
Enter the SQLMANEX.EXE (within the ManEx root directory)
This action will then prompt the user for a password
|
 |
The following screen will be displayed, select Material Planning/Purchase Setup/Supplier Contacts Information
|
 |
The following screen will be displayed:
Once you have made your choice, the information will be displayed as follows:
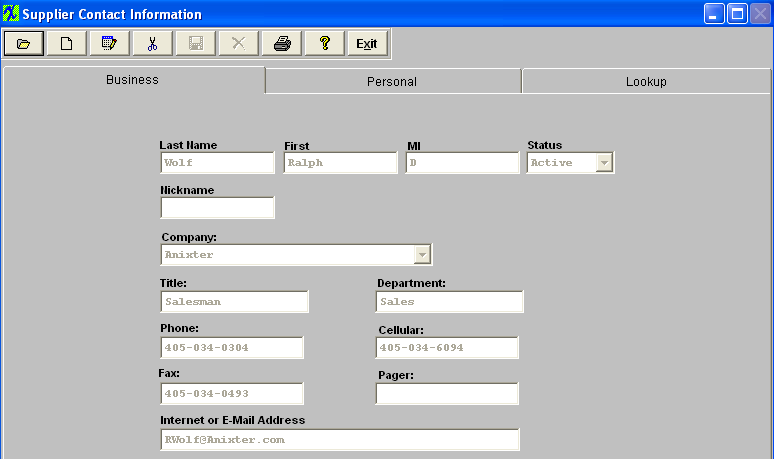
Depress the Edit action button. Enter password.
All fields available for editing will be enabled for modification.
At the conclusion of the modifications process, the user must Save changes, or Abandon changes using the action buttons.
Depress the Exit action button to return to the previous screen.
|
1.3.2.5. Reports - Supplier Contact Information |
To access the reports, depress the Print button at the top of the screen.
The report screen will be displayed:
Highlight the report desired and Depress the OK button.
The following report will print:
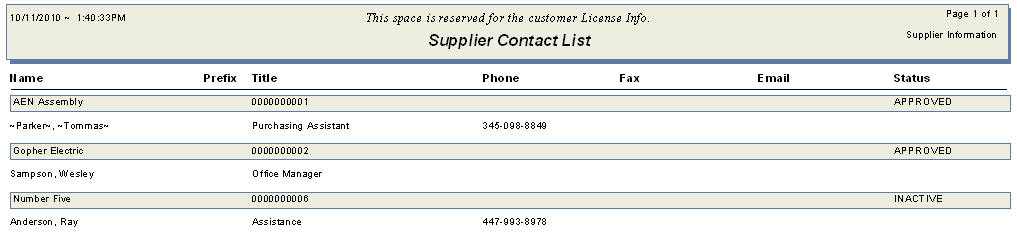
|
1.3.3. Receiving And Billing Information | |
1.3.3.1. Prerequisites for Receiving & Billing Information | Prerequisites for Entering Receiving & Billing Information:
After activation, "Receiving Information" access for each user must be setup in the ManEx System Security module. Users with “Supervisor Rights” will automatically have access.
Sales Tax Authority |
The Sales Tax Authority must be setup in System Setup /Sales Tax Authority Table
|
Ship Via |
The Ship Via must be set up in System Setup /Ship Via
|
FOB |
The FOB must be setup in System Setup /FOB
|
Ship Charge |
The Ship Charge must be setup in System Setup /Ship Charge
|
|
1.3.3.2. Introduction for Receiving & Billing Information | The Receiving & Billing Information Module is used to record the details of the user’s billing and receiving addresses. |
1.3.3.3. Fields & Definitions for Receiving & Billing Information |
1.3.3.3.1. Receiving Address Tab | 
Receiving Location |
This is the company name of the user’s receiving location. If you have more than one receiving location, you must select at least one as the default. You can choose among the selection of receiving addresses when you prepare the purchase order. |
 |
User must select at least one as the default by checking this box |
 |
Check this box if you would like to add the same address selected to the Billing Information as a Billing Address. |
 |
If the “Use One Default Tax for This Receiving Address and Use Single Tax Per PO Item” checkbox is not checked, the user can add multiple taxes for the receiving address, and the PO will calculate all taxes that are added in the tax list.
If the checkbox is checked, the user can add many taxes for the receiving address but only check one as default tax. When a PO is created, the default tax will be used to calculate. User can select different tax to calculate, but still only use one tax to calculate.
In supplier module, the user can set up default receiving address and default tax (if the default receiving address has single tax checkbox checked.)
|
Address |
This is the street address where you want your product delivered. Two address lines are allowed. The second line is for a suite number, etc.
|
City |
This is the City where you want your product delivered |
State |
This si the State where you want your product delivered |
Postal Code/Zip |
This is the Zip code where you want your product delivered |
Country |
This is the country of the receiving location. |
Phone |
This is the phone number at the receiving location.
|
Fax |
This is the fax number at the receiving location.
|
Attention |
This is the name of the contact at the receiving location.
|
Receiving Addresses |
All the Receiving addresses available are displayed in this box. |
|
1.3.3.3.2. Tax & Shipping Mode Tab | 
Receiving Location |
This is the name of the company at the receiving location. This carries over from the previous screen and can’t be edited.
|
Ship Via |
This is the name of the carrier |
FOB |
This selection is for Free-on-board information. This is the point when title passes |
Ship Charge |
This selection is for Shipcharge selection. This will indicate the shipcharge preference of the user. |
Account Number |
This is the user’s account number in those instances where the user will be paying the freight charges directly to the carrier and not to the supplier.
|
Delivery Time |
This is the time when the delivery is expected to be at the receiving location. |
Tax Exempt Number |
This is the user’s sales tax identification number for those purchases which are not subject to sales tax. Please check with your state or local sales tax authorities for more information regarding Sales Tax exemptions since the laws vary from state to state.
|
Default Tax |
This is available if the "use One Default Tax for This Receiving Address and use Single Tax Per PO Item" is checked in the Receiving Address tab. The user would then highlight the desired Tax rate they wish to have as the Default and check mark the Default Tax Box. This tax rate will default into the Purchase Order with the option for the user to change it per order.
|
Sales Tax Authority/Tax % |
This is the sales tax authority and the Tax % is for those purchases which are subject to tax. |
|
1.3.3.3.3. Billing Information Tab | 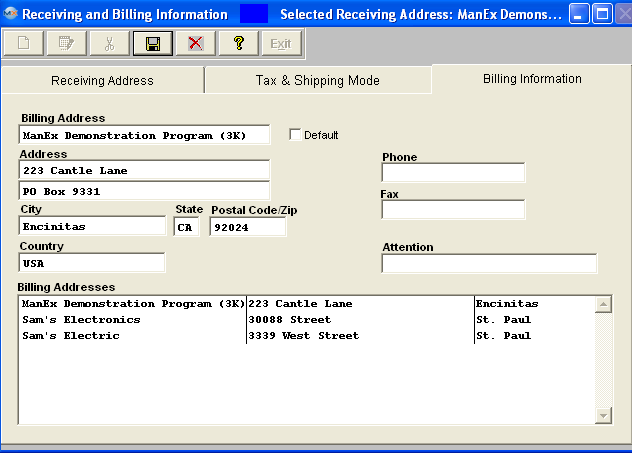
Billing Address |
This is the company name of the user’s billing location. If you have more than one billing location, you must select at least one as the default. You can choose among the selection of billing addresses when you prepare the purchase order. |
 |
User must select at least one as the default by checking this box |
Address |
This is the street address where you want your billing mailed. Two address lines are allowed. The second line is for a suite number, etc.
|
City |
This is the City where you want your billing mailed. |
State |
This si the State where you want your billing mailed. |
Postal Code/Zip |
This is the Zip code where you want your billing mailded. |
Country |
This is the country of the billing location. |
Phone |
This is the phone number at the billing location.
|
Fax |
This is the fax number at the billing location.
|
Attention |
This is the name of the contact at the billing location. Example: Accounts Payable.
|
Receiving Addresses |
All the billing addresses available are displayed in this box. |
|
1.3.3.4. How To ..... for Receiving & Billing Information |
1.3.3.4.1. Add Receiving and Billing Information |
Enter the SQLMANEX.EXE (within the ManEx root directory)
This action will then prompt the user for a password
|
 |
The following screen will be displayed, select Material Planning/Purchase Setup/Receiving and Billing Information Setup
|
|
The following screen will be displayed:
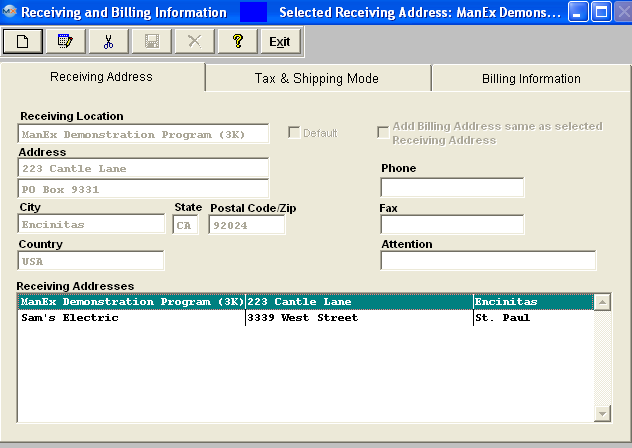
Depress the Add action Button. Note: When the Add button is selected user will be able to add "Receiving" and "BIlling" addresses.
Enter in all of the receiving information as you would like it to appear on your Purchase Order.
Enter a Receiving Location - this is a required field. If you have more than one receiving location, you must select at least one as the default. You can choose among the selection of receiving addresses when you prepare the purchase order.
Enter a street address - this would be where you would like the goods delivered. Two address lines are allowed. The second line is for a suite number, etc.
Enter a phone number at the receiving location (if applicable).
Enter a fax number at the receiving location (if applicable).
Enter in the city, state and zip code.
Enter in the country of the receiving location.
Enter in the name of the contact at the receiving location.
Check the "Add Billing Address same as selected Receiving Address" box if you would like this address added to the Billing Address list also. Note: If you check this box, it will stay checked until you select a different receiving address. Unchecking this box will not affect any data. If this box is check and the address user is trying to add already exists they will receive the following message:
A sample of the completed screen appears below:
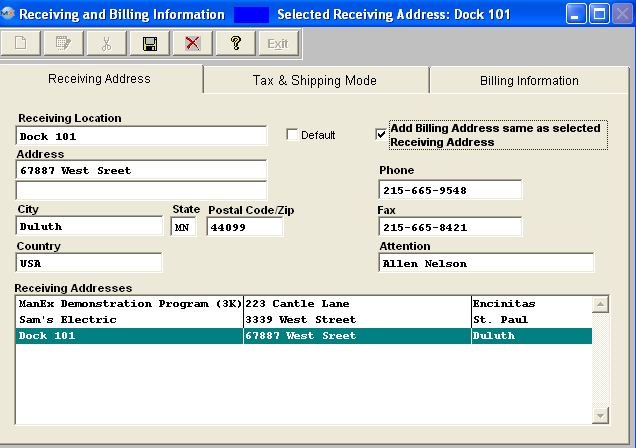
Depress the Tax and Shipping Mode information.
This screen has information for carrier name, FOB, tax status, etc.
The name of the company at the receiving location carries over from the previous screen and can NOT be edited.
Select the carrier from the pull down. The selections default in from the Ship Via setup module within System Setup.
|
|
Select the FOB (Free-on-board) information from the pull down. This is the point when title passes. the selection default in from the FOB setup module within System Setup.
|
|
Sales Tax
The sales tax authority and the Tax % is for those purchases which are subject to tax. Depress the "Add Tax" button and the selections will default in form the Sales Tax Authority Table setup module setup within the System Setup.
Choose the one applicable to your company’s purchases.
|
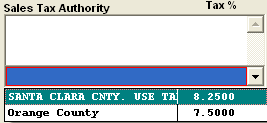 |
Select the Ship Chargefrom the pull down. The selections are defaulted in from the Ship Charge setup module within System Setup. This will indicate the shipcharge preference of the user
|
|
Enter in the user’s account number in those instances where the user will be paying the freight charges directly to the carrier and not to the supplier.
Enter in the time when the delivery is expected to be at the receiving location.
Enter in the user’s sales tax identification number for those purchases which are not subject to sales tax. Please check with your state or local sales tax authorities for more information regarding Sales Tax exemptions since the laws vary from state to state.
A sample of the completed screen appears below:
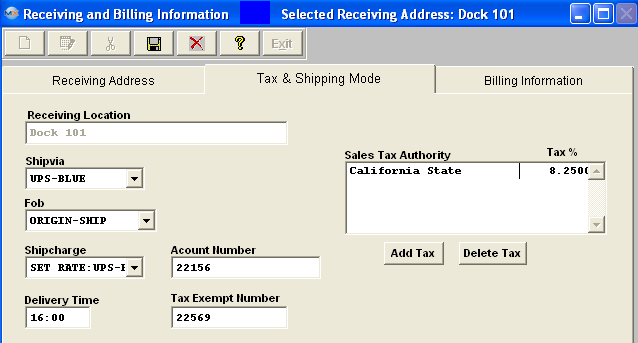
Depress the Billing information tab. This would be the address of the user’s Accounts Payable department. If you checked the "Add Billing Address same as selected Receiving Address" box on the Receiving address page the address was automatically added, however you can over write this address if you choose to do so.
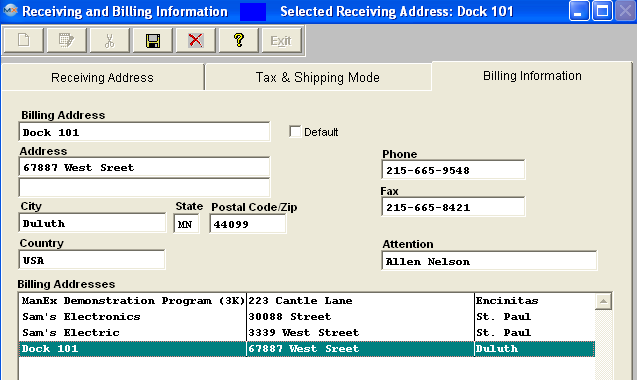
If you want to keep all the addresses listed and add a new address then you would need to depress the Save button at this point, then depress the Add button to add a new address to the Billing Address list.
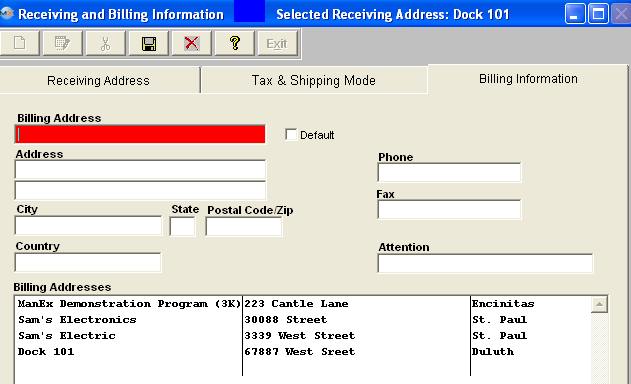
Enter in a Billing name or location. Note: This is a required field. If you have more than one billing location, you must select at least one as the default. You can choose among the selection of billing addresses when you prepare the purchase order.
Enter in the street address where you want your billing mailed. Two address lines are allowed. The second line is for a suite number, etc.
Enter in the phone number at the billing location (if applicable)
Enter in the fax number at the billing location (if applicable).
Enter in the city, state and zip code.
Enter in the country of the billing location.
Enter in th name of the contact at the billing location, normally Accounts Payable, for example.
The completed screen would appear as follows:
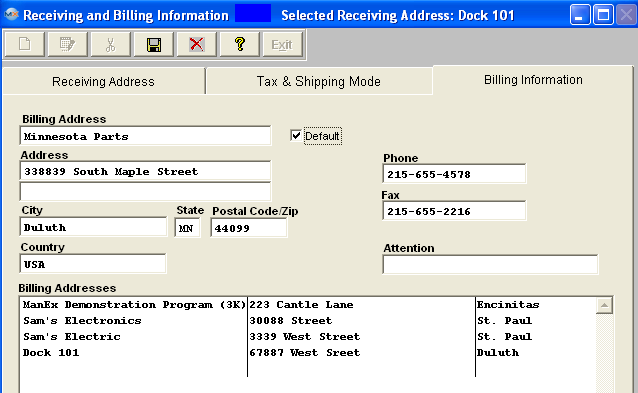
Depress the Save record action button to save changes, or depress the Abandon changes action button to abandon changes.
|
1.3.4. Supplier Contract Management (OPTIONAL Module) |
|
1.3.4.1. Prerequisites for Supplier Contract Mgmt |
ManEx’s standard module configuration allows most users to accomplish their daily tasks. For those users wanting to get more from ManEx by leveraging the total solutions, this is one of the optional modules available for purchase. If user purchase's the Optional module -In-Plant Store (IPS) they will also receive the Supplier Contract Management module. These two modules go together. To place an order or to learn more about this specific module or any of the other optional modules please contact us at http://manex.com"contactus.aspx
Prerequisites for Entering a Supplier Contract:
After activation, "Contract Purchase Management" access for each user must be setup in the ManEx System Security module. Users with “Supervisor Rights” will automatically have access.
|
1.3.4.2. Introduction for Supplier Contract Mgmt |
Supplier Contract Management is for recording the contract with the supplier for In-Store items.
IPS inventory is received via Inventory Handling or IPS Upload. The IPS module is to keep inventory as Supplier owned but is recognized as being available for consumption by MRP and kitting. When it is consumed by kitting or transfer, a Purchase Order is automatically generated to reimburse the Supplier for the material.
There are three uses for the IPS module: supplier owned but stored on-site, customer owned and stored on-site, and internally owned but obsolete parts that the user does not want to affect the books. In any of these situations a supplier must be established (this means that the customer must also be a supplier and the user must be a supplier if they have obsolete inventory in the IPS location).
Tracking In-Store processing through MANEX:
· Add the Supplier in the Supplier Information Module.
· Set up an In-Store Warehouse and the applicable G/L number in System Setup/Warehouse Setup module.
· Add the in-stores item into the Item Master in the Inventory Control Mgmt module and create an In-Store Warehouse.
· Move the materials into the warehouse using the Inventory Handling module.
· Add the In-Store Contract in the Supplier Contract Mgmt module.
· Pull a kit (only a kit shortage gets a P.O.) within the Kitting & Shortage Mgmt module.
· Add a Purchase Order and select In-Stores within the PO Mgmt module.
|
1.3.4.3. Fields & Definitions for Supplier Contract Mgmt |
1.3.4.3.1. Supplier & Contract Part List Tab |
Supplier & Contract Part List Field Definitions
Supplier |
The Name of the Supplier with which the contract exists.
|
 |
This button will be displayed in RED if there are notes regarding the contract.
|
Part Number |
The number the user has assigned to the part.
|
Rev |
The revision number applicable to the part Number. |
Part Class |
The classification to which the part is assigned.
|
Part Type |
The type within the classification to which the part is assigned.
|
Description |
The description of the part.
|
Prim |
A check in the box indicates that the supplier is considered “Primary” and will be the first supplier consider for this part.
|
Note |
This column is for notes regarding the Part Number.
|
Contract Number |
The number of the contract.
|
Quote Number |
The number of the quotation that the supplier made.
|
Start Date |
The beginning of the contract period.
|
Expiration Date |
The ending of the contract period.
|
Quantity Limit |
The top limit on each In-Store purchase.
|
UOM |
The unit of measure for the part.
|
|
1.3.4.3.2. Manufacturer & Price List Tab |
Manufacturer & Price List Tab Field Definitions
For the Part Number highlighted in the Supplier & Contract Part List tab:
Part Number |
The number the user has assigned to the part.
|
Rev |
The revision number applicable to the part Number.
|
Part Class |
The classification to which the part is assigned.
|
Part Type |
The type within the classification to which the part is assigned.
|
Description |
The description of the part.
|
Manufacturer:
Add/Delete Manufacturer (Buttons) |
These buttons are used to add or delete manufacturers |
Manufacturer |
The name of the manufacturer.
|
Manufacturer’s Part Number |
The number the manufacturer has assigned to the part.
|
Price:
Add/Delete Price (Buttons) |
These buttons are used to add or delete quantity price breaks. |
Quantity Break |
This is the point where the user wants to stop using the price listed and have the system use the next price listed. For Example if you have the following price breaks setup as in the screen above:
100 @ $2.685; This price will be used for qty's 1-100
300 @ $2.50; This price will be used for qty's 101-300
1,000 @ $2.00; This price will be used for qty's 301- and UP
If you have only one price break setup for example; 1 @ $5.65 this price will be used for qty's of 1 and UP.
|
Price Each |
The price for one unit at the quantity indicated on the left. |
|
1.3.4.3.3. Contract Part & Supplier List Tab |
Contract Part & Supplier List Tab Field Definitions
Part Number List:
Part Number |
The number the user has assigned to the part.
|
Rev |
The revision number applicable to the part Number.
|
Part Class |
The classification to which the part is assigned.
|
Part Type |
The type within the classification to which the part is assigned.
|
Description |
The description of the part. |
Div |
If the user has the multi-plant version, the division number will display here.
|
Supplier:
For the part highlighted on the left, the Supplier(s) of that part will display. The primary or “First Choice” supplier will have a check mark in the Prim column, as illustrated above.
|
1.3.4.4. How To .... for Supplier Contract Mgmt |
1.3.4.4.1. Find an In-Store Supplier Contract |
Enter the SQLMANEX.EXE (within the ManEx root directory)
This action will then prompt the user for a password
|
 |
The following screen will be displayed, enter the Material Planning/Purchase Setup/Supplier Contract Management Module
|
 |
The following screen will appear:
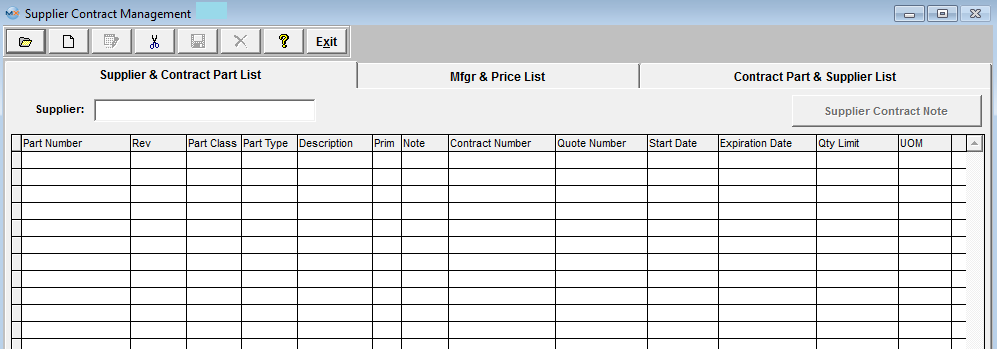
To find an existing contract, depress the Find action button.
The selection screen to the right will appear:
To find by Contract Number, Supplier, or Part Number user must enter the number in the Red Box.
|
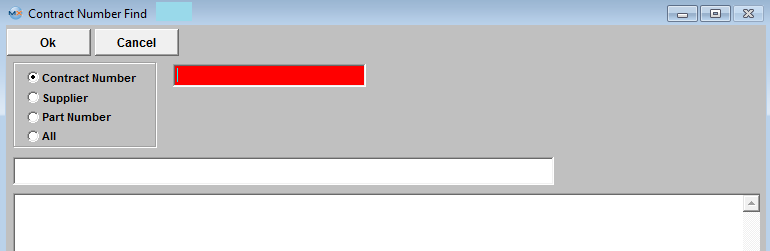 |
If you select ALL, the selection screen to the right will appear:
User can either enter the Contract number in the Red box, or highlight the selected record and double click on the highlighted record.
|
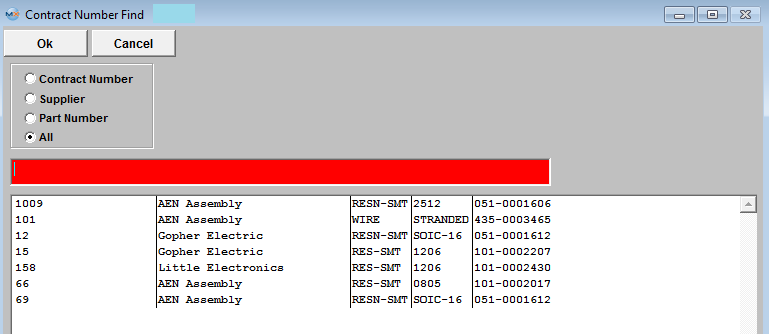 |
After the Find selection is completed, all the Contracts for the Selected Supplier are displayed on screen.
|
1.3.4.4.2. Add a New In-Store Supplier Contract |
Enter the SQLMANEX.EXE (within the ManEx root directory)
This action will then prompt the user for a password
|
 |
The following screen will be displayed, select Material Planning/Purchase Setup/Supplier Contract Management
|
 |
The following screen will be displayed:
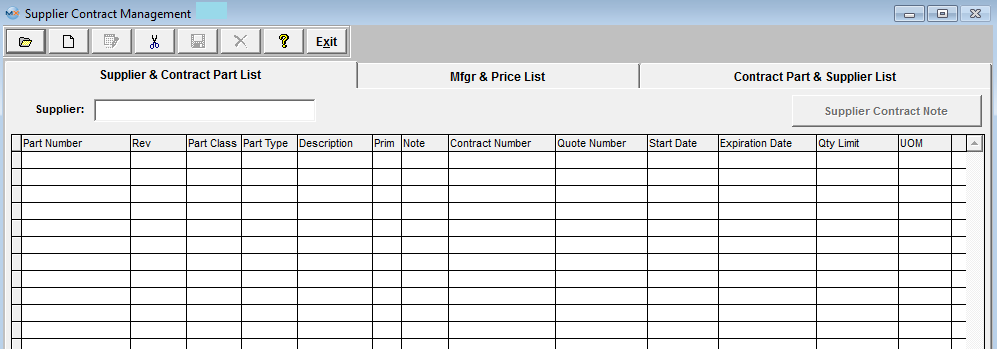
To add a new In-Store Supplier Contract, depress the Add action button while in the Supplier & Part List tab.
Enter the password. The selection screen to the right will appear: |
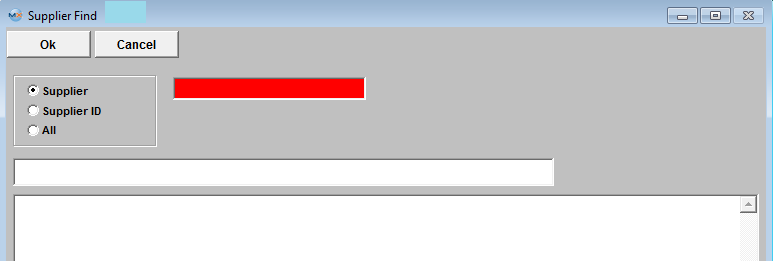 |
If you select All, the selection screen to the right will appear:
Enter the Supplier or Supplier ID into the red box or highlight and double click.
|
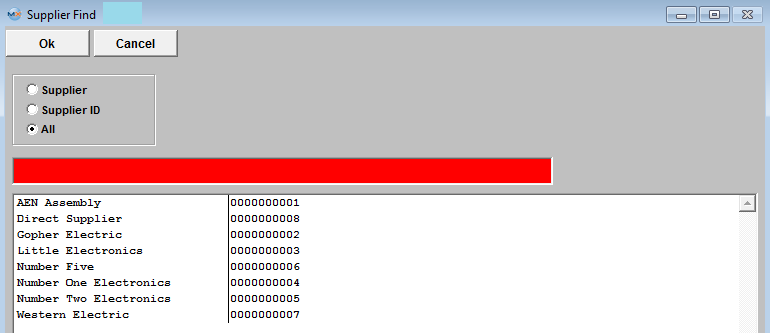 |
Once the Supplier is selected, a list of parts will appear:
Enter the applicable Part Number into the red box or highlight your selection and double click.
The part number selected will populate the screen, as displayed below:
|
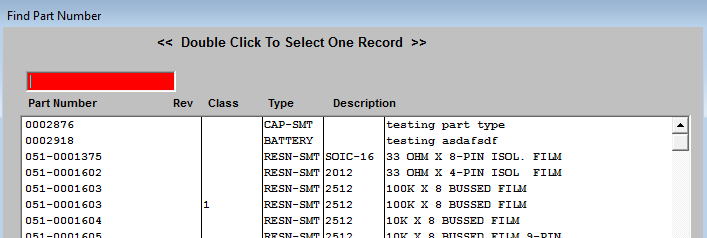 |
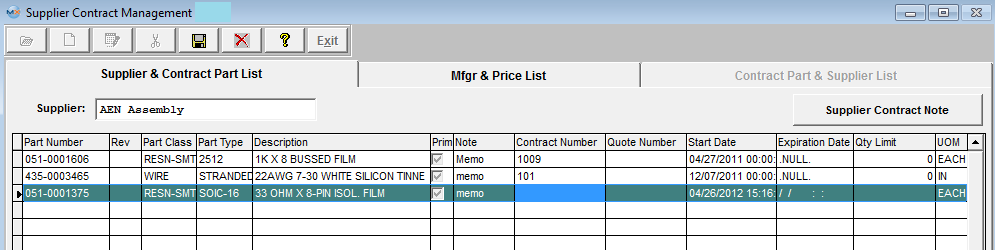
If you want to add a note regarding the supplier contract, depress the Supplier Contract Note button. Depress the Edit button. Enter in the note. Depress the Save button. Depress the Exit button.
If you want to add a note regarding the Part Number, click on the Note column. Depress the Edit button. Enter in the note. Depress the Save button. Depress the Exit button.
Enter in a Contract number, a Supplier’s Quote number, and a start date for the contract. Today’s date will default, but you can override it. Enter in an expiration date. Enter in a quantity limit (the highest quantity which can be purchased).
Depress the Manufacturer & Price list tab. The following screen will appear:
Note that the Manufacturer and Manufacturer’s Part Number per the Inventory Master have populated the left hand of the screen.
 |
If there are Manufacturer's listed in the Inventory Control module that are NOT being displayed on the Mfgr & Price List tab, user may depress this button and a list of manufacturer(s) listed in the Inventory Control module that are NOT being displayed in the Mfgr & Price List tab, will be displayed and user at this time may add them by double clicking on them.
If there are no Manufacturer's listed in the Inventory Control module other than the ones listed on screen the following message will appear:
|
 |
If user would like to Delete a Mfgr from the Mfgr list, highlight the Mfgr and depress this button, the following message will appear:
Depress "Yes" to continue the deletion process or "No" to cancel the deleting process.
|
 |
While the Manufacturer is highlighted, depress the Add Price button on the right hand side of the screen. Enter a quantity break and the Price Each for that quantity. Continue depressing the Add Price button on the right hand side of the screen, entering a quantity break and the Price Each for that quantity until ALL of the Pricing breaks under the contract are entered.
|
 |
If user would like to Delete a price, highlight the record and depress this button, and the following message will appear:
Depress "Yes" to continue the deletion process or "No" to cancel the deleting process.
|
To apply Price Breaks to other Mfgr, user has the option to apply them individually or deperss this button
If user elects to Depress the "Apply Price Break to Other Mfgrs" the following screen will appear:
Select the Mfgr(s) and depress OK to continue or Cancel to abort screen.
Depress the Save record action button.
NOTE: Users MUST enter Qauntity Break and Price Each for every manufacturer listed or they will receive the following message and will unable to Save the record until ALL Quantities and Pricing breaks have been entered for the part highlighted.
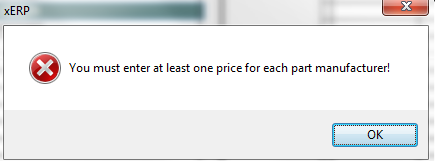
Depress the Contract Part & Supplier List tab:
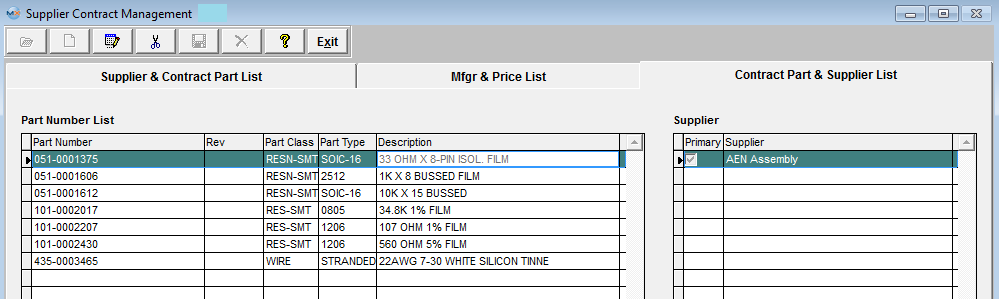
Note that the Part Number you selected in the Supplier & Contract Part List tab is listed in the Part Number list. Highlight that Part Number. The primary supplier for that part will display, as illustrated above.
|
1.3.4.4.3. Edit an In-Store Supplier Contract | Find the Supplier contract you wish to Edit.
Depress the Edit action button. Type in the password. You’ll be able to add a Contract Note, change the Contract Number, Quote Number, Start Date, Expiration Date, Quantity Limit, Quantity Break and Price Each.
Depress the Save action button to save your changes, or depress the Abandon changes button to abandon changes.
|
1.4. In-Plant Store (IPS) (OPTIONAL Module) | |
1.4.1. Prerequistes for In-Store PO |
ManEx’s standard module configuration allows most users to accomplish their daily tasks. For those users wanting to get more from ManEx by leveraging the total solutions, this is one of the optional modules available for purchase. If user purchase's the Optional module -In-Plant Store (IPS) they will also receive the Supplier Contract Management module. There are three uses for this module: supplier owned but stored on-site, customer owned and stored on-site, and internally owned but obsolete parts that the user does not want to affect the books. To place an order or to learn more about this specific module or any of the other optional modules please contact us at http://manex.com"contactus.aspx
After activation, "Purchase Order Management" access for each user must be setup in the ManEx System Security module. Users with “Supervisor Rights” will automatically have access.
Prerequisites Required for Entering an In-Store PURCHASE ORDER
Supplier |
The Supplier database must be established |
Part number |
The Part Number must exist for a product or part within Inventory Control Mgmt module. |
In-Store Location |
An In-Store Location MUST be Setup |
Purchasing Approvals |
A list of employees and their approval authorizations must exist in the Purchase Setup module. |
Supplier Contract |
The contract with the supplier must be set up in the Supplier Contract Management module
|
Accounting Setup |
Under Sqlacctsetting.exe Inventory setup make sure you have Instore Inventory Account GL setup. |
Optional Prerequisites for Entering an In-Store PURCHASE ORDER
Contacts |
Contacts can be used for identifying seller. |
Tax Authority |
If purchasing taxable items, must be established in System Setup and in Receiving & Billing. |
Units of Measure |
If purchase units are different than stocking units |
|
1.4.2. Introduction for In-Plant Store | Internal In-Plant Store Explanation
The IPS module is to keep inventory as Supplier owned but is recognized as being available for consumption by MRP and kitting. When it is consumed by kitting or transfer, a Purchase Order is automatically generated to reimburse the Supplier for the material.
This inventory type can be used to store all excess inventory caused by the minimum purchase requirement on parts for a particular turnkey job, but for which the customer does not want returned, and the User wishes not to count the inventory as assets as these parts may not be used in the future. The leftover parts can be stored in this inventory for possible future use and does not have to be treated as regular internal inventory for the accounting purpose. The system allows all in-store transactions to happen without any contract entered in the system until the user is ready to create an In-Store PO.
There are three uses for this module: supplier owned but stored on-site, customer owned and stored on-site, and internally owned but obsolete parts that the user does not want to affect the books. In any of these situations a supplier must be established (this means that the customer must also be a supplier and the user must be a supplier if they have obsolete inventory in the IPS location).
In-Store purchasing overview: In-Store is the situation where the Supplier has placed raw materials in the user’s warehouse. The Supplier still owns the raw materials. When the user is ready to use the Supplier’s raw materials, he/she issues the parts to a kit then creates an In-Store Purchase Order. For In-Store POs, the user may select by Supplier or by Part Number. Then the user may find records according to the selection. Once found, the user may create a PO for the In-Store Consumption. In-Store Purchasing also includes receiving.
This module also provides Instore designation for part numbers with a "MAKE" source. This will allow users to utilize inventory handling to add items sourced as MAKE parts to enter inventory into the IPS module. Then, as they are needed, be able to kit to work orders those subassemblies from IPS. There would be no GL records created when the material is moved into IPS via Inventory Handling. But on issue to kit, a PO will be generated, for the amount established in the IPS Contracts, and the Kit (along with WIP) will be charged for the standard cost of the assembly.
Tracking In-Store processing through MANEX:
· Add the Supplier in the Supplier Information module.
· Set up a Stores Warehouse and the applicable G/L number in System Setup/Warehouse Setup module.
· Add the in-stores item into the Item Master in the Inventory Control Mgmt module and create the In-Store warehouse.
· Move the materials into the warehouse using the Inventory Handling module.
· Add the In-Store Contract in the Supplier Contract Mgmt module.
· Pull a kit (only a kit shortage gets a P.O.) within the Kitting & Shortage Mgmt module.
· Add a Purchase Order and select In-Stores within the PO Mgmt module.
|
1.4.3. Fields & Definitions for In-Plant Store | 
Sort By |
Depress the radial to Sort the In-Store items by Supplier or Part Number |
On/Off |
Check this box to select the Part to Create In-Store PO |
Supplier |
Name of Supplier (Defaulted from Supplier Contract Mgmt) |
Issue Date |
Date issued to the In-Store Warehouse (Defaulted from the Kitting & Shortage Mgmt ) |
Used By |
Displays Work Order part is being used for (Defaulted from the Kitting & Shortage Mgmt) |
Part Number |
Part Number of In-Store item (Defaulted from the Kitting & Shortage Mgmt ) |
Rev |
Revision of In-Store item (Defaulted from the Kitting & Shortage Mgmt) |
Quantity |
Quantity required for WO from the In-Store Warehouse (Defaulted from the Kitting & Shortage Mgmt) |
Class |
In-Store item Class (Defaulted from the Kitting & Shortage Mgmt) |
Type |
In-Store item Type (Defaulted from the Kitting & Shortage Mgmt) |
Description |
In-Store item Description (Defaulted from the Kitting & Shortage Mgmt) |
Part Mfgr |
In-Store item Part Mfgr (Defaulted from the Kitting & Shortage Mgmt) |
MPN |
In-Store item Part Mfgr Part Number (Defaulted from the Kitting & Shortage Mgmt) |
Cost each |
Cost each for In-Store item (Defaulted in from Supplier Contract Mgmt ) |
Extended Amnt |
Extended Amount for In-Store item |
Contract No |
Supplier Contract Number assigned to In-Store item (Defaulted from Supplier Contract Mgmt) All parts with same contract number will be grouped together on one In-Store PO for the same supplier. For further detail see Article #3438 . |
Quote No. |
Quote number assigned to In-Store item (Defaulted from Supplier Contract Mgmt ) |
UOM |
Unit of measure for In-Store item (Defaulted from ICM) |
PUOM |
Purchase unit of measure for In-Store item (Defaulted from ICM ) |
Package |
Packaging for In-Store item (Defaulted from ICM) |
Buyer |
Buyer assigned to In-Store item (Defaulted from ICM ) |
PO No |
PO number assigned to In-Store item |
Div |
Division assigned to In-Store item |
|
1.4.4. How To ........ for In-Plant Store |
1.4.4.1. Set-Up for an In-Store PO |
Find a part or product that exists within Inventory Control Mgmt.
Setup an In-Store Warehouse for part.
Setup up a contract with a supplier(s) within the Supplier Contract Management module.
For all other Prerequisites see Article #5575.
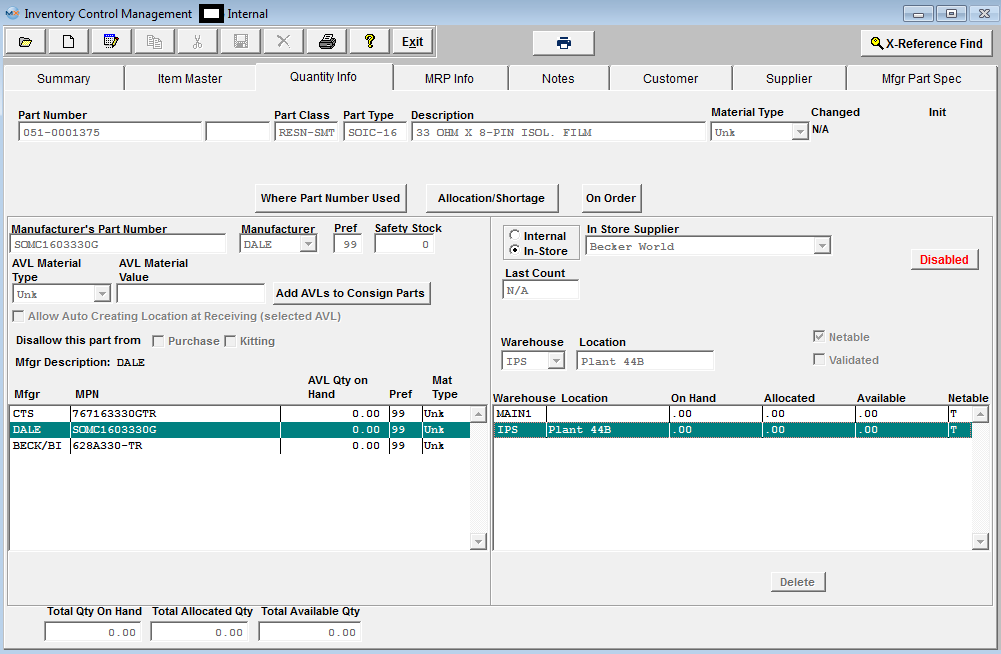
Create an Inventory Receipt in the system for the In-Store location using the Inventory Handling module. Since the Receipt was made to a In-Store location there will be no Accounting transaction created at this time.
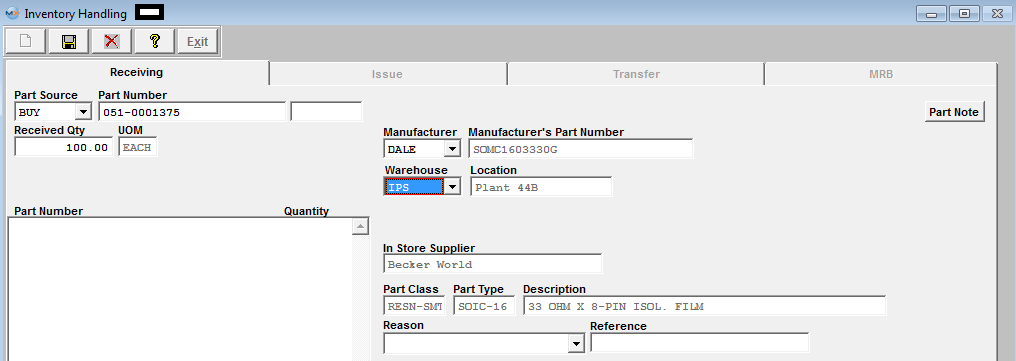
Or Upload parts to the In-Store warehouse using the IPS Upload module.
At this time the following Accounting Inventory Issue Transactions will be created within the system.
|
1.4.4.2. Creating an In-Store PO |
The following screen will appear:
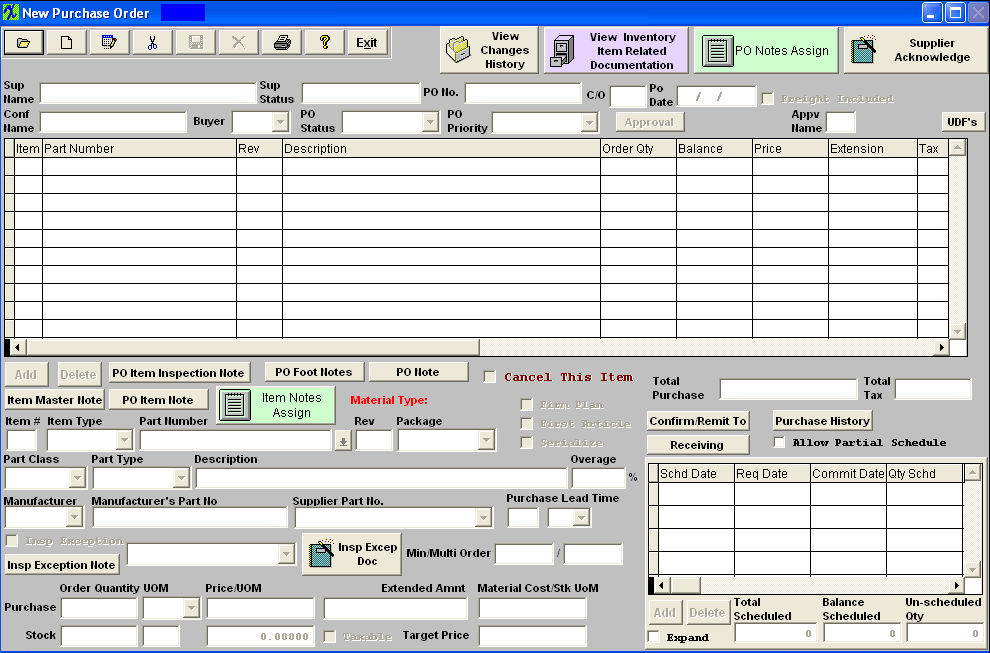
Depress the Add a record button.
Select In-Store PO |
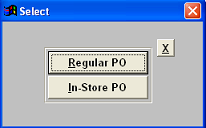 |
The following screen will appear. Sort By: Supplier or Part Number by clicking on the appropriate radial.
If you Sort By Part Number, an entry box will appear, type in the Part Number and the Revision character, if applicable.
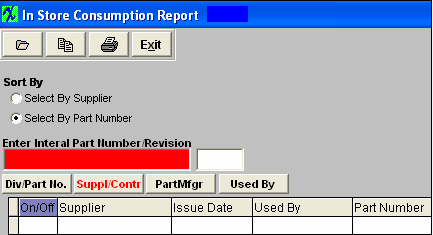
If you Sort By Supplier, the following screen will appear, highlight the supplier of choice.Depress the > button. If you want all of the Suppliers, depress the >> button.
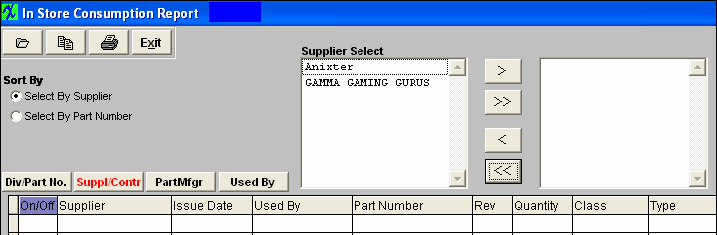
Depress the Find Record button to find records according to the selection. The bottom of the screen will populate. You may sort by Div/PartNo., Supply/Contr, Part Mfgr, or Used By; by depressing the appropriate button.
Depress the On/Off button to check all of the selections. Or, check them individually.
Depress the Copy button. This will create a list of Purchase Orders for In Store Items, which will go directly to the default printer. The temporary purchase order number will appear on the report.
NOTE: If user has contract pricing already
setup for example: Up to qty of 5 = $1.00, Up to qty of
100 = $0.94, Up to qty of 101 = $0.95. When the in-store PO is created it will find
the correct price break. Also if there are multiple records for the
same part, which will end up on the same PO, (like multiple serial numbers or lot codes), the
qty will be combined in determining the correct price break.
Depress the Exit button. This will create the IPS PO. Depress exit button again and it will pull up the IPS record created. The system will NOT allow the user to edit an IPS PO.
Note: In-Store PO's group the parts by Contract number per Supplier. For further detail see Article #3438 .
The user will then need to review the IPS PO created and approve the purchase order.
Pressing the APPROVAL button in the Purchase Order module will ask for the user’s password.
The user must enter a password that has been authorized to approve the dollar amount of the order. Entry of an authorized password and approval inactivates the 1st approval button and places the initials of the person approving the order next to the approval button. If the user is requiring two approvals, the process is repeated for the second approval. Once the PO has received it's final approval a Purchase Order number will be assinged and the PO Status marked as closed. At this point the normal Un-Reconciled Receipt account transaction will be created within the system. Then from this point on the Accounting transaction follow the normal flow through the system.
Returning In-Plant Inventory to Supplier
If the user has in-store items, which they want to return to Vendor without any impact on accounting or PO (like obsolete parts) they can return these parts using the Inventory Handling module.
Depress the Issue tab. Depress the Add record button. Enter Part Source, Part Number, Issued Qty, Issue Account Description, Issued To, Mfgr, then select the In-Store warehouse. Check the "In-Store Return 2 Vendor" box. (Note: This box will only be visible if the In-Store warehouse is selected). If this box is checked no purchase order will be created and there will be no impact on accounting.
Depress the Save button to Save the changes, depress the Abandon changes button to abandon changes.
|
1.4.5. Reports - In-Plant Store | The In-Store screen has 3 additional check boxes, one for each report and one for output to XL. If a report is selected and the user clicks on the "Print" icon the report will be generated to preview on the screen, if the output to excel is also selected, then the report data will be exported to Excel. If both reports are selected the reports will be generated in sequence.
.
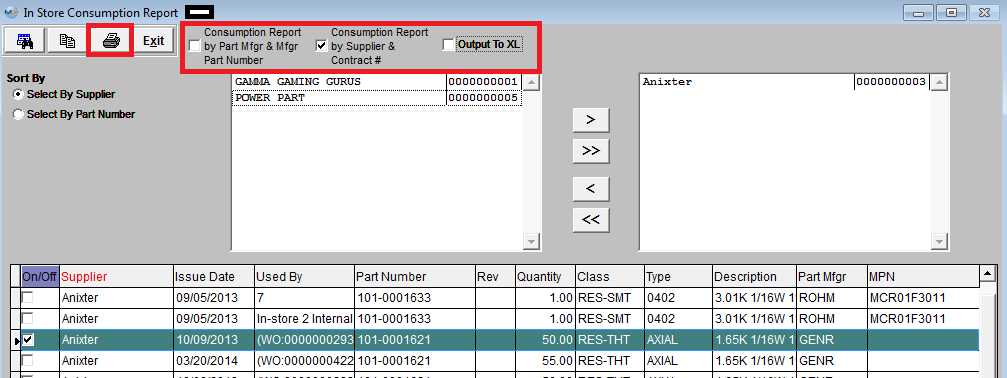
|
|