After activation, "Inventory Control" access for each user must be setup in the ManEx System Security module. Users with “Supervisor Rights” will automatically have access.
Before entering products and parts in the Item Master, the following product, part and system classifications and item parameters must be setup in ManEx using the System Setup Material Module. Note: that although data entry is possible with only the Prerequisites below, using the Data Entry Defaults explained in the next section is strongly advised to save time and maintain consistency.
Product and Part Class |
All items must be assigned a Class code (Finished Goods, Subassembly, Resistor, Capacitor, Raw PCB, etc.) in order for ManEx to number, connect, sort and organize the items. Class codes are User-defined but chosen carefully.
|
Product and Part Type |
Each Class is further grouped into Types (Surface Mount, Thru-Hole, Precision, Programmed, etc.) to standardize description fields and allow use of default values. This speeds up data entry and eliminates redundant data and duplicate records.
|
Units of Measure |
Several standard Units of Measure (U/M) are already setup in ManEx.Additional purchase or stocking U/M’s must be added in System Setup. Also, if the Purchase and Stocking U/M are different (eg. Wire purchased in FT, issued in IN.), a Conversion Formula must be entered in System Setup Unit of Measure & Conversion.
|
Numbering System |
The User must select Automatic or Manually Numbering in System Setup Number System Module. For Auto-numbering, the Beginning Number must be entered. A customer-selected prefix can be entered in System Setup Number System to be added to each Manual or Auto-Numbered part no.
|
Warehouse Assignments |
A System Setup (Warehouse Setup) to assign names and General Ledger Numbers (for ManEx Accounting) to the hard-coded MAIN1, WIP, WO-WIP and MRB Warehouses is required. Additional FGI and/or In-Store Warehouses can be added if assignment as stocking locations during Item Master data entry is desired.
|
Optional Data Entry Default fields are not required for Item Master entries, but are highly recommended to ensure consistency and save time during data entry.They are shown below.
Data Entry Defaults
Item Master Data Entry Defaults are selections that remain the same for most of the items for a particular Class and Type. These Defaults are entered in System Setup Inventory Part Class and will be automatically filled in by ManEx once the Item Class and Type have been selected during data entry of a new Item. Defaults can be over-ridden during data entry.
For instance, if the User wished to make the Default entry for Item Package to be REEL for all Items with the Class RES-SMT and the Type 0402, the User should select REEL in the Package field of the System Setup when entering Type “0402" as shown in the example.
|
|
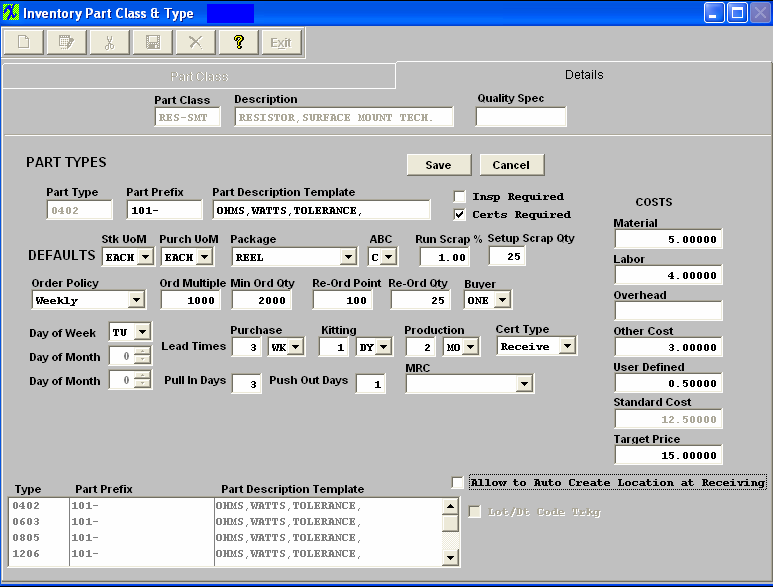
The same procedure would be used to set up Defaults for all of the fields for each Item Master Class and Type as shown. The information entered in each of the Default fields will be automatically entered in the corresponding field during data entry of a new Item after selecting the Class and Type.
Defaults should be setup to apply in most cases. If the default in a particular field is not appropriate for a new Item being entered, the User may make another choice on a one-time basis or if the default has changed. Use System Setup Inventory Part Class to change the default. If too many over-rides are necessary for a particular Type, it may be too general. Consider splitting it into two Types, each with its own set of Defaults. Changed defaults only affect future data entry, not items already entered. Each existing item must be reassigned to a new Type before the old Type can be deleted from setup.
|