1.1. Prerequisites |
User MUST have full rights to the "System Setup" in System Security . Users with “Supervisor Rights” will automatically have access.
|
1.2. Introduction | This section covers the system setups required to use Materials and Inventory related modules. These setups are fundamental to Inventory Control Management, Inventory Handling and Materials Requirements Planning. They affect everything from data entry and conversion of existing (legacy) part numbering systems to the layout of the Stockroom. It is absolutely essential to review all aspects of these Materials setups prior to beginning data entry, because once entered, many setup fields cannot be backed out without Manex's assistance.
Data Entry
MANEX System Setups and Defaults are designed to minimize the user’s keystrokes when entering actual data. Careful choice of a scheme for item master numbering of products and parts will allow MANEX to automatically create item master part numbers and enter default data when the user selects Class and Type and enters a Description.
Conversion of Legacy Product and Part Number System
The first decision to be made prior to System Setup is whether to try to use your existing product and part numbers in Manex. Because Manex item numbering is significantly different than most legacy numbering systems, this decision is best made after you understand Manex's numbering system structure, options and functionality.
· Manex uses Classes (similar to Commodity Codes) to "classify" all Items entered in the Item Master. Each Class is further broken down into Types. All screens and printouts of Items (Products and Parts) show the Class and Type for each Item; therefore it is not necessary to include Class and Type information in the Description field for an item.
· An "intelligent" prefix (3 digit numeric suggested) is usually assigned as an identifier of a particular Type of part under a particular Class which allows grouping of like items for:
1. Automatic entry of Default (common) information during data entry of items in the Item Master.
2. Prevention of double-assignment of part numbers to items already having numbers.
3. Rapid searches for existing part numbers in the database.
4. Organized viewing of items in screen displays and reports
5. Ease of assignment for planning, purchasing and inventory management.
6. Simplifying receiving, stocking, locating and kitting.
7. Maintenance of standard costing by commodity.
8. Assignment of Buyers by commodity.
· Using Autonumbering of the "root" or main part of a part or product number creates a unique identifier for each number which:
1. Is never reused, once it has been assigned to prevent two different items from having the same part number.
2. Becomes a unique identifier to provide an audit trail of any and all transactions and changes.
3. Has no significance other than unique identification to allow assignment without encoding.
4. Should be all-numeric for ease in finding, sorting and arranging items.
5. Should be at least 5 digits to allow for a minimum of 99,999 part numbers to be assigned.
· Manex suggests that you use your customers' product numbers as Manex product numbers in order to:
1. Allow transferring open Sales Orders and Work Orders into Manex with the least amount of confusion.
2. Retain established numbers for customer recognition on Sales Orders, Packing Lists and Invoices.
3. Minimize the need for reprinting of labels, travelers, serial plates and pcb artwork.
4. Provide a link between the old Bills of Material and the new ones.
· Legacy Part numbering systems that have been maintained manually usually cannot be imported directly into Manex because they:
1. Contain duplicate part number assignments, use the same part number root more than once and are not uniform in structure.
2. Use item descriptions with non-standard nomenclature, sequence, separators, abbreviations and data.
3. Have Manufacturer's data such as part number, name and/or specifications imbedded in the part number, prefix or description.
4. Use Customer part numbers instead of internally created numbers. These numbers can create confusion when created by one customer but used for another customer.
5. Were not under Engineering Change Control to insure correct assignment or change of Revision Level.
6. Have different versions or revisions all with the same part number. A new Manex part number should be assigned for each item that differs in form, fit or function.
Stockroom Layout
The simplest layout for a stockroom is in part number sequence. To make this work, Prefixes must be systematically assigned to each Item Class and Type. This type of layout:
· Eliminates the need for assignment, data entry and maintenance of aisle, row and shelf location codes for every item.
· Allows expansion for added items without re-entry of location codes. Expansion may be achieved by just shifting everything down, using empty or expansion spaces.
· Simplifies Cycle Counting and Physical Inventories by having only one location for each part number.
· Concentrates all of the same parts and all like items together for uniformity of storage of similar packaging.
The materials application module setup section allows you to prepare tables for specific material related modules your company has purchased. Once setup in the system, you will be able to use these tables and or perform certain functions automatically. Sample data is provided as a guideline in preparing the Pre-Installation Work Sheets. These Sample setups are not necessarily the only ways to setup Manex Materials, but they have been compiled as the result of many successful Manex installations and may save you many hours of "re-inventing the wheel". This section will first explain each of the Material Setup screens, then describe how to fill out the work sheets, and finally, how to enter the data into the MANEX system. |
1.3.1. Prerequisites for Part Source |
User MUST have full rights to the "System Setup" in System Security . Users with “Supervisor Rights” will automatically have access.
|
1.3.2. Introduction for Part Source |
A Part Source describes the source of the part in inventory.
|
1.3.3. Fields & Definitions for Part Source |
Part source table contains the following items:
BUY |
Purchased Parts |
CONSIGNED |
Parts that are provided and owned by a Customer |
MAKE |
An Assembly that is built in the Manufacturing Process |
PHANTOM |
A phantom assembly is a bill of materials assembled for the convenience of the user, and is not actually built or maintained in inventory. This may be useful when a certain sequence of parts is always used in many different assemblies, but the parts are actually assembled at the same time as the top assembly. Any components reporting to a phantom will be picked and assembled with the assembly to which the phantom reports.
|
|
1.3.4. How To ..... for Part Source |
1.3.4.1. Setup the Part Source |
Enter the SQLSYSSETTING.EXE (within the ManEx root directory)
This action will then prompt the user for a password
|
 |
The following screen will be displayed, enter the Material/Part Source Module |
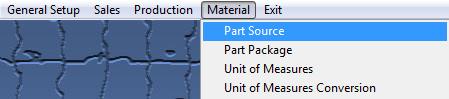 |
The following screen will be displayed:
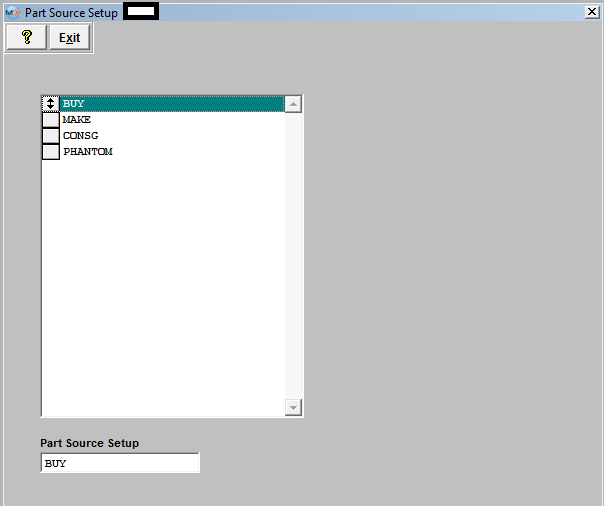
The Part Source screen is presented so that the user may rearrange the order of the presentation of the sources. If the user most frequently uses consigned parts, then the CONSG tab should be at the top of the list, probably followed by MAKE parts, etc.
This table is hard coded in the system. Therefore it is not necessary for the user to enter any information here. This is a requirement to setup the item master in the Inventory Control Management module.
These items may be sorted in any order by clicking on and dragging the box on the left side, to the (vertical) position desired. This order will be the order displayed in the pull downs when using this list in other modules within the system. Suggestion: Have the one most used at the top of the list.
«Mark as Completed in RoadMap Section B Item 4-a»
|
1.4.1. Prerequisites for Part Package |
Complete the attached worksheet and " Mark as Completed RoadMap Section B Item 4-b" before continuing the setup.
User MUST have full rights to the "System Setup" in System Security . Users with “Supervisor Rights” will automatically have access.
|
1.4.2. Introduction for Part Package | When parts are purchased, they may have several different kinds of packaging. Some examples of the way parts may come are:
in boxes at the convenience of the vendor in reels for automatic machine operations
in tubes for automatic and semi-automatic operations
in crates for protection and handling
on pallets for handling
in barrels for storage
in six-packs for convenience
in bulk
The user may identify these packaging properties in the item master descriptions for parts so that the rest of the company will know what to expect in the way of storage and handling when the parts arrive and must be stored or issued to production. The package descriptions entered may be up to 15 characters long.
|
1.4.3. Fields & Definitions for Part Package Setup |
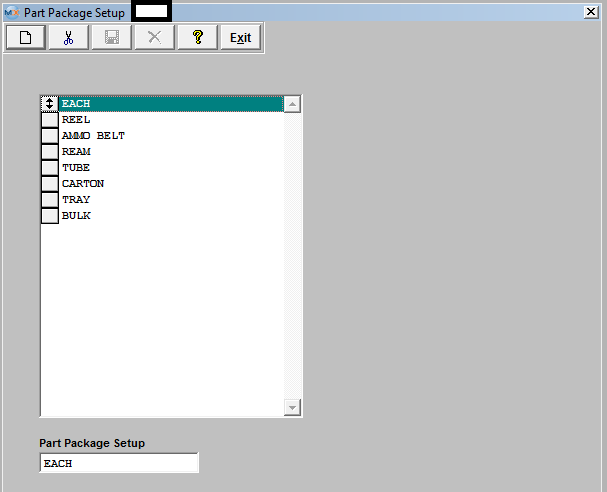
When parts are purchased, they may have several different kinds of packaging. Some examples of the way parts may come are:
in boxes at the convenience of the vendor
in reels for automatic machine operations
in tubes for automatic and semi-automatic operations
in crates for protection and handling
on pallets for handling
in barrels for storage
in six-packs for convenience
in bulk
The user may identify these packaging properties in the item master descriptions for parts so that the rest of the company will know what to expect in the way of storage and handling when the parts arrive and must be stored or issued to production. The package descriptions entered may be up to 15 characters long.
|
1.4.4. How To ..... for Part Package |
1.4.4.1. Setup the Part Package Module |
Enter the SQLSYSSETTING.EXE (within the ManEx root directory)
This action will then prompt the user for a password
|
 |
The following screen will be displayed, enter the Material/Part Package Module
|
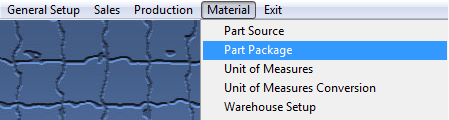 |
The following screen will be displayed:
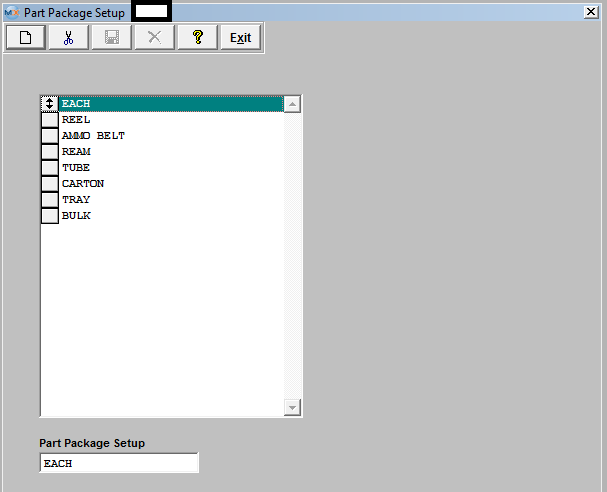
This field is to specify the kind of package the part must be in so the parts can be used in certain specific kind of machine, processing, handling, etc. This is particularly helpful if a part can be packaged so the automatic machine can accept them directly. This information is used in all materials modules including Material Requirements Planning and Purchasing. Part package examples are: Reel, Tube, Tray, Bulk, etc.
The user begins entry of a new package by selecting the Add button from the main tool bar, then enters the data in the window at the bottom of the page. When satisfied that the data was entered correctly, select the Save button from the main tool bar, and the item will be added to the list. Items may be deleted by highlighting the item and selecting the Delete button from the main tool bar.
These items may be sorted in any order by dragging the box on the left side, to the (vertical) position desired. This order will be the order displayed in the pull downs when using this list in other modules within the system. Suggestion: Have the one most used at the top of the list.
Where Used: Inventory Item Master.
«Mark as Completed in RoadMap Section B Item 4-b»
|
1.5.1. Prerequisites for Unit of Measures |
Complete the attached worksheet and " Mark as Completed RoadMap Section B Item 4-c before continuing the setup.
User MUST have full rights to the "System Setup" in System Security . Users with “Supervisor Rights” will automatically have access.
Note: Purchasing units of measure, if different than the stocking units of measure, must have a conversion factor entered in order for ManEx Material Requirements Planning and Purchasing modules to correctly interpret the amount of material required. Identifying the purchasing unit and the stocking unit and a factor between the two does this. For example, 1 foot = 12 inches, and 12 is the conversion factor.
|
1.5.2. Introduction for Unit of Measures | When parts or assemblies are stored in the storeroom, or used in Bills of Materials, the unit of measure must be defined. It is important to know if a particular wire is stored in inventory, if it is 100 inches, 100 feet, 100 yards, etc. This definition is required so that when items are counted and removed from stock inventory, it is clear what the quantity numbers represent. Other examples might be ounces, pounds, quarts, gallons, pints, milliliters, liters, etc.
It is also possible to purchase material in different units of measure than the material is accounted for in stock inventory and bills of materials. For example, wire might be purchased in feet, yards or miles, but because of the way that it is used in manufacturing, is probably stored and issued in inches. All units of measure, for both stock inventory and purchasing, are to be entered in this screen, if not already available. Once a unit of measure is entered in this screen, it can never be removed as the value of any purchases and inventory depends on having a unit of measure associated with it.
Manex is provided with a number of units of measures. The length of the unit of measure field is 4 characters.
« Purchasing units of measure, if different than the stocking units of measure, must have a conversion factor entered in order for MANEX Material Requirements Planning and Purchasing modules to correctly interpret the amount of material required. Identifying the purchasing unit and the stocking unit and a factor between the two does this. For example, 1 foot = 12 inches, and 12 is the conversion factor. |
1.5.3. Fields & Definitions for Unit of Measures |
1.5.3.1. Unit of Measures Setup |
Manex is provided with a number of units of measures. The length of the unit of measure field is 4 characters.
When parts or assemblies are stored in the storeroom, or used in Bills of Materials, the unit of measure must be defined. It is important to know if a particular wire is stored in inventory, if it is 100 inches, 100 feet, 100 yards, etc. This definition is required so that when items are counted and removed from stock inventory, it is clear what the quantity numbers represent. Other examples might be ounces, pounds, quarts, gallons, pints, milliliters, liters, etc.
It is also possible to purchase material in different units of measure than the material is accounted for in stock inventory and bills of materials. For example, wire might be purchased in feet, yards or miles, but because of the way that it is used in manufacturing, is probably stored and issued in inches. All units of measure, for both stock inventory and purchasing, are to be entered in this screen, if not already available. Once a unit of measure is entered in this screen, it can never be removed as the value of any purchases and inventory depends on having a unit of measure associated with it.
|
1.5.4. How To ..... for Unit of Measures |
1.5.4.1. Setup the Unit of Measures |
Enter the SQLSYSSETTING.EXE (within the ManEx root directory)
This action will then prompt the user for a password
|
 |
The following screen will be displayed, enter the Material/Unit of Measures
|
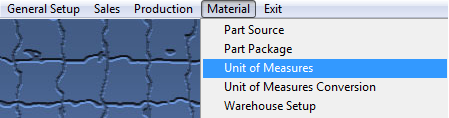 |
The followng screen will be displayed:
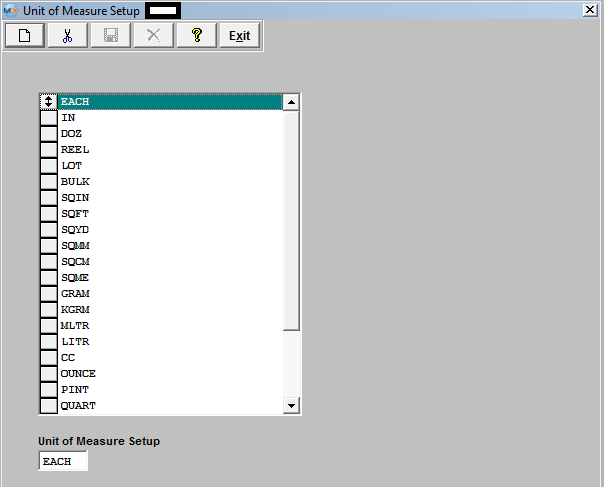
Data in this table is already entered in the basic system. Therefore, it is not necessary for the user to enter any information here, but the user may have some specific requirements that they may wnat to add to the table. Unit Of Measure table is used in all materials related modules.
To add, select the Add button from the main tool bar. Enter a new Unit of Measure. Select the Save button from the main tool bar.
These items may be sorted in any order by clicking on and dragging the box on the left side, to the (vertical) position desired. This order will be the order displayed in the pull downs when using this list in other modules within the system. Suggestion: Have the one most used at the top of the list.
Where Used: In all Purchasing and Receiving Modules
«Mark as Completed in RoadMap Section B Item 4-c»
|
1.6. Unit of Measures Conversion | |
1.6.1. Prerequisites for Unit of Measures Conversion |
Complete the attached worksheet and " Mark as Completed RoadMap Section B Item 4-c before continuing the setup.
User MUST have full rights to the "System Setup" in System Security . Users with “Supervisor Rights” will automatically have access.
Note: Purchasing units of measure, if different than the stocking units of measure, must have a conversion factor entered in order for ManEx Material Requirements Planning and Purchasing modules to correctly interpret the amount of material required. Identifying the purchasing unit and the stocking unit and a factor between the two does this. For example, 1 foot = 12 inches, and 12 is the conversion factor.
|
1.6.2. Introduction for Unit of Measure Conversion | When parts or assemblies are stored in the storeroom, or used in Bills of Materials, the unit of measure must be defined. It is important to know if a particular wire is stored in inventory, if it is 100 inches, 100 feet, 100 yards, etc. This definition is required so that when items are counted and removed from stock inventory, it is clear what the quantity numbers represent. Other examples might be ounces, pounds, quarts, gallons, pints, milliliters, liters, etc.
It is also possible to purchase material in different units of measure than the material is accounted for in stock inventory and bills of materials. For example, wire might be purchased in feet, yards or miles, but because of the way that it is used in manufacturing, is probably stored and issued in inches. All units of measure, for both stock inventory and purchasing, are to be entered in this screen, if not already available. Once a unit of measure is entered in this screen, it can never be removed as the value of any purchases and inventory depends on having a unit of measure associated with it.
Manex is provided with a number of units of measures. The length of the unit of measure field is 4 characters.
« Purchasing units of measure, if different than the stocking units of measure, must have a conversion factor entered in order for MANEX Material Requirements Planning and Purchasing modules to correctly interpret the amount of material required. Identifying the purchasing unit and the stocking unit and a factor between the two does this. For example, 1 foot = 12 inches, and 12 is the conversion factor. |
1.6.3. Fields & Definitions for Unit of Measures Conversion |
1.6.3.1. Unit of Measure Conversion |
If Purchasing units of measure, is different than the stocking units of measure, there must be a conversion factor entered in order for ManEx Material Requirements Planning and Purchasing modules to correctly interpret the amount of material required. Identifying the purchasing unit and the stocking unit and a factor between the two does this. For example, 1 foot = 12 inches, and 12 is the conversion factor.
|
1.6.4. How To ..... for Unit of Measure Conversion |
1.6.4.1. Setup the Unit of Measures Conversion |
Enter the SQLSYSSETTING.EXE (within the ManEx root directory)
This action will then prompt the user for a password
|
 |
The following screen will be displayed, enter the Material/Unit of Measures Conversion
|
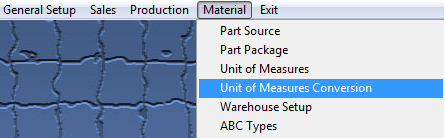 |
The followng screen will be displayed:
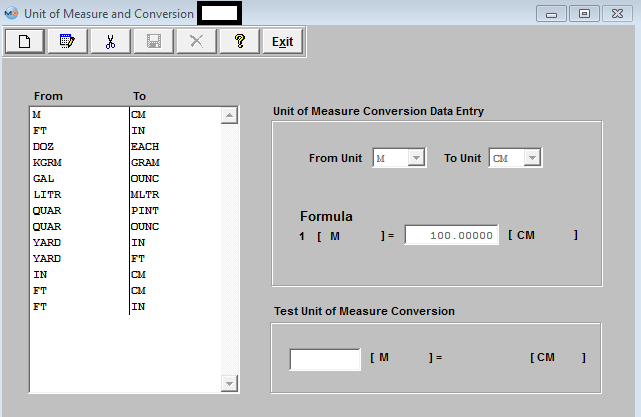
Data in this table is already entered in the basic system. Therefore, it is not necessary for the user to enter any information here, but the user may have some specific requirements that they may want to add to the table. Unit Of Measure table is used in all materials related modules.
Prerequisites
Each Unit of Measure must be in the Unit of Measures table before establishing a conversion factor.
When the user expects to purchase material in different units than which it is stored and used in BOMs, the conversion factors are required.
To ADD a new conversion, select the Add button from the main tool bar, select the "From Unit" (for purchasing) from the pull down, then select the "To Unit" (for stocking) from the pull down, then enter the conversion formula. The user may test the equation by entering in the same number in the "Test Unit of Measure Conversion" field you entered above into the formula field, depress enter and the exact same formula should appear in the test section. When the user is satisfied with the equation, select the Save button from the main tool bar. Conversion factors already entered may be Edited or Deleted but the user must be aware of any currently open orders using the factor.
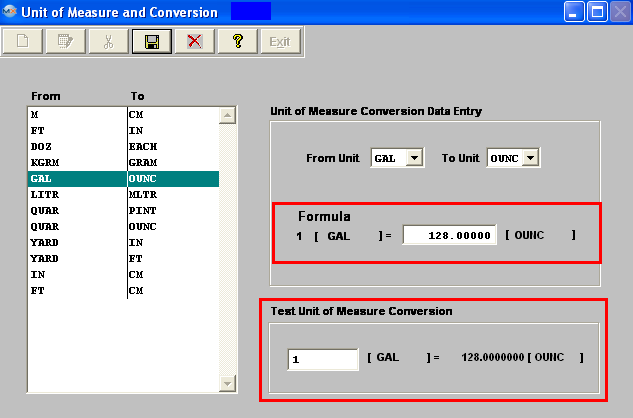
Where Used: In all Purchasing and Receiving Modules
«Mark as Completed in RoadMap Section B Item 4-c»
|
1.7.1. Prerequisites for Warehouse Setup |
Complete the attached worksheet and " Mark as Completed RoadMap Section B Item 4-d before continuing the setup.
To Add, Edit, or Save a Warehouse the user MUST have "System Setup" rights within the System Security module and also MUST have "Warehouse Setup" rights within the Accounting Security module.
Note: If you have "Supervisor Rights" in the System Security module the Warehouse Setup module will still require you to have "Warehouse Setup" rights in the Accounting Security and vis-versa if you are an Accounting Supervisor you will still be required to have "System Setup" rights in the System Security module to Add, Edit, or Save a Warehouse in Warehouse Setup.
Note: The GL numbers are required if the ACCOUNTING Module is active. ManEx recommends choosing the accounting GL numbers with care because we do NOT recommend changing them once the selection is saved. WIP and MRB GL numbers must be unique.
|
1.7.2. Introduction for Warehouse Setup | ManEx users may identify an unlimited number of warehouses in which to store materials. If the user wishes, it is possible to establish a wide variety of warehouses for special needs. If the user is involved with much consigned activity, it is possible to set up a warehouse for each customer and their material. A warehouse might be set up as a secure location for very high value material, with additional physical security precautions to access this area.
|
1.7.3. Fields and Definitions for Warehouse Setup |
ManEx users may identify an unlimited number of warehouses in which to store materials. If the user wishes, it is possible to establish a wide variety of warehouses for special needs. If the user is involved with much consigned activity, it is possible to set up a warehouse for each customer and their material. A warehouse might be set up as a secure location for very high value material, with additional physical security precautions to access this area.
For those users who want to separate the Finished Goods from the Raw Materials Inventory, be sure to include a Finished Goods Warehouse.
The MRB (Materials Review Board) Warehouse is required for the DMR (Discrepant Material Return) module.
There are at least two warehouses that cannot be removed from the system: WIP and WO-WIP. These warehouse locations are used by ManEx to track materials within the manufacturing process. For more detail on WO-WIP see Article #3061. Also, any warehouse that has material purchased to be placed in it, or has inventory in it, may NOT be deleted. All other warehouses may be deleted.
 |
Deletion of a WHSE is only flagged as deleted but is still retained within the tables for history preservation and may be restored by depressing this button. . |
One warehouse must be selected as the default warehouse. This is normally Main1 Warehouse.
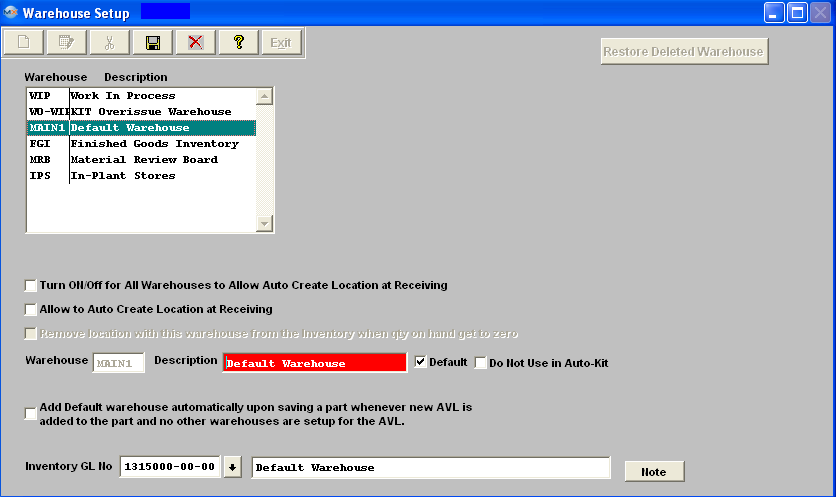
Each warehouse has associated with it a warehouse code (6 characters), a warehouse description (25 characters), Division designation, if applicable, and Inventory General Ledger Account number (setup in the GL Account Setup).
Note: The GL numbers are required if the ACCOUNTING Module is active. ManEx recommends choosing the accounting GL numbers with care because we do NOT recommend changing them once the selection is saved. WIP and MRB GL numbers must be unique. It is VERY important that the Account Number for WO-WIP is NOT the same as the WIP account number. WIP and MRB GL numbers MUST be unique. The system will not allow GL numbers that have been used by other warehouses to be entered for WIP and/or MRB warehouses and other warehouse can not use the same GL numbers that are used by WIP and/or MRB warehouses.
Turn ON/Off for All Warehouses to Allow Auto Create Location at Receiving Box - If this box is UNCHECKED it will not “Allow Auto Create Location at Receiving” for all Warehouses listed in Warehouse setup. If this box is CHECKED it will “Allow Auto Create Location at Receiving” for all Warehouses listed in Warehouse setup. This is not only controlled at the System Setup level. You will also need to check the "Allow to Auto Create Location at Receiving" box located in the Inventory Control, AVL level for this option to work properly.
Allow to Auto Create Location at Receiving Box - checking this box (along with checking the box in Inventory Control AVL level) will allow user to create a location at the PO level, PO receiving level, and/or Inventory Handling Receiving level for this warehouse. Unchecking the Auto Create disables that warehouse from being used on the fly.
Remove location with this warehouse from the Inventory when qty on hand gets to zero Box -This will only be available if user checks the “Allow to Auto Create Location at Receiving” box.You would check this box if you want the Warehouse and location created at the Inventory level, PO level or PO Receiving level to be rendered inactive (made invisible in most screens) from that Inventory part once the inventory reaches “0”. If the user de-kitted the work order, that same warehouse would be reactivated and product inserted.
Default Box – If none of the WHSE or Inventory AVL's are marked for Auto-location creation then the system will automatically assign the default whse upon creation of a brand new part number/avl. If you have the auto-location creation option enabled for the WHSE and AVL then the system will leave the WHSE section blank for new parts, and allow users to create new locations from PO Receiving.
Do Not Use in Auto-Kit – If this box is checked this warehouse will not be used in Auto-Kitting.
Add Default warehouse automatically upon saving a part whenever a new AVL is added to the part and no other warehouses are setup for the AVL -The default warehouse is added automatically upon saving a part whenever a new AVL is added to a part except; If the "Allow to Auto Create Location at Receiving" button is checked and the "Add Default warehouse automatically ....." box is unchecked the system will not add a warehouse within the Inventory module upon saving the record. This works in conjuctions with the “Allow to Auto Create Location at Receiving” button.
Note: The GL numbers are required if the ACCOUNTING Module is active. ManEx recommends choosing the accounting GL numbers with care because we do NOT recommend changing them once the selection is saved. WIP and MRB GL numbers must be unique. The system will not allow GL numbers that have been used by other warehouses to be entered for WIP and/or MRB warehouses and other warehouse can not use the same GL numbers that are used by WIP and/or MRB warehouses.
|
|
1.7.4. How To ..... for Warehouse Setup |
1.7.4.1. Setup the Warehouse Setup Module |
Enter the SQLSYSSETTING.EXE (within the ManEx root directory)
This action will then prompt the user for a password
|
 |
The following screen will be displayed, enter the Material/Warehouse Setup
This setup screen is used to enter all the warehouses used in your company. This information is used when adding and editing the item master. When an item master record is created, the system will add by default the designated default warehouse. The default warehouse assignment is accomplished by checking the default box for the selected default warehouse. Note: ManEx does NOT recommend to change the default warehouse once you’ve assigned inventory parts to that default.
|
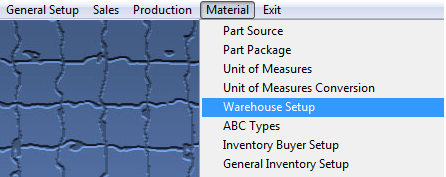 |
The following screen will appear:
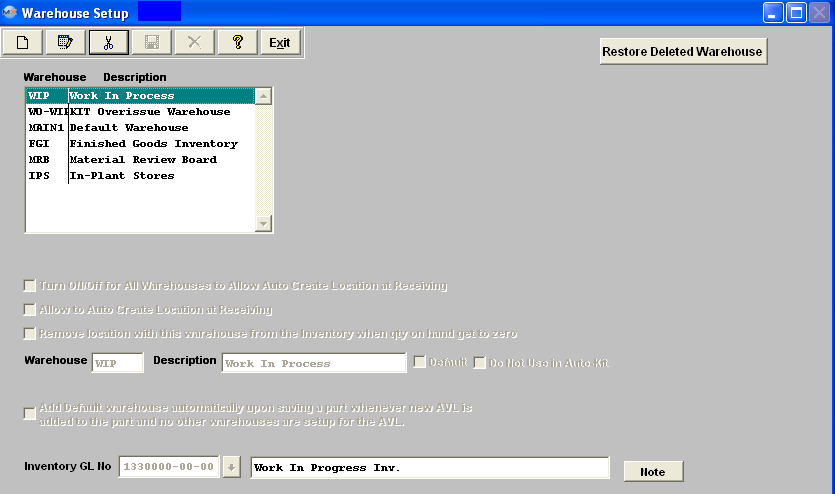
To add a new warehouse, depress the Add button. Enter your password. Type the Warehouse abbreviation into the Warehouse window. Type the Description pertaining to the warehouse into the Description window. If this is the default warehouse, check the Default box. (You may have only one default Warehouse, but MUST have at least one.) If there is not default warehouse setup using will receive the following warning upon save:
Turn ON/Off for All Warehouses to Allow Auto Create Location at Receiving Box -If this box is UNCHECKED it will not “Allow Auto Create Location at Receiving” for all Warehouses listed in Warehouse setup.If this box is CHECKED it will “Allow Auto Create Location at Receiving” for all Warehouses listed in Warehouse setup.
Allow to Auto Create Location at Receiving Box - checking this box will allow user to create a location a the PO level or PO receiving level for this warehouse. Unchecking the Auto Create disables that warehouse from being used on the fly.
Remove location with this warehouse from the Inventory when qty on hand gets to zero Box -This will only be available if user checks the “Allow to Auto Create Location at Receiving” box.You would check this box if you want the Warehouse and location created at the Inventory level, PO level or PO Receiving level to be rendered inactive (made invisible in most screens) from that Inventory part once the inventory reaches “0”. If the user de-kitted the work order, that same warehouse would be reactivated and product inserted.
Default Box – If none of the WHSE or Inventory AVL's are marked for Auto-location creation then the system will automatically assign the default whse upon creation of a brand new part number/avl. If you have the auto-location creation option enabled for the WHSE and AVL then the system will leave the WHSE section blank for new parts, and allow users to create new locations from PO Receiving.
Do Not Use in Auto-Kit – If this box is checked this warehouse will not be used in Auto-Kitting.
Add Default warehouse automatically upon saving a part whenever a new AVL is added to the part and no other warehouses are setup for the AVL -If this box is checked the system will add a warehouse within the Inventory module upon saving the record even if the Allow to Auto Create Location at Receiving box is checked.
If accounting is installed, depress the Inventory GL No field down arrow. The following GL Number account selection will appear:
Depress the down arrow next to the Find By field. Choose between Account Type or Account Numbers. Depending upon your selection, either GL Types or Account Numbers will appear.
Highlight the number of choice. Depress the Ok button. he account number will appear in the Inventory GL Number field.
|
|
Repeat this process for the selection of the Shrinkage GL number. (Note: The GL numbers are required if the ACCOUNTING Module is active. ManEx recommends choosing the accounting GL numbers with care because we do NOT recommend changing them once the selection is saved. WIP and MRB GL numbers must be unique.
WIP and MRB GL numbers MUST be unique. The system will not allow GL numbers that have been used by other warehouses to be entered for WIP and/or MRB warehouses and other warehouse can not use the same GL numbers that are used by WIP and/or MRB warehouses. If users trys to enter a GL number for a warehouse that is used for WIP or MRB or vis- versa the following message or a similar message will appear: |
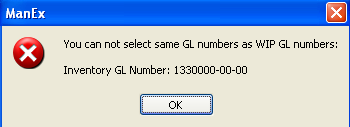 |
Depress the Save button. The following message will appear:
If you are totally satisfied with your selection, depress the OK button.
If there has been no activity in the Warehouse, the user may delete it. Highlight the warehouse. Depress the Delete button. (Note: You cannot delete a default warehouse. So, if you want to delete a default warehouse, you must create or assign the default status to another warehouse first.) You will receive a message to confirm the deletion. Depress the Yes button to confirm the deletion.
Where Used: In all Materials, Production and WIP functions
«Mark as Completed in RoadMap in Sect. B Item 4-d»
|
1.7.4.2. Edit an Existing Warehouse |
Enter the SQLSYSSETTING.EXE (within the ManEx root directory)
This action will then prompt the user for a password
|
 |
The following screen will be displayed, enter the Material/Warehouse Setup
|
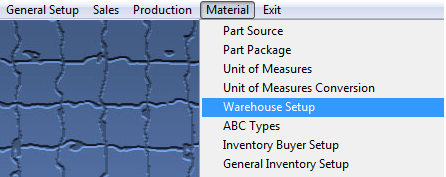 |
The following screen will be displayed:
Highlight the warehouse you would like to edit and depress the Edit button, all fields are editable with the exception of the Warehouse field.
If user decides to change the GL number the following reminder message will be displayed: Note: ManEx does NOT recommend changing the GL numbers once they have been setup.
|
1.7.4.3. Restore Deleted Warehouse |
Enter the SQLSYSSETTING.EXE (within the ManEx root directory)
This action will then prompt the user for a password
|
 |
The following screen will be displayed, enter the Material/Warehouse Setup
|
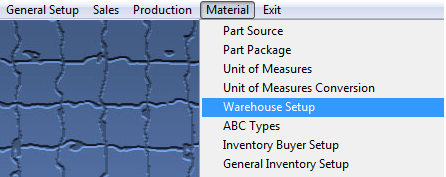 |
The following screen will be displayed:
Depress the "Restore Deleted Warehouse" Button and a selection screen will appear:
Highlight the selection and depress the (<) arrow to move your selection to the right screen.
Once selection has be made depress the "Done" button and the warehouse(s) selected will be restored.
|
1.8.1. Prerequisites for ABC Types |
Complete the attached worksheet and " Mark as Completed RoadMap Section B Item 4-e before continuing the setup.
User MUST have full rights to the "System Setup" in System Security . Users with “Supervisor Rights” will automatically have access.
|
1.8.2. Introduction for ABC Types | This section is provided to setup ABC Code template table. This information is used in the item master during add or edit mode. ABC types are used when setting up part class and types, which in turn are used when adding an inventory part to the item master. ABC codes are used as an aid to manage inventory tracking. Traditionally, ABC codes are established to divide the inventory by value, and to guide in the cycle counting of inventory. First the value of all inventory in stock is added up and listed by part in order of the highest extended value first. Then, the top 80 % of the parts value would be classified as “A” items, and will probably consist of about 10-15% of the inventory part numbers. The next 15% of the value items would be classified as “B” items, and will be in the neighborhood of 20-40% of the part numbers. The last 5% of the value will be classified as “C” items, and represent at least 50% of the part numbers.
ManEx allows the user to differentiate between assemblies and components. Users may create a setup of ABC (and DEFG...if they choose) for components (buy/consigned parts) and a different set (e.g. MNO) for assemblies. The reason for this is that it is likely that the assemblies may need tighter control than the ranges available for the whole inventory, and the user has the option of differentiating between components, and assemblies. If a user is carrying components in finished goods inventory to ship to a customer, they will still be counted as components in the ABC group. The type of warehouse is not considered when calculating cycle counts (except for in-house items, regardless of where they are stored).
|
1.8.3. Fields and Definitions for the ABC Types | 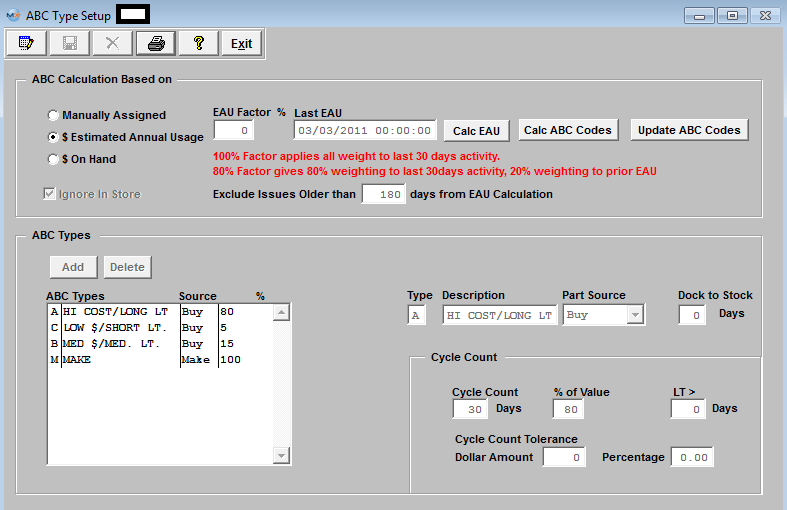
ABC Calculation Based on:
Manually Assigned |
If this radio is selected, the ABC codes are assigned when parts are created based on their class and type and must be updated manually as needed. But MUST be setup in the Inventory Part Type Setup
|
$ Estimated Annual Usage |
If this radio is selected, the ABC codes are assigned based on the value of the estimated annual usage and/or component lead time. Users must run the "Calc EAU" and Calc ABC Codes" programs to refresh EAU and ABC codes.
EAU Calculation: inventory part EAU*(1-EAU%)+total issued qty*12*EAU%. Please note the "total issued qty" get from past one month
After inventory EAU values are update
Get each BUY part number standard cost multiply EAU and divided by the total standard cost multiply EAU of all BUY parts
(qty_oh*EAU) of one BUY part/qty_oh*EAU for all BUY parts
Get each MAKE part number standard cost multiply EAU and divided by the total standard cost multiply EAU of all MAKE parts
(qty_oh*EAU) of one MAKE part/qty_oh*EAU for all MAKE parts
Sort the records by the values from highest to lowest. And then use the rank based on % of values set up for each ABC type, to assign the part to each type. For example, type ‘A’ has 85%, ‘B’ has 10% and ‘C’ has 5%. The program will get the 85% of parts rank from highest to lowest and assign those part number ABC code “A”, etc.
|
$ On Hand |
If this radio is selected, then ABC codes are assigned based on the value of inventory on hand and/or the component lead time. Users must run the "Calc ABC Codes" program to update and refresh the component ABC codes.
Get each BUY part number standard cost multiply qty OH and divided by the total cost of all BUY parts
(qty_oh*stdcost) of one BUY part/qty_oh*stdcost for all BUY parts
Get each MAKE part number cost multiply qty OH and divided by the total cost of all MAKE parts
(qty_oh*stdcost) of one MAKE part/qty_oh*stdcost for all MAKE parts
Sort the records by the values from highest to lowest. And then use the rank based on % of values set up for each ABC type, to assign the part to each type. For example, type ‘A’ has 85%, ‘B’ has 10% and ‘C’ has 5%. The program will get the 85% of parts rank from highest to lowest and assign those part number ABC code “A”, etc.
If lead time is set up in ABC type, and the part has lead time bigger than the set up lead time, the ABC type will be updated to upper level. For example, a part is type ‘C’, but it’s lead time is bigger than the lead time set up for type ‘A”, the part will be updated to type ‘A’
|
EAU Factor % |
If the user selects $ Estimated Annual Usage, Enter in the EAU factor.
|
Last EAU |
The date that the Last EAU was calculated. |
Ignore In Store |
Check this box only if you do NOT want the In-Store warehouses to be included in the Cycle Counts, regardless of which Calculation Based on is selected.
|
Exclude Issues Older than __ Days from EAU Calculation |
Enter the number of days you want to exclude older issues from the EAU Calculations. The number of days entered in this field will override the standard 30 days. The default is set to 180 days, but can be changed. |
ABC Types:
ABC Type |
The ABC code identifies a part source for inventory parts. A = Highest value, B = Medium value and C = Lowest value (Manex allows up to 36 (0-9 and A-Z) alphanumeric ABC designations). ABC codes are applied to Buy and Make part separately.
NOTE: An ABC code needs to be specifically setup for Make parts, if Make parts are to be included in the cycle count. If an ABC code is setup for a buy part and that ABC code is assigned to a Make part the make part will not be included in the cycle count and vice versa.
|
Description |
Definition of ABC parameters |
Part Source |
This identifies if a part is a Make or Buy part. Select the desired part Source radio. |
Dock to Stock |
A Dock to Stock period may be included in each ABC code. Dock to Stock is the number of days a part is expected to take to be delivered to the stock room after the part is received on the user’s dock. This duration may include the amount of time it takes to organize the shipment, count the parts, log the receipt into the inventory system, perform incoming inspection, and physically move the parts to stores. Intuitively, the higher dollar parts may have longer dock to stock times because of increased inspection. And the lesser valued parts may not require inspection. NOTE: ManEx provides for PO Receiving Inspection and for Discrepant Material Returns (Return to Vendor).
The Dock to Stock value is taken into consideration for MRP leadtime calculations in the projected requirement of the receipt of purchased parts. For Example: if the Dock to Stock time is 3 days, and the kit start date is 8/22/08, then the due date for the buy components would be 8/19/08, and the order date would be based on the purchasing leadtime to receive the parts by 8/19/08. So the Dock to Stock time is used to move back the due dates of items purchased in time for kitting
|
Cycle Count Days |
Users enter the Cycle Count Days of each ABC code. This is used to determine the number of parts to count each day. This is based on calendar days and may need to be adjusted for work days if you will not be cycle counting seven days a week. This field assists in counting all inventory over a period of time. The “A” items might be counted completely within each month. Therefore, a list of all of the “A” items (the highest dollar value) is generated, and randomly divided into 20 days, and each day 1/20th of the list counted and checked. The “B” items might be checked every quarter, and the “C” items checked once a year. This is a way to verify the accuracy of stockroom transactions, and to take measures necessary to keep the counts accurate. Type the ABC Types into the appropriate boxes. NOTE: This field MUST be populated with a number other than "0". If "0" is entered these parts will NOT be included in the Cycle Count.
Example: This is the number of days that you will re-count part numbers for the one of the ABC type, and this is calendar day. Let's say, you have entered 30 days for type "A" part. In inventory you have total of 1,000 type "A" parts. When you run cycle count, it will find how many working days from current day to current day +30, it finds you only have 20 working days, so the program will get 1,000/20 = 50 that the users need to count 50 "A" parts each day. The cycle count will randomly get 50 "A" parts that have not been counted yet. |
% of Value |
The "% of Value" determines which components will be included in the ABC code based on where their value falls within the total value Pareto (i.e. if A parts have a value of 80%, then all components comprising the top 80% of value will be included, if B parts have a "% of Value" of 15, then all components comprising the next 15% of value will be included, etc). A full 100% must be assigned to both Buy and Make parts. The "ABC calculation based on:" affect the meaning of this field. If Manual has been selected then it does not apply. If $ Estimated Annual Usage (EAU) has been selected, then it is EAU x STD cost and % of that value (top 80%, 15-80%, etc) If $ On-Hand has been selected, then it is On-Hand x STD cost and % of that value (top 80%, 15-80%, etc). Entering data in this field will NOT affect the cycle counting or include any of the parts in the cycle count until the "Calc ABC Codes" button is depressed.
|
Lead Time > |
The "LT>" determines which components will be included in the ABC code based on their purchasing lead time. This will include all components with an applicable lead time regardless of the on-hand or EAU value. |
Dollar Amount |
The dollar amount tolerance used in Cycle Count. For each ABC code, ManEx provides a cycle count tolerance, which, if exceeded, will result in reporting unfavorable results during cycle counting. These tolerances may be an absolute dollar value, or a percentage of the inventory being counted. For further information on the cycle count tolerances and what the purpose of setting them up in ManEx is see the attachment <<Cycle Count Tolerance.docx>> |
Percentage |
The Cycle Count Tolerance Percentage. For each ABC code, ManEx provides a cycle count tolerance, which, if exceeded, will result in reporting unfavorable results during cycle counting. These tolerances may be an absolute dollar value, or a percentage of the inventory being counted. For further information on the cycle count tolerances and what the purpose of setting them up in ManEx is see the attachment <<Cycle Count Tolerance.docx>> |
 |
This button will only be available if the screen is in "EDIT" . Depressing this button will update the EAU field within the ICM screen. The term EAU, (ESTIMATED Annual USAGE) may be considered as consumption, depletion, loss, used up, etc. So the EAU calculations MUST include the In-store issues to be accurate. If a user is issuing a part out of in-store to a Sales Order to be shipped the parts still count as an issue, or usage and was consumed, so it is necessary to include them when considering plans for future usage. If a user were to deliver ALL material directly to work orders from in-house, and these transactions were not included, there would be no calculated EAU. This is why we do NOT allow in-store issues to be ignored. The only time in-store issues will NOT be calculated in the EAU is if they are being returned to the vendor through Inventory Handling.
|
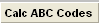 |
This button will only be available if the screen is in "EDIT" mode. Depressing this button will use the information in the % value and LT> fields are used to determine which parts should have their ABC codes automatically adjusted. After the ABC codes are updated, those parts will be included with the appropriate group for cycle counting. |
 |
This button will only be available if the screen is in "EDIT" mode. Depressing this button will use the information in the % value and LT> fields are used to determine which parts should have their ABC codes automatically adjusted. After the ABC codes are updated, those parts will be included with the appropriate group for cycle counting. |
|
1.8.4. How To ..... for ABC Types |
1.8.4.1. Setup the ABC Types |
Enter the SQLSYSSETTING.EXE (within the ManEx root directory)
This action will then prompt the user for a password
|
 |
The following screen will be displayed, enter the Material/ABC Types Module
This section is provided to setup ABC Code template table. This information is used in the item master during add or edit mode. ABC types are used when setting up part class and types, which in turn are used when adding an inventory part to the item master. ABC codes are used as an aid to manage inventory tracking. Traditionally, ABC codes are established to divide the inventory by value, and to guide in the cycle counting of inventory. First the value of all inventory in stock is added up and listed by part in order of the highest extended value first. Then, the top 80 % of the parts value would be classified as “A” items, and will probably consist of about 10-15% of the inventory part numbers. The next 15% of the value items would be classified as “B” items, and will be in the neighborhood of 20-40% of the part numbers. The last 5% of the value will be classified as “C” items, and represent at least 50% of the part numbers.
NOTE: An ABC code needs to be specifically setup for Make parts, if Make parts are to be included in the cycle count. If an ABC code is setup for a buy part and that ABC code is assigned to a Make part the make part will not be included in the cycle count and vice versa.
|
|
The following screen will be displayed:
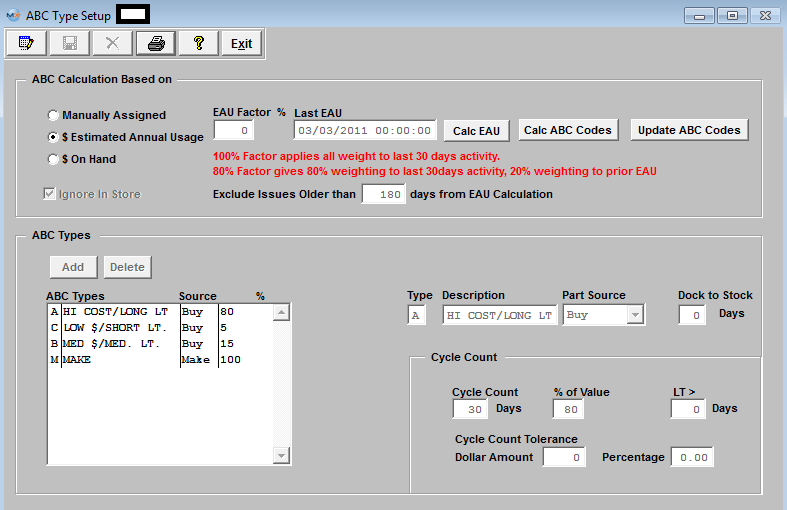
The "ABC calculation based on:" affects the meaning of the % of Value field. If Manual has been selected then it does not apply. If $ Estimated Annual Usage (EAU) has been selected, then it is EAU x STD cost and % of that value (top 80%, 15-80%, etc) If $ On-Hand has been selected, then it is On-Hand x STD cost and % of that value (top 80%, 15-80%, etc).
ABC Codes will be calculated using the information in the % value and LT> fields. These fields are used to determine which parts should have their ABC codes automatically adjusted. After the ABC codes are updated, those parts will be included with the appropriate group for cycle counting.
Check the "Ignore In-Store" box only if you do NOT want the In-Store warehouses to be included in the Cycle Counts, regardless of which Calculation Based on is selected.
Depress the Edit button. Select the "ABC Calculation based on" by clicking on the appropriate radio.
If the user selects $ Estimated Annual Usage, the following screen will appear. Type in the EAU factor. then depress the "Calc EAU" button will update the EAU field within the ICM screen.
This button will only be available if the screen is in "EDIT" . Depressing this button will update the EAU field within the ICM screen. The term EAU, (ESTIMATED Annual USAGE) may be considered as consumption, depletion, loss, used up, etc. So the EAU calculations MUST include the In-store issues to be accurate. If a user is issuing a part out of in-store to a Sales Order to be shipped the parts still count as an issue, or usage and was consumed, so it is necessary to include them when considering plans for future usage. If a user were to deliver ALL material directly to work orders from in-house, and these transactions were not included, there would be no calculated EAU. This is why we do NOT allow in-store issues to be ignored. The only time in-store issues will NOT be calculated in the EAU is if they are being returned to the vendor through Inventory Handling.
Depress the Save button.
User can then depress any of the Calculation buttons.
If the "Calc EAU" button will update the EAU field within the ICM screen. The Last EAU date will fill in.
If the "Calc ABC Codes" button is depressed, this button will use the information in the % value and LT> fields to determine which parts should have their ABC codes automatically adjusted. After the ABC codes are updated, those parts will be included with the appropriate group for cycle counting.
If the "Update ABC Codes" button is depressed this button will use the information in the % value and LT> fields to determine which parts should have their ABC codes automatically adjusted. After the ABC codes are updated, those parts will be included with the appropriate group for cycle counting.
The user then sets up an inventory counting program called “Inventory Cycle Count”, which assists in counting all inventory over a period of time. The “A” items might be counted completely within each month. Therefore, a list of all of the “A” items (the highest dollar value) is generated, and randomly divided into 20 days, and each day 1/20th of the list counted and checked. The “B” items might be checked every quarter, and the “C” items checked once a year. This is a way to verify the accuracy of stockroom transactions, and to take measures necessary to keep the counts accurate. Type the ABC Types into the appropriate boxes.
The ABC code identifies a part source for inventory parts. Because MANEX allows up to 26 ABC codes, it also provides for identifying if a part is a make or buy part. Click on the desired Part Source radial, either Buy or Make.
Enter the Dock to Stock days. In MANEX, the ABC codes have a slightly different meaning. In addition to identifying the most or least expensive part numbers, a Dock to Stock period may be included in each ABC code. Dock to Stock is the number of days a part is expected to take to be delivered to the stock room after the part is received on the user’s dock.
Also, for each ABC code, MANEX provides a cycle count tolerance, which, if exceeded, will result in reporting unfavorable results during cycle counting. These tolerances may be an absolute dollar value, or a percentage of the inventory being counted. In the Cycle Count section, enter Cycle Count Days (NOTE: This field MUST be populated with a number other than "0". If "0" is entered these parts will NOT be included in the Cycle Count), % of Value, Lead Time Greater than, and Cycle Count Tolerances: Dollar Amount and Percentage.
The user must either depress the Save or Abandon changes button.
Where Used: In all Part Type Setup, Inventory Item Master, Material Requirements Planning and Cycle Count functions.
«Mark as Completed in RoadMap in Sect. B Item 4-e»
|
1.8.5. Reports for the ABC Types |
To obtain the ABC Setup Reports within the Web, select the WEB Print button from the ManEx action buttons at the top of the screen. For further detail on How the Reports work within the Web refer to Article #5477.
Note: In order to access the Reports within the Web the Company Root URL must be setup within the System Appearance module and user must be linked to web within the System Security Module.
Select
the Report Type: ABC Setup - A List of Reports will be displayed that are
available on the Web for ABC SETUP
To obtain the ABC Setup Reports, select the Print button from the ManEx action buttons at the top of the screen.
The
following reports screen will display a list of reports that are available on
the ManEx Desktop:
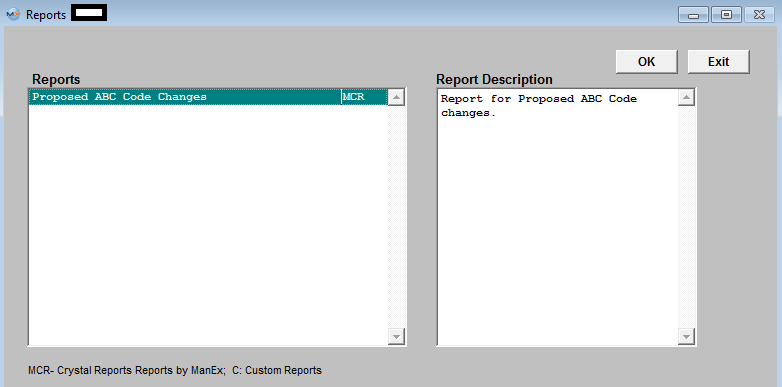
Highlight the Proposed ABC Changes Report and depress the OK button, the following screen will be displayed: (Note: This Report is available on the WEB also)
Highlight the type of parts and depress the > button. If you want both types of parts, depress the >> button.
Select "Proposed Changes Only" or "All Parts"
Depress the OK button.
The following report is available:
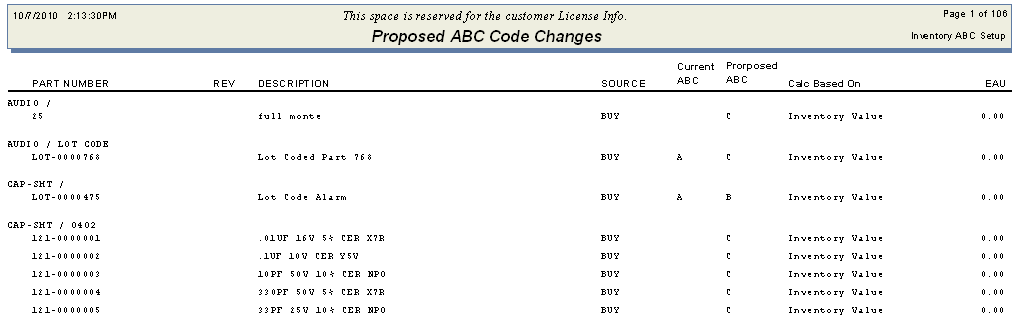
|
1.9. Inventory Buyer Setup | |
1.9.1. Prerequisites for Inventory Buyer Setup |
Complete the attached worksheet and " Mark as Completed RoadMap Section B Item 4-f before continuing the setup.
User MUST have full rights to the "System Setup" in System Security . Users with “Supervisor Rights” will automatically have access.
|
1.9.2. Introduction for Inventory Buyer Setup | This is the section to enter all the inventory buyers responsible for procuring materials. This is a requirement when adding to or editing the item master record. This information is used when setting up Part Class and Type in system setup.
|
1.9.3. Fields and Definitions for the Inventory Buyer Setup |
For inventory parts, it is often useful to assign code to parts of the person responsible for buying the parts. This makes it easy for receiving to resolve any issues with incoming material, and it makes it easy to divide up the workloads in purchasing. Also, several reports are available which can be sorted by the buyer code. One valuable report is the order actions necessary to be taken as a result of running MRP. The buyers may have a list of only those parts affecting their own workload, and not be burdened with looking at all of the rest of the actions. Also, shortages may be better resolved with the inclusion of a buyer code for the part number.
ManEx provides the ability to assign a three-character buyer code to each part. ManEx also provides for the eventuality that the buyer codes will change from time to time, and provides a buyer reassignment utility to change all parts for a specific buyer to another buyer.
|
1.9.4. How To ..... for Inventory Buyer Setup |
1.9.4.1. Setup the Inventory Buyer Setup Module |
Enter the SQLSYSSETTING.EXE (within the ManEx root directory)
This action will then prompt the user for a password
|
 |
The following screen will be displayed, enter the Material/Inventory Buyer Setup Module
This is the section to enter all the inventory buyers responsible for procuring materials. This is a requirement when adding to or editing the Item Master record. This information is used when setting up Part Class and Type .
|
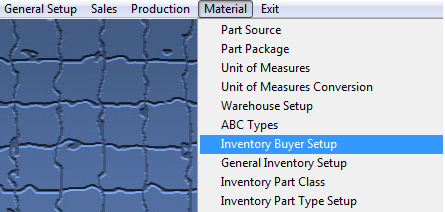 |
The following screen will be displayed:

To add and Inventory Buyer, depress the Add button. Type in the Initial, type in the Buyer Name. Depress the Save or Abandon changes button.
The user may also edit or delete an existing record by depress the Edit or Delete button.
These items may be sorted in any order by clicking on and dragging the box on the left side, to the (vertical) position desired. This order will be the order displayed in the pull downs when using this list in other modules within the system. Suggestion: Have the one most used at the top of the list.
Where Used: In all Part Type Setup, Inventory Item Master and Material Requirements Planning functions.
«Mark as Completed in RoadMap in Sect B Item 4-f»
|
1.9.4.2. Global Buyer Re-assignment | Global Buyer Reassignment is a utility program that allows users to replace current inventory buyers of all items linked to a buyer to another buyer. This is helpful when a buyer goes on vacation or leaves the company. To reassign, depress the Global Buyer Reassignment button.
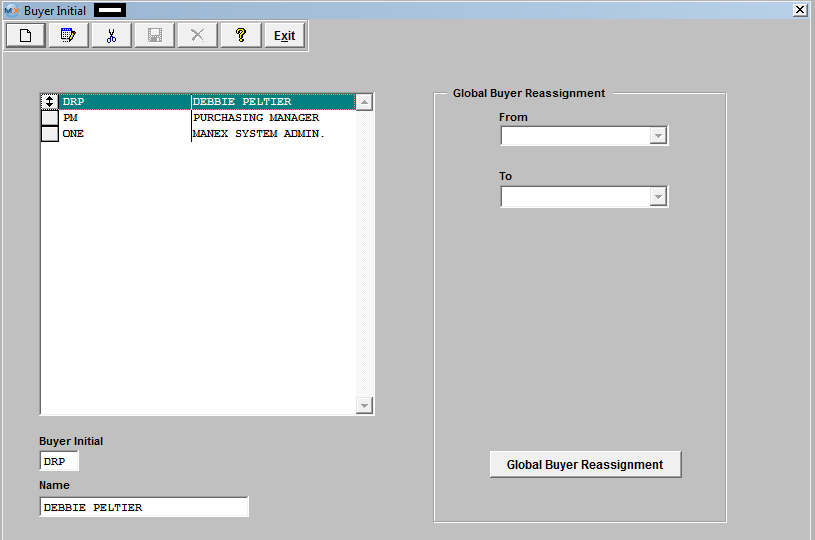
The following message will appear:
Depress the OK button to continue.
Depress the down arrow next to the From field. A list of existing buyers will appear. Select the buyer to be changed. Depress the down arrow next to the To field. Select the To buyer. Depress the Done button. All of the records (inventory part class/type setup, inventory, and purchase order) associated with the From buyer will update to the To buyer.
If the the "Done" button is depress with the From and To fields blank, user will receive the following message:
User MUST depress the "DONE" button for the changes to be made to the records.
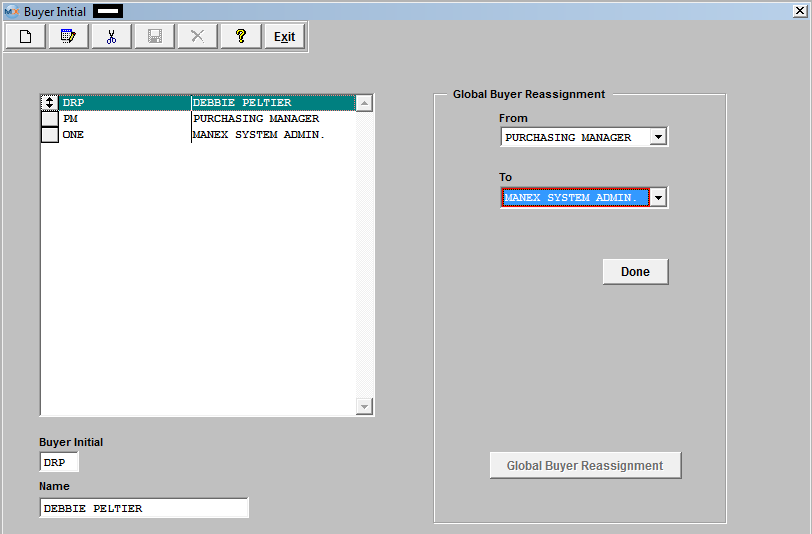
|
1.10. General Inventory Setup |
1.10.1. Fields and Definitions - General Inventory Setup |
Automatically number (MAKE and PHANTOM parts) |
Check this box to have the system automatically number new MAKE and PHANTOM parts added. |
Suppress Locations with 0 Qty |
User can select the default to Suppress Locations with "0" Qty - The following reports will take this default when printing: ICM Module Reports: Inv on hand report; Inv and WIP Valuation report; Unused INV list report. Kitting and Shortage Report: Kit pick work sheet.
|
Disable Automatic BOM AVL Update |
If you leave this box unchecked - ManEx will add the new AVL's (added within the ICM module) to all existing BOMs and check them as APPROVED. If you check this box - The AVL information will appear on the BOM's but they will be marked as NOT APPROVED. Then they will NOT drive any demands or be available for pulling to that kit. User will then have to manually go into each individual BOM and check the new AVL's that they would like to use. |
Purchase History By: |
This field allows the users to select which date "Order Date" or "Edit Date" on the PO to use when displaying the PO's in the Purchase History within the ICM module. This selection will be the default in the ICM module. |
Include PO with Status: |
This field allows the user to select the status of the Purchase Orders they would like to have displayed in the Purchase History within the ICM module "Open and Closed (Approved)" or "New and Editing (Waiting for Appr.)" or "All". This selection will be the default in the ICM module. |
When Showing Purchase History include last |
This field allows the users to setup the number of Purchase Orders they would like displayed in the Purchase History within the ICM module. This selection will be the default in the ICM module. |
Number of Purchase Orders used in the calculation of the Weighted Cost |
This field allows uers to setup the number of Purchase Orders they would like used in the calculation of the Weighted Cost within the ICM module. This selection will be the default in the ICM module. |
|
1.10.2. How To ..... General Inventory Setup |
Enter the SQLSYSSETTING.EXE (within the ManEx root directory)
This action will then prompt the user for a password
|
 |
The following screen will be displayed, enter the Material/General Inventory Setup
|
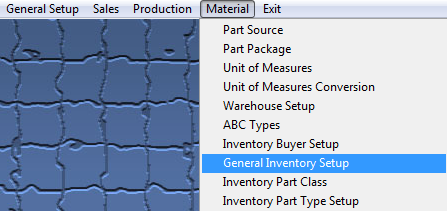 |
The following screen will be displayed:
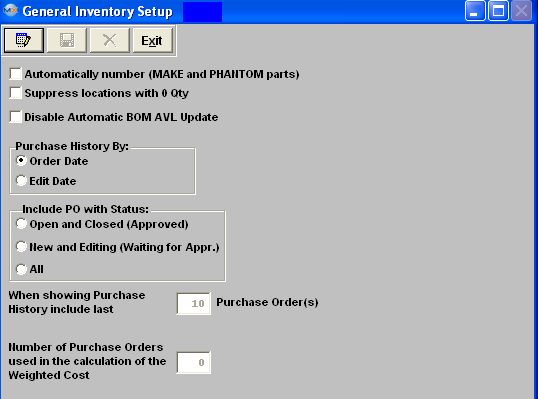
Automatically number (MAKE and PHANTOM parts) |
Check this box to have the system automatically number new MAKE and PHANTOM parts added. |
Suppress Locations with 0 Qty? |
If this box is checked the following reports will take this as a default: ICM Reports : Inv on hand report; Inv and WIP Valuation report; Unused INV list report. Kitting and Shortage Report: Kit pick work sheet.
|
Disable Automatic BOM AVL Update |
If you leave this box unchecked - ManEx will add the new AVL's (added within the ICM module) to all existing BOMs and check them as APPROVED. If you check this box - The AVL information will appear on the BOM's but they will be marked as NOT APPROVED. Then they will NOT drive any demands or be available for pulling to that kit. User will then have to manually go into each individual BOM and check the new AVL's that they would like to use. .
|
Purchase History By:
|
This field allows the users to select which date "Order Date" or "Edit Date" on the PO to use when displaying the PO's in the Purchase History within the ICM module. This selection will be the default in the ICM module.
|
Include PO with Status:
|
This field allows the user to select the status of the Purchase Orders they would like to have displayed in the Purchase History within the ICM module "Open and Closed (Approved)" or "New and Editing (Waiting for Appr.)" or "All". This selection will be the default in the ICM module.
|
When Showing Purchase History include last
|
This field allows the users to setup the number of Purchase Orders they would like displayed in the Purchase History within the ICM module. This selection will be the default in the ICM module.
|
Number of Purchase Orders used in the calculation of the Weighted Cost
|
This field allows uers to setup the number of Purchase Orders they would like used in the calculation of the Weighted Cost within the ICM module. This selection will be the default in the ICM module.
|
|
1.11. Inventory Part Class |
1.11.1. Prerequisites for Inventory Part Class |
Complete the attached worksheet and " Mark as Completed RoadMap Section B Item 4-g before continuing the setup.
User MUST have full rights to the "System Setup" in System Security . Users with “Supervisor Rights” will automatically have access.
|
1.11.2. Introduction for Inventory Part Class | The inventory class and types are one of the most powerful parts of the ManEx system. These classifications allow the users to break up large inventories into groups and sub-groups. The smaller groups make it easier to locate an item, to view reports by classes, and easier to identify a part. In ManEx, it also guides users in the addition of new parts, insuring that there are common approaches to descriptions for common parts. ManEx even will allow for automatic part number generation, where the user has to only enter a description, after selecting a part class and type. Utilization of the class and types greatly simplifies the amount of information that must be contained in the description and part number for each part. The user must enter part classes for each part, but is not required to enter part types. However, without the part types established, the user is required to enter much more data when adding specific items to the item master.
Manex uses the Part Class and Type as an extension to the description of the part. Therefore it will be displayed throughout the system on screen and in reports as an extension of the description. |
1.11.3. Fields and Definitions for Inventory Part Class | 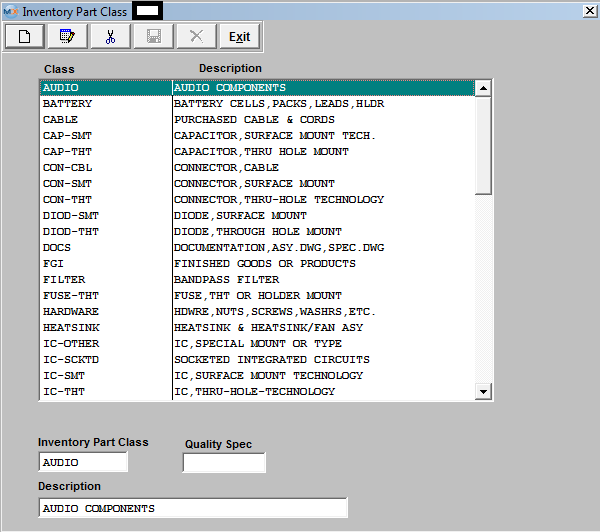
Inventory Part Class
|
The first major classification is the part Class. This classification may be used to identify major groups of parts. For example, classes may include specific part genres, such as Resistors, Capacitors, Diodes, Transistors, Connectors, Relays, PC Boards, LEDs, Wire, Hardware, etc. Part classes must also be assigned to assemblies, and may be defined as Top Assy, Sub-Assy, Spares, etc. All item master parts MUST have a part class assigned to them in ManEx. If you want to separate Finished Goods and Raw Material Inventory, be sure to include a Finished Goods Class. The Part Class can be a max of 8 characters, the Part Class description can be a max of 30 characters.
|
Once a part classification has been established, then sub-groups may be assigned to each class. The sub-groups are called Part Types, and each part type may have a number of different characteristics associated with it.
Quality Spec
|
Here you may enter a quality specification number (10 characters) that will be associated with each class. This specification number will print on purchase orders whenever placed for the part class.
|
|
1.11.4. How To ..... for Inventory Part Class |
1.11.4.1. Add, Edit, or Delete a Part Class |
Enter the SQLSYSSETTING.EXE (within the ManEx root directory)
This action will then prompt the user for a password
|
 |
The following screen will be displayed, enter the Material/Inventory Part Class
|
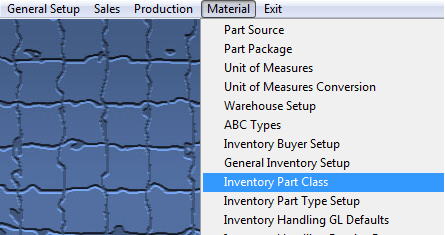 |
The following screen will be displayed:
To ADD a part class depress the Add button from the main tool bar.
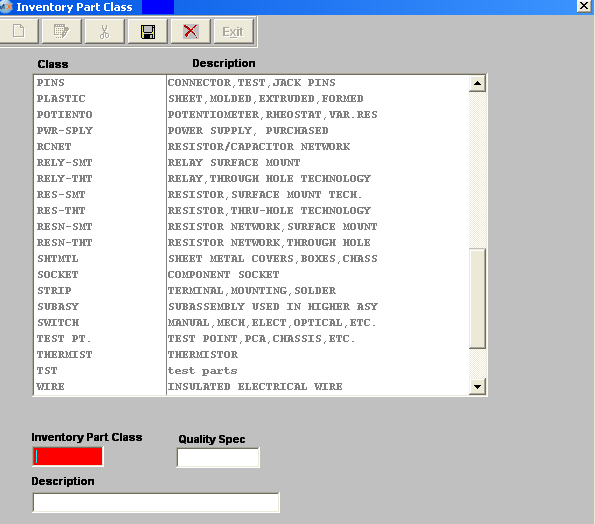
Enter in the Inventory Part Class, Description and Quality Spec information. Depress the Save button from the main tool bar to Save, depress the Abandon Changes button from the main tool bar to abandon changes.
To EDIT a part class highlight the part class that you want to make changes to, depress the Edit button from the main tool bar.
User may edit the Description or Quality Spec. Depress the Save button from the main tool bar to save changes or depress the Abandon Changes button from the main tool bar to abandon changes.
To DELETE a part class highlight the part class that you want to delete, depress the Delete button from the main tool bar. User will receive the followin popup.
Select "YES" to continue deleting the part class, select "NO" to stop the deletion.
Where Used: In all Material functions.
«Mark as Completed in RoadMap in Sect. B Item 4-g»
|
1.12. Inventory Part Type Setup |
1.12.1. Prerequisites for Inventory Part Type Setup |
Complete the attached worksheet and " Mark as Completed RoadMap Section B Item 4-g before continuing the setup.
User MUST have full rights to the "System Setup" in System Security . Users with “Supervisor Rights” will automatically have access.
|
1.12.2. Introduction for Inventory Part Type Setup | The inventory class and types are one of the most powerful parts of the ManEx system. These classifications allow the users to break up large inventories into groups and sub-groups. The smaller groups make it easier to locate an item, to view reports by classes, and easier to identify a part. In ManEx, it also guides users in the addition of new parts, insuring that there are common approaches to descriptions for common parts. ManEx even will allow for automatic part number generation, where the user has to only enter a description, after selecting a part class and type. Utilization of the class and types greatly simplifies the amount of information that must be contained in the description and part number for each part. The user must enter part classes for each part, but is not required to enter part types. However, without the part types established, the user is required to enter much more data when adding specific items to the item master.
|
1.12.3. Fields and Defintions for Inventory Part Type |
Once a part classification has been established, then sub-groups may be assigned to each class. The sub-groups are called Part Types, and each part type may have a Prefix (number of different characteristics) associated with it.
 |
This gives the user the option to re-sort the order the part types are displayed in the pulldown when setting up parts in the Inventory Control Mgmt module.
(See Article #4063 for further detail). |
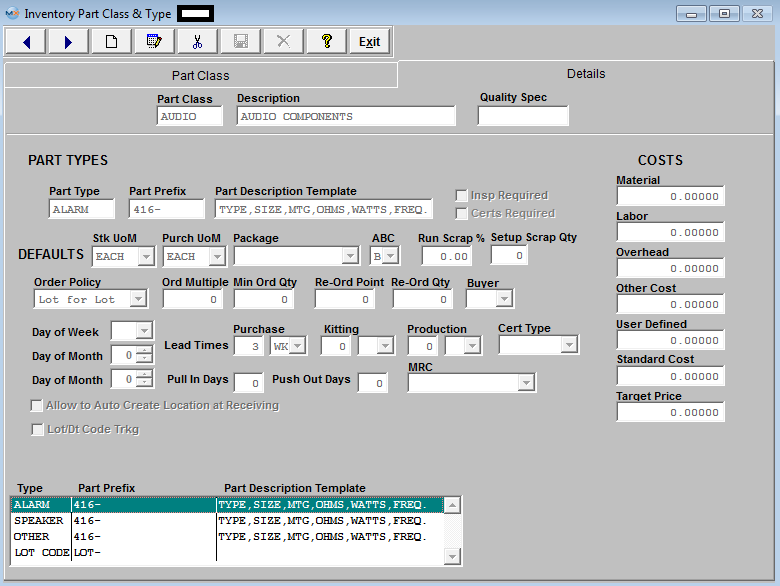
Once a part type is defined, the user’s workload in entering new part numbers is greatly reduced. For each part type, the user may set up parameters for that part type that will automatically be entered as the default condition when adding a new part for the same type.
If the user wishes, there can be a specific prefix (15 characters) added to each part number within a part type to distinguish the component from other types. The use of the prefix is entirely optional, and can be anything the user would like it to be numerical, alphabetical or both. A given prefix is tied to a part type, it is not exclusive, and can be the same prefix for many part types. When using a prefix it must have the "-", this is how the system identitifes it as the prefix. An example of a prefix might be “CS05-”, which would be the prefix for all Ceramic Capacitors in the part type SMT-0805. Then, anyone looking at the part number would know much more than otherwise possible. Also, because the part class and type is assigned to each part number, it may not be necessary to repeat the information in the description, leaving more room for specifics. If a part was in the CS05- type just described, the description would not have to include “SMT 1205” or “CER”, because they are already contained in the part type and prefix. Setting up a prefix is NOT required.
Each part type may also have a specific description template (30 characters) assigned to it to be used as a guide when entering new parts. In the example just defined, the template might appear like this: ”value xxFxx%,xxxV”. The words “CAP” and “CER” are not necessary, as all reports print out the class next to the part number. However, the user may wish to include “CAP” to aid in understanding BOMs, and searches based on part descriptions. The template entered in this setup will show under the description when defining a new item number description.
In addition to the prefix and description template, additional parameters may be set up and be defaulted into the item master when setting up a new part. These parameters are: Units of Measure, both stocking and purchasing; Packaging, ABC codes, Buyer Code, Run (production) Scrap percentage; Setup Scrap Quantity; Costs – Material, Overhead and/or User Defined, Material Requirements Planning Order Frequency, Order Multiples; Order Minimums; Re-order points (safety stock); Re-order qty; and lead-times for purchasing, kitting and production. There is also provision for MRP adjustment sensitivity in the Push-out, Pull-in days. Each of these will be discussed below.
Also, for each part type, the user may define whether or not the parts in the type are to be tracked by lot number and/or date code, inspected at incoming or require certification.
There is an option in ManEx for "Automatic Numbering of MAKE and Phantom parts" when they are added to the database. See Article #3510 for further detail.
Inspection Required
|
This box, when checked, flags the receiving department that the parts must be placed in Receiving Inspection prior to the stockroom.
|
Certification Required
|
This box, when checked, flags the receiving department to check that the vendor included the appropriate certification for the parts, and/or the shipping department included certification. The types of certificates are Receiving, Shipping or Both.
|
Unit of Measure
|
The unit of measure for both stocking and purchasing must have already been entered in the “Unit of Measure” setup.
|
Package
|
The packaging description for the parts must have already been entered in the “Part Package” setup.
|
ABC
|
The ABC codes for the parts must have already been entered in the “ABC Types” setup.
|
Run Scrap %
|
This is the amount (in percentage of the parts issued to a work order) that will be added to the kit to compensate for materials normally lost in the production processes. It is typical to have some floor losses associated with very small and inexpensive parts that may have to be replaced in the kit. This percentage will be used to issue additional parts to a kit for a work order, and by Material Requirements Planning when generating requirements for un-kitted work orders and forecasts. This number should be at a minimum to avoid ordering excess material, but should be practical enough to avoid shortages when needed for work orders in production.
|
Setup Scrap Qty
|
This is the amount (in fixed quantity) of parts that, on the average, are consumed in the set up of the parts when tape leaders are used. Sometimes a user knows that there may be several setups from one reel of parts, and that for each setup there are a fixed number of parts on the tape that will be lost when the lot runs. Then this number may be used to ensure that sufficient parts are ordered and available for kitting. Material Requirements Planning uses this number based on the number of work orders required to meet demand.
|
Order Policy (frequency)
|
This value determines how often an order action is created for a part. If the part is used in many different assemblies, with many different work orders, then the Material Requirements Planning module may create many purchasing actions for the same part. In order to reduce the work load in purchasing, the user is offered a choice of order conditions which accumulates the orders into one action. These choices are: Lot for Lot; Daily; Weekly; Semi Monthly; Monthly; and Quarterly.
|
Lot for Lot
|
This means that each work order will create a demand and separate purchasing order action. The order action will be initiated based on the due date for each of the intended work orders.
|
Daily
|
This means that instead of creating an order action for each and every work order, all of the work orders with actions due on the same day are grouped together. The order action is created once per day, with the total quantity needed for the day included in the order action.
|
Weekly
|
This works the same way, except that all order actions due within a week period are pulled forward to a specific day and all actions combined for that day. Part of selecting weekly includes selecting the day of the week that the order action is to be effective. Once the day is established, the Materials Requirements Planning module will move all order actions in the interval to the beginning of the interval and combine them. The user may wish to use different days for different part classes and types, so that the buyer’s work load is distributed throughout the week.
|
Semi Monthly
|
And so on, except that in semi-monthly, the user may select the days of the month in which the order action takes place. For example, the 1st and the 15th may be chosen, or the 10th and the 25th. Again, these dates may be arranged for different part types to spread the load in purchasing.
|
Monthly
|
In this case, only one day of the month is requested, and all order actions will be moved forward to that date.
|
Quarterly
|
In this case, only one month of the quarter is requested, and all order actions will be moved forward to that date.
|
NOTE: The most expensive parts will probably be with the shortest order policy. This will help control the customer’s inventory turns, and maintain tight control over the parts. On the other hand, the least expensive parts may be better positioned towards monthly purchases, since the cost to process purchase orders may exceed the cost of the parts and of maintaining the inventory. It is up to the user to determine the best balance between order policies, inventory turns and the cost of procurement.
Order Multiple Quantity
|
This value is used by Material Requirements Planning module to determine how to order parts over and above the minimum quantity. If a part comes in 5000 unit reels, and only in 5000 unit reels, the order multiple would be entered as 5000. If the Material Requirements Planning module determines that a quantity of 5010 is needed, it will create an order action for the full 10000 parts.
|
Minimum Order Quantity
|
This value is used by MRP to determine how to order parts. Although this may be less than the order quantity, it is more likely that the vendor will not sell (for the price) less than a certain quantity, with order multiples beyond that quantity. For example, there may be an order minimum of 50,000 parts, but order multiples of 5,000 are offered beyond that quantity.
It is especially important to watch this value in connection with the order frequency, as a part with an order frequency of lot-for-lot and a minimum order quantity may result in purchasing actions of multiple requirements at the minimum, instead of combining the requirements to meet the minimum.
|
Reorder Point
|
This is the Safety Stock quantity. It is established so that whenever the inventory drops below this point, order actions are initiated to purchase additional parts. This feature might be used to maintain free stock items, such as nuts and bolts, and set at the approximate usage experienced in the time it takes to replace the parts.
|
Reorder Quantity
|
The is the number of parts to be ordered whenever a reorder point is encountered. The Materials Requirement Planning module will use this quantity in the order action.
|
Buyer
|
The Buyer Code for the parts must have already been entered in the “Inventory Buyer” setup.
|
Lead-times
|
All lead times are calculated with the Production Calendar. There are three types of lead-times available in ManEx to describe the duration required for an operation:
|
Purchasing
|
This is the amount of time that the vendor needs to have the parts delivered to the user’s dock. It begins when the order is placed with the vendor, and ends when the part arrives at the user’s dock. The Materials Requirements Planning module uses this value to determine when the order action dates should occur in order to have the parts in stock when the kit is due to be picked.
|
Kitting
|
This is the amount of time that the stockroom needs to pull a kit for the product. It is used only in assemblies, and not available for purchased parts. The Materials Requirements Planning module uses this value to add to the production lead-time to determine when the kitting should begin.
|
Production
|
This is the amount of time that it takes to manufacture or assemble the product. It includes the duration from the time the kit is released to production to the time the product is shipped. The Materials Requirements Planning module uses this value to determine when all parts must be in stock and the work order initiated in order to meet the delivery date.
|
Note: The value of each of these terms may be in days, weeks or months.
Push-out / Pull-in
|
These values, in days, determine the sensitivity of The Materials Requirements Planning moduleto changes in demand. If the due date for an order moves within these values, then no order action is initiated to modify purchase orders or work orders in progress. If the due date falls beyond these parameters, then order actions to move the purchase orders or work orders will be initiated. The values used here should be influenced by the part cost (more expensive, the tighter the control) the order frequency (should be about one-half the order frequency) and a user’s policy regarding the cost of purchasing versus the cost of inventory. The lead-time and part availability may also be a consideration, with very difficult to obtain parts having tighter sensitivity. The Materials Requirements Planning module takes these parameters into account for changes in scheduled dates, but not for changes in quantities, since it is assumed that changes in quantity should be addressed regardless of the push-out/pull-in days.
|
Costs – These are the standard (budgeted) costs associated with the item.
Material Cost
|
In Systems with ManEx Accounting installed, the amount entered in this field is used for Cost Accounting functions. If Cost Accounting is not being used, the field can show actual, target or user defined cost. The Material Cost field adds into the Standard Cost total.
Important Note - If accounting is installed: For all buy parts, the material cost field must have data entered.If this data is missing (or wrong), the Raw Materials Inventory and theWork In Process (WIP) will be incorrect for the accounting records. All make parts which are not labor only (the customer brings you the kit and all you do is apply the labor), must have data entered in the material cost field. Additionally, the data entered in the material cost field for the make part must equal the sum of the Bill of Materials components.(Please refer to Bill of Materials Reports – Bill of Material With Standard Cost.) If the data is missing or wrong on a Make Part, the Work In Process, Cost of Goods Sold and Finished Goods Inventory will be wrong for the accounting records.If the sum of the Bill of Materials components does not equal the standard cost per the Item Master, a configuration variance will generate.
|
Labor Cost
|
This is the cost of the labor associated with the part. The Labor cost field will add into the Standard Cost total.
|
Overhead Cost
|
This is the overhead burden if the user wants to capture the overhead at the assembly level. The Overhead cost field will add into the Standard Cost total.
|
Other Costs
|
This is any other costs associated with the part. The Other costs field will add into the Standard Cost total.
|
User Defined Costs
|
This is any additional cost associated with the part, as defined by the user. The User Defined cost field will add into the Standard Cost total.
|
Standard Cost
|
This is the total of the following costs: Material, Labor, Overhead, Other Costs, and User Defined.
|
Target Price
|
This field is currently only a data entry field and will be reflected in the Purchase Order module for "BUY" or "MAKE/BUY" parts.
|
Tracking by Lot number / Date code
|
If this box is checked, the user will be required to enter a lot number, date code, expiration date (optional) and internal lot number information whenever performing a transaction for the part. If the user wishes to maintain inventory to this level, then they MUST enter information each time a part is moved. This will allow complete traceability by date and lot code for products assembled. The user will be able to determine all work orders or sales orders in which a certain date code was used. This field can NOT be edited once this part type record has been saved.
|
Auto-date for Internal Lot Code
|
When using Lot Tracking, this feature will automatically assign the current date as the internal lot code. This field may be appended or overwritten by the user during the transaction, if desired.
|
Product Expiration Days
|
When using Lot Tracking, this feature will automatically assign the current date plus the product expiration days as the expiration date on completed products moved to Finished Goods. This field may be appended or overwritten by the user during the transaction if desired.
|
The Part Class and Type MUST exist in the setup, if the user wishes to add a part to the item master within the Inventory Control Management module. Once the part class and type are entered, complete the description according to the description template established for the part type in this section. ManEx will then assign a prefix to a new part number according to the prefix in the part type setup, pick the next available sequential number (if automatic part numbering has been selected within the Numbering Setup module), and complete all of the Inventory and Material Requirements Planning module data based on the part type. The user may, if needed later, adjust any of these values within the Inventory Control Management module.
|
1.12.4. How To ..... for Inventory Part Type Setup |
1.12.4.1. Add, Edit, or Delete a Part Type |
Enter the SQLSYSSETTING.EXE (within the ManEx root directory)
This action will then prompt the user for a password
|
 |
The following screen will be displayed, enter the Material/Inventory Part Type Setup Module
|
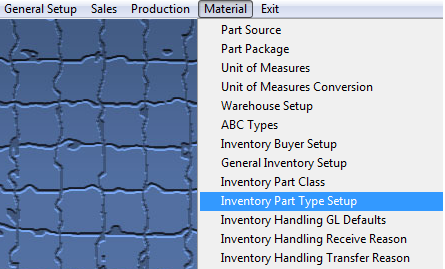 |
The following screen will be displayed: The main screen, Part Class, lists the existing records. Highlighting a part class will show the corresponding types linked to it on the right. The second screen, Details, is where records are created.
Re-Order - This gives the user the option to re-sort the order the part types are displayed in the pulldown when setting up parts in the Inventory Control Mgmt module.
First select the Part Class, the Part Types for this Class will be displayed on the right. The Part Types may be re-sorted by clicking on the REORDER button, click on and drag the box on the left side of the part type desired to the (vertical) position desired. When completed with the re-order, click on the DONE button. This order will be the order displayed in the pull downs when using this list in other modules within the system. Suggestion: Have the one most used at the top of the list.
To add a new part type to a class you must first highlight the Part Class that you want to add the part type to, then enter the Details tab:
Depress the Add button from the main tool bar:
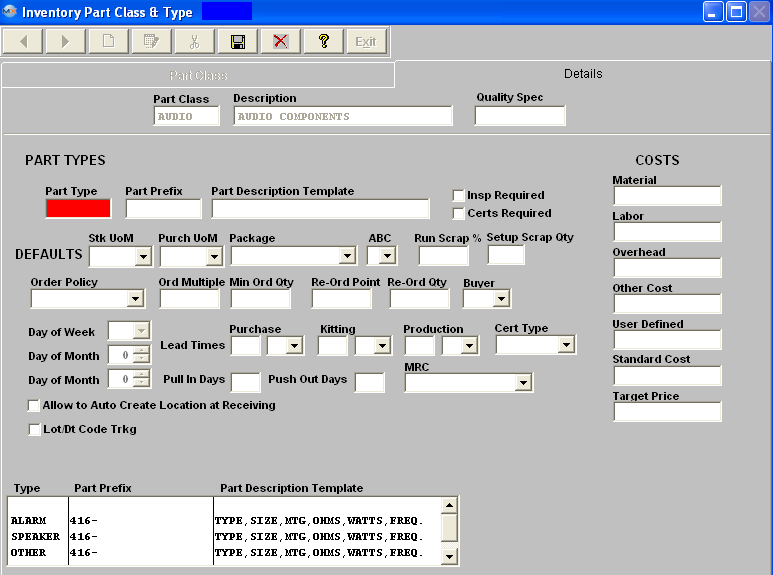
Enter the Part Type, Part Prefix, and Part Description Template. Check whether Inspection and/or Certificates are required. Select the Stock Unit of Measure, Purchasing Unit of Measure, Package, ABC code and Buyer code by depressing on the down arrow next to the field. Type in the Run Scrap %, Setup Scrap Quantity and Cost Information – Material, Labor, Overhead and/or User Defined. The total of the Costs entered will appear in the Standard Cost field. Important Note - If accounting is installed: For all buy parts, the material cost field must have data entered. If this data is missing (or wrong), the Raw Materials Inventory and the Work In Process (WIP) will be incorrect for the accounting records. All make parts which are not labor only (the customer brings you the kit and all you do is apply the labor), must have data entered in the material cost field. Additionally, the data entered in the material cost field for the make part must equal the sum of the Bill of Materials components. (Please refer to Bill of Materials Reports – Bill of Material With Standard Cost.) If the data is missing or wrong on a Make Part, the Work In Process, Cost of Goods Sold and Finished Goods Inventory will be wrong for the accounting records. If the sum of the Bill of Materials components does not equal the standard cost per the Item Master, a configuration variance will generate.
Select the Order Policy by depressing on the down arrow next to the field. Enter in the Order Multiple, the Minimum Order Quantity, Re-Order point and Re-Order Quantity. Select the Certificate type by depressing the down arrow next to the field. Select the Day of the Week or Day of the Month by depressing on the down arrow next to the field. Select the Purchase, Kitting and Production Lead Times by entering the number in the appropriate box and depressing on the down arrow to select the Days, Weeks or Months. Type in the Pull In or Push Out days. Check the Lot Code box, if desired. If you select Lot/Date Code tracking, you’ll also be prompted for Auto Date for all Lots and for the product expiration days, as displayed below.
If the user wishes to edit or delete part type information, pressing the Edit or Delete button from the main tool bar enables the user to choose a part type used in the class (assuming there is more than one) and edit or delete it. (NOTE: Users will not be allowed to delete a part type which has active inventory or orders.)
After Adding, Editing or Deleting a part type, the user must save the data, by depressing the Save button from the main tool bar.
When saving a new part type the user will receive the following message to remind the user that once this record is saved the Lot/Date code tracking field can not be edited:
At this time the user can select "YES" to continue the save or "NO" to abort the save.
Where Used: In all Material functions.
«Mark as Completed in RoadMap in Sect. B Item 4-g»
|
1.13. Inventory Handling G/L Defaults | |
1.13.1. Prerequisites for Inventory Handling GL Defaults |
Complete the attached worksheet and " Mark as Completed RoadMap Section B Item 4-h before continuing the setup.
All applicable General Ledger Account Numbers must be set up in the G/L Account Setup module.
User MUST have full rights to the "System Setup" in System Security . Users with “Supervisor Rights” will automatically have access.
|
1.13.2. Introduction for Inventory Handling GL Defaults | This section sets up the General Ledger account number defaults for items received or issued via the Manex Inventory Handling screen. This is for adding to or subtracting the quantities in the Inventory Master without using a Purchase Order or a Sales Order.
Make sure that you do not use GL account #s that are associated to Warehouses within Warehouse Setup. |
1.13.3. Fields & Definitions for Inventory Handling GL Defaults |
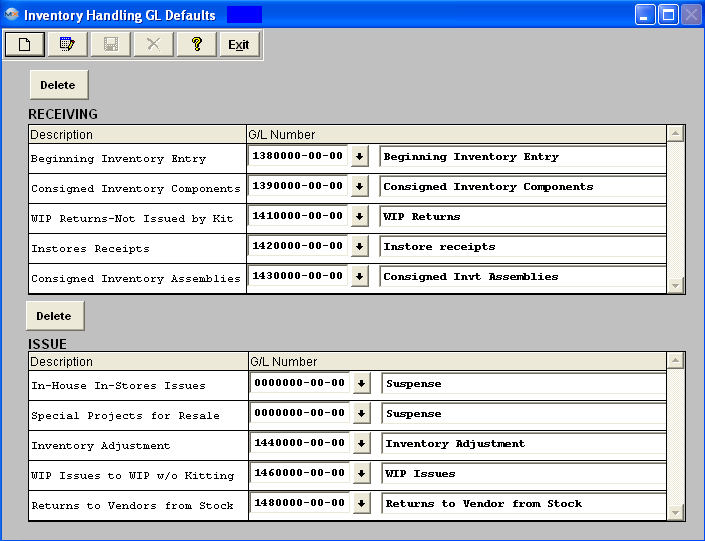
This section sets up the General Ledger account number defaults for items received or issued via the Manex Inventory Handling screen. This is for adding to or subtracting the quantities in the Inventory Master without using a Purchase Order or a Sales Order.
Determine the description of the inventory receiving or inventory issuing. At data entry, the system will display the General Ledger account number and description for your selection. Plan your selections using the worksheet.
Examples of Receiving could be Opening Inventory, receipt of free sample, etc.
Examples of Issue could be Special Project Samples sent to customers, etc.
NOTE: The Inventory Handling GL Codes entered within this screen should NOT be the same as the GL Codes selected for the Warehouse setup .
|
1.13.4. How To ..... for Inventory Handling GL Defaults |
1.13.4.1. Setup the Inventory Handling GL Defaults |
Enter the SQLSYSSETTING.EXE (within the ManEx root directory)
This action will then prompt the user for a password
|
 |
The following screen will be displayed, enter the Material/Inventory Handling GL Defaults Module
|
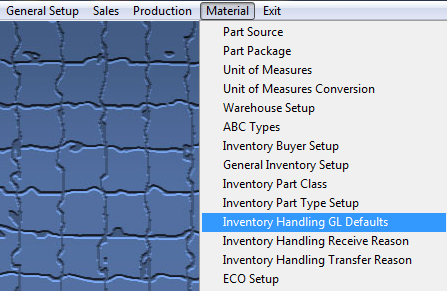 |
The following screen will be displayed:
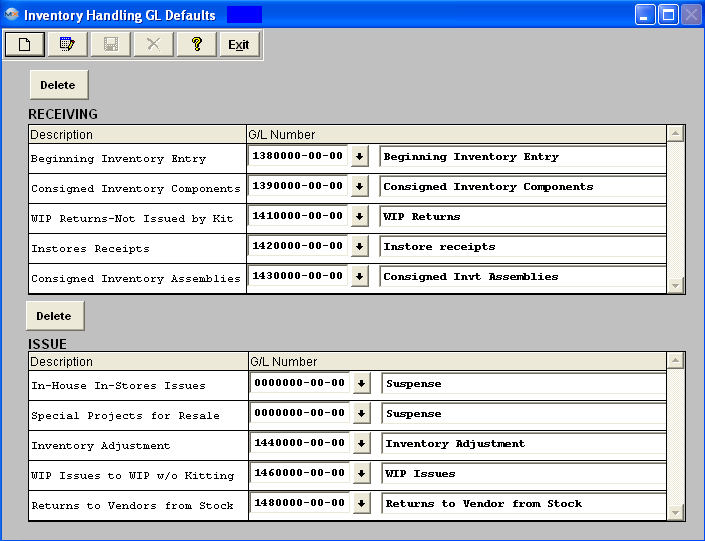
To Add a record, depress the Add button from the main tool bar, Enter in the description in the section and then select the general ledger number, from the list shown below:
Depress on the Down arrow next to the field until you reach the account. Depress the Save button in the section. The General Ledger Description will automatically fill in.
When finished depress the Save or Abandon changes button.
Where Used: This section sets up the General Ledger account number defaults for items received or issued via the Manex Inventory Handling module.
«Mark as Completed in RoadMap in Sect. B Item 4-h»
|
1.14. Inventory Handling Receive Reasons |
1.14.1. Prerequisites for Inventory Handling Receive Reasons |
Complete the attached worksheet and " Mark as Completed RoadMap Section B Item 4-i before continuing the setup.
User MUST have full rights to the "System Setup" in System Security . Users with “Supervisor Rights” will automatically have access.
|
1.14.2. Introduction for Inventory Handling Receive Reasons |
This screen is to enter Inventory Receiving reason codes in order to save the user from a lot of repetitive data entry.
The information entered here will be used in the Inventory Handling module.
|
1.14.3. Fields & Definitions for Inventory Handling Receive Reasons |
This screen is to enter Inventory Receive Reasons in order to save the user from a lot of repetitive data entry.
The information entered here will be used in the Inventory Handling module.
Examples of Receiving reasons would be Opening Inventory, Material Received on Trial, etc.
Enter the reasons in the table.
|
1.14.4. How To ..... for Inventory Handling Receive Reasons |
1.14.4.1. Setup the Inventory Handling Receive Reasons |
Enter the SQLSYSSETTING.EXE (within the ManEx root directory)
This action will then prompt the user for a password
|
 |
The following screen will be displayed, enter the Material/Inventory Handling Receive Reason
|
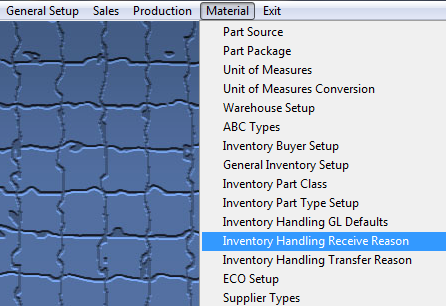 |
The following screen will be displayed:
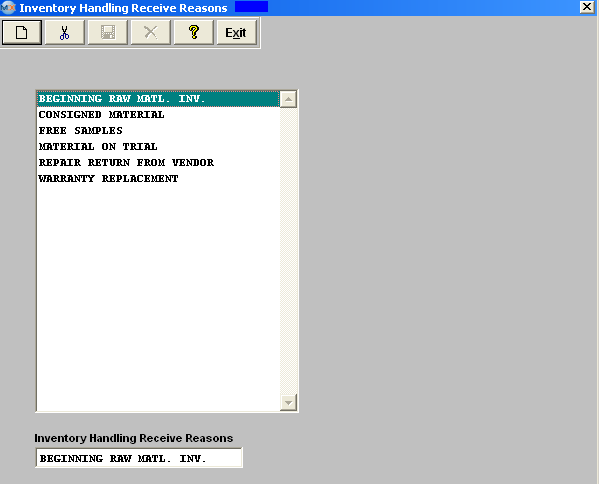
To Add a new reason, depress the Add button. Enter in the reason.
To delete a reason code, highlight the reason, and depress and Delete button.
When finished making changes depress the Save or Abandon changes button.
Where Used: The Reason Codes are used in the Inventory Handling module.
«Mark as Completed in RoadMap in Sect. B Item 4-i»
|
1.15. Inventory Handling Transfer Reasons |
1.15.1. Prerequisites for Inventory Handling Transfer Reasons |
Complete the attached worksheet and " Mark as Completed RoadMap Section B Item 4-i before continuing the setup.
User MUST have full rights to the "System Setup" in System Security . Users with “Supervisor Rights” will automatically have access.
|
1.15.2. Introduction for Inventory Handling Transfer Reasons |
This screen is to enter Inventory Transferring codes in order to save the user from a lot of repetitive data entry.
The information entered here will be used in the Inventory Handling module.
|
1.15.3. Fields & Definitions for Inventory Handling Transfer Reasons |
This screen is to enter Inventory Transferring codes in order to save the user from a lot of repetitive data entry.
The information entered here will be used in the Inventory Handling module.
Examples of Transferring codes would be Special Projects, Prototype, etc.
Enter the reasons in the table.
|
1.15.4. How To ..... for Inventory Handling Transfer Reasons |
1.15.4.1. Setup the Inventory Handling Transfer Reasons |
Enter the SQLSYSSETTING.EXE (within the ManEx root directory)
This action will then prompt the user for a password
|
 |
The following screen will be displayed, enter the Material/Inventory Handling Transfer Reason
|
 |
The following screen will be displayed:
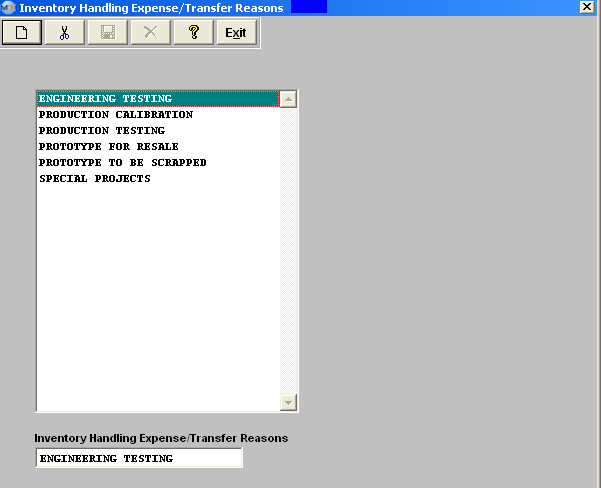
To Add a new reason code, depress the Add button. Enter in the reason.
To delete a reason code, highlight the reason, and depress and Delete button.
When finished making changes depress the Save or Abandon changes button.
Where Used: The Reason Codes are used in the Inventory Handling module.
«Mark as Completed in RoadMap in Sect. B Item 4-i»
|
1.16. Engineering Change Order Setup | |
1.16.1. Prerequisites for ECO Setup |
Complete the attached worksheet and " Mark as Completed RoadMap Section B Item 4-j before continuing the setup.
|
1.16.3. Fields & Definitions for ECO Setup |
Department |
Name of the Department defaulted in from the Administration Department |
Approval Required |
Check the department(s) which must approve a ECO |
Retain Sales Order Prices |
Check this box to Retain Sales Order Prices when an ECO is created |
|
1.16.4. How To ..... for ECO Setup |
1.16.4.1. Setup the ECO Setup Module |
Enter the SQLSYSSETTING.EXE (within the ManEx root directory)
This action will then prompt the user for a password
|
 |
The following screen will be displayed, enter the Material/ECO Setup Module
|
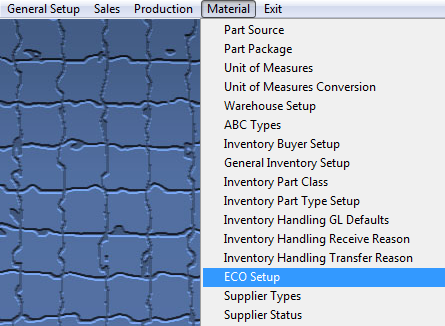 |
The following screen will be displayed:
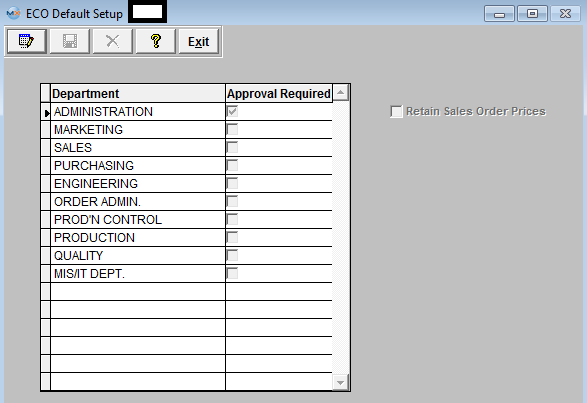
The departments displayed on the screen are setup in the Administration Department Setup module.
Depress the Edit action button, click on the appropriate boxes for those departments which must authorize an Engineering Change Order. Uncheck the appropriate boxes to remove a department which no longer must authorize an ECO.
Once the changes have been complete. depress the Save or Abandon changes button.
Where Used: In the Engineering Change Order Module.
«Mark as Completed in RoadMap in Sect. B Item 4-j»
|
1.17.1. Prerequisites for Supplier Types |
Complete the attached worksheet and "Mark as Completed RoadMap Section B Item 4-k before continuing the setup.
User MUST have full rights to the "System Setup" in System Security . Users with “Supervisor Rights” will automatically have access.
|
1.17.2. Introduction for Supplier Types |
When adding suppliers, it is convenient to identify the supplier by a type. Examples of supplier types might be:
Manufacturer, Distributor, Rep. Etc.
|
1.17.3. Fields & Definitions for Supplier Types |
When adding suppliers, it is convenient to identify the supplier by a type. Examples of supplier types might be: Manufacturer, Distributor, Rep. Etc.
A supplier type must be entered prior to entering suppliers. The field length is 20 characters.
|
1.17.4. How To ..... for Supplier Types |
1.17.4.1. Setup the Supplier Types |
Enter the SQLSYSSETTING.EXE (within the ManEx root directory)
This action will then prompt the user for a password
|
 |
The following screen will be displayed, enter the Material/Supplier Types Module
|
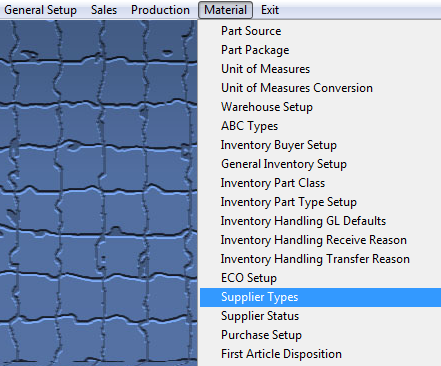 |
The following screen will be displayed:
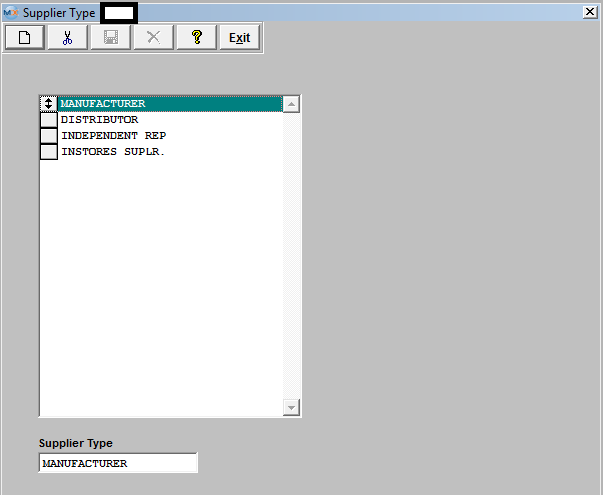
To add additional Supplier Types depress the Add button. Tye in the Supplier Type.
To delete an existing Supplier Type, highlight the Supplier Type you want to delete, and depress the Delete button.
When changes have been completed depress the Save or Abandon changes button.
These items may be sorted in any order by clicking on and dragging the box on the left side, to the (vertical) position desired. This order will be the order displayed in the pull downs when using this list in other modules within the system. Suggestion: Have the one most used at the top of the list.
Where Used: Supplier types are used in the addition of suppliers, and in some reporting functions.
«Mark as Completed in RoadMap in Sect. B Item 4-k»
|
1.18.1. Prerequisites for Supplier Status |
Complete the attached worksheet and " Mark as Completed RoadMap Section B Item 4-l before continuing the setup.
User MUST have full rights to the "System Setup" in System Security . Users with “Supervisor Rights” will automatically have access.
|
1.18.2. Introduction for Supplier Status | MANEX provides six classifications of vendor status: Preferred, Approved, Under Evaluation, Probation, Inactive and Disqualified. These Status types are permanently installed in the software, and MANEX has already provided a description for these classifications the same as the status. However, if the user wishes, the description of this status may be changed to suit the user. No action is necessary in the setup if the user is satisfied with the current defaults. |
1.18.3. Fields & Definitions for Supplier Status |
MANEX provides six classifications of vendor status: Preferred, Approved, Under Evaluation, Probation, Inactive and Disqualified. These Status types are permanently installed in the software, and MANEX has already provided a description for these classifications the same as the status. However, if the user wishes, the description of this status may be changed to suit the user. No action is necessary in the setup if the user is satisfied with the current defaults.
|
1.18.4. How To ..... for Supplier Status |
1.18.4.1. Setup the Supplier Status Module |
Enter the SQLSYSSETTING.EXE (within the ManEx root directory)
This action will then prompt the user for a password
|
 |
The following screen will be displayed, enter the Material/Supplier Status Module
|
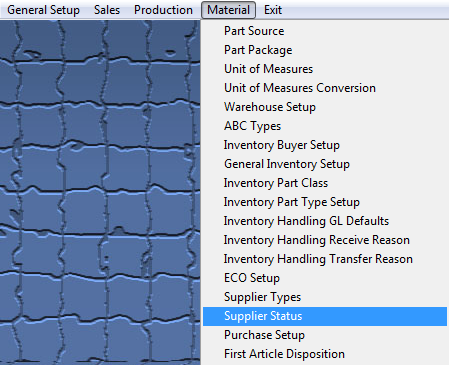 |
The following screen will be displayed:
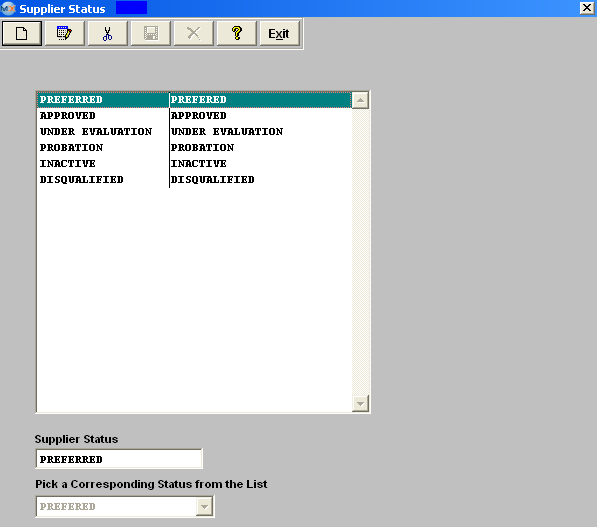
To modify the description of a supplier status, click on the Edit button, and enter the new description.
When changes have been complete, depress the Save or Abandon changes button.
Where Used: Supplier status is used during the selection of suppliers for purchasing
«Mark as Completed in RoadMap in Section B Item 3-l»
|
1.19.1. Prerequisites for Purchase Setup |
Complete the attached worksheet and " Mark as Completed RoadMap Section B Item 4-m" before continuing the setup.
The prerequisites for entering Purchasing Setups are:
User MUST have full rights to the "System Setup" in System Security . Users with “Supervisor Rights” will automatically have access.
|
1.19.2. Introduction for Purchase Setup | In this section, the approval authority is established for purchase order approval for each user. The company has the option to declare whether one or two approvals are required in order for a purchase order to be approved. If the user chooses to have two approvals, then one of the approval-users must have final approval authority. The company also has the option to declare whether they want approvals Based on the PO Value and approvals when there is date changes or note changes.
This section also establishes a default percentage that is allowed over and above the purchase order line item quantity. If material is received that exceeds in quantity the ordered amount by this percentage, then the receiving department cannot receive the material until the order is modified by purchasing. This is a default percentage applied to each order as it is placed, but may be over-ridden at the time the order is created.
|
1.19.3. Fields & Definitions for Purchase Setup |
1.19.3.1. Purchase Order Default Tab |
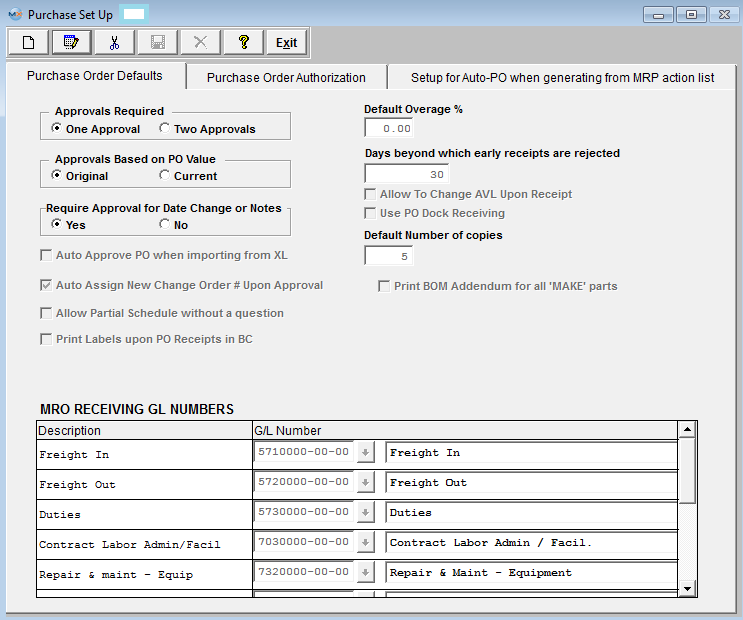
When a buyer generates a purchase order, it is created as a temporary order until it is approved. These orders will be created with a prefix to distinguish them as temporary until approved. As a temporary order, the document cannot be printed, nor will the order be considered as supply for Material Requirements Planning considerations. When a purchase order undergoes a revision, changing schedules, quantities and/or pricing, the order returns to a temporary status until approved. Note: These changed orders are not changed back to a prefix.
Approvals Required
|
The company has the option to declare whether one or two approvals are required in order for a purchase order to be approved. If the user chooses to have two approvals, then one of the approval-users must have final approval authority.
|
Approvals Based on P.O. Value
|
This will allow the PO to be approved based on the PO value |
Require Approval For Date Change or Notes
|
This gives the user the option to require approvals or not to require approvals when Date Changes or Note Changes are made. If "No" is checked user can edit the notes without going into edit mode on the PO record. NOTE: If "No" is checked any changes made to the notes will not be recorded in the "View Changes History" screen. (This includes PO Item Master Notes, PO Item Notes, PO Notes, and PO Footnotes). |
|
This is a default percentage applied to each order as it is placed, but may be over-ridden at the time the order is created. If material is received that exceeds in quantity the ordered amount by this percentage, then the receiving department cannot receive the material until the order is modified by purchasing.
|
Days beyond which early receipts are rejected
|
Enter the number of days allowed for early receipt (from the PO Scheduled Date) based on work days. This is a provision for the restriction for PO early receipt. The default for this field is 30 days. |
Allow to Change AVL Upon Receipt
|
This will allow the users within Purchase Order Receiving to change the AVL selection (based on the available AVL's that currently exist within Inventory Control for that part) upon accepting the parts into inventory. |
|
This will allow users to decide if they want to use the two-step receiving procedure (Dock Receiving & PO Receiving) or if left un-checked just the one step (PO Receiving Only) |
|
Enter in the number of copies you want the system to create per PO |
Auto Approve PO when Importing from XL
|
Default is un-checked. If the user checks this box the system will automatically approve all the POs uploaded. If this box is not checked then all the POs will be uploaded as "NEW" and users will be required to approve within the Purchase Order Management module. |
Auto Assign New Change Order # Upon Approval |
Default is un-checked. If un-checked when user makes changes the CO# will stay the same, the system will prompt the reminder, and user may manually assign a change order number if applicable. If checked, the reminder will not be issued and CO # field becomes not editable. When the user approves the change the Change Order number will be increased. NOTE: If auto assign the next change order will be referenced in the change history and the PO change order will not increase until approved. If not auto assigned then the change order will be referenced to what ever change order user enters.
|
Allow Partial Schedule without a question
|
Default is un-checked. If un-checked user will receive the popup warning them that they have not scheduled all the order qty and ask if they want to finish scheduling the order qty, upon saving a PO with only a partial schedule. If the box is checked the system will not ask any questions when saving a po with only partial schedule. |
Print Labels upon PO Receipts in BC
|
Default is un-checked. If checked it will default into the PO Bar Code Receiving Module and may be unchecked within the module if necessary. If checked the receiving label will be printed in the receipt using the PO Bar Code Receiving module.
|
Print BOM Addendum for all "MAKE" parts on the Selected PO |
Default is unchecked. If checked it will default into the PO Reports /PO Form Report Options. If this option is checked when the users add a Make/Buy part to a Suppliers PO, and checks this option the system will then print a "BOM Indented with AVL" report as an addendum to the PO form. Each BOM will be printed as a separate report and will reference PO and item on the PO. If the AVL on the approve vendor list for any of the items on the BOM happens to be checked as "disallow to buy" this AVL will not be included within the addendum to the PO. |
When a non-inventory item is being purchased, the user must indicate the General Ledger MRO receiving numbers, if Accounting is used.
|
1.19.3.2. Purchase Order Authorization |
For each user approval, the user may be authorized to approve one or both: Inventory and/or MRO. And each of these may have different levels of dollar amounts. If the administrator chooses to have one approval for orders, then there must be at least one person with approval for the expected dollar value of purchase orders. If two approvals are chosen, then there must be at least two people with approvals for the expected dollar vaule of purchase orders. The names of the users must have been entered in the Security Setup before entering in the Purchasing Setup, as they become available in the pull down listing for names.
Name |
User Name |
Initials |
User Initials |
Approval
Inventory |
Approved $ amount for User for an Inventory Part Purchased |
MRO |
Approved $ amount for User for an MRO Item Purchased |
|
1.19.3.3. Setup for Auto-PO when generating from MRP action List |
Last Purchase Price for a Supplier |
The last Purchased Price for the Supplier Selected in the Preferred Supplier field |
Quote Price |
Price from an Approved Quote in the Quotation & Estimating Module. |
Standard Material Price |
Standard Material Price listed in the Inventory Control Module. |
Last Purchase Price |
Last Purchased Price. |
Contract Price |
Price listed in the Contract Pricing Module. |
Target Price |
Target Price listed in the Inventory Control Module. |
Manual Entry |
Enter Price Manually |
|
1.19.4. How To ..... for Purchase Setup |
1.19.4.1. Setup the Purchase Setup Module |
Enter the SQLSYSSETTING.EXE (within the ManEx root directory)
This action will then prompt the user for a password
|
 |
The following screen will be displayed, enter the Material/Purchase Setup Module
|
|
The following screen will be displayed:
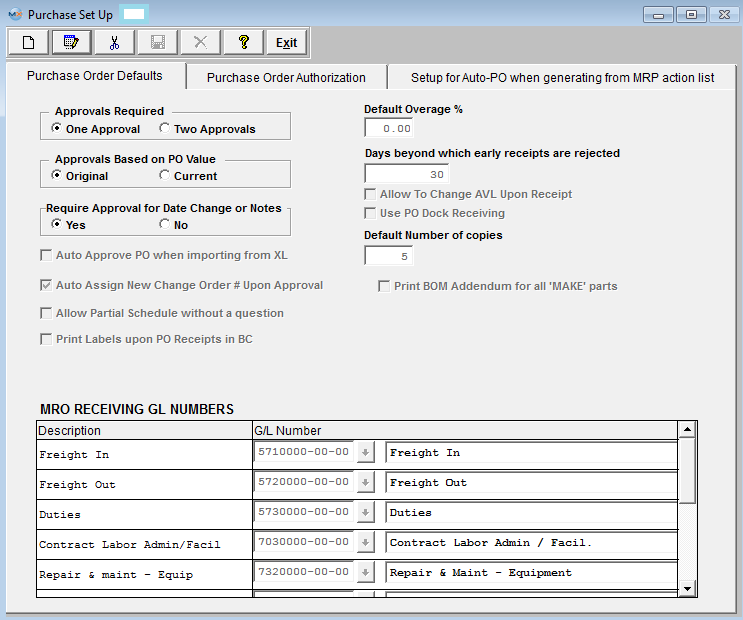
Depress the Edit button. For Approvals Required, click on the desired radial for either One Approval or Two Approvals. Enter Default Overage % if applicable. Click on desired radial for Approvals based on P.O. Value. Click on desired radial if Approvals are required for Date or Note Changes. Enter a Qty of Days beyond which early receipts are rejected if applicable. If you want to Change AVL Upon receipt this box must be checked. If you want to Use PO Dock Receiving this box must be checked. If you want to Auto Apporve PO's when importing from XL this box must be checked. If you want the system to Auto Assign New Change Order #'s upon Approval this box muxt be checked. If user wants to Allow partial schedule without receiving the reminder popup this box must be checked. If you want to Print labels upon PO receipts in the BC (Bar Code Receiving module) this box must be checked.
Depress the Add button to add additional MRO (Materials, Repairs and Other) Receiving GL Numbers, enter in the description, then select the appropriate General Ledger account number and description, by clicking on the down arrow next to the field, as follows:
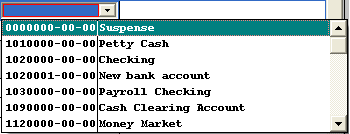
When finished, the user must depress the Save or Abandon changes button.
Purchase Order Authorization
On this screen, the user establishes the procurement authority levels for individuals.
To add a new user, click on the Add button and select a user from the Name pulldown field. Then enter the dollar amount authorized for either or both (Inventory and/or MRO) Approval and Final OK. If the company chooses only one approval, it must be in the Final column.
Each user may have different authority levels for different kinds of purchases. Additionally, the user may have different amounts authorized, depending on whether they are the first approval or the final approval. For example, a buyer may have authority to do a final approval for $1000, but must also approve P.O.s up to $10,000 before the person with final authority will authorize the P.O.
Setup for Auto-PO when generating from MRP action list
In order to create an automatic PO within the MRP action list, the system has to figure out unit cost. Within this screen the user can select multiple methods ordered by their preference, from selecting items on the left and entering them on the right. The system will try to find the price based on the first method in the selected list (on the right) and if the system cannot find any price information it will proceed with the next method (on the right) until price is found. If not found system will assign "Manual Entry" and leave it at zero as a default. The price source can be changed and the price can be overwritten in the screen which creates POs from the MRP action list.
Where Used: Approvals are required on all purchase orders in order to place and receive material. General Ledger Account selection for all MRO purchases.
«Mark as Completed in RoadMap in Section B Item 3-m»
|
1.19.5. ManEx Minute for Purchase Set-up |
1.20. First Article Disposition |
1.20.1. Prerequisites for First Article Disposition |
User MUST have full rights to the "System Setup" in System Security . Users with “Supervisor Rights” will automatically have access.
|
1.20.2. Introduction for First Article Disposition |
The First Article Disposition section is used to set up standard system instructions.
The information entered here will be used in the PO Receiving module for Inventory items that require First Article Inspections.
|
1.20.3. Fields & Definitions for First Article Disposition |
|
1.20.4. How To ..... for First Article Disposition |
1.20.4.1. Setup the First Article Disposition Module |
Enter the SQLSYSSETTING.EXE (within the ManEx root directory)
This action will then prompt the user for a password
|
 |
The following screen will be displayed, enter the Material/First Article Disposition Module
|
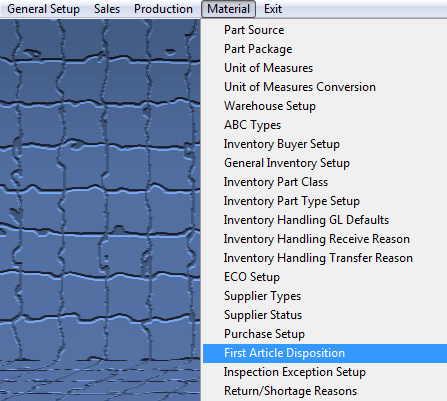 |
The following screen will be displayed:
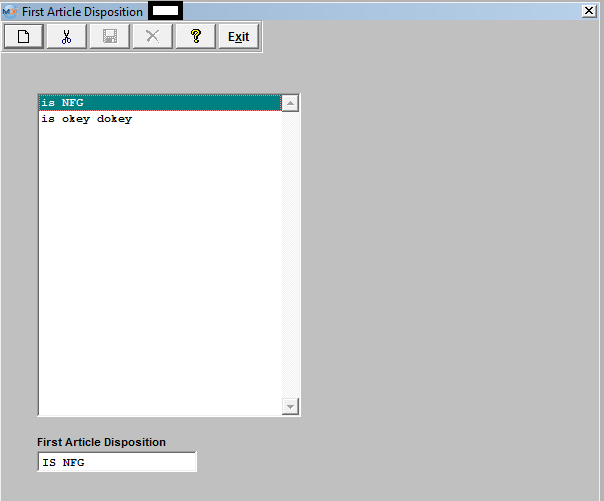
To add a new record, depress the Add button and type in description.
Depress the Save or Abandon changes button.
You may Edit or Delete existing records, also.
|
1.21. Inspection Exception Setup |
1.21.1. Prerequisites for Inspection Exception Setup |
User MUST have full rights to the "System Setup" in System Security . Users with “Supervisor Rights” will automatically have access.
|
1.21.2. Introduction for Inspection Exception Setup |
This screen is to enter Inspection Exception codes in order to save the user from a lot of repetitive data entry.
The information entered here will be used in the Purchase Order module for inventory items that require Inspection.
|
1.21.3. Fields & Definitions for Inspection Exception Setup |
|
1.21.4. How To ..... for Inspection Exception Setup |
1.21.4.1. Setup the Inspection Exception Setup Module |
Enter the SQLSYSSETTING.EXE (within the ManEx root directory)
This action will then prompt the user for a password
|
 |
The following screen will be displayed, enter the Material/Inspection Exception Setup Module
|
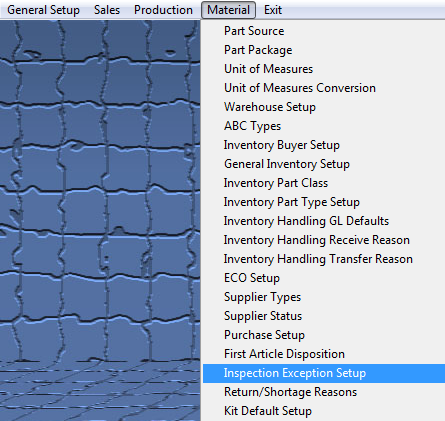 |
The following screen will be displayed:
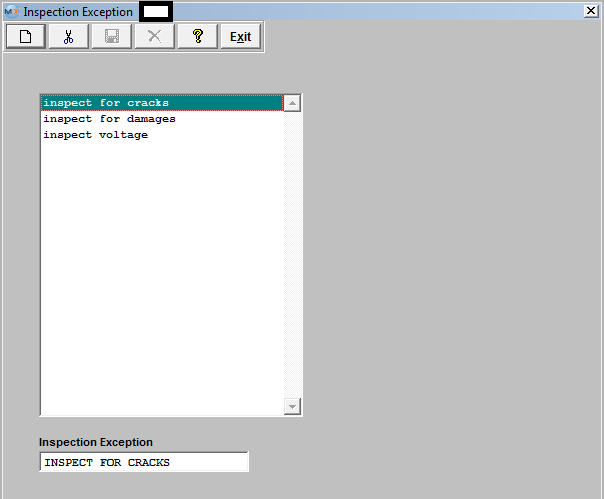
To add a new record, depress the Add button and type in description.
Depress the Save or Abandon changes button.
You may Edit or Delete existing records, also.
|
1.22. Return/Shortage Reasons | |
1.22.1. Prerequisites for Return/Shortage Reasons |
Complete the attached worksheet and "Mark as Completed RoadMap Section B Item 4-p" before continuing the setup.
User MUST have full rights to the "System Setup" in System Security . Users with “Supervisor Rights” will automatically have access.
|
1.22.2. Introduction for Return/Shortage Reasons | Throughout the operation, there will be instances where material has been rejected in the course of business. Examples of these places are Purchasing Receiving, Kit Preparation, Material Shortages, Shipping, etc. It is useful to have a common terminology to choose from, and avoid development of similar nomenclature that mean the same thing. To aid in focusing terms for reason codes, this setup area is established to be used whenever material is rejected. The available number of reasons for rejection is unlimited, but the user must have at least one entered in order to reject material in operations.
Examples of reject reasons might be: Damaged, Wrong Part, Early Delivery, Failed Spec, Failed Test, etc. The field length for a reason is 15 characters. |
1.22.3. Fields & Definitions for Return/Shortage Reasons |
Throughout the operation, there will be instances where material has been rejected in the course of business. Examples of these places are Purchasing Receiving, Kit Preparation, Material Shortages, Shipping, etc. It is useful to have a common terminology to choose from, and avoid development of similar nomenclature that mean the same thing. To aid in focusing terms for reason codes, this setup area is established to be used whenever material is rejected. The available number of reasons for rejection is unlimited, but the user must have at least one entered in order to reject material in operations.
Examples of reject reasons might be: Damaged, Wrong Part, Early Delivery, Failed Spec, Failed Test, etc. The field length for a reason is 15 characters.
|
1.22.4. How To ..... for Return/Shortage Reasons |
1.22.4.1. Setup the Return/Shortage Reasons |
Enter the SQLSYSSETTING.EXE (within the ManEx root directory)
This action will then prompt the user for a password
|
 |
The following screen will be displayed, enter the Material/Return/Shortage Reasons Module
|
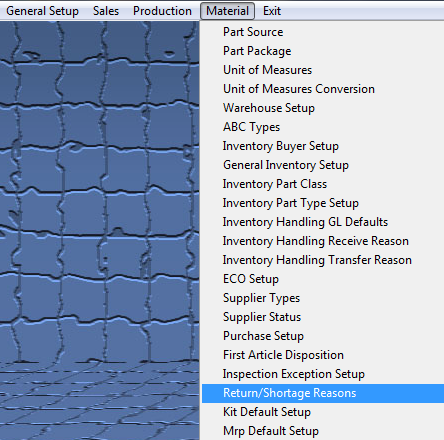 |
The following screen will be displayed:
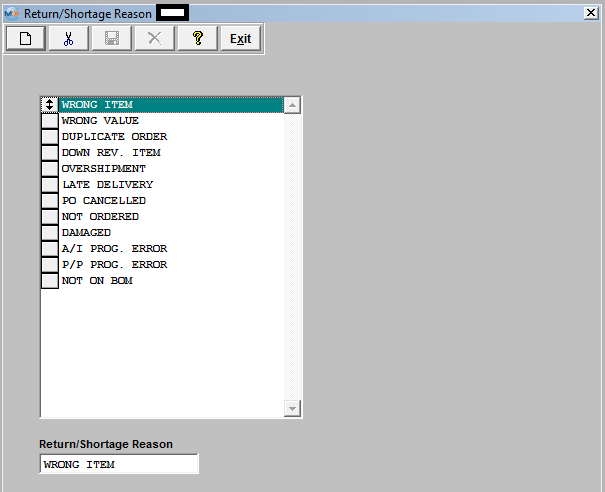
To Add a reason, depress on the Add button and enter the reason in the highlighted field.
To Delete a reason, highlight the reason you would like to delete, and depress the Delete button.
Once changes have been completed, depress the Save or Abandon changes button.
These items may be sorted in any order by clicking on and dragging the box on the left side, to the (vertical) position desired. This order will be the order displayed in the pull downs when using this list in other modules within the system. Suggestion: Have the one most used at the top of the list.
Where Used: Used by Purchase Receiving, Kit Preparation & Audit and Material Shortage Management.
«Mark as Completed in RoadMap in Section B Item 3-p»
|
1.23.1. Prerequisites for Kit Default Setup |
Complete the attached worksheet and "Mark as Completed RoadMap Section B Item 4-q" before continuing the setup
User MUST have full rights to the "System Setup" in System Security . Users with “Supervisor Rights” will automatically have access.
|
1.23.2. Introduction for Kit Default Setup |
This screen is designed for the user to select Kitting and Shortage defaults regarding the display of manufacturers, excluding Scrap from kitting, MRP or Cost Rollup, and to Allow use of non-nettable warehouse locations. The user can choose between showing all manufacturers or show only approved manufacturers, and allow use of non-nettable warehouse locations when working with the Kitting & Shortage Management module. Within this screen the user can also select the default to exclude scrap and scrap setup from any of the following three modules; kitting, MRP, and/or Cost Rollup.
|
1.23.3. Fields and Definitions for Kit Default Setup |
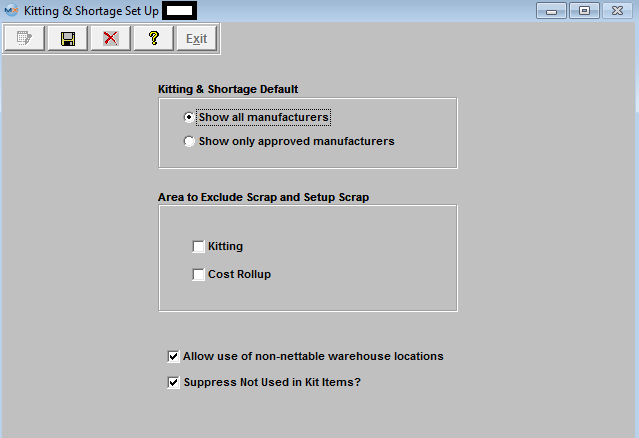
This screen is designed for the user to select Kitting and Shortage defaults regarding the display of manufacturers. The user can choose between showing all manufacturers or show only approved manufacturers when working with the Kitting & Shortage Management module.
If the "Show all Manufacturers" is selected the kitting module will display ALL AVL's and then indicate the approved ones with an "A" on the screen and will allow user to pick from the non-approved AVL's as well as the approved AVL's.
If the "Show only Approved Manufacturers" is selected the kitting module will ONLY display the approved AVL's and so users will only be able to pull parts from the Approved AVL's.
User can select the default to exclude scrap and scrap setup from any of the following three modules; Kitting, and/or Cost Rollup.
User can select the default to Suppress Not Used in Kit items - The following reports will take this default when printing: ICM Module Reports: Inv on hand report; Inv and WIP Valuation report; Unused INV list report. Kitting and Shortage Report: Kit pick work sheet.
|
1.23.4. How To ..... for Kit Default Setup |
1.23.4.1. Setup Kit Default Setup |
Enter the SQLSYSSETTING.EXE (within the ManEx root directory)
This action will then prompt the user for a password
|
 |
The following screen will be displayed, enter the Material/Kit Default Setup Module
|
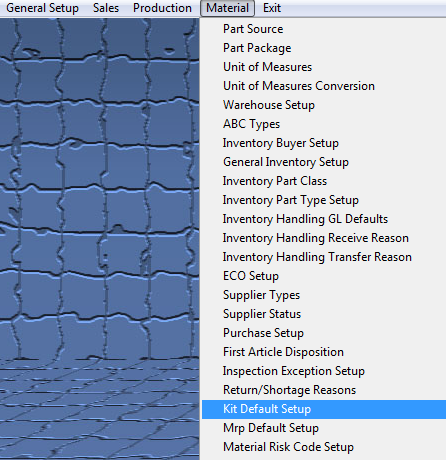 |
The following screen will be displayed:
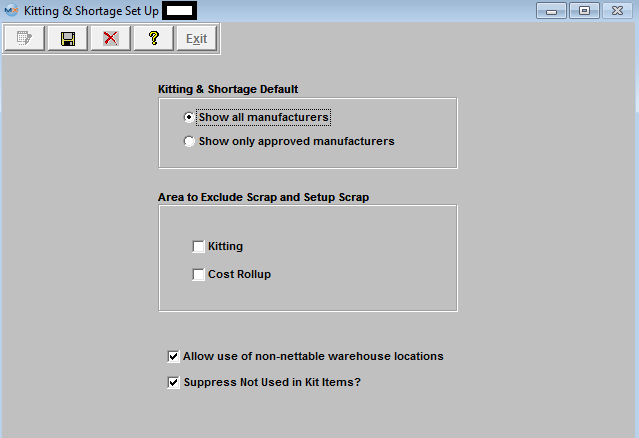
This screen is designed for the user to select Kitting and Shortage defaults regarding the display of manufacturers. The user can choose between showing all manufacturers or show only approved manufacturers when working with the Inventory Management Kitting & Shortage Management option.
If the "Show all Manufacturers" is selected the kitting module will display ALL AVL's and then indicate the approved ones with an "A" on the screen and will allow user to pick from the non-approved AVL's as well as the approved AVL's.
If the "Show only Approved Manufacturers" is selected the kitting module will ONLY display the approved AVL's and so users will only be able to pull parts from the Approved AVL's.
User can also select the default to exclude scrap and scrap setup from any of the following three modules; kitting, and/or Cost Rollup.
Depress the Edit key and then select your choice.
When finished making selections, depress the Save or Abandon changes button.
Where Used: The Kit Default Setup selection is used in the Kitting module.
«Mark as Completed in RoadMap in Section B Item 3-q»
|
1.24.1. Prerequisites for MRP Default Setup |
Complete the attached worksheet and "Mark as Completed RoadMap Section B Item 4-r" before continuing the setup.
User MUST have full rights to the "System Setup" in System Security . Users with “Supervisor Rights” will automatically have access.
Suggestion: We suggest that if the MRP takes a larger amount of time to run you may want to schedule it to run during non-working hours. If you run it during working hours and it takes a large amount of time, you might experience results that you are not expecting. Because, transactions could have been made in the system after the MRP was started and some data captured in the first part of the run may affect the transaction during the MRP run. The MRP time stamp does not get updated until the very end of the MRP run.
|
1.24.2. Introduction for MRP Default Setup | This screen is used to setup what the user wants to see when using MRP. |
1.24.3. Fields & Definitions for MRP Default Setup |
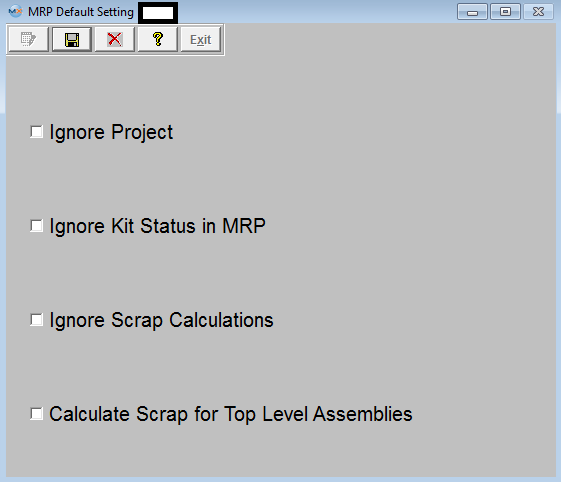
Ignore Projects in MRP |
If this box is checked MRP will Ignore Projects and take into consideration the MIN/MULT for this item.
If this box is unchecked MRP will Honor the Projects as long as the parts are on order Once the parts are received (unless they are kitted immediately) they are no longer allocated as far as MRP is concerned. MRP demands will NOT take into consideration the MIN/MULT for this item.
|
Ignore Kit Status in MRP |
If this box is checked MRP will Ignore Kit Status and instruct you to reschedule, change due dates (for Kits in Process the MRP will now ignore that it is in process and leave quantities as is. The system will only suggest to reschedule if the demand required date is earlier than the scheduled date). See the attachment below for an example (Kit Status_070606.doc).
If this box is unchecked MRP will Honor Kit Status and no longer instruct you to reschedule, change due date (for example: Kits in Process, MRP will no longer instruct the users to reschedule or change due dates) See the attachment below for an example (Kit Status_070606.doc)
|
Ignore Scrap Calculations |
If this box is checked MRP will NOT Calculate Scrap in MRP.
If this box is unchecked MRP will calculate scrap. Note: If this field is changed it will update the setting in the Kit Default Setup and visa versa.
|
Calculate Scrap for Top Level Assemblies |
If the Top Level Assembly has a run scrap and user would like MRP to calculate this run scrap in the demands for all parts on the BOM, they must check this box.
If the Top Level Assembly has a run scrap but user does NOT want MRP to calculate this run scrap in the demands then they must uncheck this box.
|
|
1.24.4. How To ..... for MRP Default Setup |
1.24.4.1. Setup the MRP Default Setup Module |
Enter the SQLSYSSETTING.EXE (within the ManEx root directory)
This action will then prompt the user for a password
|
 |
The following screen will be displayed, enter the Material/MRP Default Setup Module
|
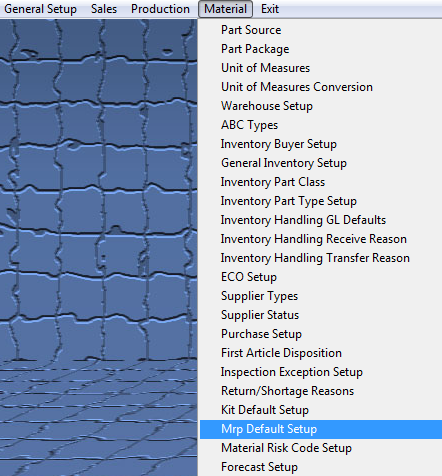 |
The following screen will be displayed:
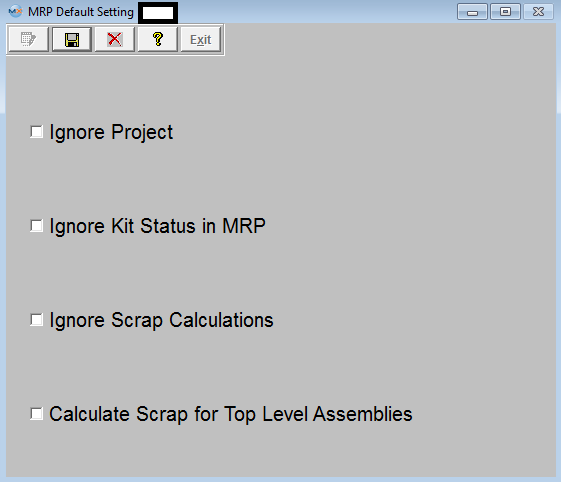
Depress the Edit button, make your choice(s). Depress the Save or Abandon changes button.
When editing the MRP Scrap Setting the following warning will appear:
|
1.25. Material Risk Code Setup |
1.25.1. Prerequisites for Material Risk Code Setup |
User MUST have full rights to the "System Setup" in System Security . Users with “Supervisor Rights” will automatically have access.
|
1.25.2. Introduction for Material Risk Code Setup | This is to inform the users which items are Low Risk or High Risk (can not be cancelled or returned).
|
1.25.3. Fields & Definitions for Material Risk Code Setup |
This is to inform the users which items are Low Risk or High Risk (can not be cancelled or returned).
|
1.25.4. How To ..... for Material Risk Code Setup |
1.25.4.1. Setup the Material Risk Code Setup Module |
Enter the SQLSYSSETTING.EXE (within the ManEx root directory)
This action will then prompt the user for a password
|
 |
The following screen will be displayed, enter the Material/Material Risk Code Setup Module
|
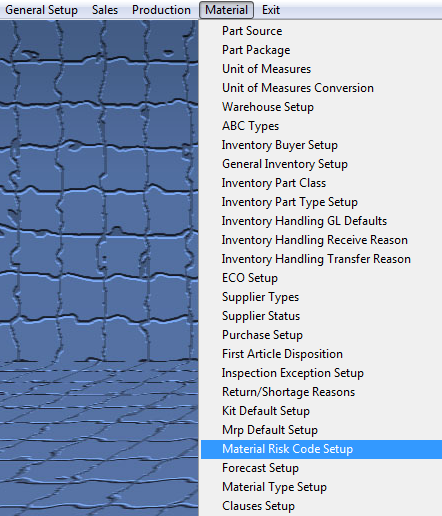 |
The following screen will be displayed:
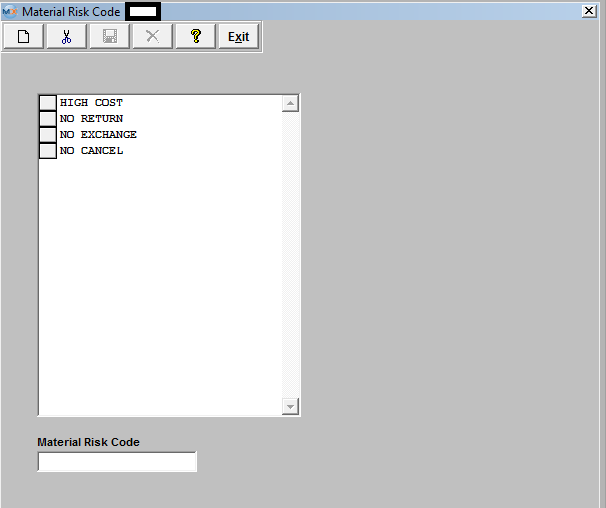
To add a new record, depress the Add button and type in a code. This is to inform the users which items are Low Risk or High Risk (can not be cancelled or returned).
Depress the Save or Abandon changes button.
You may Delete existing records, also.
|
1.26. Material Type Setup |
1.26.1. Prerequisites for Material Type Setup |
Complete the attached worksheet and " Mark as Completed RoadMap Section B Item 4-u" before continuing the setup.
User MUST have full rights to the "System Setup" in System Security . Users with “Supervisor Rights” will automatically have access.
|
1.26.2. Introduction for Material Type Setup |
The User may establish the logic by which the material type for the parts are established by the material types at the AVL level. User may also reorder the Material Type per proirity.
|
1.26.3. Fields & Definitions for Material Type Setup |
1.26.3.1. Material Type Mgmt | 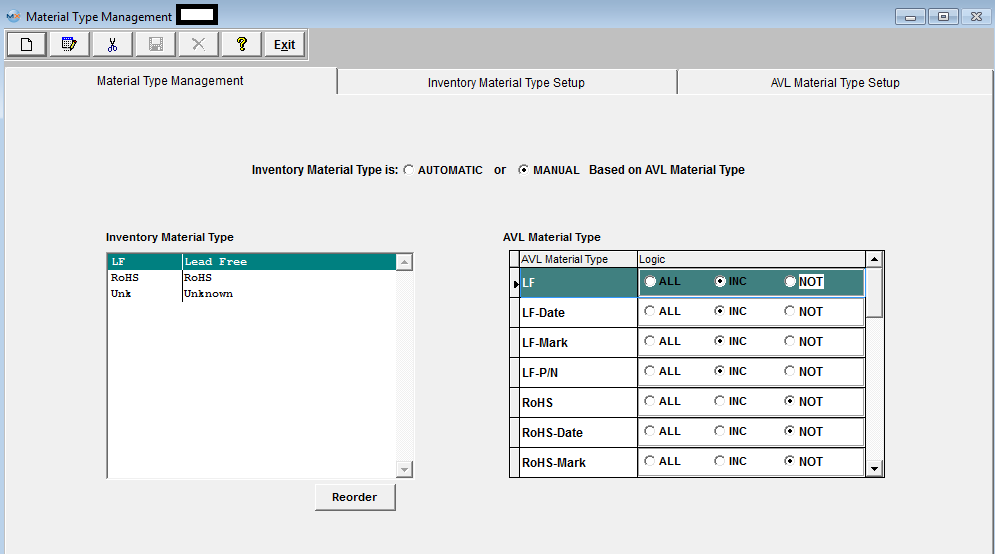

This allows the users to decide if they would like the inventory part material type controlled automatically or manually. If the user chooses MANUAL, each time an AVL is added, edited or deleted, the user would receive a popup reminder that "The Inventory level Material Type is set to Manual. Be sure to verify how changes affect the Inventory Material Type". If the user chooses AUTOMATIC then each time an AVL is added, edited or deleted, a popup will be displayed (if the the AVL material type is DIFFERENT than the inventory type) that says "AVL Material Type is different than Inventory Material Type and may affect the Inventory Material Type", with an option to proceed or cancel. If proceeding, then the system recalculates the material type on saving the edit.
Inventory Material Type
|
Material Type at the Inventory Level
|
AVL Material Type
|
Material Type at the AVL Level
|
Logic
|
There are two grids in the Material Type Management screen. The left side displays the different INVENTORY Material Types that the user has established in the Inventory Material Type setup screen. When one of these Material Types (MT) is selected, the grid on the right side of the page displays all available AVL Material Types that the user has established in the AVL Material Type Setup screen. For each INVENTORY MT, the user can select each of the AVL MT, and how they affect the INVENTORY MT. The choices to affect the INVENTORY MT selected are ALL, INC, and NOT: If ALL is selected, then every one of the AVL's available for that Inventory part must have the same MT. (There can only be one ALL selected). If INC is selected, then if any of the AVLs with that designations are included, then the INVENTORY MT will be assigned accordingly. IF ANY of the AVL's for an Inventory part contain a designation in the NOT category, then the inventory designation will become "UNK". For more MT Logic Setup Examples see attached document.
|

|
Depressing this button will allow the user to sort the Inventory Material Type in order of priorty in which the logic is checked.
|
|
1.26.3.2. Inventory Material Type Setup Fields and Definitions |
Inventory Material Type
|
Inventory Material Type Code. LF (Lead-Free), RoHS (the restriction of the use of certain hazardous substances in electrical and electronic equipment) or (In general, RoHS requirements include limitations on other heavy metals in addition to being lead free. But many companies may not meet the full requirements of RoHS, but still want to identify the material as Lead Free), and Unk (Unknown) are the Inventory Material Types that are hard-coded into the system. For further information on RoHS go to http://www.rohs.gov.uk/Default.aspx.
|
Inventory Material Type Description
|
Inventory Material Type Complete Description.
|
|
1.26.3.3. AVL Material Type Setup Fields and Definitions |
AVL Material Type
|
AVL Material Type Code. LF, LF-Date, LF-Mark, LF-P/N, RoHS, RoHS-Date, RoHS-Mark, RoHS-P/N, and Unk are the AVL Material types that are hard-coded into the system.
LF (Lead-Free), RoHS (the restriction of the use of certain hazardous substances in electrical and electronic equipment) or (In general, RoHS requirements include limitations on other heavy metals in addition to being lead free. But many companies may not meet the full requirements of RoHS, but still want to identify the material as Lead Free(, and Unk (Unknown) are the Inventory Material Types that are hard-coded into the system. Then sometimes the user wishes to identify a date code, marking or part number which designates that the part has switched from unknown to LF or RoHS, and that is what the additional modifier is for.
|
AVL Material Type Description
|
AVL Material Type Complete Description
|
|
1.26.4. How To ..... for Material Type Setup |
1.26.4.1. Edit the Material Type Logic |
Enter the SQLSYSSETTING.EXE (within the ManEx root directory)
This action will then prompt the user for a password
|
 |
The following screen will be displayed, enter the Material/Material Type Setup Module
|
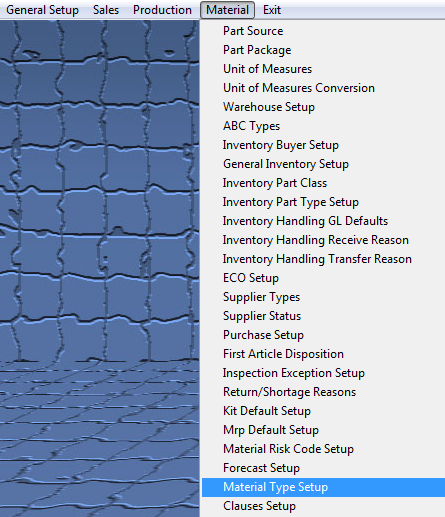 |
The following screen will be displayed:
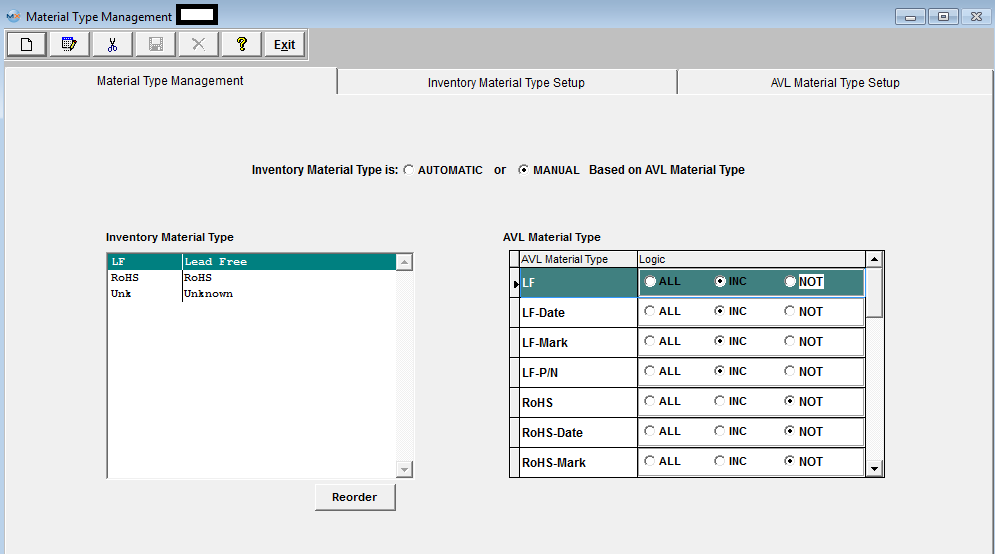
Depress the Edit action button.
This will allow you to change the Inventory Material Type to "Automatic" or "Manual" Based on AVL Material Type.
If the user chooses the MANUAL option, there will be a pull down next to the Material Type field at the top of the Quantity Info screen within the Inventory Control Mgmt module, listing all the Inventory Material Types available:
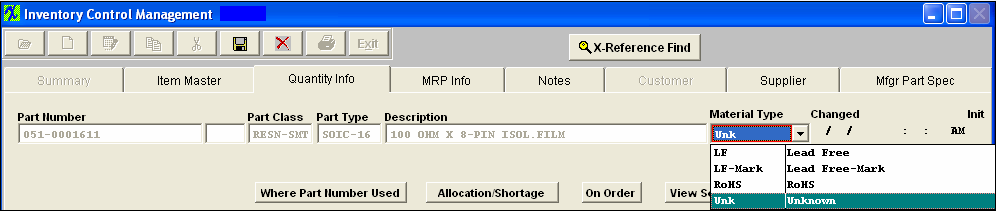
User may highlight the Material Type they wish to be assigned to this Inventory part regardless of the material types of the AVLs. Each time an AVL is added, edited or deleted, the user will receive the following popup reminder:

If the user chooses the AUTOMATIC option user must also setup the Logic by clicking on the Radial next to "ALL" "INC" or "NOT". Reminder: Make sure you do not setup duplicate logics for different material types.
There are two grids in the Material Type Management screen. The left side displays the different INVENTORY Material Types that the user has established in the Inventory Material Type setup screen. When one of these Material Types (MT) is selected, the grid on the right side of the page displays all available AVL Material Types that the user has established in the AVL Material Type Setup screen. For each INVENTORY MT, the user can select each of the AVL MT, and how they affect the INVENTORY MT. The choices to affect the INVENTORY MT selected are ALL, INC, and NOT: If ALL is selected, then every one of the AVL's available for that Inventory part must have the same MT. (There can only be one ALL selected). If INC is selected, then if any of the AVLs with that designations are included, then the INVENTORY MT will be assigned accordingly. IF ANY of the AVL's for an Inventory part contain a designation in the NOT category, then the inventory designation will become "UNK". For more MT Logic Setup Examples see attached document.
If the AVL material type is automatic, and you edit the Logic setup the following message will be displayed:
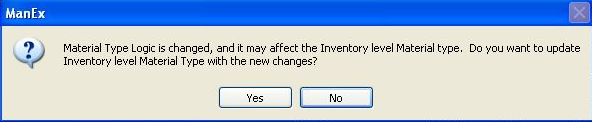
EXAMPLE:
Setup Logic for a new Inventory MT (Mixed). Go to the AVL Material Types; Check - LF-Date and RoHS-Date as INC, Check - all other AVL MT as NOT (For more MT Logic Setup Examples see attached document)
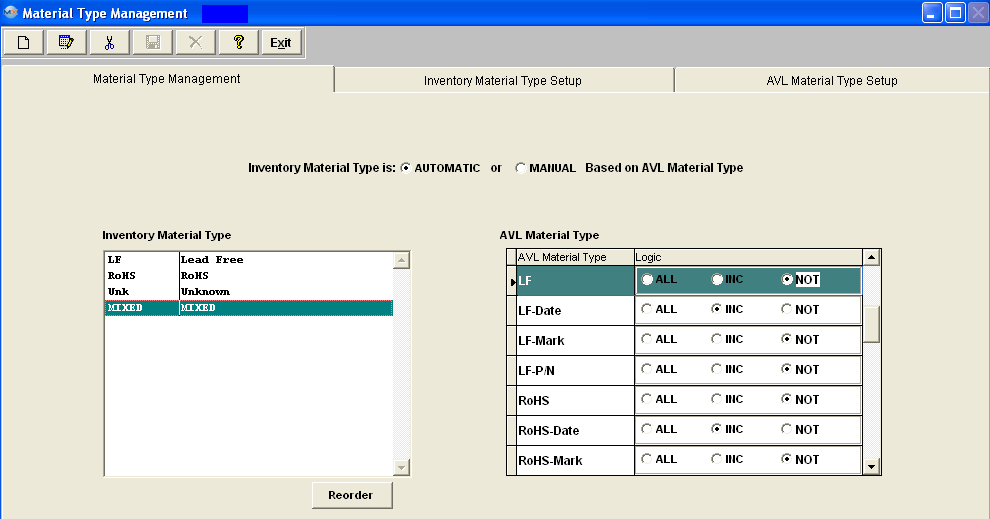
Find an existing Inventory Part # 101-0001621 with different AVL MT and Inventory MT as UNK
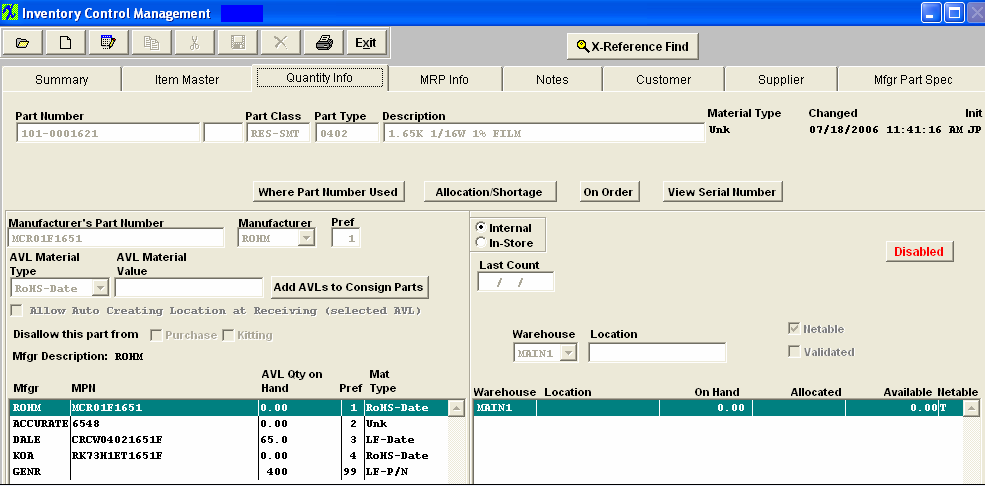
Edit record and change all AVL MT to either LF-Date or RoHS-Date and the Inventory MT will update to Mixed per the Mixed Logic in System Setup (Shown above)
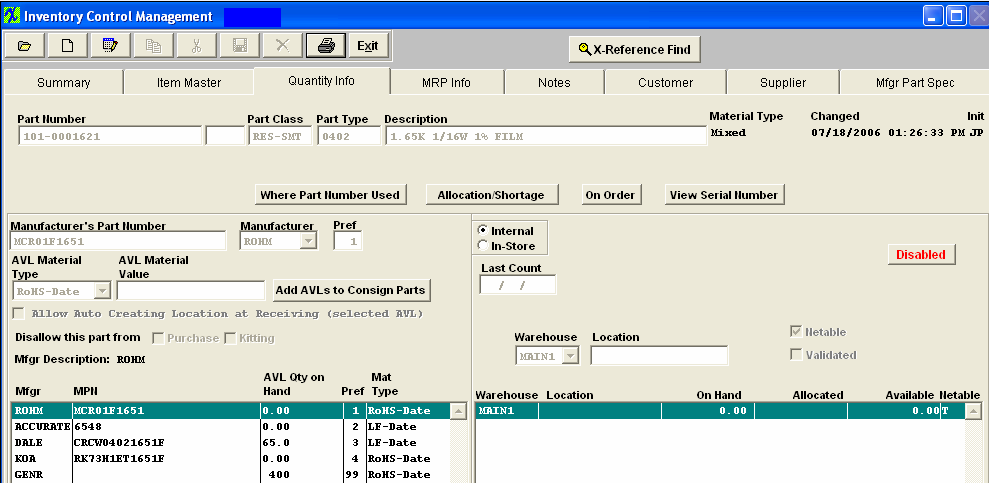
OR User can leave all AVL MT as is, go to System Setup and Edit the Inventory MT - MIXED Logic to include UNK and LF-P/N, update records.
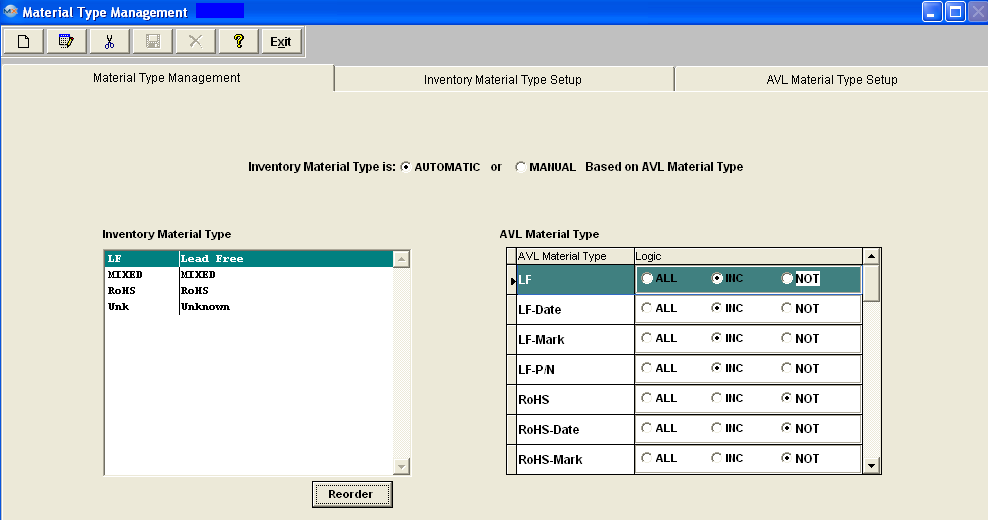
and Inventory MT will update automatically, with existing AVL MT's
User may also sort the Inventory Material Type in order of priority in which the logic is checked. By depressing the Reorder button as shown in the screen below;
Re-order by using the arrows on the left side of the Inventory Material Types
Depress the Done button when re-order is complete.
If Inventory Material Type is set to Automatic user will receive the following message:
If Inventory Material Type is set to Manual user will receive the following message:
|
1.26.4.2. Add or Edit an Inventory and/or AVL Material Type |
Enter the SQLSYSSETTING.EXE (within the ManEx root directory)
This action will then prompt the user for a password
|

|
The following screen will be displayed, enter the Material/Material Type Setup Module
|
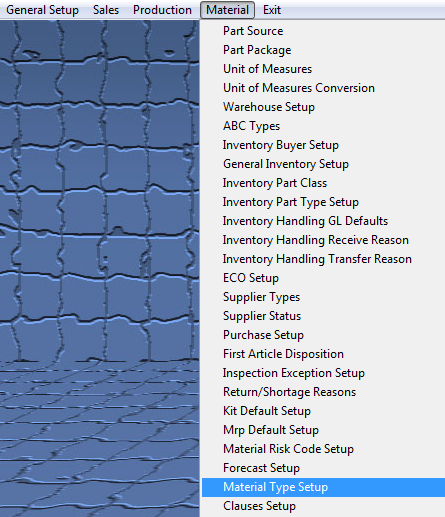 |
The following screen will be displayed:
Go to the "Inventory Material Type Setup" tab. The Inventory Material Types displayed on screen are hard-coded into the system and cannot be removed.
Select the Add button from the main tool bar to add a new Inventory Material type or select the Edit button for the main tool bar to edit an Inventory Material Type, then depress the Save record action button to save changes or depress the Abandon changes action button to abandon changes.
If Inventory Material Type is set to Automatic user will receive the following message:
If Inventory Material Type is set to Manual user will receive the following message:
Go to the "AVL Material Type Setup" tab. The AVL Material Types displayed on screen are hard-coded into the system and cannot be removed.
Select the "Add" button from the main tool bar to add a new AVL Material type or select the "Edit" button for the main tool bar to edit an AVL Material Type, then depress the Save record action button to save changes or depress the Abandon changes action button to abandon changes.
If Inventory Material Type is set to Automatic user will receive the following message:
If Inventory Material Type is set to Manual user will receive the following message:
|
1.26.4.3. Delete a Inventory and/or AVL Material Type |
Enter the SQLSYSSETTING.EXE (within the ManEx root directory)
This action will then prompt the user for a password
|
 |
The following screen will be displayed, enter the Material/Material Type Setup Module
|
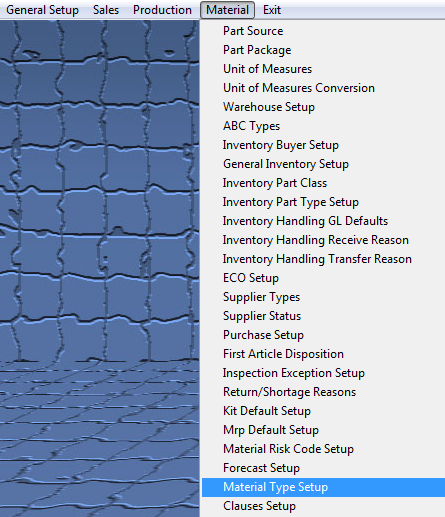 |
The following screen will be displayed:
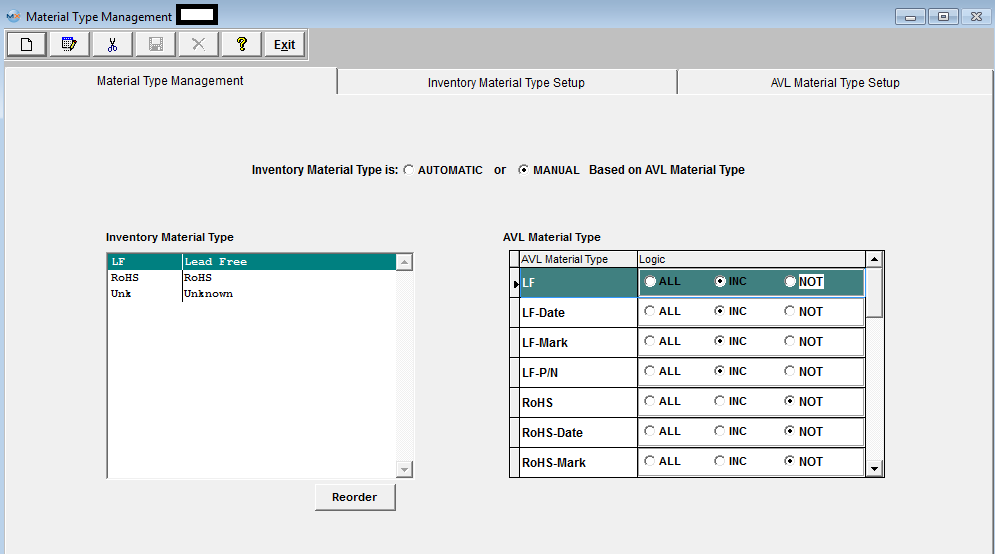
Go to either the "Inventory Material Type Setup" tab or the "AVL Material Type Setup" tab
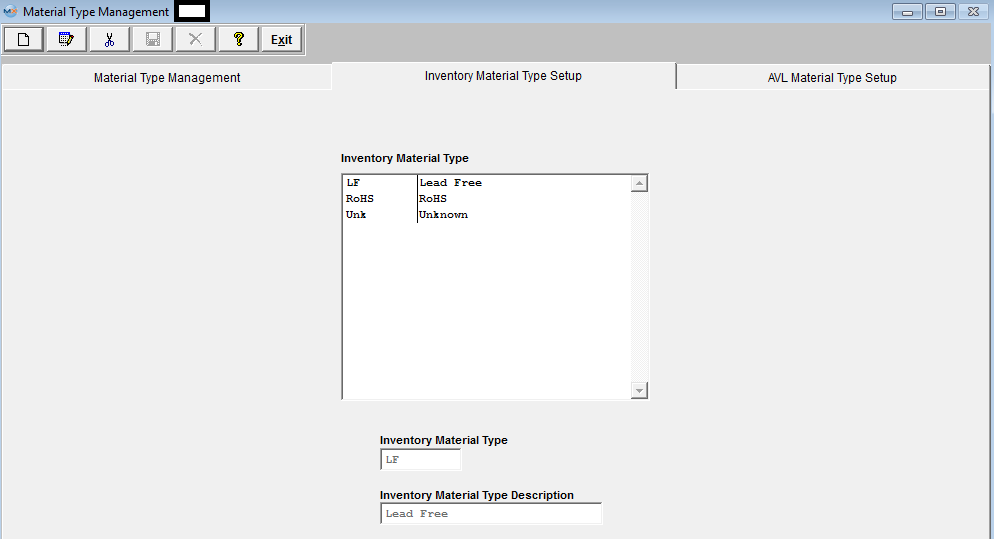
Highlight the Material Type you want to Delete, and select the Delete button from the main tool bar. A popup will appear verifying the Material Type you are deleting and giving you the option to continue with the Deletion or not:
Depress Yes to continue or No to abandon changes.
|
1.27.1. Prerequisites for Clauses Setup |
User MUST have full rights to the "System Setup" in System Security . Users with “Supervisor Rights” will automatically have access.
|
1.27.2. Introduction for Clauses Setup | This setup screen will allow you to enter Template Clauses that can be applied to Inventory parts, Purchase Orders and/or Items on the PO.
|
1.27.3. Fields & Definitions for Clauses Setup |
|
1.27.4. How To ..... for Clauses Setup |
1.27.4.1. Setup the Clauses Setup Module |
Enter the SQLSYSSETTING.EXE (within the ManEx root directory)
This action will then prompt the user for a password
|
 |
The following screen will be displayed, enter the Material/Clauses Setup Module
This setup screen will allow you to enter Templates Clauses that can be applied to Inventory Parts, Purchase Orders and/or Items on the PO.
|
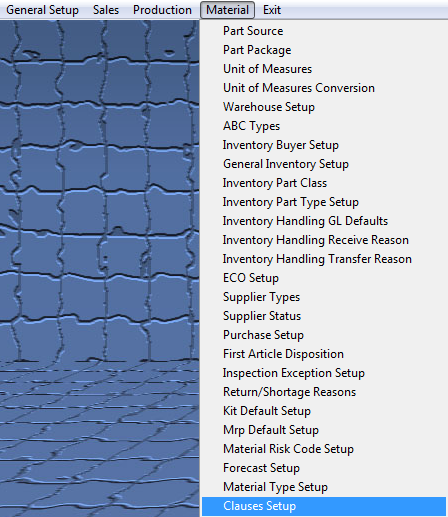 |
The following screen will be displayed:
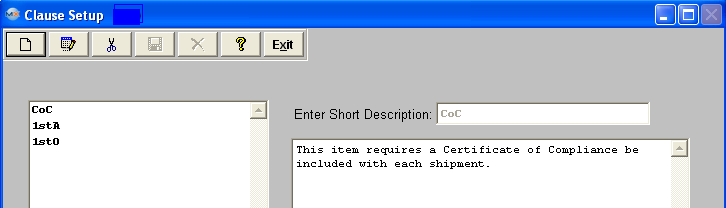
To add a new record, select the ADD button from the main tool bar and enter description/clause.
To edit a record, highlight the record and select the EDIT button from the main tool bar and edit the record.
Depress the SAVE or ABANDON changes button from the main tool bar.
To delete a record, highlight the record and select the DELETE button from the main tool bar.
|
|