Enter the SQLSYSSETTING.EXE (within the ManEx root directory)
This action will then prompt the user for a password
|
 |
The following screen will be displayed, enter the Production/Production Scheduling Method Module
|
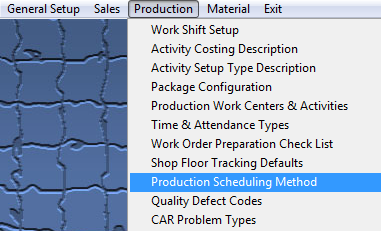 |
The following screen will be displayed:
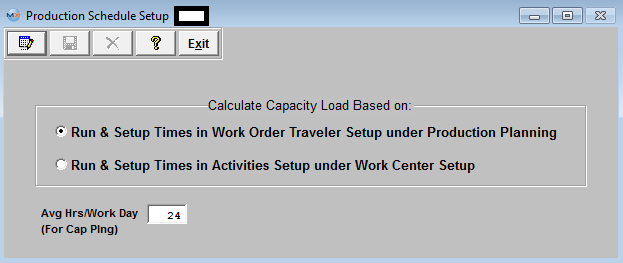
The user may select the Edit button from the main tool bar to change the defaults.
The user must select the Save or Abandon changes button from the main tool bar after entering the Edit Mode.
Where Used: In all shop floor functions defining labor costs, and for Capacity Planning Modules.
«Mark as Completed in RoadMap in Section B Item 3-g»
|