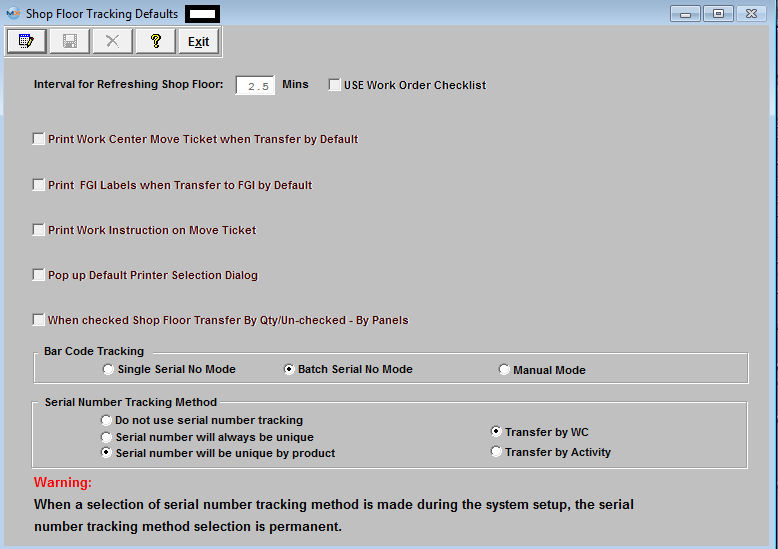
When the user is in the Shop Floor module, and has information displayed on the screen (for example, the wip status of a work order). The user then leaves the screen up and alone to do another task (say breaks for lunch). Then the data represented by the screen may actually undergo changes by other employees. If the user does not use the screen in the meantime, when they return from their alternate task, the information on the screen would be incorrect (because someone else moved material). ManEx performs a periodic update (refresh) to Shop Floor screens when the user has information displayed on the screen, but has not performed any functions in the meantime. The period of the refresh rate is initially set to every two and a half minutes by ManEx. So, if the user has a work order tracking screen displayed with a work order showing wip, and does not perform any transaction for 2-1/2 minutes, ManEx will automatically update the information on the screen. This timing is initially set at 2-1/2 minutes, but the user may change this period in this setup. However, the trade-off for shorter periods is increased network traffic, and setting too many workstations to be refreshed every few seconds will seriously impact the server’s ability to deliver data.
|