1. Production Work Center & Activity Setup | |
1.1. Prerequisites for Production Work Centers & Activities | Work Center Work Shift must be established if you intend to identify a shift number and description to a work center. Activity Costing & Volume Type setup must be established if the user plans to identify Activity Costs and/or volume types with activities. Setup type description must be set up in the Activity Costing & Volume Type Setup. Component package configuration must be set up in Package Configuration.
Complete the attached worksheet and " Mark as Completed RoadMap Section B Item 3-d" before continuing the setup.
User MUST have full rights to the "System Setup" in System Security to setup these modules. User with "Supervisor Rights" will automatically have access.
|
1.2. Introduction for Production Work Centers & Activities | Production Work center activities are optional sub-sets of work center departments. Activities may be defined prior to establishing work centers, and then used as more detailed actions within a work center. Each of these activities may be assigned a separate hourly charge rate.
Please note: As of 03/03/2016:
We are actually in the process of implementing optional routing steps in place of activities. We are working to simplify and flatten the process to make it easier for everyone.
Presently, you can still choose to setup activities if desired and then decide if you want to track production through activities or not. With the current activity setup this decision is universally applied for all work centers and work orders.
With the optional routing steps that we are implementing, you would still have to decide if you want to add activities or not (optional steps), but now you would be able to decide on the fly if you want to track production through those steps. It also means that you would have fewer places to maintain in setup. |
1.3. Fields & Definitions for Production Work Centers & Activities | |
1.3.1. Work Center Tab |
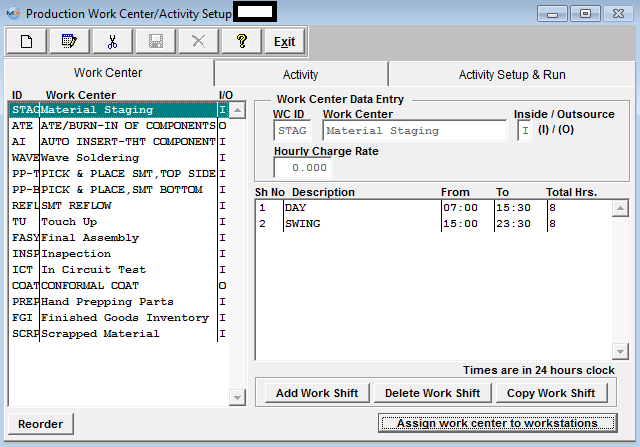
Work Center ID
|
This is the abbreviated (4 character) code for the name of the work center |
Work Center
|
This is the description of the work center. It may be 25 characters in length. Work Centers are used to calculate Values within Job Costing.
|
Inside / Outsource
|
Choose (I) inside or (O) outsource for site of activity.
|
Hourly Charge Rate
|
This is the standard hourly rate for the Work Center highlighted.
|
Shift Number |
This is the number of the shift assigned to the highlighted work center.
|
Shift Description
|
This is the description of the shift assigned to the highlighted work center. |
From |
Shift Start Time |
To |
Shift End Time |
Total Hours |
Total Hours of Shift |
Assign work center to workstations (button)
If a customer wants to install workstations along the production line, with scanners to read serial numbers as they passed down the line, this button provides the ability to limit a work station (specific computer) to be able to only transfer material “FROM” a certain Work Center. So, when a user first opens the "SFT by WO" or "Shop Floor Tracking by Bar Code" module, the module will use the default work center assigned for this workstation, but if user chooses to use a different work center, supervisor approval or a user that has the option "Allow Changing Default Work Center for Serial Number Transfer" box checked within the Security module is required to continue. After a supervisor's or user with this option’s password is entered, the default work center will be changed to the one that the supervisor entered password for. For Example: the workstation is assigned to use “TU” as default work center, now if user chooses to use “AI” to transfer, the system will ask for supervisor’s password, if user cancels the password, the default work center will still be “TU”, but if the supervisor enters his/her password on this machine, the default work center will be changed to “AI”. If now the user tried to transfer from “TU” again, the system will ask for supervisor’s password again. If user exits the module and come back, the default work center will be “TU” again.
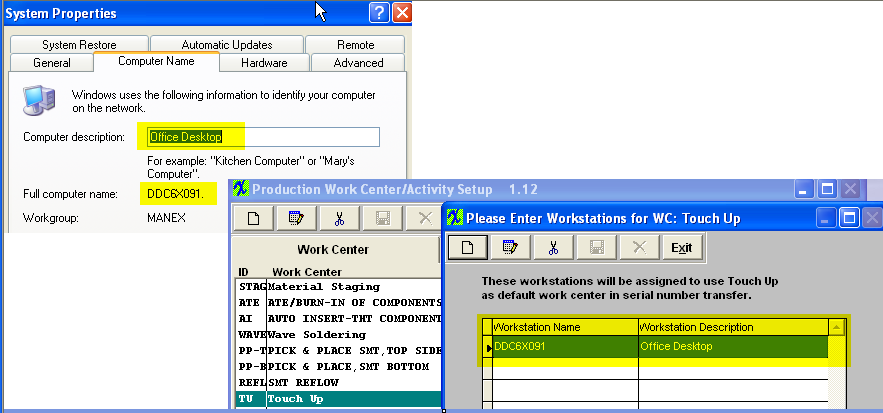
Defect Code Entry In-Line Mode, the system will check to see if the serial number is currently in the Work Center which was set up here. If not, a special supervisor’s password is required to transfer the serial number FROM a different Work Center. After the supervisor password is entered, the system will use the new Work Center to be the default FROM Work Center until the user closes the screen. The next time the user opens the screen, the default FROM Work Center will be changed back to the one defined in Systems Setup. |
1.3.2. Activity Tab |
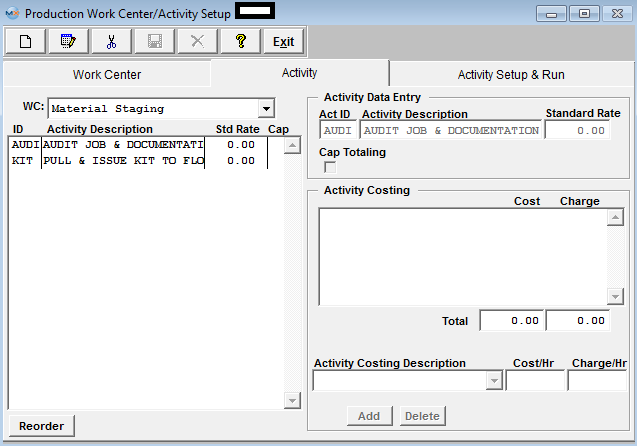
WC
|
This is the description of the work center highlighted in the Work Center tab.
|
Activity ID
|
This is the abbreviated (4 character) code for the name of the activity.
|
Activity Description
|
This is the description of the activity being performed.It may take 25 characters in length.
|
Standard Rate
|
This is the standard hourly rate for the activity performed within the Work Center.
|
Cap
|
Click here for capacity totaling election.Capacity totaling means that if multiple activities are used in a work center, and if there are multiple resources in the activities, the capacity will be the sum of the resources rather than limited by just one resource.
|
Activity Costing Description
|
This field is selected from the available activity costing descriptions created in the Activity Costing & Setup module within system setup.
|
Charge Rate |
This is the field used to enter hourly charge rates, for each activity. The formatting is three digits to the left of the decimal, and two to the right (999.99). If this optional field is entered, it will be used to determine the hourly charge rate of the activity to which it is assigned.
|
|
1.3.3. Activity Setup & Run Tab |
Setup Type List
The Setup Type description is input into a previous screen “Activity Costing & Setup Type Setup/Activity Setup Type Description”.
Setup Type Description |
This is the description of the setup type.
|
Time
|
This is the time in hours and minutes associated with the setup type.
|
Setup Instruction (button)
|
This button allows the user to enter instructions for setting up the Setup Type and applicable pictures.
|
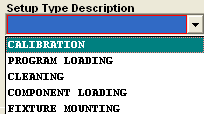
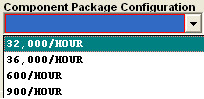
Component Package Configuration List
The Component Package Configuration is set up in a prior screen. See Setup Package Configuration.
Component Package Configuration
|
For a given machine’s Parts Per Unit, this field identifies the user defined configuration.
|
Volume/Hour
|
This is the volume type per hour. |
Yield Factor
|
This is the yield percentage.
|
Using Run and Setup Times in the Production Schedule Setup module is preferred when there is great variability in the products produced and the setup and run rates in each Work Center.
Using the Run and Setup Times in System Setup under this module, Work Center Setup, is preferred when the product flow is uniform, the machine rates are well established and the setup times very uniform regardless of product.
Use of Run and Setup Times in the Production Schedule Setup module is optional unless either Job Costing or Capacity Planning Modules are in use.
|
1.4. How To ..... for Production Work Centers & Activities |
1.4.1. Setup the Production Work Centers & Activities |
Enter the SQLSYSSETTING.EXE (within the ManEx root directory)
This action will then prompt the user for a password |
 |
The following screen will be displayed, enter the Production/Production Work Centers & Activities
|
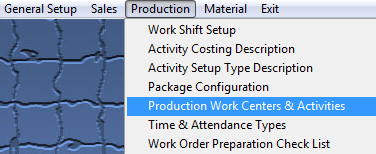 |
The following screen will be displayed:
For the highlighted Work Center, enter in the Hourly Charge Rate.
|
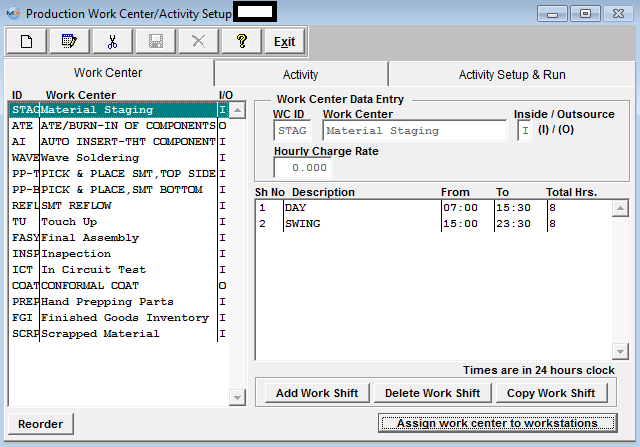 |
To add a Work Shift, highlight the Work Center, then depress the "Add Work Shift" button. The following popup screen will appear to select from. The work shifts listed on the popup screen have been setup in the Work Shift Setup module.
Highlight the work shift(s) and depress the "OK" button.
|
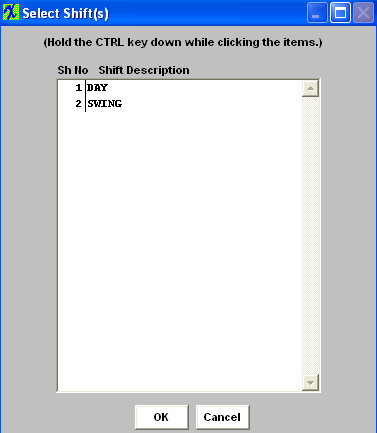 |
To Assign Work Center to Workstations In this screen, highlight the name of the Work Center. Depress the button at the bottom of the screen "Assign work center to workstations", the following assignment screen appears:
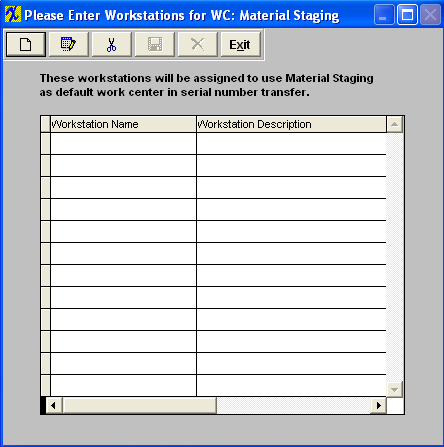
To enter a new assignment, depress the Add button. When setting up a workstation user must enter the Full computer name in the Workstation Name field and the Computer description in the Workstation Description field. See Example below.
Depress the Activity tab.
The user may add Work Center Activities by selecting the Add button from the main tool bar.
|
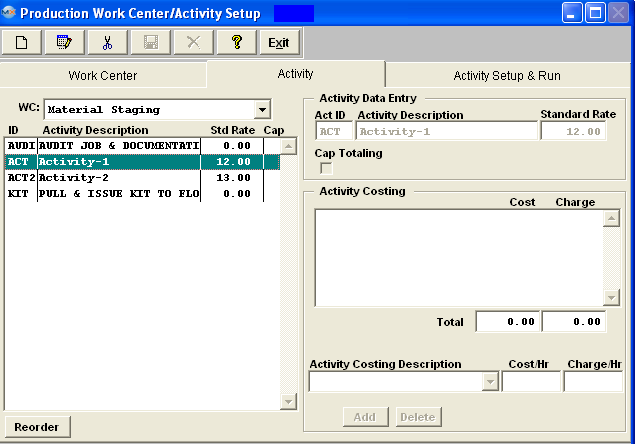 |
To add an activity ID and related description, choose the applicable work center from the drop down menu: |
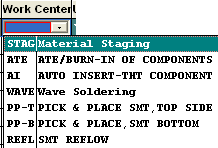 |
Enter the Act ID, Activity Description.
Click on the Cap Totaling box to elect calculating capacity.
Save changes or Abandon Changes.
|
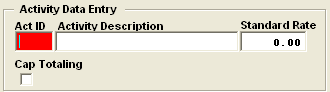 |
To attach a Cost Rate to an activity, click on the Edit button, then on the Add button (bottom of screen) in the Activity Costing Section.
|
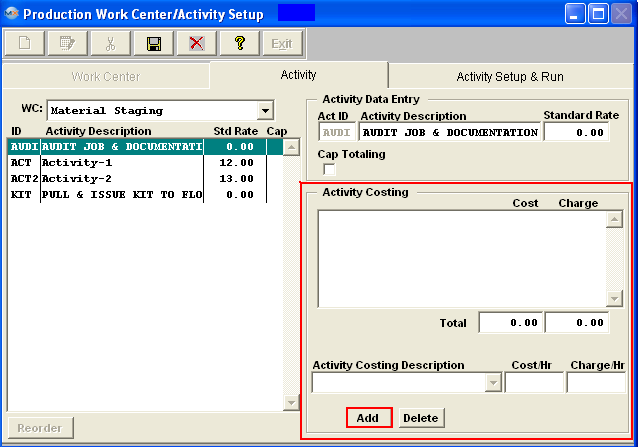 |
Enter in the Cost/hr and the Charnge/Hr.
|
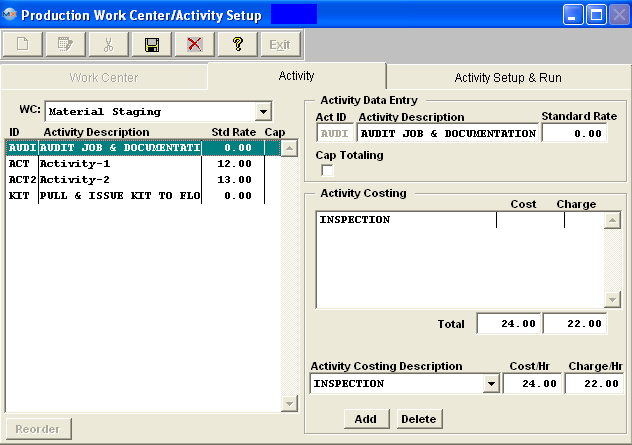 |
Save changes or Abandon Changes.
|
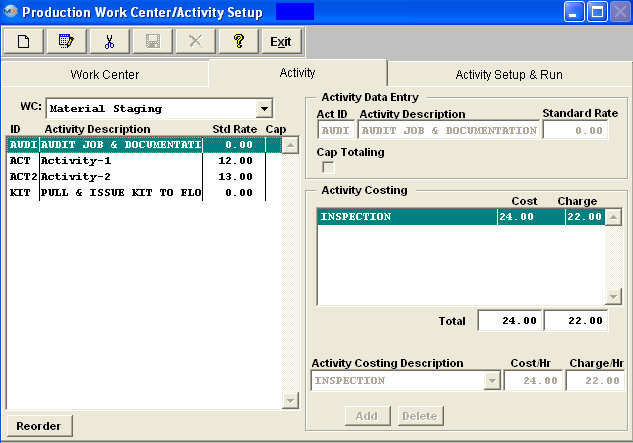 |
Once the Activity ID and Description, Cap Totaling election and hourly charge rate have been entered, depress the Activity Setup & Run tab.
|
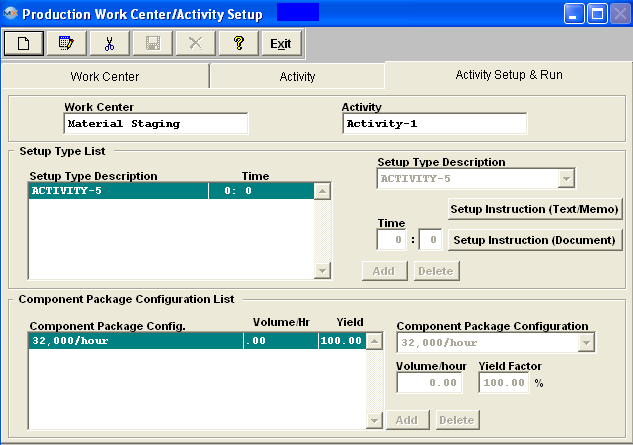 |
Depress the Edit button. For the Setup Type Description section. Depress the Add button (on screen).
Enter the time in hours and minutes
|
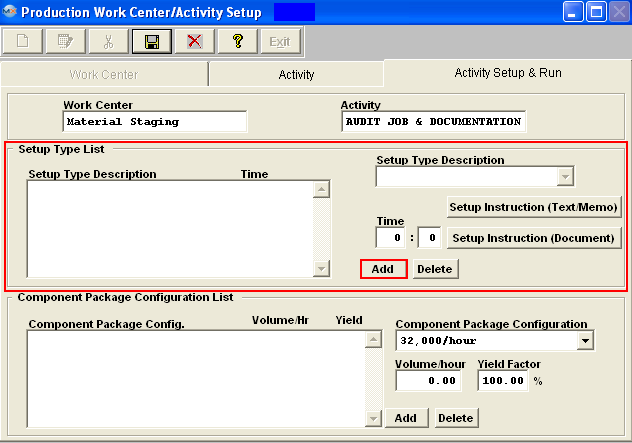 |
 |
This button allows the user to enter instructions for setting up the Setup Type. |
 |
This button allows the user to load a photo for an instruction. The photo file should be in the ManEx directory, and should be BMP or TIF format.
|
For Component Package Configuration, depress the Add button (on screen) |
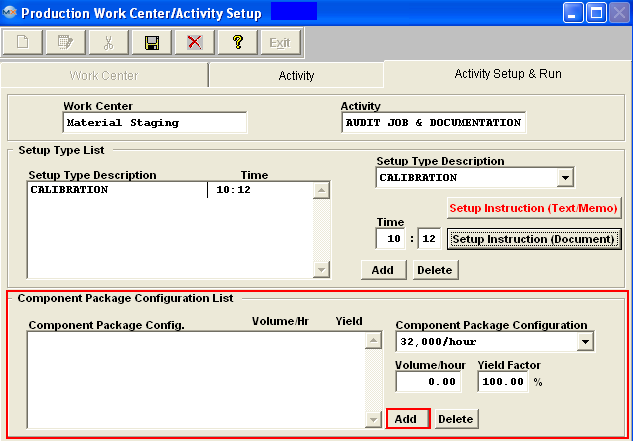 |
Select the Component Package Configuration from the pull down menu: (The Component Package Configuration(s) are defaulted in from the Package Configuration module).
Enter in the Volume per hour, and then the yield factor %.
Volume is the number of units per hour. This may be boards per hour, units per hour, connections per hour, etc.
The Yield factor affects the volume such that lower yield means it will take longer to make the same number of good parts.For example, if the standard volume is 100 parts per hour, and the total yield is 80%, then the effective yield would be 80 parts per hour.
|
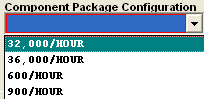 |
Once all changes are complete depress Save or Abandon changes.
Where Used: In all Shop Floor related Activities.
«Mark as Completed in RoadMap in Section B Item 3-d»
|
|