ManEx Minute - 35 - Alternate Parts |
|
|
"It's true that we don't know what we've got until we lose it, but it's also true that we don't know what we've been missing until it arrives."
-unknown
|
|
|
May, 2010
Issue 35
Dear David,
The first SQL presentation went well. We had a few scheduling conflicts so some of you that wanted to attend were unavailable at the scheduled times. To give everyone the opportunity to see the presentation, we have made it available for download. You can access the recording and spreadsheet here. Please let me know if you are unable to access the files. We will make future recordings available in this manner as well.
The next meeting will cover Sales Order, Customer Information, and Supplier Information and will show the screens and highlight the differences between ManEx SQL and the current version. We will hold this meeting on 5/14 at 9am Mountain. Seating is limited and is first come first serve. Please let me know which you would like to attend so I can provide the connection information.
The topic for this month's edition is a common problem and one that poses many challenges and obstacles. Hopefully the solution and explanation will provide new ideas and insights and help you better face this challenge.
We want to help in any way we can. If you have a challenge and want help, please take a moment to let us know and see if others can help you work through it.
As always, we look forward to your participation and feedback as you gain new insights and become a more effective provider of Electronic Manufacturing Services.
Sincerely,
David Sharp
ManEx, Inc.
|
Business Case - Inventory Control
|
Alternate Part Number Control
|
North Eastern Company (NE Company)* has seen their orders increasing recently. For the most part, they have been able to stay ahead of demand and get sufficient inventory to complete their orders. However, there are many components that they cannot get fast enough to meet the requested deliveries. For many of the shortages, they have better parts (higher voltage, tighter tolerance, gold leads, etc) available under separate internal part numbers, but don't have an easy way to setup, track, and use alternates.
Their current part number policy is to have all parts with the same form, fit, and function listed under a single internal part number regardless of the number of manufacturers that produce that component. While they want to procure the least expensive approved manufacturer for each component, sometimes using a more expensive component to finish an order is more economical than waiting for the less expensive component. At least, it can be if it isn't too difficult to use the alternates in the system.
How can NE Company identify potential alternates in their system? Because they will still need the customer's permission to use a better part, how do they track which customers have given this authorization? Once an alternate is approved, how do they notify purchasing and kitting of the alternates and ensure that they are used only if the less expensive part is not available? What impact will using alternates have on their standard costs?
*Name has been changed
|
Business Case Solution
|
For Electronic Contract Manufacturers, it is nearly impossible to completely avoid alternate part numbers. Tight production schedules and restricted material streams make it important to have a good method for tracking and managing alternate part numbers.
Read the full Business Case Solution >>
|
ManEx Case Solution
|
ManEx has some important tools to aid in alternate part number setup, usage, tracking. Although there are some significant hurdles to over come, current features go a long way aid manufacturers in this area. Future upgrades will continue to improve this process as well.
Read the full ManEx Case Solution >>
|
|
|
|
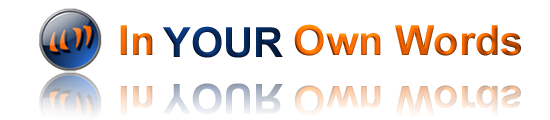
|
Alternate Part Numbers
"...I have successfully circumvented the problem by adding SoPark as the mfgr and the alternate ManEx pn as the mfgr # on the target ManEx pn.
This is used mostly to use up old revision or obsolete parts. I zero the qty_oh under the old pn and add the qty under the new Sopark mfgr line. I use disallow from Purchasing checkbox, so the part only shows on the picks.
The problem with using this with active pns is the AVL is not seen in MRP and the qty wouldn't be deducted properly from the alternate pn. Also, the standard pricing would not reflect the alternate. However, the customer AVLs would be in effect.
As a side note, we are still using general ManEx numbers here- not down to form, fit, and function. However, I believe form, fit, function pns may work better- but would require extensive work to change now. Both systems seem to have difficulties. Our problem is everyone needs to buy and pick down to specific mfgr / mfgr pn which can cause errors and costs additional labor time."
-Glenn, NY
|
|
 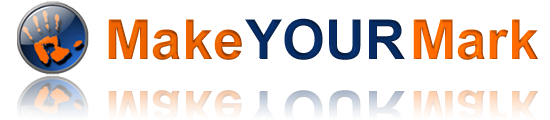 |
Please share your challenges and issues. Give us a challenge and see if we are able to provide a workable solution. All cases are presented using North Eastern Company (NE Company) as the principle in the case.
To suggest a new topic please send us an email or click here to submit the topic through our website.
|
©2008 All Rights Reserved.
ManEx Minute is a monthly email distributed by ManEx, Inc. |
 
Developing with YOU in mind! |
|
|
|
|
|
|