1. ManEx Minute - 35 - Alternate Parts |
|
|
"It's true that we don't know what we've got until we lose it, but it's also true that we don't know what we've been missing until it arrives."
-unknown
|
|
|
May, 2010
Issue 35
Dear David,
The first SQL presentation went well. We had a few scheduling conflicts so some of you that wanted to attend were unavailable at the scheduled times. To give everyone the opportunity to see the presentation, we have made it available for download. You can access the recording and spreadsheet here. Please let me know if you are unable to access the files. We will make future recordings available in this manner as well.
The next meeting will cover Sales Order, Customer Information, and Supplier Information and will show the screens and highlight the differences between ManEx SQL and the current version. We will hold this meeting on 5/14 at 9am Mountain. Seating is limited and is first come first serve. Please let me know which you would like to attend so I can provide the connection information.
The topic for this month's edition is a common problem and one that poses many challenges and obstacles. Hopefully the solution and explanation will provide new ideas and insights and help you better face this challenge.
We want to help in any way we can. If you have a challenge and want help, please take a moment to let us know and see if others can help you work through it.
As always, we look forward to your participation and feedback as you gain new insights and become a more effective provider of Electronic Manufacturing Services.
Sincerely,
David Sharp
ManEx, Inc.
|
Business Case - Inventory Control
|
Alternate Part Number Control
|
North Eastern Company (NE Company)* has seen their orders increasing recently. For the most part, they have been able to stay ahead of demand and get sufficient inventory to complete their orders. However, there are many components that they cannot get fast enough to meet the requested deliveries. For many of the shortages, they have better parts (higher voltage, tighter tolerance, gold leads, etc) available under separate internal part numbers, but don't have an easy way to setup, track, and use alternates.
Their current part number policy is to have all parts with the same form, fit, and function listed under a single internal part number regardless of the number of manufacturers that produce that component. While they want to procure the least expensive approved manufacturer for each component, sometimes using a more expensive component to finish an order is more economical than waiting for the less expensive component. At least, it can be if it isn't too difficult to use the alternates in the system.
How can NE Company identify potential alternates in their system? Because they will still need the customer's permission to use a better part, how do they track which customers have given this authorization? Once an alternate is approved, how do they notify purchasing and kitting of the alternates and ensure that they are used only if the less expensive part is not available? What impact will using alternates have on their standard costs?
*Name has been changed
|
Business Case Solution
|
For Electronic Contract Manufacturers, it is nearly impossible to completely avoid alternate part numbers. Tight production schedules and restricted material streams make it important to have a good method for tracking and managing alternate part numbers.
Read the full Business Case Solution >>
|
ManEx Case Solution
|
ManEx has some important tools to aid in alternate part number setup, usage, tracking. Although there are some significant hurdles to over come, current features go a long way aid manufacturers in this area. Future upgrades will continue to improve this process as well.
Read the full ManEx Case Solution >>
|
|
|
|
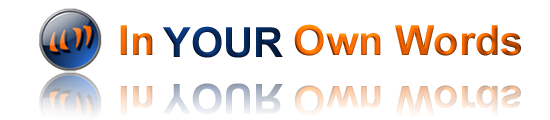
|
Alternate Part Numbers
"...I have successfully circumvented the problem by adding SoPark as the mfgr and the alternate ManEx pn as the mfgr # on the target ManEx pn.
This is used mostly to use up old revision or obsolete parts. I zero the qty_oh under the old pn and add the qty under the new Sopark mfgr line. I use disallow from Purchasing checkbox, so the part only shows on the picks.
The problem with using this with active pns is the AVL is not seen in MRP and the qty wouldn't be deducted properly from the alternate pn. Also, the standard pricing would not reflect the alternate. However, the customer AVLs would be in effect.
As a side note, we are still using general ManEx numbers here- not down to form, fit, and function. However, I believe form, fit, function pns may work better- but would require extensive work to change now. Both systems seem to have difficulties. Our problem is everyone needs to buy and pick down to specific mfgr / mfgr pn which can cause errors and costs additional labor time."
-Glenn, NY
|
|
 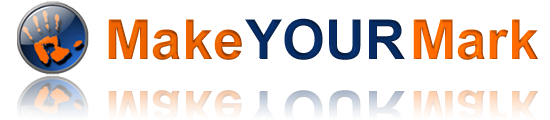 |
Please share your challenges and issues. Give us a challenge and see if we are able to provide a workable solution. All cases are presented using North Eastern Company (NE Company) as the principle in the case.
To suggest a new topic please send us an email or click here to submit the topic through our website.
|
©2008 All Rights Reserved.
ManEx Minute is a monthly email distributed by ManEx, Inc. |
 
Developing with YOU in mind! |
|
|
|
|
|
1.1. Business Solution - 35 - Alternate Parts |
Business Case Solution
For Electronic Contract Manufacturers, it is nearly impossible to completely avoid alternate part numbers. Tight production schedules and restricted material streams make it important to have a good method for tracking and managing alternate part numbers.
Before implementing an alternate tracking system, it is important to understand how you will define an alternate.
The method you use will depend in large part on how you have your part numbers setup. If your components are setup with all parts having the same form fit and function under a single internal part number, then an alternate is likely to be better in some way (i.e. tighter tolerance, higher voltage, etc). If your parts are setup for each manufacturer, customer, or similar grouping, then an alternate may be just another internal part number for the exact same part.
Ideally, your numbering setup should reduce the number of part numbers in your system and the frequency with which you have to use alternates.
Regardless of your setup, the three main considerations for you alternate part number tracking system are:
- Visibility of Possible Alternates - Users must know that an alternate is available/approved if they are going to use it. Without clear visibility of these alternates, they might as well not exist.
- Use of Alternates - If an alternate is available and the user knows it exists, they must be able to easily use the alternate part. A system that makes using the alternate too difficult may not prevent the user from using the alternate, but it increases the likelihood that the use will not be properly recorded and accounted for.
- Accounting for the Cost of Alternates - Once the user pulls the alternate, the system should provide visibility of the use and the cost differences because of its use. This can be done manually, but this is not practical, especially if alternates are used more frequently.
|
1.2. ManEx Solution - 35 - Alternate Parts |
ManEx Case Solution
ManEx has some important tools to aid in alternate part number setup, usage, tracking. Although there are some significant hurdles to over come, current features go a long way aid manufacturers in this area. Future upgrades will continue to improve this process as well.
On the surface, the topic seems straight forward and should be easy to implement. However, a more in-depth analysis reveals a few key questions that need specific answers. For example, when and why would MRP use alternates? Will each manufacturer answer that in a different way? How does this apply to all manufacturers? If alternate parts are used, what impact would that have on the actual cost of the assembly, on the standard cost of the assembly? If alternates are frequently used, should the cost of the alternates be factored into the product pricing? If alternates are frequently used, should they be considered alternates? And the list goes on.
Despite these tough questions, ManEx has provided a way to manage each of the key topics relating to alternate parts.
- Visibility of Possible Alternates - ManEx allows users to list alternate parts for each item on every BoM. This is for reference only and merely provides visibility of possible alternates. However, if alternates are used more than rare occasions this alone is not sufficient to meet users needs.
Additionally, users can setup a part manufacturer under the internal part number that ties to another internal part number, or related customer part number. If the alternate customer part number is used, then the customer AVL can be applied as well. This notifies purchasing, kitting, and production of possible alternates and allows the alternates to be used in place of the original as decided by the user.
- Use of Alternates - If alternates are rare and/or the qty using the alternate is large enough, users can use the effective and obsolete dates to turn off the original part and add the alternate to the BoM. .
In most situations, the suggested method is to leave the BoM as originally specified and issue the alternate part to the kit. Because the AVL from the original part indicates the alternate that can be used, kitting will know to look for the alternate when the original isn't on hand. Kitting should also mark the original as complete in kitting. This will remove the MRP demand for that part and prevent a duplication in demand and usage.
- Accounting for the Cost of Alternates - By recording which parts were actually used in the kit, the system will have an accurate history of part usage, material costs for the kit will reflect any part pricing differences, and standard costs will not be affected by the alternate.
While this method is not the only solution, it does seem to be the most universally applicable and acceptable. It also adds some efficiencies to the process when alternates are needed. There were other methods suggested that would work on a more specialized situation. If you are interested in learning more about those ideas, let me know and I can provide greater detail.
contact a ManEx representative for more details on any of these topics.
|
|