1. ManEx Minute - 27 - Multi-shift communications |
|
|
"The problem with communication ... is the illusion that it has been accomplished."
-George Bernard Shaw
|
|
|
July 15, 2009
Issue 27
Dear David,
The supplier directory is almost ready. We have already started receiving capability updates from the suppliers and hope to finish debug and test within the next several weeks. You will soon be able to rate your PCB suppliers and read the reviews from their other customers.
In our last survey, we asked about multi-shift communications. Although the percentage of companies running 2 or more shifts decreased, it is still around 60%. Whenever a project extends beyond a single shift, it is important to have a good system for communicating job information to other departments, shifts, and days in order to reduce errors and consistently produce a quality product.
This issue focuses on the communication challenge and offers ways to increase communication effectiveness.
As always, we look forward to your participation and feedback as you gain new insights and become a more effective provider of Electronic Manufacturing Services.
Sincerely,
David Sharp
ManEx, Inc.
|
Business Case - Production Control
|
Multi-shift Communication
|
North Eastern Company (NE Company)* had to scale back production over the last six months and has been running only a single shift. Fortunately, they have seen an increase in quoting activities and expect to again start the second shift within the next few months.
Management is concerned about their current processes for collecting, distributing, and using the production information and notes for each kit across each department, shift, and day. Even running a single shift, they lose information from one day to the next and from one production run to the next. They fear that adding more people, work orders, and shifts will only increase this problem.
They have tried several methods for documenting important information from production, but haven't been able to implement it consistently in order to significantly reduce the number of preventable errors.
What is the best way for production to communicate across departments, shifts, and days? What tools do they need to accomplish this? What impact will it have on their ISO certification?
*Name has been changed
|
Business Case Solutions
|
Most manufacturers need good communication and documentation control processes, but many underestimate its importance...
|
ManEx Case Solution
|
ManEx has several tools to allow communication between shifts, departments, and days...
Read the full ManEx Case Solution >>
|
|
|
|
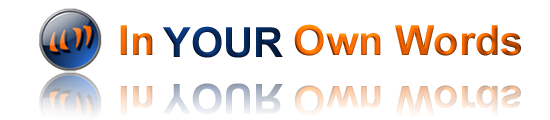
|
BoM Importing
"[We have] overlap between days and swing only. [Communication] is done by email between swing and days. We also use work order/work center notes."
-Anonymous
"ManEx provides excellent information no matter how many shifts you are running ."
-Shep, IN
"...supervision/management overlap and are required to meet to make the transition [between shifts].
This offers very little benefit and allows for mis-communication.
-Michael, IL
|
|
 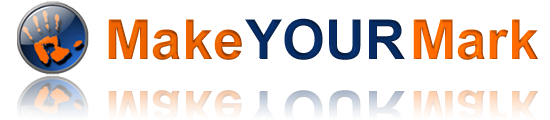 |
Please share your ideas and insights on a topic below. Use the questions to direct your response. Please contact us to submit your thoughts on the topic. Where appropriate and space permitting, we will post responses in a future newsletter so all may benefit.
System Triggers
Do you use the system triggers?
How many triggers have you created?
What is the biggest benefit received from using the triggers?
What issues have you seen from the triggers?
To suggest a new topic please contact us.
|
©2008 All Rights Reserved.
ManEx Minute is a bi-weekly email distributed by ManEx, Inc. |

Developing with YOU in mind! |
|
|
|
|
|
1.1. ManEx Solution - 27 - Multi-shfit communications |
Business Case Solution
Most manufacturers recognize the need for good communication and documentation control processes, but many underestimate its importance. They think that running one shift removes the need, or their employees have a good handle and remember what is needed without a system or process.
While that may be true, it is not only not recommended, it would fail most ISO audits.
Companies use many methods for documenting requirements and communicating between shifts. Some of the most common are:
-
Paper Based Tracking - This requires employees to document all needs, notes, and issues in paper format. While it is very inexpensive to implement, it requires additional processes for document control and is subject to employees forgetting to document or misplacing the documents.
-
Email Communication - Some companies will use internal emails to communicate needs and requirements between shifts and production builds. This creates an electronic record of the needs and notes. However, it is difficult to control and ensure everyone has only the latest information. It also requires users to check their email in order to get the latest updates.
-
Daily Meetings - This is probably the most common method for communicating information between shifts. It allows the exiting shift to update the incoming shift of any issues and important topics for the current job. However, it is subject to human error as they may forget to communicate some of the information. It also fails to document the information for later use. Also, this will not carry daily information into the next day if the company runs only a single shift and requires users to remember important information from day to day and week to week.
-
System Based Tracking - Many ERP systems provide methods for documenting important information for each job. Ideally it would allow users to communicate across departments, jobs, and days.
Companies may decide to use a combination of the above methods depending on the complexity of the assembly and production requirements.
|
1.2. ManEx Solution - 27 - Multi-shift communication |
ManEx Case Solution
ManEx has several tools to facilitate communication between departments, shifts, and days.
- Related Documentation* - The related documentation button in production is part of the Product Data Management (PDM) module. It allows users to attach numerous files and file types and electronically control documents for a given assembly. This means production always has the latest information and can easily access it from any terminal.
- Shop Floor Tracking Notes - Production workers are able to document notes and issues related to all work centers in a job, specific work centers in a job, and specific work centers across all jobs. Notes are flagged to make users aware as they click on affected work orders and work centers. This ensures they have the latest information and it is not lost between jobs, departments, shifts, and days.
- Work/Special Instructions* - In addition to related documentation, users can add work instructions and special instructions for each work center in the routing for every assembly. This ensures the needed information is readily available and current.
Case Solution
NE Company loaded all of their documentation into the PDM module* and started utilizing the numerous notes within the shop floor tracking module.
Employees were able to learn and become comfortable with these tools. These practices were carried into the second shift and enabled better communication between shifts. It also enabled production to better communicate with production management and ensure documentation was complete and accurate.
While it is difficult to quantify the benefits from this process change, they have noticed a reduction in production delays and defects as they leveraged the wealth of information well documented within the system.
*an optional module may be required
|
|