1. ManEx Minute - 25 - BoM Importing |
|
|
"Computers have enabled people to make more mistakes faster than almost any invention in history, with the possible exception of tequila and hand guns"
-Mitch Ratcliffe
|
|
|
June 10, 2009
Issue 25
Dear David,
I have wonderful news!! Initial testing went so well, that we are ready to open Component Exchange© beta to everyone. Join for free at www.manex.com/ce.
I have been pleasantly surprised by the growth. Even with the limited release, we are adding an average of 350 new part listings every week. That means that even if the components you want are not listed now, they could be tomorrow.
Make sure to tell everyone about the service. You will directly benefit along with all other users as more companies list and buy parts through this free service. Best of all, because it is free, you have absolutely nothing to loose.
This issue of ManEx Minute focuses on importing BoMs. Nearly 84% of you kit parts by the consuming work center. You also track an average of nearly 9 work centers in production. This is an easy and effective way to manage inventory and reduce attrition. Hopefully today's case will give you some ideas or confirm the effectiveness of your current methods.
As always, we look forward to your participation and feedback as you gain new insights and become a more effective provider of Electronic Manufacturing Services.
Sincerely,
David Sharp
ManEx, Inc.
|
Business Case - Inventory Control
|
BoM Importing
|
North Eastern Company (NE Company)* just won a contract from a new customer. As expected, the customer wants the first deliveries as soon as possible. However, before they can start work, they need to get the assemblies into the system so they know what to buy and can start planning for production.
To keep costs down and better manage the components in their system, NE Company does not upload a BoM until they win the business. While it keeps their parts listing as small as possible, it can create difficulties when they need to quickly start producing a product after quoting.
For the new order, NE Company will need to create 27 BoMs (including sub-assemblies). Fortunately, only 9 are required for the initial delivery.
Even with this reduced initial requirement, management is concerned. Their current importing process takes an average of 42 hours per assembly. They don't have time to run it through the standard process, but don't want to risk purchasing and producing the first orders incorrectly.
How can they accurately and quickly load the current assemblies into the system? How will they prevent duplicate parts? Can they quickly check to see if existing inventory is available to fulfill the order? What are their options to reduce the turn time on loading BoMs into the system?
*Name has been changed
|
Business Case Solutions
|
All good ERP systems give users the ability to create components and assemblies...
|
ManEx Case Solution
|
It is easy to dump information into a table, but in order to keep the information clean and accurate, users should validate and scrub data before importing...
Read the full ManEx Case Solution >>
|
|
|
|
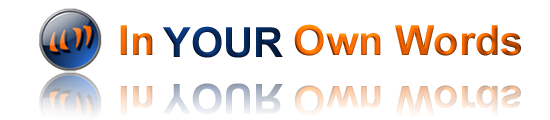
|
BoM Importing
"In most cases we use BoM Import but if we have similar BoM's we will copy, if it's a small BoM (less than 10-15 parts) or if the BoM doesn't have customer P/N's we will manually load them.
"The time it takes to load BoM's has significantly improved through [BoM Import]
"...[However] there is still the issue [where I can't] load the part but not the new AVL"
-Nick, TX
"When customers provide bom's in a format that's import friendly, the import module is a big benefit."
-Michael, IL
"We are an engineering organization so BOMs evolve over days and weeks.
"The BOMs often change during development and manual entry is required to modify a BOM. Initial entry could be done from spreadsheet to save time.
"Some large BOMs take a very long time and mistakes can occur."
"I abandoned using [BOM Import] because of the complexity...Why do you have to enter items based on the manufacturer's part numbers? These numbers have so many variations it is very difficult to get things to match up exactly."
-Justine, NH
We load 6-8 BoMs each week [of those] 3-5 are new ones.
"We Drag-n-Drop from the item master. [For us] it is enormously faster than the BOM import tool."
-Tom, OR
|
|
 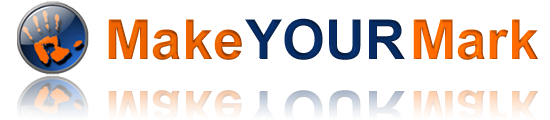 |
Please share your ideas and insights on a topic below. Use the questions to direct your response. You can submit your thoughts to mym@manex.com by clicking the topic title. Where appropriate and space permitting, we will post responses in a future newsletter so all may benefit.
Multi-level BoMs
How many levels do you track on a BoM?
Do you create sub-assemblies for each WC?
When and why do you create subassemblies?
What benefits have you seen from using sub assemblies?
To suggest a new topic please send an email to mym@manex.com.
|
©2008 All Rights Reserved.
ManEx Minute is a bi-weekly email distributed by ManEx, Inc. |

Developing with YOU in mind! |
|
|
|
|
|
1.1. ManEx Solution - 25 - BoM Import |
Business Case Solution
All good ERP systems give users the ability to create components and assemblies. However, the methods and effectiveness of the methods can vary widely.
The most common methods for creating new assemblies are:
-
Manually Load Each Item - This method gives the most control for creating parts and assemblies in a system. Users are able to configure each aspect of the components and assemblies. However, this can be a time consuming process and is prone to human error. Typically this works best for small assemblies.
-
Copy an Existing BoM - This allows users to save time by copying an existing BoM and changing only what is needed. While this can save time over the completely manual process, it works only if the assemblies are similar and determining the similarity before the copy can be difficult.
-
3rd Party/Custom Import Tools - Many ERP systems have 3rd party add-ons available. Others allow users to create custom tools. This can simplify the import process and save significant time. However, 3rd party and custom tools must be updated to work with system changes and must be thoroughly tested to ensure they work as intended without creating other issues.
-
Native Import Tools - If an ERP system has a native import module, it probably has been verified to accurately import the information. It too may save time and make the process easier. However, it may be an additional expense and may not be as flexible as custom solutions.
Companies may decide to use a combination of the above methods depending on the complexity of the assembly and production requirements.
|
1.2. ManEx Solution - 25 - BoM Import |
ManEx Case Solution
It is easy to dump information into a table, but in order to keep the information clean and accurate, users should validate and scrub data before importing. This is especially true when the data to be loaded was created by customers and other outside organizations.
ManEx has created an import module and several utilities to simplify and streamline the import process.
However, using the import module is not always the fastest way to load a BOM. Below are some tips and tricks to help you create new assemblies faster.
- Manufacturer Match - Users can use the utility to match manufacturer part numbers in a spreadsheet with existing AVLs. The utility will create a list of existing part numbers that use the manufacturer's part number. These parts should be auto selected in the import process or manually selected with the cross reference as needed.
- MFG Scrub* - Using this spreadsheet will allow you to scrub the manufacturers to ensure they are clean and accurate. Although the import process does this as well, it will allow you to create manufacturer aliases to expedite future imports.
- Skip class and type - Users are not required to load part class and type to start purchasing and production. If you skip this step in the import process it will still create the new parts and assemblies, but will assign a class and type of TBD. When ready, users can utilize the Global Class/Type Replace utility to assign the class and types and update the existing records. This allows for faster loading and more control part definition as time allows.
- BoM copy - Users can copy an existing BOM into a new BOM and modify it as needed. This method works really well for similar assemblies or revision changes.
- Drag-n-drop - For small assemblies with components already loaded in the system, using drag-n-drop may be the fastest method to create a new assembly. Users are able to create a BOM by simply dragging components from the item master into the BOM.
- Modify the import template - When loading multiple BOMs from the same customer or with similar formatting, users can modify the import template to allow for simple copy and paste from the source file. This may not make sense for one-off assemblies, but can be a significant time saver when loading numerous BOMS from the same customer.
- ECO Module - The optional ECO module will allow users to document changes to an existing BOM and create a new BOM or revision after applying the changes. This provides documentation and control while automatically creating a new assembly.
- QOT Module - The optional quote module allows users to create assemblies in the quote section without adding components and assemblies to Inventory Item Master. Once the job becomes an order, users are able to transfer the quoted assembly into the item master. This will create the new components and prepare the assembly for production. It can greatly reduce the turn time after winning a new job.
Case Solution
NE Company started creating assemblies in the quote module and is now able to convert a quote to a production assembly in less than 30 minutes. This allows them to start purchasing and preparing for production almost immediately.
For assemblies that do not go through the standard quoting process, NE Company has been able to cut the over 60% of the import time required using a combination of the methods above.
*this is a non standard tool and is not supported by ManEx. Please contact us to request a copy of this spreadsheet.
|
|