1. ManEx Minute - 24 - Kitting By BoM |
|
|
"We may be very busy, we may be very efficient, but we will also be truly effective only when we begin with the end in mind."
-Stephen R. Covey
|
|
|
May 27, 2009
Issue 24
Greetings!
I have some exciting news!! We have all but finished the Alpha testing on component exchange and are ready for a limited release. We will open it to 50 companies interested in getting started right away. Please send me an email if you are interested in participating now and I will send you the details.
We are also ready to start loading the next round of inventory lists. If you missed the cutoff on the first round, now is your chance to participate. Please email your list of parts including manufacturer, part number, quantity on hand, and any other relevant information you have.
I am optimistic that we will be ready for the general BETA release very soon.
Now, on to the newsletter. In our last survey, we asked about kitting by work center. Nearly 84% of you kit parts by the consuming work center. You also track an average of nearly 9 work centers in production. This is an easy and effective way to manage inventory and reduce attrition. Hopefully today's case will give you some ideas or confirm the effectiveness of your current methods.
As always, we look forward to your participation and feedback as you gain new insights and become a more effective provider of Electronic Manufacturing Services.
Sincerely,
David Sharp
ManEx, Inc.
|
Business Case - Inventory Control
|
Kitting by Work Center
|
North Eastern Company (NE Company)* has had to order replacement components for many kits, even though inventory claims the kits were complete when they were sent to production.
Currently, the stock room pulls the kits for all work centers together and sends the entire kit to production. Each work center in the process pulls the parts from the totes as needed and sends the totes to the next work center upon completion. This ensures that subsequent work centers have replacement parts for previous work centers, if needed.
The production manager suspects that much of the attrition actually happens in the work centers not responsible for placing the parts. They typically don't need the components and so do not handle them as carefully as they could.
If NE Company starts to kit by work center, how many work centers should they use? Should they still pull the full kit together and just keep the parts in separate bins? If the parts are pulled for each work center, how will subsequent work centers request and get replacements as needed?
*Name has been changed
|
Business Case Solutions
|
Each assembly has several steps required to complete production. Each step may be...
|
ManEx Case Solution
|
ManEx has standard fields and reports to make kitting by work center as easy as possible...
Read the full ManEx Case Solution >>
|
|
|
|
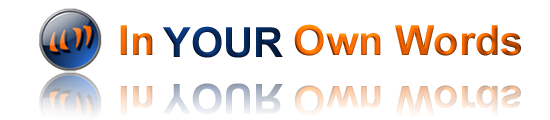
|
Kitting By BoM
"Although we have 12 potential work centers that assemblies can go through, we kit parts to only 2 work centers."
-Paul, WA
"We pull for all work centers except for SMT at one time. SMT is pulled by the operator."
-Alan, WI
"We are using point of use inventory. Each work center has its own location."
-Guy, OH
ManEx runs reports to split the kit pulls for us. We used to have to figure this manually. We have more consistency now in what parts land in each department."
-Tom, OR
| |
 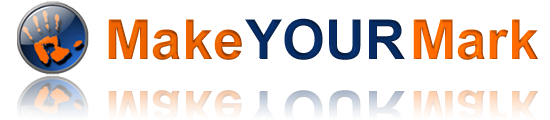 |
Please share your ideas and insights on a topic below. Use the questions to direct your response. You can submit your thoughts to mym@manex.com by clicking the topic title. Where appropriate and space permitting, we will post responses in a future newsletter so all may benefit.
BoM Import Management
How many BoM's do you load each week?
On average, how many components are on a BoM?
How long does it take you to load a BoM in your system?
What is the most time consuming part of the process?
Would you want customers to upload BoMs directly into your system?
To suggest a new topic please send an email to mym@manex.com.
|
©2008 All Rights Reserved.
ManEx Minute is a bi-weekly email distributed by ManEx, Inc. |

Developing with YOU in mind! |
|
|
|
|
|
1.1. ManEx Solution - 24 - Kitting By BoM |
Business Case Solution
Each assembly has several steps required to complete production. Each step may be responsible for placing specific components, yet many systems do not offer an easy way to identify and pull parts for each step.
Some of the most common methods for handling a situation like this are:
-
Pull parts for all work centers together - This is the easiest way to create a Bill of Material and pull parts for production. However, it increases the likelihood of lost parts in production. It makes it difficult or impossible to offset delivery dates for components needed in each work center. It also makes it difficult to find components in the totes. However, it may work well for small assemblies (few items on the BoM) or assemblies with few assembly steps.
-
Creating separate Bills of Material for each work center - This method makes it easy to see which components are required for each work center. It also makes it easy to adjust the material stream to control cash flow. However, it also creates excessive work orders to process each work center, and makes it more difficult to tie all work centers to the full assembly (users can overcome this shortfall by making the separate BoMs sub assemblies to the top assembly).
-
Changing the item numbers to indicate the work center - This allows users to see which parts belong in each work center. It requires users to manually control the item numbers, and pull parts by item number. This also is not an efficient method for control the material stream to help cash flow.
-
Creating inventory locations for each work center - This method breaks inventory into several smaller locations. Rather than a central inventory containing all parts, each work center has a mini-inventory containing all parts placed in that work center. This eliminates the need to pull parts for each work center and makes each work center responsible for the parts. However, it may require more floor space and may make it more difficult to track overall inventory. (a variation on this method is to have parts in a central inventory and then create a select few production inventory locations to handle and store the high volume common parts).
-
Using system fields to tie parts to each work center - If the system has a field for indicating the work center or the user can define a field for this purpose, this is the most flexible method. It allows users to indicate the consuming work center, kit by work center, and offset the material stream for each work center.
Companies may decide to use a combination of the above methods depending on the complexity of the assembly and production requirements.
|
1.2. ManEx Solution - 24 - Kitting By BoM |
ManEx Case Solution
ManEx has standard fields and reports to make kitting by work center as easy as possible. Users of ManEx are also able to utilize any of the methods described in the business solution.
For assemblies with few parts and/or production steps, it is can be more efficient to leave all components in the material staging work center. Fortunately, this can be updated at any time as required.
Kitting and production typically benefit by identifying consuming work centers on more complex assemblies and processes. Each component on a Bill of Material can be assigned to the consuming work center. Then, kitting can pull parts for each work center. Each production department is also able to see all parts required for their work center as well as the entire BoM. This reduces the clutter in production and the risk of misplaced parts. This also makes it easier for production to return unused components to the stock room upon completion of each step in the process.
Components used in more than one work center can be separated on the Bill of Material to indicate which locations and quantities are required for each work center. This enhances control over the disposition of the material.
Case Solution
NE Company started kitting by work center. They tied all components most assemblies to the consuming work center. They also adjusted the production offset for later work centers to get closer to a JIT material stream.
Although they have not eliminated production attrition, they have been able to reduce it significantly and increase responsibility.
|
|