1. ManEx Minute - 21 - Performance Tracking |
|
|
"It is wiser to find out than suppose."
-Mark Twain
|
|
April, 15 2009
Issue 21
Dear David,
We have released our new website. It has a much better layout and makes it easier to access the information you need. One of the new features is the full case archive from these newsletters. You can check it out here. As soon as the newsletter is published, the case and solutions will be available on this site. This will also make it easier to reference past cases and solutions.
This issue focuses on performance tracking. Although material makes up the majority of the COGS in this industry, labor is a significant factor in profitability. If a company doesn't track labor performance, how can they know if they are making money or need to make improvements?
In our most recent survey, only 18% of you do not track actual time on a job. However, 54% do all tracking on paper. Perhaps this is why over 36% don't know if or how much of a variation each job has between expected and actual labor.
This case study should help identify methods for tracking and comparing production times with expectations.
As always, we look forward to your participation and feedback as you gain new insights and become a more effective provider of Electronic Manufacturing Services.
Sincerely,
David Sharp
ManEx, Inc.
|
Business Case - Production Control
|
Performance Tracking
|
North Eastern Company (NE Company)* finished their first quarter with a moderate increase in shipped orders. Management was pleased to see this improvement. However, their profit margin was smaller than they expected.
Upon further investigation, they confirmed that materials were within acceptable limits and should not have adversely affected their profit margin. They suspected that labor may have affected their bottom line, but had to wait for the numbers to be compiled and analyzed.
How can NE Company efficiently track time spent per employee on each job? What tools can they use to report on the performance? How can they compare the actual results with expected results? If they identify a discrepancy, what is the best course of action?
*Name has been changed
|
Business Case Solutions
|
The choice between adding intelligence to Work Order Numbers and letting the system maintain the numbers may not be as obvious as it first appears. Companies must weigh the "costs" of each method and determine if they are greater than the benefits and savings created.
|
ManEx Case Solution
|
ManEx will allow users to control Work Order Numbers both manually and automatically. Users are able to switch back and forth between the methods as needed.
Read the full ManEx Case Solution >>
|
|
|
|
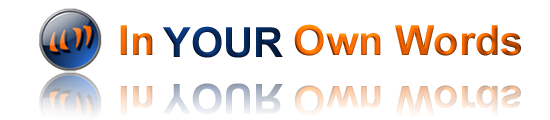
|
Performance Tracking
"We only [track production performance] occasionally on jobs that we think we are losing money based on feedback from production or if we bill time and material on certain rework type of jobs."
- Peter, WA
"[Our] variance is typically tight as we use past history performance as a target on repeat orders. However new orders, with no available tracking history, can look much different."
- Nick, OH
"When we first implemented [performance tracking], we actually re-quoted everything and even dropped non-profitable customers.
By simplifying data collection we can increase the amount of data that we actually collect.
The scanner operation has to be simple, and quick, and provide intelligent feedback to the scanner. It must be divorced from the GUI.
It must be able to track multi-tasked activities and be smart enough to know when to log off an activity by the activity that was started.
Time tracking and time and attendance must be integrated."
-Bob, UT
"That information is then entered into a third party system. That system does the comparison of times and shows us where we lost/gain.
The biggest issue we see is the times are not always accurate. The employee may fudge the time or completely forget to record it and guess later on. The other issue is it is labor intensive to enter all of these results in the third party system."
-Todd, MI
"We are currently embarking on a project to review our overall system used for quoting and time tracking. We have three goals in mind: consistency, accuracy, and the ability to easily track variances.
Over the last year we have methodically squashed homegrown systems and found ways to fulfill the requirements by integrating into ManEx or our Aegis system. Quoting and time tracking are the last hurdles."
-Tom, WA
|
 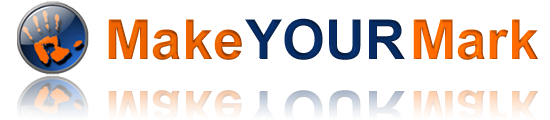 |
Please share your ideas and insights on a topic below. Use the questions to direct your response. You can submit your thoughts to mym@manex.com by clicking the topic title. Where appropriate and space permitting, we will post responses in a future newsletter so all may benefit.
Part Cross Reference
When and why do you have multiple instances of the same part in your item master?
If you duplicate a part, how do you tie it to the original?
How often do you need to cross between parts?
How long does it take to identify a matching or related part in your item master?
What is your biggest issue with crossing parts?
Minimum Purchases and Residual Inventory
How do you plan for residual inventory?
Do you charge the customer for the full reel?
Who owns the residual inventory at your facility?
How long does residual inventory stay on your shelves?
What is your biggest issue with residual inventory?
To suggest a new topic please send an email to mym@manex.com.
|
©2008 All Rights Reserved.
ManEx Minute is a bi-weekly email distributed by ManEx, Inc. |

Developing with YOU in mind! |
|
|
|
|
|
1.1. Business Case Solutions - 21 - Performance Tracking |
Business Case Solutions
Labor performance tracking can help determine if a project or customer is profitable for your business and if the product is priced correctly. Poor labor performance can turn an otherwise profitable project into a money loser. Inversely, it may also identify projects that can be priced more competitively while maintaining profit targets and goals.
Companies often take one of four approaches for their labor performance tracking:
- Bottom-line or absent - Some companies look at overall profitability at year end to determine if they have been pricing their products profitably and are making money. They do not track individual job performance. While this is the "low-cost" option because it requires no additional overhead for tracking labor performance, it does not provide enough details to direct improvements or identify unprofitable projects and customers. This "low-cost" solution may actually be one of the most expensive in terms of lost business from over pricing, and lost profits from underpricing.
- Paper based tracking - This is a common method used in manufacturing because it is quick and easy to implement and requires little money for data collection systems. It is simple to setup any workstation for data collection and employees can take their time sheet to any work station. However, it is very easy for employees to make mistakes. They can either forget to record their time, or record their time against the wrong jobs. Additionally, it is time consuming to enter the data into a system manually, or to analyze the data on paper.
- 3rd party tracking - Many companies use a 3rd party time tracking system to collect project labor information. This 3rd party system may already be in place and give users the ability to record time against projects and analyze the results. However, it either requires redundant project information in the 3rd party system, or the creation of a link between systems to allow data sharing. The same may be true of analyzing the results. This may require workers to leave their work station as they change jobs within the system.
- Integrated tracking - An Integrated tracking system allows users to collect project labor information from within the shop floor control system. This integration verifies that projects are valid and active, and keeps real-time information readily available. It also prevents the unnecessary creation of project information in multiple databases. However, depending on terminal availability, it may require workers to leave their work station as they change jobs within the system.
|
|
1.2. ManEx Solution - 21 - Performance Tracking |
ManEx Case Solution
ManEx has optional modules for both production labor tracking and performance analysis. These modules are designed to simplify production time data collection, and labor and material cost comparison.
- Time & Attendance (T&A)* - This module allows users to clock in and out of work orders and work centers and in and out of the time clock from any terminal connected to the network. It will verify that the job is active and that the work center is part of the selected work order. This verification helps to ensure that the created records are as accurate as possible.
The standard reports in this module provide information by employee for a selected date range. In addition to total hours worked, users are able to see which work orders the employee worked in and which employees worked on a selected work order.
- Job Costing* - This module provides a quick reporting analysis of performance on a selected work order. After entering expected setup and run times into each step in the routing, users are able to compare both budgeted and actual material and labor (actual labor reporting requires the T&A module). Because production workers punch in by work center, users are able to see details of which work centers required more time than expected so the quote or process can be changed accordingly.
The standard reports allow a more detailed analysis of labor, material, and overall performance.
CONCLUSION
NE Company converted to a hybrid labor tracking system. Most employees had access to at least one terminal for data collection and punched in and out of jobs directly into the integrated module. For production workers not able to use a terminal for data collection, they recorded their times and projects on paper using the job travelers as a guide to know which work orders and work centers to use. At the end of the shift, their information was entered into the system.
Using the standard reports and a few custom reports, NE Company was able to not only see how they were doing on each job, but analyze the results of process changes to ensure they were getting the desired benefit. Within six months, they were able to identify two customers that were consistently unprofitable.
*may require the purchase of an optional module
|
|