ManEx Minute - 19 - Inventory by Project |
|
|
"The secret of all victory lies in the organization of the non-obvious."
-Marcus Aurelius
|
|
March, 11 2009
Issue 19
Greetings!
Although we continue to hear about increasing unemployment and a dropping stock market, my contact with companies in this industry seem to indicate that, overall, the industry is reasonably stable.
We may not know what the future holds, but we do know that it is a great time to get organized and become more efficient.
One area of interest to many, is how to more efficiently organize and track inventory exposure by customer and project. Companies can use this information periodically throughout the job to minimize exposure and improve cash flow.
According to the most recent survey, nearly a third of you do not have a good method for tracking this inventory. It takes an average of 3.5 hours to compile this data and occasionally requiring days. For this reason, this issue will focus on compiling detailed on-hand and on-order information for inventory by customer or project.
As always, we look forward to your participation and feedback as you gain new insights and become a more effective provider of Electronic Manufacturing Services.
Sincerely,
David Sharp
ManEx, Inc.
|
Business Case - Inventory Control
|
Inventory by Project and Customer
|
North Eastern Company (NE Company)* is required to provide a monthly inventory exposure update to their three largest customers. This is a time consuming process and requires about 6 man hours per customer each month.
Additionally, NE Company is feeling the impact of the slowing economy as a small but growing number of customers stop placing new orders. According to their agreements, whenever a customer stops ordering for a period of six months or more, or when they end the relationship, NE Company will invoice for all remaining inventory purchased and on-hand for the customer. As with the monthly updates, the list of inventory takes about 6 man hours to compile.
NE Company has tried several methods to make this process easier and faster. However, they have been unable, so far, to find the right balance between consolidated inventory with increased buying power, and visibility of inventory by customer or project.
How can NE Company consolidate their inventory, while maintaining easy visibility of inventory on hand for any given project or customer? How can they reduce the time required to compile on-hand inventory information?
*Name has been changed
|
Business Case Solutions
|
The potential impact of residual inventory on profitability and cash flow increase the importance of understanding inventory on-hand by project or customer. There are numerous methods for purchasing and tracking inventory by customer or project.
|
ManEx Case Solution
|
ManEx was designed from the ground up for electronic contract manufacturing. As a result, no other system fulfills the needs better. ManEx has many standard and optional modules designed to streamline inventory tracking and control.
Read the full ManEx Case Solution >>
|
|
|
|
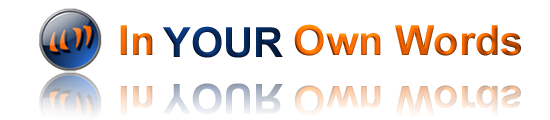 |
INVENTORY BY PROJECT AND CUSTOMER
"We choose to purchase through our MRP system but when special projects come up we still attempt to use existing P/N's and/or expedite material manually."
"We look at excess inventory to charge [the] customer accordingly."
- Nick, TX
"[Our process] takes a long long time. [It] depends on the customer and number of BoM's and parts."
- Michael, IL
|
 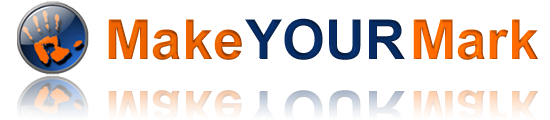 |
Please share your ideas and insights on a topic below. Use the questions to direct your response. You can submit your thoughts to mym@manex.com by clicking the topic title. Where appropriate and space permitting, we will post responses in a future newsletter so all may benefit.
Work Order Numbering
How do you use Work Order Numbering?
Do you let the system set the numbers, or do you manually set them?
Do you add intelligence to your Work Order Numbers?
If so, what type of intelligence do you add?
What benefits have you seen from this approach?
Performance Tracking
How do you track expected and actual time on a job?
What is your standard variance between expected and actual?
What do you do when you find a variance in labor hours?
Do you factor actual labor hours into your future pricing?
What benefits have you seen from this approach?
To suggest a new topic please send an email to mym@manex.com.
|
©2008 All Rights Reserved.
ManEx Minute is a bi-weekly email distributed by ManEx, Inc. |

Developing with YOU in mind! |
|
|
|
|
|
|