1. ManEx Minute - 18 - Counterfeit Components |
|
|
"Do you realize if it weren't for Edison we'd be watching TV by candlelight?"
-Al Boliska
|
|
February, 25 2009
Issue 18
Greetings,
You may have noticed an increase in discussions on counterfeit components and their impact on manufacturers. In addition to numerous web sites and articles on this subject interested companies can attend seminars addressing this issue.
According to EMSnow "Key findings and best practice recommendations from the Department of Commerce's landmark survey on counterfeiting will be presented during the keynote address at CARTS 2009, March 30 to April 2 in Jacksonville, Fla."
While this is critical for some, according to our most recent survey, 45% of you aren't concerned with counterfeiting and believe that 25% or less of the components you use are at risk for counterfeiting.
However, over 76% of you have had at least once instance and issue with counterfeit components. For this reason, this issue will address possible concerns with counterfeit parts and suggest ways to mitigate the problem.
As always, we look forward to your participation and feedback as you gain new insights and become a more effective provider of Electronic Manufacturing Services.
Sincerely,
David Sharp
ManEx, Inc.
|
Business Case - Inventory Control
|
Work Center Priorities and Scheduling
|
North Eastern Company (NE Company)* is interested in gaining customers in the military and medical fields. Because of the high reliability requirements, and the increasing proliferation of counterfeit components, they are concerned about their ability to identify and prevent the use of counterfeit parts.
*Name has been changed
|
Business Case Solutions
|
Although counterfeit components are not common, they are becoming more common and it is important for companies working in high reliability products to have...
|
ManEx Case Solution
|
ManEx has several standard and optional features designed to help with managing and mitigating the risk of counterfeit components.
Read the full ManEx Case Solution >>
|
|
|
|
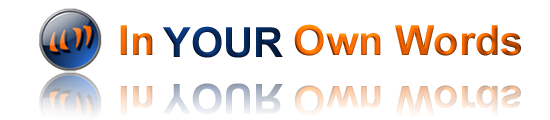 |
COUNTERFEIT COMPONENTS
We deal with high reliability products and have to avoid counterfeit components at whatever the cost. We cannot use any parts or purchase from any source that is not 100% guaranteed to provide authentic and certifiable components.
- Greg, CA
"We only have had one issue with counterfeit parts and that was several years ago."
- Mark, WI
|
 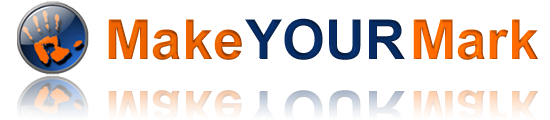 |
Please share your ideas and insights on a topic below. Use the questions to direct your response. You can submit your thoughts to mym@manex.com by clicking the topic title. Where appropriate and space permitting, we will post responses in a future newsletter so all may benefit.
On Hand Inventory By Project
How do you track inventory purchased for a project or customer?
Do you allocate parts by customer?
How often do you provide customer's a update of their inventory exposure?
How long does it take to gather information on inventory purchase for a customer?
Work Order Numbering
How do you use Work Order Numbering?
Do you let the system set the numbers, or do you manually set them?
Do you add intelligence to your Work Order Numbers?
If so, what type of intelligence do you add?
What benefits have you seen from this approach?
To suggest a new topic please send an email to mym@manex.com.
To see additional topics, please click here.
|
©2008 All Rights Reserved.
ManEx Minute is a bi-weekly email distributed by ManEx, Inc. |

Developing with YOU in mind! |
|
|
|
|
|
1.1. Case Write-up - 18 |
|
Business Case - Inventory Control
|
Counterfeit Components
|
North Eastern Company (NE Company)* recently completed their ISO 13485 certification. They have been working with several medical device companies and are confident they will win some new business in the near future. One of the potential customers has had issues with their current supplier providing product with counterfeit components. This is a significant concern for the potential customer and they want to know how NE Company can avoid using and providing counterfeit parts.
In their 26 years of business, NE Company has never had a significant issue with counterfeit components and management believes that over 93% of their part numbers are not at risk for counterfeiting. For this reason, they are comfortable with their current practices and procedures for the majority of their purchasing activities.
However, because of the demand and strict requirements for the components used in the potential customer's products, they estimate that nearly 32% of those components may be at risk for counterfeiting. This increased risk and concerns from the potential customer have prompted management to review their practices.
How can NE Company identify components at risk for counterfeiting? How can they reduce the risk of purchasing counterfeit components? What tools are available to increase communication between purchasing and receiving to ensure the parts ordered are in fact the parts going through receiving?
|
|
1.2. Business Case Solutions - 18 - Counterfeit Components |
|
Business Case Solutions
Although counterfeit components are not common, they are becoming more common and it is important for companies working in high reliability products to have established procedures and methods to identify and control counterfeit components.
Common Signs of Counterfeiting*-
- Part Markings - Improperly marked components are a key indicator of counterfeiting. The markings may be poor reproductions of the original designs, double markings as the counterfeiters stamp over the original etchings, or incorrect sizing and layout (i.e. 3 lines of text instead of 2).
- Incorrect Device Lead Type - if a component should have gold leads, but does not, the part should be considered suspect and investigated before use.
- Lead Conditions - damaged, tinned, or corroded leads are common indicators of counterfeit components.
- Component Condition - reclaimed parts sold as new have suspect reliability. Some indicators are improper or missing documentation, minor damage, presence of solder on leads, etc.
Common Sources of Counterfeit Components-
- The most common source of counterfeit components are non-franchised distributors. While they are not the ONLY source, they are responsible for a majority of counterfeit components.
Methods for Prevention -
- Trusted Sources - All at-risk components should be purchased only from the manufacturer or franchised distributor. If this is not possible, then incoming components should be thoroughly inspected and tested to ensure their validity.
- Incoming Inspection - Inspecting incoming inventory for known and possible signs of counterfeiting should reduce the risk and increase reliability.
- Certificates of Compliance - requiring a certificate of compliance and verifying the certificate will not completely prevent counterfeit parts (due to the possibility of counterfeit certificates), but it can significantly reduce the probability and provide traceability.
- Quality Systems Audit - periodically auditing the suppliers quality processes can ensure they are doing everything possible to prevent the shipment of counterfeit components.
*information comes from "Counterfeit Electronic Parts" report by Brian Hughitt, NASA 2008
|
|
1.3. ManEx Solution - 18 - Counterfeit Components |
ManEx Case Solution
ManEx has several standard and optional features designed to help with managing and mitigating the risk of counterfeit components.
- Material Risk Code - this is an optional field used in inventory control, and MRP. It allows users to establish risk procedures and ensure that buyers are following those procedures.
- Product Data Management* - users can attach component documentation to each part within the system. This can be part specs, images, markings, etc. This information is electronically distributed to purchasing, receiving, and production.
- Inspection and First Article Requirements - users can indicate if a component always requires incoming inspection and first article or enforce the inspection for any given order as needed.
- Supplier ratings* - based on supplier performance over time, users can establish supplier ratings to help identify at-risk or restricted suppliers and thereby reduce the risk of counterfeit components
- CofC tracking - users can indicate CofC requirements and automatically communicate those requirements to suppliers. They can also upload the CofC into ManEx providing electronic documentation of component compliance.
- Purchase Order Notes - Once at-risk components are identified, buyers can communicate requirements to suppliers, and receiving.
NE Company was able to identify the at-risk components and establish procedures from purchasing through production to ensure that only authentic and approved parts were purchased and used. The checks and verifications were clearly visible throughout the process and increased their customer's comfort level and confidence.
Since implementing the procedures, they prevented three instances of counterfeit components and have a perfect record. In fact, the customer was so pleased with the procedures and results that NE Company has started promoting their practices to existing and potential customers as a differentiator from the competition.
*may require the purchase of an optional module
|
|