1. ManEx Minute - 17 - WC Priorities and Scheduling |
|
|
"The farther backward you can look, the farther forward you are likely to see."
-Winston Churchill
|
|
February, 11 2009
Issue 17
Greetings!
Welcome to the new face of ManEx Minute. We want the newsletter to be as beautiful as it is helpful and have therefore updated the look and feel.
I want to thank everyone who has participated for your positive feedback and suggestions. You have helped make ManEx Minute what it is today. We continue to upgrade and update this newsletter to make it better and more applicable to your business. So far, the response has been very encouraging and we hope that you will continue to benefit from our efforts.
For this issue, we will focus on production scheduling and communication. It is critical for sustained success and profitability.
According to our last survey, more than 76% of your orders, on average, are shipped on time. That is pretty good, but almost everyone indicated that improvements in communication and prioritization would improve performance. Sometimes that requires significant process changes, and sometimes small changes can bring significant results. After you read the case, let us know what you think.
As always, we look forward to your participation and feedback as you gain new insights and become a more effective provider of Electronic Manufacturing Services.
Sincerely,
David Sharp
ManEx, Inc.
|
Business Case - Inventory Control
|
Work Center Priorities and Scheduling
|
North Eastern Company (NE Company)* strives to provide accurate lead-times and costs for its customers. They also strive to make it clear to their customers that the lead times they provide are realistic and that orders should be placed with more than enough time to allow for the highest quality and best on-time performance. Despite their efforts, many of their customers still place orders with shortened lead times while expecting the same quality and pricing.
|
Business Case Solutions
|
To effectively schedule each work center and increase on-time performance without increasing capacity...
|
ManEx Case Solution
|
ManEx has several standard and optional features designed to help with identifying bottlenecks and setting...
Read the full ManEx Case Solution >>
|
|
|
|
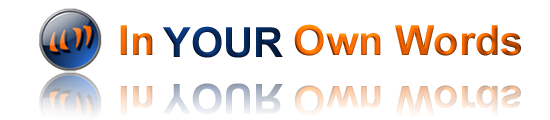 |
WC PRIORITIES & SCHEDULING
"We issue monthly schedules for pick & place equipment and daily schedules for all assembly
personnel by WO.
"Daily schedules quickly show where capacity is limited and monthly machine schedules high light where over and under loading is occurring.
"Our ISO Certification is based on 96% or better and we are consistently above 96%."
- Shep, IN
"If we can start a job on time it will finish on time. Purchasing, Non-conformances, verifying weigh bills, etc. all play into it."
- Bob, UT
|
 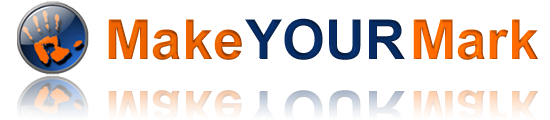 |
Please share your ideas and insights on a topic below. Use the questions to direct your response. You can submit your thoughts to mym@manex.com by clicking the topic title. Where appropriate and space permitting, we will post responses in a future newsletter so all may benefit.
Counterfeit Components
What percentage of your parts are considered at-risk for counterfeiting?
What are you doing to ensure your components are not counterfeit?
Have you been impacted by counterfeit parts? If so, how?
Are you promoting your counterfeit measures to your customers to increase confidence?
On Hand Inventory By Project
How do you track inventory purchased for a project or customer?
Do you allocate parts by customer?
How often do you provide customer's a update of their inventory exposure?
How long does it take to gather informaiton on inventory purchase for a customer?
To suggest a new topic please send an email to mym@manex.com.
To see additional topics, please click here.
|
©2008 All Rights Reserved.
ManEx Minute is a bi-weekly email distributed by ManEx, Inc. |

Developing with YOU in mind! |
|
|
|
|
|
1.1. Case Write-up - 17 |
|
Business Case - Inventory Control
|
Work Center Priorities and Scheduling
|
North Eastern Company (NE Company)* strives to provide accurate lead-times and costs for its customers. They also strive to make it clear to their customers that the lead times they provide are realistic and that orders should be placed with more than enough time to allow for the highest quality and best on-time performance. Despite their efforts, many of their customers still place orders with shortened lead times while expecting the same quality and pricing.
Over the last six months, NE Company's on-time delivery performance averaged about 82%. Within a week after the due date, they were able to complete over 97% of their orders. Given the reduced lead times, and on-time deliveries for most of the order, many of the customers are ok with the performance and have not complained too loudly or too often. But an 82% on-time history doesn't look good, and it is difficult to maintain the breakneck pace required to achieve even that level of performance.
Currently, NE Company sets their schedule based on the WO Due Date. When production loads are reduced and customers place the order in plenty of time, this method is simple and very effective. However, as the load increases and lead times decrease, it becomes more of a challenge and often fails to deliver the full order on-time. Additionally, the extra work often reduces profitability and increases the opportunities for defects and errors.
Production blames the customers for lack of foresight and sales for overbooking the schedule. Sales blames production for asking for more orders yet failing to deliver as promised. Top management just wants to remain profitable and keep the good reputation they have worked so hard to develop.
Management has reviewed their capacity and load and is convinced that they should be able to increase throughput with existing loads and capacity and improve on-time performance to well over 97%. They believe the scheduling and prioritization methods are partly to blame, but haven’t yet figured out how to make it work.
What other methods can they use to schedule production and increase throughput without adding capacity or reducing load? How can they most effectively communicate priority changes to production? How often do they meet their commitments, but fail to meet the customer's expectations?
|
|
1.2. Business Case Solutions - 17 - WC Priorities and Scheduling |
|
Business Case Solutions
To effectively schedule each work center and increase on-time performance without increasing capacity, NE Company must be able to identify bottle necks and set schedules and priorities based on several factors.
Identify Bottlenecks-
- Load vs Capacity - It is critical for production to have a clear picture of load vs capacity for each work center in production. Having access to this information well in advance will allow production to adjust schedules and capacities before it becomes an issues and delays deliveries.
- Infinite vs Finite Capacity - Finite capacity planning systems will level the load for each work center and push out less important jobs. This makes it easy to see when all current jobs will be completed given current capacity constraints. However, it can make it difficult to identify when work centers will exceed capacity thus allowing managers to adjust capacity and increase throughput as needed. Infinite capacity planning systems do not level the load and push out deliveries. This will clearly identify when a work center will reach or exceed capacity and allow for adjustments as needed. However, this method does not make it easy to identify when all current jobs will be completed without changes to current capacity unless the schedules are manually adjusted.
- Common Work Centers and Activities - It stands to reason that work centers and activities that are used more often and across more jobs are more likely to be the source of a bottle neck. This is typically a great place to start looking for bottlenecks and working to streamline the process.
- Material Availability - Depending on the type of component and the number of times it is placed on an assembly, material shortages can have as great or greater impact on on-time performance than capacity and load. It is important to have visibility of all parts needed for each work center and whether you currently have or will have enough on-hand in time to complete the job for any work center as scheduled. If critical components are missing, then production may need to reset priorities and schedules.
Scheduling and Prioritization Methods-
- Customer Importance - It is common for CMs to push jobs important to customers or for large customers. While this may satisfy the customer, it is very likely to decrease overall on-time performance and establish a precedence the customer will want to repeat. That isn't to say it should never happen. However, it should be used sparingly and after proper consideration. If the other methods are used properly scheduling will become less of an issue and even the large customers should be able to get their orders on-time without hurting all other jobs, customers, and performance.
- Material Availability - This method will reduce the priority for any job without sufficient material on-hand to complete the job. Since some components are too difficult and/or time consuming to place late in the process, these parts can and should affect when a job is sent through each step in the process. However, many components can be placed later without significant impact to schedule or processing time required. Therefore, it is important to identify which components should and should not impact scheduling if they are missing.
- WO Due Date - Setting schedules based on due date is one of the simplest methods of scheduling. It requires little effort to maintain and each Work Center will have the priorities set automatically. However, for this method to allow for the highest possible on-time performance sales needs to confirm that sufficient capacity and lead-time are built in to the order before placing it in the queue. If the load is near capacity or the customer doesn't allow enough lead time, this method is inadequate for completing all jobs on time.
- WC Bottle Necks - Identifying the Work Centers with the highest load and increasing the priorities on all jobs that must pass through that Work Center can increase throughput without increasing capacity. For example, if ICT is the largest bottle neck and only 1/3 of the jobs need ICT, then those jobs should have a higher priority in all prior Work Centers. This will ensure they have as much time as possible to pass through ICT and that ICT is always at capacity without down time. Although this will not guarantee that all jobs will ship on time, it should increase the likelihood.
- Job Slack Time - The difference between the processing time required to compete a job and the available work hours until a job is complete can be called a job's slack time. Using this method will increase a job's priority as the time required approaches the time remaining. This is a dynamic method that may increase and decrease a job's priority as it moves between work centers based on the performance of each work center. This also means that a job with less slack time, but later due date may get a higher priority. For example, a job with 3 days of actual processing time required and 7 work days until it is due will have a lower priority than a job with 10 days of actual processing required and 12 work days until it is due. This method will help ensure the highest possible on-time performance, but requires that processing and available work times are setup accurately and completely.
ManEx Case Solution
|
|
1.3. ManEx Solution - 17 - Work Center Priorities and Scheduling |
ManEx Case Solution
ManEx has several standard and optional features designed to help with identifying bottlenecks and setting work center priorities and schedules.
- Dynamic Production Scheduling* - This screen allows production managers to monitor and track a jobs progress through the production floor. It sets priorities based on slack time and allows managers to adjust those priorities as needed. It also communicates those priorities to production workers so they know the most important jobs, in their work centers, at any given time and can focus their attentions where it can do the most good. The production schedules are adjusted each day to account for the process made that day and the update priorities as needed.
- Capacity Critical Path* - This screen gives immediate visibility of potential bottle necks by allowing the user to select a date (grouped by day, week, or month) and/or work center and see the capacity and load. This information is available as soon as a job is in the system and scheduled. This can provide sufficient time to adjust the schedule or the capacity as needed and maximize throughput.
- Open Work Order List - This screen provides a summary of all open jobs in production and allows users to sort by WO, Customer, Due Date, and Status. It also shows the build quantity, how many are complete, and the balance. This can help production workers know which jobs are in process and when they are due.
- WO Shortage Summary List - This list identifies component shortages by WO, WC, and part number. By displaying which parts are currently missing and expected delivery quantities and dates, this screen helps production identify critical shortages and adjust the schedule as needed.
- Web Based Order Simulation* - This screen allows users to enter and assembly, requested quantity, and requested date. It evaluates processing time and material availability and indicates how many can be done by the requested date, when the full quantity can be done (worst case scenario), and the components currently preventing an on-time delivery with short quantity and expected lead time.
- Customer On-time Delivery Reporting* - The report in eManEx will allow users to show on-time delivery performance for selected assemblies or customers over a selected period of time. This enables production to evaluate their current processes and process changes to see how it impacts on-time performance. This report is also available as a third party ad-on. As part of our plans to help all users get the most of their system and leverage our focus and features, we have the first user develop report available for on-time delivery reporting. This report was created by a ManEx user and can be used by other ManEx users to evaluate their on-time performance and make necessary adjustments and improvements. If you are interested in this report, please contact sales@manex.com.
NE Company started using slack time and capacity in their prioritization and have realized important gains in their on-time performance. Within a three month period, they were able to increase their on-time deliveries to over 90% and they expect that number to steadily increase as they complete the previously existing orders already behind schedule.
As they expected and hoped, with few exceptions, they were able to achieve this level of performance without rushing their orders and accruing extra man hours on each job, thereby preserving their profits and quality.
*may require the purchase of an optional module
|
|