1. FAQ for Quality/Engineering Module |
1.1. FAQ - Bill of Material (BOM) |
1.1.1. BOM Unit of Measure | If a user tries to enter in a fraction of a number for a part that is setup with a UOM of EACH or EA, they will receive the following warning:
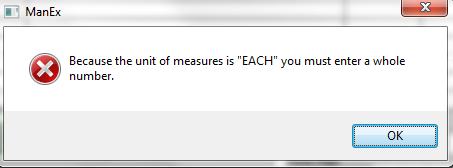
EACH or EA in the system is considered a whole number and you will not be allowed to enter in a fraction of a number for those UOMs. The reason is you can NOT actually have a Fraction of whole number. If you need to have a fraction of a number on the bom, etc. . . we recommend that you use a UOM other than EACH or EA then the system will allow you to enter in the Fraction.
The maximum number of decimals in the BOM quantity is 2, allowing for 1/100th of an item. The reason is so the system operates properly (mainly the MRP and Kitting). If we allowed a fraction of a number to be used the order or kitting quantities may be incorrect for the customers that use the MRP and Kitting modules. If users need a finer resolution, you may want to consider using a different UoM than EACH, and buy in one unit and use a fractional unit for inventory (e.g. Purchase in Gallons, and Stock/Issue in ounces). The system will allow you to create other categories in the UOM to correct this problem. With this fix, both the MRP and Kitting works correctly.
|
1.1.2. Do Users Tie Parts to Specific Operations to Help Issue Separate Kits to Various Dept? |
Do Users Tie Parts to Specific Operations to Help Issue Separate Kits to Various Dept?
ManEx does have the ability, and many users utilize it, to identify the work station where components will be used. This is identified in the BOM. Kitting may then kit specifically for work stations for which the parts are consumed.
|
1.1.3. How does the Std Bld affect the Std Cost Roll-up? |
1.1.4. How do I create a list of BOMs with and without components loaded? | ManEx has created a utility called bomlisting.exe that will create an excel file of all make parts in ManEx and designate which have components and which do not.
stats |
part_no |
revision |
descript |
Has Components: |
000-0000259 |
|
PAGER,OPTION LCR5000H |
Has Components: |
000-0000258 |
A |
PAGER,OPTION LCR5000H |
Has Components: |
910-0000288 |
|
QPLTESTBOM1 |
Has Components: |
910-0000290 |
|
QPLTESTBOM2 |
Has Components: |
000-0000324 |
|
SMART DISPLAY |
Has Components: |
COH-0011-0855 |
A |
COH-0011-0855 |
Has Components: |
000-0000335 |
|
Test BoM |
Has Components: |
910-1001.1 |
A |
Test-1A |
No Components: |
910-1000 |
A |
Test-a |
No Components: |
910-247767-01900 |
9 |
PCB,MAIN W/O ATP |
No Components: |
5FG6HJ791 |
|
Test 1 |
No Components: |
910-TEST2 |
|
TEst2 |
Although this executable is not commonly available, it can be made available upon request. If you would like a copy of this file, please contact cs@manex.com requesting this executable. |
1.1.5. Possible Reasons why the Std Cost Roll differs from the Cost BOM Rpts |
The values displayed should be in sync with the BOM with Std Cost Report values. The following may be why the Standard Cost Roll is different from the Cost BOM Reports.
a) On the costed BOM Report for a Make/Buy assembly we display the value of the BOM in the costed report, but that total is NOT used in subsequent rollups to higher levels only the standard cost is.
b) In Kit Default Setup , user can exclude scrap and setup scrap in Kitting, MRP, and Cost Rollup, this will overwrite what user check in the BOM. Therefore, if user checks "Setup Scrap" checkbox in BOM, but checks to exclude in cost roll, the costroll will not calculate setup scrap cost, but BOM will always calculate setup scrap cost if the Setup Scrap checkbox in check in BOM.
|
1.1.6. When using the Excel printing option for a Bill of Material, why is there multiple columns used for the reference designators? | Question: When using the Excel printing option for a Bill of Material, why is there multiple columns used for the reference designators?
Answer: When there is a large number of reference designators loaded on the BOM for a particular item and the BOM is exported from the system to an excel spreadsheet the Reference Designators will be split into separate columns. We could attempt to make some changes to the excel spreadsheet and place all Ref Designators in one column but then you would be unable to read the contents. We are aware of the capability to create a larger length cell using excel 2003, but the engine that produces the excel sheets from Visual FoxPro is an older version and this is where the limitations are coming from.
Resolution: At this point in time the Excel output will have to remain as is.
|
1.1.7. Why doesn’t MRP use Alternate Parts in its Calculations? |
|
1.1.8. Why am I unable to Change Customer Name on BOM? | Q. Why am I unable to Change the Customer Name on a BOM?
Possiblity #1
The system will not allow to reassign customer for the assembly, which has subassembly with the customer attached to it. It is true that the subassembly does not have any CONSGN parts, but it is also true that this subassembly is attached to a customer. And unless you detach the customer from that subassembly first, you will not be able to change the customer for the top level.
Possibility #2
Unable to actually change the name of the sub-level BOM. Run the Bill of Material , outdented report and you will see all of the top assemblies which are using this part as a component. Once you find all of those records and updated accordingly you should then also be able to edit the desired bom record customer name to match.
|
1.1.9. Why is MRP giving me Demands for an Inactive BOM? | Q. Why is MRP giving me Demands for an Inactive BOM?
A. Changing the BOM status to Inactive will NOT remove the MRP demands you MUST Inactivate the part number in ICM to remove the MRP demands.
Resolution. Add a warning when user trys to create a SO and/or WO for a Make part if the BOM status is something other than "ACTIVE". Also, modify the BOM module so that the quote module will automatically change the BOM status to "Quote" when a quote for the BOM is initiated, and change it back to ‘Active’ when quote is approved.
|
1.1.10. Why isn't the Customer Part Number Displayed on the BOM Main Screen? | Q. Why isn't the Customer Part Number Displayed on the BOM Main Screen if the part source is "BUY"?
A. The customer part number is only shown on the BOM Main Screen when it is a "CONSG" part, unless user has checked the box to "Display Customer # for the "BUY" parts if BOM linked with a customer" located on the find screen, (however this may slow down the results). This is why the customer part number for a "BUY" part is only shown on the Detail screen and not the BOM Main screen for a "BUY" part.
|
1.1.11. Why are the XLS output truncating or exporting corrupted information? | Issue: When exporting the Bill of Material reports to XLS output some of the items are truncating or corrupting the information that is exported out of the system.
Answer or Possible Solution: Check the description loaded for that item and make sure that it does not start with a quotation mark. During exporting of the files to XLS the excel does not like the quotation mark and may cause truncating or corrupting results. Please make sure that there are no quotation mark as the first character of the description, and that should resolve the issue.
|
1.1.12. When the "Bill of Material with Ref Desg & AVL" report is exported to XLS format why does it show ALL AVL's? | Q. When the "Bill of Material with Ref Desg & AVL" report is exported to XLS format why does it show ALL AVL's?
A. When the "Bill of Material with Ref Desg & AVL" report is exported to XLS format the system dumps all raw data and it can not be a controlled form. When the "Bill of Material with Ref Desg & AVL" report is printed to screen or paper, the requirements of this particular report is that it needs to see parts even if all Mfgrs on the list are not approved, then in the report form the form manipulates the data dump to show only the approved MPNs and filters out non-approved MPN's.
Resolution: The raw data does however have a column named "Uniqanti" if the "Uniqanti" has a "NULL" value the MPN is approved. ManEx suggests that you create an XL template which would have a macro that will remove MPN information if "Uniqanti" is NOT "NULL". Then you can simply copy our XL output into this template and it will show the correct data.
|
1.1.13. SYSTEM LOCK ERROR - What to do when if System Lock appears when Attempting to Edit a BOM? |
What to do if system locks up while attempting to edit a Bill of Material, and the following messages appear:
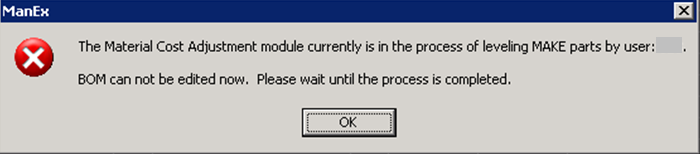
Or if user attempts to launch a new Leveling process within the Standard Cost Adjustment module and the following message appears:
.
A resetcostrolllock.exe has been made available within this article. Running this program from the Manex Directory will remove the Standard Cost Adjustment Lock placed on your tables.
Reason: The lock will occur either by the user saving a record lost connection to the network (or computer crashed) Normally the lock is only on for a small amount of time to allow the first user to finish saving the record and then the next user usually then can proceed. If Users becomes impatient during the leveling process and Clt+Alt+Delete out of the system, this too would place the permanent lock on the records and would then require you to run the resetcostrolllock.exe file.
|
1.2. FAQ - Express Import to BOM or Quote (QBI) |
1.2.1. Why do I keep receiving a Uniqueness of index message when import to BOM? | Q. Why do I keep receiving a Uniqueness of index message when import to BOM?
A. There are a few scenarios that could be causing this message to appear:
- A same part, with different description associated with different product, will cause this message to appear upon import.
- If the Auto numbering is turned OFF and user has entered the same part number to items with same description but different customer part numbers will cause this message to appear.
When loading one BOM/product at a time into the ManEx System it checks to see if the users might have the same part number, but with different descriptions or different customer part numbers loaded on the spreadsheet. If found then it would display that information in an XLS spreadsheet for the users to address.
|
1.2.2. Why can you not go back to the previous tab when using the QBI module? |
Q. Why can you not go back to the previous tab when using the QBI module.
A. Unfortunately, there is not a lot we can do about this. It builds the import BOM as it proceeds and doesn’t save the old versions to revert back to if you decide to go back. However, we are adding more verification to help prevent the user from accidentally proceeding to the next tab before they are ready.
|
1.2.3. When I import a BOM (within the QBi module) with no Internal part number assigned, does it automatically go to the next sequential number? | Q. When I import a BOM (in QBi) with no Internal P/N assigned, does it automatically go to the next sequential number?
A. The user has the option of auto numbering or manual numbering.
AUTO Numbering: The main concern when creating a part number is not to ensure a sequential part numbering by class, but rather the ability to track additional information (AVL, on hand qty, where used, standard cost) by one internal part number. Because of this, the actual number doesn't really matter as long as the system knows which additional information to attach to the internal part number. This is why ManEx works as well with a manually created number as with an auto-generated number. If you use auto-numbering, the numbers can be arranged on the shelf in ascending order (even if there are gaps between the numbers). The auto-numbering in ManEx simplifies the part number creation process and provides a count of the total parts in your system (141-0001000 is the 1000th part loaded).
MANUAL Numbering: This will allow user to use any part numbering method.
|
1.3. FAQ - ECO, BCN, Deviation (EBD) |
1.3.1. Can users leave parts removed through ECO in the kit for costing purposes? | Q: Can users leave parts removed through ECO in the kit for costing purposes?
A: The ECO won't remove parts, if you click that specific work order to take effect to use the new created assembly (with parts removed), you will have to click "Update Kit" button in Kit module in order to remove the parts, and if you have issued parts already, the system will ask you where you want to put those qty. (This is if the parts are already pulled for the kit before the ECO was approved).
|
1.3.2. Can we use the ECO module to process BUY part changes? | From time to time, a BUY part changes revision because the manufacturer changed specifications for the part. So things that might change would be the description, maybe the material type code, and maybe the related documents. The question arose because users wanted a place to track the changes in revision, like they can with assemblies.
PROPOSED SUGGESTION:
We are going to suggest that the users copy the old buy part to a new one with a different revision, but then they would have to keep track of why they changed both of them in a notes field for both parts. |
1.3.3. Do line shortages pull through with an ECO? | Question: Do line shortages pull through with an ECO?
Answer: No |
1.3.4. If the user has already recorded kit shortages before an ECO, will they still be displayed after the kit is updated? | Question: If the user has already recorded kit shortages before an ECO, will they still be displayed after the kit is updated?
Answer: Yes, they should still be there. |
1.3.5. How to Handle items left in FGI at old Rev after ECO udpate. | If user creates a SO and WO for product #123 Rev. A qty of 15. Transfer 7 into FGI leaving a balance of 8 in process. Creates a packing list and invoice for 5, leaving 2 in FGI and 8 in process. Creates an ECO to change the revision from A to B. The SO and WO update to Revison B for qty of 8 that was in process. The qty of 2 in FGI remain at Revision A and will not be affected by the ECO changes.
The user has the following two options to choose from in order to be able to ship the qty of 2 remaining in FGI at Revision A:
1. Create a rework work order for the new revision, and a shortage for the old revision, rework as necessary, and then place in FGI again under the updated revision.
OR
2. They can do an Inventory Handling Issue for the old revision, then receive the new revision back in. This assumes there is a very simple and non-functional change to the updated revision. |
1.3.6. How to Handle Temporary Deviations. | How to Handle Temporary Deviations.
It will depend on the sequence in which the user creates their work orders.
If users want the deviation applied to the work orders due within a date range, then when the work orders are created, based on the deviation they would have someone add the alternate part to the kit and remove the part it replaces. In the work order notes, reference to the deviation should be made.
If users want the deviation applied to the work orders as they are going through kitting within a certain time frame, then they will need to put a copy of the deviation on the "Do NOT Use" part and when they go to kit, the storeroom needs to make the same change to the kit described above.
Either way, the reference to the deviation on the kit will provide the authorization and record that the deviation was applied.
|
1.3.7. Will an ECO work on a Phantom Make Assembly? | Question: Will an ECO work on a Phantom/Make Assembly?
Answer: Yes
|
1.3.8. Why doesn't my approved deviation appear as approved in the shop floor tracking? | Q. Why doesn't my approved deviation appear as approved in the shop floor tracking?
A. Because deviations are temporary, they must have an expiration date before they will appear as approved in SFT (Shop Floor Tracking). Ensure that the deviation has an effectivity and expiration date and the deviation status is Approved before checking in SFT. Once the status of the deviation has been changed from Approved to Complete the deviation will no longer appear in SFT.
Deviation is for Reference only, it allows the users to have documentation as to why the temp change to the product was made, etc. .. but, if you are truly changing the product, then it should require a Revision change and there for be an ECO or BCN not a Deviation.
|
1.3.9. When an ECO is created to change the Revision or Part Number then why wouldn't the customer part number be changed also? | Q. When an ECO is created to change the Revision or Part Number then why wouldn't the customer part number be changed also?
A. We can not assume just because you are changing the revision of your Internal Make Product that your customers are also changing their Revision for their part number. You could have multiple Customer Part number linked to the Same Internal Part number for different Customers all together. Again we can not assume that just because you are increasing your internal Part number revision that all Customers are also increasing their Revision.
Resolution: When time allows, ManEx will add a checkbox to the EBD/update-create records screen that is captioned “update BOM CPN Rev ”, and defaulted to true (checked). Modify the logic so that the customer part number for the customer associated with the BOM (as determined by the inventor.bomcustno) is automatically updated to match the new revision in the ECO (if there is one). But before proceeding, check to see if the checkbox has been unchecked, and skip it if it has been unchecked . Enhancement Ticket #1461.
|
1.4. FAQ - WO Traveler Set-up |
1.4.1. How can ManEx help with Setting Work Center Priorities and Scheduling? | Q. How can ManEx help with Setting Work Center Priorities and Scheduling?
ManEx has several standard and optional features designed to help with identifying bottlenecks and setting work center priorities and schedules.
- Dynamic Production Scheduling * - This screen allows production managers to monitor and track a jobs progress through the production floor. It sets priorities based on slack time and allows managers to adjust those priorities as needed. It also communicates those priorities to production workers so they know the most important jobs, in their work centers, at any given time and can focus their attentions where it can do the most good. The production schedules are adjusted each day to account for the process made that day and the update priorities as needed.
- Capacity Critical Path* - This screen gives immediate visibility of potential bottle necks by allowing the user to select a date (grouped by day, week, or month) and/or work center and see the capacity and load. This information is available as soon as a job is in the system and scheduled. This can provide sufficient time to adjust the schedule or the capacity as needed and maximize throughput.
- Open Work Order List - This screen provides a summary of all open jobs in production and allows users to sort by WO, Customer, Due Date, and Status. It also shows the build quantity, how many are complete, and the balance. This can help production workers know which jobs are in process and when they are due.
- WO Shortage Summary List - This list identifies component shortages by WO, WC, and part number. By displaying which parts are currently missing and expected delivery quantities and dates, this screen helps production identify critical shortages and adjust the schedule as needed.
- Web Based Order Simulation* - This screen allows users to enter and assembly, requested quantity, and requested date. It evaluates processing time and material availability and indicates how many can be done by the requested date, when the full quantity can be done (worst case scenario), and the components currently preventing an on-time delivery with short quantity and expected lead time.
- Customer On-time Delivery Reporting* - The report in eManEx will allow users to show on-time delivery performance for selected assemblies or customers over a selected period of time. This enables production to evaluate their current processes and process changes to see how it impacts on-time performance. This report is also available as a third party ad-on. As part of our plans to help all users get the most of their system and leverage our focus and features, we have the first user develop report available for on-time delivery reporting. This report was created by a ManEx user and can be used by other ManEx users to evaluate their on-time performance and make necessary adjustments and improvements. If you are interested in this report, please contact sales@manex.com.
|
1.4.2. What does PPM mean? | Answer: PPM (Part Per Million) this field is where you would enter in the defect opportunities.
In the ROUTING screen, the PPM is opportunities for defects. What this means is there are a certain number of things that can go wrong and cause a failure of the assembly. The PPM is the total number of defects that might occur at each work center in the assembly of the product.
Example: If you have a board with one part on it, you can start with PPM = 2: the board can be wrong, and the part can be wrong. But then you can expand on that by counting the number of leads on the component. It is possible that if there are eight leads on the component, any one of them may have a bad solder joint. So now the PPM is 2 + 8 or 10. Now it is possible to insert the component backwards, so polarity is another PPM. So now the PPM is 10 + 1 or 11. It may be that the part is correct, the leads are ok, but it is defect. Now the PPM is 11 + 1 = 12. The 8 leads on the component must go somewhere, so there will be traces or conductors on the board. Each of these may be a defective due to the manufacturing process by creating either shorts or opens. So now the PPM is 12 + 8 or 20.
Lets say that there are two such parts on the board. Now the PPM rises by the same complexity (but not the board itself), so now the PPM is 20 + 19 or 39 PPM.
There may be similar PPM's for each step in the process, depending on what is done in the process, and which parts might be affected.
So, if the work order is for a total of 100 boards (and we didn't add any other PPM's), then the PPM for the lot would be 3900.
What PPM is readlly intended to convey, is a measure of the quality of the boards assembled. It is the number of defects observed in the lot divided by the total opportunities for defects. In this example, if one board was found with one unsoldered pin, that would account for one defect out of 3900 possible defects, or approximately 256 PPM (1/3900*1,000,000).
Obviously, most assemblies will have much more PPM's than this example. The Customers of Manufacturers sometimes require certain PPM quality or penailize the CM. Of course, the Manufacturer will then attempt to make the PPM's as high as they can, to lower the defects. |
1.5. FAQ - Product Data Mgmt (PDM) |
1.5.1. Why are my notes within the PDM module disappearing? |
Q. Why are my notes within the PDM module disappearing?
Possible scenarios that could cause the notes to ‘disappear’ from the PDM module.
- Someone may have updated the routing by removing the WC that had the notes on it. Even if it is immediately replaced back into the routing before saving the changes, the notes will be lost.
- Where could be a case where two users are saving changes on the same product within the PDM module. First user adds WO instruction notes then saves while second user was just editing the tooling and fixture or adding a separate note, etc. If second user saves then the notes added by the first user may get overwritten or wiped out.
- It also could be that a user did go into the PDM and accidently removed the notes manually.
- Also keep in mind that if you are using the copy feature the notes on the existing routing will be removed and/or replaced with the new routing notes.
|
1.6. FAQ - Statistical Quality Control (SQC) |
1.6.1. What does DPMO Mean? | Q. What does DPMO Mean?
A. DPMO means defects per million opportunity. What does this mean? Defects means the number of things wrong observed in the inspection of a part, or board assembly. Users can decide how to count defects. They may say that a resistor with two leads that are not properly soldered is counted as two defects. But they could also count it as one defect, since it is one part that was assembled incorrectly. Or, a 24-pin integrated circuit in a 24-pin package might be counted as one wrong defect if it was inserted backwards. Or one wrong defect if one of the pins was not soldered correctly.
Now consider what opportunities mean. It is the number of possible defects that can occur on a product. Again, this is subject to a lot of interpretation. In the case of the two-lead resistor, one might say that if it was incorrectly installed, that was one opportunity for a defect. If one of either leads were soldered incorrectly, there are two more opportunities for defects. If the resistor was ok, but the wrong value, it might be counted as another opportunity for defect (now we’re up to four opportunities for defects).
Now let’s say there are 10 resistors on a board being inspected. That is 40 opportunities for defects. And let’s say that we are INSPECTING 100 boards at one time. The opportunity for defects is now 4000. And lets consider the IC with 24 pins. Each pin is an opportunity for a defect. Likewise, getting the wrong part is an opportunity for a defect. So is getting the part installed incorrectly or missing altogether. Let’s say there are 10 IC’s on the same boards we’re inspecting. That’s then 250 opportunities per board, or 25,000 opportunities for the 100 Inspected boards. So now, in this lot, so far, we have 29,000 opportunities for defects. To that we can add similar opportunities for the many other parts on the board, as well as some for the board itself. Taken to an extreme, a user may wish to include an opportunity for every hole on the board, because some of them may not have a “through-hole” connection. (Usually though, this is taken into account in the original inspection of the board when they are received.)
So, after all is counted up, a lot like we’re discussing could have 100,000 opportunities for a defect. Remember that this is the number of boards actually observed through inspection. If a sample of a lot is taken, then the opportunities for defects is based on the sample size observed, not the whole lot size.
Now back to DPMO. Let’s say that an inspector examined all 100 boards in this lot, and found that there were two leads (anywhere) that were not soldered correctly. This then amounts to 2 defects per 100,000 opportunities, or 20 DPMO.
It used to be that as a contract manufacturer, we were held to a specific DPMO value for our products for this customer. However, even though the number of defects observed was the same, we could manipulate the DPMO by simply counting more possibilities as an opportunity, thus driving down the reported DPMO, It’s amazing how many things you can find to go wrong if you look hard.
Long and short – Only the boards actually examined are counted in the calculation, and how the opportunities are calculated is up to the user. That’s why we have the place in the routing for them to enter the number of opportunities for each work center. Each work center can have a different number of opportunities, depending on the operations performed at the work center.
|
1.6.2. What if a workstation is unable to view any of the graphs within the ManEx system? | Q. What if a workstation is unable to view any of the graphs within the ManEx system?
A. User must have the Silent Client files install on their workstation. First install the Silent Client 8 and then Silent Client 9 files on that workstation.
|
|