1. FAQ for Material Planning Modules |
1.1. FAQ- Purchase Order Management (PO) |
1.1.1. How are PO Confirm/Remit and Receiving information Edited? | Question: How are PO Confirm/Remit and Receiving information Edited?
Answer: The user must first enter at least one set of data in the Purchase Setup/Receiving and Billing screen. The user may enter as many Receiving Addresses and Billing Addresses as desired, but one must be checked as the default address for each.
The user must then find the Purchase Order in the Purchase Order module. Then, while on the main Purchase Order screen, press the Edit button. Then, press the Confirm/Remit to button, and make the changes needed by selecting an address if different from the default (or if PO entered before default established). After making the changes on that screen, exit it back to the main screen, then SAVE the changes.
This same procedure applies to the Receiving screen, and after it, the Send Invoice To screen.
|
1.1.2. How can the user Purchase inventory parts as "Taxable"? | Question: How can the user Purchase inventory parts as "Taxable"?
Answer: The user may enter them as MRO and enter the applicable part number into the part number box and check them as taxable.
Please refer to the Purchase Order Management module if user wants to include MRO lines with inventory purchases on Purchase Order.
|
1.1.3. How Can ManEx help Manage the Risk of Counterfeit Components? | Q. How Can ManEx help Manage & Mitigating the Risk of Counterfeit Components?
ManEx has several standard and optional features designed to help with managing and mitigating the risk of counterfeit components.
- Material Risk Code - this is an optional field used in inventory control, and MRP. It allows users to establish risk procedures and ensure that buyers are following those procedures.
- Product Data Management - users can attach component documentation to each part within the system. This can be part specs, images, markings, etc. This information is electronically distributed to purchasing, receiving, and production.
- < Inspection and First Article Requirements - users can indicate if a component always requires incoming inspection and first article or enforce the inspection for any given order as needed.
- Supplier ratings* - based on supplier performance over time, users can establish supplier ratings to help identify at-risk or restricted suppliers and thereby reduce the risk of counterfeit components
- CofC tracking - users can indicate CofC requirements and automatically communicate those requirements to suppliers. They can also upload the CofC into ManEx providing electronic documentation of component compliance.
- Purchase Order Notes - Once at-risk components are identified, buyers can communicate requirements to suppliers, and receiving.
|
1.1.4. Why does ManEx no longer have the Change Order tracked per each Change? | Question: Why does ManEx no longer have the Change Order tracked per each Change?
Answer: The difference between 8.0 and 9.0 is; ManEx removed the details for every set of change orders and removed the CO from the linkage, leaving only one (current) set of data associated with each Purchase Order. The purpose for doing so was that having almost duplicate files for every change order was creating such large databases that we were losing the ability to quickly create and change Purchase Orders. There is no link related to the change order, but there continues to be the same linkage through POMAIN to POITEMs and from there to POITSCHD.
|
1.1.5. Why does ManEx only allow assigning an Item Note or PO Note within the View mode and not the Edit or Add mode? | Q. Why does ManEx only allow assigning an Item Note or PO Note within the View mode and not the Edit or Add mode?
A. The programmers designed the "note" screen so it allows the user to view/add/remove the notes assigned without closing and opening the popup screen each time and for every PO. Let's say you have 30 items on the PO and each item has some kind of note assigned.
You can select an item click on the "Assign Note" button and view/add/remove notes. Click on the "Save" button to commit the changes to the note, but do not exit the "note" screen. Now you can go back to the PO screen and select the next item, the "Note" screen will refresh with the next item "Note" information.
You can even find a new PO without closing the "Note" form. This way it saves you time going from item to item and clicking on the "Note" button, saving and exiting the "Note" screen and clicking on the note button again. Currently the "Note" screen is using different data sessions and has to be saved independent of the PO.
If we would allow the notes to be updated in the "Add"/Edit" mode and the note would be saved, but changes to the PO cancelled afterword, we could have a problem with the data integrity.
|
1.1.6. Why doesn't the supplier address show on the Purchase Order printout? | Question: Why doesn't the supplier address show on the Purchase Order printout?
Answer: The supplier address that prints on the purchase order comes from the Confirm To information entered for the Supplier. If there is no confirm to address entered in the Supplier Information module, then it will not print on any purchase order created using that supplier information. (More than one address may be entered.) One address must be designated as the default address. Then the user returns to the purchase order and edits the supplier information, by clicking on the edit button, then on the confirm/remit to button, and selects the correct (or only) address. Then saving the purchase order, and re-approving it, and printing the purchase order will now have the supplier confirm to address.
|
1.1.7. Why am I receiving a System Error when attempting to Print Closed/Cancelled PO's? | Q. Why am I receiving a System Error when attempting to Print Closed/Cancelled PO's?
A. It may be due to a VFP limitation on the number of lines in the list box. This is a know bug in VFP when a list is longer than a certain number it will produce an error.
Resolution: We suggest that you use "Single PO#" selection and type in the PO in question and you should be able to proceed with no errors.
NOTE: I f the user prints out the Purchase Order form AFTER some receiving has occurred against that PO, then ONLY the un-received still open amounts will print on this form. Any line items COMPLETELY RECEIVED will NOT display on the PO form.
|
1.1.8. What is the typical method for tracking expediting fees for components? |
When Creating the Purchase Order (#221) a Buyer can add an MRO item for qty of 1 for the extra charges such as expedite,etc. as displayed below.
You will then need to receive both items on the same PO Receipt (for PO #221) as displayed below:
These items will then need to be Reconciled as displayed below:
Then Transferred to Accounts Payable as displayed below:
|
1.1.9. What would cause a Purchase Order to remain “OPEN” even when the balance is “0”? | Depending on the users SysSetup for when Change Order Approvals is required, sometimes the PO's appear to get stuck open. But is it due to the fact that your change order settings are not forcing the refresh of the order status.
To be able to close those PO manually, you need to modify either the price or qty to some number and then without saving change it back to what ever the original number was. Now save the record. this will trigger the change of status to become "EDITING" and need of approval. When "Approval" button is clicked the PO status will become "Closed"
|
1.1.10. When should I use a Service PO instead of an MRO PO? | Question: When should I use a Service PO instead of an MRO PO?
Answer: There are times when the user wants to issue an immediate receiver and have the invoice forward directly into accounting. For example: When there is no tangible item to receive such as services performed that do not create, modify or add value to a product – plumbers fix the leak, etc.
- A Service PO changes to a Closed status once it’s approved. The invoice may then be reconciled in Accounting without a receipt.
- Most companies use a manual signature approval of Service Invoices by the Requestor instead of matching an invoice to a receipt.
Please refer to the Purchase Order Managment module and Accounts Payable module.
|
1.1.11. SYSTEM LOCK ERROR - What to do if System PO Lock appears? | Q. What to do if system locks up while in Purchase Order records, and one of the following messages appear:
A. There is a Resetpolock9.exe located within the Manex Root Directory. Running this program will remove the PO Lock placed on your tables.
Reason: The lock will occur either by the user saving a record lost connection to the network (or computer crashed) or there are two users attempting to save the exact same Purchase Order record at the same time. This lock is to prevent duplications. Normally the lock is only on for a small amount of time to allow the first user to finish saving the record and then the next user usually then can proceed. If User #2 becomes impatient and does not wait for the temp lock to clear and Clt+Alt+Delete out of the system, this too would place the permanent lock on the records and would then require you to run the resetPOlock9.exe file.
Prevention: If users see a message that the file is currently in use have them wait a few minutes and try again, not to Clt+Alt+Delete out of the system. |
1.1.12. SQL-SYSTEM LOCK ERROR - What to do if System PO Lock appears? | Q. What to do if system locks up while in Purchase Order records, and one of the following messages appear:
A. There is a PO_lock.sql attached below and/or there is a stored procedure sp_unlockPoFlag as part of the database. Go into the SQL Server Management and run the attached script, this will remove the PO Lock placed on your tables.
Reason: The lock will occur either by the user saving a record lost connection to the network (or computer crashed) or there are two users attempting to save the exact same Purchase Order record at the same time. This lock is to prevent duplications. Normally the lock is only on for a small amount of time to allow the first user to finish saving the record and then the next user usually then can proceed. If User #2 becomes impatient and does not wait for the temp lock to clear and Clt+Alt+Delete out of the system, this too would place the permanent lock on the records and would then require you to run the PO_lock.sql file.
Prevention: If users see a message that the file is currently in use have them wait a few minutes and try again, not to Clt+Alt+Delete out of the system.
|
1.2. FAQ- Material Requirement Planning (MRP) |
1.2.1. What do some of these WO actions mean? | -Work Order Past Due: WO is not firm planned and the WO qty is still required to fulfill the SO demand. however WO is not complete yet so behind schedule on the WO due date.
-Cancel Work Order:WO is not kitted and not firm planned and qty's are not required to fulfill any demand.
-No WO Action: WO due date is still not past due to fulfill the demand requirement. Qty of WO matches demand requirement, Kit is not started and not firm planned either. Therefore no actions required by the user. |
1.2.2. WHY MRP IS SETUP LIKE IT IS: | Listed below are a few things users need to understand about why MRP is setup like it is:
1. Most EMS companies have small margins and need to move quickly. If MRP waits for a planner to change a WO because they made a mistake, buyers may have already ordered excess inventory and that will hurt cash flow. This has significant potential negatives and may result in parts that cannot be returned or used.
2. MRP will tell them to buy/produce what and how they said they want to do it. The whole point is to reduce the reviews and updates required by buyers and planners. If the settings are correct, users can purchase and produce as indicated. If they are not correct, they should be adjusted rather than trying to work around them and ignore the actions. Most EMS companies are Make to Order. However, standard make-to-stock should be handled with mins and safety stock, not random increases in WO qtys.
3. Most EMS companies deal with many exceptions to the rule. This may be why they don't want to adjust settings. If that is driving the need to build outside standard settings, we have added many checks so that they can tell MRP that they are deviating from the standard and it can ignore the specific instance.
4. Firm planned (FP) cannot and should not be used as a catchall for incorrect settings and has gotten many companies in trouble. Any company that needs to use FP all the time is not setup correctly. However, it is a perfectly acceptable and suggested method for dealing with exceptions. If they do not use FP UNLESS it is an exception and they know about the exception, they should not have the issues he described.
5. We have reports available to show excess inventory after all MRP demands.
6. Kanban can be closely simulated with min/mults and safety stock. Once again, system settings are critical. But, using this method, they will have enough on hand and ready to replace actual demand.
|
1.2.3. Can Users Access System when MRP is Running? | Question: Can Users Access System when MRP is Running?
Answer: It is fine to have users in the system at the time the MRP trigger is running. MRP will still just use the information that is saved into this temp table at the time of the run. Any changes to records after that point will have to be captured in the next MRP run. Keep in mind, depending on the size of your data files, this MRP run could take hours to complete, and in addition may slow down the response time of the ManEx system during this time. This is why many elect to run the MRP at night when traffic is the least.
|
1.2.4. Can the MRP PN Range Find Message be Changed when PN entered does NOT Exist in ICM? | When a user enters in a part that DOES NOT exist within inventory in the MRP Part Number Range Find feature - why don't we display the same message that is displayed in the MRP Find by Parent BOM feature "The Part/Revision typed in does not exist in the inventory tables" rather than displaying "NO MRP records were located for the criteria Selected" that we currently display.
There are a couple reasons why we cannot display "The Part/Revision typed in does not exist in the inventory tables" message rather than the current message we display "NO MRP records were located for the criteria Selected" when user enters in a part that DOES NOT exist within the inventory in the MRP Part Number Range Find feature.
1. If we were to change the valid in the part number field the user would no longer be able to go to the Find screen and leave the part number field blank and just click on the OK button to display ALL of the parts. Instead the user would get the message "The PartRevision typed in does not exist in the inventory tables" and no parts would be displayed.
2. Another reason is if the user would like to find all the parts within a range, say 100-0000000 to 199-9999999. The part numbers at each end of the range might not exist, but the parts within the range would be displayed under the current system.
Reference Ticket #2616 for further detail.
|
1.2.5. Do Users Run MRP and Base Purchases from Action Reports? |
Do Users Run MRP and Base Purchases from Action Reports?
ManEx MRP is tailored especially for electronic manufacturing, and helps manage AVLS for all their customers. It also has great flexibility in the ability to control the sensitivity to order changes, various leadtimes, and offset times. It is the biggest reason Manex users have the system. When aggregating requirements to cover multiple orders for the same parts, Manex has the ability to determine the most efficient distribution of AVLS for a given part.
|
1.2.6. Does ManEx have a report that shows the demand requirements for components used on a product for the next 12 months? |
Question - Does ManEx have a report that shows the demand requirements for components used on a product for the next 12 months?
Option 1 - If the Customer provides a rolling forecast for the User to use over the following 12 months time, then that forecast can be placed in the forecast module, and MRP results would include the parts needed over that period, as well as create the order actions for them.
Option 2 - But if a more simple route is desired, take the total amount of product expected and use that number to create a Kit Material Availability simulation report. If there are many products involved, create an excel sheet for each and combine them.
You would find the Kit Material Availability report mentioned within the Kitting module and you would run this report with the Simulation option. If you have more than one product, then you have to run the report for each product and dump it to XLS format and manually combine them through XLS after that.
|
1.2.7. Does ManEx have a MRP Differential Report? | Q. Does ManEx have a MRP Differential Report?
A. ManEx does Not have a report like this at this time but here is a temporary work around to follow:
- Setup up a bogus top level, to include all of the top level assemblies involved. Use the quantity needed for each assembly as the quantity for the assembly in the top level.
- Once this is done, prepare to run MRP. Run MRP (without the bogus top level), and make a copy of the MRPACT table. Copy that table to an Excel Format.
- Then put in 1 of the bogus top level assembly, and run MRP again. Make a second copy of the MRPACT table (don't use the same name as before).
- Make an Excel copy of that second listing.
- Remove the 1 bogus top level part requirement and run MRP again to clear out the momentary information.
- Compare the two lists, and whatever is different is the result of the proposed additional parts (unless you don't run the second MRP very quickly after the first).
- It sounds complicated, but I think it is eassier and more accurate than running the kit shortage report and trying to fathom it out from there.
|
1.2.8. Does MRP Consider Allocations? | Q. Does MRP Consider Inventory Allocations?
A. Inventory Allocations are not a factor in MRP demands, because it could result in excess inventory.
For example, if 100 parts are allocated to a WO due in October. Meanwhile another demand for the same part comes in with an earlier required due date such as July. If we honored allocations, then MRP would recommend a new PO for the July demand even though there is sufficient parts already on hand. This would tie up capital in excess inventory.
Right now MRP would use the inventory for the earliest demand and would recommend a new PO for the later demand. |
1.2.9. Does MRP Consider Dock to Stock days? | Q. Does MRP Consider Dock to Stock days?
A. The Dock to Stock value entered in the ABC Type Setup Screen is taken into consideration for MRP leadtime calculations in the projected requirement of the receipt of purchased parts. For Example: if the Dock to Stock time is 3 days, and the kit start date is 8/22/08, then the due date for the buy components would be 8/19/08, and the order date would be based on the purchasing leadtime to receive the parts by 8/19/08. So the Dock to Stock time is used to move back the due dates of items purchased in time for kitting
|
1.2.10. How is the Lead Times for a Level BOM calculated? | Q - How is the Lead TImes for a Level BOM calculated?
|
1.2.11. How is the Customer Projected Excess Inventory Report Intended to Work? | Q. How is the Customer Projected Excess Inventory Report intended to work?
A. This report will list out parts that are used ONLY on BOM's assigned to that customer. If the part is used on any other BOM not assigned to the same customer, then the part is excluded from the report.
|
1.2.12. How does Pull-in Push-out days affect MRP? | Question - How does Pull-in Push-out days affect MRP?
Answer - Pull-in/Push-out uses the order policy, demand due date, demand quantity, minimum order qty, and safety stock to determine if an existing order needs to be rescheduled and/or have the qty adjusted when the demand date changes. It does not allow for grouping orders outside the order policy setting, or produce more than is needed for a specific demand (over the min order quantities or safety stock).
For example: If the order policy is set to daily, and the existing work order is setup to meet a monthly demand, the user will get an action message to adjust the work order according to a daily grouping of the demand (reduce the existing wo qty and create new wo(s) as needed). In the same scenario, if the order policy was changed to monthly, then the single work order should not be affected.
If the user wants to maintain an order policy that is NOT consistent with their desired grouping, they must either firm plan the order, or create a separate Work Order for each demand grouping. The latter would result in multiple Work Order’s due on the same day with a qty set for each demand’s required qty rather than one Work Order on that day for the total demand.
|
1.2.13. How does MRP Demands work with Safety Stock? | Setup an Inventory Part #101-0002525 with Safety Stock of 500 for Mfgr - KOA (if Safety Stock is listed in Genr system will use qty from any of the AVLs to full fill the Safety Stock). Dale having a Qty on Hand of 100. (Note: Safety stock is calculated at the AVL level not part # level)
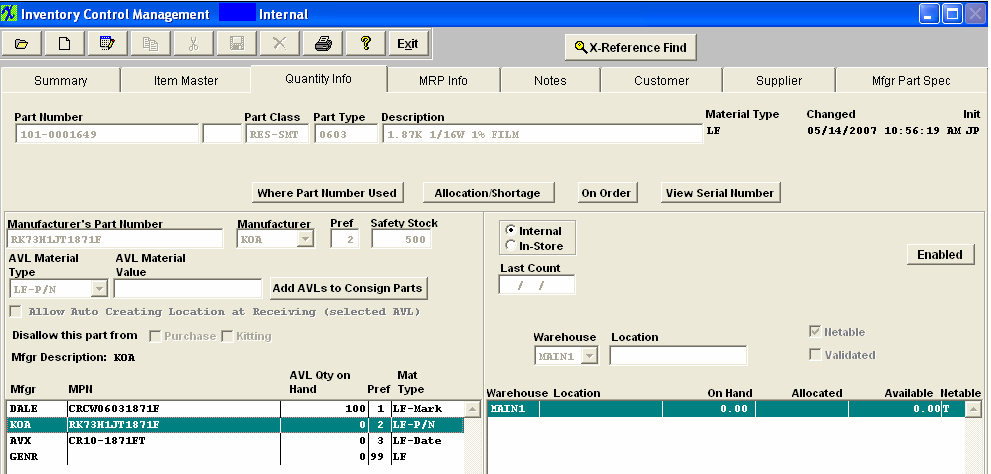
MRP Demands - Displaying Required Qty of 500 for Safety Stock and 450 for a WO release - MRP Action List is saying to Release PO's for qty of 500 and 350
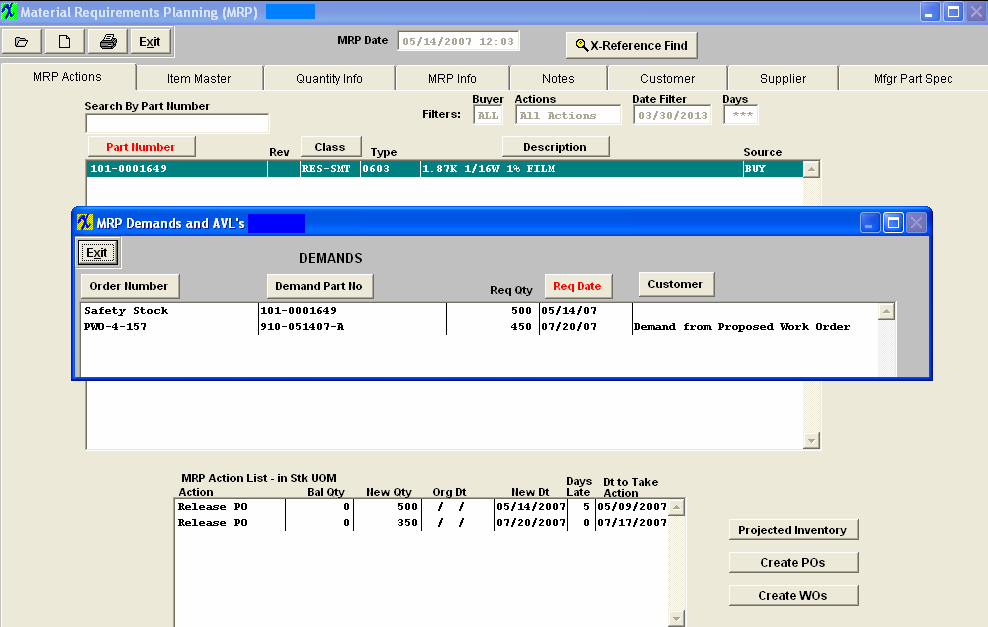
Projected Inventory is displaying that there is available inventory of 100. To fulfill the requirements user needs to release a PO for 500 and a PO for 350 (using the available qty to full fill the WO demand.
Drill down to Create POs and here is where system will tell you which mfgr to release POs for to full fill the demands.
|
1.2.14. How does MRP Calculate the Make/Phantom Leadtimes? | If the Make/Phantom is used as a Top-Level Assembly MRP demands are calculated using the Kit lead times and production lead times setup in the Inventory Control Module.
For example: If the M/P part had a 2 day kit lead time and a 3 days production lead time. MRP demands for the M/P will allow 5 days total (2 days kit + 3 days prod from M/P)
If the Make/Phantom is used at a Sub-Level . MRP calculates both the Top-Level leadtimes and the Sub-Level (Make/Phantom) leadtimes setup in the Inventory Control Module.
For example: If the M/P part had a 2 day kit lead time and a 3 days production lead time and the top-level had a 1 day kit lead time and a 2 day production lead time. MRP demands for the M/P will allow 10 days total (2 days kit + 3 days prod from M/P) + (1 day kit + 2 day prod from Top level) + (2 days for the weekend)
NOTE: A TRUE phantom does not require any lead times and should be left blank. - BUT . . . if for some reason user needs to enter a lead time for a TRUE phantom ManEx does have the capability.
|
1.2.15. How does MRP Handle Blank/Null Effectivity Dates? | Q. How does MRP Handle Blank/Null Effectivity Dates?
|
1.2.16. How does the AVL Pref Codes affect MRP? | Question: How does AVL Pref Codes affect MRP?
Answer: When the users have a part set with the Order Action Policy (OAP) of "Lot for Lot" MRP will provide suggested actions per each requirement, in this setting the MRP will ALWAYS apply the Pref Code rule (See Article #943 for further detail on the Pref Code rule). But, then when a part happens to have the OAP set to "Daily, Weekly, Monthly, etc..." the calculation of the suggest MRP actions become more complicated. In aggregation mode, there may be a number of different requirements all for the same exact part. And those requirements may be spread over some period of time, e.g. one week. In the weekly OAP, we will accumulate all of the different demands for the part, and present an order action for the sum total of that parts requirements, setting it due for the earliest day of the week selected in the system setup.
SInce the requirements for the same part may have different AVLs for different demand, as generated from different customers and different BOM's, and there may not be one AVL that is common to all demands. When this happens, MRP performs an analysis of these AVL requirements and determines what the best mix of AVL's and quantities would be to most efficiently satisfy the diverse AVL demands. This results in selecting the AVL that has the most universal application to the requirements as the greatest number of parts needed. Next the demands are searched for remaining AVL demands (those not satisfied by the first round), and performs the same analysis for that AVL, resulting in an order demand to also by X quantity of the next AVL. If there are still any demands that are not covered by the first two AVL's selected, the process is repeated until all demands are covered. The result may end up that in order to meet the specific AVL demands for a variety of customers and BOM's several AVL's are ordered with varied quantities for the same internal part number.
In doing this calculation, and in order to provide the most efficient buying information, we could NOT include the AVL preference considerations. It would defeat the purpose of maximizing the order efficiency and minimizing the number of parts orders. But remember, this is NOT the issue, when "Lot for Lot" aggregation is selected for the parts, then the order preference takes precedence.
If the preferred AVL quantity needed for a period (day, week, month, etc...) is exactly equal to the largest quantity for any other AVL for a part, the program will substitute the preferred AVL for any other AVL and only in that case. If the quantities are not equal, then our optimization algorithm will apply as explained above.
Note: If the part is on a Customer BOM and assigned to that Customer then the Preference's from the Customer part number will dictate how other modules within the system (MRP, Purchasing, Kitting, Allocations) determine what is suggested or defaulted into the screens.
|
1.2.17. How does an RMA impact MRP? |
How does an RMA impact MRP?
If the user enters a scheduled delivery for both the returning item(s) (a minus quantity, those coming back to the user) and the reship items (a positive quantity, returning the items to the customer) on the RMA. MRP will display a demand for a Rework Firm Order for their replacements, to satisfy the return to customer requirements based off the scheduled delivery date entered in the RMA.
Note: When the RMA Receiver is created the Work Order due dates are generated automatically based on the date the RMA was created. This date may need to be reviewed and adjusted to match the RMA reshipment date. MRP will NOT instruct you to reschedule a rework firm work order, so it is important to make sure these two dates match.
RMA's will NOT drive MRP:
-
if there are no scheduled delivery dates entered
-
if the Rework Work Order that was generated has been completely scrapped out
-
if product moved into FGI was accidentally shipped against another order
-
if the Rework Work Order build qty was changed to 0 and the Work Order closed.
If the RMA only has the return to User, (a minus quantity), but not a return to the customer(a positive quantity), then the product will become available for other orders, if it makes it to FGI. If the user scraps it in this case, there is NO impact to MRP, as there is no requirement to replace the items. If there are other requirements for the same item, however, then MRP will use the rework order as a source for additional demands.
There would be no reason to create an RMA to ship only, without the return to our user. We would call that a Sales Order. Which would be visible anywhere.
The Word attachment <<RMA Orders Affect MRP.docx>> will display how MRP works if the RMA's are properly processed through the system.
|
1.2.18. If the MFGR has GENR anywhere in the mfgr name, MRP will treate it like a GENR part. | If there is GENR in the MFGR name the system will treat it like a GENR part. If user is reporting AVL conflicts within MRP, they may want to check the MFGR name to be sure it does not contain the word GENR. Example: 3M-GENR; GENRAD, etc.
Example Print Screen have been attached: Inventory PN 101-0002418 with qty on hand in AVL "KOA", but only approved "GENRAD" on BOM, MRP demands will consider "KOA's" qty on hand, (which is incorrect). Inventory PN 105-0002825 with qty on hand in AVL "GENRAD" but only approved "DALE" on BOM, MRP demands will NOT consider "GENRAD" qty on hand, (which is correct).
|
1.2.19. Is MRP Available in Net Change Mode or Re-Generation Mode Only? |
Is MRP available in Net Change Mode or Re-Generation Mode Only?
ManEx MRP, when initiated, gathers all information relating to inventory, work order shortages, purchase orders, sales orders, work orders, and forecasts, and develops order actions based on very complicated algorithms, many which are controlled by the user.
|
1.2.20. MRP demands for Sub-Assemblies not Listed on SO? | Q. If a BOM with sub-assemblies exist, will MRP requirements be created for the Sub-assemblies when only the top level is entered into the Sales order?
A. MRP will explode the requirements down 99 levels for all components and subassemblies reporting to a top level assembly required by a sales order. For further information see the Bill of Materials Management procedures and the Materials Requirements Planning Management producedures..
|
1.2.21. This Article explains the process MRP goes through to optimize the on hand inventory to requirements. | This Article explains the process MRP goes through to optimize the on hand inventory to the requirements.
First it finds how many requirements there are for each MRP, not the quantity but just the number of requirements and then the requirements are processed from the lowest to the highest number of requirements. In this example the requirements are as follows:
AVL Number of Requirements
AVX 1
DALE 2
KOA 1
Panasonic 2
Genr 3
At this Point there are only 2 Inventory Parts with Inventory
AVL On Hand Qty
KOA 24,000
Genr 8,472
Because the KOA is a specific requirement the KOA requirements are process before the GENR and the inventory is consumed by this requirement.
MRP Requirements
Date Needed Qty Approved AVL's On-hand Balance
05/05/11 24,000 All AVL's Approved -0-
After all of the KOA inventory has been appplied to the requirements, then the GENR is process and applied as below:
MRP Requirements
Date Needed Qty Approved AVL's On-hand Balance
07/26/10 8,472 Genr. Dale -0-
08/27/10 MRP Instructing User to Release PO for qty of 3,000 (Genr)
08/27/10 3,000 Genr, Panasonic -0-
The GENR inventory is consumed by the 7/26/10 requirement so MRP is instructing the user to release a PO to meet the (Genr) requirement of 3,000 on 8/27/10.
|
1.2.22. Will MRP generate Buy demands for components if I do not create Work Orders? | Yes, MRP will generate buy orders for all Demand (Both top and sub level assemblies). MRP demand comes from three places: SO’s, WO’s and Forecast. MRP assumes that you will generate work orders when needed, and generates the buy orders so that the material is ready when it is time to generate the work order.
Some users prefer not using the Work Order creation in the Sales Order module and believe that it is inefficient to have the work orders created before they are needed. The MRP will say when they are needed, and the user is better off waiting until that time to due so, since it alleviates extra handling should the conditions of the assembly change in the meantime.
|
1.2.23. Why is MRP not recognizing Min/Mult when SO is assigned to a Project? | Q. Why is MRP not recognizing Min/Mult when SO is assigned to a Project?
A. If there is a Min/Mult setup for an Inventory part, and the SO is assigned to a project, you will need to check the MRP Default Setup screen. If Honor Projects is flagged MRP will NOT consider the Min/Mult, but if Ignor Projects is flagged then MRP will consider the Min/Mult.
|
1.2.24. Why is MRP demands being Calculated from Kit Shortages and Not Prod Offset LT? | Q Why is the MRP Demands being calculated from the Kit Shortages and Not the Production Offset Lead Times?
A Once the parts have been pulled to the kit and the kit status is changed to "Kit in Process" MRP is designed to calculate from the Kit Shortage and production lead time NOT from the production offset lead times. Once the parts have been pulled to the kit, the system is assuming that the shortages are needed by the WO due date, rather than the Production offset lead time, so MRP then calculates using the production lead time and due date of the WO as the date the materials must be on hand, MRP no longer takes the production offset lead time into consideration
|
1.2.25. Why is MRP giving me demands for the past? | Q. Why is MRP giving me demands for the past?
A. If the demand falls after the systems last calendar date, MRP will default the demand to the 1st day within the calendar date.
For Example: If your First System Calendar date is 01-01-2002 and your Last System Calendar date is 12-31-2007.
You create a SO with a delivery beyond the last calendar date of 12-31-2007, MRP cannot calculate the correct date so it will default to the first calendar date of 01-01-2002. Once the system calendar is updated and MRP is re-ran the demands should be correct.
User does receive several warnings when saving the SO that the calendar in System setup needs to be updated.
|
1.2.26. Why is the sub assembly MRP demand after the Top Assembly MRP demand? | If you look at the BOM for product 910-110205 you will see that part 990-110205 has an offset of 20 days, that means that it is not needed until 20 days after the Work order for 910-110205 has been started.
 |
1.2.27. Why is MRP Recommending to Create a Phantom Assembly? | Q. After running MRP, it recommends the creation of a Phantom Assembly. How is this possible?
A. It's not. The MRP is only showing you what the source of the requirements for the parts contained in the phantom are. Without showing this information, users become lost trying to understand where the demand is. Knowing that a part is used in the phantom, the user can then look up the requirements for the phantom to ascertain the parent requirements. MRP recommendations for phantoms may be safely ignored. |
1.2.28. Why is MRP instructing me to release two PO’s on the same day? | Why is MRP instructing me to release two PO’s on the same day, because the demand for 55 on 10/06/08 can use either AVL?
The MRP processes the records in date order. In this case this is how the records were processed.
date Qty Req Order Amt Excess Release PO's for AVL's Approved AVL's
09/29/08 45 100 (Min Qty) 55 AVX CR21-181JT AVX CR21-181JT
09/29/08 25 --- 30 AVX CR21-181JT AVX CR21-181JT
10/06/08 55 100 (Min Qty) 75 AVX CR21-181JT AVX CR21-181JT & AVX CR21-181JP
10/06/08 35 100 (Min Qty) 65 AVX CR21-181JP AVX CR21-181JP
Note that orders for the same day are sorted with the highest required quantity being processed first, this is because of the way the program processes the data for the most efficient use of inventory and excess from minimum orders and POs. We can only process one item at a time and because of that.
Many years ago we tried to look at all of the requirements for a part at the same time but we found that this meant that we were processing every record many times, in the case above each item would have had to be process 16 times to get the desired results ( The reason is that each record must be processed against every other record to see if the dates, AVLs, minimum orders and order multiples can be matched, if there were 5 items it would be 25 times, 6 items - 36 times, just take the square of the number of items.). We found that the MRP became very very slooooooooow even on a small data set, so we went to this method of processing each record only once.
|
1.2.29. Why doesn't MRP use Alternate Parts in its Calculations? | Q. Why doesn't MRP use Alternate Parts in its Calculations?
A. Alternate Parts are components that can be used to replace existing parts if needed, they are not the preference. Alternate parts are assigned in the AVL and Reference Designator tab within the BOM module and they are assigned to specific parts on the BOM. Each part on the BOM can have one or more alternate parts. Frequently, this is because the alternates (although acceptable) are more expensive. This information is provided in the event that the user CANNOT find the required parts for the kit and/or the MRP order actions are too far out to meet requirements. This information provides guidance on which parts the user may substitute in the kit, by creating a manual kit shortage for the alternate part, then checking (in the kit screen) that the original part is not needed, so it will come off the shortage list which drives MRP. When the alternate part is added to the kit, the MRP will look for those parts as well, and create order actions if necessary. This also will give Manufacturers visibility of the parts so they can be used in production if needed, but will only use the parts if the original is not available.
This part needs verification - IF the user has setup customer AVL's for the selected alternate part in the Item Master, and IF the work order is for that customer, then the customer AVL will be honored in kitting. Otherwise, the standard AVL at the internal part level will be used.
If the MRP factored in alternates and you had stock on the more expensive component, MRP would not give the action message to buy the original. This could easily lead to an unnecessary increase in the cost to build the assembly.
For example:
Given
1. Part A (the original) is used 10 times on a BoM and had a standard cost of $0.25.
2. Part B had a standard cost of $0.35, and can be used as needed.
3. If total demand for Part A is 2000 and you have 0 on hand, but you have 2500 of part B on hand.
MRP would try to use part B instead. You would now have spent an extra $200 on placing that part (a 40% increase). On the other hand, if MRP does not consider the alternates, the buyer would try to order 2000 of part A. If they can only get 1800, they can fill in the missing pieces (in kitting) with part B and only increase the total spent on the job by $20 (a 4% increase).
|
1.2.30. Why, if a Work Order Status is Rework the Product will not be Available for Demand? | This is to make sure that reworked products are checked and transfered into FGI before they are considered available, otherwise, MRP might be counting on product that might not make it to FGI. If the user has high confidence that the reworked parts are going to be available when they get to FGI, then you would mark the Order Status as Rework Firm, and the product will be considered as available to meet demand. |
1.2.31. Why are my demands appearing duplicate times in MRP? | Q. Why are my Demands appearing Duplicate times in the MRP Action screen and MRP Projected Inventory screen?
A. If the same part is listed on the BOM multiple times assigned to different item numbers and/or different Work Centers, MRP will display the part for each item number and/or each Work Center. It does not combine the qty's per BOM. The quantities being being displayed are correct and are not driving extra demands.
|
1.2.32. Why are my PO demands in MRP not being displayed in the Create PO Screen? | Question: Why are my PO demands in MRP not being displayed in the Create PO Screen?
If parts in MRP have demands to release a PO but are not being displayed in the Create PO screen you may want to check the following:
1. Check to see if the "Do Not Allow Purchase" box is checked in the Inventory screen.
2. Check the "Effectivity Date" and the "Obsolete Date" on the BOM.
3. Check for Spaces in the MFGR Code.
|
1.2.33. Why MRP does not Consider Consigned MRP demands? | MRP does not include consigned parts in any order actions. Shortages for Consigned parts are available after kitting the work order for the assembly. The user may also use the Availability Report in Kitting to ascertain consigned shortages based on a proposed quantity of a product.
Manex policy is that it is up to the Users customers to keep them supplied with consigned inventory. This is in accordance with most MRP policies and programs.
|
1.2.34. What Conditions would make the Numeric Overflow Message to Appear during a New MRP Run? | 
This message appears because somewhere you have a date or date-related field, or a conversion field that is causing a number to be out of range for the size allotted for the answer. Three possible causes are:
- Production Calendar is not configured correctly
- SO, WO dates are incorrect
- An assembly contains itself as a subassembly.
Examples might be if if you have entered a due date somewhere for 06/21/2070 instead of 06/21/2007, or entered a leadtime of 38 months instead of 38 days. Or, possibly a conversion factor for purchasing that resulted in a number too big for the system.
MRP will still run okay, and the user can usually find the error by looking at the dates on the action messages - they will be at one end or the other if their production calendar. If it is a quantity problem, the number will simply show as ****, indicating an over flow number.
|
1.2.35. What Is The Purpose Of The MRP Date Filter? | The Filter section on the MRP screen allows the user to tailor the order actions displayed. By selecting a specific buyer code, and purchase order actions only, then only the actions for the buyer are selected.
The date filter allows the user to define how far in the future they wish to see order actions. Any order actions falling on a date before the filter date will be shown. Any order action that is shown also shows all of the subsequent actions recommended by MRP. A part for which the first order action falls later than the filter date will not be shown or printed. In this manner, the user may narrow down the list of actions to be taken to only those due in the next week.
If MRP is run once per week, then the order action filter date should be 5 to 7 days, to cover actions required until MRP is run again. The frequency of running MRP depends on the turn-around times of the company’s orders. If the turn-around time is measured in days (including purchase of parts) then it would be better to run MRP every day or so. In that case, the filter date should be 4 or 5 days out.
In the beginning of bringing up MRP, companies usually suffer a large backlog of order actions. Sometimes these actions cannot be covered before the next MRP runs, so the actions continue to be generated until they are completed. As the process settles down, the company can comfortably run MRP as often as necessary to keep purchasing up with the MRP needs.
For further dteail see Article #1080 .
|
1.3. FAQ- In-Plant Store Mgmt (IPS) |
1.3.1. Can you Edit an IPS PO? | Q. Can you Edit an IPS PO?
A. The system has the capability to Edit an IPS Purchase Order. When you depress the Edit button for an IPS order the user will only be able to change the PO Status for that record. For further detail see Article #626 .
|
1.3.2. Does IPS allow you to have Multiple Contracts per Customer or Supplier? | Q. Does IPS allow you to have Multiple Contracts per Customer or Supplier?
A. You can have as many IPS contracts as you want (for each customer and supplier). You can also have as many IPS manufacturers as internal manufacturers. |
1.3.3. When Creating an IPS for a Single Supplier why is it Creating Multiple PO's? | Q. When Creating an IPS for a Single Supplier why is it Creating Multiple PO's?
A. When the system creates In-Store PO's it groups them together by contract number. So if user is creating In-Store PO's for several items all for the same supplier, but parts have different contract numbers the system will create a seperate In-Store PO for each group of contract numbers even though they are all for the same supplier.
|
1.4. FAQ - Master Production Schedule (MPS) & Forecast |
1.4.1. Is ManEx forecast module set up to work with final top level and not the lower sub level for demand supply alignment? | Q. Is ManEx forecast module set up to work with final top level and not the lower sub level for demand supply alignment?
A. If both an assembly and one or more of it’s subassemblies are in a forecast, then both the forecasted subassembly and the subassembly for the forecasted assembly will have demands. This is how the system is intended to function. This is so that users can forecast requirements for spare parts if needed. I don’t think there is any other way to have spares built except to use a sales order instead of a forecast. Using a firm-planned work order for spares will cause the spares to be consumed by the assembly order.
So, if you have a Top level Assembly A and a Sub level Assembly B that reports to A; and have a forecast at Assembly B but final Sales Order is only at Assembly A
Perhaps the way to deal with this is to create a firm-planned work order for the subassembly (instead of a forecast) due on the date they placed the forecast for the subassembly. Then when the order is placed for the assembly (due after the work order for the subassembly), MRP will recognize the availability of the subassemblies and will not “double-drive” the requirements.
.
|
1.4.2. How can I fix a planning error within the Forecast Module? |
Question: How can I fix a planning error within the Forecast Module?
(Example: User set a plan to build 800 pcs of a P/N in the forecast module for 1/29/07 a few weeks ago. Then found out they actually only needed 500 pcs for 1/29/07 and the other 300 pcs on 2/28/07).
Answer: The forecast module does not allow for changes in the forecast for the current period, however, it does allow for changes in any future period, depending on the setup tolerances for how far out in the future the change is.
Suggestion: You could open a SO for the near term activity and cancel the forecast. Then start a new forecast for future periods.
|
1.4.3. How to use the forecast module if you do not want the SO schedule driving MRP | If a customer has the Forecast module and wants to be able to have a Sales Order in the system to create shipments against, but they do not want any of the SO schedules driving MRP.
In this situation we would suggest that the user leaves the Schedule information Blank and create the qty's needed through the Forecast module. Forecast will drive MRP and users will be able to still ship them against any sales order in the system. View the attached Print Screens for further detail. |
1.4.4. How do I determine if an order can be shipped sooner than the scheduled due date? | Question: What reports or screens can we view to see the material status, so we can determine whether or not we can change the Sales Order Schedule Due Date in order to ship it earlier?
Answer: First check the Customer Order Status screen by customer PO and/or Sales Order number. From this screen you will be able to determine the status of any work order(s) in progress and if there are any shortages.
Second you may run a Kit Material Availability W/AVL Detail (Simulation) report, by product number and revision. This report will display the Quantity on Hand and the Quantity Available for each part used on that product.
Third you can check the MRP status of the product for proposed work orders and purchase orders. This will inform you if the scheduled delivery date (s) will be met.
|
|