1.1. Prerequisites for ABC Types |
Complete the attached worksheet and " Mark as Completed RoadMap Section B Item 4-e before continuing the setup.
User MUST have full rights to the "System Setup" in System Security . Users with “Supervisor Rights” will automatically have access.
|
1.2. Introduction for ABC Types | This section is provided to setup ABC Code template table. This information is used in the item master during add or edit mode. ABC types are used when setting up part class and types, which in turn are used when adding an inventory part to the item master. ABC codes are used as an aid to manage inventory tracking. Traditionally, ABC codes are established to divide the inventory by value, and to guide in the cycle counting of inventory. First the value of all inventory in stock is added up and listed by part in order of the highest extended value first. Then, the top 80 % of the parts value would be classified as “A” items, and will probably consist of about 10-15% of the inventory part numbers. The next 15% of the value items would be classified as “B” items, and will be in the neighborhood of 20-40% of the part numbers. The last 5% of the value will be classified as “C” items, and represent at least 50% of the part numbers.
ManEx allows the user to differentiate between assemblies and components. Users may create a setup of ABC (and DEFG...if they choose) for components (buy/consigned parts) and a different set (e.g. MNO) for assemblies. The reason for this is that it is likely that the assemblies may need tighter control than the ranges available for the whole inventory, and the user has the option of differentiating between components, and assemblies. If a user is carrying components in finished goods inventory to ship to a customer, they will still be counted as components in the ABC group. The type of warehouse is not considered when calculating cycle counts (except for in-house items, regardless of where they are stored).
|
1.3. Fields & Definitions for ABC Type |
ABC Calculation Based on:
Manually Assigned |
If this radio is selected, the ABC codes are assigned when parts are created based on their class and type and must be updated manually as needed. But MUST be setup in the Part Class Setup.
|
$ Estimated Annual Usage |
If this radio is selected, the ABC codes are assigned based on the value of the estimated annual usage and/or component lead time. Users must run the "Calc EAU" and Calc ABC Codes" programs to refresh EAU and ABC codes.
|
$ On Hand |
If this radio is selected, then ABC codes are assigned based on the value of inventory on hand and/or the component lead time. Users must run the "Calc ABC Codes" program to update and refresh the component ABC codes.
|
EAU Factor % |
If the user selects $ Estimated Annual Usage, Enter in the EAU factor.
|
Last EAU |
The date that the Last EAU was calculated. |
Ignore In Store |
Check this box only if you do NOT want the In-Store material to be included when running Cycle Counts, regardless of which Calculation Based on is selected. |
Exclude Issues Older than __ Days from EAU Calculation |
Enter the number of days you want to exclude older issues from the EAU Calculations. The number of days entered in this field will override the standard 30 days. The default is set to 180 days, but can be changed. |
ABC Types:
ABC Type |
The ABC code identifies a part source for inventory parts. A = Highest value, B = Medium value and C = Lowest value (Manex allows up to 36 (0-9 and A-Z) alphanumeric ABC designations). ABC codes are applied to Buy and Make part separately.
NOTE: All Make parts should be assigned a Make ABC type and the same goes for buy parts, if you want the most accurate Cycle counting to take place. However, ff an ABC code is setup for a buy part and that ABC code is assigned to a Make part the make part will still be included in the cycle count and vice versa.
|
Description |
Definition of ABC parameters |
Part Source |
This identifies if a part is a Make or Buy part. Select the desired part Source radio. The part souce does NOT control whether a part is counted. It is stricly based on what the ABC code is given to that part and whether that part has been counted within the specified days. |
Dock to Stock |
A Dock to Stock period may be included in each ABC code. Dock to Stock is the number of days a part is expected to take to be delivered to the stock room after the part is received on the user’s dock. This duration may include the amount of time it takes to organize the shipment, count the parts, log the receipt into the inventory system, perform incoming inspection, and physically move the parts to stores. Intuitively, the higher dollar parts may have longer dock to stock times because of increased inspection. And the lesser valued parts may not require inspection. NOTE: MANEX provides for PO Receiving Inspection and for Discrepant Material Returns (Return to Vendor).
The Dock to Stock value is taken into consideration for MRP leadtime calculations in the projected requirement of the receipt of purchased parts. For Example: if the Dock to Stock time is 3 days, and the kit start date is 8/22/08, then the due date for the buy components would be 8/19/08, and the order date would be based on the purchasing leadtime to receive the parts by 8/19/08. So the Dock to Stock time is used to move back the due dates of items purchased in time for kitting
|
Cycle Count Days |
Users enter the Cycle Count Days of each ABC code. This is used to determine the number of parts to count each day. This is based on calendar days and may need to be adjusted for work days if you will not be cycle counting seven days a week. This field assists in counting all inventory over a period of time. The “A” items might be counted completely within each month. Therefore, a list of all of the “A” items (the highest dollar value) is generated, and randomly divided into 20 days, and each day 1/20th of the list counted and checked. The “B” items might be checked every quarter, and the “C” items checked once a year. This is a way to verify the accuracy of stockroom transactions, and to take measures necessary to keep the counts accurate. Type the ABC Types into the appropriate boxes. NOTE: This field MUST be populated with a number other than "0". If "0" is entered these parts will NOT be included in the Cycle Count. |
% of Value |
The "% of Value" determines which components will be included in the ABC code based on where their value falls within the total value Pareto (i.e. if A parts have a value of 80%, then all components comprising the top 80% of value will be included, if B parts have a "% of Value" of 15, then all components comprising the next 15% of value will be included, etc). A full 100% must be assigned to both Buy and Make parts. The "ABC calculation based on:" affect the meaning of this field. If Manual has been selected then it does not apply. If $ Estimated Annual Usage (EAU) has been selected, then it is EAU x STD cost and % of that value (top 80%, 15-80%, etc) If $ On-Hand has been selected, then it is On-Hand x STD cost and % of that value (top 80%, 15-80%, etc). Entering data in this field will NOT affect the cycle counting or include any of the parts in the cycle count until the "Calc ABC Codes" button is depressed.
|
Lead Time > |
The "LT>" determines which components will be included in the ABC code based on their purchasing lead time. THis will include all components with an applicable lead time regardless of the on-hand or EAU value. |
Dollar Amount |
The dollar amount tolerance used in Cycle Count. For each ABC code, ManEx provides a cycle count tolerance, which, if exceeded, will result in reporting unfavorable results during cycle counting. These tolerances may be an absolute dollar value, or a percentage of the inventory being counted. For further information on the cycle count tolerances and what the purpose of setting them up in ManEx is see the attachment <<Cycle Count Tolerance.docx>> |
Percentage |
The Cycle Count Tolerance Percentage. For each ABC code, ManEx provides a cycle count tolerance, which, if exceeded, will result in reporting unfavorable results during cycle counting. These tolerances may be an absolute dollar value, or a percentage of the inventory being counted. For further information on the cycle count tolerances and what the purpose of setting them up in ManEx is see the attachment <<Cycle Count Tolerance.docx>> |
 |
This button will only be available if the screen is in "EDIT" . Depressing this button will update the EAU field within the ICM screen. The term EAU, (ESTIMATED Annual USAGE) may be considered as consumption, depletion, loss, used up, etc. So the EAU calculations MUST include the In-store issues to be accurate. If a user is issuing a part out of in-store to a Sales Order to be shipped the parts still count as an issue, or usage and was consumed, so it is necessary to include them when considering plans for future usage. If a user were to deliver ALL material directly to work orders from in-house, and these transactions were not included, there would be no calculated EAU. This is why we do NOT allow in-store issues to be ignored. The only time in-store issues will NOT be calculated in the EAU is if they are being returned to the vendor through Inventory Handling. |
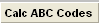 |
This button will only be available if the screen is in "EDIT" . Depressing this button will use the information in the % value and LT> fields are used to determine which parts should have their ABC codes automatically adjusted. After the ABC codes are updated, those parts will be included with the appropriate group for cycle counting. |
 |
This button will only be available if the screen is in "EDIT" mode. Depressing this button will use the information in the % value and LT> fields are used to determine which parts should have their ABC codes automatically adjusted. After the ABC codes are updated, those parts will be included with the appropriate group for cycle counting. |
|
1.4. How To ..... for ABC Types |
1.4.1. Setup the ABC Types |
Enter System Setup/Material/ABC Types Module
This section is provided to setup ABC Code template table. This information is used in the item master during add or edit mode. ABC types are used when setting up part class and types, which in turn are used when adding an inventory part to the item master. ABC codes are used as an aid to manage inventory tracking. Traditionally, ABC codes are established to divide the inventory by value, and to guide in the cycle counting of inventory. First the value of all inventory in stock is added up and listed by part in order of the highest extended value first. Then, the top 80 % of the parts value would be classified as “A” items, and will probably consist of about 10-15% of the inventory part numbers. The next 15% of the value items would be classified as “B” items, and will be in the neighborhood of 20-40% of the part numbers. The last 5% of the value will be classified as “C” items, and represent at least 50% of the part numbers.
NOTE: An ABC code needs to be specifically setup for Make parts, if Make parts are to be included in the cycle count. If an ABC code is setup for a buy part and that ABC code is assigned to a Make part the make part will NOT be included in the cycle count and vice versa.
|
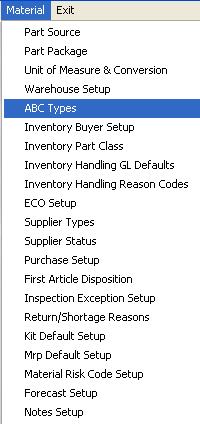 |
The following screen will appear:
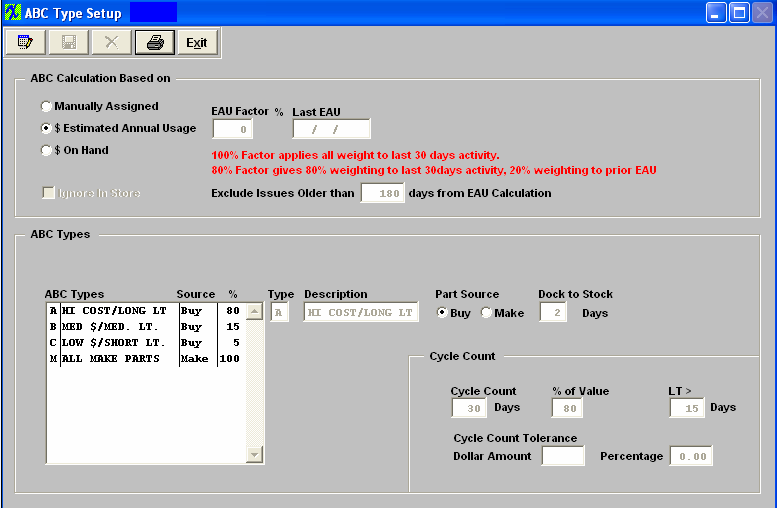
The "ABC calculation based on" affects the meaning of the % of Value field. If Manual has been selected then it does not apply. If $ Estimated Annual Usage (EAU) has been selected, then it is EAU x STD cost and % of that value (top 80%, 15-80%, etc) If $ On-Hand has been selected, then it is On-Hand x STD cost and % of that value (top 80%, 15-80%, etc).
ABC Codes will be calculated using the information in the % value and LT> fields. These fields are used to determine which parts should have their ABC codes automatically adjusted. After the ABC codes are updated, those parts will be included with the appropriate group for cycle counting.
Check the "Ignore In-Store" box only if you do NOT want the In-Store material to be included when running Cycle Counts, regardless of which Calculation Based on is selected.
Depress the Edit button. Select the "ABC Calculation based on" by clicking on the appropriate radio.
If the user selects "$ Estimated Annual Usage", the following screen will appear. Type in the EAU factor, then depress the "Calc EAU" button will update the EAU field within the ICM screen.
This button will only be available if the screen is in "EDIT" . Depressing this button will update the EAU field within the ICM screen. The term EAU, (ESTIMATED Annual USAGE) may be considered as consumption, depletion, loss, used up, etc. So the EAU calculations MUST include the In-store issues to be accurate. If a user is issuing a part out of in-store to a Sales Order to be shipped the parts still count as an issue, or usage and was consumed, so it is necessary to include them when considering plans for future usage. If a user were to deliver ALL material directly to work orders from in-house, and these transactions were NOT included, there would be no calculated EAU. This is why we do NOT allow in-store issues to be ignored. The only time in-store issues will NOT be calculated in the EAU is if they are being returned to the vendor through Inventory Handling.
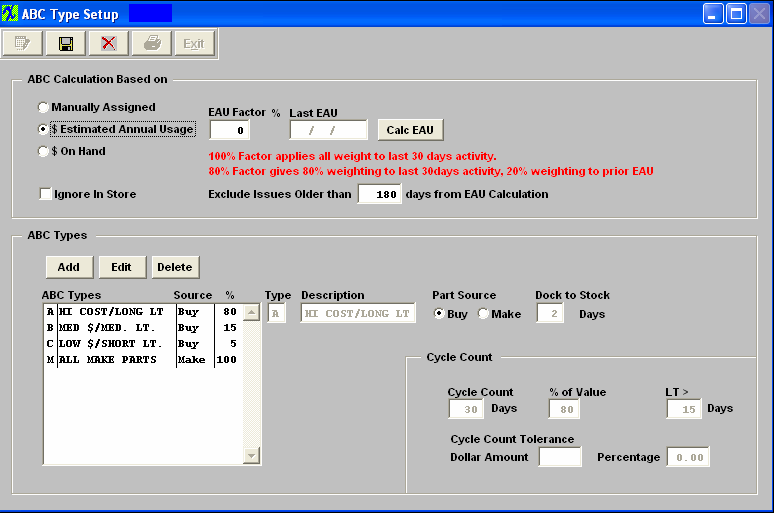
The last EAU date will fill in and the "Calc ABC Codes" button will appear on screen. Depress the "Calc ABC Codes" button, this button will use the information in the % value and LT> fields are used to determine which parts should have their ABC codes automatically adjusted. After the ABC codes are updated, those parts will be included with the appropriate group for cycle counting.
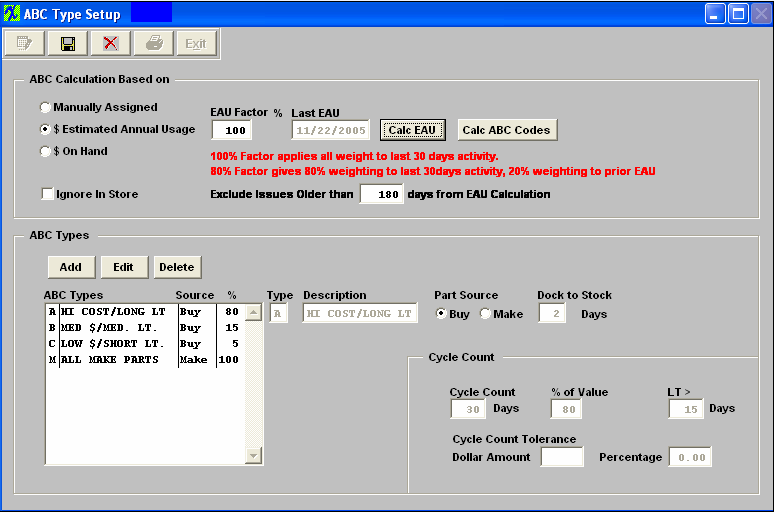
The "Update ABC Codes" button will appear on screen. Depress the "Update ABC Codes" button will use the information in the % value and LT> fields are used to determine which parts should have their ABC codes automatically adjusted. After the ABC codes are updated, those parts will be included with the appropriate group for cycle counting..
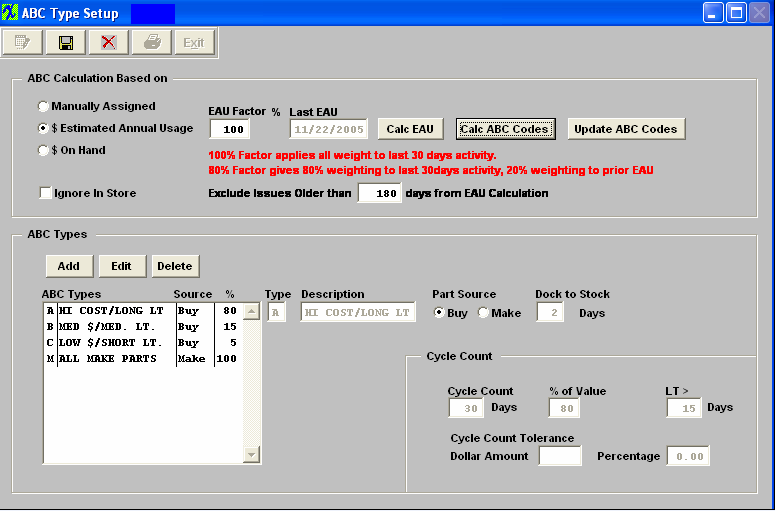
The user then sets up an inventory counting program called “Inventory Cycle Count”, which assists in counting all inventory over a period of time. The “A” items might be counted completely within each month. Therefore, a list of all of the “A” items (the highest dollar value) is generated, and randomly divided into 20 days, and each day 1/20th of the list counted and checked. The “B” items might be checked every quarter, and the “C” items checked once a year. This is a way to verify the accuracy of stockroom transactions, and to take measures necessary to keep the counts accurate. Type the ABC Types into the appropriate boxes.
The ABC code identifies a part source for inventory parts. Because ManEx allows up to 26 ABC codes, it also provides for identifying if a part is a make or buy part. Click on the desired Part Source radial, either Buy or Make.
Enter the Dock to Stock days. In ManEx, the ABC codes have a slightly different meaning. In addition to identifying the most or least expensive part numbers, a Dock to Stock period may be included in each ABC code. Dock to Stock is the number of days a part is expected to take to be delivered to the stock room after the part is received on the user’s dock.
Also, for each ABC code, ManEx provides a cycle count tolerance, which, if exceeded, will result in reporting unfavorable results during cycle counting. These tolerances may be an absolute dollar value, or a percentage of the inventory being counted. In the Cycle Count section, enter Cycle Count Days (NOTE: This field MUST be populated with a number other than "0". If "0" is entered these parts will NOT be included in the Cycle Count), % of Value, Lead Time Greater than, and Cycle Count Tolerances: Dollar Amount and Percentage.
The user must either depress the Save or Abandon changes button.
Where Used: In all Part Type Setup, Inventory Item Master, Material Requirements Planning and Cycle Count functions.
«Mark as Completed in RoadMap in Sect. B Item 4-e»
|
1.5. Reports for the ABC Types | Proposed ABC Changes Report
To obtain a printout, depress the Reports button. The following screen will appear:
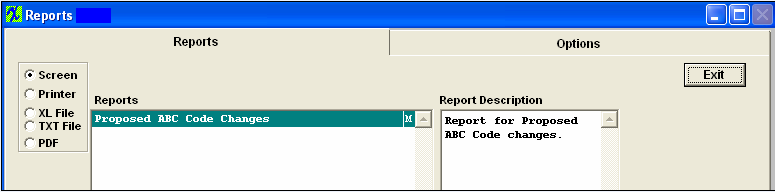
Highlight the report and depress the Options tab.The following screen will appear:
Select the output desired by clicking on the Screen, Printer, XL File, TXT File, or PDF radial.
Click on the Make Parts and/or Buy Parts box(es), as desired. Click on the Proposed Changes Only or All Parts radial, as desired.
Depress the OK button.
The following report is available:
|
|