Enter Inventory Mgt/Inventory Control Management/Standard Cost Adjustment Module |
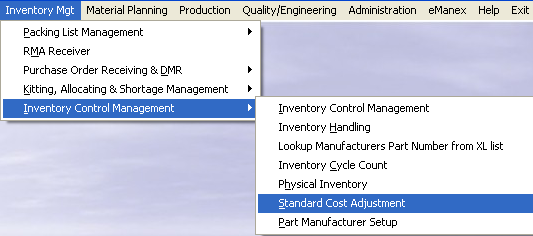 |
The following screen will appear:
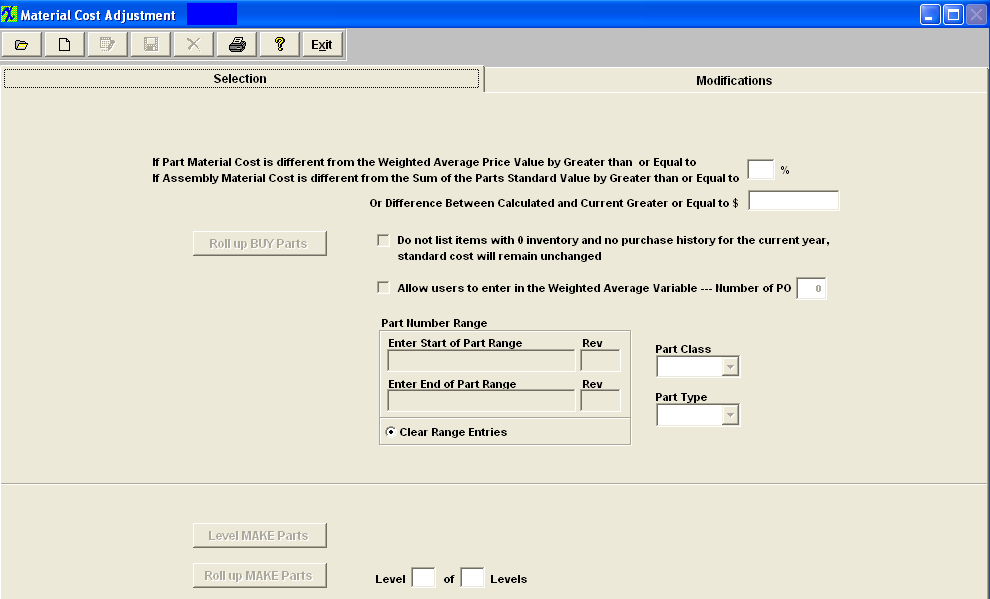
Depress the Add action button (Start New Cost Roll) and the folloiwng items will become enabled:
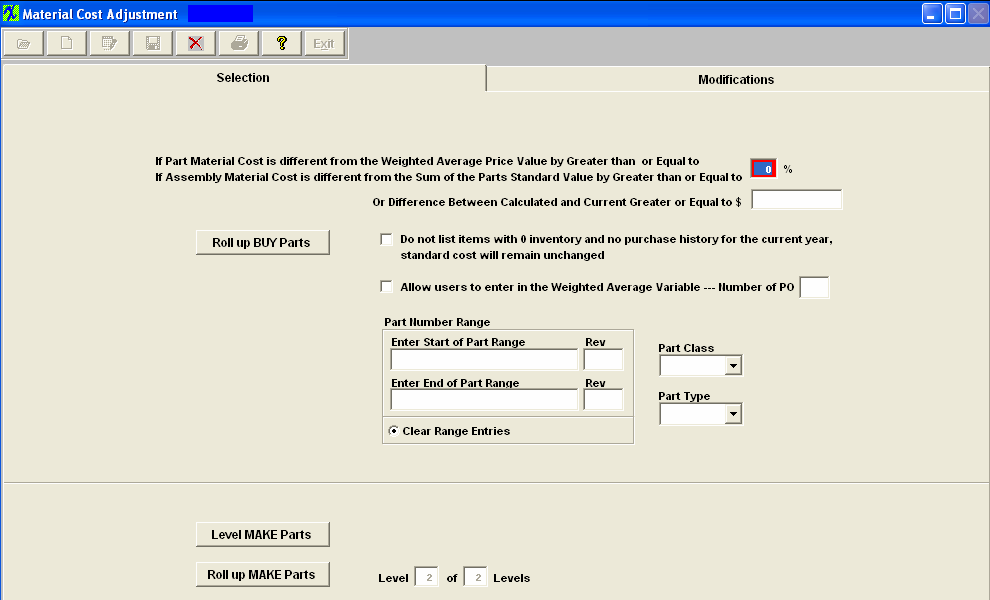
Type in the percentage to use if the part material cost is different from the Weighted Average Price Value by Greater than or Equal to or if the assembly material cost is different from the Sum of the parts standard value by Greater than or Equal to Or Difference between Calculated and Current Greater or Equal to $
Example: if there is a $2000.00 assembly in stock, and users apply the 1% criteria, a $19.00 difference won't be brought into the matrix to be checked. On the other users enter 0%, then every single part will be included. A Minimum dollar value has been added to the Standard Cost Adjustment screen that will be used to determine whether or not an item is included in the matrix. If left blank then the percentage rules. If value entered then it becomes the criteria for inclusion in the matrix.
Check box if you "Do not want items listed with 0 inventory and no purchase history for the current year", then the standard cost will remain unchanged
Check this box if you want to "Allow user to enter in the Weighted Average Variable" or you can type in the number of PO(s) to include in the calculated weighted cost.
User also has the option to select the part number range , class, or type, on which part(s) to process. This will complete the adjustment process faster and user will be able to maintain more accurate records and also allow the users the ability to narrow the resulting filter of the Buy parts. NOTE: The Part Number range selection is offered only for BUY parts. ManEx does not offer it for MAKE parts, because the system needs to roll ALL sub assemblies up to determine the top level costs. However, in the modifications tab, it is possible to sort by part number or class, to make it easier for the user to find specific items of interest.
NOTE: Due to the fact that inventory records flagged as MAKE/BUY can not have Work Orders generated for them. The Standard Cost Adjustment module will consider MAKE/BUY inventory part numbers as BUY parts and will be rolled into the Buy portion of the Std Cost Adjustment module.
To roll up the Buy Parts, depress the Roll up BUY Parts button. Upon rolling the records the system will now consider all of the Costs, and not just the material cost.
After the calculation is complete, the following message will appear:

Depress the OK button. Depressing on the Modifications tab reveals the following:
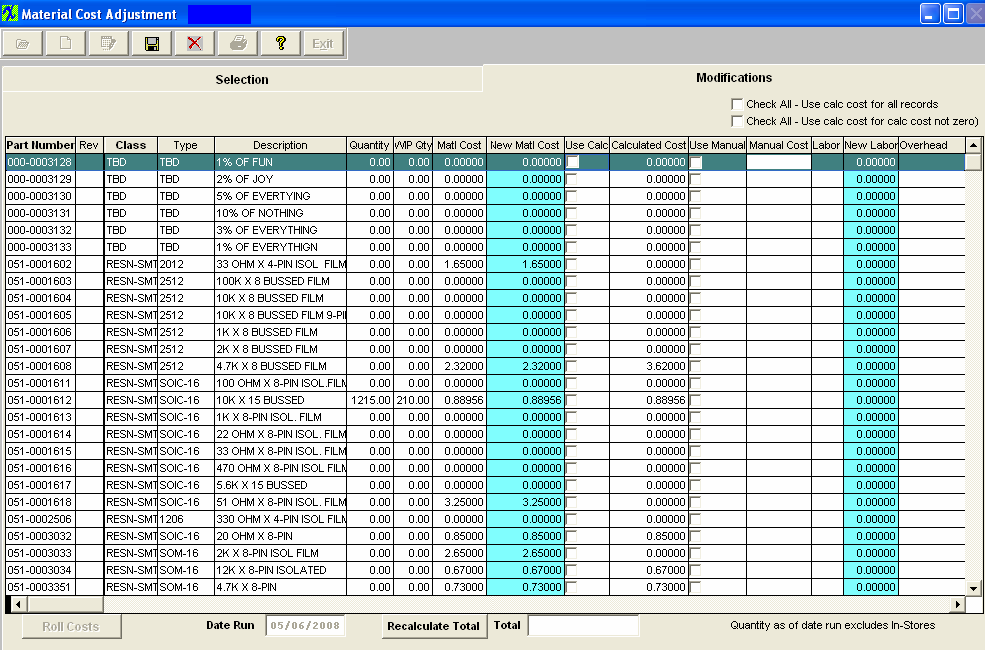
Depress the Edit button. To effect a change, click on either the Use Calc column or the Use Manual column.
If you choose Use Manual column, you must also enter a new manual, labor, overhead, other, or user defined cost:
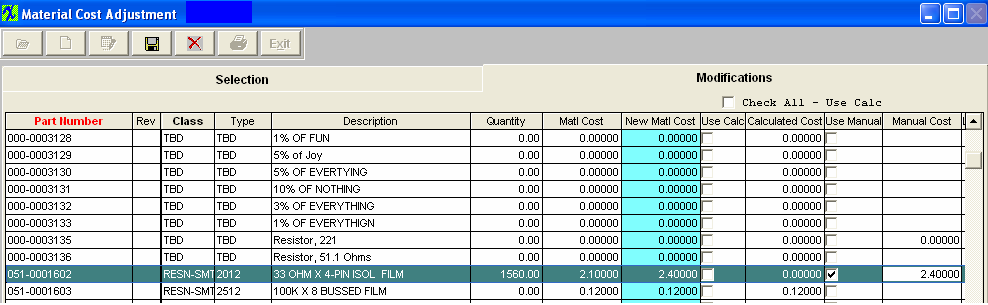
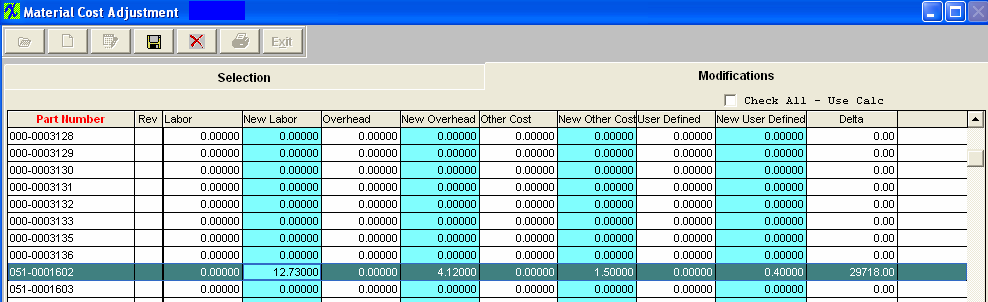
Note that the Delta column updates automatically. This is the difference between the old Standard Cost and the New Standard Cost multiplied by the Quantity. (Note: The quantity may include setup scrap and/or run scrap if the box to exclude scrap from Cost Rollup is not checked in the Kit Default Setup screen).
To Re-calculate the total change (Delta), depress Recalculate Total button.The Total will update, as illustrated:
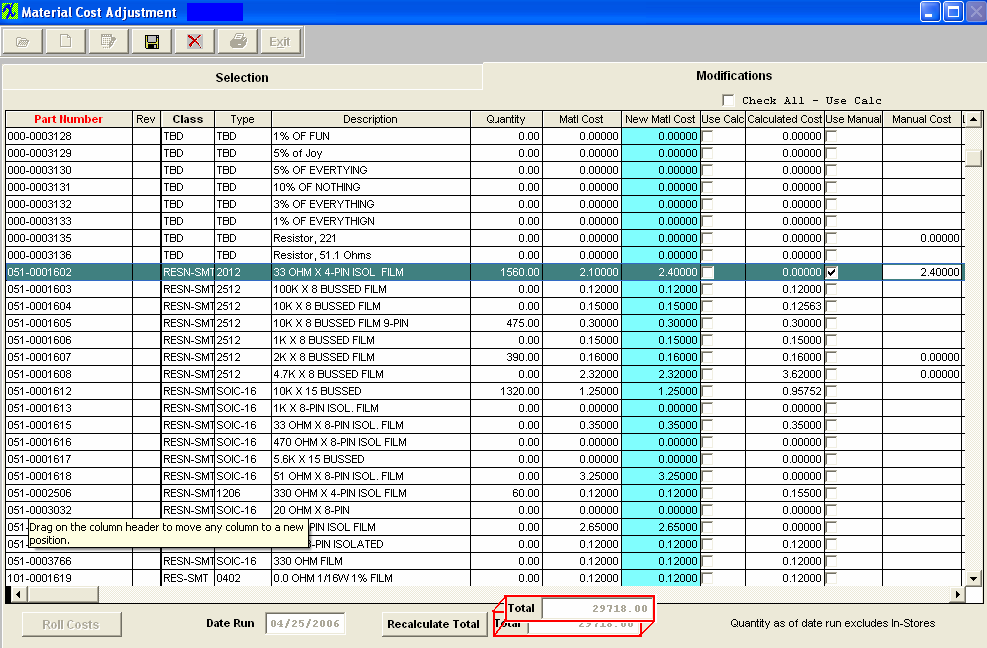
Depress the Save record action button.
To Post the changes to the Standard Cost and generate the General Ledger entries, depress the Roll Costs button. The system will update the "Last Change" field (within the ICM screen) for part numbers that actually had pricing information changed within the Std Cost Adjustment.
Enter your password. Note: This requires a high level accounting password.
The following message will appear once the update has been completed.

Depress the OK Button.
|