1. Statistical Quality Control (SQC) (OPTIONAL Module) |
1.1. Prerequisites for SQC | Required Prerequisites:
ManEx’s standard module configuration allows most users to accomplish their daily tasks. For those users wanting to get more from ManEx by leveraging the total solutions, this is one of the optional modules available for purchase. To place an order or to learn more about this specific module or any of the other optional modules please contact us at http://manex.com\contactus.aspx
After activation, "Statistical Quality Control" (SQC) access for each user must be setup in the ManEx Security module. Users with “Supervisor Rights” will automatically have access.
Customer |
Part number |
Defect Codes |
The Defect Codes must be established in the Quality Defect Codes setup. The options for the viewing of serial numbers, number of times that “No Problem Found” are permitted, defects displayed for routing or all must be established in the setup. |
Optional Prerequisites:
Pricing |
Otherwise must be entered in Sales Order.
|
Bill of Material-Locations |
If locations (reference designators) are entered in the Bill of Material, the user may identify specific locations for each defect.
|
BOM Appvd Mfgrs |
If the AVLs are entered in the Bill of Materials, the user may identify specific manufacturers for each defect.
|
|
1.2. Introduction for SQC | The STATISTICAL QUALITY CONTROL (SQC) Module ~ Defect Entry screen is used to record defects and inspection results during the movement of product through the production Work In Process (WIP). The user has a choice of entering data in a batch mode or in an in-line mode See Article #1769 for further detail. Batch mode is the entry of data accumulated during an inspection period, and is data entry only (does NOT transfer product from one work center to another). In-line mode is where inspection is done at the end of a work center or activity, and the product is to be moved to another work center based on the results of the inspection. In-line inspection would require inspection of 100% of the product, in order to move the product from one step to another. It also requires the use of a ManEx workstation at the inspection station, so the data may be entered real-time.
Defect entry is based on having a standard nomenclature for the defects in the Quality Defect Codes setup, so that the users do not have the option of creative descriptions. The defects in the setup may be ascribed to specific work centers, to minimize the number of defects that an inspector (or data entry person) has to view to find the appropriate defect.
Defect information may be recorded by work order and/or by serial number. Defects may be associated with a specific “location” (reference designator) on the assembly, providing the user has entered reference designators for the assembly in its Bill of Material .
If the user chooses to enter reference designator locations for the defects, and has entered reference designators on the Bill of Materials, then ManEx will prompt the user to select the manufacturer for the part used at the location, as well as automatically enter the internal part number at that location.
There is also provision for tracking the diagnostics and repair of each defect and assembly. The user may view the history of the assembly’s movement through production, and all of the defects associated with each assembly.
Data entered for defects will be used in the Statistical Quality Control module for charting pareto charts, control charts and more.
|
1.3. Fields & Denfintions for SQC |
1.3.1. Defect Data Collection |
1.3.1.1. Quality Inspection Entry Tab | Quality Inspection Entry Screen Field Definitions
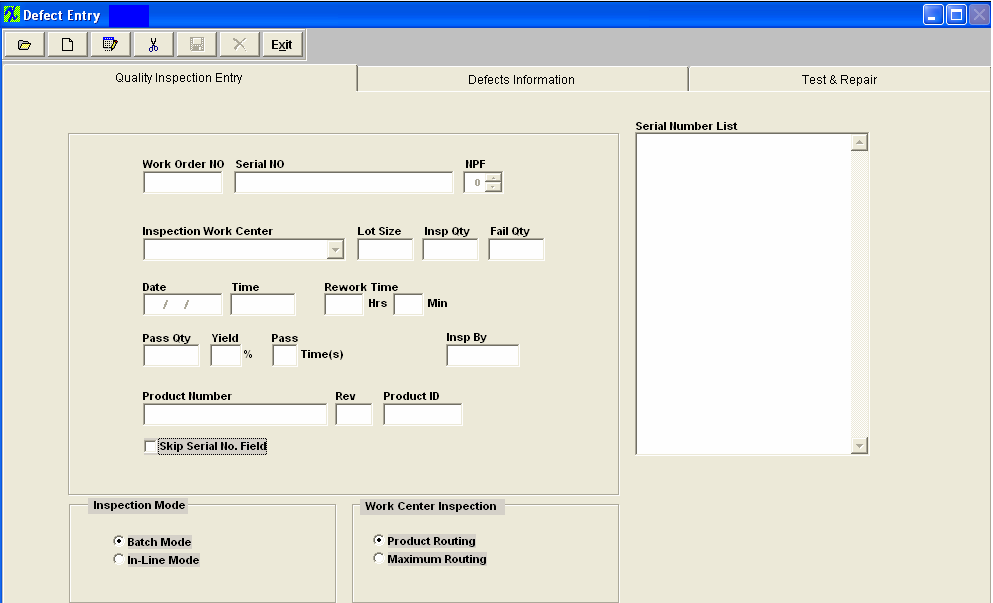
Work Order Number |
The number of the Work Order which was inspected.
|
Serial Number |
The serial number assigned to the specific assembly unit.
|
NPF |
The next field, “NPF”, no problems found, is provided for the user to record when observing the product. If the serial number had previously been rejected, and analysis of the product yield no further problem, either with cosmetics or function, then the user may change this number to 1, meaning the first time it was inspected or tested, no problem was found. If the product serial number is subsequently rejected again, and a second inspection finds a problem, the number may be incremented to a “2”. This will alert users to repeated rejections of a product serial number, one or more times with no discernable defects. If the number of times that a part has experienced an NPF (no of problems found) exceeds that established in the Quality Defect Codes setup, the user will receive a warning message and will allow you to proceed on with the Inspection. This is just a notification that the board has passed the maximum NPF cycle.
|
Inspection Work Center |
This is the name of the Work Center where the inspection took place.
|
Lot Size |
This is the number of assemblies available for testing.
|
Insp Qty |
This is the number ofassemblies actually tested.
|
Fail Qty |
The number of assemblies which failed inspection.
|
Date |
The date whereby the inspection took place.
|
Time |
The time (24 hour clock) when the failure was recorded.
|
Rework Time |
The time estimated to rework the failed assembly |
Pass Qty |
The number of assemblies which passed inspection.
|
Yield |
The percentage of assemblies which passed inspection.
|
Pass Times |
This is the number of times a particular Serial Number can pass through this Inspection screen. In Quality Defect Code Setup, there is a field called :maximum number of inspections/WC”. The user may define how many times a given serial number can pass through a given Work Center. |
Product Number |
The internal number assigned to the assembly.
|
Rev |
The revision number associated with the Product Number.
|
Product ID |
This field is no longer used and is left blank.
|
Skip Serial Number Field |
This box is checked if the user wishes to do Without Serial Number Inspection.
|
Enter Serial Number Without Validation |
Only Enabled if user skips regular serial number entry.
This feature has been added to allow the users the ability to inspect Serial Numbers that do not actually exist within the ManEx system. (for example serial number created outside of ManEx, by customer or other software, etc. . .)If the user checks the “Enter serial number without validation” then ManEx does not validate when the users enters the Serial Number. The system just records the entry for later SQC analysis purpose.(note: if the work order is serialized, then the user can not use this feature)
|
Inspection Mode |
Determines whether inspection is performed via Batch or In Line mode.
Batch mode is used for entering data previously recorded during inspection of the product. When the user chooses to enter defect data in “In-Line” mode with the serial number, the user won’t be able to enter “lot quantity”, “inspection quantity” or “failed quantity”. These fields are all automatically when the user goes into the “Defects Information” tab. However, if the user enters defect data in “batch” mode without the serial number, then the user will be able to enter “lot quantity”, “inspection quantity” and “failed quantity”.
If the user wishes to 100% inspect material, and directly move the passed material to the next routing work center, then the In-Line Inspection mode may be used.
|
Work Center Inspection |
The user has the option of viewing defects based on the product routing (Product Routing), or to view all defects (Maximum Routing).
|
Serial Number List |
The numbers of all of the Serial Numbers which were inspected. Depress the Edit button and then highlight the serial number of choice.
|
|
1.3.1.2. Defect Information Tab | Defect Information Screen Field Defintions
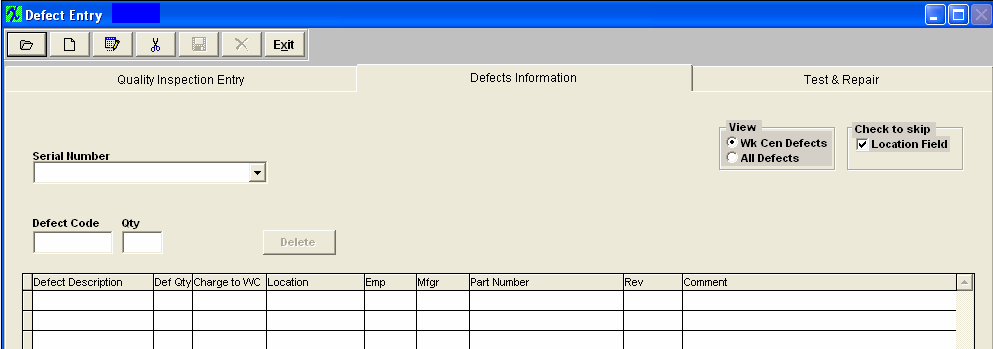
View |
This displays whether the view of the defects is by Work Center only or covers All defects.
|
Check to skip location field |
If this box is checked, the location field may be skipped.
|
Serial Number |
The Serial Number of the failed assembly.
|
Defect Code |
The code used to describe the defect.
|
Defect Description |
The description of the defect.
|
Def Qty |
The number of defects.
|
Charge to WC |
The name of the Work Center where the defect will be charged.
|
Location |
The Reference Designator as set up in the assembly’s Bill of Materials.
|
Emp |
Employee number assigned to the defect |
Mfgr |
The name of the manufacturer of the component.
|
Part Number |
The internal number assigned to the component.
|
Rev |
The revision number pertaining to the internal part number.
|
Comments |
Additional comments entered by the user.
|
|
1.3.2. View Chart Tab |
See Article #5082 for more detail on each individual Chart Listed at the Top. Once you have selected the type of graph you wish to view the graph will be displayed in the window below the selection.
|
1.3.3. Template Selection/Setup Tab |
Template Selection Setup
This is the first screen to be used in the module. In this screen, STATISTICAL QUALITY CONTROL graphics are created by selecting parameters to be considered in the graph.
This screen operates differently than all other ManEx screens. When bringing up the SQC module, the user is first presented with a template screen from which to choose parameters to be included in the information displayed.
When the user enters the system, he/she may select how they want to start the process of selection. Click on the Customer, Part Number or Work Order radial.
|
1.3.4. Template Detail Tab |
Date Range |
Enter the Date Range, From and To. Mark the Radial for the view by Daily, Weekly, Monthly, or Yearly. |
User Defined Limits for DPM Chart |
Central Line
lnCentralLine=lnTotalDef/lnTotalComp, where lnTotalDef is sum of all defect quantities * 1000000 and lnTotalComp is sum of inspected quantities*Parts Per Unit (entered in the routing module)
At this time system will decide if it can use average group size or not. If the size group varies more tan 15% the system will use variance Upper and Lowercontrol limit. If average group size could be used the average group size gets calculated by taking lnAvrgSubgrSize=lnTotalComp divided by number of groups and rounded to the nearest integer.
Calculation for the Upper Control Line
LnUpperLine=ROUND(((3*(SQRT(lnCentrLine*(1000000-lnCentrLine))))/SQRT(lnAvrgSubgrSize)),3)
Calculation for the Lower Control Line
lnLowerLine = ROUND(lnCentrLine -((3*(SQRT(lnCentrLine*(1000000-lnCentrLine))))/SQRT(lnAvrgSubgrSize)),3)
lnLowerLine = IIF(lnLowerLine<0,0,lnLowerLine)
|
User Defined Limits for pChart |
The formula for the Central line (Red) is: p = Total Number Failed (divided by) Total Number Inspected
Upper Control Limit (UCL) = p + 3 (divided by) p (1-p) divided by n
Lower Control Limit (LCL) = p - 3 (divided by) p(1-p) divided by n (or 0, whichever is greater)
n = number inspected (sample size)
|
User Defined Goal for the Yield Chart |
"Yield" = Total number of units handled correctly through the process step(s). This is usually measured in a percentage. The results being displayed in the "Yeild Chart" is the ratio of summed inspected qty and summed passed qty, grouped by date (user can select WO number, defect code to be filtered). |
|
1.4.1. Enter the Defect Data Information | All data must be Entered in the Quality Inspection Entry and Defect Information screens, with in the Shop Floor Tracking Module.
Entering a Defect Code Entry to a Work Order
For closed Work Orders: In the Security module, there is an option which must be checked per user for the “Defect Code Entry”. Once the Security right has been entered, the user may edit a “closed” Work Order.
The first screen presented to the user depends on whether or not in the system setup/Quality Defect Codes, the user has selected to enter defect information in BATCH or IN-LINE mode. If the user has selected IN-LINE in the setup, then only the IN-LINE screen will be displayed. Otherwise, the user will be presented with the batch screen, and the option to enter IN-LINE data.
Batch mode is used for entering data previously recorded during inspection of the product. When the user chooses to enter defect data in “In-Line” mode with the serial number, the user won’t be able to enter “lot quantity”, “inspection quantity” or “failed quantity”.These fields are all defaulted in when the user goes into the “Defects Information” tab. However, if the user enters defect data in “batch” mode without the serial number, then the user will be able to enter “lot quantity”, “inspection quantity” and “failed quantity”.
If the user wishes to 100% inspect material, and directly move the passed material to the next routing work center, then the In-Line Inspection mode may be used.
The user has the ability to limit some workstations (specific PCs) (which is defined in the Security Module) to be able to only transfer material “FROM” a certain Work Center. When the user transfers material from a Work Center (A Serialized part Number Only) in the Defect Code Entry In-Line Mode, the system will check to see if the serial number is currently in the Work Center. If not, a special supervisor’s password is required to transfer the serial number FROM a different Work Center. After the supervisor’s password is entered, the system will use the new Work Center to be the default FROM Work Center until the user closes the screen. The next time the user opens the screen, the default FROM Work Center will be changed back to the one defined in the Security Module.
Enter Production/Shop Floor Tracking by Work Order Module
Find a Work Order in SFT Module,
| 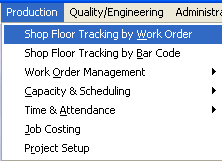 |
The following screen will appear:
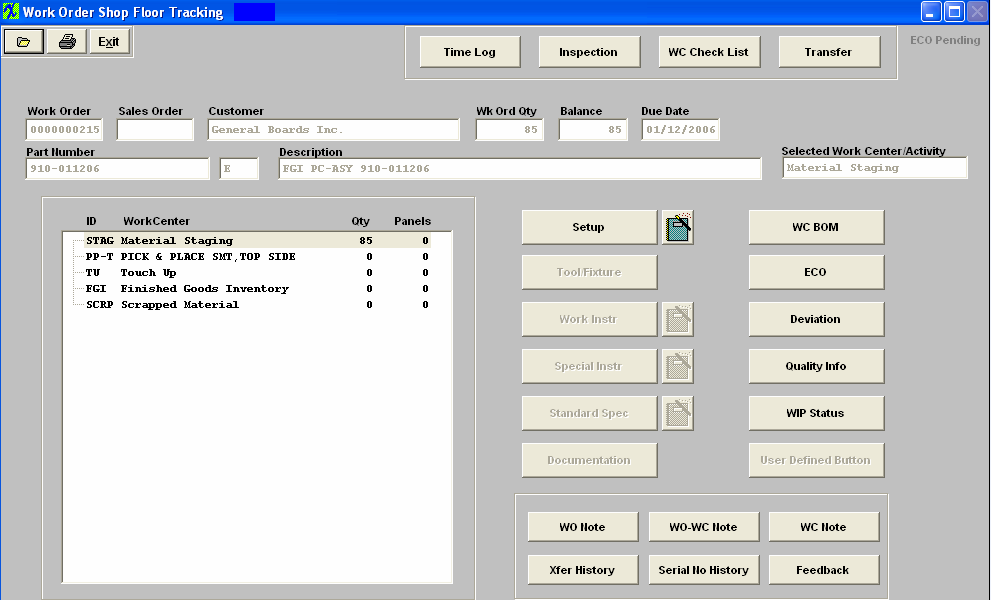
Depress the "Inspection" button located at the top of the screen.
The following screen will appear:
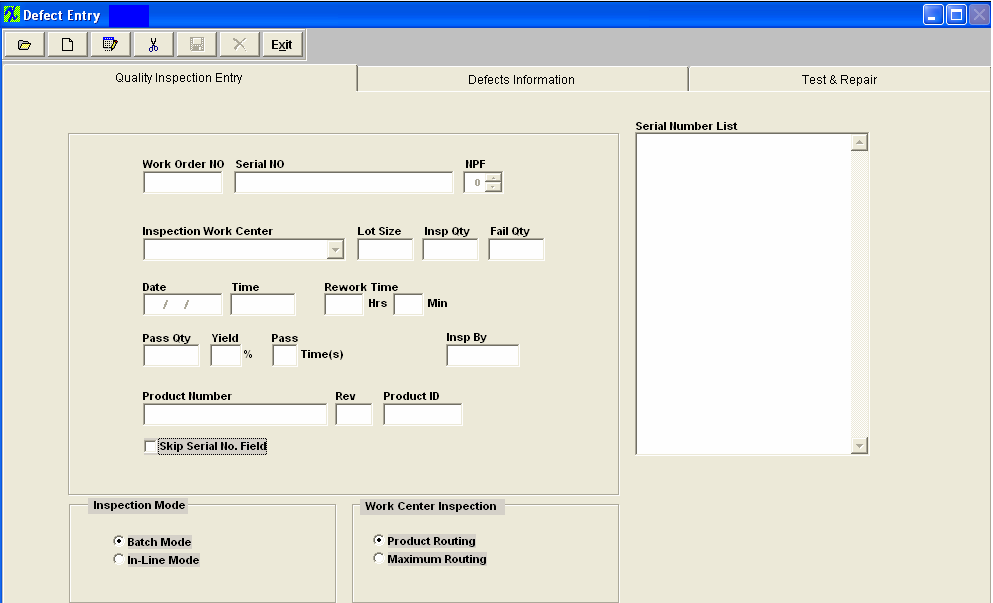
Entering Quality Inspection Data
There are two different ways to enter the Inspection Data: Batch Mode or In-Line Mode
Batch Mode
The first information tab records information about the work order. This includes lot size, failures, inspection quality, date, etc.
Depress the Add action button. Enter the password of the Employee that has inspected the product.
When the user first brings up the Defect Entry program, and before entering or editing data, they have the option to check or uncheck the “Skip Serial No. Field”. Once the data entry process is begun, the option is cleared until the user exits the defect entry form and re-enters it.
Adding Work Order Defect Information Without Serial Number Tracking
Enter the Work Order number, choose the Inspection Work Center from the pulldown, enter Lot Size inspected, Inspected Qty, and Failed Qty.
The Date, Time, Pass Qty, and Yeild % will default in. The date and time may be changed if needed.
The user may enter estimated rework time, if desired.
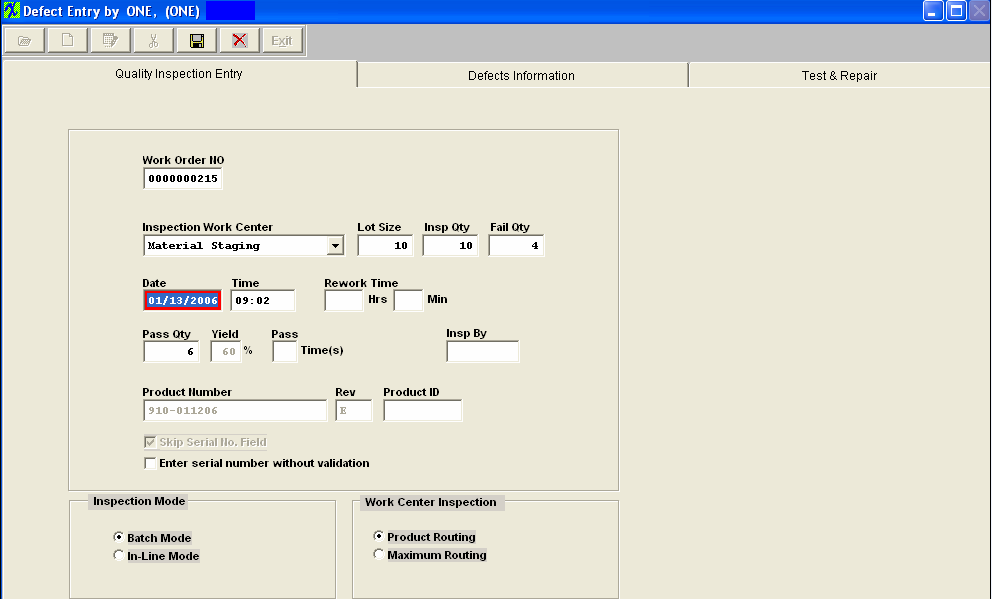
Depress the Defects Information tab and the following screen will appear:
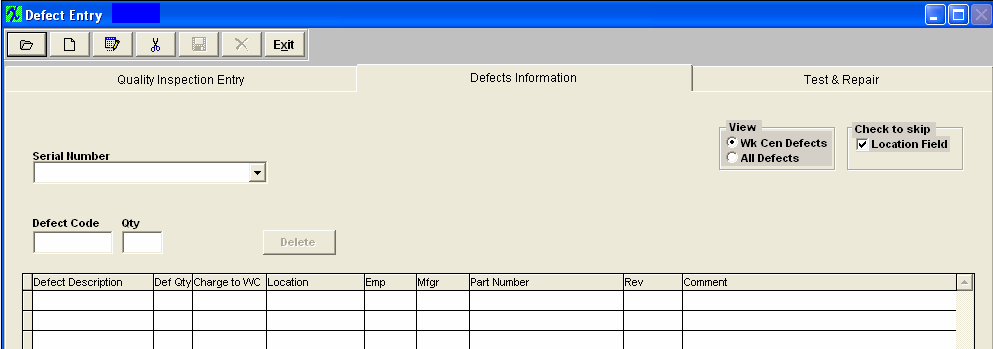
The user may then enter a defect code by manually typing in the code, or by scanning a bar-code menu, or by double clicking on the field to review a list of defect codes.
The list displayed will depend on which view is selected (in upper right hand corner of screen). If Work Center Defects is chosen, only those defects associated with the work center (as established in the system setup/Quality Defect Codes) will be displayed. If All Defects is chosen, then every defect entered in the system setup/Quality Defect Codes will be displayed.
The user may select one or more defects from the list by holding down the Control Key while clicking on the defects to be selected.
After completing the selection of the defects involved with the current inspection, clicking on the OK button loads the selected defects into the defect information screen.
Although ManEx will enter a Charge To Work Center code based on the work center entered or the location of the part, the user may modify the originating work center by clicking on the field and selecting another work center from the list.
The user may (optionally) then enter in the location (reference designator) where the defect was observed.
The user then must select an Employee from the pull down. The employee's being displayed in the pull down are only the employee's that are assigned to work centers (in the Security module) that are the same work centers listed in the Shop Floor Tracking by Work Order module and is sorted by the Employee User ID Number.
The system will check the BOM to be sure that the location entered here matches locations entered on the Bill of Materials.
When a valid location is entered, then system searches the Bill of Material to find manufacturers approved for the product, and displays a list of the approved manufacturers for the user to identify which manufacturer was associated with the defect observed. The user double-clicks on the manufacturer's name for the defective part, and the manufacturers name is placed in the defect information screen.
ManEx defaults the number of defects to one item, but the user may overwrite the quantity with an observed quantity greater than one.
The user may also enter a brief comment about the defect, for future reference.
The completed screen should appear as follows:
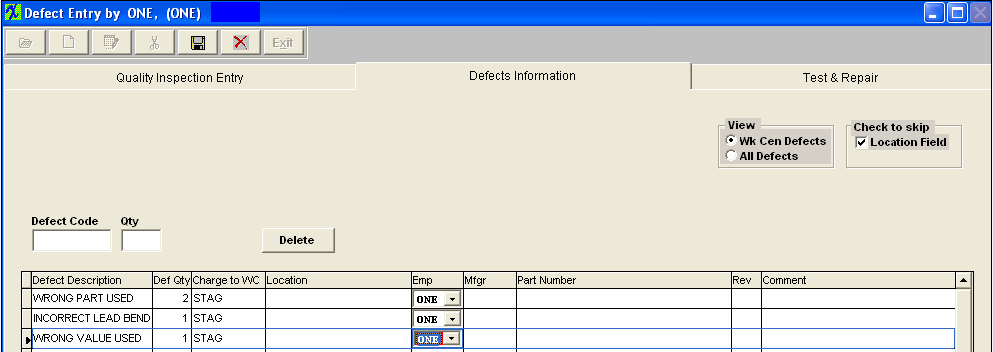
Depress the Save record action button to save changes or the Abandon changes action button to abandon changes.
If you depress the Save record action button, the following message will appear:
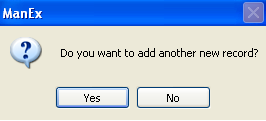
If you want to add another defect record for the same user "ONE" then depress YES, if you want to add a defect record for a different user (Example user "TWO"), then you must depress NO. Depress the Add record action button and enter user "TWO"s password and continue to enter the defect information.
When the user has completed the defect information, they may click on the Test & Repair tab, to enter more information about the part.
NOTE: The Test & Repair is actually a separate OPTIONAL module, but has been included into the Defect Entry screen for ease of use for the operators. For further detail about this module see Article #3291..
Adding Work Order Defect Information With Serial Number Tracking
Enter the Defect Entry screen. Depress the Add Record action button. Un-check the "Skip Serial No Field"
If the user is tracking serial numbers, then the first field to be entered (or bar-code scanned) is the serial number of the product being inspected. (Not the Work Order number).
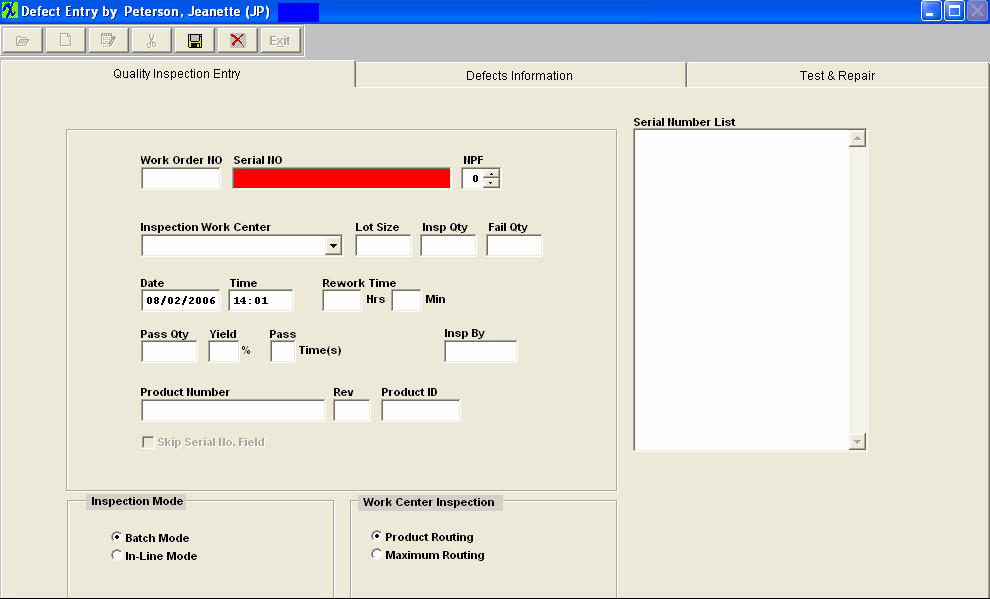
Type in the serial number. When the serial number has been entered, ManEx will complete the work order and product information. ManEx will also enter the current work center location of the serial number supplied.
The user now has the option of continuing to scan (or type) serial numbers, and log the defect information for each one later, or enter a serial number then the defects for that serial number, enter the next serial number, then the defects for the second serial number, etc. When multiple serial numbers have been entered, the data will refer to the serial number that is highlighted in the Serial Number list.
ManEx will enter in the lot size according to the quantity of serial numbers showing in the serial number list.
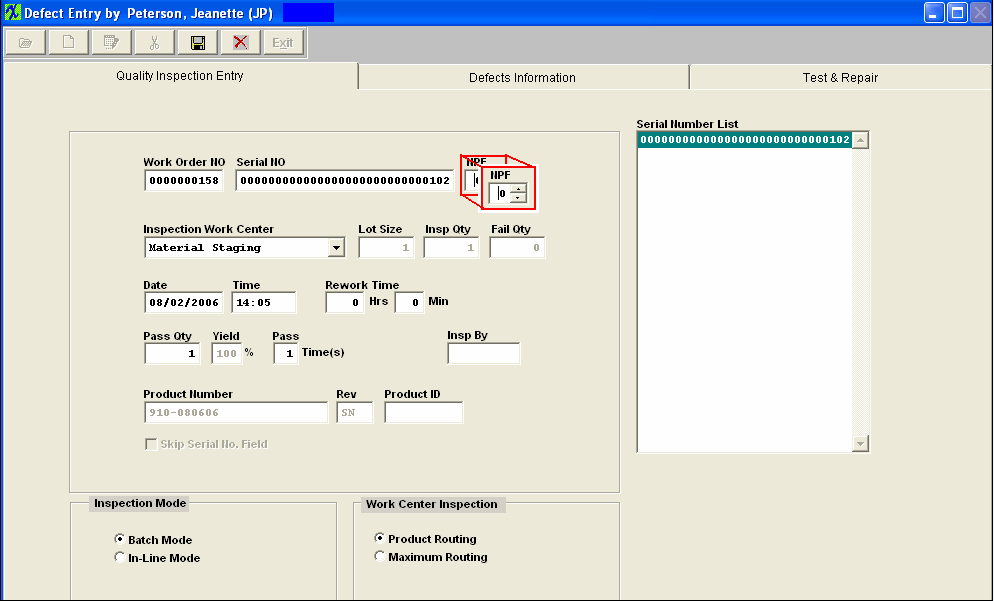
The next field, “NPF” is provided for the user to record when observing the product and finding that there is “No Problem Found”. If the serial number had previously been rejected, and analysis of the product yield no further problem, either with cosmetics or function, then the user may change this number to 1, meaning the first time it was inspected or tested, no problem was found. If the product serial number is subsequently rejected again, and a second inspection finds no problem, the number may be incremented to a “2”. This will alert users to repeated rejections of a product serial number, one or more times with no discernable defects.
If the number of times that a part has experienced an NPF exceeds that established in the system setup/Quality Defect Codes the user will receive the displayed warning message and will allow you to proceed on with the Inspection. This is just a notification that the board has passed the maximum NPF cycle.
Entering Defect Information
This screen operates as described under Entering Defect Information without serial numbers, except that the user must enter data for each serial number recorded. The serial number may be chosen by highlighting the serial number in the serial number box on the first screen, or in the defects information screen, by pressing the down arrow button next to the serial number field and selecting a serial number.
Defect information is entered in the same fashion as described above, except that the user should remember that the data being entered is for one part at a time, by serial number of the part.
The other difference in using serial number defect tracking is that on the Test & Repair screen, the user may view the Serial Number History tab. This view will display both the transfer history of the serial number through the work centers, and the history of defects associated with the serial number of the product.
(Note: if you are entering Defect information and not using the Serial No, then this screen will remain blank)
The user completes the defect entry for the first defect code (The location, quantity of defects observed, etc.). The process is repeated for each defect observed, storing the location and serial number to be analyzed at a later time.
At the conclusion of defect entries for the lot, the Save action button is pressed to retain the data. If the user elects to ignore all data entered in this session, the Abandon changes action button may be clicked to void any entries. Notice that ManEx computes the total number of defects observed for the defect code and displays the number next to the defect code.
Entering Defect Information Without Serial Number Validation
The “Enter Serial Number without Vailidation” option will only be enabled if the user skips the regular Serial number entry, and if the Work Order Product has not been serialized within the ManEx system.
This feature has been added to allow the users the ability to inspect Serial Numbers that do not actually exist within the ManEx system. (for example serial number created outside of ManEx, by customer or other software, etc. . .) If the user checks the “Enter serial number without validation” then ManEx does not validate when the users enters the Serial Number. The system just records the entry for later SQC analysis purpose. (note: if the work order is serialized, then the user can NOT use this feature).
Enter the Defect Entry screen. Depress the Add Record action button. Select “Enter Serial Number without Validation. ”
Enter the Work Order number.
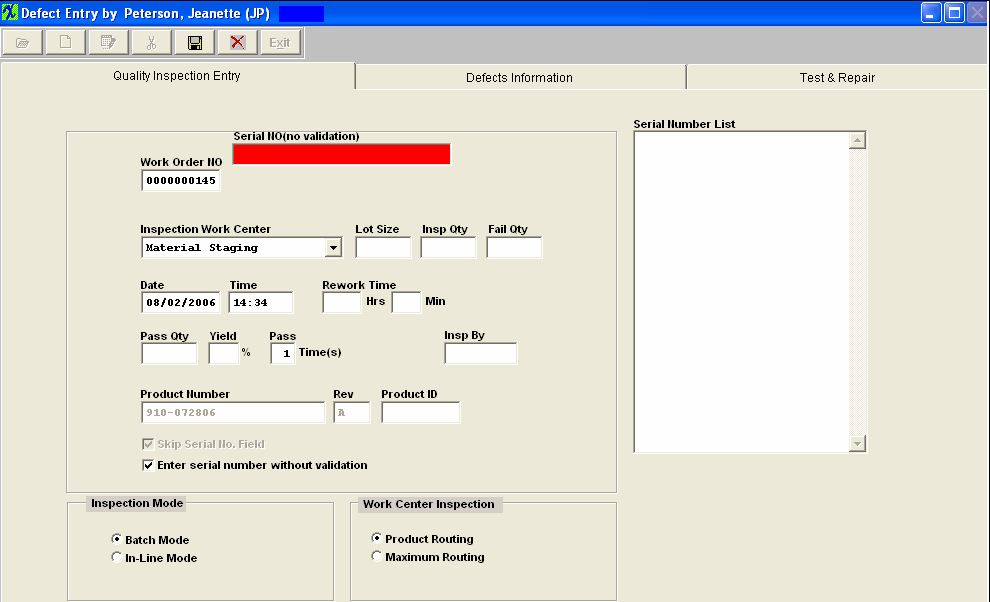
Then enter in the desired Custom Serial Numbers. The remaining process will then be the same as listed above.
In-Line Mode
When the user chooses In-Line inspection, either by setting it as the default in the Quality Defect Setup, or by selecting In-Line on the initial Quality Inspection Entry screen.
The first information tab records information about the work order. This includes lot size, failures, inspection quantity, date, etc.
Depress the Add action button. Enter the password of the Employee that has inspected the product.
Check the Skip Serial No. Field (if not applicable).
Enter the Work Order number, choose the Inspection Work Center from the pulldown.
The Product Number, Revision and Current Qty will default in.
Then the Passed and Failed buttons are active. The user then clicks on either of these two buttons to proceed with the inspection.
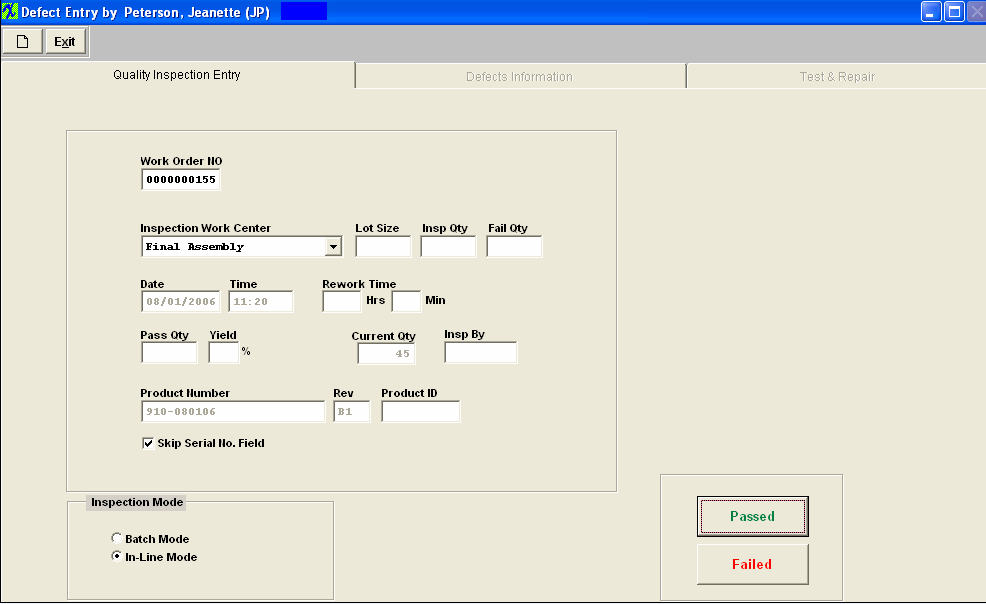
Clicking on the Passed button transfers the serial number to the next work center (based on the product routing), and increments the lot inspection information by one and records the date time and inspector.
Clicking on the Failed button activates the Defect Information Entry screen for the user to record his/her observations.
Defect information is entered in the same fashion as described above, based on with or without serial numbers.
When the user has completed the defect information, may click on the Test & Repair page, to enter more information about the part.
The Test & Repair is actually a separate OPTIONAL module, but has been included into the Defect Entry screen for ease of use for the operators. Please see the Test & Repair article for further detail.
Edit Work Order Defect Information
After a work order has been found or entered, it may be edited by selecting the Edit record action button.
After selecting the transaction, the user may edit fields as described above in entering data.
|
1.4.2. Enter the Defect Data Information for the DPMO by Employee Report | In order to have the "DPMO by Employee" report create valid data, the user must be sure to enter the opportunities for defects (PPM) in the Work Order Traveler Setup and the employee must inspect the board and be assigned to the defects. The "DPMO by Employee" report only gathers data if BOTH "Inspected By" and "Emp" are the same user, and the PPM is setup. See Article #3156 for further detail on DPMO. The following steps need to be followed to collect and track defects per employee.
All data must be Entered in the Quality Inspection Entry and Defect Information screens, with in the Shop Floor Tracking Module.
Entering a Defect Code Entry to a Work Order for the "DPMO by Employee" report
Enter Production/Shop Floor Tracking by Work Order Module
Find a Work Order in SFT Module.
| 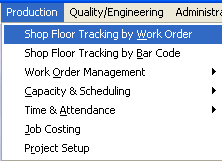 |
The following screen will appear:
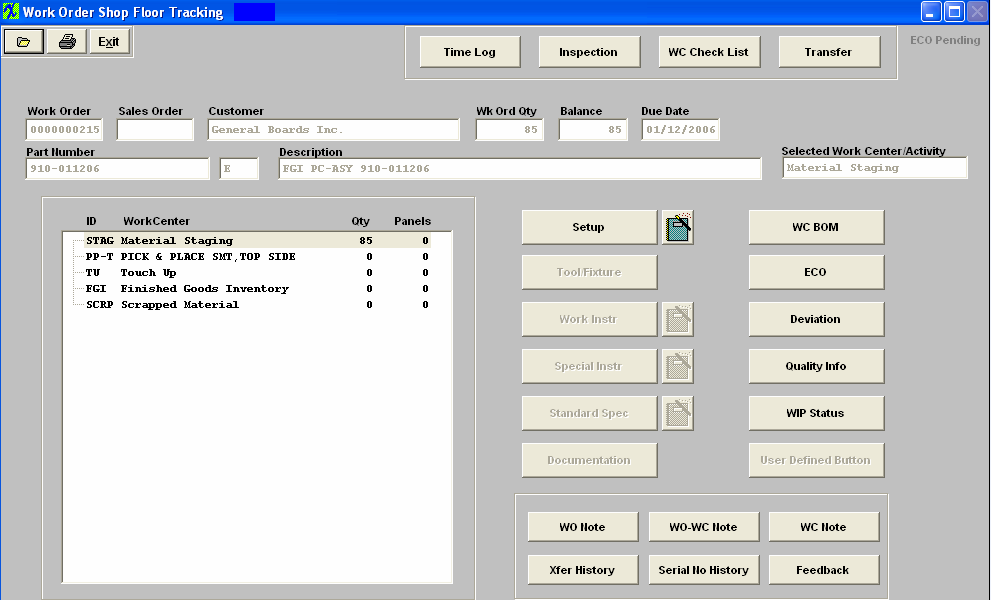
Depress the "Inspection" button located at the top of the screen.
The following screen will appear:
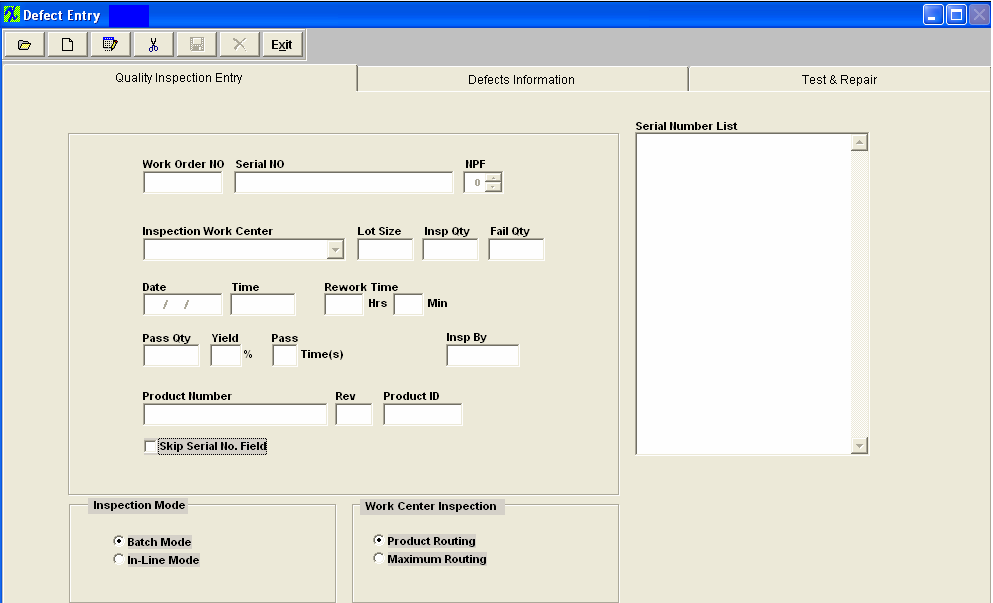
Entering Quality Inspection Data
The first information tab records information about the work order. This includes lot size, failures, inspection quality, date, etc.
Depress the Add action button. Enter the password of the Employee that has inspected the product and will be assigned to the defects. Example: If user "ONE" is going to be assigned to the defect(s) then you must enter user "ONE"'s password.
Check the Skip Serial No. Field (if not applicable).
Enter the Work Order number, choose the Inspection Work Center from the pulldown, enter Lot Size inspected, Inspected Qty, and Failed Qty.
The Date, Time, Pass Qty, and Yeild % will default in.
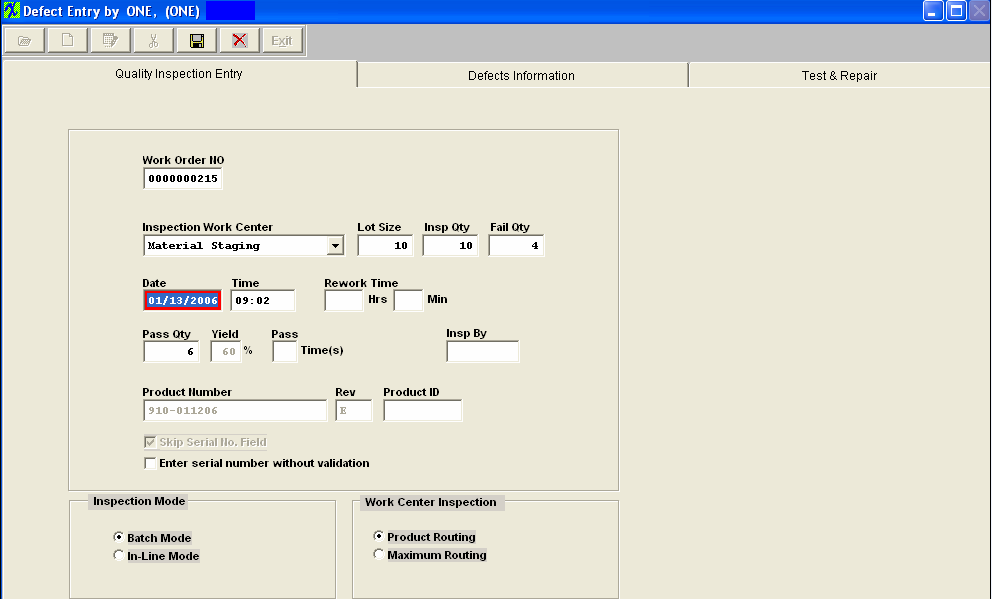
Depress the Defects Information tab and the following screen will appear:
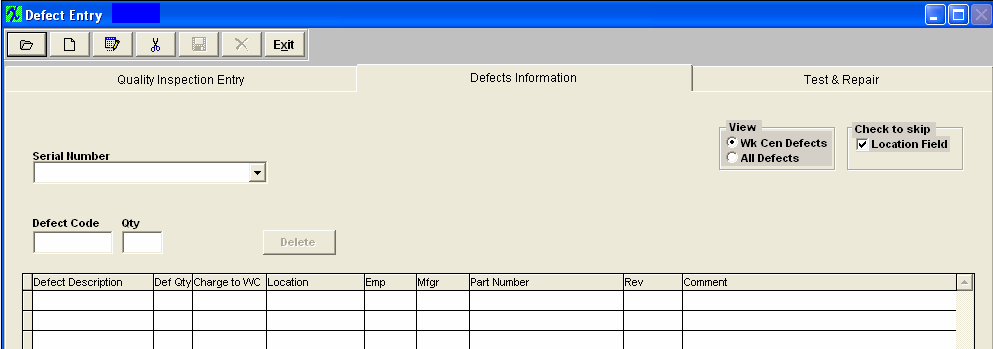
The user may then enter a defect code by manually typing in the code, or by scanning a bar-code menu, or by double clicking on the field to review a list of defect codes.
The list displayed will depend on which view is selected. If Work Center Defects is chosen, only those defects associated with the work center (as established in the Quality Defect Codes setup) will be displayed. If All Defects is chosen, then every defect entered in the Quality Defect Codes setup will be displayed.
The user may select one or more defects from the list by holding down the Control Key while clicking on the defects to be selected.
After completing the selection of the defects involved with the current inspection, clicking on the OK button loads the selected defects into the defect information screen.
Although Manex will enter a Charge To Work Center code based on the work center entered or the location of the part, the user may modify the originating work center by clicking on the field and selecting another work center from the list.
The user may (optionally) then enter in the location (reference designator) where the defect was observed.
The user then must choose the Emp from the pull down, which would be "ONE", because it needs to be the same user that has been entered in the "Inspected By". The user is allowed to enter other user's name on Defect detail page in the "Emp" column. But when the "DPMO by Employee" report is run, it will not display the records assigned to the different users.
The system will check the BOM to be sure that the location entered here matches locations entered on the Bill of Materials.
When a valid location is entered, then system searches the Bill of Material to find manufacturers approved for the product, and displays a list of the approved manufacturers for the user to identify which manufacturer was associated with the defect observed. The user double-clicks on the manufacturer's name for the defective part, and the manufacturers name is placed in the defect information screen.
Manex defaults the number of defects to one item, but the user may overwrite the quantity with an observed quantity greater than one.
The user may also enter a brief comment about the defect, for future reference.
The completed screen should appear as follows:
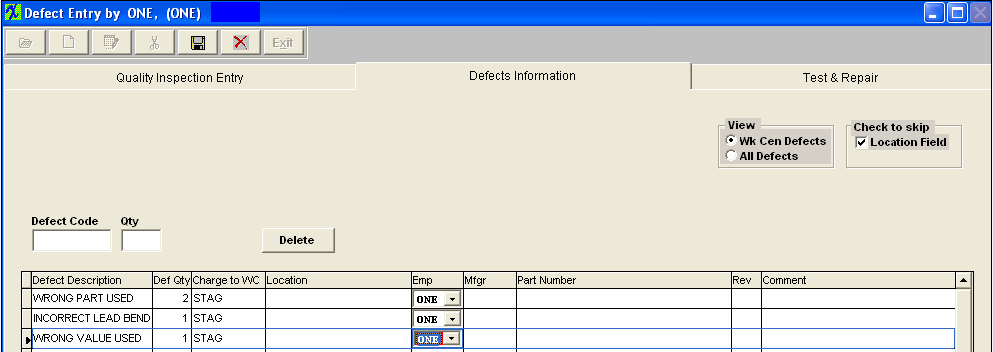
Depress the Save record action button to save changes or the Abandon changes action button to abandon changes.
If you depress the Save record action button, the following message will appear:
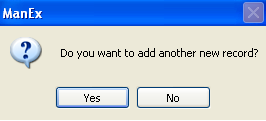
If you want to add another defect record for the same user "ONE" then depress YES, if you want to add a defect record for a different user (Example user "TWO"), then you must depress NO. Depress the Add record action button and enter user "TWO"s password and continue to enter the defect information.
When the user has completed the defect information, he/she may review the "DPMO by Employee" report Article #815, or may click on the Test & Repair page, to enter more information about the part.
The Test & Repair is actually a separate OPTIONAL module, but has been included into the Defect Entry screen for ease of use for the operators. Please see the Test & Repair Management (T&R) article for more information.
|
1.4.3. SQC - Setup an SQC Template |
Enter Quality/Engineering/Statistical Quality Control (SQC) Module |
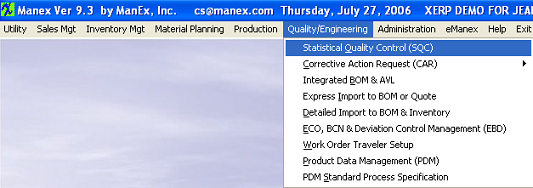 |
The following screen will be displayed:
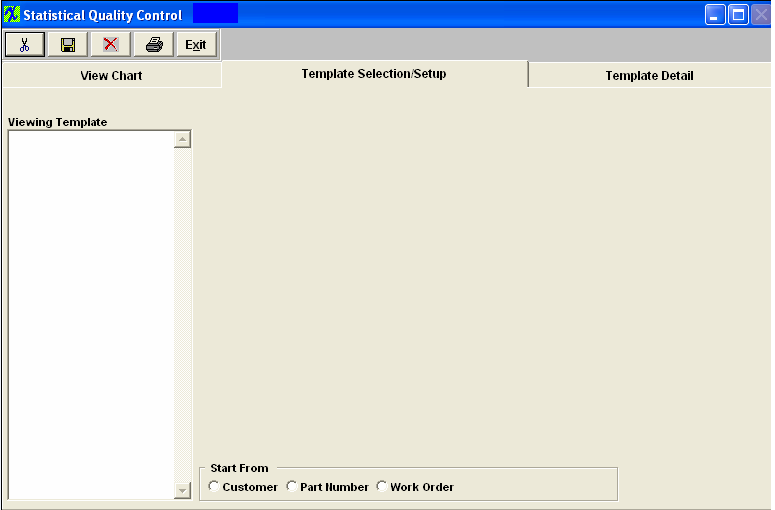
Template Selection Setup
This is the first screen to be used in the module. In this screen, STATISTICAL QUALITY CONTROL graphics are created by selecting parameters to be considered in the graph.
This screen operates differently than all other ManEx screens. When bringing up the SQC module, the user is first presented with a template screen from which to choose parameters to be included in the information displayed.
When the user enters the system, he/she may select how they want to start the process of selection. Click on the Customer, Part Number or Work Order radial.
Clicking on the Customer radial will bring up the following selection screen:
Select either Customer List or All Customers. |
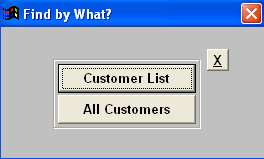 |
Selecting by Customer List will bring up the following selection screen:
(If the user selects by All Customers, the same screen will appear except All available Customers will be listed within the Customer section)
Type the desired customer into the red box or highlight and double click.
|
|
The following screen will appear:
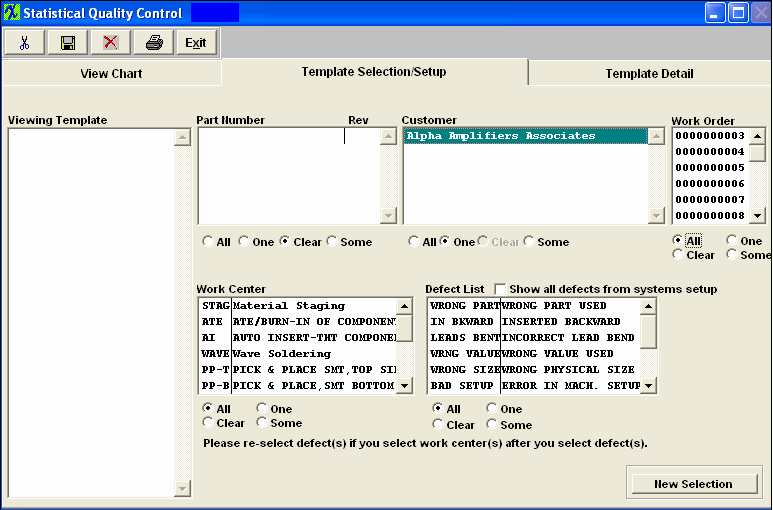
If the start is from Part Number, the following selection will appear: |
|
If the user selects Product Number List, the following list will appear:
(If the user selects All Products, the same screen will be displayed except all products will be listed in the part number section)
Type the Part Number into the red box or highlight and double click.
|
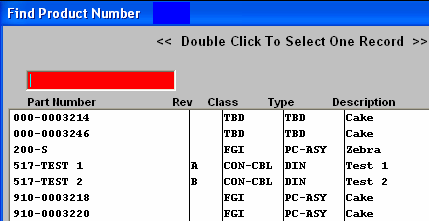 |
The following screen will appear:
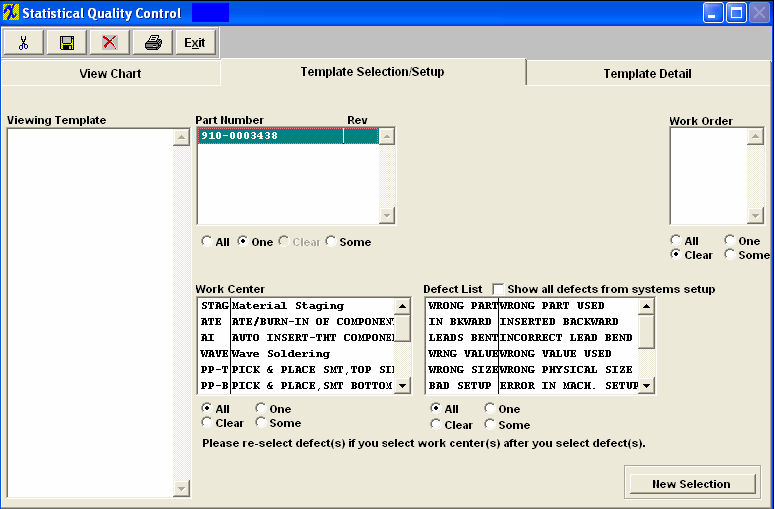
If the user starts with the Work Order start, the following selection will appear:
|
|
If the user selects the Work Order List option, the following list of Work Orders will appear:
(If the user selects All Work Orders the same screen will be displayed except all work orders will be listed in the Work Order section)
Select between Open or All. Type the Work Order Number into the red box or highlight and double click.
|
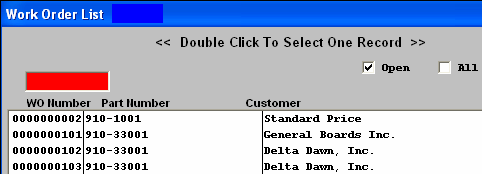 |
The following screen will appear:
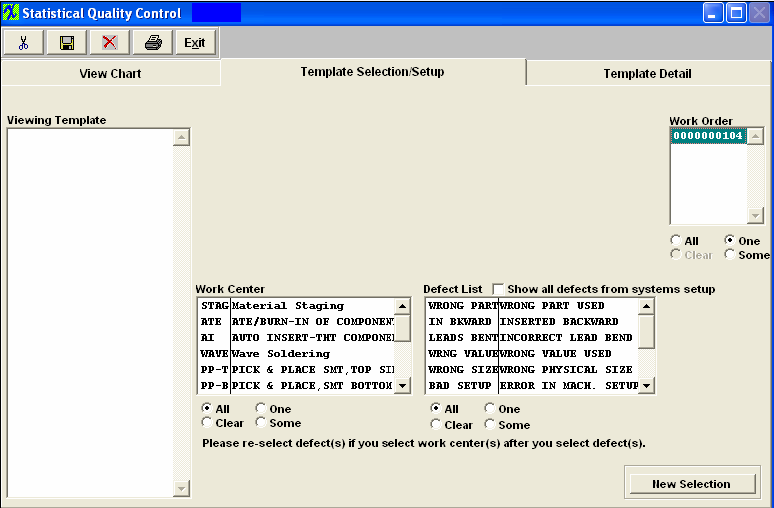
|
In the Work Order section, choose from All, One or Some. If you’ve selected one, highlight the desired work order. If you want more than one, depress the Ctrl key and click on the ones desired.
|
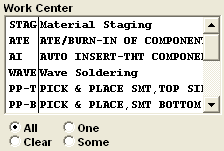 |
In the Work Center section, choose from All, One or Some. If you’ve selected one, highlight the desired work center. If you want more than one, depress the Ctrl key and click on the ones desired.
|
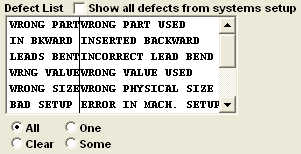 |
Make the same selection in the Defect List section. If you want all defects displaying as per the System Setup, check the Defect List box.
|
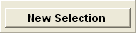 |
To make a new selection, depress the New Selection button.
|
Template Detail Screen
Pressing on the Template Detail tab brings up the following screen:
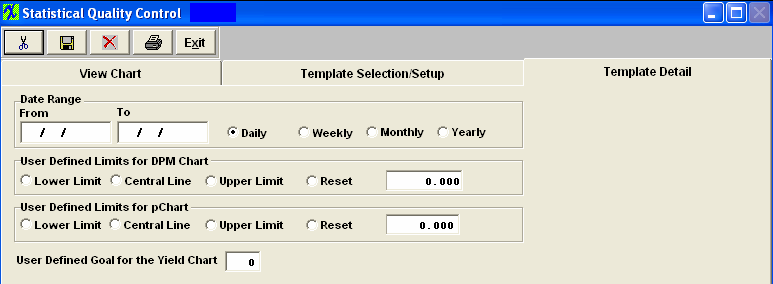
Enter the Date Range, From and To. Mark the Radial for the view by Daily, Weekly, Monthly, or Yearly.
Mark the radial for the User Defined Limits for DPMO chart: Lower Limit, Central Line, Upper Limit or Reset. Indicate Central Line amount in box.
Mark the radial for the User Defined Limits for pChart: Lower Limit, Central Line, Upper Limit or Reset. Indicate Central Line amount in box.
Indicate the user defined goal for the Yield Chart.
To Save this template for future use go back to the Template Selection/Setup tab enter in a name and depress the Save button.
The Template will be saved in the Viewing Template field for future use.
|
1.4.4. SQC - Data Viewing And Analysis |
Enter Quality/Engineering/Statistical Quality Control (SQC) Module |
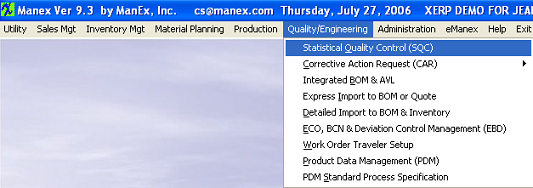 |
The following screen will be displayed:
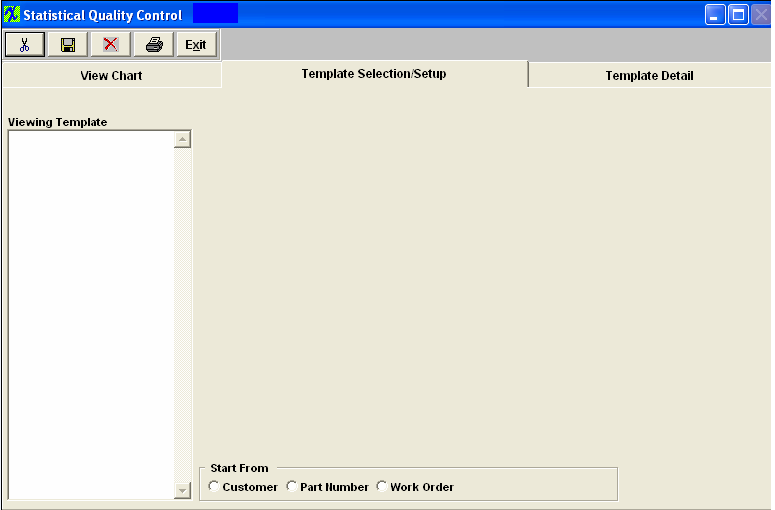
Template Selection Setup
This is the first screen to be used in the module. In this screen, STATISTICAL QUALITY CONTROL graphics are created by selecting parameters to be considered in the graph.
This screen operates differently than all other ManEx screens. When bringing up the SQC module, the user is first presented with a template screen from which to choose parameters to be included in the information displayed.
When the user enters the system, he/she may select how they want to start the process of selection. Click on the Customer, Part Number or Work Order radial.
Clicking on the Customer radial will bring up the following selection screen:
Select either Customer List or All Customers. |
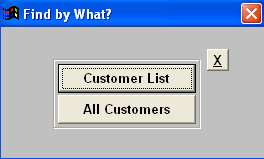 |
Selecting by Customer List will bring up the following selection screen:
(If the user selects by All Customers, the same screen will appear except All available Customers will be listed within the Customer section)
Type the desired customer into the red box or highlight and double click.
|
|
The following screen will appear:
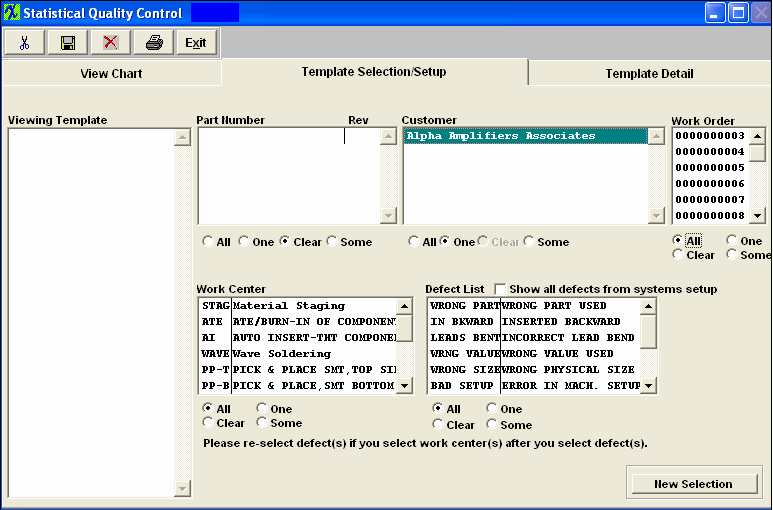
If the start is from Part Number, the following selection will appear: |
|
If the user selects Product Number List, the following list will appear:
(If the user selects All Products, the same screen will be displayed except all products will be listed in the part number section)
Type the Part Number into the red box or highlight and double click.
|
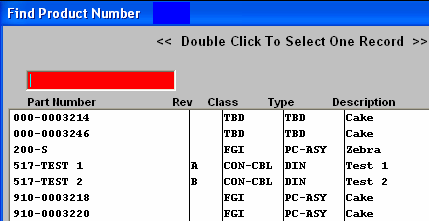 |
The following screen will appear:
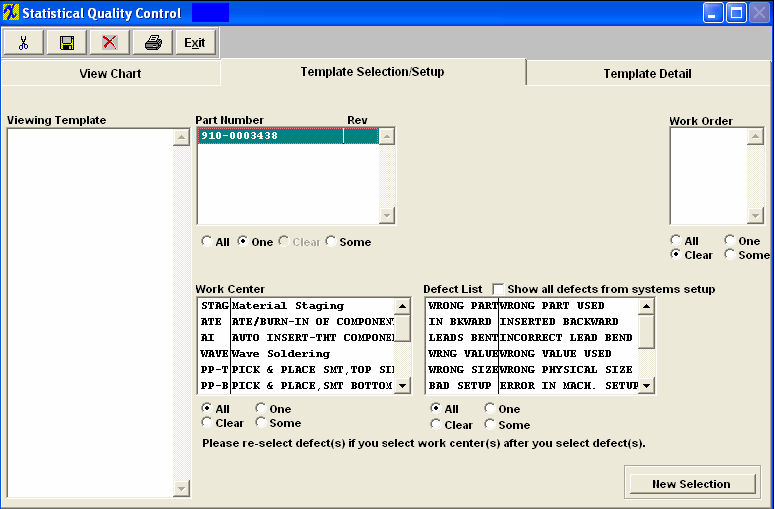
If the user starts with the Work Order start, the following selection will appear:
|
|
If the user selects the Work Order List option, the following list of Work Orders will appear:
(If the user selects All Work Orders the same screen will be displayed except all work orders will be listed in the Work Order section)
Select between Open or All. Type the Work Order Number into the red box or highlight and double click.
|
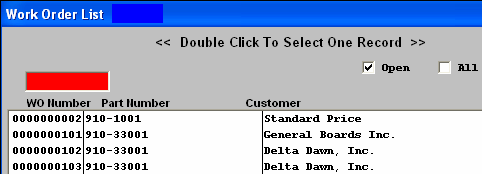 |
The following screen will appear:
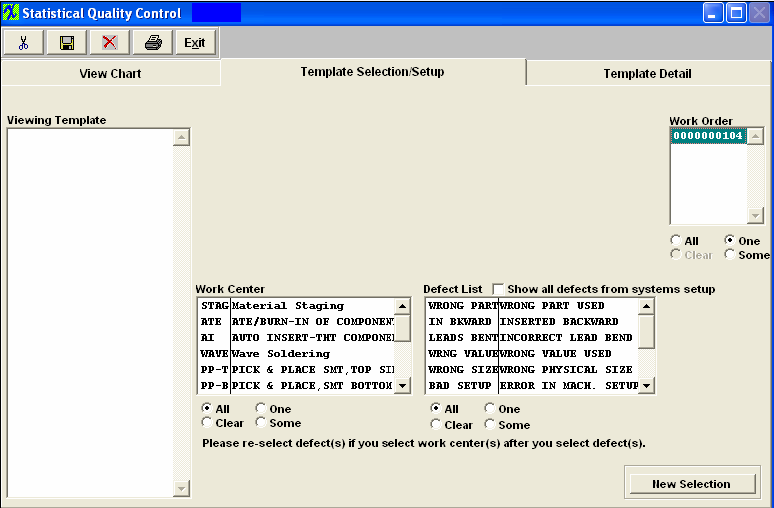
|
In the Work Order section, choose from All, One or Some. If you’ve selected one, highlight the desired work order. If you want more than one, depress the Ctrl key and click on the ones desired.
|
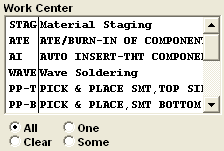 |
In the Work Center section, choose from All, One or Some. If you’ve selected one, highlight the desired work center. If you want more than one, depress the Ctrl key and click on the ones desired.
|
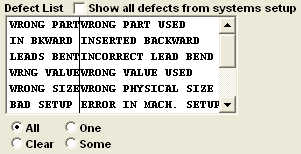 |
Make the same selection in the Defect List section. If you want all defects displaying as per the System Setup, check the Defect List box.
|
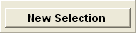 |
To make a new selection, depress the New Selection button.
|
Template Detail Screen
Pressing on the Template Detail tab brings up the following screen:
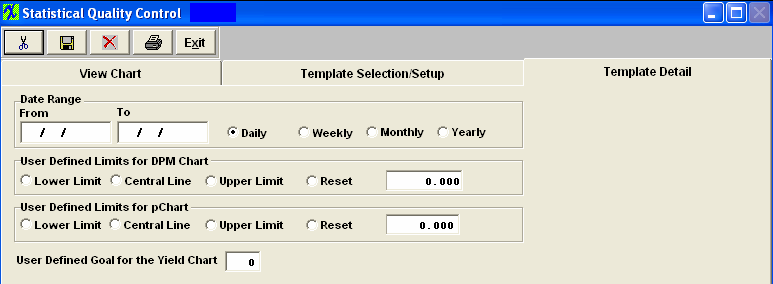
Enter the Date Range, From and To. Mark the Radial for the view by Daily, Weekly, Monthly, or Yearly.
Mark the radial for the User Defined Limits for DPMO chart: Lower Limit, Central Line, Upper Limit or Reset. Indicate Central Line amount in box.
Mark the radial for the User Defined Limits for pChart: Lower Limit, Central Line, Upper Limit or Reset. Indicate Central Line amount in box.
Indicate the user defined goal for the Yield Chart.
View Chart Screen/Graphs
Pressing on the View Chart brings up the Graphics Display Window.
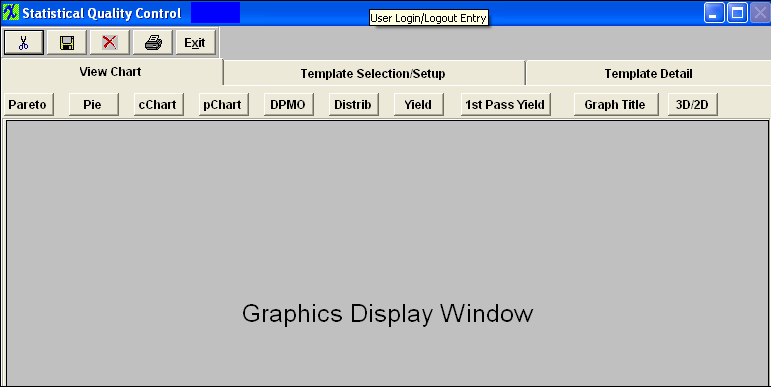
Defect Pareto Chart - The results being displayed in the Pareto Chart are from WO #242 for a build of 500. Qty of 5 with Wrong Part (Displayed in Blue) and Qty of 3 with Leads Bent (Displayed in Green) Total of 8 Failed 500/8 = 62.5% Failed and 37.5% Passed
Note: The black line is a cumulative % of total defects represented by the current defect and all preceding defects. That is why it reaches 100% by the right side of the graph.
Defect Pie Chart - The results being displayed in the Defect Pie Chart are from WO #242 for a build of 500. Qty of 5 with Wrong Part (Displayed in the Blue) 62.5% and Qty of 3 with Leads Bent (Displayed in Green) 37.5%. Total qty failed 8.
cChart (Not available in 3D) The results being displayed in the cChart are from all Work Orders, Work Centers, and all defects from 062706 thru 072706 (1 month)
The formula for the Central line (Red) is: c = Total Defects (divided by) Number of Subgroups
Upper Control Limit (UCL) = c + 3 (divided by) p
Lower Control Limit (LCL) = c - 3 (divided by) p (or 0, whichever is greater)
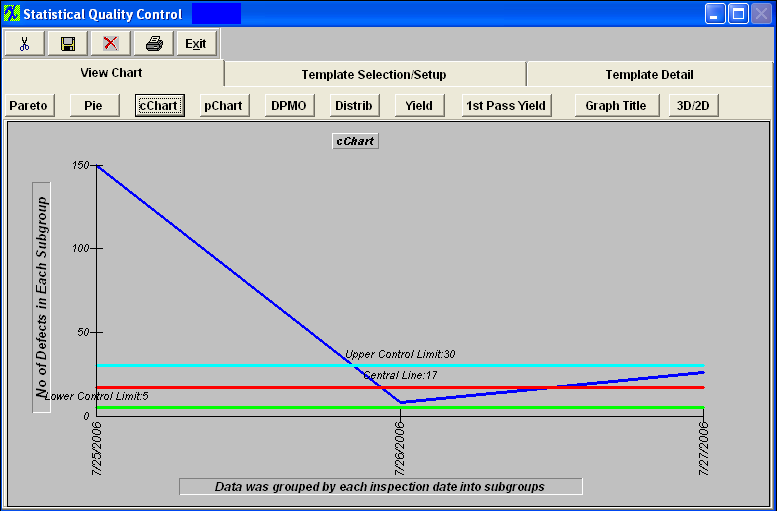
pCHART (not available in 3D) The results being displayed in the pChart are from all Work Orders, Work Centers, and all defects from 062706 thru 072706 (1 month)
The formula for the Central line (Red) is: p = Total Number Failed (divided by) Total Number Inspected
Upper Control Limit (UCL) = p + 3 (divided by) p (1-p) divided by n
Lower Control Limit (LCL) = p - 3 (divided by) p(1-p) divided by n (or 0, whichever is greater)
n = number inspected (sample size)
DPMO (Defects Per Million Opportunities) Chart (Which means the number of things wrong observed in the inspection of a part, or board assembly). The results being displayed in the DPMO Chart are from WO #242 for a build of 500. DPMO Example below = 8(Total qty failed)* 1000000/100*500 (Qty Inspected) = 160
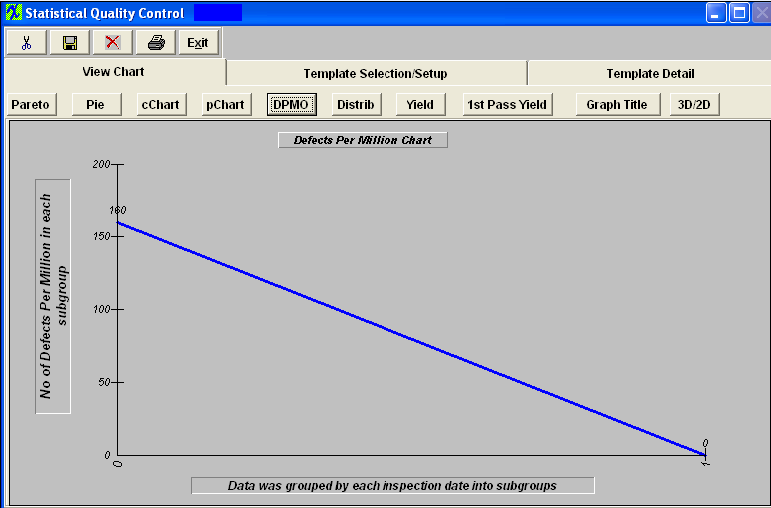
Defects Per Million Opportunities. There are several ways to setup the opportunities (which means the number of possible defects that can occur on a product), but it is up to each company to make that decision. For Example: Some may say that a resistor with two leads that are not properly soldered is counted as two defects and some may only count it as one defect, since it is one part that was assembled incorrectly. The opportunity or the standard opportunity is entered in the Work Order Traveler Setup module. The field is called PPM = Parts per million.
The DPMO chart uses the PPM as a reference to measure the actual failures against the total inspected quantity.
See Article #3156 for further detail on DPMO.
The formula for calculating DPMO chart is as follows:
Example (2+3+3) = SUM of defect quantities (8) * opportunities or PPM (1,000,000) (divided by) Qty Inspected (500) (divided by) parts per unit (100) = 160
Daily, Weekly, Monthly, Yearly
On the Y axes the graph shows number of defects per million
One the X axes day or week or month or year
This graph collects defect information for the selected work centers and work orders in the selected date range. The user also has to select if the information will be grouped by day, week, month, or year.
The selected group will be your X coordinates on the graph.
The Y coordinates will be calculated as sum of the defect quantities *opportunities or PPM divided by total Qty inspected (divided by) parts per unit (qty was entered in the routing module) grouped by X coordinate unit (Daily, weekly, monthly, yearly).
This is a data line there is three more control lines displayed on the graph:
Central control line:
Upper control line:
Lower control line
All three lines could be user define lines.
If the lines are not user define lines they calculated as following
Central Line
lnCentralLine=lnTotalDef/lnTotalComp, where lnTotalDef is sum of all defect quantities * 1000000 and lnTotalComp is sum of inspected quantities*Parts Per Unit (entered in the routing module)
At this time system will decide if it can use average group size or not. If the size group varies more tan 15% the system will use variance Upper and Lowercontrol limit. If average group size could be used the average group size gets calculated by taking lnAvrgSubgrSize=lnTotalComp divided by number of groups and rounded to the nearest integer.
Calculation for the Upper Control Line
LnUpperLine=ROUND(((3*(SQRT(lnCentrLine*(1000000-lnCentrLine))))/SQRT(lnAvrgSubgrSize)),3)
Calculation for the Lower Control Line
lnLowerLine = ROUND(lnCentrLine -((3*(SQRT(lnCentrLine*(1000000-lnCentrLine))))/SQRT(lnAvrgSubgrSize)),3)
lnLowerLine = IIF(lnLowerLine<0,0,lnLowerLine)
Defects Distribution Chart - The results being displayed in the pChart are from all Work Orders, Work Centers, and all defects from 062706 thru 072706 (1 month)
Yield Chart - "Yield" = Total number of units handled correctly through the process step(s). This is usually measured in a percentage. The results being displayed in the "Yeild Chart" is the ratio of summed inspected qty and summed passed qty, grouped by date (user can select WO number, defect code to be filtered). The results below are from all Work Orders, Work Centers, and all defects from 062706 thru 072706 (1 month).
1st Pass Yield Chart The results being displayed are from all Work Orders, Work Centers, and all defects from 062706 thru 072706 (1 month).
1st Pass Yield chart in the SQC module is designed only when the serial number is used for the work order. The system uses the serial number to determine how many serial numbers passed without failure/defects within a work order. 1st Pass Yield chart will be blank if there are no product tracked by serial number within the production floor
To enter a new title, depress the Graph Title button. The following will be displayed:
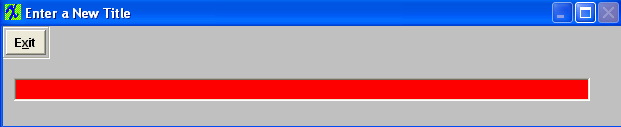
Enter in the new desired Graph Title. Depress the Exit button, and the graph title will be updated.
3D/2D - This is if you want to view the 1st Yield Chart in 3D
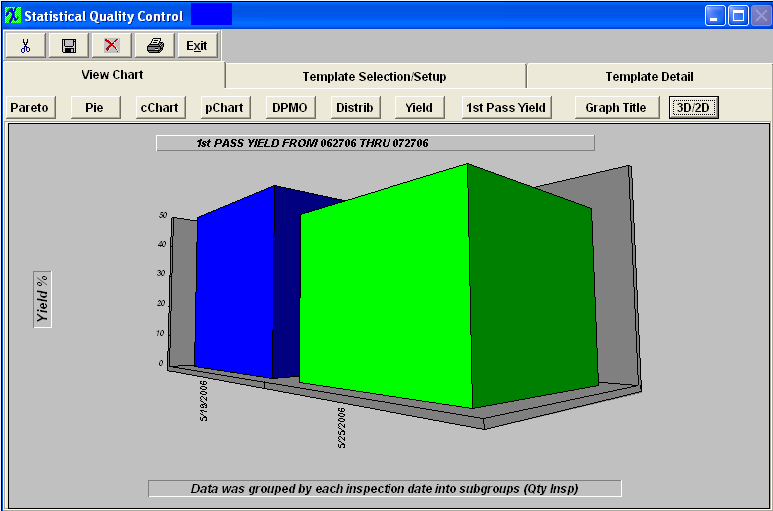
|
1.5. Reports - SQC |
To display or print a Report from the Statistical Quality Control (SQC), module. Enter the module.
1. To access the reports, depress the Print action button at the top of the screen. The report screen will appear.
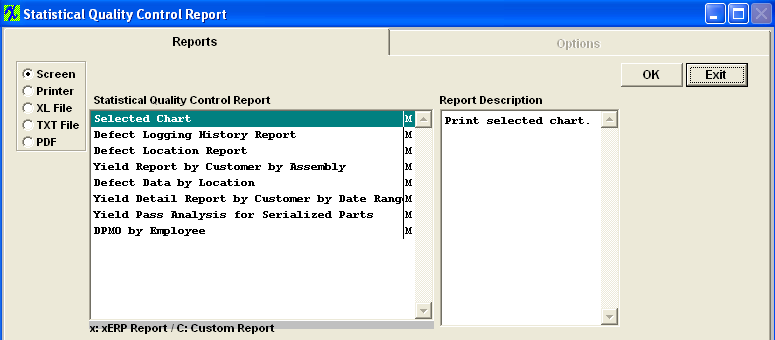
2. Select the output you desire by selecting one of the output radial selections at the top left of the screen, Screen, Printer, XL File, TXT File, or PDF.
3. Highlight the report desired and click on the option tab (if applicable).
Selected Chart report
If you want to print the selected chart, the chart you want to print must be displaying in the View Chart tab. The same exact chart viewed on screen will be printed.
Depress the OK button, and you will receive the following message. The selected chart only goes to printer or file, please go back to main screen to view chart.
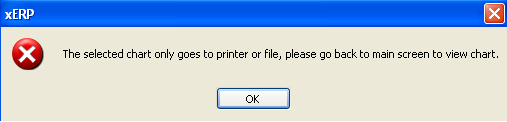
Defect Logging History report
If you select Defect Logging History Report, you will be asked to select the sort.
Select one of the following:Customer, Product Number, Work Order Number or Work Center.
|
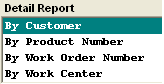 |
Select the date range. Highlight the Customer desired. Depress the > button. If you want all customers, depress the >> button.
Depress the Ok button.
|
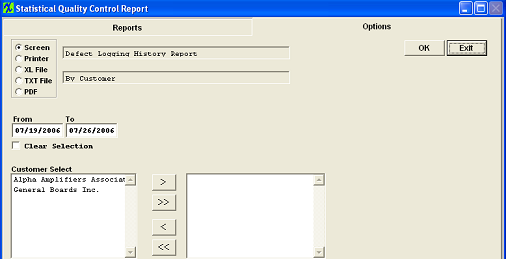 |
The following report will print:

Defect Location report
Select the date range. Highlight the Customer desired and depress the > button. If you want all customers, depress the >> button. Highlight the Work Center and depress the > button. If you want all Work Centers, depress the >> button.
Depress the OK button.
|
|
The following report is available:
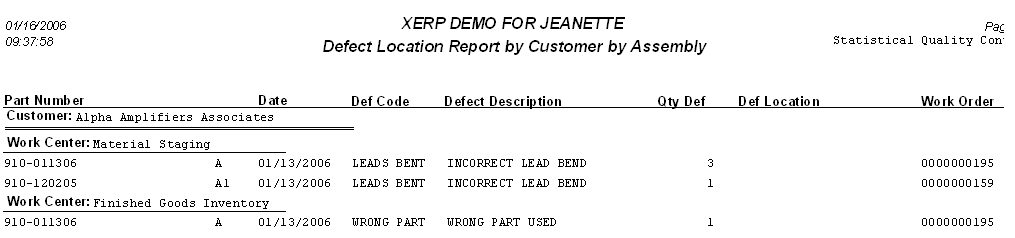
Yield Report by Customer by Assembly report
Select the date range. Highlight the Work Center and depress the > button. If you want all Work Centers, depress the >> button.
Depress the OK button.
|
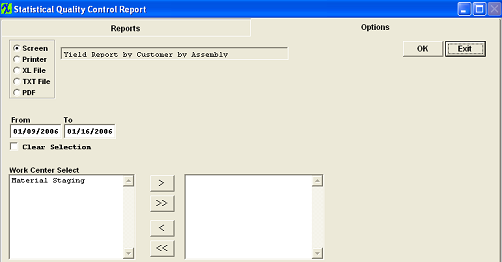 |
The following report will print:
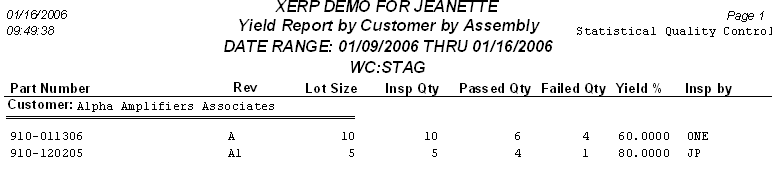
Defect Data by Location report
First you must enter data in Template Selection/Setup and Template Detail Screen. Then depress the Print action button, Highlight the Defect Data by Location report and depress the Ok button.
The following report will print:
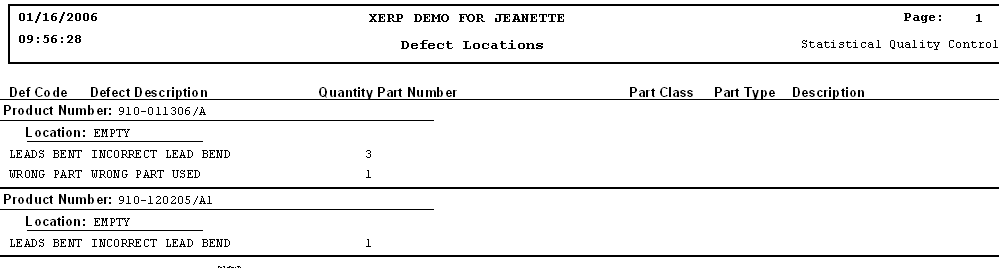
Yield Detail Report by Customer by Date Range
Select the Date Range. Click on the desired radial to select Open Work Orders only or All Work Orders. Highlight the Work Order desired and depress the > button. If you want all Work Orders, depress the >> button. Highlight the Work Center and depress the > button. If you want all Work Centers, depress the >> button. Highlight the Customer desired and depress the > button. If you want all customers, depress the >> button.
Depress the OK button
|
|
The following screen will appear:

Yield Pass Analysis for Serialized Parts report
Select the Date Range. Type the Yield Pass Number. Highlight the Work Center and depress the > button. If you want all Work Centers, depress the >> button.
Depress the OK
|
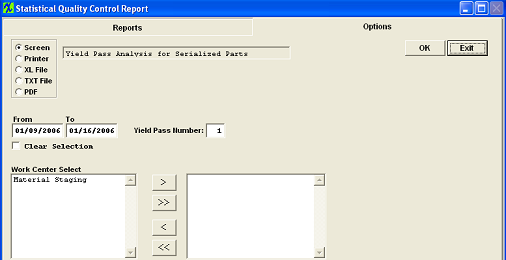 |
The following report will print:
DPMO by Employee
Select the Date Range. Highlight the Work Center desired and depress the > button. If you want all Work Centers, depress the >> button. Highlight the Employee and depress the > button. If you want all Employee's, depress the >> button.
Depress the OK button.
DPMO = Number of defect * opportunities or PPM (1,000,000) (divided by) Qty Inspected (divided by) parts per unit
In order to make this report data valid, the employee must inspect the board and be assigned to the defect. For more information see Article #1776.
|
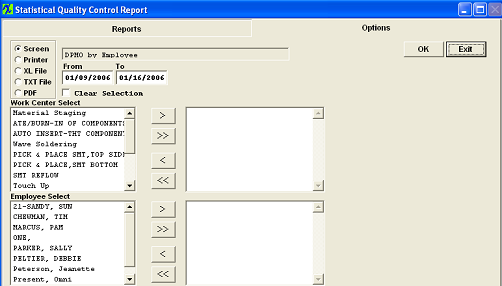 |
For Example: the PPM for each work center is:
Work center PPM
STAG 2
SMT 1
FGI 5
SCRP 3
User ONE inspect two records in Defect code entry module:
1) Insp Qty 10, Work Center: STAG
Defec detail:
Defect Code Chg WC Defect Qty Emp
Defect-1 STAG 2 ONE
Defect-2 SMT 1 JM
Defect-3 STAG 5 ONE
2) Insp Qty 20, Work Center: SMT
Defect Detail:
Defect Code Chg WC Defect Qty Emp
Defect-4 SMT 1 ONE
Defect-3 SMT 4 ONE
Defect-6 WAVE 7 MP
If user selects all work centers (on report option page)
The Defect Qty for ONE will be 2+5+1+4 = 12
Number of Unit*Number of opportunities = 2*10+1*20=40
DPMO for User ONE is 12*1,000,000/40=300,000
As displayed:

The user has option to select for certain work centers, for example, if user only selects for "STAG" work center, then
The Defect Qty for ONE will be 2+5 = 7
Number of Unit*Number of opportunities = 2*10=20
DPMO for User ONE is 7*1,000,000/20 = 350,000
As displayed:

|
|