1. Fields & Definitions for Kitting & Shortage |
1.1. Main Tab | 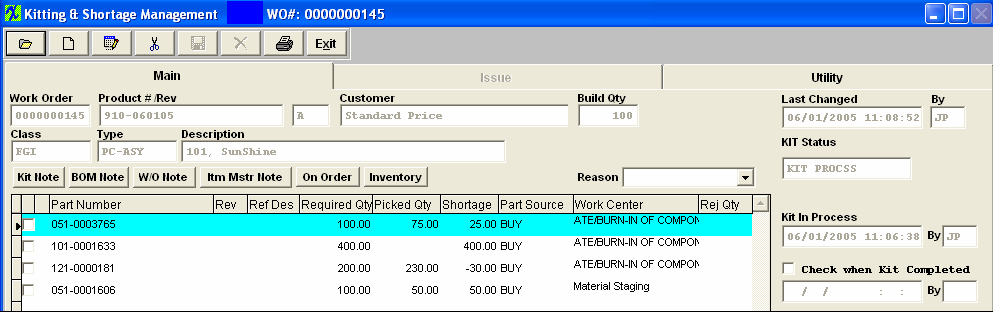
Main Screen Field Definitions
Work Order |
The work order selected for kitting activities |
Product # |
The Part number assigned to the assembly in the work order |
(Rev) |
The Part Number Revision for the assembly |
Customer |
The customer for the work order |
Build Qty |
The quantity of assemblies to be made for the work order |
Class |
The classification of the assembly |
Type |
The type of assembly |
Description |
Consists of the Inventory Control Item Master Description |
Last Changed |
Date and Time of Last Change to this Work Order/Kit |
By |
Initials of person who made last change to this Work Order/Kit |
Kit Status |
KITSTATUS ( character field) may be empty, or one of the following: Kit Closed, Kit Process, Rework. If the KIT MANAGEMENT screen has been opened, and any material issued to the kit, the condition of this field will be changed from empty to Kit Process. This field is NOT dependant on the KIT field, but by the logic described in Article #2679 , and cannot be changed unless the kit is released.
|
Reason |
When user pulls kit, edit, update..... all these details are saved in a table called "Kadetail". All these records will have a "short reason" which is hard-coded in the program. Here are some examples:
Procedures Reasons
Edit kit(edit qty or delete): KIT MODULE/REV
New Kit Pull KIT MODULE/Issu
Auto Kit KIT MODULE
Kit Update KIT UPDATE or KIT MODULE/Upd(if user has overissue)
Delete part DEL
Add misc shortage ADD
Edit misc shortage EDT
If it's a line shortage, then user can select the reasons that's set up in System Setup . So, when user highlights an item, the user will be able to view all different reasons for this item.
|
Kit in Process |
Date and Time status of Kit was changed to "Kit in Process" |
By |
Initials of person who changed kit status to "Kit in Process" |
Check when Kit Completed |
Date and Time when Kit Complete box was checked |
By |
Initials of person who checked the Kit Complete box |
Component Section - NOTE: Items will appear on screen only if the "Used in Kit" on the BOM is "Y". For further detail see Article #34.
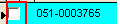 |
This is the “Ignore Shortage” box: If you want to remove the component from the shortage reports and MRP, check the box at the left of the part number. Note: the box for checking KITTED shortages only works with those items that are kitted based on the BOM for the assembly. Checking the boxes means that the part on the BOM will NOT be considered for MRP purposes, and not show up on shortage lists. This is the only way you can get a part on the BOM off of the shortage list. Line shortages, however, can be edited to make them larger or completed. The user will not be able to create a line shortage, then try to check the “ignore shortage” box, this box is disabled for added line shortages. |
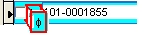 |
This symbol before a part number is to inform the user that this part is originating from a Phantom BOM.
|
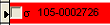 |
When shortages have been saved for the work order, they will be added to the Kit Status section of the main information tab. The item will be preceded with the rho (? ) symbol to differentiate it from a kit shortage. |
Part Number |
The part number of a component belonging to the Bill of Materials for the assembly |
Rev |
The part number revision of the component |
Ref Designator |
The Reference Designator as assigned in the BOM Module |
Required Qty |
The number of parts required of the component in the work center shown. (A component may be used in more than one work center.) This qty may include Setup Scrap if the "Setup Stcrp" box is check on the BOM Header Information and/or Run Scrap if selected to include scrap in the Kit Default Setup . |
Picked Qty |
The number of parts already picked from stores for the work order |
Shortage |
The quantity of parts short for the work order will be displayed as a positive number, the quantity of parts issued as an overage will be displayed with a negative number. |
Part Source |
The source code for the part, BUY, MAKE, Phantom or Consigned |
Work Center |
The work center in which the part is needed and to which it is to be kitted |
Rej Qty |
If parts have been rejected during the kitting process, the quantity of parts rejected |
DIRECTIVE BUTTONS
The following buttons are displayed on the Kitting Main screen
 |
Kit Note will bring up any notes entered concerning the kitting or shortages |
 |
BOM Note will show any notations entered at the Bill of Material level |
 |
W/O Note will display any notes entered about the work order |
 |
Item Mstr Note will display any notes entered in the Inventory Control Item Master about the part highlighted |
 |
On Order button will display information about any open orders that may exist for the part highlighted, as shown below |
The user may sort by Date, Supplier, PO Number or Manufacturer by depressing any of those buttons. |
 |
 |
The Inventory button will display on hand and location information for the part highlighted, as shown below |
|
1.1.1. Kit Status Logic | Status of Kit: Released is a term that means the work order has moved from the initial input condition, where it is possible to check on details of the work order and to utilize a check list to indicate certain functions (established in the setup) have been completed (e.g., necessary documents have been received, shortages have been resolved, tooling is available, etc.). An unreleased work order cannot be kitted, nor moved on the shop floor.
KIT (a logic field) means that the work order has been released for production to work on it. This includes kitting and SFT. It means that in the WO screen, the user has clicked on the “Work Order Released” checkbox. Or, this box is automatically checked when all of the items on a work order check list have been completed. It does not mean that the work order or the kit have been started. Until this box is checked, no kitting nor SFT activities can begin.
OPENCLOS ( character field) is the status, or condition of the work order. This condition is required to initiate a work order. These conditions must be one of the following: Archived, Cancel, Closed, Firm Plann, Rework, ReworkFirm, Standard. Every work order must have one of these conditions.
|
1.2. Issue Tab | 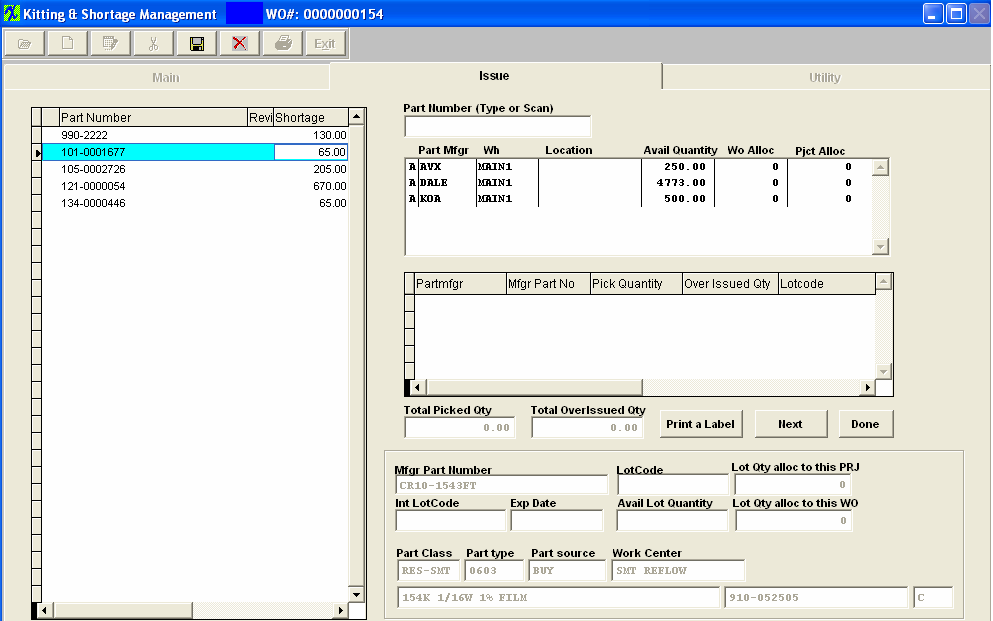
Issue Screen Fields
KIT STATUS SECTION
Part Number |
The part number of a component belonging to the Bill of Materials for theAssembly.
|
Rev |
The part number revision of the component |
Shortage |
The quantity of parts short for the work order.
|
INVENTORY STATUS SECTION
Part Mfg |
The name of the manufacturer for the highlighted part |
Warehouse |
The name of the warehouse |
Location |
The location within the warehouse listed, such as Row 2, Bin 34 |
Available Qty |
The quantity available for this part for this work order |
WO Alloc |
The quantity allocated to other Work Orders. |
Pjct Alloc |
The quantity allocated to other projects.
|
PICKED STATUS SECTION
|
An "A" will be displayed in this column if the Manufacturer is approved |
Part Mfgr |
The name of the manufacturer for the highlighted part. |
Mfgr Part Number |
The manufacturer number for the part highlighted |
Pick Qty |
The qty required for this WO. See Article #1240 for more detail on why the system will not allow user to enter in a fraction of a number, and an alternative. |
Over issued Qty |
The qty over issued to this WO. See Article #1240 for more detail on why the system will not allow user to enter in a fraction of a number, and an alternative. |
Lot Code |
The manufacturers lot code for the part highlighted |
Total Picked Qty |
The quantity of the highlighted part already picked. Below that is the part number of the completed assembly.
|
Total Overissued Qty |
Any quantity issued over what the Bill of Materials depict. Below that is the revision number of the completed assembly. |
 |
When depressing this button a bar code label will be printed |
 |
The "Next" button should be used with the top "part number (type or scan)" field. When user types (or scans) the part number the user wants to issue, the cursor on the left list will move to the right part number record, then user can issue it. After the user is done, click the "Next" button, the system will save the issued record, and the cursor will move to top "part number" field again for user to enter whatever part number the user wants to issue next. It doesn't mean the "next one" record in sequence.
|
 |
When the user is finished pulling the parts to the kit, they would depress this button and it will bring them back to the Main screen |
LOT CODE INFORMATION
Mfgr Part Number |
The manufacturer number for the part highlighted |
Lot Code |
The manufacturers lot code for the part highlighted |
Lot Qty alloc to this PRJ |
The quantity allocated to this specific project. |
Int. Lot Code |
The users internal lot code for the part highlighted. |
Exp Date |
The assigned date of expiration for the lot. |
Avail Lot Quantity |
The quantity available for that lot which is available to assign to the work order. |
Lot Qty alloc to this WO |
The quantity allocated to this specific work order. |
ADDITIONAL PART INFORMATION
Part Class |
The classification of the highlighted part. Below that is the part description |
Part Type |
The type of part |
Part Source |
The source for the part: Buy, Phantom, etc. |
Work Center |
The work center where the part will be needed for the assembly |
|
1.3. Utility Tab | The Utility Tab has four functions:
1. Close Kit - This section is used to close the kit from further transactions. Once closed, no further parts may be issued to or from the work order.
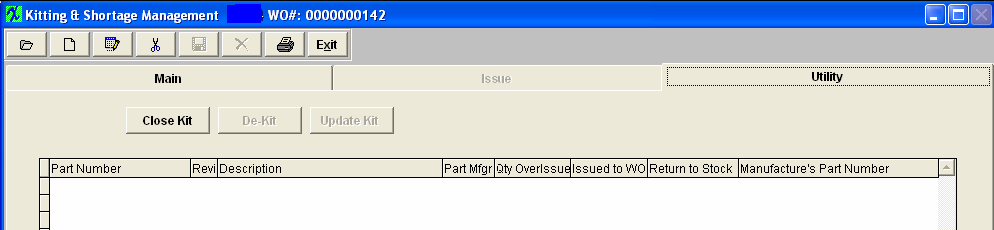
Once the Close Kit button has been depress the following screen will appear, this screen will list all over-issues for disposition, it defaults all items to have the over-issue qty returned to stock. If the users wants to return all to stock they just have to click the OK button. If they want to assign all the over-issue to the Work Order (kit) they can do so by depressing the "Issue All to Kit" button.
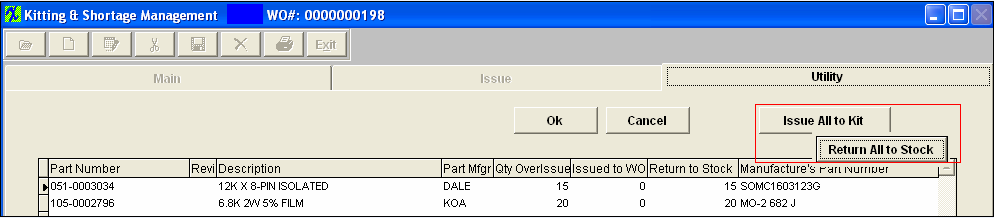
The act of closing the kit sets up the material variance entry for the Accounting module if more parts or less parts than called for by the Bill of Materials were actually used. Note: Only an accounting password can close the kit.
The manufacturing variance is based on what should have been kitted according to the BOM for the work order. Under issues, overissues and alternate parts are considered as variances.
If a part is allocated to a Work Order or a Project (linked to the work order), when the KIT over-issues to WO-WIP location. Once the WO is closed, and user chooses to return stock, the WO allocation will be cleared, but the Project allocations will be retained and carry back to stock as still allocated to that project.
What are the actions that would cause a work order to appear on the “Kits to Close” report?
The action that causes a work order to appear on the Kits to Close report is when the Work order is closed. (In the Shop floor tracking module, the units are transferred to the Finished Goods work center). There is no longer a balance due on the order but the work order has not yet had the kit closed. There are two aspects of closing a work order activity – 1, closing the work order; and 2, closing the kit. The work order closes when all of the scheduled parts are either in finished goods or scrap. This happens automatically when the last transfer is made in the shop floor tracking module. The kit closing is a manual function. It is separate, because even though the work order may be closed, somebody may not have completed kitting all the parts to the work order, nor moved all of the over-issue out of the work order. These actions are prompted for when the kit is closed. The user may close the kit without addressing the open issues, but if that happens, each will become a variance within accounting. Unfilled shortages will become a positive variance and overissued parts will become a negative variance.
(Important Note: For those instances where the user didn’t issue the parts to the work order initially, but completed the work order in shop floor tracking and then closed the kit, there will be a very large positive variance created because the system will assume that the cost of the components = zero.) Therefore, do not close a kit if it was never pulled.
2. Re-open kit - If the user wishes, he/she may re-open the kit once it has been closed. Note: Only an accounting password can re-open the kit.
3. De-Kit - The act of de-kitting will return all of the previously picked parts to inventory. If a part is allocated to a Work Order or a Project (linked to the work order), once the part is issued to the WO (not over-issue) the allocation will be removed, only the allocation for over-issue parts can be kept. Once the WO is closed, and user chooses to return stock, the WO allocation will be cleared, but the Project allocations will be retained and carry back to stock as still allocated to that project. The appropriate accounting entry will also be generated to return all parts to Raw materials inventory from Work in Process. The system will not allow you to de-kit with product in finished goods.
4. Update Kit - The Update Kit button will update the work order with any BOM changes.
Depress the Update Kit button. Type in your password.
You will receive a confirmation message.
|
|
If the changes to the BOM reflect inventory parts that require dispositioning the following screen will appear:
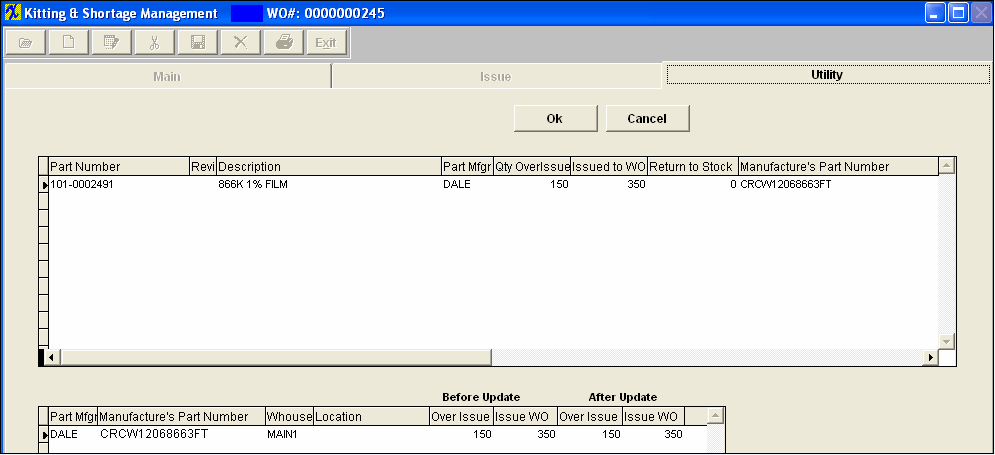
Highlight the item. The system will default in the issued qty into the Issue WO field. If you wish to issue the parts directly to the cost of the Work Order then you can leave the qty in Issue WO. Depressing the OK button will then issue and cost those parts to the kit.
If you wish to return those part back to inventory you will change the Issue WO qty to 0 and then you will see the Return to Stock qty adjust. That amount in the Return to Stock will be the amount that will be returned back to stock as available inventory.
If there is an Over Issue Quantity found during the update kit, user will receive a message to remind the user that there was an Over-issue qty found, and to make any needed changes to those quantities to "Return to Stock". (If you wish to return those part back to inventory you will change the Over Issue qty to 0 (bottom screen) and then you will see the Return to Stock qty adjust (top screen)). That amount in the Return to Stock will be the amount that will be returned back to stock as available inventory.
If not the over-issued qty will remain as an overissue - and upon completion of the update kit the parts will be issued to the WO (costed to the kit) and accounted for as a Mfgr Variance upon closing.
If a part is allocated to a Work Order or a Project (linked to the work order), when the KIT over-issues to WO-WIP location. Once the WO is closed, and user chooses to return stock, the WO allocation will be cleared, but the Project allocations will be retained and carry back to stock as still allocated to that project.
Depress the OK button and you will receive a confirmation message.
For any new parts added to the BOM, they will appear as shortages. You need to make sure to pull them to the kit.
If any of the quantities per within the BOM were increased, you’ll have to also pull additional amounts, which will now show as shortages to the Work Order:
In the example below, part number 105-0002726 was just added to the BOM and must now be pulled. Additionally, part number 101-0001633 had the quantity per on the BOM increased and now the shortage must be pulled.
|
|