To Un-allocate an allocation, thus freeing up the amount allocated to a Work Order or Project, first go to the Allocation Maintenance screen.
Depress the Edit Record button.
The following find record options will be displayed
|
|
If you had selected to find per Work Order or Project the following screen will appear which lists all open WO numbers or project numbers with allocations.
Type the WO or project number in the red box or double click on the number and the screen below will appear with the allocation information listed.
|
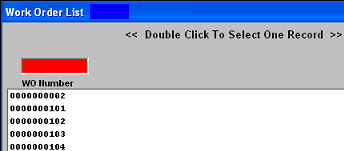 |
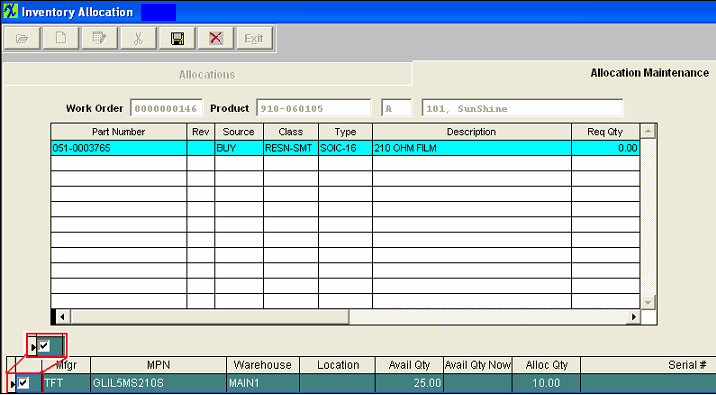
Depress the Delete button.
Enter your password and the following prompt will appear which is defaulted to "No"
“No” will allow you to select which ones to un-allocate individually
Yes” will un-allocate all items on screen automatically
|
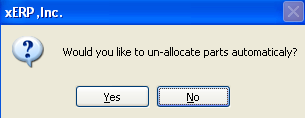 |
Highlight the desired part number and then Check mark which items you wish to un-allocate.
Depress the Save record action button and any marked item should now be unallocated and be considered available inventory.
If you had selected to find by Part Number the following screen will appear which lists all Part Numbers with allocations.
Type the Part number in the red box or double click on the number and the screen below will appear with the allocation information listed.
|
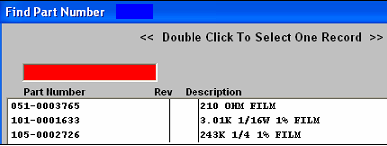 |
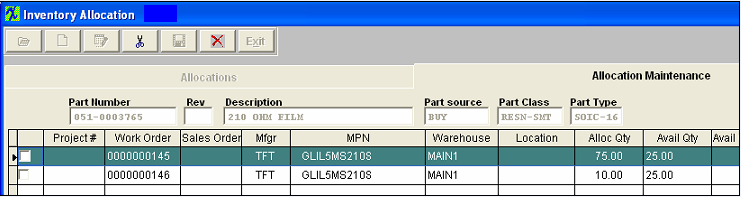
Depress the Delete button.
Enter your password and the following prompt will appear
YES” will un-allocate all items on screen automatically
“No” will allow you to select which ones to un-allocate individually
|
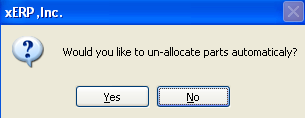 |
Highlight the desired part number and then Check mark which items you wish to un-allocate.
Depress the Save record action button and any marked item should now be unallocated and be considered available inventory.
The Inventory Control Item Master will update automatically. Note: For reports on Allocated Inventory, please refer to the ICM reports
|