1.1. Prerequisties for WO Mgmt | Prerequisites for Entering a New Work Order
After activation, "Work Order Management" access for each user must be setup in the ManEx System Security module. Users with “Supervisor Rights” will automatically have access.
Customer |
A Customer database must be established in the Customer Information module.
|
Contact (Buyer) (Optional) |
If the user wishes to include the buyer on the order |
Product number |
The part number must exist for a product or part in the Inventory Control Mgmt module. |
BOM (Optional) |
The Bill of Material must be entered (AVL optional)
|
|
1.2. Introduction for WO Mgmt | The Work Order Module is used to record the details required for initiating assembly of products.
The whole purpose of the WO Release is for various departments to fulfill their part of the task of releasing the WO on-line to avoid doing it manually. This is a very valuable feature and should not be by passed. This is why we do not allow the Work Order to be released within the Sales Order module.
The user initiates the internal flow of work actions by completing the Work Order. This order includes Kitting the material for the order, issuing the material to the production line, tracking the assembly of the order, and completing and evaluation of production performance.
A Sales Order number will be displayed if the Work Order was created within the Sales Order Mgmt module. If you are entering a Work Order through the Work Order module, you can manually link an existing Sales Order to the Work Order. Only if the Sales Order and Work Order is for the same customer and same product number. Keep in mind though that even if you have the SO linked to a WO does not mean that the quantities will always be the same. The link is for reference only between the two modules and they are still individual records so when any changes are made to either the SO or the WO the change will not update or be carried forward to the other. A message is displayed to the users that they will have to make the same changes to the WO.
NOTE: ManEx does not allow a Work Order to be created for a Make/Buy Product, (due to MRP calculating incorrect demand and showing incorrect message with safety stock).
|
1.3. Fields & Definitions for WO Mgmt |
1.3.1. Work Order Tab |
Work Order Tab field definitions
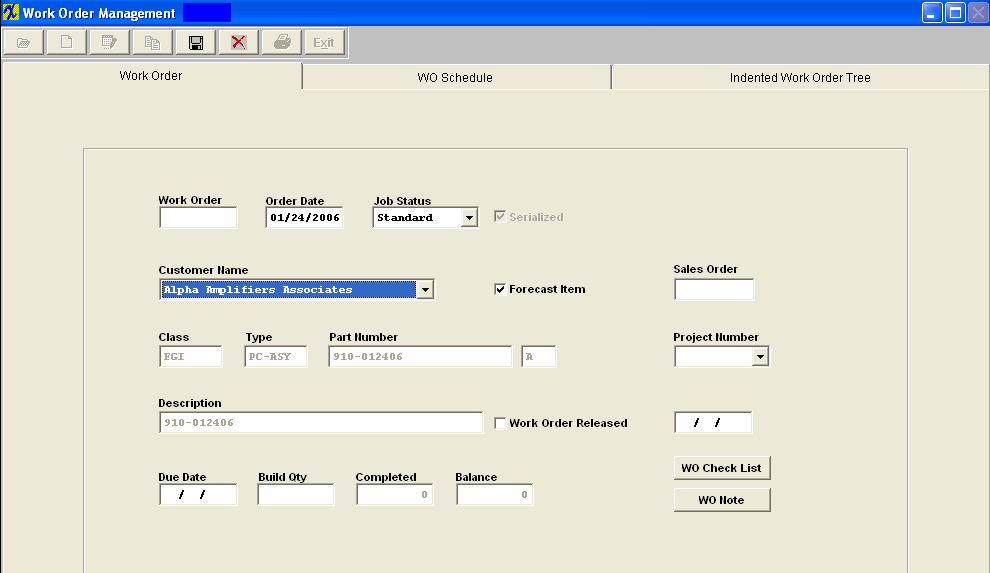
Work Order |
The number assigned to the Work Order.
|
Order Date |
The date the Work Order was created.
|
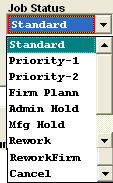 |
The status of the Work Order: Standard; Priority-1; Priority-2; Firm Plann; Admin Hold; Mfg Hold; Rework; ReworkFirm; or Cancel.
The system defaults to Standard. Standard is the ordinary work order status. Priority is set up as a make ahead of all other orders, 1 being the most important and 2, the second most important. Firm Plann, lets MRP know that the Work Order decision is intentional and NO action is required. Admin Hold is an order on hold due to customer credit, etc (this will NOT interfere with the kitting, production or shipping). Mfg Hold WILL prevent the order from being put In-Process, Kitted, or Assembled. Note: If the WO is put on Mfgr Hold before being put In-Process no demands will be displayed in MRP. Rework is to fix or redo a previous order. Rework Firm or Cancel.
Firm Plann = Example: The requirement may be 100 but the Firm Plann WO is only for 60. Normally in this case if the WO status was standard MRP would instruct user to increase the WO qty from 60 to 100 to fulfill the requirement of 100. But since the WO is Firm Plann, MRP will take no action. See defintion for DUE DATES below for further detail.
If user changes the Work Order Status to Admin Hold or Mfgr Hold, a box will appear on the Work Order Screen (as shown below) giving the user the option to put the Work Order on MRP Hold. If the user does NOT check this box, orders that are In-Process will not be affected in MRP. Manufacturing hold on a Work Order will disallow movement of the parts through SFT.
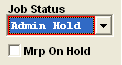
Rework = users will use this status if they do not want to have it included as available to meet demands.
ReworkFirm = users will use this if they want to have it included as available to meet demands. The only thing is that they will have to be sure the due dates for a rework firm precede any demand that was created to use those parts.
NOTE: Work Orders originated from an RMA Receiver will have "ReworkFirm" Job Status and users will NOT be allowed to change the Job Status. Since the material issued to the RMA is likely to be a defective assembly, or requires re-inspection, the work order must be completed by either transferring the material to FGI or to scrap to close the work order. Therefore, an RMA work order cannot be cancelled. Also, users will NOT be allowed to edit or change the Bld qty because when product is brought into the system with an RMA Receiver it is then automatically issued as itself to the kit at that time.
|
Serialized |
If this box is checked, the completed units must be assigned unique serial numbers. |
Customer Name |
The name of the customer for which this Work Order applies.
If BOM is assigned to specific customer, and if there is CONSG part in the BOM -- Only that customer will be available in the WO customer list
If BOM is assigned to specific customer, and no CONSG parts in the BOM -- Default to that customer, but all other customers are available to be selected.
If BOM is not assigned to specific customer, all customer should be available.
|
Forecast Item |
The Forecast checkbox is defaulted as True whether or not there actually is a forecast. By doing this, we minimize the possibility of the MRP double ordering parts for the SO. If there is a forecast, then the SO will be subtracted from it. If there isn’t a forecast, the SO will drive as usual. Users can change to un-checked in the Sales order/Work order if desired. |
Sales Order |
A Sales Order number will be displayed if the Work Order was created within the Sales Order Mgmt module. If you are entering a Work Order through the Work Order module, you can manually link an existing Sales Order to the Work Order. Only if the Sales Order and Work Order is for the same customer and same product number. Keep in mind though that even if you have the SO linked to a WO does not mean that the quantities will always be the same. The link is for reference only between the two modules and they are still individual records so when any changes are made to either the SO or the WO the change will not update or be carried forward to the other. A message is displayed to the users that they will have to make the same changes to the WO.
|
Class |
The classification of the product to be assembled. |
Type |
The type with the classification of the product to be assembled.
|
Part Number |
The number of the make part to be assembled
|
(Rev) |
The revision number pertaining to the part number.
|
Description |
The description of the part to be assembled.
|
Work Order Released |
If this box is unchecked, you are able to kit the work order but you will not be allowed to process the material through SFT. Once this box has been checked, you will be able to move the material through SFT. If user is using the WO checklist feature this box will not be checked until all checkpoints including the "Kit Complete" have been marked off. Once the "Kit Complete" checkpoint has been checked the WO Released checkbox will be checked automatically.
|
(Date) |
The date the Work Order was released.
|
Due Date |
This is the date by which the completed assembly must be completed. Note: The Sales Order Ship Date must be the same or later than the Work Order completion date. MRP will look at the SO Ship Date which should be the same or precede the WO Due Date by the transit time from your dock to the Customer’s dock. The SO Ship Date becomes the Work Order due date when the Work Order is created from the Sales Order, but user may change this date. MRP will recognize the WO as being due in time for the SO ship date, and therefore include the work order as supply to meet the sales order demand, whether or not it’s kitted. If the Work order is kitted and then the dates are moved (either in the sales order ship date to a later date or the work order due date to an earlier date), then MRP will not view the work order (supply) as meeting the sales order (demand). If the work order has been kitted, and thus changed status to a firm planned work order (as far as the MRP module is concerned), then MRP will NOT suggest adjusting the work order delivery date to meet the demand, but WILL suggest creating a new work order (or moving a non-firm planned work order) and ordering the parts for the new work order date. So the keys are the work order due date, and the sales order ship date. The former must be the same or precede the latter, to keep the work order identified as supplying the product for the sales order. User does have the ability to turn off the function of the Sales order driving the demands for the MRP and just use the Work Order for buying components by checking the MRP on Hold box in the Sales Order module per line item.
Note: The Kitted BOM Cost calculations displayed on the "Kit to Close Report" is based off the WO Due date and compares that to the EFF/OB dates on the BOM. So users need to be VERY careful with the WO Due Dates and make sure that they stay current along with the EFF/OB dates on the BOM.
|
Build Qty |
The number of units which must be completed.
|
Completed |
The number of units already completed.
|
Balance |
The number of units which still must be completed.
|
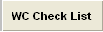 |
Depressing this button will display the applicable Work Order Check List (shown below).
|
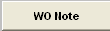 |
Depressing this button will display the applicable Work Order Notes |
WO Check List Screen field definitions:
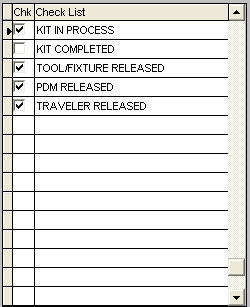
Chk |
A check mark in this box means that the check list item has been completed.
|
Check List |
The description of the check list item.
|
Init |
The initials of the person who performed the check.
|
Date |
The date of the check list performance.
|
Time |
The time of the check list performance.
|
|
1.3.1.1. Changing Work Order Status, how it affects Kit Status and MRP? | Once a Kit has been flagged as "In Process" the Work Order management module will not allow the users to change the WO status between Standard and Rework.
WO form Modifications:
When a user is trying to change the status for the work order from the "REWORK" to any other status we check the KIT data and if the KIT has only line shortages present the KIT status will become empty (instead of "KIT PROCSS"). The reason is that MRP is checking for the KIT status in order to determine whether it needs to explode the BOM to get the demands for this work order or BOM is already exploded. When changing status from anything to "REWORK" check CURVAL () because if someone else pulled the kit for that work order while the user was editing the status the kit status might already be updated to the "KIT PROCSS".
KIT form Modifications:
In the save method when line shortages are added and rework work order is selected replace start date and initials only when they are empty. When re-opening the KIT, check if work order status is rework kit status has to be "REWORK" as well. When saving, after issuing items from the inventory, do not update Kit Status if WO status is not "REWORK". For the regular WO if BOM is already exploded and shortages are created the kit status would be already updated, but if BOM was not exploded and only line shortage are present we do not want to change the kit status because MRP will only use line shortages and miss all the demands from the BOM.
|
1.3.2. Work Order Schedule Tab | 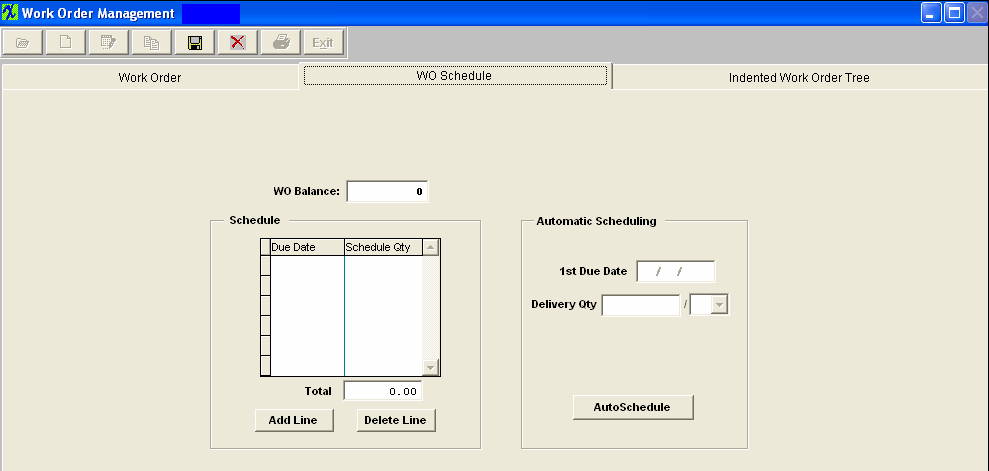
Work Order Schedule Field definitions
WO Balance |
The quantity of product that is not in finished goods
|
Schedule
Due Date |
The date by which the completed assembly must be ready for shipment |
Schedule Quantity |
The amount of quantity scheduled for that due date |
Total |
The total of all of the scheduled quantities |
 |
Depressing this button will allow the user to add a line |
 |
Depressing this button will allow the user to Delete a line |
Automatic Scheduling
First Due date |
The date of the first shipment |
Delivery Quantity |
Quantity per each shipment
|
/Day/Wk/Mo |
The increments per each schedule, either Day, Week or Month
|
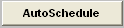 |
This allows the user to have MANEX schedule each shipment |
Note: Keep in mind that this is for your reference only - this screen does not affect any other portion of the ManEx system.
|
1.3.3. Indented Work Order Tree | 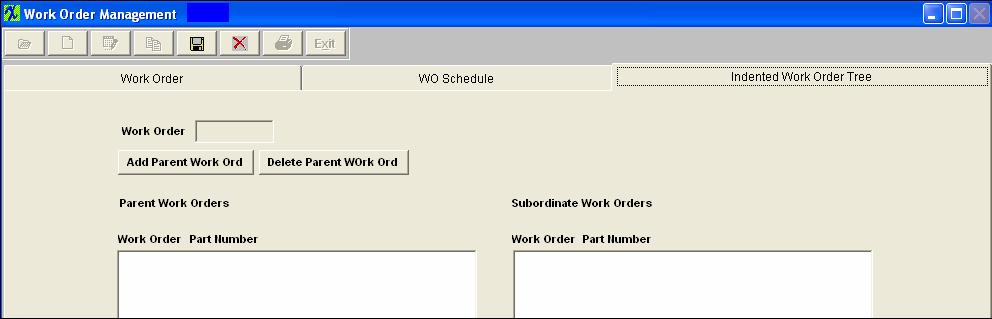
Indented Work Order Tree field definitions
Work Order |
The number assigned to the Work order.
|
 |
Depressing this button allows the user to associate this work order with its parent work order.
|
 |
Depressing this button allows the user to delete the parent work order association.
|
Parent Work Orders
Work Order |
The Work Order number of the parent work order.
|
Part Number |
The number of the part to which the parent work order pertains. (Subordinate)
|
Work Orders
Work Order |
The Work Order number of the subordinate work order.
|
Part Number |
The number of the part to which the subordinate work order pertains.
|
|
1.4. How To ..... for WO Mgmt |
1.4.1. Find a Work Order |
Enter Production/Work Order Managment/Work Order Mangement Module |
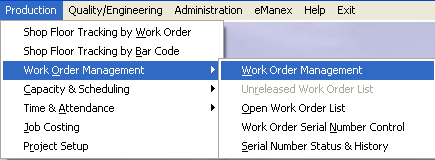 |
The following screen will apear:
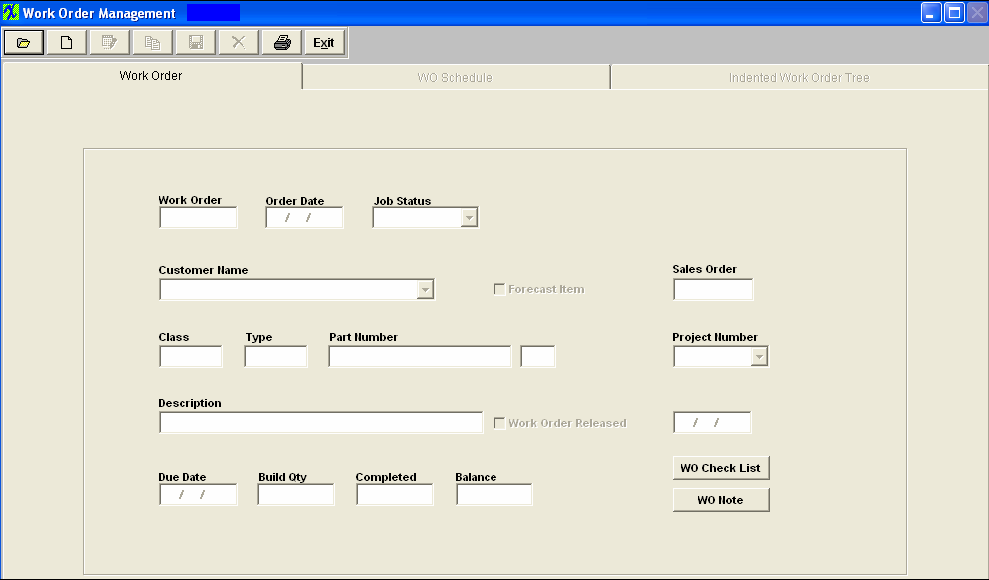
When the screen first opens, the user is limited to only four of the eight action buttons shown: Find an existing Work Order, Add a new Work Order, Print a report, or Exit.
Pressing the Find Action Button displays the following sequences:
User may choose to find or search for an existing order: by entering the Work Order Number, by entering a Product Number, by entering a Customer Name, or by entering a Sales Order Number. |
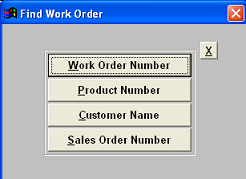 |
If the user elects to find an order by the Work Order Number, a screen appears listing work orders in numerical order, along with the Part Number and Customer name. User has the option to view Open orders only or All orders. The user selects the work order by either entering it into the red box, or scrolling down the list and clicking on the selected order.
The Work Order screen is populated with the appropriate data. |
|
When the user elects to find an order by the Product Number, a screen appears listing part numbers in numerical order. The user selects the part number by either entering it into the red box, or scrolling down the list and clicking on the selected part. |
|
A list of all of the Work Orders assigned to the selected part is shown in numerical order, along with the customer name, Due Date and Build Qty. The user finds a work order by either entering it into the red box, or scrolling down the list and clicking on the selected work order.
The Work Order screen is populated with the appropriate data. |
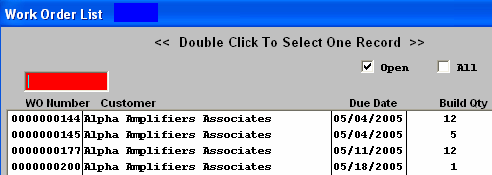 |
If the user elects to find an order by the Customer, a screen appears listing customers in alphabetical order. The user selects the customer by either entering it into the red box, or scrolling down the list and clicking on the selected order. |
|
A list of all of the selected customer’s orders are shown in numerical order, along with the customer name, Due Date and Build Qty. The user selects the work order by either entering it into the red box, or scrolling down the list and clicking on the selected order.
The Work Order screen is populated with the appropriate data.
|
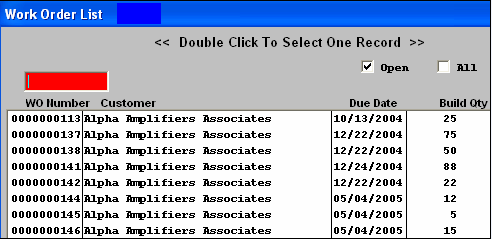 |
When the user elects to find an order by the Sales Order Number, a screen appears listing open Sales Orders in numerical order. The user selects the Sales Order by either entering it into the red box, or scrolling down the list and clicking on the selected order. |
|
A list of all of the Work Orders assigned to the selected sales order is shown in numerical order, along with the part number, revision, class an type. The user finds a work order by either entering it into the red box, or scrolling down the list and clicking on the selected work order.
The Work Order screen is populated with the appropriate data. |
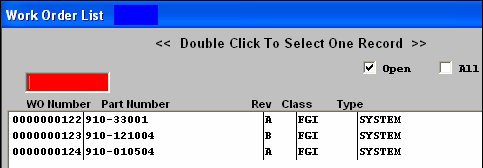 |
|
1.4.2. Add a Work Order |
Enter Production/Work Order Management/Work Order Management Module |
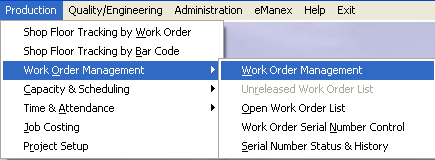 |
The following screen will appear:
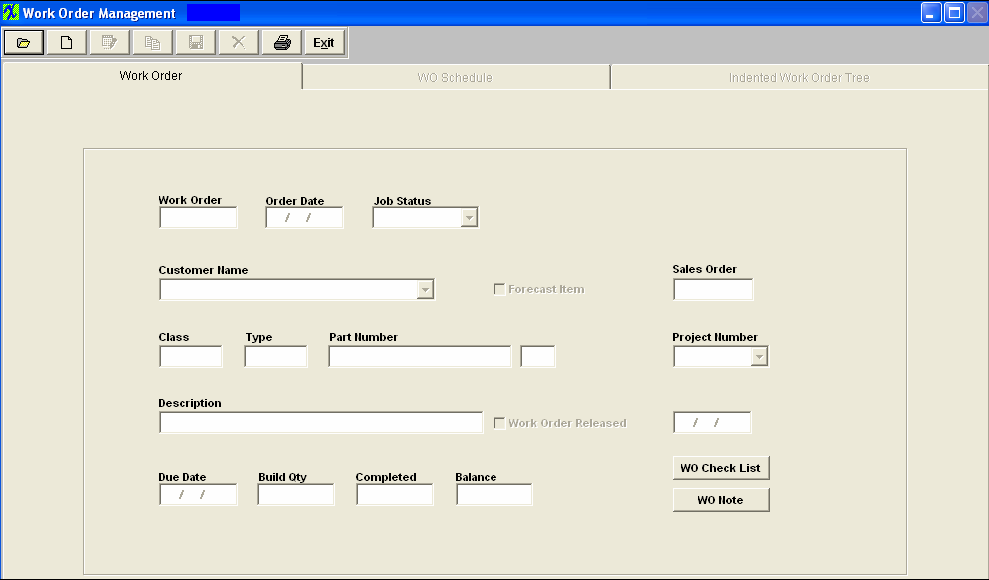
To ADD a new work order, depress the Add Action button. The user is first prompted for the appropriate password:
The following screen appears:
You may find a Product Number directly (see all parts), or limit the field by selecting a Part Class code first.
|
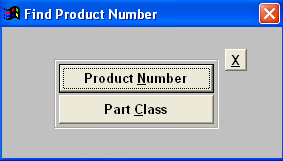 |
If the user selects the by "Product Number” button, a pop-up screen listing all of the part numbers appears. Select the part by typing the part number into the red box or highlighting and double clicking.
|
|
If the user selects the by "Part Class" button the find part class screen appears. Select the Part Class by typing the part class into the red box or highlighting and double clicking.
|
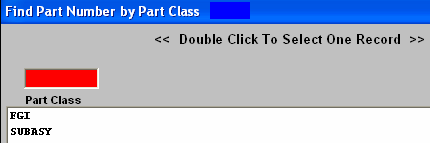 |
After selecting the part class to be entered, the Find Part screen appears, but only includes those parts with the selected class code inventory type. Select the part by typing the part number into the red box or highlighting and double clicking.
|
|
Note: If the Product Number you are looking for does not appear in the Find screens listed above you may want to check the Part Source of the Product number you are looking for. ManEx does not allow a Work Order to be created for a Make/Buy Product, (due to MRP calculating incorrect demand and showing incorrect message with safety stock).
And the screen is populated with information about the part number.
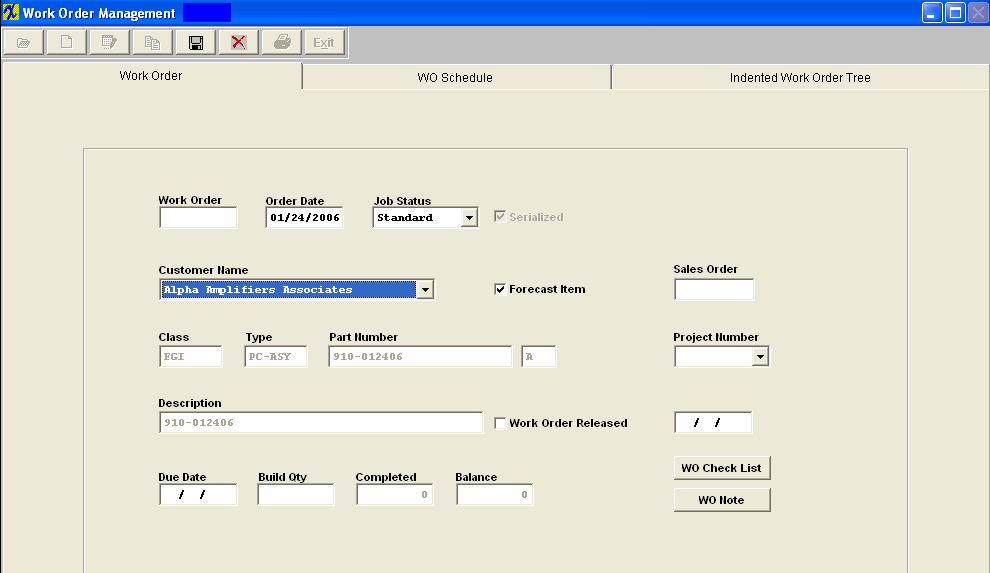
If the work order numbering is set to manual, the first prompt is for the Work Order Number. MANEX will enter the current system date as the Order Date, and the user may revise the date if desired
The next field to enter is the Job Status. Clicking on the down-arrow on the right side of this field activates a pop-up screen providing a list of status from which to select.
The system defaults to Standard. Standard is the ordinary work order status. Priority is set up as a make ahead of all other orders, 1 being the most important and 2, the second most important. Admin Hold is an order on hold due to customer credit, etc. Mfg Hold would prevent the order from being kitted and assembled. Rework is to fix or redo a previous order (See Article #1520), Rework Firm or Cancel.
The user may put orders on Admin or Manufacturing Hold without affecting MRP. Manufacturing hold on a Work Order will disallow movement of the parts through SFT.
Rework = users will use this status if they do not want to have it included as available to meet demands.
ReworkFirm = users will use this if they want to have it included as available to meet demands. The only thing is that they will have to be sure the due dates for a rework firm precede any demand that was created to use those parts.
|
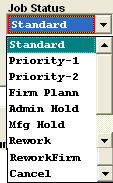 |
Serial Number box. If this box is checked, the units must have a unique serial number assigned. (Note: Serial numbers are assigned in the Work Order Serial Number Control Module).
Sales Order Number. A Sales Order number will be displayed if the Work Order was created within the Sales Order Mgmt module. If you are entering a Work Order through the Work Order module, you can manually link an existing Sales Order to the Work Order. Only if the Sales Order and Work Order is for the same customer and same product number. Keep in mind though that even if you have the SO linked to a WO does not mean that the quantities will always be the same. The link is for reference only between the two modules and they are still individual records so when any changes are made to either the SO or the WO the change will not update or be carried forward to the other. A message is displayed to the users that they will have to make the same changes to the WO.
The next field to enter is the CUSTOMER. When Adding a new Work Order, the user may select a Customer from the pull down or begin entering the customer name, and ManEx will immediately begin tracking the key-entry to bring up the customer with as few keystrokes as necessary to identify the customer. If there is no customer to be associated with the order, the user may select Standard price.
If the Part Number selected is setup in the Sales Price List Information module the customers from the customer list within this module will be the only customer(s) to appear in the pull down.
If BOM is assigned to specific customer, and if there is CONSG part in the BOM -- Only that customer will be available in the WO customer list
If BOM is assigned to specific customer, and no CONSG parts in the BOM -- Default to that customer, but all other customers are available to be selected.
If BOM is not assigned to specific customer, all customer should be available.
|
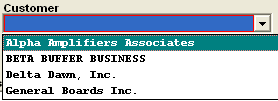 |
If the work order is ready to start being moved through SFT (material obtained and shortages at a minimum), then the user may check the Work Order Released box, which will allow the material to be moved through Shop Floor Tracking. If MRP is used, the demand for the material will be generated, but the work order cannot begin production. To see a list of unreleased work orders, request Back Log Report by Work Center as discussed in the Reports section.
After that, the user enters a Due Date for the order (the date due of finished goods), and the Build Quantity. The shipped quantity will be set to zero, and the balance due to the same as the work order build quantity.
Work Order Schedule Tab
After all the information has been entered in the Work Order screen, depress the WO Schedule tab. The following screen will appear: Note: Keep in mind that this is for your reference only - this screen does not affect any other portion of the ManEx system.
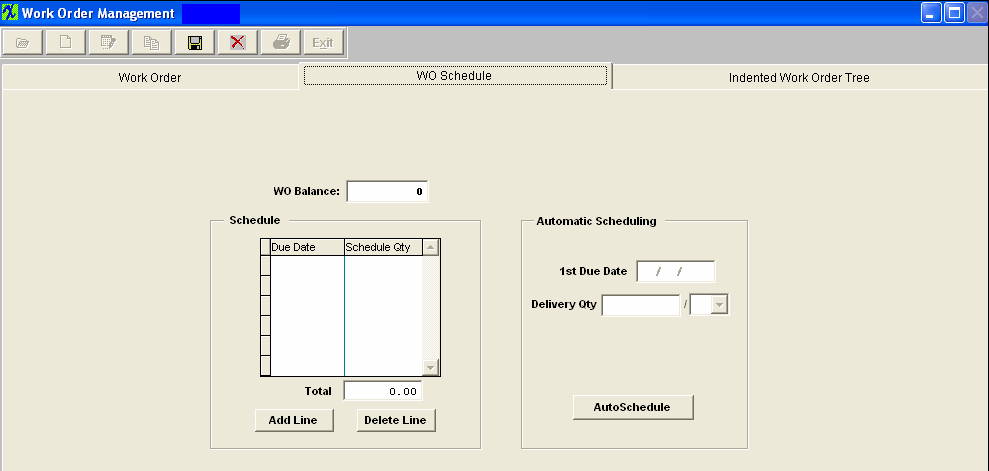
There are two modes available for completing a scheduled delivery for a product: Automatic and Manual. In the Automatic mode, MANEX will take a beginning date and a quantity to be delivered each period (Days, Weeks or Months) and schedule out the delivery.
The following activities are available:
Automatic Scheduling. Pressing this button enables the scheduling box and places the default lead time date in the 1st Due Date box. (The user may establish a default number of days in the System Setup.) The user can then use that date, or enter the first (beginning delivery) date the customer expects to receive the order. The WO Schedule tab allows the user to divide the shipment into multiple deliveries of equal parts. For example, if the order is for a total of 100 pieces, and the customer wishes delivery to be at the rate of 10 units each day, then the delivery quantity should be entered as 10. The next box allows the user to select the delivery intervals. The options are by day (DY), week (WK) or month (MO).
After selecting the delivery interval, pressing the SAVE button creates a line for each delivery date in the sequence requested.
In this WO Schedule tab, the user may further edit, delete or add lines.
Manual Scheduling. Pressing the Add Line button enables the delivery schedule box and places the cursor in the Due Date box. The user can then enter the first (beginning delivery) date the customer expects to receive the order. Next, the Ship Date (the date the order is to leave the user’s dock) will be entered by MANEX based on the transit days entered. This date can then be modified by the user if a different date is desired. Then the scheduled quantity is entered. The Shipped quantity will be completed by MANEX when the line has material shipped against it. Additional lines may be added or deleted by pressing the appropriate button. The total number of units scheduled will be displayed at the bottom of the box, so the user can verify all units have been scheduled.
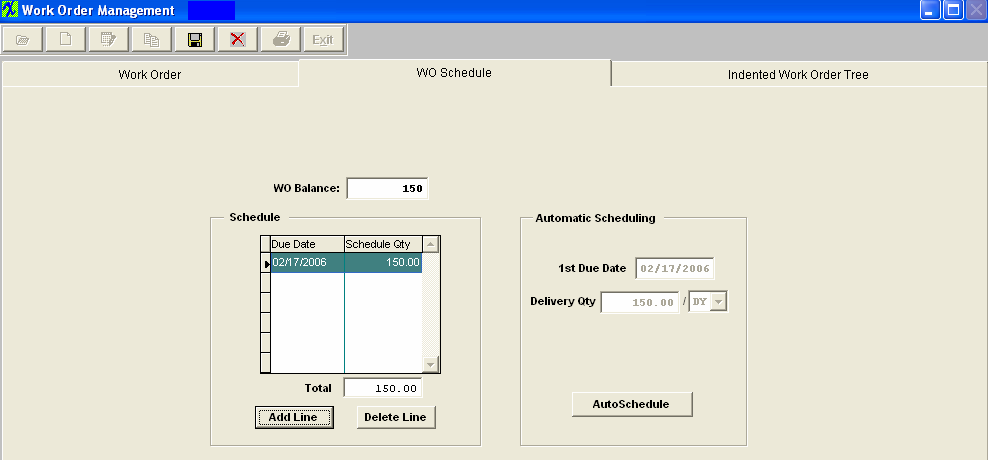
Indented Work Order Tab
If the user has multi-level products, and there are other work orders upon which the current work order depends having material, then the Indented Work Order tab will allow the user to establish relationships between those work orders and the current one.
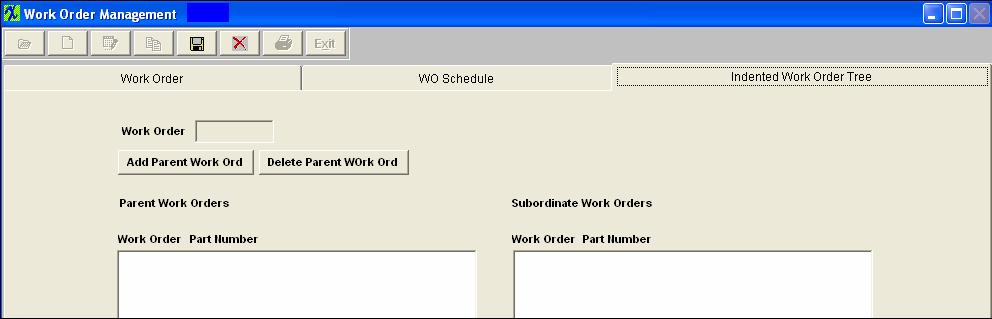
Depress the Add Parent Work Ord button. A red box will appear, as illustrated below:
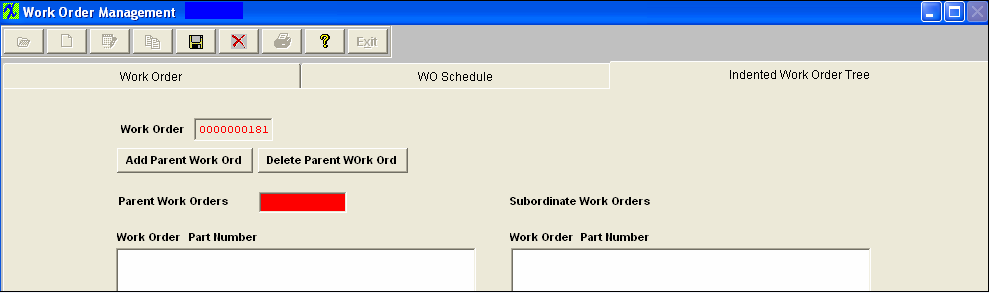
Type the Parent Work Order number into the box.
After entering a valid work order, the user is presented with a screen completed with the work order information, but with a blank work order number (if numbering is manual). After entering the work order, the schedule and quantity, the new work order may be saved.
Once all information is entered, the user may either Save by depressing the Save Record action button, or Abandon Changes by depressing the Abandon Changes Action buttons.
|
1.4.3. Edit a Work Order | Find an existing Work Order
After a Work Order has been found, it may be edited by selecting the Edit Action button.
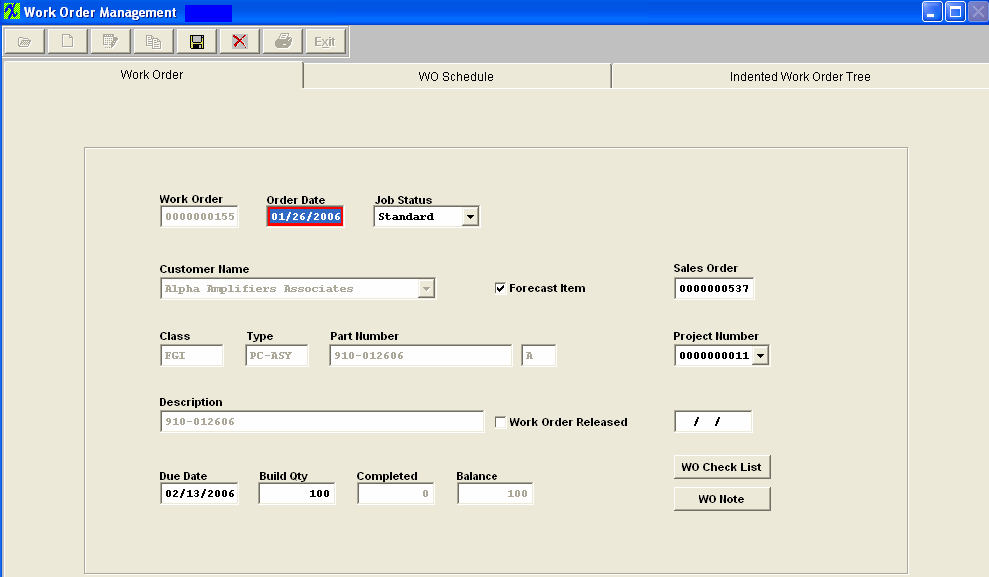
All fields available for editing will be enabled for modification. The fields which may be edited are:
Order Date, Job Status, Work Order Release, Due Date, Build Qty. The user may also add a note, or add or delete a parent work order. Note: Once a Kit has been flagged as "In Process" the Work Order Management module will NOT allow the users to change the Work Order status between Standard and Rework. For further detail see Article #2691 .
If the user wishes to change the Build Qty on a Work Order in process on the Floor the system will provide the users with what work center location they would like to reduce the qty from to match the new Work Order Qty. At this point the Kitting module will still show the original WO qty and what was picked. But if they depress the Update Kit button it will refresh the kit based off of the new WO Qty and now the qty that was adjusted will become WO-WIP. Which means it is available to fulfill any other demand that might be out there. Then upon Closing the kit the user has the option to cost that wo-wip to the kit or return it to stock. If they return it to stock it will have no affect on their Mfgr Variance for that work order.
NOTE: Work Orders originated from an RMA Receiver will have "ReworkFirm" Job Status and users will NOT be allowed to change the Job Status, due to the fact that when the Work Order is created from RMA module all kitting, serial number, .... records are created and if user changes the WO status the system may loose track of these records. User will receive the following message if they try to change the job status on a Work Order that was originated from an RMA Receiver.
Since the material issued to the RMA is likely to be a defective assembly, or requires re-inspection, the work order must be completed by either transferring the material to FGI or to scrap to close the work order. Therefore, an RMA work order cannot be cancelled.
Also, users will NOT be allowed to edit or change the Bld qty because when product is brought into the system with an RMA Receiver it is then automatically issued as itself to the kit at that time.
At the conclusion of the modification process, the user may either Save the changes by depressing the Save changes action button or Abandon the changes by depressing the Abandon changes action buttons.
The following message will be displayed to the user if a SO is linked to a WO:

NOTE: The link is for reference only between the two modules and they are still individual records so when any changes are made to either the SO or the WO the change will not update or be carried forward to the other.
|
1.4.4. Cancel A Work Order | Find the Work Order you want to cancel.
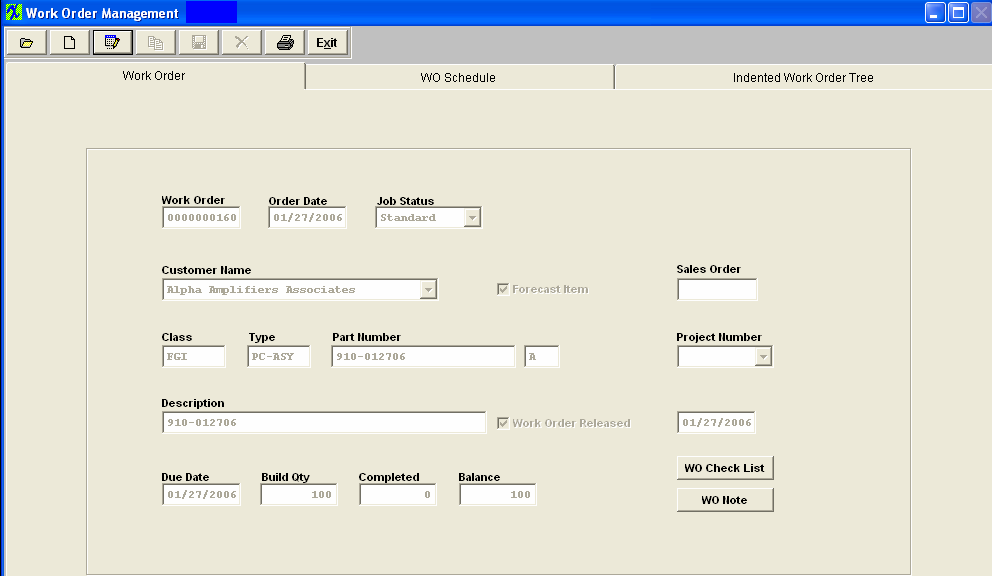
Depress the Edit button and enter your password.
Depress the arrow next to the Job Status and change the Job Status to Cancel as displayed below.
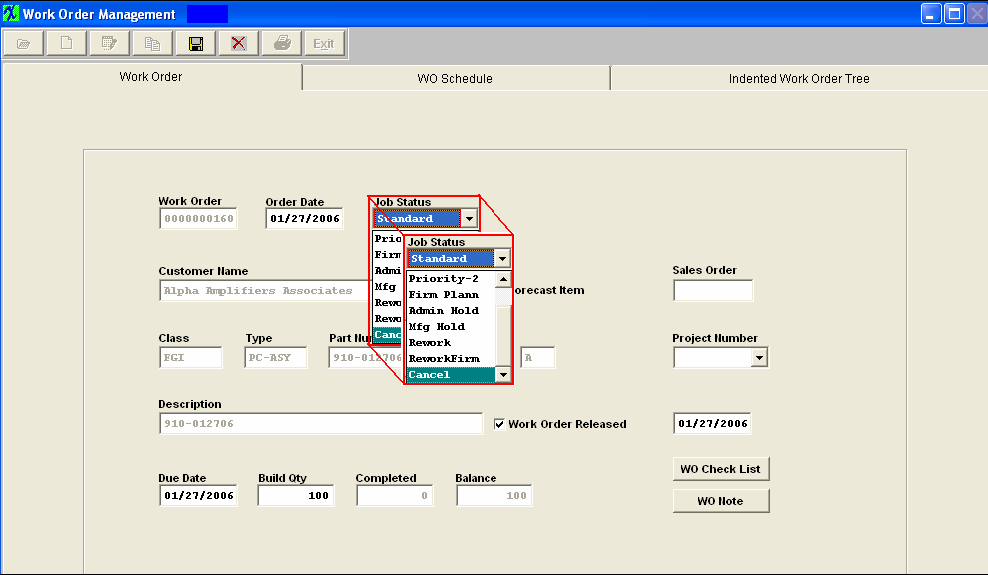
Depress the Save action button.
Note: You can’t Cancel a Work Order that has been kitted. If you must cancel a kitted Work Order, go into the Kitting & Shortage Mgmt module and de-kit the order.
NOTE: Work Orders originated from an RMA Receiver will have "ReworkFirm" Job Status and users will NOT be allowed to change the Job Status, due to the fact that when the Work Order is created from RMA module all kitting, serial number, .... records are created and if user changes the WO status the system may loose track of these records. User will receive the following message if they try to change the job status on a Work Order that was originated from an RMA Receiver.
Since the material issued to the RMA is likely to be a defective assembly, or requires re-inspection, the work order must be completed by either transferring the material to FGI or to scrap to close the work order. Therefore, an RMA work order cannot be cancelled or re-opened.
|
1.4.5. Manually Re-Open or Close a Work Order | Find a Closed Work Order
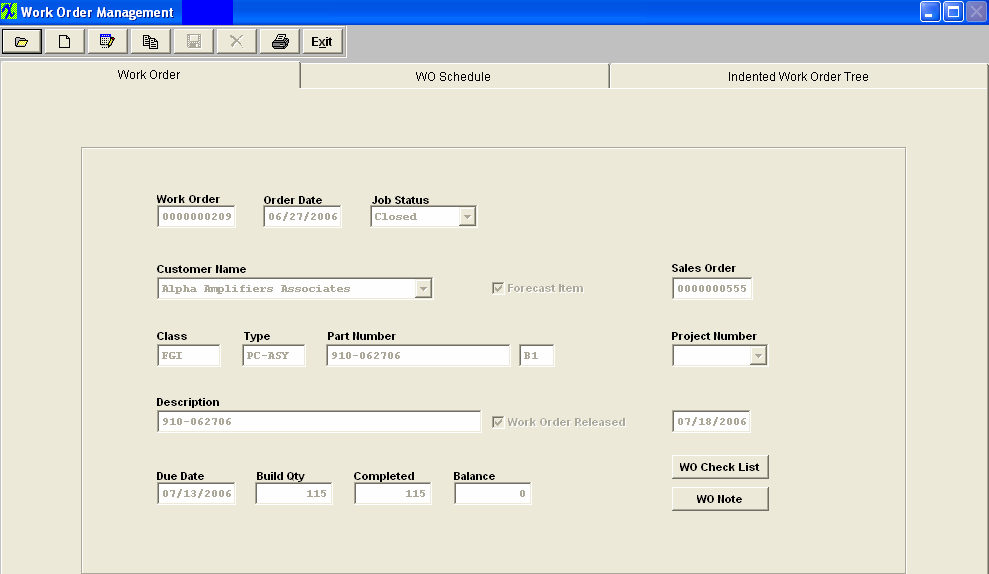
Depress the Edit action button and change the Job Status from Closed to Standard
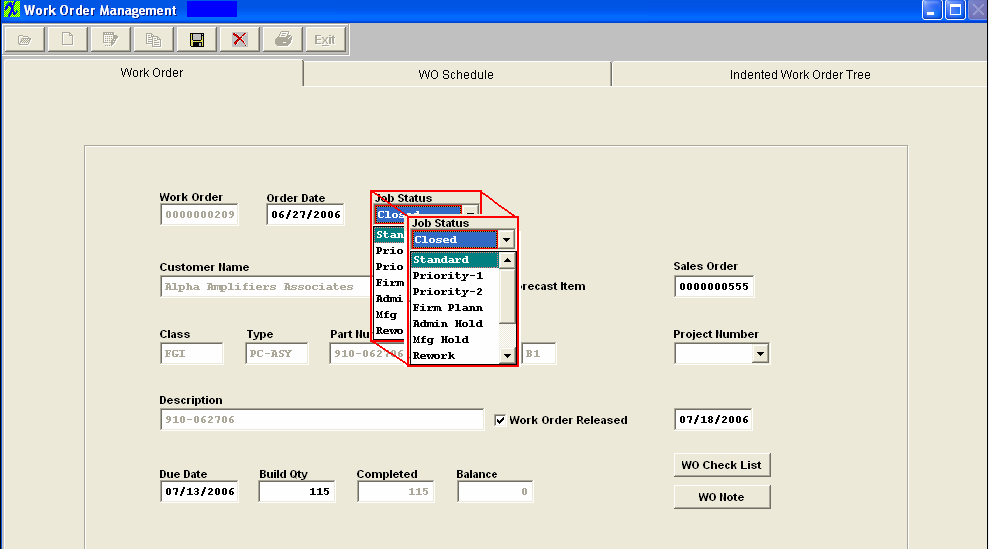
User will receive the following warning

Depress OK then Depress the Save record action button, The following message will be displayed to the user if a SO is linked to a WO:
NOTE: The link is for reference only between the two modules and they are still individual records so when any changes are made to either the SO or the WO the change will not update or be carried forward to the other.
Depress OK WO status is changed from closed to Open/Standard
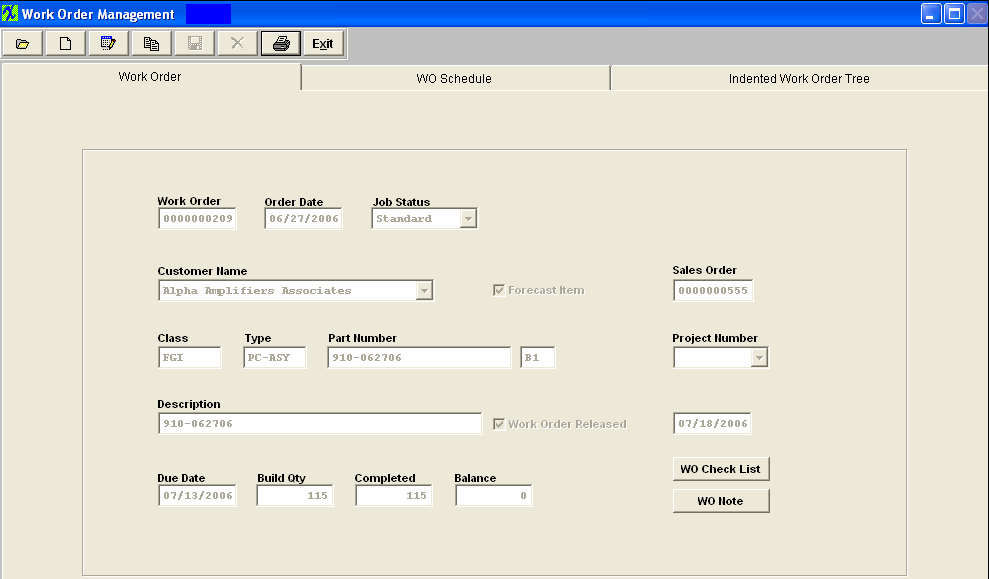
To Manually Close Work Order
Find Work Order with Job Status anything other than "Closed"
Dperss the Edit action button (do not edit anything)
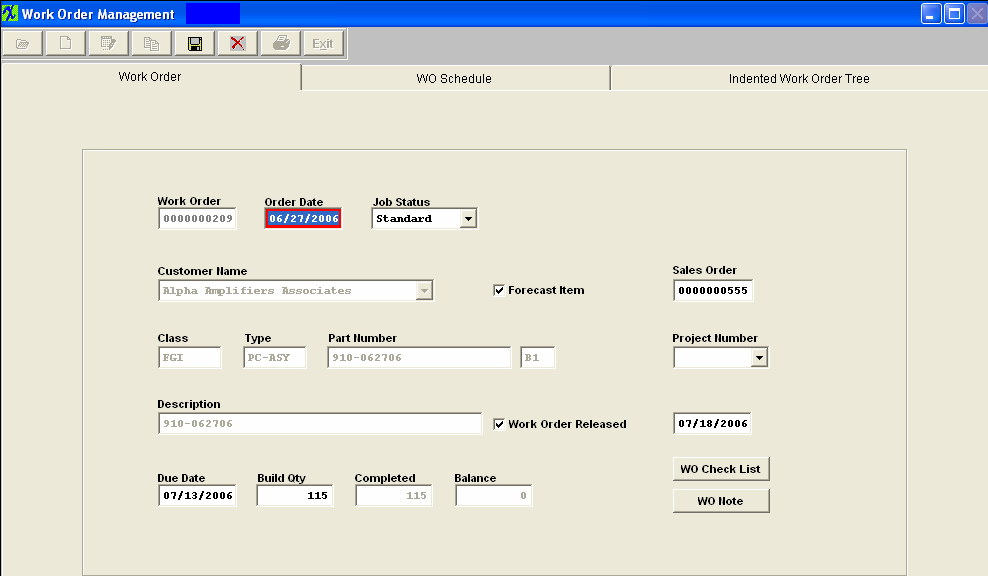
Depress the Save record Action button. The following message will be displayed to the user if a SO is linked to a WO:

NOTE: The link is for reference only between the two modules and they are still individual records so when any changes are made to either the SO or the WO the change will not update or be carried forward to the other.
Depress Ok and Job Status will automatically change to Closed
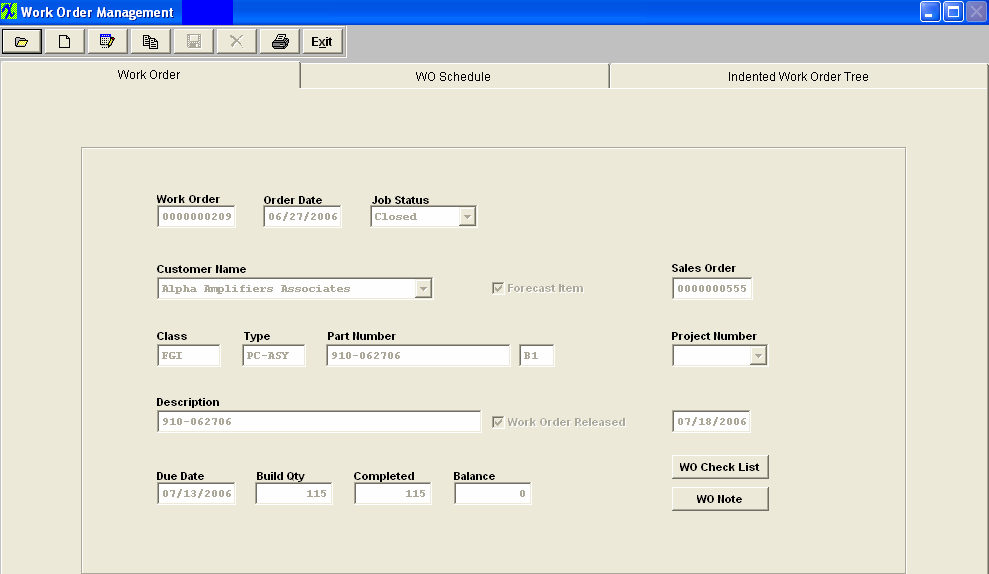
NOTE: Work Orders originated from an RMA Receiver will have "ReworkFirm" Job Status and users will NOT be allowed to change the Job Status, due to the fact that when the Work Order is created from RMA module all kitting, serial number, .... records are created and if user changes the WO status the system may loose track of these records. User will receive the following message if they try to change the job status on a Work Order that was originated from an RMA Receiver.
Since the material issued to the RMA is likely to be a defective assembly, or requires re-inspection, the work order must be completed by either transferring the material to FGI or to scrap to close the work order. Therefore, an RMA work order cannot be cancelled or re-opened.
|
1.4.6. Add a Parent Work Order | Indented Work Order Tab
If the user has multi-level products, and there are other work orders upon which the current work order depends having material, then the Indented Work Order tab will allow the user to establish relationships between those work orders and the current one.
Find an existing Child Work Order
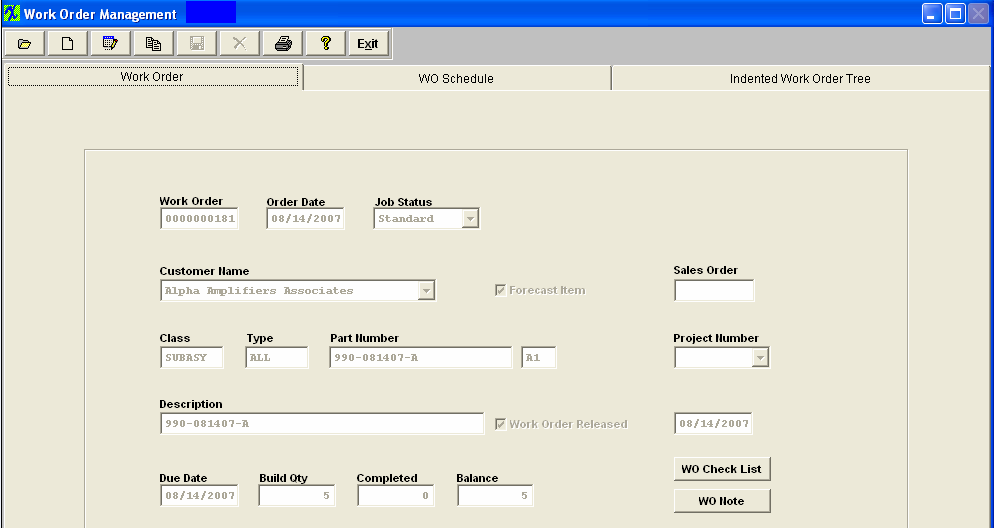
Go to the Indented Work Order Tree tab. Depress the Edit button.
Depress the Add Parent Work Ord button. A red box will appear, as illustrated below:
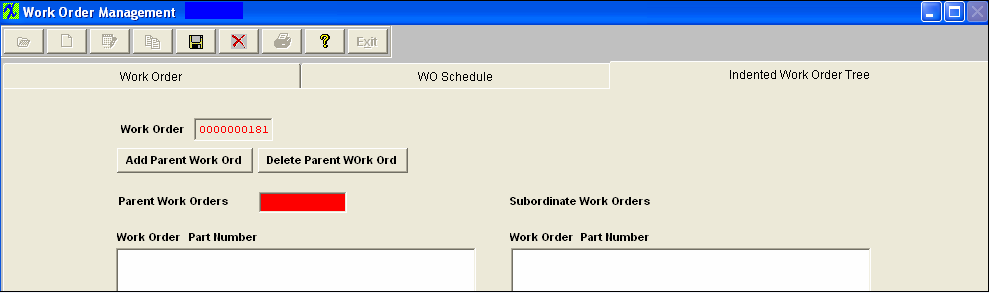
Type the Parent Work Order number into the box. The Parent Work Order number will disappear and will not appear in the Work Order box until the Save record action button is depressed as displayed below. Depress the Abandon changes Action buttons to abandon changes.
Find the Parent Work Order, go to the Indented Work Order Tree tab and the Child Work Order linked will be displayed:
|
1.5. Reports for WO Mgmt |
To obtain the Work Order reports, depress the Reports button. The following screen will appear:
Select the output you desire by clicking on the radial. Choose from Screen, Printer, XL File, TXT File, or PDF.
Highlight the report.
Note: The Work Center Information may not appear in some of the WIP reports within WO Management if the user prints it to an Excel Worksheet file. Some of the reports are quite complex, with multiple relationships and filters. In this instance, the Work Center Information is in a different data base and therefore will not be available.
|
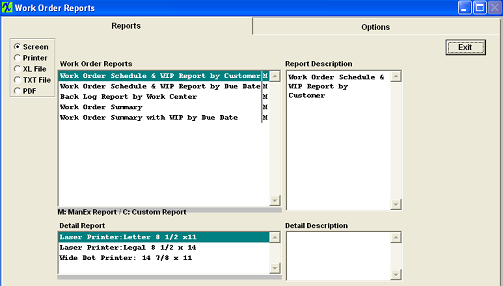 |
Work Order Schedule & WIP Report by Customer
Highlight "Work Order Schedule & WIP Report by Customer" a Detail Report selection will appear at the bottom of the screen. Select the Printer to be used.
Depress the Option tab
|
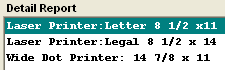 |
Select: All Customers or One Customer |
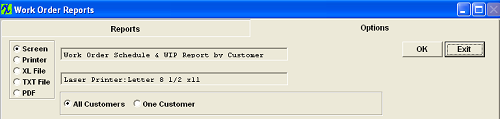 |
The following report will print: This report provides a listing of the status of each job on the production floor. With this report, users can see where each board is in production.
Work Order Schedule & WIP Report by Due Date
Highlight the "Work Order Schedule & WIP Report by Due Date" a Detail Report selection will appear at the bottom of the screen. Select the printer to be used.
Depress the OK button
|
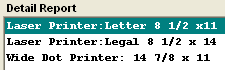 |
The following Report will print : This report provides a listing of the status of each job on the production floor. With this report, users can see where each board is in production by Due Date.

Back Log Report by Work Center
Select the Work Center by highlighting the one you wish and depressing the > button. If you want all work centers, depress the >> button.
Depress OK
|
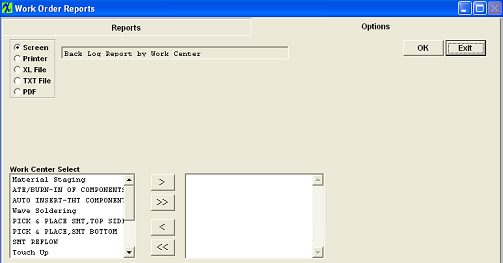 |
The following report will print:
Work Order Summary
Highlight "Work Order Schedule & WIP Report by Customer" a Detail Report selection will appear at the bottom of the screen. Select the Printer.
Depress the OK button
|
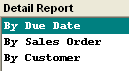 |
The following report will print:
Work Order Summary with WIP by Due Date
Highlight "Work Order Summary with WIP by Due Date Report" a Detail Report selection will appear at the bottom of the screen. Select to print report with price or without price.
Depress the Option tab.
|
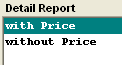 |
Enter the "From" and "To" Dates, and select the customer by highlighting the one you wish and depressing the > button. If you want all customers, depress the >> button.
Depress the OK button.
This report is to be Printed on Legal size Paper.
|
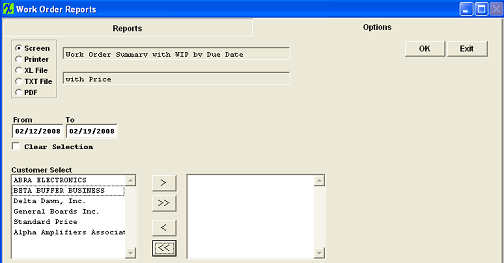 |
The following Report will print: The report can show up to 11 work center information at one time, if user has more than 11 work centers, the program will generate another set of report with same header information (due date, wono, build qty, part number...), with the rest of work center information (at right side). If you run by Screen, Printer...., it should appear twice too.
|
|