1. Shop Floor Tracking by Work Order |
1.1. Prerequisties for SFT by WO | Prerequisites Required for Shop Floor Tracking:
After activation, "Work Order Shop Tracking" access for each user must be setup in the ManEx System Security module. Users with “Supervisor Rights” will automatically have access.
Work Order |
The SHOP FLOOR TRACKING must refer to a Work Order, which includes the part numbers and description of the product being built.
Note: If the "Status" field in the Work Order is set to Manufacturing Hold, the user will NOT be able to transfer product for that Work Oder. If the “Status” field in Sales Order or RMA is set to Administrative Hold, the user may finish transfering the product, but a Packing List can not be issued.
|
Routing |
The Routing must exist for the product, which includes the work centers and activities for the product being built.
|
Optional Prerequisites for Shop Floor Tracking:
Defect Codes |
Required if Inspection data is to be entered.
|
Product Data Mgmt |
Work Instructions should be established if the user wishes to utilize setup and work instructions.
|
Serial Numbering |
The System Setup must define whether or not serialization is required for the part type.
|
Time & Attendance |
User Work Shift information and Time & Attendance features must be installed before you will be able to use the “Time Log” button within the Shop Floor Tracking module.
|
|
1.2. Introduction for SFT by WO | The Shop Floor Tracking Module is used to record detailed transactions of all of the user’s Work In Process (WIP) activity. This screen is a critical piece in the communication process. This allows production to update the system as products move through the shop floor. Production can add notes and indicators to identify current issues and delays. This information is readily available for program managers and others so they have important information when it is needed and without chasing it down in production.
From within this module, the following functions are available, depending on the user’s configuration:
Time Log |
The Time Card module has two functions:1) to enter the worker coming in at the first of the shift and exiting for the day, and 2) to track time spent by each worker on each Work Order (Job), by date and time.This information will forward to the Time and Attendance module.
|
Inspection |
A function for entering quality inspection results. Data may be used to track line quality based on customer, work center, product, location, etc. All Statistical Quality Control information and graphics are based on data entered here.
|
WC Check List |
A list of items defined to be checked as completed for the work order and work center. The users visit this screen, identify the items completed, and enter their password, marking the check list with their initials and date completed.
|
Transfer |
Ths is the key function of this module. This is where the users identify the number of products being transfered from one work center to another during the production of the work order.
|
Setup |
When the Work Center Activity Setup and Run is entered in System Setup, clicking in this area will provide the user with both text and pictorial instructions for setting up the work center.
|
Tool/Fixture |
Depressing this button will display any Tool/Fixture information which has been assigned to the Product through the Routing or Product Data Management (PDM) Module.
|
Work Instructions |
When the PDM module is used, clicking in this area will provide the user with both text and pictorial instructions for processing the product in the work center.
|
Special Instructions |
When the PDM module is used, clicking in this area will provide the user with both text and pictorial instructions for the product and work center.
|
Standard Specifications |
Identifies standard specifications relating to this product per the Standard Process Specification module.
|
Documentation |
Provides a list of documents relating to the product being assembled. Displays the document number, revision, document date, and notes about the document.
|
WC BOM |
Will list all part number assigned to the specific Work Center within the BOM module. It will also allow the user to view the entire BOM if desired.
|
ECO |
This screen will list the detailed information pulled forward from the ECO Control Management module.
|
Deviation |
This screen will list the detailed information pulled forward from the ECO Control Management module pertaining to any approved Deviations for the selected product.
|
Quality Info |
Will display the Quality information for the selected Work Center based on the information entered within the Inspection module.
|
WIP Status |
Show all the open work orders for this product and show where the quantities are in the shop floor
|
User Defined Button |
This is an outside call program that ManEx has implemented into the system. The Users can have their own program to run when they scan their serial number inside of shop floor tracking by using the “User defined” button. Within the Outside Program Call Setup module, the user will have the ability to change the button name of the “User Defined” button and select which program (EXE) they want to run after the users scans specific Serial Numbers.
|
Work Order Note |
Any notes entered for the work order on the shop floor tracking screen will cause the button to turn Red. Any comments in this area will be visible to all work centers which are included in the work order routing.
|
Work Order / Work Center Note |
Any notes entered specifically for the work order and the work center being viewed will cause the button to turn Red, calling the user’s attention to review notes that are applicable to the order. This button is sensitive to the work center being highlighted on the shop floor tracking screen.
|
Work Center Note |
Any notes entered for the work center highlighted on the shop floor tracking screen will cause the button to turn Red. Any comments in this area will be visible to all products which include the work center in the routing.
|
Xfer History |
This button lists the history of transfers.
|
Serial No History |
This button will display Transfer History and Defect History by specific serial numbers.
|
Feedback |
This is simply a note screen that may be used to record information about the product during the course of manufacturing.
|
For further detail of these functions see Article #3107 .
|
1.3. Fields & Definitions for SFT by WO |
1.3.1. Work Order Shop Floor Tracking | 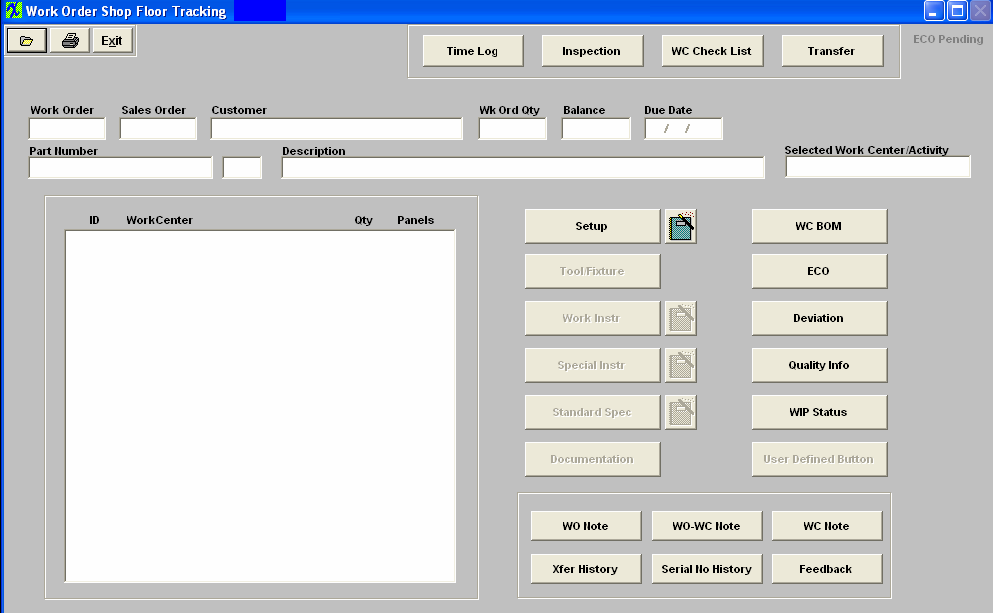
Work Order Shop Floor Tracking Fields and Definitions
 |
This Text/characters turns RED if an ECO (Engineering Change Order) is Added and Saved. When the ECO is approved, this button characters turns back to gray. This criteria is based on the product number and no revision number as the ECO will change the revision number.
This feature has been added because of the importance of the users needing to know that an ECO is being initiated by the production personnel. This will help prevent product being built according to the original instructions and cut down on any additional rework or schedule delays.
|
Work Order |
The Selected Work Order |
Sales Order |
The Sales Order linked to the Selected Work Order |
Customer |
The Customer Name associated with the Selected Work Order |
Wk Ord Qty
|
The number of units for the Selected Work Order |
Balance |
The remaining balance of the parts to be delivered for the work order |
Due Date |
The due date for the first shipment remaining to be shipped in the work order (ignores due dates that have already been shipped). |
Part Number
|
The part number of the assembly being built for the work order. Next to the part number is a space for revision |
Description |
This field will contain the Class, Type and Description of the assembly being built for this work order. |
Selected Work Center/Activity |
This area displays the work center (or activity) from which each of the action buttons below are launched.It is selected by placing the cursor (by mouse or tab) on the work center (or activity) of interest. |
ID |
The ID or abbreviation established for the work center. |
Work Center |
The Work Center's assigned to the MAKE part in Work Order Traveler Setup |
Qty |
The quantity of parts pertaining to the work order that are currently in the work center.
|
Panels |
This field will contain the number of panels in the work center (if the user tracks panels, based on conditions in the Shop Floor Tracking Defaults).
|
See Article #3107 for the Directive Buttons fields and definitons
|
1.3.1.1. Directive Buttons | SFT by WO Directive Buttons
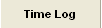 |
The Time Card module has two functions:1) to enter the worker coming in at the first of the shift and exiting for the day, and 2) to track time spent by each worker on each Work Order (Job), by date and time. This information will forward to the Time and Attendance module. |
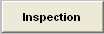 |
See Article #1769 for detail on entering Quality Inspection results using this function. Data may be used to track line quality based on customer, work center, product, location, etc. All Statistical Quality Control information and graphics are based on data entered here. |
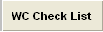 |
Depressing this button will display a list of items defined to be checked as completed for a specific Work Center. The users visit this screen, identify the items completed, and enter their password, marking the check list with their initials and date completed. For further information see Article #3552. |
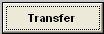 |
The key function of this module. This is where the users identify the number of products moved from one work center to another during the production of the work order. For further detail see Article #857 . |
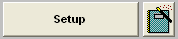 |
When the Work Center Activity Setup and Run is entered, clicking in this area will provide the user with both text and pictorial instructions for setting up the work center. |
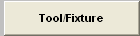 |
Depressing this button will display any Tool/Fixture information which has been assigned to the Product through the Routing or Product Data Management (PDM) Module. NOTE: For this button to be enabled user MUST have the "Tool/Fixture Released" box checked on the Check List Title screen.
|
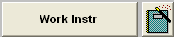 |
When the Product Data Management module is used, clicking in this area will provide the user with both text and pictorial instructions for processing the product in the work center. NOTE: For this button to be enabled user MUST have the "PDM Released" box checked on the Check List Title screen. |
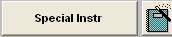 |
When the Product Data Management module is used, clicking in this area will provide the user with both text and pictorial instructions for the product and work center. The Special Instructions are not printed on the travelers. NOTE: For this button to be enabled user MUST have the "PDM Released" box checked on the Check List Title screen. |
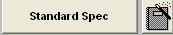 |
Identifies standard specifications relating to this product per the Standard Process Specification module. NOTE: For this button to be enabled user MUST have the "PDM Released" box checked on the Check List Title screen. |
 |
Provides a list of documents relating to the product being assembled. Displays the document number, revision, document date, and notes about the document. NOTE: For this button to be enabled user MUST have the "PDM Released" box checked on the Check List Title screen. |
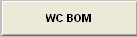 |
This screen will list all part number assigned to the specific Work Center within the BOM module. It will also allow the user to view the entire BOM if desired.
|
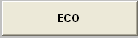 |
|
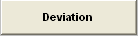 |
This screen will list the detailed information pulled forward from the ECO Control Management module pertaining to any approved Deviations for the selected product. |
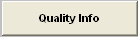 |
Will display the Quality information for the selected Work Center based on the information entered within the Inspection module.
|
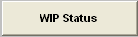 |
Show all the open work orders for this product and show where the quantities are in the shop floor.
|
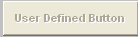 |
This is an outside call program that ManEx has implemented into the system. The Users can have their own program to run when they scan their serial number inside of shop floor tracking by using the “User defined” button. Within the System Setup/Outside Program Calls Setup module, the user will have the ability to change the button name of the “User Defined” button and select which program (EXE) they want to run after the users scans specific Serial Numbers. |
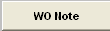 |
Any notes entered for the work order in the Shop Floor Tracking screen will cause the button to turn Red. Any comments in this area will be visible to all work centers which are included in the work order routing. |
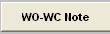 |
Any notes entered specifically for the work order and the work center being viewed will cause the button to turn Red, calling the user’s attention to review notes that are applicable to the order. This button is sensitive to the work center being highlighted on the shop floor tracking screen. |
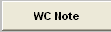 |
Any notes entered for the work center highlighted on the shop floor tracking screen will cause the button to turn Red. Any comments in this area will be visible to all products which include the work center in the routing. |
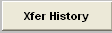 |
This button allows the user to view the history of product transfer from one work center to another. NOTE: If the product has changed revisions from the ECO module, the SFT module will see it as a different product and no longer display the Transfer History information on screen for the old revision. (See Article #3401 for more detail).
Note: If product is serialized the transfer history screen will list each product individually, treating each serial numbered product as its own seperate part for tracking purposes, as displayed in the screen below:
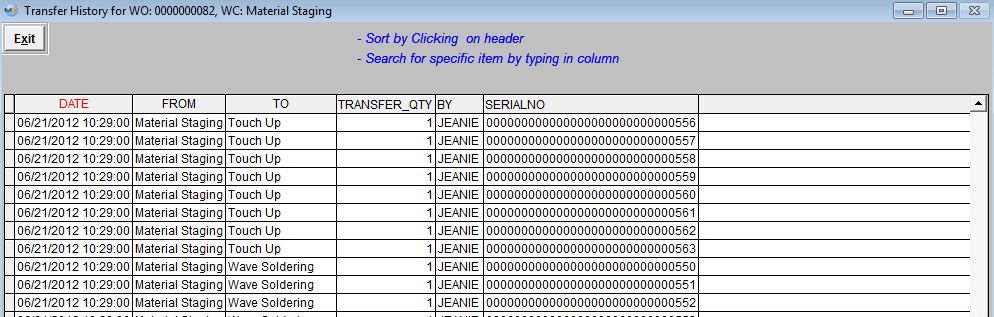
If product is not serialized the xfer history will list qty's as they are transfered, as displayed in the screen below:
|
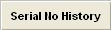 |
This button will display Transfer History and Defect History by specific serial numbers.
|
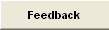 |
This is simply a note screen that may be used to record information about the product during the course of manufacturing, and is specific to the work center and work order. |
|
1.3.2. Transfer Screen | 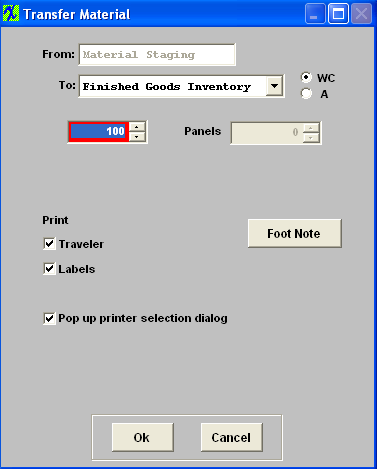
From |
Work Center Highlighted that product is currently in |
To |
Work Center that product being transferred to |
WC/A |
The user may elect to transfer material within work centers (WC) or within activities (A) by pressing the appropriate radio button |
|
Qty of product being transfered |
Panels |
Number of Panels (if applicable) |
Traveler |
Whenever a product is moved from one work center to another, the user has the option to print a move ticket (like a traveler) for each transaction. This move ticket may be printed and accompany the material to the next work center, identifying the work order, product date, work center, etc. The user may choose to turn this feature off by selecting the “Printer OFF” button in the SFT Defaults setup . If the printer is turned on (“Printer ON”), then a sheet with the details will be printed for every product movement.
If the user chooses to print move tickets, then they may also choose whether or not work instructions and work order notes are included in the printing within the SFT defaults setup.
|
Labels |
Whenever a product is moved from one work center to the Work Center called FGI (Finished Goods Inventory), the user has the option to print a move ticket (like a traveler) for each transaction. This move ticket may be printed and accompany the material to finished goods, identifying the work order, product date, work center, etc. The user may choose to turn this feature off by selecting the “Printer OFF” button in the SFT Defaults setup. If the printer is turned on (“Printer ON”), then a sheet with the details will be printed for every product movement.
|
Pop up printer selection dialog |
If this box is checked the system will not print directly to the default printer, it will bring up the Printer dialog box and allow the user to select which printer to send the traveler to. The user may choose to turn this feature off by selecting the "OFF” button in the SFT Defaults setup |
 |
Add any Foot Notes that you would like printed on the Traveler. Note: These notes are not retained in any tables and are only temporary. |
|
1.4. How To ..... for SFT by WO |
1.4.1. Finding A Work Order |
To Enter the Shop Floor Tracking by Work Order Module depress Production/Shop Floor Tracking by Work Order |
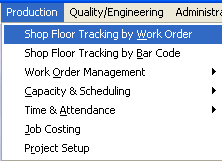 |
The Main Screen will appear.
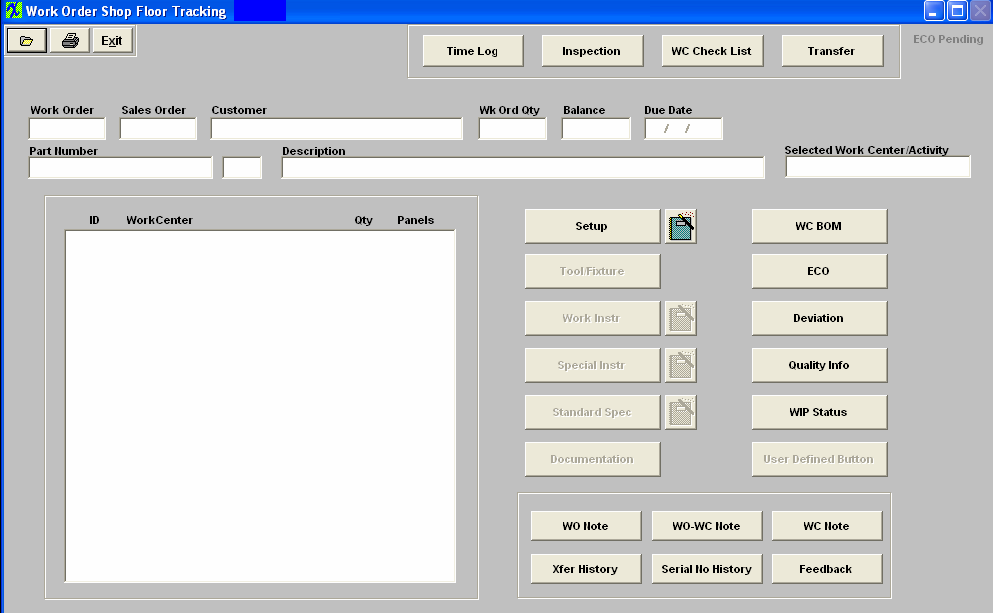
Depress the Find Button displays the following sequences:
|
|
Select the desired Work Order record.
The Shop Floor Tracking screen is then populated with the appropriate data.
The Products will be listed in alpha-numerical order, along with the Revision, Class, Type and Description.
Select the desired Product Number.
|
1.4.2. Shop Floor Tracking - Transfer | Find the desired Work Order record within the system.
Highlight the current Work Center where quantity is displayed, as illustrated:
Depress the “Transfer” button. The system will prompt for a password. The following dialogue box will be displayed.
The user may elect to transfer material within work centers (WC) or within activities (A) by pressing the appropriate radial button on the screen.
Manex will determine the next area to transfer product based on the product routing, and enter the location in the “To:” field.
The user may elect to change this location by pressing the down-arrow button next to the field and selecting a different location.(NOTE: The user MUST have "Skip rights" or "Supervisor rights" setup within the Security module in order to skip work center locations, or move product backwards)
|
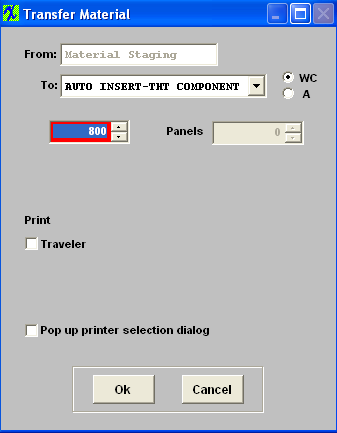 |
Next, Manex lists the number of products at the current location. The user may move all items, or select the quantity to be moved. This may be done by simply over-writing the quantity or by using the “arrows” to raise or lower the quantity shown.
The user may also elect to print a traveler to accompany the parts at this time. Once the Print Traveler box is checked, a Footnote button appears, as shown. Any Footnotes that a person enters within this screen is just temporary and is only printed on the Traveler report.
The user may also elect to print a label to accompany the parts to material to finished goods, identifying the work order, product date, work center, etc.
If the user elects to have the “Pop up printer Selection dialog” marked. The system will not print directly to the default printer. It will then bring up the Printer dialog box and allow the user to select which printer to send the traveler to.
|
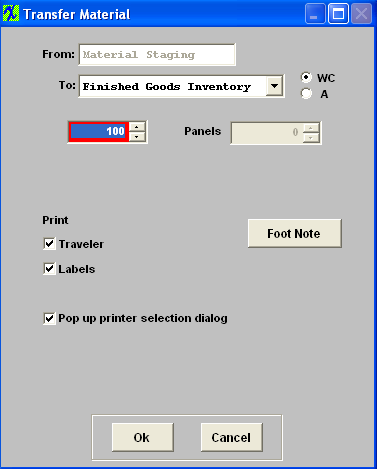 |
Depressing the Footnote button will bring up a note screen.

Depress the Edit button, Type in the footnote. Depress the Save button. Depress the Exit button.
Depress the OK button. The material will transfer and the Traveler will go directly to the default printer. (This report requires that the user have the bar code font available).
If a balance still remains in the selected work center then the system will prompt the user if they would like to transfer to a different Work Center.
Yes – will bring up the Transfer Material screen again.
No – will bring you back to the regular Shop Floor Tracking module.
|
|
If the product is included in an active Cycle count, or Physical Inventory count, the following message will appear after depressing the OK button on the transfer screen anud user will not be allowed to transfer product until the count has been completed and posted.

If user is transfering product into FGI and the Work Order has any item(s) that has short qty > 0 and the "Ignore Kit" box is NOT checked the following message will popup giving the user the option to continue moving the product or not.
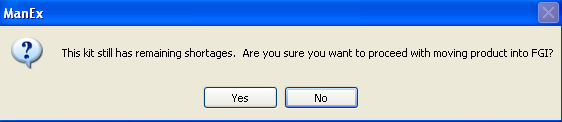
Transferring Serialized product
If the work station being used to transfered serialized material is assigned to use a default work center in Production Work Center/Activity Setup module, when the user first opens the module, the module will use the default work center assigned for this workstation, if the transfer is "FROM" a different work center other than the default and user is NOT a supervisor or has the option "Allow Changing Default Work Center for Serial Number Transfer" box checked within the Security module, they will receive the following message:
When user depresses "OK" a supervisor approval is required to continue. After supervisor’s password is entered, the default work center will be changed to the one that the supervisor entered password for. For example: the workstation is assigned to use “TU” as default work center, now if user chooses to use “AI” to transfer, the system will ask for supervisor’s password, if user cancels the password, the default work center will still be “TU”, but if the supervisor enters his/her password on this machine, the default work center will be changed to “AI”. If now the user tried to transfer from “TU” again, the system will ask for supervisor’s password again. If user exits the module and come back, the default work center will be “TU” again.
If the user is tracking by serial numbers, and if the user is transferring a lesser quantity than displayed, Manex will display a screen from which to select the serial number(s) to be moved in the transaction.
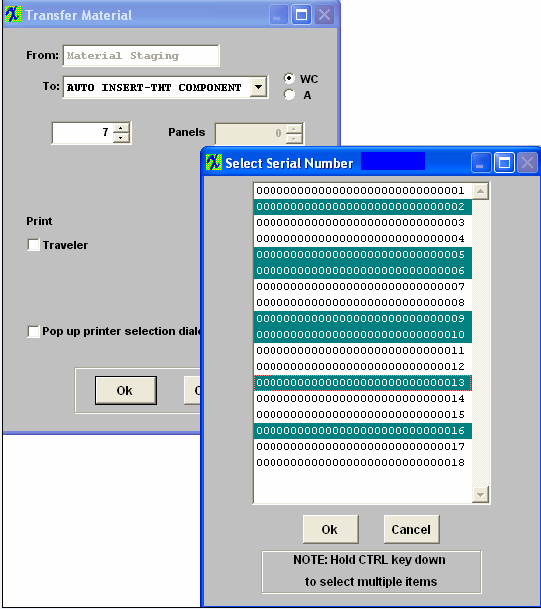
The user may select one or more serial numbers to match the quantity being transferred, and then press the OK button.
The user must select the proper number of serial numbers or the transaction will be cancelled.
Since less is being transferred, the following message will appear:
Yes – will bring up the Transfer Material screen again.
No – will bring you back to the regular Shop Floor Tracking module.
|
|
Discussion on the Accounting Entries
If the user also has accounting installed, then the appropriate journal entries will forward to the Accounting “Release to General Ledger” screen. Briefly, assuming that the user has the material cost set up in the Inventory Control Item master, then when the product reaches the Work Center “Finished Goods Inventory”, the entry will be to debit Finished Goods Inventory (or the warehouse home general ledger number of the product) and to credit WIP .If the product ended up in the Work Station “Scrap”, then the debit would be to the default scrap general ledger account, as set up in the Accounting Set Up.
Configuration Variance
If the Material Cost per the product was not equal to the sum of the standard costs per the BOM components, then a configuration variance will be created.
Please refer to the “Wip Value" Article #913 for further explanation.
|
1.4.3. Use Work Center CheckList within SFT Module |
Create a Routing within the WO Traveler Setup module for Product. For further detail see Article #850
Create a Checklist for a Specific WC within the PDM module. For further detail see Article #2824 .
Create a Work Order for the product within the Work Order module. For further detail see Article #1815.
Transfer product through SFT when product reachs the Work Center with the checklist the "WC Check List" butoon will be displayed in Red (as displayed below).
Click on the "WC Check List" button and the check list will appear (as displayed below):
User must then review the list and check the box when task has been completed and their initials, time and date will default in (as displayed below): Note: This check List is for reference only and WILL allow the users to transfer product to the next Work Center if not all items have been checked off.
Once all the boxes have been checked within the Work Center CheckList user may complete the transfers. Note: This checklist is for users to check if they do all the necessary task, but it does NOT enforce the user to check all items before the user can transfter to next WC.
|
1.4.4. Enter Defect Data Entry | Follow the Steps in Article #1769 to move product by using the Defect Entry Module.
|
1.5. Reports - SFT by WO | To obtain reports, depress the Report button. The following screen will appear:
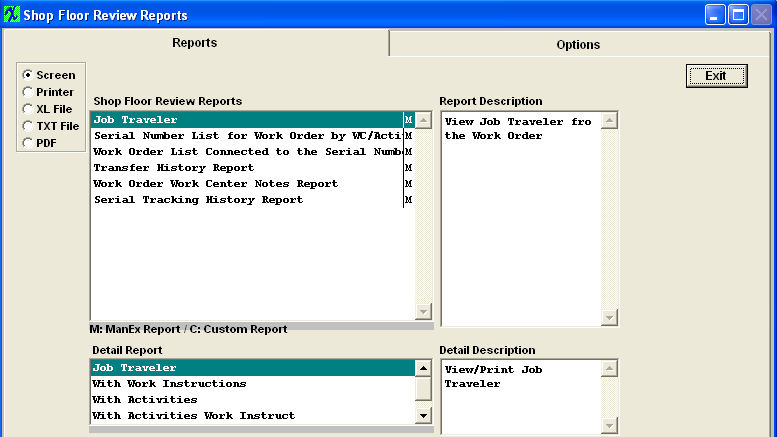
JOB TRAVELER REPORT
Highlight the “Job Traveler” report. Make the desired selections in the Detail Report Section.
Note: The Work Instruction may not appear in the Traveler if the user prints it to an Excel Worksheet file. Some of the reports are quite complex, with multiple relationships and filters. In this instance, the Work Instructions are in a different data base than the routing and therefore will not be available.
Then depress the Options tab. The following screen will appear:
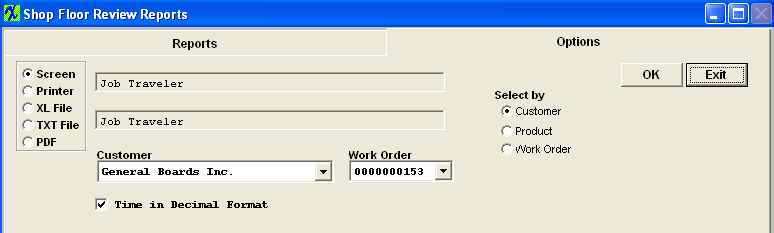
Select the desired radial selection:Customer, Product or Work Order. Select the desired Customer and Work Order by using the Down Arrows next to the fields.
If you do not want time in decimal format, uncheck the box. The following reports will be displayed:
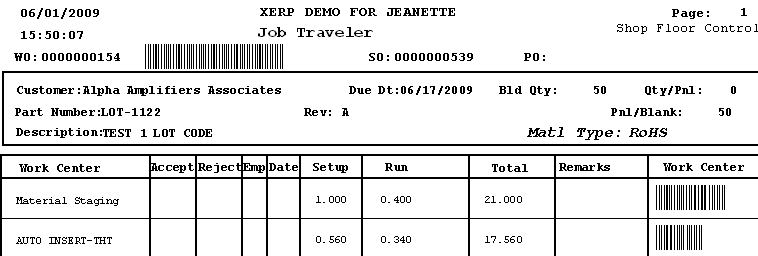
SERIAL NUMBER LIST FOR WORK ORDER BY WC/ACTIVITY REPORT
Highlight the “Serial Number List for Work Order by WC/Activity” report. Depress the Options tab. The following screen will appear:
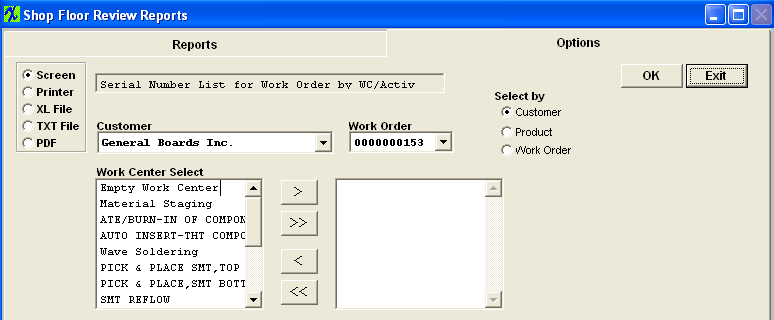
Select the desired radial selection:Customer, Product or Work Order. Select the desired Customer and Work Order by using the Down Arrows next to the fields.
Highlight the Work Center and depress the > button. If you want all work centers, depress the >> button. The leading zero's for SN will be removed from Report.
The following report is available:
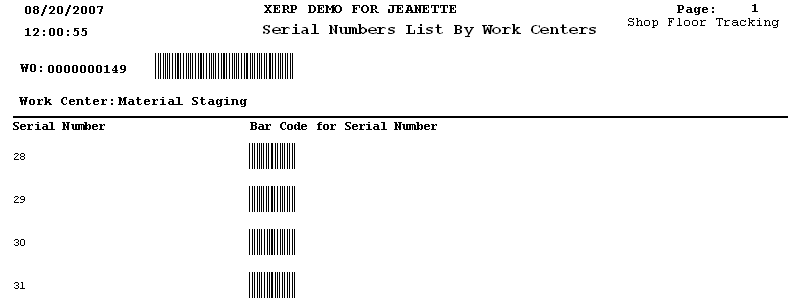
WORK ORDER LIST CONNECTED TO THE SERIAL NUMBER REPORT
Highlight the “Work Order List Connected to the Serial Number” Report. Note:that this report is a View screen only – no report will be generated as an output.
Depress the Options tab. Type in the Serial Number and the following will display.
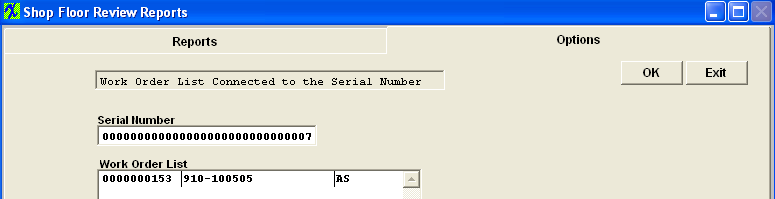
Hitting the OK button will bring you back to the Shop Floor Tracking module.
TRANSFER HISTORY REPORT
Highlight the “Transfer History” report.
Depress the Options tab. The following screen will appear:
Select the Work Center by highlighting and depressing the > button. If all Work Centers are desired, depress the >> button. If you do not want time in decimal format, uncheck the box.
Enter in the desired Date Range. Leading zero's for SN will be removed from report. The following Report will be displayed.
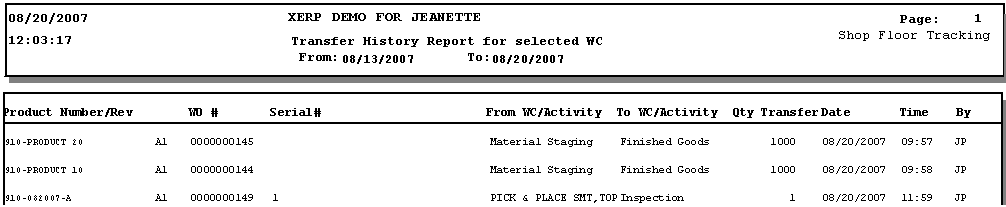
WORK ORDER WORK CENTER NOTES REPORT
Highlight the “Work Order Work Center Notes” report.
Depress the Options tab. The following screen will appear:
All Work Centers are selected by default. If you wish to deselect any Work Centers use the < Button. The following report will be displayed:
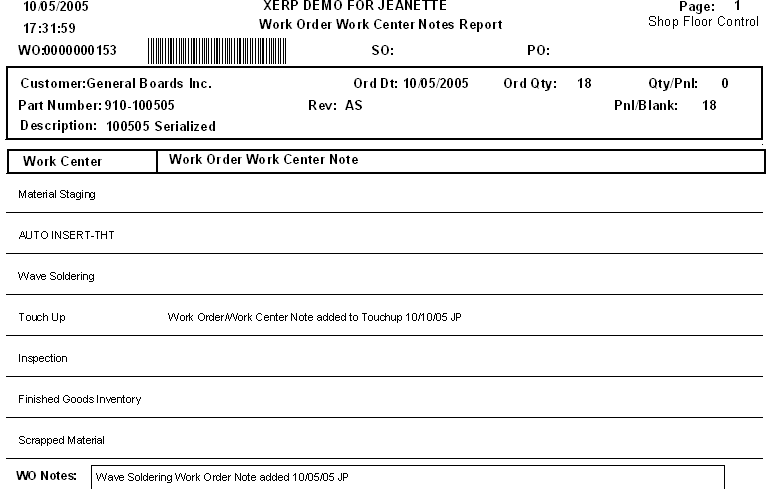
SERIAL NUMBER TRACKING HISTORY REPORT
Highlight the “Serial Number Tracking History” report.
Depress the Options tab.The following screen will appear:
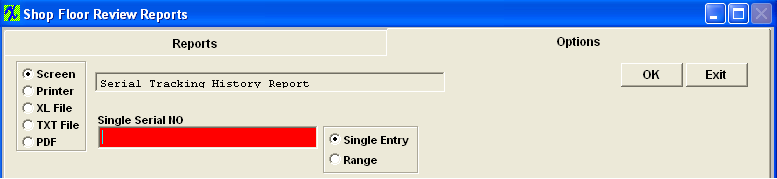
Select the desired radial button: Single Entry or Range. Enter Serial Number. Leading zero's for SN will be removed from report.
The following report will be displayed: This report will gather transfer history and defect history for those serial numbers that have been linked to more than one work order and display the transfer history and defect history for all those work orders.
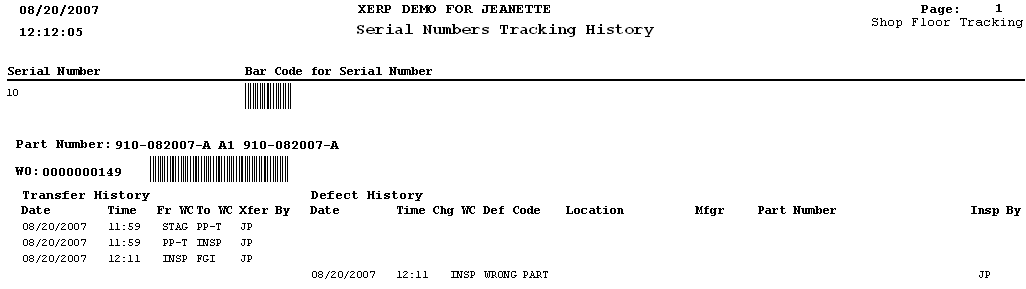
|
1.7. Test & Repair (T & R) (OPTIONAL Module) |
1.7.1. Prerequisites for the T & R Module |
The Test & Repair is actually a separate OPTIONAL module, but has been included into the Defect Entry screen for ease of use for the operators.
After activation, Work Order Shop Tracking, Defect Code Entry, and Test & Repai access for each user must be setup in the ManEx Security module. Users with “supervisor’s rights” will automatically have access.
|
1.7.2. Introduction for the T & R Module | Test & Repair Management (T&R) has been designed to capture testing results and failure information such as: In-circuit Testing, Sub-Assembly Functional Testing and System Final Assembly Testing.
Once this information has been entered this will allow the users the ability to see the Serial Number History and view all of the testing and repair results as well as when it had been shipped to customers. It will also keep track of any associated returns or warranty work that had been done against this particular Serial Number, continuing history as long as the unit is in service.
|
1.7.3. Fields & Definitions for the T & R Module |
1.7.3.1. Test & Repair Tab | Test & Repair Screen Field Definitions
The Test & Repair is actually a separate OPTIONAL module, but has been included into the Defect Entry screen for ease of use for the operators.
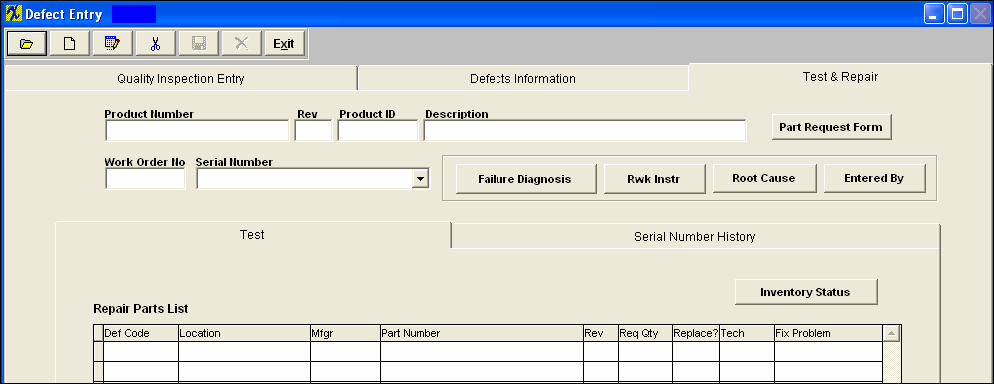
Product Number |
The internal number assigned to the assembly.
|
Rev |
The revision number associated with the Product Number.
|
Product ID |
This field is no longer used and will be left blank.
|
Description |
The description of the Product Number.
|
 |
If the component part is to be replaced, this button will be available to view and print the request for replacement. This request/form should be sent to the stockroom showing them that replacements are needed for the components identified as failing inspection or test. If the part is issued, it will be charged to the work order.
|
Work Order Number |
The number of the work order which was inspected.
|
Serial Number |
The serial number of the assembly which failed inspection.
|
|
These three buttons are for viewing notes on the topics of diagnosis of failure, instruction for reworking and the cause of the defect |
 |
This button will open up a screen which will display the initials of the user who entered the failure: |
Test Tab Field Defintions
Repair Parts List
Def Code |
The code assigned to the defect.
|
Location |
The Reference Designator as set up in the assembly’s Bill of Materials.
|
Mfgr |
The name of the manufacturer of the failed part.
|
Part Number |
The internal number assigned to the failed component.
|
Rev |
The revision number assigned to the internal part number.
|
Req Qty |
The number rejected of the assembly.
|
Replace ? |
If this box is checked, the user intends to replace the rejected component.
|
Tech |
This field will display the name of the technician who fixed the defect. To get the name to display user must double click in the field. This is a read only field and can NOT be edited.
|
Fix Problem |
If the user decides to fix the problem, he/she may choose one of the following selections:
|
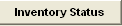 |
Depressing this button will bring up the following information:
|
Serial Number History tab
Transfer History Section
Date & Time |
The date and time (24 hour clock) the assembly was transferred to the Work Center.
|
From/To |
The Work Centers involved in the transfer.
|
Qty |
The quantity transferred.
|
By |
The initials of the user who recorded the transfer.
|
Defect History Section
Date & Time |
The date and time (24 hour clock) the assembly was rejected.
|
Init |
The initials of the user who recorded the rejection.
|
WC |
The Work Center where the failure was noted.
|
Def Code |
The code relating to the defect.
|
Location |
The Reference Designator as set up in the assembly’s Bill of Materials.
|
Part Manufacturer |
The name of the manufacturer of the failed component.
|
Part Number |
The internal number assigned to the component.
|
|
1.7.4. How To ...... for the T & R Module |
1.7.4.1. Add Test and Repair Information | When the user has completed the Defect information, they may enter the Test & Repair tab to enter more information about the part, or may depress the Open/Find record button to find this information at a later time.
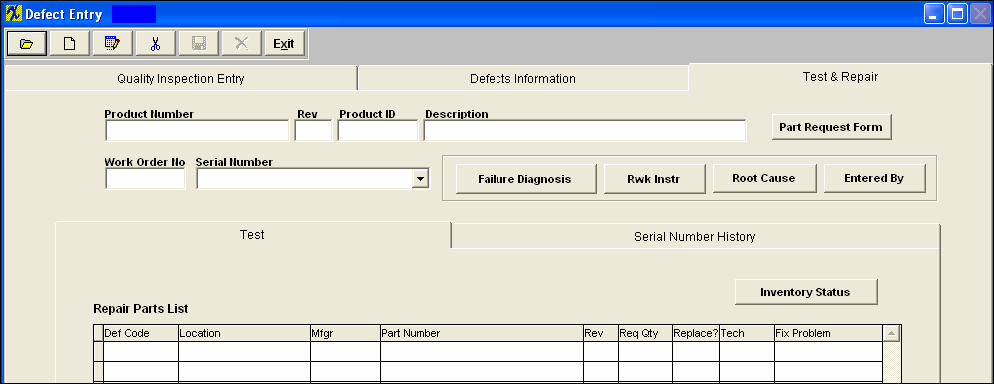
Once user has selected a transaction the following screen appears displaying the record you selected:
Depress the Edit button and enter your password, user may at this time edit the Quality Inspection Entry info, the Defects Information, or the Test & Repair info:
Depress the Test & Repair Tab: (System will only display information for one serial number at a time).
In the edit mode user can edit the required qty, check the Replace? box, or select to Fix Problem from the pull down:
NOTE: To have the initials of the technician who fixed the defect displayed, user must double click in the field.
User may enter information in the Failure Diagnosis, Rwk Instructions, and/or Root Cause (these 3 fields are text fields). Within this screen you may also View the "Entered By" or "Inventory Status" of Part Number.
Depress the Save button to save changes or Depress the Abandon changes button to abandon changes.
User may at this time print the "Part Request Form" which will need to be approved and hand delivered to the stockroom, so they may fill the shortage(s) and issue part(s) to the kit.
To View the Serial Number History depress the "Serial Number History" tab
|
|