1. How To ..... for PO Mgmt |
1.1. Find a Purchase Order |
Depress Material Planning/Purchase Order Management/Purchase Order Management. The main screen will appear.
|
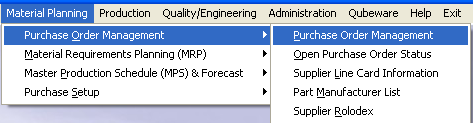 |
1. Depress the Find Record icon.The following screen will be displayed.
2. On the left hand side of the screen, choose what you’re looking for – either Open PO, All, Closed/Cancelled PO or For Approval, by clicking on the appropriate radial.
|
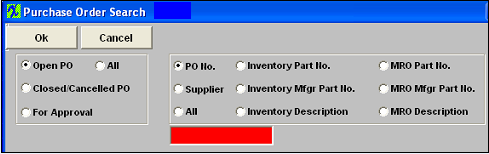 |
3. Once you’ve made your “search for” choice, determine the search method by choosing between PO Number, Inventory Part Number, MRO Part Number, Supplier, Inventory Manufacturer Part Number, MRO Manufacturer Part Number, All, Inventory Description, or MRO Description.
4a. For example, a selection on the left for an Open PO, and a selection of ALL on the right will produce the following screen, listing all open purchase orders.
Double click on the Open PO displayed to make your selection.
|
|
4b. A selection on the left for All and a selection of All on the right will produce a list of all purchase orders, open, closed, etc. |
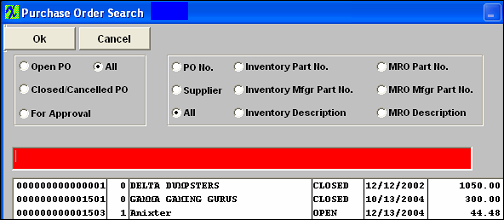 |
4c. A selection on the left of For Approval and a selection on the right for All will produce the following selection. (Pending, Editing, New, etc.)
|
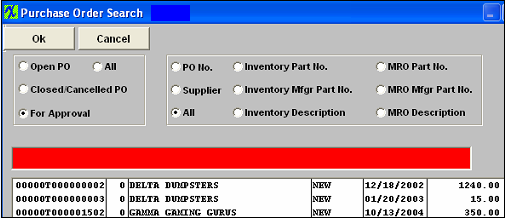 |
4d. If you are searching for a specific PO, select All on the left and PO No. on the right.Then type in the purchase order number and hit enter.The PO record will pull onto screen. |
|
4e. If you are interested in a specific supplier with open POs, mark the left hand side Open PO and the right as Supplier.Type in the Supplier Name.
A list of all of the Open POs for that Supplier will appear, as shown.
|
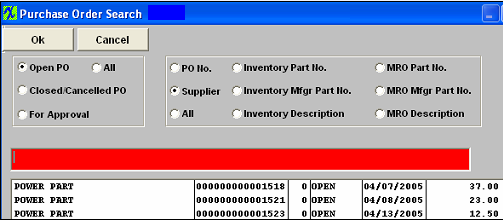 |
4f. If you are interested in a specific part number on Open POs, select Open PO on the left and Inventory Part No. on the right.Type in the Part Number.
Any open POs containing this part number will appear, as shown.
|
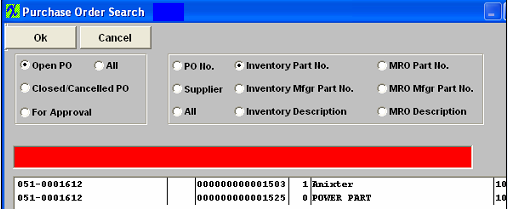 |
The rest of the right hand selections are essentially the same as for those illustrated above.
5. After finding the Purchase Order, the Purchase Order screen appears, populated with any parts on order.
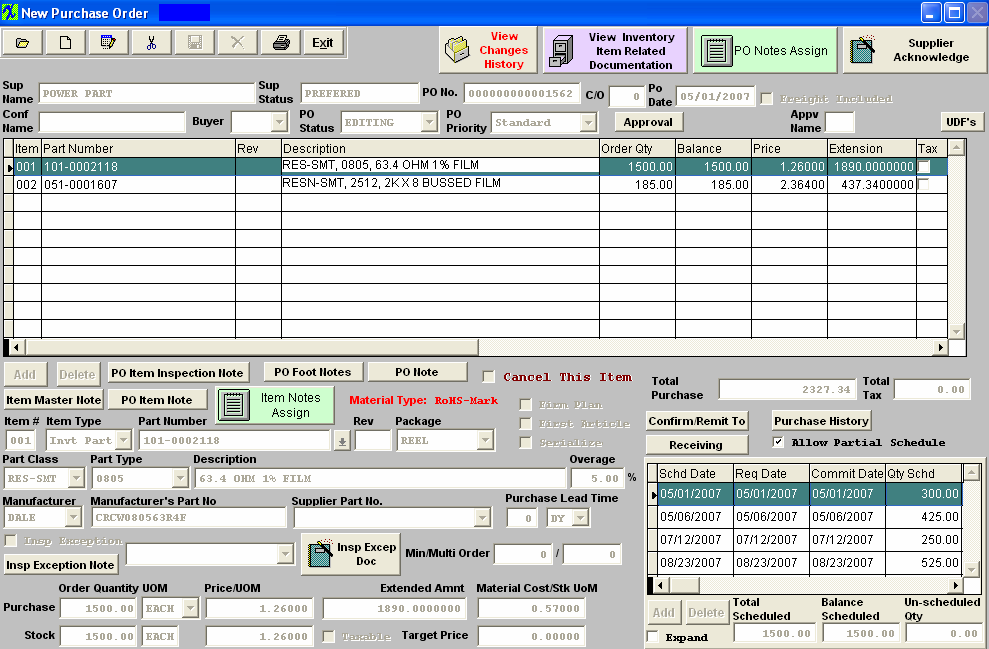
|
1.2. Add A Purchase Order |
Enter Manex.exe
Material Planning/Purchase Order Management/Purchase Order Management
|
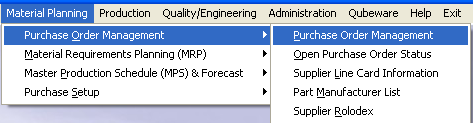 |
The following screen will appear:
Depress the Add Record Button (in the Purchase Order Tab screen) displays the following sequences:
The user will be prompted for the password. The first step is to Select Regular PO or In-Store PO
|
|
If Regular PO is selected then another Selection box will appear. The user must define the supplier for the purchase order.
The user is asked if they wish to locate the supplier by the name or supplier ID code.
|
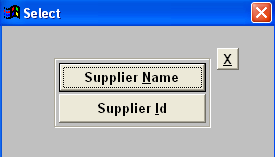 |
If the user selects to find a supplier by the name, a screen is presented listing all of the suppliers in alphanumeric order |
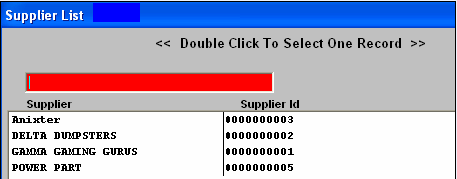 |
If the user selects to find a supplier by the ID code, a screen is presented listing all of the supplier ID codes in alphanumeric order |
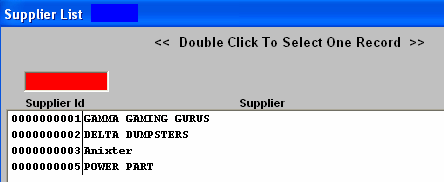 |
The user may enter the number or name in the red edit box above the Supplier or Supplier ID label, or scroll down to select a supplier. Double clicking on a supplier or pressing the ENTER key on a highlighted supplier selects the supplier and displays the Purchase Order screen with the supplier included.
Once a supplier is identified, the remaining information fields become active. The user can CANCEL the action if needed.
The user then may fill in the Confirm Name, Buyer and add items to the purchase order.
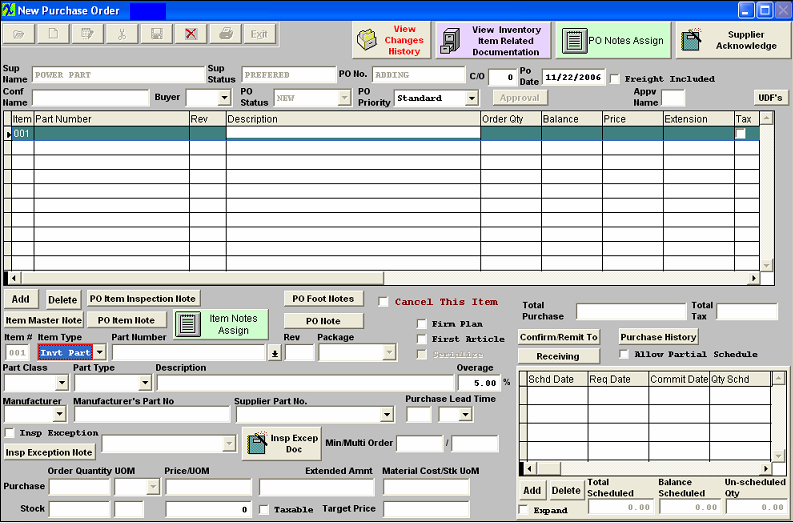
Entering Item Detail Information
The user must first select the Item Type to be entered as a line item. Item types include Inventory Parts (parts to be delivered to on hand inventory), MRO (expensed items) or Services .
|
|
|
1.2.1. Inventory Part | Selecting Inventory Parts as the item type, the user may jump directly to the part number box (click on it) and enter a part number. Or, the user may step through the Part Classes and Part Types to narrow the focus and then select a part from the desired part type. Once a part number from Inventory has been entered, ManEx completes the boxes associated with the item master.
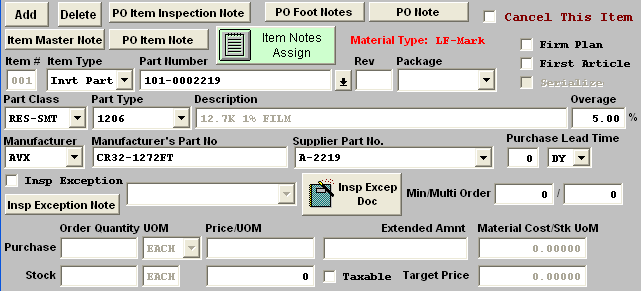
If more than one manufacturer exists for the part, the user may click on the down-arrow next to the manufacturer edit box and select the appropriate manufacturer for the order. The Material type will be displayed in the pulldown next to the Mfg. and Mfgr. PN. |
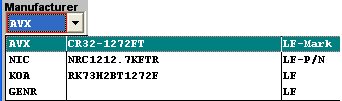 |
If more than one supplier part number exists for the part, the user may click on the down-arrow next to the supplier part no. edit box and select the appropriate supplier part no. for the order.
The system will look for the preferred supplier part number and if found will show it as a display. At this time the user can leave the part number as is or select a different one if available. After a user will save the PO, the supplier part number will be saved and next time you will see the selected suppler part number when viewing the same PO.
No history will be saved because this field is for the information only.
|
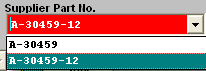 |
Firm Plan |
If this box is checked, the MRP module will not try to override the purchasing decision. For Example: The user makes a decision to block order 600 parts, but the need is only for 100 parts per month for the next six months. Without the Firm Plan command, the MRP module would tell the user to cancel the PO for 600 quantity and re-issue for 6 separate purchases of 100 each. With the Firm Plan command, this tells MRP that the purchasing decision was intentional. (Please refer to the Material Requirements Planning article).
|
First Article |
This box will be checked if set-up in the Inventory Control Management Module. You may uncheck it or check it if user has been instructed that it may be changed for this item only. This information will be carried forward to the PO Receiving screen for reference. |
Serialized |
This box will be checked if set-up in the Inventory Control Management Module and will not be editable within the Purchase Order Management. This indicates to the user that this BUY part has been marked as Serialized and any product coming in or out of the system will require serial number tracking. |
The user may edit or add a percentage amount of extra material that will be allowed to be shipped against the order. By entering a percentage in the OVERAGE field, receiving will be allowed to receive extra parts up to the limit imposed in this field.
The user may also edit or add in purchasing lead time and min/mult order quantities through the Purchase Order Management module.Once the record has been saved this information will then be updated within the Inventory Control Management under the MRP Info screen.
The user may check the box for Inspection Exception and select from the Inspection Exception Pulldown (which is established in the Inspection Exception Setup module). The user will then also be allowed to enter any Inspection Exception Notes and/or Load Insp Excep doc that pertain to that PO line item. This information will then be displayed within the PO Receiving as reference information to the users that are processing the Receipts through the system.
The user is then prompted for the purchase order quantity of parts to be ordered. The user may enter either the Purchase Quantity or the Stocking Quantity, and ManEx will complete the other field based on the purchase/stocking unit of measure and conversion field.
NOTE: When creating a PO for an item with different purchasing and stocking UoMs, be sure to enter the MRP suggestion into the Stocking qty field rather than the purchasing qty field. The system will automatically convert the stocking unit into the purchasing unit for the purchase order qty.
For example if the buyer is creating a PO for an item that is used by inches but sold by the foot, the user would enter qty of 24 into the stocking qty field and the PO would automatically convert it to 2 feet in the purchasing qty field. So the supplier deals in feet, but ManEx deals in inches. The conversion between the two are established in the Unit of Measure & Conversion module.
Then the unit price is entered (Price Each). The extended amount is shown, calculated by extending the quantity by price. (If the inventory part that you are creating a line item for currently has a standard cost of 0.00 within inventory control the system will prompt the user if you wish to take that Purchase Order Price entered and use it as the standard cost for that item within inventory control). This can not be controlled by the Security level due to the fact that it is better practice to have a $$ assigned to the ICM record before the Purchase Order Receipt is accepted into the system. Otherwise you will have stock that is not valued properly, accounting records that will not be correct, etc. . . . So this is why ManEx allows any Purchase Order user to populate the STD cost field for that record with the purchase $ that you are loading. BUT . . Once a Std Cost is associated with the ICM record - the users within Purchase Order Management should no longer be able to change that value through the PO module.
The user may then indicate that the items are taxable by clicking on the Taxable check box.
The Stock/BOM field will update automatically based upon the conversion table defined in setup. The completed screen should appear as follows:

Before saving the order you will need to check the expand box and enter the Schedule detail information.
There are situations when the users will either not enter a schedule or enter a partial schedule at time of creating PO. If the scheduled qty does not match the order qty or the "Allow Partial Schedule" box is unchecked, upon depressing the Save button the following message will be displayed. This gives the user the option to stop the save process and return to the item and schedule or continue on and save without scheduling. Some users may not know an exact date for scheduling at the time of the PO creation and just create the PO to get the part on order. Then upon the supplier response add the scheduled dates to the PO at a later time. This is why we do not enforce the scheduling at the time of the PO creation.
If the "Allow Partial Schedule" box is checked upon saving the PO without a schedule or a partial schedule this message will not be displayed.
Entering Schedule Detail Information
The item will schedule automatically by adding the lead time to todays date and schedule the entire order amount. (Note: MRP will NOT acknowledge qty's that are not scheduled).
At this time the user has the option to change the Schd date/Req date/commit date information and also the Qty Schd.
Note: If user is not following MRP suggestions when creating POs they need to keep in mind inspection time when entering a schedule for a PO.
If the user wants to modify the automatic scheduled date, they can either manually adjust the Date information by highlighting the field and typing in the new date, or place the cursor in the Due Date field.Type in a ?. A calendar will appear.
Depress the desired delivery date.To advance into the next month, depress the > button.
|
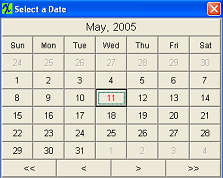 |
Schedule Field Definitions
Schd Date |
The date the material is due to land on the users dock. This is the date MRP uses. |
Req Date |
This is the internally required or desired date. It is not used for the supplier or MRP. |
Commit Date |
The commit date is a reference field for the buyer. |
Qty Schd |
The quantity scheduled for the due date. |
Warehouse |
The User can choose the Warehouse from the pulldown or leave it blank. The Y next to the Warehouse location indicates that, that Warehouse is set-up in the AVL. The N next to the Warehouse location indicates that, that Warehouse is not set-up in the AVL. If the warehouse field is left blank then the warehouse can then be assigned at PO Receiving Management. Once the record has been saved within the PO Receiving this information will then be updated within the Inventory Control Management under the Qty info screen. |
Location |
The Location field will update automatically from the Inventory Control Management module. The user can edit this field in the scheduling detail. This will not change the location in the Inventory Control Management module under the quantity info screen. |
Distribute To |
This is classification of the distribution of the item when received, either to regular Inventory Receiving or to Allocate to Special Work Order or Project |
GL Number |
The General Ledger number where the purchase order will post. |
Schd Notes |
Depressing on the button will bring up a screen where the user can enter in specific notes that pertain to that one schedule, item, and date. Type in the note. Depress the Save button. Exit |
Pressing the Save button at the top of the screen saves the order and item(s) entered, and assigns a temporary number to the order. After adding items to the purchase order and saving them, the Purchase Order will display all items added to the order.
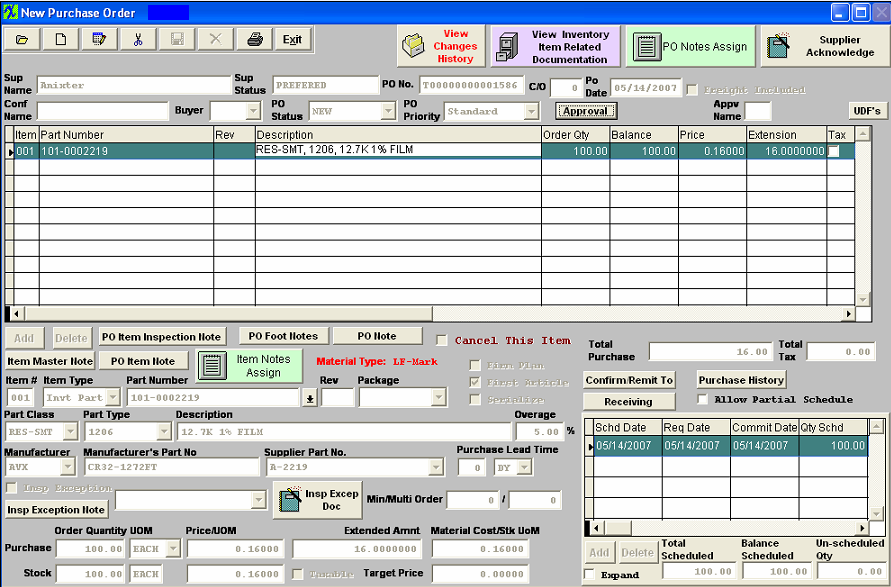
The user may use the scroll bars at the right and bottom of the items listed to scroll over additional information.
The user may modify the column widths in the current view by placing the cursor on the right border of the column in the column header, and pressing the left mouse button. Moving the border while holding the mouse button then releasing at the new location resizes the columns.
|
1.2.1.1. Allocate to Special Work Order or Project | Introduction
Inventory Allocation is used to allocate (reserve) quantities of existing items in stock or future Purchase Order deliveries to a Work Order or Project Number.This allocation prevents issuing the quantity reserved to any other use except the Work Order or Project Number specified. Purchase Order Line Item allocations may be removed prior to receipt of the parts by editing the Purchase Order.After receipt of parts allocated by Purchase Order, the allocation may only be removed after the parts are in stock, by using the Inventory Allocation module.
ALLOCATION OF PURCHASE ORDER DELIVERIES
Allocating a PO Line Item is used to make sure that the item will be reserved for a particular Work Order or Project Number when it is received.PO line item allocation is generally used when allocating to a Work Order or Project Number for which the items are not available in stock.Line Shortages of items not on the BOM, which are not in stock, are an example of typical PO Line Item Allocations.To allocate Purchase Order Line Item Deliveries to a Work Order or Project Number:
- A Work Order or Project Number must be open for the product.
- The Item to be allocated must be entered in the Inventory Control Item Master.
- The quantity allocated must equal the quantity ordered. ie. The total quantity ordered on a line item may be allocated to multiple Work Orders or Project Numbers through the schedule screen.
PROCEDURES
To Allocate a PO Line Item to a Work Order or Project Number:
- Allocate to a new or existing PO.
- Select the desired PO in Article #153.
- Highlight the line item you want to allocate.
- (If it is an existing PO) Depress the Edit action button.
- Expand the Schedule Screen, tab or click on the "Distribute to" field.
- Select WO Alloc or Prj Alloc, enter the Work Order number or Project number to allocate to in the WO # field or Project # field.
- Follow normal PO Mgmt procedures to save and approve.
NOTE:The user may wish to allocate a line item to multiple Work Orders and/or Project Numbers. In the schedule for an item, the user can create as many schedule lines as required. Each schedule line can have a different allocation. If the user had a requirement for 5 Work Orders and/or Project Numbers of 100 parts for each Work Order and/or Project Number, the user would add a line to the PO for 500 parts, then in the schedule, the user can add a line for each Work Order and/or ProjectNumber to which the parts are allocated. The schedule dates can be the same or different. The supplier will see only the total quantity required by the schedule date and is not bothered with the individual allocations.
To Un-allocate a PO Line Item that has not yet been Dock Received:
- Select the desired PO in Article #153.
- Highlight the line item you want to un-allocate.
- Depress the Edit action button.
- Expand the Schedule Screen, tab or click on the "Distribute to" field.
- Select Inv Recv.
- Follow normal PO Mgmt procedures to save and approve.
To Un-allocate a PO Line Item that has already been Dock Received:
-
-
|
1.2.2. MRO Items | MRO stands for Maintenance, Repair and Operations. Generally this is used for supplies, etc. purchases.
After selecting the Item Type to be "MRO"
If the MRO item is included in inventory
a. The user may jump directly to the part number box (click on it) and enter a part number. Or, the user may step through the Part Classes and Part Types to narrow
the focus and then select a part from the desired part type.
b. Fill in the quantity and unit price.
If the MRO item is NOT included in inventory
a. The user may enter in the Suppliers part number manually (or leave blank) and then jump to the description field and enter the description.
The finished screen should look like the screen displayed:
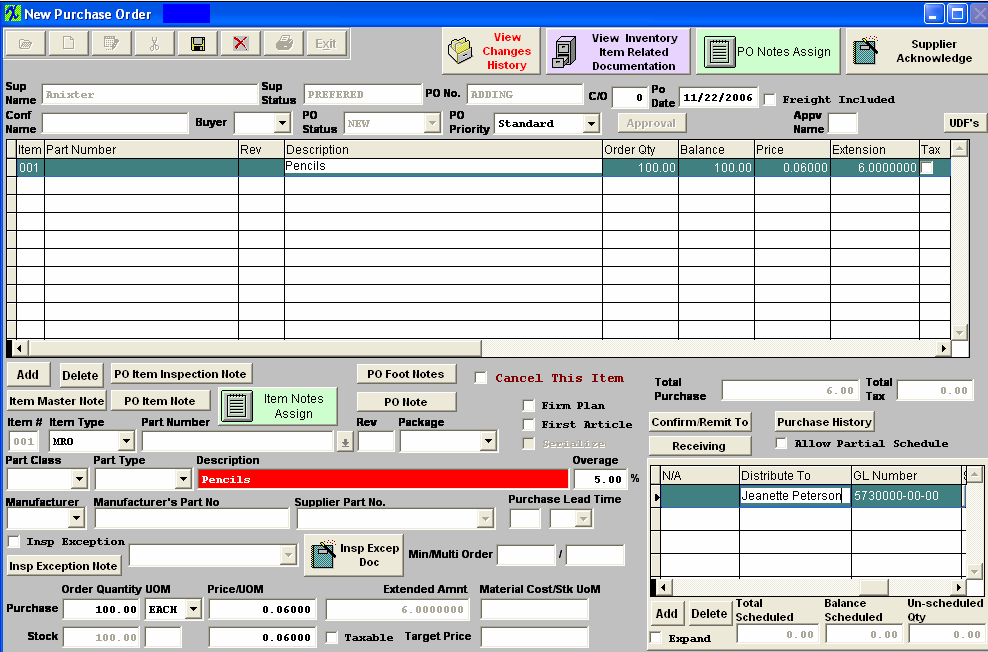
- Check the Expand box in the Schedule screen.
- Enter schedule dates and quantity scheduled.
- Type in the title or name of the person requesting the item in the “Distribute To” field.
- Enter a General Ledger account number in the GL Number field.
The completed Schedule screen will appear as follows:
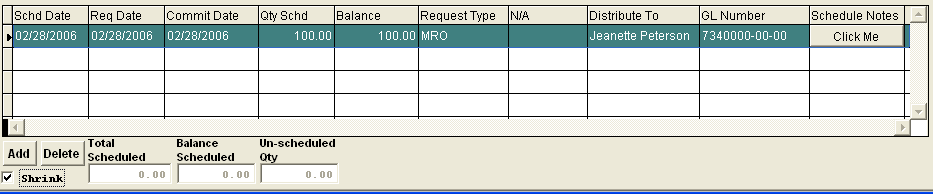
- At the conclusion of entry for the item, the user may depress the Save record action button or the Abandon record action button.
- Approve record.
|
1.2.3. Service Items | Service items are for those instances where the assembly is outsourced.
After selecting the Item Type to be "Service"
- The user may enter the supplier Part number manually (or leave blank) and then go to the description field and enter the description.
- Fill in the quantity and unit price.
The finished screen should look like the screen displayed:
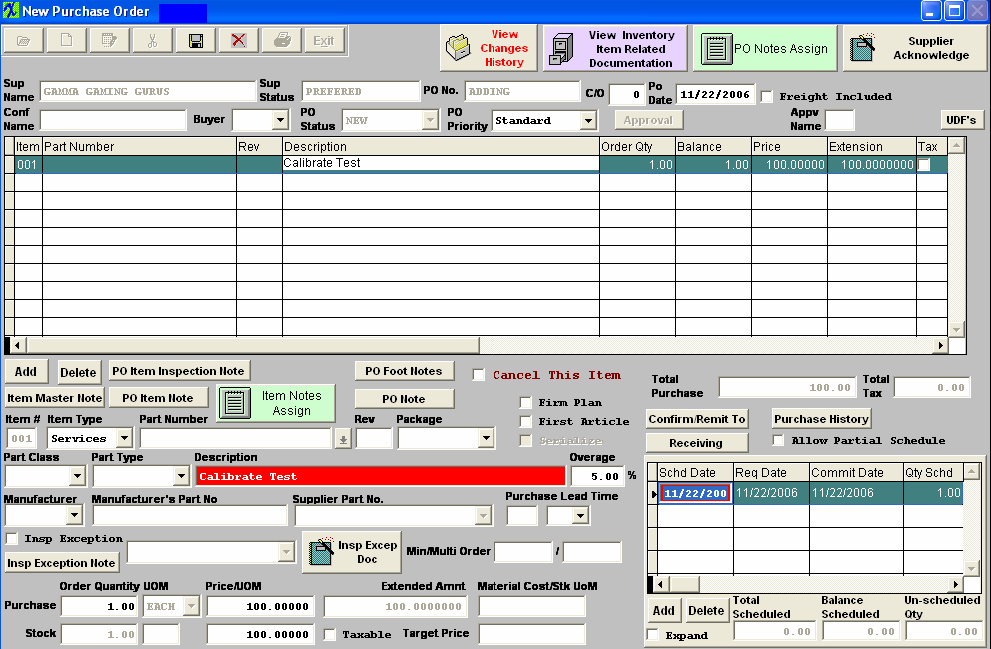
- Check the Expand box in the Schedule screen.
- Enter schedule dates and quantity scheduled.
- Type in the title or name of the person requesting the item in the “Distribute To” field.
- Enter a General Ledger account number in the GL Number field.
The completed Schedule screen will appear as follows:
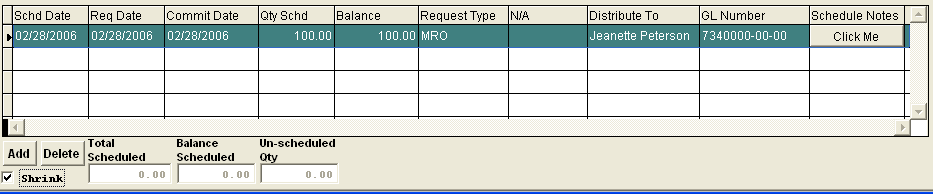
- At the conclusion of entry for the item, the user may depress the Save record action button or the Abandon changes action button.
- Approve record. Please note upon approval the service item is marked as received and balance updated to 0.
|
1.3. Edit, Cancel, or Close a Purchase Order | Find the Purchase Order that you would like to edit.
Pressing the Edit record action button in the Purchase Order screen will allow the user to modify all the following information:
- The Confirmation Name, Buyer, PO Priority, Supplier Ack., check or uncheck Freight Included box.
- The Status field will only be enabled in the edit mode for users with approval rights. User MUST have approval rights to Modify the PO Status.
- Order quantity and unit price, min/multi qty, purchase lead time, overage amount, Firm Plan or First Article.
- Add or Deletion of a Line Item
- By depressing the Add button allows the user to add additional items to the PO.
- By depressing the Delete button you can delete an existing line Item from the PO.
- Highlight the line item that you wish to delete, then depress the Delete button .
- The user will be asked to validate the deletion before proceeding.
- If you select OK the item will be deleted from the order.
- Information about the terms, FOB, Ship Via, Ship Charge, and Account number, Ship Charge Amount, whether taxable, the tax %
- Schd Date, Requested Date, Commit Date, Quantity Scheduled, Warehouse, Location, Distribute To and Schd Notes.
- Modify or add any information in the Item Master Notes, PO Item Notes, PO Notes, and PO Foot Notes. (Depending on how the user has Purchase Setup module marked depends on whether user can edit the notes without going into edit mode on the PO record. If the "Require approvals for Date changes and Notes" is marked as "Yes" then it will force the users to first put the PO in edit mode before they will be allowed to edit any notes and the note changes will be recorded in the "View Changes History" screen. But if it is marked "No" then the notes become editable without the actual record in Edit mode and the note changes will NOT be recorded in the "View Changes History" screen).
Depress the Save record action button after you have finished with editing the record. The user will then need to approve the order. If user has the "Auto Assign new Change Order # Upon Approval" box checked within the Purchase Setup module, the reminder will NOT be issued and CO# field becomes NOT editable. When the user approves the change the Change Order number will be automatically increased. If user has the "Auto Assign New Change Order # Upon Approval" box unchecked within the Purchase Setup module when user makes changes the CO# will stay the same, the system will prompt the reminder, and user may manually assign a change order number if applicable.

There are situations when an item may not have a schedule or may have a partial schedule. If the "Allow Partial Schedule" box is checked within the Purchase Setup module, the system will NOT ask any questions when saving a po with only partial schedule. (Note: MRP will NOT acknowledge qty's that are not scheduled). If the " Allow Partial Schedule" box is unchecked within the Purchase Setup module , user will receive the following popup warning when editing and saving that line item or any other line item on that same purchase order:
NOTE: If the "Auto Assign new Change Order # Upon Approval" box is checked, and PO is new and the user goes into the "Edit" mode prior to approval, no changes will be made to the CO# on screen or in the "View Changes History" screen. If PO has been approved and the user goes into the "Edit" mode the next CO# will be referenced in the "View Changes History" screen but will NOT increase on screen until PO has been approved. If the user goes to the "Edit" mode more than once before approving the change the CO# will only increase once in the "View Changes History" screen.
NOTE: If users enter a PO number manually using a "T", then changes the numbering to Auto, and later edits and approves this PO the "T" will be changed to "0". The system has no way of knowing that the PO was manual numbered before the change.
If multiple users are editing the same PO and the PO has not been approved yet, so it still has a temp # and the 1st users approves the PO, while the 2nd user is still making their changes, when the 2nd user goes to exit and save their changes they will receive the following message:
Manex tracks all revisions of a Purchase Order and each receipt against each revision of the order. The system will NOT allow any changes to a Purchase Order which has parts in Dock Receiving that have not yet been processed in the Purchase Order Receiving & Inspection module.
Cancel a Purchase Order
Find the Purchase Order you want to cancel. Press the Edit record action button in the Purchase Order screen this will allow the user to change the PO status from Open to Cancel. Note: User MUST have approval rights to Modify the PO Status.
Each line item will need to be deleted using the instructions above. Once all line items have been deleted from the PO. The status on the PO will show cancel.
Closing out a Purchase Order
At times, the user may wish to close out a PO to suppliers who have either shipped short or overages of ordered components. For example, say a user has a Purchase Order for 100 components. 100 units are received with 5 rejections. (See the DMR procedures). This would show the Purchase Order showing a quantity of 5 for a balance. What if the user informs the supplier that they do not want the last 5 pieces.
In the above set of circumstances, the user will be allowed to change the ORIGINAL order quantity by removing the rejected quantity via the DMR procedure. When the Received quantity PLUS the DMR quantity is LESS than the order quantity, the user will be allowed to decrease the order quantity by that many. Original Order 100; Received quantity 100; Rejected quantity 5. Returned to supplier via DMR 5. At this point, the user may reduce the quantity ordered, AND the accompanying amount scheduled to 95. This action will close out the Purchase Order.
The user must depress the Edit button. Change the Purchase Order Quantity, then change the Quantity Scheduled so that the total of the schedule dates exactly equals the new quantity. Depress the Save button. Approve the PO and the PO status will change to close.
|
1.4. E-mail Purchase Order(s) | To e-mail a Purchase Order report(s), depress the Reports button.
Note: You MUST have the e-mail setup within the Trigger.exe setup and working before the PO e-mail will work.
The reports screen will appear:
Select the output XL File, TXT File, or PDF by clicking on the radial.
Check the Email box located int he left hand corner of the Reports Tab.
Highlight the report you want to Email.
Depress the option tab.
|
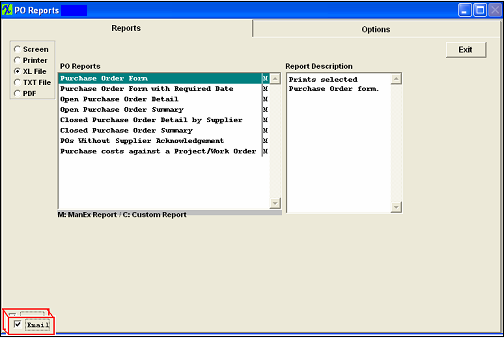 |
Complete the Option tab with the information required: Note: User has the option to check the Email box on the Options screen also.
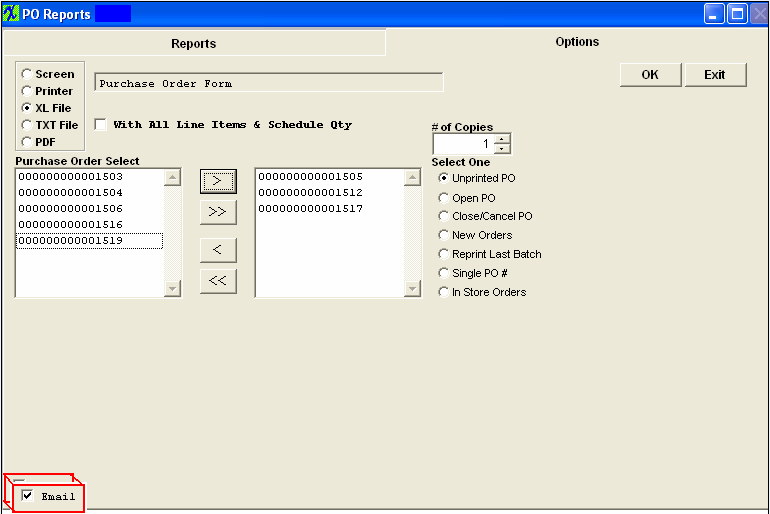
Depress OK. The following screen will appear. Select or Enter File Name.
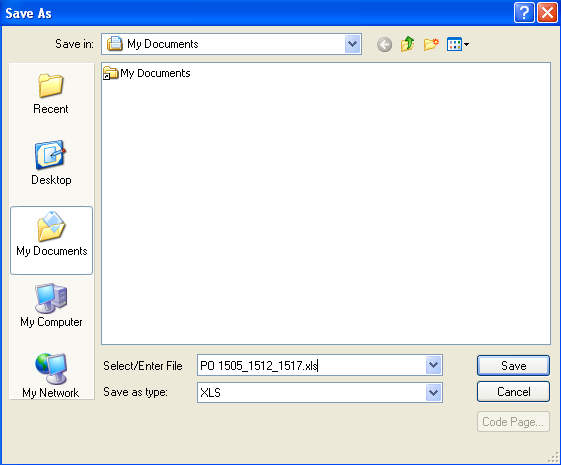
Depress Save, the following Check Email Addresses screen will appear. Within this screen you can enter an e-mail address or add any special notes needed:
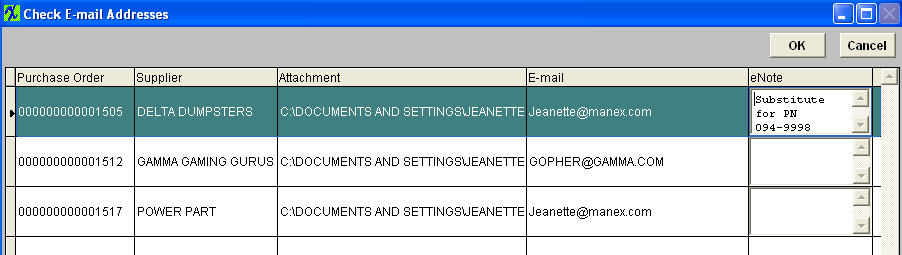
Depress OK and documents will be sent to e-mail addresses assigned.
The following is what the receiver will receive:
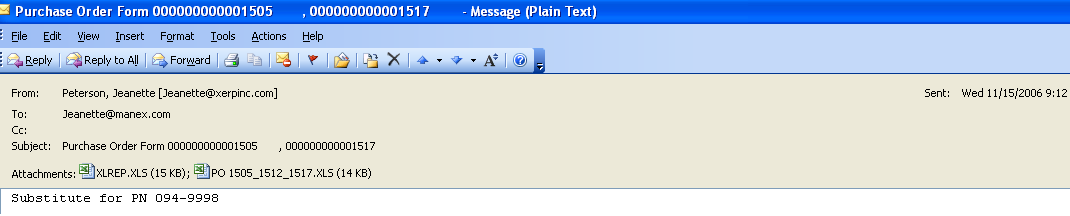
|
1.5. Approve a Purchase Order |
Material Planning/Purchase Order Management/Purchase Order Management
|
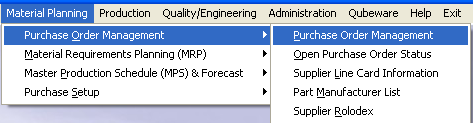 |
The following screen will appear:
Depress the Find record button and follow the Find a PO procedures to find a PO for Approval.
Approve PO
Pressing the Approval button in the Purchase Order module will ask for the user’s password. The user must enter a password that has been authorized (within the Purchase Setup module) to approve the dollar amount of the order.
Entry of an un-authorized password will receive the following message:
|
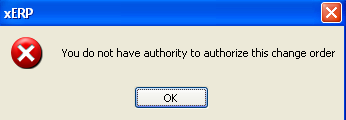 |
Entry of an authorized password and approval will inactivate the 1st approval button and place the initials of the person approving the order next to the approval button , (If in the Purchase Setup , the company has selected to allow one approval of purchase orders). Then upon approval the temporary Purchase Order number will be replaced with a permanent PO number (replacing the "T" with a "0").
If in the Purchase Setup , the company has selected requiring two approvals, then the process must be repeated for the second approval, and the temporary Purchase Order number will be replaced with a permanent PO number (replacing the "T" with a "0") once both approval are granted.
Note: That if the Purchase Order is an Service or In-store order, once the PO has received it’s final approval the temporary Purchase Order number will be replaced with a permanent PO number (replacing the "T" with a "0") and the PO Status marked as closed.
If the user has elected to use manual purchase order number,the screen will prompt the user for an order number to be applied to the purchase order. Note: If users enter a PO number manually using a "T", then changes the numbering to Auto, and later edits and approves this PO the "T" will be changed to "0". The system has no way of knowing that the PO was manual numbered before the change.
|
1.5.1. Inventory Part | Selecting Inventory Parts as the item type, the user may jump directly to the part number box (click on it) and enter a part number. Or, the user may step through the Part Classes and Part Types to narrow the focus and then select a part from the desired part type. Once a part number from Inventory has been entered, Manex completes the boxes associated with the item master.
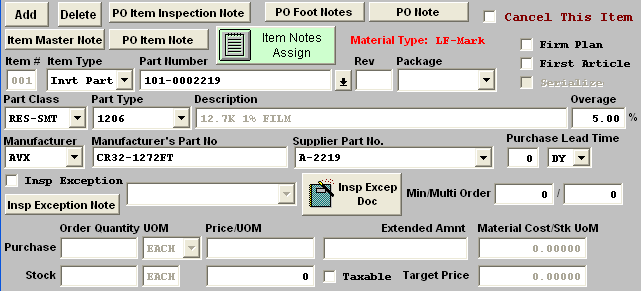
If more than one manufacturer exists for the part, the user may click on the down-arrow next to the manufacturer edit box and select the appropriate manufacturer for the order. The Material type will be displayed in the pulldown next to the Mfg. and Mfgr. PN. |
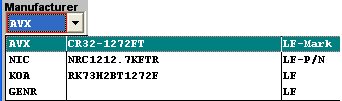 |
If more than one supplier part number exists for the part, the user may click on the down-arrow next to the supplier part no. edit box and select the appropriate supplier part no. for the order.
The system will look for the preferred supplier part number and if found will show it as a display. At this time the user can leave the part number as is or select a different one if available. After a user will save the PO, the supplier part number will be saved and next time you will see the selected suppler part number when viewing the same PO.
No history will be saved because this field is for the information only.
|
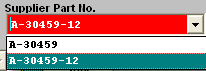 |
Firm Plan |
If this box is checked, the MRP module will not try to override the purchasing decision. Lets take a test case. The user makes a decision to block order 600 parts, but the need is only for 100 parts per month for the next six months. Without any Firm Plan command, the MRP module would instruct the user to cancel the PO for 600 quantity and re-issue for 6 separate purchases of 100 each. Firm Plan tells MRP that the purchasing decision was intentional and no action is required. (For further detail see Article #1080 ).
|
First Article |
This box will be checked if set-up in the Inventory Control Management Module. You may uncheck it or check it if user has been instructed that it may be changed for this item only. This information will be carried forward to the PO Receiving screen for reference. |
Serialized |
This box will be checked if set-up in the Inventory Control Management Module and will not be editable within the Purchase Order Management . This indicates to the user that this BUY part has been marked as Serialized and any product coming in or out of the system will require serial number tracking. |
The user may edit or add a percentage amount of extra material that will be allowed to be shipped against the order. By entering a percentage in the OVERAGE field, receiving will be allowed to receive extra parts up to the limit imposed in this field.
The user may also edit or add in purchasing lead time and min/mult order quantities through the Purchase Order Management module.Once the record has been saved this information will then be updated within the Inventory Control Management under the MRP Info screen.
The user may check the box for Inspection Exception and select from the Inspection Exception Pulldown (which is established in the Inspection Exception Setup module).The user will then also be allowed to enter any Inspection Exception Notes and/or Load Insp Excep doc that pertain to that PO line item.This information will then be displayed within the PO Receiving as reference information to the users that are processing the Receipts through the system.
The user is then prompted for the purchase order quantity of parts to be ordered. The user may enter either the Purchase Quantity or the Stocking quantity, and Manex will complete the other field based on the purchase/stocking unit of measure and conversion field.
Then the unit price is entered (Price Each). The extended amount is shown, calculated by extending the quantity by price. (If the inventory part that you are creating a line item for currently has a standard cost of 0.00 within inventory control the system will prompt the user if you wish to take that Purchase Order Price entered and use it as the standard cost for that item within inventory control). This can not be controlled by the Security level due to the fact that it is better practice to have a $$ assigned to the ICM record before the Purchase Order Receipt is accepted into the system. Otherwise you will have stock that is not valued properly, accounting records that will not be correct, etc. . . . So this is why ManEx allows any Purchase Order user to populate the STD cost field for that record with the purchase $ that you are loading. BUT . . Once a Std Cost is associated with the ICM record - the users within Purchase Order Management should no longer be able to change that value through the PO module.
The user may then indicate that the items are taxable by clicking on the Taxable check box.
The Stock/BOM field will update automatically based upon the conversion table defined in setup. The completed screen should appear as follows:

Before saving the order you will need to check the expand box and enter the Schedule detail information.
Entering Schedule Detail Information
The item will schedule automatically by adding the lead time to todays date and schedule the entire order amount.

At this time the user has the option to change the Schd date/Req date/commit date information and also the Qty Schd.
Note: If user is not following MRP suggestions when creating POs they need to keep in mind inspection time when entering a schedule for a PO.
If the user wants to modify the automatic scheduled date, they can either manually adjust the Date information by highlighting the field and typing in the new date, or place the cursor in the Due Date field.Type in a ?. A calendar will appear.
Depress the desired delivery date.To advance into the next month, depress the > button.
|
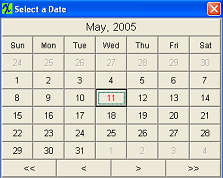 |
Schedule Field Definitions
Schd Date |
The date the material is due to land on the users dock |
Req Date |
This is the internally required or desired date.It is not used for the supplier |
Commit Date |
The commit date is a reference field for the buyer |
Qty Schd |
The quantity scheduled for the due date |
Warehouse |
The User can choose the Warehouse from the pulldown or leave it blank. The Y next to the Warehouse location indicates that, that Warehouse is set-up in the AVL. The N next to the Warehouse location indicates that, that Warehouse is not set-up in the AVL. If the warehouse field is left blank then the warehouse can then be assigned at PO Receiving Management. Once the record has been saved within the PO Receiving this information will then be updated within the Inventory Control Management under the Qty info screen. |
Location |
The Location field will update automatically from the Inventory Control Management module. The user can edit this field in the scheduling detail. This will not change the location in the Inventory Control Management module under the quantity info screen. |
Distribute To |
This is classification of the distribution of the item when received, either to regular Inventory Receiving or to Allocate to Special Work Order or Project |
GL Number |
The General Ledger number where the purchase order will post |
Schd Notes |
Depressing on the button will bring up a screen where the user can enter in specific notes that pertain to that one schedule, item, and date. Type in the note. Depress the Save button. Exit |
Pressing the Save button at the top of the screen saves the order and item(s) entered, and assigns a temporary number to the order. After adding items to the purchase order and saving them, the Purchase Order will display all items added to the order.
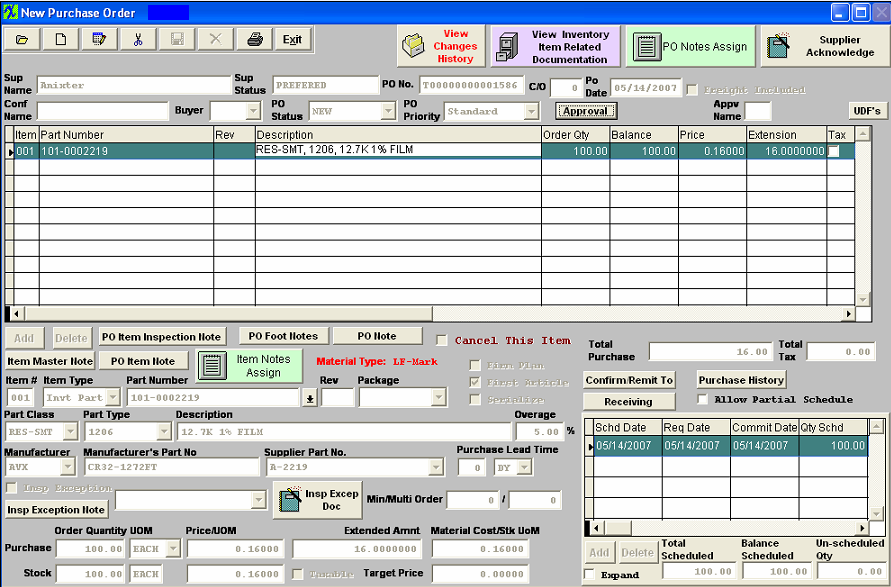
The user may use the scroll bars at the right and bottom of the items listed to scroll over additional information.
The user may modify the column widths in the current view by placing the cursor on the right border of the column in the column header, and pressing the left mouse button. Moving the border while holding the mouse button then releasing at the new location resizes the columns.
|
1.5.1.1. Allocate to Special Work Order or Project | Introduction
Inventory Allocation is used to allocate (reserve) quantities of existing items in stock or future Purchase Order deliveries to a Work Order or Project Number.This allocation prevents issuing the quantity reserved to any other use except the Work Order or Project Number specified. Purchase Order Line Item allocations may be removed prior to receipt of the parts by editing the Purchase Order.After receipt of parts allocated by Purchase Order, the allocation may only be removed after the parts are in stock, by using the Inventory Allocation module.
ALLOCATION OF PURCHASE ORDER DELIVERIES
Allocating a PO Line Item is used to make sure that the item will be reserved for a particular Work Order or Project Number when it is received.PO line item allocation is generally used when allocating to a Work Order or Project Number for which the items are not available in stock.Line Shortages of items not on the BOM, which are not in stock, are an example of typical PO Line Item Allocations.To allocate Purchase Order Line Item Deliveries to a Work Order or Project Number:
- A Work Order or Project Number must be open for the product.
- The Item to be allocated must be entered in the Inventory Control Item Master.
- The quantity allocated must equal the quantity ordered. ie. The total quantity ordered on a line item may be allocated to multiple Work Orders or Project Numbers through the schedule screen.
PROCEDURES
To Allocate a PO Line Item to a Work Order or Project Number:
- Allocate to a new or existing PO.
- Select the desired PO in Article #153.
- Highlight the line item you want to allocate.
- (If it is an existing PO) Depress the Edit action button.
- Expand the Schedule Screen, tab or click on the "Distribute to" field.
- Select WO Alloc or Prj Alloc, enter the Work Order number or Project number to allocate to in the WO # field or Project # field.
- Follow normal PO Mgmt procedures to save and approve.
NOTE:The user may wish to allocate a line item to multiple Work Orders and/or Project Numbers. In the schedule for an item, the user can create as many schedule lines as required. Each schedule line can have a different allocation. If the user had a requirement for 5 Work Orders and/or Project Numbers of 100 parts for each Work Order and/or Project Number, the user would add a line to the PO for 500 parts, then in the schedule, the user can add a line for each Work Order and/or ProjectNumber to which the parts are allocated. The schedule dates can be the same or different. The supplier will see only the total quantity required by the schedule date and is not bothered with the individual allocations.
To Un-allocate a PO Line Item that has not yet been Dock Received:
- Select the desired PO in Article #153.
- Highlight the line item you want to un-allocate.
- Depress the Edit action button.
- Expand the Schedule Screen, tab or click on the "Distribute to" field.
- Select Inv Recv.
- Follow normal PO Mgmt procedures to save and approve.
To Un-allocate a PO Line Item that has already been Dock Received:
-
-
|
1.5.2. MRO Items | MRO stands for Management Required Options. Generally this is used for supplies, etc. purchases.
After selecting the Item Type to be "MRO"
- If the MRO item is included in inventory
- The user may jump directly to the part number box (click on it) and enter a part number. Or, the user may step through the Part Classes and Part Types to narrow the focus and then select a part from the desired part type.
- Fill in the quantity and unit price.
- If the part is not in inventoryThe user may enter in the Suppliers part number manually (or leave blank) and then jump to the description field and enter the description.
The finished screen should look like the screen displayed:
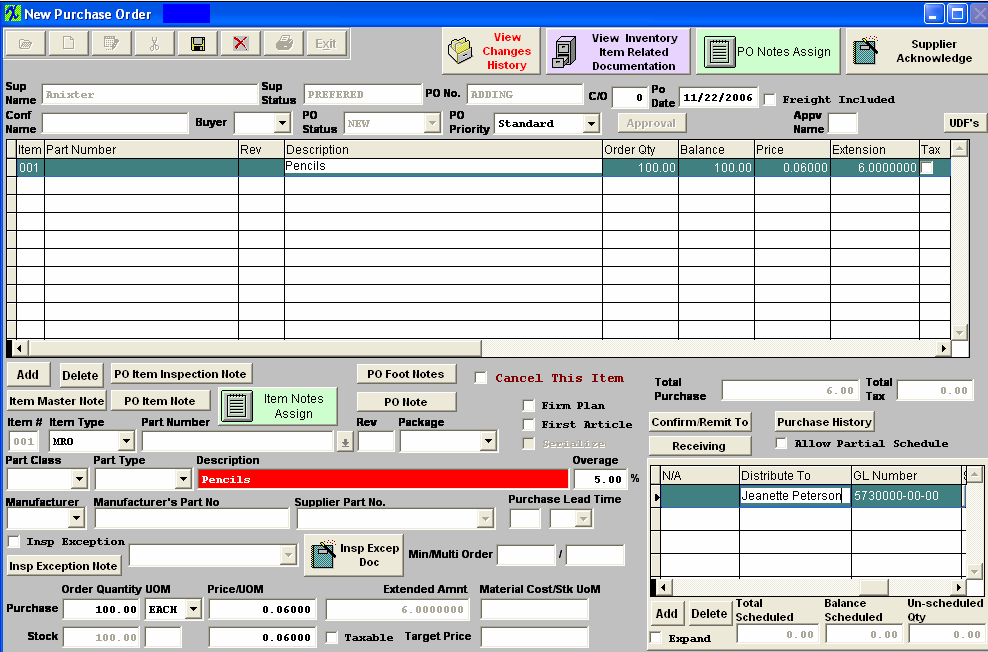
- Check the Expand box in the Schedule screen.
- Enter schedule dates and quantity scheduled.
- Type in the title or name of the person requesting the item in the “Distribute To” field.
- Enter a General Ledger account number in the GL Number field.
The completed Schedule screen will appear as follows:
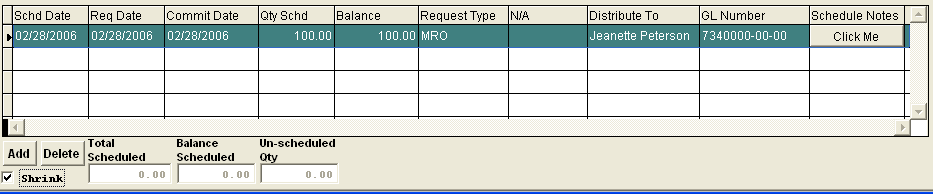
- At the conclusion of entry for the item, the user may depress the Save record action button or the Abandon record action button.
- To complete see Add a PO .
|
1.5.3. Service Items | Services items are for those instances where the assembly is outsourced.
After selecting the Item Type to be "Service"
- The user may enter the supplier Part number manually (or leave blank) and then go to the description field and enter the description.
- Fill in the quantity and unit price.
The finished screen should look like the screen displayed:
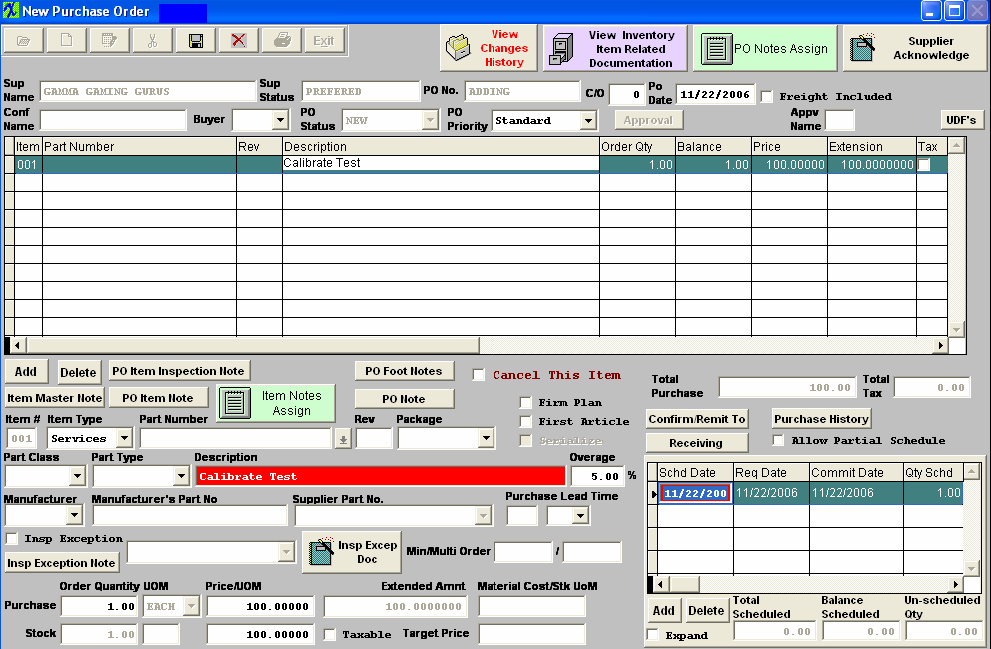
- Check the Expand box in the Schedule screen.
- Enter schedule dates and quantity scheduled.
- Type in the title or name of the person requesting the item in the “Distribute To” field.
- Enter a General Ledger account number in the GL Number field.
The completed Schedule screen will appear as follows:
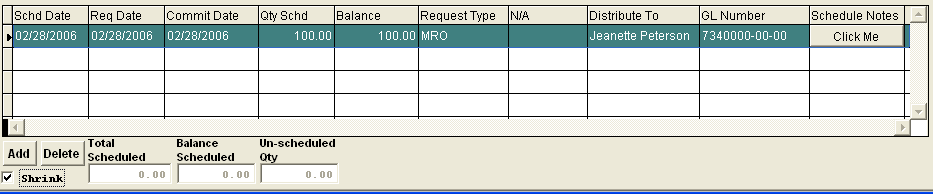
- At the conclusion of entry for the item, the user may depress the Save record action button or the Abandon changes action button.
- Approve record.
|
1.6. Load Supplier Acknowledgement |
How to attach or load a Supplier Acknowledge document to a PO. Note: User is only allowed to load one document per Purchase order.
Depress the "Supplier Acknowledge" button and the following screen will appear:
To load images or documents, depress the "Load Document" button, up in the right hand corner of the screen. A browser screen will appear similar to the one below:
Find and highlight the desired Image file, as illustrated.
Once the file name appears, depress the Ok button.
Note: that the user can also load other document types by changing the File of Type to ALL
The file will appear in the screen as displayed:
Depress the Save action button to save the changes or depress the Abandon changes action button to abandon changes. Exit will bring the user back to the Purchase Order Management module. If user selected to Save the Supplier Acknowledge button will be displayed in Red as shown below.
|
1.7. Copy "View Change History" Notes | Find the Purchase Order you want to Copy the "View Changes History" notes on.
Depress the "View Changes History" button, When in the “Change PO history” screen, click on the vertical scroll (on your keyboard), you will see the cursor appeared on the top inside the window with the text.
Depress the "CTRL" button + the vertical scroll buttons to highlight the information you wish to copy;
Depress the "CTRL + C" to copy, then paste to a document, e-mail, etc....
|
|