1. Master Production Schedule (MPS) & Forecast (OPTIONAL Module) |
1.1. Master Production Schedule |
1.1.1. Prerequisites for MPS & Forecast | Prerequisites Required for Entering a New Master Production Schedule:
ManEx’s standard module configuration allows most users to accomplish their daily tasks. For those users wanting to get more from ManEx by leveraging the total solutions, this is one of the optional modules available for purchase. The forecast module is designed to be the controlling factor for a product when it is used. To place an order or to learn more about this specific module or any of the other optional modules please contact us at http://manex.com\contactus.aspx
After activation, "Master Production Schedule" access for each user must be setup in the ManEx System Security module. Users with “Supervisor Rights” will automatically have access.
Part number |
The part number must exist for a product or part in the Item Master.
|
AVL |
The Manufacturer Names must exist when using the AVL in the Bill Of Materials. |
MRP Policies |
The Material Requirements Planning policies should exist for each product or part in Inventory Control. |
|
1.1.2. Introduction for MPS & Forecast | ManEx’s standard module configuration allows most users to accomplish their daily tasks. For those users wanting to get more from ManEx by leveraging the total solutions, this is one of the optional modules available for purchase. The forecast module is designed to be the controlling factor for a product when it is used. To place an order or to learn more about this specific module or any of the other optional modules please contact us at http://manex.com\contactus.aspx
|
1.1.3. Fields & Definitions for MPS & Forecast |
1.1.3.1. Forecast | 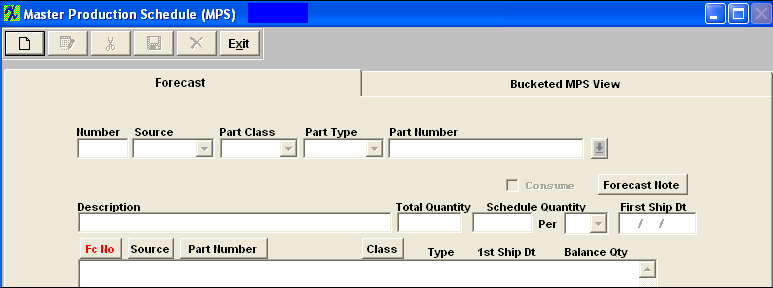
Master Production Schedule Forecast tab Field Definitions:
Header Portion of Screen
Number |
The number assigned to the forecast. |
Source |
Whether the forecast involves a Make or Buy Part. |
Part Class |
The classification of the Part. |
Part Type |
The Type assigned to the part number. |
Part Number |
The unique number assigned to the part. |
Consume |
The box is checked if the user expected to ship eventually under a Sales Order. |
 |
Depress this button to enter any special notes that pertain to the forecast. |
Description |
The description of the part. |
Total Quantity |
The total quantity of the Forecast. |
Schedule Quantity |
The portion of the total quantity scheduled and the frequency of the schedule. |
First Ship Date |
The Date the schedule quantity displayed is expected to ship. |
Body of Screen
Forecast Number |
The number assigned to the forecast for the part listed. |
Source |
Whether the forecast involves a Make or Buy Part. |
Part Number |
The unique number assigned to the part. |
(Rev) |
The revision character assigned to the part Number, if such exists. |
Part Class |
The classification of the Part. |
Part Type |
The Type assigned to the part number. |
First Ship Date |
The Date the schedule quantity displayed is expected to ship. |
Balance Quantity |
The unshipped quantity amount. |
|
1.1.3.2. Bucketed MPS View | 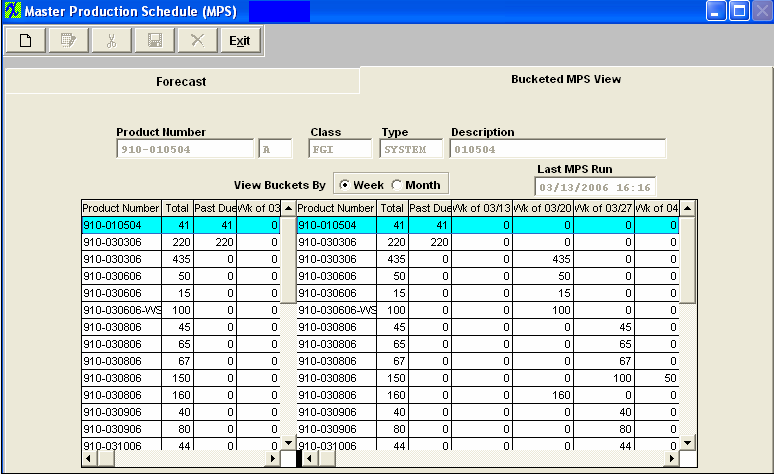
Bucketed Master Production Schedule tab Field Definitions:
Top of Screen:
Product Number |
The unique number assigned to the product. |
(Rev) |
The revision character assigned to the Product Number, if any. |
Class |
The classification of the Product. |
Type |
The Type to which the highlighted Product Number is assigned. |
Description |
The description of the Product Number highlighted. |
View Buckets by |
The radial selection dictates how the buckets are viewed, by Week or by Month. |
Last (MPS) Material Requirements Planning Run |
This is the date of the last Material Requirements Planning run. |
Left Side of Screen:
Product Number |
The unique number assigned to the product. |
Total |
The total originally forecasted. |
Week of or Month of |
Displays the quantity of the amount scheduled, by week or by month. |
Out |
This column indicated the quantity scheduled beyond the Weeks or Months displayed. |
Right Side of Screen:
Product Number |
The unique number assigned to the product. |
Total |
The total originally forecasted. |
Week of or Month of |
Displays the quantity of the amount scheduled, by week or by month. |
Out |
This column indicated the quantity scheduled beyond the Weeks or Months displayed. | |
1.1.4. How To ..... for MPS & Forecast |
1.1.4.1. Adding A New Master Production Schedule |
Enter Material Planning/Master Production Schedule (MPS) & Forecast/Master Production Schedule Module |
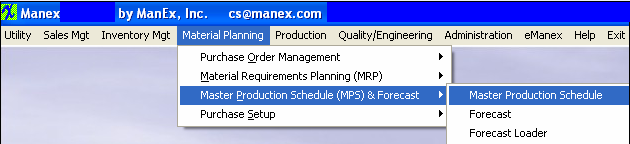 |
The following screen will appear:
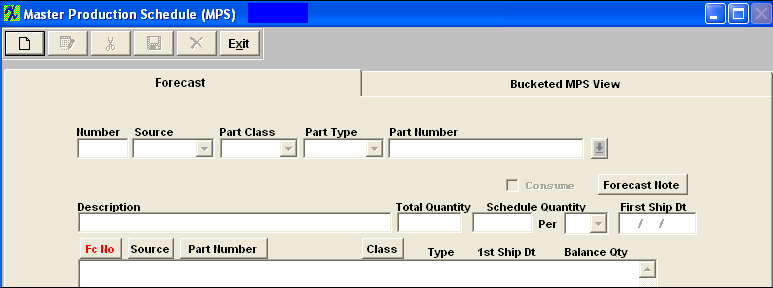
To ADD a new Master Production Schedule, depress the Add action button. Enter your password.
Select the Source from the Drop down menu.
Select the Part Class from the Drop down menu.
Select the Part Type from the Drop down menu.
Select the Part Number from the Drop down menu.
Either type the Part Number into the red box or scroll down until the part number is located.Then, double click to select.
On the main screen, type in the total forecasted quantity for the part.Type in the scheduling parameters.For example, if the forecasted need is 1000 and your plant has the capacity to make 250 units per week, schedule 250 over the next 4 weeks.
Type in the first ship date or type a ? in the First Ship Date box and a calendar will appear on the screen:
Click on the date of interest.To advance into the next month, depress the right hand > button.To advance into the same month next year, depress the right hand >> button.
To go back to last month, depress the left hand < button.To go back a full year, depress the << button.
Click on the date desired.
Check the consume box if the forecast will eventually be replaced by a Sales Order.
If you want to add a Forecast note, depress that button.The following Forecast Item Note screen is available:
Depress the Edit button.Type in the note.Depress the Save button.Exit.
Once you’ve finished the data entry in this screen, depress the Save button |
1.1.4.2. Bucketed Master Production Schedule Tab | Depress the Bucketed Master Production Schedule tab.The following screen will appear:
This screen displays the results of the latest Material Requirements Planning run.
Highlight the Product Number of Interest.
Bucketed Master Production Schedule tab Field Definitions:
Top of Screen:
Product Number |
The unique number assigned to the product.
|
(Rev) |
The revision character assigned to the Product Number, if any. |
Class |
The classification of the Product. |
Type |
The Type to which the highlighted Product Number is assigned. |
Description |
The description of the Product Number highlighted.
|
View Buckets by |
The radial selection dictates how the buckets are viewed, by Week or by Month.
|
Last Material Requirements Planning Run
This is the date of the last Material Requirements Planning run.
Left Side of Screen:
Product Number |
The unique number assigned to the product. |
Total |
The total originally forecasted. |
Right Side of Screen:
Week of or Month of
|
Displays the quantity of the amount scheduled, by week or by month.
|
Out |
This column indicated the quantity scheduled beyond the Weeks or Months displayed.
|
Once a new Material Requirements Planning run is made, this screen will update
|
1.2.1. Prerequisites for Forecast |
ManEx’s standard module configuration allows most users to accomplish their daily tasks. For those users wanting to get more from ManEx by leveraging the total solutions, this is one of the optional modules available for purchase. The forecast module is designed to be the controlling factor for a product when it is used. To place an order or to learn more about this specific module or any of the other optional modules please contact us at http://manex.com"contactus.aspx
After activation, "Master Production Schedule" access for each user must be setup in the ManEx System Security module. Users with “Supervisor Rights” will automatically have access.
|
1.2.2. Introduction for Forecast |
The forecast is designed to be the controlling factor for a product when it is used. There are rules in the Forecast Setup that the user can use to establish the maximum increase or decrease for the product by how far out (how many months) the order is. The Forecast module will reduce the requirement to MRP as a forecast is consumed by ships, but will not increase the requirements to MRP beyond the forecast guidelines. It will, however, provide a warning to users that their Sales Order Demand exceeds the forecast (when there is one, and the item is a forecast item on the Sales Order) and refer to a report generated whenever the forecast is regenerated or run by MRP. It is the users responsibility to either adjust the forecast, or adjust the Sales Order accordingly. If the user really does want the extra product over and above the forecast, they can add a line to the sales order that is NOT a forecasted item, and then both the forecast and the sales order should drive demand.
The Forecast checkbox is defaulted as True within the SO Module whether or not there actually is a forecast. By doing this, we minimize the possibility of the MRP double ordering parts for the SO. If there is no forecast for the product, MRP will look at the SO as normal and create the demands. As soon as a Forecast is created for that product (regardless if Forecast Detail is blank) the system will then consider the Forecast information over the SO schedule for MRP. The users can un-check the Frcst check box within the SO/WO for that item if desired. The user will then receive a warning message that the orders exceed the forecast and to read the report to verify that’s what the user wants. (This is done so that the customer doesn’t try to sneak in last minute upswings that exceed the forecast).
Note: The programmers have confirmed that we do have a bit of a disconnect. The Forecast setup has 24 "Future Periods", and the Forecast Module "Detail" tab is setup for 26 weeks. At the time it was originally designed it was not seen as a need to go out that far within the Forecast module itself. We do recognize that this needs to be addressed by making changes to the Forecast module to add another page to extend the weeks out further.
The 2 principal methods ( Firm Planned WO being the only other) of driving demand in the MRP system are:
- Forecasts
- Sales Orders ( only those flagged as non-consuming )
It is important to draw the distinction between the two kinds of Sales Order items that exist in Manex.
- Forecast-Consuming Sales Orders ( these do not drive demand unless no active forecast exists for the item )
- Non-consuming Sales Orders ( drives demand in addition to the Forecast if it exists )
The default during Sales Order Entry is that the Flag is set to consuming. If the sales order has an active forecast, the Sales Order will not drive demand – shipments against it will reduce Forecast by the same amount. If there is no active forecast, it will behave exactly the same way as a non-consuming SO. If an item is dropped from the Forecast (revision change or otherwise), what do we do with the consuming Sales Order? Should the system prompt if there are Sales Orders with consuming set to “yes”, yet there is no Sales Order.
Forecasts
Forecasts can be loaded for up to 24 weeks for any assembly/rev into the Manex Forecast Module. Forecasts are uploaded from an XL template. Forecast module buckets the loaded demand into weeks.
The calculation of “net demand to MRP” is as follows:
Forecast Qty-shipments ( consuming sales orders only)
In other words as we ship against the Forecast the net demand decreases by that amount.
As Consuming Sales Orders are created they may have schedule ship dates that do not align with the Forecast. For example , customer may provide Sales Orders with quantities that are due on a date before the Forecast due date. Since we are driving material to the Forecast date, this might create a condition where we cannot meet the date. The Forecast module generates a report where you can view the alignment of the Sales Orders to Forecast. This is an important report to review with the customer.
In the event that the total consuming Sales Order qty exceeds the entire forecast ( you can see in the afore mentioned report) you should advise the customer that we will not be driving demand for the excess. They must either amend the forecast or clearly indicate. in the PO ( or through some other dependable means ) that the PO is in addition to the Forecast.
Each new Forecast is compared to the previous to look for differences. The following analysis is performed by the system:
Review of results |
Probable reason |
Analyst Action |
Are there any new items? |
New parts being driven |
|
Have any revisions changed? |
This could be the reason for item 1. |
Analyst must copy the forecast of the old rev to the new rev so that we do not lose the history and are able to apply the violation tolerances appropriately. Then the new forecast is loaded at the new revision.
|
Have some items been dropped from the Forecast? |
Revision change or demand has completely disappeared |
Analyst must note that there is a setup option by customer which will inactivate any existing Forecast that is not present in the new forecast. In other words, only items in the most current forecast are driven. There is potential excess from such a change and must be reviewed carefully. |
What are the potential changes in “net demand to MRP” in demand as a result of the new forecast? |
|
|
Have any of the quantities changed where they violate the allowed flexibility?
A typical Customer Forecast flexibility may be as shown in the next table |
|
Analyst should review. If it is not clear why there is a violation ( last forecast same as current) then run a waterfall report for the part in question. The violation may have happened in previous weeks and the forecast was forced.. |
0 to 30 days |
No Change Allowed |
31 to 60 |
25% Change |
61 to 90 |
50% Change |
91 Plus |
Unlimited flexibilty |
The responsibility of the Forecast analyst or PM is to review the reports and seek appropriate resolution from the customer before the end of the week.
|
1.2.3. Fields and Definitions for Forecast |
1.2.3.1. Main | 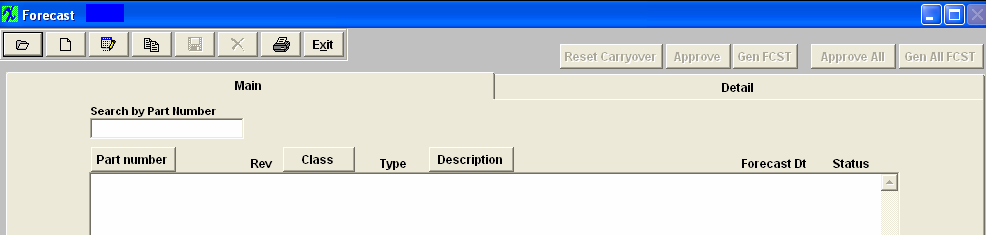
Search by Part Number |
Search for Inventory Product or Part. |
Part Number |
the unique number assigned to the Inventory Product or Part selected. |
Rev |
The revision character assigned to the Product or Part selected, if any. |
Class |
The classification of the Product or Part selected. |
Type |
The type assigned to the Product or Part selected. |
Description |
The description of the Product or Part selected. |
Forecast Dt |
The date the forecast was originated.
|
Status |
Status of forecast "Active" or "Inactive". |
|
1.2.3.2. Detail | 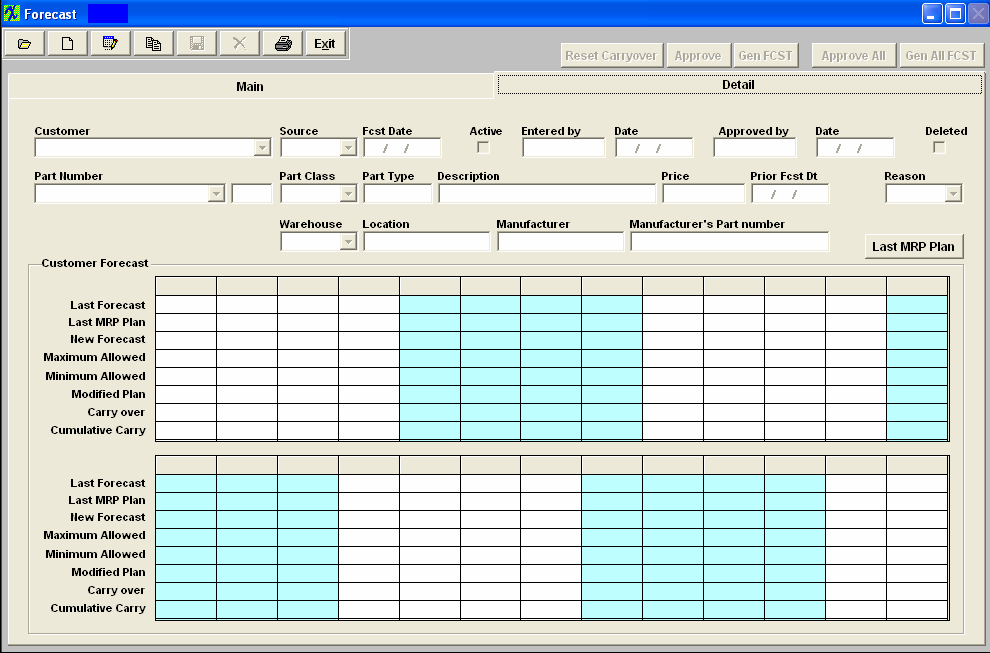
Fields and Definitions
Customer |
The name of the customer providing the forecast
|
Source |
Part Source - Make, Buy
|
Fcst Date |
The date the forecast was originated
|
Active |
Current forecast, as opposed to history or pending forecast
|
Entered By |
User initials entering forecast
|
Date |
Date of original forecast
|
Approved By |
Initials of person approving the forecast
|
Date |
Date of approval
|
Deleted |
A forecast that has been made inactive - history
|
Part Number |
The part number for the forecast listed |
Part Class |
The classification of the Part. |
Part Type |
The Type assigned to the part number. |
Description |
The description of the Product or Part Number. |
Price |
Price was intended to be utilized for forecasting revenue - not developed any further |
Prior Fcst Date |
The most recent forecast created prior to the current active forecast.
|
Reason |
The reason the prior forecast was made history.
|
Warehouse |
This field will only be displayed if it is a "BUY" part. Select the Warehouse from the Pull down.
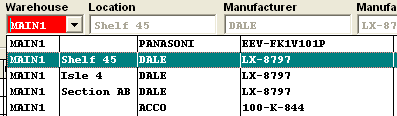
|
Location |
This field will only be displayed if it is a "BUY" part. This will default in upon selection of warehouse.
|
Manufacturer |
This field will only be displayed if it is a "BUY" part. This will default in upon selection of warehouse.
|
Manufactuer Part Number |
This field will only be displayed if it is a "BUY" part. This will default in upon selection of warehouse.
|
Action Buttons
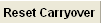 |
The purpose of this function is to get the snap shot of the carry over data into the history table and capture the carryover clear date. This clear date is been used in the MRP logic to get the total consumable sales orders and total shipments against the forecast. By using this date we can get the total sales order due, and shipments from the reset date to current date.
The reason a password is being asked for when depressing the Reset Carryover button is because it is the same as making an edit to the screen, so it is proper to request a password to clear the carryover quantities.
You can print the carry over history by selecting the carry over reset date from the drop down in the report form on which you can see what was the carryover was over quantity at the time of reset.
|
|
Approve the forecast currently being displayed. The approval requirements means that the whole forecast is approved to be used in running MRP, not for any specific changes to the forecast. Without the approval, the forecast will not replace the prior forecast and be ready to use by MRP (unless no approval is required). If no approval is required in the system setup, then any user with edit rights can render the old forecast that has history and make the new one active for MRP.
|
 |
Generate a forecast based on the “New Forecast”, the “Last Forecast” and the Forecast Allowed Tolerance for the customer involved |
 |
Approve all Forecasts currently in pending status. The approval requirements means that the whole forecast is approved to be used in running MRP, not for any specific changes to the forecast. Without the approval, the forecast will not replace the prior forecast and be ready to use by MRP (unless no approval is required). If no approval is required in the system setup, then any user with edit rights can render the old forecast that has history and make the new one active for MRP. |
 |
Same as Gen FCST, except does so for all forecasts in the system |
 |
Shows what the last MRP requirements were. Will vary as transactions and MRP occur |
Customer Forecast
Last Forecast |
The Last Forecast will be the values entered in the most recent previous forecast plan upon which MRP acted.
|
Last MRP Plan |
The Last MRP Plan will be what MRP will be providing as a basis for component and work orders.
|
New Forecast |
The New Forecast is the forecast being entered in the edit mode.
|
Maximum Allowed |
The Maximum Allowed is the last forecast plan modified by the system setup tolerances. If the last FORECAST was for 100 units on the first week, and the tolerance was for 50%, then this line would have the number 150.
|
Minimum Alowed |
The next is calculated similarly, showing the Minimum Allowed. So if the tolerance was 10%, then this line would be 90 units.
|
Modified Plan |
The Modified Plan is the New Forecast modified by the constraints of the Maximum and Minimum allowed. In this example, no change is allowed, because of the system setup and the fact that we are in the current period. Notice in the 5th week, these numbers become active as it falls in the next period.
|
Carry over |
The Carry Over is anything that is not covered by the forecast modified by the tolerances. Thus, if the previous forecast were 200, and the current forecast is for 300, and the tolerance is zero, the forecast could not be changed from 200 to 300, but held constant at 200. But the 100 left over that couldn’t be added to that week of the forecast becomes the carryover to the next week. As long as the tolerance allows it, the next week will be inclusive of the carryover. If it still falls outside the tolerance, it carries over to the following week. It will carryover until it can be absorbed into the forecast based on the tolerances for each period.
|
Cumulative Carry |
The Cumulative carryover is simply adding up any individual carryovers to keep track of the total amount of “catch-up” that is required.
|
|
1.2.4. How To ..... Forecast |
1.2.4.1. Find a Forecast |
Enter Material Planning/Master Production Schedule (MPS) & Forecast/Forecast |
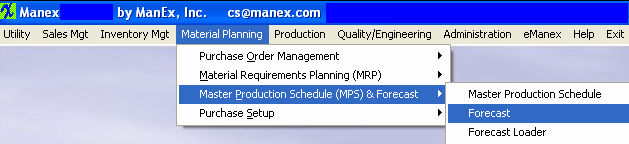 |
The following screen will appear:
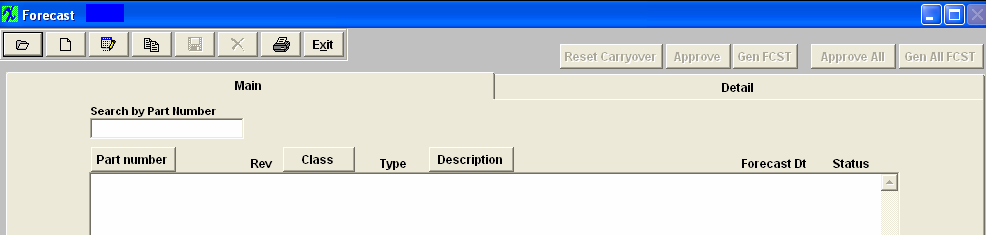
Depress the Find action button. A dialogue box will appear that will filter the amount of forecasts displayed. For example, clicking on OK without any entry will display all active forecasts. Selecting a customer will then display only forecasts for the selected customer. Clicking on a part number (or range of part numbers) will display all forecasts for them, if they are available. |
|
After depressing the OK button the following screen will appear:
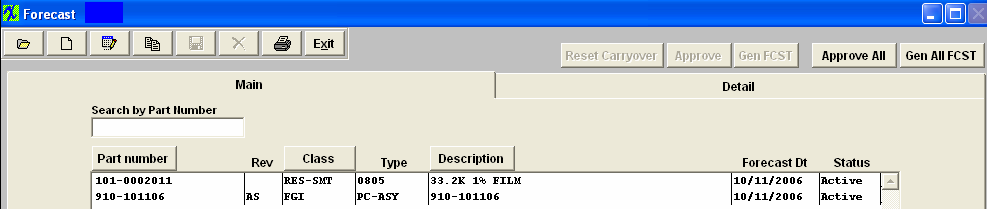
Highlight the PN of interest, then click on the Detail tab and the forecast detail for that PN will be displayed
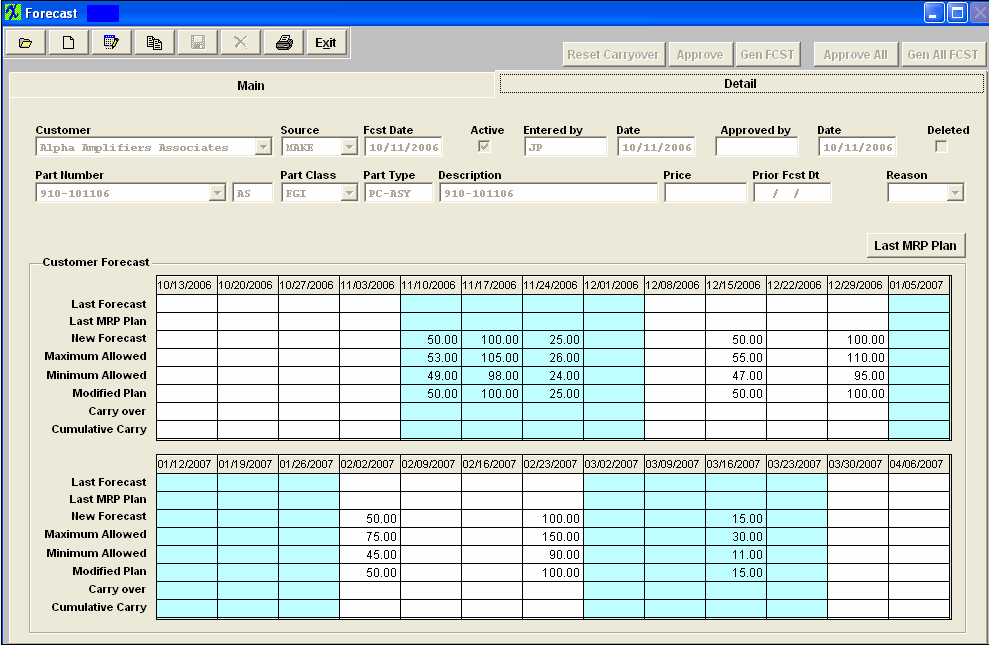
The weekly buckets are established as of the end date of the current week. Any data loaded from an excel sheet will aggregate the data by these week end dates.
The Maximum Allowed and Minimum Allowed rows of data are calculated based on the tolerances provided for the customer in the Forecast Setup module.
|
1.2.4.2. Add a Forecast |
Enter Material Planning/Master Production Schedule (MPS) & Forecast/Forecast |
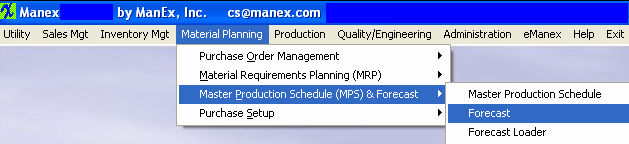 |
The following screen will appear:
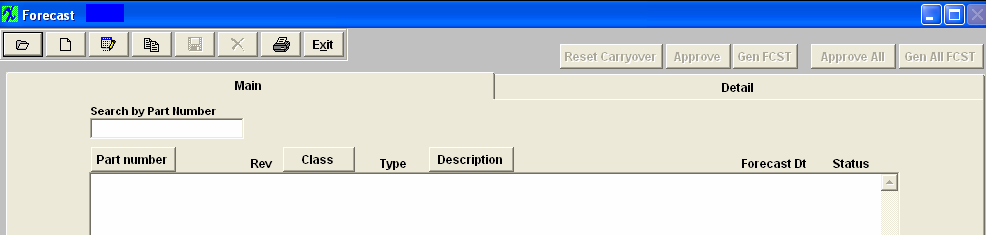
Depress the Add a record action button. The following screen will appear. Select a Customer from the dropdown list.
|
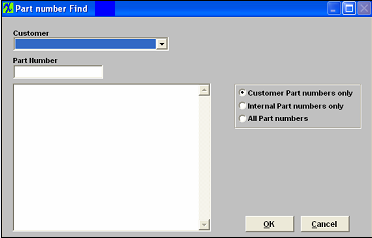 |
Once a Customer is selected, the user may view a list of part CUSTOMER numbers for the chosen customer, or…
Choose from a list of INTERNAL part numbers associated with the chosen customer, or…
Choose from a list of ALL part numbers in the database.
Using the Highlighted RED box, the user may type in a part number, and the dropdown list will move to show the information typed.
When the Customer and Part number are identified, depress the OK button.
|
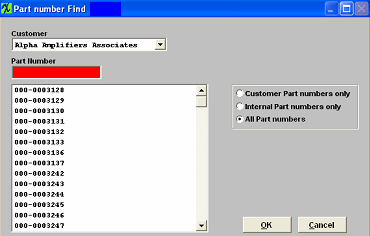 |
Go to the Detail Tab Screen. The header information will deafult in;
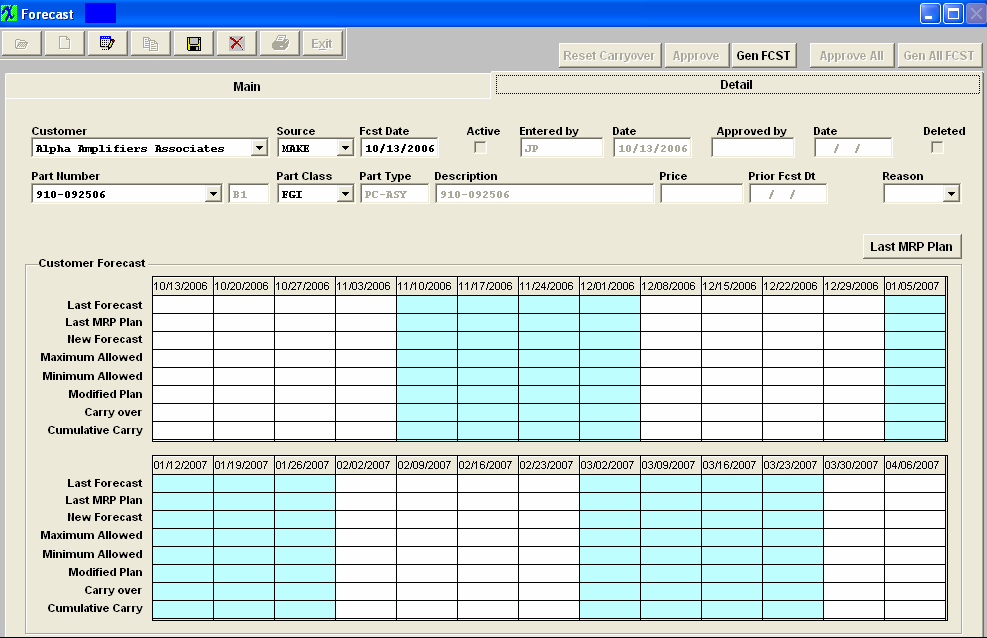
Enter in the new forecast;
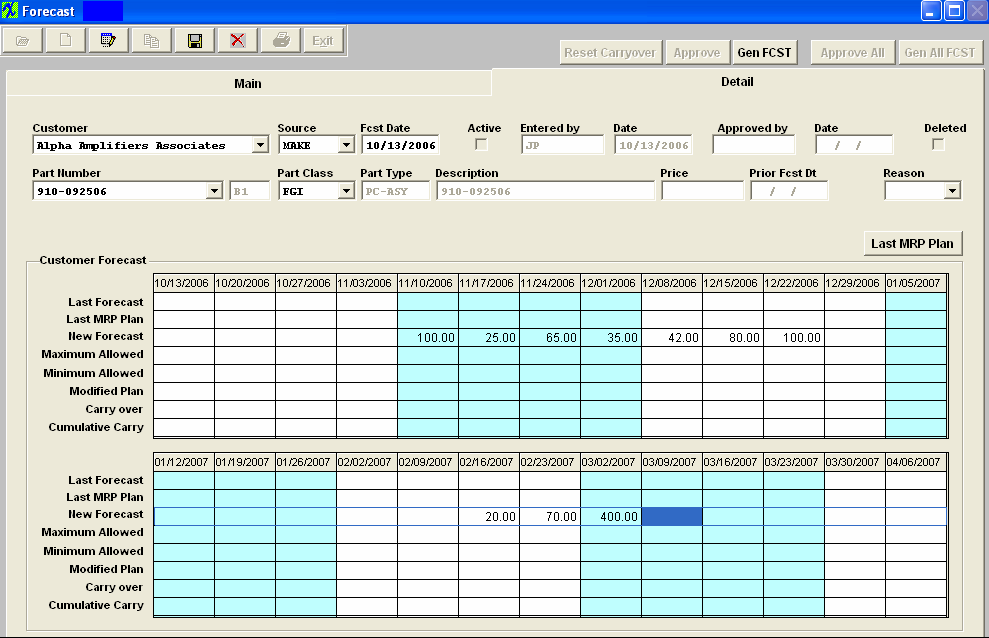
Once the forecast is entered, the User should save the information by depressing the Save record action button, and/or depress the GenFCST button to extend the Original forecast to the Planned Forecast, based on the system setup for the customer.
The user may also approve the forecast, if they have the authority. If the Forecast Setup indicates that approval is NOT required, the Approval button will be inactive, and saving the forecast will automatically make it active.
|
1.2.4.3. Edit a Forecast |
Enter Material Planning/Master Production Schedule (MPS) & Forecast/Forecast
|
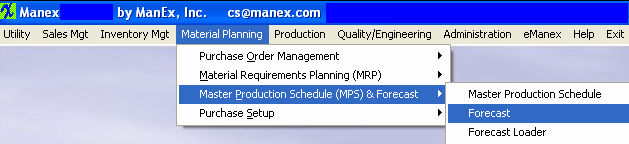 |
Find a Forecast
Depress the Edit button. Then the NEW FORECAST line can be edited. If there was a previous forecast, it will be shown on the top line.
In order to move forward with the forecast, the ACTIVE checkbox needs to be unchecked (in edit). After saving the changes and checkbox, then re-entering the same forecast in edit mode will activate the Approval and Gen FCST buttons. (If approvals are not required in the system setup, the Approval buttons will not be displayed.)
The Reset Carryover button can be used but as mentioned earlier, needs to have an approval entered in the system setup. The purpose of this button is to allow the user to eliminate any items carried over from previous or unfulfilled forecasts. When activated and password entered, the prompt is for a date on which the carryover will be eliminated.
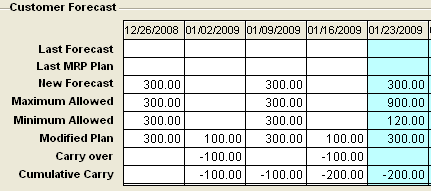 |
The Last Forecast will be the values entered in the most recent previous forecast plan upon which MRP acted.
The Last MRP Plan will be what MRP will be providing as a basis for component and work orders.
The New Forecast is the forecast being entered in the edit mode.
The Maximum Allowed is the last forecast plan modified by the system setup tolerances. If the last FORECAST was for 100 units on the first week, and the tolerance was for 50%, then this line would have the number 150.
The next is calculated similarly, showing the Minimum Allowed. So if the tolerance was 10%, then this line would be 90 units.
The Modified Plan is the New Forecast modified by the constraints of the Maximum and Minimum allowed. In this example, no change is allowed, because of the system setup and the fact that we are in the current period. Notice in the 5th week, these numbers become active as it falls in the next period.
The Carry Over is anything that is not covered by the forecast modified by the tolerances. Thus, if the previous forecast were 200, and the current forecast is for 300, and the tolerance is zero, the forecast could not be changed from 200 to 300, but held constant at 200. But the 100 left over that couldn’t be added to that week of the forecast becomes the carryover to the next week. As long as the tolerance allows it, the next week will be inclusive of the carryover. If it still falls outside the tolerance, it carries over to the following week. It will carryover until it can be absorbed into the forecast based on the tolerances for each period.
The Cumulative carryover is simply adding up any individual carryovers to keep track of the total amount of “catch-up” that is required.
|
|
1.2.5. Reports - Forecast |
To obtain the Forecast reports, depress the Reports button. The following screen will appear:
Select the output you desire by clicking on the radial.Choose from Screen, Printer, XL File, TXT File, or PDF.
Highlight the report.
Depress the option tab.
|
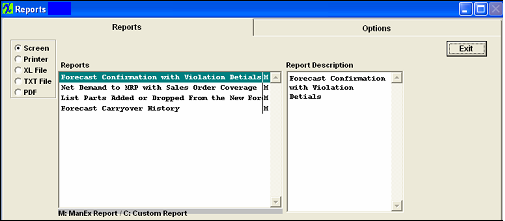 |
Forecast Confirmation with Violation Detail
Select the From and To Dates; Check For Approval or Violations Only; select Customer from pull down.
Depress the OK button
|
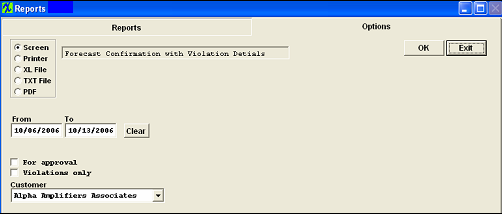 |
The following report will print:
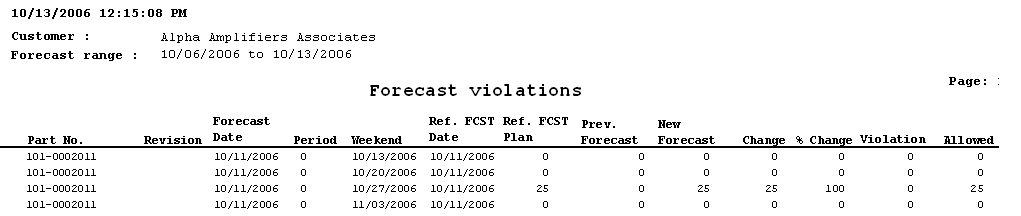
Net Demand to MRP with Sales Order Coverage
Depress the OK button |
 |
The following report will print:
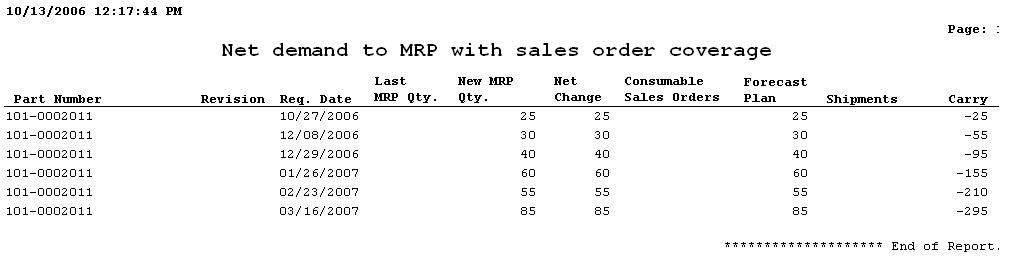
List Parts Added or Dropped from the New Forecast
Select the Customer from the pull down.
Depress the OK button.
|
 |
The following report will print:
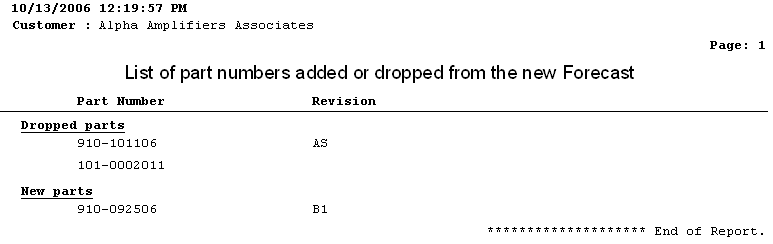
Forecast Carryover History
Select the Reset date from the pull down:
Depress the OK button
|
 |
The following report will print:
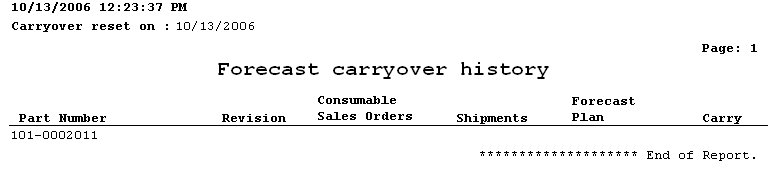
|
1.3.1. Prerequisites for Forecast Loader |
ManEx’s standard module configuration allows most users to accomplish their daily tasks. For those users wanting to get more from ManEx by leveraging the total solutions, this is one of the optional modules available for purchase. The Forecast Loader is used to add new forecasts to the system from an Excel template. To place an order or to learn more about this specific module or any of the other optional modules please contact us at http://manex.com"contactus.aspx
After activation, "Master Production Schedule" access for each user must be setup in the ManEx System Security module. Users with “Supervisor Rights” will automatically have access.
Forecast Loader Template Complete
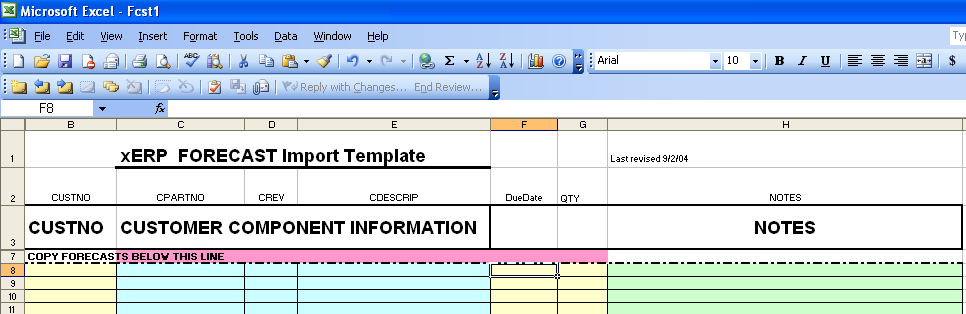
|
1.3.2. Introduction for Forecast Loader | The Forecast Loader is used to add new forecasts to the system from an Excel template.
|
1.3.3. Fields and Definitions - Forecast Loader | 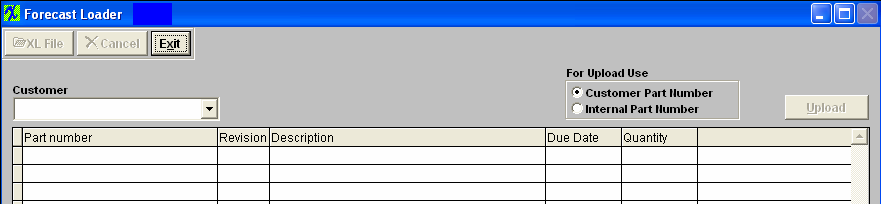
Customer |
Customer Name |
|
Upload by Customer Part number or Internal Part number |
Upload Button |
Depress this button to continue the upload |
Part number |
Part number being uploaded |
Revision |
Revision of part number being uploaded |
Description |
Description of part being uploaded |
Due Date |
Due Date of part being uploaded |
Quantity |
Quantity of part being uploaded | |
1.3.4. How To ..... for Forecast Loader |
1.3.4.1. Load Forecast |
Enter Material Planning/Master Production Schedule (MPS) & Forecast/Forecast Loader |
|
The following screen will appear:
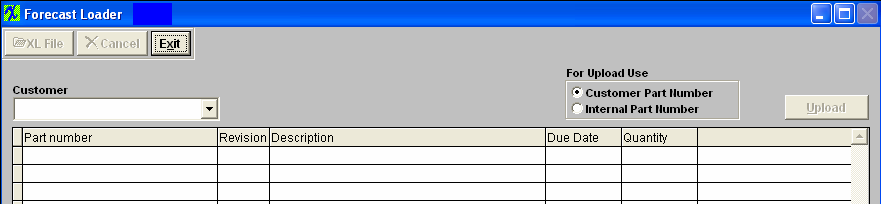
Select a customer from the pulldown, then click on the XL File Button to locate the file to be loaded.
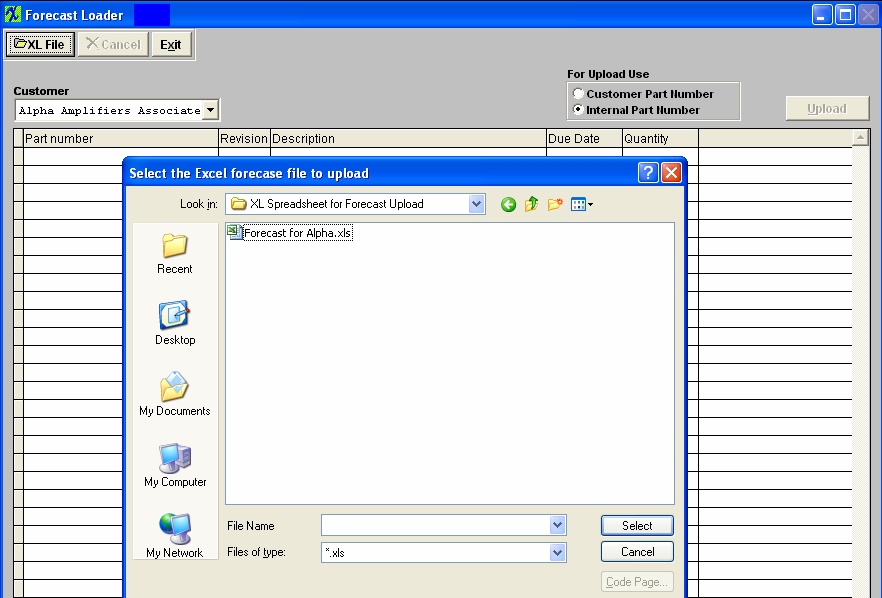
Double click on the file you choose to import and the information will be imported into the Forecast Loader screen as shown below. You can change the Part numbers to internal part numbers or leave them as the Customer Part numbers for the Upload.
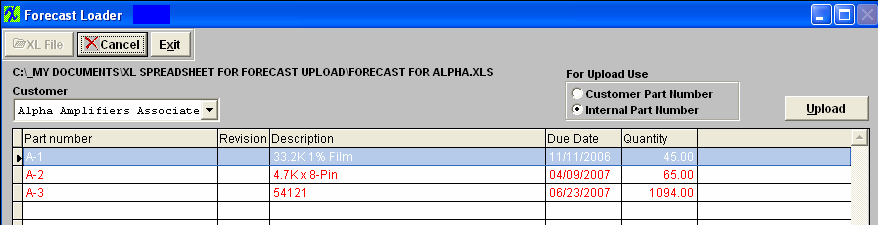
Depress the Upload button and a forecasst will be created. Then depress the exit or Cancel button to exit this screen.
|
|