1. Inventory Control Management (ICM) |
1.1. Prerequisties for ICM Mgmt |
After activation, "Inventory Control" access for each user must be setup in the ManEx System Security module. Users with “Supervisor Rights” will automatically have access.
Before entering products and parts in the Item Master, the following product, part and system classifications and item parameters must be setup in ManEx using the System Setup Material Module. Note: that although data entry is possible with only the Prerequisites below, using the Data Entry Defaults explained in the next section is strongly advised to save time and maintain consistency.
Product and Part Class |
All items must be assigned a Class code (Finished Goods, Subassembly, Resistor, Capacitor, Raw PCB, etc.) in order for ManEx to number, connect, sort and organize the items. Class codes are User-defined but chosen carefully.
|
Product and Part Type |
Each Class is further grouped into Types (Surface Mount, Thru-Hole, Precision, Programmed, etc.) to standardize description fields and allow use of default values. This speeds up data entry and eliminates redundant data and duplicate records.
|
Units of Measure |
Several standard Units of Measure (U/M) are already setup in ManEx.Additional purchase or stocking U/M’s must be added in System Setup. Also, if the Purchase and Stocking U/M are different (eg. Wire purchased in FT, issued in IN.), a Conversion Formula must be entered in System Setup Unit of Measure & Conversion.
|
Numbering System |
The User must select Automatic or Manually Numbering in System Setup Number System Module. For Auto-numbering, the Beginning Number must be entered. A customer-selected prefix can be entered in System Setup Number System to be added to each Manual or Auto-Numbered part no.
|
Warehouse Assignments |
A System Setup (Warehouse Setup) to assign names and General Ledger Numbers (for ManEx Accounting) to the hard-coded MAIN1, WIP, WO-WIP and MRB Warehouses is required. Additional FGI and/or In-Store Warehouses can be added if assignment as stocking locations during Item Master data entry is desired.
|
Optional Data Entry Default fields are not required for Item Master entries, but are highly recommended to ensure consistency and save time during data entry.They are shown below.
Data Entry Defaults
Item Master Data Entry Defaults are selections that remain the same for most of the items for a particular Class and Type. These Defaults are entered in System Setup Inventory Part Class and will be automatically filled in by ManEx once the Item Class and Type have been selected during data entry of a new Item. Defaults can be over-ridden during data entry.
For instance, if the User wished to make the Default entry for Item Package to be REEL for all Items with the Class RES-SMT and the Type 0402, the User should select REEL in the Package field of the System Setup when entering Type “0402" as shown in the example.
|
|
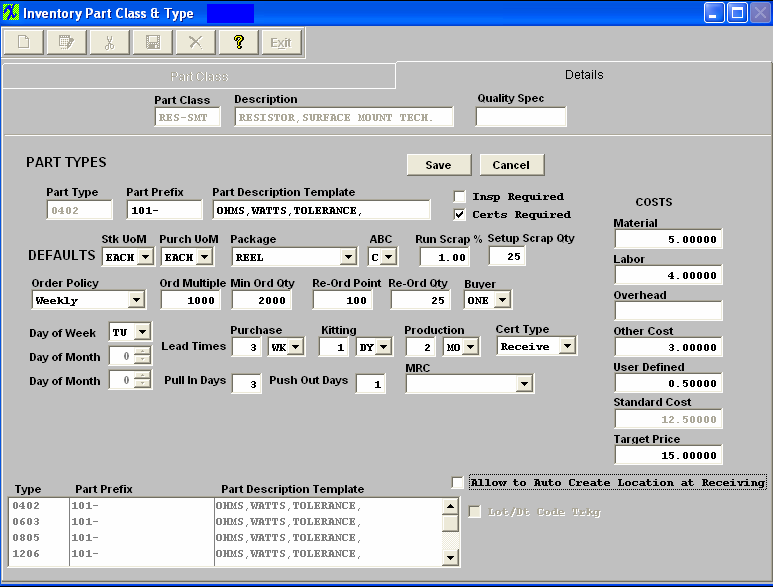
The same procedure would be used to set up Defaults for all of the fields for each Item Master Class and Type as shown. The information entered in each of the Default fields will be automatically entered in the corresponding field during data entry of a new Item after selecting the Class and Type.
Defaults should be setup to apply in most cases. If the default in a particular field is not appropriate for a new Item being entered, the User may make another choice on a one-time basis or if the default has changed. Use System Setup Inventory Part Class to change the default. If too many over-rides are necessary for a particular Type, it may be too general. Consider splitting it into two Types, each with its own set of Defaults. Changed defaults only affect future data entry, not items already entered. Each existing item must be reassigned to a new Type before the old Type can be deleted from setup.
|
1.2. Introduction for ICM Mgmt | Information entered and maintained in the Inventory Control Management Module is used in nearly ALL of the ManEx Modules. Product, assembly and part information that is necessary to plan, purchase, receive, inspect, stock, issue, kit and cost all items can be found and should be maintained in this location. In particular this information includes:
- Item Master Part and Product Descriptions, Classifications and Revisions
- Purchasing Parameters, Buyer Assignments, Lead Times and Units of Measure
- Inspection, Certification and Specification Data and Notes
- Warehouse Assignments, Inventory and Stocking Locations and Quantities on Hand
- Material Requirements Planning Variables, Re-order Policy and Re-stocking Method
- Internal and Customer Approved Vendor List with Manufacturer Part Numbers
- Our system operates on a "Standard Cost Basis" (for further information see Article #3386 ) and Purchase Price Weighted Averages for Parts and Assemblies
- ABC Classification for Cycle Counts, Buyer Assignment and Inventory Stratification
- Supplier Name and Supplier Part Number
- Manufacturing Specifications with either a .bmp or a .pdf file
|
1.3. Fields & Definitions for ICM Mgmt |
1.3.1. Summary Tab | The Summary Tab (screen) displays the results of an Inventory Find operation and is the starting point for further sorts, searches and selections based on Part Number, Part Class or a word or string of characters in the Description field. To view detailed information on a particular item, highlight the item and click on the appropriate Tab. An example Summary screen for all Internal Inventory is shown below.
Note: To display changes made in other windows or by other Users while this window is open, you must repeat the Inventory Find and refresh the screen data.
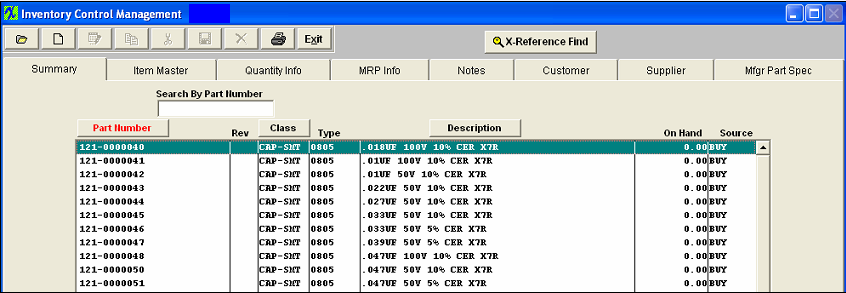
If a particular item does not appear on the Summary Screen, it may have been excluded by an Inventory Find that was too specific. Click on the Find a record and broaden the search criteria to display more records. Clicking OK with “Internal Inventory” and both “All Records” boxes checked will display ALL Internal items. Display all Consigned or In-Store records for a selected Customer or Supplier the same way.
Sorting, Searching and Selecting in the Inventory Summary Screen
- To sort the contents of the Summary screen by Part Number, Part Class or Description, click the button at the top of the column.
- It will turn red and the list will automatically sort in ascending alphanumeric sequence per the selection.
- To search for an item by Part Class, click Class and enter the first few characters of the Part Class in the Search by Part Class field.
- The list will scroll down to the first incidence of each character in the sequence entered. If a character is not found in the position typed, the list will scroll to the bottom.
- To Search for an item by Description starting with the 1st character on the left, click Description and begin entering the first characters in the field. The list will scroll down to the first incidence of each character in the sequence entered. If a character is not found in the position typed, the list will scroll to the bottom.
- To Search for an item by a word or character string anywhere in the Description, click on Description, click on the Left button next to the Search by Description window (changes to “Random”).
- Enter the search word or characters in the window. Hit return and the first match in the list will be highlighted. Click on the window and hit return to highlight the next match in the summary list. After the last match or if a match is not found, the last item in the summary list will be highlighted.
- To visually search the summary list, use the scroll bar or arrows to the right of the list. The Source (Buy, Make, Consigned or In-Store) and total On Hand quantity is displayed in the last two columns.
For further Details on any item in the summary list, highlight the item by a search or mouse click and select the appropriate Tab to display the desired detail information.
To display changes made in other windows or by other Users while this window is open, you must repeat the Inventory Find and refresh the screen data.
|
This button will take the user to a screen, where they can make a selection by what ever criteria needed by choosing (internal part number, mfgr part number, customer part number, supplier part number, or description) to search. |
The following screen will appear:
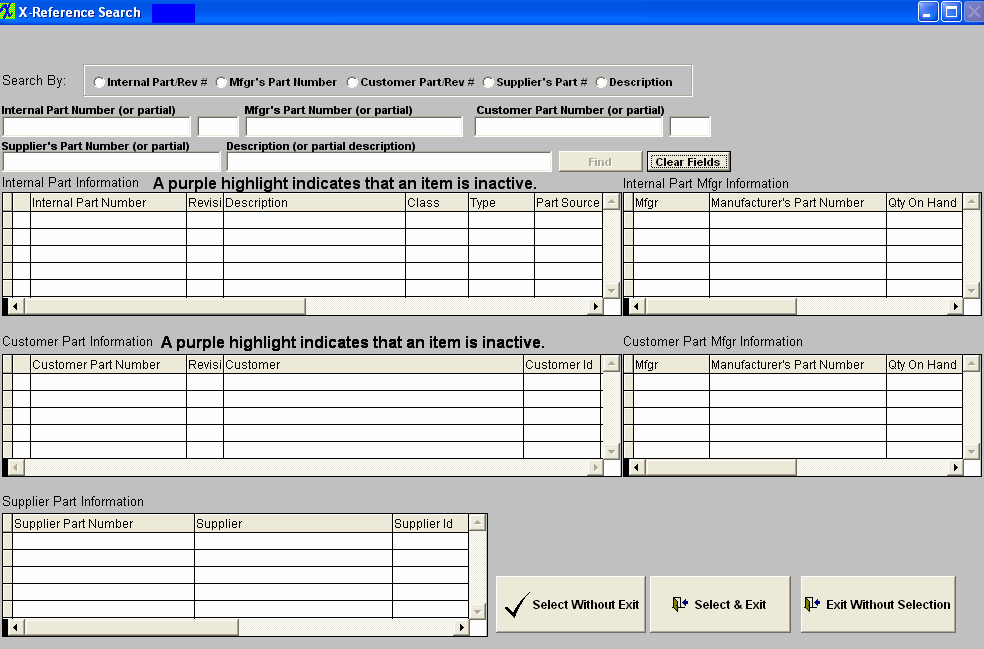
The user can enter partial string and search is not case sensitive. After system finds parts in response to the search (inactive parts will be highlighted in Purple), the user can make a selection by checking on one of the check boxes located at the left. If system was unable to find the exact match, a message will appear up in the right hand corner (in red) to let the user know that the part did not exist in the item master but the following are similar parts found.
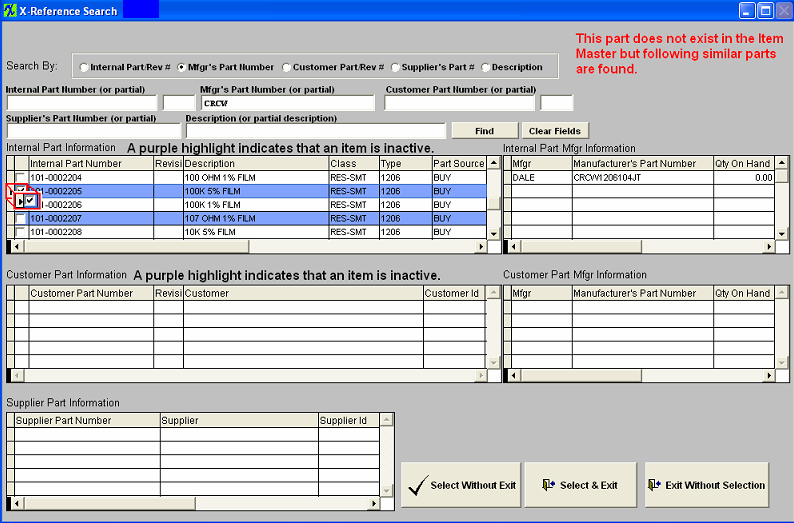
The user can choose to Select Without Exit; Select & Exit; or Exit Without Selection.
|
1.3.2. Item Master Tab | The following fields may be viewed in the Item Master screen. This screen is the starting point when the Add a New Inventory Record Action button is clicked or an existing record is highlighted within the summary screen. Clicking the Edit action button allows editing of existing Fields that are not grayed out. The ICM module will display "Internal" in the screen Header/Title bar, if internal inventory is open, and display the Customer name in the Screen Header/Title Bar if you have consigned inventory open. This will allow users that have multiple inventory screens open at the same time to seen at first glance which screen contains what type of inventory data.
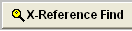 |
See Article #4765 for further detail on how to Use the X-Reference Find |
Item Master Tab Field Definitions
Part Source |
This field is hard coded in the system. Select BUY for purchased parts and assemblies, MAKE for an item made in-house (assemblies and sub-assemblies) and PHANTOM which is a list of parts that is common to several subassemblies.
A good example of where a Phantom can be used is a video card with different memory options. On all the variations of the memory card, there are a lot of parts which are common, including the circuit board. If we assume the only thing unique to each assembly is the amount or type of memory component and a couple of resistors, then the parts common to all the assemblies can be listed as a PHANTOM assembly. The PHANTOM part number is then listed as a component under each of the top-level assemblies. The BOM of the Phantom is exploded in the kitting module as if they were part of the BOM (hence the word Phantom) and pulled with the top level assembly. It becomes easy to maintain these BOMs since one change in the Phantom will ripple through all the video card variations.
|
Phantom/Make |
If the Part Source is a MAKE and this box is checked, the system will treat the part as a Phantom when the sub-assembly components are called up during the Kitting process BUT as a Make part for a stand alone assembly when the part is NOT a sub-assembly.
You can assign the status of "Make/Phantom" to a sub assembly. In this condition, it will cause the components to be added to a kit for the top assembly as if it was a Phantom BOM. On the other hand, you can also create work orders and demands for the sub assembly itself. The difference between this Make/Phantom and a straight Phantom is that you cannot build the straight Phantom.
Phantoms - We suggest that the user utilizes this feature, especially if the subgroup of parts are going to be used in more than one top assembly. If the subgroup has a modification to its BOM, the user does not have to go to each top level and change all of them. By simply changing the BOM in the Phantom assembly (or Make/Phantom), the kitting for all top assemblies including this subassembly will be changed to the new configuration. If you did not use the Phantom, and copied the parts into numerous top assemblies, you will have to make a change to every one of them if the subgroup of parts was modified. |
Make/Buy |
Make/Buy is setup to allow users to have a part in the system that they wished to BUY but also keep documentation within the system (BOM). If the Part Source is a MAKE and this box is checked, the assembly MUST be purchased from an outside source. If a Part is marked as Make/Buy within Inventory the MRP will only give PO Actions and that product will NOT be available for selection within the Work Order Management module, (due to MRP calculating incorrect demand and showing incorrect message with safety stock). If the part souce on a product is originally setup as a MAKE the user WILL be allowed to edit the record and change the part souce to Make/Buy. For further details see Article #3289 .
|
Part Class |
This is a general part, product or item classification that must be selected from the drop-down box. If an appropriate choice is not available when entering a new item, you may add a new part class in Inventory Part Class, (examples of Part Classes are BATTERY, DIODE, FUSE, FILTER, IC-SMT, CAP-SMT, RES-TH, etc.)
|
Part Type |
Type is a sub-classification of Part Class. If an appropriate choice is not available when entering a new item, you may add a new part type in Inventory Part Class (examples of Part Types for the Class IC-SMT would be 0603-5%, 0805-10%, 0805-5%, 1206-5%, 1210-5%, etc.)
NOTE: A user does have the option of leaving the Part Type blank, however if this option is selected the prefix for the part number will be omitted. There is no reason to enforce part type if a user doesn’t want to have that kind of detailed classification. If the user decides to leave the Part Type blank they will receive a message and at this point they have the option to continue or go back and pick a Part Type.
|
Description |
There are 45 characters available to put descriptive data about the item being entered that is not already in Part Class and Part Type. For instance, in the previous figure the Part Class and Type already show that it is a RESN-SMT 2512 so this information need not be repeated in the Description. We suggest when entering the description, that you be consistent with your capitalization and punctuation. Some of the screens and reports can be sorted by description so the more consistent you are the easier it will be to use the system in the future.
|
Material Type |
This field is an Item fields which is repeat at the top of all Tabs to display the selected Item.
If the Inventory Material Type is set to "Auto" (within the Material Type Setup), everytime the user modifies the AVL material type, the program will update the Inventory Material Type automatically.
>> If any of the AVL material type for the item is 'Unk' - the item level type will be 'Unk'
>> If any the material type is the same for all of the AVL's of the same item, the material type for the item will be the same as material type of the AVL's without a suffix. For example: if AVL types is anyof the 'LF-P/N', 'LF-Date', 'LF-Mark', the material type for the item will be 'LF'. If AVL's material type is 'ROHS-P/N', 'ROHS-Date', 'ROHS-Mark', the item's material type will be 'ROHS'
>> If any of the material type of the AVL's for the same item are different and none of them is 'Unk' then the type of the item will be 'LF'
Any changes to the AVL material type that drives the item material type to a lower level will display a warning.
If the control is set to "Manual", then the user will be able to modify the Inventory Material Type from the Material Type pulldown. Keep in mind that the program will NOT validate if the material type in Inventory and AVL levels are in sync.
The AVL Material Type is carried forward for the consign part when the consign part is first added to the system or when new AVL was added to the internal part and the user elects to add this AVL to the existing consign parts. If the user later changes the Material Type on the internal part, the change is NOT carried over to the consigned part.
|
Changed |
This field will display the date of the last change to the material type. |
Initials |
This field will display the initials of the user that made the last change to the material type. |
Serialize |
This box will be available only if the option to use Serial Number Tracking in Shop Floor Tracking Defaults is set up.
The system allows this box to be check for a MAKE or BUY part. If this box is checked for a BUY part, all components are being tracked by a serial number that was assigned to the part at time of receipt. If this box is checked for a MAKE part, the FG assemblies will be tracked by the serial number through complete process. Note: Once a serial number for a MAKE part is created, we don't allow user to turn off the serialized checkbox anymore, even if there is no qty on hand and all accounting records are cleared. This is so no history of Shop Floor tracking, shipping, RMA’s, etc. . . . for the Make Parts are lost.
If a user changes a non-serialized part to a Serialize part the system will check. * If the part has allocated qty, (user has to un-allocate parts before the system will allow user to check the "Serialize" box). *If the part has any OPEN kit (kit in process), (user has to de-kit or close kit before system will allow user to check the "Serialize" box) *If the parts is a BUY part and has un-reconciled PO (user has to reconcile all receipts before system will allow user to check the "Serialize" box).
After all these criterias are passed, if the part has quantity on hand, the user has to enter the serial numbers to match the quantity on hand.
Note: Users have to have special access in order to modify this checkbox, this access is assigned through Security/User Rights.
|
Status |
All items must be Active in order to buy, receive, issue, invoice or ship. Use Inactive Status to remove items from use that have already had transactions against the Part Number. Use Delete button to delete Items with no transactions. Changing status from Active to Inactive (for a Make Inventory part) will NOT change BOM status. User will have to change BOM status seperately. Changing from Inactive to Active status can be used to release items from Engineering. Note: If WIP (Work-in-Process) exists for a part the system will not allow the part status to be changed. This will prevent any possiblity's of qty on hand being returned to an inactive part if the users would happen to dekit. |
Part Number |
Item/Part number is a unique identifier for every Item Master record entered in the database. Part numbers can be setup to be manual numbered, or auto assigned to all items except MAKE assemblies, or all items including MAKE assemblies (within the Number System setup module). The standard part number is a 3-digit dash seven digit format where the three-digit prefix is used to define the part class, part type setup in the Inventory Part Class setup module to work with auto or manual numbered parts and assemblies. A manually assigned part number can be 25 characters. Alphanumeric part numbers are permitted. The revision field is 4 characters, also alphanumeric. ManEx uses separate assembly and revision fields making it easier to group all revisions of the same assembly and verify that the correct version is selected for production
|
ABC |
|
|
This is the Unit Of Measure (Foot, Inch, Each, Gallon, Quart, etc.) that is used to specify how much of the Item displayed or being entered is issued from Stock or is used in a Bill of Material for an assembly. ManEx tracks stocking units of measure within inventory, kitting, MRP, etc.
|
Purchase UOM |
This is the Unit Of Measure (Foot, Inch, Each, Gallon, Quart, etc.) that is used to specify how the Item displayed or being entered is purchased from a supplier.
NOTE: When creating a PO for an item with different purchasing and stocking UoMs, be sure to enter the MRP suggestion into the Stocking qty field rather than the purchasing qty field. The system will automatically convert the stocking unit into the purchasing unit for the purchase order qty.
For example if the buyer is creating a PO for an item that is used by inches but sold by the foot, the user would enter the 24 inches into the stocking qty field and the PO would automatically convert it to 2 feet in the purchasing qty field. So the supplier deals in feet, but ManEx deals in inches. The conversion between the two are established in the Unit of Measure & Conversion module.
Once the items have been accepted into inventory it is then converted over to Stock UOM and from that point forward everything within the system is using the Stock UOM.
ManEx DOES NOT recommend changing either of the UOM's if the part has a qty on hand. See Article #3414 for further detail.
|
Package |
This field defines how the components are to be packaged (ie. Reel, Tray, 6-Pak, Ream, Individually, etc.) when it is delivered. This defaults to what is setup in the Inventory Part Class setup. User can edit this field to fit the component package as it is purchased for your organization. This will default to the PO Screen. The buyer has the right to override the package definition in the item master or on the PO screen. (ie. Reel, Tray, 6-Pak, Ream, Individually, etc.)
|
Last Changed |
This captures the date,and time from the password of the individual making the changes to this screen and/or changes to the fields displayed on this screen from outside modules. Anytime an edit/save occurs this field is updated. Note: This field will NOT be adjusted from outside modules that change the costs, such as the Purchase Order module or the Cost Adjustment module those Last Changed dates will be displayed in the Last Changed fileds displayed next to the costs. |
By |
This captures the initials from the password of the individual making the changes to this screen and/or changes to the fields displayed on this screen from outside modules. Anytime an edit/save occurs this field is updated. Note: This field will NOT be adjusted from outside modules that change the costs, such as the Purchase Order module or the Cost Adjustment module
|
Buyer |
This field is automatically filled in from the information entered in the Inventory Part Class setup module. This field is used in the MRP lookup as a sort field to allow a buyer to find the parts they are exclusively responsible to purchase. If a buyer leaves or is replaced, there is a global replacement of one buyer to another located in the System Utilities.exe/Change Parameters for the Part/Class .
|
Mgmt Lock |
This option is for Inventory parts that need to be protected, even from those users that have edit capabilities. Only Supervisors or users with Lock/Unlock rights within the Security/User rights can modify this checkbox. If locked, all users can access the screen, but only supervisors or those with Lock/Unlock rights will have the capability to bypass the lock and make changes, while the Inventory part is still in lock mode. The reason we do NOT force the user to unlock the Inventory part before making any changes, is to protect it from anyone else making changes while the 'authorized" user is making their changes.
|
Lock Date |
This displays the date and time the Approved user implemented the Mgmt lock. |
By |
This is the users initials that implemented the Mgmt lock.
|
Configuration Charge |
This is NOT a part of the standard cost total.It is a specific cost used with the MANEX Order Configurator module and represents any additional cost over and above the standard cost total.
|
Run Scrap % |
This amount is added to the exact quantity used on an assembly to provide an overage to cover losses during running due to predictable machine and human losses.
|
Setup Scrap Qty |
Setup losses may be added to the BOM requirement and Run Scrap for an item.For instance, an auto-insertion machine may use extra parts for alignment checks.
|
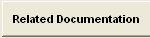 |
Depressing this button will give the users the ability to scan any related documents directly into the ManEx system and attached the document directly to the item in the ICM Module. For further detail see Article #2396. If this button is displayed in Red there is Related documents attached. |
Inspection / Quality Spec |
Checking the box will cause the item to require inspection to whatever Quality Spec. shows in the Quality Spec box. The Quality Spec appearing in the box is entered in System Setup Inventory Part Class Setup. Any Part Type in a particular Part Class can have Inspection Required turned on or off.
|
Certs Required/ Cert Type |
Checking this box will allow selection of Cert Type. Cert Type choices are Receive, Ship or Both. A typical Cert would be UL or CSA Certification on wire. Check the box and then depress the down arrow for the types to display. Select the desired type: Receive - Requires user to check the "Certificate Required" box has been Done at Receiving. Ship - Requires user to check the "Certificate Required" box on Packing List/SHipping. Both - Requires user to check the "Certificate Required" box at both Receiving and Packing List/Shipping.
|
First Article |
Checking this box will alert the users that the item requires a first article check at receiving inspection |
NC NR |
Checking this box, means that once the part is ordered it can not be returned or the order can not be cancelled.
|
MRC |
The Material Risk Codes listed in the pull down are entered in the System Setup Material Risk Code Setup. This is to inform the users which items are Low Risk or High Risk (can not be cancelled or returned).
|
EAU |
The quantity displayed in this box is the estimated Annual quantity. This is calculated from information entered into the ABC Types screen. |
Last EAU Calculated |
The date shown in this box is the date the EAU was last calculated in the ABC Types screen. |
PPM (Parts per million) |
This is a data entry field and is not involved in any calculations or used anywhere within the system at this point.It is planned to be used in the future to calculate the component level of PPM and then update the assembly PPM within the routing module.
|
Length |
Specific length allowed for part.
|
Width |
Specific width allowed for part.
|
Depth |
Specific depth allowed for part |
Weight |
Specific weight allowed for part.
|
Material Cost |
For BUY Parts: This is the purchase price of the BUY part. For MAKE Parts: The sum of the STANDARD COSTS of BUY parts in the assembly. Whether or not setup scrap is included is a system setup option. |
Labor Cost |
For BUY Parts: If the user wishes to include any preparation labor costs associated with a BUY part, like crimping, tinning testing. etc., those costs may be included here. For MAKE Parts: The user may include the labor associated with building the assembly. |
Overhead Cost |
For BUY Parts: Any additional costs associated with the labor, such as heating, lighting, etc., that the user may wish to include in the cost of the inventory value. For MAKE Parts: Any additional costs associated with the labor, such as vacations, sick leave, meeting times, etc., that the user may wish to include in the inventory value.
|
Other Cost |
For BUY or MAKE Parts: This is up to the user to decide if there are any other costs that should be absorbed in the inventory value. |
User Defined |
For BUY or MAKE Parts: This is a field where a user may define the field name and include any optional costs. |
Standard Cost |
The STANDARD COST of an item is a calculated value determined by the sum of individual costs. These individual costs may be in any combination of the Material, Labor, Overhead, Other and User Defined costs. Each of the individual costs should have their own account number in the Inventory Setup , and those accounts will accrue the costs when material is added to inventory. User MUST have optional rights within the Security module to "Allow Updating Inventory Std Cost and Standard Cost Rollups".
If ManEx Accounting is neither installed nor active, then there is no value other than reference in including values in these fields.
Important Notice: It is very important to have standard costs (as determined above) in place for any part entering inventory. ManEx allows users to enter a standard material cost at the time of purchase, if one is not already entered. Without accurate cost data, the inventory value could be next to useless, and major variances would show in Purchase Price, Configuration and Manufacturing Variances. If the material cost if the assembly does not equal the computed sum of the standard costs of the components based on the system setup, a configuration variance will be accrued.
|
Target Price |
This field is currently only a data entry field and will be reflected in the Purchase Order module for "BUY" or "MAKE/BUY" parts. This field is not editable for "MAKE" or "PHANTOM" parts. NOTE: To assign prices to products ("MAKE" parts), ManEx suggests using the Sales Price List Information module. This module allows users to enter prices by product and by customer so different customers can have different prices. This price will default into the sales order, but is still editable within the Sales Order module. |
Weighted Cost - Last 5 |
If the Part Source is a BUY, the weighted cost is calculated by dividing the extended total cost from 5 purchase order by the total qty from 5 Purchase Orders. The Purchase Orders used is with the latest version date (example if the original PO date is 1/3/06, but it was revised/edited on 12/5/06 it will use the 12/5/06 date, no matter what was edited on the PO). (if a user accidently selected the wrong PO to edit and had depressed the edit button, they could depress the abandon changes button to avoid the PO version date from being updated).
|
Last Changed |
This captures the date of the last change to the cost within this module and/or the outside modules such as the Purchase Order module and/or the Cost Adjustment module. |
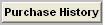 |
If the Part Source is a BUY, the purchase history will list information of 10 latest POs. The PO's will only be displayed on this list if the status is "OPEN" or "CLOSED". If the PO status is "EDIT" or "CANCEL" it will NOT be displayed on the the list. The system will select POs by original date. Note that the User may sort by depressing the Date, Supplier, PO Number, Manufacturer or Price button. For further detail see Article #3203 .
|
|
1.3.3. Quantity Info Tab | This screen is used to enter, edit and display Warehouse, Location, Manufacturer, and Safety Stock information for an inventory item. Also, after an item has been entered, complete inventory stock, allocation and usage information by Manufacturer is displayed or available at the click of a button. All current inventory information about any selected part can be displayed here.
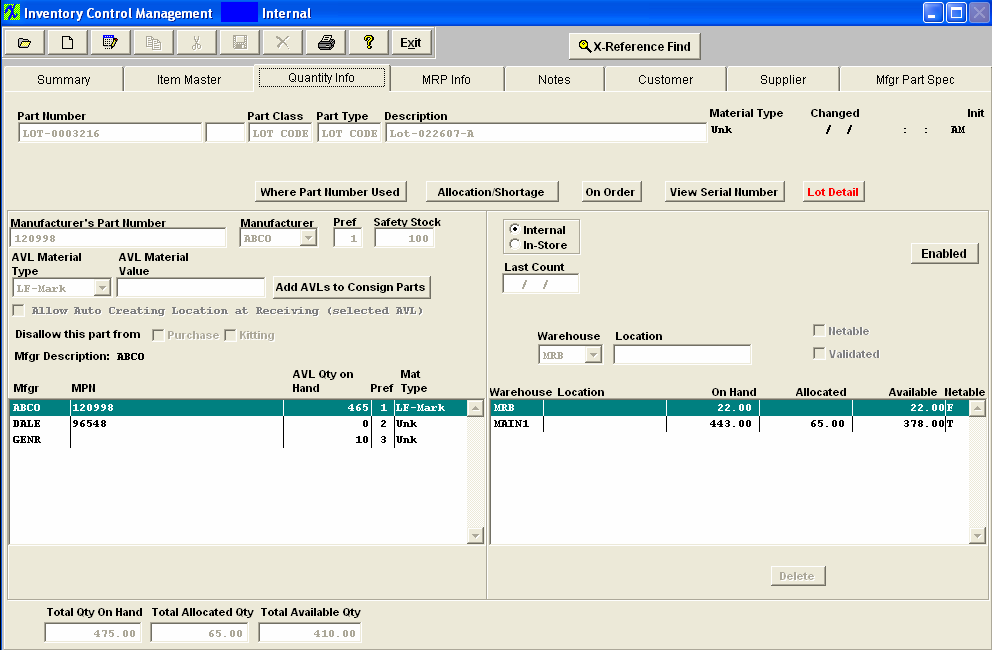
Header Information fields
Part Number, Part Class, Part Type, Description and Material Type are Item fields which repeat at the top of all Tabs to display the selected Item.
 |
Clicking on this button will display all Active assemblies and sub-assemblies with this item appearing in their BOM. |
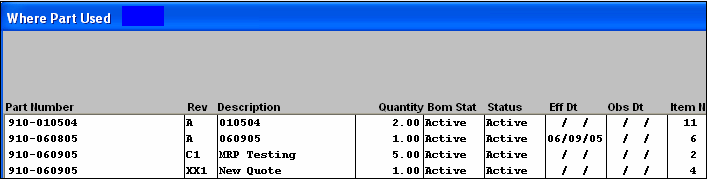
Where Part Used field Definitions
Part Number |
Is the number assigned to the assembly for which the internal Part Number is a component |
Rev |
Is the revision number of the assembly |
Description |
Is the description of the assembly |
Quantity |
Pertains to the amount of the component used for 1 unit of the completed assembly |
Bom Stat |
Is status of the Bom (Active, Inactive,etc.) |
Status |
Is status of the assembly (Active, Inactive, etc.) |
Eff Dt |
Pertain to any effective dates regarding the assembly |
Obs Dt |
Pertain to any obsolete dates regarding the assembly |
Item Number |
Is the item number on the Bom |
 |
Clicking on this button will display Inventory Allocations and Shortages for this item by Work Order number, as displayed:
|

Part Shortage and Allocation Field definitions
WoNo |
Is the number assigned to the Work Order for which the component part is short |
Project No |
Is the number assigned to a work order for a special project |
Wk Ctr |
Is the name of the Work Center where the Part Number is short |
PartMfgr |
Is the name of the manufacturer of this part. |
Wh |
Is the name of the warehouse where this Part Number is stored |
Location |
Displays if the shortage is a kit shortage, line item shortage or an allocation |
Qty Alloc |
Displays the quantity allocated to a specific Work Order or Project |
Qty Short |
Shows the number of units short for the Work Order |
The User may sort on Work Order Number, Project No, Work Center, Part Manufacturer or Warehouse by depressing the appropriate button.
 |
Clicking on this button will display all Open, Approved Purchase Orders for this item, as displayed: (The quantity being displayed is the qty scheduled not the qty on order) |

On Order Field definitions
Date |
Represents the calendar date of the Purchase Order |
Supplier |
Is the name of the Supplier to which the Purchase Order was sent |
PO Number |
Is the internal number assigned to that Purchase Order |
Mfgr |
Is the name of the Manufacturer specified in the Purchase Order |
Price |
Is the amount of money to be paid for one unit in the Purchase Order line item |
Quantity |
Is the amount of unit(s) scheduled on the PO, not the qty on order |
The User may sort on Date, Supplier, PO Number, Manufacturer or Price by depressing on the appropriate button.
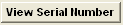 |
This field is read only. The button will be displayed in Red when there are serial numbers present. Clicking on this button will display all serial numbers assigned to this item, as display: (only if this item is serialized). This information comes from the PO Receiving module or Inventory Handling (Receiving) module and is not editable. |
Serial Number Field definitions
Sequence # |
Is the order in which the serial numbers were assigned |
Serial Number |
Is the number assigned to that part |
WH Qty |
Is the quantity available in the warehouse being used |
Warehouse |
Is the name of the warehouse the parts are being stored in |
Location |
Displays where the parts can be found |
Manufacturer |
Is the name of the mfg. specified |
Manufacturers Part Number |
Is the mfg. part number being used |
If the part is lot coded the additional fields will appear on the View Serial Number screen
|
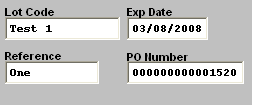 |
Lot Code |
Is the number of the lot |
Exp Date |
Displays the date the parts can no longer be used. This field is for reference only. Manex doesn't act on that date to expire the part. But it is part of the unique combination users can have LOT code A, exp date 01/10/2005 and LOT code A, exp date 01/01/2010 and the system will consider it as a completely different LOT.
|
Reference |
Is a name/number to identify the Lot. |
PO Number |
Is the internal number assigned when order is placed. |
 |
This field is read only and is not editable. The button will be displayed in Red and will be only displayed if the item is Lot Coded. Clicking on this button will display all the Lot Code Detail assigned to this item, as display below. All Lot Codes received by Purchase Order (in the PO Receiving module) will have a PO Number displayed against which they were received. If received using the Inventory Handling (Receiving) module the PO Number will be empty. |
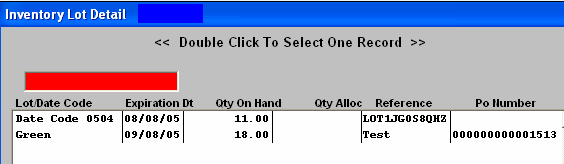
Lot Detail Field Definitions
Lot/Date Code |
Is the number of the Lot/Date Code |
Expiration Dt |
Displays the date the parts can no longer be used. This field is for reference only. Manex doesn't act on that date to expire the part. But it is part of the unique combination users can have LOT code A, exp date 01/10/2005 and LOT code A, exp date 01/01/2010 and the system will consider it as a completely different LOT.
|
Qty on Hand |
Displays the qty available in Inventory |
Qty Alloc |
Displays the quantity allocated to a specific Work Order or Project |
Reference |
Is a name/number identify the Lot |
PO Number |
Is the internal number assigned when order is placed |
AVL Information
This section will define all the AVL, and Safety Stock information assigned to the inventory part. The user may Add, Delete, or Edit the AVL information here.
When adding new MPN's to the item master, if you do not want the BOM's automatically updated be sure that the "Disable Automatic BOM AVL update" is Enabled. See article #1477 for more information.
Note: When deleting an MPN - keep in mind that the MPN will be deleted from the screen but NOT from the tables. The MPN's that have been deleted are retained in the tables for history tracking purposes.
|
|
AVL Field Definitions
Manufacturers Part Number |
Displays the Mfg. Part Number for an existing highlighted Mfg. Also, Used to enter Mfg. Part Number during data entry. If no manufacturers Part Number is entered into the Inventory Master during data entry, GENR (Generic) will be automatically entered by the system as the Manufacturer and the Manufacturers Part Number will be left blank. If a Buy item is fabricated by a customer, then the Customers name must be added to the list of Manufacturers and the Customers Part Number entered in the Manufacturers Part Number field.
|
Manufacturer |
Any Manufacturer entered in Part Manufacturer Setup can be selected in this field. If no specific Manufacturer is required, GENR. (Generic) may be used to show that any Manufacturer is usable. Also displays Manufacturer for an existing inventory record choosen.
|
Pref |
This is a number indicating the preference for use in Work Order Kitting for each Manufacturer shown. The number 1 indicates 1st ranking, 2 is 2nd ranking, etc. User will only be allowed to enter postive numbers (1 through 99). If no preference code is entered the preference automatically is assigned 99. All items will be at the bottom of the preference list unless the user assigns another number to it. For further detail on how the preference code is used in MRP see Article #3032 . |
Safety Stock |
Enter in a qty that you want kept on hand for this specific AVL. User may have safety stock for more than one AVL for a given part number. (Safety stock is calculated in MRP at the AVL level NOT the part number level). This qty is in addition to the MRP demands. ManEx will ensure that there is always the safety stock qty on hand regardless of the MRP demands. Please see Article #2331 for more detail. (This field is calculated off of the Stock UOM).
|
AVL Material Type |
Select from the pull down, Unk, LF-P/N, LF-Date, LF-Mark, RoHS-P/N, RoHS-Date, RoHS-Mark. See Article 2267 for definitions. These choices have been defaulted in. Customers may establish the logic by which the material type for the parts are established by the material types at the AVL level in Material Type Setup.
The AVL Material Type is carried forward for the consign part when the consign part is first added to the system or when new AVL was added to the internal part and the user elects to add this AVL to the existing consign parts. If the user later changes the Material Type on the internal part, the change is NOT carried over to the consigned part.
If the Inventory Material Type is set to "Auto" (within the Material Type Setup), everytime the user modifies the AVL material type, the program will update the Inventory Material Type automatically, if the control is set to "Manual", then the user will be able to modify the Inventory Material Type from the Material Type pulldown. Keep in mind that the program will NOT validate if the material type in Inventory and AVL levels are in sync.
|
AVL Material Value |
This field is a text modifier for a given material type. For example, if the material type was "LF-Date", the text in the field could be a date code. This value could be different for various AVL with the same Material Code. This field is optional and does not have to be populated. |
 |
This field is to add the AVL(s) to a consigned part.
|
Allow Auto Creating Location at Receiving (Selected AVL) |
Note: Users have to have special access in order to modify this checkbox, this access is assigned through Security/User Rights.
If the box is checked (for the highlighted AVL) it will allow the user to create a location when entering the Purchase Order or at PO Receiving. Note: The "Allow Auto Creating Location at Receiving" box must be checked also in Warehouse Setup.
If the user has the " Remove location with this warehouse from the Inventory when qty on hand gets to zero Box" box checked within the Warehouse Setup Setup module this box MUST be checked also.
|
 |
There are situations where the Users customers will allow them to use up non-conforming inventory, but cannot replace the same AVLs. So, at the AVL level, we added two logic fields that would signify that the AVL is NOT to be purchased and/or kitted. In such a circumstance, it is NOT appropriate to delete the parts, but neither can they be purchased for future requirements. Likewise, they may want to avoid kitting so you would check these boxes to "Disallow this part from Purchase and/or Kitting". For special circumstances, the user can override the block from kitting if their customer permits it. For further information on how to use these fields effectively refer to Article #2329. For information on how these fields affect MRP refer to Article #3211 . (See the non-nettable function for the warehouse level described below). |
AVL Qty on Hand |
Total qty on hand for each individual mfg. |
Total Qty on Hand |
Total qty on hand for all mfg.'s combined
|
Total Allocated Qty |
Total qty allocated to a specific work order or project |
Total Available Qty |
Total qty available minus the allocated qty
|
Add |
Allows data entry to add Manufacturer record. Enter Manufacturer part number and a drop down list will appear to choose the Manufacturer. Click on the save button and the information entered will be displayed in the screen.
|
Delete |
Deletes the highlighted manufacturer part number record. A ????? screen will appear. Click the NO button to restore the deleted record if this button is clicked in error. Deletion of manufacturer part number records is not allowed if a Warehouse quantity other than zero (0) is shown for that record. Before manufacturer records are deleted, please realize that SOME of the history regarding the manufacturer may also be deleted.
|
Save |
Appears after clicking the Add button. Clicking on this button saves the record |
Cancel |
Appears after clicking the Add button. Click to abort saving a new record or changes to existing records.
|
Warehouse Information
This section will define all the Warehouse information assigned to the inventory part. The user may add or edit the Warehouse information here also.
|
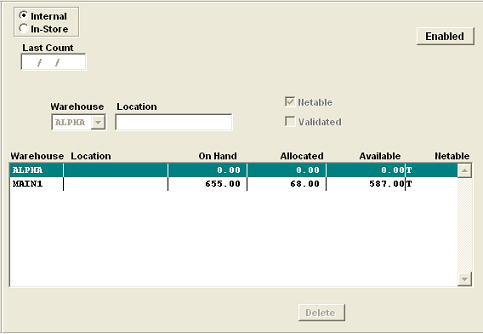 |
Warehouse Field Definitions
 |
One of these radials must be checked. Internal (User owned) or In-Store (supplier owned). This selection is available only for "BUY" parts. This selection will not be displayed for "MAKE" or "PHANTOM" parts.
|
Last Count |
Displays the date of the last physical Inventory or Cycle Count for the highlighted item in the Warehouse/Location/Manufacturer display window.
|
Warehouse |
Used to display the stocking Warehouse for an existing item or to select a Warehouse during entry of a new Location or Manufacturers Part Number. Only Warehouses entered in Warehouse Setup may be selected in this field.
|
Location |
Allows entry of any Location code desired. It could be an area assigned for Finished Goods, High Value items, Programmed parts or a Row, Aisle and Shelf Code. Also displays Location for an existing highlighted Warehouse record. This field is flagged "Read Only" for MRB whse (meaning you can not create a location for an MRB whse).
|
Netable (box) |
If this is checked, any On Hand inventory of the item in the Warehouse location being added or highlighted (if already added) will be used to fill Material Requirements Planning stipulations when processing the MRP. If you want to exclude this part from MRP and Kitting Issue screens, uncheck this box. You Cannot have a netable part that is excluded by MRP. The only warehouse that is non-netable is the MRB warehouse. Any parts in that warehouse are deemed questionable until the parts are validated and returned to a normal warehouse. So they will not be considered by MRP.
|
Validated (box) |
This is for reference only and does not affect any other modules in Manex. This is simply to help users keep track of changes and for the users to check that the part being added has been verified as appropriate.
|
or  |
If Enabled ManEx will add the new AVL to all existing BOMs and check them as approved. If Disabled ManEx will add the new AVL to all existing BOMs but will NOT mark them as approved. Then they will not drive any demands or be available for pulling to that kit. Then you will have to manually go into each individual BOM and Check mark the ones that you do intend to use that new AVL on. See article #1477 for more information.
|
On Hand |
Shows the total quantity of the Manufacturer Part Number indicated which is currently in the Warehouse and Location shown.
|
Allocated |
Quantity of the item that has been allocated to a Work Order in the Inventory Mgt./ Kitting, Allocating and Shortage Management/ Work Order Allocation screen.
|
Available |
(Calculated field) Equals the quantity On Hand minus the Allocated quantity.
|
Add |
Allows data entry to add a Warehouse, and Location. A drop down list appears to select a warehouse. Enter in a location if you choose. Click on the save button and the information entered will appear in the screen.
|
Delete |
Deletes the highlighted Warehouse record. A reminder screen will appear. Click the NO button to restore the Deleted record if this button is clicked in error. Deletion of Warehouse records is not allowed if a Warehouse quantity other than zero (0) is shown for that record.Before warehouse records are deleted, please realize that SOME of the history regarding the warehouse may also be deleted.
|
Save |
Appears after depressing the Add button. Depressing this button saves the record.
|
Cancel |
Appears after depressing the Add button. Depress to abort saving a new record or changes to existing records.
|
|
1.3.4. MRP Tab (Material Requirements Planning Info Tab) | This Tab displays the screen in which Material Requirements Planning parameters are entered, edited or viewed. Default choices for each of these fields may be selected in System Setup Inventory Part Class Setup.
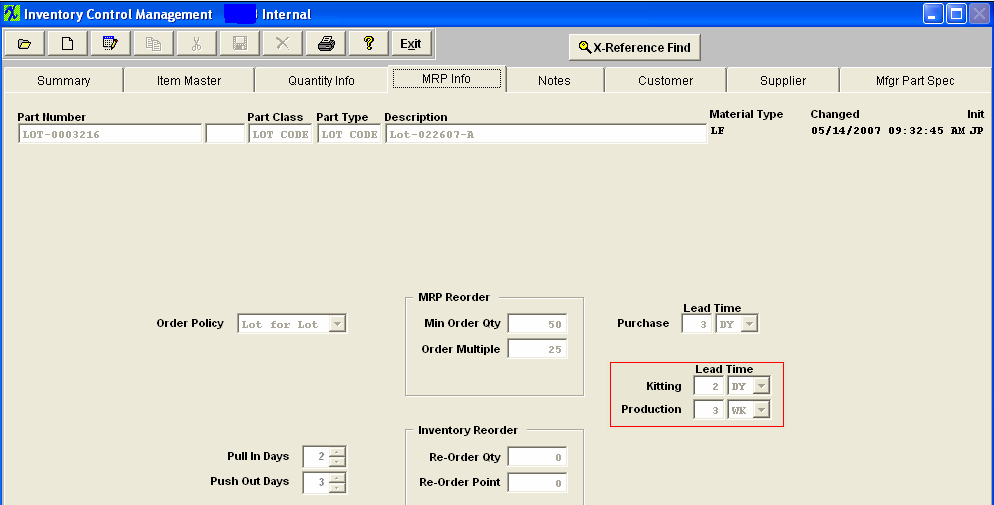
Header Information fields
Part Number, Part Class, Part Type, Description, and Material type are Item fields which repeat at the top of all Tabs to display the selected Item.
Note: All lead times are calculated with the Production Calendar.
Order Policy field |
This field is used to select the method used by the Material Requirements Planning module to combine requirements for this item in creating Planned Purchase Orders (PO’s). For instance if the choice is “Lot for Lot”, for a BUY part, the Material Requirements Planning module will plan one PO for the total requirements on a daily basis. If the choice is "Lot for Lot" for a MAKE part MRP will calculate off of each Sales Order individually . If the choice were “Weekly”, for a BUY part, the Material Requirements Planning module would combine all the requirements each week and plan one PO on the first requirement day for the entire week’s needs, etc. Note: If order policy is left blank "Lot For Lot" will be used upon default for MRP calculations.
|
Min Order Qty field |
This is smallest number of the item that can be ordered from the supplier in one PO. For instance, Surface Mount components on a reel usually have a minimum order of 1000 items or more. (This field is calculated off of the Stock UOM).
|
Order Multiple field |
This field defines the even multiples of the Unit of Measure in which an item must be purchased. For example, 16AWG Wire might be only available in even hundreds of feet on a spool in which case the Material Requirements Planning module would plan a PO for the next higher even hundred above the requirement. (This field is calculated off of the Stock UOM). |
Purchase Lead Time field |
This field will be displayed for a Buy part or a Make with Make/Buy Flag part. Purchase of all items other than In-Store items requires that the PO be placed a minimum number of days before the actual requirement. This Lead Time requirement is what tells the Material Requirements Planning module how many days before a requirement to plan a PO. Changing the leadtime of a Buy part will NOT change the due date in MRP, only the date to take action. For more detail see diagram shown below. |
Kitting Lead Time field |
This field will be displayed for a Regular Make part or a Make with Make/Phantom Flag part. This Lead Time requirement is what tells the Material Requirements Planning module how many days to allow for kitting. Changing the kitting leadtime of a Make or Make/Phantom part will change the due date in MRP. A TRUE phantom does NOT require any lead times and should be left blank. BUT . . . if for some reason you need to add a lead time for a TRUE phantom ManEx does have the capability. For more detail see diagram shown below.
|
Production Lead Time field |
This field will be displayed for a Regular Make part, a Make with Make/Phantom Flag part or a Straight Phantom part. This Lead Time requirement is what tells the Material Requirements Planning module how many days to allow for production. Changing the production leadtime of a Make or Make/Phantom part will change the due date in MRP. A TRUE phantom does NOT require any lead times and should be left blank. BUT . . . if for some reason you need to add a lead time for a TRUE phantom ManEx does have the capability. For more detail see diagram shown below.
NOTE: Once the parts have been pulled to the kit and the kit status is changed to "Kit in Process" MRP is designed to calculate from the Kit Shortage and production lead time NOT from the production offset lead times. Once the parts have been pulled to the kit, the system is assuming that the shortages are needed by the WO due date, rather than the Production offset lead time, so MRP then calculates using the production lead time and due date of the WO as the date the materials must be on hand, MRP no longer takes the production offset lead time into consideration.
|
Pull In Days field |
When PO due date is more than this number of days too late for a Material Requirements Planning module requirement, a PO Due Date change Action Notice will be generated. It allows the user to have the flexability for SO and WO due dates to be different without MRP actions being generated. For more information on how the Pull-in days work within MRP see Article #2557. Note: These parameters may be thought of as filters for MRP Order Actions when the requirement dates for the parts changes. In the case of the customer pulling forward their required date, it is a greater imperative that the work orders (thus the assembly) be pulled in to match the earlier due date. So the assemblies should probably have a minimum number of days to be sensitive to earlier demands. See attached Document <<pullin-pushout discussion.docx>>.
|
Push Out Days field |
When PO due date is more than this number of days too early for a Material Requirements Planning module requirement, a PO Due Date change Action Notice will be generated. Example: if there is a PO that is due to be delivered Dec 15, but now it is not needed until Dec 26 and the Push out is 30 days, then there WOULD NOT be a message issued within MRP to reschedule the PO delivery, because it is within 30 days, but if the Push out was 5 days then an action message WOULD BE issue to reschedule the delivery because the new date was outside of the push-out days. It allows the user to have the flexability for SO and WO due dates to be different without MRP actions being generated. For more information on how the Push-out days work within MRP see Article #2557. Note: These parameters may be thought of as filters for MRP Order Actions when the requirement dates for the parts changes. The Push Out value (in days) is the number of days that the required date, base on MRP, may be pushed out (required later than the original date) but will not result in a change order to move the required delivery for the item involved. See attached Document <<pullin-pushout discussion.docx>>.
|
Re-Order Point field |
To use the Re-Order Point and Re-Order Qty rather than Material Requirements Planning for reordering this item, enter the quantity at or below which the item should be replenished. Print the "Inventory Material Reorder List" report to show items which have dropped below re-order point minimums. NOTE: The Re-Order Point/Qty fields have NO AFFECT on MRP at all. MRP will NOT consider these fields for any calculations (these fields have no connection with MRP). These fields are intended to control stock on overhead items. (This field is calculated off of the Stock UOM).
|
Re-Order Quantity field |
To use the Re-Order Point and Re-Order Qty rather than Material Requirements Planning for reordering this item, enter the quantity of the re-order here. Print the "Inventory Material Reorder List" report to show items which have dropped below re-order point minimums. NOTE: The Re-Order Point/Qty fields have NO AFFECT on MRP at all. MRP will NOT consider these fields for any calculations (these fields have no connection with MRP). These fields are intended to control stock on overhead items. (This field is calculated off of the Stock UOM). |
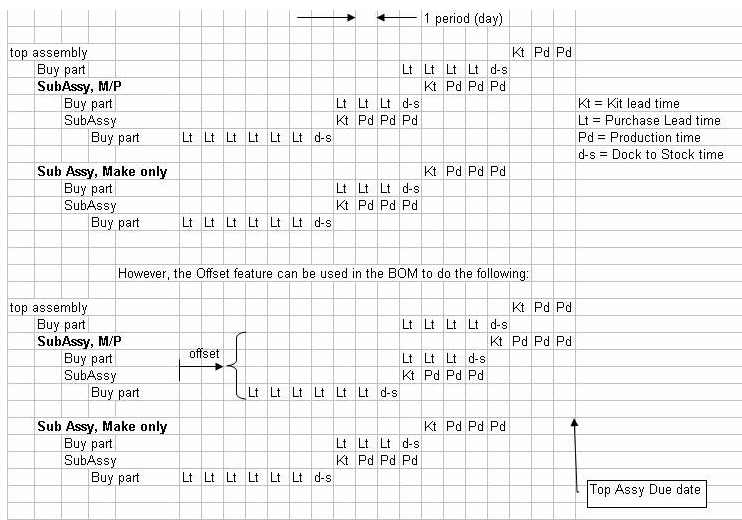
|
1.3.5. Notes Tab | Notes are usable for text information relevant to this item that is of interest to Engineering, Purchasing, Stores or Planning. A typical note is shown below. These item notes are viewable from the Material Requirements Planning, Bill of Material and Purchasing screens.
|
1.3.6. Customer Tab | This screen allows users to connect the customer part number and revision with the internal part number and revision. Entry of a Customer Part Number creates a Consigned Inventory Record that does several very important functions:
-
Serves as the place for selection of each Approved Manufacturers (Customer’s Approved Vendor List) from the list of all Manufacturer Part Numbers for that particular generic part
-
Provides a way to cross reference Customer Part Numbers to Internal Part Numbers
-
Allows generation of Bills of Material with Customer Part Numbers
-
Sets up a Consigned Inventory Warehouse(s) to allow receipt, issue and tracking of this Customer part
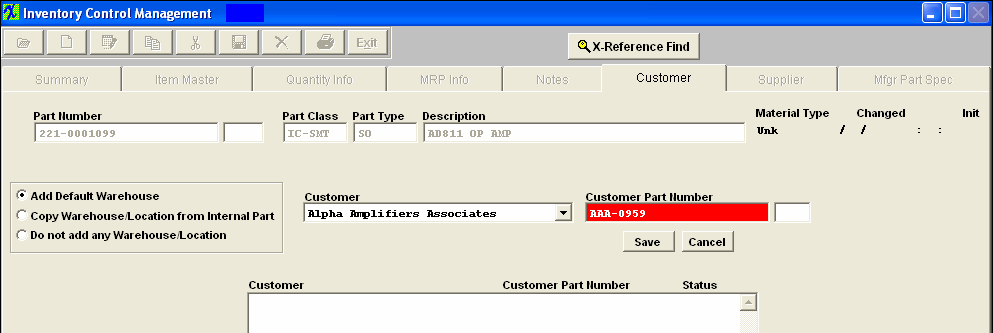
Header information fields: Displays the Part Number, Class, Type, Description and Material Type selected in the Summary Tab.
Customer field |
In View Mode, this screen shows the Customer selected from the Customer window.In Edit Mode, use this field to enter Customer Name |
Customer Part Number |
For viewing or entry of Customer Part Number for the internal Part Number displayed in the Header.
|
Display/ select window |
Shows all Customers and Customer Part Numbers for this internal part and their status, (active, in-active, etc).
|
Add |
Add a new Customer and customer part number |
Delete |
Delete an existing Customer and customer part number |
Save |
Save new Customer Part Number |
Cancel |
Cancel a Customer Part Number |
Add Default Warehouse |
Select to add only the default warehouse to customer side when adding a Customer Part Number |
Copy Warehouse Location from Internal Part |
Select to Copy Warehouse Location(s) from Internal Part to customer side when adding a Customer Part Number |
Do not add any Warehouse/Location |
Select if user does not want to add any Warehouse/Location(s) from the interanl side to the customer side when adding a Customer Part Number |
ManEx does not allow user to link same customer with multiple customer part numbers to the same internal part number. Our structure is based tightly on the internal part number. We link to customer part numbers when needed for showing customer part numbers or for MRP AVL limitations. If we allowed more than one customer part number for the same customer, we would not be able to process mrp AVL selection, nor reports that currently show customer part numbers.
|
1.3.7. Supplier Tab | This screen is for referencing the supplier(s) of this part and the Supplier’s Part Number.
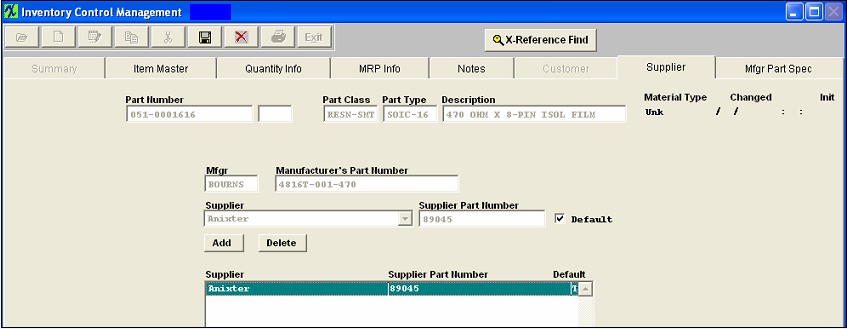
Header information fields: Displays the Part Number, Class, Type, Description, and Material Type selected in the Summary Tab.
Mfg field |
Displays the mfg. selected in the quantity info. Tab |
Manufacturer’s Part Number |
Displays the manufactuer’s part number selected in the quantity info. tab.
|
Supplier field |
In View Mode, this screen shows the Supplier selected from the Supplier window. In Edit Mode, use this field to enter Supplier Name.
|
Supplier Part Number |
For viewing or entry of Supplier Part Number for the internal Part Number displayed in the Header.
|
Default |
Check this box if you would like this supplier to show automatically when purchasing this part number.
|
Display Select Window |
Shows all Suppliers and Supplier Part Numbers for this internal part and whether it is chosen as a defalut.
|
Add |
Add a new supplier and supplier part number |
Delete |
Delete an existing supplier and supplier part number |
Note: The system allows you to have multiple suppliers per AVL and one default supplier per AVL. But each AVL can have a different default supplier and different suppliers.
|
1.3.8. Mfg. Part Spec Tab | This screen is used to view or enter a link to a drawing, photograph,image or .pdf file to be used as an on-line reference for engineering, purchasing, quoting or any other item master usage. It can be an assembly drawing, purchased part specification, spec. control drawing, photograph or any other image or .pdf file linkable to Manex. The image or .pdf file is not stored in Manex. The file in which the image or .pdf file is stored is linked to this screen in Manex and can be maintained without access to Manex.
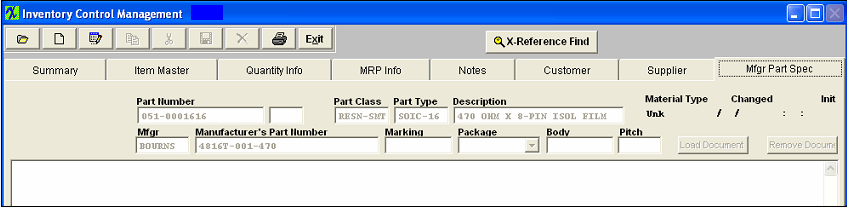
Header Information: Displays the Part Number, Rev, Class, Type and Description selected in the Summary screen. Displayed on the 2nd line is the manufacturer information:Mfg. Name, Manufacturer’s Part Number, Marking, Package, Body and Pitch.
Load Picture or PDF document (Buttons): Used to link the Image Space below to a file on the local hard drive or any other location on the network connected to the Manex Server. To Load a Picture, while in the add or edit mode, the LOAD PICTURE button becomes active. Pressing this button prompts the User to enter the location of a picture file created for this particular inventory part.
Files (pdf.; word; jpeg;, etc.) should be stored in a permanent directory on the server (all users need network security access). The user will define the directory and file for each product in this module, but the information will be available elsewhere throughout the manufacturing module.
After defining the location for the document, the document is available for viewing, as displayed
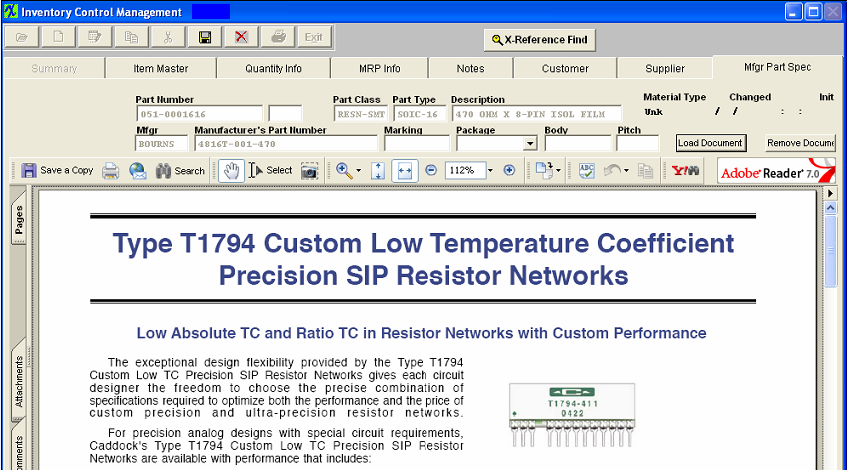
Scroll bars: The bars at the bottom and side of the picture allow viewing of the parts of the image that are outside the window’s display. This allows detail viewing of large drawings.
As soon as you enter the module, Acrobat will load.The user may load a PDF file to the Mfgr Part Spec tab. This allows users access to whole textbooks from within MANEX.PDF files can be drawings, images, CAD files (as printed to a plotter), and multiple pages of mixed text and graphics.Users may also print these PDF files from MANEX.
PDF and Image files:
PDF and Image files used in the MANEX system should be placed in the server, where all users have access to them. These files are used in the Product Data Management, Inventory, Customer and Supplier Contact programs. We suggest that the users create an additional directory, called "Images" under the MANEX System directory on the server. So then under the Main MANEX system directory, there would be the \apps, \dbfs, \images and \reports subdirectory.
If the user is going to make extensive use of the image capability, they may wish to further provide subdirectories under the Image. These might be called "inventory", "PDM", "photos" etc. These files could, in turn, have further subdirectories. For example, under \manex\images\inventory there might be one for each class of part. Or one for make parts and one for buy parts. Under the PDM group could breakdowns by customer.
Such organization will make it much easier to find files when it is time to update them. MANEX can accommodate file path-names up to 100 characters long.
While viewing a PDF document, the user may scan and zoom throughout the document. Items may be copied from it, and the document can be printed from the MANEX program, as long as there is a default printer assigned to the workstation.
|
1.4. How To ..... for ICM Mgmt |
1.4.1. Find an Inventory Control Record |
Entering the Inventory Control Management Module. Depress Inventory Mgt/Inventory Control Managment/Inventory Control Management.
The main screen will appear.
|
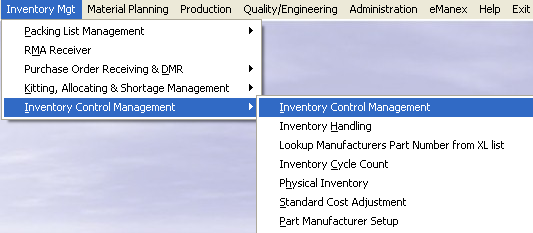 |
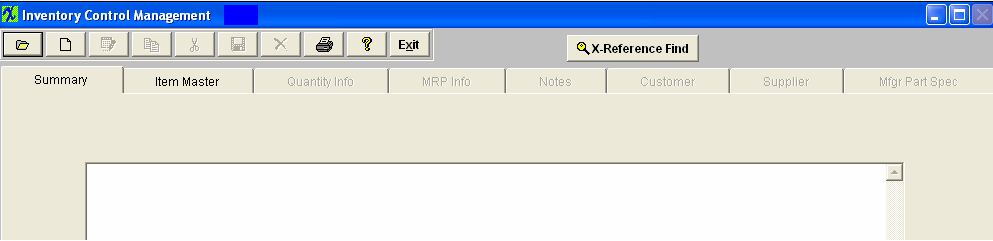
Inventory Find Prerequistes
In order to Find items with certain characteristics or parameters using the Inventory Find Screen, the items must have been entered in the Item Master with those characteristics. Listed below are the pre-requisites for doing 3 different kinds of Inventory Finds:
- Internal items must be in the system to be found.Searches for parts between a Starting number and Ending Part Number must include the prefix and any dashes or special characters.
- A part cannot be found in an “In-Store part find” unless it has been set up with an In-Store warehouse and supplier in the Item Master Quantity Info. screen.
- A Consigned record cannot be found for an item until the Customer has been entered and the item has been given a Customer Part No. in the Item Master Customer Reference screen.
When the user does an Inventory Find, in order to speed up the process the user may eliminate the quantity display.
Depress the Find button. The following screen will display:
Note that the default is for the Summary screen to NOT display the quantity.
|
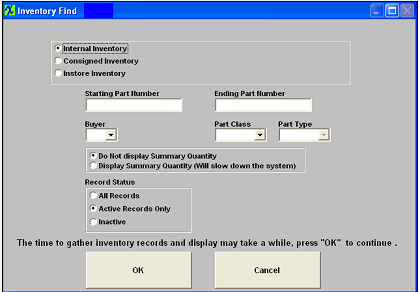 |
If the user wants to have the quantity display on the Summary screen, highlight the desired part number and right click your mouse. The quantity will display for the one part number:
|
 |
If the user wants the entire summary screen to display all of the quantities, then select the Display Summary Quantity radio.
Inventory Find Search Field Definitions
- Internal Inventory – Products, Parts and Assemblies purchased, received, stocked, issued and shipped using standard in-house internal item numbers.These numbers are required and serve as the basis for creation of Consigned and In-Store parts. Just clicking on OK with the default selections shown in the preceding Find Screen will bring up all internal inventory parts in the Item Master Summary screen.
- Consigned Inventory – these records are created every time a Customer Part Number is entered in the Item Master Customer Reference screen. These records are used to enter Customer requirements (Approved Vendor List) and preferences (choices within the Approved Vendor List) for Manufacturers for a given Part Number.It is also where Customer-owned item inventory levels and locations can be seen.
- In-Store Inventory – any internal item can be setup with an In-Store Inventory for a Supplier under contract to supply that item. In-Store items are setup in the Internal Inventory Item Master Quantity Info screen and can be viewed individually in that screen or as a group by supplier in the Summary Screen as the result of an Inventory Find by In-Store Inventory.
- Starting Part Number and an Ending Part Number
- Enter all prefixes, dashes, spaces and alpha charactersto show the entire number.
- Enter first and last Part Number of a series for those and all items numbered between.
- Enter a desired single item in the 1st box and hit return to select only that record.
- Assigned Buyer will bring up all items assigned to that particular Inventory Buyer.The Buyer assignment is made in Part Class and Type System Setup Defaults or in the Item Master.
- Part Class and/or Part Type will bring up only those items that match all entries made.Both Part Class and Part Type must be specified to bring up any items.
- Do not display Summary Quantity radio will by-pass the quantity calculation.
- Display Summary Quantity radio will open up another selection "Total On Hand Quantities"
- Total On Hand Quantities will bring up only items with matching inventory quantities.The user may choose from Total Quantity on Hand, Quantity on Hand > 0, or Quantity on Hand = 0.
- Record Status allows selection of All, Active Only or Inactive Only item records.
Tips on Using the Inventory Find Screen
- Selection of at least one parameter will reduce the time to retrieve the information.
- In-Store Inventory searches require that a Supplier Contract be entered in order to select a Supplier.
- Consigned Inventory searches show Customer-specific information (such as Approved Vendor List information) as well as Consigned Inventory On-Hand Quantities.
- If no information is selected in a Find operation, try using broader or fewer selection criteria.
Combination Searches
Combinations of search parameters may be made for further filtering of the Inventory Item Master files to see item(s) of interest. For instance, selecting the items on the example screen will find all ACTIVE, In-Store Inventory for "Anixter" with the Class “CABLE”.In-Store Inventory Searches are Supplier specific whereas Consigned Inventory searches require entry of a Customer in order to initiate the search.
|
|
Inventory Find Example
The screen shown below is to illustrate Inventory Find results from selecting Internal Inventory, a Part Class of CAP-SMT, a type of 0805, Total On Hand Quantities of Qty on Hand = 0, and Record Status of Active Records Only
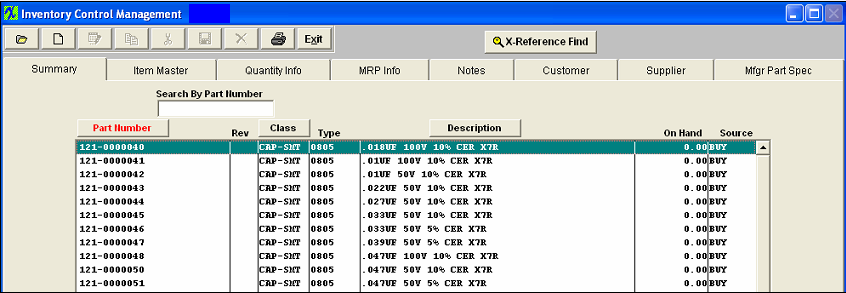
The first tab (Summary Tab) is used to display the results of an Inventory Find. The remaining Tabs will then display detail information for any item selected (highlighted) in the Summary screen. If no items have yet been entered in the system or copying an existing part is not needed, it is not necessary to populate the Summary screen by doing an Inventory Find.
If user has the internal inventory screen open as well as the customers inventory screen open, the customer name will be displayed at the top of the page. So when switching between the two screens user will easily be able to determine which screen they are in.
|
1.4.2. Find an Inventory Control Record Using the X-Reference Find |
|
This button will take the user to a screen, where they can make a selection by what ever criteria needed by choosing (internal part number, mfgr part number, customer part number, supplier part number, or description) to search. |
The following screen will appear:
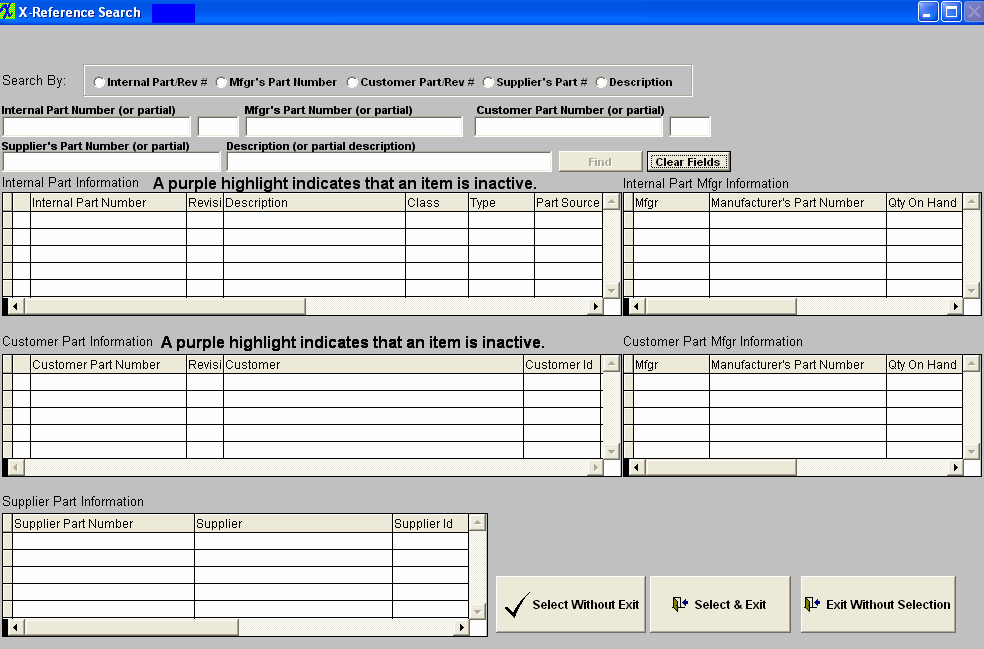
The user can enter partial string and search is not case sensitive. After system finds parts in response to the search (inactive parts will be highlighted in Purple), the user can make a selection by checking on one of the check boxes located at the left. If system was unable to find the exact match, a message will appear up in the right hand corner (in red) to let the user know that the part did not exist in the item master but the following are similar parts found.
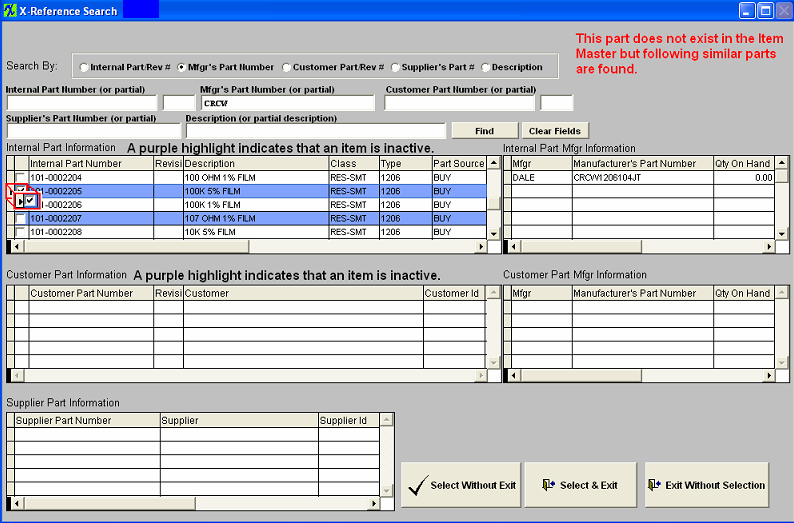
The user can choose to Select Without Exit; Select & Exit; or Exit Without Selection.
To Select user must check the box to the left of the Part Number. If user Selects a Part Number (Internal or Customer Part Number) then depresses the Select and Exit button, the part will be displayed in the Summary Tab as shown below.
|
1.4.3. Add an Inventory Control Record | Following a logical sequence when adding items into the Inventory Master not only eliminates lost time due to continual back-tracking, but ensures that decisions will be made in a sequence which will support the data entry process.
The sequence shown below is for adding products, parts, assemblies, subassemblies or Phantoms to the Item Master after completion of System Setup.
-
Search whether item already exists. Use Find an Inventory Control Part to search the existing database along with the archived database, to verify that the items to be added do not already exist.
-
Verify Available Class and Type. Use Find an Inventory Control Part by Class and Type to verify that the item to be added will fit into the existing Class and Types . Refer to System Setup, Inventory Part Class if a new Part Class or Type and the corresponding Data Entry Defaults must be added.
-
Is Customer available? If the items to be entered will have a Customer-Specific Approved Vendor List (Approved Vendor List), then verify that the Customer is in the database using Customer Information. Add the Customer Information if it is not there.
-
Does Manufacturer exist? Use Part Manufacturer Setup to view existing Manufacturers. Enter new Manufacturers for Buy Items as required and enter the Source for Fabricated items being purchased as outside purchased assemblies. Please refer to procedures below.
-
Add a part/product, etc. Depress the Item Master screen tab. Use the Add button to enter the stand-alone product number or the top level assembly number for a Bill of Material (BOM) MAKE item that must be added. If the product is purchased complete and has no BOM, enter it as a BUY item. Enter your Password.
-
Enter information. Enter all basic item information in the Item Master Screen.
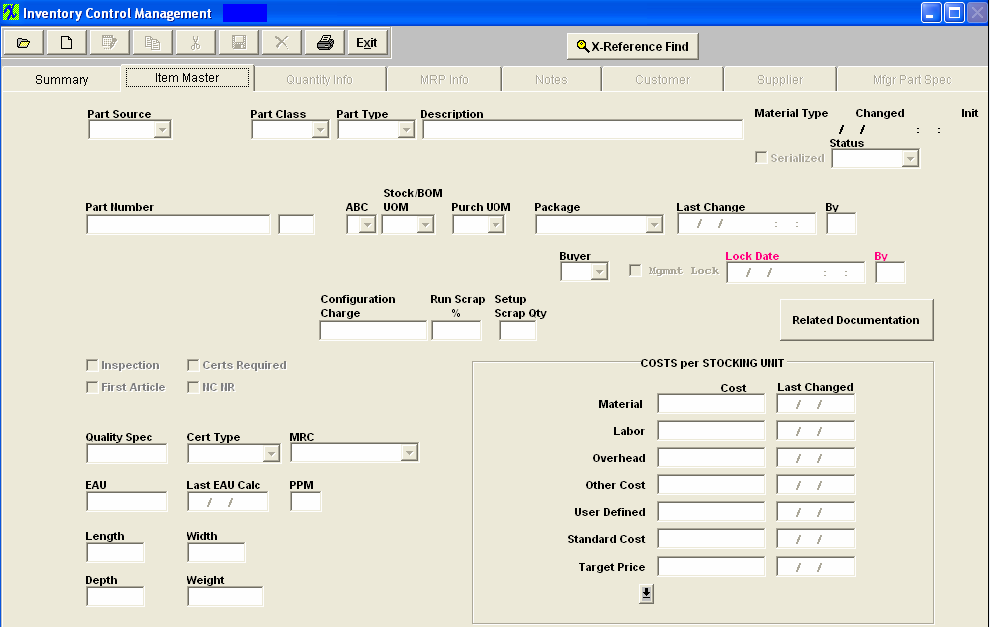
Part Source: This field is hard coded in the system. Select BUY for purchased parts and assemblies, MAKE for an item made in-house (assemblies and sub-assemblies) and PHANTOM for a number used to define a collection of items that does not exist as a separate assembly built on a Work Order (ship kits, upgrade packages, spares kits, etc.).
|
 |
-
Phantom/Make: If the Part Source above is a MAKE and this box is checked, the system will treat the part as a Phantom when the sub-assembly components are called up during the Kitting process BUT as a Make part for a stand alone assembly when the part is NOT a sub-assembly.
-
Make/Buy: Make/Buy is setup to allow users to have a part in the system that they wished to BUY but also keep documentation within the system (BOM). If the Part Source is a MAKE and this box is checked, the assembly could also be purchased from an outside source. If a Part is marked as Make/Buy within Inventory the MRP will only give PO Actions and that product will not be available for selection within the Work Order management module. If the part souce on a product is originally setup as a MAKE the user will be allowed to edit the record and change the part souce to Make/Buy. For further details see Article #3289 .
Part Class: This is a general part, product or item classification that must be selected from the drop-down box. If an appropriate choice is not available when entering a new item, see System Setup/Inventory Part Class to add a part class (examples of Part Classes are BATTERY, DIODE, FUSE, FILTER, IC-SMT, CAP-SMT, RES-TH, etc.)
|
|
Part Type: Type is a sub-classification of Part Class. If an appropriate choice is not available when entering a new item, see System Setup/Inventory Part Class to add a Part Type (examples of Part Types for the Class CAP-SMT would be 0402, 0603, 0805,1206, 1210, etc.)
To re-sort the order the part types are being displayed in the pulldown See Article #214
A user does have the option of leaving the Part Type blank, however if this option is selected the prefix for the part number will be omitted. There is no reason to enforce part type if a user doesn’t want to have that kind of detailed classification. If the user decides to leave the Part Type blank they will receive the following message:
At this point they have the option to continue or go back and pick a Part Type.
|
|
Description: There are 45 characters available to put descriptive data about the item being entered that is not already in Part Class and Part Type. For instance, in the previous figure the Part Class and Type already show that it is a CAP-SMT. 0603 so this information need not be repeated in the Description. We suggest when entering the description, that you be consistent with your capitalization and punctuation. Some of the screens and reports can be sorted by description so the more consistent you are the easier it will be to use the system in the future.
 |
If the Inventory Material Type is set to "Auto" (within the Material Type Setup), everytime the user modifies the AVL material type, the program will update the Inventory Material Type automatically, if the control is set to "Manual", then the user will be able to modify the Inventory Material Type from the Material Type pulldown. Keep in mind that the program will NOT validate if the material type in Inventory and AVL levels are in sync.
The AVL Material Type is carried forward for the consign part when the consign part is first added to the system or when new AVL was added to the internal part and the user elects to add this AVL to the existing consign parts. If the user later changes the Material Type on the internal part, the change is NOT carried over to the consigned.
|
Serialized: Check this box if the parts need to be tracked with serial numbers. This box will allow you to mark either Make or Buy parts as Serialized.
Note :Users MUST have special access with the Security module for the Inventory Control module to modify the serialized checkbox.
When the serialized checkbox is checked for an existing BUY part and there is open kit records in the system the following message will appear:
|
|
When serialized checkbox is checked for an existing MAKE or BUY part and there are open work orders or inventory against it the following message will appear: |
 |
If user checks the Serialized box and receives the following message, this means that the "Do not use serial number tracking" checkbox is checked within SFT Setup.
|
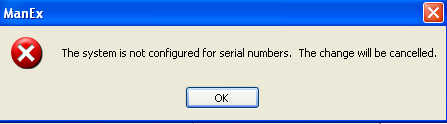 |
Depress Yes and the following screen appears
If user doesn' t know the available work orders which have FGI qty, he/she can double click the work order number field (red box).
|
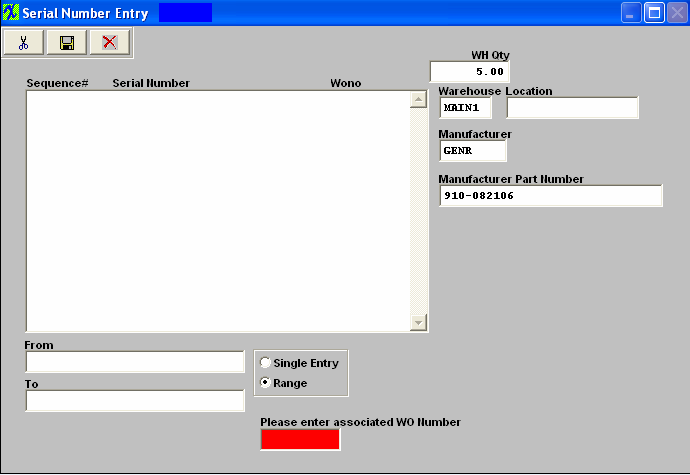 |
A list with work order numbers and FGI qty for that part number will appear (as shown below). The user then can select one for entering serial numbers.
|
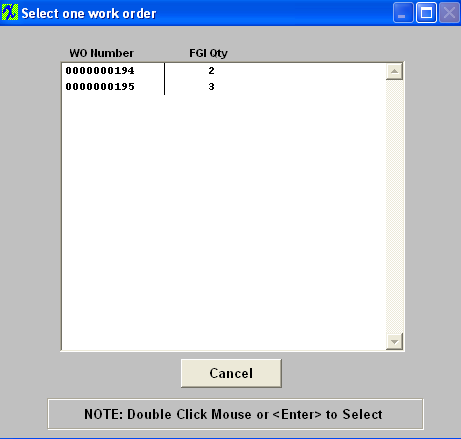 |
The users can enter the serial numbers by clicking "single" or "range" option.
Once all the serial numbers have been entered for all work orders the completed screen will look like this.
Depress the Save button.
|
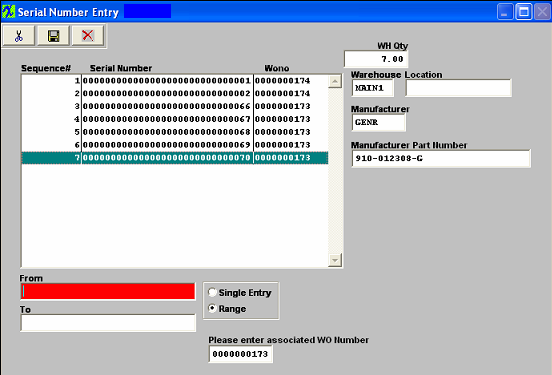 |
The following message will appear reminding the user that they will need to assign serial numbers to the balance of the work orders in order to transfer to FGI.
|
 |
Status: All items must be Active in order to buy, receive, issue, Invoice, or ship. Use Inactive Status to remove items from use that have already had transactions against the Part Number. Use the Delete button to delete Items with no transactions for further detail see Article #3143. Changing from Inactive to Active status can be used to release items from Engineering. The system will not allow you to change the status from Active to Inactive if there is WIP for that item. This will prevent the possibility of qty on hand being returned to an inactive part upon dekitting.
|
|
Part Number: The item/Part Number is a unique identifier for every Item Master record entered into the database. Part Numbers can be auto-assigned to all items or all items except Make assemblies or all items including Make Assemblies. Use of a 3-digit prefix for each different Part Type may be setup in System Setup Number System to work with auto or manual numbered parts and assemblies..
ABC: This field allows further grouping of items (parts, products or assemblies) into classes according to: 1) the percent of the total inventory their current stock value represents.2) the percent of total inventory their forecasted value will represent.3) a manual classification based upon chosen factors. If an appropriate choice is not available when entering a new item, see System Setup ABC Types to add a new Type.
|
|
Stock/BOM UOM: This is the Unit Of Measure (Foot, Inch, Each, Gallon, Quart, etc.) that is used to specify how much of Item displayed or being entered is issued from Stock or is used in a Bill of Material for an assembly. Note that in ManEx, the Unit of Measure Each is treated as being an integer unit. That is, you can only have one or multiples of an Each, but not a fraction of an each. You can have fractions of inches, feet, pounds, ounces and any other Unit of Measure. Although you can use fractions in the Bill of Material, the User can't kit fractions of each parts. ManEx will round up to the nearest whole number. The proper way to approach the situation where the kit amount is expressed in fractions, is to use any Unit of Measure other than Each. If an appropriate choice is not available when entering a new item, see System Setup/Unit of Measure & Conversion to set up a new Unit of Measure.
ManEx DOES NOT recommend users to change the Unit of Measure while there is qty on hand within the system. See Article #3414 for further detail.
|
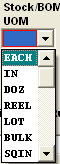 |
Purchase UOM: This is the Unit Of Measure (Foot, Inch, Each, Gallon, Quart, etc.) that is used to specify how the Item displayed or being entered is purchased from a vendor. If an appropriate choice is not available when entering a new item, see System Setup/Unit of Measure & Conversion to set up a new Unit of Measure.
ManEx DOES NOT recommend users to change the Unit of Measure while there is qty on hand within the system. See Article #3414 for further detail.
|
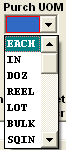 |
Package: Specifies the way in which the Item is packaged when it comes from a vendor (ie. Reel, Tray, 6-Pak, Ream, Individually, etc.) If an appropriate choice is not available when entering a new item, see System Setup/Part Package to set up additional part packaging. |
|
Buyer: All items with the same Buyer's initials in this field will be grouped together for display or printout of the Material Requirements Planning Action List when filtered or displayed by Buyer. If an appropriate choice is not available when entering a new item, see System Setup/Inventory Buyer Setup to set up additional buyers. |
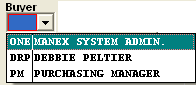 |
Last Change |
This automatically defaults in the date and time of the last change made to this part number in the item master. Once the change has been saved.
|
By |
This automatically defaults in the initials of the user that made the last change to this part in the item master. Once the change has been saved.
|
Configuration Charge |
This is NOT a part of the standard cost total, as discussed below.It is a specific cost used with the ManEx Order Configurator module and represents any additional cost over and above the standard cost total.
|
Run Scrap % |
This amount is added to the exact quantity used on an assembly to provide an overage to cover losses during running due to predictable machine and human losses.
|
Setup Scrap Qty |
Setup losses may be added to the BOM requirement and Run Scrap for an item.For instance, an auto-insertion machine may use extra parts for alignment checks. |
Mgmt Lock: Only Supervisors or users with Lock/Unlock rights within the Security/User rights can modify this checkbox. If locked, all users can access the screen, but only supervisors or those with Lock/Unlock rights will have the capability to bypass the lock and make changes, while the Inventory Part is still in lock mode. The reason we do NOT force the user to unlock the Inventory Part before making any changes, is to protect it from anyone else making changes while the 'authorized" user is making their changes.
Lock Date: This automatically defaults in the date and time the lock was implemented to this part number in the item master.
By: This automatically defaults in the initials of the user that implemented the lock to this part number in the item master.
|
|
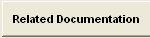 |
Depressing this button will give the users the ability to scan any related documents directly into the ManEx system and attached the document directly to the item in the ICM Module. For further detail see Article #2396. If this button is displayed in Red there is Related documents attached. |
Inspection Required/ Quality Spec |
Checking the box will cause the item to require inspection to whatever Quality Spec. shows in the Quality Spec box. The Quality Spec appearing in the box is entered in System Setup in the Inventory Part Class & Type Setup.Any Part Type in a particular Part Class can have Inspection Required turned on or off.
|
Certs Required/ Cert Type: Checking this box will allow selection of Cert Type. Cert Type choices are Receive, Ship or Both. A typical Cert would be UL or CSA Certification on wire. Check the box and then depress the down arrow for the types to display. Select the desired type: Receive - Requires user to check the "Certificate Required" box has been Done at Receiving. Ship - Requires user to check the "Certificate Required" box on Packing List/SHipping. Both - Requires user to check the "Certificate Required" box at both Receiving and Packing List/Shipping. |
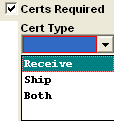 |
MRC |
This is to inform the users which items are Low Risk, High Risk, etc.This will need to be defined in System Setup Material Risk Code Setup.
|
EAU/Last EAU Calc |
These fields display the Estimated Annual Usage, if applicable and the last date that the EAU was calculated.
|
PPM |
This field is a data entry field and is not currently involved in any calculations or used anywhere else within the system at this point. It is planned to be used in the future to calculate the component level of PPM and then update the assembly PPM within the routing module.
|
The dimensions such as Length, Width, Depth and Weight are entered in this section |
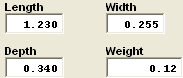 |
Within Security there is the option to allow users to have access (all or partial) to the Inventory Control Management module. Then within those Inventory Security settings there is a provision for optional additional privileges, including the ability to make changes to the Standard Costs. Only a user with these rights will be allowed to change any of the costs listed below. Also, none of the cost listed below will be editable if there is inventory or WIP on hand.
Material Cost
|
For BUY Parts: This is the purchase price of the BUY part. For MAKE Parts: The sum of the STANDARD COSTS of BUY parts in the assembly. Whether or not setup scrap is included is a system setup option |
Labor Cost |
For BUY Parts: If the user wishes to include any preparation labor costs associated with a BUY part, like crimping, tinning testing. etc., those costs may be included here. For MAKE Parts: The user may include the labor associated with building the assembly.
|
Overhead Cost |
For BUY Parts: Any additional costs associated with the labor, such as heating, lighting, etc., that the user may wish to include in the cost of the inventory value. For MAKE Parts: Any additional costs associated with the labor, such as vacations, sick leave, meeting times, etc., that the user may wish to include in the inventory value. |
Other Cost |
For BUY or MAKE Parts: This is up to the user to decide if there are any other costs that should be absorbed in the inventory value. |
User Defined Cost |
For BUY or MAKE Parts: This is a field where a user may define the field name and include any optional costs. |
Standard Cost |
The STANDARD COST of an item is a calculated value determined by the sum of individual costs. These individual costs may be in any combination of the Material, Labor, Overhead, Other and User Defined costs. Each of the individual costs should have their own account number in the Inventory setup, and those accounts will accrue the costs when material is added to inventory.
If ManEx Accounting is neither installed nor active, then there is no value other than reference in including values in these fields.
Important Notice: It is very important to have standard costs (as determined above) in place for any part entering inventory. ManEx allows users to enter a standard material cost at the time of purchase, if one is not already entered. Without accurate cost data, the iventory value could be next to useless, and major variances would show in Purchase Price, Configuration and Manufacturing Variances.
|
Target Price |
This field is currently only a data entry field and will be reflected in the Purchase Order module for "BUY" or "MAKE/BUY" parts. This field is not editable for "MAKE" or "PHANTOM" parts. NOTE: To assign prices to products ("MAKE" parts), ManEx suggests using the Sales Price List Information module. This module allows users to enter prices by product and by customer so different customers can have different prices. This price will default into the sales order, but is still editable within the Sales Order module.
|
Weighted Cost |
If the Part Source is a BUY, the last five purchases expressed as a weighted average will appear here.
|
The completed Item Master screen will appear:
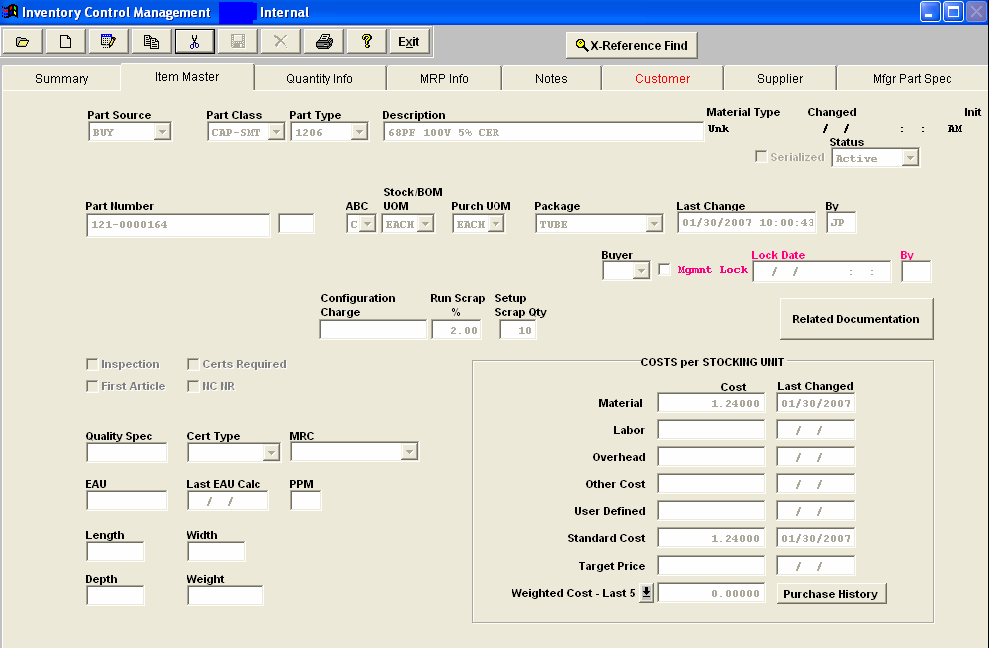
Click on the Quantity Info tab and the following screen will appear. This screen is split. You must enter in the manufacturer information and click save. Then the system will allow you to add the warehouse and location information.
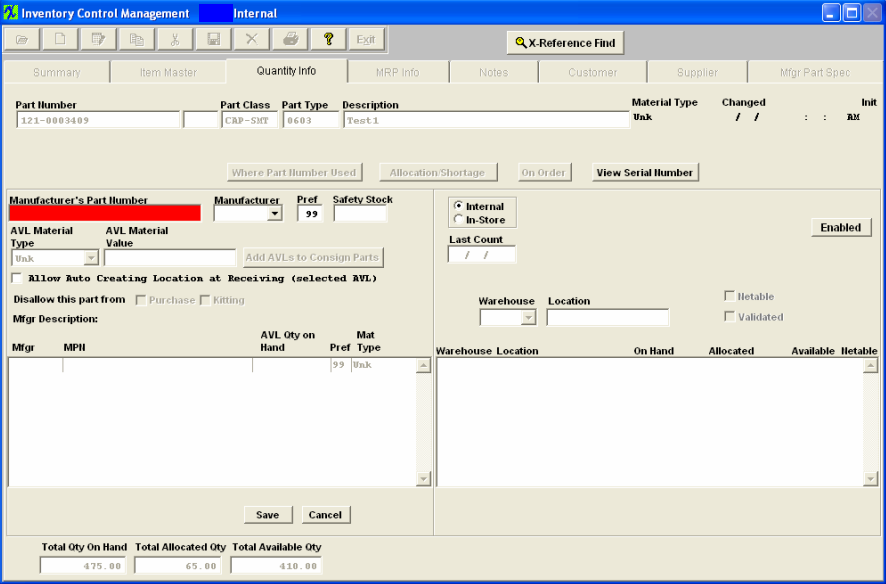
If the Inventory Material Type is set to "Auto" (within the Material Type Setup), everytime the user modifies the AVL material type, the program will update the Inventory Material Type automatically, if the control is set to "Manual", then the user will be able to modify the Inventory Material Type from the Material Type pulldown. Keep in mind that the program will NOT validate if the material type in Inventory and AVL levels are in sync.
The AVL Material Type is carried forward for the consign part when the consign part is first added to the system or when new AVL was added to the internal part and the user elects to add this AVL to the existing consign parts. If the user later changes the Material Type on the internal part, the change is NOT carried over to the consigned.
|
 |
Enter Manufacturers Part Number: Type in the manufacturers part number.
Enter Manufacturer: Choose a mfgr from the pull down. If no Manufacturer is specified use GENR (Generic). If no information is entered in the Quantity Info screen, GENR will be added by the system automatically when saving the item.
System will not allow users to have duplicate AVL/MPN combinations. If user has same mfgr and mfgr PN but different material types, we suggest that the user create a new AVL with a dash (or any other symbol) and use that designation to transfer to the UNK material type parts or create a different location for the same part, but have it be non-nettable, making it ineligible as a source for MRP.
|
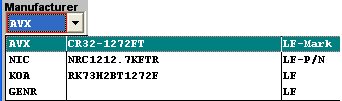 |
Enter Pref: Type in the Preference. (Whether this is a preferred manufacturer and if so the ranking or preference). If no preference code is added, 99 will be assigned automatically. All items will be at the bottom of the preference list unless the user assigns another number to it. See Article 943 for more information. The Pref Code is carried forward for the consign part when the consign part is first added to the system or when new AVL was added to the internal part and the user elects to add this AVL to the existing consign parts. If the user later changes the preference code on the internal part, the change is not carried over to the consigned part.
Enter Safety Stock: Enter in a qty that you want kept on hand for this specific AVL. (User may have safety stock for more than one AVL in a given part number). This qty is in addition to the MRP demands. (Note: Safety stock is calculated at the AVL level not part # level). ManEx will ensure that there is always the safety stock qty on hand regardless of the MRP demands. Please see Article #2331 for more detail.
If this option is check marked then the users will be able to automatically create any new Location for this part within the PO Receiving module. Note: Users MUST have special access within the Inventory Control Security setup module to modify this checkbox. There is also a similar check box within System Setup, Warehouse Setup, this will also have to be marked for the warehouse in order for this option to be applied. |
 |
Depress the save button located at the bottom of the screen. You now have the option of entering an AVL Material Type (as described below) for the existing mfg., enter in another manufacturer part number or creating a warehouse for the existing manufacturer.
AVL Material Type: Choose from the pull down, Unk, LF-P/N, LF-Date, LF-Mark, RoHS-P/N, RoHS-Date, RoHS-Mark. See Article 2267 for definitions. These choices have been defaulted in. Customers may establish the logic by which the material type for the parts are established by the material types at the AVL level in System setup/Material Type Setup.
The AVL Material Type is carried forward for the consign part when the consign part is first added to the system or when new AVL was added to the internal part and the user elects to add this AVL to the existing consign parts. If the user later changes the Material Type on the internal part, the change is NOT carried over to the consigned part.
If the Inventory Material Type is set to "Auto" (within the Material Type Setup), everytime the user modifies the AVL material type, the program will update the Inventory Material Type automatically, if the control is set to "Manual", then the user will be able to modify the Inventory Material Type from the Material Type pulldown. Keep in mind that the program will NOT validate if the material type in Inventory and AVL levels are in sync.
|
|
AVL Material Value |
This is a text field for a given material type. For example: if the material type was "LF-Date" user could enter the date code in this field. The Value could be different of various AVL's with the same material code. This fields is a reference only field and is optional. |
 |
If the users add new AVL's to the Internal part number, they can add it to a Consigned part number by depressing this button. A screen will appear and within that screen they can select which AVL they want to add to a Customer consigned part number. |
 |
There are situations where the Users customers will allow them to use up non-conforming inventory, but cannot replace the same AVLs. So, at the AVL level, we added two logic fields that would signify that the AVL is NOT to be purchased and/or kitted. In such a circumstance, it is NOT appropriate to delete the parts, but neither can they be purchased for future requirements. Likewise, they may want to avoid kitting so you would check these boxes to "Disallow this part from Purchase and/or Kitting". For special circumstances, the user can override the block from kitting if their customer permits it. For further information on how to use these fields effectively refer to Article #2329. For information on how these fields affect MRP refer to Article #3211 . (See the non-nettable function for the warehouse level described below).
|
When the "Disallow Purchase" is checked ON - ManEx will check if any Safety Stock (SS) is entered, if so the following prompt will be displayed and will un-check the checkbox upon depressing the OK button.

When the "Disallow Purchase" is checked OFF - ManEx will check and if "Disallow Kit" is ON the following prompt will be displayed and will revert the change to leave "Disallow Purchase" ON and leave "Disallow Kit" ON.

When the "Disallow Kit" is checked ON - ManEx will check if any SS is entered, if so the following prompt will be displayed and will un-check the checkbox upon dpressing the OK button. If SS is zero, no message will be displayed and ManEx will auto check "Disallow Purchase"

When the "Disallow Kit" is checked OFF - ManEx will check and if "Disallow Purchase" is still checked ON the following message will be displayed giving the user the option to uncheck the "Disallow Purchase" but is not required.

To create a warehouse, depress the Add button (located under the right hand section of the screen)
Enter Warehouse: Select the Warehouse from the pulldown. In ManEx, the default warehouse is Main 1. If the User has accounting, this would equate to the Raw Materials Inventory. Many Users want to separate their Raw Materials and Finished Goods Inventories. So, if this is a Make part, the User may want to select the finished goods inventory warehouse. Some Users also set up separate warehouses and general ledger account numbers for In-Stores and Consigned. If no warehouse is selected upon saving the record the system will deafult in the default warehouse setup in System Setup Warehouse Setup.
|
|
Enter Location |
The location entered is where the parts will be stocked and/or located within the warehouse. System will NOT allow users to add same locations with leading spaces. This field is flagged as “Read Only” for an MRB whse item. (Meaning you can not create new locations for MRB whse). Due to the fact that the MRB location is usually generated from a PO rejection – and if so, it needs to retain that link back to the original PO information and that is populated into the location field and is not editable. If you move into MRB via Inventory Handling then no location information is populated, but you are still unable to edit it. |
Netable box |
Remove the check mark from Netable only if the item entered is NOT to be considered as Supply when running Material Requirements Planning. If the MRB whse is being added the Netable field is disabled and unchecked.
|
Validated box |
This is for reference only and does not affect any other modules in Manex. This is simply for the users to check that the part being added has been verified as appropriate.
|
Depress the Save button at the bottom of the screen.
The completed Quantity Info screen looks like this:
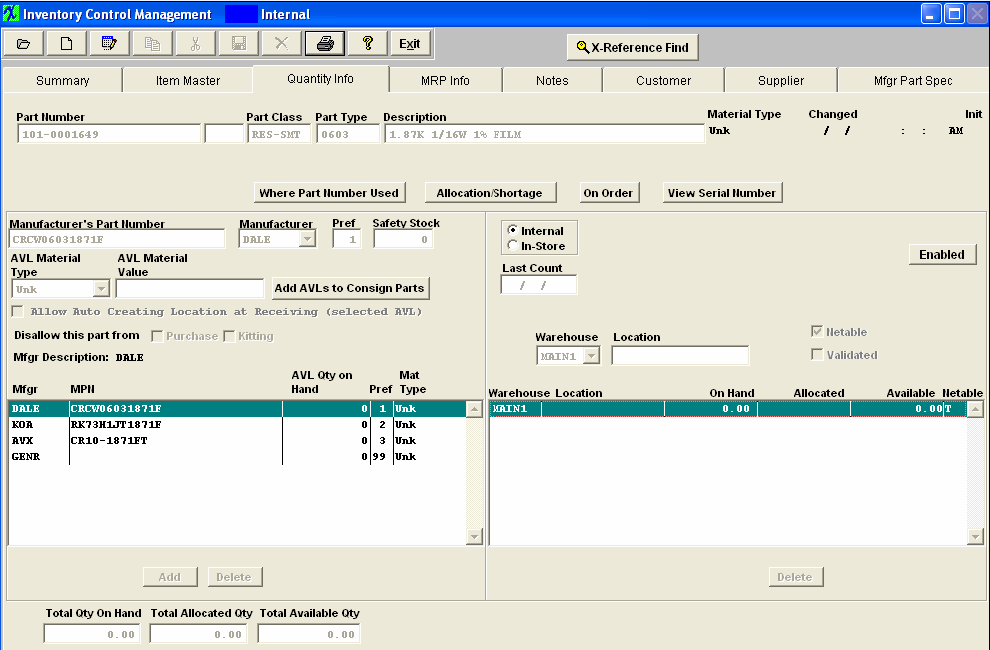
Material Requirements Planning Information: Depress the MRP tab and the following screen will appear. Enter the Material Requirements Planning information for the item.
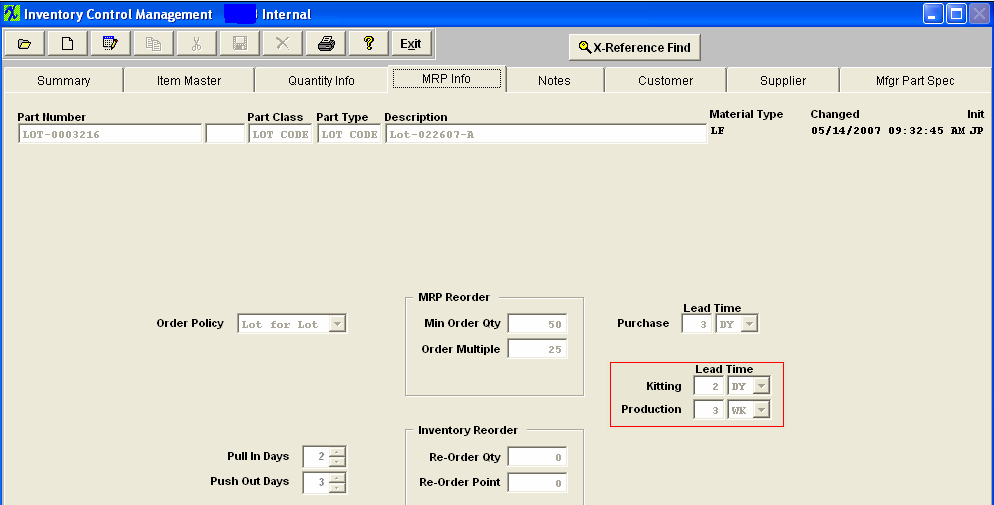
Order Policy: This field is used to select the method used by the Material Requirements Planning module to combine requirements for this item in creating Planned Purchase Orders (POs). For instance if the choice is (Lot for Lot), the Material Requirements Planning module will plan one PO for the total requirements on a daily basis. If the choice were (Weekly), the Material Requirements Planning module would combine all the requirements each week and plan one PO on the first requirement day for the entire weeks needs.
|
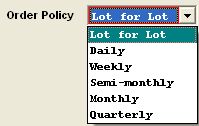 |
Min Order Qty |
This is the smallest number of the item that can be ordered from the vendor in one PO. For instance, Surface Mount components on a reel usually have a minimum order of 1000 items or more.
|
Order Multiple |
This field defines the even multiples of the Unit of Measure in which an item must be purchased. For example, 16AWG Wire might be only available in even hundreds of feet on a spool in which case the Material Requirements Planning module would plan a PO for the next higher even hundred above the requirement.
|
Purchase Lead Time: Purchase of all items other than In-Store items requires that the PO be placed a minimum number of days before the actual requirement. This Lead Time requirement is what tells the Material Requirements Planning module how many days before a requirement to plan a PO. Changing the leadtime of a Buy part will NOT change the due date in MRP, only the date to take action.
|
|
Kitting Lead Time: This field will be displayed only if it is a Make or Phantom part. This Lead Time requirement is what tells the Material Requirements Planning module how many days to allow for kitting. Changing the kitting leadtime of a Make or Phantom part will change the due date in MRP. A TRUE phantom does NOT require any lead times and should be left blank. BUT . . . if for some reason you need to add a lead time for a TRUE phantom ManEx does have the capability.
Production Lead Time: This field will be displayed only if it is a Make or Phantom part. This Lead Time requirement is what tells the Material Requirements Planning module how many days to allow for production. Changing the production leadtime of a Make or Phantom part will change the due date in MRP. A TRUE phantom does NOT require any lead times and should be left blank. BUT . . . if for some reason you need to add a lead time for a TRUE phantom ManEx does have the capability.
|
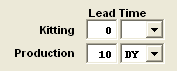 |
Pull In Days |
When PO due date is more than this number of days too late for an Material Requirements Planning module requirement, a PO Due Date change Action Notice will be generated. Note: These parameters may be thought of as filters for MRP Order Actions when the requirement dates for the parts changes. See attached Document <<pullin-pushout discussion.docx>>.
|
Push Out Days |
When PO due date is more than this number of days too early for an Material Requirements Planning module requirement, a PO Due Date change Action Notice will be generated. Note: These parameters may be thought of as filters for MRP Order Actions when the requirement dates for the parts changes. See attached Document <<pullin-pushout discussion.docx>>. |
Re-Order Qty |
This is the number of the item to order at time of order.
|
Re-Order Point |
To use a Min/Max system rather than Material Requirements Planning for reordering this item, enter the quantity at or below which the item should be replenished. Print the Inventory Material Reorder List report to show items which have dropped below re-order point minimums.
|
The completed MRP screen would appear as follows:
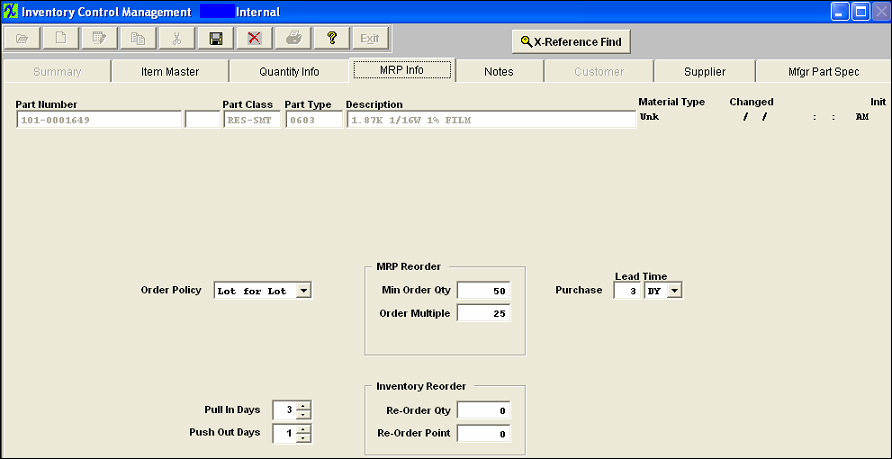
Notes Tab |
Depress the Notes tab. Add Notes by clicking the Edit Action Button and typing in manually. Use Utility/ Copy or Ctrl+C and Utility/ Paste Ctrl+V to copy and paste from the existing Item Notes to new Item Notes.
|
Depress the Customer tab. Depress the Edit button and the following screen will appear:
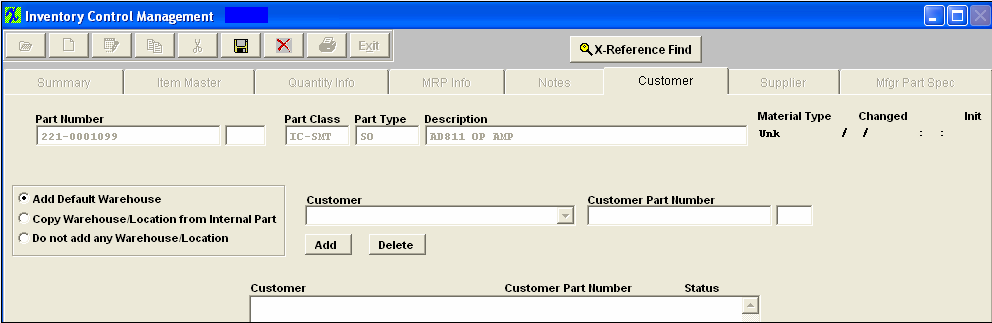
Depress the Add button (under to the Customer Field) to select a Customer. A customer list will appear. Select the customer desired. For every Customer that requires an Approved Vendor List, selection of these items Manufacturer Part Numbers list (in the Quantity Info Screen), a Customer Part Number must be entered in the Customer Screen. Enter a Customer Part Number and Save. When you create a Customer Part number (Consigned) within the system, user has the option to Add Default Warehouse, Copy Warehouse Location from Internal Part, or Do not add any Warehouse Location upon creation. Note: System does not allow you to enter more than one part number per customer to the same internal part, (for more detail see Article #2389).
|
|
Depress the Supplier tab, depress the Edit button and then the Add button (under the Supplier Field) to select a Supplier, enter a Supplier Part Number and Save.
|
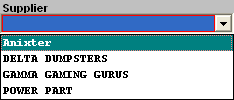 |
The completed Supplier screen would appear as follows:
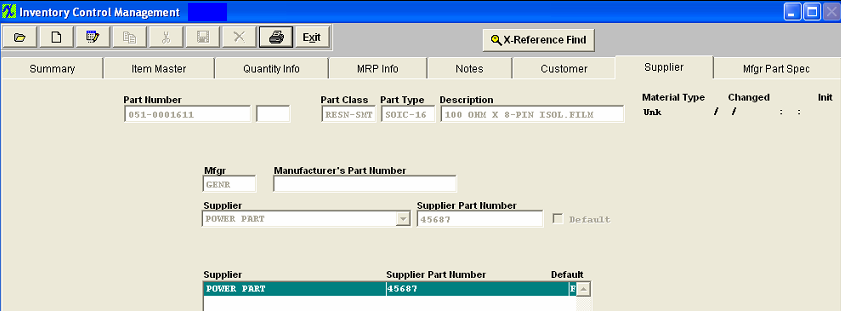
Manufacturer Part Specifications |
Depress the Mfgr Part Spec tab. Add the Marking and Package, Body and Pitch, if desired. Add Manufacturer Part Spec drawings, images or .pdf file by clicking on Load Document and linking to the desired image or pdf file. The completed screen will appear:
|
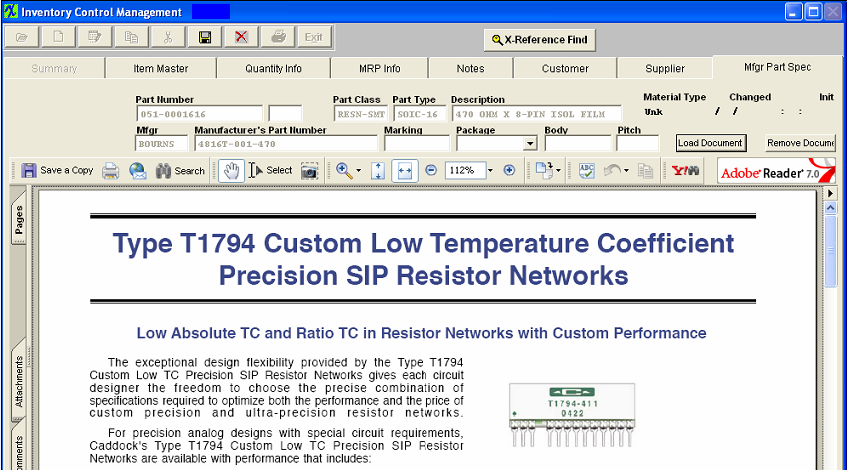
Once all information for new record has been entered, depress the Save button to save the record, or the Abandon record button to abandon record.
|
1.4.4. Copy or Edit an Inventory Record | Copy a Part Number
To copy an existing part, Find the part you want to copy, using Find an Inventory Control Record. Highlight that part number and then depress the Item Master tab. Depress the Copy icon at the top of the screen. The following message will appear.
The following message will appear. Depress the "Yes" button. Enter your password.
|
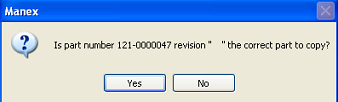 |
The following selection menu will appear:
Selecting Copy & Autonumber will create a copy, and open the Item Master Screen. The fields which may be edited are highlighted.
|
|
Selecting Copy & Edit Number/Revision will bring up a reminder message:
Depress the Ok button.
The Item Master Screen will open. All of the fields which can be edited, including the part number and the revision number, will be available for editing.
|
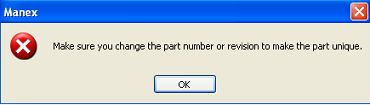 |
Selecting Copy & Increment Revision, will cause the system to assign the same part number and the revision number will automatically increment by 1. In the Item Master all the fields which may be edited are highlighted, as illustrated below:
Edit an Inventory Item
Find an Inventory Control Record Note: How to remove or inactive an Inventory record see Article #924 Status defintion.
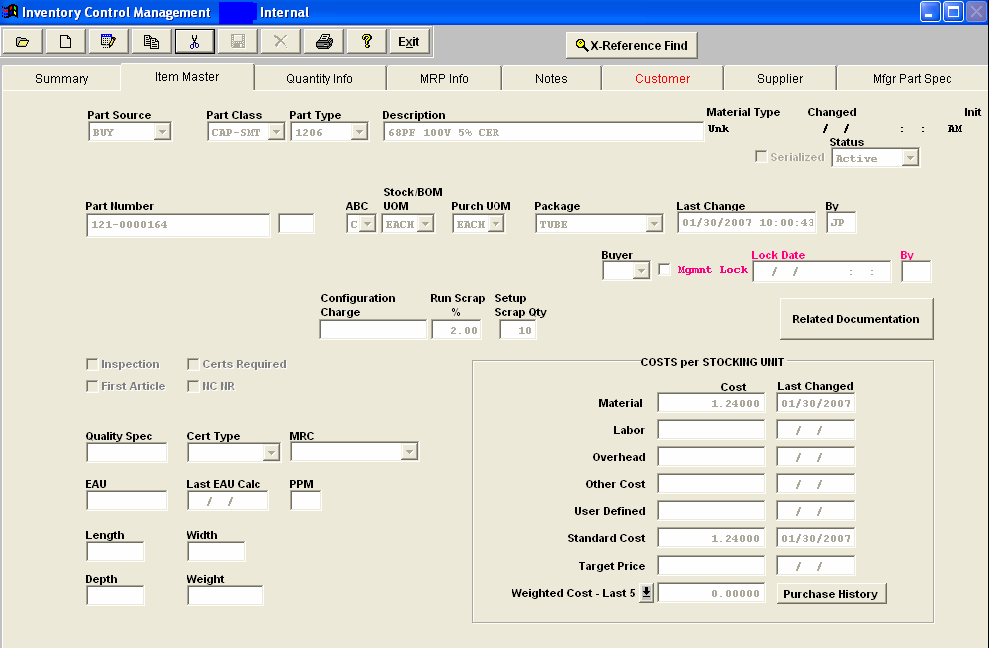
Depress the appropriate tab which needs to be modified. Depress the Edit button. Enter your Password. The items displayed in Black may be edited:
ITEM MASTER TAB
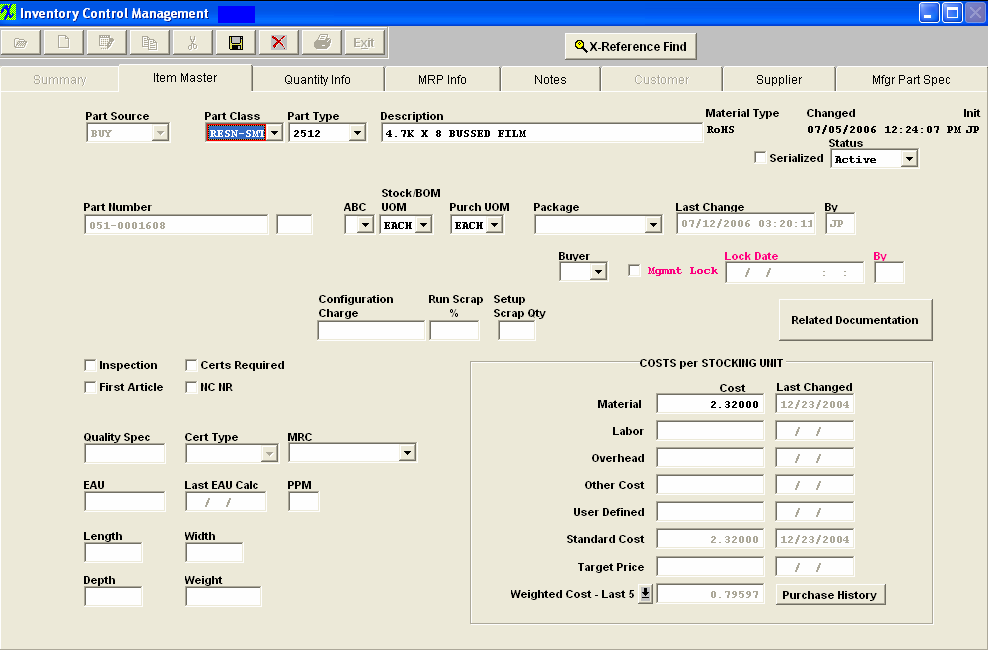
Item Master tab |
The following fields are all editable: Part Class, Part Type, Description, Material Type, Serialize box, Status (for status defintions see Article #924), ABC code, Stock / BOM UOM, Purchase UOM, Package, Buyer, Mgmt Lock, Configuration Charge, Run Scrap %, Setup Scrap Qty, Costs (see NOTE below), Inspection box, Certs Required box, First Article box, NC NR, box, MRC, PPM, Length, Depth, Width, & Weight.
ManEx DOES NOT recommend users to change the Unit of Measure while there is qty on hand within the system. For further detail see Article #3414.
If the part souce on a product is originally setup as a MAKE the user WILL be allowed to edit the record and change the part souce to Make/Buy and/or Phantom/Make. For further details see Article #3289 .
After all these criterias are passed, if the part has quantity on hand, the user has to enter the serial numbers to match the quantity on hand.
Note re Editing Standard Cost: You will need a Supervisors Password to change the Standard Cost. The best procedure is to use the Standard Cost Adjustment module. The Standard Cost Adjustment module will update the Inventory records AND will create the appropriate accounting entry. If you edit the cost in this screen, a manual accounting entry will be required.
|
Changing a non-serialized part to a serialized part
BUY - If a user changes a non-serialized BUY part to a Serialize part the system will check. *If the part has allocated qty, (user has to un-allocate parts before the system will allow user to check the "Serialize" box). *If the part has any OPEN kit (kit in process), (user has to de-kit or close kit before system will allow user to check the "Serialize" box). *If the part has un-reconciled PO (user has to reconcile all receipts before system will allow user to check the "Serialize" box).
MAKE - If a user changes a non-serialized MAKE part to a Serialize part and the part has quantity in FGI the following message will appear:
NOTE: User is NOT allowed to change a Make/BUY part from a non-serialized part to a serialized part if there is qty on hand.

Depress the Yes button and the following screen will appear, which is the Serial number entry screen: The WH Qty is displayed in upper right hand corner. This is the number of serial numbers that need to be assigned.
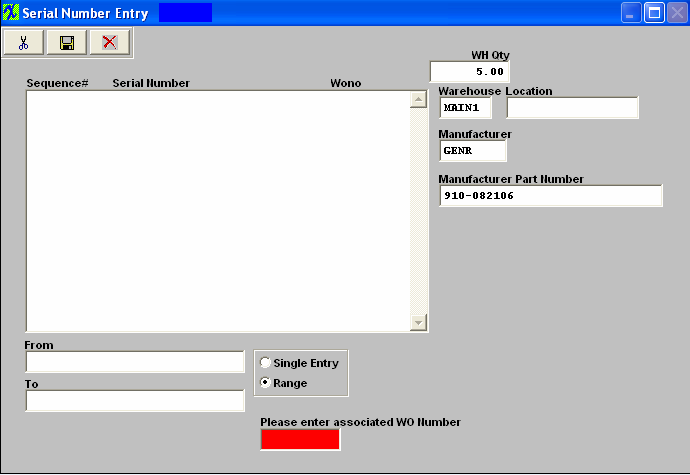
If user does not know the available work orders which have FGI quantity, they can double click the work order number field (displayed in Red), and a list with work order numbers and FGI qty for that part number will pop up and the user can select one for entering serial numbers.
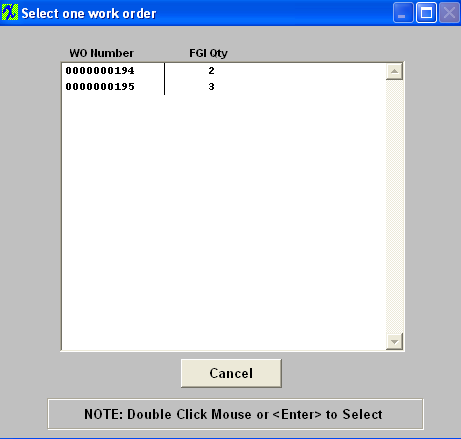
When user returns to the SN Entry screen they can leave the SN option at "Range". The system will default in the full Qty on Hand amount for the Serial Numbers, but if the user manually edits the ending serial number before entering the system appears to work okay, then when the user adds the remaining serial number for the last work order the system will default the correct amount of remaining serial number to be assigned.
Changing a Lot Coded Part to a Non-Lot Coded Part or Vis-Versa - ManEx does NOT recommend users changing parts from Lot Coded to Non Lot Coded or vis-versa unless it is absolutely necessary.
If a user is changing a Non Lot Coded part to a Lot Coded part they will receive the following message informing the user that "Dummy" lot codes will be setup for existing oh hand quantities and asking the user if they would like to continue.
If a user is changing a Lot Coded part to a Non Lot Coded part they will receive the following message informing them that any existing Lot Code information for this part will be deleted from the system if these changes are saved and asking the user if they would like to continue.
If a user is changing a Lot Coded part to a Non Lot Coded part or vis-versa and the part is also serialized and if there is qty on hand, user will receive the following message and will be unable to save the change.
QUANTITY INFO TAB
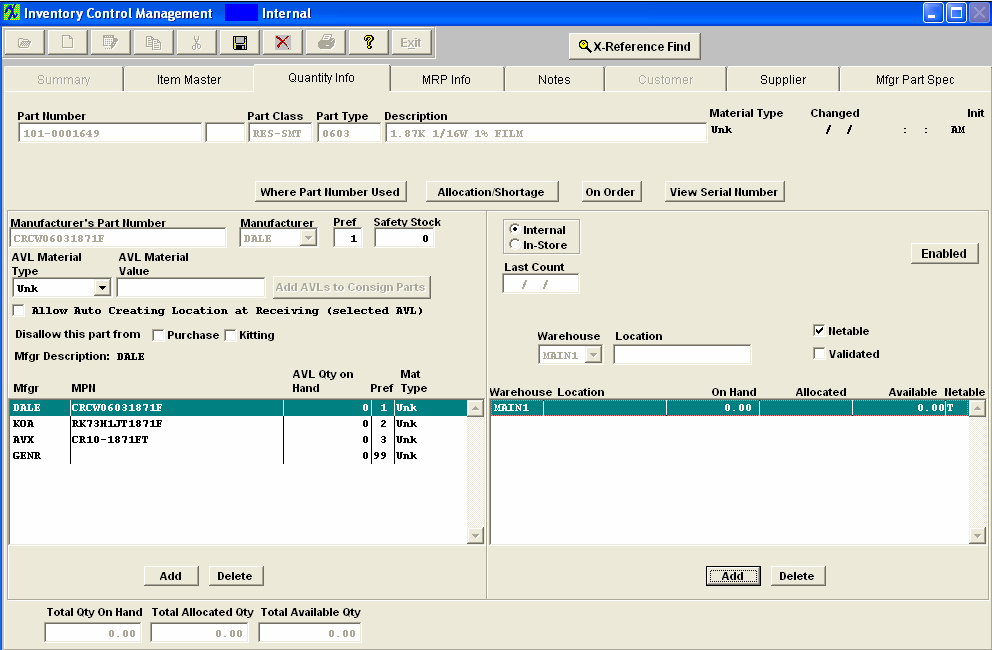
Material Type
|
Select from the pull down, Unk, LF-P/N, LF-Date, LF-Mark, RoHS-P/N, RoHS-Date, RoHS-Mark. See Article 2267 for definitions. These choices have been defaulted in. Customers may establish the logic by which the material type for the parts are established by the material types at the AVL level in System setup/Material Type Setup.
The AVL Material Type is carried forward for the consign part when the consign part is first added to the system or when new AVL was added to the internal part and the user elects to add this AVL to the existing consign parts. If the user later changes the Material Type on the internal part, the change is NOT carried over to the consigned.
If the inventory material type update is set to "Auto" (within the Material Type Setup), everytime the user modifies a part or AVL, the program will update the inventory material type automatically, if the control is set to "Manual" then user will be able to modify inventory material type on "Quantity Info" page via a Material Type pulldown, the program will not validate if the material type in inventory and AVL levels are in sync.
|
AVL Info |
User can edit the Pref Code, Safety Stock, AVL Material Type, Enter AVL Material Value info, check the Allow Auto Creating Location at Receiving (selected AVL) and/or Disallow this part from Purchasing and/or Kitting (if applicable). Depress the ADD button to enter a new mfgr and mfgr PN. Highlight an existing mfgr and mfgr PN in the box and depress the DELETE button to delete an existing mfgr and mfgr PN (if there is no qty on hand). Note: When deleting an MPN - keep in mind that the MPN will be deleted from the screen but NOT from the tables. The MPN's that have been deleted are retained in the tables for history tracking purposes.
NOTE: If the user changes the preference code or material type these changes are NOT carried forward to the existing consigned parts.
System will not allow users to have duplicate AVL/MPN combinations. If user has same mfgr and mfgr PN but different material types, we suggest that the user create a new AVL with a dash (or any other symbol) and use that designation to transfer to the UNK material type parts or create a different location for the same part, but have it be non-nettable, making it ineligible as a source for MRP.
|
Warehouse Info |
User can edit a location to an existing Warehouse, check or uncheck the Netable and Validated boxes. Depress the ADD button to add a new Warehouse. Highlight an existing warehouse in the box depress the DELETE button to delete an existing warehouse (if there are no qty on hand). Caution on deleting warehouses: Please remember if you delete a warehouse for a given part number, that you are ALSO deleting some of the history for that part at that location. If you think that such history will be required in the future, then DO NOT delete the warehouse. NOTE: When removing/changing WH/Location system will prompt the user if any POs are open, which are using the modified location. This prompt will allow the user to abort or continue with the change. |
If the user adds new AVL's to the Internal part number, they may click on this button and it will bring up the following screen. |
 |
Check the radial for the Warehouse to be added.Choose the mfg. from the pull down you want added to the consigned AVL. Highlight the Customer(s) Consigned Part number you want to update.
Depress on "Add Selected AVL to the Highlighted Parts"
The following warning will appear.
|
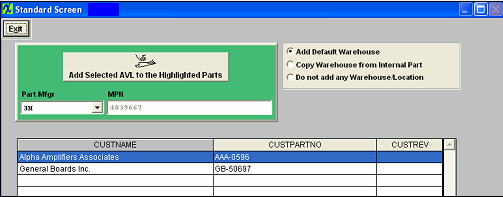 |
If "yes" is depressed you will receive the following screen:
If "No" is depressed the action will be deleted.
Depress "OK" and the transaction is completed
|
 |
MRP INFO TAB
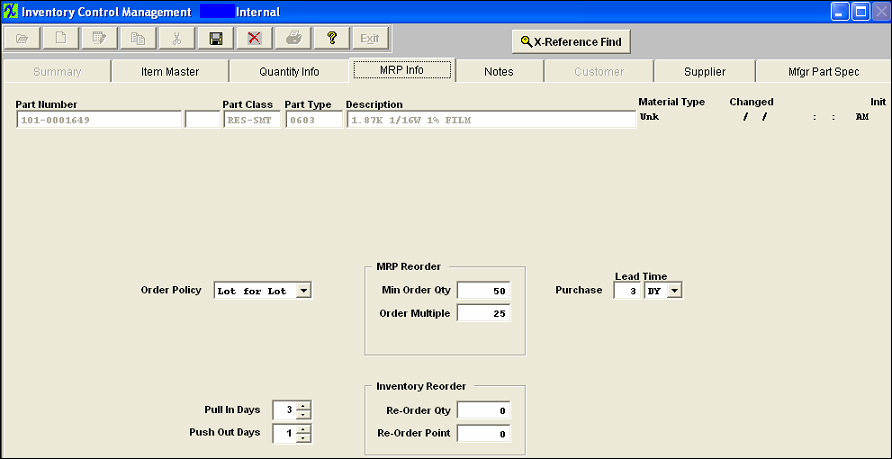
MRP Info Tab |
Order Policy, Min Order Qty, Order Multiple, Purchase Lead Time, Pull In Days,Push Out Days, Re-Order Qty, Re-Order Point |
CUSTOMER TAB
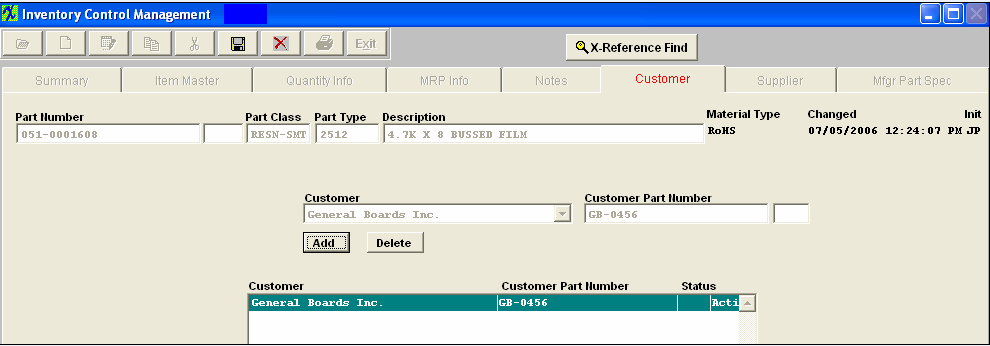
Customer Tab |
Add or Delete a Customer and Customer PN. |
SUPPLIER TAB
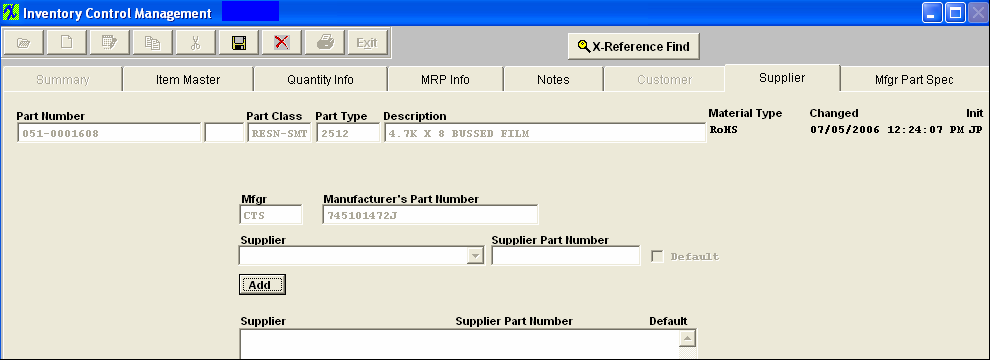
Supplier Tab |
Add or Delete a Supplier and Supplier PN. |
MFGR PART SPEC
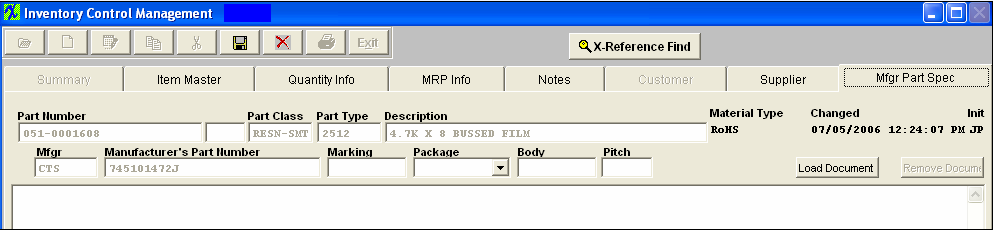
Mfgr Part Spec |
Load/change picture or .pdf file. |
Depress the Save Action button at the completion of each edit.
|
1.4.5. Delete an Inventory Control Record |
Depress the Delete button and the following message will appear for a BUY part:
Depress the Delete button and the following message will appear for a MAKE part: NOTE: Any ECO's created against this part will NOT be available for selection.
The System will allow the users to delete an Inventory Part from the system if:
there is no Quantity on Hand
it is not used on a BOM
there is no shortages or allocations
there is no open Purchase Orders and if the receipt has been reconciled and posted to the General Ledger
Note: When deleting an MPN - keep in mind that the MPN will be deleted from the screen but NOT from the tables. The MPN's that have been deleted are retained in the tables for history tracking purposes.
If BUY or MAKE part has qty on hand the following message will appear and user will NOT be allowed to delete the inventory part:
|
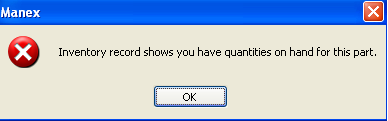 |
If BUY Part is associated with consigned part(s) the following message will appear and user will NOT be allowed to delete inventory part: |
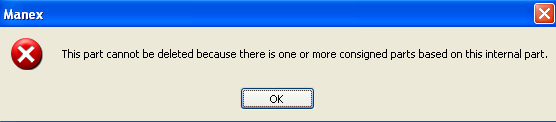 |
If BUY part is used on a BOM the following message will appear and user will NOT be allowed to delete the ivnentory part: |
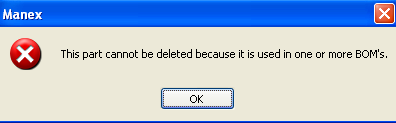 |
If BUY part has shortages or allocations the following message will appear an XL spreadsheet will be created with detailed information and user will NOT be allowed to delete the inventory part: |
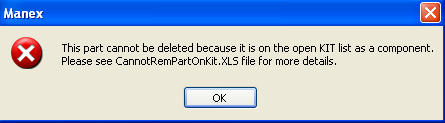 |
If BUY part has open PO(s) the following message will appear and user will NOT be allowed to delete the inventory part: |
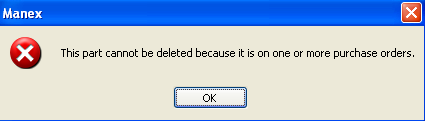 |
If BUY part has NOT been reconciled the following message will appear and user will NOT be allowed to delete the inventory part: |
 |
If BUY part has NOT been Posted to GL the following message will appear and user will NOT be allowed to delete the inventory part: |
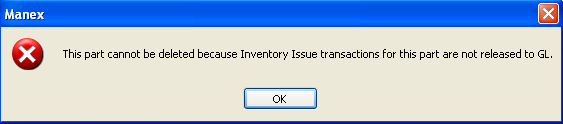 |
If MAKE part has NOT been Posted to GL the following message will appear and user will NOT be allowed to delete the inventory part: |
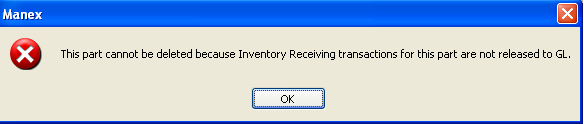 |
If you do not want to loose the History, the other option you have is to change the Status of the Part from Active to Inactive rather than deleting the ICM part. To see further detail on change the status of a part see Article #931 .
|
1.4.6. Attach a Related Document | Find an existing Inventory item Record, or Add a new Inventory item record.
Depress the button, and enter password.
The following screen will appear:
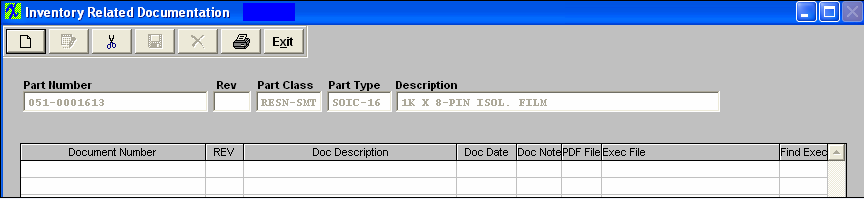
Depress the Add record icon, enter in a Document Number, REV, Doc Description, Doc Date, Doc Note;
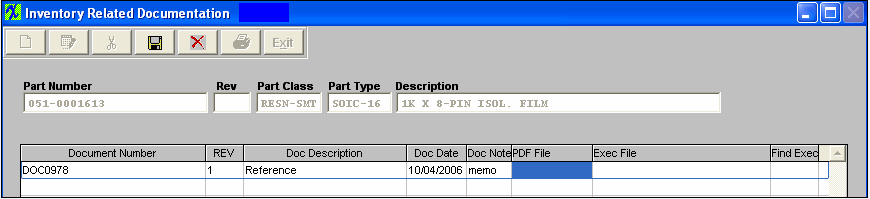
To load a document double click in the PDF File field and the following screen will appear:

Depress the Load Document button and the following screen will appear: The PDF screen will allow you to load almost any type of document; (Word, Excel, pdf, Images, etc .... ) It will NOT let you load a document with symbols in the file name. Example "Int ' l". (Symbol in Red). If you are receiving a system error when attempting to load a document check the file name to make sure there are no symbols within that file name.
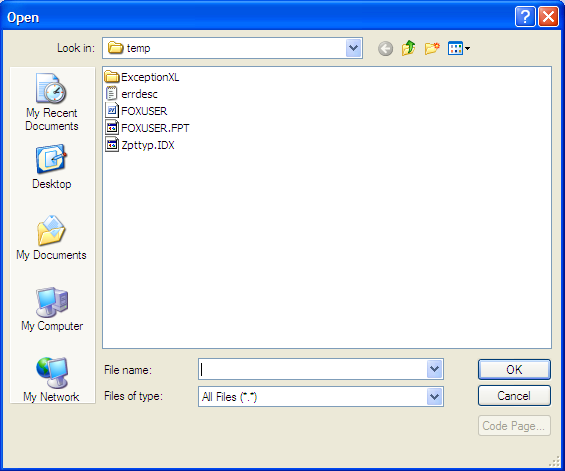
Locate the document and double click on it and the document will populate screen.
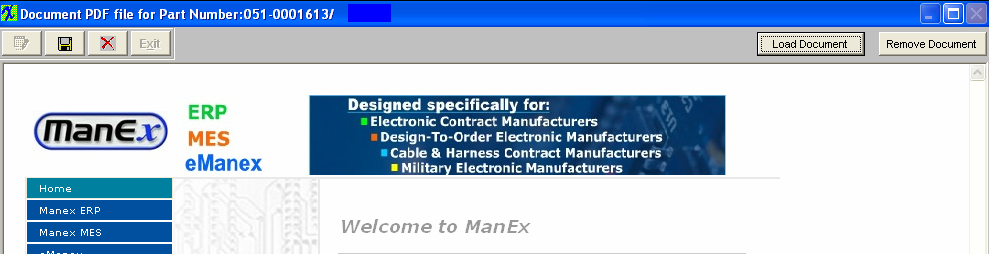
Depress the Save record icon to save or depress the Abandon changes icon to abandon changes. The following screen will appear:
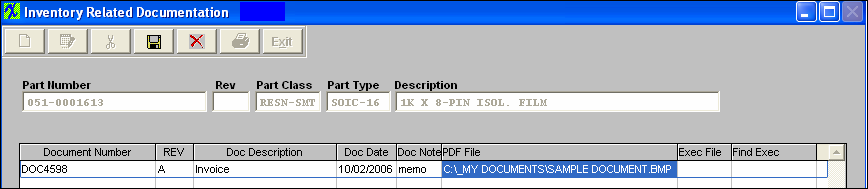
Depress the Save record icon to save or depress the Abandon changes icon to abandon changes.
Once documents are saved the "Related Documentation" button will display in Red. This Document will be available to view in the PO Module and PO Receiving Module also.
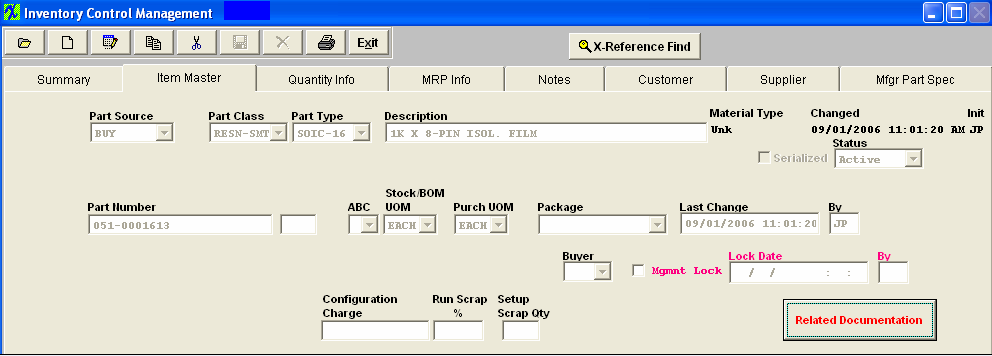
|
1.5.1. Inventory Control Reports |
To obtain the Inventory reports, select the Print button from the ManEx action buttons at the top of the screen.

The following screen will appear:
Select the appropriate radio for the output format you desire: Screen, Printer, XL File, TXT File, or PDF.
Highlight the desired report and then depress the Option tab if applicable.
|
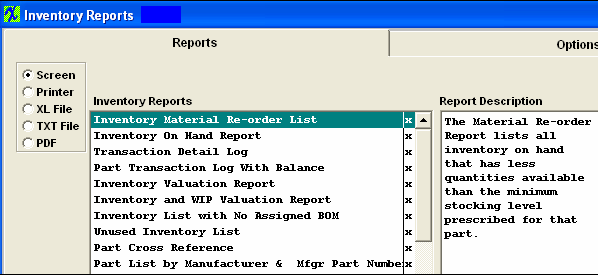 |
Inventory Material Re-order List Report - The Material Re-order Report lists all inventory on hand that has less quantities available than the minimum stocking level prescribed for that part.
Select the Inventory Type, either Internal, In Store, Internal & In Store or Consign by clicking on the appropriate radio button. Depress the OK button.
This report uses the "Re-order Point" to decide if the part need to be re-ordered, not the "Re-order Qty" .
|
|
The Following is printed: This report displays all inventory on hand that has less quantities available than the minimum stocking level prescribed for that part.
Inventory On Hand Report - This report lists material on hand in inventory locations, including WIP. There are several ways to select the information so that the report is specific to chosen areas. The report shows the amount of inventory in each location, including identification of the manufacturer and allocated inventory.
To select class, highlight the Class and depress the > button. If you want all classes, depress the >> button.
To select warehouse, highlight the warehouse and depress the > button. To select all warehouses, depress the >> button.
Enter Part Number range, if desired. If left blank it will check all records.
Select to sort by, either Part Number or Warehouse by clicking on the appropriate radio button.
If you want to suppress records with a zero, check the box.
Depress the OK button.
|
|
The following is printed: This report displays the amount of inventory on hand in each location, including WIP, and identification of the manufacturer, Lot Code information, and allocated inventory. There are several ways to select the information so that the report is specific to chosen areas.
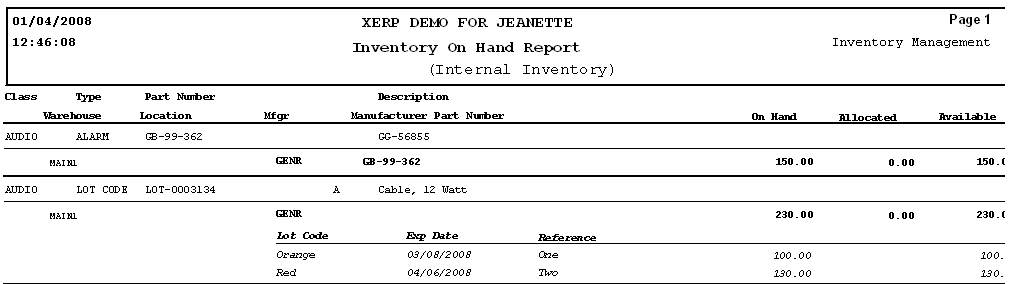
Transaction Detail Log Report - This Report lists all inventory movement transactions for the selected criteria for the report.
Highlighting the Transaction Detail Log report brings up a further selection:
Highlight the desired selection, either All, Receipt, Issue or Trans/Exp.
Depress the Options tab will bring up the following screen:
|
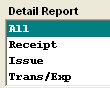 |
To select class, highlight the Class and depress the > button. If you want all classes, depress the >> button.
To select warehouse, highlight the warehouse and depress the > button. To select all warehouses, depress the >> button.
Enter Part Number range, if desired. If left blank it will check all records.
To clear the part range, check the Clear Range Entries box.
Enter the desired date range From and To. To clear the date, check the Clear Selection box.
If you want the reason to appear on the report, check the With Reason? box.
If you want the Serial numbers to appear on the report, check the box. (Note: Leading Zero's will not be displayed on report).
Select the Inventory Type, either Internal, Internal & In Store, In Store or Consign by clicking on the appropriate radio button.
Depress the OK button.
|
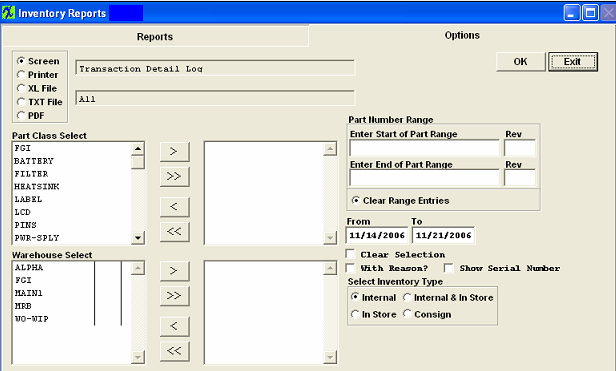 |
The following is printed: This report displays all inventory movement transactions for the selected criteria for the report. Issued qty's are displayed as negative, and Received qty's are displayed as postive.
Note: The reference field as entered in the Inventory Handling module will display on the Transaction Detail report.
Part Transaction Log With Balance Report - Lists all transactions for a specific part from date selected.
Select the Inventory Type, either Internal, Internal & In Store, In Store or Consign by clicking on the appropriate radio button.
Enter the Internal Part Number/Revision.
Enter the From Date, (the To Date is todays), Part Number/Revision.
If you want the reason to appear on the report, check the With Reason? box.
If you want the Serial numbers to appear on the report, check the box. (Note: Leading Zero's will not be displayed on report).
Depress the OK button.
Note: The beginning balance is a calculation based on transactions. It is not associated with the GL, nor has any effect on it. If the beginning balance is being displayed as anthing other than "0" it may be caused by the UOM being changed with qty on hand. See Article #3414 for further detail.
|
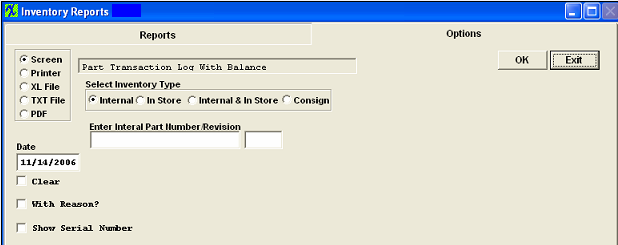 |
The following is printed: This report displays all transactions for a specific part from date selected. Issued qty's are displayed as negative, and Received qty's are displayed as postive.
To read this report you need to start from the bottom and work your way up.
We use the current qty OH, then get all the receiving, issue, transfer... records, and go backwards to create the transaction with balance report. For example, I have a new part like this:
Starts with a 0.00 balance:
01/05/09 receiving 230
01/08/09 issue 15
01/15/09 receiving 75
The Qty OH now is 290, the report gets all the receiving, issue, transfer records and sorts the data by date from latest to oldest to get the beginning balance.
Qty OH: 290
+75 balance: 215 (by -75 from the 290)
-15 balance 230 (by adding 15)
+230 beginning balance: 0 (by -230 to get the balance)
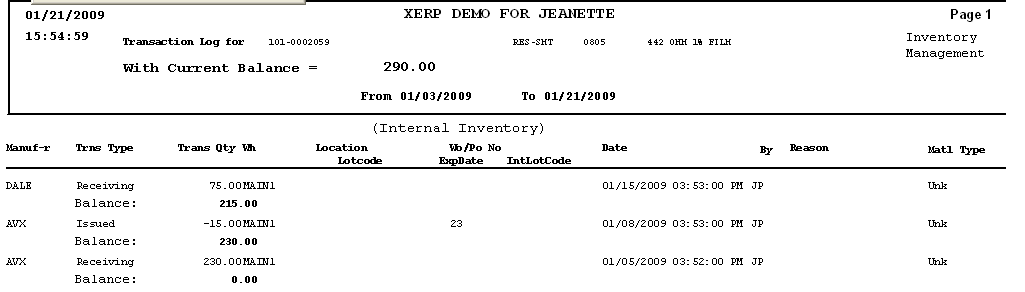
Inventory Valuation Report - This Report lists all inventory by part class and summerizes the inventory value of the parts selected.
To select class, highlight the Class and depress the > button. If you want all classes, depress the >> button.
To select warehouse, highlight the warehouse and depress the > button. To select all warehouses, depress the >> button.
Enter Part Number range, if desired. If left blank it will check all records.
To clear the part range, check the Clear Range Entries box.
Select the type of Cost you want to appear on the report: Standard, Purchase or User Define by depressing the appropriate radio button.
Select status of parts: All or Active Only by depressing the appropriate radio button.
Depress the OK button.
NOTE: The Last Paid information is calculated from the Last Change date not necessarily the PO Date that is displayed in the Purchase History box. If a user happens to edit an older PO (that does not match the Purchase Order History screen) and saves the changes the Last Paid will be updated based on the last change order recorded and the PO History screen will still remain as is. (Example: If a PO was originally created in 2002 , but edited and saved today, it would then be included into the Last Paid record from the date it was modified).
|
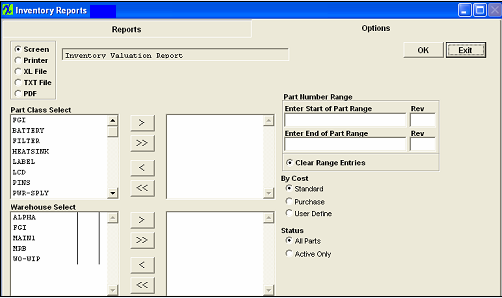 |
The following is printed: This report displays all inventory by part class and summerizes the inventory value of the parts selected.
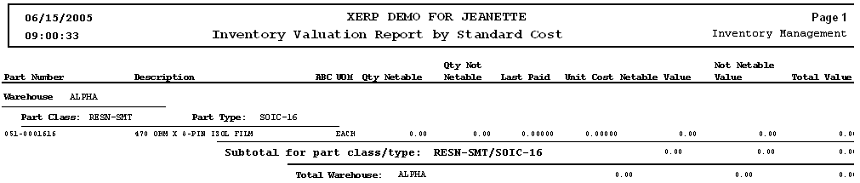
Inventory and WIP Valuation Report
Check the box if you want to suppress 0 quantity on hand.
Check the box if you want to round quantities to Integer.
Select the part class by highlighting the one you wish and depressing the > button. If you want all classes, depress the >> button.
Enter Part Number range, if desired. If left blank it will check all records.
To clear the part range, check the Clear Range Entries box.
Select the type of Cost you want to appear on the report: Standard, Purchase or User Define by depressing the appropriate radio button.
Select status of parts: All or Active Only by depressing the appropriate radio button.
Depress the OK button.
|
|
The following is printed:

See Article #1777 "How WIP Qty and WIP Value is Calculated".
See Article #913 "How Manex tracks and values the dollars in WIP".
See Article #3068 "Why the Accounting Values do not always match the Inventory reports".
Inventory WIP Valuation Report by Work Order
Check the box if you want to round quantities to Integer.
Select the Part Class by highlighting the one you wish and depressing the > button. If you want all classes, depress the >> button.
Select the Work Order by highlighting the one you wish and depressing the > button. If you want all classes, depress the >> button.
Enter Part Number range, if desired. If left blank it will check all records.
To clear the part range, check the Clear Range Entries box.
Select the type of Cost you want to appear on the report: Standard, Purchase or User Define by depressing the appropriate radio button.
Depress the OK button.
|
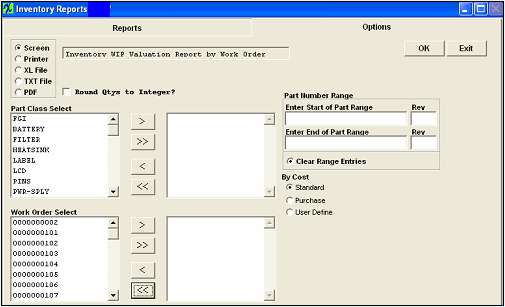 |
The following is printed: Every new WO will start on the new page.
Inventory List With No Assigned BOM Report - All material on hand with no parent assembly associated with it.
This report displays all material on hand with no parent assembly associated with it.
Select the Part Type to Display: All, Internal, or Consigned Only by depressing the appropriate radio button.
|
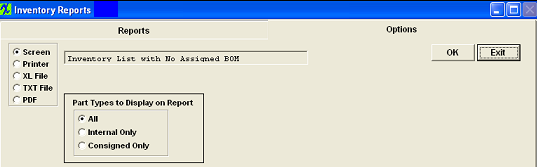 |
The following is Printed: Note: The first letter of the Status is displayed to the left of the "Part Number" column (A for Active and I for In-active).
Unused Inventory List Report - All inventory for which no transactions have occured since a selected date.
Select Inventory Type: Internal, In-Store, Internal & In-Store, or consign by depressing the appropriate radio button .
Select the part class by highlighting the one you wish and depressing the > button. If you want all classes, depress the >> button.
To select warehouse, highlight the warehouse and depress the > button. To select all warehouses, depress the >> button.
Enter Part Number range, if desired. If left blank it will check all records.
To clear the part range, check the Clear Range Entries box.
Enter the desired date.
To Clear selection, check the Clear Selection box.
If you want to suppress records with a zero, check the box.
Depress the OK button. Note: The search for the un-used parts will be based on the MFGR/ MPN level.
|
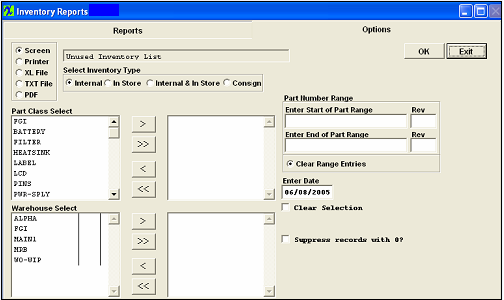 |
The following is printed: This report displays all inventory for which no transactions have occured since the selected date based on the MFGR/MPN level.
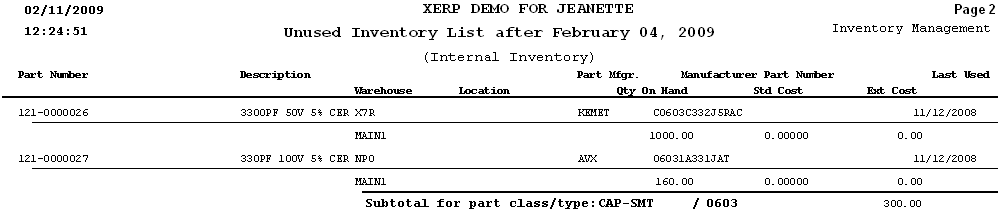
Part Cross Reference Report
Highlighting the Part Cross Reference report brings up a further selection:
Select the type of Cross Reference desired.
This will display the relation between Mfgr part number and Internal part number.
|
|
Choose Sort By selection, either Manufacturer Part Number or Manufacturer by clicking on the radial.
Depress the OK button.
|
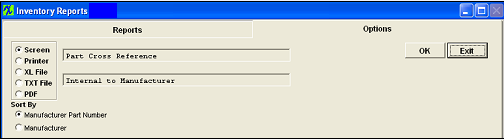 |
The following is printed: This will display the relation between Mfgr part number and Internal part number.
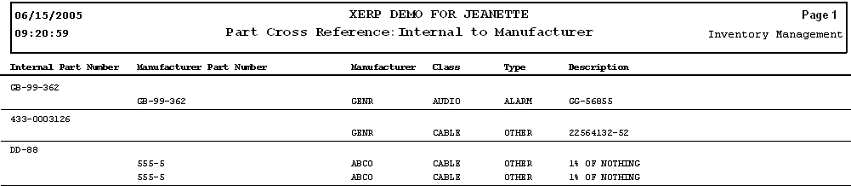
Part List by Manufacturer and Manufacturer Part Number Report - Lists by manufacturers, all part numbers by manufacturers part number, user type, class, description and part number, along with quantity in stores.
Highlight the manufacturer of preference and depress the > button. If you want all manufacturers depress the >> button.
Depress the OK button.
|
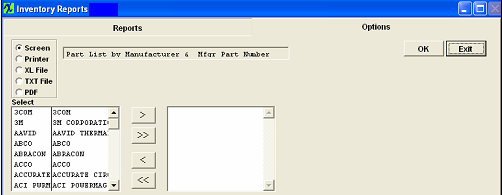 |
The following is printed: This report displays all part numbers by manufacturers part number, user type, class, description and part number, along with quantity in stores.

Physical Inventory Work Sheets Report - Work sheets to be used to take physical inventory.
Select Inventory Type: Internal, In-Store, Internal & In-Store, or consign by depressing the appropriate radio button .
Select the part type: Make, Buy or Both by depressing the appropriate radio button.
Select either With Book Quantity or Without Book Quantity by depressing the appropriate radio button.
Select to sort by: Warehouse/Location or Part Number by depressing the appropriate radio button.
Enter Part Number range, if desired. If left blank it will check all records.
To clear the part range, check the Clear Range Entries box.
Depress the OK button.
|
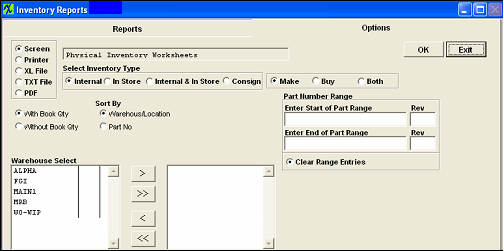
|
The following is printed: This is the Worksheets to be used to take physical inventory.
List of Duplicate Descriptions - This report displays all part numbers with duplicate descriptions
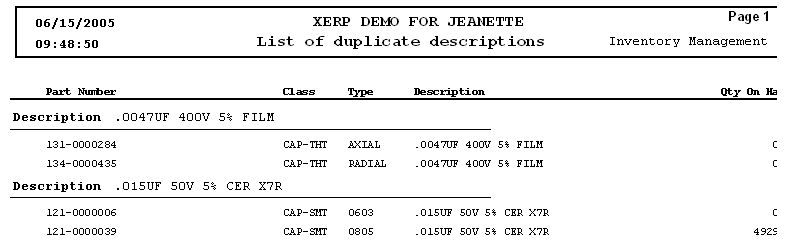
In Store Items Without Contract Report - This report displays all part numbers from Invt mfgr Instore without contract
In Store Issued Items Without Contract Report - This report displays a list of items issued from in-stores without contract
Customer Reference Report - This report lists by customers, all customers part number along with quantity in stores
Part Class and Type List - This report is a listing of Part Classes & Types
Print Inventory Labels
The Print Inventory labels report requires that the Barcode Font be installed.
Highlighting the Print Inventory Labels brings up a selection of printers to be used:
Laser Printer (sheet): Avery Label # 5163, 4" x 2", 2 accross, 5 down, printed portrait
Portable Printer (roll): Redline Solutions, Zebra QL DT Labels 4x3 PN 81475
Portable Printer (roll): Zebra Printer (roll): Label size 2" x 3" (for Zebra printers Part #10000286 (or equivalent)
|
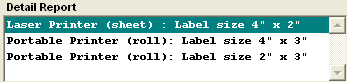 |
Select Inventory Type: Internal, In-Store, Internal & In-Store, or consign by depressing the appropriate radio button .
Enter number of Labels to Print (1-99).
Enter Part Number range. (This field is required).
To clear the part range, check the Clear Range Entries box.
Enter the Warehouse and location, if desired.
Depress the OK button.
|
|
The following is printed.
|
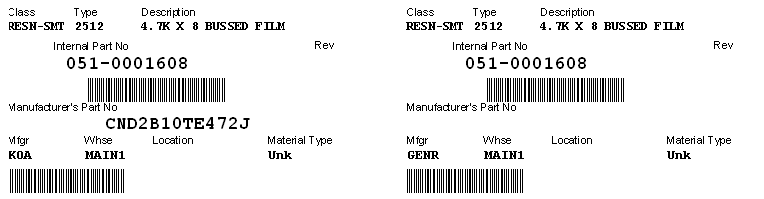 |
Allocated Report for Closed and Cancelled WO - This report displays a listing of Part Classes & Types
Allocated Report by Part Number Report - This report displays a listing of Allocated Part Numbers
Allocated Report by Work Order Report - This report displays a listing of Allocated Part Numbers by Work Order
Material Type Change Report - Listing of the parts that have their material type changed since given date.
Enter the From Date, (the To Date is todays).
To clear date check the clear box.
Depress the OK button.
|
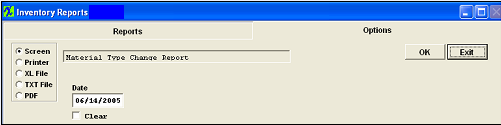 |
The following is printed: - Listing of the parts that have their material type changed since given date.
Material Type Change Log Detail Report - Listing of the parts that have their old and current material types changed since given date.
Enter the From Date, (the To Date is todays).
To clear date check the clear box.
Enter in a Part Range, if desired. If left blank it will check all records.
To clear the part range, check the Clear Range Entries box.
Depress the OK button.
|
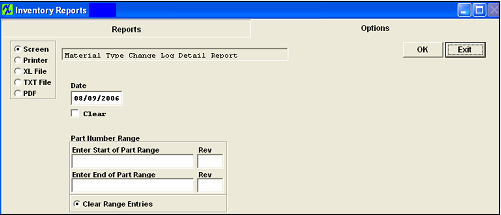 |
The following is printed: This report displays the history of the Inventory Material Type Changes.

Inventory and AVL Material Type Validation - This report goes through the inventory part numbers to check and lists if the Inventory and AVL material types are not in sycn. It does not update the inventory material types.
Depress the OK button. User will receive the following popup to warn them that the report could take a while to run. So at this point you have the option of continuing or aborting the procedure.

Depress Yes and the following report will appear: This report compares inventory material type with AVL calculated material type and lists those part numbers which have different material types in inventory and AVL levels.

|
|