1.1. Statistical Quality Control (SQC) (OPTIONAL Module) |
1.1.1. Prerequisites for SQC | Required Prerequisites:
ManEx’s standard module configuration allows most users to accomplish their daily tasks. For those users wanting to get more from ManEx by leveraging the total solutions, this is one of the optional modules available for purchase. To place an order or to learn more about this specific module or any of the other optional modules please contact us at http://manex.com\contactus.aspx
After activation, "Statistical Quality Control" (SQC) access for each user must be setup in the ManEx Security module. Users with “Supervisor Rights” will automatically have access.
Customer |
Part number |
Defect Codes |
The Defect Codes must be established in the Quality Defect Codes setup. The options for the viewing of serial numbers, number of times that “No Problem Found” are permitted, defects displayed for routing or all must be established in the setup. |
Optional Prerequisites:
Pricing |
Otherwise must be entered in Sales Order.
|
Bill of Material-Locations |
If locations (reference designators) are entered in the Bill of Material, the user may identify specific locations for each defect.
|
BOM Appvd Mfgrs |
If the AVLs are entered in the Bill of Materials, the user may identify specific manufacturers for each defect.
|
|
1.1.2. Introduction for SQC | The STATISTICAL QUALITY CONTROL (SQC) Module ~ Defect Entry screen is used to record defects and inspection results during the movement of product through the production Work In Process (WIP). The user has a choice of entering data in a batch mode or in an in-line mode See Article #1769 for further detail. Batch mode is the entry of data accumulated during an inspection period, and is data entry only (does NOT transfer product from one work center to another). In-line mode is where inspection is done at the end of a work center or activity, and the product is to be moved to another work center based on the results of the inspection. In-line inspection would require inspection of 100% of the product, in order to move the product from one step to another. It also requires the use of a ManEx workstation at the inspection station, so the data may be entered real-time.
Defect entry is based on having a standard nomenclature for the defects in the Quality Defect Codes setup, so that the users do not have the option of creative descriptions. The defects in the setup may be ascribed to specific work centers, to minimize the number of defects that an inspector (or data entry person) has to view to find the appropriate defect.
Defect information may be recorded by work order and/or by serial number. Defects may be associated with a specific “location” (reference designator) on the assembly, providing the user has entered reference designators for the assembly in its Bill of Material .
If the user chooses to enter reference designator locations for the defects, and has entered reference designators on the Bill of Materials, then ManEx will prompt the user to select the manufacturer for the part used at the location, as well as automatically enter the internal part number at that location.
There is also provision for tracking the diagnostics and repair of each defect and assembly. The user may view the history of the assembly’s movement through production, and all of the defects associated with each assembly.
Data entered for defects will be used in the Statistical Quality Control module for charting pareto charts, control charts and more.
|
1.1.3. Fields & Denfintions for SQC |
1.1.3.1. Defect Data Collection |
1.1.3.1.1. Quality Inspection Entry Tab | Quality Inspection Entry Screen Field Definitions
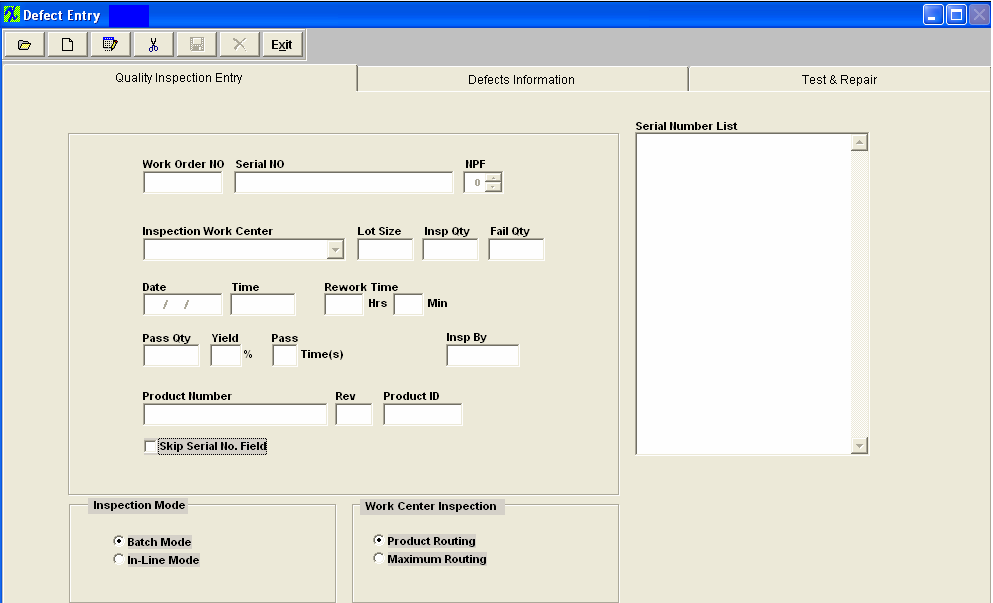
Work Order Number |
The number of the Work Order which was inspected.
|
Serial Number |
The serial number assigned to the specific assembly unit.
|
NPF |
The next field, “NPF”, no problems found, is provided for the user to record when observing the product. If the serial number had previously been rejected, and analysis of the product yield no further problem, either with cosmetics or function, then the user may change this number to 1, meaning the first time it was inspected or tested, no problem was found. If the product serial number is subsequently rejected again, and a second inspection finds a problem, the number may be incremented to a “2”. This will alert users to repeated rejections of a product serial number, one or more times with no discernable defects. If the number of times that a part has experienced an NPF (no of problems found) exceeds that established in the Quality Defect Codes setup, the user will receive a warning message and will allow you to proceed on with the Inspection. This is just a notification that the board has passed the maximum NPF cycle.
|
Inspection Work Center |
This is the name of the Work Center where the inspection took place.
|
Lot Size |
This is the number of assemblies available for testing.
|
Insp Qty |
This is the number ofassemblies actually tested.
|
Fail Qty |
The number of assemblies which failed inspection.
|
Date |
The date whereby the inspection took place.
|
Time |
The time (24 hour clock) when the failure was recorded.
|
Rework Time |
The time estimated to rework the failed assembly |
Pass Qty |
The number of assemblies which passed inspection.
|
Yield |
The percentage of assemblies which passed inspection.
|
Pass Times |
This is the number of times a particular Serial Number can pass through this Inspection screen. In Quality Defect Code Setup, there is a field called :maximum number of inspections/WC”. The user may define how many times a given serial number can pass through a given Work Center. |
Product Number |
The internal number assigned to the assembly.
|
Rev |
The revision number associated with the Product Number.
|
Product ID |
This field is no longer used and is left blank.
|
Skip Serial Number Field |
This box is checked if the user wishes to do Without Serial Number Inspection.
|
Enter Serial Number Without Validation |
Only Enabled if user skips regular serial number entry.
This feature has been added to allow the users the ability to inspect Serial Numbers that do not actually exist within the ManEx system. (for example serial number created outside of ManEx, by customer or other software, etc. . .)If the user checks the “Enter serial number without validation” then ManEx does not validate when the users enters the Serial Number. The system just records the entry for later SQC analysis purpose.(note: if the work order is serialized, then the user can not use this feature)
|
Inspection Mode |
Determines whether inspection is performed via Batch or In Line mode.
Batch mode is used for entering data previously recorded during inspection of the product. When the user chooses to enter defect data in “In-Line” mode with the serial number, the user won’t be able to enter “lot quantity”, “inspection quantity” or “failed quantity”. These fields are all automatically when the user goes into the “Defects Information” tab. However, if the user enters defect data in “batch” mode without the serial number, then the user will be able to enter “lot quantity”, “inspection quantity” and “failed quantity”.
If the user wishes to 100% inspect material, and directly move the passed material to the next routing work center, then the In-Line Inspection mode may be used.
|
Work Center Inspection |
The user has the option of viewing defects based on the product routing (Product Routing), or to view all defects (Maximum Routing).
|
Serial Number List |
The numbers of all of the Serial Numbers which were inspected. Depress the Edit button and then highlight the serial number of choice.
|
|
1.1.3.1.2. Defect Information Tab | Defect Information Screen Field Defintions
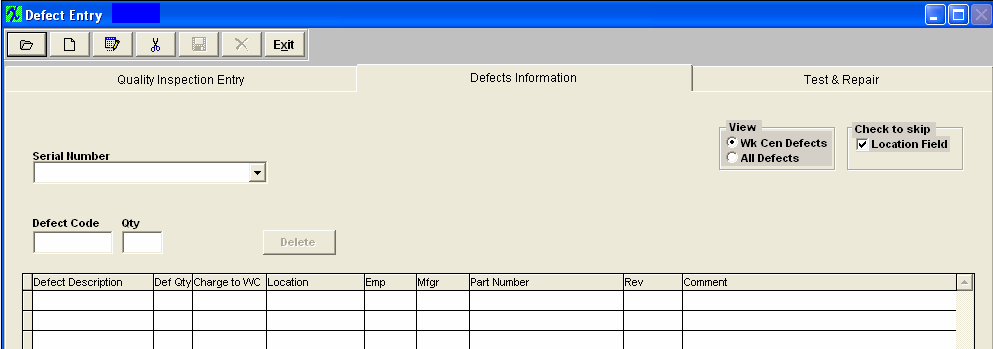
View |
This displays whether the view of the defects is by Work Center only or covers All defects.
|
Check to skip location field |
If this box is checked, the location field may be skipped.
|
Serial Number |
The Serial Number of the failed assembly.
|
Defect Code |
The code used to describe the defect.
|
Defect Description |
The description of the defect.
|
Def Qty |
The number of defects.
|
Charge to WC |
The name of the Work Center where the defect will be charged.
|
Location |
The Reference Designator as set up in the assembly’s Bill of Materials.
|
Emp |
Employee number assigned to the defect |
Mfgr |
The name of the manufacturer of the component.
|
Part Number |
The internal number assigned to the component.
|
Rev |
The revision number pertaining to the internal part number.
|
Comments |
Additional comments entered by the user.
|
|
1.1.3.2. View Chart Tab |
See Article #5082 for more detail on each individual Chart Listed at the Top. Once you have selected the type of graph you wish to view the graph will be displayed in the window below the selection.
|
1.1.3.3. Template Selection/Setup Tab |
Template Selection Setup
This is the first screen to be used in the module. In this screen, STATISTICAL QUALITY CONTROL graphics are created by selecting parameters to be considered in the graph.
This screen operates differently than all other ManEx screens. When bringing up the SQC module, the user is first presented with a template screen from which to choose parameters to be included in the information displayed.
When the user enters the system, he/she may select how they want to start the process of selection. Click on the Customer, Part Number or Work Order radial.
|
1.1.3.4. Template Detail Tab |
Date Range |
Enter the Date Range, From and To. Mark the Radial for the view by Daily, Weekly, Monthly, or Yearly. |
User Defined Limits for DPM Chart |
Central Line
lnCentralLine=lnTotalDef/lnTotalComp, where lnTotalDef is sum of all defect quantities * 1000000 and lnTotalComp is sum of inspected quantities*Parts Per Unit (entered in the routing module)
At this time system will decide if it can use average group size or not. If the size group varies more tan 15% the system will use variance Upper and Lowercontrol limit. If average group size could be used the average group size gets calculated by taking lnAvrgSubgrSize=lnTotalComp divided by number of groups and rounded to the nearest integer.
Calculation for the Upper Control Line
LnUpperLine=ROUND(((3*(SQRT(lnCentrLine*(1000000-lnCentrLine))))/SQRT(lnAvrgSubgrSize)),3)
Calculation for the Lower Control Line
lnLowerLine = ROUND(lnCentrLine -((3*(SQRT(lnCentrLine*(1000000-lnCentrLine))))/SQRT(lnAvrgSubgrSize)),3)
lnLowerLine = IIF(lnLowerLine<0,0,lnLowerLine)
|
User Defined Limits for pChart |
The formula for the Central line (Red) is: p = Total Number Failed (divided by) Total Number Inspected
Upper Control Limit (UCL) = p + 3 (divided by) p (1-p) divided by n
Lower Control Limit (LCL) = p - 3 (divided by) p(1-p) divided by n (or 0, whichever is greater)
n = number inspected (sample size)
|
User Defined Goal for the Yield Chart |
"Yield" = Total number of units handled correctly through the process step(s). This is usually measured in a percentage. The results being displayed in the "Yeild Chart" is the ratio of summed inspected qty and summed passed qty, grouped by date (user can select WO number, defect code to be filtered). |
|
1.1.4. How To .... for SQC |
1.1.4.1. Enter the Defect Data Information | All data must be Entered in the Quality Inspection Entry and Defect Information screens, with in the Shop Floor Tracking Module.
Entering a Defect Code Entry to a Work Order
For closed Work Orders: In the Security module, there is an option which must be checked per user for the “Defect Code Entry”. Once the Security right has been entered, the user may edit a “closed” Work Order.
The first screen presented to the user depends on whether or not in the system setup/Quality Defect Codes, the user has selected to enter defect information in BATCH or IN-LINE mode. If the user has selected IN-LINE in the setup, then only the IN-LINE screen will be displayed. Otherwise, the user will be presented with the batch screen, and the option to enter IN-LINE data.
Batch mode is used for entering data previously recorded during inspection of the product. When the user chooses to enter defect data in “In-Line” mode with the serial number, the user won’t be able to enter “lot quantity”, “inspection quantity” or “failed quantity”.These fields are all defaulted in when the user goes into the “Defects Information” tab. However, if the user enters defect data in “batch” mode without the serial number, then the user will be able to enter “lot quantity”, “inspection quantity” and “failed quantity”.
If the user wishes to 100% inspect material, and directly move the passed material to the next routing work center, then the In-Line Inspection mode may be used.
The user has the ability to limit some workstations (specific PCs) (which is defined in the Security Module) to be able to only transfer material “FROM” a certain Work Center. When the user transfers material from a Work Center (A Serialized part Number Only) in the Defect Code Entry In-Line Mode, the system will check to see if the serial number is currently in the Work Center. If not, a special supervisor’s password is required to transfer the serial number FROM a different Work Center. After the supervisor’s password is entered, the system will use the new Work Center to be the default FROM Work Center until the user closes the screen. The next time the user opens the screen, the default FROM Work Center will be changed back to the one defined in the Security Module.
Enter Production/Shop Floor Tracking by Work Order Module
Find a Work Order in SFT Module,
| 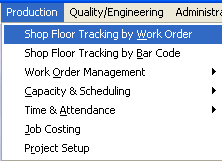 |
The following screen will appear:
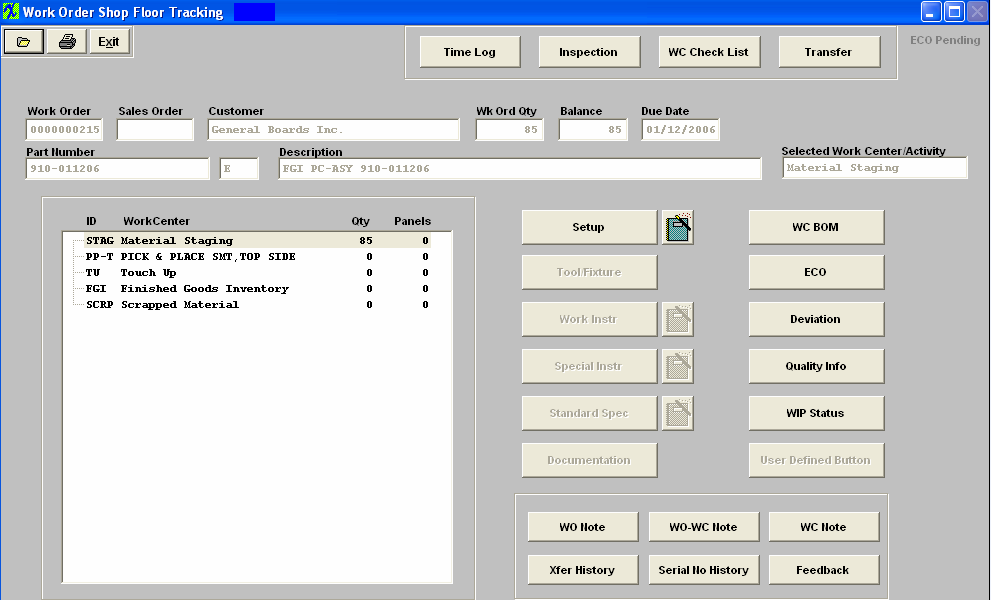
Depress the "Inspection" button located at the top of the screen.
The following screen will appear:
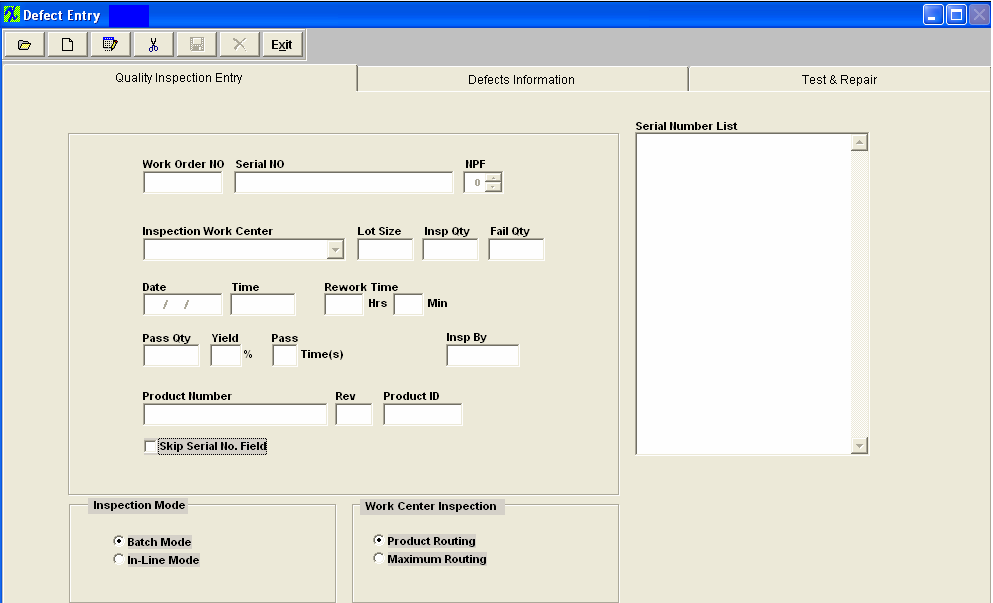
Entering Quality Inspection Data
There are two different ways to enter the Inspection Data: Batch Mode or In-Line Mode
Batch Mode
The first information tab records information about the work order. This includes lot size, failures, inspection quality, date, etc.
Depress the Add action button. Enter the password of the Employee that has inspected the product.
When the user first brings up the Defect Entry program, and before entering or editing data, they have the option to check or uncheck the “Skip Serial No. Field”. Once the data entry process is begun, the option is cleared until the user exits the defect entry form and re-enters it.
Adding Work Order Defect Information Without Serial Number Tracking
Enter the Work Order number, choose the Inspection Work Center from the pulldown, enter Lot Size inspected, Inspected Qty, and Failed Qty.
The Date, Time, Pass Qty, and Yeild % will default in. The date and time may be changed if needed.
The user may enter estimated rework time, if desired.
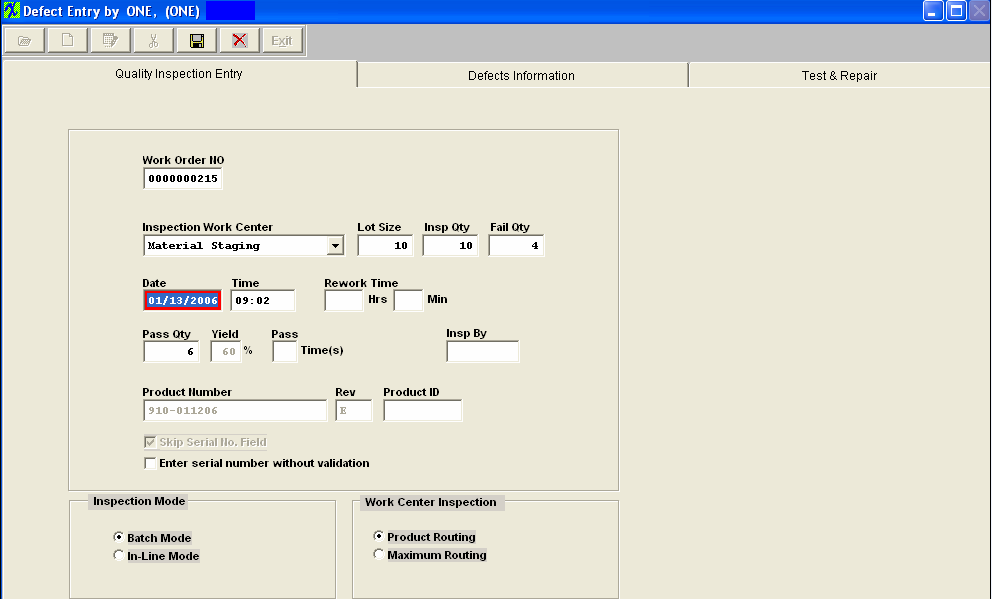
Depress the Defects Information tab and the following screen will appear:
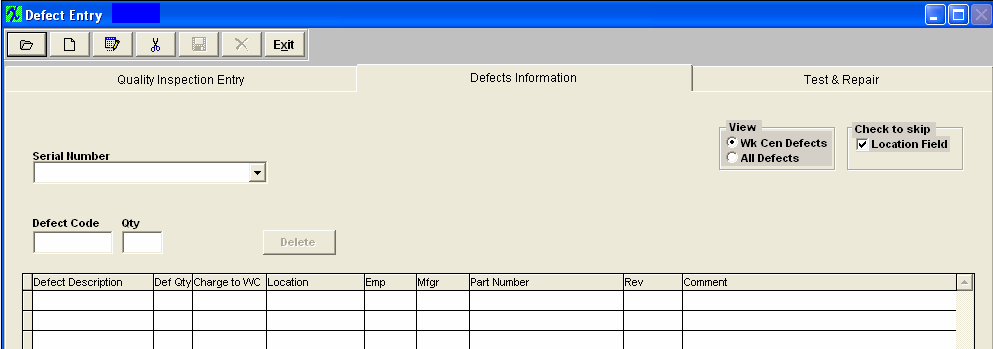
The user may then enter a defect code by manually typing in the code, or by scanning a bar-code menu, or by double clicking on the field to review a list of defect codes.
The list displayed will depend on which view is selected (in upper right hand corner of screen). If Work Center Defects is chosen, only those defects associated with the work center (as established in the system setup/Quality Defect Codes) will be displayed. If All Defects is chosen, then every defect entered in the system setup/Quality Defect Codes will be displayed.
The user may select one or more defects from the list by holding down the Control Key while clicking on the defects to be selected.
After completing the selection of the defects involved with the current inspection, clicking on the OK button loads the selected defects into the defect information screen.
Although ManEx will enter a Charge To Work Center code based on the work center entered or the location of the part, the user may modify the originating work center by clicking on the field and selecting another work center from the list.
The user may (optionally) then enter in the location (reference designator) where the defect was observed.
The user then must select an Employee from the pull down. The employee's being displayed in the pull down are only the employee's that are assigned to work centers (in the Security module) that are the same work centers listed in the Shop Floor Tracking by Work Order module and is sorted by the Employee User ID Number.
The system will check the BOM to be sure that the location entered here matches locations entered on the Bill of Materials.
When a valid location is entered, then system searches the Bill of Material to find manufacturers approved for the product, and displays a list of the approved manufacturers for the user to identify which manufacturer was associated with the defect observed. The user double-clicks on the manufacturer's name for the defective part, and the manufacturers name is placed in the defect information screen.
ManEx defaults the number of defects to one item, but the user may overwrite the quantity with an observed quantity greater than one.
The user may also enter a brief comment about the defect, for future reference.
The completed screen should appear as follows:
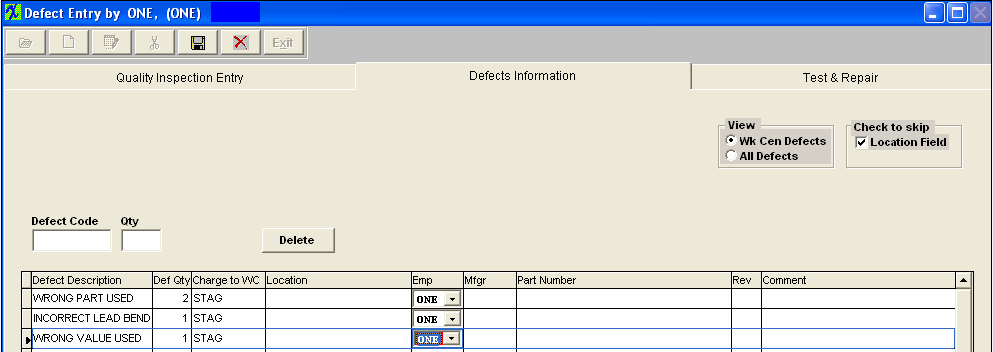
Depress the Save record action button to save changes or the Abandon changes action button to abandon changes.
If you depress the Save record action button, the following message will appear:
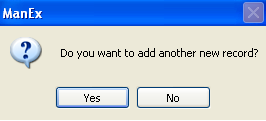
If you want to add another defect record for the same user "ONE" then depress YES, if you want to add a defect record for a different user (Example user "TWO"), then you must depress NO. Depress the Add record action button and enter user "TWO"s password and continue to enter the defect information.
When the user has completed the defect information, they may click on the Test & Repair tab, to enter more information about the part.
NOTE: The Test & Repair is actually a separate OPTIONAL module, but has been included into the Defect Entry screen for ease of use for the operators. For further detail about this module see Article #3291..
Adding Work Order Defect Information With Serial Number Tracking
Enter the Defect Entry screen. Depress the Add Record action button. Un-check the "Skip Serial No Field"
If the user is tracking serial numbers, then the first field to be entered (or bar-code scanned) is the serial number of the product being inspected. (Not the Work Order number).
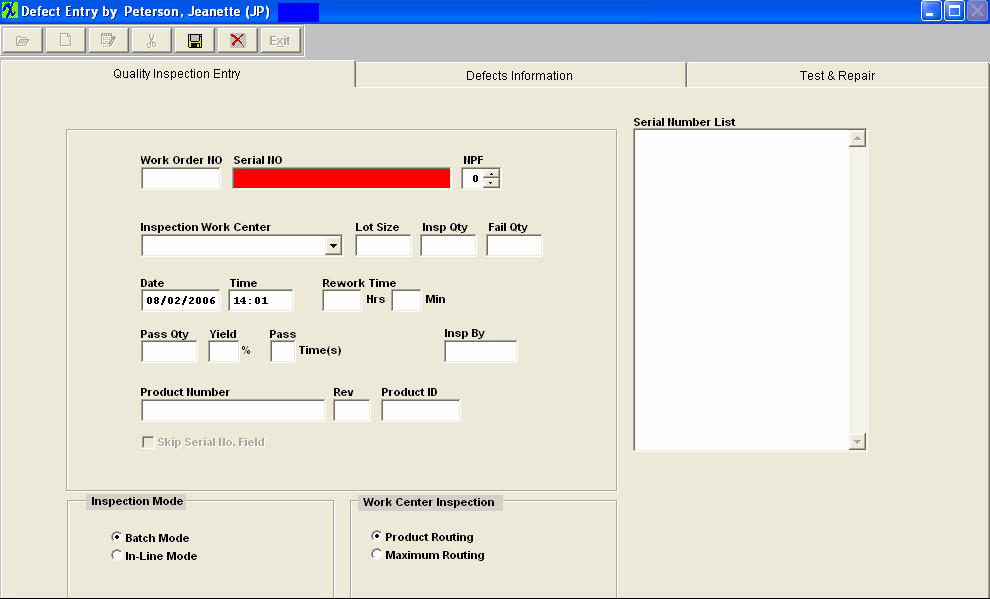
Type in the serial number. When the serial number has been entered, ManEx will complete the work order and product information. ManEx will also enter the current work center location of the serial number supplied.
The user now has the option of continuing to scan (or type) serial numbers, and log the defect information for each one later, or enter a serial number then the defects for that serial number, enter the next serial number, then the defects for the second serial number, etc. When multiple serial numbers have been entered, the data will refer to the serial number that is highlighted in the Serial Number list.
ManEx will enter in the lot size according to the quantity of serial numbers showing in the serial number list.
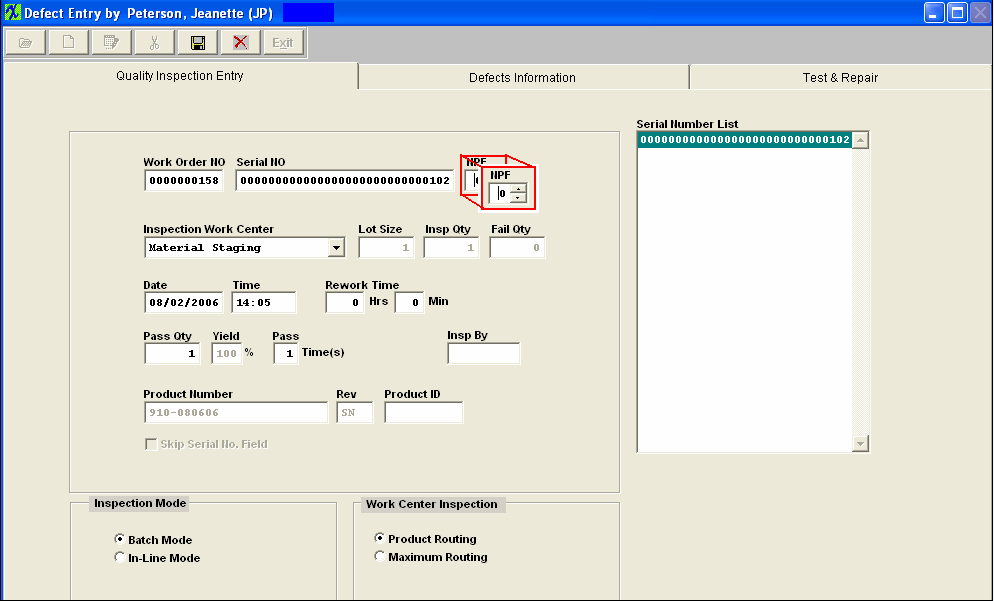
The next field, “NPF” is provided for the user to record when observing the product and finding that there is “No Problem Found”. If the serial number had previously been rejected, and analysis of the product yield no further problem, either with cosmetics or function, then the user may change this number to 1, meaning the first time it was inspected or tested, no problem was found. If the product serial number is subsequently rejected again, and a second inspection finds no problem, the number may be incremented to a “2”. This will alert users to repeated rejections of a product serial number, one or more times with no discernable defects.
If the number of times that a part has experienced an NPF exceeds that established in the system setup/Quality Defect Codes the user will receive the displayed warning message and will allow you to proceed on with the Inspection. This is just a notification that the board has passed the maximum NPF cycle.
Entering Defect Information
This screen operates as described under Entering Defect Information without serial numbers, except that the user must enter data for each serial number recorded. The serial number may be chosen by highlighting the serial number in the serial number box on the first screen, or in the defects information screen, by pressing the down arrow button next to the serial number field and selecting a serial number.
Defect information is entered in the same fashion as described above, except that the user should remember that the data being entered is for one part at a time, by serial number of the part.
The other difference in using serial number defect tracking is that on the Test & Repair screen, the user may view the Serial Number History tab. This view will display both the transfer history of the serial number through the work centers, and the history of defects associated with the serial number of the product.
(Note: if you are entering Defect information and not using the Serial No, then this screen will remain blank)
The user completes the defect entry for the first defect code (The location, quantity of defects observed, etc.). The process is repeated for each defect observed, storing the location and serial number to be analyzed at a later time.
At the conclusion of defect entries for the lot, the Save action button is pressed to retain the data. If the user elects to ignore all data entered in this session, the Abandon changes action button may be clicked to void any entries. Notice that ManEx computes the total number of defects observed for the defect code and displays the number next to the defect code.
Entering Defect Information Without Serial Number Validation
The “Enter Serial Number without Vailidation” option will only be enabled if the user skips the regular Serial number entry, and if the Work Order Product has not been serialized within the ManEx system.
This feature has been added to allow the users the ability to inspect Serial Numbers that do not actually exist within the ManEx system. (for example serial number created outside of ManEx, by customer or other software, etc. . .) If the user checks the “Enter serial number without validation” then ManEx does not validate when the users enters the Serial Number. The system just records the entry for later SQC analysis purpose. (note: if the work order is serialized, then the user can NOT use this feature).
Enter the Defect Entry screen. Depress the Add Record action button. Select “Enter Serial Number without Validation. ”
Enter the Work Order number.
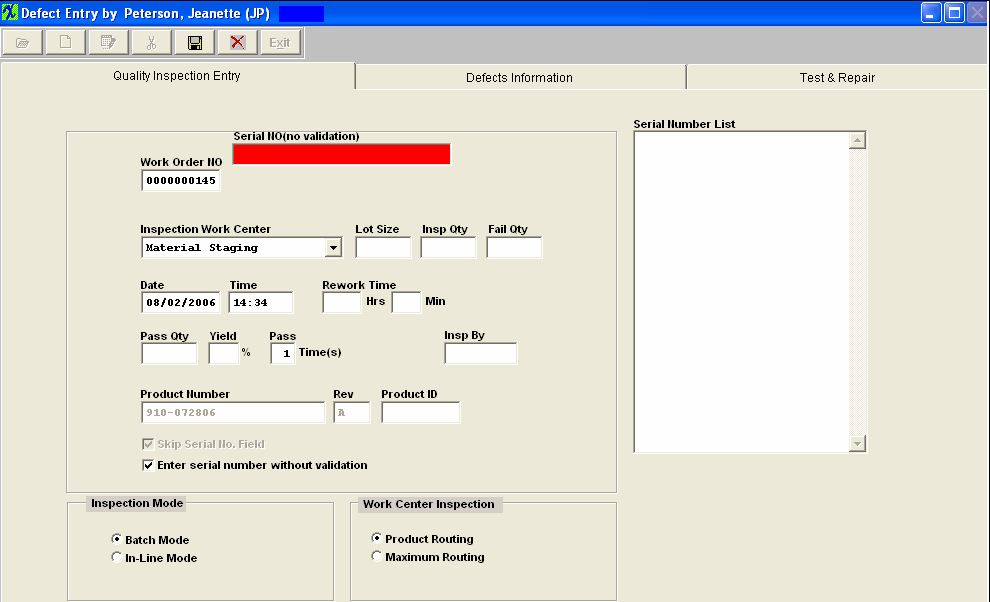
Then enter in the desired Custom Serial Numbers. The remaining process will then be the same as listed above.
In-Line Mode
When the user chooses In-Line inspection, either by setting it as the default in the Quality Defect Setup, or by selecting In-Line on the initial Quality Inspection Entry screen.
The first information tab records information about the work order. This includes lot size, failures, inspection quantity, date, etc.
Depress the Add action button. Enter the password of the Employee that has inspected the product.
Check the Skip Serial No. Field (if not applicable).
Enter the Work Order number, choose the Inspection Work Center from the pulldown.
The Product Number, Revision and Current Qty will default in.
Then the Passed and Failed buttons are active. The user then clicks on either of these two buttons to proceed with the inspection.
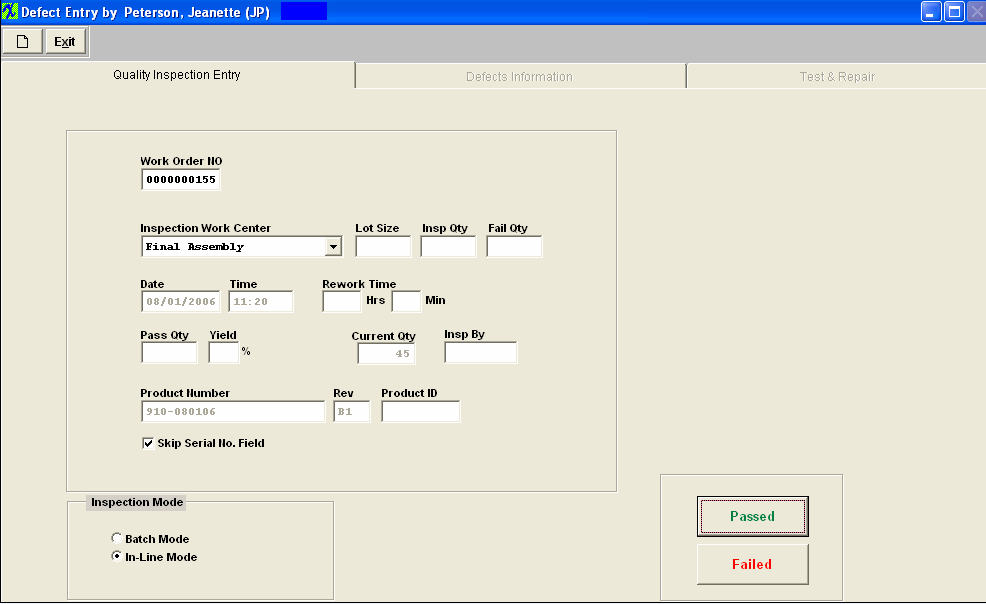
Clicking on the Passed button transfers the serial number to the next work center (based on the product routing), and increments the lot inspection information by one and records the date time and inspector.
Clicking on the Failed button activates the Defect Information Entry screen for the user to record his/her observations.
Defect information is entered in the same fashion as described above, based on with or without serial numbers.
When the user has completed the defect information, may click on the Test & Repair page, to enter more information about the part.
The Test & Repair is actually a separate OPTIONAL module, but has been included into the Defect Entry screen for ease of use for the operators. Please see the Test & Repair article for further detail.
Edit Work Order Defect Information
After a work order has been found or entered, it may be edited by selecting the Edit record action button.
After selecting the transaction, the user may edit fields as described above in entering data.
|
1.1.4.2. Enter the Defect Data Information for the DPMO by Employee Report | In order to have the "DPMO by Employee" report create valid data, the user must be sure to enter the opportunities for defects (PPM) in the Work Order Traveler Setup and the employee must inspect the board and be assigned to the defects. The "DPMO by Employee" report only gathers data if BOTH "Inspected By" and "Emp" are the same user, and the PPM is setup. See Article #3156 for further detail on DPMO. The following steps need to be followed to collect and track defects per employee.
All data must be Entered in the Quality Inspection Entry and Defect Information screens, with in the Shop Floor Tracking Module.
Entering a Defect Code Entry to a Work Order for the "DPMO by Employee" report
Enter Production/Shop Floor Tracking by Work Order Module
Find a Work Order in SFT Module.
| 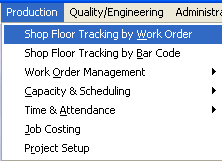 |
The following screen will appear:
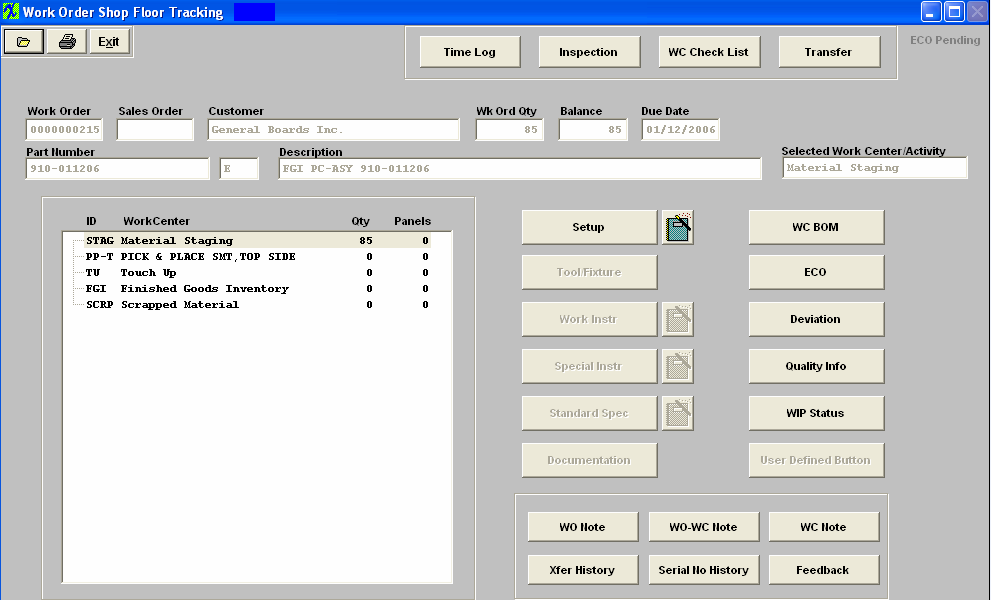
Depress the "Inspection" button located at the top of the screen.
The following screen will appear:
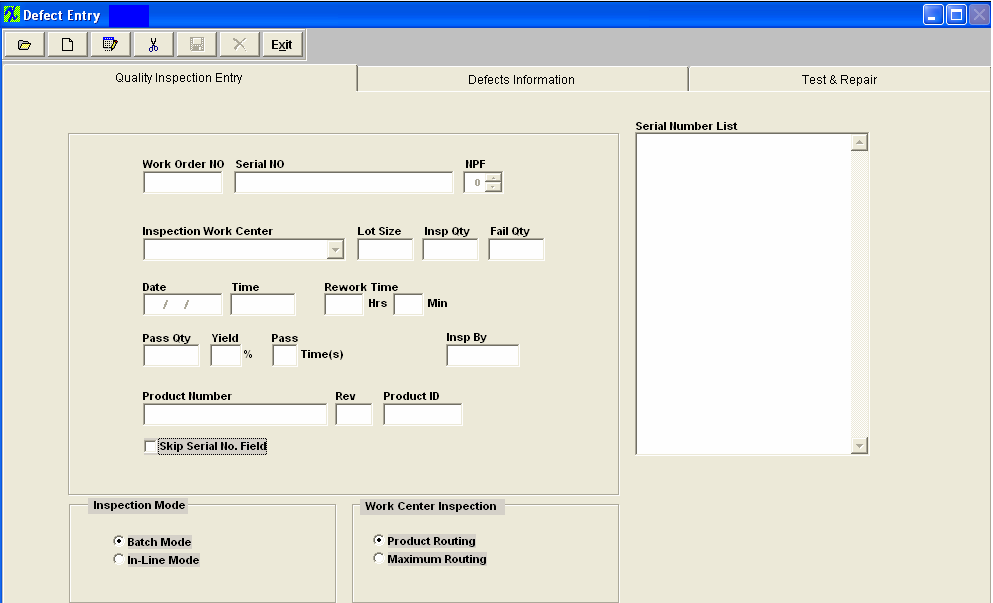
Entering Quality Inspection Data
The first information tab records information about the work order. This includes lot size, failures, inspection quality, date, etc.
Depress the Add action button. Enter the password of the Employee that has inspected the product and will be assigned to the defects. Example: If user "ONE" is going to be assigned to the defect(s) then you must enter user "ONE"'s password.
Check the Skip Serial No. Field (if not applicable).
Enter the Work Order number, choose the Inspection Work Center from the pulldown, enter Lot Size inspected, Inspected Qty, and Failed Qty.
The Date, Time, Pass Qty, and Yeild % will default in.
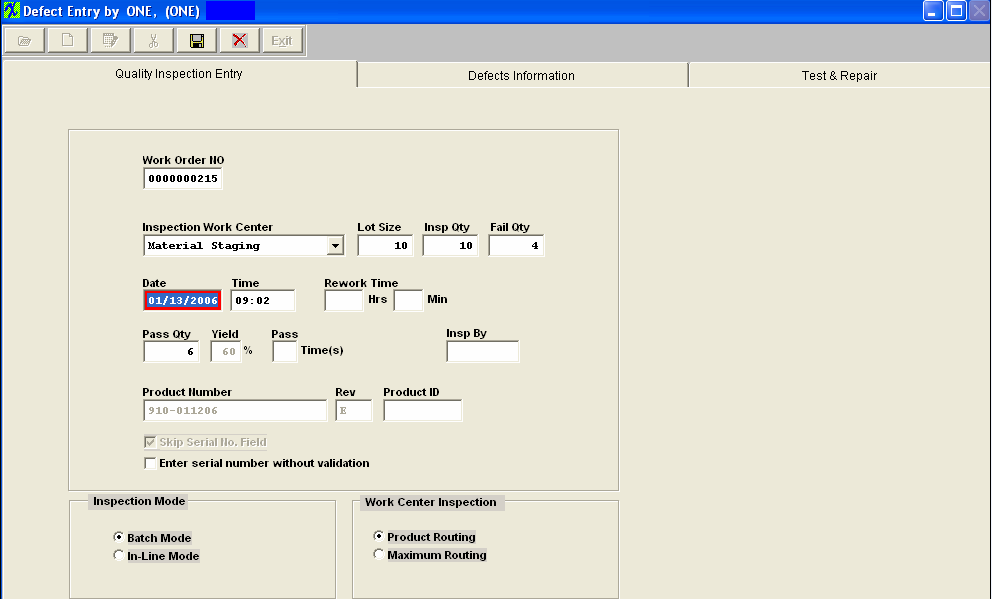
Depress the Defects Information tab and the following screen will appear:
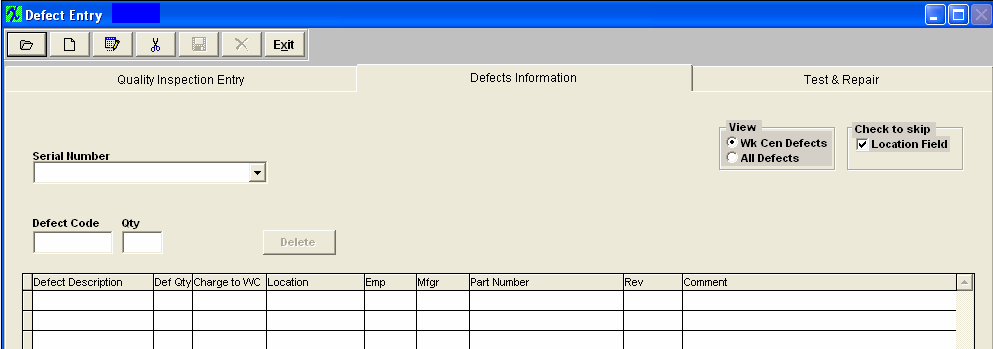
The user may then enter a defect code by manually typing in the code, or by scanning a bar-code menu, or by double clicking on the field to review a list of defect codes.
The list displayed will depend on which view is selected. If Work Center Defects is chosen, only those defects associated with the work center (as established in the Quality Defect Codes setup) will be displayed. If All Defects is chosen, then every defect entered in the Quality Defect Codes setup will be displayed.
The user may select one or more defects from the list by holding down the Control Key while clicking on the defects to be selected.
After completing the selection of the defects involved with the current inspection, clicking on the OK button loads the selected defects into the defect information screen.
Although Manex will enter a Charge To Work Center code based on the work center entered or the location of the part, the user may modify the originating work center by clicking on the field and selecting another work center from the list.
The user may (optionally) then enter in the location (reference designator) where the defect was observed.
The user then must choose the Emp from the pull down, which would be "ONE", because it needs to be the same user that has been entered in the "Inspected By". The user is allowed to enter other user's name on Defect detail page in the "Emp" column. But when the "DPMO by Employee" report is run, it will not display the records assigned to the different users.
The system will check the BOM to be sure that the location entered here matches locations entered on the Bill of Materials.
When a valid location is entered, then system searches the Bill of Material to find manufacturers approved for the product, and displays a list of the approved manufacturers for the user to identify which manufacturer was associated with the defect observed. The user double-clicks on the manufacturer's name for the defective part, and the manufacturers name is placed in the defect information screen.
Manex defaults the number of defects to one item, but the user may overwrite the quantity with an observed quantity greater than one.
The user may also enter a brief comment about the defect, for future reference.
The completed screen should appear as follows:
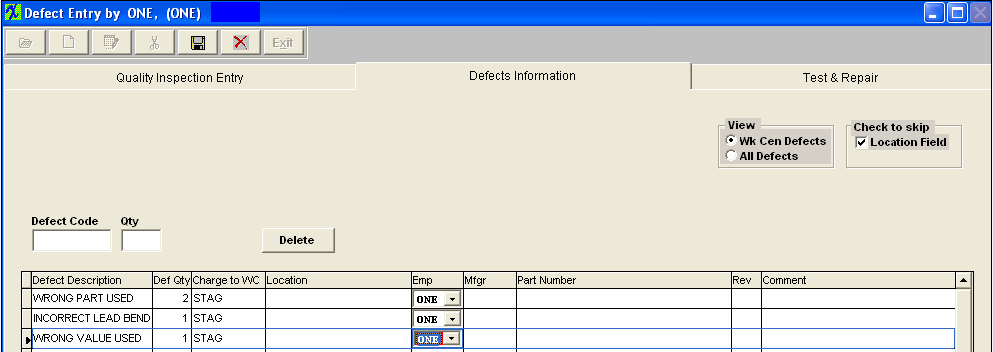
Depress the Save record action button to save changes or the Abandon changes action button to abandon changes.
If you depress the Save record action button, the following message will appear:
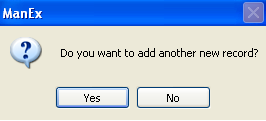
If you want to add another defect record for the same user "ONE" then depress YES, if you want to add a defect record for a different user (Example user "TWO"), then you must depress NO. Depress the Add record action button and enter user "TWO"s password and continue to enter the defect information.
When the user has completed the defect information, he/she may review the "DPMO by Employee" report Article #815, or may click on the Test & Repair page, to enter more information about the part.
The Test & Repair is actually a separate OPTIONAL module, but has been included into the Defect Entry screen for ease of use for the operators. Please see the Test & Repair Management (T&R) article for more information.
|
1.1.4.3. SQC - Setup an SQC Template |
Enter Quality/Engineering/Statistical Quality Control (SQC) Module |
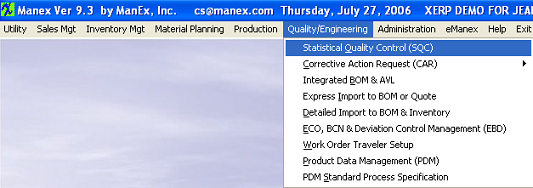 |
The following screen will be displayed:
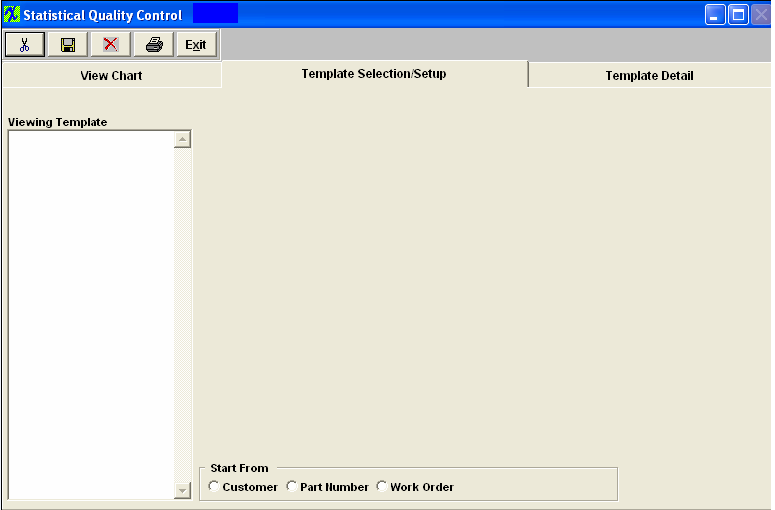
Template Selection Setup
This is the first screen to be used in the module. In this screen, STATISTICAL QUALITY CONTROL graphics are created by selecting parameters to be considered in the graph.
This screen operates differently than all other ManEx screens. When bringing up the SQC module, the user is first presented with a template screen from which to choose parameters to be included in the information displayed.
When the user enters the system, he/she may select how they want to start the process of selection. Click on the Customer, Part Number or Work Order radial.
Clicking on the Customer radial will bring up the following selection screen:
Select either Customer List or All Customers. |
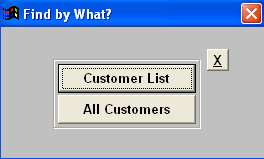 |
Selecting by Customer List will bring up the following selection screen:
(If the user selects by All Customers, the same screen will appear except All available Customers will be listed within the Customer section)
Type the desired customer into the red box or highlight and double click.
|
|
The following screen will appear:
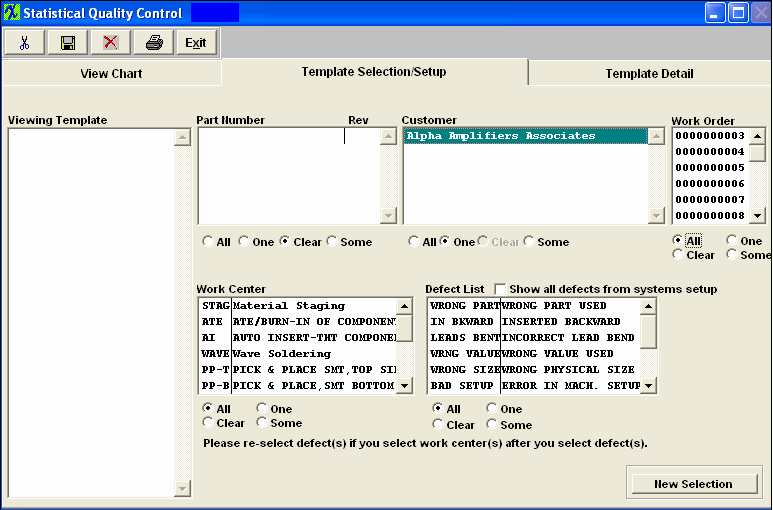
If the start is from Part Number, the following selection will appear: |
|
If the user selects Product Number List, the following list will appear:
(If the user selects All Products, the same screen will be displayed except all products will be listed in the part number section)
Type the Part Number into the red box or highlight and double click.
|
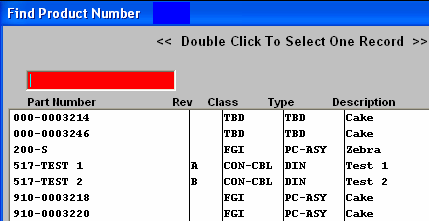 |
The following screen will appear:
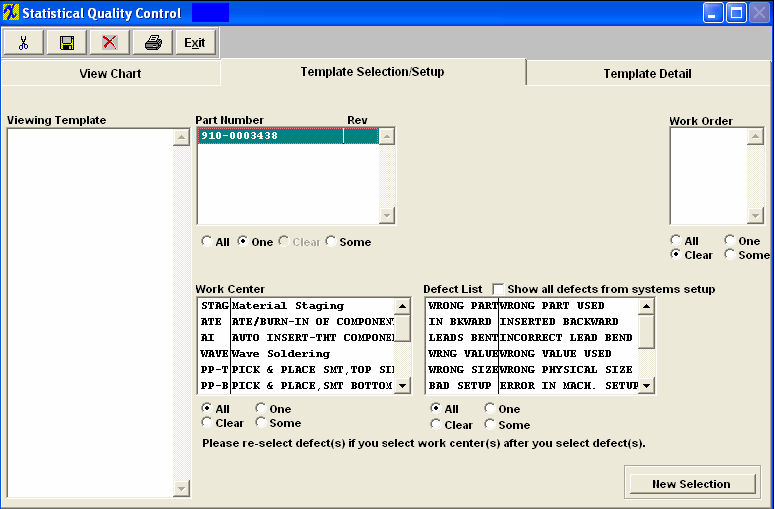
If the user starts with the Work Order start, the following selection will appear:
|
|
If the user selects the Work Order List option, the following list of Work Orders will appear:
(If the user selects All Work Orders the same screen will be displayed except all work orders will be listed in the Work Order section)
Select between Open or All. Type the Work Order Number into the red box or highlight and double click.
|
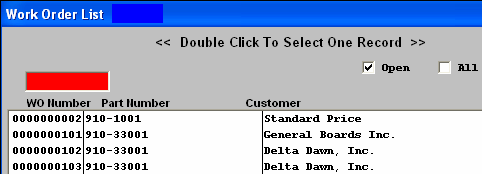 |
The following screen will appear:
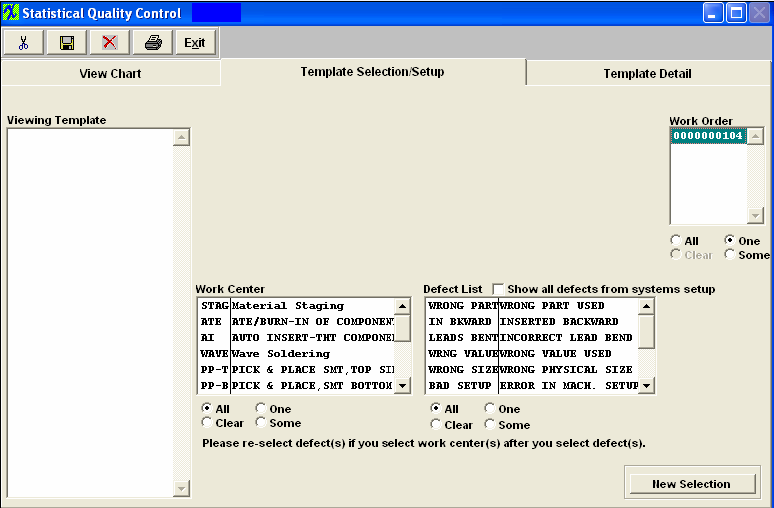
|
In the Work Order section, choose from All, One or Some. If you’ve selected one, highlight the desired work order. If you want more than one, depress the Ctrl key and click on the ones desired.
|
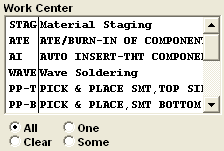 |
In the Work Center section, choose from All, One or Some. If you’ve selected one, highlight the desired work center. If you want more than one, depress the Ctrl key and click on the ones desired.
|
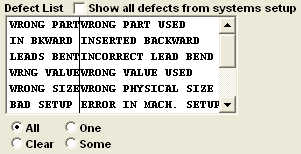 |
Make the same selection in the Defect List section. If you want all defects displaying as per the System Setup, check the Defect List box.
|
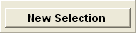 |
To make a new selection, depress the New Selection button.
|
Template Detail Screen
Pressing on the Template Detail tab brings up the following screen:
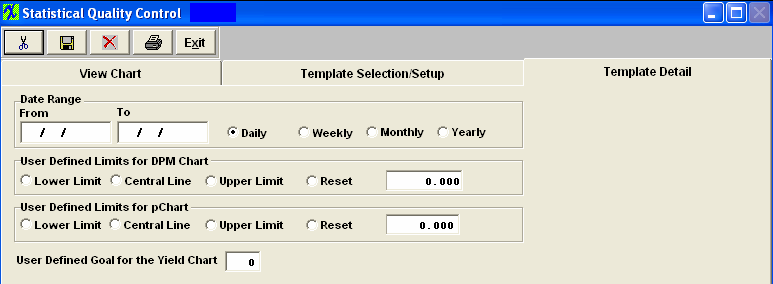
Enter the Date Range, From and To. Mark the Radial for the view by Daily, Weekly, Monthly, or Yearly.
Mark the radial for the User Defined Limits for DPMO chart: Lower Limit, Central Line, Upper Limit or Reset. Indicate Central Line amount in box.
Mark the radial for the User Defined Limits for pChart: Lower Limit, Central Line, Upper Limit or Reset. Indicate Central Line amount in box.
Indicate the user defined goal for the Yield Chart.
To Save this template for future use go back to the Template Selection/Setup tab enter in a name and depress the Save button.
The Template will be saved in the Viewing Template field for future use.
|
1.1.4.4. SQC - Data Viewing And Analysis |
Enter Quality/Engineering/Statistical Quality Control (SQC) Module |
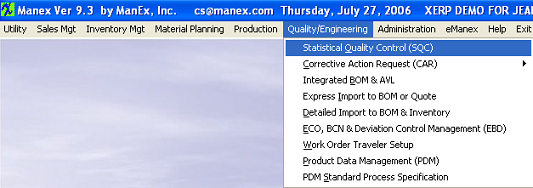 |
The following screen will be displayed:
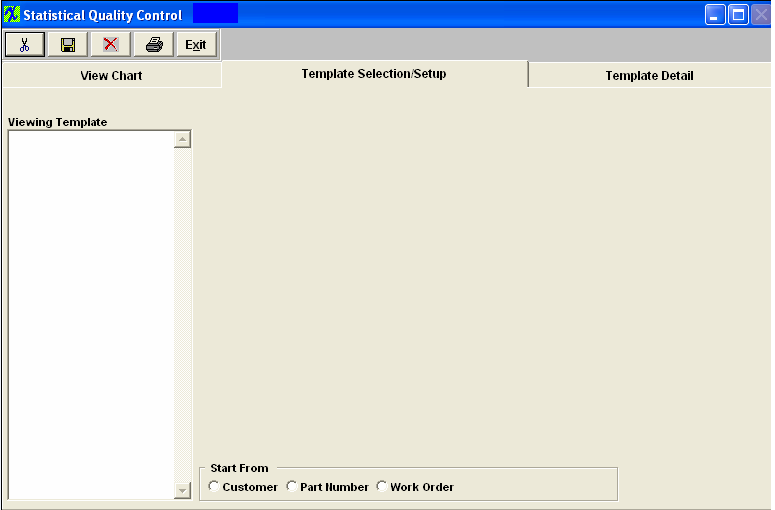
Template Selection Setup
This is the first screen to be used in the module. In this screen, STATISTICAL QUALITY CONTROL graphics are created by selecting parameters to be considered in the graph.
This screen operates differently than all other ManEx screens. When bringing up the SQC module, the user is first presented with a template screen from which to choose parameters to be included in the information displayed.
When the user enters the system, he/she may select how they want to start the process of selection. Click on the Customer, Part Number or Work Order radial.
Clicking on the Customer radial will bring up the following selection screen:
Select either Customer List or All Customers. |
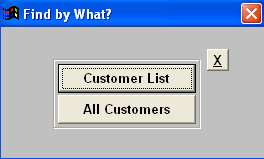 |
Selecting by Customer List will bring up the following selection screen:
(If the user selects by All Customers, the same screen will appear except All available Customers will be listed within the Customer section)
Type the desired customer into the red box or highlight and double click.
|
|
The following screen will appear:
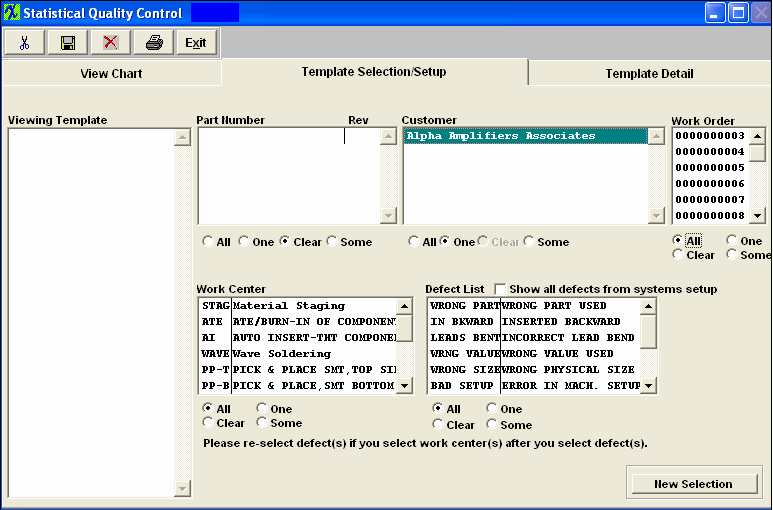
If the start is from Part Number, the following selection will appear: |
|
If the user selects Product Number List, the following list will appear:
(If the user selects All Products, the same screen will be displayed except all products will be listed in the part number section)
Type the Part Number into the red box or highlight and double click.
|
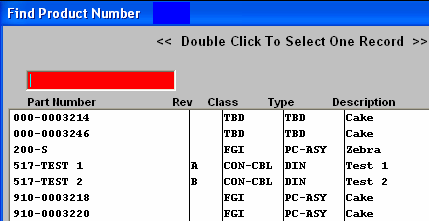 |
The following screen will appear:
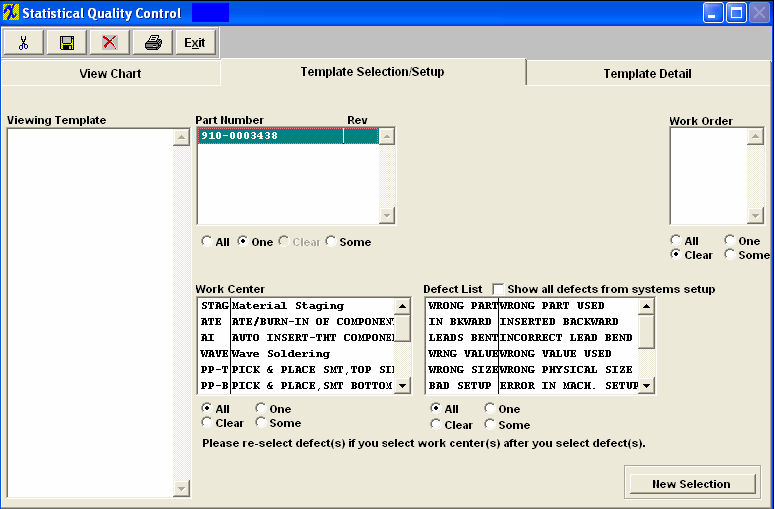
If the user starts with the Work Order start, the following selection will appear:
|
|
If the user selects the Work Order List option, the following list of Work Orders will appear:
(If the user selects All Work Orders the same screen will be displayed except all work orders will be listed in the Work Order section)
Select between Open or All. Type the Work Order Number into the red box or highlight and double click.
|
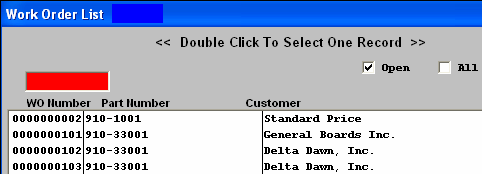 |
The following screen will appear:
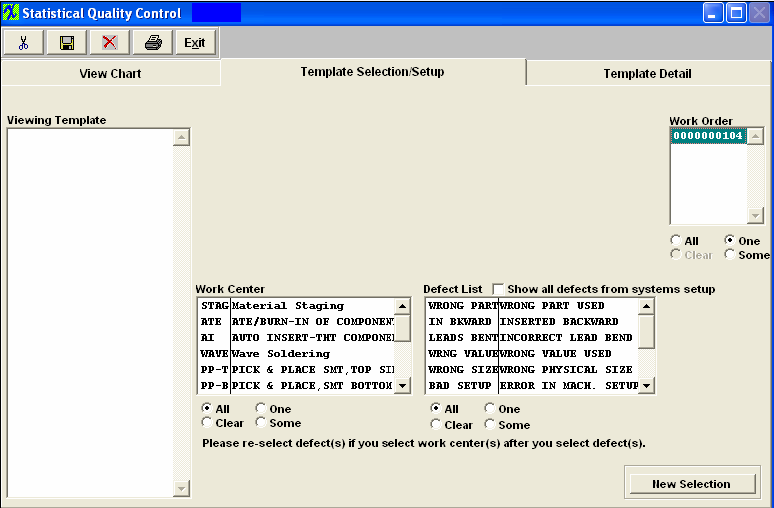
|
In the Work Order section, choose from All, One or Some. If you’ve selected one, highlight the desired work order. If you want more than one, depress the Ctrl key and click on the ones desired.
|
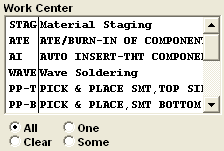 |
In the Work Center section, choose from All, One or Some. If you’ve selected one, highlight the desired work center. If you want more than one, depress the Ctrl key and click on the ones desired.
|
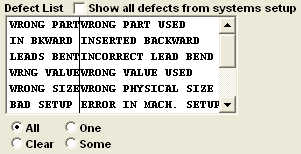 |
Make the same selection in the Defect List section. If you want all defects displaying as per the System Setup, check the Defect List box.
|
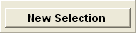 |
To make a new selection, depress the New Selection button.
|
Template Detail Screen
Pressing on the Template Detail tab brings up the following screen:
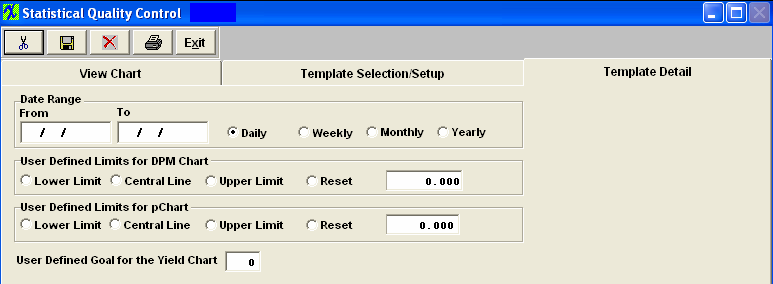
Enter the Date Range, From and To. Mark the Radial for the view by Daily, Weekly, Monthly, or Yearly.
Mark the radial for the User Defined Limits for DPMO chart: Lower Limit, Central Line, Upper Limit or Reset. Indicate Central Line amount in box.
Mark the radial for the User Defined Limits for pChart: Lower Limit, Central Line, Upper Limit or Reset. Indicate Central Line amount in box.
Indicate the user defined goal for the Yield Chart.
View Chart Screen/Graphs
Pressing on the View Chart brings up the Graphics Display Window.
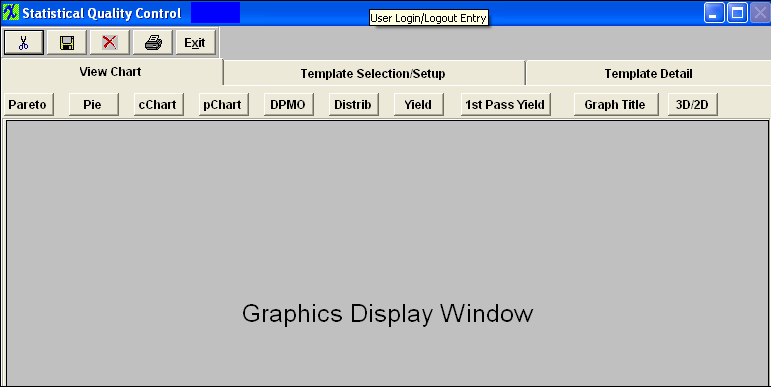
Defect Pareto Chart - The results being displayed in the Pareto Chart are from WO #242 for a build of 500. Qty of 5 with Wrong Part (Displayed in Blue) and Qty of 3 with Leads Bent (Displayed in Green) Total of 8 Failed 500/8 = 62.5% Failed and 37.5% Passed
Note: The black line is a cumulative % of total defects represented by the current defect and all preceding defects. That is why it reaches 100% by the right side of the graph.
Defect Pie Chart - The results being displayed in the Defect Pie Chart are from WO #242 for a build of 500. Qty of 5 with Wrong Part (Displayed in the Blue) 62.5% and Qty of 3 with Leads Bent (Displayed in Green) 37.5%. Total qty failed 8.
cChart (Not available in 3D) The results being displayed in the cChart are from all Work Orders, Work Centers, and all defects from 062706 thru 072706 (1 month)
The formula for the Central line (Red) is: c = Total Defects (divided by) Number of Subgroups
Upper Control Limit (UCL) = c + 3 (divided by) p
Lower Control Limit (LCL) = c - 3 (divided by) p (or 0, whichever is greater)
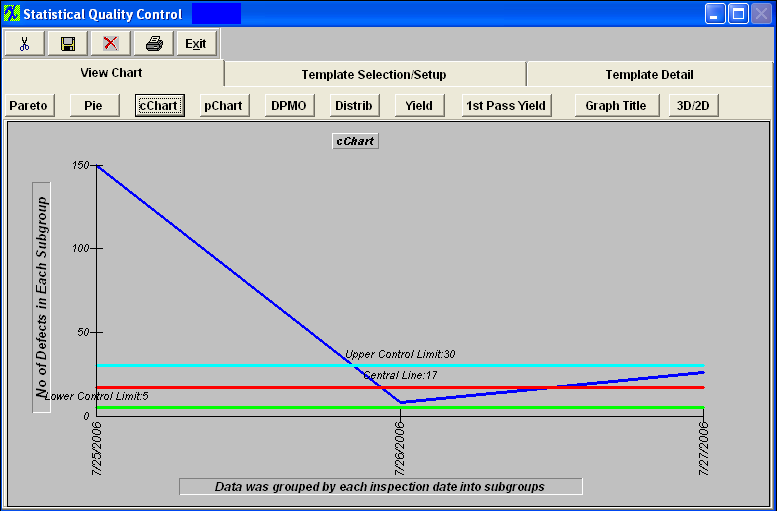
pCHART (not available in 3D) The results being displayed in the pChart are from all Work Orders, Work Centers, and all defects from 062706 thru 072706 (1 month)
The formula for the Central line (Red) is: p = Total Number Failed (divided by) Total Number Inspected
Upper Control Limit (UCL) = p + 3 (divided by) p (1-p) divided by n
Lower Control Limit (LCL) = p - 3 (divided by) p(1-p) divided by n (or 0, whichever is greater)
n = number inspected (sample size)
DPMO (Defects Per Million Opportunities) Chart (Which means the number of things wrong observed in the inspection of a part, or board assembly). The results being displayed in the DPMO Chart are from WO #242 for a build of 500. DPMO Example below = 8(Total qty failed)* 1000000/100*500 (Qty Inspected) = 160
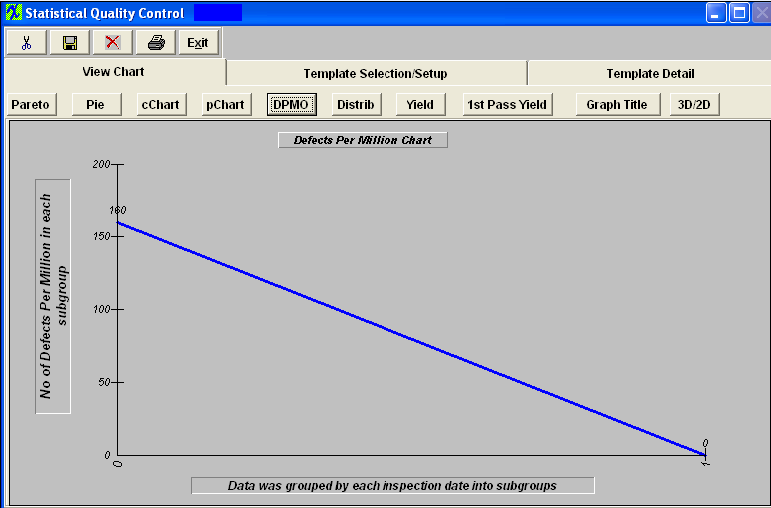
Defects Per Million Opportunities. There are several ways to setup the opportunities (which means the number of possible defects that can occur on a product), but it is up to each company to make that decision. For Example: Some may say that a resistor with two leads that are not properly soldered is counted as two defects and some may only count it as one defect, since it is one part that was assembled incorrectly. The opportunity or the standard opportunity is entered in the Work Order Traveler Setup module. The field is called PPM = Parts per million.
The DPMO chart uses the PPM as a reference to measure the actual failures against the total inspected quantity.
See Article #3156 for further detail on DPMO.
The formula for calculating DPMO chart is as follows:
Example (2+3+3) = SUM of defect quantities (8) * opportunities or PPM (1,000,000) (divided by) Qty Inspected (500) (divided by) parts per unit (100) = 160
Daily, Weekly, Monthly, Yearly
On the Y axes the graph shows number of defects per million
One the X axes day or week or month or year
This graph collects defect information for the selected work centers and work orders in the selected date range. The user also has to select if the information will be grouped by day, week, month, or year.
The selected group will be your X coordinates on the graph.
The Y coordinates will be calculated as sum of the defect quantities *opportunities or PPM divided by total Qty inspected (divided by) parts per unit (qty was entered in the routing module) grouped by X coordinate unit (Daily, weekly, monthly, yearly).
This is a data line there is three more control lines displayed on the graph:
Central control line:
Upper control line:
Lower control line
All three lines could be user define lines.
If the lines are not user define lines they calculated as following
Central Line
lnCentralLine=lnTotalDef/lnTotalComp, where lnTotalDef is sum of all defect quantities * 1000000 and lnTotalComp is sum of inspected quantities*Parts Per Unit (entered in the routing module)
At this time system will decide if it can use average group size or not. If the size group varies more tan 15% the system will use variance Upper and Lowercontrol limit. If average group size could be used the average group size gets calculated by taking lnAvrgSubgrSize=lnTotalComp divided by number of groups and rounded to the nearest integer.
Calculation for the Upper Control Line
LnUpperLine=ROUND(((3*(SQRT(lnCentrLine*(1000000-lnCentrLine))))/SQRT(lnAvrgSubgrSize)),3)
Calculation for the Lower Control Line
lnLowerLine = ROUND(lnCentrLine -((3*(SQRT(lnCentrLine*(1000000-lnCentrLine))))/SQRT(lnAvrgSubgrSize)),3)
lnLowerLine = IIF(lnLowerLine<0,0,lnLowerLine)
Defects Distribution Chart - The results being displayed in the pChart are from all Work Orders, Work Centers, and all defects from 062706 thru 072706 (1 month)
Yield Chart - "Yield" = Total number of units handled correctly through the process step(s). This is usually measured in a percentage. The results being displayed in the "Yeild Chart" is the ratio of summed inspected qty and summed passed qty, grouped by date (user can select WO number, defect code to be filtered). The results below are from all Work Orders, Work Centers, and all defects from 062706 thru 072706 (1 month).
1st Pass Yield Chart The results being displayed are from all Work Orders, Work Centers, and all defects from 062706 thru 072706 (1 month).
1st Pass Yield chart in the SQC module is designed only when the serial number is used for the work order. The system uses the serial number to determine how many serial numbers passed without failure/defects within a work order. 1st Pass Yield chart will be blank if there are no product tracked by serial number within the production floor
To enter a new title, depress the Graph Title button. The following will be displayed:
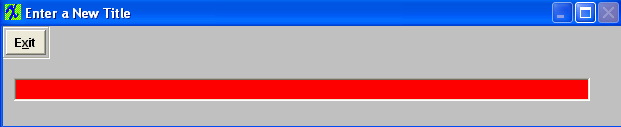
Enter in the new desired Graph Title. Depress the Exit button, and the graph title will be updated.
3D/2D - This is if you want to view the 1st Yield Chart in 3D
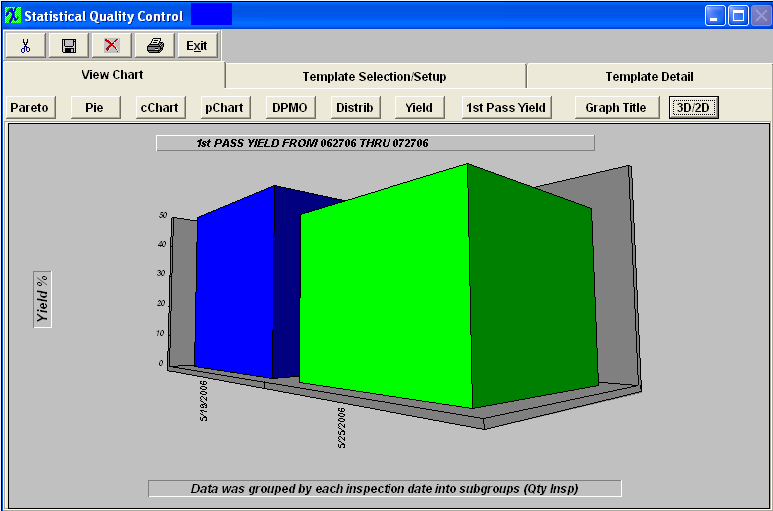
|
1.1.5. Reports - SQC |
To display or print a Report from the Statistical Quality Control (SQC), module. Enter the module.
1. To access the reports, depress the Print action button at the top of the screen. The report screen will appear.
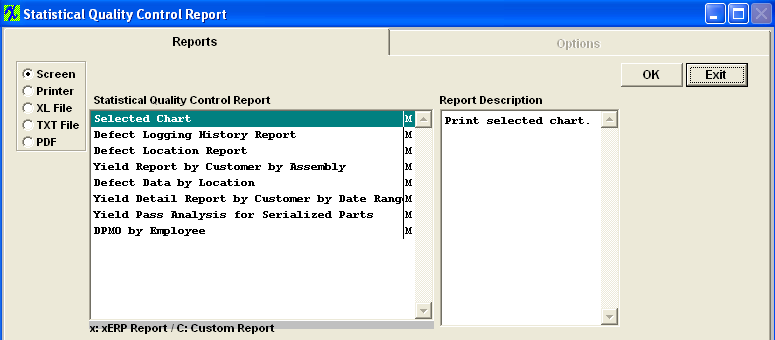
2. Select the output you desire by selecting one of the output radial selections at the top left of the screen, Screen, Printer, XL File, TXT File, or PDF.
3. Highlight the report desired and click on the option tab (if applicable).
Selected Chart report
If you want to print the selected chart, the chart you want to print must be displaying in the View Chart tab. The same exact chart viewed on screen will be printed.
Depress the OK button, and you will receive the following message. The selected chart only goes to printer or file, please go back to main screen to view chart.
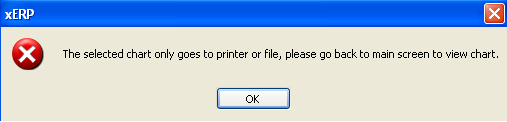
Defect Logging History report
If you select Defect Logging History Report, you will be asked to select the sort.
Select one of the following:Customer, Product Number, Work Order Number or Work Center.
|
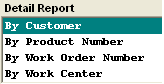 |
Select the date range. Highlight the Customer desired. Depress the > button. If you want all customers, depress the >> button.
Depress the Ok button.
|
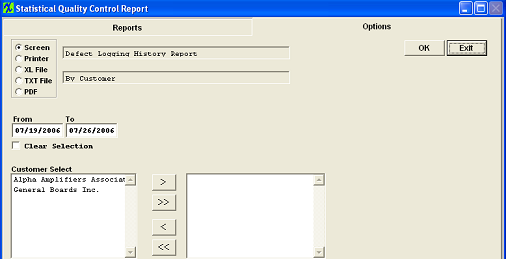 |
The following report will print:

Defect Location report
Select the date range. Highlight the Customer desired and depress the > button. If you want all customers, depress the >> button. Highlight the Work Center and depress the > button. If you want all Work Centers, depress the >> button.
Depress the OK button.
|
|
The following report is available:
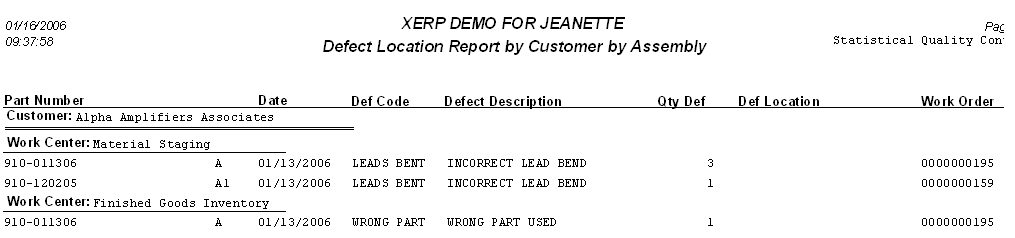
Yield Report by Customer by Assembly report
Select the date range. Highlight the Work Center and depress the > button. If you want all Work Centers, depress the >> button.
Depress the OK button.
|
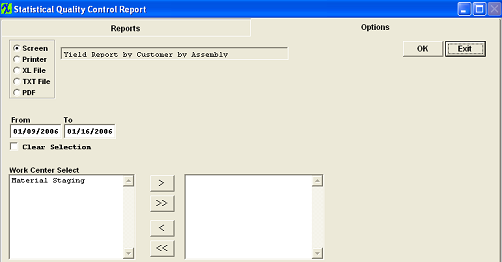 |
The following report will print:
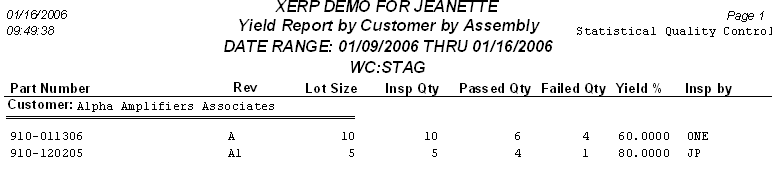
Defect Data by Location report
First you must enter data in Template Selection/Setup and Template Detail Screen. Then depress the Print action button, Highlight the Defect Data by Location report and depress the Ok button.
The following report will print:
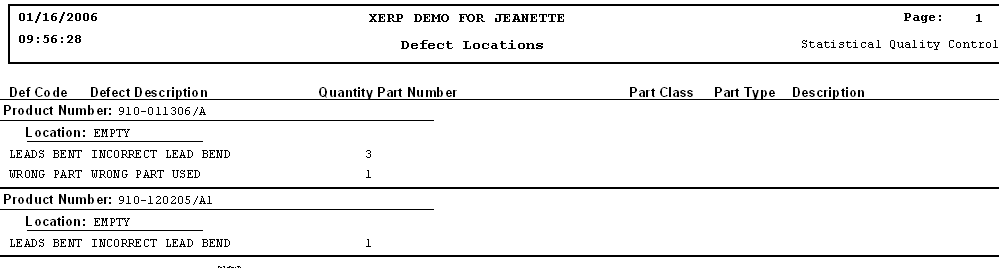
Yield Detail Report by Customer by Date Range
Select the Date Range. Click on the desired radial to select Open Work Orders only or All Work Orders. Highlight the Work Order desired and depress the > button. If you want all Work Orders, depress the >> button. Highlight the Work Center and depress the > button. If you want all Work Centers, depress the >> button. Highlight the Customer desired and depress the > button. If you want all customers, depress the >> button.
Depress the OK button
|
|
The following screen will appear:

Yield Pass Analysis for Serialized Parts report
Select the Date Range. Type the Yield Pass Number. Highlight the Work Center and depress the > button. If you want all Work Centers, depress the >> button.
Depress the OK
|
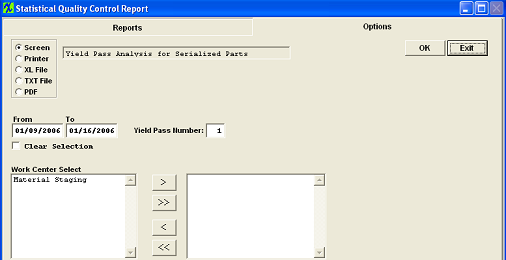 |
The following report will print:
DPMO by Employee
Select the Date Range. Highlight the Work Center desired and depress the > button. If you want all Work Centers, depress the >> button. Highlight the Employee and depress the > button. If you want all Employee's, depress the >> button.
Depress the OK button.
DPMO = Number of defect * opportunities or PPM (1,000,000) (divided by) Qty Inspected (divided by) parts per unit
In order to make this report data valid, the employee must inspect the board and be assigned to the defect. For more information see Article #1776.
|
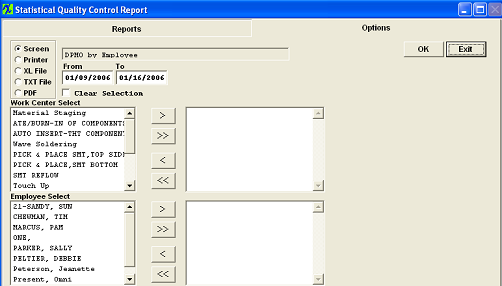 |
For Example: the PPM for each work center is:
Work center PPM
STAG 2
SMT 1
FGI 5
SCRP 3
User ONE inspect two records in Defect code entry module:
1) Insp Qty 10, Work Center: STAG
Defec detail:
Defect Code Chg WC Defect Qty Emp
Defect-1 STAG 2 ONE
Defect-2 SMT 1 JM
Defect-3 STAG 5 ONE
2) Insp Qty 20, Work Center: SMT
Defect Detail:
Defect Code Chg WC Defect Qty Emp
Defect-4 SMT 1 ONE
Defect-3 SMT 4 ONE
Defect-6 WAVE 7 MP
If user selects all work centers (on report option page)
The Defect Qty for ONE will be 2+5+1+4 = 12
Number of Unit*Number of opportunities = 2*10+1*20=40
DPMO for User ONE is 12*1,000,000/40=300,000
As displayed:

The user has option to select for certain work centers, for example, if user only selects for "STAG" work center, then
The Defect Qty for ONE will be 2+5 = 7
Number of Unit*Number of opportunities = 2*10=20
DPMO for User ONE is 7*1,000,000/20 = 350,000
As displayed:

|
1.1.7. ManEx Minutes (SQC) |
1.2. Corrective Action Request (CAR) (OPTIONAL Module) |
1.2.1. Prerequisites for CAR | Prerequisites Required for Entering a New Corrective Action Request:
ManEx’s standard module configuration allows most users to accomplish their daily tasks. For those users wanting to get more from ManEx by leveraging the total solutions, this is one of the optional modules available for purchase. To place an order or to learn more about this specific module or any of the other optional modules please contact us at http://manex.com\contactus.aspx
After activation, "Corrective Action Request" (CAR) access for each user must be setup in the ManEx System Security module. Users with “Supervisor Rights” will automatically have access.
Quality Inspection Entry |
A Quality Inspection entry must have been entered in Work Order Shop Floor Tracking. |
Customer |
The Customer database must be established for Consigned part numbers. |
Supplier |
The Supplier database must be established for purchased parts. |
Part number in Item Master |
The part number must exist for a product or part. |
Quality Defect Codes |
The Defect Codes and Names have been entered in System Setup. |
CAR Types |
The Corrective Action Request types must have been entered in System Setup. |
CAR Number Type |
The Corrective Action Request Numbers must have been entered in System Setup. |
Work Center |
The Work Center must have been entered in System Setup. |
Work Order |
There must be a Work Order associated with the Corrective Action Request. |
|
1.2.2. Introduction for CAR | The Corrective Action Request (CAR) module is used to record and track to the conclusion of all corrective action requests.
The user may establish his/her own type(s) of corrective actions in the system setup. Examples of types of corrective actions may be Supplier, Customer, Production, Administration, etc. In addition to classifying corrective actions by type, the user may also establish number types for the corrective action. Examples of number types might be RMA, DMR, Internal, etc.
The user enters information relating to each CAR including ISO reference, Quality Manual Descriptions, Customer/Supplier information and/or Work Center/Department involved.
There is provision for text entry of the Description of Condition, the Apparent Cause, and the Actual Cause, along with provision to enter a graphics image.
In the Corrective Action section, there is provision to enter Corrective Action Taken, as well as information for Follow Up & Review.
In the Main screen, a list of all open corrective actions is displayed, and may be sorted by Due Date, New Due Date (if revised), CAR number or CAR Type. There is provision to enter the name of the CAR Coordinator, and include a list of team members and their percent completion of the task. There is also a place for users to enter the date and name of the team member who verified the problem; the date and name of the team member who granted the final approval of the CAR; the date and name of the team member who followed up on the CAR; and the date and name of the team member who closed the CAR.
|
1.2.3. Fields and Definitions for CAR |
1.2.3.1. Open List Tab | 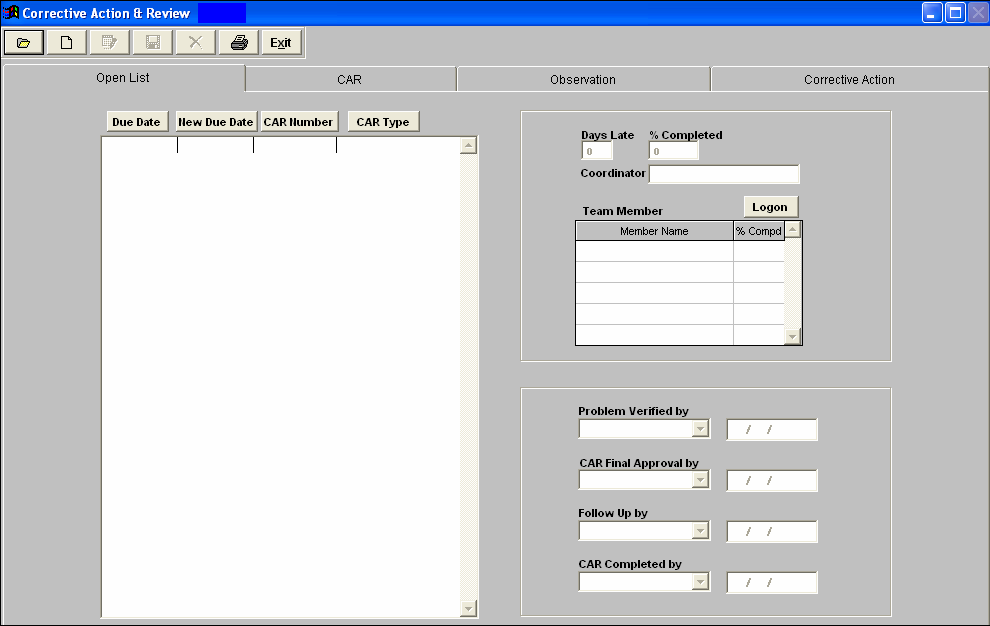
|
1.2.3.2. CAR Tab | 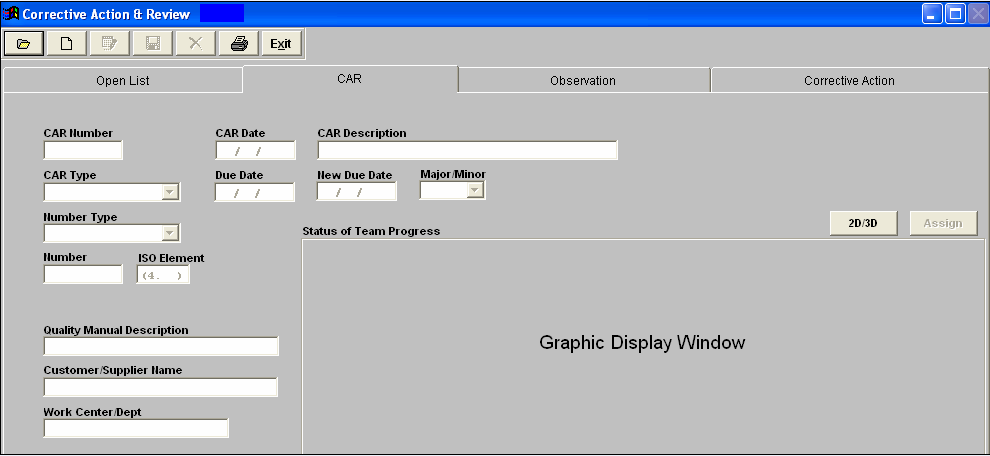
CAR Number
|
The number assigned to the Corrective Action Report.
|
CAR Date |
The date the Corrective Action Report was created. |
CAR Description |
The description of the Corrective Action Report. |
CAR Type |
The type of Correction Action. |
Due Date |
The due date of the Correction Action.
|
New Due Date |
If revised, the revision due date.
|
Major/Minor |
Describes whether the corrective action is major or minor.
|
Number Type |
The type of CAR number as set up in system setup.Please refer to the Implementation – Production manual.
|
Number |
The number associated with the Number Type. |
ISO Element |
The element pertaining to ISO. |
Quality Manual Description |
This is a read only field. |
Customer/Supplier Name |
If the CAR type is Customer, the name of the customer will appear. If the CAR type is Supplier, the name of the supplier will appear here. |
Work Center/Dept. |
If the CAR type is Work Center/Dept., the name of the Work Center or Department will appear here. |
Status of Team Progress section
Graphics Display Window |
If some work has been completed by the team and registered in the Open List tab, a graph displaying the percentage of completion by each team member will display.
|
|
 |
Depress this button to change graph view to 3D or back to 2D.
|
|
 |
This button will bring up a list of users who can be assigned to the CAR team.
In order for the user to be displayed on this list they must have Edit or Add rights to the CAR module within the ManEx System Security module. Users with “Supervisor Rights” will automatically have access.
.
|
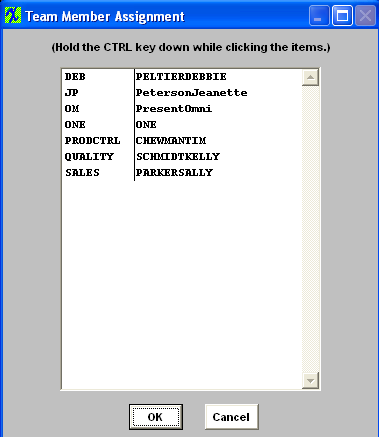 |
|
1.2.3.3. Observation Tab | 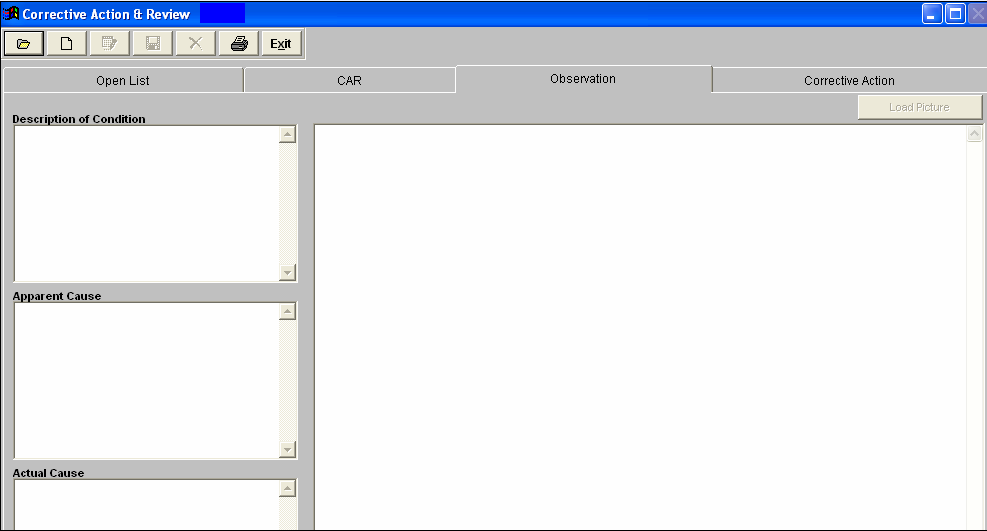
Description of Condition
|
This window will display the description of the CAR.
|
Actual Cause |
This window will display the actual cause.
|
Apparent Cause |
This window will display the apparent cause.
|
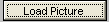 |
This window will display a schematic.
|
|
1.2.3.4. Corrective Action Tab |
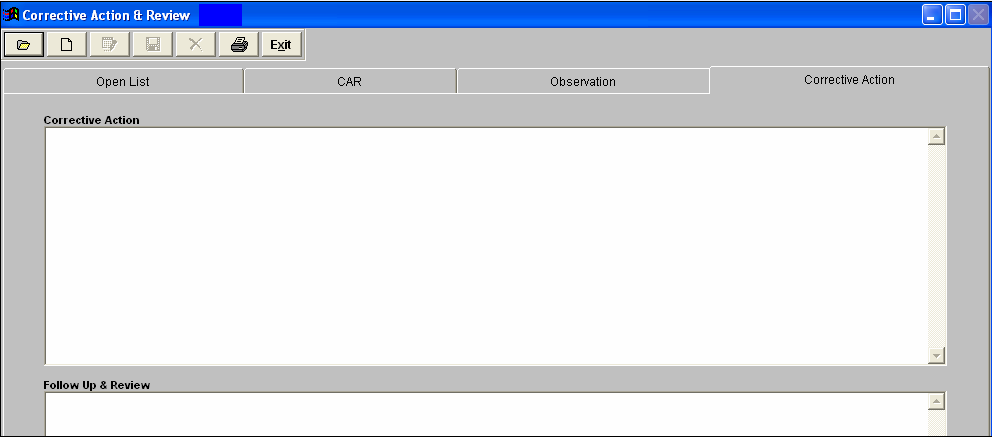
This tab is available for notes regarding corrective action and follow up and review.
|
1.2.4. How To ..... for CAR |
1.2.4.1. Finding A Corrective Action Request Record |
Enter Quality/Engineer/Corrective Action Request(CAR/Corrective Action Request (CAR) |
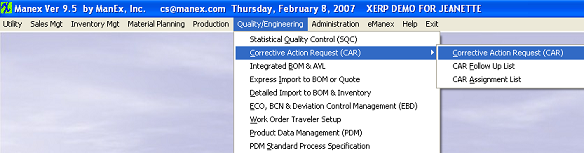 |
The following screen will appear:
Depress the Find Record action button .
The following selections will be displayed:
|
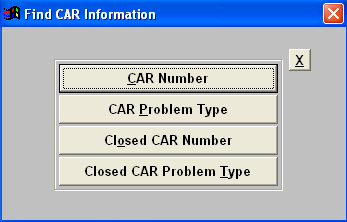 |
Find by CAR Number
Depressing the Find by CAR Number button, will display the following listing of all of the Open CAR Numbers available.
Type the CAR Number into the red box or highlight and Double Click to select.
|
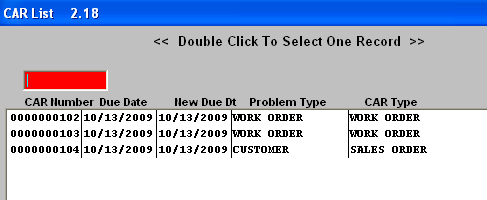 |
Find by CAR Problem Type
Selecting the Find by CAR Problem Type option, will display the following listing of Open records.
Type the problem type into the red box or highlight and double click.
|
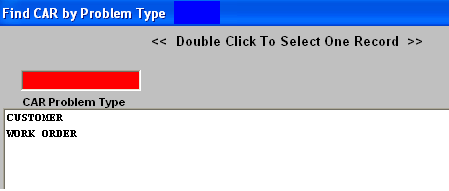 |
The following selection screen will appear:
Type the CAR Number into the red box or highlight the selection and double click.
|
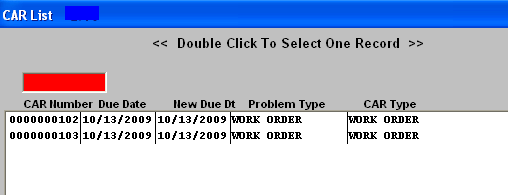 |
Find by Closed CAR Number
Selecting the find by Closed CAR number, will display the following listing of Closed CAR’s.
Type the CAR Number into the red box or highlight the selection and double click.
|
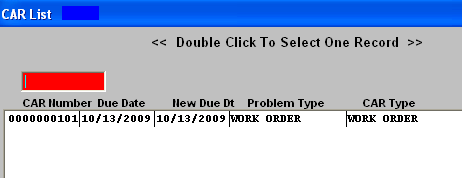 |
Find by Closed CAR Problem Type
Selecting the Find by Closed CAR Problem Type, will display the following listing:
Type the CAR problem type into the red box or highlight the selection and double click.
|
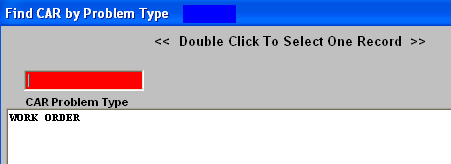 |
A list of all closed CAR's for that problem will appear:
Type the CAR number into the red box or highlight and double click.
|
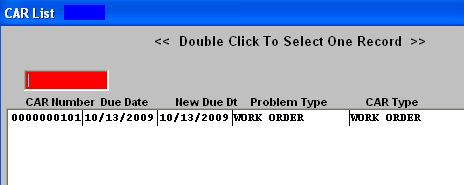 |
|
1.2.4.2. Adding a Corrective Action Record |
Enter Quality/Engineering/Corrective Action Request(CAR)/Corrective Action Request (CAR) |
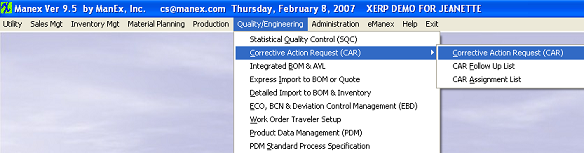 |
The following screen will be displayed:
Depress the Add Record action button. The following screen will be displayed:
Enter the CAR Description.
Depress on the down arrow to select the CAR Type:
|
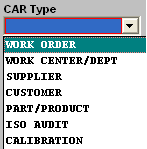 |
If you select Work Center/Dept, a further selection screen will appear.
Select one Work Center or Department. Upon selection, the name of that Work Center will appear in the Work Center/Department box.
|
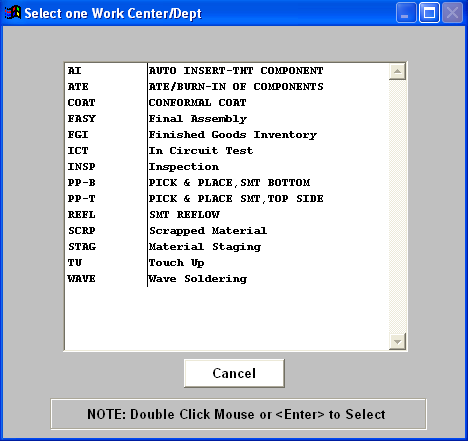 |
If you selected Customer or Supplier from the above as the CAR Type, a further selection screen will appear:
The Supplier List will be sorted by Supplier Number. The Customer List will be sorted by Customer Name in Alphabetical Order.
The name of the Customer or Supplier will appear in the Customer/Supplier Name box.
|
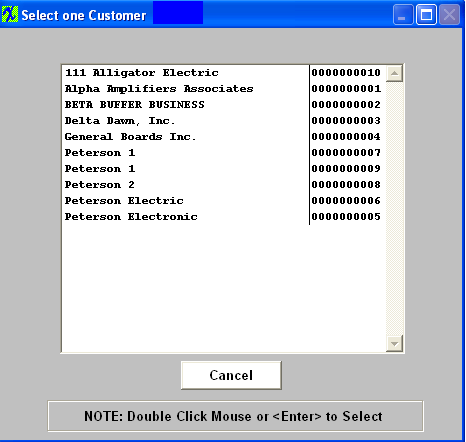 |
Enter the Due Date and New Due Date.
Depress on the down arrow to select whether the problem is Major or Minor.
|
 |
Depress the down arrow next to the Number Type field. The following list will appear:
Select the type applicable to the CAR.
|
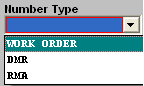 |
Enter in the Number, Work Order, DMR or RMA and the ISO element.
Depress the Assign button and a list of employees will appear that have Add or Edit access rights to the CAR module setup in the ManEx System Security module. Users with “Supervisor Rights” will automatically have access.
Make the selection for the Team Members.
Depress the OK button.
|
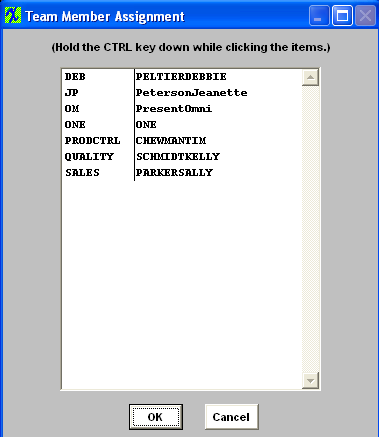 |
Depress the Observation Tab to enter - Description of Condition, Apparent Cause, and Actual Cause information. Within this screen user can also Load a Picture if applicable.
Depress the Corrective Action tab to enter the Corrective Action and Follow Up and Review information.
Once user has completed adding all the pertain information for the CAR. They may depress the Save button to save the changes or depress the Abandon Changes button to abandon all changes.
The completed screen should appear as follows:
Depress the Open List tab - The Due Date, New Due Date, CAR Number and CAR Type will be displayed for all open records.
Depress the Edit button and the Approval lists will be enabled:
|
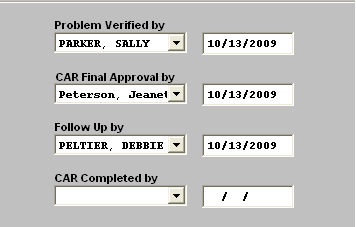 |
To enter a percentage of completion, place the cursor in the % Completion column. Enter in the percentage completed. Depress the Enter key. You will be prompted for the password. The password entered must “match” the name of the user.
The user may then depress the CAR tab to view the Team Member Project Status of completion graph.
To obtain a 3D version, depress the 2D/3D button.
|
1.2.4.3. Editing a Corrective Action Request Record | Find the CAR of interest and the following screen will appear:
Depress the Edit record and the following fields will become activated on the Open List screen:
Depress the down arrow next to each or desired fields. A list of employees will display. Note: That an entry in the CAR Completed By field will Close the record.
Depress the CAR tab and the following fields are activated when editing a record:
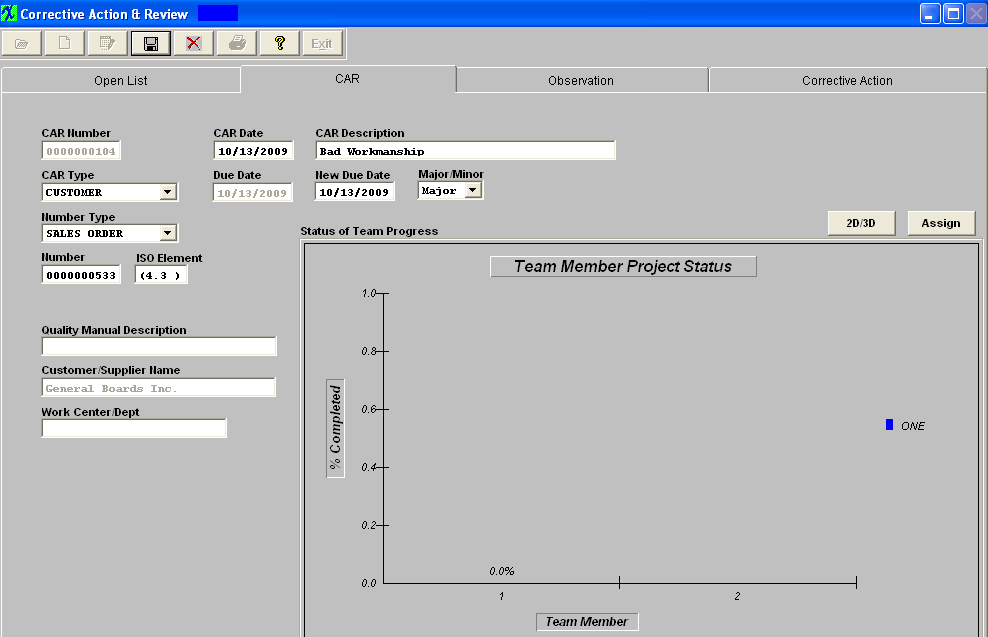
Depress the Observation tab enter any Description of Condition, Apparent Cause, or Actual Cause information.
If you wish to load a picture, depress the Load Picture button. The following dialog box will be displayed.
Select a bit map image/file you want to load by highlighting and double clicking. The load picture will display the image loaded.
Depress the Corrective Action tab - and enter any Corrective action and/or Follow Up & Review information:
Once the desired information has been entered into the appropriate locations, depress the Save Button, and enter your password.
|
1.2.5. Reports - CAR |
Depress the Printer icon. The following screen will be displayed: |
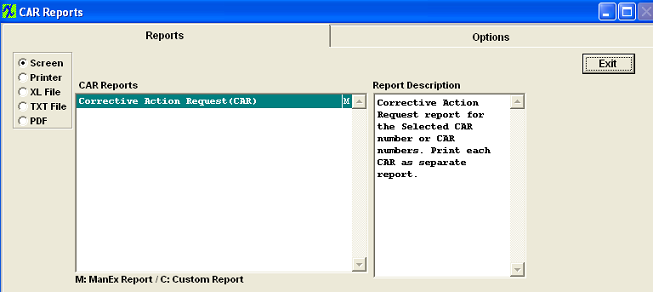 |
Enter the Option tab, the following will be displayed:
Select whether you want an Open CAR or a Completed CAR by clicking on the radial. Highlight the CAR you want and then click on the > button. If you want all of the CARs, depress on the >> button. Toggle on the arrows to select the number of copies you want.
Depress the OK button.
|
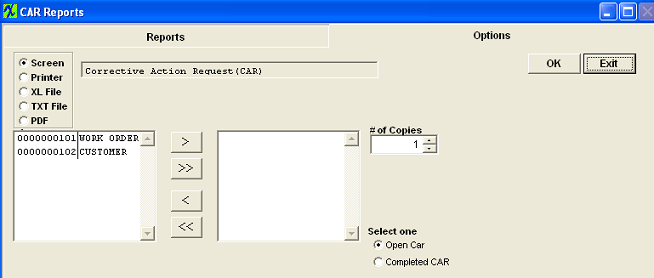 |
The following report is available:
|
1.2.6. CAR Follow Up List |
Enter Quality/Engineering/Corrective Action Request (CAR)/CAR Follow Up List
After activation, "Corrective Action Request" (CAR) access for each user must be setup in the ManEx System Security module. Users with “Supervisor Rights” will automatically have access.
|
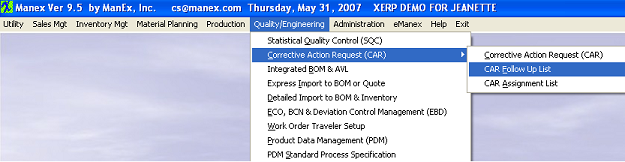 |
The following screen will be displayed:
Displayed will be all of the Correction Action Requests upon which follow up action has taken place.
The fields displayed are as follows:
Member Name |
This is the name of the Quality Control Team member who did the follow up inspection.The user may sort on this column by depressing the Member Name button.
|
Follow Up Date |
This is the date when the Quality Control Team member did the follow up inspection.The user may sort on this column by depressing the Follow Up Date button.
|
CAR No. |
The number assigned to the Corrective Action Request.The user may sort on this column by depressing the CAR No. button.
|
Description |
The description of the problem leading to the issuance of the Corrective Action Request, such as broken, wrong part, etc.The user may sort on this column by depressing the Description button.
|
Depressing the Reports icon, the system will then display the following dialog box.
Select the desired Printer.
Depress the OK button and the report will be sent directly to the selected printer.
|
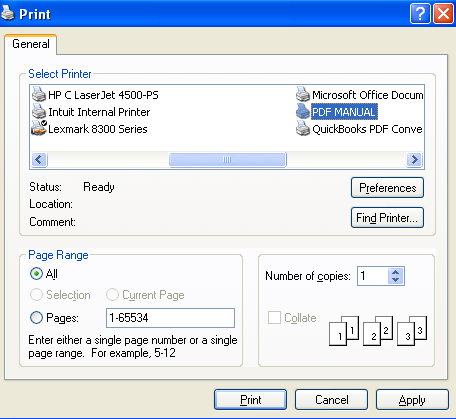 |
|
1.2.7. CAR Assignment List |
Enter Quality/Engineering/Corrective Action Request (CAR)/CAR Assignment List
After activation, "Corrective Action Request" (CAR) access for each user must be setup in the ManEx System Security module. Users with “Supervisor Rights” will automatically have access.
|
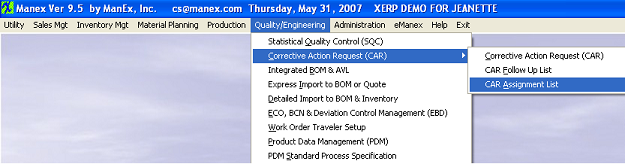 |
The following screen will be displayed:
This screen will display all of the Corrective Action Request for which a team member has been assigned, and has not been completed.
The fields displayed are as follows:
Member Name |
This is the name of the Quality Control Team member who was assigned to the problem.The user may sort on this column by depressing the Member Name button.
|
CAR No. |
The number assigned to the Corrective Action Request.The user may sort on this column by depressing the CAR No. button.
|
Due Date |
This is the date by which the Quality Control Team member will do the correction action.The user may sort on this column by depressing the Follow Up Date button.
|
Description |
The description of the problem leading to the issuance of the Corrective Action Request, such as broken, wrong part, etc.The user may sort on this column by depressing the Description button. |
Depressing the Reports icon, the system will then display the following dialog box.
Select the desired Printer.
Depress the OK button and the report will be sent directly to the selected printer.
|
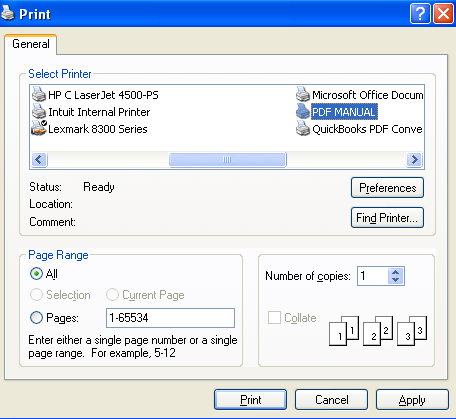 |
|
1.3. Integrated BOM & AVL |
1.3.1. Prerequisties for BOM & AVL |
Bills of Material (BOM’s) may be created a part at a time or all at once. Although they may be created from the top down or from the bottom up, entering of components and subassemblies first is faster. Copying similar existing BOM’s and editing the copy can greatly shorten the process. BOM’s can be created as Inactive while under construction to prevent premature use.
Prerequistes
After activation, "Bill of Material and AVL" access for each user must be setup in the ManEx System Security module. Users with “Supervisor Rights” will automatically have access.
Customer Part numbers for Consigned Parts to be added to the BOM must exist in the Inventory Control Mgmt module.
Optional Data
Component Costs (Standard, Budgeted or Quoted) for manual calculation of the Standard cost of the Assembly. Note that if the Accounting Module is installed, the cost information must be filled out.
|
1.3.2. Introduction for BOM & AVL | The Integrated Bill of Material and AVL Module allows the user to create, modify, copy, inactivate or delete Bills of Material (BOM’s).BOM’s are the master documents that define what material goes into a product. Item numbers (Product, assembly, subassembly or component) used in BOM’s link the BOM’s to the data that is entered and maintained in the Inventory Control Management- Item Master and Quantity Info screens. Most of the basic data fields (class, type, description, revision, unit of measure, warehouse and order policy) remain the same whenever an item is used in a BOM. Only the data fields that are maintained in the BOM Module, such as the reference designators, kit-to Work Center and quantity per assembly may be changed from one BOM to the next.BOM’s are used to kit components and subassemblies for Work Orders and to drive demand for Material Requirements Planning.
See Article #2560 to view how Inventory, BOM's and AVL's are connected within the ManEx system.
NOTE: If users choose to use effective and obsolete dates in place of proper revision control, you must be absolutely certain that they do not take effect at any point after production begins and before the WO is closed. If this isn't properly managed, you will get the variances. While some may be minor and positive variances may partially offset negative variances, you CANNOT rely on this and you WILL have discrepancies.
The best approach is to always roll the revision when there is a change to an assembly that will affect the value in any way. This becomes even more important if you have WOs open long after the due date and it has had additional changes to the configuration. See Article #5055 for further detail.
Definitions
Indented Bill of Material: The Top-down breakdown of the structure of a product. In an indented BOM listing, every subassembly and component is indented one level from the assembly or subassembly into which it goes.
Parent and Child Relationships in BOM’s: Each product “parent” has an indented list of “child” components and subassemblies that go into it. Each child item is indented under its parent and may in turn have child components indented under it.
Accepted Manufacturer List (AML): The AML is the list of manufacturer part numbers entered in the Inventory Control Mgt.- Quantity Info screen. A manufacturer must first be set up in the Inventory Control Mgt./ Part Manufacturer Setup before its approved part number can be added.
Accepted Vendor List (AVL): AVL’s show which manufacturers are approved or qualified for use for a particular customer’s product line or individual product. Only manufacturer part numbers that have been entered in the AML for a particular item can be selected or deleted from the AVL for a customer. A customer’s Approved Vendor List of manufacturers for each internal part is maintained in that customer’s Consigned Inventory record for that part.
Consigned Inventory AVL Record: When a Customer part number is assigned in the Inventory Control Mgt.- Customer Reference screen, a Consigned Inventory Record is generated for that item and customer. The Quantity Info screen for the Consigned Customer part number is where the Customer’s AVL is maintained. Q.Do I have to go into the Inventory Control Management module and assign a customer to the part number? A.Only if the user wants the cross-reference to the customer part number to show for internal parts on the BOM. This field will show up if a BOM Assembly is attached to a specific customer.
Anti-AVL: Normally the AVL for each customer applies to all of their product BOM’s. However, if a customer wishes to disqualify a manufacturer from use in one particular BOM, removing a check-mark from the Anti-AVL field may be used to keep the otherwise approved manufacturer from being used on specific BOM’s.
Generic and Manufacturer Preferences: A Generic (Genr) manufacturer means that any manufacturer’s part can be used.Generic is generated by the system as the default manufacturer if no other is specified. If specific manufacturers are listed for a part, preferences for use in an Internal or in a Customer’s product may be entered. Preferences are entered in the Inventory Control Mgt.- Quantity Info screen as 1 for 1st, 2 for 2nd, etc. next to the manufacturer.
Functions
Bills of Material serves many functions in the manufacturing environment. They are central to all manufacturing operations and are used for everything from product specification to quotation document. BOM’s are key to material requirements planning, kit organization, product structure, and configuration control.
Material Requirements Planning (MRP): The BOM is the master plan for building product. An indented BOM from the product top level down to the lowest level component provides the entire material picture for a product. Its quantity and manufacturer preferences are used to kit materials for production to assemble. Its linkage to Item Master Purchase and Production Lead Times and Work Center offsets are used by the MRP to determine which parts to purchase or make and when to provide them. By listing multiple manufacturers and alternate part numbers, the BOM can be used to manage work order shortages.
Kitting by Work Center: Selection of a Work Center for each BOM Line Item causes that item to be kitted with other parts for that Work Center. Grouping of the parts needed for the first Work Center helps determine when to start a work order and eliminates the need for sorting out needed parts at each Work Center. Also if parts are not kitted until needed for later work centers, they need not be purchased or made until closer to the time they are actually needed.
Production Offset: This time difference between the start of the kit for the first Work Center and the kitting for the Work Center where the part is needed is called Production Offset and can be entered for each line item in the BOM. For example, mechanical parts and chassis parts may not be needed until the work order reaches the final assembly work center. By identifying those parts as Final Assembly parts and entering “x” number of days of Production Offset, the parts will not be scheduled for delivery by the MRP nor need they be kitted for “x” days later than the rest of the Work Order. An entry in this field will displace the due date required by the amount of offset established in the BOM. If the user wanted a part or assembly to be ready on the third week of an order that took 4 weeks, then the user would enter a 3 week offset, and the MRP module would suggest ordering the parts three weeks later than otherwise. Please refer to the Material Requirements Planning Management manual.
Engineering Change Control: BOM’s are unique by their revision number and as such are used to control changes to the structure or components in a product. By creating a new Revision level of the BOM with an Effective Date the next day after the Obsolete Date for the old BOM Revision, the user can drive changes in material requirements, kitting and work orders. Or if the new BOM Revision level is to co-exist with the down-rev. Revision, the new BOM is just activated without obsoleting the old BOM. With BOM Revision control, several revisions may exist with different definitions for each. BOM Notes may be used to record Engineering Changes for tracking purposes in the absence of a formal ECO system or documentation.
Reference Designators: Unique reference or insertion designations can be assigned in the BOM as guides for placement, assembly, repair or data recording for Statistical Quality Control (SQC).
Note: If the Leveling of Make items is in process then the users will not be able to Add/Edit a BOM, even if the user is already in modifucation mode of the BOM, the user will not be allowed to save the changes until the leveling process is complete. This is due to the fact that the affected records in leveling of Make Parts is large and complex, the saving time to commit the whole changes to inventory tables does take a large amount of time, so we do not want users making modifications to the BOM when the process is still leveling, so we have added a flag that the users will see within the BOM module.
|
1.3.3. Fields & Definitions for BOM & AVL | |
1.3.3.1. Bill Of Material Main Screen |
This is the screen that appears when opening the module. The product number is displayed in the Bill of Material Module screen header as a reference. The product information will remain on screen while viewing other sections of the BOM module. BOM Main may be used to view, edit, add or delete a Bill of Material. BOM Header information is displayed for any item located after a FIND. If any Line Items have been added to an assembly in the BOM Header, they will be displayed in the Detail Window below. The lines that are inactive will be highlighted in purple. Selection of a Line Item in the Detail Window will cause the other BOM screens to be populated with default and/or added information for that Line Item. Start with this screen to add a new BOM, edit an existing BOM, add a new Line Item or change detail information for existing Line Items.
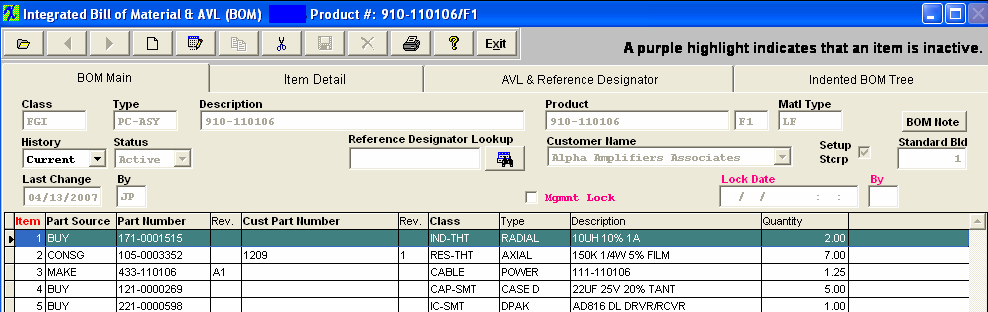
The Header Information fields across the upper half of the screen are populated from the item master and from keyed-in assembly data. The fields in the Body (Detail Window) show information about the components included in the assembly.
BOM Main Field Definitions
Class |
The Part Class assigned to the assembly in the Item Master.
|
Type |
The Part Type assigned to the assembly in the Item Master.
|
Description |
The Item Master description for the Assembly Part.
|
Product |
The Part Number for the assembly. Can be the customers product no. or an auto-assigned internal Part Number.
|
Rev |
The Part Number Revision for the assembly. An assembly may exist under multiple revisions.A separate BOM is required for each.
|
Matl Type |
This is defaulted in from Inventory Control |

|
Any notes pertaining to the BOM will display upon depress the Note button.
|
|
Depressing the down arrow will display the history of the BOM components. Current reflects the most recent listing; BOM History will display the history of changes. Selected Date will bring up a selection screen.
Note: If the effectivity and obsolete dates are used, then it is possible to check the specific parts list at any given data using the BOM history.
|
|
Status |
The BOM Status: Active - BOM is Active;
Inactive - BOM is Inactive which will affect Cost Roll up. NOTE: Changing the BOM status to Inactive will NOT remove the MRP demands you MUST Inactivate the part number in ICM to remove the MRP demands. See Article #3430 for further detail.
Quote - This status is in case a BOM is in a quote stage and the user needs a reminder that the quote for this BOM is pending.
This status is for the BOM ONLY, it will NOT change the status of the Inventory part. The Inventory part status and BOM status can be different. This is to allow flexibility so the BOM can be inactive and will NOT be displayed in the BOM module, but the part will still be displayed in the inventory listing. Users will be allowed to change the status on a BOM from Active to Inactive with open SO, WO, etc. and MRP will still show demands. Users will also still be allowed to Create NEW SO, WO, etc if ONLY the BOM status is Inactive. Users will NOT be allowed to change the status on the Inventory part from Active to Inactive with open SO, WO, etc.
|
 |
When the BOM is made Inactive this field will display the status along with the date and Initials of the user that Inactivated the BOM. |
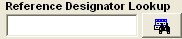 |
This allows the user to find part by Reference Designator. If user starts typing reference designator into the text box it will auto fill the information, when done entering user can press "Enter" or click on the search button next to it and the record pointer in the grid will advance to the part if a match is found. |
Customer Name
|
The name of the customer for whom the user is making the assembly.Select from pull-down list. Add new customers in Customer Information Management. Use Standard Pricing as the customer or leave blank if the assembly is built to stock or has more than one potential customer. This field must match the Customer for any Consigned parts used in the BOM.
|
Setup Stscp |
This box MUST be checked if you wish for the setup scrap qty’s to be included in the Kitting and MRP calculations, Checking this box along with a Standard Bld qty will tell the system to use Setup Scrap when calculating the standard cost. Note: The "Exclude Scrap & Setup Scrap" options within the Kitting Setup module will overwrite this option.
|
Standard Bld
|
The quantity normally built. Entering a quantity in this box will be used when calculating the Standard Cost. See Article 3040 for information on how this affects the Std Cost. See Articles #3067 , #3053 , and #3320 for information on how this affects the Configuration Variance. |
Last Change |
The date and time of the last change to the BOM automatically enters this field.
|
By |
Initials of user that made last change to BOM. |
Mgmt Lock |
This option is for BOM's that need to be protected, even from those users that have edit capabilities. Only Supervisors or users with Lock/Unlock rights within the Security/User rights can modify this checkbox. If locked, all users can access the screen, but only supervisors or those with Lock/Unlock rights will have the capability to bypass the lock and make changes, while the BOM is still in lock mode. The reason we do NOT force the user to unlock the BOM before making any changes, is to protect it from anyone else making changes while the 'authorized" user is making their changes.
|
Lock Date |
The date the Managment Lock Box was checked. |
By |
The initials of the user that check the Managment Lock Box. |
COMPONENT INFORMATION (Displayed in the Body (Detail Window)
Item |
The item numbers assigned to the components in the BOM.
|
Part Source |
The sources of the assembly components.Select Make, Buy, Consigned or Phantom.
|
Part Number/Rev |
The components internal Manex part number. The Part Number Revision for the component. A component may exist under multiple revisions. Each Rev. is considered a unique part number and may co-exist with other Revs. or replace other Revs.
|
|
The component's customer part number. The Part Number Revision for the component. A component may exist under multiple revisions. Each Rev. is considered a unique part number and may co-exist with other Revs. or replace other Revs.
|
Class |
The Part Class of the component part as assigned in the Item Master.
|
Type |
The Part Type of the component part as assigned in the Item Master.
|
Description |
The Item Master description of the component part.
|
Quantity |
The quantity of the component part used in the assembly.Do not add to the quantity field to compensate for setup and run losses; Use the Setup % and Run Qty. fields in the Item Master screen to add components to cover production losses.
|
Column Heading in Bold Font
|
These columns, when selected will cause the Detail information below them to be sorted by the field selected. Selected Column headers turn Red. |
|
1.3.3.2. Item Detail Information Tab | When the user has displayed component parts on the BOM Main screen, and has highlighted one of the parts, pressing on the Item Detail Tab will display information about
that component part. The NEXT and PRIOR buttons are activated in the Detail Information Tabs. Clicking on either button will display the details of the next component in the BOM.
The first row of Header information repeats the assembly Product information.
The remaining fields describe Detail information about the component part.
Item Detail Screen Fields
HEADER INFORMATION
Product |
The Part Number of the assembly. Make Items are referred to as Products. |
Rev |
The Revision of the assembly number, phantom or subassembly. |
COMPONENT INFORMATION
Item No |
The item number assigned to the components in the BOM. |
Work Center |
The work center identified in the routing for the assembly at which the part is needed. Kitting of the part by work center will use this information to determine which parts are to be kitted for each work center. |
Source |
The Source Code for the component part on the BOM. May be another MAKE assembly, a PHANTOM assembly, a BUY part, or a CONSIGNED part.
When building a BOM in order to have the Source "CONSIGNED" displayed a Customer MUST be assigned to the BOM.
When building a BOM and you enter the source as a “Phantom”, then when entering the part number that is a “Make/Phantom”, the source changes to a Make” part. The reason the source field shows at all is to limit the number of part numbers that are available to choose from. But you can enter any valid part number and the source will change to the source of the part number entered. So, yes, the source of the sub-assemblies will show as a “Make” part, even though they are actually “Make/Phantom” parts. The details of the BOM will also show they are “Make/Phantoms”. We allow nested phantoms, of either the “PHANTOM” or the “Make/Phantom” variety. In kitting, we have the code to blow down through the first level of make/phantoms, so that the parts included in the first sub-assembly level down are listed as kit requirements. We have extended this further so that if there are Make/Phantom parts in the first sub-assembly level, those also break down to the components in the second sub-assembly level. This process extends as long as there are “Make/Phantoms” in the indented BOM.
|
Part Class |
The Part Class of the component part. |
Part Type |
The Part Type of the component part. |
Part Number |
The component part number. |
Rev |
The Revision number of the component. |
Customer Part Number |
The number the customer uses to identify the part. |
Rev |
The Revision number of the customer’s component. |
Description |
The description of the component part. |
Quantity |
The quantity of the component part used in the assembly. The maximum number of decimals in the BOM quantity is 2, allowing for 1/100th of an item. If users need a finer resolution, they may consider using a different UoM than EACH, and buy in one unit and use a fractional unit for inventory (e.g. Purchase in Gallons, and Stock/Issue in ounces). |
UOM |
The stocking/kitting unit of measure for the part. |
Production Offset |
Production offset is a BoM item level field that allows users to control delivery dates in relation to the starting date of the work order. By using this field, the user may move the material requirement date by the specified number of days in either direction. Enter the number of days after the start date (based on the production lead-time for the assembly) that the part is needed at the kit-to Work Center. NOTE: This will affect the MRP demands until the kit status has been changed to "KIT IN PROCESS". Once the kit status has been changed to "Kit in Process" the parts now become a kit shortage, and the system will calculate from the WO due date or production lead time and NOT from the production offset. . A Negative Offset is one that SUBTRACTS time from the normal kit required date. So an item normally due on March 26 would, with a -3 day offset, be due in the stockroom on March 21st . Conversely, a Positive Offset is one that ADDS time to the normal kitting time. So an item normally due on March 26 would, with a 3 day offset, be due in the stockroom on March 29th (skipping the weekend). Offsets are only managed by days, so there would never be a 3 week or 2 month offset, only 21 days or 60 days.
|
Used in Kit |
"Y", "N", or "F" - Identifies the part if requires kitting from the storeroom. Typical Non-kitted items include chemicals and adhesives that are re-issued when they run low but are included on the BOM for costing or reference. Note: A non-kitted item will create MRP demands. For more information see Article #34. |
Effectivity Date |
This is the date that the part is added and/or removed from the BOM and the demands will be displayed in MRP. MRP picks up all the records with an effective date earlier or equal to current date, and all NULL/BLANK effective dates. If the user changes parts in the BOM, without changing the revision of the BOM, then they should be entering the effectivity date of the new part, and the obsolete date of the old part. Usually, they are the same date for a replacement item. It is the date that is used in the determination of what material is to be used in kitting. If the kit is due to ship before the date(s), then the old definition will apply. If the kit is due to ship after the date(s), then the new definition will apply when the kit is updated. When printing BOMs, the information included will depend on the selection they want to see. Current will display whatever is effective on today’s date. History will display ALL items. Selected date will display the BOM as of the date entered. The old items will continue to show up on a where-used report. This is a good thing, because when you are trying to figure out where all of the old obsolete inventory came from, you can trace it back to the assembly and customer.
Note: The Kitted BOM Cost calculations displayed on the "Kit to Close Report" is based off the WO Due date and compares that to the EFF/OB dates on the BOM. So users need to be VERY careful with the WO Due Dates and make sure that they stay current along with the EFF/OB dates on the BOM.
|
Obsolete Date |
The date the part is no longer required on the BOM for new work orders and the demands will NOT be displayed in MRP.
Note: The Kitted BOM Cost calculations displayed on the "Kit to Close Report" is based off the WO Due date and compares that to the EFF/OB dates on the BOM. So users need to be VERY careful with the WO Due Dates and make sure that they stay current along with the EFF/OB dates on the BOM.
|
DIRECTIVE BUTTON
The following button is displayed on the BOM Item Detail screen:
 |
Pressing the BOM Item Note button will allow the user to create a notation specific to the component shown, in the current BOM. To enter a note, depress the BOM Item Note button. Depress the edit button. Type in the note. Depress the Save button. Depress the Exit button. |
|
1.3.3.3. AVL And Reference Designator Tab | When the user has displayed component parts on the summary screen, and has highlighted one of the parts, pressing on the AVL & REF Tab will display Part Manufacturer and Reference Designation information about the component part. The NEXT and PRIOR buttons are activated in the AVL Information Tab. Clicking on either button will display the AVLs of the next component in the BOM.
The first row of Information displays the selected detail part information.The Customer Part Number will be displayed if entered in the Item Master.
The Left Center portion of the screen displays the Approved Vendors List (AVL). These manufacturers and their part numbers have been selected and designated as approved sources for this particular BOM assembly. When the BOM for the assembly has a customer assigned to it, then Manex will pull the approved AVL's from the customer side NOT the Internal side. If no customer is assigned to the BOM then the AVL’s will be pulled from the internal side. For further detail see Article #2560 . NOTE: If "GENR" is approved on the BOM MRP will consider any inventory for that part even if the AVL is not approved on the BOM.
The left hand column displays the preference order, as assigned in Inventory Control Management.
The right hand column box must be checked for the Kit to issue the part to the Work Order. (At least one AVL must be selected as approved within the BOM module before save will be allowed).
The Right Center portion of the screen displays the reference designators assigned to the component. These fields are optional, but must be completed if reference designator information is to be used in the quality defect collection information. (The ref designators are case sensitive).
The bottom portion of the screen is available to list alternate parts that may be used in the absence of the primary part. However, these alternate parts are not listed on kit lists, and are only displayed on this screen. On the BOM, Manex provides a place for users to identify “Alternate Part” for each part called out in the BOM. However, this is for information and cross reference ONLY and there is no connection with the MRP, Purchasing or Kitting, etc. modules. The concept here is that if the engineers want to include alternate (not preferred, and not on AVL) parts for the possibility that in case purchasing can’t get the original parts called for by MRP, they could look up the alternate part on the BOM, and then order that part. However, to get the part into the kit, they will have to add the alternate part as a line shortage to the Work Order, and also check the “ignore shortage” for the part(s) originally required and short on the Work Order. Then MRP will work as needed, and the kit will show the alternate part as a (line) shortage until filled. Incidentally, creating the line shortage and checking the ignore shortage for the original part will result in an MRP directive (the next time it is run) to buy the alternate (line shortage) part. Please refer to the Material Requirements Planning and the Kitting, Allocating & Shortage Management modules.
AVL & Ref Designator Field Definitions
COMPONENT INFORMATION
Item No |
The item number assigned to the components in the BOM. |
Part Class |
The Part Class of the component part.
|
Part Type |
The Part Type of the component part.
|
Part Number |
The component part number.
|
Rev |
The Revision number of the component. |
Customer Part Number
|
The customer part number as entered in the Item Master.
|
Rev |
The Revision number of the customer’s part number.
|
AVL INFORMATION
Pref |
The order of preference number.
|
Part Mfgr |
An approved manufacturer for the component on the current BOM. NOTE: When the BOM for the assembly has a customer assigned to it, then Manex will pull the approved AVL's from the customer side NOT the Internal side. If no customer is assigned to the BOM then the AVL’s will be pulled from the internal side. For further detail see Article #2560 .
|
Mfgr Part No |
The commercial part number.
|
Checkuse |
This box must be checked for kitting to pull the component. NOTE: If "GENR" is approved on the BOM MRP will consider any inventory for that part even if the AVL is not approved on the BOM. (At least one AVL must be selected as approved within the BOM module before save will be allowed).
|
REFERENCE DESIGNATOR INFORMATION
Number |
The sequential number assigned to each occurrence of the component on the assembly.
|
Ref Designator |
The assigned location for each occurrence of the part. (The ref designators are case sensitive).
|
Prefix |
A prefix assigned to reference designators for the current component. Is usually a “C” for capacitors, “R” for resistors, etc |
Start No |
If the user wishes to fill in the reference designators automatically, then the start number will be the beginning number in the sequence of reference designators assigned.
|
End No |
If the user wishes to fill in the reference designators automatically, then the end number will be the last number in the sequence of reference designators assigned.
|
 |
Pressing the Calculate button will fill in all reference designators with the prefix plus incremental numbers beginning with the start number entered. |
Quantity |
The quantity of components used in the assembly.
|
ALTERNATE PART INFORMATION
These items are the same as previously described.
DIRECTIVE BUTTONS
 |
Pressing the Add button in the ALTERNATE area will allow the user to add additional item master part numbers as approved alternates.
|
|
Pressing the Delete button in the ALTERNATE area will allow the user to remove item master part numbers as approved alternates.
|
|
1.3.3.4. Indented BOM Tree Tab | When the user has displayed component parts on the BOM Main screen, and has highlighted one of the parts, pressing on the Indented BOM Tree tab will display the components with additional information about a make part components.
The first row of data reminds the user of the assembly information.
The bottom portion of the screen displays the components of this assembly. If there is a plus sign to the left of a listed component, click on the plus sign and the components of the listed
components will also appear.
|
1.3.4. How To ..... for BOM & AVL |
1.3.4.1. Find a BOM |
To enter the Bill of Material Module depress Quality/Engineering/Integrated BOM & AVL |
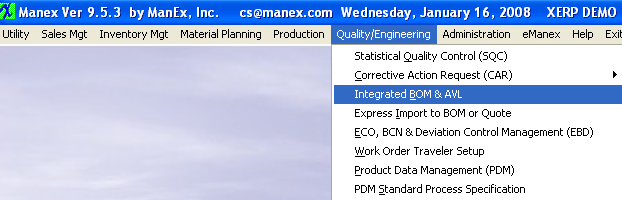 |
When the screen first opens, the user is limited to only three of the eleven action buttons shown: Find an assembly, run a Report or Exit. After finding an assembly, the user may page ahead or back through all Make items using the > right arrow or < left arrow button. Assemblies having Bills of Material will display the components in the Body (Detail Window) below. Selection of one of the components in the window will cause detail information for that item to be displayed if any other BOM screen Tab is selected. Use the Add icon to add components to the BOM of a displayed assembly. Use Edit to change or add Header information. Use the Delete icon to Delete the entire BOM ONLY (See Deletions section). Note: Go to the Item Detail screen to delete only one item from the BOM.
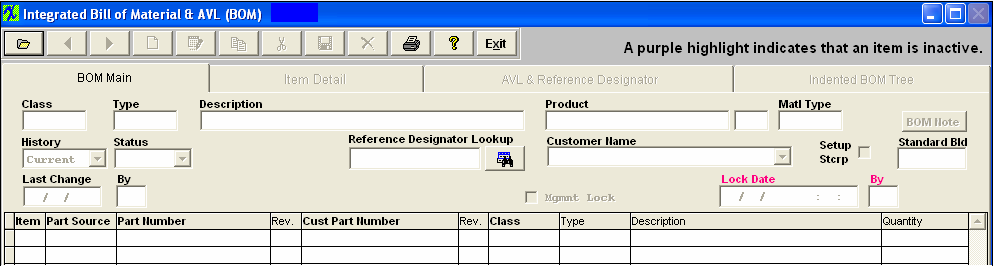
Find a Bill of Material
To view an existing BOM or to find an existing Make Source Item (Product, Assembly, Subassembly or Phantom) under which to build a BOM.
Click on the Find an existing record Action Button.
Find an existing BOM screen selection will display:
Select the desired search radials by clicking on them. Choose between Active, Inactive or All for the status, (Note: The status of the BOM may be different than the status of the Inventory Part). Since you are doing a find for the BOM you would search by the status of the BOM.
Check the "Display Customer Part #..." box to display the Customer Part number for the "Buy" parts if the BOM is linked to a customer. Selecting this option may slow down the results. The system will retain the last choice the user makes for this check box until the module has been exited.
|
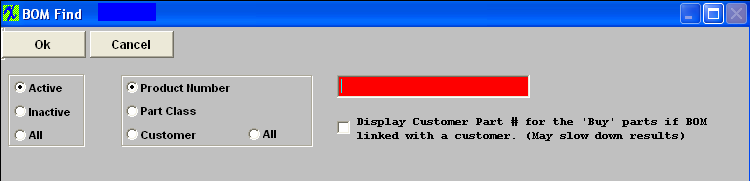 |
Find an Existing BOM by Product Number
If you know the product number, click on the Search by product number radial and then type the part number into the red box and depress the OK button.
If the part number entered cannot be found you will receive a message (shown in the screen) asking you if you would like to select Product from the list of Products.
|
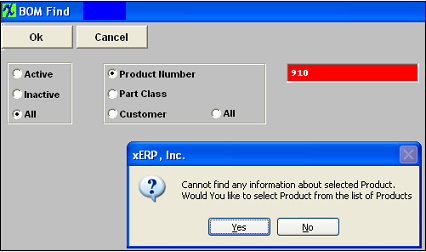 |
Depress "YES" and a List of Products will be displayed in the bottom section of the screen.
The parts are listed in alphanumeric order, with the Revision, Product ID, Class and Type.
Note: The status listed on the right of the screen is displaying the status of the Inventory Part not the status of the BOM, which may be different.
The user selects the Part Number by either entering it into the red box, or scrolling down the list and clicking on the selected part.
|
|
Find a BOM by Part Class
If you know the Part Class, click on the Search by part class radial and then type the part class into the red box and depress the OK button.
|
|
When the user is searching for an assembly through the part class option, a screen appears listing all of the products within that class in alphanumeric order.
Note: The status listed on the right of the screen is displaying the status of the Inventory Part not the status of the BOM, which may be different.
The user selects the Part Number by either entering it into the red box, or scrolling down the list and clicking on the selected part.
|
|
Find a BOM by Customer
If you know the Customer, click on the Search by Customer radial and then type the Customer into the red box and depress the OK button.
|
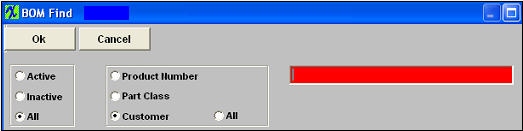 |
When the user is searching for an assembly through the Customer option, a screen appears listing all of the product numbers assigned to that customer in alphanumeric order.
Note: The status listed on the right of the screen is displaying the status of the Inventory Part not the status of the BOM, which may be different.
The parts are listed in alphanumeric order, with the Revision, Class and Type. The user selects the Part Number by either entering it into the red box, or scrolling down the list and clicking on the selected part.
|
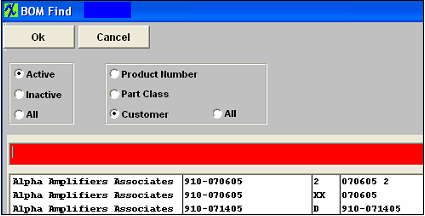 |
BOM Search Results
After finding the Part Number through either the Class Code, Customer, or directly by the Part Number, the BOM Main screen appears, populated with any parts already entered for the BOM of the assembly selected. If no parts have been added to the assembly, the Body (Detail Window) is blank. When BOM is found and displayed the order will be by "Item #". User can re-sort list by clicking on a header that is in Bold that header will display in red. The lines that are inactive will be highlighted in purple. When double clicking on an item, system will take you to the detail page.
User may find a part using the Reference Designator Lookup, by typing a reference designator into the text box it will auto fill the information, when done entering you can press “Enter” or click on the search button next to it and the record pointer in the grid will advance to the part if found.
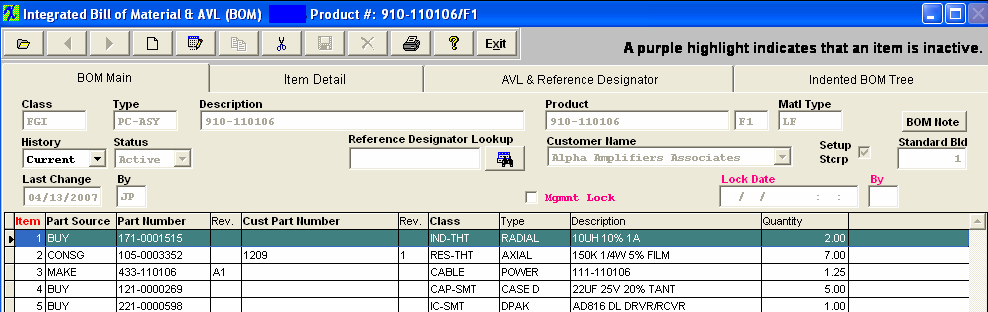
The Header Information fields across the upper half of the screen are populated from the item master and from keyed-in assembly data. The fields in the Body (Detail Window) show information about the components included in the assembly.
|
1.3.4.2. Adding BOM Header Information | A BOM Header is created by the system when a Make Item is added to the Inventory Control Mgt Item Master and Saved. When the user wishes to create a BOM by adding Line Items to the header, the existing Header is used. The Header identifies the assembly or product and its revision level, shows the status and after creation, allows Viewing BOM components by Current, All, or Selected Effective Dates.
Depress the Find button. See Article #571 for Find procedures.
Depress the Edit button. Enter your password. The following selection screen will appear:
Select BOM Header Information button.
|
|
|
Select status from the drop down menu. When selecting the status, this status is for the BOM ONLY, it will NOT change the status of the Inventory part. The Inventory part status and BOM status can be different. This is to allow flexibility so the BOM can be inactive and will NOT be displayed in the BOM module, but the part will still be displayed in the inventory listing. User will be allowed to change the status on a BOM from Active to Inactive with open SO, WO, etc. and MRP will still show demands. User will also still be allowed to Create NEW SO, WO, etc if ONLY the BOM status is Inactive. Users will NOT be allowed to change the status on the Inventory part from Active to Inactive with open SO, WO, etc. |
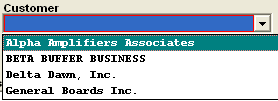 |
If there is a Customer associated with this product, select the customer by depressing on the down arrow next to the customer box. A list of customers will appear. Highlight the customer name and double click.
Assigning the customer name to the BOM is an option which you can elect to use or not as long as there is no consigned part. If you do not assign an assembly to a customer, this BOM can be used for any customer you want and not limited to a customer. Assigning to a customer is a requirement if you have any consigned part within the BOM. For the sales price, we allow you to add one or more customers in the Price List module and you can determine the quantity breaks and prices by each customer for the same assembly. When they are assigned in the Price List, SO module will show those assemblies only tied to the customer and avoids having to wade through all assemblies.
- If BOM is assigned to specific customer, and if there is CONSG part in the BOM -- Only that customer will be available in the WO customer list
- If BOM is assigned to specific customer, and no CONSG parts in the BOM -- Default to that customer, but all other customers are available to be selected.
- If BOM is not assigned to specific customer, all customer should be available.
|
To enter a BOM Note depress the BOM Note button. Depress the Edit button. Enter in the note. Depress the Save button. Depress the Exit button.
If you want set up scrap to be considered in Standard Cost calculation, check the Setup Stcrp box.
If you want a standard build to be considered in Standard Cost calculation, enter the quantity. See Article 2504 for information on how this affects the Std Cost.
To Lock or Unlock a BOM: Only Supervisors or users with Lock/Unlock rights within the Security/User rights can modify this checkbox. If locked, all users can access the screen, but only supervisors or those with Lock/Unlock rights will have the capability to bypass the lock and make changes, while the BOM is still in lock mode. The reason we do NOT force the user to unlock the BOM before making any changes, is to protect it from anyone else making changes while the 'authorized" user is making their changes.
When changes are complete depress the Save button to save the changes or Abandon changes button to delete changes.
|
1.3.4.3.1. Drag & Drop Procedure | 1. Procedure for Drag & Dropping
The Drag and Drop Operation allows the user to select components in the Summary screen of Inventory Control Management and drag the items into the Integrated Bill of Material & AVL Main screen to add them as line items in the BOM.
Use this procedure as an alternative to Manually Adding Line Items to a BOM.
Open the Inventory Control Mgt. Summary screen and use Find to display the desired components.
Size the Inventory Control display by placing the cursor on the far right hand side of the display. Wait until it turns into an arrow. Holding the mouse button down, move it to the left until just the following displays:
|
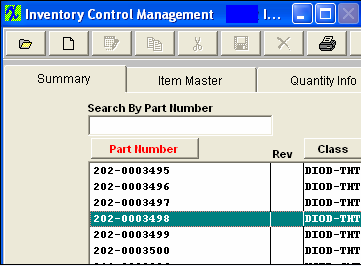 |
Open the Integrated Bill of Material & AVL BOM Main screen, position it in the lower right hand corner of the Manex screen.
Depress the Edit button and enter your password.
|
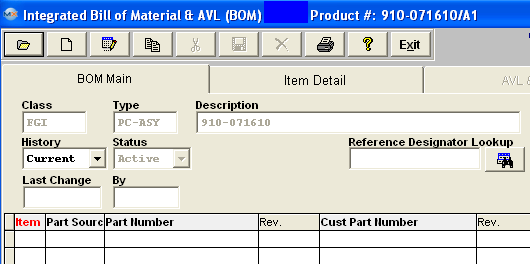 |
The following selection screen will appear:
Choose Drag and Drop.
|
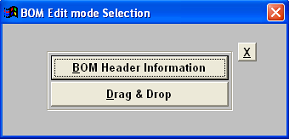 |
The following message will appear:
|
 |
Move the cursor to the Inventory window. Highlight the desired component. Use the left mouse button to select an item in the Inventory Control Management screen. Release the left mouse button. RIGHT click on the mouse button and CONTINUING TO HOLD THE RIGHT MOUSE BUTTON DOWN, move the mouse cursor over to the BOM screen. Release the right mouse button.
Note: When you drop (release the mouse button), be sure that you have the cursor over the white area,. Drag each component into the BOM in Line Item # sequence.
Enter the quantity of the part per assembly when prompted. Select the Work Center.
Type in the prefix for the Reference Designator. Type in the Reference Designator Start Number. Depress the Calculate button.
The Number and Reference Designator Fields will fill in.
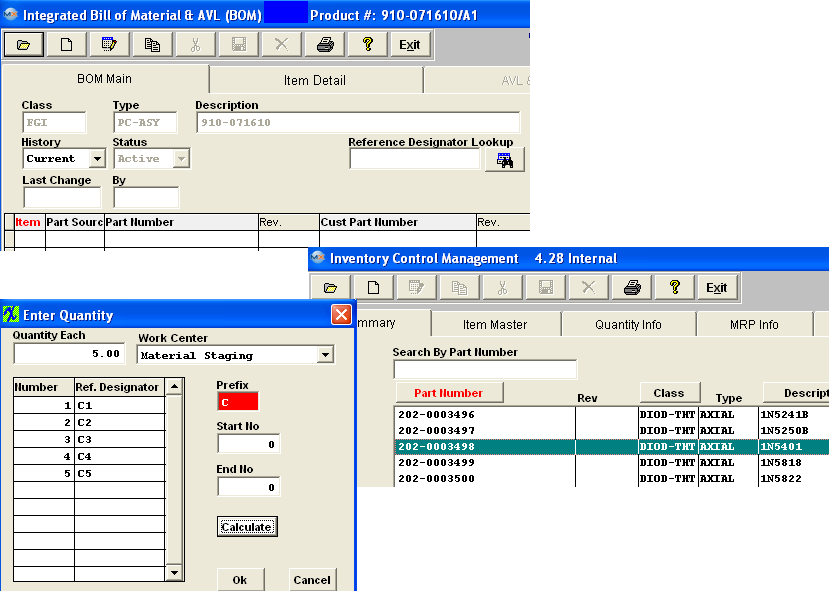
Depress the "OK" button to Save or the "Cancel" button to abandon changes. User may also click on the X button to save the changes and close the screen.
Depress the Save button in the BOM screen when finished dragging and dropping.
Depress the Item Detail tab in the BOM module. The following screen will appear:
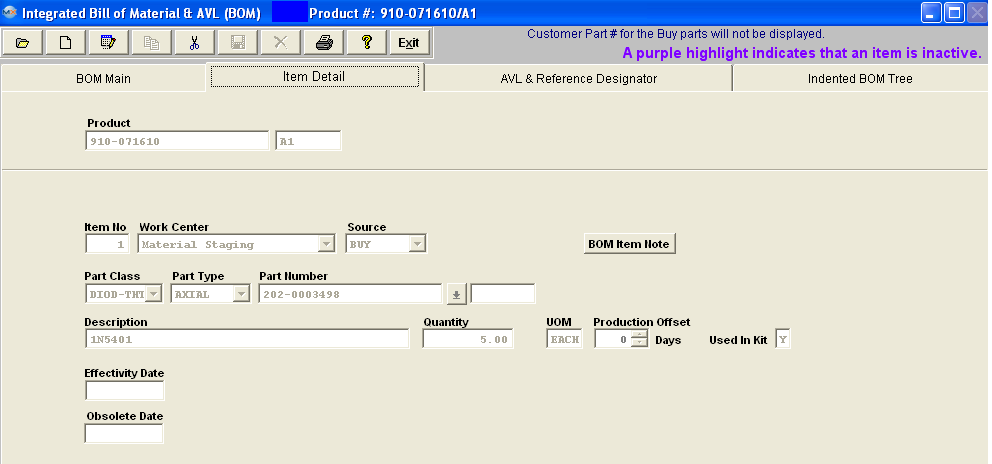
Review the detail. If you want to make any changes, depress the Edit button while this screen is open. Type in your password. You may change Item Number, Work Center, Quantity, Production Offset days, Used in Kit, and may add Effectivity Date and Obsolete Date. Depress the Save button.
All the AVL's will default in as approved and require the user to deselect as desired. If no AVL's are approved a popup will appear forcing the user to approve at least one AVL.
When the BOM for the assembly has a customer assigned to it, then ManEx will pull the approved AVL's from the customer side NOT the internal side. For example: Part “XYZ” may have several AVL’s and several different customers linked to it. Each customer may approve different AVL’s. So when the part is linked to a specific customer’s BOM only the AVL’s linked to that customer part will be displayed on the BOM as approved. The AVL screen looks at the accepted AVL’s for that customer on the “consigned” or “Customer” side of each part whether it was added to the BOM as a “BUY”, “MAKE” or “Consigned”. If no customer is assigned to the BOM then the AVL’s will be pulled from the internal side. NOTE: If "GENR" is approved on the BOM MRP will consider any inventory for that part even if the AVL is NOT approved on the BOM. For further detail refer to Article #2560 .
If you want to add alternate parts, depress the AVL and Reference Designator tab. Depress the Edit button. Enter your password. Depress the Add button next to the alternate parts section of the screen.
The following selection option will appear:
If you select Internal Part Number, then enter the Part Number into the Red Box.
|
 |
If you select Consigned Part Number, Select the Customer from the Pull Down list, then enter the Customer PN into the Red Box.
|
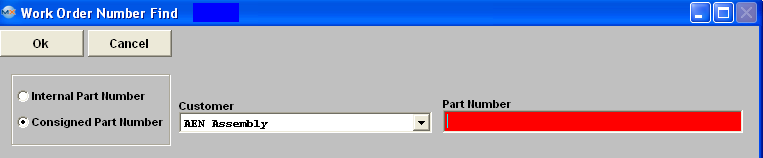 |
Information regarding the alternate part will display in the bottom section, as displayed below:
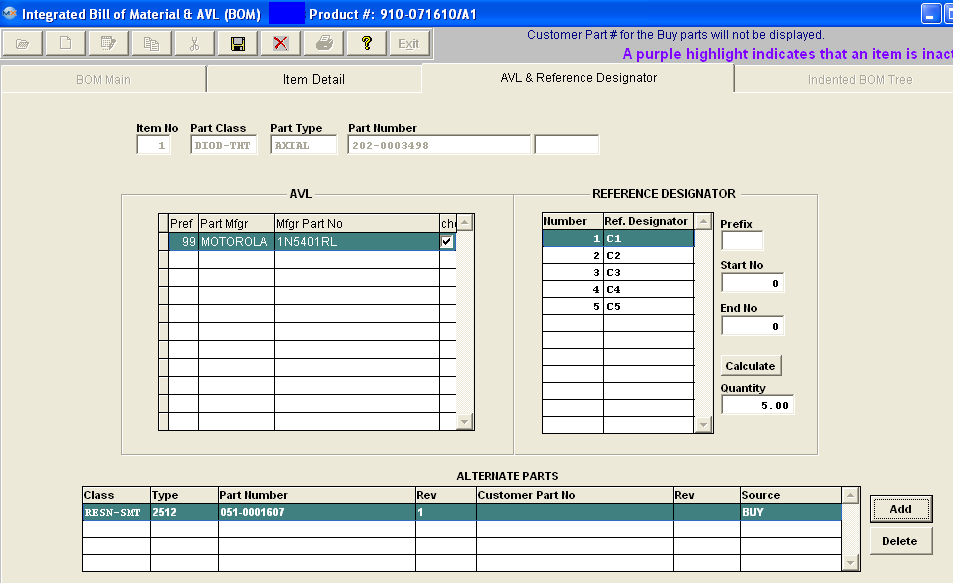
Depress the Save button.
|
1.3.4.3.2. Manual Entry | Procedure for Manually Adding Line Items
Use this procedure as an alternative to Drag and Dropping from the Inventory Summary screen.
Open the Integrated Bill of Material & AVL BOM Main screen and Find desired Header.
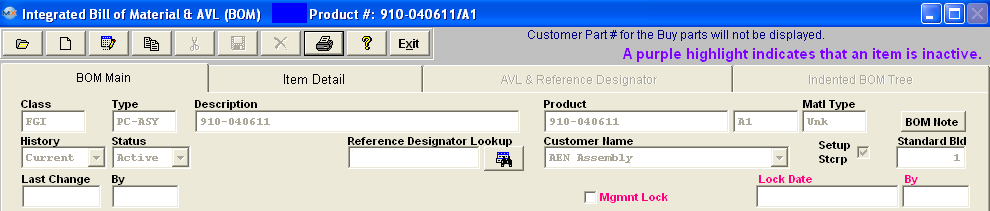
To add a component, click on the Add Record button, enter password.
The following screen will appear:
Select "Yes" or "No" to Auto Line Item Numbering.
|
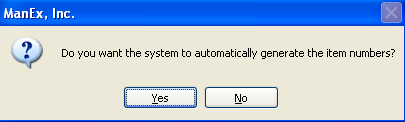 |
The item detail screen will appear:
In the Item Detail screen select Work Center to Kit to (use Material Staging if not known), from the drop down menu: |
|
Then select Source (Make, Buy, Consigned or Phantom), from the drop down menu:
When building a BOM in order to have the Source "CONSIGNED" displayed a Customer MUST be assigned to the BOM.
When building a BOM and you enter the source as a “Phantom”, then when entering the part number that is a “Make/Phantom”, the source changes to a Make” part. The reason the source field shows at all is to limit the number of part numbers that are available to choose from. But you can enter any valid part number and the source will change to the source of the part number entered. So, yes, the source of the sub-assemblies will show as a “Make” part, even though they are actually “Make/Phantom” parts. The details of the BOM will also show they are “Make/Phantoms”. We allow nested phantoms, of either the “PHANTOM” or the “Make/Phantom” variety. In kitting, we have the code to blow down through the first level of make/phantoms, so that the parts included in the first sub-assembly level down are listed as kit requirements. We have extended this further so that if there are Make/Phantom parts in the first sub-assembly level, those also break down to the components in the second sub-assembly level. This process extends as long as there are “Make/Phantoms” in the indented BOM.
|
|
Either enter the item number by typing it directly into the Part Number field or select Part Class and Part Type, as illustrated below:
Select the Part Class.
|
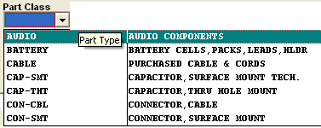 |
Select the Part Type.
|
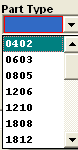 |
Depress the down arrow next to the Part Number box. A list of all of the inventory parts within the selected Class and Type will appear.
Type the Part Number into the Red box or highlight and double click to select.
If the item is a Consigned Item, enter either the Customer part number OR the Internal Part number, in the respective fields
|
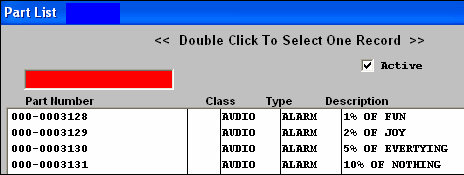 |
If you added an internal part and if there is a matching Customer part number in the Inventory Customer screen, it will automatically appear as soon as the internal inventory part is selected. Conversely, if you typed in a customer part number, the internal part number information will automatically appear.
Enter the Quantity of the item required for each assembly produced.
(Note: Extra parts for setup or run losses should be added in the Inventory Control Mgt. Item Master Run Scrap % or Setup Scrap Qty. field, not in the Bill of Material.)
Enter the production offset days by toggling on the up and down buttons.
If the component is to be pulled in the kit, leave the Y in the Kit box.If not, remove it.
Enter the effectivity and obsolete dates, if desired.
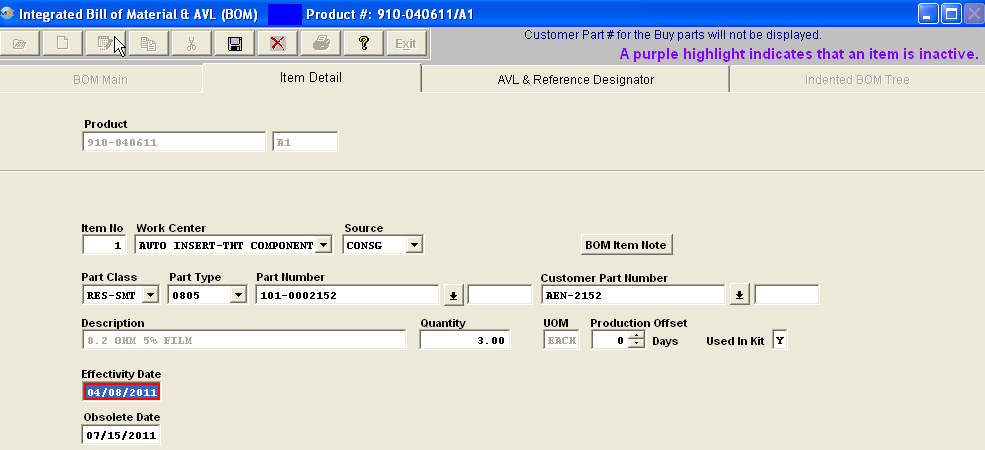
Depress the AVL & Reference Designator tab
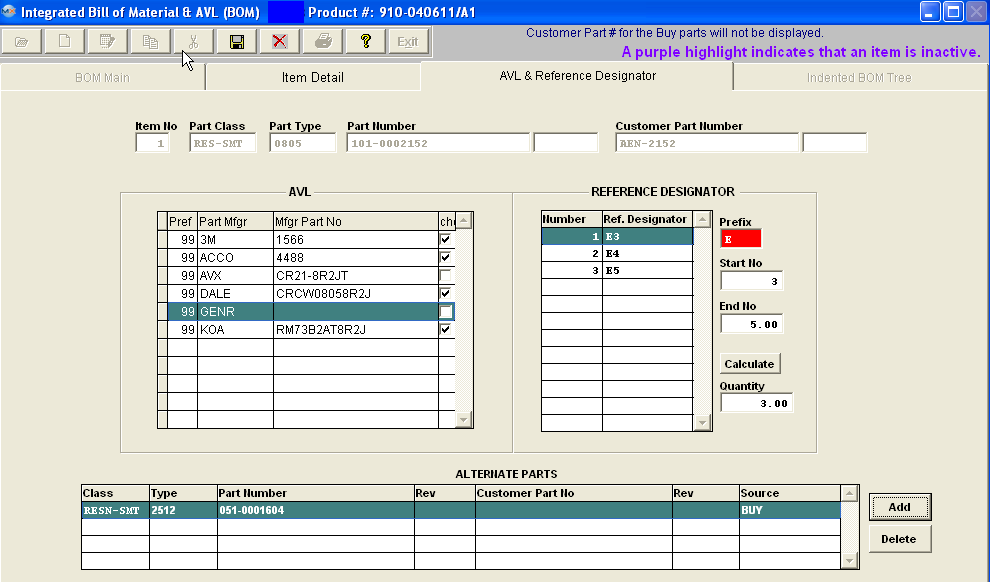
All the AVL's will default in as approved and require the user to deselect as desired. If no AVL's are approved a popup will appear forcing the user to approve at least one AVL.
When the BOM for the assembly has a customer assigned to it, then ManEx will pull the approved AVL's from the customer side NOT the internal side. For example: Part “XYZ” may have several AVL’s and several different customers linked to it. Each customer may approve different AVL’s. So when the part is linked to a specific customer’s BOM only the AVL’s linked to that customer part will be displayed on the BOM as approved. The AVL screen looks at the accepted AVL’s for that customer on the “consigned” or “Customer” side of each part whether it was added to the BOM as a “BUY”, “MAKE” or “Consigned”. If no customer is assigned to the BOM then the AVL’s will be pulled from the internal side. NOTE: If "GENR" is approved on the BOM MRP will consider any inventory for that part even if the AVL is NOT approved on the BOM. For further detail refer to Article #2560 .
Enter the Ref designators manually in the table or enter the prefix letter, Start No and End No and depress the Calculate button to auto-number.
If you want to add alternate parts, depress the AVL and Reference Designator tab. Depress the Add button next to the alternate parts section of the screen.
The following selection option will appear, Select Internal Part Number, enter the part number in the red box. |
 |
If you select Consigned Part Number, select a Customer from the pull down list, enter in the Customer Part Number in the Red Box.
|
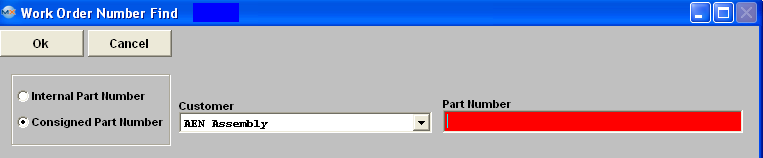 |
Information regarding the alternate part will display in the bottom section, as displayed below.
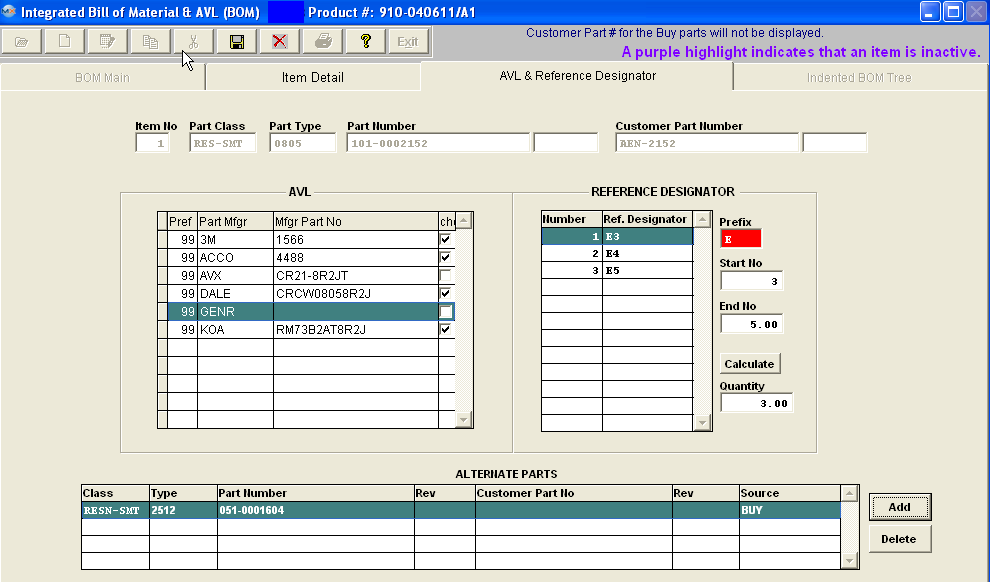
Once user has completed entering all information for line item number, depress the Save button.
|
1.3.4.3.3. Copy an Existing BOM | Procedure for Copying from an Existing BOM
A new assembly may have a BOM applied to it by copying the bill of material from an existing assembly. To simplify changing a Bill of Material, while maintaining the original version of the assembly, users can copy the parts list into a new assembly and make changes as needed.
After finding the new (and empty) assembly.
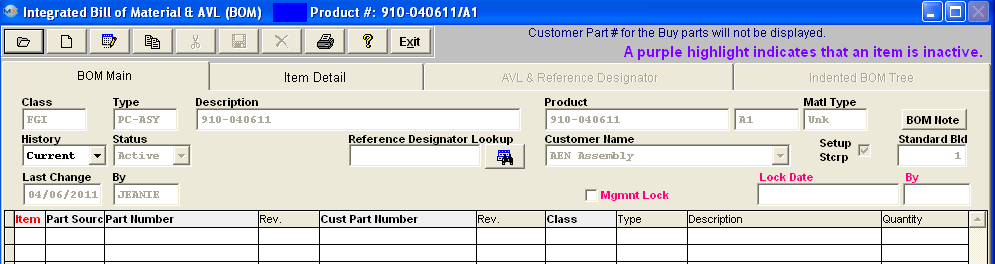
Depress the Copy button and enter the user’s password will prompt the user for the existing bill of materials from which to copy the components.
The user may find the existing assembly from which to copy either by part number or by part class.
If the BOM being copied from contains references to a customer, and or consigned part numbers, the following message appears: |
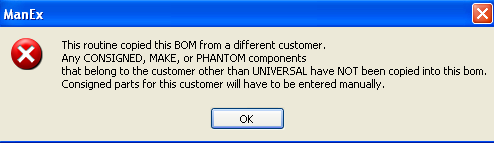 |
MANEX will populate the new assembly with all of the part information from the existing assembly, except for parts belonging to a customer. Those items will have to be added manually. The filled in BOM is displayed below:
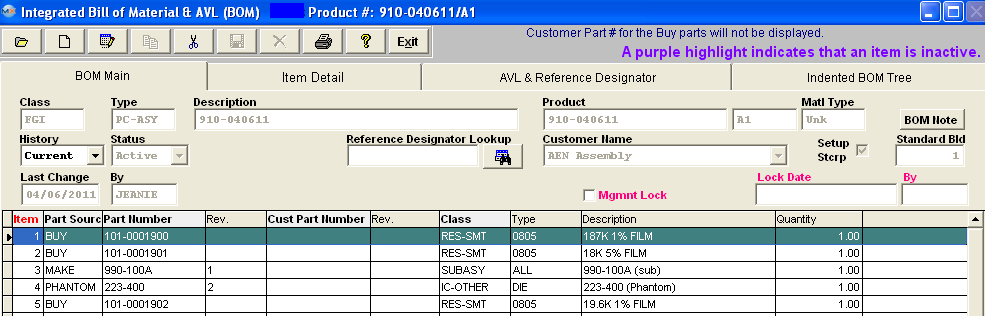
Depress the Edit button to add the customer name and any other needed changes, in any of the screens.
The user can then either Save the new assembly with all of the components, or Cancel the operation.
|
1.3.4.4. Bill Of Material Deletions | The Delete button takes on dual meanings. If the user is in the BOM Main Tab when the button is pushed, the button will delete ALL items on the BOM. You will be prompted for your password. The following message will appear:

If there are open work orders for the assembly, then the user is presented with a prompt advising that the bom cannot be deleted while open orders exist, as displayed below:

If the user is in the Item Detail Information Tab when the button is pushed, the button will delete only the item highlighted. You will be prompted for your password. The following message will appear:
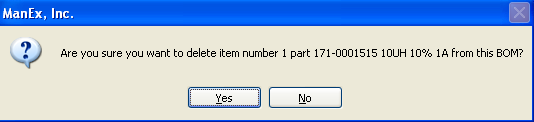
|
1.3.4.5. Procedure For Editing Line Item Details | Use this procedure to edit Line Item details after entering BOM Header information and Line Item Part Numbers and Quantities per assembly manually, using drag and drop, or copying.
Click on the Item Detail tab. Depress the Edit button and enter password.
NOTE: If users choose to use effective and obsolete dates in place of proper revision control, you must be absolutely certain that they do not take effect at any point after production begins and before the WO is closed. If this isn't properly managed, you will get the variances. While some may be minor and positive variances may partially offset negative variances, you CANNOT rely on this and you WILL have discrepancies.
The best approach is to always roll the revision when there is a change to an assembly that will affect the value in any way. This becomes even more important if you have WOs open long after the due date and it has had additional changes to the configuration. See Article #5055 for further detail.
The Item number, Work Center, Qty, Production Offset, Used in Kit, Effective Date, and Obsolete Date can be edited on this screen.
The Production Offset would be edited, If an item is to be kitted to a Work Center that will not be reached by the Work Order until X days later, enter X days in the Production Offset to allow kitting to that Center X days later. NOTE: This will affect the MRP demands until the kit status has been changed to "KIT IN PROCESS". Once the kit status has been changed to "Kit in Process" the parts now become a kit shortage, and the system will calculate from the WO due date or production lead time and NOT from the production offset.
Enter Effectivity Date for the line item to be used in the BOM.
(Note: Prior to Effectivity Date or after Obsolete Date, the line item will not appear on the Current BOM view nor will it appear on a Pick List to Kit the Assembly.)
Edit the "Used in Kit" by selecting Y (Yes) for Used in Kit unless the item is not to be issued when a kit is pulled. Select P (Phantom) to cause a Make subassembly to be treated as a Phantom when kitted. Select N (No) if the item is provided to the Line by some other means than kitting. (Note: Chemicals and adhesives are typical not-kitted items that are referenced on the BOM for costing or specification but issued to the production floor on a bulk replenishment basis.)
If you depress the AVL & Reference Designator tab the Ref designators can be edited manually in the table OR Enter the Prefix letter, Start No and End No and click on the Calculate button to auto-number. Here is where you will also check the approved AVL's and uncheck the AVL's that are NOT approved for this BOM. NOTE: If "GENR" is approved on the BOM MRP will consider any inventory for that part even if the AVL is NOT approved on the BOM. When adding new AVL's to the item master, if you do not want the BOM's automatically updated be sure that the "Disable Automatic BOM AVL update" is Enabled. See article #1477 for more information.
You may also Add or Delete Alternate Parts by depressing the Add or Delete button near the Alternate Parts to select alternative part numbers for the Line Item currently being edited in the BOM. This table is in the BOM screen because alternate part usage is always dependent upon the application and hence is BOM specific. (Note: Use the Quantity Info screen and AVL window to show alternate manufacturers; the alternate part window is only for items with a different internal part number (such as faster or tighter tolerance parts) that can be used on a temporary deviation when there is no choice.)
Once you have completed the changes, depress the Save button and BOM will be updated.
Note: If the Leveling of Make items is in process then the users will not be able to Add/Edit a BOM, even if the user is already in modifucation mode of the BOM, the user will not be allowed to save the changes until the leveling process is complete. This is due to the fact that the affected records in leveling of Make Parts is large and complex, the saving time to commit the whole changes to inventory tables does take a large amount of time, so we do not want users making modifications to the BOM when the process is still leveling, so we have added a flag that the users will see within the BOM module.
|
1.3.4.6. Bill of Material (BOM) Used in Kit Option and how it affects Kitting & MRP | Within the Bill of Material module the users have the option to mark each item loaded to the BOM as Used in Kit Y, N or F.
Y = Yes, this part is used in the Kit and will be considered fro MRP demands and appear within the Kitting module Qty Pick screen. Once the parts have been issued to the kit the system will automatically decrement it from inventory upon WO complete.
N = No, this part is NOT used in the kit, but it will be considered by MRP for demands but will NOT appear in the Kit module Qty Pick screen. This item will still be displayed on the Kit Pick Worksheet but it will have the “N” next to the item so users will know that it is not used in the kit. Example: you would use this option for Documentation. NOTE: Keep in mind that this item will be picked by the users on the floor but it will not be relieved from inventory in any way through the Kitting module. Users have to go make and manually adjust the inventory qty’s for this type of item.
MRP includes items with "N" flag in "used in kit" for Purchase Order Actions. The flag does not mean don't buy it, but instead, it means don't kit it. The part is still needed, or it wouldn't be on the BOM. Or the quantity would be zero. This feature is usually used by Users who have bulk stock on the floor, and the assemblers pull the parts out of floor stock. But there still remains the requirement to get the parts in house so they can be put into floor stock.
F = Floor, this would be used for an item that is not kept in the Stock room but is physically stored out on the Floor in production. “F” items will also be considered by MRP for demands, but will NOT be displayed on Kit Module Qty Pick Screen or the Shortage report. This item will still be displayed on the Kit Pick Worksheet but it will have the “F” next to the item to indicate to the users that it is located on the Floor. NOTE: Keep in mind that this item will be picked by the users on the floor but it will not be relieved from inventory in any way through the Kitting module. Users have to go make and manually adjust the inventory qty’s for this type of item.
|
1.3.4.7. Bill of Material Setup Scrap Checkbox | Within the Bill of Material Module you will see a Setup Scrap check box and a Standard Build field. If you wish for the setup scrap qty’s to be included in the Kitting and MRP calculations, Standard Cost Adjustments, etc. . . you need to make sure that the BOM has the Setup Scrp box marked. Then upon checking this box the system will default in the Standard Build qty to 1 (just because it can not be blank) It is recommend that you change the Standard Build qty to the desired average build qty for the product (the Standard Build will affect how the system will calculate Standard Cost Adjustments, etc. . . within the system)
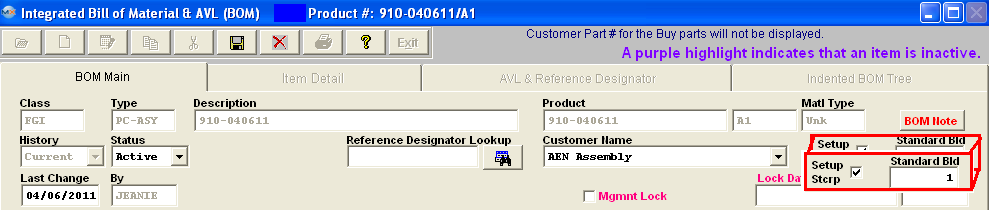
|
1.3.4.8. Make a Obsolete Part Available on a BOM |
Depress the pulldown next to the History and Select BOM History, all parts will be displayed, including the parts that have been obsoleted.
Highlight the part that has been obsoleted and enter the item detail screen, depress the edit button and remove the obsolete date or change it to a later date.
Now the part is available to use.
|
1.3.5. Reports - BOM & AVL | To display or print a Report for a BOM, first find the BOM. (See Article #571).
1. To access the reports, depress the Print action button at the top of the screen. The report screen will appear.
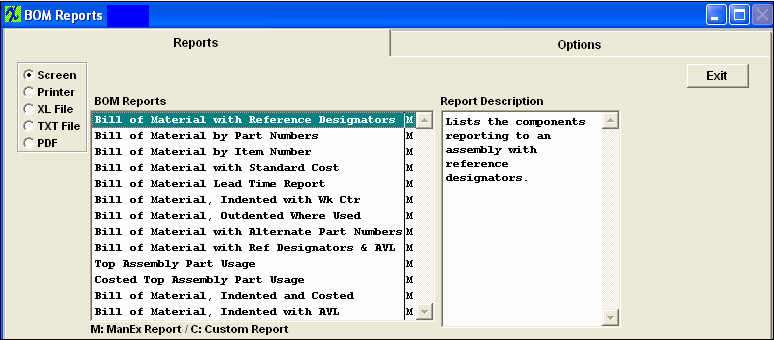
2. Select the output you desire by selecting one of the output radial selections at the top left of the screen, Screen, Printer, XL File, TXT File, or PDF.
3. Highlight the report desired and click on the option tab. (The BOM reports will indicate in the Source column if the item is setup as Make/Buy or Make/Phantom, along with Consigned or Buy).
BILL OF MATERIAL WITH REFERENCE DESIGNATORS
For the BOM with Reference Designators report check if you would like the BOM Notes to be displayed on the report.
Depress the OK button.
|
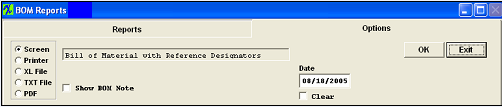 |
The following is printed
BILL OF MATERIAL BY PART NUMBERS
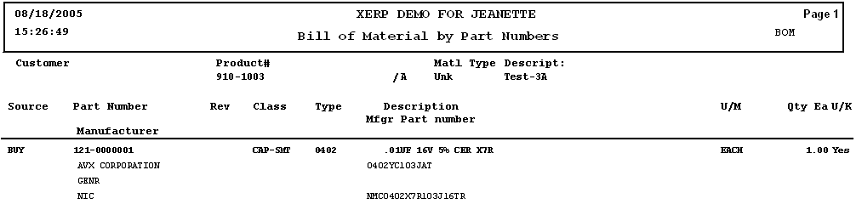
BILL OF MATERIAL BY ITEM NUMBERS
Check the boxes if you want the BOM item notes list and/or the BOM notes to be displayed on the report.
Depress Ok.
|
|
The following report will print:
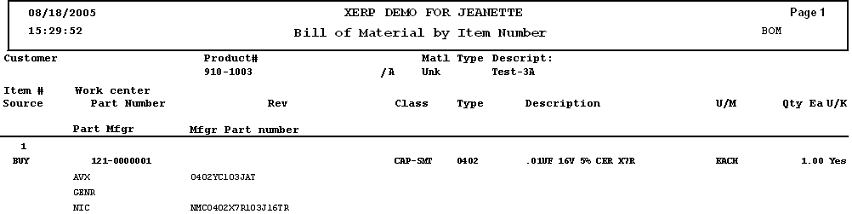
BILL OF MATERIAL WITH STANDARD COST
Choose By Item #, By Part #, or Descending Extended Cost from the Detail Report.
Depress Ok.
|
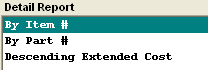 |
Note: This report takes into consideration the Std Bld Qty when calculating the setup scrap. You might find the cost calculated in SFT is different from the calculation shown on this report due to, that if the part UOM is "EACH" and the part has scrap % the code will round it up to next inter number.
a) For the PHANTOM parts in this report the standard cost calculated is based on their components (SUM of component's qty * component standard cost). Once the standard cost is calculated for the PHANTOM part, the report will treat the PHANTOM part as a single entity on the top assembly BOM and proceed as it was a BUY part with the std cost already entered.
b) If one of the component parts is a MAKE (not MAKE_BUY) and HAVE components assigned to it, the report will NOT show std cost of the parts itself, it will only show std cost of its subcomponents.
c) If one of the component parts is a MAKE (not MAKE_BUY) and does NOT HAVE parts assigned to it the report will show std cost of the part itself.
d) If one of the component part is a MAKE and MAKE_BUY the report will show price for the part itself and will show 0.00 costs for the subcomponents.
e) If one of the component part is a MAKE and a Phantom/Make the report will NOT display the std price for this part because the report will show the cost of this parts components.
Note: This report will only display the costs for ACTIVE parts and subassemblies as of the date of the report and will NOT include any parts that may have been identified as inactive either in the item master or in the obsolete date of the part on the BOM.
The values displayed should be in sync with the Cost Roll Up values. The following may be why the Standard Cost Roll is different from the Cost BOM Reports.
a) On the costed BOM Report for a Make/Buy assembly we display the value of the BOM in the costed report, but that total is NOT used in subsequent rollups to higher levels only the standard cost is.
b) In Kit Default Setup , user can "Exclude Scrap and Setup Scrap" in Kitting, MRP, and Cost Rollup, and this will override the "Setup Stcrp" box in the BOM. Therefore, if user checks "Setup Stcrp" checkbox along with a Standard Bld qty in BOM header, but has the checkbox checked in Kit Default Setup to "Exclude Scrap and Setup Scrap" for Cost Roll, the Cost Roll will NOT calculate the Setup Scrap cost, but this report will always calculate the Setup Scrap cost and this will cause unfavorable Configuration Variances. For further detail on how Excluding Scrap and Setup Scrap values will affect the variances see Articles #3067, #3053, and #3320 .
The following report will print: This report ALWAYS includes ALL the parts (including the items flagged as "N" for Used in kit)
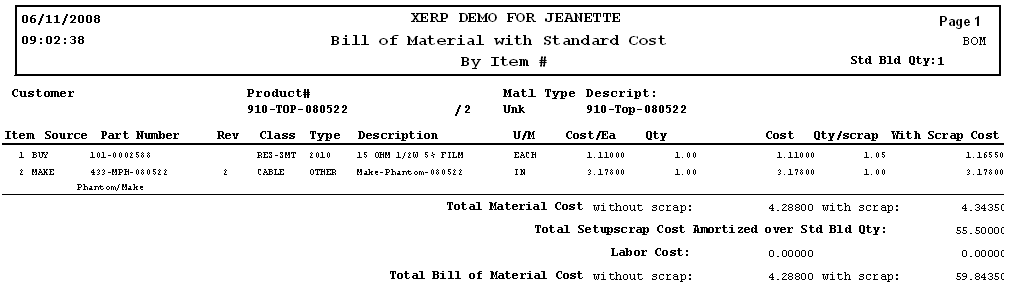
BILL OF MATERIAL LEAD TIME REPORT
Choose By Lead Time, or By Part # from the Detail Report.
Check Ok.
The BOM with Lead Time report will add the lead time of the parent part into the lead time field. So if you have a child part with a Purchase lead time of 30 days, and a parent part with a lead time of 1 day for Kitting and 3 days for Production, the lead time of the child part will be 1+3+30 = 34.
|
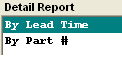 |
The following report will print:
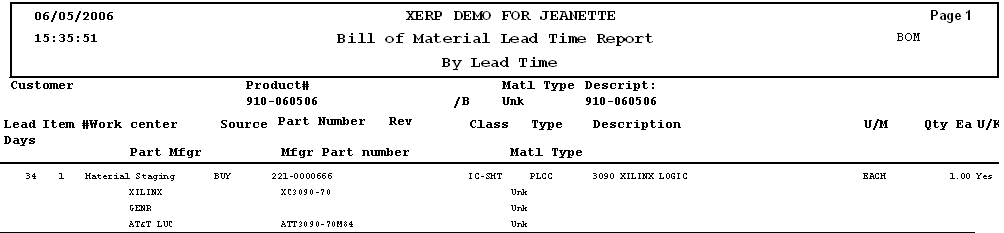
BILL OF MATERIAL, INDENTED WITH WORK CENTER

BILL OF MATERIAL, OUTDENTED WHERE USED
Select the Inventory Type by choosing the radial. Enter the Internal Part Number and Rev.
Check the box if you want the BOM items that are expired or not effective yet to be displayed on the report.
|
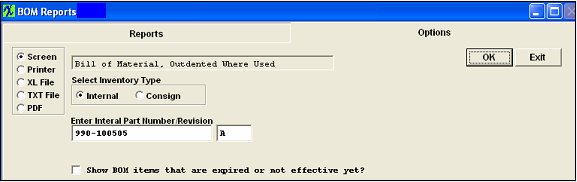 |
The following report will print:

BILL OF MATERIAL WITH ALTERNATE PART NUMBERS
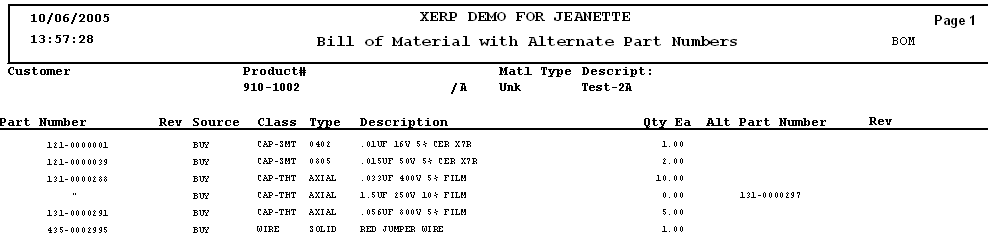
BILL OF MATERIALS WITH REFERENCE DESIGNATORS & AVL
Check the boxes if you want the BOM item notes list and/or BOM notes to be displayed on the report.
The AVL Order Pref Code will be displayed in front of the Mfgr and Mfgr PN information.
|
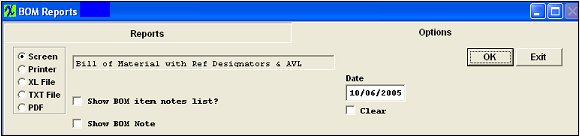 |
The following report will print:
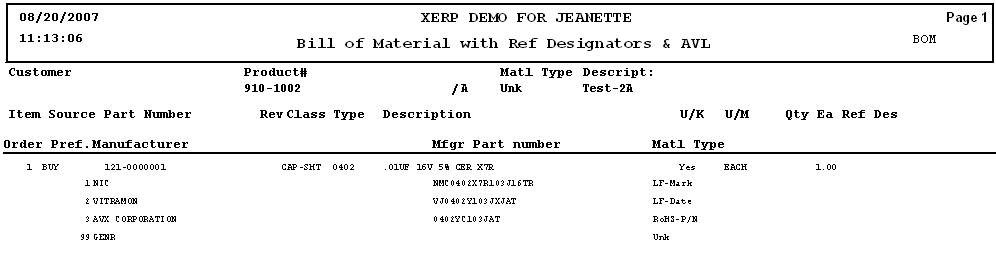
TOP ASSEMBLY PART USAGE
Select the Product number and applicable revision.
Select the quantity by toggling on the up and down arrows.
Choose between All Current Components, Used in Kit Components Only and Not used in kit Components by clicking on the desired radial.
Choose between Group by Component/Work Center and Show with Parent Assembly by clicking on the desired radial.
Depress Ok.
|
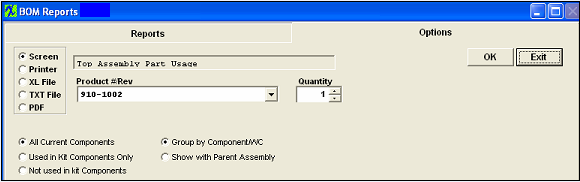 |
The following report is printed:
COSTED TOP ASSEMBLY PART USAGE
Select the Product number and applicable revision.
Select the quantity by toggling on the up and down arrows.
Choose between All Current Components, Used in Kit Components Only and Not used in kit Components by clicking on the desired radial.
Choose between Group by Component/Work Center and Show with Parent Assembly by clicking on the desired radial.
Depress Ok.
|
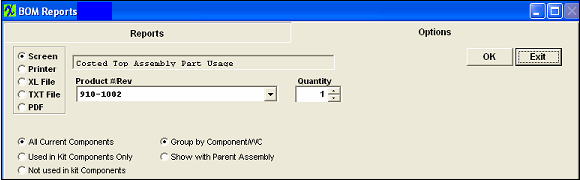 |
The following report will print:
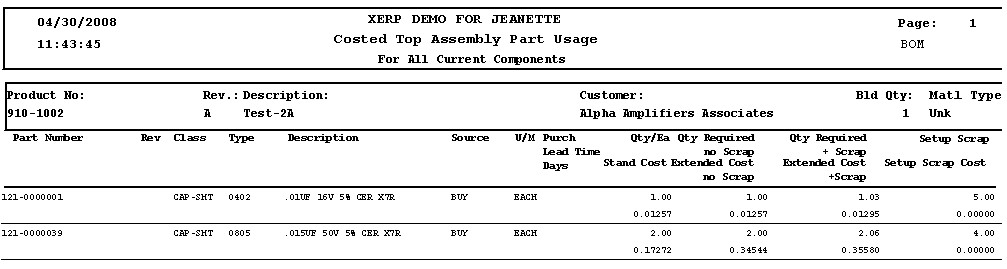
BILL OF MATERIAL, INDENTED AND COSTED - the following rules are applied to make sure that the Cost is properly calculated:
a) If one of the component parts are MAKE (not MAKE_BUY) and have components assigned to it, the report will NOT show cost of the parts itself, it will only show cost of its subcomponents.
b) If the component part is MAKE (not MAKE_BUY) and has no parts assigned to it the report will show cost of the part itself.
c) If the component part is MAKE and MAKE_BUY the report will show price for the part itself and will show 0.00 costs for the subcomponents and display the following message "Standard price of the subcomponents of this part is omitted, because the part is marked as a MAKE/BUY and report will consider this part's own cost.".
d) If the component part is a MAKE and a Phantom/Make the report will not display the std price for this part because the report will show the cost of this parts components.
Note: Only Approved AVL's will be displayed on report. Note: This report will only display the costs for ACTIVE parts and subassemblies as of the date of the report and will NOT include any parts that may have been identified as inactive either in the item master or in the obsolete date of the part on the BOM.
BILL OF MATERIAL, INDENTED WITH AVL - This report will list out the Indented BOM information, and the Approved AVL information.
The BOM reports will indicate in the Source column if the item is setup as Make/Buy or Make/Phantom, along with Consigned or Buy.
|
1.3.6. FAQs - BOM & AVL | Facts and Questions for the Bill of Material (BOM) Module |
1.3.7. ManEx Minutes (BOM) |
1.4. Express Import to BOM or Quote (OPTIONAL Module) |
1.4.1. Prerequisites - QBI | Prerequisites Required to Import a BOM
ManEx’s standard module configuration allows most users to accomplish their daily tasks. For those users wanting to get more from ManEx by leveraging the total solutions, this is one of the optional modules available for purchase. To place an order or to learn more about this specific module or any of the other optional modules please contact us at http://manex.com\contactus.aspx
To import a BOM, the template qabim.xlt must be used. Note: The module will only recognize and import data that is populated within the "Supplied BOM" worksheet within the template. The other worksheets are for additional reference only.
After activation, "Express Import to BOM or Quote" access for each user must be setup in the ManEx System Security module. Users with “Supervisor Rights” will automatically have access.
|
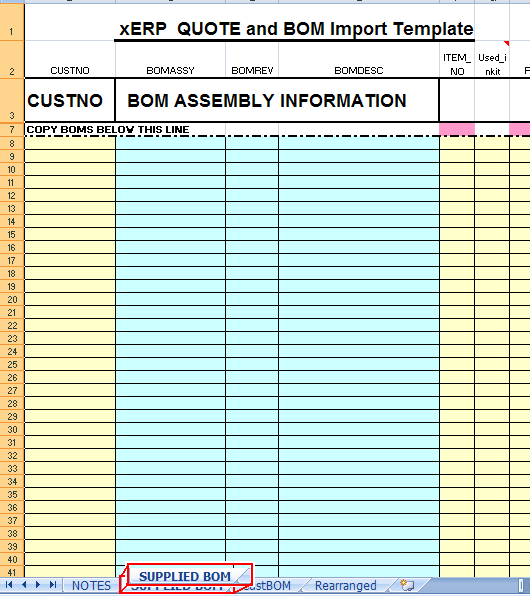 |
This template has the required fields to begin the import of new Item masters and BOMs. It contains two named ranges, COLHDR and IMPTDATA, which must be included. In the COLHDR are contained the field names for each column, and must not be modified. The IMPTDATA range must include all data to be imported (not the field names). The cells that must be in the IMPTDATA range are colored, and as the sheet is supplied, contain 1500 lines. More may be added, but the range must be expanded to include them.
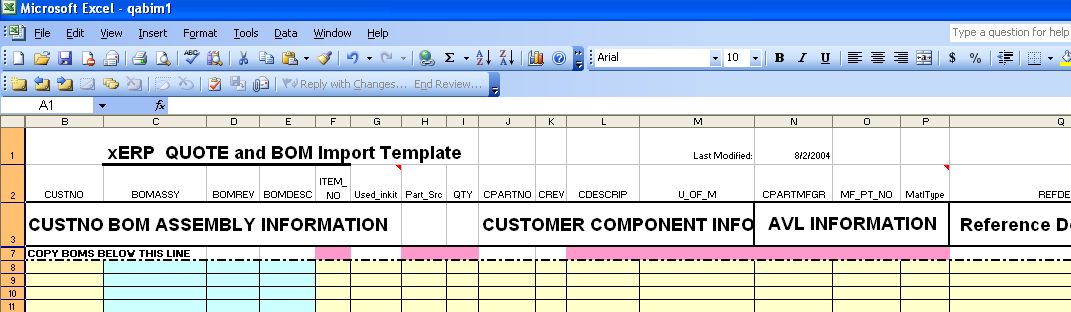
The top four rows are protected to avoid accidental modification, but there is no password required to un-protect the sheet. Once un-protected, the user may rearrange the columns to match data as received from each customer, then saved the modified sheet as a template for each customer.
The BOMASSY, BOMREV, and BOMDESC (highlighted in blue) listed MUST match either what is already in the system , or MUST be listed as a component on the spreadsheet (as shown below in the RED box). The same assembly and revision cannot be for two different customers. These fields are required.
To import a brand new Product/assembly into the system from the spreadsheet, the customer number and the columns in pink are REQUIRED to be completed, as shown below:
The columns in pink are required to be completed.
To import Make or Buy parts to a BOM you must popluate the following fields: ITEM NO, Part Src, QTY, CPARTMFGR
To import Consigned parts to a BOM you must popluate the following fields: ITEM NO, Part Src, QTY, CPARTMFGR, CPARTNO and/or CDESCRIP
To import to Quote you must populate the following fields: ITEM NO, Part Src, QTY, CPARTMFGR, CUSTNO, CPARTNO and/or CDESCRIP
The fields listed on the XLS spreadsheet are:
CUSTNO: |
The 10 character Customer code (optional) |
BOMASSY: |
The 20 character Customer part number of the ASSEMBLY (required) |
BOMREV: |
The 4 character Customer revision of the ASSEMBLY (required) |
BOMDESC: |
The 30 character Customer description of the ASSEMBLY (required) |
ITEM_NO: |
The line item that each component is on each BOM (required) (NOTE: The line item must be unique for each component). |
Used in Kit |
Enter in "Y" if this part is to be used in kit, Enter "N" if this part is NOT to be used in kit. If this field is left blank "Y" will be defaulted into the BOM when import is complete.(optional) |
Part_Src: |
If it is a BUY, MAKE, CONSIGN, or PHANTOM (required) |
QTY: |
The quantity per assembly (required) |
CPARTNO: |
The CUSTOMER Part number for the components (optional) NOTE: This field is required if Auto Numbering is Disabled. |
CREV: |
The CUSTOMER Revision for the components (optional) |
CDESCRIP: |
The CUSTOMER Description of the component (required) |
U_of_M: |
The unit of measure of the component. Usually EACH (required) NOTE: If you wish for the system to take the system defaults for UoM we recommended that you leave the UOM column blank on the XLS spreadsheet and based on the Class/type selections made within the BOM Import module the system will then populate both Stock and Purchase UOM for the new Inventory Part number that is generated. |
CPARTMFG: |
The MANUFACTURER of the customer part number (required) |
MF_PT_NO: |
The manufacturer of Part Number of the customer part number (optional) |
MatlType |
This is the AVL Material Type.(required) The choices are hard coded in the ManEx system. If this field is left blank "Unk" will be defaulted into the BOM and ICM when import is complete. (Depress the red mark in the right hand corner to view the choices) |
REFDESG: |
The reference designator(s) for the customer part number (optional) |
NOTE: The Reference Designator field is unlimited in size, and can ONLY accept the following formats or combinations, thereof:
C1, C2, C3, C5, C6, C10, . . . . . . .,
C1-C3, C5-C6, C10, . . . . . . .,
C103, C5-6, C10, . . . . . . . . . .,
It is very critical that the user follows these formats or combinations. If the program cannot decipher the reference designators it will confuse the system and create the system to hang up and/or crash.
If there are multiple AVL's for the same component, it is necessary to repeat all the information including the item number and Reference Designators for each AVL, ONLY changing the CPARTMFGR and MFGR PN. All other information MUST be the same. See example below.
The Assemblies listed must either already be in the system , or included in the spreadsheet. The same assembly and revision cannot be for two different customers.
The spreadsheet can be save in any folder accessible by Manex and under any name.
|
1.4.2. Introduction for QBI | To provide the capability to load Bills of Material (BOM), to Manex Production and Quotation modules from a simplified Excel spreadsheet.Parts lists, AVL's, and Reference Designators, are all included.
A specific excel template has been created for the module and must be used.There is no limit to the size of the BOMs (number of components), nor to the number of BOMs (assemblies) that can be loaded at one time.The only restrictions are that when loading to a Quote, only one customer may be on the spreadsheet, and when loading to a BOM, only one customer may be associated with a given BOM.
After a preliminary validation of the data, the Import procedure will attempt to locate existing components in the system, and offer the user the choice to use alternate existing components, or to load the spreadsheet again with a different part number. All NEW part numbers will be loaded into inventory, and the BOMs created. If there is already an existing BOM, the user will be prompt to decide to override the existing BOM, or ignore the BOM being loaded in the spreadsheet. If new AVLs are involved with existing parts, the user will be prompt to add the new AVL to the existing part, or create a new part number. However, it will not overide the material type on existing AVL's, due to the fact that there might be inventory on hand at that time that is not LF (for example) and if we changed the material type upon load it would no longer match the parts on hand. |
1.4.3. How To ..... for QBI |
1.4.3.1. Import to BOM or Quote |
Once the spreadsheet is completed, it may be loaded from within the Manex Express Import to BOM or Quote Module.
|
|
Enter the Express Import to BOM or Quote module and the following screen will appear:
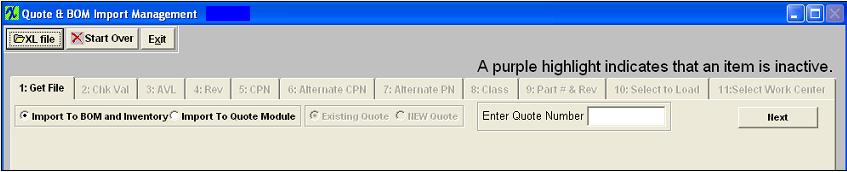
1. Choose to either Import to BOM and Inventory or Import to Quote Module by Selecting the appropriate radial.
- If you choose to Import to Quote Module. The user will need to select Existing Quote or New Quote. If Existing Quote is selected you must enter in the Quote Number. If New Quote is selected and system setup is on auto numbering for new quote number, program will not take the next number until the "Load" button is clicked. The last quote number is displayed on the screen in the beginning of the import process. When the "Load" button is clicked the system will check for the next new number and display a prompt to the user. When selecting to import to new quote you can only import new products. To import a brand new Product/assembly into the system from the spreadsheet, the customer number and the columns in pink are REQUIRED to be completed, and MUST match the BOMASSY, BOMREV, and BOMDESC listed in the blue shaded columns. For further detail see Article #1805 .
- When importing to an existing Quote number through the QBi module, upon depressing the Load button, the system will first find if any products, (disregarding if the product is the same or different from the new import), exist in the Manex under the given quote #. If the system finds any records it will ask the user whether or not to overwrite them. If the user selects "Yes" the system will proceed the same way it was always working replacing what ever was under the quote module with new import information. If the user selects "No" the system will then check if the new import information has any product listed that is the same as the product under the existing quote, and if it does user will be prompted again, but this time if they want to overwrite those records for the products that are the same in both quote and new import file. If the user chooses "Yes" the system will overwrite existing product information and add any new product to the quote. If the user chooses "No" the system will only add any new products to the quote.
- If you choose to Import to BOM and Inventory
2. Depress the XL File Button. The following screen will appear.
3. The user will highlight the file to be uploaded.
|
There are several validations run at this point, these are a few. Note: If the XLS file is not displayed on screen go to your Local_manex directory. There you should be able to find {{ C:\"_ManexLocal"temp"POExceptionXL}} within that directory is where some of the XLS files that are displayed for your reference could be listed.
If the part Source on the excel template does not exactly match what is in the Part Source Setup (for example: having CONG on the excel template and CONSG setup in Part Source Setup) the following message will be displayed and you may choose to continue or abort.
|
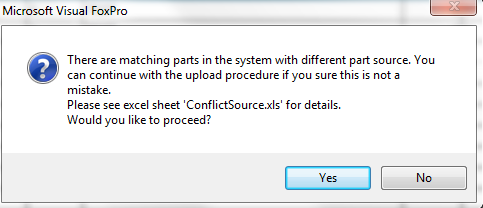 |
If there is missing data or invalid data on spreadsheet the following prompt will be displayed and you may choose to continue or abort.
|
|
If there are different components with the same item numbers for the same BOM listed on the spreadsheet the following prompt will be displayed. The upload will abort, so you may review the "DupItem.xls" file and correct the spreadsheet.
If users happen to be loading more than one BOM/product into the system on the same spreadsheet and they have the same part number associated with different products with different descrptions that information will also be displayed in an XLS spreadsheet.
|
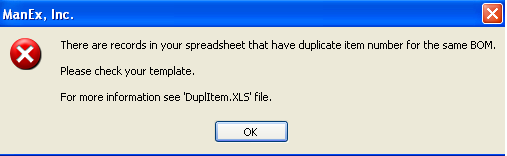 |
If there are incorrect ref designator count on the spreadsheet the following prompt will be displayed. You may choose to continue or abort to review the XLS file created and correct the spreadsheet. |
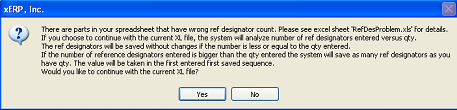 |
If the material type has been entered incorrectly on the spreadsheet the following prompt will be displayed. You may choose to continue or abort to review the XLS file created and correct the spreadsheet. |
 |
Once all the validations are run, The 1: Get File tab appears and the contents of the file are displayed.
If user has entered an existing ManEx PN in the CPARNO field on the Template, they have the option to check this box "Use Information in 'Cpartno' field as Internal Part Number". If this box is checked the system will use the PN in the CPARTNO field on the template as the internal PN not as a customer/consigned PN. Note: The Mfgr on the template MUST be Genr, also. See the example below.
4. The user may click on the "Next" button to continue or the "Start Over" button to clear the contents and select another file. Again several validations are run.
If there are multi part sources (same part number listed twice; one as MAKE and one as BUY) listed on the spreadsheet the following warning will appear. The upload will abort so you may review the "DupSource.xls" file and correct the spreadsheet. |
 |
If the BOM assembly you are uploading does not exist in ManEx as a Customer assembly nor is in the components of the import list or is different than what is listed on the import list this warning will appear. The upload will abort so you may review the "MissingAssy".xls" file and correct the spreadsheet. |
 |
If you are uploading an existing product to the Quote module you will receive the following message. You can only import new products into the Quote Module. To import a brand new Product/assembly into the system from the spreadsheet, the customer number and the columns in pink are REQUIRED to be completed, and MUST match the BOMASSY, BOMREV, and BOMDESC listed in the blue shaded columns. For further detail see Article #1805 . |
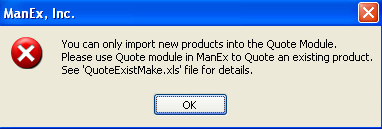 |
If there is more than one customer listed on the spreadsheet the following warning will appear. the upload will abort so you may review the "QuoteCust.xls" file and correct the spreadsheet.
|
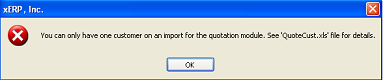 |
If there are more than one customer ID listed on the spreadsheet the following warning will appear. The upload will abort so you may review the "ConflictCust.xls" file and correct the spreadsheet. |
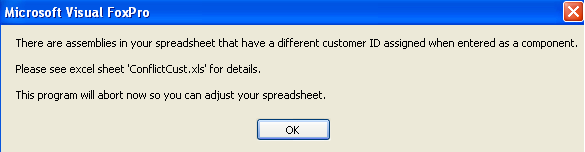 |
Once all the validations are run, The 2: Check Val tab appears. If validation of certain data fails, the following screen will be displayed, with a grid of problems, and the User asked to clarify the data.
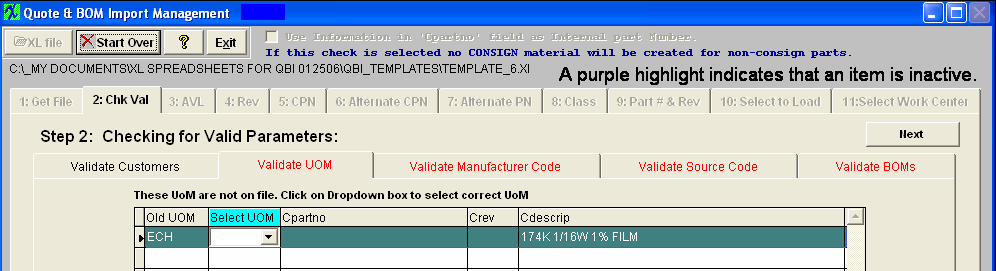
The first check is to verify that valid Customer Codes are used in the spreadsheet. If one or more invalid customers are found, then a grid will be displayed with the appropriate information, and the user must select an appropriate customer from the drop-down list of customer codes. Or, the user may exit the screen and clarify the spreadsheet.
The next check is to validate that a valid Unit of Measure (UOM) is on each line of the spreadsheet. If an invalid UOM is found, the user is presented with a list of invalid UOMs and may select a valid one from a drop down list of valid UOMs. Or, the user may exit the screen and clarify the spreadsheet. Clicking on the dropdown arrow will display available Units of Measure to replace the invalid one.
The next check is to validate that correct Manufacturer Codes have been used in the spreadsheet. If not, a grid is displayed with the invalid manufacturer codes, and the use may select from a dropdown list of valid manufacturers to replace the invalid code. Or, the user may exit the screen and clarify the spreadsheet. Clicking on the dropdown arrow will display available Manufacturers to replace the invalid one. Once the user identifies a MFGR all like MFGRS on the BOM will be updated with the same selection.
The next check is to validate that correct Source Codes have been used in the spreadsheet. If not, a grid is displayed with the invalid source codes, and the user may select from a dropdown list of valid source codes (BUY, MAKE, CONSG or PHANTOM). Or, the user may exit the screen and clarify the spreadsheet. Clicking on the dropdown arrow will display available Source Codes to replace the invalid one.
The next check is to ascertain whether or not there is an existing BOM for assemblies contained in the spreadsheet. If there is, the user must indicate whether or not the existing BOM is to be overwritten with the new data in the spreadsheet. If the user elects to NOT overwrite the existing BOM, the data will not be loaded to the BOM, but the item master will still be updated with any new parts contained in the spreadsheet. Or, the user may exit the screen and clarify the spreadsheet.
5. When all of the foregoing information has been validated or corrected, the user may click on the "Next" button. The program will be sure that all information is valid, and proceed to the next page. Or, it will redirect the user to the invalid information and allow correction of the data.
The 3: AVL tab appears.
The program will search the database for existing Item Masters with the same Customer Part Number and Revision and for the same Customer as contained in the spreadsheet (although is a different AVL.
The user will be presented with a list of components on the spreadsheet with NEW AVLS (same customer, Customer Part Number, Customer Revision, but AVL is different on spreadsheet). The user is then prompted to select (by check box) AVLs they wish to add to the existing customer part numbers. Items not checked will be retained for further disposition in the program.
NOTE: If a customer selects to use an existing PN, when they import a BOM the new AVL(s) will NOT be added to existing BOM's.
For Example: If user has a part listed on their XL file with customer part number "215002-002" and customer id '0000000004'. When the user moves on to the AVL page (page 3), the program will try to located the part listed on the XL file in the inventory. It will search for all the consigned parts with customer part number = "215002-002" and customer id = '0000000004'. In the inventory data the system found two different internal parts with the same consigned part number and the same customer id. One part is '101-0001621' and another is '515-0003224'. Then the system will proceed with comparing AVL's for those parts with AVL's entered in the XL. It found that the part number '515-0003224' has Mfgr: 'SWITCHCR', MPN: 'RTT34B02', which is a match to the AVL entered in the XL file. You can see "Same as in upload" in the MPN column on the screen. For the part number '101-0001621' the system found "GENR" AVL, which is different from our XL file, so the system indicates that if this part will be selected a new AVL 'SWITCHCR' with MPN: 'RTT34B02' will be added to it. Base on this information a user can make a decision on which part to use.
6. Pressing the "Next" button will add the checked AVLs to existing Customer Part Numbers. It will also find all existing parts in the item master and include all inventory item master information with those parts being loaded.
The 4: Rev tab appears.
The import program will search the existing database for parts having the same AVL (Mfgr and Mfrg PN) as the spreadsheet parts, under the same customer part number, but with a different customer revision. The user will be presented with a list of those parts, and may take the option to use them instead of creating a new part number. If accepted (by check box), the alternate customer part number and revision will be used in the BOM.Items not checked will be retained for further disposition in the program.
7. Pressing the "Next" button will revise the checked items to existing (alternate) Customer Part Numbers.
The 5: CPN tab appears.
The import program will search the existing database for parts having the same AVL as the spreadsheet parts, under the ANY CUSTOMER with the same customer part number, and without regard to customer revision. (Some users may use the manufacturers part number for their own.) The user will be presented with a list of those parts, and may take the option to use them instead of creating a new part number. If accepted (by check box), the alternate customer part number and revision will be used in the BOM. However, the Customer will be added to the customer list for the existing part. Of the checked items, there must be only one check to select an alternate part number, although the search of existing part numbers may find several. Items not checked will be retained for further disposition in the program.
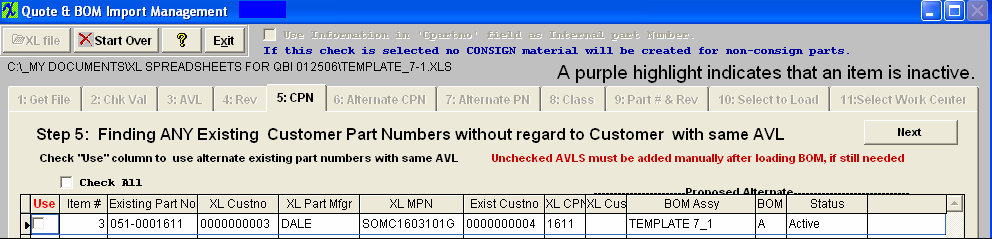
8. Pressing the "Next" button will revise the checked items to existing (alternate) Customer Part Numbers.
The 6: Alternate CPN tab appears.
The import program will search the existing database for parts having the same AVL as the spreadsheet parts, under the same customer, but with ANY customer part number, and without regard to customer revision. The user will be presented with a list of those parts, and may take the option to use them instead of creating a new part number. If accepted (by check box), the alternate customer part number and revision will be used in the BOM. However, the Customer will be added to the customer list for the existing part. Items not checked will be retained for further disposition in the program.
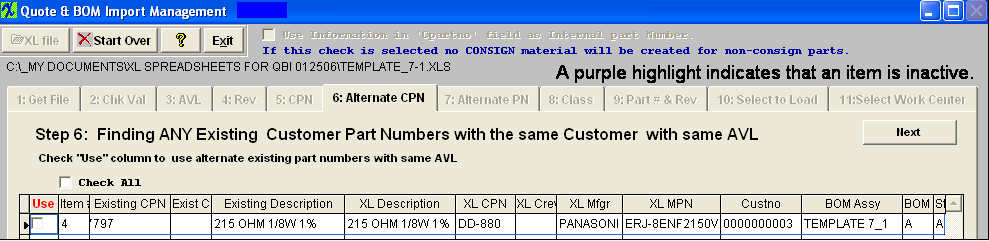
9. Pressing the Next button will revise the checked items to existing (alternate) Part Numbers.
The 7: Alternate PN tab appears.
The import program will search the existing database for ANY parts having all the same AVL(s) (Same Mfgr and Mfgr PN) as the spreadsheet parts.
If the part number listed on the spreadsheet has ALL the same AVL(s) and/or some additional AVL(s), as a part in the system, the user will be presented with a list of those parts, and may take the option to use them instead of creating a new part number. If accepted (by checkbox), the alternate part number and revision will be used in the BOM, the Customer will be added to the customer list for the existing part, along with any new AVL information from the xls spreadsheet, which is automatically added to the BOM and Inventory Control records. If the part number listed on the spreadsheet has some AVL(s) that match a part in the system, but not all of them, the system will NOT consider this as an alternative part number.
Here is an example of why the system will NOT list a part as an Alternative part if only 1 AVL matches and not all AVLs match: Lets say we have PART A (internal part) with AVL1, AVL2, AVL3. This part is on the BOM for the customer A. Lets say the user is loading BOM for customer B and it has PART B (which is NOT in the system yet) with AVL6, AVL7, AVL1. If the system recognized PART A as an alternative to PART B and adds AVL6, AVL7 to the PART A. Then when you go and view BOM for customer A you will see AVL1, AVL2, AVL3, AVL6, and AVL7 on the list of approved manufacturers. This list was changed seamlessly and without real understanding on the users part or without customers consent. If this is not enough we added X-Ref that will find anything the user want and replace the part selected.
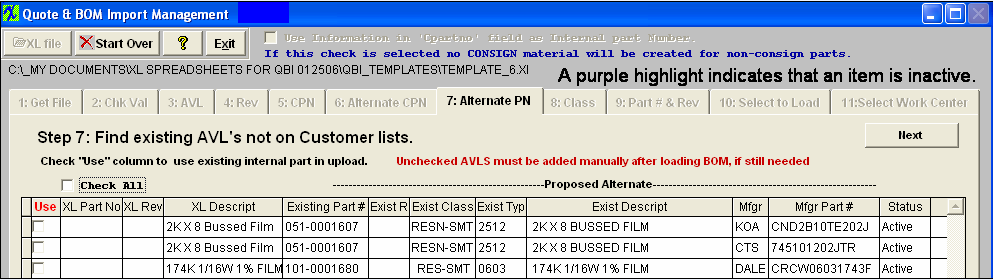
Items not checked will be retained for further disposition in the program. A purple highlight indicates that the item is Inactive. If the user still elects to use the Inactive part the system will display a warning message that the inactive items selected and the users will option of changing the status to Active.
10. Pressing the "Next" button will revise the checked items to existing (alternate) Customer Part Numbers.
The 8:Class tab will appear.
The import program will display all parts for which an existing nor alternate part number have been selected. These parts will be new parts added to the item master, and must have additional information included in order to be loaded. The user may select a part class and (optionally) part type for each item or leave it blank. Blank classes will be assigned "TBD" when loaded into Inventory. Items for which there are multiple AVLS will only require the class and type to be entered once. The user selects each from a dropdown list. Once a Class is assigned, the available Types for that class will be available for inclusion in the part Type. Because the descriptions are loaded from customer documentation, and the user may wish to clarify the description, the opportunity to do so is on this page.Items not completed will be loaded into the item master with a part class of TBD.
11. Pressing the "Next" button will then search the database for the default information for the class and type, and populate the required fields for the new parts based on the class and type. If no parts have been checked for uploading the system will prompt the user and place them back on the Part Class/Type page.
The 9:Part # & Rev tab appears.
The import program will determine whether or not the user has Auto-Part Numbering enabled. If it is enabled, the program will assign internal part numbers based on the class and type setups, and move to the next page. If Auto-Part Numbering is disabled (or off), the user must enter valid internal part numbers and Revisions for each new part. The internal part number entered may not already exist in the database. If user wants to use the CustPN and CustRev (from the template) for the internal Part # and Rev check the Copy box. Checking/Uncheckiing the "Check All" box (located above the CustPN and CustRev columns) will check/uncheck all the records. If user wants to add the prefix setup for that customer (the prefix must be setup within the Customer Information Module) to the new part number they must check the PRFX box. Checking/Un-checking the "Check All" box to the far right globally check/uncheck all the records. Items not completed will NOT be loaded into the item master nor the BOM.
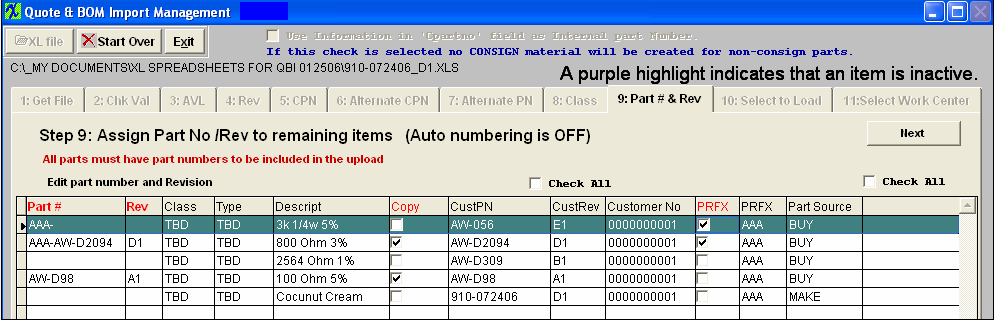
12. Pressing the "Next" button will then search the database to validate the entered part numbers.
The 10:Select to Load tab appears.
The import program will display the entire list of part numbers being entered by assembly. If the auto numbering is on, user will have the ability to copy the XL revision to the new part revision by checking the box. Check/Un-Check All box (located above the Rev column) gives the user the ability to check/uncheck all records to copy the XL Rev to new part Rev. The user has a final opportunity to verify that the parts and BOMs are to be loaded. A Check/Un-Check All box is available (located after the Step 10: Select items to Load title) to give the user the ability to check/uncheck all records to be loaded into the item master or the BOM. (In-Active records will have to be manually checked). Items not checked will NOT be loaded into the item master nor the BOM.
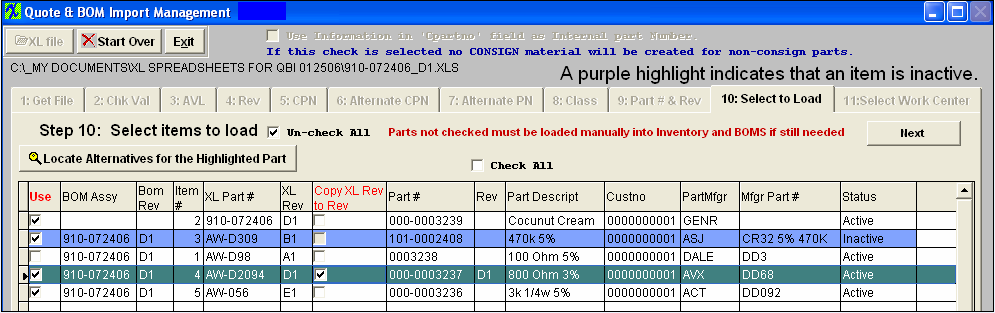
This button will take the user to a screen, where they can make a selection by what ever criteria needed by choosing (Internal Part Number, Mfgr Part Number, Customer Part Number, Supplier's Part Number, or Description,etc) to search.
Note: If a customer selects to "Locate Alternatives for the Highlighted Part" within Step 10, when they import a BOM that uses an existing ManEx PN and adds new AVL(s), the new AVL(s) are NOT added to any existing BOM's.
|
|
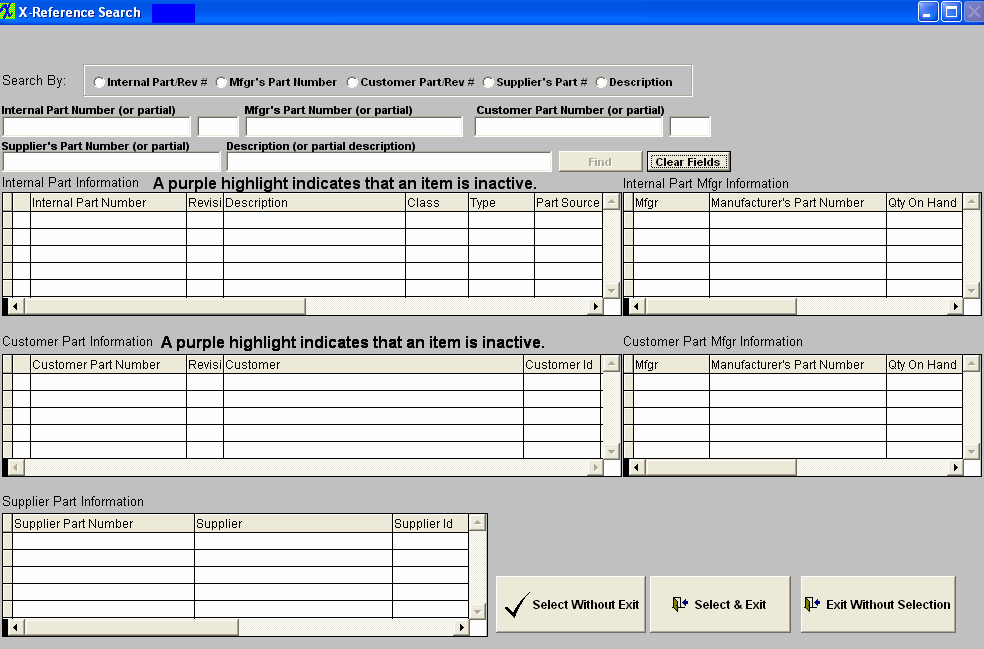
The user can enter partial string and search is not case sensitive. After system will find parts in response to the search, the user can make a selection by checking on one of the check boxes. The user can click one of the buttons on the bottom of the screen when done. And if the user selects one of the buttons with "Select" on it the part that was highlighted in the BOM import screen will be replaced. Please note the search screen can be up all the time, so if the user selects a part find replacement and click "Select without Exit" button then select next part on the import screen and look for the replacement without exiting search screen.
13. Pressing the "Next" button will then remove the parts that are not to be loaded into the system.
The 11:Select Work Center tab will appear.
The import program will display the entire list of part numbers to be loaded into the item master or BOM. All components will be defaulted to the Staging work center. The user has the option to change the work center at this time. Highlight the part number you would like to change.Choose a work center from the pull down list. Click on the Replace Highlighted Records box.
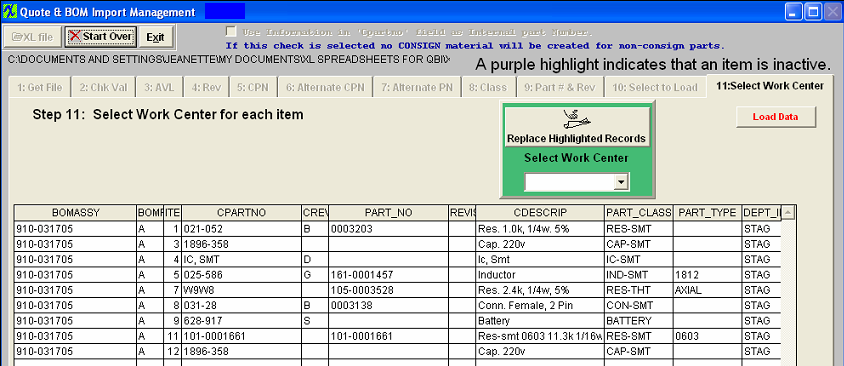
14. Pressing the "Load Data" button will complete the upload. The tables updated will be the INVENTOR, INVTMFGR, INVTMFHD, BOM_DET and BOM_REF.
If you receive the following message after depressing the "Load Data" button there are a few scenarios that could be causing this message to appear:
1. A same part, with different description associated with different product, will cause this message to appear upon import.
2. If the Auto numbering is turned OFF and user has entered the same part number to items with same description but different customer part numbers will cause this message to appear.
When loading one BOM/product at a time into the ManEx System it checks to see if the users might have the same part number, but with different descriptions or different customer part numbers loaded on the spreadsheet. If found then it would display that information in an XLS spreadsheet for the users to address.
|
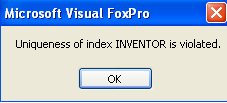 |
|
1.5. ECO, BCN & Deviation Control Management (EBD) (OPTIONAL Module) |
1.5.1. Prerequisites - EBD |
ManEx’s standard module configuration allows most users to accomplish their daily tasks. For those users wanting to get more from ManEx by leveraging the total solutions, this is one of the optional modules available for purchase. To place an order or to learn more about this specific module or any of the other optional modules please contact us at http://manex.com\contactus.aspx
After activation, "Engineering Change Order" access for each user must be setup in the ManEx System Security module. Users with “Supervisor Rights” will automatically have access.
A Bill of Materials must exist for the product being revised.
|
1.5.2. Introduction - EBD | This module allows users to document the source (internal or customer), the purpose, the details, and the impact of the change. The module can apply the changes to new and existing jobs, and ensure that production is aware of the change and is using the latest information.
This module allows users to document the changes using one of the following three approaches:
"ECO" = An ECO records Engineering changes for assemblies when there is a Revision or Part Number change. There can be changes to the Bill of Materials components and/or quantity, to the materials cost, labor cost, whether or not there is a serial number required and to the description. The user can enter whether existing WIP or FGI items are to be scrapped or modified. Once all of the engineering changes are entered, the ECO needs to be approved by the the approvals (as specified in the ECO setup module). Once the approvals are entered, the user may Update the following records: Inventory Master, Product Routing, Product Data Management and Bill of Materials. NOTE: These records will ONLY be updated if the Revision or Part Number has been changed.
"DEVIATION" = A Deviation creates a record that someone approved the change in the process for individual work order(s). Such as using a different part, leaving a part off, or perform a special additional step in the process, etc. When a Deviation is created within this module no records are updated or changed. It is a document for reference only. The user may print the deviation and it will list the work orders selected to be updated. Deviations have an expiration date so users will know that their customer or management allowed the modification for a limited period of time.
"BCN" = When "BCN" type is selected, the user can change all part information just like ECO, but user won't be able to create a new product number/rev, or click any "copy" checkboxes on "Update/Create records" page. WO and SO lists will also not be available for selections. When the "Update All Records" button is clicked, the BOM of the product number will be updated just as if the BOM was changed in BOM module. This feature will track any changes to the BOM through the system.
|
1.5.3. Fields & Definitions - EBD |
1.5.3.1. Header Tab |
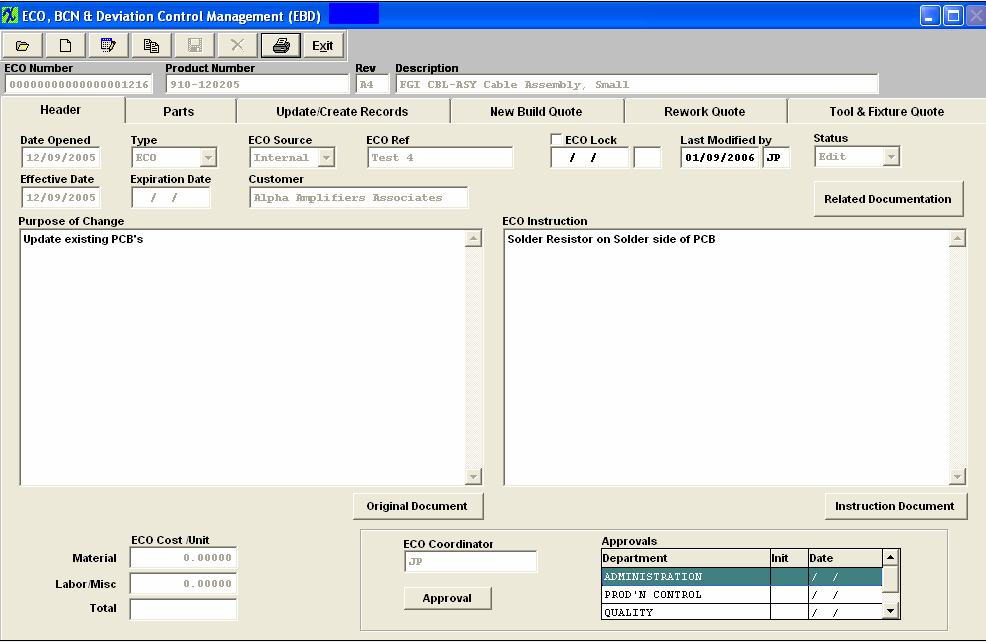
Header Tab Field Definitions
ECO Number |
The number assigned to the ECO, BCN, or Deviation.
|
Product Number |
The unique internal number assigned to the product |
Rev |
The revision number or character assigned to the product.
|
Description |
The description of the product. |
Date Opened |
The date the ECO/BCN/Deviation was started.
|
Type |
The type of change, either ECO (Engineering Change Order), BCN (BOM Change Notice), or Deviation. ECO is for permanent changes to the Inventory Item Master and the Bill of Materials when there is a revision or part number change. BCN is for permanent changes to the BOM. Deviation is for a one time change to a work order(s).
|
ECO Source |
This is the source of the ECO, Customer or Internal.This allows the users to know if this ECO was created internally or upon Customer request. At this time this field is for reference only, but will be used for reporting later on.
|
ECO Ref |
An internally assigned reference number.
|
ECO Lock |
If this box is checked, all users can access the screen, but will not be able to edit the record until Aprroved users remove the lock. When locked the users initials and date will default in.
Note: Users MUST have special rights within the Security module to modify this field.
|
Last Modified |
The users initials and date will default in when modified. |
Status |
The status of the Engineering Change Order, either Approved, Edit, Pending or Cancelled.
|
Effective Date |
The date that this ECO become effective. (This Date MUST be prior to the Work Order date to be applied).
|
Expiration Date |
The date that the Deviation will expire. (This field is only enabled for a deviation and MUST be popluated for the Deviation to be available within the SFT module ) |
Customer |
The name of the Customer which is linked with the Bill Of Materials.
|
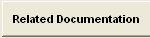 |
This button will allow users the ability to load more documents pertaining to the ECO (cutomer ECO,drawings, instructions,etc). Loaded files will not be carried fwd to the PDM module upon ECO approval. |
Purpose of Change |
The intent of the change.
|
ECO Instruction |
The description of the change.
|
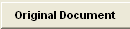 |
This Button will allow the users to view any hard copy ECO drawing or Documentation loaded. When files have been loaded this button will appear with Red Text. |
 |
This Button will allow the users to view any hard copy ECO drawing or Documentation loaded. When files have been loaded this button will appear with Red Text.
|
ECO Cost per Unit |
Material is the Material Cost Change Total forwarding from the Parts tab.
Labor is the Labor Cost Change Total forwarding from the New Build Labor Cost tab.
Total is the sum of the changes in Materials and Labor, above.(Note that the signs can be either positive or negative depending upon the changes made.)
Note: Users MUST have special rights within the Security module to view the pricing information.
|
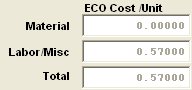 |
ECO Coordinator |
The name of the engineer entering the Engineering Change Order. |
Approvals |
The name of the department, initials of the approver and the date of approval. Note: The approving department is setup in the ECO Setup module.
|
 |
This button is used for the approval process for each department indicated |
|
1.5.3.2. Parts Tab |
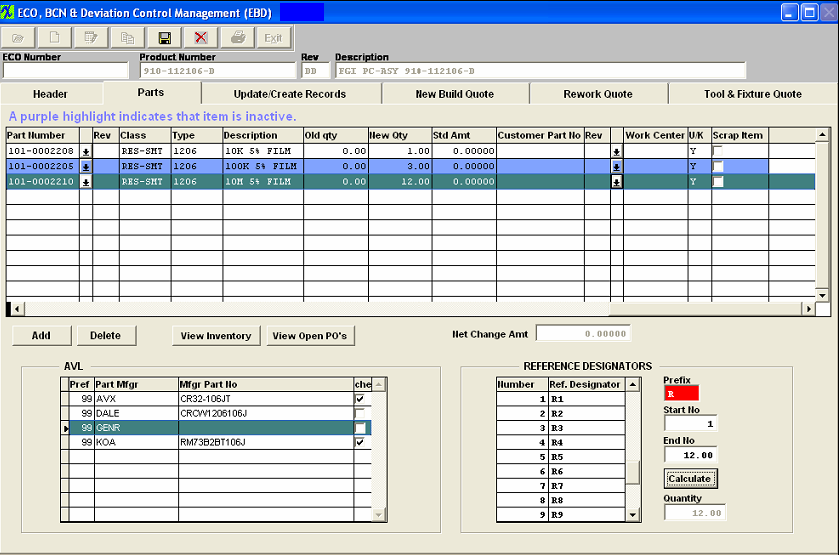
Parts Tab Field Definitions - The Parts tab displays any additional changes or deletions of Bill of Material Components. If the part added has a status of "Inactive" within the Inventory Control Management, it will be highlighted in purple as an indicator to the user that this item is inactive at this time. If the user chooses to leave the inactive part on the ECO, that part number record status will automatically be changed to Active upon the "Update Records" button being depressed, so user will not have inactive parts listed on the BOM. The user will receive a warning that an XLS file has been created for reivew.
Status |
The status of the component, either Add, Delete, Change. |
Line No |
The Bill of Materials line number.
|
Source |
The source of the component, either Buy, Make, Phantom or Consign.
|
Part Number |
The internal number assigned to the component |
Rev |
The revision character pertaining to the component part number |
Class |
The classification of the component.
|
Type |
The type within the classification of the component |
Description |
The description of the component part number |
Old Qty |
The quantityof thecomponent currently called for in the Bill of Materials.
|
New Qty |
The new quantity ofthe component which will be called for. |
Std Amt |
The standard cost per the Inventory Control Item Master multiplied by the net change in the number of components used.
|
Customer Part No |
If there is a customer part number associated with the user’s part number, it will appear here.
|
Rev |
The revision character associated with the Customer Part number.
|
Work Center |
The work station where is component is 1st used in the assembly production process.
|
U/K |
Valid entries for this field are “Y” – Yes used in Kit, “N” – Not used in Kit, “F” – Free Stock.The system will default the value to be “Y.”
|
Scrap Item |
This field is for reference only, it will not affect any other modules. |
Net Change Amount |
The sum of the Standard Amount column.
|
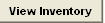 |
The following screen will be displayed, showing the currently available inventory information for the line item highlighted.
|
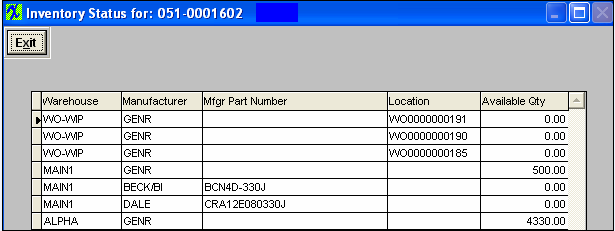
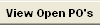 |
The following screen will be displayed, showing current Open PO for the line item highlighted: |

AVL Information |
For the highlighted line item |
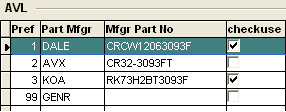 |
Pref |
This is a number indicating the preference for use |
Part Mfgr |
Displays the Part mfgr. name |
Mfgr Part No |
Displays the Part mfgr. part number |
Checkuse |
This box will be checked if this Mfg. and Mfg. Part number may be used |
Reference Designator |
For the highlighted line item |
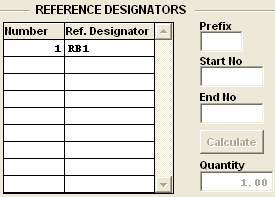 |
Number |
The number assigned to the reference designator.
|
Ref. Designator |
The alpha numeric characters assigned to the Reference Designator number.
|
Prefix |
The character assigned to all of the reference designator numbers.
|
Start No |
The first Reference Designator number.
|
End No |
The last Reference Designator number.
|
Calculate (button) |
The button used to calculate the Reference Designator.
|
Quantity |
The new quantity for which Reference Designators have been assigned.
|
|
1.5.3.3. Update/Create Records Tab |
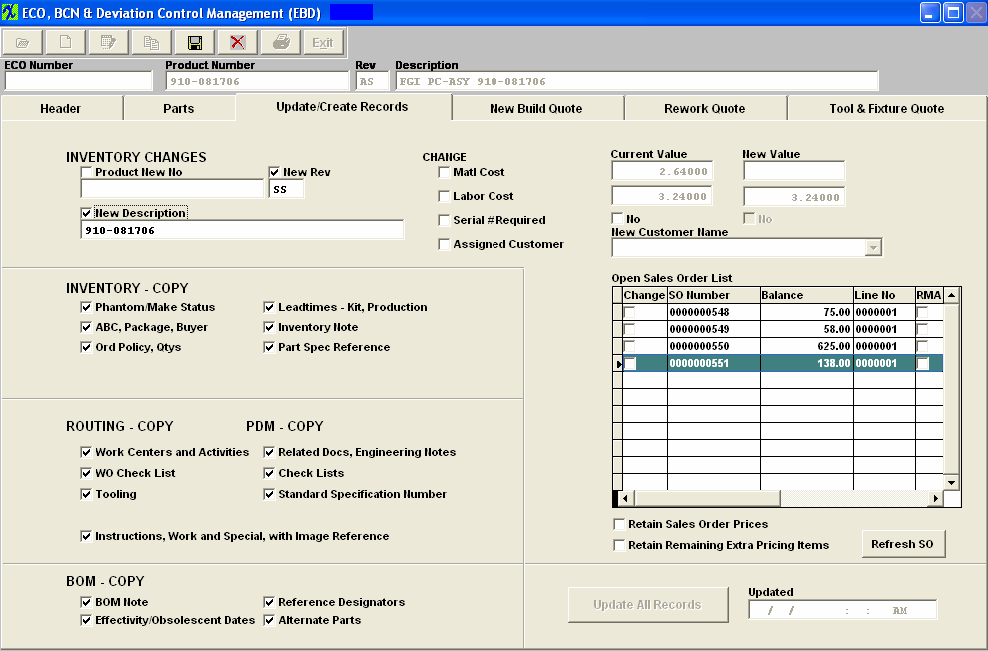
Update/Create Records Tab Field Definitions - This tab displays the revised product number, description, changes in Standard Cost, Labor Cost, whether serial number is required and updates for Engineering Change Orders only. Note: This tab is not available for Deviations or BCN.
Inventory Changes section:
Product New No: |
If the check box is checked, a new product number may be entered here.
|
New Rev: |
If the check box is checked, the new revision character may be added here.
Note: that either a new Product No or Rev has to be entered in order for the system to allow the user to save the ECO record – this check has been added to prevent any duplicated inventory records within the system. See Article #3062 on why the customer part number or revision is not updated at the same time.
NOTE: When product is changed through ECO module the same material type will be carried fwd for the next/new product at the part level but not at the AVL level.
|
New Description: |
If the check box is checked, a new description may be entered.
|
Change section:
Matl Cost |
If this box is checked, the material cost for the product will be updated based on the changes made within the Parts Section and the inventory part standard cost. |
Labor Cost |
If this box is checked, the new Labor cost for the product will be updated based on information entered within the ECO New Build Labor Cost section. |
Current Value |
The mat'l or labor cost currently existing for the product within the Inventory Control Module. |
New Value |
The revised mat'l or labor cost for the product. |
Serial # Required |
If box is checked, user then has the option of checking the "YES" or "NO" box to the right for this part to be a serialized part or not. |
No/Yes |
If the serial box is checked you have an option to check Yes or No to require the revised product to be a serialized part or not. NOTE: This box will remain NO until checked then it will update to YES. |
Assigned Customer |
This will allow the user to Assign a new Customer to the BOM. NOTE: This field is only editable if there are NO open Sales Orders or Work Orders linked to this product. |
New Customer Name |
If the Assigned Customer box is checked, user may select a customer from the pull down.
Note: Customer name can be changed on the BOM for the product only if either the Product number or revision and the product has no consigned parts for another customer nor any make/phantom parts that are assigned to another customer, and the product is not a sub-assembly for another product.
|
Open Sales Order List |
Shows all SOs (with any status except for cancel) and RMAs with this assembly number, Balance and item number. The selected SOs and RMAs will be updated with the new Product number and/or Rev number and/or Description shown upper left corner.
Note: If there have been no items shipped against the sales order selected then the system will just replace the existing product with the new within the Sales Order.
If shipments have been made against the item the old line item will be have the Ord Qty updated to equal the total Shipped and the status changed to Closed.A new line item will have been create for the new Product/Rev for the remaining balance that was left on the original item.
|
Retain Sales Order Prices |
Check this box only if you want the Unit Price to remain the same. |
Retain Remaining Extra Pricing Items |
Check this box only of you want the extra pricing to remain the same. Note: If you don't check "Retain Sales Order Prices"checkbox, then for either part itself or extra price item, no price will be updated. The "Retain Remaining Extra Pricing Items" is for adding extra items only, for the "price" column, it's still controlled by "Retain Sales Order Prices" checkbox. |
 |
“Refresh SO” button has been provided so the user can refresh the Sales Order list to check for any new SO created in the system since the ECO was first created.
|
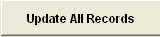 |
This button is depressed to update all records within the system based on the selections made. |
The rest of this screen comes up with all of the boxes checked for copying the revisions into the Inventory Master, Production Routing, Product Data Management and Bill of Materials. If the user does not want the assembly copied, the box will be unchecked.
|
1.5.3.4. New Build Quote Tab | 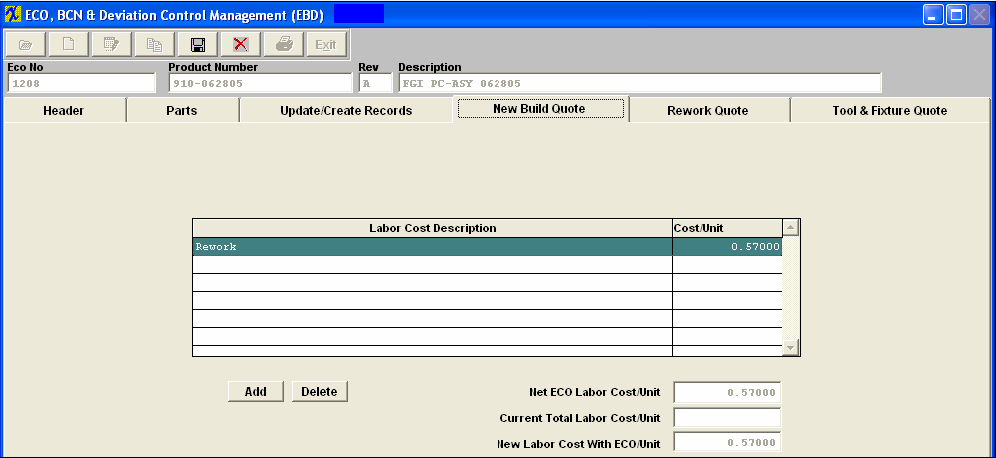
New Build Quote Tab Field Defintions - This tab desplays Labor Costs associated with the build of the new product number and revision and calculates the New labor Cost associated with each new unit.
Labor Cost Description |
Description of the labor. |
Cost/Unit |
Cost of the Labor |
Net ECO Labor Cost/Unit |
Sub of the total Labor costs. |
Current Total Labor Cost/Unit |
This is the total Labor information pulled from the Inventory Control Management module for the Product. |
New Labor Cost with ECO/Unit |
This is the sum of the new Net Labor and the Current Labor. | |
1.5.3.5. Rework Quote Tab | 
Rework Quote tab Field Definitions - The Rework Quote tab details any Rework Costs due to reworking the existing quantity in Work In Process and/or Finished Goods Inventory.
Open Work Order List (As of ECO Open Date) window: Note: The value of the "as of" is that it can affect the quote pricing and allows customers to better get that information.
Change |
A check in this column indicates that the Work Order will be revised to the newly changed product number/revision. The system will automatically update the Work Orders to the newest revision number. If a kit is in process for the WO selected user MUST depress the "Update Kit" button within the kitting module after the ECO is approved for any part changes to be reflected. NOTE: When the ECO takes place and the WO record is updated SFT losses the transfer history for the old revision and starts over with only xfer history for the new revision from that point on. See Article #3401 for further detail.
|
Work Order |
Shows all WOs (with any status except for cancel) with this assembly number,. The selected WOs will be updated with the new Product number and/or Rev number and/or Description shown upper left corner.
|
Balance Qty |
This field indicates the quantity remaining in the specific Work Order. |
Due Date |
Due date from WO. |
Status |
Status of WO. |
Total of Selected WOs |
The sum of all of the Balance Quantity column, above.
|
 |
Refresh WO button has been provided so the user can refresh the Work Order list to check for any new WO's created in the system since the ECO was first created. The value of the "refresh" is they can refresh after it was created if they created it several days before the quote is ready. |
Rework Cost Description window:
Rework Cost Description |
This is a description of the rework cost line item.
|
Cost/Unit |
This is the cost per unit pertaining to the description on the left.
|
Total Rework Cost/Unit |
The sum of the cost/unit column above.
|
Inventory Locations (As of ECO Open Date) window: Note: The value of the "as of" is that it can affect the quote pricing and allows customers to better get that information.
Warehouse |
The name of the warehouse where the completed product is stored.
|
Location |
The name of the location (such as Row 13, Bin 3) within the warehouse above.
|
Quantity On Hand |
The quantity within that location.
|
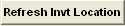 |
Refresh Invt Location button has been provided so the user can refresh the Invt Location list to check for any new Locations created in the system since the ECO was first created. The value of the "refresh" is they can refresh after it was created if they created it several days before the quote is ready. |
Total |
(As of ECO Open Date)The total of Finished Goods Inventory. Note: The value of the "as of" is that it can affect the quote pricing and allows customers to better get that information
|
The window at the bottom right hand side of the tab will display the total costs associated with the rework. Note that these costs DO NOT forward into either the Inventory Control Item Master nor the Accounting records.They are not associated with any new products which will be manufactured after the update to the latest revision, but pertain only to the costs associated with reworking either existing WIP or Finished Goods.
Totals (As of ECO Open Date): Note: The value of the "as of" is that it can affect the quote pricing and allows customers to better get that information
Qty in WIP |
This is the quantity in WIP which is available to be reworked.
|
Qty in FGI |
This is the quantity in FGI which is available to be reworked.
|
Units to Rework:
Qty in WIP |
This is the quantity in WIP which is available to be reworked.
|
Qty in FGI |
This is the quantity in FGI which is available to be reworked.
|
Cost to Rework:
Qty in WIP |
This is the quantity in WIP which is available to be reworked.
|
Qty in FGI |
This is the quantity in FGI which is available to be reworked.
|
Total Cost to Rework Selected Quantity |
This is the sum of the two above amounts.
|
|
1.5.3.6. Tool & Fixture Quote | 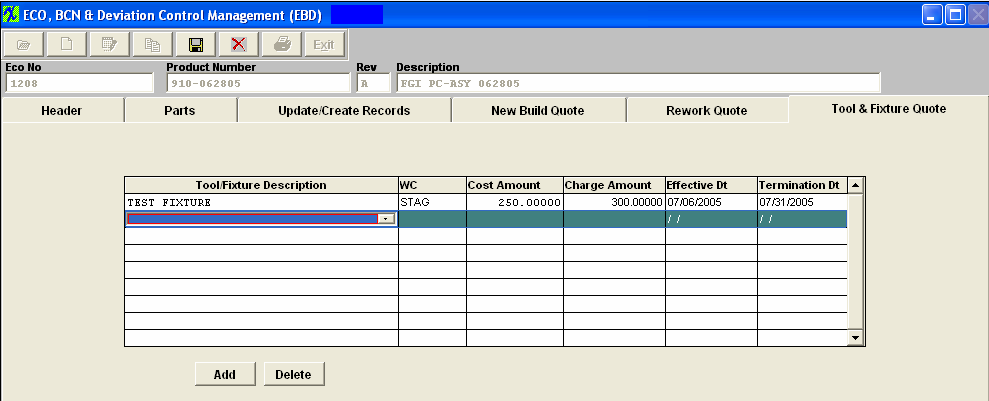
Tool & Fixture Quote Field Definitions - Once the ECO record has been approved and updated within the system. This Tool/Fixture information will then be carried forward into the PDM and Routing Setup modules.
Tool/Fixture Description |
This is the description information loaded form the System setup/Tooling Setup for selection. |
WC |
Work Center |
Cost Amount |
Original Cost of the Tool/Fixture |
Charge Amount |
The amounted that is planned to be charged for the Tool/Fixture |
Effective Date |
Date that the Tool/Fixture becomes effective. |
Termination Date |
Date that the Tool/Fixture will be terminated. | |
1.5.4. How To .... for EBD |
1.5.4.1. Find An Engineering Change Order(ECO), BOM Change Notice(BCN), or Deviation |
Enter Quality/Engineering/ECO, BCN & Deviation Control Management (EBD) Module |
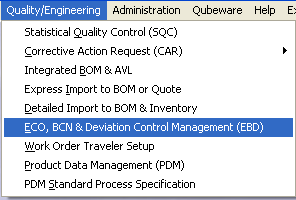 |
The following screen will appear:
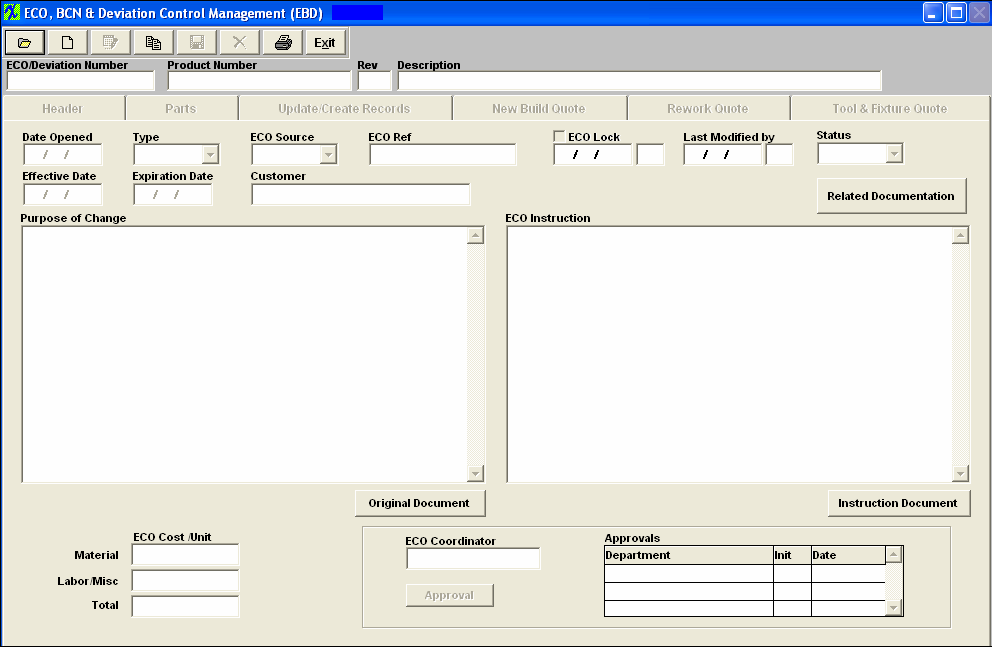
Depressing the Find action button will bring up a selection screen.
Select the appropriate radial for the find.
|
|
If you select ECO/Deviation No or ECO Reference No radial, then type the desired number into the box. Once you depress the enter key the system will pull up the matching record onto the screen.
If the system does not find a match to the information entered then the following message will be displayed.
Answer Yes, and then the system will display a listing of available ECO records to choose from.
|
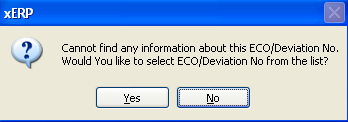 |
If you select to find by Product No, type the product number into the box. If there is more than one Engineering Change Order, a list of all Engineering Change Orders for that product will appear: Highlight and double click on the ECO/Dev No desired.
If you select to find by Status, a further selection will appear. Choose between New, Edit, Approved, Cancelled or Completed by clicking on the appropriate radial. A list of all of the Engineering Change Orders falling within that category will appear. Highlight and double click on the appropriate record.
Information regarding the ECO, BCN, or deviation, will appear.
|
1.5.4.2. Edit an ECO, BCN or Deviation | Find an existing ECO, BCN or Deviation. The information will populate the screen.
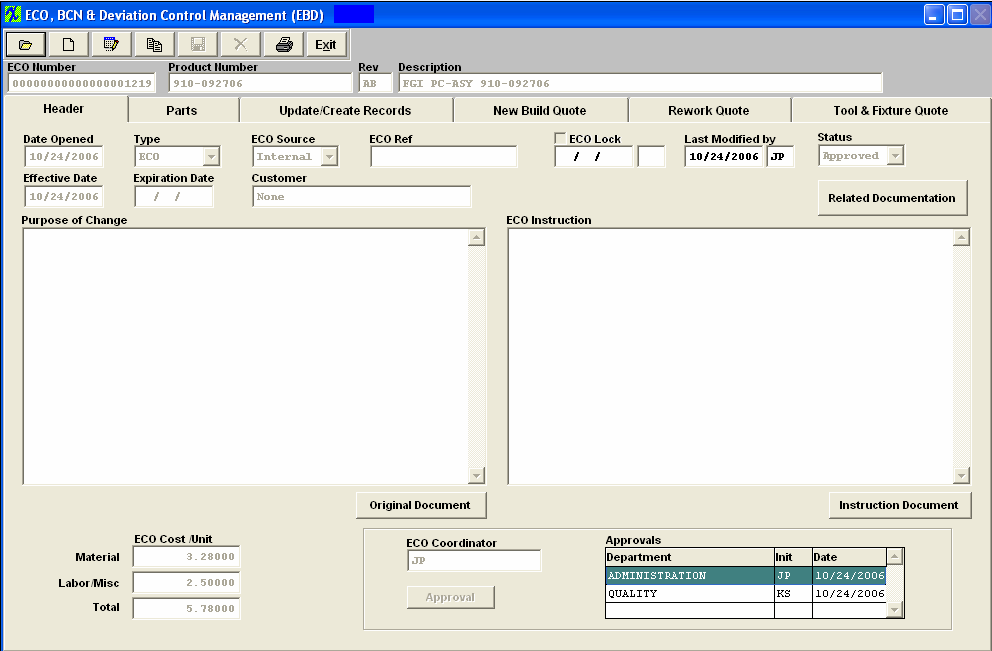
Depress the Edit record action button. Status will change to Edit.
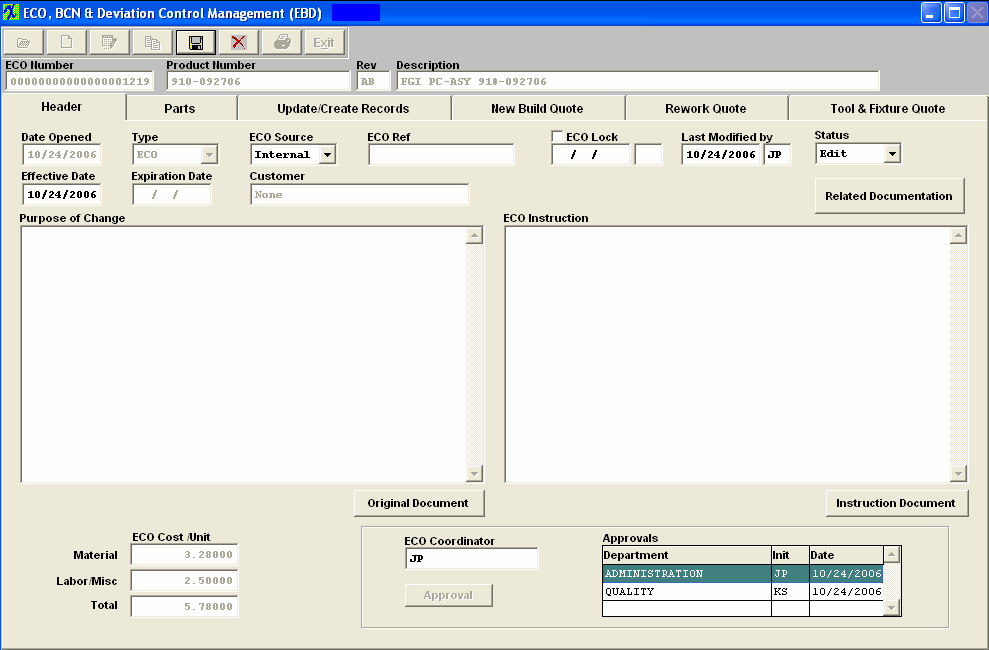
Once the necessary changes have been completed depress the Save record action button to Save changes, or depress the Abandon changes action button to abandon changes.
If the Save record action button is depressed, changes will be saved. The following screen will appear. NOTE: The Approvals will be removed and the ECO changes will need to be re-approved.
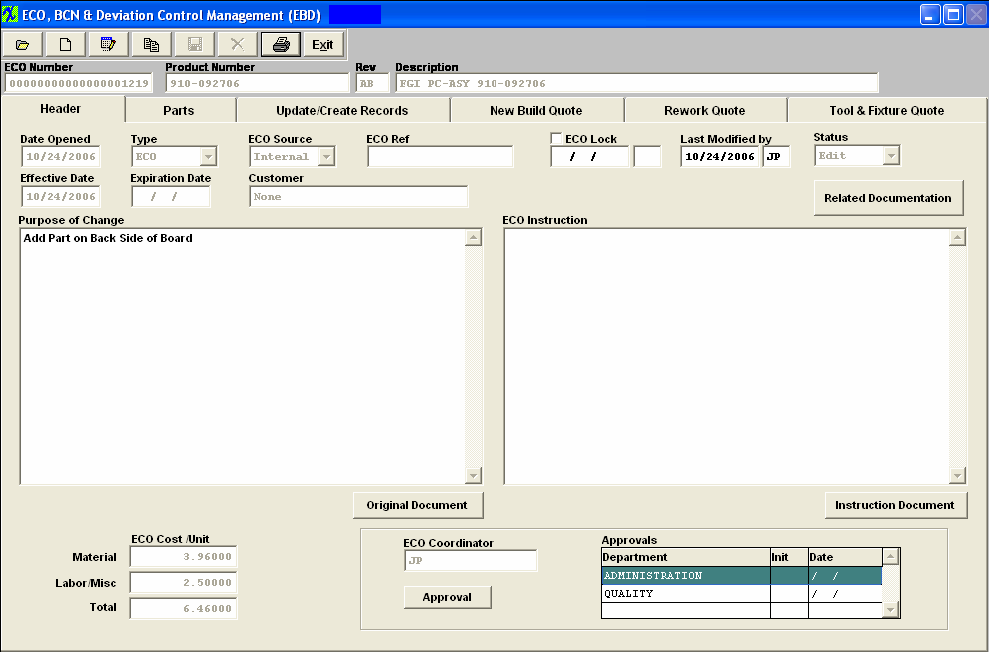
The changes will need to be Approved, before the ECO status will change back to Approved. |
1.5.4.3. Adding A New ECO, BCN, or Deviation |
To add a new ECO, BCN, or Deviation within the system, open the ECO,BCN, & Deviation Control Management (EBD) module. |
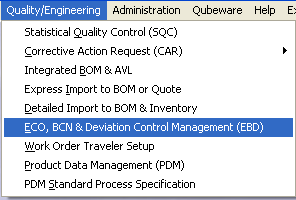 |
The following screen will appear.
Depress the Add Record Action button. Enter your password. The following selection screen will appear.
|
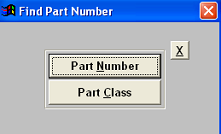 |
If you decide to find an existing Part Number, depress that button.
The following selection screen will appear:
Type the part number into the red box or highlight it and double click.
|
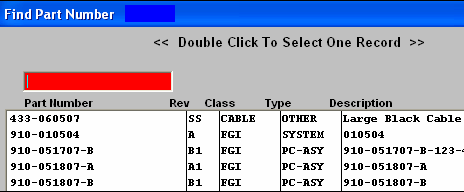 |
If you decide to find the Part Number by Part Class, depress that button.
The following selection screen will appear.
Type the Part Class into the red box or highlight your selection and double click.
|
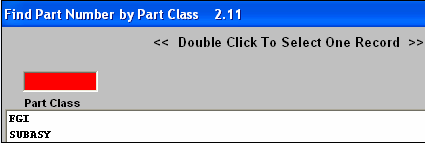 |
From there a list of all product numbers within that class will appear.
Type the Part Number into the red box or highlight your selection and double click.
|
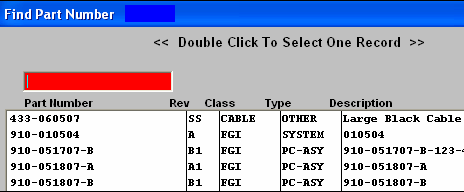 |
Information pertaining to that part number will appear on the screen, as follows:
Select the type of change by depressing the down arrow next to the Type box.
An ECO selection is for a permanent change to the Inventory Master, Bill of Materials and Product Data Management (normally a revision added). NOTE: These records will ONLY be updated if the Revision or Part Number has been changed.
A Deviation selection is for a one time change to existing Finished Goods Inventory and/or Work In Process. A selection of Deviation will not update no records; such as Inventory Master, Bill of Materials or Product Data Management.(The Update/Create Record tab will be grayed out.) This is a document for reference only.
A BCN selection is to change all part information just like an ECO, but user won't be able to create a new product number/rev, or click any "copy" checkboxes on "Update/Create records" page. WO and SO lists will also not be available for selections.
|
 |
Select the ECO Source by depressing the down arrow next the the ECO Source box.
|
 |
Type in the ECO Reference.
Enter in the Effective Date. (Note: This date MUST be prior to the WO Due Date to be applied).
Expiration Date field is only enabled when creating a deviation.
Type in the purpose of the change and Description of change.
Type in the name of the ECO Coordinator.
The screen will appear as follows:
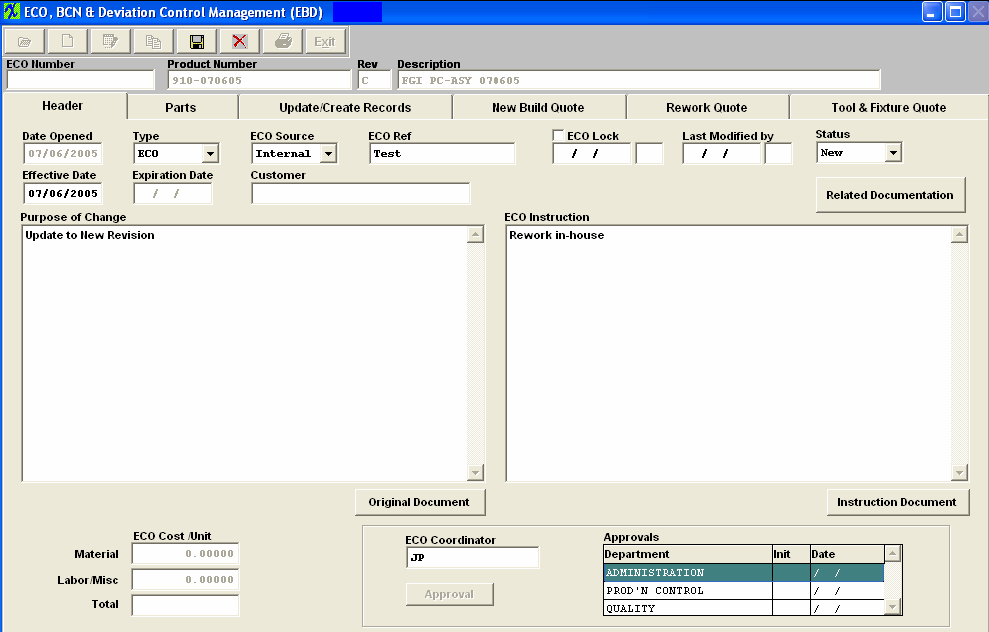
PARTS TAB
Enter the Parts screen
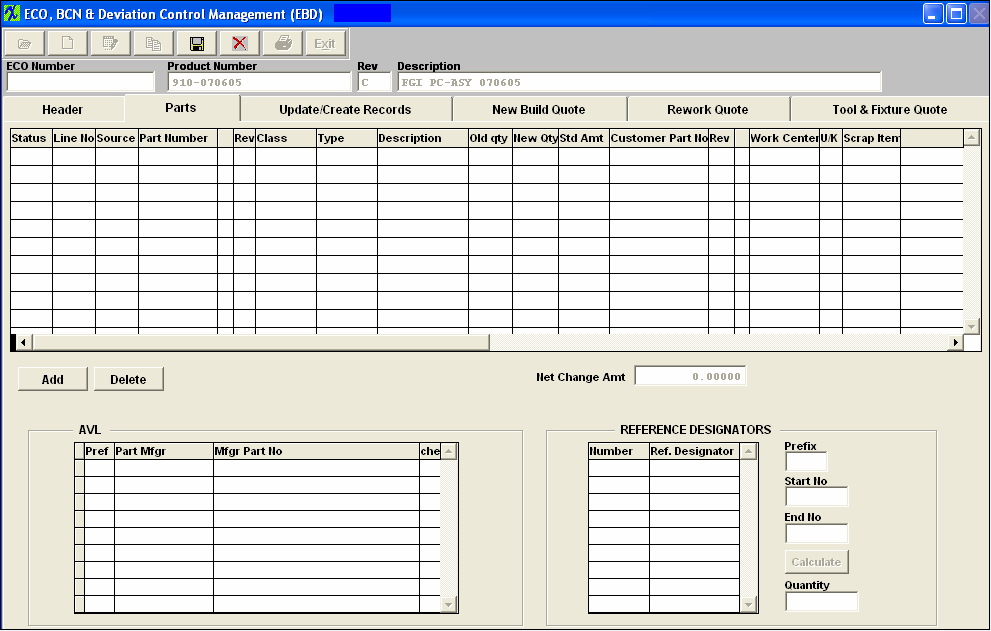
To record an ADD to an ECO record
Depress the Add Button.
The system will then default to the Status field. Depress the down arrow next to the Status field.
The following choices will appear.
Select Add from the Status listing.
|
 |
Enter in the new Line No that it will be listed as on the BOM.
Select Source by depressing on the down arrow next to that field.
The following selection will appear:
|
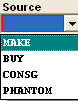 |
Type in the Part Number. The Revision number, Type, Class, Description, and AVL information will update automatically. If the part added has a status of "Inactive" within the Inventory Control Management, it will be highlighted in purple as an indicator to the user that this item is inactive at this time. If the user chooses to leave the inactive part on the ECO, that part number record status will automatically be changed to Active upon the "Update Records" button being depressed, so user will not have inactive parts listed on the BOM. The user will receive a warning that an XLS file has been created for reivew.
Type in the new quantity to be used in the assembly.
Type in customer part number and rev. if applicable.
Scroll over to the right and choose the Work Center by clicking within the Work Center field. The following selection screen will appear.
|
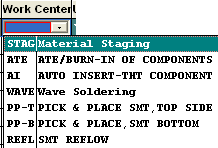 |
The system will default into the U/K field, for the component to be included in the kit. You have the option to change this entry to one of the following Yes, No, or Free Stock.
If the user attempts to enter any other characters into this field they will receive the following warning message.
|
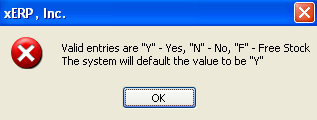 |
Type in the Reference designator(s), enter the character in the prefix box. Indicate the Start number. Depress the Calculate button. The Reference Designator will update.
You will then be able to view the Inventory Locations for the highlight part number, by depressing the View Inventory button.The following information will be displayed:
|
|
You will also be able to view any Open PO for the highlighted part number, by depressing the View Open POs button.The following information will be displayed:
|
 |
The AVL info will default in from the Inventory Control module. You may check or uncheck the approved AVLs. If the program finds duplicate part numbers in a BOM, any Alternate part number associated with the original line item will be carried fwd to the new item using the same part. As far as the AVLs, the program will get all unchecked AVLs from all items and to update all items. For example, BOM item #2 have AVL A,B,C, and D, only C is unchecked. Now in ECO, user adds item #5, it has AVL A unchecked. And if item #2 had a alternate part associated with it, that ALT part will also be carroed fwd to Item #5. We have added a message in the updating routine, if the system does find duplicate Part number, then a message will popup and let the users know then system will take the actions explained above. |
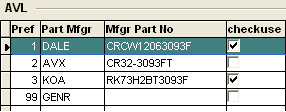 |
To update the Reference designator, enter the character in the prefix box. Indicate the Start number. Depress the Calculate button. The Reference Designator will update.
To record a DELETE to an ECO
Depress the Add Button.
The system will then default to the Status field. Depress the down arrow next to the Status field.
The following choices will appear.
Select Delete from the Status listing.
|
 |
Type in the Bill of Material line Item, that you wish to have removed from the BOM.
The screen will then update with the information pertaining to that item.
Leave the New Quantity as zero.
If you do not want the part scrapped, scroll to the right and remove the check mark from the Scrap Item field.
To record a CHANGE to an ECO
Depress the Add Button.
The system will then default to the Status field. Depress the down arrow next to the Status field.
The following choices will appear.
Select Change Qty from the Status listing.
|
 |
Then type in the Bill of Material line Item, that you wish to have changed on the BOM.
The screen will then update with the information pertaining to that item.
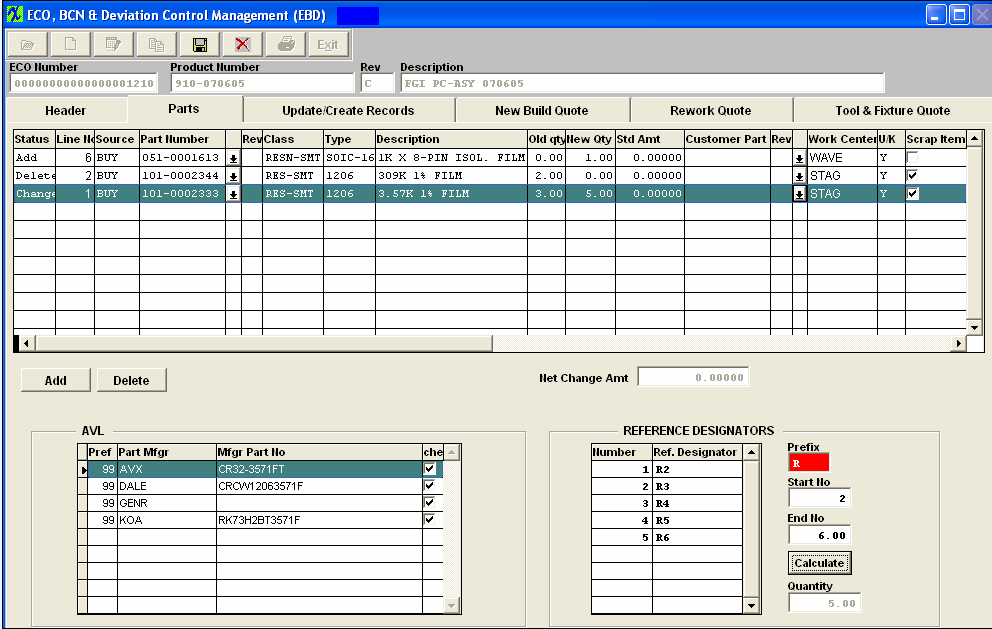
Type in the new quantity.
Update the Reference Designator information.
In the U/K field, change to if you do not want the change to be used in the kit.
If you do not want the item scrapped, remove the check mark from the Scrap Item box.
If you want to change the Work Center where the component is added, depress the down arrow next to the Work Center field. The following selection screen will appear
Make your selection.
|
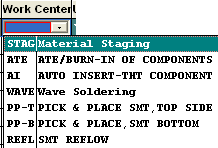 |
UPDATE/CREATE RECORDS TAB
Enter the Update Records screens.(Note:that if the type was selected as Deviation within the Header screen, then the Update Records screen will be grayed out and unavailable for selection)
Inventory Changes Section:
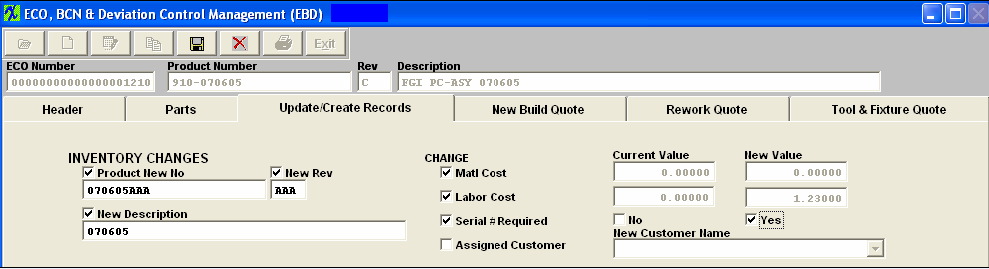
Check the applicable box and then Type in a new product number, revision number, or new description, if desired. NOTE: The BOM will NOT be updated if no new Product Number or Revision as been created.
NOTE: For the purpose of many users wanting to create several ECOs for the same product number without really updating the records (meaning creating a new part in inventory) Manex will allow you to save and approve the ECO even if they have not selected to create a new Part or Rev within the system. Upon depressing the Update Records button the system will check to see if New Product No or New Rev has been marked, if left blank then the system will just update the status of the ECO to Complete without creating a new product number in the system.
NOTE: When product is changed through ECO module the Material Type will be carried fwd to the next/new Product/Rev that is being generated at the part level, but will not carry fwd the material type at the AVL level. The system will default in "UNK" as the Material Type for the AVL Level.
If you want to update the Material Cost, then check mark the box next to Matl Cost. The new Value field will update based on the changes made within Parts screen.
If you want to update the Labor Cost, then check mark the box next to Labor Cost.The New Value field will update based on the changes made within the New Build Quote screen.
If you want to require a serial number, then check mark the box next to Serial # Required. Then go to the box under the New Value column it will remain NO until checked then it will update to YES.
If you want to change or assign a customer, check the Assigned Customer box. Depress the down arrow to see a list of customers. Select the customer of choice.
Note: Customer name can be changed on the BOM for the product only if either the Product number or revision and the product has no consigned parts for another customer nor any make/phantom parts that are assigned to another customer, and the product is not a sub-assembly for another product
NOTE: This field is only editable if there are NO open Sales Orders or Work Orders linked to this product.
|
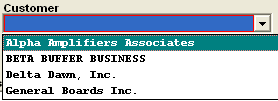 |
If user is attempting to assign a new customer to a product with any Open Sales Orders or Work Orders linked to it they will receive one of the following messages and will NOT be able to save the ECO. |
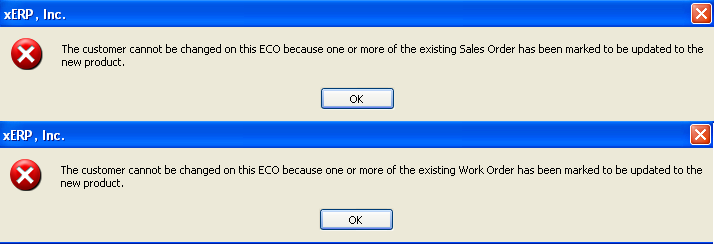 |
In the ECO process of modifying or adding Parts to the ECO, there is a field which contains the Customer Part number, if available. At the present time, this field is empty and non-editable for changing or deleting a part from the BOM. But if the user wishes to add a part, they may do so by entering in either the internal part number or the customer part number in the customer part number field, and the program will locate the corresponding internal part number and enter it. The search is based on the customer part number entered AND the customer associated with the BOM from which the ECO was originated.
Because Manex allows users the ability to use the ECO module to create New Part Numbers via the ECO process, and even assign a new customer to the new part number, we must limit the customer information to that of the original customer, as we cannot determine at what point the reference should change customers, or even if it should. Furthermore, if the user does elect to create a new part number for a new customer, items unchecked on the AVL will transfer to the new bom (if checked on the update sheet). However, there may be a conflict between the AVL of the original customer and the AVL of the new customer, so the user is urged to verify the AVL content of a new bom for a new customer created with this module.
COPY SECTIONS:
Look at the items all ready checked to be copied. If you do not want the items copied, uncheck them.
Note: When creating new Product within Inventory via ECO change the new Product's AVL will be auto assigned with the Material Type of "Unk". It will not keep the MT from the original Product the ECO was originated from.
|
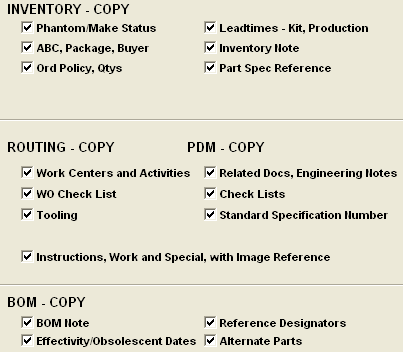 |
OPEN SALES ORDER LIST:
The Open Sales Order List will include all open Sales Orders including the ones that are flagged as "Admin Hold" and//or "Mfgr Hold", and any open RMAs against this product.
In the Open Sales Order List, check mark within the Change box column if you want the Sales Order and/or RMA to be changed.
Note: If there have been NO items shipped against the sales order selected then the system will just replace the existing product with the new product and/or revision within the Sales Order.
If there have been shipments made against the item the old line item will have the Ord Qty updated to equal the total Shipped and the status changed to Closed. A new line item will have been created for the new Product/Rev for the remaining balance that was left on the original item.
If you do not want the price changes to affect the sales order prices check the "Retain Sales Order Prices" box. If you would like to retain any extra charges against the line item check the "Retain Remaining Extra Pricing Items" box.
Refresh SO button has been provided so the user can refresh the Sales Order list to check for any new SO created in the system since the ECO was first created.
|
|
The completed screen will appear as follows:
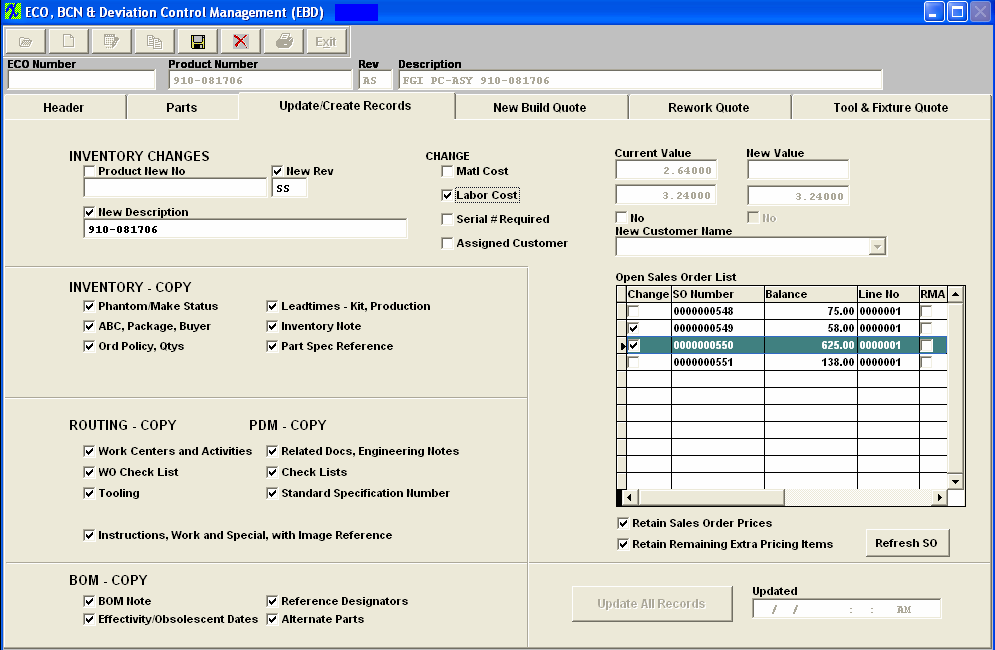
NEW BUILD QUOTE TAB
Enter the New Build Quote screen.
To add a new Labor Cost associated with the new revision, depress Add the button. Type in the Labor Cost Description. Type in the new revision cost per unit. Continue to Add as required.
The completed screen will appears as follows:
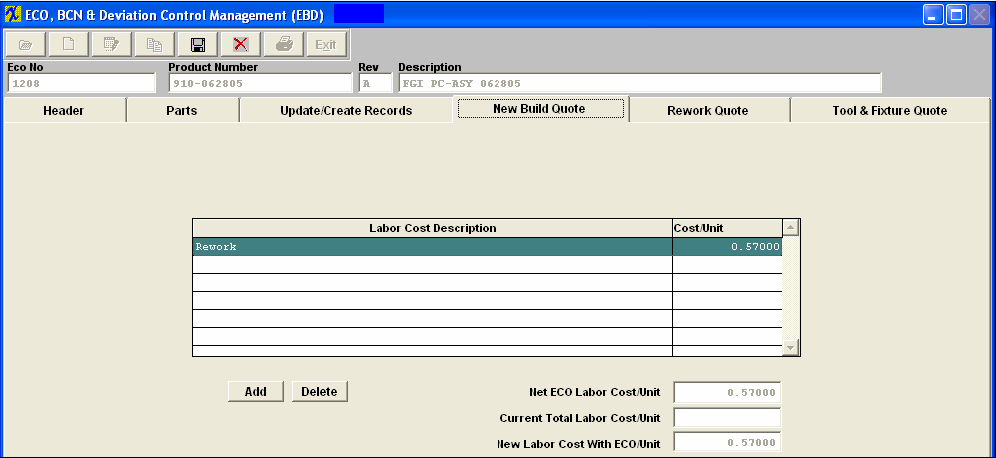
REWORK QUOTE TAB
Enter the Rework Quote screen.
In the Open WO List (As of ECO Open Date), check mark within the Change box column if you want the WO to be changed/reworked. The WO's checked will only be changed/reworked when creating an ECO. They will not be changed/reworked when creating a deviation. (This field is for reference only when creating a deviation).
You will receive the following message, as you check each box:

Depress the OK button to continue.
NOTE: When the ECO takes place and the WO record is updated SFT losses the transfer history for the old revision and starts over with only xfer history for the new revision from that point on. See Article #3401 for further detail.
If needed, you have the option to refresh the Work Order listing to see if any new Work Orders have been created for this product since this ECO was originally opened, by depressing the "Refresh WO" button.
To add costs solely associated with the rework of open Work Orders and/or Finished Goods Inventory, depress the Add button under the Rework Cost Description window. Type in the Rework Cost Description and the related cost per unit.
The Inventory Locations (As of ECO Open Date), will default in and is for reference only.
The Totals (As of ECO Open Date) will default in displaying the quantity in WIP and the quantity in FGI. The Units to Rework and the Cost to Rework will update automatically.
NOTE: If you use the ECO module to add a part to a BOM, and flag the ECO to update a work order in WIP, in order to process correctly through the GL, the following criteria must be met:
- The WO due date must be later than the ECO
- The ECO must have updated all records
- The Kit must be updated
- The changes in the BOM in the Kit must be attended to by either kitting new parts, unkitting deleted parts, or modifying quantities.
The WO in process will be updated with the new revision.
The completed screen will appears as follows:
TOOL & FIXTURE QUOTE TAB
To add new Tool/Fixture Information, depress the Add button below the section.
Then add the Tool/Fixture information from the pull down.
|
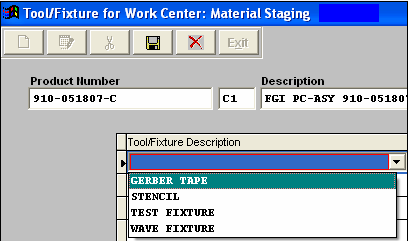 |
Choose the Work Center from the pull down. |
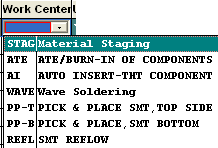 |
Fill in the cost amount, Charge Amount, Effective Date, and Termination Date.
Once the ECO record has been approved and updated within the system, this Tool/Fixture information will be carried forward into the PDM and Routing Setup modules.
The completed screen will appears as follows:
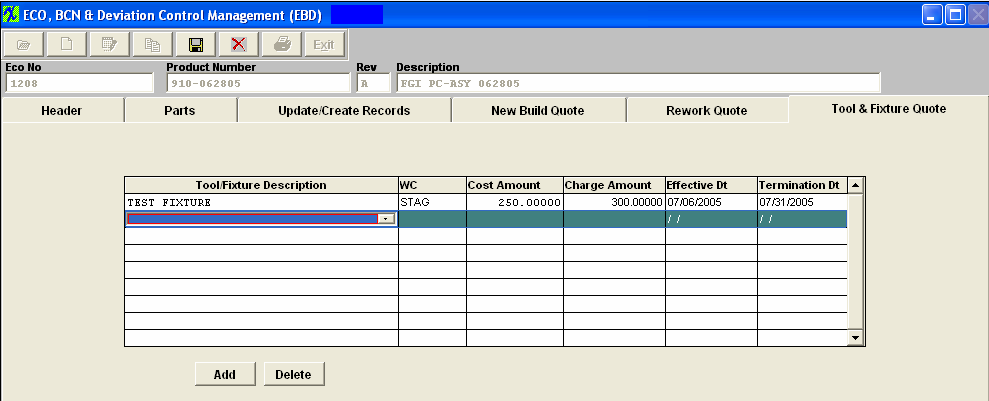
Depress the Header tab. Note that the ECO Cost/Unit columns have updated at the bottom left hand side of the screen:
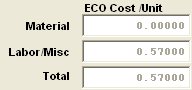
Depress the Save record action button or the Abandon changes action button.
Upon Saving the user may be given a message if one or more of the parts do not have the same number of reference designators as the new quantity within the ECO, or BCN. This is giving the users the option to print out a report to list these item or not.

If Yes is selected the report, ECO Report Incorrect number of reference designators will go directly to the default printer and the next message will be displayed.
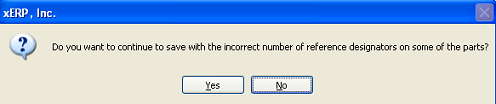
The user now has the option to cancel out of the save or continue.
The user should go back to the reference designators section for the part listed in the report and change the number of designators to equal the quantity required.
The Approval button will be available. Depress the Approval button.You will be prompted for the appropriate department password. Continue this process until all of the departmental approvals have been entered, as displayed:
|
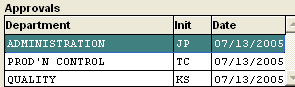 |
Once all of the Approvals have been fulfilled then within the Update Records tab the “Update All Records" button will become available.
Depress the Update All Records button. The records you selected will update. The ECO or BCN will now show with the following Updated time stamp.
Note: For a new revision, P/N, etc., go into the Inventory Master and if desired, update for the Warehouse location in the Quantity Information tab (the system will copy the warehouse information from original Product selected). Also, update for Mfgr Part Spec.
Adding A New ECO Deviation Record
Overview:
The difference between the ECO and the Deviation is: A Deviation is a method to document and approve a temporary change from the normal operation until an ECO is created to replace the Deviation, it is only a record that someone approved a change in some method for a work order(s). That is the reason the Deviation has an Expiration Date field in the main page and it will not update any active modules, part number change, rev change, description change or anything else. Whereas, ECO is a permanent change and change the part number, or rev or description, or standard cost, or anything thing else including updating any or all active files.
The basic procedure of processing a Deviation follow basically the same rules as a Regular ECO except for the Update Records button is disabled.
Enter the ECO module. Depress the Add Record action button Select the desired product number. Then for the Type Select Deviation
|
|
Once Deviation has been selected as the Type, continue on and enter in the remaining Deviation information as explained in the Adding ECO section above. Note: For a Deviation you MUST make sure you complete the expiration date so users know that it is for a limited period of time. If this field is left blank the deviation will NOT be displayed in the SFT module.
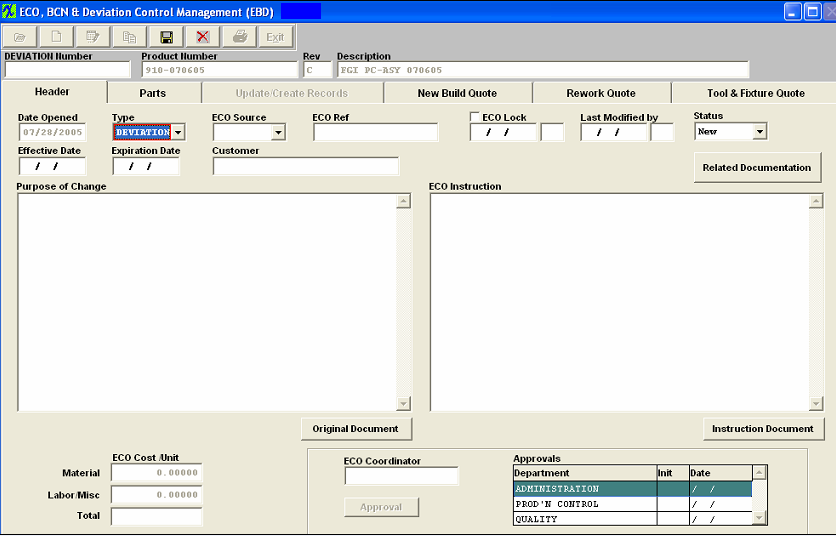
Note: The Update Create Records tab will remain grayed out and unavailable for any Deviation records entered within the system.
Once the Deviation has been completed the normal list of Approvals need to be entered.
The status of the Deviation record will update to Approved.
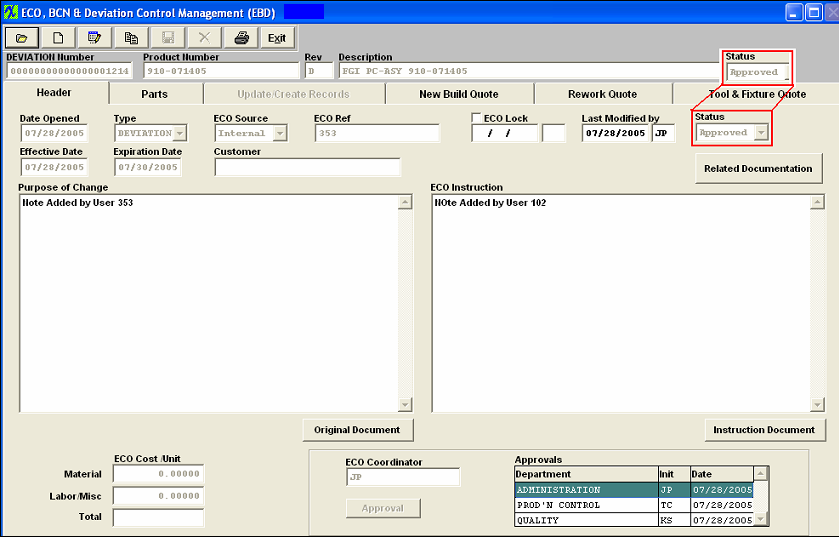
Changing the status of a Deviation from Approved to Completed.
The Status of a Deviation will remain as Approved in the system until the users manually changes the status to Completed. Once the status of a deviation has been changed from Approved to Completed it will no longer appear in the SFT (Shop Floor Tracking) module.
Find the desired Deviation record. |
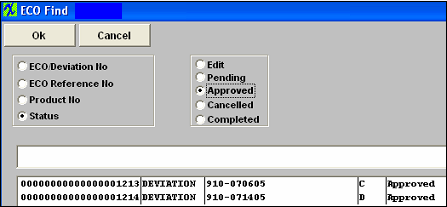 |
Depress the Edit record action button. Click on the down arrow next to the Status field, the following selections will be available for Deviations.
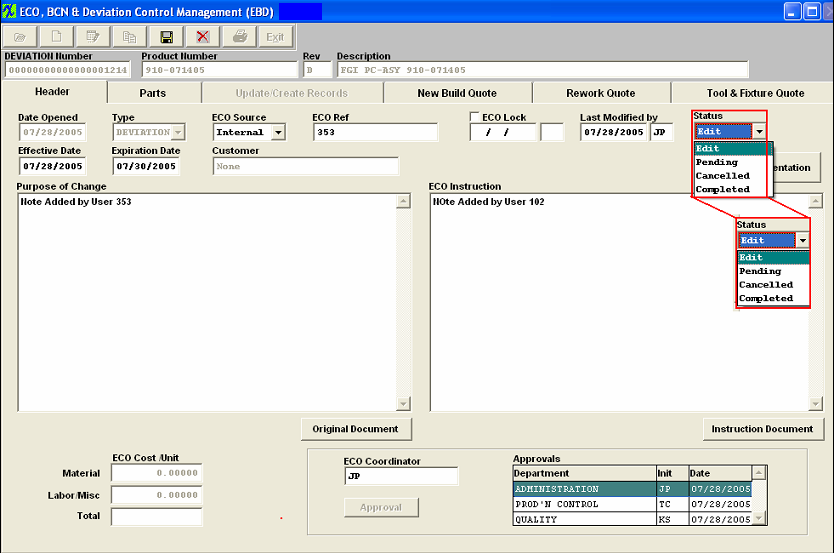
Change the status to Completed. Depress the Save record action button to save the changes the changes, or depress the Abandon changes action button.
The Deviation will now show in the listing of completed Records.
|
1.5.4.4. Copying An Engineering Change Order | Enter the ECO module. Find an existing ECO record within the system.
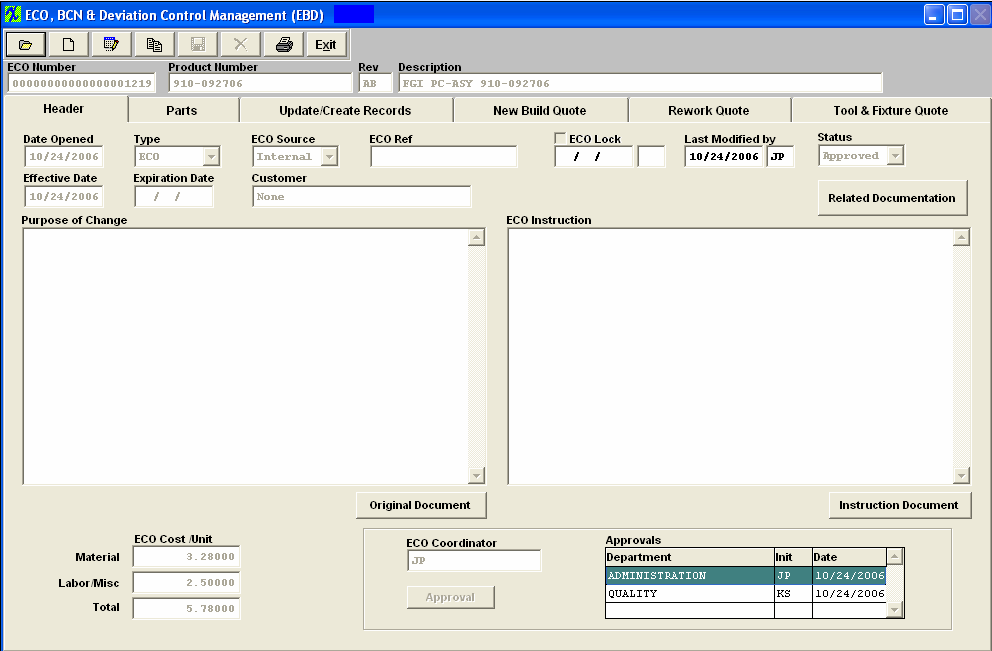
Depress the Copy Record action button. The following message will be displayed.
Select Yes, enter your password. Then the next message will be displayed.
|
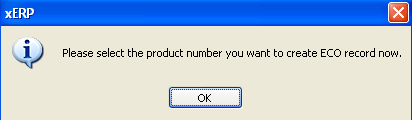 |
The following selection will appear. Depress Part Number. |
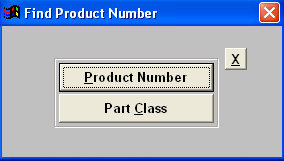 |
The following Part List will be displayed. Select the desired part number.
|
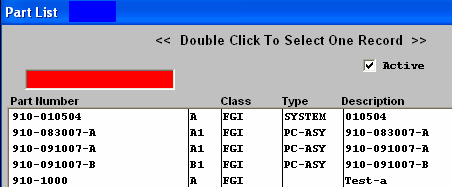 |
Once you have selected the desired product number the following will be displayed.
|
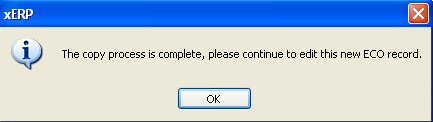 |
The following information will be copied fwd from the original ECO to the new ECO record.
- ECO Type
- ECO Source
- Customer
- ECO Coordinator
- New Build Quote Information
|
1.5.5. Reports - EBD |
To print out reports, depress the Report button. The following screen will appear:
|
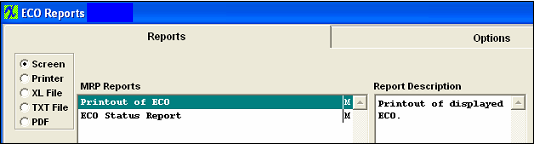 |
PRINT OUT OF ECO REPORT
Select the Printout of ECO report and then selecting the Option tab. The following screen will appear:

The ECO record that is open within the ECO module will default in – but the user does have the option to enter in a different ECO # record if desired.
The ECO Printout Report will appear as follows:
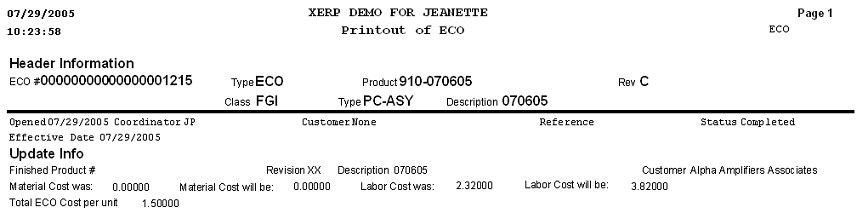
ECO STATUS REPORT
If you highlight the ECO Status Report and then depress the Options tab, the following screen will appear:
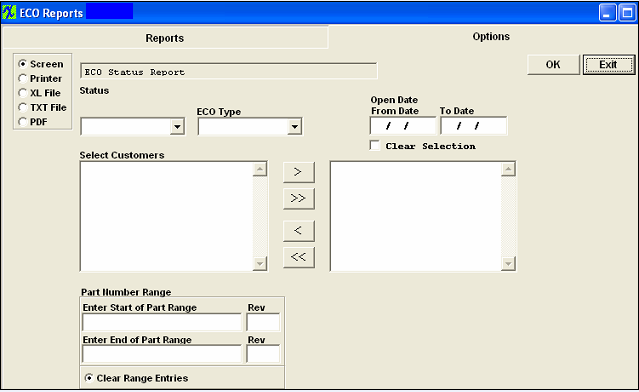
Select the status by pressing on the down arrow next to the window. Highlight the desired status.
Select the ECO Type.
Type in the From and To Dates.
Select the applicable customer(s) by highlighting and depressing the > arrow.If you want all of the customers, depress the >> arrow.
Note that you have to have a Customer selected in order for this report to work. If the ECO record does not have a customer selected, then it will not appear on this report.
If you want a part range, type in the beginning and the ending part numbers.
Depress the Ok button. The following ECO Status Report will appear as follows:
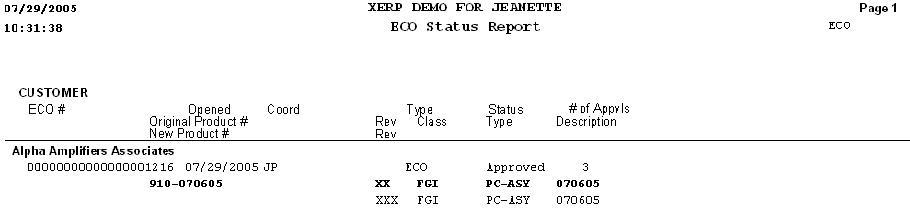
|
1.5.7. ManEx Minutes for (EBD) |
1.6. Work Order Traveler Setup |
1.6.1. Prerequisties for WO Traveler Setup |
After activation, "Product Routing" access for each user must be setup in the ManEx System Security module. Users with “Supervisor Rights” will automatically have access.
|
1.6.2. Introduction for WO Traveler Setup | The Work Order Traveler Setup module is used to define the details of the Production Work Order Traveler Setup for a product. Certain work centers are “hard-coded” into the ManEx program. These are Material Staging, Finished Goods, MRB and Scrap. These work centers may not be modified by the user, or omitted from a Work Order Traveler Setup, because they are associated with special codes that are essential to our system.
For example: "STAG" is the first step so when a Work Order is created the material can go into Staging.
"FGI" when material is moved into finished goods a number of thing happen within the system, (1. Receiving into the inventory; 2. accounting transaction WIP to inventory, etc.)
"SCRP" and "MRB" - if material is moved into scrap or MRB some GL transactions are associated with the move.
They are the gateways to and from the Work Order Traveler Setup for WIP management.
|
1.6.3. Fields and Definitions for WO Traveler Setup |
1.6.3.1. Header | Work Center and Activities Routing Setup Header Field Definitions

Class |
This is the classification for the product.
|
Type |
This is the type within the classification. |
Part Number Rev |
This is the internal part number and revision for the product. |
Per Pnl/Sht |
If the user wishes to move material by the panel, sheet or roll, they may select “Default to PANEL” as the method of tracking quantities in the Shop Floor Tracking Defaults setup. This requires the user to define in the product definition the number of products contained in a panel/sheet/roll. Then, if this method is chosen, the user moves panels and ManEx keeps track of the number of units .If this is the case, the field will contain the number of panels associated with the product.
|
Serialize |
If this box is checked, the product will be subject to serialization.
|
Description |
This is the description of the product.
|
Status |
The status of the product, either Active or Inactive.
|
Current Work Center |
The name of the Work Center highlighted.
|
Traveler Released |
Check this box when ready to release Traveler/WO and the date, time and users initials will be recorded at that time. Note: Users MUST have special rights within the Security module to modify this field. Users with “supervisor’s rights” will automatically have access. |
|
1.6.3.2. Work Center Tab |
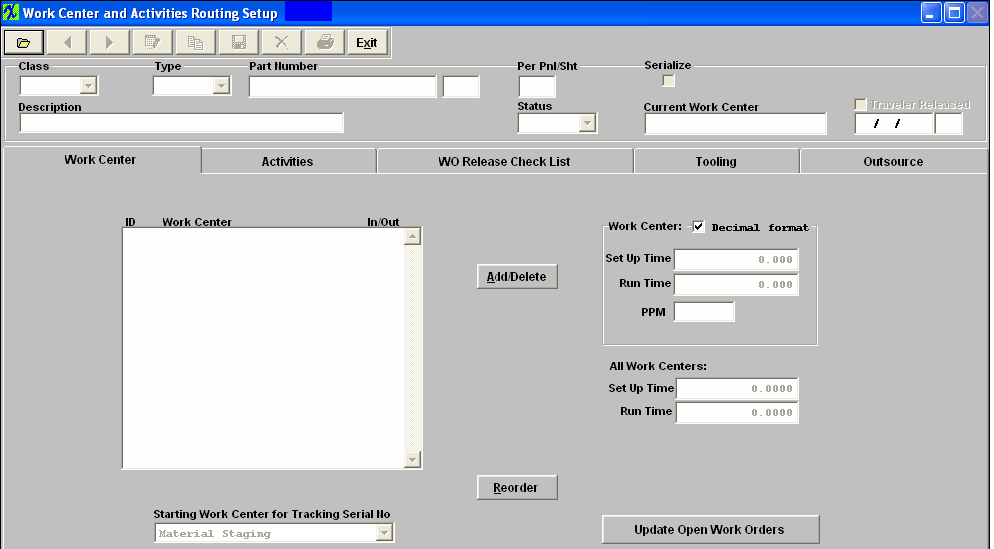
Fields and Definitions
ID |
The ID established for the work center.
|
Work Center |
The name of the work center.
|
In/Out |
The indication if the work center is to be processed Inside or Outside the company.
|
 |
This button allows the user to "Add" or "Delete" a Work Center to the routing for this product.
|
Work Center Decimal Format |
If this box is checked the setup time and run time is set to decimal format (1.575 hours). If this box is unchecked the 1.575 hours is converted to 1:34:30.000. So with the decimal field unchecked you can put in hours, minutes, and seconds. Note: To add Times in Routing, the run and set up times must be selected in Production Scheduling Method module.
|
Setup Time |
The set up time for the work center selected. If there are activities present and the user adds or edits the setup time on the activity level the WC setup time will be re-calculated from the activity level. |
Run Time |
The unit run time for the work center selected. If there are activities present and the user adds or edits the run time on the activity level the WC run time will be re-calculated from the activity level. |
PPM |
This is the number of defect opportunities that exist for an assembly in a Work Center. For more detail see Article #674 |
Setup Time |
(Total) setup time for all work centers and/or activities. |
Run Time |
(Total) run time for all work centers and/or activities. |
 |
Depressing this button will allow the user to reorder the routing for this product. |
 |
Once the routing is set, the user may use this button to update any Work Orders which were created before the routing was entered or changed. |
Starting Work Center for Tracking Serial No |
This field will display the name of the Work Center where Serial Number Tracking will begin, if the Serialize box is checked at the top of the screen. NOTE: If the starting work center is removed, when user clicks “Update WO” button, all the WC qty and SN (if any) except for FGI and SCRP work centers will be moved back to STAG work center because the system will treat the STAG as the starting tracking SN work center.
|
|
1.6.3.3. Activities Tab |
The activities tab is used to add specific activities that take place within a Work Center. For the Work Center which is highlighted within the Current Work Center field, the Activities Tab will change to RED text if activities have been assigned to that work center. Within the window, the 1st column is the abbreviation used for the activity and the 2nd column is the full activity for the Work Center listed. The list of activities are set up in System setup – Production Work Centers & Activities.

Fields & Definitions
Add/Delete |
This button is used to add or delete activities for the Work Center listed.
|
Reorder |
This button is used to reorder the list.
|
Setup Time
|
For the activity highlighted, this field is for the set up times. If user enters setup time at activity level the system will accumulate the times for all the activities (for that specific work center) and assign it to the WC level and overwrite whatever number if any entered there.
|
Run Time |
For the activity highlighted, this field is for the run times. If user enters run time at activity level the system will accumulate the times for all the activities (for that specific work center) and assign it to the WC level and overwrite whatever number if any entered there. |
|
1.6.3.4. WO Release Check List Tab |
The Work Order Release Check List tab is for the user to select check list items for the Work Center listed in the Current Work Center field. The Work Order Release Check List items are set up in the Shop Floor Tracking Default set up screen. These items will then be displayed within the Unreleased WO List for approval.
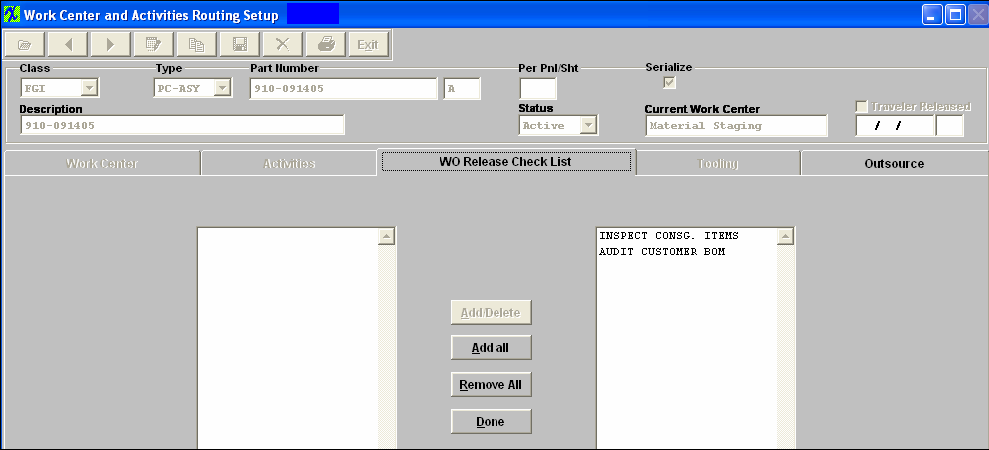
Fields & Definitions
Add/Delete |
This button allows the user to add or delete the check list items to or from the Work Center being displayed above.
|
Add all |
This button allows user to add all check list items (displayed on the right) to the current work center being displayed above. |
Remove All |
This button allows user to remove all check list items (displayed on the left) from the current work center being displayed above. |
Done |
Depress this button when you are done making changes. |
|
1.6.3.5. Tooling Tab |
The Tooling tab is used to describe the tooling requirements for the Work Center. It also provides for a location notation and an Expire Date. An example of a Check List item as discussed above might be to perform the Work Center tooling, as detailed in this tab.
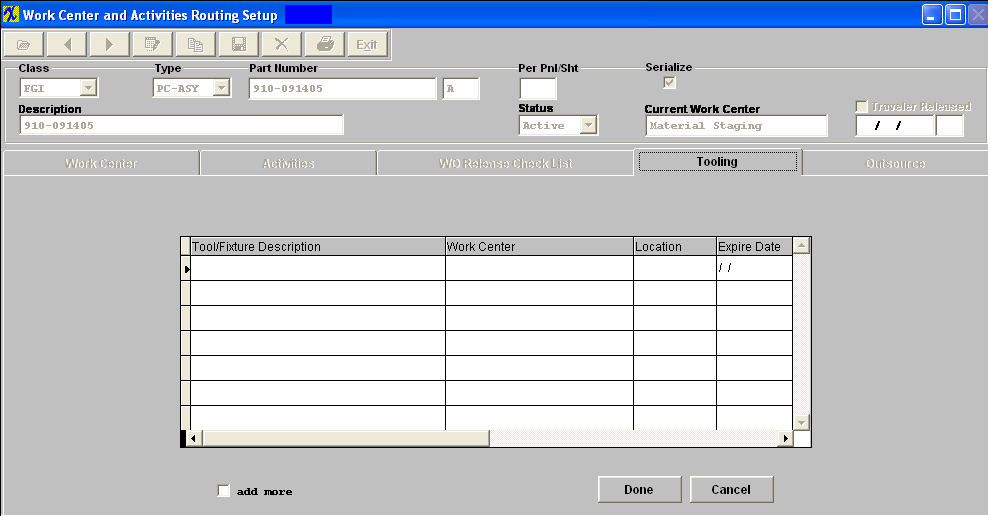
Fields & Definitions
Tool/Fixture Description |
This is the description of the Tooling item.
|
Work Center |
This is the name of the Work Center where the tooling will take place.
|
Location |
This is the location within the Work Center where the tooling will take place.
|
Expire Date |
This is the date of expiration of the tooling.
|
add more |
Checking this box allows the user to add additional tooling lines.
|
Add |
These buttons allow the user to add, edit or delete tooling items.
|
Edit |
The Tool/Fixture description pulldown information is setup within the System Setup/Tools Setup . The Tooling/Fixture information can also be added, edited, or deleted from the PDM (Product Data Management) module
|
Delete |
To delete a line item from the Tooling Tab. Highlight the line item. Depress the Delete button. Click on the second column (which is NOT labeled), the field will change to Black. Depress the Done button.
|
|
1.6.3.6. Outsource Tab | The Outsource tab shows the services to be performed outside of the user’s shop. These services are indicated with an “O” in the work center tab.
Within the window, the 1st column is the abbreviation used for the activity and the 2nd column is the full activity for the Work Center listed. The list of activities are set up in System setup – Production Work Centers & Activities Setup.
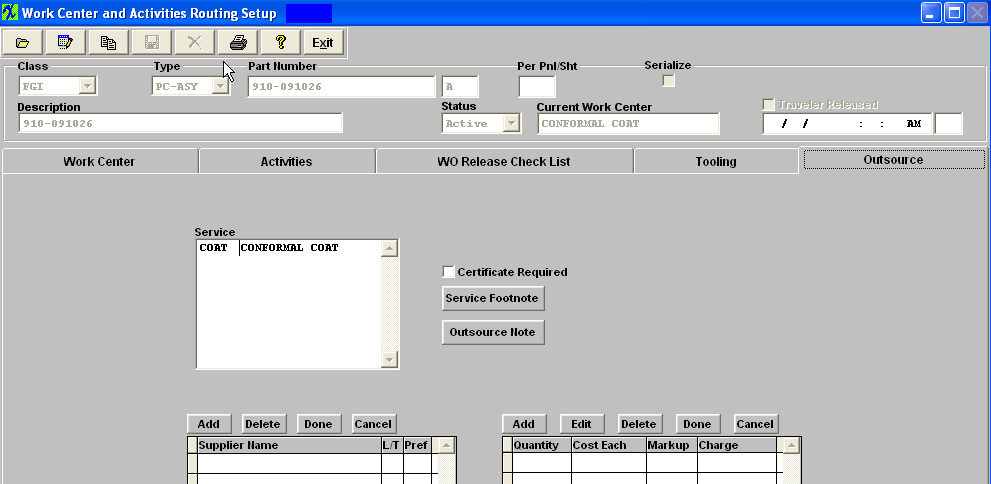
Certificate Required |
This box is checked if the outsource supplier is required to provide a certificate of completion. |
Service Footnote |
This button is for notes regarding Service. |
Outsource Note |
This button is for notes regarding Outsource. |
|
1.6.4. How To ..... for WO Traveler Setup |
1.6.4.1. Find a Work Order Traveler |
Highlight Quality Engineering/Work Order Traveler Set-up. |
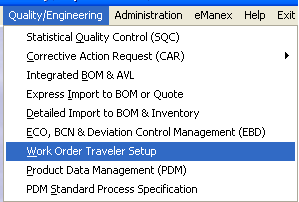 |
The following screen will be displayed:
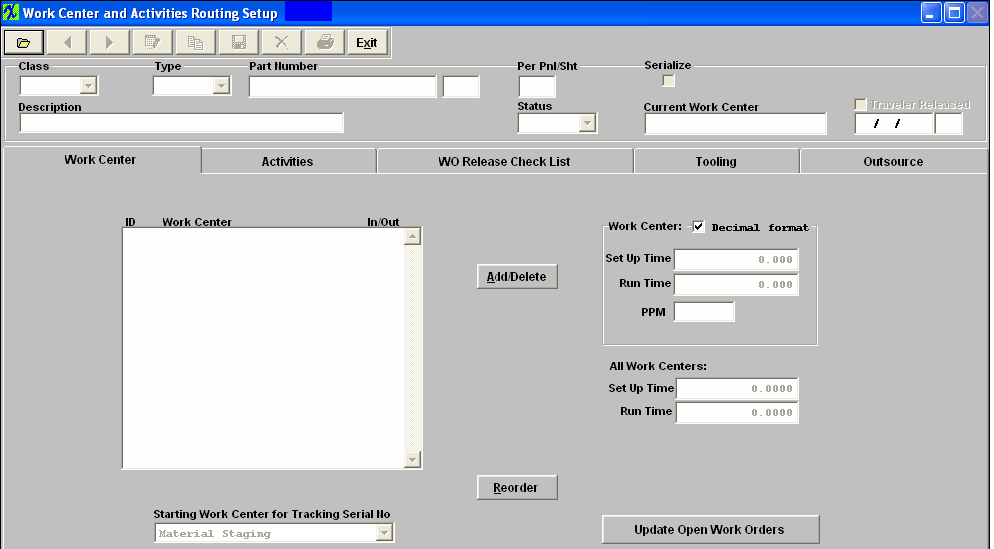
In this screen, a Work Order Traveler setup is either Created or Edited.
Depress the Find record icon, the following dialog box will be displayed: |
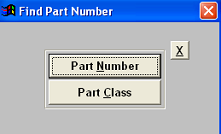 |
When the user elects to find a Product by the Part Number, the following screen will be displayed:
This screen will list available Part Number in numerical order, along with the Class, Type and Description.
The users selects the product by either entering it into the red box, or scrolling down the list and double-clicking on the desired part.
|
|
When the user elects to find a Product by the Part Class, the following screen will be displayed:
This screen will list the available part classes in Alphabetical order.
The user selects the Class by either entering it into the red box, or scrolling down the list and double-clicking on the desired class.
|
|
From this point, the “Find by Part Number” screen is shown, but only includes those parts in the selected class.
The user selects the desired product by either entering it into the red box, or scrolling down the list and double-clicking on the desired product.
|
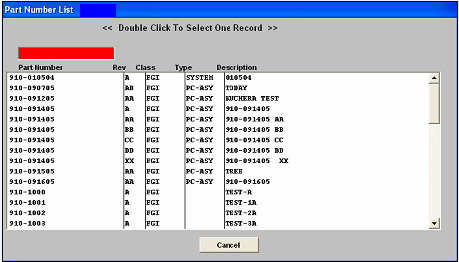 |
The following screen will be displayed with the data for the selected product.
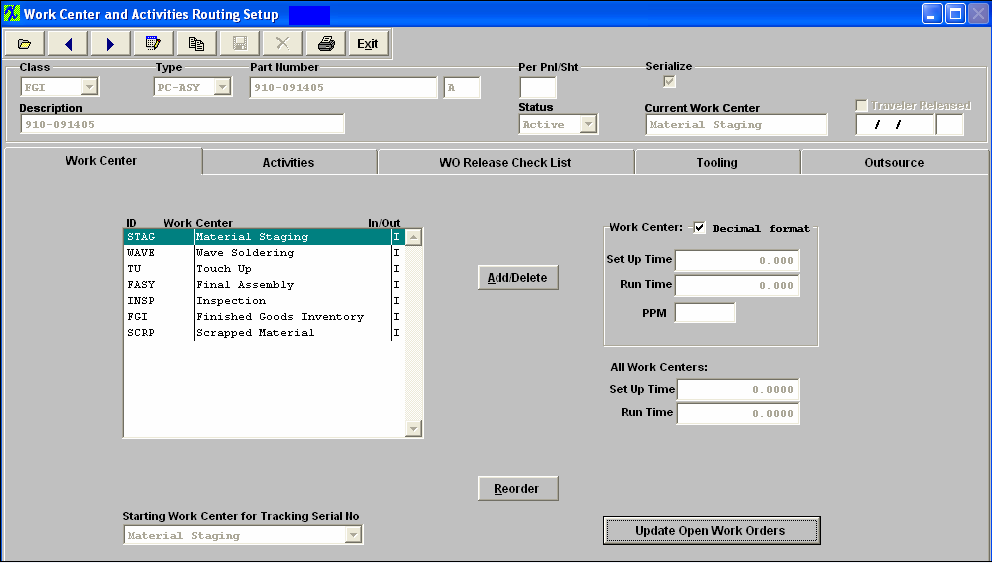
.
|
1.6.4.2. Setup/Edit a Work Order Traveler Routing | Add/Removing Work Centers
Find the desired Product number record.
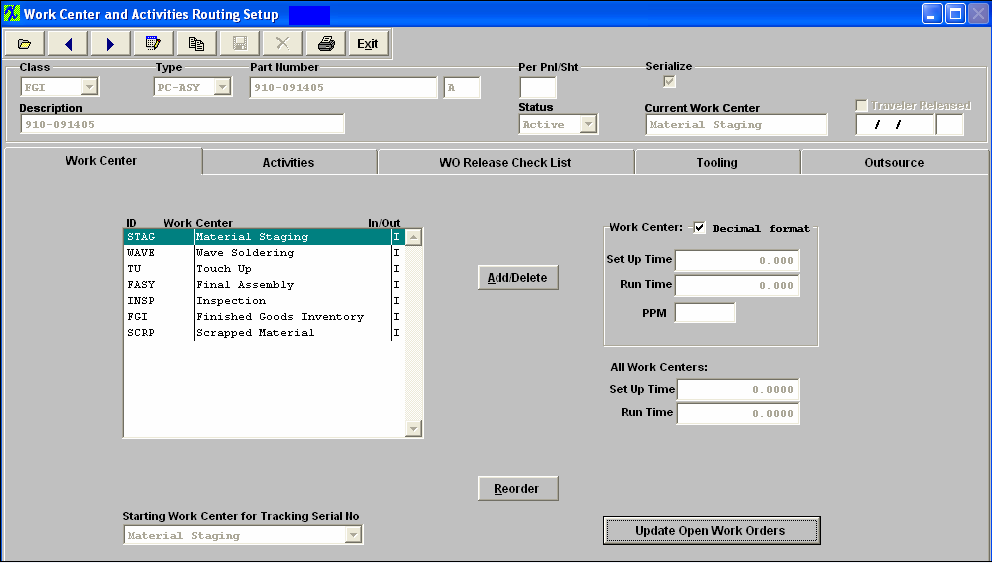
The "Add/Delete"button enables the user to add or delete work centers to the Work Order Traveler Setup. The screen then fills the right side with all of the standard work centers, and enables an Add All and a Remove All button.
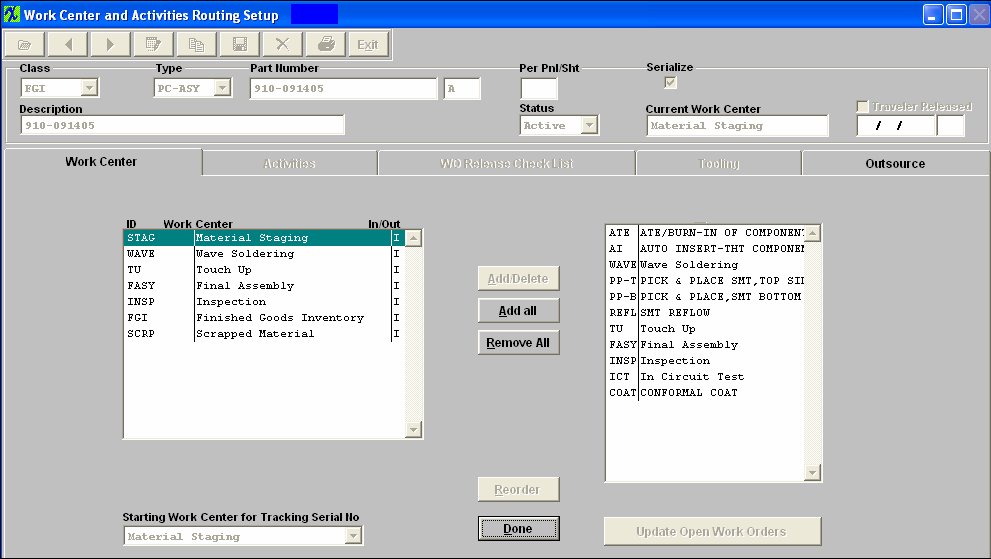
Work Centers may be moved to either side by double clicking on the side from which to move.
If the user wishes to add all work centers to the Work Order Traveler Setup, then remove a few unwanted ones, pressing the “Add All” button will transfer all work centers to the Work Order Traveler Setup. Likewise, pressing the “Remove All” button will remove all but the fixed work centers from the Work Order Traveler Setup.
Work Order Traveler Setups may be added more than once, to accommodate multiple visits to the same work area during production (e.g. test). Depress the Done button when the movement is completed.
The "Reorder" button allows the user to reorder the Work Order Traveler Setup in any order desired. Pressing this button will bring up ordering buttons on the left side of each work center in the Product Work Order Traveler Setup.
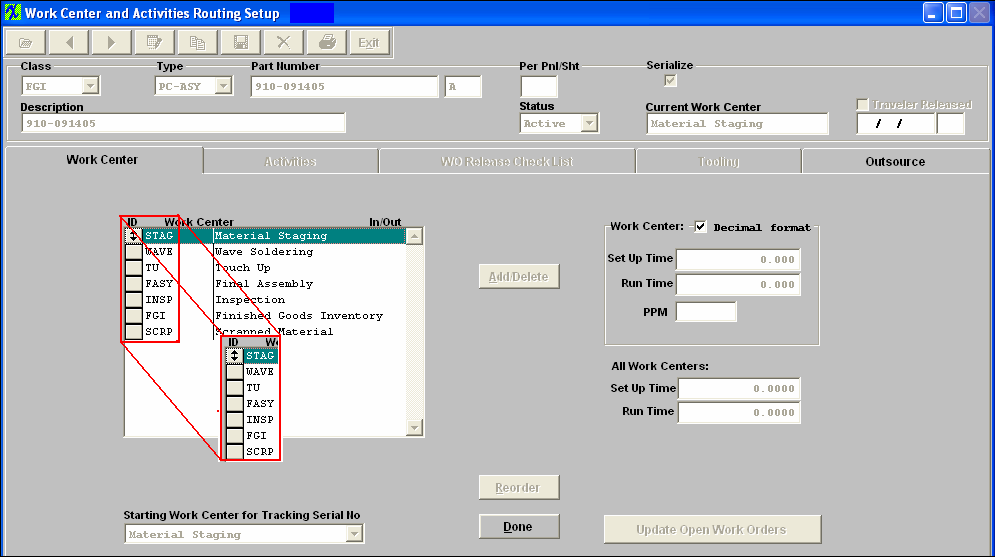
The user may then click on any of these buttons and drag a work center to the desired order.
Depress the Done button when the reordering is completed.
Update Open Work Orders
This button allows the user the option to update specific work orders which will then reflect the modified Work Order Traveler Setup. Otherwise, current Work Orders will NOT be updated, but future Work Orders created will carry the modified Work Order Traveler Setup. Depressing the button will bring up the following screen:
To select multiple items in the list, hold the Ctrl key down and click on those items you want to update.
Depress the OK button.
|
|
Editing the Run/Setup Times or Part Number Info
Find the desired Product number record.
Depressing the Edit Record button within any of the tabs will display the following dialogue box:
|
|
WC Run/Setup time
Selecting the WC Run/Setup Time allows the user to edit the Work Center data on the mid-right side of the screen and if the product is serialized it allows you to choose the Work Center to start tracking ther serial number.
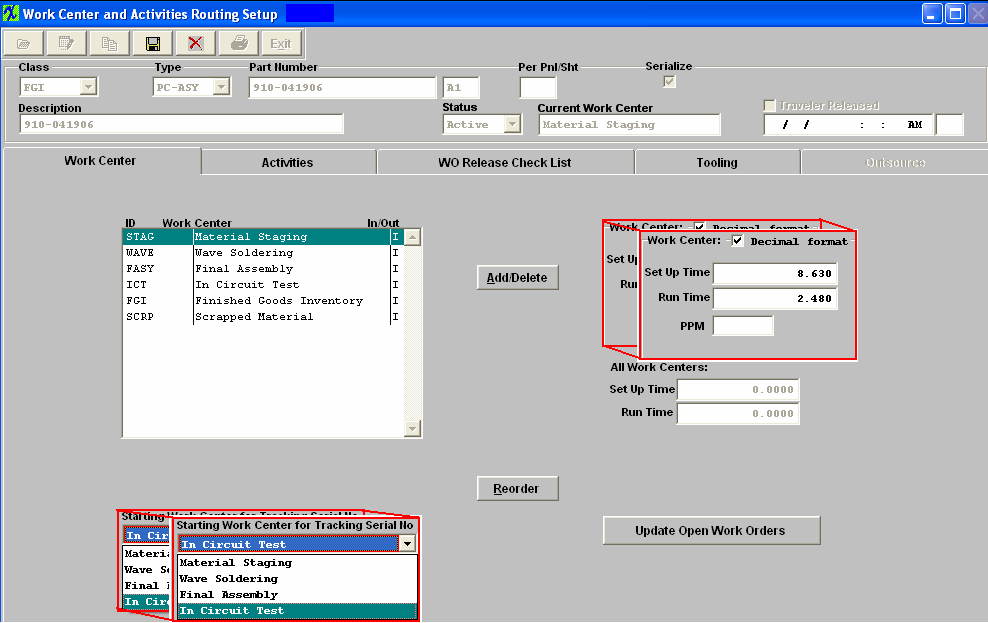
The user should place the cursor on the work center to be edited, then on the times to be edited. The user may modify one or more Work Centers, and then, after modification, the user must either Save or Cancel the modifications.
The area below this screen, labeled All Work Centers, will show the total times of all work centers and/or activities. This will automatically update.
Note: There are two different ways to track SETUP and RUN times for Job Costing and Product Data Management in ManEx.
1. By entering Run and Setup Times in the Work Order Traveler Setup under Production Planning.
2. By entering the Run and Setup Times in Activities Setup under the Work Center Setup.
Using the first choice is preferred when there is a great variability in the products produced and the setup and run rates in each work center. The second choice is preferred when the product flow is uniform, the machine rates are well established and the setup times very uniform regardless of product. The choice is made in the Production Schedule Setup module. Use of Run and Setup Times is optional unless Job Costing module is in use.
"Starting Work Center for Tracking Serial No" Choose from the pull down which Work Center you would like to begin tracking the Serial numbers. The system does not allow selection of "FGI" or "SCRP" as a starting WC for Serialization, because this will cause the system to become stuck bewteen SFT and Serial number assignment. NOTE: If the starting work center is removed, when user clicks “Update WO” button, all the WC qty and SN (if any) except for FGI and SCRP work centers will be moved back to STAG work center because the system will treat the STAG as the starting tracking SN work center.
Activity Run/Setup Time
Selecting the Activity Run/Setup Time will open up the Activities tab and then the system allows the user to edit the timing established for Activities associated with the work center.
If the Work Center has no activities assigned, the screen will remind the user accordingly. |
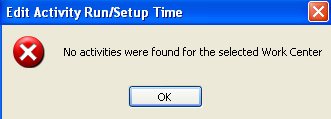 |
If there are activities associated with the work center, they may be edited on the lower middle of the Action screen.
Note: If user enters setup/run times at activity level the system will accumulate the times for all the activities (for that specific work center) and assign it to the WC level and overwrite whatever number if any entered there. If the user tries to change the WC setup/run times they will receive a warning that there are setup/run times at the activity level and these must be removed before they will be allowed to change the WC setup/run times. If the user decreases the activity setup/run times to 0 or remove the activity, then the user can add or edit the WC setup/run time.
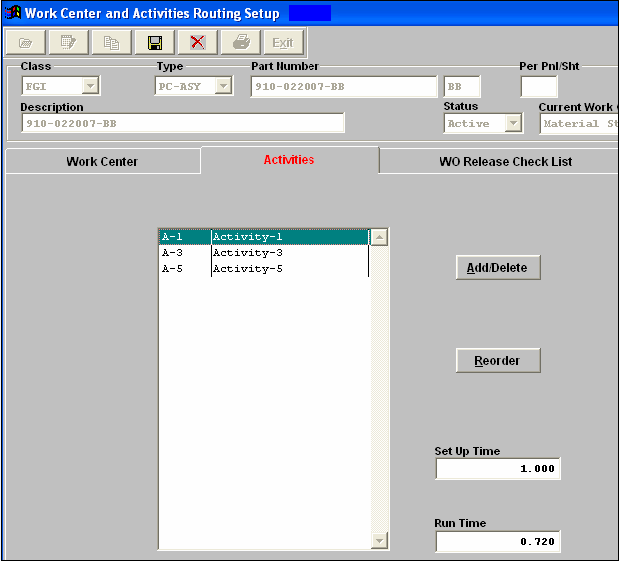
After modification, the user must either Save or Cancel the modifications.
Part Number Information
Selecting the Part Number Information allows the user to edit the part description, status, and/or per pnl/sht.
Note: Users MUST have special rights within the Security module to check the "Traveler Released" box. Users with “supervisor’s rights” will automatically have access. This box must be check when usiing the Unreleased Work Order List and the Work Center Checklist .

After modification, the user must either or Save or Cancel the modifications.
|
1.6.4.3. Copying a Work Order Traveler Setup | Find the desired Product Number, that you wish to have updated.
Depress the Copy Record icon. The following dialogue box will be displayed:
|
 |
Clicking on the down arrow at the Product Number box displays a listing of product numbers.
Clicking on the product number enters the number into the box. The user may elect to copy Routing Only or Routing & Instructions from the selected product by clicking on the appropriate radio button. The Setup Times/Run Times, for Work Centers and Activities, WO Release Check List, Tooling, and Outsource information will also be copied.
|
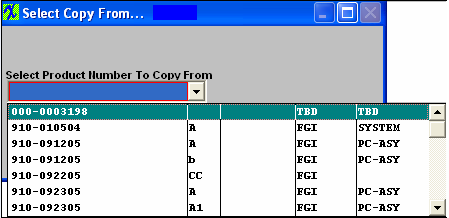 |
After verifying entries are correct, pressing the “OK” button will copy the Work Order Traveler Setups (and instructions) to the current product.
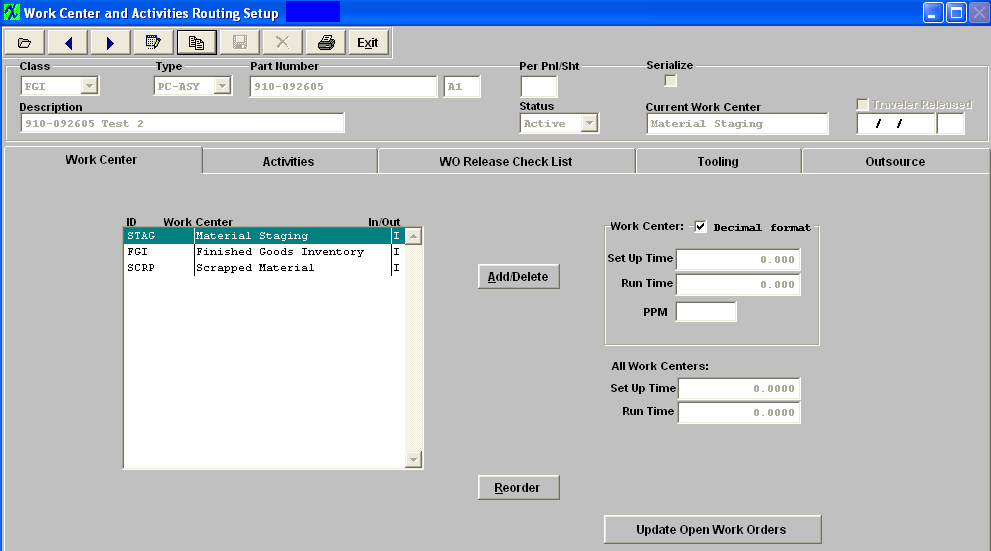
|
1.6.4.4. Setup/Edit Work Center Activities | Note that if a Work Center has activities associated with it, the “ACTIVITIES” tab will be showing in red font.
Add/Removing Activities
In the Activities screen, the user may add or modify activities used in a work center.
The activities must have been set up in the Production Work Centers & Activities module and be attached to the Work Center.
Find the desired Product number. Highlight the Work Center. Then enter the Activities screen.

The "Add/Delete" button will allow the addition or deletion of activities associated with the Work Center. The activities listed on the right side will show only activities associated with the work center in the system setup.
Make the desired selections. Depress the Done button.
The "Reorder" button allows the user to reorder the Work Order Traveler Setup in any order desired. Pressing this button will bring up ordering buttons on the left side of each work center in the Product Work Order Traveler Setup.
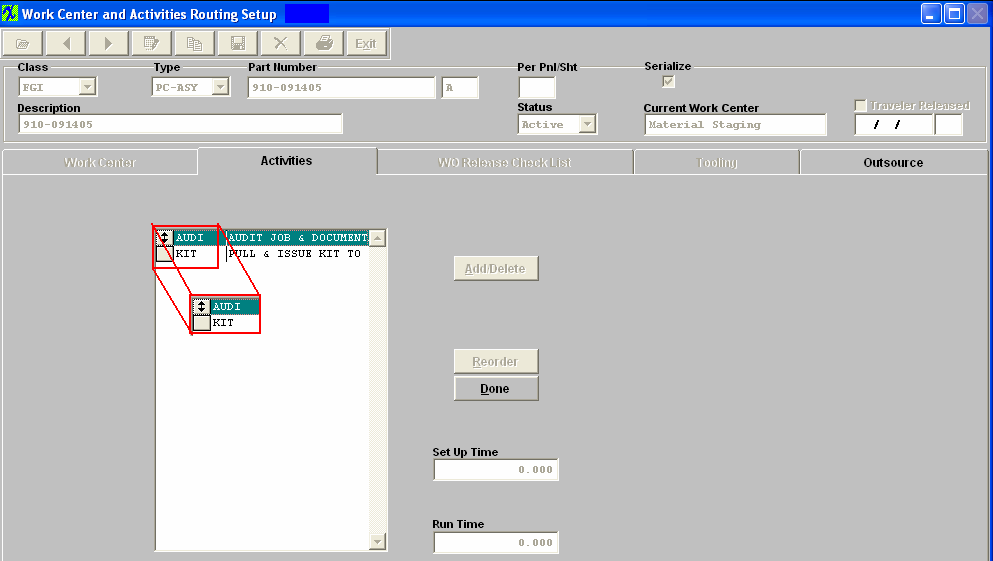
The user may then click on any of these buttons and drag an activity to the desired order.
See Article #850 to add or edit the Setup and Run Times for the Activities.
|
1.6.4.5. Add/Remove Work Order Release Check List Items |
In this screen, the user may add or modify Work Order Release Check List items used in a Work Center. These items are setup within the Shop Floor Default module.
Find a Product within the Work Order Traveler Setup module.
Highlight the Work Center you want to create a WO Release Check List for, then depress the Edit button and the following dialog screen will appear:
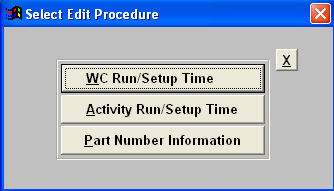
Select "WC Run/Setup Time" and go to the WO Release Check List tab:
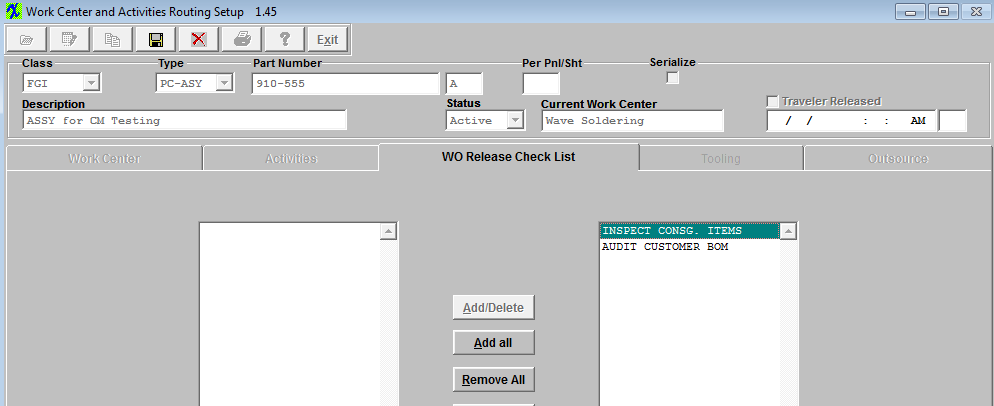
Depress the Add/Delete button and the Check List items will be displayed in the right screen. Select or de-select the itemsto be associated with the Work Center by double clicking on them or using the "Add all" "Remove All" buttons.
Check list items must have been set up in the SFT Defaults module prior to being used in this module.
Once the WO Release Check List is complete depress the Done button.
|
1.6.4.6. Add/Edit Tooling Information | Adding Tooling Information
The Tooling tab is used to describe the tooling requirements for the Work Center. It also provides for a location notation and an Expire Date. An example of a Check List item as discussed above might be to perform the Work Center tooling, as detailed in this tab. |
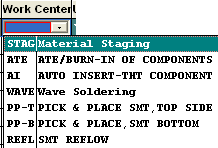 |
Find the desired Product number, enter the Tooling screen.
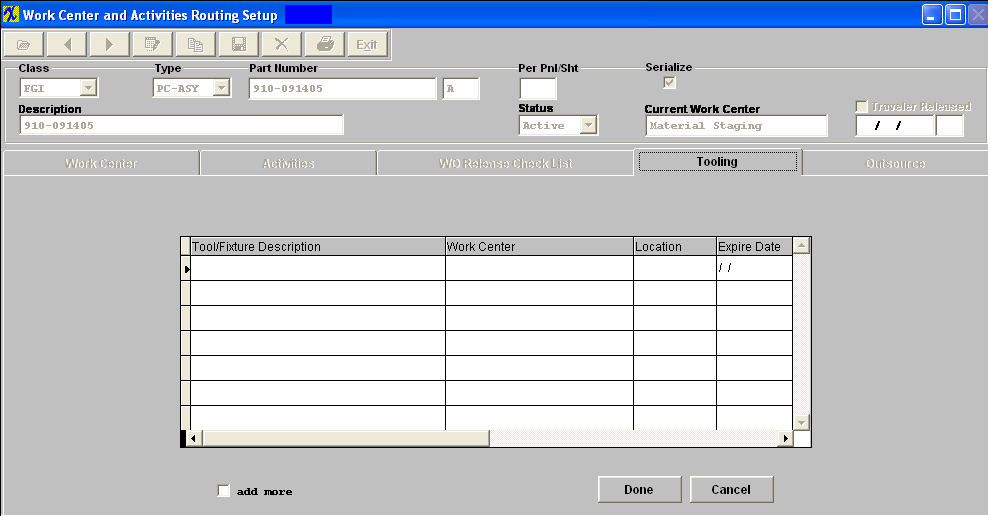
Depress the "Add" button. Select the description from the available pull down selections (originally setup within the System Setup/tooling Setup). Select the Work Center from the pull down menu, as illustrated: |
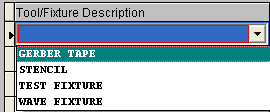 |
Type in the Location. Type in the Expire date. Depress the Done button. The completed screen will appear as follows:
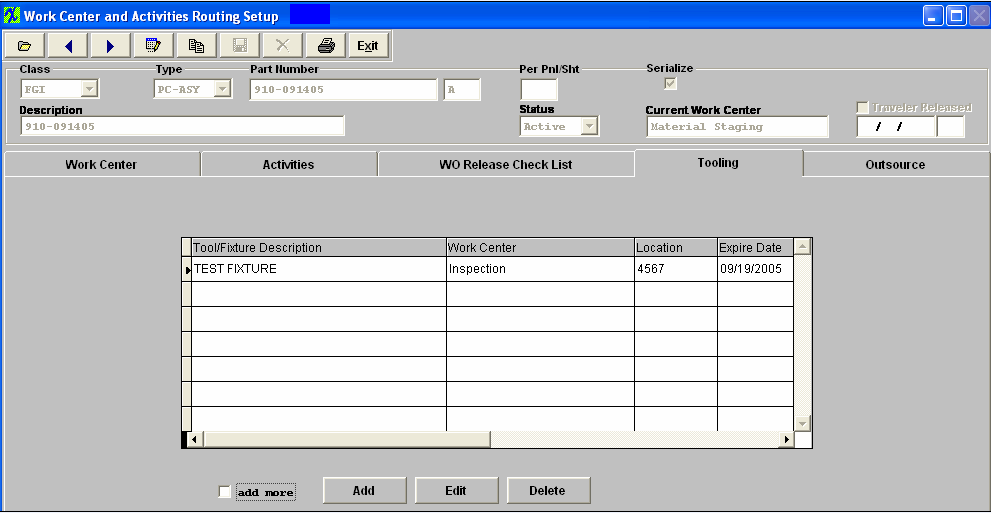
You may Edit any of your entries after depressing the Edit button.
To delete a line item from the Tooling Tab. Highlight the line item. Depress the Delete button. Click on the second column (which is NOT labeled), the field will change to Black.
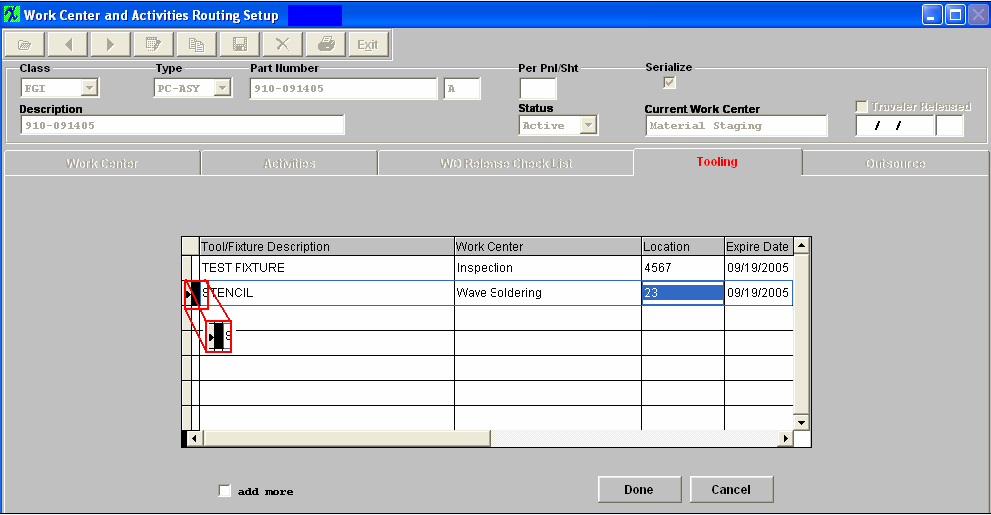
Depress the Done button.
The item will then be removed from the record. |
1.6.4.7. Add Outsource Information |
The Outsource tab shows the services to be performed outside of the user’s shop. These services are indicated with an “O” in the work center tab.
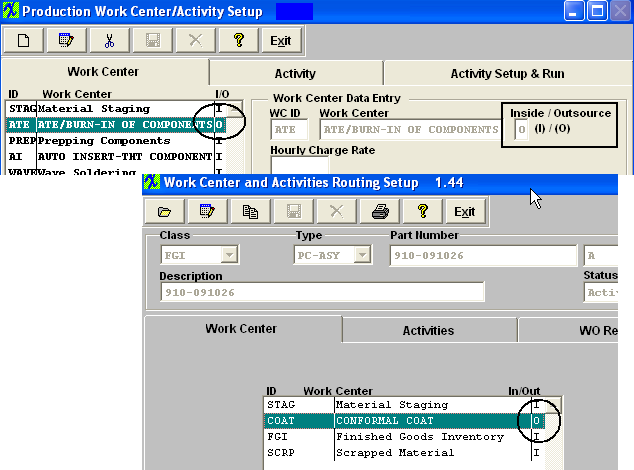
Highlight the Outsource Service, then go to the Outsource Tab and the following screen will appear:
Highlight the Outsource Service. Depress the Add button for the Supplier. Select the Supplier from the pull down.
Then continue across the columns and enter the quantity, cost each and markup. The Charge column will automatically update. When data entry is complete, depress the Done button.
In a future release, outsourcing will be available to create POs, receivers, etc.
If the "Certificate Required" box is checked, this indicates that the supplier of the outsourced service is required to provide a certificate of completion.
Depress the "Service Footnote" to attach a footnote regarding the services for this product.
Depress the "Outsource Note" to attach a note regarding the outsourcing for this product.
If you want to add a Service Footnote or an Outsource note, depress the applicable button. Depress the Edit button. Type in the note. Depress the Save button. Depress the Exit button.
Depress the Save button at the top of the screen to save changes, depress the Abandon changes button to abandon changes.
|
1.6.5. Reports - WO Traveler Setup |
Depressing the Printer icon, the following selections will be available.
Note: The Work Instruction may not appear in the Traveler if the user prints it to an Excel Worksheet file. Some of the reports are quite complex, with multiple relationships and filters. In this instance, the Work Instructions are in a different data base than the routing and therefore will not be available.
|
|
Job Traveler Report
If you select "Job Traveler", the following report will be printed:
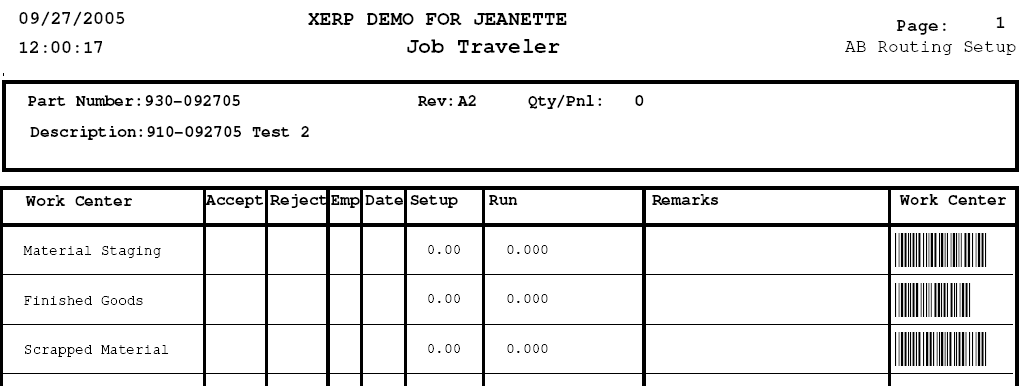
Job Traveler with Work Instructions Report
If you select “Job Traveler With Work Instructions” , the following will be printed:
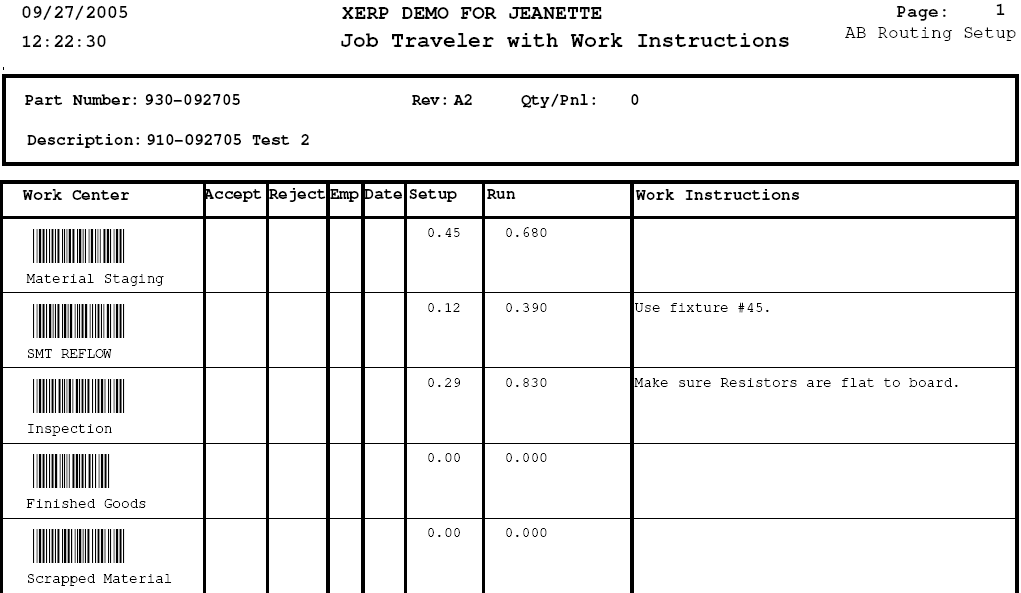
Job Traveler with Activities report
If you select “Job Traveler With Activities” , the following will be printed:
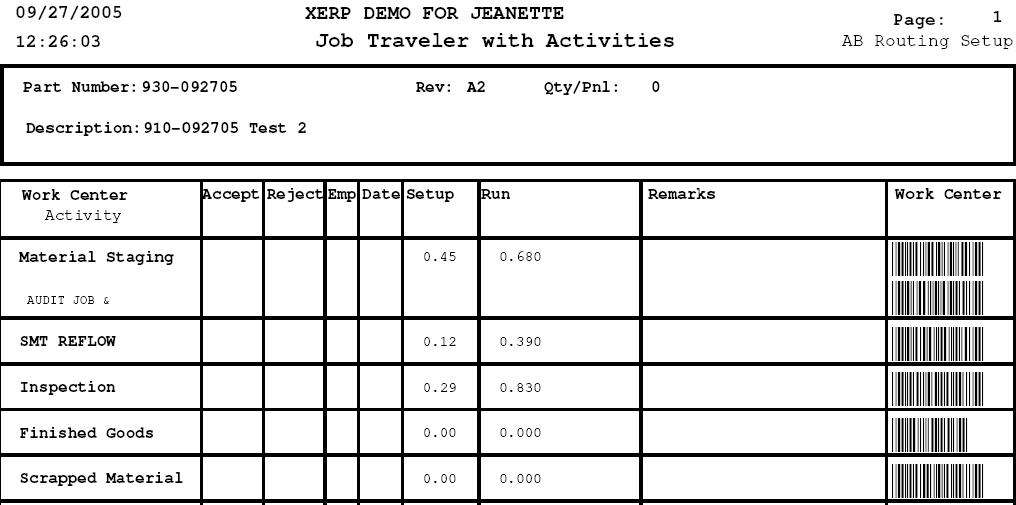
Job Traveler with Activities & Work Instructions report
If you select “Job Traveler With Activities & Work Instructions” , the following will be printed:
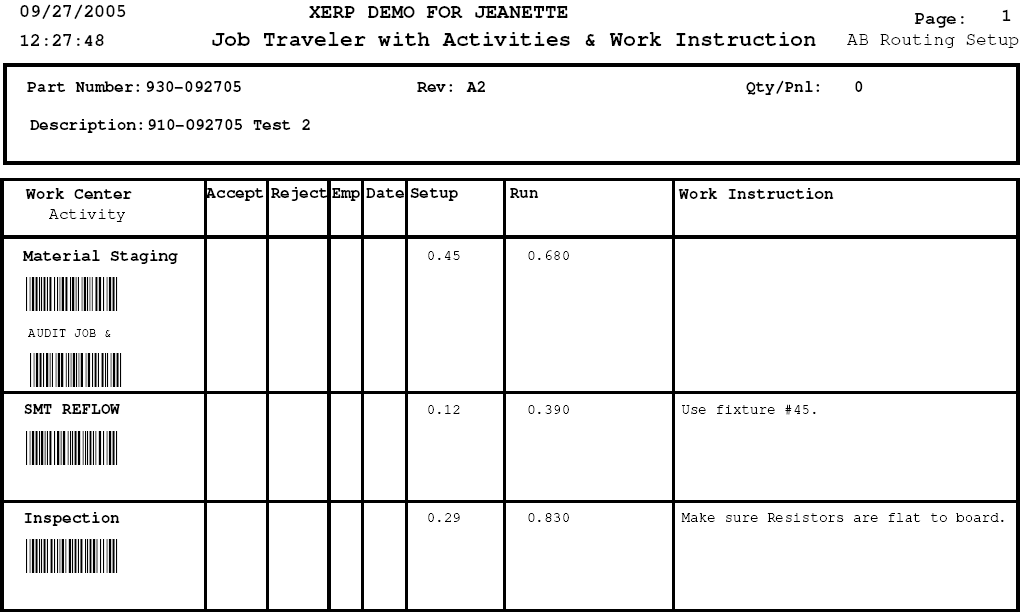
Job Traveler with Activities & All Instructions report
If you select “Job Traveler With Activities & All Instructions” , the following will be printed:
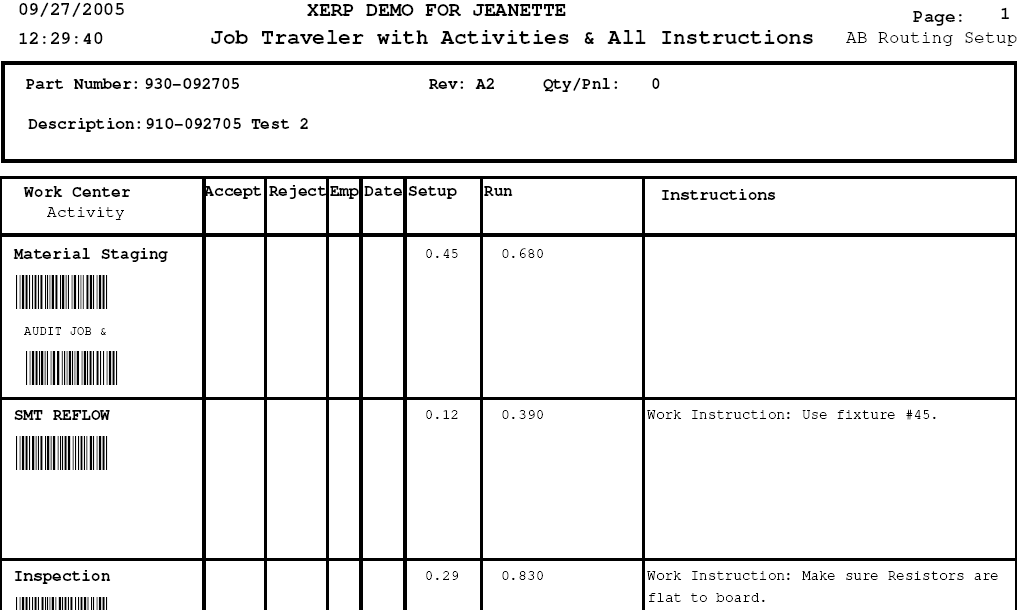
Routing Summary report
If you select “Routing Summary Report”, the following message will appear.

Depress the OK button, the following will be printed:

|
1.6.7. ManEx Minutes for - WO Traveler Setup |
1.7. Product Data Management (PDM) (OPTIONAL Module) |
1.7.1. Prerequisites for PDM | Prerequisites Required For PRODUCT DATA MANAGEMENT:
ManEx’s standard module configuration allows most users to accomplish their daily tasks. For those users wanting to get more from ManEx by leveraging the total solutions, this is one of the optional modules available for purchase. To place an order or to learn more about this specific module or any of the other optional modules please contact us at http://manex.com\contactus.aspx
After activation, "Product Data Management" (PDM) access for each user must be setup in the ManEx System Security module. Users with “Supervisor Rights” will automatically have access.
Optional Prerequisites for Entering a New PRODUCT DATA MANAGEMENT:
Pictures |
If images are to be included in Work Instruction and Set Up Instruction view screens.
|
|
1.7.2. Introduction for PDM | The Product Data Management (PDM) Module is the place where Engineering may establish work instructions, setup instructions and/or checklists. References to related documentation, Engineering notes, and production feedback on the product is also available. With the PDM module, the user may create both text instruction and graphical images.
Once a product has been established, similar products with some or all of the same instructions can have instructions copied from the original product, then modified to suit requirements.
The work instructions are available to users in the shop floor module, and users may elect to print the work instructions in the Work Order Traveler Setup traveler module.
Information entered in this module can be accessed via the Shop Floor Mgmt module. Work Instructions, Special Instructions, Documentation, Work Center Check List and Notes are available.
|
1.7.3. Fields & Definitions for PDM |
1.7.3.1. Header Information |
Product No |
The part number of the assembly. |
Rev |
The revision of the assembly. |
Description |
This field will contain the Description of the assembly. |
Selected Work Center/Activity |
This area displays the work center (or activity) from which each of the action buttons below are launched. It is selected by placing the cursor (by mouse or tab) on the work center (or activity) of interest |
|
1.7.3.2. Routing Tab | 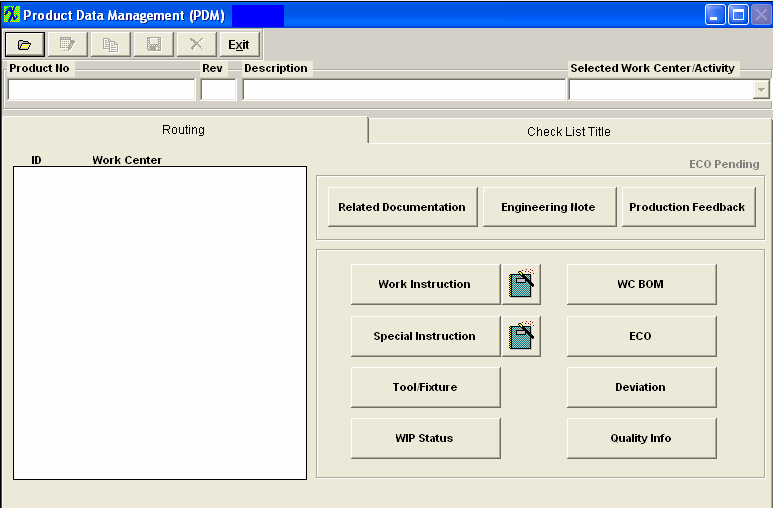
ID |
The ID or abbreviation established for the work centers |
Work Center |
The name of the work center |
ECO Pending |
This Text/characters turn RED if an ECO is Added and Saved. When the ECO is approved, this button characters turns back To gray. This criteria is based on the product number and no revision number as the ECO will change the revision number. This feature has been added because of the importance of the users needing to know that an ECO is being initiated by the production personnel. This will help prevent product being built according to the original instructions and cut down on any additional rework or schedule delays. |
|
If this button is displayed in Red there is Related documents attached. Depressing this button will give the users the ability to scan any related documents directly into the ManEx system and attached the document directly to the item in the ICM Module. For further detail see Article #2396. Once the information is loaded, the user may re-visit the Documentation in the PDM module and may also access the information from the Shop Floor Tracking Module.
|
|
If Red there is information available related to the product and the work center. User may edit or add information in this module also.
|
|
If Red, there is information available related to the product and the work center. This field is provided as a means of recording observations and communications about the product as it is being manufactured. User may edit or add information in this module, as well as from the Shop Floor module. Production Feedback note is intended as one way of communication from the production floor to the engineers of the suggestions and pointing out the errors created by the engineering department. Engineering department reading the feedback can take necessary action to correct or incorporate the information and then erase the contents of the Feedback note. This information may be added or edited in this module as well as from the Shop Floor module.
|
|
If Red, this button displays Work Instructions in text and pictorial format for operations associated with the work center. The Work Instructions must have been established in the Product Data Management module first. Users may load a PDF file in the Work Instructions. This allows users access to whole textbooks from within ManEx. PDF files can be drawings, images, CAD files (as printed to a plotter) and multiple pages of mixed test and graphics. Users may also print these PDF files from ManEx.
|
|
If Red, this button displays Special Instructions in text and pictorial format for setting up the work center. The Special Instructions are not printed on the travelers. The Special Instructions must have been established in the Product Data Management Module first.
|
|
If Red, this button will display any Tool/Fixture information which has been assigned to the Product through the Routing or Product Data Management (PDM) Module. This information is then also updated to the Routing setup module. Users will be able to edit the information from both the PDM and Routing setup screens. This information will then be available within the Shop Floor Tracking module for the users to View only.
|
|
If Red, this screen will display the WIP Status of all the open work orders for this product and show where the quantities are in the shop floor.
|
|
If Red, the part numbers that are assigned to that specific Work Center within the BOM module will be listed within this screen.
|
|
If Red, there is an ECO with the status of Approved within the system.
|
|
If Red, this screen will list the detailed information pulled forward from the ECO Control Management module pertaining to any approved Deviations for the selected product.
|
|
If Red, this screen will display Quality information for the Product that is displayed for the selected work center.
|
|
1.7.3.3. Check List Title Screen | This screen allows the user to establish check lists for each PRODUCT. Note that this is a different check list than the one for Work Order which is set up in Shop Floor Tracking Defaults . Items may be added to the check list in the edit mode.
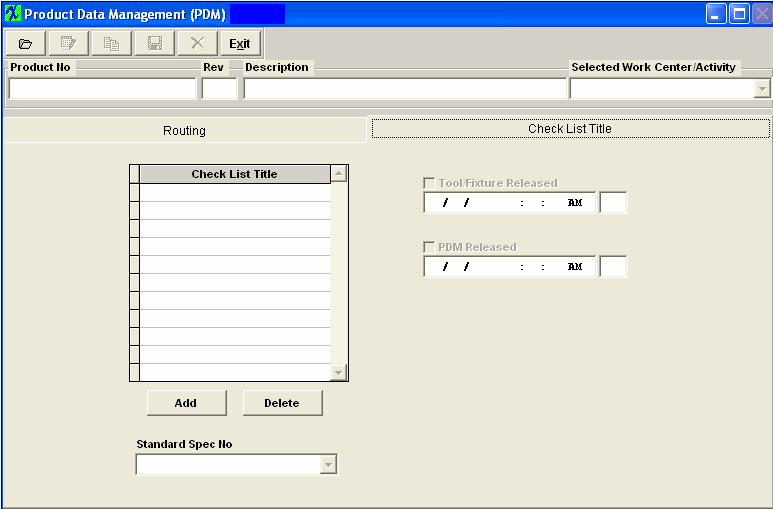
Check List Title |
Description of the Check to be Performed |
Tool/Fixture Released |
Check this box to release the Tool Fixture. This box MUST be check when usiing the Unreleased Work Order List and/or for the Tool/Fixture button to be enabled in the Shop Floor Tracking module..
Note: Users MUST have special rights within the Security module to check this box. Users with “supervisor’s rights” will automatically have access.
|
 |
This box will display the date and time of when the Tool/Fixture was Released and will also display the initials of the user that checked the box. |
PDM Released |
Check this box to release the PDM. This box must be check when usiing the Unreleased Work Order List .
Note: Users MUST have special rights within the Security module to check this box. Users with “supervisor’s rights” will automatically have access.
|
 |
This box will display the date and time of when the PDM was Released and will also display the initials of the user that checked the box. |
 |
Pressing the ADD button opens another field in which information may be placed in the Check List. |
 |
Pressing the DELETE button deletes the item from the Check List that the cursor is on when the delete button is pushed.
|
Standard Spec No |
Select the Standard Specification Number from the pull down list displaying after depressing the down arrow. These are defaulted in from the PDM Standard Process Specification module. |
This information will be carried forward into the Shop Floor Tracking module for the highlight Work Center.
|
1.7.4. How To ..... for PDM |
1.7.4.1. Finding A Product Data Management Record |
Enter Quality Engineering/Product Data Management (PDM) |
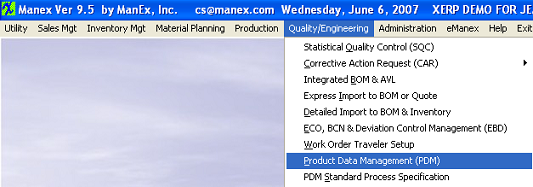 |
The following screen will appear:
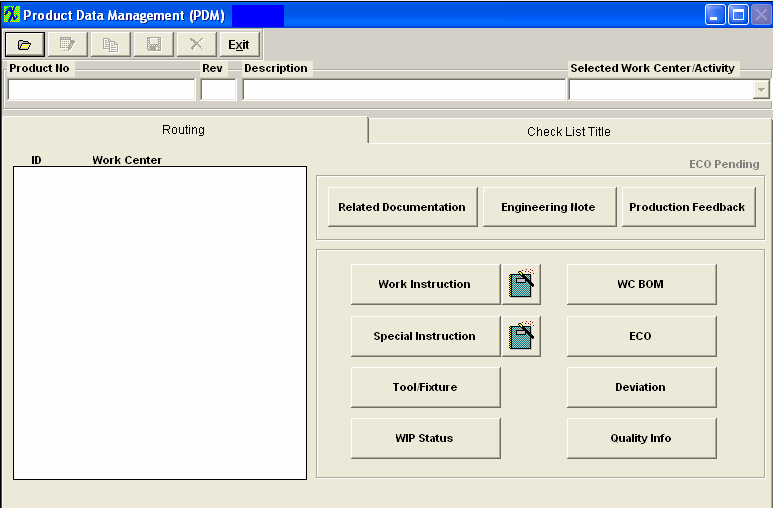
Depress the Find Record action button. The following Selections will appear. |
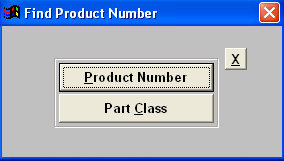 |
If the user selected to find by Product Number the following will appear:
The user may find a MAKE part directly by typing in the part number in the red prompt box, or scan down the list of part numbers until the correct part is located.
When the appropriate part is found, double-clicking on the part number loads the information for that part.
|
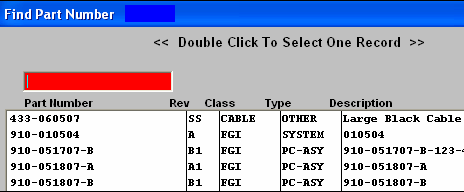 |
If the user wishes to narrow the search for an assembly number, they may first elect to search by Part Class.
Choosing that option will bring up a screen with part classes displayed.
After selecting a part class, the search by part number screen (as described in previous paragraphs) is displayed, but showing only those part numbers contained in the part class that was selected.
|
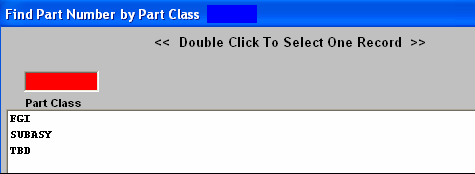 |
When the part number is located, the screen displays Work Order Traveler Setup information about the product.
The plus (+) mark preceding work centers indicate that additional activities are included in the work center, and may be viewed by clicking on the plus sign.
|
1.7.4.2. Add Information to the PDM Module |
To attach Related Documentation See Article #2396 . Once the information is loaded, the user may re-visit the Documentation in the PDM module and may also access the information from the Shop Floor Tracking Module.
See Article #3272 on how ManEx can help to simplify the process of identifying, tracking, and eliminating attrition and scrap.
To add Engineering Notes or Production Feedback, depress the buttons, a blank screen will appear, type in the information, and depress the Save action button to save the changes or depress the Abandon changes action button to abandon changes.
|
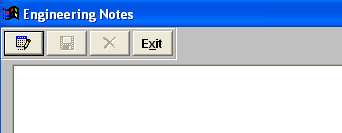 |
To view existing Instructions or add Work Instruction or Special Instructions, depress the buttons, a screen will appear, type in the information, and depress the Save action button to save the changes or depress the Abandon changes action button to abandon changes. To load PDF files depress the clipboard next to the Work Instruction or Special Instructions. This allows the user to load and give users access to whole textbooks from within ManEx. PDF files can be drawings, images, CAD files (as printed to a plotter) and multiple pages of mixed test and graphics. Users may also print these PDF files from ManEx. See Article #2823 for instructions on loading pdf files to the Work Instructions or Speical Instructions.
|
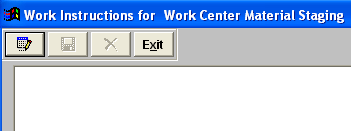 |
Depress the Tool/Fixture button and this screen will appear: |
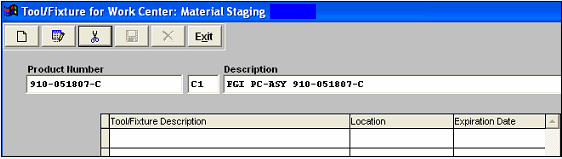 |
Depress the Add action button. Select the Tool/Fixture from the pull down. |
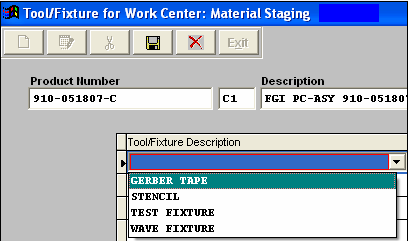 |
Enter the Location and Expiration Date. Depress the Save action button to save the changes or depress the Abandon changes action button to abandon changes
|
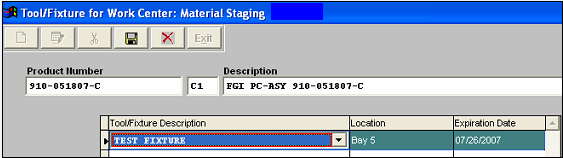 |
WIP Status - displays the WIP Status of all the open work orders for this product and displays where the quantities are in the shop floor.
WC BOM - The part numbers that are assigned to that specific Work Center within the BOM module will be listed within this screen.
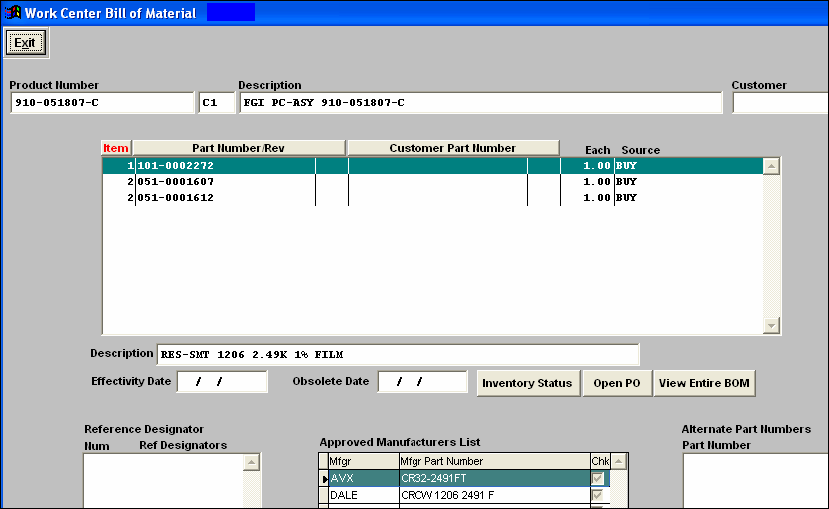
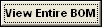 |
Depressing the “View Entire BOM” button will then display all parts listed on that BOM regardless of the Work Center. If there is a customer part number linked to the highlighted number in the main grid, then the Customer Part number information will be displayed. The Reference Designators will be listed for the highlighted part number, which is pulled forward from the BOM module. All AVL information will be displayed in the Approved Manufacturer list, and the system will show the approved AVL’s with a check mark next to it (same as in the BOM module) Alternate Part Number section will list any Alternate part numbers that were selected within the BOM module.
|
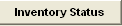 |
Depress the “Inventory Status” button, the following screen will be display Available Inventory information for the highlighted part number. EXIT will bring you back to the previous screen.
|
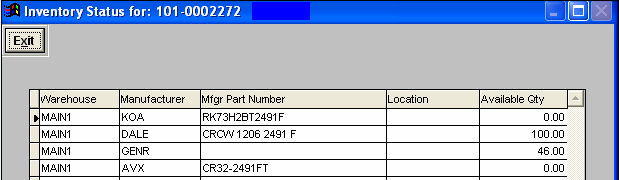
 |
Depress the “Open PO” button. The following screen will display all open Purchase Orders and their Balance Quantities for the highlighted part number. Exit will bring you back to the previous screen. |
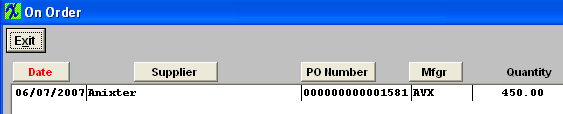
ECO - All of this information is carried forward from the ECO Control Management module. If the highlighted part number within the Part Change Information section was added as a Consigned item, then the associated Customer Part Number information will populate the field. EXIT will bring you back to the Product Data Management module.
Deviation - All of this information is carried forward from the ECO Control Management module. If the highlighted part number within the Part Change Information section was added as a Consigned item, then the associated Customer Part Number information will populate the field. EXIT will bring you back to the Product Data Management module.
Quality Info - This screen will display Quality information for the Product that is displayed for the selected work center.
If the highlighted work center has had not Inspection information entered against it, then the following message will be displayed |
|
Once you depress the OK button the following screen will be displayed. You can then change the selections to view All Work Centers if need.
If there has been Inspection information entered for the highlighted work center then the following screen will be displayed. The Quality information displayed on screen will appropriately update as the user selects the desired button selections. Exit will bring you back to the Product Data Management Module.
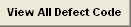 |
Depressing this button will display the following screen. Which is just there for reference for the users to use, just in case they do not recall what the displayed Defect Code stands for on the previous screen. |
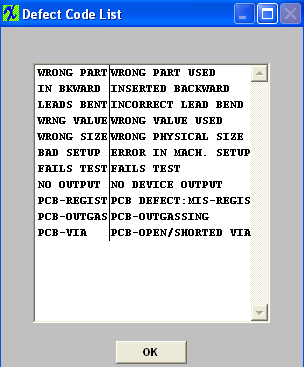 |
|
1.7.4.2.1. Load Document |
Depress the Clipboard next to the Work Instructions or Special Instructions Button |
 |
The following screen will appear:
To load images or documents, depress the "Load Document" button, up in the right hand corner of the screen. A browser screen will appear similar to this one:
Find and highlight the desired Image file, as illustrated.
Once the file name appears, depress the Ok button.
Note: that the user can also load other document types by changing the File of Type to ALL
|
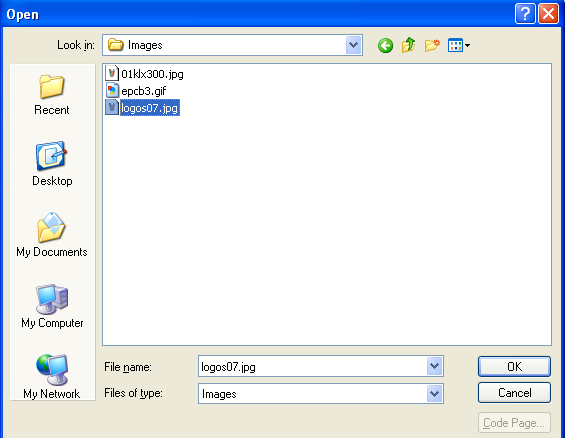 |
The file will appear in the screen as displayed:
Depress the Save action button to save the changes or depress the Abandon changes action button to abandon changes. Exit will bring the user back to the Product Data Management module.
All files and images planned to be used within the Product Data Management module should be stored in a permanent directory on the server, which users will have read access to. The user will define the directory and file for each product in this module, but the information will be available elsewhere throughout the manufacturing module.
|
1.7.4.3. Setup a Checklist |
Depress the CheckList Title tab. The following screen will appear:
This screen allows the user to establish check lists for a specific Work Center for a specific PRODUCT. This checklist is for users to check if they do all the necessary task, but it does NOT enforce the user to check all items before the user can transfter to next WC. Note: this is a different check list than the one setup for Work Orders which is set up in Shop Floor Tracking Defaults .
Select the Work Center/Activity from the Pull down: |
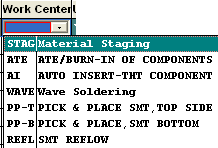 |
Select the Standard Specification Number from the Pull down:
|
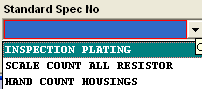 |
If the specification is not listed in the pulldown, user may depress the ADD button and enter a new specification in the CheckList Title screen:
Pressing the DELETE button deletes the item that the cursor is on when the delete button is pushed.
While screen is in Edit mode, user may also check the Tool/Fixture Released and/or PDM Released boxes. Note: Users MUST have special rights within the Security module to check these boxes. Users with “supervisor’s rights” will automatically have access. These boxes must be check when usiing the Unreleased Work Order List and the Work Center Checklist .
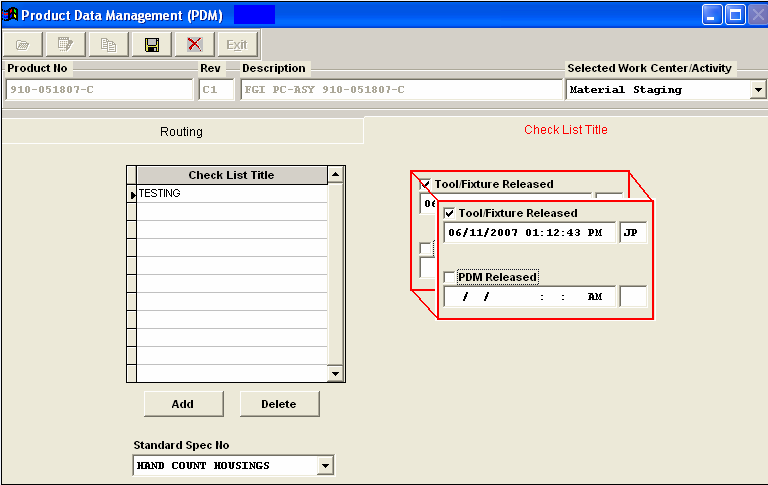
Depress the Save button to save changes or depress the Abandon changes button to abandon changes. The completed screen should appear as follows:
This information will be carried forward into the Shop Floor Tracking module for the highlight Work Center. NOTE: If there are existing Work Orders to update user MUST go to the WO Traveler screen and depress the "Update Open Work Orders" button.
|
1.7.4.4. Copy Information from another Product | Find a PDM Record.
The following screen will appear:
Depress the Copy button, to copy a routing and the following selection screen will appear:
Users can select one or more of the options by highlighting them. To continue depress the "OK" button.
Note: All notes on the existing routing will be removed and/or replaced with the new notes when copying a routing.
|
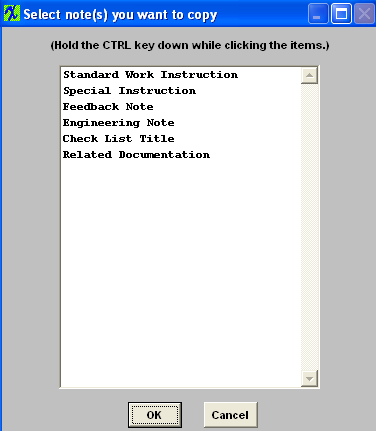 |
The following message will appear:
Depress the OK button
|
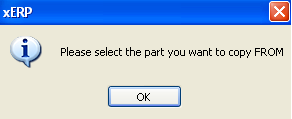 |
The following selection screen will appear:
Choose to find Product by Product Number or Part Class
|
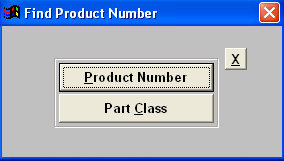 |
If user selects by Product Number the following list will appear:
Double click on the Product number or or Type the Product number in the Red box:
|
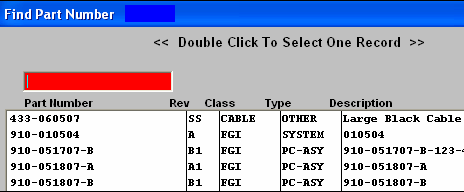 |
The following message will appear:
Depress the OK button
|
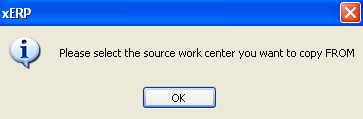 |
Double click on the Work Center Selection |
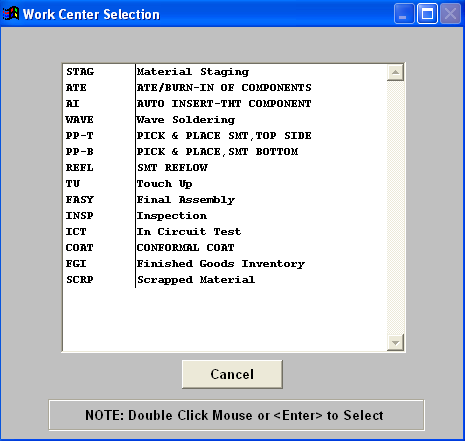 |
|
1.8. PDM Standard Process Specification |
1.8.1. Prerequisites for PDM Standard Process Specifications |
ManEx’s standard module configuration allows most users to accomplish their daily tasks. For those users wanting to get more from ManEx by leveraging the total solutions, this is one of the optional modules available for purchase. To place an order or to learn more about this specific module or any of the other optional modules please contact us at http://manex.com\contactus.aspx
After activation, "Standard Process Specifications" access for each user must be setup in the ManEx System Security module. Users with “Supervisor Rights” will automatically have access.
|
1.8.2. Introduction for PDM Standard Process Specification | The PDM Standard Process Specification Module is the place where Engineering may establish process specifications. Text and pictures may be included in detailing the specifications. Standard specifications relating to the Work Center can be accessed in the PDM and Shop Floor Tracking Mgmt module.
|
1.8.3. Fields & Definitions for PDM Standard Process Specifications |
Spec Description
|
Standard Process Specification Description.
|
Work Center
|
The Work Center the Standard Process Specification Applies to.
|
|
Depressing this button will allow you to edit or add text to the Standard Process Specification. This button will be Red if there is Text or Memo that applies to the Standard Process Specification Highlighted.
|
|
Depressing this button will allow you to edit or add text to the Standard Process Specification. This button will be Red if there is a Document attached that applies to the Standard Process Specification Highlighted.
|
|
1.8.4. How To ...... for PDM Standard Process Specifications |
1.8.4.1. Add a PDM Standard Procress Specification |
Enter the Quality/Engineering/ PDM Standard Process Specification |
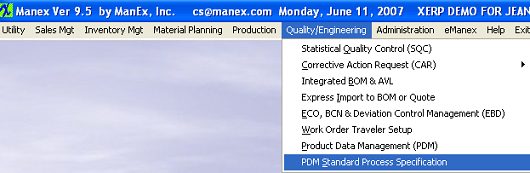 |
The following screen will be displayed:
Depress the Add Record button. You’ll be prompted for your password. Type in the Specification Description.
Select the Work Center by depressing the down arrow: |
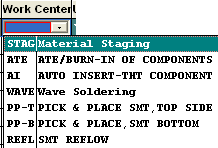 |
To add Text/Memo depress the "Standard Spec (Text.Memo)" button and the following screen will appear:
Type in the notes, depress the Save button to save notes or the Abandon changes button to abandon the changes.
Depress the Exit button to return to the Standard Process Specification module.
|
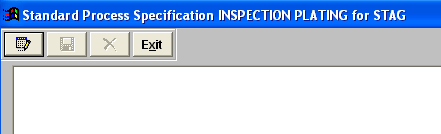 |
To load images or documents, depress the "Standard Spec (Document)" button. The following screen will appear:

Depress the "Load Document" button, a browser screen will appear:
Find and highlight the desired Image file, as illustrated.
Once the file name appears, depress the Ok button.
Note: The user can also load other document types by changing the File of Type to ALL.
|
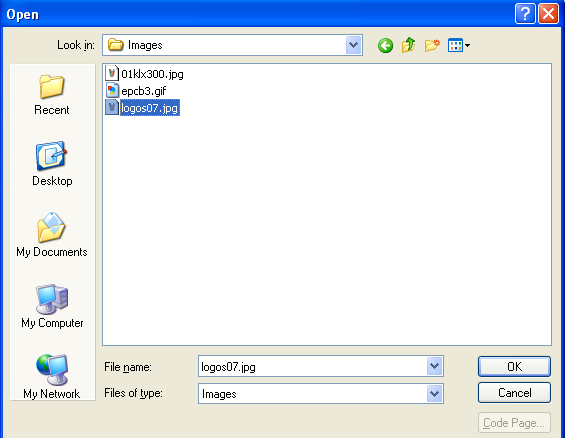 |
Depress the Save button to save the changes or depress the Abandon changes to abaondon the changes. Depress the Exit button will bring yor back to the Standard Process Specification. module.
All files and images planned to be used within the ManEx system should be stored in a permanent directory on the server, which users will have read access to. The user will define the directory
and file for each product in this module, but the information will be available elsewhere throughout the manufacturing module.
The complete screen will look like this.
Note: The Standard Spec buttons are now being displayed in Red.
User may add more standard process specifications, edit or delete existing specifications or exit.
|
1.8.4.2. Edit a PDM Standard Process Specification |
Enter Quality/Engineering/PDM Standard Process Specification |
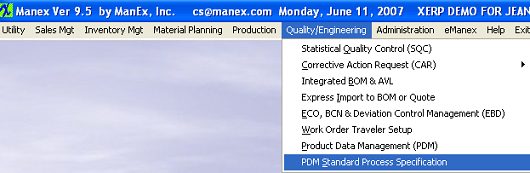 |
The following screen will appear:
Highlight the Specification user wants to edit. Depress the Edit button.
User may change the Work Center, edit the Standard Spec (Text/Memo) or (Document).
Once the changes have been completed, depress the Save button to save the changes or depress the Abandon changes button to abandon the changes.
|
1.8.4.3. Delete a PDM Standard Process Specification |
Enter Quality/Engineering/PDM Standard Process Specification |
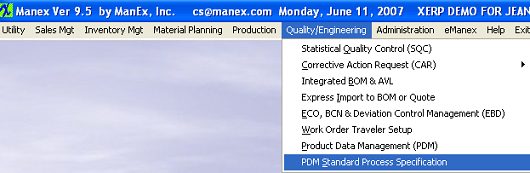 |
The following screen will appear:
Highlight the Specification user wants to delete. Depress the Delete button, enter password.
The following message will appear:
It will be defaulted to No. Depress the Yes to continue the Deleting and No to abandon without deleting the specification.
|
|