1.1. Prerequisties for Production Setup | In general, the production work is divided up among several departments. Some products may require that some work that is done in each of these departments. Other products may require that work be done in only a few of all the departments in operation. In order to identify the work processes for each product, ManEx allows the user to define Work Centers. These Work Centers describe a physical aspect (usually) of production operations that applies a specific type of labor to the product. Examples of work centers may be: SMT - where the product is assembled on a surface mount line; AI - where parts are Auto-Inserted into the product; Wave - where the parts are wave soldered; Cleaning; Inspection; Test; etc. Each of these work centers contains within it, a common aspect of production. For example, in SMT, the surface mount operator’s pay scale is probably higher than other parts of production, the parts are all contained within one area, the setup time is appropriate to one lot of a given product, and the parts are contained within the work area. If inventory counting is necessary, the user can identify that the parts are in the work center.
The user may create as many work centers as necessary to define the production activities that occur within the operation.
Within a work center, the user may establish additional definitions, called Activities. These activities may be set up separately from the work centers, and then used as needed within individual work centers. The activities may be assigned their own hourly charge rate.
And within an Activity, there is yet another classification called sub-activities, which have activity costs associated with them. These activity costs are established in the Activity Cost & Volume Type setup.
Also, in this section the setups for Quality items are accomplished, and will be discussed in each setup. Outside Program Calls Setup is also available.
User MUST have full rights to the "System Setup" in System Security to setup these modules. User with "Supervisor Rights" will automatically have access.
|
1.1.1. Manex Notes Matrix |
See the word attachement <Notes Matrix.doc>> for a table which shows the cross-reference for all ManEx Notes.
|
1.2. Introduction for Production Setup | This section covers the production setup to be used in all production related modules. Please take time to think about how you want to use these tables for best production management. Some sample data is provided with this setup as a guideline. These tables are used in various modules throughout the system.
The production application module setup section allows you to prepare tables for specific production related modules your company has purchased. Once setup in the system, you will be able to use these tables and/or perform certain functions automatically. These tables are completed by preparing worksheet tables and/or setting certain switches.
Production System worksheet covers the following modules: Work Shift Set Up, Activity Costing & Volume Type Set Up, Package Configuration, Production Work Centers & Activities, Time & Attendance Types, Shop Floor Tracking Defaults, Production Scheduling Method, Quality Defect Codes, CAR Problem Types, CAR Number Types, Tools Setup and Outside Program Calls Setup.
This section will first define the nature of each of the Production Setup screens, then describe how to fill out the work sheets, and finally, how to enter the data into the ManEx system.
|
1.3.1. Prerequisites for Work Shift Setup | Complete the attached worksheet and " Mark as Completed RoadMap Section B Item 3-a" before continuing the setup.
User MUST have full rights to the "System Setup" in System Security to setup these modules. User with "Supervisor Rights" will automatically have access.
|
1.3.2. Introduction for Work Shift Setup |
|
1.3.3. Fields & Definitions for Work Shift Setup | 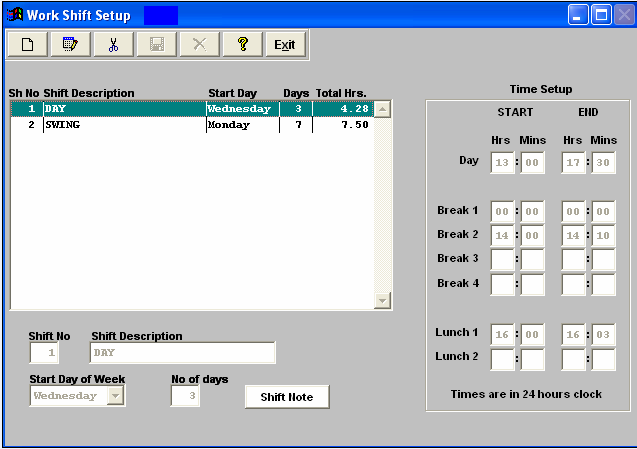
|
Shift Description |
|
|
|
Total Hours |
|
|
|
Start and End times |
|
Day: The beginning and end of the shift
|
|
1.3.4. How To ..... for Work Shift Setup |
1.3.4.1. Setup the Work Shift Module |
Enter System Setup/Production/Work Shift Setup
|
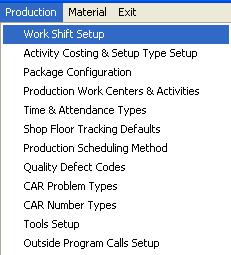 |
The following screen will appear:
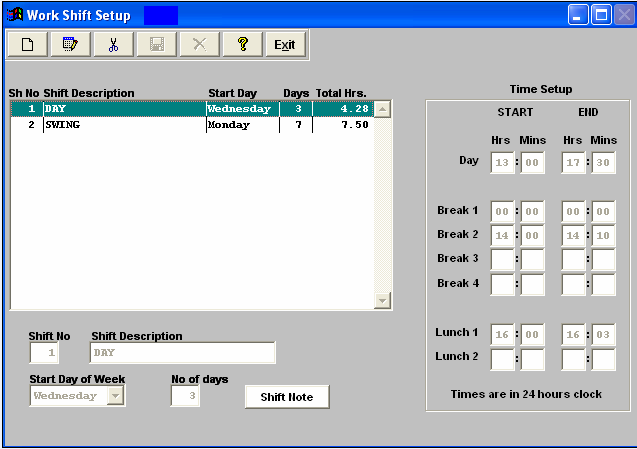
The user may Add new or Edit and Delete existing shifts.
The user must either Save or Abaondon to close the screen.
Where Used: In the job routing functions for a product.
«Mark as Completed in RoadMap in Section B Item 3-a»
|
1.4. Activity Costing and Setup Type Setup | |
1.4.1. Prerequisites for Activity Costing & Setup Type Setup |
Complete the attached worksheet and " Mark as Completed RoadMap Section B Item 3-b" before continuing the setup.
User MUST have full rights to the "System Setup" in System Security to setup these modules. User with "Supervisor Rights" will automatically have access.
|
1.4.2. Introduction for Activity Costing & Setup Type Setup | This module is essential if you are using Activity Based Cost (ABC) methodology for managing the production floor. The information entered here forwards to Production Work Center/Activity Setup. Then both setups are used in the MANEX Capacity Planning module.
Activity Costing and Activity Volume Type Description setup is a requirement only if your company is employing Activity Based Cost (ABC) methodology for managing the production floor. The Activity Costing and Activity Volume Type Descriptions are used in Production Work Center/Activity setup to assign Activity Costs and Activity Volume Types to a production Work Center/Activity. The Activity Volume Type Description is a pre-requisite for Production Work Centers & Activities / Activity Setup & Run tab.
Your company should become knowledgeable about the principles of ABC prior to using Activity Costing and Activity Volume Type Descriptions.Activity Cost and Volume types allow the users to define the costs and capacity for individual activities within a work center. It is used in the capacity planning module to determine available and required capacities. It is also used to assign costs of operation. For example, there may be several machines that can do the same job in a work center. However, one may have a higher operating cost, but also greater capacity. Both machines can be displayed as a resource. The selection of the machine is performed in the routing and capacity modules.
|
1.4.3. How To ..... for Activity Costing & Setup Type |
1.4.3.1. Setup the Activity Costing & Setup Type Setup Module |
Enter System Setup/Production/Activity Costing & Setup Type Setup |
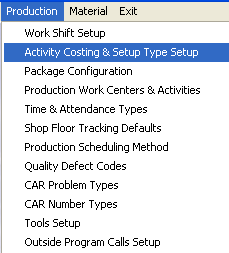 |
The following screen will appear:
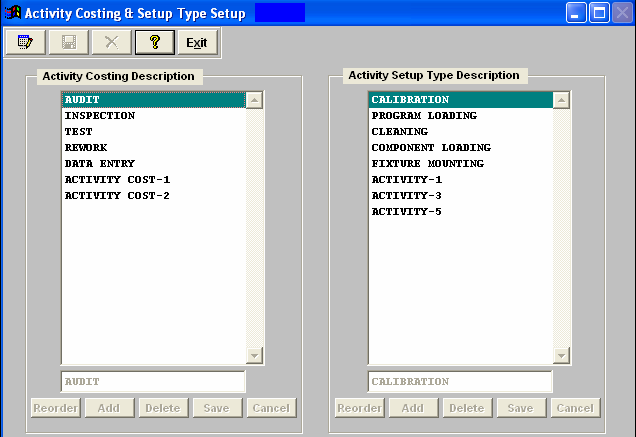
To ADD new descriptions to these tables, click on the Edit button. The Reorder, Add, Delete buttons will become available under each column. Depress the Add button, enter the description. When complete depress the Save or Cancel button under the table.
To DELETE existing descriptions to these tables, click on the Edit button. The Reorder, Add, Delete buttons will become available uder each column. Highlight the description you want to delete, depress the Delete button. When complete depress the Save or Cancel button under the table.
to REORDER descriptions to these tables, click ont he Edit button. The Reorder, Add, Delete buttons will become available under each column. Depress the REORDER button, then click and drag the activities to the desired order. When completed depress the Save or Cancel button uder the table.
The user then must Save or Abandon the changes using the icons at the top of the screen.
Where Used: In the Production Work Center/Activity Setup.
«Mark as Completed in RoadMap in Section B Item 3-b»
|
1.5. Package Configuration | |
1.5.1. Prerequisites for Package Configuration |
Complete the attached worksheet and " Mark as Completed RoadMap Section B Item 3-c" before continuing the setup.
User MUST have full rights to the "System Setup" in System Security to setup these modules. User with "Supervisor Rights" will automatically have access.
|
1.5.2. Introduction for Package Configuration | Package configuration setup is provided so that the user may define a machine’s Units Per Hour. This definition can then be accessed in the Production Work Centers & Activities setup/Activities Setup & Run tab.
|
1.5.3. Fields & Definitions for Package Configuration | 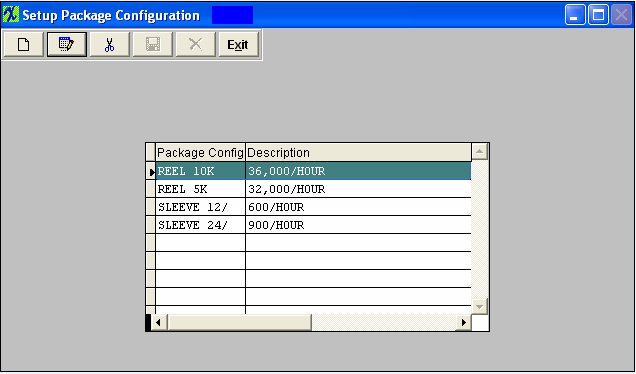
Package Configuration |
This is the user defined field for Package Configuration.Normally some reference to Units per Hour.
|
Description |
This is the description pertaining to the Package Configuration.
|
|
1.5.4. How To ..... for Package Configuration |
1.5.4.1. Setup the Package Configuration Module |
Enter System Setup/Production/Package Configuration Module |
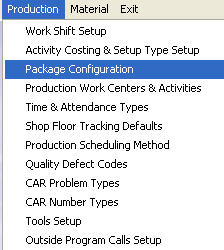 |
The following screen will appear:
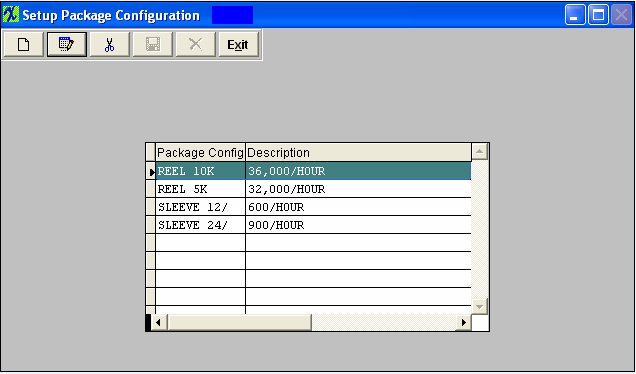
To ADD a record, depress the Add button, type in the Package Configuration and description.
To EDIT a record, depress the Edit button, edit the Package Configuration and/or description.
To DELETE a record, highlight the Package Configuration and description you wish to delete, depress the Delete button.
The user must then Save or Abandon changes after modifications are complete.
"Mark as Completed RoadMap Section B Item 3-c"
Where Used: In the Production Work Center/Activity Setup.
|
1.6. Production Work Center & Activity Setup | |
1.6.1. Prerequisites for Production Work Centers & Activities | Work Center Work Shift must be established if you intend to identify a shift number and description to a work center. Activity Costing & Volume Type setup must be established if the user plans to identify Activity Costs and/or volume types with activities. Setup type description must be set up in the Activity Costing & Volume Type Setup. Component package configuration must be set up in Package Configuration.
Complete the attached worksheet and " Mark as Completed RoadMap Section B Item 3-d" before continuing the setup.
User MUST have full rights to the "System Setup" in System Security to setup these modules. User with "Supervisor Rights" will automatically have access.
|
1.6.2. Introduction for Production Work Centers & Activities | Production Work center activities are optional sub-sets of work center departments. Activities may be defined prior to establishing work centers, and then used as more detailed actions within a work center. Each of these activities may be assigned a separate hourly charge rate. |
1.6.3. Fields & Definitions for Production Work Centers & Activities | |
1.6.3.1. Work Center Tab |
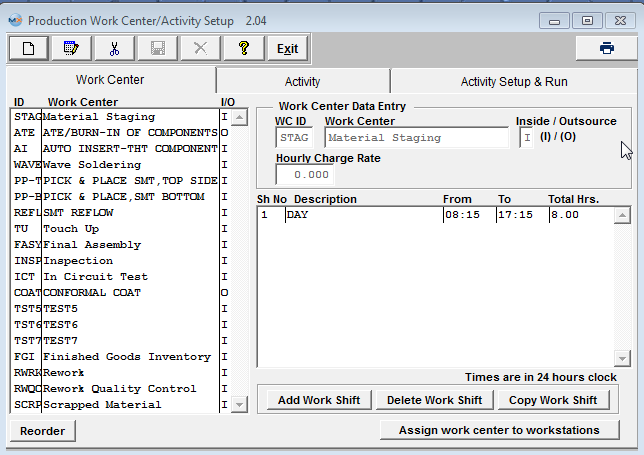
Work Center ID
|
This is the abbreviated (4 character) code for the name of the work center |
Work Center
|
This is the description of the work center. It may be 25 characters in length.
|
Inside / Outsource
|
Choose (I) inside or (O) outsource for site of activity.
|
Hourly Charge Rate
|
This is the standard hourly rate for the Work Center highlighted.
|
Shift Number |
This is the number of the shift assigned to the highlighted work center.
|
Shift Description
|
This is the description of the shift assigned to the highlighted work center. |
From |
Shift Start Time |
To |
Shift End Time |
Total Hours |
Total Hours of Shift |
Assign work center to workstations (button)
If a customer wants to install workstations along the production line, with scanners to read serial numbers as they passed down the line, this button provides the ability to limit a work station (specific computer) to be able to only transfer material “FROM” a certain Work Center on serialized Work Orders only. So, when a user first opens the "SFT by WO" or "Shop Floor Tracking by Bar Code" module, the module will use the default work center assigned for this workstation, but if user chooses to use a different work center, supervisor approval or a user that has the option "Allow Changing Default Work Center for Serial Number Transfer" box checked within the Security module is required to continue. After a supervisor's or user with this option’s password is entered, the default work center will be changed to the one that the supervisor entered password for. For Example: the workstation is assigned to use “TU” as default work center, now if user chooses to use “AI” to transfer, the system will ask for supervisor’s password, if user cancels the password, the default work center will still be “TU”, but if the supervisor enters his/her password on this machine, the default work center will be changed to “AI”. If now the user tried to transfer from “TU” again, the system will ask for supervisor’s password again. If user exits the module and come back, the default work center will be “TU” again.
When setting up a workstation user must enter the Full computer name in the Workstation Name field and the Computer description in the Workstation Description field. See Example below.
Defect Code Entry In-Line Mode, the system will check to see if the serial number is currently in the Work Center which was set up here. If not, a special supervisor’s password is required to transfer the serial number FROM a different Work Center. After the supervisor password is entered, the system will use the new Work Center to be the default FROM Work Center until the user closes the screen. The next time the user opens the screen, the default FROM Work Center will be changed back to the one defined in Systems Setup. |
1.6.3.2. Activity Tab | 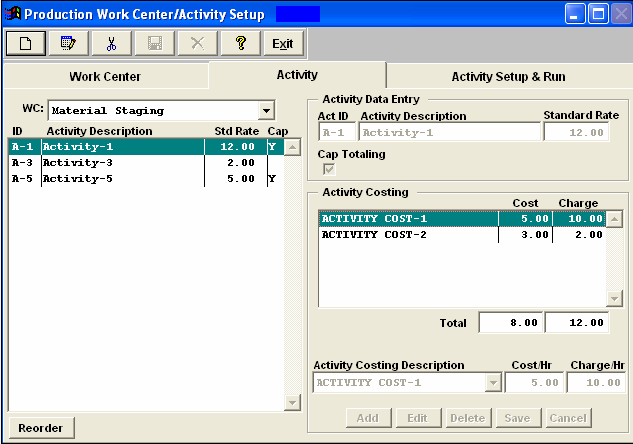
WC |
This is the description of the work center highlighted in the Work Center tab.
|
Activity ID
|
This is the abbreviated (4 character) code for the name of the activity.
|
Activity Description
|
This is the description of the activity being performed.It may take 25 characters in length.
|
Standard Rate
|
This is the standard hourly rate for the activity performed within the Work Center.
|
Cap
|
Click here for capacity totaling election.Capacity totaling means that if multiple activities are used in a work center, and if there are multiple resources in the activities, the capacity will be the sum of the resources rather than limited by just one resource.
|
Activity Costing Description
|
This field is selected from the available activity costing descriptions created in the Activity Costing & Setup module within system setup.
|
Charge Rate |
This is the field used to enter hourly charge rates, for each activity. The formatting is three digits to the left of the decimal, and two to the right (999.99). If this optional field is entered, it will be used to determine the hourly charge rate of the activity to which it is assigned.
|
|
1.6.3.3. Activity Setup & Run Tab |
Setup Type List
The Setup Type description is input into a previous screen “Activity Costing & Setup Type Setup/Activity Setup Type Description”.
Setup Type Description |
This is the description of the setup type.
|
Time
|
This is the time in hours and minutes associated with the setup type.
|
Setup Instruction (button)
|
This button allows the user to enter instructions for setting up the Setup Type and applicable pictures.
|
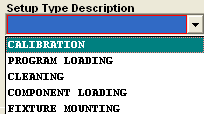
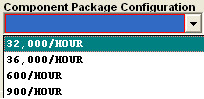
Component Package Configuration List
The Component Package Configuration is set up in a prior screen. See Setup Package Configuration.
Component Package Configuration
|
For a given machine’s Parts Per Unit, this field identifies the user defined configuration.
|
Volume/Hour
|
This is the volume type per hour. |
Yield Factor
|
This is the yield percentage.
|
Using Run and Setup Times in the Production Schedule Setup module is preferred when there is great variability in the products produced and the setup and run rates in each Work Center.
Using the Run and Setup Times in System Setup under this module, Work Center Setup, is preferred when the product flow is uniform, the machine rates are well established and the setup times very uniform regardless of product.
Use of Run and Setup Times in the Production Schedule Setup module is optional unless either Job Costing or Capacity Planning Modules are in use.
|
1.6.4. How To ..... for Production Work Centers & Activities |
1.6.4.1. Setup the Production Work Centers & Activities |
The following screen will appear:
For the highlighted Work Center, enter in the Hourly Charge Rate.
|
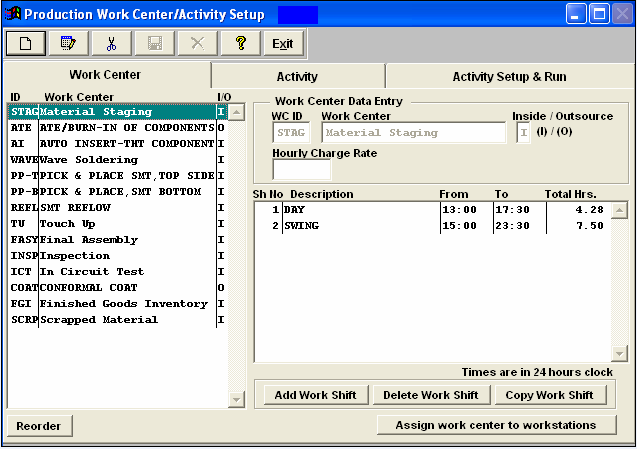 |
To add a Work Shift, highlight the Work Center, then depress the "Add Work Shift" button. The following popup screen will appear to select from. The work shifts listed on the popup screen have been setup in the Work Shift Setup module.
Highlight the work shift(s) and depress the "OK" button.
|
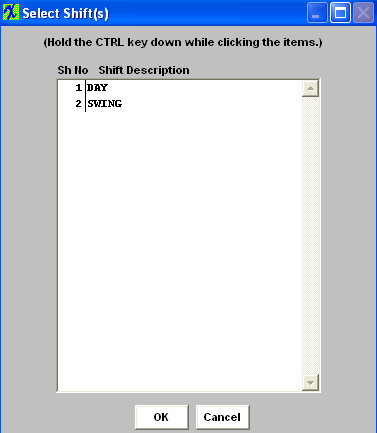 |
To Assign Work Center to Workstations In this screen, highlight the name of the Work Center. Depress the button at the bottom of the screen "Assign work center to workstations", the following assignment screen appears:
To enter a new assignment, depress the Add button. When setting up a workstation user must enter the Full computer name in the Workstation Name field and the Computer description in the Workstation Description field. See Example below.
Depress the Activity tab.
The user may add Work Center Activities by selecting the Add button from the main tool bar.
|
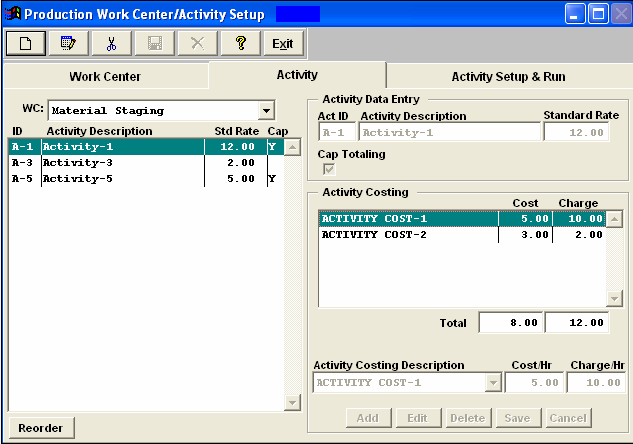 |
To add an activity ID and related description, choose the applicable work center from the drop down menu: |
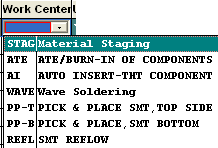 |
Enter the Act ID, Activity Description.
Note: The system does NOT allow you to generate the same Activity ID in different Work Centers.
Click on the Cap Totaling box to elect calculating capacity.
Save changes or Abandon Changes.
|
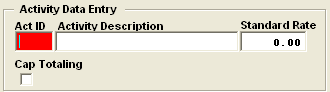 |
To attach a Cost Rate to an activity, click on the Edit button, then on the Add button (bottom of screen) in the Activity Costing Section.
|
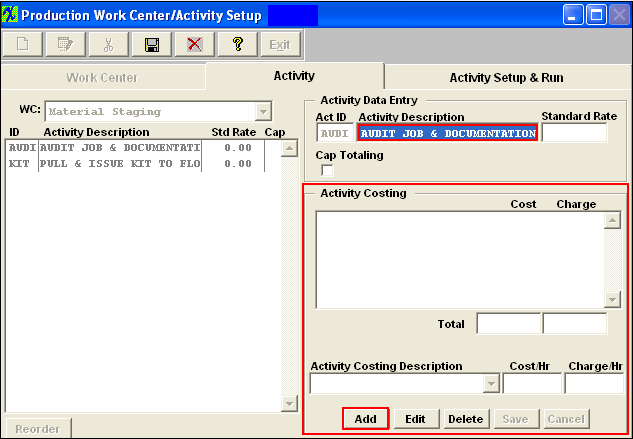 |
To attach a Cost Rate to an activity, click on the Edit button, then on the Add button (bottom of screen) in the Activity Costing Section. |
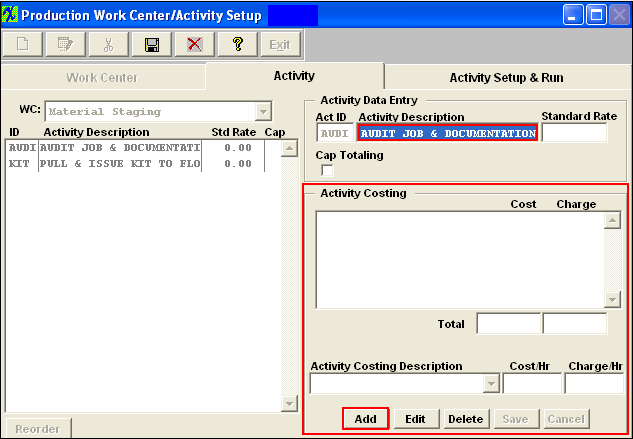 |
Select the activity from the pull down: (The activity costing descriptions are defaulted in from the Activity Costing & Setup Type Setup module)
Highlight the activity to which the Cost Rate will be attached.
Enter in the Cost/hr rate.
|
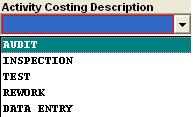 |
Once the Activity ID and Description, Cap Totaling election and hourly charge rate have been entered, depress the Activity Setup & Run tab.
|
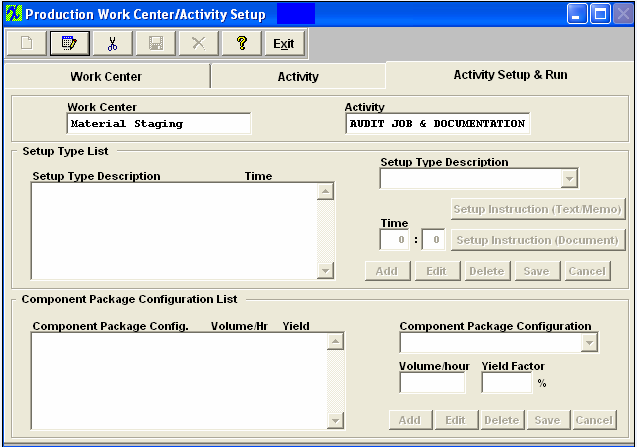 |
Depress the Edit button. For the Setup Type Description section. Depress the Add button (on screen). |
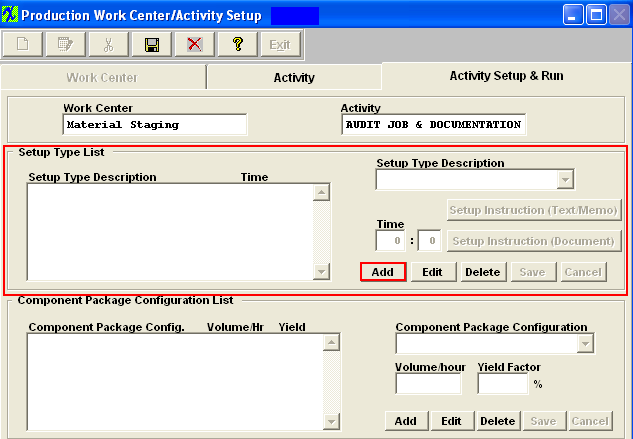 |
Select the Setup Type Description from the pull down: (These are defaulted in from the Activity Costing & Setup Type Setup module).
Enter the time in hours and minutes. Depress the Save button (on screen).
|
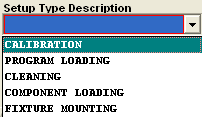 |
 |
This button allows the user to enter instructions for setting up the Setup Type. |
 |
This button allows the user to load a photo for an instruction. The photo file should be in the ManEx directory, and should be BMP or TIF format.
|
For Component Package Configuration, depress the Add button (on screen) |
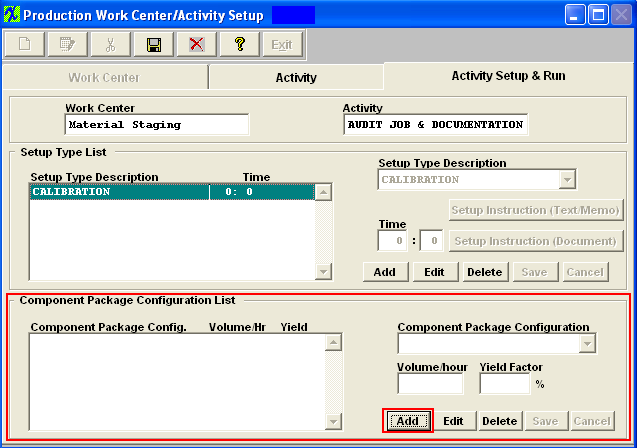 |
Select the Component Package Configuration from the pull down menu: (The Component Package Configuration(s) are defaulted in from the Package Configuration module).
Enter in the Volume per hour, and then the yield factor %.
Volume is the number of units per hour. This may be boards per hour, units per hour, connections per hour, etc.
The Yield factor affects the volume such that lower yield means it will take longer to make the same number of good parts.For example, if the standard volume is 100 parts per hour, and the total yield is 80%, then the effective yield would be 80 parts per hour.
Depress the Save button (on screen).
|
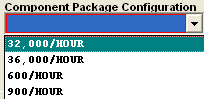 |
Once all changes are complete depress Save or Abandon changes.
Where Used: In all Shop Floor related Activities.
«Mark as Completed in RoadMap in Section B Item 3-d»
|
1.7. Time and Attendance Types | |
1.7.1. Prerequisites for Time & Attendance Types |
Complete the attached worksheet and " Mark as Completed RoadMap Section B Item 3-e" before continuing the setup.
User MUST have full rights to the "System Setup" in System Security to setup these modules. User with "Supervisor Rights" will automatically have access.
|
1.7.2. Introduction for Time & Attendance Types |
|
1.7.3. Fields & Definitions for Time & Attendance Types |
Is the code for the time setting description. Example V-Vacation, H-Holiday, T-Time Clock, W-Work Order, etc. |
Description |
Description of the Time Log Type Code. Example Vacation, Holiday, Time Clock, etc. |
|
If this box is checked, the user will be able to enter hours directly in Time used field for that type in the Time Log Management module. Once user adds a new record for a time log type which is allowed to enter hours directly, the time in and time out fields will be blank out and disabled, and user can enter how many hours for that record directly. Otherwise, the user has to enter time in/out.
The system only allows user to enter "RT" no "OT" can be entered. Therefore, user can not check type "W" or "T" to enter hours directly. The system will have to calculate the total log in time and determine what's the RT and OT for type "W" and "T".
The time in and out will also be blank if the type is "H" -- holiday, and the system will use shift to calculate the RT, no OT will be calculated.
|
After Hours Worked |
Enter the number of regular time hours in the period. Any time after these hours will be paid at overtime rates. |
Start Day of Week |
Select the Day of Week you want to start the week on Sunday, Monday, etc. This means the OT hours are calculated starting from that day. |
Enforce Breaks |
This box only applies to type "T"-Time Card. When checked it will deduct the lunch 1 and 2, but does not deduct the break times from the total hours. If unchecked it does not deduct lunch 1 and 2, or break times from the total hours. For example see attached "Print Screens_2006-02-09_a.doc". |
User Work Shift |
Check this radial if you want this as a work shift |
|
|
1.7.4. How To ..... Time & Attendance Types |
1.7.4.1. Setup the Time and Attendance Module |
Enter System Setup/Prduction/Time & Attendance Types Module
This section is provided to add additional ways for logging and keeping track of time spent by employees on each work order. Enter various different time tracking modes in this section.
|
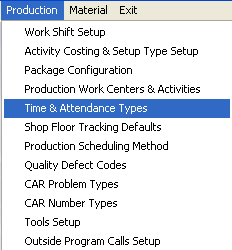 |
The following screen will appear:

The ADD, EDIT, and DELETE buttons are available.
The user adds a type by clicking on the ADD button and entering the type in the entry field box. Time and Attendance Types indicate how the hours are to be collected. (In the future, General Ledger Numbers will be associated with each type listed.) Therefore, each type of job (Work Order) logging will collect charges accordingly.
If you check the Pay box, that means the company will pay for that type. For example, an unexcused absence would NOT be checked, but Jury Duty might be checked if it is the company policy to pay for jury duty.
"Allow to enter hours directly in Time Log Management" checkbox in T&A setup, if it's checked, the user will be able to enter hours directly in Time used field for that type in the Time Log Management module. Once user adds a new record for a time log type which is allowed to enter hours directly, the time in and time out fields will be blank out and disabled, and user can enter how many hours for that record directly. Otherwise, the user has to enter time in/out.
The system only allows user to enter "RT" no "OT" can be entered. Therefore, user can not check type "W" or "T" to enter hours directly. The system will have to calculate the total log in time and determine what's the RT and OT for type "W" and "T".
The time in and out will also be blank if the type is "H" -- holiday, and the system will use shift to calculate the RT, no OT will be calculated.
Overtime hours are established for determining overtime pay if the timeclock function is used without shift data per person. Hours entered in excess of X hours per day or week would be counted as overtime.
Enforce Breaks - This box only applies to type "T"-Time Card. When checked it will deduct the lunch 1 and 2, but does not deduct the break times from the total hours. If unchecked it does not deduct lunch 1 and 2, or break times from the total hours. See attachment "Print Screens_2006-02-09_a.doc" for example.
User Work Shift - user will check this radial if they want this as a work shift.
Maximum hours logged on in the system is the number of hours which, if a user has remained logged on, the system would automatically log them off, assuming that they left without logging off. Note: ManEx suggests that you populate this field with a number of 1-24. If left empty or with a -0-, the automatic loggout process will NOT run and will NOT logout the user automatically.
This field is restricted to only allow a minimum entry of "0" and a maximum entry of "24".
Shift Tolerance allows users to consider a line at the timeclock .If an employee logs in a few minutes early, or late, the system will log them in at the beginning of their shift.
Once you have completed all modifications to screen depress the Save or Abandon changes button.
These items may be sorted in any order by clicking on and dragging the box on the left side, to the (vertical) position desired. This order will be the order displayed in the pull downs when using this list in other modules within the system. Suggestion: Have the one most used at the top of the list.
Where Used: In all job logging functions for a product’s work orders.
«Mark as Completed in RoadMap in Section B Item 3-e»
|
1.8. Shop Floor Tracking Defaults | |
1.8.1. Prerequisites for SFT Defaults |
Complete the attached worksheet and " Mark as Completed RoadMap Section B Item 3-f" before continuing the setup.
User MUST have full rights to the "System Setup" in System Security to setup these modules. User with "Supervisor Rights" will automatically have access.
|
1.8.2. Introduction for SFT Defaults | |
1.8.3. Fields & Definitions for SFT Defaults |
When the user is in the Shop Floor module, and has information displayed on the screen (for example, the wip status of a work order). The user then leaves the screen up and alone to do another task (say breaks for lunch). Then the data represented by the screen may actually undergo changes by other employees. If the user does not use the screen in the meantime, when they return from their alternate task, the information on the screen would be incorrect (because someone else moved material). ManEx performs a periodic update (refresh) to Shop Floor screens when the user has information displayed on the screen, but has not performed any functions in the meantime. The period of the refresh rate is initially set to every two and a half minutes by ManEx. So, if the user has a work order tracking screen displayed with a work order showing wip, and does not perform any transaction for 2-1/2 minutes, ManEx will automatically update the information on the screen. This timing is initially set at 2-1/2 minutes, but the user may change this period in this setup. However, the trade-off for shorter periods is increased network traffic, and setting too many workstations to be refreshed every few seconds will seriously impact the server’s ability to deliver data.
|
1.8.4. How To ..... SFT Defaults |
1.8.4.1. Setup the Shop Floor Tracking Defaults |
Enter System Setup/Production/Shop Floor Tracking Defaults Module |
|
The following screen will appear:
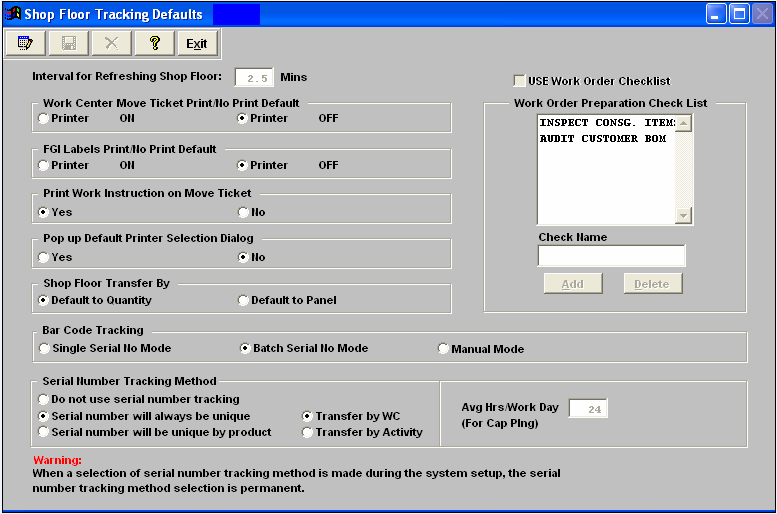
The user may edit any of the defaults by clicking on the Edit button and selecting the default to be changed. Check List items may be added by clicking on the Add button and entering the description of the item to be listed.
Use Work Order Check List
User MUST check this box to activate the Unreleased Work Order List module.
Serial Number Tracking Method can NOT be changed once a selection has been made at the beginning of a ManEx implementation. THIS DECISION, ONCE STARTED, IS IRREVOCABLE. The decision to be made is:
1, Do NOT use Serial Number tracking. If this box is checked users will NOT be allowed to check the serialized box within the ICM module, and they will receive a warning message.
2, Serial Number will always be unique. This will insure that a serial number is unique throughout the company; (meaning once used, can NEVER be used again, no matter what product).
3, Serial Number will be unique by Product. This will allow duplicate serial numbers to be used throughout the company, but they must be unique for a given product, (can be used for other products, but never again for the same product).
If Serial Numbers are NOT to be used, then the option will NOT appear when creating new part numbers within the ICM module.
If Serial Numbers ARE used, then the user will have the option when creating parts within the ICM module to either serialize the part or leave it unserialized.
If Serial Numbers are used on a part, then the user MUST enter Serial Numbers in order to move product through the SFT for shipment.
The user will also need to define whether Serial Numbers are to be transferred by Work Center or by Activity within a Work Center.
When the user has completed the changes they must press the Save or Abandon button, before exiting.
Where Used: In all shop floor functions for a product’s work orders.
Mark as Completed in RoadMap Section B Item 3
|
1.9. Production Scheduling Method | |
1.9.1. Prerequisites for Production Scheduling Method |
User MUST have full rights to the "System Setup" in System Security to setup these modules. User with "Supervisor Rights" will automatically have access.
|
1.9.2. Introduction for Production Scheduling Method | In this setup, the user defines the method to be used by ManEx to determine the capacities and scheduling in the Capacity Planning module.
|
1.9.3. Fields & Definitions for Production Scheduling Method | 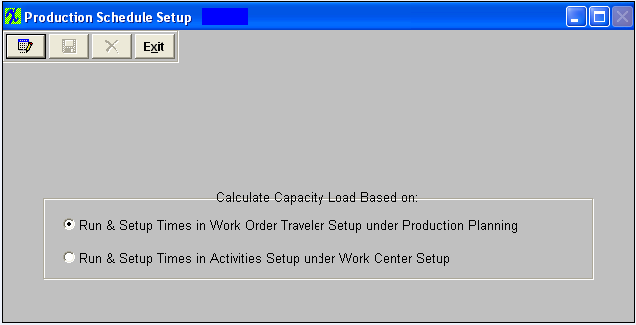
The default, “Run & Setup Time” will calculate the resources and costs associated with those entered in the work center setups and activities for the product. The costs will be based on the work center rates, and the capacity on the product routing information.
The Activities Drivers option may be used in conjunction with the Job Planning module, and will calculate the costs and durations based on parameters entered by the users in the planning module.Normally, the Run & Setup time option is used.However, once the system has an active capacity planning module in place, the user may use Activities Drivers to schedule priorities in the Dynamic Scheduling Module.
No change is required in this setup unless the user is going to make extensive use of the job planning module.
Note: In order to add Times in Routing, the Run and Setup Time MUST be selected in this module.
|
1.9.4. How To ..... for Production Scheduling Method |
1.9.4.1. Setup Production Scheduling Method |
Enter System Setup/Production/Production Scheduling Method Module |
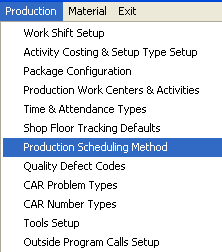 |
The following screen will appear:
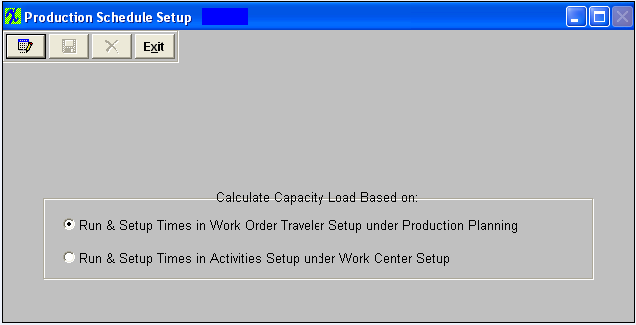
The user may click on the Edit button to change the defaults.
The user must Save or Abandon changes after entering the Edit Mode.
Where Used: In all shop floor functions defining labor costs, and for Capacity Planning Modules.
«Mark as Completed in RoadMap in Section B Item 3-g»
|
1.10. Quality Defect Codes | |
1.10.1. Prerequisites for Quality Defect Codes |
Complete the attached worksheet and " Mark as Completed RoadMap Section B Item 3-h" before continuing the setup.
User MUST have full rights to the "System Setup" in System Security to setup these modules. User with "Supervisor Rights" will automatically have access.
|
1.10.2. Introduction for Quality Defect Codes |
|
1.10.3. Fields & Definitions for Quality Defect Codes |
“Maximum number of inspections/WC” Box: This field is for serial number use only. The user may define how many times a given serial number can pass through a given Work Center. If the user selects the “Skip Serial Number” field, this max number will be come invisible. In the Defect Entry screen, once the pass number of a serial number exceeds the max number as set up here, a supervisor or special rights password is needed to continue. Please refer to the Implementation – Security
|
1.10.4. How To ..... for Quality Defect Codes |
1.10.4.1. Setup Quality Defect Codes Module |
Enter System Setup/Production/Quality Defect Codes Module |
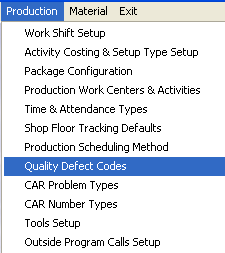 |
The following screen will appear:
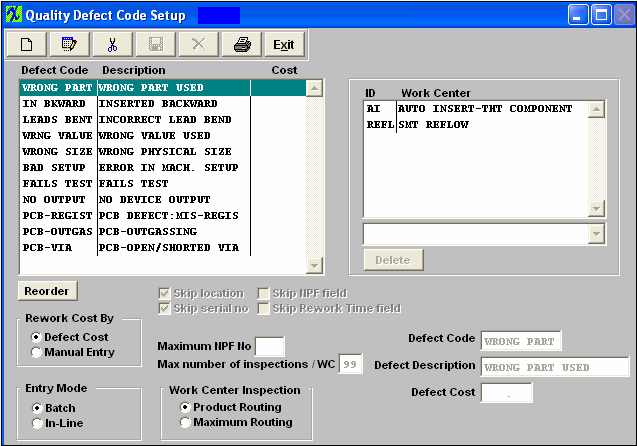
The user initiates a new defect code by clicking on the Add button. Note: When creating a new Defect Code you will want the Defect Code descriptive as possible because this is what appears in the Pareto Chart in the SQC module information. NOTE: The "Defect Code" field is NOT editable once it has been saved.
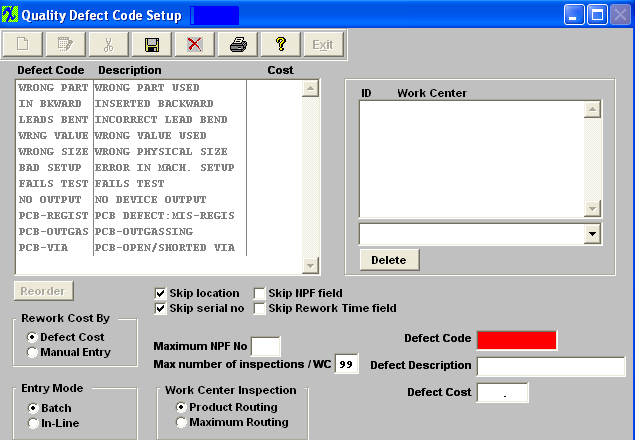
To associate a Work Center with a defect code, depress the Edit button and place the cursor in the ID Work Center window, as illustrated
|
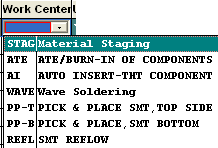 |
Enter in the maximum NPF number. Type in the desired number of times for Maximum number of inspections /WC.T his field is for serial number use only. If the user selects the “Skip Serial Number” field, this max number will be come invisible. In the Shop Floor Tracking module, Inspections section, once the pass number of a serial number exceeds the max number as set up here, a supervisor or special rights password is needed to continue.
Items may be re-sorted by clicking on the REORDER button, click on and drag the box of the left side of the defect desired to the (vertical) position desired. When completed with the order, click on the DONE button to return to the edit screen, and Save to record the changes. This order will be the order displayed in the pull downs when using this list in other modules within the system. Suggestion: Have the one most used at the top of the list.
When all changes have been completed, the user must Save or Abandon changes.
Depress the Edit button and work centers assigned to or deleted from the defect code. All fields are editable except for the "Defect Code" field.
When all changes have been completed, the user must Save or Abandon changes.
User may ONLY delete a Defect Code if it has not been used in the SQC module. This info needs to be retained for history/reporting purposes. If the defect code has been used in the SQC module user will receive the following warning when trying to delete the defect code.
If defect code has NOT been used in the SQC module the defect code may be deleted. User will receive the following confirmation to be sure they want to delete the Defect Code.
Depress OK to continue or Cancel to abandon the deletion.
Where Used: In all Statistical Quality Control tracking operations and reporting.
«Mark as Completed in RoadMap in Section B Item 3-h»
|
1.11. Corrective Action Reporting Problem Types | |
1.11.1. Prerequisites for CAR Problem Types |
Complete the attached worksheet and " Mark as Completed RoadMap Section B Item 3-i" before continuing the setup.
User MUST have full rights to the "System Setup" in System Security to setup these modules. User with "Supervisor Rights" will automatically have access.
|
1.11.2. Introduction for CAR Problem Types |
|
1.11.3. Fields & Definitions for CAR Problem Types |
|
1.11.4. How To ..... for CAR Problem Types |
1.11.4.1. Setup the CAR Problem Types Module |
Enter System Setup/Production/CAR Problem Types Module |
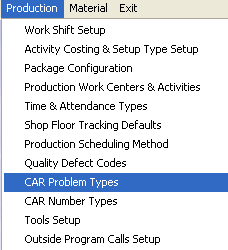 |
The following screen will appear:
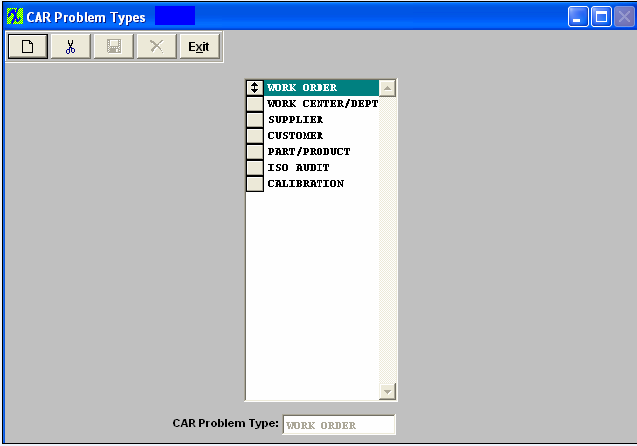
To Add CAR Problem types, depress the Add button, and enter the type in the text box at the bottom of the list.
These items may be sorted in any order by clicking on and dragging the box on the left side, to the (vertical) position desired. This order will be the order displayed in the pull downs when using this list in other modules within the system. Suggestion: Have the one most used at the top of the list.
Where Used: In all Corrective Action activities.
«Mark as Completed in RoadMap in Section B Item 3-i»
|
1.12. Corrective Action Reporting Number Types | |
1.12.1. Prerequisites for CAR Number Types |
Complete the attached worksheet and " Mark as Completed RoadMap Section B Item 3-j" before continuing the setup.
User MUST have full rights to the "System Setup" in System Security to setup these modules. User with "Supervisor Rights" will automatically have access.
|
1.12.2. Introduction for CAR Number Types | This Corrective Action Reporting number type refers to the number of the document that resulted in the corrective action. While the Corrective Action Reporting itself has a number assigned to it, there is usually another document that originates the corrective action. This document may be an RMA (Returned Material Authorization) report from the customer (e.g. RMA # 0112), and the Corrective Action Reporting Number type would be “RMA Number”. The source document may be a DMR (Discrepant Material Return) originated by production inspection or incoming inspection. The Corrective Action Reporting number type would be “DMR Number” to describe the number identified in the Corrective Action Reporting report. The number type is used solely to identify the source of the numbered document referred to in the Corrective Action Reporting.
|
1.12.3. Fields & Definitions for CAR Number Types | 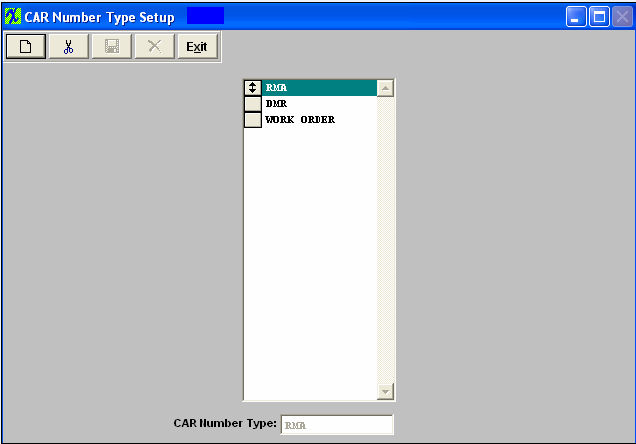
This Corrective Action Reporting number type refers to the number of the document that resulted in the corrective action. While the Corrective Action Reporting itself has a number assigned to it, there is usually another document that originates the corrective action. This document may be an RMA (Returned Material Authorization) report from the customer (e.g. RMA # 0112), and the Corrective Action Reporting Number type would be “RMA Number”. The source document may be a DMR (Discrepant Material Return) originated by production inspection or incoming inspection. The Corrective Action Reporting number type would be “DMR Number” to describe the number identified in the Corrective Action Reporting report. The number type is used solely to identify the source of the numbered document referred to in the Corrective Action Reporting. |
1.12.4. How To ..... for CAR Number Types |
1.12.4.1. Setup CAR Number Types Module |
Enter System Setup/Production/CAR Number Types Module |
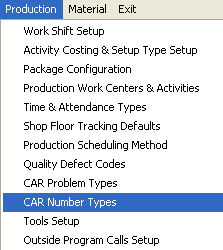 |
The following screen will appear:
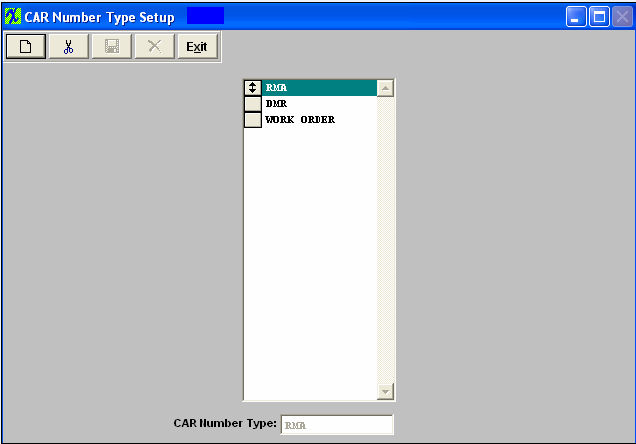
To add CAR Number types, depress the Add button, and enter the type in the text box at the bottom of the list.
The user must Save or Abandon changes.
These items may be sorted in any order by clicking on and dragging the box on the left side, to the (vertical) position desired. This order will be the order displayed in the pull downs when using this list in other modules within the system. Suggestion: Have the one most used at the top of the list.
Where Used: In all Corrective Action activities.
«Mark as Completed in RoadMap in Section B Item 3-j»
|
1.13.1. Prerequisites for Tools Setup |
Complete the attached worksheet and " Mark as Completed RoadMap Section B Item 3-k" before continuing the setup.
User MUST have full rights to the "System Setup" in System Security to setup these modules. User with "Supervisor Rights" will automatically have access.
|
1.13.2. Introduction for Tools Setup |
It’s for non recurring charges relating to tools or fixtures, etc. purchased for a particular make assembly.
|
1.13.3. Fields & Definitions for Tools Setup | 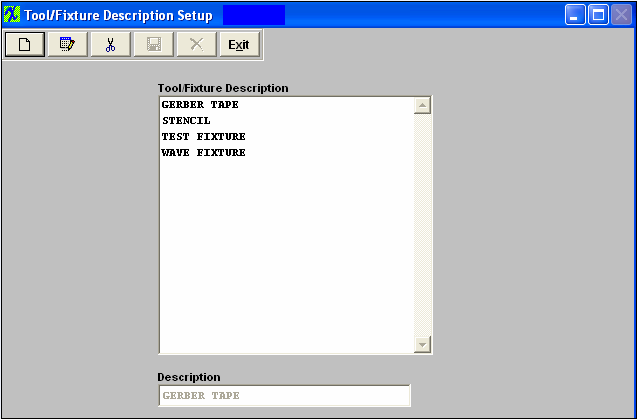
These are the descriptions to be selected from in the NRE (Non-Recurring Charges relating to Tools and/or Fixtures) section of the Customer Quote module.
|
1.13.4. How To ..... for Tools Setup |
1.13.4.1. Setup Tools Setup Module |
Enter System Setup/Production/Tools Setup Module |
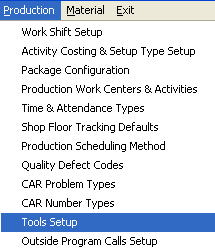 |
The following screen will appear:
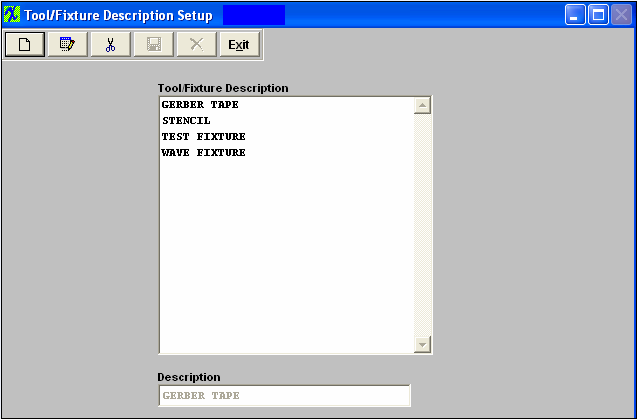
To Add, depress the Add button. Type in the description. To Edit, depress the Edit button. Highlight the description to be edited. Make any changes.
To Delete, depress the Delete button. Highlight the item you want to delete.
Where Used: Customer Quote module.
« Mark as Completed in RoadMap in Section B Item 3-k»
|
1.14. Outside Program Calls Setup | |
1.14.1. Prerequisites for Outside Program Calls Setup |
Complete the attached worksheet and " Mark as Completed RoadMap Section B Item 3-l" before continuing the setup.
User MUST have full rights to the "System Setup" in System Security to setup these modules. User with "Supervisor Rights" will automatically have access.
|
1.14.2. Introduction for Outside Program Calls Setup | User can enter a program within this screen which is used to create a button that will appear in the Shop Floor Tracking module. In Shop Floor Tracking, when user depresses this button, they will need to enter a serial number, the program will then gather all the part number, work order information into a text file, and the user defined program will use the text file to print the label.
|
1.14.3. Fields & Definitions for Outside Program Calls Setup | 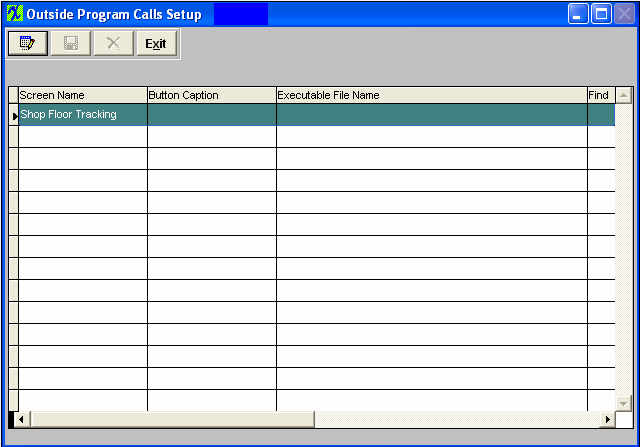
This screen is used to create a button which will appear in the Shop Floor Tracking module. The button will direct the program to a user written program which is used to print labels for serialization.
The system automatically enters the screen name as Shop Floor Tracking. Then the user types in the Button Caption and the name and path of the executable file.
|
1.14.4. How To ..... for Outside Program Calls Setup |
1.14.4.1. Setup the Outside Program Calls Setup Module |
Enter System Setup/Production/Outside Program Calls Setup Module |
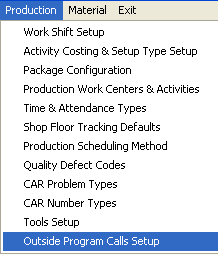 |
The following screen will appear:
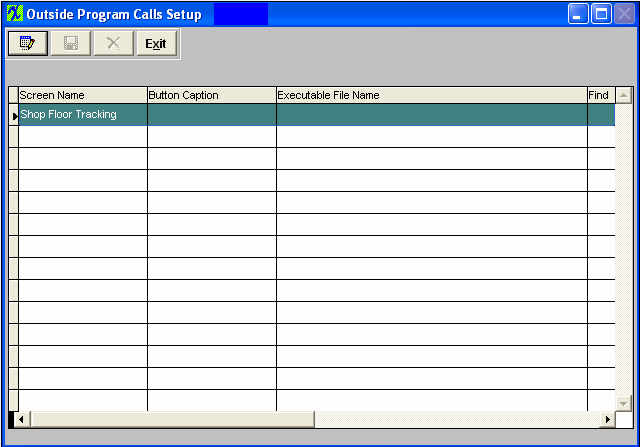
The system automatically enters the screen name as Shop Floor Tracking. Depress the Edit button to enter in the caption you want to appear in the Shop Floor Tracking module, then enter in the executable file name.
If you don’t know the executable file name, double click on the Find column. The browse window will appear:
Select the correct directory. Highlight the file name, the file name will appear in the File name field. Depress the "OK" button and the exe file name will default into the Outside Program Calls Setup screen
The user must Save or Abandon changes after entering the Edit mode.
If the user Saves the changes. A button will be created in Shop Floor Tracking with the Button Caption name entered in the Setup screen:
When user depresses this button, the following screen will appear and they will need to enter a serial number, the program will then gather all the part number, work order information into a text file, and the user defined program will use the text file to print the label.
Where Used: Shop Floor Tracking module.
« Mark as Completed in RoadMap in Section B Item 3-l»
|
|