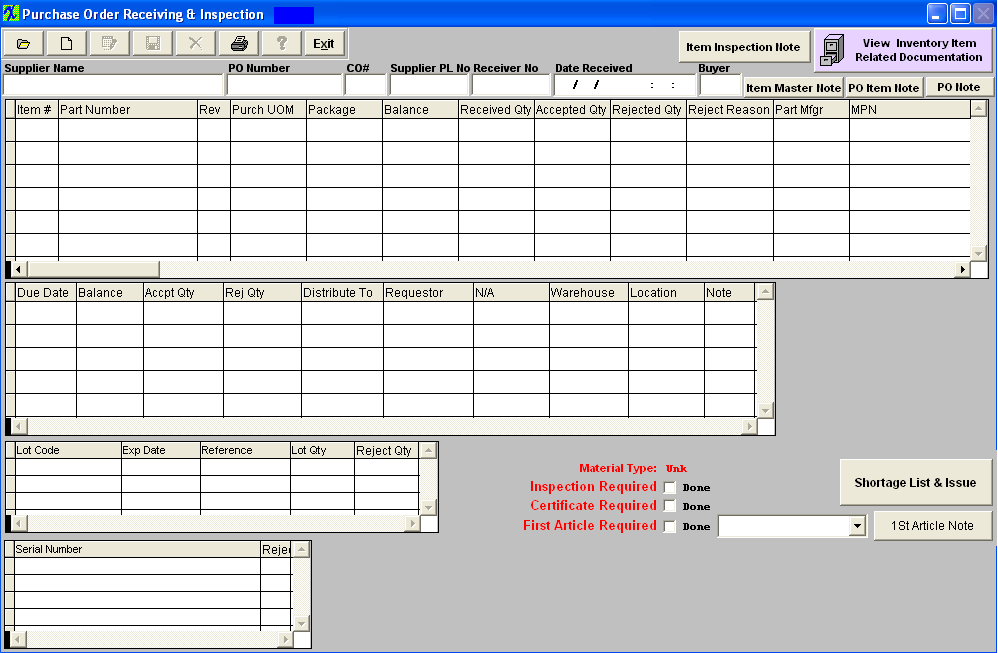
Supplier Name |
The supplier or vendor with whom the order was placed. |
P O Number |
The Purchase Order number of the order. |
CO Number |
The Change Order revision status of the order placed. |
Supplier PL No |
The number of the supplier’s Packing List. |
Receiver No |
The Purchase Order Dock Receiving number. |
Date Received |
The date the Purchase Order Receiving was completed. |
Buyer |
The initials of the buyer for the order. |
Item |
The Purchase Order Item Number. |
Part Number |
The number the user has assigned to the part. |
Rev |
The revision number assigned to the part. |
Purch UOM |
The Purchased unit of measure. (May be different than stocking unit of measure). |
Package |
The package type assigned to part in Inventory Control module. |
Balance |
The un-received quantity. |
Received Qty |
The quantity received in Purchase Order Dock Receiving. See Article #1240 for more detail on why the system will not allow user to enter in a fraction of a number, and an alternative. Note: Users must have special access in order to receive overages, There is a checkbox to allow overages within Security/User Rights for PO Receiving. Note: The overage is applied to the entire PO order qty - it does not go down to the schedule level. Example: If you have an order qty of 100 and an allowed overage of 5% the system will allow you to receive in a total overage of 105. But if you have only scheduled a qty of 25 and go to recieve in qty of 30 the system will allow you to do so, because it has not met the order overage yet. |
Accept Qty |
The quantity accepted within Purchase Order Receiving. |
Reject Qty |
The quantity rejected. |
Reject Reason |
The rejection reason Pull down list, (which is created within the System Setup Return/Shortage Reasons), is to allow the users to be able to select the Reject Reason code rather then writing notes and to be more consistent. |
Part Mfgr |
The manufacturer for the part. |
MPN |
The manufacturer part number. |
Description |
The description pertaining to the part number. |
For the Highlighted Line Item:
Due Date |
The date the item was due to the user’s dock. |
Balance |
The un-received balance of the order. |
Accept Qty |
The quantity accepted in Purchase Order Receiving. |
Reject Qty |
The quantity rejected which will be placed in the Material Review Board warehouse. |
Distribute To |
This is classification of the distribution of the item when received, either to regular Inventory Receiving or to Allocate to a specific Work Order or Project. |
Requestor |
On MRO and Services Purchase Orders, the name of the requestor is indicated. |
N/A |
For future use. |
WO Number |
The number of the Work Order for which the item was purchased. |
Warehouse |
The name of the warehouse where the accepted quantity will be placed. |
Location |
The specific location within the warehouse. |
Note |
Schedule notes pertaining to that specific item and scheduled date. |
Material Type |
The material type listed is at the AVL level |
Inspection Required |
This will be visible ONLY when selected in the Inventory module. Check box when complete. If box is NOT checked user will NOT be able to save record. |
Certificate Required |
This will be visible ONLY when selected in the Inventory and/or PO module. Check box when complete. If box is NOT checked user will NOT be able to save. |
First Article Required |
This will be visible ONLY when selected in the Inventory module. Check box when complete. If box is NOT checked user will NOT be able to save record. |
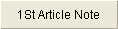 |
Enter any special notes pertaining to the 1st article. |
Lot Code |
Lot Code number assigned to part. |
Exp. Date |
Expiration date of Lot Code. |
Reference |
User assigned number or code for reference |
Lot Qty |
Qty of parts lot includes. |
Reject Qty |
Qty of parts rejected out of lot. |
Serial Number |
Serial numbers assigned to parts. |
Reject |
Check box if that serial number is being rejected. |
Insp Exception Note |
This information is displayed as reference information for processing the Receipts through the system. |
Insp Excep Doc. |
This information is displayed as reference information for processing the Receipts through the system. |
Directive Buttons:
|
The Item Inspection Note screen will be editable in the Add/Edit mode within the PO Receiving module (not editable when in view mode). This button will turn Red when information has been entered. The information added in the PO Receiving module will also be viewable in the Purchase Order module.
|
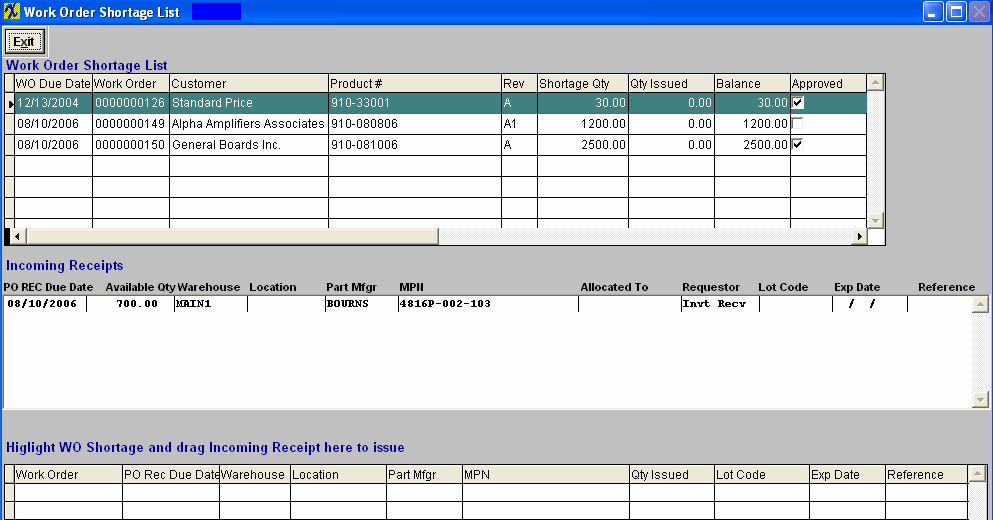
The system shows all the shortages for the part that is received, if:
- the WO is not closed or cancelled
- the WO balance is more than 0
- the kit line "Ignore Kit" flag is not on
- the Kit status is "Released"
It is up to the user to decide which receipt has to be applied to which shortage.
Work Order Shortage List field definitions:
Work Order Due Date |
The date the Work Order was due to be completed and ready to ship. |
Work Order Number |
The number of the Work Order. |
Customer |
The name of the customer listed on the Work Order. |
Product Number |
The Product number listed on the Work Order. |
Revision |
The revision listed on the Work Order. |
Shortage Quantity |
The amount of the Work Order shortage. |
Qty Issued
|
The quantity issued to the Work Order shortage. System does not allow you to issue quantities greater than the shortage quantity. For more detail see Article #2479.
|
Balance
|
The balance of the shortage after issuing parts to WO.
|
Approved
|
This will be checked if the AVL that you are receiving is an approved AVL for that shortage. This will give the users the needed information on screen to make the decision to use or not use a non-approved AVL to fulfill a shortage.
|
Incoming Receipts field definitions:
PO REC Due Date |
The date the Purchase Order Receiving was completed. |
Available Qty |
The quantity accepted within Purchase Order Receiving. |
Warehouse |
The name of the warehouse where the accepted quantity will be placed. |
Location |
The specific location within the warehouse. |
Part Mfgr |
The manufacturer for the part. |
MPN |
The manufacturer part number. |
Allocated To |
If the parts have been allocated to a WO or project when PO was created. |
Requestor |
On MRO and Services Purchase Orders, the name of the requestor is indicated. |
Lot Code |
Lot Code number assigned to part. |
Exp Date |
Expiration date of Lot Code. |
Reference |
User assigned number or code for reference |
Highlight WO Shortage and drag Incoming Receipt here to issue field defintions:
Work Order |
The number of the Work Order. |
PO Rec Due Date |
The date the Purchase Order Receiving was completed. |
Warehouse |
The name of the warehouse where the accepted quantity will be placed. |
Location |
The specific location within the warehouse. |
Part Mfgr |
The manufacturer for the part. |
MPN |
The manufacturer part number. |
Qty Issued |
The quantity issued to Work Order Shortage |
Lot Code |
Lot Code number assigned to part. |
Exp Date |
Expiration date of Lot Code. |
Reference |
User assigned number or code for reference |
|