Following a logical sequence when adding items into the Inventory Master not only eliminates lost time due to continual back-tracking, but ensures that decisions will be made in a sequence which will support the data entry process.
The sequence shown below is for adding products, parts, assemblies, subassemblies or Phantoms to the Item Master after completion of System Setup.
-
Search whether item already exists. Use Find an Inventory Control Part to search the existing database along with the archived database, to verify that the items to be added do not already exist.
-
Verify Available Class and Type. Use Find an Inventory Control Part by Class and Type to verify that the item to be added will fit into the existing Class and Types . Refer to System Setup, Inventory Part Class if a new Part Class or Type and the corresponding Data Entry Defaults must be added.
-
Is Customer available? If the items to be entered will have a Customer-Specific Approved Vendor List (Approved Vendor List), then verify that the Customer is in the database using Customer Information. Add the Customer Information if it is not there.
-
Does Manufacturer exist? Use Part Manufacturer Setup to view existing Manufacturers. Enter new Manufacturers for Buy Items as required and enter the Source for Fabricated items being purchased as outside purchased assemblies. Please refer to procedures below.
-
Add a part/product, etc. Depress the Item Master screen tab. Use the Add button to enter the stand-alone product number or the top level assembly number for a Bill of Material (BOM) MAKE item that must be added. If the product is purchased complete and has no BOM, enter it as a BUY item. Enter your Password.
-
Enter information. Enter all basic item information in the Item Master Screen.
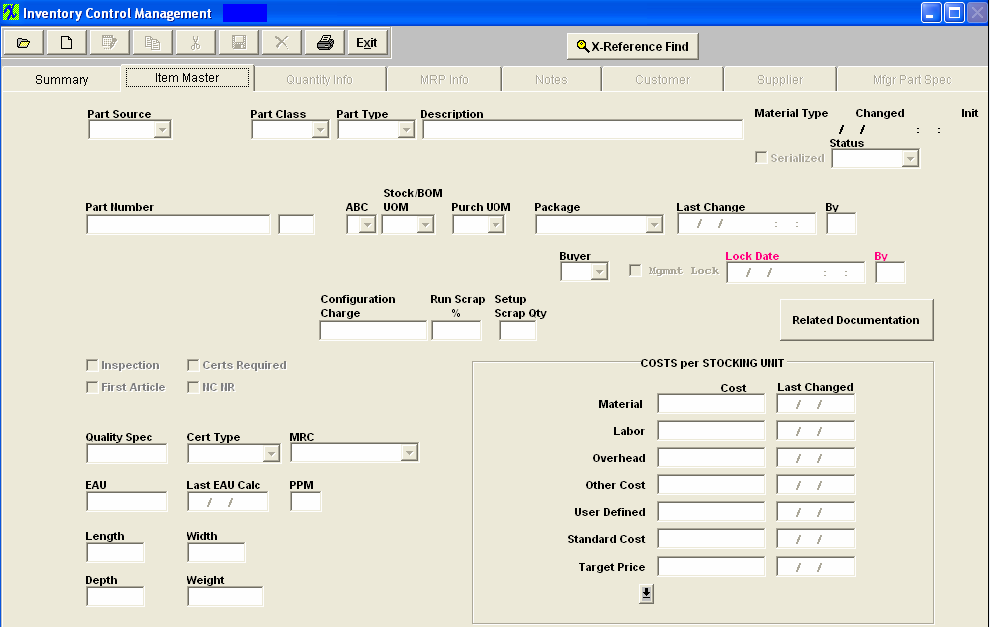
Part Source: This field is hard coded in the system. Select BUY for purchased parts and assemblies, MAKE for an item made in-house (assemblies and sub-assemblies) and PHANTOM for a number used to define a collection of items that does not exist as a separate assembly built on a Work Order (ship kits, upgrade packages, spares kits, etc.).
|
 |
-
Phantom/Make: If the Part Source above is a MAKE and this box is checked, the system will treat the part as a Phantom when the sub-assembly components are called up during the Kitting process BUT as a Make part for a stand alone assembly when the part is NOT a sub-assembly.
-
Make/Buy: Make/Buy is setup to allow users to have a part in the system that they wished to BUY but also keep documentation within the system (BOM). If the Part Source is a MAKE and this box is checked, the assembly could also be purchased from an outside source. If a Part is marked as Make/Buy within Inventory the MRP will only give PO Actions and that product will not be available for selection within the Work Order management module. If the part souce on a product is originally setup as a MAKE the user will be allowed to edit the record and change the part souce to Make/Buy. For further details see Article #3289 .
Part Class: This is a general part, product or item classification that must be selected from the drop-down box. If an appropriate choice is not available when entering a new item, see System Setup/Inventory Part Class to add a part class (examples of Part Classes are BATTERY, DIODE, FUSE, FILTER, IC-SMT, CAP-SMT, RES-TH, etc.)
|
|
Part Type: Type is a sub-classification of Part Class. If an appropriate choice is not available when entering a new item, see System Setup/Inventory Part Class to add a Part Type (examples of Part Types for the Class CAP-SMT would be 0402, 0603, 0805,1206, 1210, etc.)
To re-sort the order the part types are being displayed in the pulldown See Article #214
A user does have the option of leaving the Part Type blank, however if this option is selected the prefix for the part number will be omitted. There is no reason to enforce part type if a user doesn’t want to have that kind of detailed classification. If the user decides to leave the Part Type blank they will receive the following message:
At this point they have the option to continue or go back and pick a Part Type.
|
|
Description: There are 45 characters available to put descriptive data about the item being entered that is not already in Part Class and Part Type. For instance, in the previous figure the Part Class and Type already show that it is a CAP-SMT. 0603 so this information need not be repeated in the Description. We suggest when entering the description, that you be consistent with your capitalization and punctuation. Some of the screens and reports can be sorted by description so the more consistent you are the easier it will be to use the system in the future.
 |
If the Inventory Material Type is set to "Auto" (within the Material Type Setup), everytime the user modifies the AVL material type, the program will update the Inventory Material Type automatically, if the control is set to "Manual", then the user will be able to modify the Inventory Material Type from the Material Type pulldown. Keep in mind that the program will NOT validate if the material type in Inventory and AVL levels are in sync.
The AVL Material Type is carried forward for the consign part when the consign part is first added to the system or when new AVL was added to the internal part and the user elects to add this AVL to the existing consign parts. If the user later changes the Material Type on the internal part, the change is NOT carried over to the consigned.
|
Serialized: Check this box if the parts need to be tracked with serial numbers. This box will allow you to mark either Make or Buy parts as Serialized.
Note :Users MUST have special access with the Security module for the Inventory Control module to modify the serialized checkbox.
When the serialized checkbox is checked for an existing BUY part and there is open kit records in the system the following message will appear:
|
|
When serialized checkbox is checked for an existing MAKE or BUY part and there are open work orders or inventory against it the following message will appear: |
 |
If user checks the Serialized box and receives the following message, this means that the "Do not use serial number tracking" checkbox is checked within SFT Setup.
|
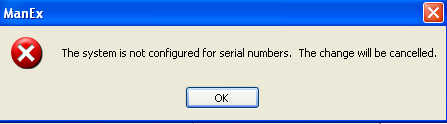 |
Depress Yes and the following screen appears
If user doesn' t know the available work orders which have FGI qty, he/she can double click the work order number field (red box).
|
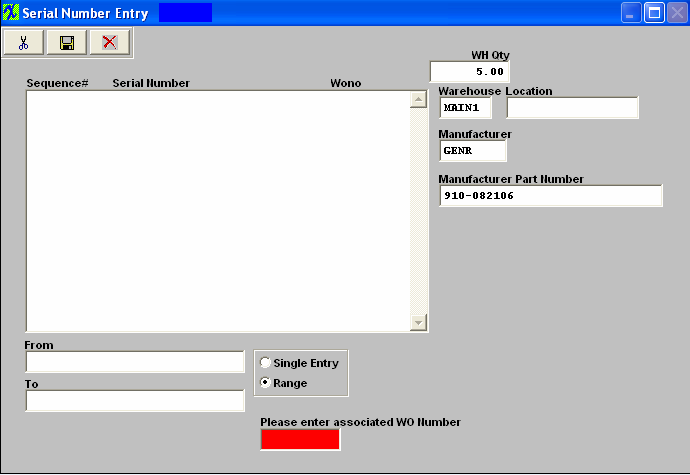 |
A list with work order numbers and FGI qty for that part number will appear (as shown below). The user then can select one for entering serial numbers.
|
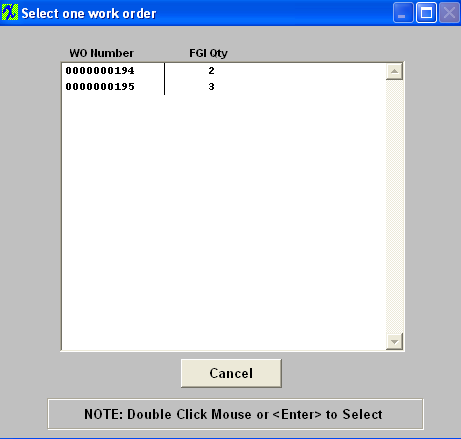 |
The users can enter the serial numbers by clicking "single" or "range" option.
Once all the serial numbers have been entered for all work orders the completed screen will look like this.
Depress the Save button.
|
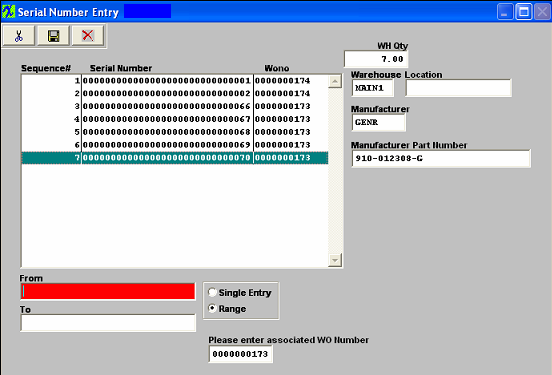 |
The following message will appear reminding the user that they will need to assign serial numbers to the balance of the work orders in order to transfer to FGI.
|
 |
Status: All items must be Active in order to buy, receive, issue, Invoice, or ship. Use Inactive Status to remove items from use that have already had transactions against the Part Number. Use the Delete button to delete Items with no transactions for further detail see Article #3143. Changing from Inactive to Active status can be used to release items from Engineering. The system will not allow you to change the status from Active to Inactive if there is WIP for that item. This will prevent the possibility of qty on hand being returned to an inactive part upon dekitting.
|
|
Part Number: The item/Part Number is a unique identifier for every Item Master record entered into the database. Part Numbers can be auto-assigned to all items or all items except Make assemblies or all items including Make Assemblies. Use of a 3-digit prefix for each different Part Type may be setup in System Setup Number System to work with auto or manual numbered parts and assemblies..
ABC: This field allows further grouping of items (parts, products or assemblies) into classes according to: 1) the percent of the total inventory their current stock value represents.2) the percent of total inventory their forecasted value will represent.3) a manual classification based upon chosen factors. If an appropriate choice is not available when entering a new item, see System Setup ABC Types to add a new Type.
|
|
Stock/BOM UOM: This is the Unit Of Measure (Foot, Inch, Each, Gallon, Quart, etc.) that is used to specify how much of Item displayed or being entered is issued from Stock or is used in a Bill of Material for an assembly. Note that in ManEx, the Unit of Measure Each is treated as being an integer unit. That is, you can only have one or multiples of an Each, but not a fraction of an each. You can have fractions of inches, feet, pounds, ounces and any other Unit of Measure. Although you can use fractions in the Bill of Material, the User can't kit fractions of each parts. ManEx will round up to the nearest whole number. The proper way to approach the situation where the kit amount is expressed in fractions, is to use any Unit of Measure other than Each. If an appropriate choice is not available when entering a new item, see System Setup/Unit of Measure & Conversion to set up a new Unit of Measure.
ManEx DOES NOT recommend users to change the Unit of Measure while there is qty on hand within the system. See Article #3414 for further detail.
|
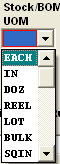 |
Purchase UOM: This is the Unit Of Measure (Foot, Inch, Each, Gallon, Quart, etc.) that is used to specify how the Item displayed or being entered is purchased from a vendor. If an appropriate choice is not available when entering a new item, see System Setup/Unit of Measure & Conversion to set up a new Unit of Measure.
ManEx DOES NOT recommend users to change the Unit of Measure while there is qty on hand within the system. See Article #3414 for further detail.
|
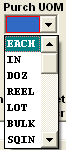 |
Package: Specifies the way in which the Item is packaged when it comes from a vendor (ie. Reel, Tray, 6-Pak, Ream, Individually, etc.) If an appropriate choice is not available when entering a new item, see System Setup/Part Package to set up additional part packaging. |
|
Buyer: All items with the same Buyer's initials in this field will be grouped together for display or printout of the Material Requirements Planning Action List when filtered or displayed by Buyer. If an appropriate choice is not available when entering a new item, see System Setup/Inventory Buyer Setup to set up additional buyers. |
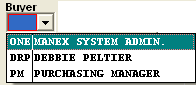 |
Last Change |
This automatically defaults in the date and time of the last change made to this part number in the item master. Once the change has been saved.
|
By |
This automatically defaults in the initials of the user that made the last change to this part in the item master. Once the change has been saved.
|
Configuration Charge |
This is NOT a part of the standard cost total, as discussed below.It is a specific cost used with the ManEx Order Configurator module and represents any additional cost over and above the standard cost total.
|
Run Scrap % |
This amount is added to the exact quantity used on an assembly to provide an overage to cover losses during running due to predictable machine and human losses.
|
Setup Scrap Qty |
Setup losses may be added to the BOM requirement and Run Scrap for an item.For instance, an auto-insertion machine may use extra parts for alignment checks. |
Mgmt Lock: Only Supervisors or users with Lock/Unlock rights within the Security/User rights can modify this checkbox. If locked, all users can access the screen, but only supervisors or those with Lock/Unlock rights will have the capability to bypass the lock and make changes, while the Inventory Part is still in lock mode. The reason we do NOT force the user to unlock the Inventory Part before making any changes, is to protect it from anyone else making changes while the 'authorized" user is making their changes.
Lock Date: This automatically defaults in the date and time the lock was implemented to this part number in the item master.
By: This automatically defaults in the initials of the user that implemented the lock to this part number in the item master.
|
|
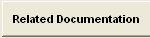 |
Depressing this button will give the users the ability to scan any related documents directly into the ManEx system and attached the document directly to the item in the ICM Module. For further detail see Article #2396. If this button is displayed in Red there is Related documents attached. |
Inspection Required/ Quality Spec |
Checking the box will cause the item to require inspection to whatever Quality Spec. shows in the Quality Spec box. The Quality Spec appearing in the box is entered in System Setup in the Inventory Part Class & Type Setup.Any Part Type in a particular Part Class can have Inspection Required turned on or off.
|
Certs Required/ Cert Type: Checking this box will allow selection of Cert Type. Cert Type choices are Receive, Ship or Both. A typical Cert would be UL or CSA Certification on wire. Check the box and then depress the down arrow for the types to display. Select the desired type: Receive - Requires user to check the "Certificate Required" box has been Done at Receiving. Ship - Requires user to check the "Certificate Required" box on Packing List/SHipping. Both - Requires user to check the "Certificate Required" box at both Receiving and Packing List/Shipping. |
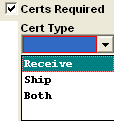 |
MRC |
This is to inform the users which items are Low Risk, High Risk, etc.This will need to be defined in System Setup Material Risk Code Setup.
|
EAU/Last EAU Calc |
These fields display the Estimated Annual Usage, if applicable and the last date that the EAU was calculated.
|
PPM |
This field is a data entry field and is not currently involved in any calculations or used anywhere else within the system at this point. It is planned to be used in the future to calculate the component level of PPM and then update the assembly PPM within the routing module.
|
The dimensions such as Length, Width, Depth and Weight are entered in this section |
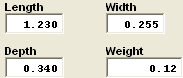 |
Within Security there is the option to allow users to have access (all or partial) to the Inventory Control Management module. Then within those Inventory Security settings there is a provision for optional additional privileges, including the ability to make changes to the Standard Costs. Only a user with these rights will be allowed to change any of the costs listed below. Also, none of the cost listed below will be editable if there is inventory or WIP on hand.
Material Cost
|
For BUY Parts: This is the purchase price of the BUY part. For MAKE Parts: The sum of the STANDARD COSTS of BUY parts in the assembly. Whether or not setup scrap is included is a system setup option |
Labor Cost |
For BUY Parts: If the user wishes to include any preparation labor costs associated with a BUY part, like crimping, tinning testing. etc., those costs may be included here. For MAKE Parts: The user may include the labor associated with building the assembly.
|
Overhead Cost |
For BUY Parts: Any additional costs associated with the labor, such as heating, lighting, etc., that the user may wish to include in the cost of the inventory value. For MAKE Parts: Any additional costs associated with the labor, such as vacations, sick leave, meeting times, etc., that the user may wish to include in the inventory value. |
Other Cost |
For BUY or MAKE Parts: This is up to the user to decide if there are any other costs that should be absorbed in the inventory value. |
User Defined Cost |
For BUY or MAKE Parts: This is a field where a user may define the field name and include any optional costs. |
Standard Cost |
The STANDARD COST of an item is a calculated value determined by the sum of individual costs. These individual costs may be in any combination of the Material, Labor, Overhead, Other and User Defined costs. Each of the individual costs should have their own account number in the Inventory setup, and those accounts will accrue the costs when material is added to inventory.
If ManEx Accounting is neither installed nor active, then there is no value other than reference in including values in these fields.
Important Notice: It is very important to have standard costs (as determined above) in place for any part entering inventory. ManEx allows users to enter a standard material cost at the time of purchase, if one is not already entered. Without accurate cost data, the iventory value could be next to useless, and major variances would show in Purchase Price, Configuration and Manufacturing Variances.
|
Target Price |
This field is currently only a data entry field and will be reflected in the Purchase Order module for "BUY" or "MAKE/BUY" parts. This field is not editable for "MAKE" or "PHANTOM" parts. NOTE: To assign prices to products ("MAKE" parts), ManEx suggests using the Sales Price List Information module. This module allows users to enter prices by product and by customer so different customers can have different prices. This price will default into the sales order, but is still editable within the Sales Order module.
|
Weighted Cost |
If the Part Source is a BUY, the last five purchases expressed as a weighted average will appear here.
|
The completed Item Master screen will appear:
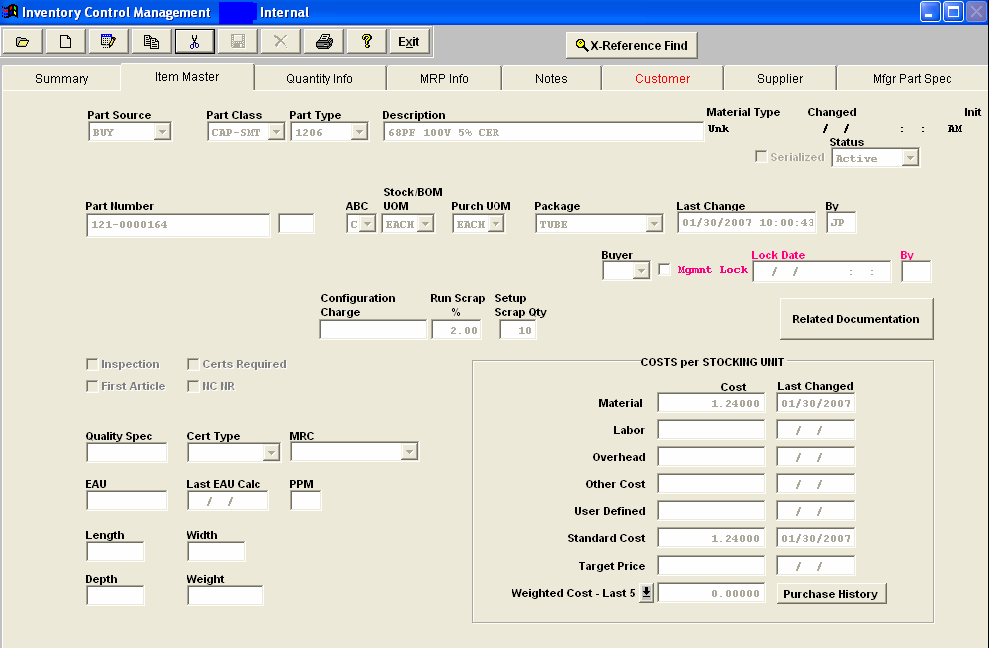
Click on the Quantity Info tab and the following screen will appear. This screen is split. You must enter in the manufacturer information and click save. Then the system will allow you to add the warehouse and location information.
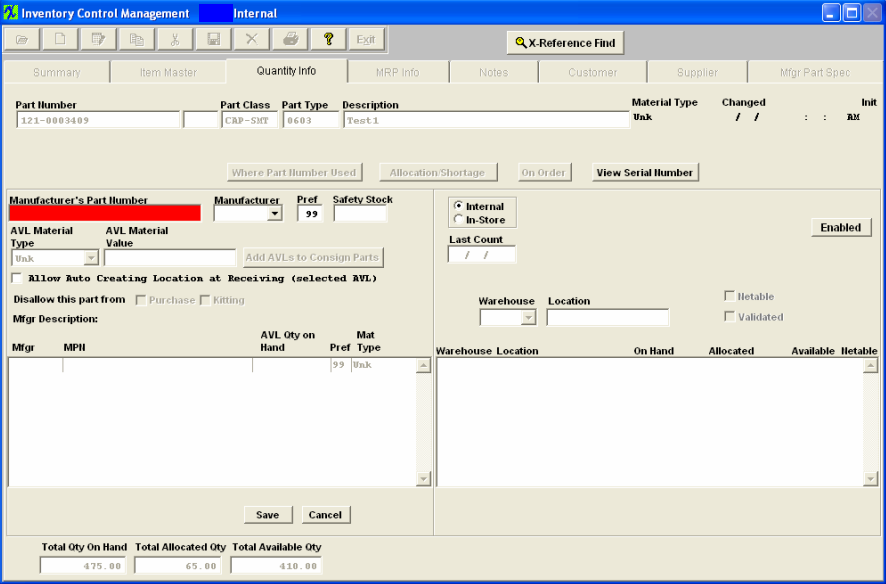
If the Inventory Material Type is set to "Auto" (within the Material Type Setup), everytime the user modifies the AVL material type, the program will update the Inventory Material Type automatically, if the control is set to "Manual", then the user will be able to modify the Inventory Material Type from the Material Type pulldown. Keep in mind that the program will NOT validate if the material type in Inventory and AVL levels are in sync.
The AVL Material Type is carried forward for the consign part when the consign part is first added to the system or when new AVL was added to the internal part and the user elects to add this AVL to the existing consign parts. If the user later changes the Material Type on the internal part, the change is NOT carried over to the consigned.
|
 |
Enter Manufacturers Part Number: Type in the manufacturers part number.
Enter Manufacturer: Choose a mfgr from the pull down. If no Manufacturer is specified use GENR (Generic). If no information is entered in the Quantity Info screen, GENR will be added by the system automatically when saving the item.
System will not allow users to have duplicate AVL/MPN combinations. If user has same mfgr and mfgr PN but different material types, we suggest that the user create a new AVL with a dash (or any other symbol) and use that designation to transfer to the UNK material type parts or create a different location for the same part, but have it be non-nettable, making it ineligible as a source for MRP.
|
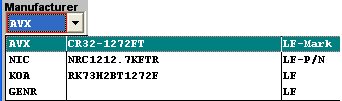 |
Enter Pref: Type in the Preference. (Whether this is a preferred manufacturer and if so the ranking or preference). If no preference code is added, 99 will be assigned automatically. All items will be at the bottom of the preference list unless the user assigns another number to it. See Article 943 for more information. The Pref Code is carried forward for the consign part when the consign part is first added to the system or when new AVL was added to the internal part and the user elects to add this AVL to the existing consign parts. If the user later changes the preference code on the internal part, the change is not carried over to the consigned part.
Enter Safety Stock: Enter in a qty that you want kept on hand for this specific AVL. (User may have safety stock for more than one AVL in a given part number). This qty is in addition to the MRP demands. (Note: Safety stock is calculated at the AVL level not part # level). ManEx will ensure that there is always the safety stock qty on hand regardless of the MRP demands. Please see Article #2331 for more detail.
If this option is check marked then the users will be able to automatically create any new Location for this part within the PO Receiving module. Note: Users MUST have special access within the Inventory Control Security setup module to modify this checkbox. There is also a similar check box within System Setup, Warehouse Setup, this will also have to be marked for the warehouse in order for this option to be applied. |
 |
Depress the save button located at the bottom of the screen. You now have the option of entering an AVL Material Type (as described below) for the existing mfg., enter in another manufacturer part number or creating a warehouse for the existing manufacturer.
AVL Material Type: Choose from the pull down, Unk, LF-P/N, LF-Date, LF-Mark, RoHS-P/N, RoHS-Date, RoHS-Mark. See Article 2267 for definitions. These choices have been defaulted in. Customers may establish the logic by which the material type for the parts are established by the material types at the AVL level in System setup/Material Type Setup.
The AVL Material Type is carried forward for the consign part when the consign part is first added to the system or when new AVL was added to the internal part and the user elects to add this AVL to the existing consign parts. If the user later changes the Material Type on the internal part, the change is NOT carried over to the consigned part.
If the Inventory Material Type is set to "Auto" (within the Material Type Setup), everytime the user modifies the AVL material type, the program will update the Inventory Material Type automatically, if the control is set to "Manual", then the user will be able to modify the Inventory Material Type from the Material Type pulldown. Keep in mind that the program will NOT validate if the material type in Inventory and AVL levels are in sync.
|
|
AVL Material Value |
This is a text field for a given material type. For example: if the material type was "LF-Date" user could enter the date code in this field. The Value could be different of various AVL's with the same material code. This fields is a reference only field and is optional. |
 |
If the users add new AVL's to the Internal part number, they can add it to a Consigned part number by depressing this button. A screen will appear and within that screen they can select which AVL they want to add to a Customer consigned part number. |
 |
There are situations where the Users customers will allow them to use up non-conforming inventory, but cannot replace the same AVLs. So, at the AVL level, we added two logic fields that would signify that the AVL is NOT to be purchased and/or kitted. In such a circumstance, it is NOT appropriate to delete the parts, but neither can they be purchased for future requirements. Likewise, they may want to avoid kitting so you would check these boxes to "Disallow this part from Purchase and/or Kitting". For special circumstances, the user can override the block from kitting if their customer permits it. For further information on how to use these fields effectively refer to Article #2329. For information on how these fields affect MRP refer to Article #3211 . (See the non-nettable function for the warehouse level described below).
|
When the "Disallow Purchase" is checked ON - ManEx will check if any Safety Stock (SS) is entered, if so the following prompt will be displayed and will un-check the checkbox upon depressing the OK button.

When the "Disallow Purchase" is checked OFF - ManEx will check and if "Disallow Kit" is ON the following prompt will be displayed and will revert the change to leave "Disallow Purchase" ON and leave "Disallow Kit" ON.

When the "Disallow Kit" is checked ON - ManEx will check if any SS is entered, if so the following prompt will be displayed and will un-check the checkbox upon dpressing the OK button. If SS is zero, no message will be displayed and ManEx will auto check "Disallow Purchase"

When the "Disallow Kit" is checked OFF - ManEx will check and if "Disallow Purchase" is still checked ON the following message will be displayed giving the user the option to uncheck the "Disallow Purchase" but is not required.

To create a warehouse, depress the Add button (located under the right hand section of the screen)
Enter Warehouse: Select the Warehouse from the pulldown. In ManEx, the default warehouse is Main 1. If the User has accounting, this would equate to the Raw Materials Inventory. Many Users want to separate their Raw Materials and Finished Goods Inventories. So, if this is a Make part, the User may want to select the finished goods inventory warehouse. Some Users also set up separate warehouses and general ledger account numbers for In-Stores and Consigned. If no warehouse is selected upon saving the record the system will deafult in the default warehouse setup in System Setup Warehouse Setup.
|
|
Enter Location |
The location entered is where the parts will be stocked and/or located within the warehouse. System will NOT allow users to add same locations with leading spaces. This field is flagged as “Read Only” for an MRB whse item. (Meaning you can not create new locations for MRB whse). Due to the fact that the MRB location is usually generated from a PO rejection – and if so, it needs to retain that link back to the original PO information and that is populated into the location field and is not editable. If you move into MRB via Inventory Handling then no location information is populated, but you are still unable to edit it. |
Netable box |
Remove the check mark from Netable only if the item entered is NOT to be considered as Supply when running Material Requirements Planning. If the MRB whse is being added the Netable field is disabled and unchecked.
|
Validated box |
This is for reference only and does not affect any other modules in Manex. This is simply for the users to check that the part being added has been verified as appropriate.
|
Depress the Save button at the bottom of the screen.
The completed Quantity Info screen looks like this:
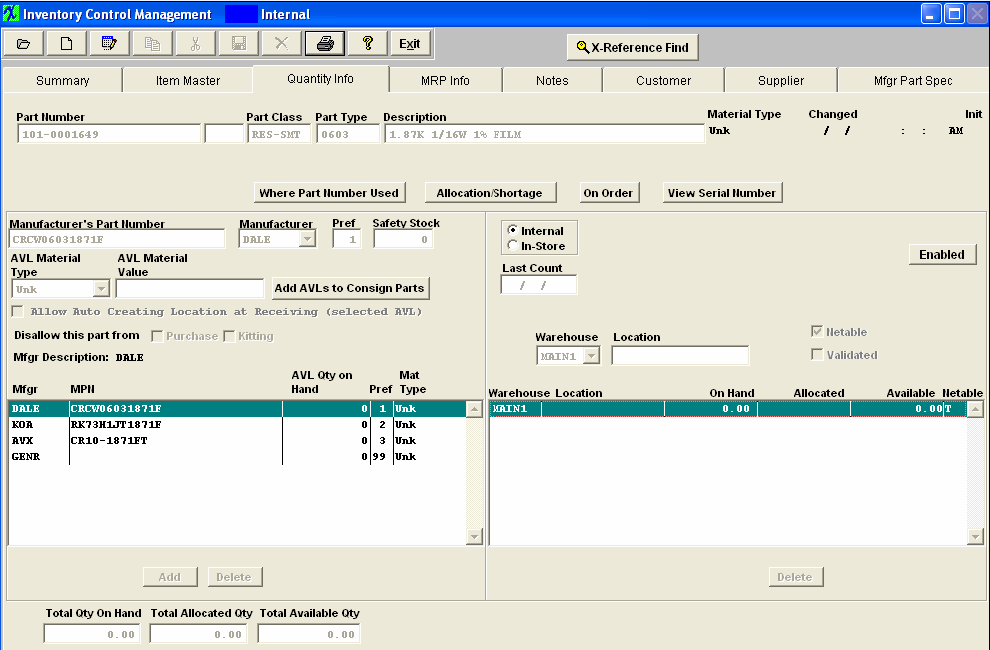
Material Requirements Planning Information: Depress the MRP tab and the following screen will appear. Enter the Material Requirements Planning information for the item.
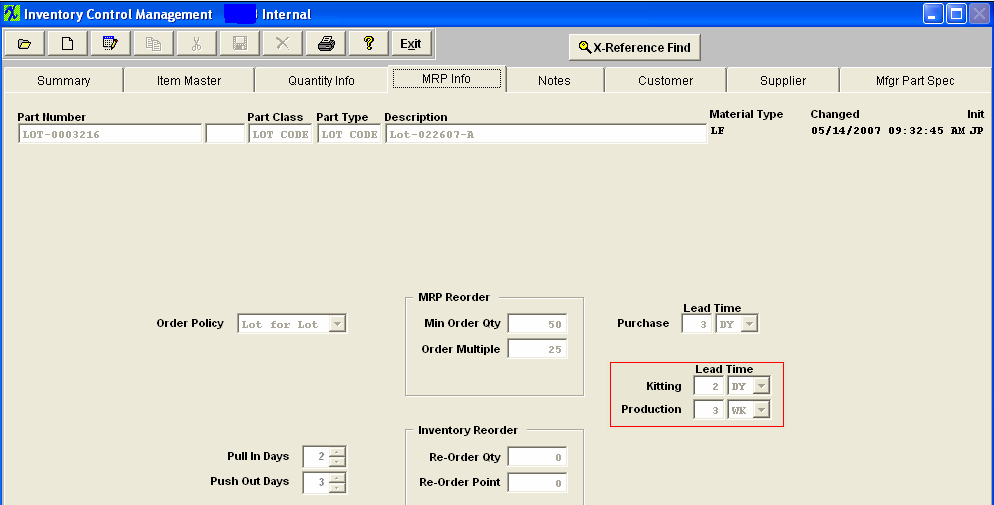
Order Policy: This field is used to select the method used by the Material Requirements Planning module to combine requirements for this item in creating Planned Purchase Orders (POs). For instance if the choice is (Lot for Lot), the Material Requirements Planning module will plan one PO for the total requirements on a daily basis. If the choice were (Weekly), the Material Requirements Planning module would combine all the requirements each week and plan one PO on the first requirement day for the entire weeks needs.
|
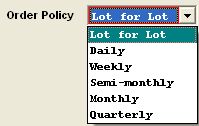 |
Min Order Qty |
This is the smallest number of the item that can be ordered from the vendor in one PO. For instance, Surface Mount components on a reel usually have a minimum order of 1000 items or more.
|
Order Multiple |
This field defines the even multiples of the Unit of Measure in which an item must be purchased. For example, 16AWG Wire might be only available in even hundreds of feet on a spool in which case the Material Requirements Planning module would plan a PO for the next higher even hundred above the requirement.
|
Purchase Lead Time: Purchase of all items other than In-Store items requires that the PO be placed a minimum number of days before the actual requirement. This Lead Time requirement is what tells the Material Requirements Planning module how many days before a requirement to plan a PO. Changing the leadtime of a Buy part will NOT change the due date in MRP, only the date to take action.
|
|
Kitting Lead Time: This field will be displayed only if it is a Make or Phantom part. This Lead Time requirement is what tells the Material Requirements Planning module how many days to allow for kitting. Changing the kitting leadtime of a Make or Phantom part will change the due date in MRP. A TRUE phantom does NOT require any lead times and should be left blank. BUT . . . if for some reason you need to add a lead time for a TRUE phantom ManEx does have the capability.
Production Lead Time: This field will be displayed only if it is a Make or Phantom part. This Lead Time requirement is what tells the Material Requirements Planning module how many days to allow for production. Changing the production leadtime of a Make or Phantom part will change the due date in MRP. A TRUE phantom does NOT require any lead times and should be left blank. BUT . . . if for some reason you need to add a lead time for a TRUE phantom ManEx does have the capability.
|
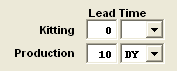 |
Pull In Days |
When PO due date is more than this number of days too late for an Material Requirements Planning module requirement, a PO Due Date change Action Notice will be generated. Note: These parameters may be thought of as filters for MRP Order Actions when the requirement dates for the parts changes. See attached Document <<pullin-pushout discussion.docx>>.
|
Push Out Days |
When PO due date is more than this number of days too early for an Material Requirements Planning module requirement, a PO Due Date change Action Notice will be generated. Note: These parameters may be thought of as filters for MRP Order Actions when the requirement dates for the parts changes. See attached Document <<pullin-pushout discussion.docx>>. |
Re-Order Qty |
This is the number of the item to order at time of order.
|
Re-Order Point |
To use a Min/Max system rather than Material Requirements Planning for reordering this item, enter the quantity at or below which the item should be replenished. Print the Inventory Material Reorder List report to show items which have dropped below re-order point minimums.
|
The completed MRP screen would appear as follows:
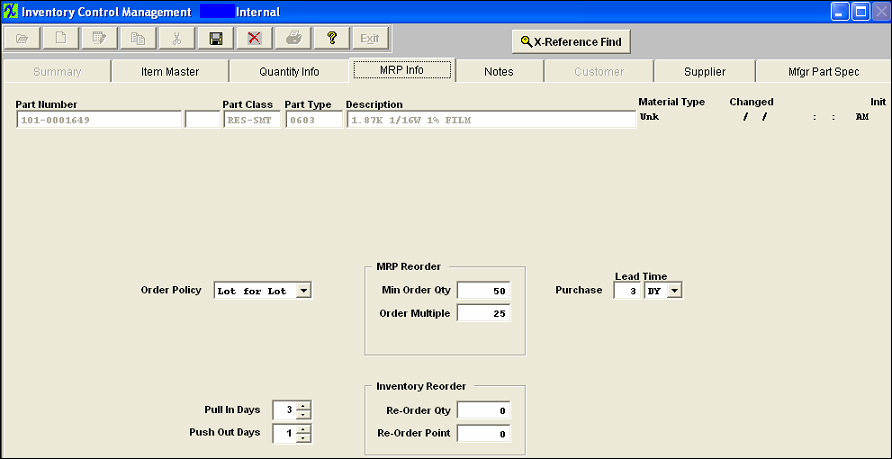
Notes Tab |
Depress the Notes tab. Add Notes by clicking the Edit Action Button and typing in manually. Use Utility/ Copy or Ctrl+C and Utility/ Paste Ctrl+V to copy and paste from the existing Item Notes to new Item Notes.
|
Depress the Customer tab. Depress the Edit button and the following screen will appear:
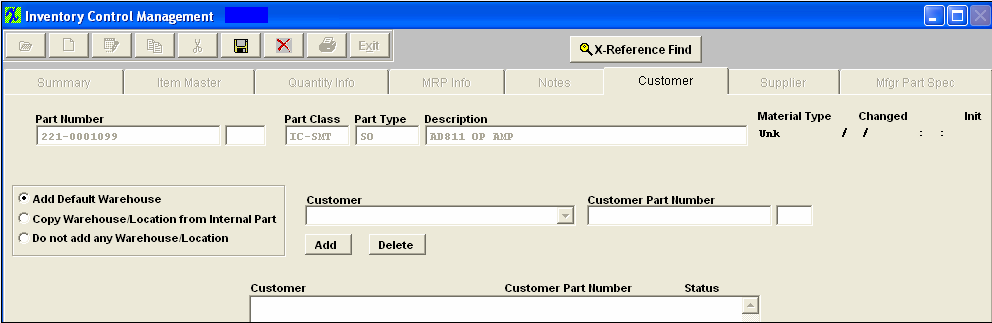
Depress the Add button (under to the Customer Field) to select a Customer. A customer list will appear. Select the customer desired. For every Customer that requires an Approved Vendor List, selection of these items Manufacturer Part Numbers list (in the Quantity Info Screen), a Customer Part Number must be entered in the Customer Screen. Enter a Customer Part Number and Save. When you create a Customer Part number (Consigned) within the system, user has the option to Add Default Warehouse, Copy Warehouse Location from Internal Part, or Do not add any Warehouse Location upon creation. Note: System does not allow you to enter more than one part number per customer to the same internal part, (for more detail see Article #2389).
|
|
Depress the Supplier tab, depress the Edit button and then the Add button (under the Supplier Field) to select a Supplier, enter a Supplier Part Number and Save.
|
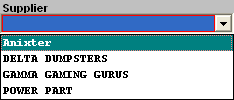 |
The completed Supplier screen would appear as follows:
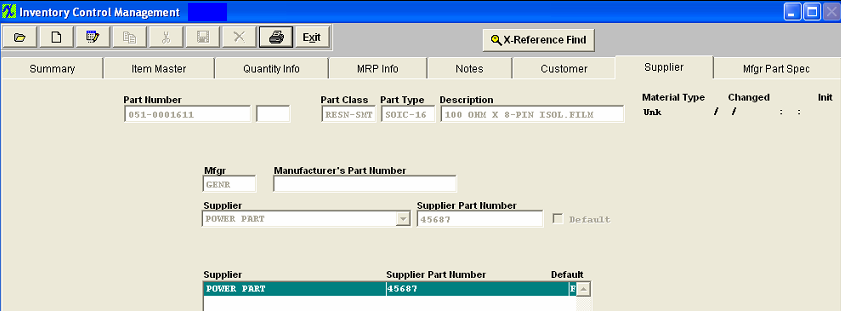
Manufacturer Part Specifications |
Depress the Mfgr Part Spec tab. Add the Marking and Package, Body and Pitch, if desired. Add Manufacturer Part Spec drawings, images or .pdf file by clicking on Load Document and linking to the desired image or pdf file. The completed screen will appear:
|
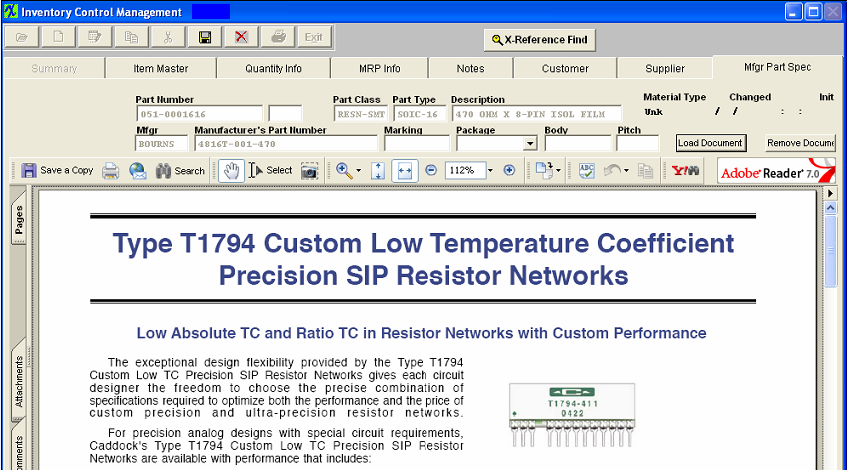
Once all information for new record has been entered, depress the Save button to save the record, or the Abandon record button to abandon record.
|