Work Order Tab field definitions
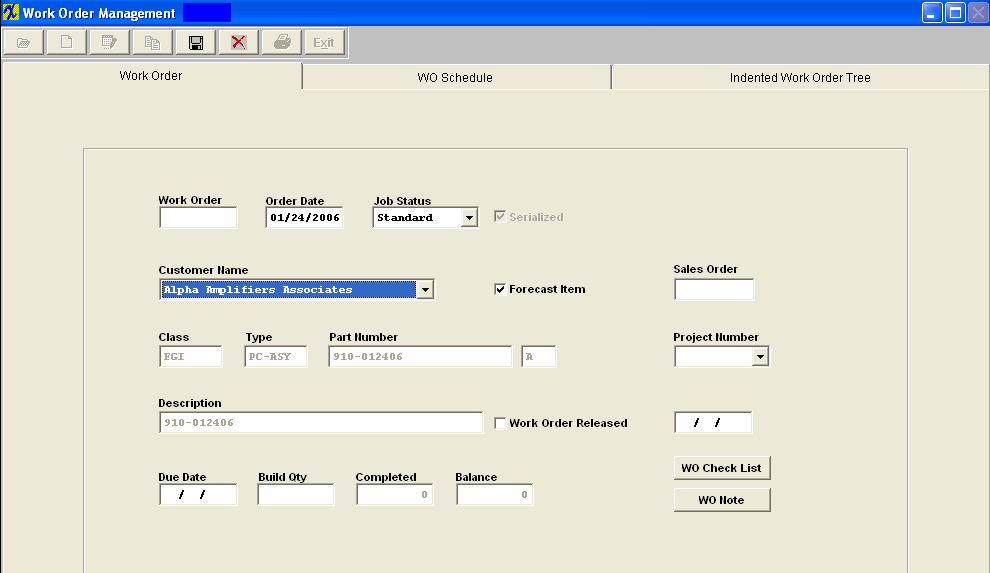
Work Order |
The number assigned to the Work Order.
|
Order Date |
The date the Work Order was created.
|
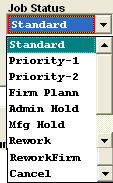 |
The status of the Work Order: Standard; Priority-1; Priority-2; Firm Plann; Admin Hold; Mfg Hold; Rework; ReworkFirm; or Cancel.
The system defaults to Standard. Standard is the ordinary work order status. Priority is set up as a make ahead of all other orders, 1 being the most important and 2, the second most important. Firm Plann, lets MRP know that the Work Order decision is intentional and NO action is required. Admin Hold is an order on hold due to customer credit, etc (this will NOT interfere with the kitting, production or shipping). Mfg Hold WILL prevent the order from being put In-Process, Kitted, or Assembled. Note: If the WO is put on Mfgr Hold before being put In-Process no demands will be displayed in MRP. Rework is to fix or redo a previous order. Rework Firm or Cancel.
Firm Plann = Example: The requirement may be 100 but the Firm Plann WO is only for 60. Normally in this case if the WO status was standard MRP would instruct user to increase the WO qty from 60 to 100 to fulfill the requirement of 100. But since the WO is Firm Plann, MRP will take no action. See defintion for DUE DATES below for further detail.
If user changes the Work Order Status to Admin Hold or Mfgr Hold, a box will appear on the Work Order Screen (as shown below) giving the user the option to put the Work Order on MRP Hold. If the user does NOT check this box, orders that are In-Process will not be affected in MRP. Manufacturing hold on a Work Order will disallow movement of the parts through SFT.
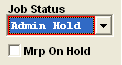
Rework = users will use this status if they do not want to have it included as available to meet demands.
ReworkFirm = users will use this if they want to have it included as available to meet demands. The only thing is that they will have to be sure the due dates for a rework firm precede any demand that was created to use those parts.
NOTE: Work Orders originated from an RMA Receiver will have "ReworkFirm" Job Status and users will NOT be allowed to change the Job Status. Since the material issued to the RMA is likely to be a defective assembly, or requires re-inspection, the work order must be completed by either transferring the material to FGI or to scrap to close the work order. Therefore, an RMA work order cannot be cancelled. Also, users will NOT be allowed to edit or change the Bld qty because when product is brought into the system with an RMA Receiver it is then automatically issued as itself to the kit at that time.
|
Serialized |
If this box is checked, the completed units must be assigned unique serial numbers. |
Customer Name |
The name of the customer for which this Work Order applies.
If BOM is assigned to specific customer, and if there is CONSG part in the BOM -- Only that customer will be available in the WO customer list
If BOM is assigned to specific customer, and no CONSG parts in the BOM -- Default to that customer, but all other customers are available to be selected.
If BOM is not assigned to specific customer, all customer should be available.
|
Forecast Item |
The Forecast checkbox is defaulted as True whether or not there actually is a forecast. By doing this, we minimize the possibility of the MRP double ordering parts for the SO. If there is a forecast, then the SO will be subtracted from it. If there isn’t a forecast, the SO will drive as usual. Users can change to un-checked in the Sales order/Work order if desired. |
Sales Order |
A Sales Order number will be displayed if the Work Order was created within the Sales Order Mgmt module. If you are entering a Work Order through the Work Order module, you can manually link an existing Sales Order to the Work Order. Only if the Sales Order and Work Order is for the same customer and same product number. Keep in mind though that even if you have the SO linked to a WO does not mean that the quantities will always be the same. The link is for reference only between the two modules and they are still individual records so when any changes are made to either the SO or the WO the change will not update or be carried forward to the other. A message is displayed to the users that they will have to make the same changes to the WO.
|
Class |
The classification of the product to be assembled. |
Type |
The type with the classification of the product to be assembled.
|
Part Number |
The number of the make part to be assembled
|
(Rev) |
The revision number pertaining to the part number.
|
Description |
The description of the part to be assembled.
|
Work Order Released |
If this box is unchecked, you are able to kit the work order but you will not be allowed to process the material through SFT. Once this box has been checked, you will be able to move the material through SFT. If user is using the WO checklist feature this box will not be checked until all checkpoints including the "Kit Complete" have been marked off. Once the "Kit Complete" checkpoint has been checked the WO Released checkbox will be checked automatically.
|
(Date) |
The date the Work Order was released.
|
Due Date |
This is the date by which the completed assembly must be completed. Note: The Sales Order Ship Date must be the same or later than the Work Order completion date. MRP will look at the SO Ship Date which should be the same or precede the WO Due Date by the transit time from your dock to the Customer’s dock. The SO Ship Date becomes the Work Order due date when the Work Order is created from the Sales Order, but user may change this date. MRP will recognize the WO as being due in time for the SO ship date, and therefore include the work order as supply to meet the sales order demand, whether or not it’s kitted. If the Work order is kitted and then the dates are moved (either in the sales order ship date to a later date or the work order due date to an earlier date), then MRP will not view the work order (supply) as meeting the sales order (demand). If the work order has been kitted, and thus changed status to a firm planned work order (as far as the MRP module is concerned), then MRP will NOT suggest adjusting the work order delivery date to meet the demand, but WILL suggest creating a new work order (or moving a non-firm planned work order) and ordering the parts for the new work order date. So the keys are the work order due date, and the sales order ship date. The former must be the same or precede the latter, to keep the work order identified as supplying the product for the sales order. User does have the ability to turn off the function of the Sales order driving the demands for the MRP and just use the Work Order for buying components by checking the MRP on Hold box in the Sales Order module per line item.
Note: The Kitted BOM Cost calculations displayed on the "Kit to Close Report" is based off the WO Due date and compares that to the EFF/OB dates on the BOM. So users need to be VERY careful with the WO Due Dates and make sure that they stay current along with the EFF/OB dates on the BOM.
|
Build Qty |
The number of units which must be completed.
|
Completed |
The number of units already completed.
|
Balance |
The number of units which still must be completed.
|
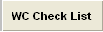 |
Depressing this button will display the applicable Work Order Check List (shown below).
|
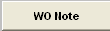 |
Depressing this button will display the applicable Work Order Notes |
WO Check List Screen field definitions:
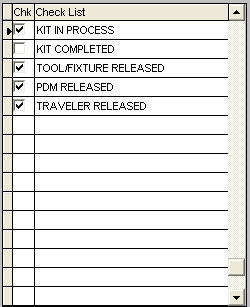
Chk |
A check mark in this box means that the check list item has been completed.
|
Check List |
The description of the check list item.
|
Init |
The initials of the person who performed the check.
|
Date |
The date of the check list performance.
|
Time |
The time of the check list performance.
|
|