. . . . . . . . . . . . .
|
|
Add a Line Item Shortage |
Pressing the Add Button (after finding a work order) displays the following selection choices:
|
|
Shortages other than those resulting from an incomplete kit are considered Line Shortages. Line shortages may be a result of poor yield on a part, and additional parts are required, or because one or more additional parts are needed for the work order beyond those described in the bill of materials. Line shortages may be created because of alternate parts, special engineering evaluations, or for any reason that the user decides to enter in the system setup.
For Miscellaneous Shortages, (this selection may be used to issue non-inventory items to kit) the user may type in the Part Number, Revision and Description and then select Source, Class, Type, Department and Reason from the respective Drop Down lists. The user may type in the Quantity and Quantity/Unit.
If you select Add Line Shortages, you will be prompted for your password and then the following screen will appear: (NOTE: If line shortages are added and issued to rework WOs, the kit status will update to “REWORK”). True "Phantoms" cannot be added as a line item shortage to a kit.
NOTE: The Line item shortages are considered as in the WIP account all the way through until the Kit is closed within the Kitting module. Upon Closing the kit within the Kitting module the Line Item Shortages are then costed out and credited out of WIP account and debited in the Mfgr Variance account. So the “Inventory WIP Valuation Report” by Work Order by Standard Cost does not deduct those line item shortages as the product is moved into FGI. See Article #1777 for further detail.
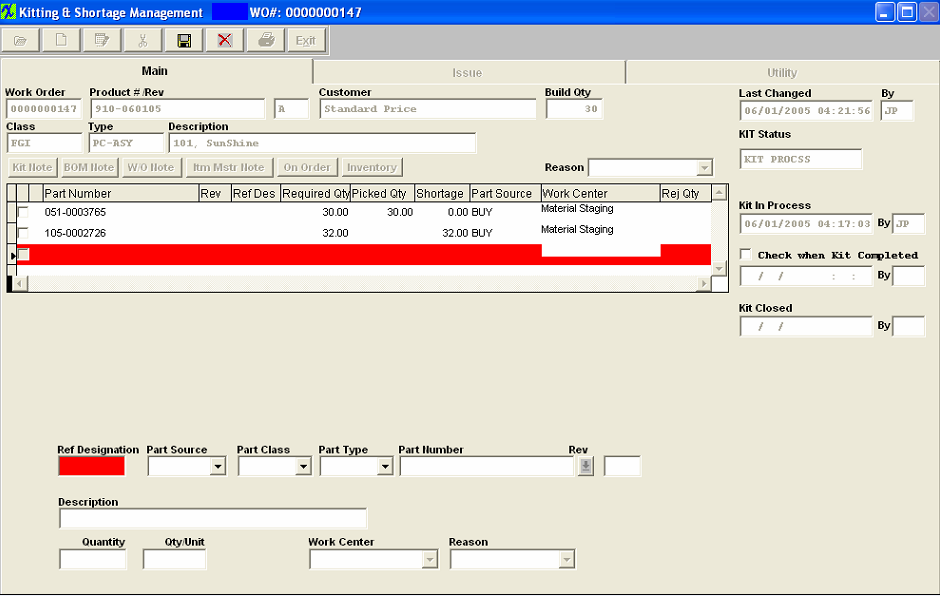
The bottom of the Main information tab is opened up to display an area to enter the part information necessary to describe the shortages.
The part information for the shortage is entered. The part must be a part defined in the Inventory Control Item Master. Select Part Source, Part Class, Part Type, Part Number from the respective drop down lists. Type in the Quantity and the Quantity per Unit. Note: Shortages recorded by Ref Designator are case sensitive.
If the part is already on the Bill of Material, the work center may be selected. Otherwise, it is left blank.
There must be a reason for the shortage entered in the Reason field. These reasons are established in the Return/Shortage Reason in System Setup. The user chooses the appropriate reason from the drop down list. The reason will appear in the Reason box.
|
|
When shortages have been saved for the work order, they will be added to the Kit Status section of the main information tab. The item will be preceded with the rho (? ) symbol to differentiate it from a kit shortage, as displayed:
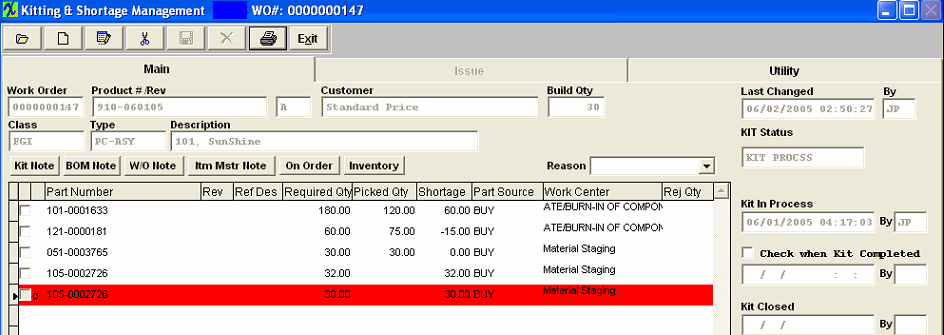
“Ignore Shortage” box: If you want to remove the component from the shortage reports and MRP, check the box at the left of the part number. Note that the box for checking KITTED shortages only works with those items that are kitted based on the BOM for the assembly. Checking the boxes means that the part on the BOM will NOT be considered for MRP purposes, and NOT show up on shortage lists. This is the only way you can get a part on the BOM, off of the shortage list. Line shortages, however, can be edited to make them larger or completed. The user should NOT create a line shortage, then try to check the “ignore shortage” box. A line shortage is either short or not. If it is not short for this particular work order, then check the box to take it off of the shortage list.
Add a Miscellaneous Shortage
If you select Add a Miscellaneous Shortage you will be prompted for your password, and then the following screen will appear:
Type in the Part Number, Revision and Description. Select Source, Class, Type, Department, Reason from the respective Drop Down lists. Type in the Quantity and Quantity/Unit. Continue in this fashion until all entries are made. Depress the Save button.
Issue or Edit a Line Item Shortage
Pressing the Edit Button (after finding a work order) displays the following selection choices:
|
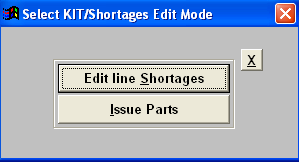 |
If user selects "Edit line Shortages", you will be prompted for your password and then you will have the opportunity to change Quantity, Quantity/Unit or Work Center Selection for an existing line item shortage.
This field is intended for the user to enter in the qty needed for the shortage and the system will make the needed adjustments based off from that qty.
For Example: if the user originally added a line item shortage for a qty of 5, and picked a total of 7 to the kit. (Production has no way of knowing how many were pulled to the kit originally, so a week later they come back to the stockroom, and request 4 more). The stockroom will then edit the line item shortage at this time the qty will display a -2.00, stockroom will issue 4 more by entering a qty of 4, the system will make the adjustments based off from that qty, so the Required qty will then become 11.
NOTE: You can only reduce the shortage qty if there are no issues against it. If the complete shortage qty has been issued, and user depress the Edit line Shortage button and the qty field is "0" and user enters a qty in the qty field the system will interpret this as an additional qty. To change a qty that has already been issued user would need to un-issue the complete qty and then go back and change the shortage qty. System will not allow user to enter a negative qty.
Depress the Save button when changes are completed.
If user selects " Issue Parts" enters their password, they may follow the steps outlined in Article #904.
Add a Line Shortage to a Rework Work Order
Overview of a Rework Order
When a rework order is created via the RMA Receiver module (Please refer to the Return Material Authorization Management manual), there is no demand created for any parts on the BOM for the product of the work order. But, demand will be created for any line shortages established for the work order. There should be a line shortage created for the assembly being reworked, so the product can be issued to the work order.
When the work order has the kit closed, the manufacturing variance is created that is the difference between the standard cost of the parts issued to the work order and the standard cost of the sum of all of the BOM components.
If there is no BOM for the product, but if the assembly has a standard cost assigned to it, the following will happen:
There will be a favorable variance to the wip (the difference between the standard cost of the product and the standard cost of the sum of the materials on the BOM) Assembly Standard cost – zero BOM cost.
The kit close will have an unfavorable variance created for accounting which will be the sum of the standard cost of the components issued to the work order. The kit close will offset the line shortages pulled.
To add a line shortage to a rework work order, follow the same procedures as finding the work order, as detailed above.
Depress the Add button to add a new line shortage. Type in your password. Then follow the procedures to add and pull a line shortage as detailed above. Upon completion, you will see a message at the top right hand side of the screen that inventory files are being updated. Then the part information in the lower part of the screen will turn blank.
Exit the kitting module and then proceed to the shop floor tracking module to complete the rework order.
The Delete button is used to remove line shortages before the part has been pulled for that line item. Find the Work Order containing the line shortage, using the find procedures. After selecting the delete button, the user is asked for an authorized password. Then the user selects the item to be deleted. Highlight the line item containing a rho symbol (? ) at the far left of the part number.
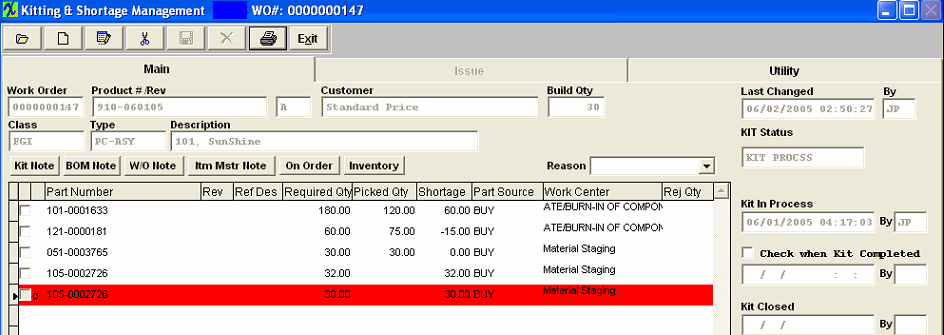
The following message will appear:
Depress the OK button.
The item will disappear.
|
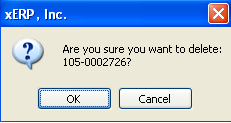 |
|
|
|
|
|
Article ID: 4842 |
|