Work Order Shop Floor Tracking |
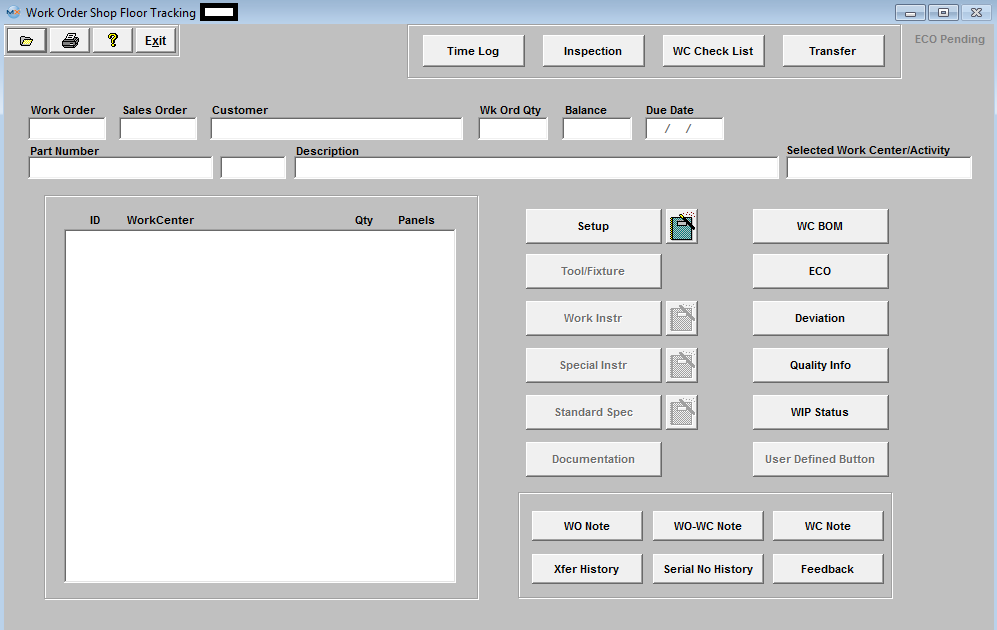
Work Order Shop Floor Tracking Fields and Definitions
 |
This Text/characters turns RED if an ECO (Engineering Change Order) is Added and Saved. When the ECO is approved, this button characters turns back to gray. This criteria is based on the product number and no revision number as the ECO will change the revision number.
This feature has been added because of the importance of the users needing to know that an ECO is being initiated by the production personnel. This will help prevent product being built according to the original instructions and cut down on any additional rework or schedule delays.
|
Work Order |
The Selected Work Order |
Sales Order |
The Sales Order linked to the Selected Work Order |
Customer |
The Customer Name associated with the Selected Work Order |
Wk Ord Qty
|
The number of units for the Selected Work Order |
Balance |
The remaining balance of the parts to be delivered for the work order |
Due Date |
The due date for the first shipment remaining to be shipped in the work order (ignores due dates that have already been shipped). |
Part Number
|
The part number of the assembly being built for the work order. Next to the part number is a space for revision |
Description |
This field will contain the Class, Type and Description of the assembly being built for this work order. |
Selected Work Center/Activity |
This area displays the work center (or activity) from which each of the action buttons below are launched.It is selected by placing the cursor (by mouse or tab) on the work center (or activity) of interest. |
ID |
The ID or abbreviation established for the work center. |
Work Center |
The Work Center's assigned to the MAKE part in Work Order Traveler Setup |
Qty |
The quantity of parts pertaining to the work order that are currently in the work center.
|
Panels |
This field will contain the number of panels in the work center (if the user tracks panels, based on conditions in the Shop Floor Tracking Defaults).
|
See Article #3107 for the Directive Buttons fields and definitons
|
|
|
|
|
Article ID: 4220 |