. . . . . . . . . . . . .
|
|
Sales Order Tab |
Sales Order Tab field definitions
 |
Access to WebManEx |

|
Depressing this button will display the complete history of all changes made to this order. It will list the Date/Time of Change, By User, SO Total at time of change, and List of Changes recorded. The following changes are recorded when a sales order is saved, if a new sales order is created, or if an existing sales order is edited.
For the header level - Customer PO#, Billing and Shipping Address changes, SO status changes, Approved and acknowledge status changed, Acknowledge document name changes, recognizes if notes have been changed (SO Note, SO Acknowledgement Footnote), but will not record the differences between them. This will be the users responsibility to record and track the modifications within the note fields.
For the detail level - New item, removed item, quantity changes, status for the item changes.
For the schedule level - New/removed schedule line, qty scheduled, date scheduled.
For the price level - New price line, removed price line, price description, price, sales type.
|
Sales Order |
This is the number assigned to the Sales Order. |
Order Date |
This is the date of the Sales Order.
|
Customer |
This is the Name of the Customer.
|
SO Status |
This is the status of the Sales Order, Open or Closed.
|
 |
The main purpose of this button is to link a scanned copy of the signed acknowledgement from the customer to the SO for records, so you have proof linked right to the sales order that it was acknowledged by the customer. |
Buyer |
This is the name of the Customer’s purchasing agent.
|
Customer PO |
This is the Customer’s Purchase Order Number.
|
SO Approved |
This field will only be displayed on this screen if the "SO Approval Required" box is check within the Sales Order Defaults & Sales Discount Type module. This box must be checked (if displayed) before a WO can be created for this SO. Below the check mark is the date of approval and the User ID of the user who approved the SO. |
Order Ack |
A check in this box means the Customer’s Purchase Order has been accepted by the user. Below the check mark is the date of acknowledgement and the User ID of the user who acknowledged the Sales Order. Note: Without this check mark, the order can’t go forward in the system.
|
Last Modified by |
This will display the date and User ID of the last person that made changes to the Sales Order |
Ln |
The Sales Order Line Item Number.
|
Part Number |
The number the user has assigned to the part or product.
|
Rev |
The revision number pertaining to the part number.
|
Class |
The classification to which the part number belongs.
|
Type |
The type within the classification to which the part number belongs.
|
Description |
The description of the part number. |
Ord Qty |
The quantity of that part number ordered by the Customer.
|
Back Order |
The un-shipped portion of the part number.
|
Shipped Qty |
The amount of the order already shipped.
|
UOM |
Unit of Measure.
|
Extended |
If the Pricing Screen has been filled in, this will be the amount that the user will charge the customer for this line item.It is the sales quantity multiplied by the price for 1 unit.
|
Project Number |
Select a Project number from the pulldown if this record is to be associated to a project. To remove the Project number, right click on the field. If parts are allocated to a project and the project is selected in SO for the SO item, when the part is shipped, those allocated to that project parts will be available to be shipped. After the project is selected in SO, the new created WO will link to that project.
|
Line Status |
This is the status for the line item highlighted on Sales Order: (Standard; Priority-1; Priority-2; Admin Hold; Mfgr Hold; Forecast; or Cancel)
The system defaults the line item to Standard. Standard is the ordinary Sales order line item status. Priority is set up as a make ahead of all other orders, Priority-1; being the most important and Priority-2; the second most important. Admin Hold is an order on hold due to customer credit, etc (this will not interfere with the production but will prevent shipping). Mfg Hold will not interfere with the production but will prevent shipping. Forecast will not interfere with the production but will prevent shipping. Status means user is entering SO line item as a forecasted item. Will not allow WO's to be created for the line item while in forecast status. Only drives demand on the components in MRP does not call out for WO's to be created.
The user may put orders on Admin, Manufacturing Hold, or Forecast without affecting MRP. If user wants to prevent MRP from giving Release WO demands for line items with Admin or Mfgr Hold Status they will need to check the MRP on hold checkbox.
|
MRP On Hold |
This option gives the users the ability to turn OFF the function of the Sales Order line item driving the demands for the MRP and just use Work Order for buying components. If this box is checked on the SO, MRP will instruct you to cancel all open PO(s) for the components needed for this SO and to cancel any WO demands linked to this SO.
There is an option in System Setup/Sales Order Defaults that will automatically check the box when adding a SO Line item. When using the system in this mode if you create a WO Manually, the MRP will tell you to cancel the WO since there is no SO demand. This can be solved by doing the below.
Open/create Firm planned WO's so the MRP will not keep instructing you to cancel the order.
This is a perfect solution for customers who want to build products based on forecasts or promised to maintain certain amount of FGI in inventory. They can use the Forecast Line status along with firm planned WO status to accomplish this and use the SO still to ship products from FGI inventory.
|
SI |
(Source Inspection) This field has been added for future use. It is not linked to any other modules at this time. |
FA |
(First Article) This field has been added for future use. It is not linked to any other modules at this time. |
Fcst Item |
The Forecast checkbox is defaulted as True whether or not there actually is a forecast. By doing this, we minimize the possibility of the MRP double ordering parts for the SO. If there is a forecast, then the SO will be subtracted from it. If there is NOT a forecast, the SO will drive MRP as usual. Users can change to un-checked in the Sales order/Work order if desired. |
SO Amount |
The sum of the Extended column.
|
Primary Tax |
The Primary tax pertaining to the sale. If foreign tax is checked in the Customer Information module. |
Secondary Tax |
The Secondary tax pertaining to the sale. If foreign tax is checked in the Customer Information module. |
Tax |
The total tax pertaining to the sale.
|
Discount |
The sales discount allowed to this customer. This will default in from the Customer Information module.
|
SO Total |
The total of the Sales Order.This is adding the Tax to and subtracting the Discount from the SO Amount.
|
For the line item highlighted:
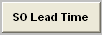 |
Depressing this button will bring up the the following message:
|
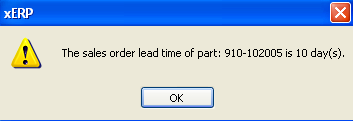 |
This message is for a MAKE part only. This message will display the Longest Lead Time based on the following:
Component Purchase Lead Time 1 week (5 days)
Product Kitting Lead Time& 2 days
Product Production Lead Time& 3 days
Total Sales Order Lead Time& 10 days
Note: The SO lead-time does NOT calculate the purchase lead-times of buy parts associated to sub assemblies. It will consider the kitting and production lead-times of the make part itself along with any buy components on the top level assembly in calculating the longest lead-time. The system assumes that the sub-assembly is complete at the time your kitting it for the top assembly.
|
 |
Depressing this button will bring up the following screen.
|
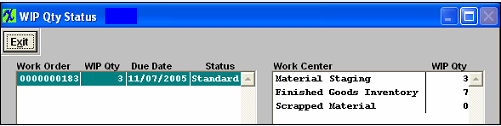 |
For the Work Order number highlighted, the WIP quantity, due date, status and the Work Center location will display.
|
FGI Qty |
This is the quantity currently on the floor ready to ship.
|
 |
Depress this button to add a note for the line item highlighted, this note is for internal use only. This note will be printed on the Sales Order Acknowledgement report but will NOT be printed on Packing List or Invoice. This note will be displayed on screen when viewing the Packing List and/or Invoice.
|
Directive Buttons:
|
|
|
|
|
Article ID: 4094 |
|