ManEx Minute - 23 - Minimum Buys and Residual Inventory |
|
|
"Again gain is gain, however small."
-Robert Browning
|
|
|
May 13, 2009
Issue 23
Greetings!
We have started loading the lists of excess inventory into component exchange. I am excited for the pending BETA release. I hope to have screen shots and instructions ready very soon.
This issue of the newsletter focuses on handling minimum buys and residual inventory. It is a tough problem and one that many companies do not handle well. It is hard to find the balance between competitive pricing and profitability and minimum buys can often make the difference.
As always, we look forward to your participation and feedback as you gain new insights and become a more effective provider of Electronic Manufacturing Services.
Sincerely,
David Sharp
ManEx, Inc.
|
Business Case - Inventory Control
|
Residual Inventory
|
North Eastern Company (NE Company)* is finalizing a bid for a prospective customer launching a new product. The business has the potential of exceeding 40% of last year's sales. This customer has requested pricing on small to large volumes so they can ramp up production.
The customer will start with small orders. For those assemblies that go into high volume production, excess inventory is a non-issue. The inventory turn is high enough to minimize the impact of keeping extra parts on the shelf. However, any assemblies that do not go in to high volume production could potentially result in a significant inventory value sitting on the shelf.
Fortunately, many of the components are common among multiple customers and have high annual usage. These parts are not a concern. However, there are also several parts that are unique to the customer and that have high minimum order quantities and multiples.
At the time of the quotation, there is no way to know which assemblies will result in large production orders. NE Company wants to account for the minimum buys, but cannot simply roll it in to the quote as it would cause the pricing to be uncompetitive. They need some way to account for the extra parts and recoup the cost if they cannot use the parts in a reasonable time.
How can NE Company efficiently track inventory purchased for a job? How will they charge the customer for the parts not used? Is there a way for them to maintain visibility of the parts and make it easy to consume them if possible on other jobs?
*Name has been changed
|
Business Case Solutions
|
Component Pricing and Residual Inventory are critical factors in the contract manufacturing world...
|
ManEx Case Solution
|
ManEx is the best ERP system on the market for electronic contract manufacturers. No other system provides better control and more detail in component tracking than ManEx ERP...
Read the full ManEx Case Solution >>
|
|
|
|
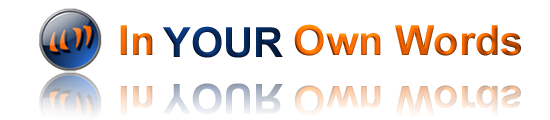
|
Minimum Purchases and Residual Inventory
"Because of the nature of our business, QTY and EAU decide the method.
"Decision on how to handle the cost is, relative to the customers business model. Can they provide EAU's? If so, we may sit on it or put it in one of our Suppliers in-house stores for their releases. If it is shared, than we wouldn't charge them. If it's a one time build, than we buy strips. If we cannot, than we charge them for the excess."
-Mike, AZ
"We charge customers for the excess parts qty. We then ship the parts to the customer. There is a period of time where we are holding the inventory on our books."
-Tom, OR
"[Using In-Store is] improving inventory turns."
-Mike, IL
|
 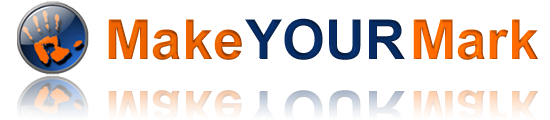 |
Please share your ideas and insights on a topic below. Use the questions to direct your response. You can submit your thoughts to mym@manex.com by clicking the topic title. Where appropriate and space permitting, we will post responses in a future newsletter so all may benefit.
Tracking Components in Production
When you kit, do you kit by production work center?
Do you have separate bin for each work center?
Do you try to offset the components for later work centers to maximize cash flow?
How often do components end up in the wrong work center?
Do you track when you have pulled extra parts for a kit?
To suggest a new topic please send an email to mym@manex.com.
|
©2008 All Rights Reserved.
ManEx Minute is a bi-weekly email distributed by ManEx, Inc. |

Developing with YOU in mind! |
|
|
|
|
|
|
|
|
|
Article ID: 3316 |