ManEx Minute - 20 - Work Order Numbering |
|
|
"It is wiser to find out than suppose."
-Mark Twain
|
|
March, 25 2009
Issue 20
Dear David,
We are already to our 20th issue. So far, most have focused on obvious and big decisions or challenges, but there are many, seemingly small, choices that CMs make that can have a significant impact on efficiency.
As suggested by one of our readers, today's newsletter will focus on the decision for numbering Work Orders.
According to the most recent survey, 75% of you do not give Work Order Numbering a second thought letting the system determine the next work order number. However, another 15% are interested in and considering this option.
Is there a best practice, or like most things, is the answer "it depends" ?
As always, we look forward to your participation and feedback as you gain new insights and become a more effective provider of Electronic Manufacturing Services.
Sincerely,
David Sharp
ManEx, Inc.
|
Business Case - Inventory Control
|
Work Order Numbering
|
North Eastern Company (NE Company)* recently hired a new production manager. Dan has extensive experience in the industry and NE Company is confident he will be able to help them improve their processes and profitability.
Along with other ideas, Dan suggested they consider implementing an intelligent numbering system for Work Orders.
At his last company, Dan set his work order numbers to coincide with the related sales order number and believed it offered real value for improving traceability and reporting. NE Company was letting the system generate the Work Order numbers and wasn't sure if there was a need or benefit to manually managing these numbers. However, at Dan's suggestion, they decided to review this practice to see if they could benefit from this change.
Before making the change, they needed to know, what benefit could they realize from this change? What impact would it have on their processes? What were the negative implications of this change? What were the system capabilities and limitations in implementing a change like this? And finally, did it make sense for them given their current situation, operations, and mix of customers and assemblies?
*Name has been changed
|
Business Case Solutions
|
The choice between adding intelligence to Work Order Numbers and letting the system maintain the numbers may not be as obvious as it first appears. Companies must weigh the "costs" of each method and determine if they are greater than the benefits and savings created.
|
ManEx Case Solution
|
ManEx will allow users to control Work Order Numbers both manually and automatically. Users are able to switch back and forth between the methods as needed.
Read the full ManEx Case Solution >>
|
|
|
|
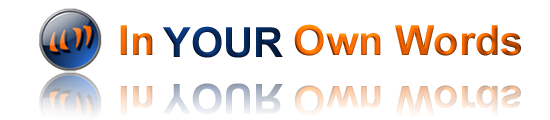
|
WORK ORDER NUMBERING
"[With intelligent numbers] we are able to track: Labor time by Sales Order, Shortages by Sales Order, [and] Purchases by Sales Order.
"Also, we are able to associate Work Order items with a Sales Order even though the assembly is not a deliverable item on the Sales Order."
- Nick, PA
"We use the following categories:
N00000009999 - N denotes a prototype department work order. Number characters are not intelligent
V00000009999 - V denotes a first production run item. Number characters are not intelligent.
000000009999 - regular number is for regular repeat order production and is not intelligent
00000R99999 - R denotes RMA followed by the RMA number. If multiple shipments come in it will be followed by b,c,d, etc."
- Mark, WI
"A short numerical number is the best way to handle this...Making [work order numbers] significant would be a mistake."
-Wayne, OR
"Our work order numbers have the sales order number, item number, and then the work order number (separated by dashes) to indicate the related sales order for the job (i.e. 9999-99-9999)."
-Anonymous
We use two digit codes to indicate Customer, Assembly, and Facility. For example: 01AESJ would be for assembly code AE for [Customer A] built in San Jose.
-Anonymous, TX
|
 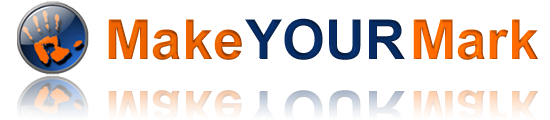 |
Please share your ideas and insights on a topic below. Use the questions to direct your response. You can submit your thoughts to mym@manex.com by clicking the topic title. Where appropriate and space permitting, we will post responses in a future newsletter so all may benefit.
Performance Tracking
How do you track expected and actual time on a job?
What is your standard variance between expected and actual?
What do you do when you find a variance in labor hours?
Do you factor actual labor hours into your future pricing?
What benefits have you seen from this approach?
Part Cross Reference
When and why do you have multiple instances of the same part in your item master?
If you duplicate a part, how do you tie it to the original?
How often do you need to cross between parts?
How long does it take to identify a matching or related part in your item master?
What is your biggest issue with crossing parts?
To suggest a new topic please send an email to mym@manex.com.
|
©2008 All Rights Reserved.
ManEx Minute is a bi-weekly email distributed by ManEx, Inc. |

Developing with YOU in mind! |
|
|
|
|
|
|
|
|
|
Article ID: 3280 |