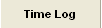 |
The Time Card module has two functions:1) to enter the worker coming in at the first of the shift and exiting for the day, and 2) to track time spent by each worker on each Work Order (Job), by date and time. This information will forward to the Time and Attendance module. |
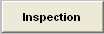 |
See Article #1769 for detail on entering Quality Inspection results using this function. Data may be used to track line quality based on customer, work center, product, location, etc. All Statistical Quality Control information and graphics are based on data entered here. |
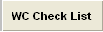 |
Depressing this button will display a list of items defined to be checked as completed for a specific Work Center. The users visit this screen, identify the items completed, and enter their password, marking the check list with their initials and date completed. For further information see Article #3552. |
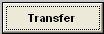 |
The key function of this module. This is where the users identify the number of products moved from one work center to another during the production of the work order. For further detail see Article #857 . |
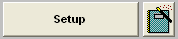 |
When the Work Center Activity Setup and Run is entered, clicking in this area will provide the user with both text and pictorial instructions for setting up the work center. |
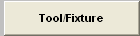 |
Depressing this button will display any Tool/Fixture information which has been assigned to the Product through the Routing or Product Data Management (PDM) Module. NOTE: For this button to be enabled user MUST have the "Tool/Fixture Released" box checked on the Check List Title screen.
|
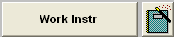 |
When the Product Data Management module is used, clicking in this area will provide the user with both text and pictorial instructions for processing the product in the work center. NOTE: For this button to be enabled user MUST have the "PDM Released" box checked on the Check List Title screen. |
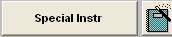 |
When the Product Data Management module is used, clicking in this area will provide the user with both text and pictorial instructions for the product and work center. The Special Instructions are not printed on the travelers. NOTE: For this button to be enabled user MUST have the "PDM Released" box checked on the Check List Title screen. |
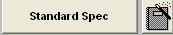 |
Identifies standard specifications relating to this product per the Standard Process Specification module. NOTE: For this button to be enabled user MUST have the "PDM Released" box checked on the Check List Title screen. |
 |
Provides a list of documents relating to the product being assembled. Displays the document number, revision, document date, and notes about the document. NOTE: For this button to be enabled user MUST have the "PDM Released" box checked on the Check List Title screen. |
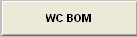 |
This screen will list all part number assigned to the specific Work Center within the BOM module. It will also allow the user to view the entire BOM if desired.
|
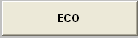 |
|
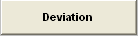 |
This screen will list the detailed information pulled forward from the ECO Control Management module pertaining to any approved Deviations for the selected product. |
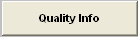 |
Will display the Quality information for the selected Work Center based on the information entered within the Inspection module.
|
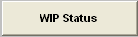 |
Show all the open work orders for this product and show where the quantities are in the shop floor.
|
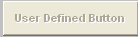 |
This is an outside call program that ManEx has implemented into the system. The Users can have their own program to run when they scan their serial number inside of shop floor tracking by using the “User defined” button. Within the System Setup/Outside Program Calls Setup module, the user will have the ability to change the button name of the “User Defined” button and select which program (EXE) they want to run after the users scans specific Serial Numbers. |
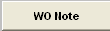 |
Any notes entered for the work order in the Shop Floor Tracking screen will cause the button to turn Red. Any comments in this area will be visible to all work centers which are included in the work order routing. |
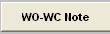 |
Any notes entered specifically for the work order and the work center being viewed will cause the button to turn Red, calling the user’s attention to review notes that are applicable to the order. This button is sensitive to the work center being highlighted on the shop floor tracking screen. |
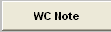 |
Any notes entered for the work center highlighted on the shop floor tracking screen will cause the button to turn Red. Any comments in this area will be visible to all products which include the work center in the routing. |
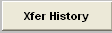 |
This button allows the user to view the history of product transfer from one work center to another. NOTE: If the product has changed revisions from the ECO module, the SFT module will see it as a different product and no longer display the Transfer History information on screen for the old revision. (See Article #3401 for more detail).
Note: If product is serialized the transfer history screen will list each product individually, treating each serial numbered product as its own seperate part for tracking purposes, as displayed in the screen below:
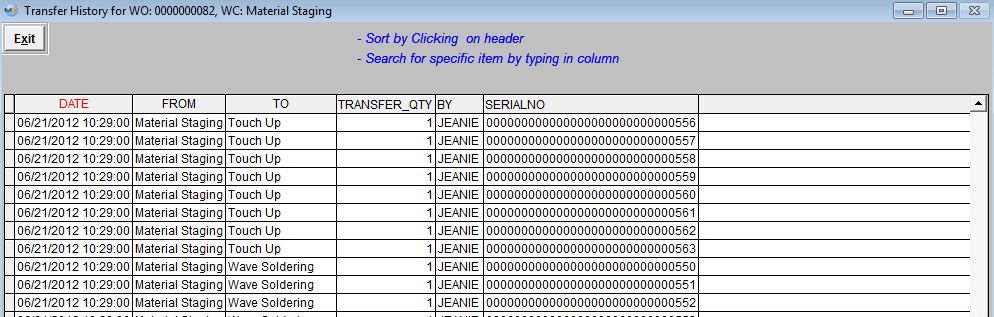
If product is not serialized the xfer history will list qty's as they are transfered, as displayed in the screen below:
|
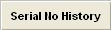 |
This button will display Transfer History and Defect History by specific serial numbers.
|
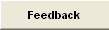 |
This is simply a note screen that may be used to record information about the product during the course of manufacturing, and is specific to the work center and work order. |